武钢炼铁厂5号高炉实习报告[1]
炼钢实习报告5篇
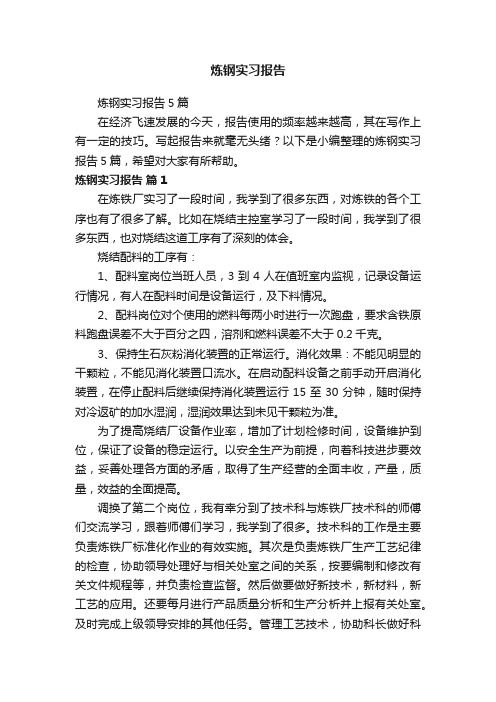
炼钢实习报告炼钢实习报告5篇在经济飞速发展的今天,报告使用的频率越来越高,其在写作上有一定的技巧。
写起报告来就毫无头绪?以下是小编整理的炼钢实习报告5篇,希望对大家有所帮助。
炼钢实习报告篇1在炼铁厂实习了一段时间,我学到了很多东西,对炼铁的各个工序也有了很多了解。
比如在烧结主控室学习了一段时间,我学到了很多东西,也对烧结这道工序有了深刻的体会。
烧结配料的工序有:1、配料室岗位当班人员,3到4人在值班室内监视,记录设备运行情况,有人在配料时间是设备运行,及下料情况。
2、配料岗位对个使用的燃料每两小时进行一次跑盘,要求含铁原料跑盘误差不大于百分之四,溶剂和燃料误差不大于0.2千克。
3、保持生石灰粉消化装置的正常运行。
消化效果:不能见明显的干颗粒,不能见消化装置口流水。
在启动配料设备之前手动开启消化装置,在停止配料后继续保持消化装置运行15至30分钟,随时保持对冷返矿的加水湿润,湿润效果达到未见干颗粒为准。
为了提高烧结厂设备作业率,增加了计划检修时间,设备维护到位,保证了设备的稳定运行。
以安全生产为前提,向着科技进步要效益,妥善处理各方面的矛盾,取得了生产经营的全面丰收,产量,质量,效益的全面提高。
调换了第二个岗位,我有幸分到了技术科与炼铁厂技术科的师傅们交流学习,跟着师傅们学习,我学到了很多。
技术科的工作是主要负责炼铁厂标准化作业的有效实施。
其次是负责炼铁厂生产工艺纪律的检查,协助领导处理好与相关处室之间的关系,按要编制和修改有关文件规程等,并负责检查监督。
然后做要做好新技术,新材料,新工艺的应用。
还要每月进行产品质量分析和生产分析并上报有关处室。
及时完成上级领导安排的其他任务。
管理工艺技术,协助科长做好科技创新质量改进工作,负责炼铁厂的工艺技术管理,确保质量指标的完成。
负责炼铁厂生产工艺纪律检查查处的问题及时反馈处理。
还要负责生产车间用料结构的制定和月度用料计划的制定。
负责进厂原燃料成分统计汇总分析,检查督促练铁厂标准化作业的实施,负责组织练铁厂新技术,新材料,新工艺的实验工作及时出具实验报告,及时完成上级领导安排的任务,领导,设备科全体成员干好本职工作,协调设备科与上级职能部门和下层单位的关系,编制全厂设备的大中修计划,监督计划的实施。
炼铁厂工作的社会实践报告

炼铁厂工作的社会实践报告炼铁是将铁矿石炼制成铁水的过程,它是钢铁工业中最重要的环节之一、炼铁厂是一个庞大而复杂的工业园区,由许多设备和工艺组成,这次我的社会实践就是在一家炼铁厂进行的。
在这段时间的社会实践中,我主要参观了和了解了炼铁厂的生产过程和工作环境。
首先,炼铁过程的核心是高炉炼铁,这是通过高炉将铁矿石、焦炭和石灰石等原料加热、还原和冶炼的过程。
在高炉旁边,我看到了巨大的铜牌,上面记录了各种数据,如炉温、气体流量等,这些数据对于生产和控制炼铁过程非常重要。
在高炉的周围,还有许多设备和工人,他们负责控制、维护和监测高炉的运行情况。
参观炼铁厂的过程中,我发现工人们的工作非常辛苦和复杂。
高炉炼铁是一个持续进行的过程,工人们需要时刻关注各种指标和数据,进行调整和控制。
他们需要服从严格的工作安排,经常需要在高温环境下工作,这对于他们的身体和心理都是一种挑战。
另外,工人们还需要遵守严格的安全规定,因为炼铁厂存在一定的危险性,只有保持警惕和遵循规定,才能保障自己和他人的安全。
此外,我还了解到炼铁厂对环保的重视。
炼铁过程会产生大量的尘埃、气体和废水,这些都对环境和健康造成一定的影响。
为了减少对环境的污染,炼铁厂采取了一系列的措施,如安装废气处理设备、净化废水等。
在参观炼铁厂的过程中,我看到了大型的废气处理设备和水处理设备,这些设备不仅能够减少对环境的影响,也为工人们提供了更好的工作环境。
通过这次社会实践,我深入了解了炼铁厂的生产过程和工人们的辛勤付出。
炼铁过程不仅需要高度的技术和专业知识,也需要工人们的毅力和勤奋。
同时,我也意识到环境保护在炼铁过程中的重要性。
我相信,在不断的科技进步和社会意识的提高下,炼铁厂将会更加高效、环保和安全地发展。
武钢炼铁厂实习报告
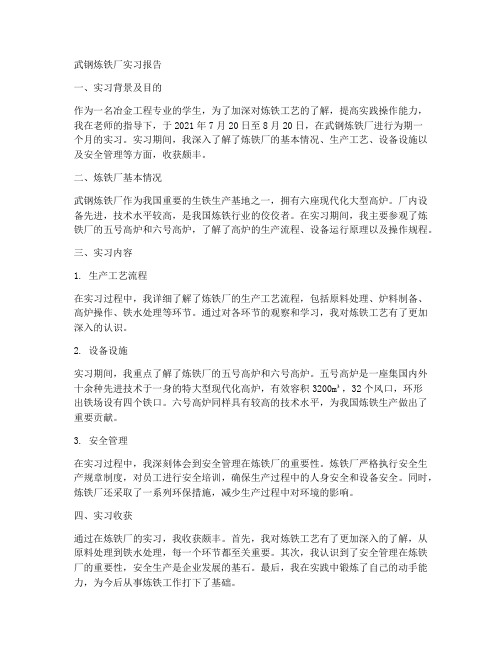
武钢炼铁厂实习报告一、实习背景及目的作为一名冶金工程专业的学生,为了加深对炼铁工艺的了解,提高实践操作能力,我在老师的指导下,于2021年7月20日至8月20日,在武钢炼铁厂进行为期一个月的实习。
实习期间,我深入了解了炼铁厂的基本情况、生产工艺、设备设施以及安全管理等方面,收获颇丰。
二、炼铁厂基本情况武钢炼铁厂作为我国重要的生铁生产基地之一,拥有六座现代化大型高炉。
厂内设备先进,技术水平较高,是我国炼铁行业的佼佼者。
在实习期间,我主要参观了炼铁厂的五号高炉和六号高炉,了解了高炉的生产流程、设备运行原理以及操作规程。
三、实习内容1. 生产工艺流程在实习过程中,我详细了解了炼铁厂的生产工艺流程,包括原料处理、炉料制备、高炉操作、铁水处理等环节。
通过对各环节的观察和学习,我对炼铁工艺有了更加深入的认识。
2. 设备设施实习期间,我重点了解了炼铁厂的五号高炉和六号高炉。
五号高炉是一座集国内外十余种先进技术于一身的特大型现代化高炉,有效容积3200m³,32个风口,环形出铁场设有四个铁口。
六号高炉同样具有较高的技术水平,为我国炼铁生产做出了重要贡献。
3. 安全管理在实习过程中,我深刻体会到安全管理在炼铁厂的重要性。
炼铁厂严格执行安全生产规章制度,对员工进行安全培训,确保生产过程中的人身安全和设备安全。
同时,炼铁厂还采取了一系列环保措施,减少生产过程中对环境的影响。
四、实习收获通过在炼铁厂的实习,我收获颇丰。
首先,我对炼铁工艺有了更加深入的了解,从原料处理到铁水处理,每一个环节都至关重要。
其次,我认识到了安全管理在炼铁厂的重要性,安全生产是企业发展的基石。
最后,我在实践中锻炼了自己的动手能力,为今后从事炼铁工作打下了基础。
五、实习总结回顾在炼铁厂的一个月实习,我深感实践是检验真理的唯一标准。
通过实习,我将理论知识与实际操作相结合,提高了自己的实践能力。
同时,我也认识到了自己的不足,需要在今后的学习中更加努力,为我国炼铁事业贡献自己的力量。
炼钢炼铁实习报告

一、实习背景随着我国经济的快速发展,钢铁产业作为国家的基础产业,其重要性日益凸显。
为了深入了解炼钢炼铁的生产过程,提高自己的专业技能,我于20xx年xx月xx日至20xx年xx月xx日在我国某知名钢铁企业进行了为期一个月的实习。
实习期间,我参观了炼铁、炼钢等生产车间,了解了钢铁生产的基本流程,掌握了相关设备的使用方法,并对炼钢炼铁的工艺原理有了更深入的认识。
二、实习内容1. 炼铁车间实习(1)参观高炉:在高炉车间,我了解了高炉的结构、工作原理以及原料的配比。
高炉是炼铁生产的核心设备,其主要原料包括铁矿石、焦炭、石灰石等。
在高炉内,焦炭燃烧产生的热量将铁矿石还原成铁水。
(2)参观烧结机:烧结机是将铁矿石、焦炭等原料进行烧结的设备。
在烧结过程中,原料被加热至一定温度,使其充分氧化,形成烧结矿。
(3)参观焦炉:焦炉是炼焦车间的核心设备,其主要作用是将煤炭转化为焦炭。
在焦炉内,煤炭在高温下发生化学反应,形成焦炭。
2. 炼钢车间实习(1)参观转炉:转炉是炼钢车间的核心设备,其主要作用是将生铁转化为钢水。
在转炉内,氧气吹入生铁中,使铁水中的杂质氧化,形成钢水。
(2)参观连铸机:连铸机是将钢水连续铸造成钢材的设备。
在连铸过程中,钢水从转炉中流出,经过冷却、凝固、切割等工序,形成各种规格的钢材。
(3)参观轧钢机:轧钢机是将钢坯轧制成各种规格钢材的设备。
在轧钢过程中,钢坯经过加热、轧制、冷却等工序,最终形成所需规格的钢材。
三、实习收获1. 提高了专业技能:通过实习,我对炼钢炼铁的生产过程有了更深入的了解,掌握了相关设备的使用方法,为今后从事相关工作打下了坚实的基础。
2. 增强了团队协作能力:在实习过程中,我与同事们共同完成了各项工作任务,培养了良好的团队协作精神。
