电动注塑机技术简介
全电动注塑机工作原理
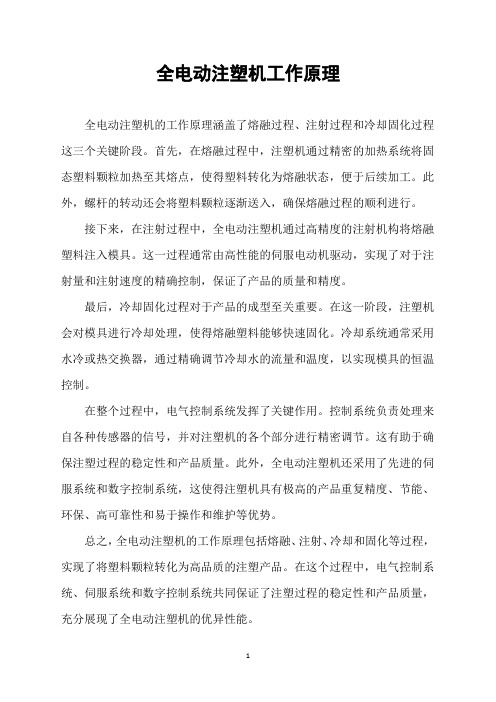
全电动注塑机工作原理
全电动注塑机的工作原理涵盖了熔融过程、注射过程和冷却固化过程这三个关键阶段。
首先,在熔融过程中,注塑机通过精密的加热系统将固态塑料颗粒加热至其熔点,使得塑料转化为熔融状态,便于后续加工。
此外,螺杆的转动还会将塑料颗粒逐渐送入,确保熔融过程的顺利进行。
接下来,在注射过程中,全电动注塑机通过高精度的注射机构将熔融塑料注入模具。
这一过程通常由高性能的伺服电动机驱动,实现了对于注射量和注射速度的精确控制,保证了产品的质量和精度。
最后,冷却固化过程对于产品的成型至关重要。
在这一阶段,注塑机会对模具进行冷却处理,使得熔融塑料能够快速固化。
冷却系统通常采用水冷或热交换器,通过精确调节冷却水的流量和温度,以实现模具的恒温控制。
在整个过程中,电气控制系统发挥了关键作用。
控制系统负责处理来自各种传感器的信号,并对注塑机的各个部分进行精密调节。
这有助于确保注塑过程的稳定性和产品质量。
此外,全电动注塑机还采用了先进的伺服系统和数字控制系统,这使得注塑机具有极高的产品重复精度、节能、环保、高可靠性和易于操作和维护等优势。
总之,全电动注塑机的工作原理包括熔融、注射、冷却和固化等过程,实现了将塑料颗粒转化为高品质的注塑产品。
在这个过程中,电气控制系统、伺服系统和数字控制系统共同保证了注塑过程的稳定性和产品质量,充分展现了全电动注塑机的优异性能。
1。
电动注塑机和液压注塑机的区别及优缺点【对照表】
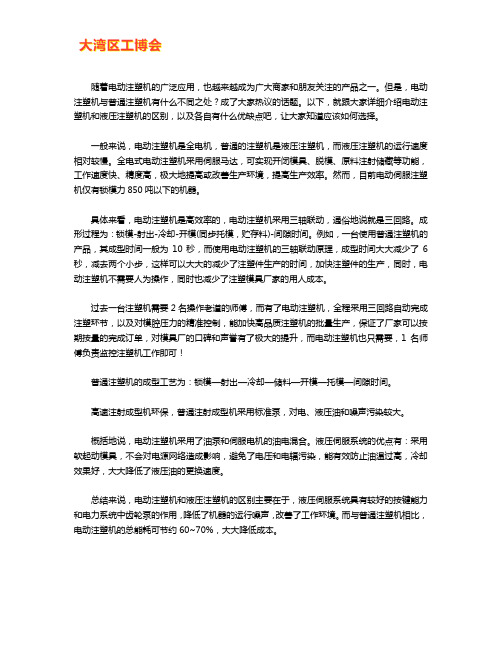
随着电动注塑机的广泛应用,也越来越成为广大商家和朋友关注的产品之一。
但是,电动注塑机与普通注塑机有什么不同之处?成了大家热议的话题。
以下,就跟大家详细介绍电动注塑机和液压注塑机的区别,以及各自有什么优缺点吧,让大家知道应该如何选择。
一般来说,电动注塑机是全电机,普通的注塑机是液压注塑机,而液压注塑机的运行速度相对较慢。
全电式电动注塑机采用伺服马达,可实现开闭模具、脱模、原料注射储藏等功能,工作速度快、精度高,极大地提高或改善生产环境,提高生产效率。
然而,目前电动伺服注塑机仅有锁模力850吨以下的机器。
具体来看,电动注塑机是高效率的,电动注塑机采用三轴联动,通俗地说就是三回路。
成形过程为:锁模-射出-冷却-开模(同步托模,贮存料)-间隙时间。
例如,一台使用普通注塑机的产品,其成型时间一般为10秒,而使用电动注塑机的三轴联动原理,成型时间大大减少了6秒,减去两个小步,这样可以大大的减少了注塑件生产的时间,加快注塑件的生产,同时,电动注塑机不需要人为操作,同时也减少了注塑模具厂家的用人成本。
过去一台注塑机需要2名操作老道的师傅,而有了电动注塑机,全程采用三回路自动完成注塑环节,以及对模腔压力的精准控制,能加快高品质注塑机的批量生产,保证了厂家可以按期按量的完成订单,对模具厂的口碑和声誉有了极大的提升,而电动注塑机也只需要,1名师傅负责监控注塑机工作即可!普通注塑机的成型工艺为:锁模—射出—冷却—储料—开模—托模—间隙时间。
高速注射成型机环保,普通注射成型机采用标准泵,对电、液压油和噪声污染较大。
概括地说,电动注塑机采用了油泵和伺服电机的油电混合。
液压伺服系统的优点有:采用软起动模具,不会对电源网络造成影响,避免了电压和电辐污染,能有效防止油温过高,冷却效果好,大大降低了液压油的更换速度。
总结来说,电动注塑机和液压注塑机的区别主要在于,液压伺服系统具有较好的按键能力和电力系统中齿轮泵的作用,降低了机器的运行噪声,改善了工作环境。
全电动注塑机介绍
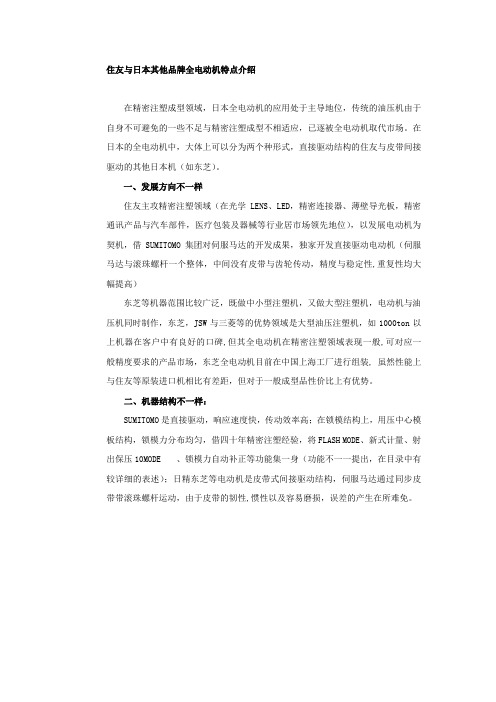
住友与日本其他品牌全电动机特点介绍在精密注塑成型领域,日本全电动机的应用处于主导地位,传统的油压机由于自身不可避免的一些不足与精密注塑成型不相适应,已逐被全电动机取代市场。
在日本的全电动机中,大体上可以分为两个种形式,直接驱动结构的住友与皮带间接驱动的其他日本机(如东芝)。
一、发展方向不一样住友主攻精密注塑领域(在光学LENS、LED,精密连接器、薄壁导光板,精密通讯产品与汽车部件,医疗包装及器械等行业居市场领先地位),以发展电动机为契机,借SUMITOMO集团对伺服马达的开发成果,独家开发直接驱动电动机(伺服马达与滚珠螺杆一个整体,中间没有皮带与齿轮传动,精度与稳定性,重复性均大幅提高)东芝等机器范围比较广泛,既做中小型注塑机,又做大型注塑机,电动机与油压机同时制作,东芝,JSW与三菱等的优势领域是大型油压注塑机,如1000ton以上机器在客户中有良好的口碑,但其全电动机在精密注塑领域表现一般,可对应一般精度要求的产品市场,东芝全电动机目前在中国上海工厂进行组装, 虽然性能上与住友等原装进口机相比有差距,但对于一般成型品性价比上有优势。
二、机器结构不一样:SUMITOMO是直接驱动,响应速度快,传动效率高;在锁模结构上,用压中心模板结构,锁模力分布均匀,借四十年精密注塑经验,将FLASH MODE、新式计量、射出保压10MODE 、锁模力自动补正等功能集一身(功能不一一提出,在目录中有较详细的表述);日精东芝等电动机是皮带式间接驱动结构,伺服马达通过同步皮带带滚珠螺杆运动,由于皮带的韧性,惯性以及容易磨损,误差的产生在所难免。