3. 了解了企业文化和规章制度:实习期间,我了解了企业的文化理念、规章制度以及安全生产的重要性,为今后更好地融入企业打下了基础。
4. 培养了创新意识:在实习过程中,我积极参与技术创新和改进工作,为企业发展贡献了自己的力量。
武钢炼钢厂实习报告
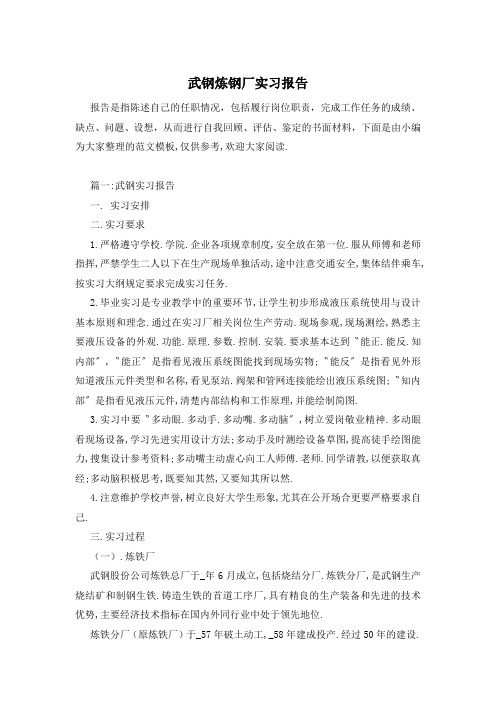
武钢炼钢厂实习报告报告是指陈述自己的任职情况,包括履行岗位职责,完成工作任务的成绩、缺点、问题、设想,从而进行自我回顾、评估、鉴定的书面材料,下面是由小编为大家整理的范文模板,仅供参考,欢迎大家阅读.篇一:武钢实习报告一. 实习安排二.实习要求1.严格遵守学校.学院.企业各项规章制度,安全放在第一位.服从师傅和老师指挥,严禁学生二人以下在生产现场单独活动,途中注意交通安全,集体结伴乘车,按实习大纲规定要求完成实习任务.2.毕业实习是专业教学中的重要环节,让学生初步形成液压系统使用与设计基本原则和理念.通过在实习厂相关岗位生产劳动.现场参观,现场测绘,熟悉主要液压设备的外观.功能.原理.参数.控制.安装.要求基本达到〝能正.能反.知内部〞,〝能正〞是指看见液压系统图能找到现场实物;〝能反〞是指看见外形知道液压元件类型和名称,看见泵站.阀架和管网连接能绘出液压系统图;〝知内部〞是指看见液压元件,清楚内部结构和工作原理,并能绘制简图.3.实习中要〝多动眼.多动手.多动嘴.多动脑〞,树立爱岗敬业精神.多动眼看现场设备,学习先进实用设计方法;多动手及时测绘设备草图,提高徒手绘图能力,搜集设计参考资料;多动嘴主动虚心向工人师傅.老师.同学请教,以便获取真经;多动脑积极思考,既要知其然,又要知其所以然.4.注意维护学校声誉,树立良好大学生形象,尤其在公开场合更要严格要求自己.三.实习过程(一).炼铁厂武钢股份公司炼铁总厂于_年6月成立,包括烧结分厂.炼铁分厂,是武钢生产烧结矿和制钢生铁.铸造生铁的首道工序厂,具有精良的生产装备和先进的技术优势,主要经济技术指标在国内外同行业中处于领先地位.炼铁分厂(原炼铁厂)于_57年破土动工,_58年建成投产.经过50年的建设.改造和发展,已拥有8座现代化大型高炉,其中3_ m3的有3座, 38_m3的有1座(暂未投产),年生产能力超过__万吨,是我国生铁的主要生产基地之一. 炼铁分厂坚持走引进.消化与自主开发之路,无料钟炉顶.软水密闭循环.环保型INBA炉渣处理系统.薄炉衬铜冷却壁.高炉专家系统等一大批当代先进的炼铁工艺广泛应用于高炉生产之中,高炉利用系数进入国际一流.国内领先水平.武钢炼铁厂5号高炉是武钢自行投资建成的一座集国内外十余种先进技术于一身的特大型现代化高炉,于_91年_ 月_日点火投产.高炉有效容积3_ m3,共有32个风口,皮带上料,环形出铁场,设有4个出铁口,对称的两个铁口出铁,另两个检修备用,日产生铁7_0t以上.引进卢森堡PW公司的第四代水冷传动齿轮箱并罐式无钟炉顶设备,设计顶压可达.该高炉配备有4座矩形陶瓷燃烧器内燃式热风炉,可稳定地提供_50℃的热风.武钢炼铁主要原料包括烧结矿.球团矿.块矿(海南矿.南非矿以及澳矿等).熔剂(以石灰石和白云石为主).焦炭.煤粉和热风等,这些都有相应的车间进行准备.高炉的入炉熟料率达80%_85%,外加少量品位较高的块矿和球团矿,炉料碱度为1.8.高炉炉顶采用并罐式无钟炉顶设备,可以使炉顶压力相应提高,有利于高压操作.并罐式无钟炉顶由受料漏斗.称量料罐.中心喉管.气密箱.旋转溜槽等五部分组成.十五年来,武钢5号高炉在高效长寿生产实践中取得了一定成绩.今后,要实现一代炉龄_余年和单位炉容产铁量_ _0 t/m3 以上的目标,还面临着许多困难,必须从生产操作.设备运行和生产管理等方面着手解决,如 (1)进一步改善原燃料质量; (2) 降低生铁含硅;(3)加强设备管理,进一步提高炉顶压力; (4)努力提高煤气利用率,降低消耗;(5)加快喷煤系统的改造,为进一步提高煤比创造条件; (6)不断提高富氧率和风温水平.(二).二炼钢厂武钢二炼钢厂是一个转炉全连铸炼钢厂,要求1_%的钢水经过炉外精炼后再进行连铸浇钢,以保证浇铸顺利和铸坯质量.与顶吹氩相比,底吹氩具有可以使钢水温度和成份更加均匀,中包温度更加均匀,更有利于夹杂物的富聚和上浮的优点,吹氩时间可缩短1min左右,同时去氧去氢的效果明显优于顶吹氩.由于不用顶吹氩棒,可节约大量的耐火材料,从而减少了耐材熔损对钢水的污染._年8月后,钢厂彻底拆除了用于挽救事故钢水的顶吹氩棒装置,实现1_%钢水底吹氩.由于对单透气砖堵塞各种原因认识仍存在不足,致使连续3个月底吹失败炉数达8-_炉,给生产组织和安全顺行带来困难.为此我们迅速组成提高钢包底吹氩成功率攻关组,经过生产和技术人员的联合攻关,底吹吹成率达到99.95%以上的历史最好水平,为钢厂品种钢生产和质量保证及降成本工作创造了有利条件.主要品种第二炼钢厂是武汉钢铁股份有限公司的高难品种钢生产基地,常年生产_个系列4_多个品种钢.包括超低碳钢.低碳钢.中碳钢.高碳钢.硅钢等钢种,双高品种钢产量占总产量的87%以上.经过多年的技术.管理攻关,武钢第二炼钢厂80t钢包单块透气砖在拆除顶吹装置的条件下,底吹率达到了99.95%以上的水平,满足了生产和品种质量控制的要求,取得了良好的效益.(1)选用狭缝型透气砖,氩气压力调节范围大,供气性能较稳定,吹开率高,底吹氩畅通率高,使用安全可靠,钢包透气砖实现漏钢事故为零.(2)通过攻关使钢包单透气砖底吹氩吹成率稳定在99.95%以上,能够满足第二炼钢厂冶炼多品种钢对吹氩的质量要求.(3)通过采取一些底吹氩畅通技术措施,每月底吹失败炉数由8~_炉下降到1~2炉,消除了因底吹氩失败引起钢水成份和温度不合格而造成回炉和铸机中断现象.(三).热轧厂武钢热轧厂8月份轧制量达4.7万吨,创历史同期最好水平;热装热送量达_.5万吨.热装率为48%,均为历史新高;同时主轧线日历作业率.有效作业率.工序能耗.商品材合格率.产品成材率.精轧四项精度命中率等主要经济技术指标均保持国内领先水平.该厂马不停蹄正全力向新目标冲刺,主轧线.平整线.纵切线等生产线均满负荷生产.在激烈的市场竞争中,武钢热轧厂工作定位在高标准高起点上,自我加压,力求发挥〝主体〞最大效益,瞄准世界先进钢铁企业的先进水平攀高,突出管理创新,挖掘内部潜力,促进了质量.生产.设备.成本等管理水平不断提高,不仅适应了市场竞争风高浪急的要求,而且增强了企业发展后劲.针对设备集中管理,热轧厂党委工作主动,从7月份开始就深入一线向职工征求意见,在不同层次的专题会议上重申公司〝二个不变〞,并在此基础上结合热轧厂的实情明确〝感情不变.责任不变.信心不变.目标不变.贡献不变〞的〝五个不变思路,要求职工顾大局识大体,以良好的状态适应改革,并做好一人一事的思想工作,是交接工作平稳.又序.纵深推进.进入8月份以来,反映热轧厂主轧线设备〝绩效〞的日历作业率和有效作业率一直稳定在一流水平.石油套管用钢.集装箱用钢.硅钢.船板等专用钢生产捷报频传,3号加热炉一次集中硅钢投放量达54_吨,创该炉历史最好水平,_70的高温度管线用钢已开始大批量生产.与此同时,热轧普材也大量出口古巴.热装热送量不断定高,创下历史新高.武钢热轧带钢主要生产工艺流程武钢热扎带厂主要设备有步进式加热炉4座,__毫米(3/4)连续式热轧机1套,包括大立辊轧机1架,粗轧机4架,精轧机7架,切头飞剪1台,层流冷却装置1套,地下卷取机3台,热轧钢卷精整加工线5条(即一.二.三号横切线,热平整线,纵切线).武钢热轧带的主要生产工艺流程为原料板坯经加热.除鳞.粗轧.精轧.剪切.冷却卷取.入库.精整(板坯→加热炉→粗轧区→精轧区→卷取区→精整区).具体流程为:将合格板坯由吊车运至辊道,由推钢机推入加热炉内加热.板坯在加热炉内被加热到约_50-_50℃,用取料机将加热好的板坯从加热炉内托出放到出炉辊道上.当板坯经过立辊和第一架轧机时,板坯的四面都受到轻微的挤压,氧化铁皮开始炸裂,然后经高压水装置清除钢坯表面的氧化铁皮,除鳞后的板坯,送入第二架粗轧机进行轧制.第二架粗轧机为可逆轧机可进行多次扎制,一般情况进行五或七次扎制即可.经过第二架粗轧机多次轧制后,轧件再进入三.四轧机进行扎制.从粗轧区域出来后轧件进入精轧机组进行轧制.精轧机组是热轧生产的核心部分,轧件在精轧机组中轧制七个道次后得到成品厚度.精轧机组间设有电动活套装置,使带材进行恒定的微张力轧制,保证带钢的轧制精度.带钢的精轧温度一般应控制在850—950°C之间.精轧后的带钢经过切头切尾等工序后经夹送辊送入卷取机卷成钢卷.在精轧后输出辊道上设有层流冷却装置,分别对带刚上下表面进行冷却,根据带刚的品种.尺寸.速度.和终轧温度调节层流冷却装置喷咀的组数和水量,将带刚的卷取温度控制在550_650°C之间.层流冷却主要是控制钢板的卷取温度,也就是淬火质量.钢卷从卷取机卸下来后经过钢卷称称重后打印出生产报表和质量报表并入库,入库的钢卷再经精整作业线剪切.矫直.平整包装成品.整个过程由1台过程控制计算机和3台直接数字控制计算机组成分级系统.其设备特点是:轧制线全部采用大型计算机控制;自动化系统的设计与制造的内容为从步进式加热炉加热燃烧全部采用温度自动控制开始至带卷收集装置为止的全套控制设备以及与这些设备相关的自动测厚.测宽.测温.测压.高压水除鳞设施.层流冷却.压缩空气等控制设备及仪表等.包括加热炉区.粗轧区.精轧区和卷取区在内的整个车间的全套电控系统设计.设备设计和设备制造(含生产联系信号),以及与轧制工艺和控制相关的过程控制应用软件.基础自动化应用软件和人机界面,配有工业电视.彩色显示装置和跟踪轧制盘等.四.实习总结通过两周的毕业实习,我了解了自己今后就业所涉及到的一些很重要的行业和流程,也为自己将来的就业指明了方向,更是进入社会努力学好专业知识奠定了心理基础和信心.其次,我对武钢的人员状况有了概括的了解.武钢钢铁集团有限责任公司始终坚持全心全意依靠职工办企业的方针和〝以人为本〞的员工管理思想,并将其贯穿于生产经营和模拟市场核算机制的全过程,培养和造就一支高素质的员工队伍是公司员工管理的最终目标.近些年来,武钢十分重视技术创新和管理创新以及人才的引进.培养和使用,并注重人力资源的开发和合理配置.在公司内部建立了人才市场和劳动力市场,内部人员流动均通过市场的形式实现,为各类人才提供了学习提高的机会和施展才华的广阔舞台.截止_年底,武钢本部从事生产经营管理.工程技术.后勤服务和现场操作的员工共9万多人.其中操作人员占75%,服务人员占_%,工程技术人员占5%,管理人员占9%.在技术管理人员中2%为研究生,40%为大学生,24%为大专生,_%为中专生,高中以下_%左右.从这些数字我们可以看出武钢的人员配置是比较合理的,而且文化程度也是比较高的.对于一个国有的大型工业企业,基本符合生产的需要,有能力生产出世界一流的钢材.篇二:武钢参观实习报告目录1. 实习概况 (1)1.1实习时间 (1)1.2实习地点 (1)2.实习地点简介 (1)2.1武汉钢铁集团简介 (1)3. 实习内容及过程 (3)3.1参观炼铁厂......................................... 错误!未定义书签.3.2参观炼钢厂......................................... 错误!未定义书签.3.3热轧厂............................................. 错误!未定义书签.3.4参观冷轧钢厂....................................... 错误!未定义书签.3.5武钢博物馆......................................... 错误!未定义书签.3.6武钢高新技术产业园................................. 错误!未定义书签.3.7通信分公司......................................... 错误!未定义书签.4.参观体会................................................ 错误!未定义书签.1.实习概况1.1 实习时间:_年7月_日至_年8月9日1.2 实习地点:武汉钢铁公司2.实习地点简介2.1武汉钢铁集团简介武汉钢铁公司,以下简称武钢.武钢是新中国成立后兴建的第一个特大型钢铁联合企业,于_55年开始建设,_58年9月_日建成投产,是中央和国务院国资委直管的国有重要骨干企业.本部厂区座落在湖北省武汉市东郊.长江南岸,占地面积_._平方公里.武钢拥有从矿山采掘.炼焦.炼铁.炼钢.轧钢及配套公辅设施等一整套先进的钢铁生产工艺设备,是我国重要的优质板材生产基地,为我国国民经济和现代化建设作出了重要贡献.武钢联合重组鄂钢.柳钢.昆钢后,已成为生产规模近4_0万吨的大型企业集团,居世界钢铁行业第四位,_年,武钢跻身世界5_ 强行列.武钢现有三大主业,即钢铁制造业.高新技术产业和国际贸易.钢铁产品主要有热轧卷板.热轧型钢.热轧重轨.中厚板.冷轧卷板.镀锌板.镀锡板.冷轧取向和无取向硅钢片.彩涂钢板.高速线材等几百个品种.其中,冷轧硅钢片和船板钢获〝中国名牌产品〞称号,汽车板.桥梁用钢.管线钢.压力容器钢.集装箱用钢.帘线钢.耐火耐候钢.电工系列用钢等优质名牌产品在国内外市场享有广泛的声誉,〝武钢牌〞被评为全国驰名商标.近年来,武钢先后获得国家技术创新奖.全国质量管理奖.全国质量效益型先进企业.全国用户满意先进单位.全国企业管理杰出贡献奖.全国文明单位以及中央企业十大典型之一等荣誉称号.武钢在青山地区的厂区布局:整个厂区占地面积为_._平方公里,按工艺流程可划分为三大片,分别是冶炼片.炼钢片和轧钢片.武钢拥有长江边上最大的企业专业港口——工业港.工业港是武钢原燃料.钢坯材进出港口和大型原料场,共有_座码头,已形成较完整的水运物流供应链.运入厂区的煤炭和铁矿石等原材料,先分别在焦化公司和烧结分厂进行加工,加工成冶金焦炭和烧结矿.球团矿.焦化公司是我国中南地区最大的煤化工生产基地,也是武钢非钢产业的支柱,拥有_座大型焦炉,完备的备煤.炼焦.煤气净化和化工产品回收.精制四大生产系统,并采用国际上最先进的干法熄焦,装备技术水平达到国内同行前列.烧结分厂拥有5个车间,年生产能力_24万吨.处理好的原料将送往炼铁总厂进行冶炼.武钢炼铁总厂的主要经济技术指标居国内同行业前茅,拥有八座现代化大型高炉,年生产能力超过__万吨,是我国生铁的主要生产基地之一,高炉利用系数进入国际一流.国内领先水平.铁水将被运往炼钢片.条材总厂下辖一炼钢分厂.大型分厂和棒材分厂,拥有从国外引进的现代化生产线.主要生产低.中.高碳钢.低合金钢等_0多个钢种,主要产品有钢帘线.钢绞线.弹簧钢.焊丝钢.齿轮钢.高速重轨.圆钢棒材等.CSP分厂:武钢转炉-薄板坯连铸连轧生产线(CSP)是国际上技术最先进,集炼钢.连铸.轧钢三位一体的全新生产线,脱硫.转炉.LF炉炼钢技术能有效提高生产效率.武钢CSP生产线设计年产薄板坯253万吨.热轧卷248万吨,产品定位于生产硅钢.汽车结构钢.集装箱钢等高附加值产品.炼钢总厂是具有国际先进水平的现代化大型钢厂,拥有从铁水脱硫到铸坯质量控制的整套核心技术,其转炉顶底复吹炉龄.纯净钢冶炼等技术指标位居国内前茅,是武钢硅钢.汽车板用钢.高性能工程结构钢三大战略品种的冶炼基地.总厂下设三个分厂,二炼钢分厂是武钢重要的品种钢生产基地,每年可生产4_个牌号的品种钢;三炼钢分厂是武钢最大的炼钢厂;四炼钢分厂主要是为硅钢产品提供板材.炼钢总厂年产钢1_万吨以上,生产品种涵盖_大系列5_多个钢种牌号,〝双高〞产品达90%以上.钢坯进入轧钢片进行轧制.武钢的热轧总厂下设四个分厂,是我国最大热轧板和中厚板生产基地之一,年产量超过__万吨,专用钢占产品比例80%以上.磁轭钢.管线钢.桥梁钢.压力容器用钢.工程结构用钢.铁道车辆用钢.船舶及海洋用钢等8大系列产品独树一帜,声名远播.冷轧薄板总厂是我国第一个从国外成套引进设备的专业冷轧厂,也是国内唯一可以生产宽度超过_MM冷轧板的厂家.总厂下设三个分厂,主要品种有冷轧板卷.热镀板卷.电镀锡板卷和彩涂板卷,其生产的高档轿车面板填补了国内空白.冷轧硅钢片素有冶金工业〝工艺品〞之称,代表着当今冶金工业生产技术的最高水平.武钢硅钢总厂是中国第一代冷轧硅钢产品的专业化生产厂,也是我国目前唯一的冷轧晶粒取向硅钢和高档无取向硅钢产品的生产企业.总厂下设三个分厂,产品品种达9大规格近80个牌号,几乎覆盖机电.