射出,计量,开关模,顶出均采用皮带间接驱动。
而住友在射出,计量,开关模,顶出均采用独家开发的直接驱动,主导电动机结构发展的主要方向。
住友成型机的一般结构住友的射出,计量,开关模,顶针均采用直接驱动,传动部没有皮带,克服了皮带传动的不利影响。
使瞬间启动与停止速度,开关模速度,顶出速度均达到业界最快。
全电动注塑机介绍

全电动注塑机介绍住友与⽇本其他品牌全电动机特点介绍在精密注塑成型领域,⽇本全电动机的应⽤处于主导地位,传统的油压机由于⾃⾝不可避免的⼀些不⾜与精密注塑成型不相适应,已逐被全电动机取代市场。
在⽇本的全电动机中,⼤体上可以分为两个种形式,直接驱动结构的住友与⽪带间接驱动的其他⽇本机(如东芝)。
⼀、发展⽅向不⼀样住友主攻精密注塑领域(在光学LENS、LED,精密连接器、薄壁导光板,精密通讯产品与汽车部件,医疗包装及器械等⾏业居市场领先地位),以发展电动机为契机,借SUMITOMO集团对伺服马达的开发成果,独家开发直接驱动电动机(伺服马达与滚珠螺杆⼀个整体,中间没有⽪带与齿轮传动,精度与稳定性,重复性均⼤幅提⾼)东芝等机器范围⽐较⼴泛,既做中⼩型注塑机,⼜做⼤型注塑机,电动机与油压机同时制作,东芝,JSW与三菱等的优势领域是⼤型油压注塑机,如1000ton以上机器在客户中有良好的⼝碑,但其全电动机在精密注塑领域表现⼀般,可对应⼀般精度要求的产品市场,东芝全电动机⽬前在中国上海⼯⼚进⾏组装, 虽然性能上与住友等原装进⼝机相⽐有差距,但对于⼀般成型品性价⽐上有优势。
⼆、机器结构不⼀样:SUMITOMO是直接驱动,响应速度快,传动效率⾼;在锁模结构上,⽤压中⼼模板结构,锁模⼒分布均匀,借四⼗年精密注塑经验,将FLASH MODE、新式计量、射出保压10MODE 、锁模⼒⾃动补正等功能集⼀⾝(功能不⼀⼀提出,在⽬录中有较详细的表述);⽇精东芝等电动机是⽪带式间接驱动结构,伺服马达通过同步⽪带带滚珠螺杆运动,由于⽪带的韧性,惯性以及容易磨损,误差的产⽣在所难免。
射出,计量,开关模,顶出均采⽤⽪带间接驱动。
⽽住友在射出,计量,开关模,顶出均采⽤独家开发的直接驱动,主导电动机结构发展的主要⽅向。
住友成型机的⼀般结构住友的射出,计量,开关模,顶针均采⽤直接驱动,传动部没有⽪带,克服了⽪带传动的不利影响。
使瞬间启动与停⽌速度,开关模速度,顶出速度均达到业界最快。
发那科全电动注塑机参考资料

发那科全电动注塑机参考资料注塑机是现代工业中不可缺少的设备之一,它主要通过将熔化的塑料高压注入模具中制造出各种各样的塑料制品,包括塑料家居用品、塑料零件、玩具、汽车配件等。
而发那科全电动注塑机则是现代注塑机发展的一大趋势,因其具有低噪音、高效率、节能环保等优势而备受注塑行业的青睐。
本文将从发那科全电动注塑机的基本结构、技术特点、应用范围等方面进行介绍和分析,旨在为读者提供一份全面的参考资料。
基本结构发那科全电动注塑机与传统的液压注塑机相比,最显著的区别就是其不再使用液压系统,而是采用全电动系统。
其基本结构主要包括机身、注射部分、型腔和模具部分、以及控制系统。
1.机身机身是注塑机的主体部分,其外观一般采用铝合金、镁合金等金属材料,以保证机身的坚固和耐用性。
发那科全电动注塑机采用的是全封闭式设计,除了安全门和排气口外,其他部分基本上都被罩住了,以保证生产过程中的安全性和环保性。
2.注射部分注射部分包括供料系统、螺杆、加热器、喷嘴等组成,主要完成对塑料原料的熔化和注塑过程。
发那科全电动注塑机的注射部分采用全电动伺服系统,相比传统液压系统更加智能化,能够根据需要调整注塑压力和速度,实现注塑过程的全程控制。
3.型腔和模具部分型腔和模具部分是注塑过程中最核心的部分,也是影响注塑品质和生产效率的关键因素。
发那科全电动注塑机采用的是高精度的双机械手抓手操作技术,可在约0.6秒的时间内完成模具的取放、定位和调整等工作,大大缩短了模具更换的时间,提高了生产效率。
4.控制系统控制系统是整个注塑机的“大脑”,控制着注塑过程中各个部件的运行状态和参数设置。
发那科全电动注塑机的控制系统采用的是PC机控制技术,具有模块化设计和各种故障保护功能,大大减少了维修成本和故障率。
技术特点1.动力系统发那科全电动注塑机采用全电动伺服系统,与传统的液压系统相比,具有响应速度快、能耗低、噪音小等优势。
2.省能环保全电动注塑机在能源利用方面比传统液压注塑机更加节能环保,不仅可以减少能源消耗,同时还可以降低废气排放和噪声污染。
全电机注塑机控制原理

一、全电动注塑机机械原理1、开模、锁模、顶针等动作采用高精度丝杠螺母,传动精度0.01mm。
2、直线导轨,将传统往复滑动引导转变为滚动引导,提高定位精度,降低机械造价并且大幅度节省电力,可长时间维持高精度。
3、采用新型测力传感器,准确控制背压取得稳定的精密注塑。
4、同步带轮及同步带,结构简单、安装方便、传动精度高,噪声低。
5、采用集中式润滑,容积式比例分配器,保证每点润滑充分。
就上述所说的零件除外还有注塑机器机械原理。
止逆环(过胶圈)---顾名思义,止逆环的作用就是止逆。
它是防止塑料熔体在注射时往后泄漏的一个零件。
射嘴----射嘴是联接料筒和模具的过渡部分。
法兰------法兰是连接射嘴与机筒的零件?在塑料的塑化注射过程中只起通道的作用。
加料斗-----加料斗是储存塑料原料的部件,也有的在加料斗上加上发热和吹风装置做成干燥料斗二、全电动注塑机电控原理伺服系统:是使物体的位置、方位、状态等输出被控量能够跟随输入目标(或给定值)的任意变化的自动控制系统。
伺服的主要任务是按控制命令的要求、对功率进行放大、变换与调控等处理,使驱动装置输出的力矩、速度和位置控制的非常灵活方便。
锁模伺服电机三、伺服电机的工作原理:伺服电机是一个典型闭环反馈系统,减速齿轮组由电机驱动,其终端(输出端)带动一个线性的比例电位器作位置检测,该电位器把转角坐标转换为一比例电压反馈给控制线路板,控制线路板将其与输入的控制脉冲信号比较,产生纠正脉冲,并驱动电机正向或反向地转动,使齿轮组的输出位置与期望值相符,令纠正脉冲趋于为0,从而达到使伺服电机精确定位的目的。
四、伺服电机的控制:标准的伺服电机有三条控制线,分别为:电源、地线及控制。
电源线与地线用于提供内部的电机及控制线路所需的能源,电压通常介于4V—6V之间,该电源应尽可能与处理系统的电源隔离(因为伺服电机会产生噪音)。
甚至小伺服电机在重负载时也会拉低放大器的电压,所以整个系统的电源供应的比例必须合理。
全电动注塑机的特性

全电动注塑机的特性作者:力劲集团 高级工程师 汪存亮1983年日精树脂公司生产出世界上第一台全电动注塑机,一段时期内,因价格和技术的因素限制了全电动注塑机的应用,国内的全电动注塑机市场份额亦非常少,只是近年来,随着伺服电机技术的日趋成熟和价格的大幅度下降,以及环保和节能的需要,为全电动式注塑机的发展注入了新的活力。
与传统的全油压注塑机相比,全电动注塑机在动力驱动系统上彻底抛弃了全油压机油泵马达产生的油压驱动系统,而采用伺服电机(Servo motor )驱动,传动结构采用滚珠丝杆和同步皮带,大幅度提高了注塑机动力系统的控制精度,彻底解决了液压油对环境的污染问题,机械产生的噪声也随之下降,全油压机在能源消耗,性能,使用的费用及机器本身的性价比已处于劣势,那么就此是不是说全电动注塑机将来会取代全油压机呢?下面从几个方面比较两类不同动力源注塑机的特点,全电动注塑机特性与卖点,供注塑机制造商和塑胶制品厂客户选购注塑机时参考:一、从制造环境上讲:全电动注塑机具有节能、环保、噪音低、计量准确等优点,但价格高,且使用寿命上不如全油压机注塑机,而全油压机有环境污染大,噪音高、耗能大之特点,但制造成本低,维修亦比较方便,从制造环境上讲,全电动注塑机对比全油压机有如下特性:1.设计加工精度要求高、外形设计、外购配件质量要求亦高;2.在装配上要求具备高级装配技工的技能支持和清洁的装配工作环境;3.要求有稳定的供电电压;4.如果增加功能,如中子抽芯,则需增加伺服电机数量,成本会更高,维修成本也高;5.使用背压状态,容易造成螺杆卡死;6.机械传动易出现磨损,需使用更多的润滑油脂;7.只能机铰锁模,而油压机除常用的机铰锁模外,亦有直压锁模结构。
二、从控制系统的精度及可靠性来讲:油压机压力油温度或粘度变化时直接影响机械精确度,油压油、液压管通的可压缩性、弹性都对精度产生影响。
注塑机的控制系统也是影响精度的一个重要的方面,油压机控制系统复杂,电子尺位置控制,储料计算,I/O点及模拟量信号处理亦相对复杂,要保证射胶、开锁模控制精度必须使用带闭环控制的伺服阀,而伺服阀价格昂贵亦会带来成本上升,全电动注塑机控制系统比油压机简单,反映也迅速,具有优良的控制精度:1.伺服马达本身特性已可保证提供高精度的位置、速度控制,滚珠丝杆的精度能达到微米级(0.01mm),定位重复精度误差是0.01%;2.提供高响应和高灵敏度的动作;3.提供复杂同步动作,缩短生产周期;全油压机的安装尺寸有其国际标准,多家厂家元件可以互换,带来维修方便、费用低;而全电机伺服马达及其驱动器每个厂家都不尽相同,自我维修困难,维修费用高。
发那科全电动注塑机参考资料

保壓時間 (s e c)
★澆口封閉時間的設定﹐慢慢延長保壓時間﹐不斷觀察樣品并測定重 量﹐直到重量不再談變化為止﹐這之間的時間就叫做保壓時間或澆口 封閉時間﹒ 由保壓工程引起的不良現象﹕
保壓過低 充填不足
縮痕 外觀不良 收縮應力 尺寸減小
保壓過高 毛邊
變形﹒彎曲 破裂
脫模困難 尺寸增大
(3)多段保壓的必要性
2.熱固性樹脂:加熱以后軟化流動,在一定的溫度下固化.它跟雞蛋一樣,在 一的溫度下硬化,而再次加熱后卻不會再軟化熔融.該樹脂在加工成制 品后失去了成型性﹐因而﹐不能再生﹒
FANUC成型机的一般結构
合模軸 Y軸
頂出軸 A軸
計量軸 C軸
射出軸 X軸
模厚調整馬達
射座調整馬達
一.机械部位的构成.
ROBOSHOT射出机不使用液壓油,而是通過伺服馬達直接驅動机械 机构的全電動式射出成型机.其机械部位有用于射出.螺桿回轉,頂出 及開關模的四個AC伺服馬達,而用于模厚調整和噴嘴接触的是齒輪 馬達.
4-1螺桿不后退時﹐是因為背壓設定太高﹐要調整得低一點. 4-2螺桿快速后退時﹐是因為背壓設定太低﹐要調低一點﹒ 5.變更背壓設定值﹐要把螺桿是后退﹐還是不后退的臨界線的背壓作為背 壓設定的最低壓力來理解﹒以背壓的最低壓為基礎﹒觀察成型品﹐慢慢 地提高背壓﹒同時還要考慮樹脂溫度和螺桿回轉數﹒
2﹒螺桿回轉數的設定方法
射出成型工程
1. 射出過程動畫 2.射出過程各動作
o
螺杆的构造
計量部 壓縮部 供給部
壓縮比TF/TM一般取2-3,壓縮比越大,剪切作用越大. FANUC一般取值2.5.
L/D:是指螺杆的有效長度L与直徑D的比.這個比值越大就能達到混煉 良好的樹脂.L/D一般取值為16-20. FANUC一般取值20.