家电.航空航天等所有电工钢应用领域,深受广大用户信赖,为国民经济的发展做出了重要贡献.3.实习内容及过程3.1参观炼铁厂武钢股份公司炼铁总厂于_年6月成立,包括烧结分厂.炼铁分厂,是武钢生产烧结矿和制钢生铁.铸造生铁的首道工序厂,具有精良的生产装备和先进的技术优势,主要经济技术指标在国内外同行业中处于领先地位.武钢炼铁主要原料包括烧结矿.球团矿.块矿(海南矿.南非矿以及澳矿等).熔剂(以石灰石和白云石为主).焦炭.煤粉和热风等,这些都有相应的车间进行准备.高炉的入炉熟料率达80%_85%,外加少量品位较高的块矿和球团矿,炉料碱度为1.8.高炉炉顶采用并罐式无钟炉顶设备,可以使炉顶压力相应提高,有利于高压操作.并罐式无钟炉顶由受料漏斗.称量料罐.中心喉管.气密箱.旋转溜槽等五部分组成.炼铁是指将金属铁从含铁矿物(主要为铁的氧化物)中提炼出来的工艺过程,主要有高炉法,直接还原法,熔融还原法,等离子法高炉炼铁是指把铁矿石和焦炭,一氧化碳,氢气等燃料及熔剂(从理论上说把活动性比铁的金属和矿石混合后高温也可炼出铁来)装入高炉中冶炼,去掉杂质而得到金属铁(生铁).高炉炼铁主要设备有高炉.高炉热风炉.铁水罐车.高炉是横断面为圆形的炼铁竖炉,用钢板作炉壳,里面砌耐火砖内衬.高炉生产是连续进行的.生产时,从炉顶(一般炉顶是由料种与料斗组成,现代化高炉是钟阀炉顶和无料钟炉顶)不断地装入铁矿石.焦炭.熔剂,从高炉下部的风口吹进热风(1_0~__摄氏度),喷入油.煤或天然气等燃料.装入高炉中的铁矿石,主要是铁和氧的化合物.在高温下,焦炭中和喷吹物中的碳及碳燃烧生成的一氧化碳将铁矿石中的氧夺取出来,得到铁.铁矿石通过还原反应炼出生铁,铁水从出铁口放出.铁矿石中的脉石.焦炭及喷吹物中的灰分与加入炉内的石灰石等熔剂结合生成炉渣,从出铁口和出渣口分别排出.篇三:武钢实习报告机械工程及自动化专业认识实习报告武汉科技大学机械自动化学院(_年9月)实习学生: _级机工__班姓名文维学号____30一.实习目的1.初步了解钢铁联合企业主要生产流程及主要设备所在位置与用途2.通过在实习厂主要岗位的现场参观.现场学习和讨论,提高分析问题和解决问题的能力,培养科学的思维方法和加强理论联系实际的能力.3.在学习工程技术人员和工人师傅在长期实践中积累的丰富知识和经验的同时,学习他们勤奋工作的精神和实事求是的作风,增强热爱专业,热爱劳动的思想.4.了解自己专业方面的知识和专业以外的知识,让我们早认识到我们将面临的工作问题,让我明白了以后读大学是要很认真的读,要有好的专业知识,才能为好的实际动手能力打下坚实的基础.5.通过认识实习认识钢铁生产企业的概貌,了解钢铁企业的主要生产工艺,增加对安全工程专业学科的感性认识,了解安全工程专业在国民经济建设中的地位.作用和发展趋势,熟悉安全工程技术人员的工作职责和工作程序,了解企业安全管理的现状和模式.二.实习内容武钢简介:武钢_55年始建,_58年9月_日建成投产.拥有从矿山采掘.炼焦(产能吨).炼铁(产能吨).炼钢(产能吨).轧钢及配套公辅设施等一整套先进的钢铁生产工艺设备,是我国重要的优质板材生产基地.武钢现已成为生产规模近4_0万吨的大型企业集团,居世界钢铁行业第四位,_年,武钢跻身世界5_强行列.现有钢铁制造业.高新技术产业和国际贸易三大主业.产品主要有热轧卷板.热轧型钢.热轧重轨.中厚板.冷轧卷板.镀锌板.镀锡板.冷轧取向和无取向硅钢片.彩涂钢板.高速线材等几百个品种.(一).炼铁厂实习报告实习时间_年_月_日实习地点武钢炼铁厂指导老师 :王涛1.武钢股份公司炼铁总厂简介武钢股份公司炼铁总厂于_年6月成立,包括烧结分厂.炼铁分厂,是武钢生产烧结矿和制钢生铁.铸造生铁的首道工序厂,具有精良的生产装备和先进的技术优势,主要经济技术指标在国内外同行业中处于领先地位.武钢炼铁主要原料包括烧结矿.球团矿.块矿(海南矿.南非矿以及澳矿等).熔剂(以石灰石和白云石为主).焦炭.煤粉和热风等,这些都有相应的车间进行准备.高炉的入炉熟料率达80%_85%,外加少量品位较高的块矿和球团矿,炉料碱度为1.8.高炉炉顶采用并罐式无钟炉顶设备,可以使炉顶压力相应提高,有利于高压操作.并罐式无钟炉顶由受料漏斗.称量料罐.中心喉管.气密箱.旋转溜槽等五部分组成.2.炼铁厂主要生产流程炼铁是指将金属铁从含铁矿物(主要为铁的氧化物)中提炼出来的工艺过程,主要有高炉法,直接还原法,熔融还原法,等离子法高炉炼铁是指把铁矿石和焦炭,一氧化碳,氢气等燃料及熔剂装入高炉中冶炼,去掉杂质而得到金属铁(生铁).其反应式为:Fe2O3+3CO=3CO2+2FeFe2O3+3H2=3H2O+2Fe2Fe2O3+3C=3CO2+4Fe高炉炼铁主要设备有高炉.高炉热风炉.铁水罐车.高炉是横断面为圆形的炼铁竖炉,用钢板作炉壳,里面砌耐火砖内衬.高炉生产是连续进行的.生产时,从炉顶(一般炉顶是由料种与料斗组成,现代化高炉是钟阀炉顶和无料钟炉顶)不断地装入铁矿石.焦炭.熔剂,从高炉下部的风口吹进热风(1_0~__摄氏度),喷入油.煤或天然气等燃料.装入高炉中的铁矿石,主要是铁和氧的化合物.在高温下,焦炭中和喷吹物中的碳及碳燃烧生成的一氧化碳将铁矿石中的氧夺取出来,得到铁.铁矿石通过还原反应炼出生铁,铁水从出铁口放出.铁矿石中的脉石.焦炭及喷吹物中的灰分与加入炉内的石灰石等熔剂结合生成炉渣,从出铁口和出渣口分别排出.煤气从炉顶导出,经除尘后,作为工业用煤气.高炉炼铁流程图如下:(二).炼铁厂实习报告实习时间 ___ 实习地点武钢二炼钢厂指导老师王涛。
武钢实习报告4篇
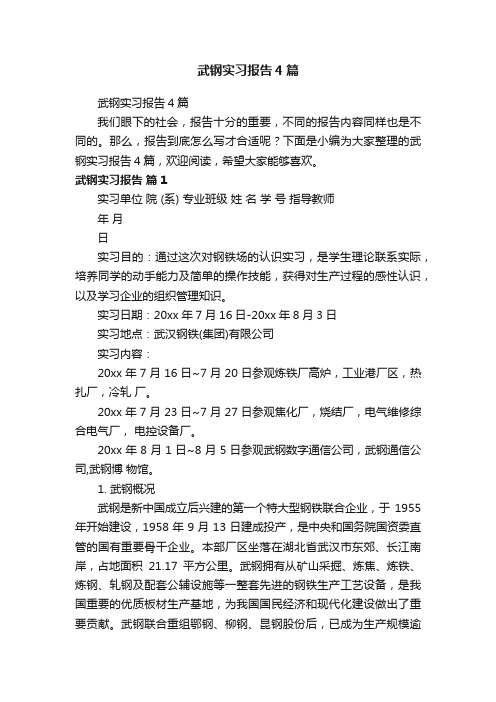
武钢实习报告4篇武钢实习报告4篇我们眼下的社会,报告十分的重要,不同的报告内容同样也是不同的。
那么,报告到底怎么写才合适呢?下面是小编为大家整理的武钢实习报告4篇,欢迎阅读,希望大家能够喜欢。
武钢实习报告篇1实习单位院 (系) 专业班级姓名学号指导教师年月日实习目的:通过这次对钢铁场的认识实习,是学生理论联系实际,培养同学的动手能力及简单的操作技能,获得对生产过程的感性认识,以及学习企业的组织管理知识。
实习日期:20xx 年7月16日-20xx年8月3日实习地点:武汉钢铁(集团)有限公司实习内容:20xx年7月16日~7月20日参观炼铁厂高炉,工业港厂区,热扎厂,冷轧厂。
20xx年7月23日~7月27日参观焦化厂,烧结厂,电气维修综合电气厂,电控设备厂。
20xx年8月1日~8月5日参观武钢数字通信公司,武钢通信公司,武钢博物馆。
1. 武钢概况武钢是新中国成立后兴建的第一个特大型钢铁联合企业,于1955年开始建设,1958年9月13日建成投产,是中央和国务院国资委直管的国有重要骨干企业。
本部厂区坐落在湖北省武汉市东郊、长江南岸,占地面积21.17平方公里。
武钢拥有从矿山采掘、炼焦、炼铁、炼钢、轧钢及配套公辅设施等一整套先进的钢铁生产工艺设备,是我国重要的优质板材生产基地,为我国国民经济和现代化建设做出了重要贡献。
武钢联合重组鄂钢、柳钢、昆钢股份后,已成为生产规模逾4000万吨的大型企业集团,居世界钢铁行业第四位。
20xx年武钢实现营业收入1907亿元,资产总额达到20xx亿元,现排名世界500强企业第340位。
武钢现有三大主业,即钢铁制造业、高新技术产业和国际贸易。
钢铁产品主要有热轧卷板、热轧型钢、热轧重轨、中厚板、冷轧卷板、镀锌板、镀锡板、冷轧取向和无取向硅钢片、彩涂钢板、高速线材等几百个品种。
目前武钢三大战略产品基地基本建成,武钢已成为全球最大、质量品种一流的硅钢生产基地;自主研发的汽车面板具备中高档轿车整车供货能力;高性能工程结构用钢、精品长材等保持国内领先地位。
武钢认识实习报告

2010年9月武钢认识实习报告经过两个星期的课程设计,我们终于迎来了去武钢实习的第三周。
周一下午,我们机工8个班一起来到教室进行实习前的培训。
老师给每位同学发了份《机械工程及自动化专业认识实习提纲》。
我们的实习目的是:初步了解钢铁联合企业主要生产流程及主要设备的位置及用途。
我知道我们将去四个厂,分别是热轧厂、二炼钢厂、炼铁厂和扎板厂。