全电动注塑机设计简介
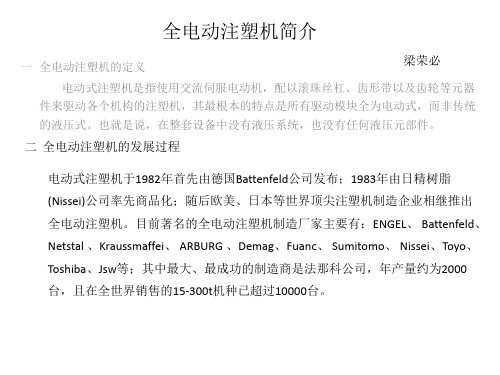
arburg全电动注塑机射胶系统结构
Demag全电动注塑机射胶系统结构
海天全电动注塑机射胶系统结构
六 全电动注塑机设计应注意的地方
1.4 全电动注塑机锁模滚珠的几种安装方式
全电动注塑机丝杠安装方式一
全电动注塑机丝杠安装方式二
全电动注塑机丝杠安装方式三
1.5 目前主流注塑机的锁模系统设计
住友全电动注塑机锁模系统
JSW全电动注塑机锁模系统
法那科全电动注塑机锁模系统
battenfeld全电动注塑机锁模系统
KraussMaffei全电动注塑机锁模系统
arburg全电动注塑机锁模系统
海天全电动注塑机锁模系统
1.6 全电动注塑机主流厂家射胶结构
Toshiba全电动注塑机射胶系统
住友全电动注塑机射胶系统
JSW全电动注塑机射胶系统
battenfeld全电动注塑机射胶系统
FUNAC全电动注塑机射胶系统结构
KraussMaffei全电动注塑机射胶系统结构
三 全电动注塑机优缺点
优点: 1.注射性能稳定。全液压注塑机各项动态技术参数受到液压油温变化的影响,容易发生波动。 相比之下,全电动注塑机的各项动态技术参数基本上没有外界因素的干扰,电脑储存的模具 成型参数始终符合实际成型条件,所以注射性能稳定。精确的注射成型参数的快速应答反应, 只有在伺服电机系统上才能真正体现出来。 2.节能。节能是电动注塑机最大的优势。由于伺服电机根据各执行机构所需力的要求直接进 行驱动,不但提高了效率,而且提高了能量利用率,其能量的利用率可达到95%以上,因此 可比全液压注塑机节能25%~60%。 3. 节水。由于全电动注塑机不使用液压油,仅在加料口处需要冷却水,所以和负载敏感泵的 液压注塑机相比,冷却水的使用量可减少70%;和普通的定量泵的液压注塑机相比,冷却水 可减少90%。 4.效率高。伺服电机的应用,提高了系统的反应性。以ES系列的全电动注塑机为例,其成型 时间仅为全液压注塑机的1/3。由于电动注塑机的各个执行机构都有独立的伺服电机驱动,而 不受系统的影响,所以它能够进行复合动作,例如,在开模过程中可以同时顶出,在塑化过 程中能同时进行合模,从而大大提高了生产率。
全电动注塑机的优缺点分析及技术发展趋势

课题文献综述题目:全电动注塑机的优缺点分析及技术发展趋势学生:指导老师:何亚东一前言我国是塑料制品的消费大国, 而且每年以7%-8%的速度快速增长。
在这期间期间, 油压一机械式注塑机扮演了重要角色, 但在能源日益匿乏、生态环境日益恶化的今天, 油压一机械式注塑机所消耗的能源, 越来越受到人们的重视和关注, 环保式“绿色”伺服电动注塑机的开发己经越来越紧迫和重要。
随着新型合成材料的涌现、高精度注塑件使用范围的扩大及节能环保意识的日益增强, 人们对注塑机的要求进一步提高。
在各种新型精密注塑机中, 最具代表性的为全电动式精密注塑机。
如电子零件、数码相机、手机外壳以及光学器件的精密性不仅对材料的要求很高, 而且对成型技术也提出了相当高的要求。
伺服电动注塑机在解决这类问题上具有得天独厚的优势, 有减轻环境负荷和高性能两大显著特点。
它不仅在节能(耗电量约为一般油压机的1/3)、低噪声、省水(耗水量约为一般油压机的1/12)及电源设备表现出极大的优势, 而且在性能方面具有高注射率、高应答、稳定的注射速度、稳定的背压系统、精确的定位控制、精确的压力闭环、高重复精度、周期短等优点。
因此, 作为“绿色”注塑机, 它的发展不仅符合社会生产力发展的趋势, 而且对发展民族塑机工业并参与国际竞争, 提升整个注塑机行业技术水平具有非常重要的意义。
2 全电动注塑机的技术特点2. 1全电动注射装置全电动注塑机根据注射(螺杆前进/后退)电机的不同分为两种基本结构: 一种是采用旋转电机, 可以很容易产生高速度和高的充模压力; 另一种采用直线电机, 可以实现超高速度注塑。
2. 1. 1 旋转电机驱动注射2. 1. 1. 1 电机通过丝杆传动机构驱动注射螺杆伺服电机驱动滚珠丝杆传动机构时, 可以是传动螺母转动, 丝杆作往复运动; 或者是丝杆转动, 传动螺母作往复运动。
该传动结构又可以分为皮带驱动方式和直接驱动方式:a. 皮带驱动方式是由伺服电机的轴带动皮带轮转动, 再用皮带连接螺杆, 当伺服电机转动时, 动力通过皮带传到螺杆上。
电动注塑机与油压型注塑机的百科全书

电动注塑机与油压型注塑机的百科全书电动/油压注塑机的的由来及发展史电动注塑机(Electric injection molding machine)于1982年首先由德国Battenfeld公司发布;1983年由日精树脂(Nissei)公司率先商品化,当时的产品型号为MM5;在1984年日本塑料工业展览会上,法那克公司、东洋机械金属公司和新泻铁工所分别展出了AUTOSHOT系列、TU系列和MD系列的电动式注塑机。
什么是电动注塑机了,所谓电动式注塑机是指使用交流伺服电动机,配以滚珠丝杠、齿形带以及齿轮等元器件来驱动各个机构的注塑机,其最根本的特点是所有驱动模块全为电动式,而非传统的液压式。
也就是说,在整套设备中没有液压统,也没有任何液压元部件。
电动式注塑机的应用相当广泛,从一般民用和工业用品如汽机车零件、化妆品用容器、家庭用容器、精密齿轮等。
全电动式注塑机是电动式注塑机的主要机型,其注塑装置中的各机构(注射、塑化、计量和移座等)及合模装置的各机构(开合模、锁模、顶出等)全部采用电动机驱动。
与油压式注塑机相比,具有以下优点。
电动注塑机械原理1、开模、锁模、顶针等动作采用高精度丝杠螺母,传动精度0.01mm。
2、直线导轨,将传统往复滑动引导转变为滚动引导,提高定位精度,降低机械造价并且大幅度节省电力,可长时间维持高精度。
3、采用新型测力传感器,准确控制背压取得稳定的精密注塑。
4、同步带轮及同步带,结构简单,安装方便,传动精度高,噪声低。
5、采用集中式润滑,容积式比例分配器,保证每点润滑充分。
注塑油压机也称是一种利用液体静压力来加工金属、塑料、橡胶、木材、粉末等制品的机械。
它常用于压制工艺和压制成形工艺,据需要是多种多样的。
如按传递压强的液体种类来分,有油压机和水压机两大类。
液压传动:它是以液压油为工作介质,通过动力元件(油泵)将原动机的机械能变为液压油的压力能,再通过控制元件,然后借助执行元件(油缸或油马达)将压力能转换为机械能,驱动负载实现直线或回转运动,且通过对控制元件遥控操纵和对流量的调节,调定执行元件的力和速度。
电动注塑机工作原理
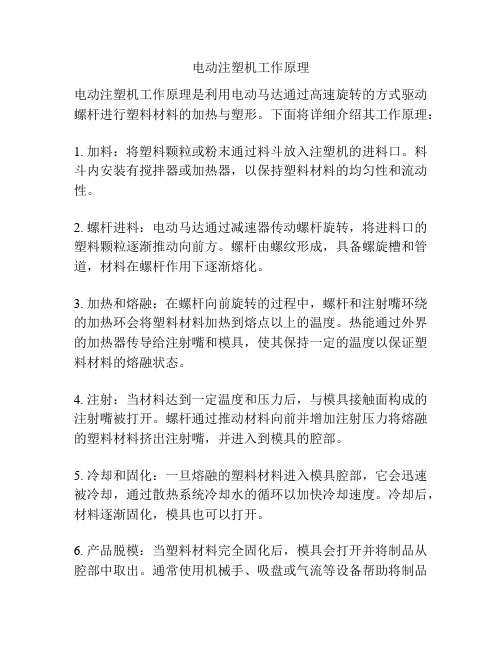
电动注塑机工作原理
电动注塑机工作原理是利用电动马达通过高速旋转的方式驱动螺杆进行塑料材料的加热与塑形。
下面将详细介绍其工作原理:
1. 加料:将塑料颗粒或粉末通过料斗放入注塑机的进料口。
料斗内安装有搅拌器或加热器,以保持塑料材料的均匀性和流动性。
2. 螺杆进料:电动马达通过减速器传动螺杆旋转,将进料口的塑料颗粒逐渐推动向前方。
螺杆由螺纹形成,具备螺旋槽和管道,材料在螺杆作用下逐渐熔化。
3. 加热和熔融:在螺杆向前旋转的过程中,螺杆和注射嘴环绕的加热环会将塑料材料加热到熔点以上的温度。
热能通过外界的加热器传导给注射嘴和模具,使其保持一定的温度以保证塑料材料的熔融状态。
4. 注射:当材料达到一定温度和压力后,与模具接触面构成的注射嘴被打开。
螺杆通过推动材料向前并增加注射压力将熔融的塑料材料挤出注射嘴,并进入到模具的腔部。
5. 冷却和固化:一旦熔融的塑料材料进入模具腔部,它会迅速被冷却,通过散热系统冷却水的循环以加快冷却速度。
冷却后,材料逐渐固化,模具也可以打开。
6. 产品脱模:当塑料材料完全固化后,模具会打开并将制品从腔部中取出。
通常使用机械手、吸盘或气流等设备帮助将制品
从模具中取出并排放到指定位置。
以上就是电动注塑机的工作流程及工作原理,通过螺杆的旋转和加热系统的作用,可以实现塑料材料的熔融、注射、冷却和固化,最终制造出符合要求的塑料制品。
电动注塑机工作原理
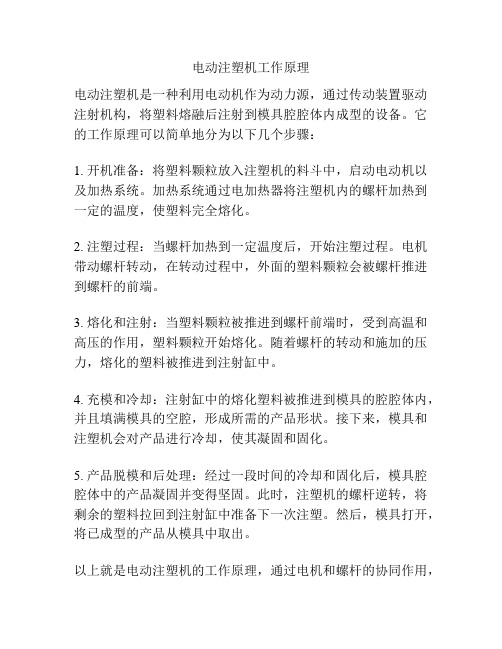
电动注塑机工作原理
电动注塑机是一种利用电动机作为动力源,通过传动装置驱动注射机构,将塑料熔融后注射到模具腔腔体内成型的设备。
它的工作原理可以简单地分为以下几个步骤:
1. 开机准备:将塑料颗粒放入注塑机的料斗中,启动电动机以及加热系统。
加热系统通过电加热器将注塑机内的螺杆加热到一定的温度,使塑料完全熔化。
2. 注塑过程:当螺杆加热到一定温度后,开始注塑过程。
电机带动螺杆转动,在转动过程中,外面的塑料颗粒会被螺杆推进到螺杆的前端。
3. 熔化和注射:当塑料颗粒被推进到螺杆前端时,受到高温和高压的作用,塑料颗粒开始熔化。
随着螺杆的转动和施加的压力,熔化的塑料被推进到注射缸中。
4. 充模和冷却:注射缸中的熔化塑料被推进到模具的腔腔体内,并且填满模具的空腔,形成所需的产品形状。
接下来,模具和注塑机会对产品进行冷却,使其凝固和固化。
5. 产品脱模和后处理:经过一段时间的冷却和固化后,模具腔腔体中的产品凝固并变得坚固。
此时,注塑机的螺杆逆转,将剩余的塑料拉回到注射缸中准备下一次注塑。
然后,模具打开,将已成型的产品从模具中取出。
以上就是电动注塑机的工作原理,通过电机和螺杆的协同作用,
将塑料熔化并注射到模具中形成产品。
电动注塑机具有高效、精准、可重复性好等特点,被广泛应用于塑料制品的生产。
电动注塑机的技术简介
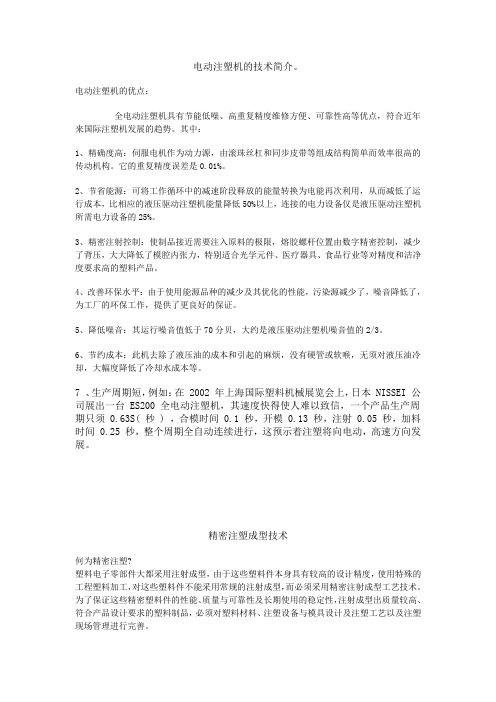
电动注塑机的技术简介。
电动注塑机的优点:全电动注塑机具有节能低噪、高重复精度维修方便、可靠性高等优点,符合近年来国际注塑机发展的趋势。
其中:1、精确度高:伺服电机作为动力源,由滚珠丝杠和同步皮带等组成结构简单而效率很高的传动机构。
它的重复精度误差是0.01%。
2、节省能源:可将工作循环中的减速阶段释放的能量转换为电能再次利用,从而减低了运行成本,比相应的液压驱动注塑机能量降低50%以上,连接的电力设备仅是液压驱动注塑机所需电力设备的25%。
3、精密注射控制:使制品接近需要注入原料的极限,熔胶螺杆位置由数字精密控制,减少了背压,大大降低了模腔内张力,特别适合光学元件、医疗器具、食品行业等对精度和洁净度要求高的塑料产品。
4、改善环保水平:由于使用能源品种的减少及其优化的性能,污染源减少了,噪音降低了,为工厂的环保工作,提供了更良好的保证。
5、降低噪音:其运行噪音值低于70分贝,大约是液压驱动注塑机噪音值的2/3。
6、节约成本:此机去除了液压油的成本和引起的麻烦,没有硬管或软喉,无须对液压油冷却,大幅度降低了冷却水成本等。
7 、生产周期短,例如:在 2002 年上海国际塑料机械展览会上,日本 NISSEI 公司展出一台 ES200 全电动注塑机,其速度快得使人难以致信,一个产品生产周期只须 0.63S( 秒 ) ,合模时间 0.1 秒,开模 0.13 秒,注射 0.05 秒,加料时间 0.25 秒,整个周期全自动连续进行,这预示着注塑将向电动,高速方向发展。
精密注塑成型技术何为精密注塑?塑料电子零部件大都采用注射成型,由于这些塑料件本身具有较高的设计精度,使用特殊的工程塑料加工,对这些塑料件不能采用常规的注射成型,而必须采用精密注射成型工艺技术。
为了保证这些精密塑料件的性能、质量与可靠性及长期使用的稳定性,注射成型出质量较高、符合产品设计要求的塑料制品,必须对塑料材料、注塑设备与模具设计及注塑工艺以及注塑现场管理进行完善。