培训时,老师着重强调了安全问题,要求实习必须遵守“两穿一带”(穿劳保、劳保鞋、带安全帽)。
第二天的早上,我们穿着————,不到9点就来到教一楼前等待,看到很多同学已经在此等待,戴着钢帽,有红,有蓝,五颜六色。
9点一刻终于等来了我们的热轧2号车,怀着无比激动的心情踏上了我们此次武钢的首旅。
坐在车上,欣赏沿路的风景,看到了武钢博物馆,武钢研究所-------终于来到了武钢,看到了毛主席招手的铜像,这也许是武钢的一号高炉练出他第一炉铁水时,毛主席来到武钢向工人致敬时的情景。
终于来到心中梦想已久的武钢。
进入武钢,满眼都是林立的厂房,翠绿的大树,粗长的管道,马路,横竖交纵,火车轨道遍布厂区。
蓝天白云,遍地绿茵,到处都有悦目的风景。
昔日浓烟滚滚的十里渣场,今天宛如美丽的花园。
第一站——二热轧厂二热轧厂所属热轧总厂。
热轧总厂下辖四座分厂,分别是一热轧厂、二热轧厂、三热轧厂以及轧板厂。
看到工人的安全帽上都标有“wisco 热轧总厂”的标识。
跟着带队老师来到厂房里,就听见机器的轰鸣声,一股热气扑面而来,不愧热轧厂的称号。
走上安全通道,一边走一边观看,并听着老师的讲解,做好笔记。
我看到了热轧四号加热炉(重庆赛迪工业炉有限公司),热轧三号加热炉,热轧二号加热炉,一些冷却去磷装置。
我还看到了吊车,有的挂着我们画过的吊钩,有的挂着夹子,在我们的头上作业。
还看到轧机上“争气争光争一流”响亮口号。
厂房里实在太热太吵了,也没听懂老师在讲什么,再加上当时厂里也没有生产,只能看到一些大型机器,听说二热轧拥有现在国内最宽也是最先进的轧机——2250轧机,但我却不识他。
武钢实习报告参考
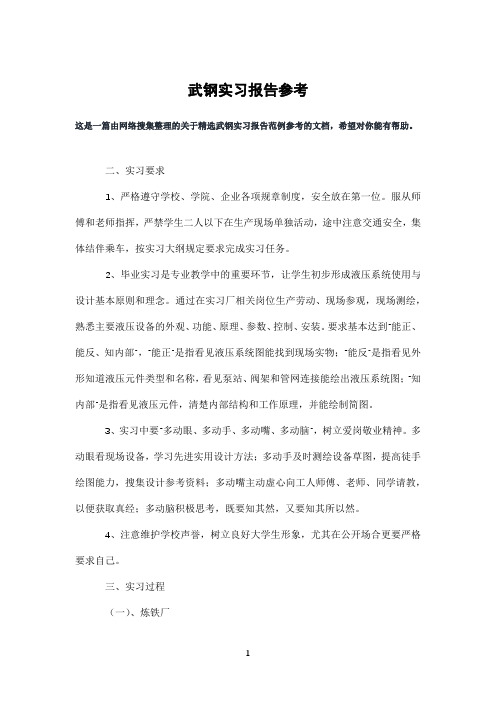
武钢实习报告参考这是一篇由网络搜集整理的关于精选武钢实习报告范例参考的文档,希望对你能有帮助。
二、实习要求1、严格遵守学校、学院、企业各项规章制度,安全放在第一位。
服从师傅和老师指挥,严禁学生二人以下在生产现场单独活动,途中注意交通安全,集体结伴乘车,按实习大纲规定要求完成实习任务。
2、毕业实习是专业教学中的重要环节,让学生初步形成液压系统使用与设计基本原则和理念。
通过在实习厂相关岗位生产劳动、现场参观,现场测绘,熟悉主要液压设备的外观、功能、原理、参数、控制、安装。
要求基本达到“能正、能反、知内部”,“能正”是指看见液压系统图能找到现场实物;“能反”是指看见外形知道液压元件类型和名称,看见泵站、阀架和管网连接能绘出液压系统图;“知内部”是指看见液压元件,清楚内部结构和工作原理,并能绘制简图。
3、实习中要“多动眼、多动手、多动嘴、多动脑”,树立爱岗敬业精神。
多动眼看现场设备,学习先进实用设计方法;多动手及时测绘设备草图,提高徒手绘图能力,搜集设计参考资料;多动嘴主动虚心向工人师傅、老师、同学请教,以便获取真经;多动脑积极思考,既要知其然,又要知其所以然。
4、注意维护学校声誉,树立良好大学生形象,尤其在公开场合更要严格要求自己。
三、实习过程(一)、炼铁厂武钢股份公司炼铁总厂于2008年6月成立,包括烧结分厂、炼铁分厂,是武钢生产烧结矿和制钢生铁、铸造生铁的首道工序厂,具有精良的生产装备和先进的技术优势,主要经济技术指标在国内外同行业中处于领先地位。
炼铁分厂(原炼铁厂)于1957年破土动工,1958年建成投产。
经过50年的建设、改造和发展,已拥有8座现代化大型高炉,其中3200 m3的有3座,3800m3的有1座(暂未投产),年生产能力超过1500万吨,是我国生铁的主要生产基地之一。
炼铁分厂坚持走引进、消化与自主开发之路,无料钟炉顶、软水密闭循环、环保型INBA炉渣处理系统、薄炉衬铜冷却壁、高炉专家系统等一大批当代先进的炼铁工艺广泛应用于高炉生产之中,高炉利用系数进入国际一流、国内领先水平。
武钢炼钢厂实习报告
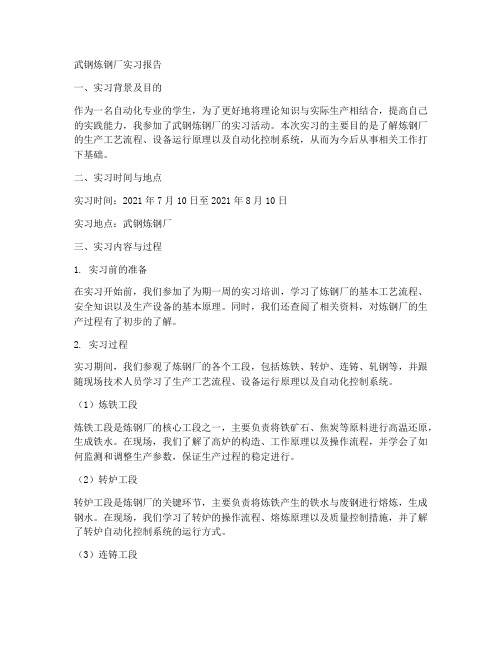
武钢炼钢厂实习报告一、实习背景及目的作为一名自动化专业的学生,为了更好地将理论知识与实际生产相结合,提高自己的实践能力,我参加了武钢炼钢厂的实习活动。
本次实习的主要目的是了解炼钢厂的生产工艺流程、设备运行原理以及自动化控制系统,从而为今后从事相关工作打下基础。
二、实习时间与地点实习时间:2021年7月10日至2021年8月10日实习地点:武钢炼钢厂三、实习内容与过程1. 实习前的准备在实习开始前,我们参加了为期一周的实习培训,学习了炼钢厂的基本工艺流程、安全知识以及生产设备的基本原理。
同时,我们还查阅了相关资料,对炼钢厂的生产过程有了初步的了解。
2. 实习过程实习期间,我们参观了炼钢厂的各个工段,包括炼铁、转炉、连铸、轧钢等,并跟随现场技术人员学习了生产工艺流程、设备运行原理以及自动化控制系统。
(1)炼铁工段炼铁工段是炼钢厂的核心工段之一,主要负责将铁矿石、焦炭等原料进行高温还原,生成铁水。
在现场,我们了解了高炉的构造、工作原理以及操作流程,并学会了如何监测和调整生产参数,保证生产过程的稳定进行。
(2)转炉工段转炉工段是炼钢厂的关键环节,主要负责将炼铁产生的铁水与废钢进行熔炼,生成钢水。
在现场,我们学习了转炉的操作流程、熔炼原理以及质量控制措施,并了解了转炉自动化控制系统的运行方式。
(3)连铸工段连铸工段是将转炉产生的钢水通过连铸机进行浇铸,形成钢坯的过程。
我们了解了连铸机的构造、操作流程以及质量控制方法,并学会了如何监测和调整生产参数,保证钢坯质量。
(4)轧钢工段轧钢工段是将连铸产生的钢坯进行轧制,形成各种钢材的过程。
在现场,我们学习了轧钢机的操作流程、轧制原理以及产品质量控制,并了解了轧钢自动化控制系统的运行方式。
3. 实习成果通过实习,我们深入了解了炼钢厂的生产工艺流程、设备运行原理以及自动化控制系统,提高了自己的实践能力。
同时,我们学会了如何监测和调整生产参数,保证生产过程的稳定进行,为今后从事相关工作打下了基础。
工作报告-武钢炼钢厂实习报告

工作报告-武钢炼钢厂实习报告
尊敬的领导:
我是在武钢炼钢厂进行为期两个月的实习生。
在这段时间里,我有幸参与了武钢炼钢厂的生产运营和管理工作,并且深入学习了炼钢厂的各项操作技术和管理方法。
现在我将向您汇报我的实习情况和所做的工作。
首先,在炼钢车间实习期间,我主要负责监督炼钢过程并提供技术支持。
我熟悉了炼钢的基本流程和常见问题的处理方法,并且参与了几个炼钢项目的实施。
通过实际操作,我不仅学到了很多理论知识,还掌握了一些实际技能,比如使用炼钢设备和检测仪器等。
其次,在实习期间,我还参与了炼钢厂的生产计划和生产调度工作。
我学习了如何制定合理的生产计划,如何安排生产任务和资源,并且了解了生产过程中可能出现的问题和应对方法。
在实习期间,我与其他员工密切合作,共同解决了一些生产上的困难和难题,提高了工作效率和质量。
最后,我还参与了炼钢厂的质量管理和安全管理工作。
我学习了如何进行质量控制和质量检测,并且了解了炼钢过程中可能存在的安全隐患和事故预防措施。
我积极参与了炼钢厂的安全培训和演练活动,提高了自己的安全意识和应急处理能力。
通过这次实习,我深刻体会到了炼钢厂的复杂性和挑战性。
我学到了很多专业知识和技能,提高了自己的综合素质和工作能力。
同时,我也意识到自己在实习期间还存在一些不足和需要改进的地方,比如沟通能力和团队合作能力等。
因此,我会继续努力学习和提升自己,争取更好地适应和发展在这个行业。
感谢领导和公司给予我这次宝贵的实习机会,我会珍惜这次机会,继续向前努力。
如果有机会,我愿意留在武钢炼钢厂工作,为公司的发展做出自己的贡献。
谢谢!。
【实习报告】武钢实习报告
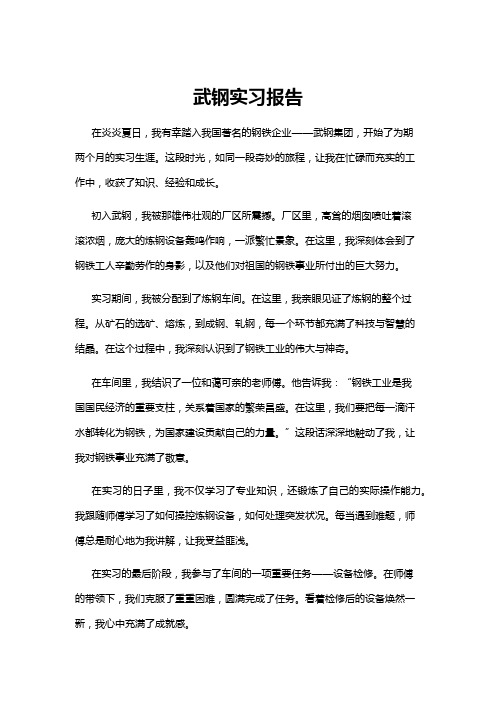
武钢实习报告在炎炎夏日,我有幸踏入我国著名的钢铁企业——武钢集团,开始了为期两个月的实习生涯。
这段时光,如同一段奇妙的旅程,让我在忙碌而充实的工作中,收获了知识、经验和成长。
初入武钢,我被那雄伟壮观的厂区所震撼。
厂区里,高耸的烟囱喷吐着滚滚浓烟,庞大的炼钢设备轰鸣作响,一派繁忙景象。
在这里,我深刻体会到了钢铁工人辛勤劳作的身影,以及他们对祖国的钢铁事业所付出的巨大努力。
实习期间,我被分配到了炼钢车间。
在这里,我亲眼见证了炼钢的整个过程。