多图详细说明全电动注塑机工作原理
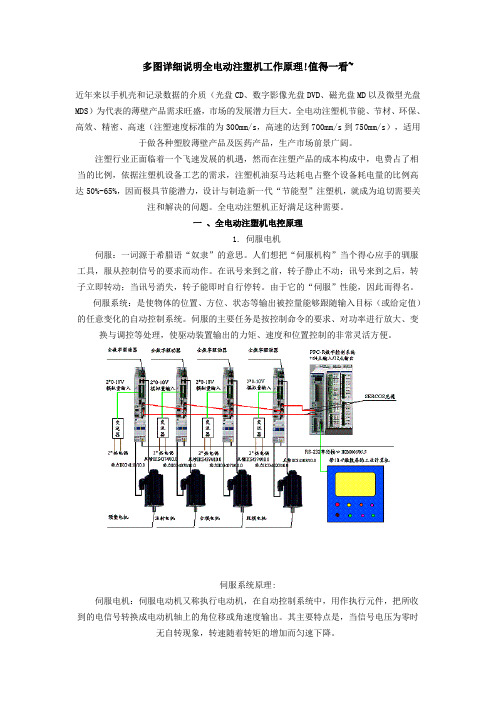
多图详细说明全电动注塑机工作原理!值得一看~近年来以手机壳和记录数据的介质(光盘CD、数字影像光盘DVD、磁光盘MD以及微型光盘MDS)为代表的薄壁产品需求旺盛,市场的发展潜力巨大。
全电动注塑机节能、节材、环保、高效、精密、高速(注塑速度标准的为300mm/s,高速的达到700mm/s到750mm/s),适用于做各种塑胶薄壁产品及医药产品,生产市场前景广阔。
注塑行业正面临着一个飞速发展的机遇,然而在注塑产品的成本构成中,电费占了相当的比例,依据注塑机设备工艺的需求,注塑机油泵马达耗电占整个设备耗电量的比例高达50%-65%,因而极具节能潜力,设计与制造新一代“节能型”注塑机,就成为迫切需要关注和解决的问题。
全电动注塑机正好满足这种需要。
一、全电动注塑机电控原理1. 伺服电机伺服:一词源于希腊语“奴隶”的意思。
人们想把“伺服机构”当个得心应手的驯服工具,服从控制信号的要求而动作。
在讯号来到之前,转子静止不动;讯号来到之后,转子立即转动;当讯号消失,转子能即时自行停转。
由于它的“伺服”性能,因此而得名。
伺服系统:是使物体的位置、方位、状态等输出被控量能够跟随输入目标(或给定值)的任意变化的自动控制系统。
伺服的主要任务是按控制命令的要求、对功率进行放大、变换与调控等处理,使驱动装置输出的力矩、速度和位置控制的非常灵活方便。
伺服系统原理:伺服电机:伺服电动机又称执行电动机,在自动控制系统中,用作执行元件,把所收到的电信号转换成电动机轴上的角位移或角速度输出。
其主要特点是,当信号电压为零时无自转现象,转速随着转矩的增加而匀速下降。
伺服电机的优点:大扭力、控制简单、装配灵活。
伺服电机的结构:一个伺服电机内部包括了一个直流电机;一组变速齿轮组;一个反馈可调电位器;及一块电子控制板。
其中,高速转动的电机提供了原始动力,带动变速(减速)齿轮组,使之产生高扭力的输出,齿轮组的变速比愈大,伺服电机的输出扭力也愈大,也就是说越能承受更大的重量,但转动的速度也愈低。
全电动注塑机的优缺点分析及技术发展趋势

课题文献综述题目:全电动注塑机的优缺点分析及技术发展趋势学生:指导老师:何亚东一前言我国是塑料制品的消费大国, 而且每年以7%-8%的速度快速增长。
在这期间期间, 油压一机械式注塑机扮演了重要角色, 但在能源日益匿乏、生态环境日益恶化的今天, 油压一机械式注塑机所消耗的能源, 越来越受到人们的重视和关注, 环保式“绿色”伺服电动注塑机的开发己经越来越紧迫和重要。
随着新型合成材料的涌现、高精度注塑件使用范围的扩大及节能环保意识的日益增强, 人们对注塑机的要求进一步提高。
在各种新型精密注塑机中, 最具代表性的为全电动式精密注塑机。
如电子零件、数码相机、手机外壳以及光学器件的精密性不仅对材料的要求很高, 而且对成型技术也提出了相当高的要求。
伺服电动注塑机在解决这类问题上具有得天独厚的优势, 有减轻环境负荷和高性能两大显著特点。
它不仅在节能(耗电量约为一般油压机的1/3)、低噪声、省水(耗水量约为一般油压机的1/12)及电源设备表现出极大的优势, 而且在性能方面具有高注射率、高应答、稳定的注射速度、稳定的背压系统、精确的定位控制、精确的压力闭环、高重复精度、周期短等优点。
因此, 作为“绿色”注塑机, 它的发展不仅符合社会生产力发展的趋势, 而且对发展民族塑机工业并参与国际竞争, 提升整个注塑机行业技术水平具有非常重要的意义。
2 全电动注塑机的技术特点2. 1全电动注射装置全电动注塑机根据注射(螺杆前进/后退)电机的不同分为两种基本结构: 一种是采用旋转电机, 可以很容易产生高速度和高的充模压力; 另一种采用直线电机, 可以实现超高速度注塑。
2. 1. 1 旋转电机驱动注射2. 1. 1. 1 电机通过丝杆传动机构驱动注射螺杆伺服电机驱动滚珠丝杆传动机构时, 可以是传动螺母转动, 丝杆作往复运动; 或者是丝杆转动, 传动螺母作往复运动。
该传动结构又可以分为皮带驱动方式和直接驱动方式:a. 皮带驱动方式是由伺服电机的轴带动皮带轮转动, 再用皮带连接螺杆, 当伺服电机转动时, 动力通过皮带传到螺杆上。
全电动注塑机机械结构及设备维护保养介绍

¡ 工作开始前检查 在注塑运行开始前必须要检查的项目。防止出现设备故障、 人身事故。
¡ 日常检查 在注塑运转的日常作业中应该检查的项目,主要以声音、 振动、温度、压力、速度为中心进行检查。
¡ 定期检查 1个月检查、3个月检查、6个月检查、1年检查 指定保养负责人,必须要实行定期检查
1.锁模装置的保养
日常检查
¡ 1.机器在工作情况下,确认伺服电机、同步带、滚珠丝杠 是否有异常声音现象,请停止设备检查
¡ 2.伺服电机是否有烧焦的味道,电机温度是否偏高,并确 保电机的通风效果是否良好
¡ 3.冷却水是否有漏水现象,请及时处理
1个月检查
¡ 电源电压是否在其它设备动作中电压波动,测定额在10V 左右以内
及具有基础电气知识的人进行。 ¡ 进行控制盘内、电机、加热器的检查时,必须要把主电源
关闭。 ¡ 在注塑机上安装有控制装置冷却空气吸入/排出口。该位
置如果被堵塞,控制装置就不能充分冷却,造成控制盘内 温度上升,从而影响设备的使用寿命。 ¡ 在控制装置冷却空气吸人口安装有防尘过滤网,防尘过滤 网如果长期使用,会发生堵塞现象。需要定期(每6个月)清 扫一次。如果过滤网眼堵塞会造成控制盘内温度上升,影 响设备的使用寿命。在清扫过滤网的同时要把粘附在冷却 风扇上的灰尘清扫于净。
一年检查
¡ 1.整机的水平度测量,并重新调整
¡ 2.整台设备的各部件的连接螺钉进行增紧
¡ 3.检查可接触可动部件的电缆线、润滑管是否有磨损、损伤 现象。
谢谢合作!