从矿石的选矿、熔炼,到成钢、轧钢,每一个环节都充满了科技与智慧的结晶。
在这个过程中,我深刻认识到了钢铁工业的伟大与神奇。
在车间里,我结识了一位和蔼可亲的老师傅。
他告诉我:“钢铁工业是我国国民经济的重要支柱,关系着国家的繁荣昌盛。
在这里,我们要把每一滴汗水都转化为钢铁,为国家建设贡献自己的力量。
”这段话深深地触动了我,让我对钢铁事业充满了敬意。
在实习的日子里,我不仅学习了专业知识,还锻炼了自己的实际操作能力。
我跟随师傅学习了如何操控炼钢设备,如何处理突发状况。
每当遇到难题,师傅总是耐心地为我讲解,让我受益匪浅。
在实习的最后阶段,我参与了车间的一项重要任务——设备检修。
在师傅的带领下,我们克服了重重困难,圆满完成了任务。
看着检修后的设备焕然一新,我心中充满了成就感。
这段实习经历让我明白了:一是钢铁工业的重要性,它是国家工业的基石;二是团队协作的力量,只有团结一致,才能战胜一切困难;三是敬业精神,每一位钢铁工人都在为国家的繁荣昌盛默默奉献。
如今,实习生涯即将结束,我带着满满的收获和感动回到了校园。
这段经历将成为我人生中宝贵的财富,激励我不断前行,为实现中华民族伟大复兴的中国梦贡献自己的力量。
高炉炼铁实习报告

一、实习背景为了更好地了解我国钢铁行业的发展现状,提高自己的实践能力,我于2023年X月X日至X月X日在XX钢铁集团有限公司炼铁厂进行了为期两周的实习。
本次实习让我对高炉炼铁工艺有了更为深入的了解,对钢铁行业有了更加全面的认知。
二、实习内容1. 高炉结构及工作原理在实习期间,我首先学习了高炉的结构及工作原理。
高炉主要由炉体、炉顶、炉喉、炉腹、炉腰、炉底等部分组成。
高炉炼铁是将铁矿石、焦炭和石灰石等原料在高炉内加热还原,生产出铁水的过程。
在高炉内,焦炭燃烧产生的高温气体将铁矿石中的铁氧化物还原成铁水,同时生成炉渣。
2. 原料处理原料处理是高炉炼铁的重要环节。
实习期间,我参观了原料场,了解了铁矿石、焦炭、石灰石等原料的存放、运输和处理过程。
原料场采用皮带输送机将原料送至高炉原料仓,再通过配料系统按比例加入高炉。
3. 上料系统上料系统是高炉炼铁的关键设备之一。
实习期间,我学习了上料系统的组成、工作原理及维护保养方法。
上料系统主要包括料仓、配料系统、输送皮带、振动给料机等设备。
4. 高炉操作高炉操作是高炉炼铁的核心环节。
实习期间,我参观了高炉操作室,了解了高炉操作的流程和注意事项。
高炉操作主要包括炉顶加料、炉喉探尺、炉腰探尺、炉底放渣等。
5. 环境保护在实习过程中,我了解到炼铁厂高度重视环境保护,采取了一系列措施减少污染物排放。
如采用湿法脱硫、干法脱硫等技术降低二氧化硫排放;采用静电除尘、布袋除尘等技术降低粉尘排放。
三、实习心得1. 理论与实践相结合通过本次实习,我深刻体会到理论与实践相结合的重要性。
在课堂上学习到的理论知识,在实习过程中得到了实际应用,使我对高炉炼铁工艺有了更为深刻的理解。
2. 团队协作精神在实习过程中,我认识到团队协作精神的重要性。
炼铁厂的生产过程需要各个岗位的紧密配合,只有团结协作,才能保证生产顺利进行。
3. 安全意识实习期间,我时刻保持安全意识,严格遵守操作规程,确保自身和他人的安全。
武钢高炉炼铁厂实习报告
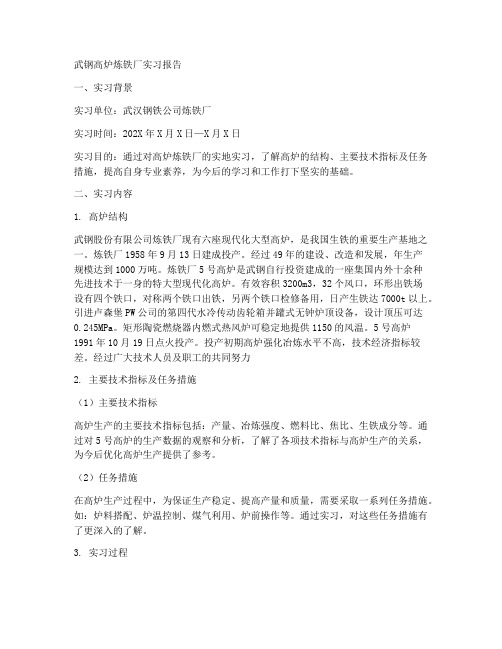
武钢高炉炼铁厂实习报告一、实习背景实习单位:武汉钢铁公司炼铁厂实习时间:202X年X月X日—X月X日实习目的:通过对高炉炼铁厂的实地实习,了解高炉的结构、主要技术指标及任务措施,提高自身专业素养,为今后的学习和工作打下坚实的基础。
二、实习内容1. 高炉结构武钢股份有限公司炼铁厂现有六座现代化大型高炉,是我国生铁的重要生产基地之一。
炼铁厂1958年9月13日建成投产。
经过49年的建设、改造和发展,年生产规模达到1000万吨。
炼铁厂5号高炉是武钢自行投资建成的一座集国内外十余种先进技术于一身的特大型现代化高炉。
有效容积3200m3,32个风口,环形出铁场设有四个铁口,对称两个铁口出铁,另两个铁口检修备用,日产生铁达7000t以上。
引进卢森堡PW公司的第四代水冷传动齿轮箱并罐式无钟炉顶设备,设计顶压可达0.245MPa。
矩形陶瓷燃烧器内燃式热风炉可稳定地提供1150的风温。
5号高炉1991年10月19日点火投产。
投产初期高炉强化冶炼水平不高,技术经济指标较差。
经过广大技术人员及职工的共同努力2. 主要技术指标及任务措施(1)主要技术指标高炉生产的主要技术指标包括:产量、冶炼强度、燃料比、焦比、生铁成分等。
通过对5号高炉的生产数据的观察和分析,了解了各项技术指标与高炉生产的关系,为今后优化高炉生产提供了参考。
(2)任务措施在高炉生产过程中,为保证生产稳定、提高产量和质量,需要采取一系列任务措施。
如:炉料搭配、炉温控制、煤气利用、炉前操作等。
通过实习,对这些任务措施有了更深入的了解。
3. 实习过程在实习期间,我们参观了炼铁厂的生产现场,了解了高炉的生产流程。
同时,我们还参加了炼铁厂组织的座谈会,与技术人员进行了深入交流,了解了高炉生产的难点和热点问题。
三、实习收获通过在高炉炼铁厂的实习,我对高炉的结构、主要技术指标及任务措施有了全面的认识。
实习过程中,我深刻体会到理论与实践相结合的重要性,为我今后的学习和工作打下了坚实的基础。
炼铁实习的报告

一、实习背景随着我国经济的快速发展,钢铁行业作为国民经济的重要支柱产业,其发展势头迅猛。
为了更好地了解钢铁行业的生产过程,提高自己的专业素养,我在2021年7月至9月期间,在XX钢铁有限公司进行了为期两个月的炼铁实习。
本次实习旨在让我深入了解炼铁工艺,掌握炼铁生产的基本流程,提升自己的实践能力。
二、实习内容1. 实习岗位及职责在实习期间,我主要在炼铁厂的高炉车间进行实习。
实习岗位包括高炉工、原料工、烧结工等。
我的主要职责是:(1)高炉工:负责高炉的日常操作,包括点火、加料、放渣、检查炉况等。
(2)原料工:负责原料的接收、检验、储存和输送,确保原料的质量和供应。
(3)烧结工:负责烧结矿的生产,包括配料、烧结、冷却、破碎等环节。
2. 实习过程(1)高炉工实习在高炉工实习期间,我跟随师傅学习了高炉的操作流程。
首先,了解了高炉的结构、原理和操作要点。
接着,在师傅的指导下,参与了高炉的点火、加料、放渣等操作。
在实习过程中,我掌握了以下技能:① 熟悉高炉操作规程,了解高炉生产的基本原理。
② 掌握高炉炉况检查方法,能够及时发现并处理异常情况。
③ 掌握高炉加料、放渣等操作技巧,确保高炉生产的稳定。
(2)原料工实习在原料工实习期间,我主要负责原料的接收、检验、储存和输送。
具体内容包括:① 接收原料:对 incoming 的原料进行验收,确保原料质量符合要求。
② 检验原料:对原料进行化学成分、粒度等检验,确保原料质量。
③ 储存原料:将检验合格的原料按照种类、规格分类储存。
④ 输送原料:将原料输送到高炉车间,确保原料供应。
(3)烧结工实习在烧结工实习期间,我参与了烧结矿的生产过程。
具体内容包括:① 配料:根据生产计划,将不同种类、规格的原料按照比例进行配料。
② 烧结:将配料好的原料送入烧结机进行烧结,生成烧结矿。
③ 冷却:将烧结好的烧结矿进行冷却,降低温度。
④ 破碎:将冷却后的烧结矿进行破碎,得到符合要求的烧结矿。
三、实习收获1. 提升了专业技能通过实习,我对炼铁工艺有了更深入的了解,掌握了高炉操作、原料处理、烧结等环节的基本技能。
高炉车间实习报告

高炉车间实习报告一、实习背景及目的随着我国经济的快速发展,钢铁工业作为国民经济的重要支柱产业,其生产技术和设备水平不断提高。
高炉作为钢铁生产中的关键环节,其运行状态和操作水平直接影响到整个钢铁厂的生产效率和产品质量。
为了更好地了解高炉的生产工艺和操作流程,提高自身的实践能力,我参加了为期一个月的在高炉车间的实习。
本次实习的主要目的是通过实际操作,深入了解高炉的生产工艺、操作流程和设备运行原理,培养自己的团队合作精神和职业道德,提高自己的独立工作能力和劳动观念。
二、实习内容及收获1. 实习内容在实习期间,我参与了高炉车间的日常生产操作,了解了高炉的生产工艺流程,包括原料准备、配料、炉料装填、炉操作、煤气净化和回收等环节。