2006.06.02
¡ 关于运转结束后的清洗,慢慢降低螺杆的回料速度,禁止 不必要的空转。
¡ 原材料内混入金属异物会损坏螺杆和料筒,以及导致螺杆 头的折损事故。因此请尽量保持保管材料的环境清洁,特 别是在使用再生材料时尤其要务必注意。
全电动注塑机的特点及应用领域

全电动注塑机的特点及应用领域全电动注塑机的特点及应用领域摘要:随着伺服电机技术的日趋成熟和价格的大幅度下降,以及对环保和节能的需要,为全电动注塑机的发展注人了新的活力。
关键词:全电动;数控;注塑机注塑机械是重要的技术装备,主要对注塑机目前的发展现在及趋势、全电动注塑机与传统注塑机的特点分析、以及其在不同产品领域的实际应用案例进行介绍,对全电动注塑机在注塑装备行业的发展进行了展望。
一、全电动注塑机的特点全电动式注塑机作为节能环保、高速、高精密注塑机代表,其与传统的液压注塑机相比,全电动注塑机由于具有一些良好的性能和特点,越来越受到广大用户的重视。
全电动注塑机广泛使用交流伺服电动机,使用齿轮、滚珠丝杆以及齿形带等传动器件,与传统的注塑机比较,最大的特点就是抛弃了液压器件,改为全电动式驱动模块。
1.节能性能。
传统液压机械,完成部件的动作都是通过油压、油路来实现,因此,在油压控制时,油压损失、管路损耗、阀门阻塞、摩擦等流动性能耗损失不可避免。
特别是在高流量时,上述的能耗损失特别突出。
根据研究数据,对于液压式注塑机,由于采用高压节油方式,能量损耗为36%~68%之间;在设备待机的时候,上述损失继续存在。
由于伺服电机和伺服驱动在全电动注塑机上的使用,设备在运转时无液压系列损失,控制与磁滞损失也非常低;且在待机时不转动,可有效节能,与传统液压机相比可降低能耗达30%~50%。
2.清洁及噪音低。
全电动式注塑机没有油压缸,无漏油问题,车间干净,便于维护;另一方面,伺服电机产生的激活阻力小、加减速特性控制容易、噪音低、惯性低,,因此,全电动式注塑机比液压式塑机的噪音低10~15dB。
3.控制精度和可靠性高。
全电动伺服注射机对比与液压注射机,其在注射时,注射压力经过高精度的压力传感器采集,送至控制系统处理,由于压力传感器直接与螺杆相连,避免了中间环节,感应精度高、速度快。
全电动注塑机采用全闭环控制,重复定位精度较高,适合生产高精度产品。
注塑机原理详解
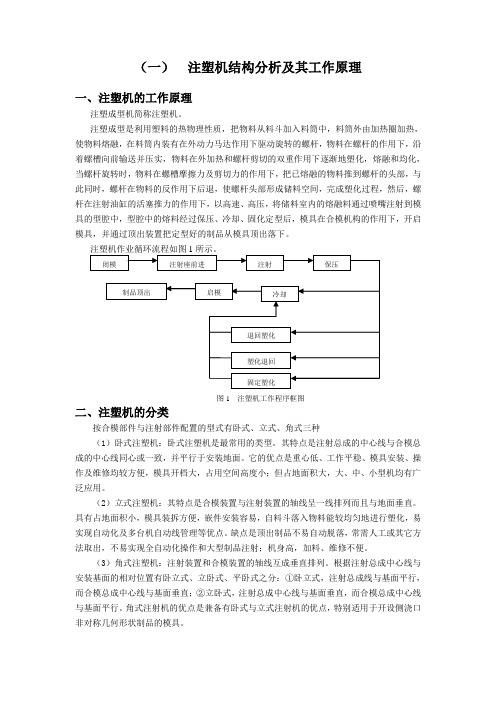
(一)注塑机结构分析及其工作原理一、注塑机的工作原理注塑成型机简称注塑机。
注塑成型是利用塑料的热物理性质,把物料从料斗加入料筒中,料筒外由加热圈加热,使物料熔融,在料筒内装有在外动力马达作用下驱动旋转的螺杆,物料在螺杆的作用下,沿着螺槽向前输送并压实,物料在外加热和螺杆剪切的双重作用下逐渐地塑化,熔融和均化,当螺杆旋转时,物料在螺槽摩擦力及剪切力的作用下,把已熔融的物料推到螺杆的头部,与此同时,螺杆在物料的反作用下后退,使螺杆头部形成储料空间,完成塑化过程,然后,螺杆在注射油缸的活塞推力的作用下,以高速、高压,将储料室内的熔融料通过喷嘴注射到模具的型腔中,型腔中的熔料经过保压、冷却、固化定型后,模具在合模机构的作用下,开启模具,并通过顶出装置把定型好的制品从模具顶出落下。
注塑机作业循环流程如图1所示。
图1 注塑机工作程序框图二、注塑机的分类按合模部件与注射部件配置的型式有卧式、立式、角式三种(1)卧式注塑机:卧式注塑机是最常用的类型。
其特点是注射总成的中心线与合模总成的中心线同心或一致,并平行于安装地面。
它的优点是重心低、工作平稳、模具安装、操作及维修均较方便,模具开档大,占用空间高度小;但占地面积大,大、中、小型机均有广泛应用。
(2)立式注塑机:其特点是合模装置与注射装置的轴线呈一线排列而且与地面垂直。
具有占地面积小,模具装拆方便,嵌件安装容易,自料斗落入物料能较均匀地进行塑化,易实现自动化及多台机自动线管理等优点。
缺点是顶出制品不易自动脱落,常需人工或其它方法取出,不易实现全自动化操作和大型制品注射;机身高,加料、维修不便。
(3)角式注塑机:注射装置和合模装置的轴线互成垂直排列。
根据注射总成中心线与安装基面的相对位置有卧立式、立卧式、平卧式之分:①卧立式,注射总成线与基面平行,而合模总成中心线与基面垂直;②立卧式,注射总成中心线与基面垂直,而合模总成中心线与基面平行。
角式注射机的优点是兼备有卧式与立式注射机的优点,特别适用于开设侧浇口非对称几何形状制品的模具。
- 1、下载文档前请自行甄别文档内容的完整性,平台不提供额外的编辑、内容补充、找答案等附加服务。
- 2、"仅部分预览"的文档,不可在线预览部分如存在完整性等问题,可反馈申请退款(可完整预览的文档不适用该条件!)。
- 3、如文档侵犯您的权益,请联系客服反馈,我们会尽快为您处理(人工客服工作时间:9:00-18:30)。
电动注塑机技术简介日期:2004年5月13日作者:人气:487 查看:[大字体中一、电动注塑机的优点:全电动注塑机具有节能低噪、高重复精度维修方便、可靠性高等优点,符合近年来国际注塑机发展的趋势。
其中:1、精确度高:伺服电机作为动力源,由滚珠丝杠和同步皮带等组成结构简单而效率很高的传动机构。
它的重复精度误差是0.01%。
2、节省能源:可将工作循环中的减速阶段释放的能量转换为电能再次利用,从而减低了运行成本,比相应的液压驱动注塑机能量降低50%以上,连接的电力设备仅是液压驱动注塑机所需电力设备的25%。
3、精密注射控制:使制品接近需要注入原料的极限,熔胶螺杆位置由数字精密控制,减少了背压,大大降低了模腔内张力,特别适合光学元件、医疗器具、食品行业等对精度和洁净度要求高的塑料产品。
4、改善环保水平:由于使用能源品种的减少及其优化的性能,污染源减少了,噪音降低了,为工厂的环保工作,提供了更良好的保证。
5、降低噪音:其运行噪音值低于70分贝,大约是液压驱动注塑机噪音值的2/3。
6、节约成本:此机去除了液压油的成本和引起的麻烦,没有硬管或软喉,无须对液压油冷却,大幅度降低了冷却水成本等。
7、生产周期短,例如:在2002年上海国际塑料机械展览会上,日本NISSEI公司展出一台ES200全电动注塑机,其速度快得使人难以致信,一个产品生产周期只须0.63S(秒),合模时间0.1秒,开模0.13秒,注射0.05秒,加料时间0.25秒,整个周期全自动连续进行,这预示着注塑将向电动,高速方向发展。
NETSTAL 全电动注塑机二、NETSTAL 全电动注塑机Development of technology for moulding new types of disc originates in the laboratories of the major materials suppliers and is eve- ntually directed by them to replicators, or to replicators via integrators and mak- ers of injection moulding machines. A set of machine control parameters for the pro- duction of a particular type of disc does not, how- ever, apply universally to all makes and types of ma- chine because there are design differences between models, for example in the location of thermal and pressure sensors and the response times of control systems. It is therefore necessary for machine manufacturers to augment thedevelopment work of materials suppliers to be able to provide users with advice specific to their products.Machine manufacturers also tend to become involved in specific projects which might result in profitable sales for them but not the consumption of large tonnages of material. Materials manufacturers may understandably be reluctant to participate heavily in such ventures, but theoverall picture is that the R&D efforts of materials and machinery manufacturers complement each other for the replicator抯 benefit.A replicator seeking novel technology for the production of 22 or 100 gigabyte pre-recorded, recordable or rewritable discs, for example, has therefore to seek it from a materials manufacturer or the integrator from whom he obtains his lines. However, the production of future advanced formats will not depend entirely upon the availability of materials with suitably refined properties butalso the development of appropriate moulding techniques. These will necessarily be more complex owing to the highly critical configurations of the discs concerned. It is also desirable that a reasonable processing window be available for replicators working in an indu- strial, as distinct from a laboratory, environme- nt. This is a further incentive for machine ma- nufacturers to undertake R&D in relation to advanced formats. They simply will not be able to sell their machines unless they can also supply the know how that replicators will need. It is not possible at the present time to describe in any detail what these new techniques might be, if only becausethe necessary development work is still going on and under wraps to a large extent, but a study of Michigan to assist R&D into DVD and recordable format production.Moulding trials conducted by Dow in cooperation with UK replicator Plasmon have proved that data densities of 15 to 18 GB per layer can be obtained using Dow PCHE (polycycloexylethylene) material. The discs were metallised, bonded and tested on blue laser players. Nanophotography of a disc with 15 GB density showed features 65 nm deep, 175 nm wide, 0.27 microns wide, 0.27 microns long and 0.4 microns track pitch.PCHE is stated to have an inherent moisture content of less than 0.01 per cent, conferring good dimensional stability. No drying is required before processing, says Dow. The special characteristics of PCHE material can be employed to identify legitimate disc production, the company adds. Suppliers of PMMA (acrylic) materials emphasise the claimed better light transmission and lower birefringence of this material compared with PC and its resultant suitability for advanced formats. Both companies claim that birefringence achieved with their acrylic materialsis less than 20 nm across the full radius of the disc compared with a range of from 50 to 100 nm in PC.A transmission rate of 92 per cent with a laser wavelength of 630 nm is claimed both by Atoglas for its Oroglas VOD-100 material and Roehm for its Plexiglas DQ501 and ompared with 89 per cent for DVD grade PC. Better light transmission is not only advantageous in respect of disc performance, particularly with blue lasers, but also UV curing.Roehm ran two Netstal Discjets on its stand at Replitech Europe 2001 to demonstrate DVD5 moulding in Plexiglas DQ501 material. Rudolf Blass, marketing director, said: "PMMA discs have a harder surface than PC and this is important for the video rental sector as they do not scratch so easily. We have installed ultra clean material production lines and are easily able to supply the DVD market."We claim a 15 per cent price advantage for PMMA over PC anywhere in the world. Pre drying is unnecessary in most territories except humid Asian countries." Atoglass has also established a Singulus Spaceline laboratory line equipped with two Netstal Discjet machines and Axxiconmoulds in a Class 10000 clean room. Raphael Cherbonneau, Atoglas applications engineer, claimed: "VOD-100 is easy to process and offers potential to reduce cycle times."