同时,我还学习了高炉设备的工作原理和维护保养知识,以及高炉生产过程中的安全注意事项。
2. 实习收获(1)了解了高炉的生产工艺流程,掌握了各环节的操作要领,为以后从事钢铁生产工作打下了基础。
(2)学会了使用高炉生产设备,提高了自己的动手能力。
(3)深入了解了高炉生产过程中的安全注意事项,增强了安全意识。
(4)培养了团队合作精神和职业道德,提高了自己的独立工作能力和劳动观念。
三、实习中遇到的问题及解决办法在实习过程中,我遇到了一些问题,如在高炉操作过程中对设备运行原理不熟悉,导致操作不当;在煤气净化和回收环节中,对安全注意事项掌握不充分,存在一定的安全隐患等。
针对这些问题,我通过向师傅请教、查阅资料和参加培训等方式,不断丰富自己的专业知识,提高自己的操作技能和安全意识。
四、实习总结通过在高炉车间的实习,我对高炉的生产工艺和操作流程有了更深入的了解,提高了自己的实践能力和综合素质。
同时,我也认识到了团队合作和职业道德在实际工作中的重要性。
在今后的工作中,我将继续努力学习,不断提高自己的专业水平,为我国钢铁事业的发展贡献自己的力量。
最后,我要感谢高炉车间全体师傅的悉心教导和帮助,使我能够在短时间内掌握高炉的生产技能。
高炉炉前工实习报告

高炉炉前工实习报告一、实习时间与地点实习时间:202X年X月X日—X月X日实习地点:XX钢铁公司炼铁厂五号高炉二、实习目的1. 了解高炉炉前工作的基本流程和操作规范。
2. 学习高炉炉前各项检测技术,掌握高炉操作参数的监测方法。
3. 掌握高炉炉前工具的使用方法,提高自身的安全操作意识。
4. 了解高炉炉前设备的维护保养,为高炉的正常生产提供保障。
三、实习内容与过程1. 实习开始前,我参加了炼铁厂组织的安全培训,学习了高炉炉前工作的安全操作规程和应急预案。
通过培训,我对高炉炉前工作有了初步的了解,为实际操作打下了基础。
2. 在实习过程中,我跟随师傅学习了高炉炉前的各项检测技术,包括温度、压力、流量等参数的监测。
我了解到,高炉炉前的检测工作至关重要,直接关系到高炉生产的稳定性和产品质量。
3. 我学会了使用高炉炉前工具,如钻头、钎子、风铲等,并掌握了相应的操作技巧。
在实际操作中,我严格按照操作规程进行,确保了自身和他人的安全。
4. 实习期间,我参与了高炉炉前设备的维护保养工作,学习了设备维护的基本知识和技巧。
我了解到,设备维护是保证高炉正常生产的关键,必须做到精细化、规范化。
5. 实习的最后阶段,我参与了高炉炉前的故障排查工作。
通过实际操作,我学会了分析问题、解决问题的方法,提高了自身的故障排除能力。
四、实习收获与体会1. 通过实习,我掌握了高炉炉前工作的基本流程和操作规范,为今后从事相关工作打下了基础。
2. 我学会了高炉炉前各项检测技术,了解了高炉操作参数的监测方法,提高了自身的技术水平。
3. 实习过程中,我学会了使用高炉炉前工具,提高了自身的安全操作意识。
4. 我了解了高炉炉前设备的维护保养,为保证高炉的正常生产提供了保障。
5. 实习使我认识到,高炉炉前工作责任重大,必须严谨认真,一丝不苟。
同时,团队协作也是高炉炉前工作成功的关键。
五、实习总结通过本次实习,我对高炉炉前工作有了更深入的了解,自身的能力也得到了提高。
高炉工种实习报告

一、实习时间20XX年X月X日—20XX年X月X日二、实习地点武汉钢铁公司炼铁厂五号高炉三、实习目的1. 了解高炉的结构和工作原理,掌握高炉炼铁的基本流程。
2. 学习高炉操作技术,提高实际操作能力。
3. 了解高炉生产过程中的安全知识和应急处理措施。
4. 培养团队合作精神和敬业精神。
四、实习内容1. 高炉结构及工作原理在实习期间,我首先学习了高炉的结构和工作原理。
高炉是炼铁的主要设备,其主要结构包括炉顶、炉身、炉底、炉缸、炉喉等部分。
高炉的工作原理是利用焦炭、铁矿石、石灰石等原料在高温下发生还原反应,生成铁水。
2. 高炉操作技术在高炉操作方面,我主要学习了以下内容:(1)高炉送风操作:掌握送风设备的操作方法,调整送风量,保证高炉稳定生产。
(2)高炉加料操作:了解加料设备的操作方法,按照生产要求加料,保证高炉炉料平衡。
(3)高炉测温操作:学习测温仪器的使用方法,掌握高炉炉温变化情况。
(4)高炉探尺操作:了解探尺的使用方法,测量高炉炉缸内铁水液面高度。
3. 安全知识和应急处理措施在高炉生产过程中,安全至关重要。
我学习了以下安全知识和应急处理措施:(1)高炉操作人员必须穿戴好个人防护用品,如安全帽、工作服、手套等。
(2)严禁在高炉周围吸烟、喝酒,防止火灾发生。
(3)发现设备故障或异常情况,应立即停止操作,并向班长报告。
(4)掌握高炉停电、断风等突发事件的应急处理方法。
4. 团队合作和敬业精神在高炉实习过程中,我深刻体会到团队合作和敬业精神的重要性。
高炉生产是一个复杂的系统工程,需要各个岗位的密切配合。
我学会了与同事相互沟通、协作,共同完成生产任务。
五、实习体会和收获1. 通过实习,我对高炉炼铁的基本流程和操作技术有了更深入的了解,提高了自己的实际操作能力。
2. 在实习过程中,我学会了如何处理生产过程中的突发事件,提高了自己的应急处理能力。
3. 通过与同事的协作,我培养了团队合作精神,提高了自己的沟通能力。
炼钢厂的实习报告

一、实习背景随着我国经济的快速发展,钢铁产业作为国民经济的重要支柱,其地位日益凸显。
为了深入了解钢铁生产过程,提高自身专业素养,我于2023年6月至7月在某大型炼钢厂进行了为期一个月的实习。
通过这次实习,我对炼钢工艺、设备操作、安全管理等方面有了更为全面的认识。
二、实习目的1. 了解炼钢生产的基本流程,掌握炼钢工艺原理;2. 熟悉炼钢厂各类设备,提高实际操作能力;3. 增强团队协作意识,培养职业素养;4. 为今后从事相关工作奠定基础。
三、实习内容1. 炼钢工艺流程炼钢生产主要包括以下几个步骤:熔融、精炼、浇铸、冷却、热处理、检验等。
在实习过程中,我了解了熔融阶段的氧气顶吹转炉炼钢、电弧炉炼钢等工艺;精炼阶段的脱氧、脱硫、脱磷等处理;浇铸阶段的连铸、模铸等工艺;冷却阶段的水冷、风冷等冷却方式;热处理阶段的退火、正火、调质等工艺;检验阶段的化学成分、力学性能等检测。
2. 炼钢设备操作实习期间,我学习了转炉、电炉、连铸机、冷却塔等设备的操作方法。
在师傅的指导下,我亲自操作了部分设备,如转炉的加料、吹氧、取样等。
通过实践,我对设备的操作原理和注意事项有了更加深刻的理解。
3. 安全管理炼钢厂生产过程中存在一定的安全隐患,因此在实习过程中,我特别注重安全管理。
我学习了安全操作规程、应急预案等内容,提高了自己的安全意识。
同时,我还参加了安全培训,了解了事故案例分析,为今后从事相关工作积累了经验。
4. 团队协作实习期间,我深刻体会到团队协作的重要性。
在完成各项任务的过程中,我与同事相互配合,共同解决问题。
通过这次实习,我的团队协作能力得到了提高。
四、实习收获1. 理论与实践相结合:通过实习,我对炼钢工艺、设备操作等理论知识有了更深刻的理解,并将理论知识运用到实际工作中。
2. 增强职业素养:在实习过程中,我学会了如何与同事、领导沟通,提高了自己的职业素养。
3. 培养安全意识:实习使我认识到安全生产的重要性,增强了安全意识。
炼铁炼钢厂实习报告

炼铁炼钢厂实习报告一、实习背景作为钢铁行业的重要组成部分,炼铁炼钢厂是钢铁生产的关键环节。
在中国这个工业大国,炼铁炼钢厂的实习经历对于学生来说是非常有价值和意义的。
本次实习是我在大学期间的一次重要实践机会,通过实地实习,深入了解钢铁生产工艺和操作流程,提高自己的专业技能和实践能力。
二、实习目标和任务本次实习的主要目标是了解炼铁炼钢厂的运营模式和工艺流程,掌握炼铁炼钢厂的基本操作方法和安全规范,熟悉钢铁产品的生产过程和质量检验标准。
同时,通过实践操作,提高自己的团队合作能力和沟通能力,增强自己的实际操作技能。
在实习期间,我的任务主要是参与炼铁炼钢厂的生产现场操作,包括原料处理、炉料配料、炉的操作监控、钢水处理、冶炼炉维护等工作。
同时,我也要协助工程师进行设备检修、质量检验等工作,提供必要的技术支持和实际操作。