三、KM 电动注塑机The changes in moulding technology brought about by the introduction of the DVD following the CD gives some indication of the problems that the new formats may present.When production of the thinner substrates for DVD began, typical interactions and sensitivities involved in making CDs were found not to apply. A number of fresh factors became critical. As well as the introduction of injection compression moulding, these included the use of higher melt and mould temperatures and dependency upon the accuracy and repeatability of clamping pressure andtiming.The number of processing factors that affect the physical properties of a DVD were found to be greater than for CD and the interactions between them more critical. If any one factor changed, others altered in a greater magnitude than occured in CD moulding.GE Plastics Corporate R&D Optical Media Development Center in Massachusetts, USA, used a rigorous methodology to understand the interactions that influence DVD production. The chief lesson learned was that all attributes had a high dependence upon initial clamp tonnage and timing. The next step was to identify the critical interactions of the clamping and filling sequences and determine whether any other parameters could be eliminated or their effects minimised.It was found from this that initial clamp tonnage, injection timing and the clamp tonnage profile all had considerable effects upon product quality, and a further experiment to define the interaction of clamping with other variables was undertaken. This revealed that control of clamp timing, clamp tonnage and the profile at whichclamping pressure was applied during mould fill were highly critical.Close control of the clamping profile was found to be the key to DVD moulding. Almost all other variables are highly sensitive to small changes in the clamping profile. For example, a change of only 0.05 second in clamp delay time had a significant effect upon peak injection pressure. Accurate control of the clamping speed profile was defined as essential to minimise cycle times while maintaining product quality. Six significant factors were chosen for further investigation - melt temperature, mould temperature, cooling time, first stage clamp tonnage, first stage clamp duration and second stage clamp tonnage. Results showed that pit replication and HF signals improved as melt temperature, mould temperature and first and second stage clamp tonnages were increased. However, raising these tended to worsen tangential and radial tilt. GE Plastics researchers concluded that factors that make for good optical properties and electrical performance are ‘at war’ with making go od flat discs that bond easily and the replicator must walk a tightropebetween the two. The company also established that less variation in birefringence occurs when material viscosity is controlled within close limits during production. The ability to mould flat discs is affected by viscosity variations. Better control of viscosity reduces variations in radial and tangential tilt. GE Plastic’s patented material production process enables the viscosity of the melt to be controlled within a melt flow range of 0.6, compared with a range of 1.4 typical of a process without this control. The technology constantly monitors and adjusts the viscosity of the Lexan material during the stage of its manufacture when it is converted from powder into pellet form. Response to the smallest fluctuation in molecular weight is immediate so that viscosity variations is greatly reduced.Bayer, maker of Makrolon PC material, states that new advanced disc formats always set fresh requirements. Material specifications become more demanding because of the increasing data storage density. Material has to fulfil different standards but still offer a balanced product profile. The company’s criteria for substrate materials are set out in Table 1. Improving an existingmaterial or developing a new one means taking all these into consideration.TABLE 1 (SOURCE: BAYER)STANDARDS TO BE MET BY SUBSTRATE MATERIALOptical propertiesTransparencyBirefringencePurityMechanical propertiesDimensional stabilityStiffness/toughnessHeat resistanceProcessing factorsFlow characteristicsThermal stabilityPit and groove replicationRelease propertiesMetal adhesionWater uptakeCycle timeEconomical factorsPriceProcessabilityRecyclingSurface quality considerably determines disc quality and, in particular, replication is of great importance for a DVD-RAM structure which has information written and read on pits and wobbled grooves. Bayer initiated a replication program using special stampers with prismatic nanostructures even more finely configured than those for DVD. The replication of these was examined for different materials under various moulding conditions.These tests showed that replication quality between different materials varied even when viscosity was constant and confirmed the importance of polymer composition. Indents comparable to the size of actual pits were made with an atomic force microscope, and the microhardness of the surface area of a disc was determined by analysing the geometries of a set of indents in relation to the force needed for their indentation. Materials can produce disc surface hardnesses which are different from their hardnesses in bulk form, that is before processing, and material development has to take this into account. The influence of material composition upon surfacehardness must be distinguished from that of processing factors, Bayer emphasises. The more information that a disc carries, the smaller the tilt limit becomes and a disc has to be extremely flat and remain so under environmental changes. If the climate changes from dry to wet, the substrate material at the surface of the disc absorbs water and swells, causing tilt. After a time, the water concentration becomes more evenly distributed throughout the substrate and the disc relaxes, but the extent of water uptake and its kinetic function are determined by the polymer structure.Optical properties are the key factors for future formats, Bayer states. The company employs a special optical test bed which can operate with different lasers including infra red, red, green and blue. In addition, the optical pick up is capable of being set to different numerical apertures and disc thicknesses over a wide range. This makes advanced testing of new formats possible. Copolycarbonates - polycarbonates with a modified chemical structure and having tailor made properties in respect of water absorption and rheological and optical characteristics - are believed by Bayer to bethe key to further development. Increase in storage density also means that particular attention will have to be paid to dimensional stability.The micro hardness of the surface of a moulded disc can differ from that of the bulk raw PC material because of variations in the stability of the polymer during processing. Taking a cross section through the thickness of a disc, birefringence is higher on the outer surfaces than in the middle. This is because the material at the surfaces is subject to greater shear (as it flows over the surfaces of the mould and the stamper) and the anisotropy and orientation of the polymer molecules - which determines birefringence - is different from that occurring in the centre. However, the degree of anisotropy can be reduced by modifying the chemical structure of the PC material, described technically as adding a further aromatic ring linked to the polymerbackbone.Much of the work undertaken in the Bayer laboratory at Leverkusen, Germany, concerns the interdependence between process parameters. Suitable settings for generalparameters such as melt and mould temperatures, clamping force and cooling time normally result in discs that pass quality control for electrical signals, but slight changes to parameters that seem less important, such as screw suckback, nozzle temperature and punch delay, can produce major faults during the injection moulding stage. These parameters have to be fine tuned for every machine/mould set up as they depend greatly upon specific conditions.Teijin-Kasei claims that its Panlite AD-5503 PC material has capacity for 10 to 27 GB per side. The company is developing materials for the next generation of high density media. Teijin-Bayer Polytec, a joint venture between Teijin Chemicals and Bayer Japan, has introduced ST-3000 PC material which is claimed to reduce birefringence by 50 per cent and water absorption by 25 per cent compared with conventional materials. This grade is also being directed towards new high density discs. Dow Plastics has installed a CD Associates DVD 1000P with Pulsetec drive DVD tester and a Dr Schenk Prometeus MT-136E instrument at its Optical Media Development Laboratory in。