三、实习过程和收获1. 炼铁厂实习过程在炼铁厂的实习中,我主要负责矿石破碎和筛分过程中的操作。
首先,我了解了矿石的种类和特性,学会正确进行矿石的破碎和筛分操作,确保矿石粒度符合要求。
其次,我还学习了矿石浮选和磁选等分离技术,掌握了矿石精矿的提取和浓缩方法。
这些实践操作让我深入理解了炼铁厂的矿石处理工艺和技术要点。
2. 炼钢厂实习过程在炼钢厂的实习中,我主要参与了炉料配料和钢水处理的操作。
在炉料配料过程中,我学习了不同原料的比例配比和混合方法,了解了炉料配料对钢水质量的影响。
而在钢水处理过程中,我掌握了钢水温度的控制和钢水中杂质的除去方法。
通过这些实践操作,我对炼钢厂的生产流程和工艺规范有了更加深入的了解。
3. 实习收获通过整个实习过程,我深刻认识到了炼铁炼钢厂的重要性和复杂性。
炼铁炼钢厂是一个高风险、高技术含量的工作环境,需要严格遵循操作规程和安全规范。
同时,我也了解到了钢铁行业在中国社会经济发展中的重要地位和贡献。
钢铁产品是工业生产的基础材料,对于国家经济和国防建设有着重要的支撑作用。
通过这次实习,我不仅加深了对炼铁炼钢厂工艺流程和操作方法的理解,还提高了自己的实际操作能力和团队合作能力。
- 1、下载文档前请自行甄别文档内容的完整性,平台不提供额外的编辑、内容补充、找答案等附加服务。
- 2、"仅部分预览"的文档,不可在线预览部分如存在完整性等问题,可反馈申请退款(可完整预览的文档不适用该条件!)。
- 3、如文档侵犯您的权益,请联系客服反馈,我们会尽快为您处理(人工客服工作时间:9:00-18:30)。
武钢炼铁厂5号高炉实习目的毕业实习是我们专业重要的教学环节,是专业课教学的一个组成部分。
通过在实习厂主要岗位的生产劳动、现场参观、现场教学和讨论,培养和锻炼我们在生产现场独立工作的能力,分析问题的方法和解决问题的能力,理论联系实际的能力及科学的思维方法。
在牢固掌握专业理论知识的基础上,我们深入到武汉钢铁集团炼铁厂5号高炉,详细了解炼铁工艺流程及其主要设备,收集毕业设计所需的参数等相关资料。
在学习工程技术人员和工人师傅在长期实践中积累的丰富知识和经验的同时,我们还要学习他们勤奋工作的精神和实事求是的工作作风,学习他们的生产实际知识和为“四化”勤奋工作的精神,增强热爱专业,热爱劳动的思想。
为毕业设计的顺利进行以及以后踏上工作岗位奠定坚实的基础。
实习时间共两周,即20xx年x月x日—20xx年x月xx日实习地点武钢炼铁厂5号高炉1 武钢炼铁厂简介武钢股份公司炼铁总厂于2008年6月成立,包括烧结分厂、炼铁分厂,是武钢生产烧结矿和制钢生铁、铸造生铁的首道工序厂,具有精良的生产装备和先进的技术优势,主要经济技术指标在国内外同行业中处于领先地位。
炼铁分厂(原炼铁厂)于1957年破土动工,1958年建成投产。
经过50年的建设、改造和发展,已拥有8座现代化大型高炉,其中3200 m3的有3座,3800m3的有1座(暂未投产),年生产能力超过15 00万吨,是我国生铁的主要生产基地之一。
炼铁分厂坚持走引进、消化与自主开发之路,无料钟炉顶、软水密闭循环、环保型INBA炉渣处理系统、薄炉衬铜冷却壁、高炉专家系统等一大批当代先进的炼铁工艺广泛应用于高炉生产之中,高炉利用系数进入国际一流、国内领先水平。
武钢炼铁厂5号高炉是武钢自行投资建成的一座集国内外十余种先进技术于一身的特大型现代化高炉,于1991年10 月19日点火投产。
高炉有效容积3200 m3,共有32个风口,皮带上料,环形出铁场,设有4个出铁口,对称的两个铁口出铁,另两个检修备用,日产生铁7000t以上。
引进卢森堡PW公司的第四代水冷传动齿轮箱并罐式无钟炉顶设备,设计顶压可达。
该高炉配备有4座矩形陶瓷燃烧器内燃式热风炉,可稳定地提供1150℃的热风。
具体生产技术设计指标见表1。
表1 5号高炉的生产技术设计指标有效容积3200 m3炉缸直径12000mm4800 mm 风口数32个炉缸有效高度铁口数4个(互成90°)年产量324万吨利用系数 2.0—2.5 入炉焦比450 kg/t煤比100—120kg/t 热风温度1200℃烧结矿率80%—85% 渣比<470 kg/t炉顶压力2 炼铁原料及有关设备武钢炼铁主要原料包括烧结矿、球团矿、块矿(海南矿、南非矿以及澳矿等)、熔剂(以石灰石和白云石为主)、焦炭、煤粉和热风等,这些都有相应的车间进行准备。
高炉的入炉熟料率达80%~85%,外加少量品位较高的块矿和球团矿,炉料碱度为1.8。
其具体炉料结构参见表2.1。
高炉炉顶采用并罐式无钟炉顶设备,可以使炉顶压力相应提高,有利于高压操作。
并罐式无钟炉顶由受料漏斗、称量料罐、中心喉管、气密箱、旋转溜槽等五部分组成。
旋转溜槽可以完成两个动作:①绕高炉中心线的旋转运动;②在垂直面内可以改变溜槽的倾角。
该设备具有以下优点:①布料理想,调剂灵活;②设备总高度较低;③密封性好,能承受高压操作;④两个称量料罐交替工作。
但其缺点也是很明显的:①中心喉管磨损较快;②存在并罐效应。
由于称量料罐中心线和高炉中心线有较大的间距,会在布料时产生料流偏析现象,称之为并罐效应。
图1 并罐式无钟炉顶装置示意图5号高炉目前采用先进的软水闭路循环冷却系统,工作可靠,系统稳定,冷却效果好,而且节能节水(漏损率只有0.4‰),这对水资源紧张的钢铁企业来说无疑具有重要的现实意义。
另外,因回水余压可以利用,故可节省供水加压的部分能耗。
其进水总量达到5176 m3/h,软水总进温℃,进出水温差℃。
表2.1 5号高炉炉料结构炉料烧结矿球团矿进口块矿海南矿钒钛矿配比(%)68~72 16~20 5~12 1~6 1.5~55号高炉现配有4座高温内燃式热风炉,采用眼睛式燃烧室和霍戈文式矩形陶瓷燃烧器,用两台驱动电力为6kV,800kW的助燃风机集中供风。
可利用热风炉废气预热高炉煤气和助燃空气到130℃,以利于提高热风炉热效率,4座热风炉运行时可实现交替并联送风,即三烧一送,时间原则45分钟,温度原则自动,系统半自动。
压力为的冷风鼓入已经蓄热好的热风炉,冷风与格子砖进行充分的接触换热。
热风通过热风总管送入围管,再由32个风口鼓入炉内。
其他相应参数见表2.2。
表2.2 5号高炉鼓风参数冷风流量6623 m3/min 风速m/s冷风压力MPa 进风面积m2冷风温度197℃鼓风动能14150 kg·m/s热风温度A 1100℃热风压力MPa热风温度B 1068℃这座高炉配备有4个铁口,采用摆动流嘴受铁,2套INBA炉渣粒化装置,一套可供2个铁口使用。
炉前环形出铁场有2台环形吊车,作业面积可达到98%。
环形布置使得渣沟、铁沟短,炉前除尘设备容易安装,目前高炉采用了2台224 m2 电除尘器。
4个铁口各自配备一台风动开口机,有效行程4000mm,开口深度3800mm,开口角度9度、12度,并各配一台液压泥炮。
5号高炉炉顶压力为MPa,顶压直接影响到炉料的下降、冶炼强度以及高炉顺行。
矿石和焦炭的反应是随着炉料的下降逐级进行的。
由于温度越来越高,产生液态的炉渣和铁在滴落带滴入炉缸。
本高炉的炉缸高度是4800 mm,炉缸直径为12200 mm,两小时出一次铁,出铁时间目前为1个半小时。
出铁时,铁水和炉渣一起流入主沟,然后用挡渣板挡渣,使渣铁分离,分别进入铁水沟和渣沟。
铁水则流入铁水罐,由火车运入炼钢车间,渣则用水冲,水冲渣用于造水泥等。
3 生产水平5号高炉投产至今,已有近15年的炉龄,是目前武钢超期使用最长的一座高炉。
它于2007年6月开始大修,历时六个月,为炼铁系统实现高产、优质、低耗创造了必要条件。
同年12月23日开炉,3天达产。
达产当日,利用系数达t/m3·d,产量达6484.6吨,之后,该高炉生产快速步入良性循环,利用系数一直稳定在2.0吨/立方米每天以上,开炉后8天的平均系数在t/m3·d以上。
大修后的5号高炉技术装备达到国内同类高炉先进技术水平,预计每年可产生铁280万吨,可继续使用20年。
此外,高炉大修还充分重视环保,改造后可达到废水零排放,粉尘排放浓度也低于国家标准。
随着炉龄的增长,炉墙厚度逐渐减薄,基本上形成了一座薄炉衬高炉,目前实际有效容积已经达到了340 0~3600 m3。
经过广大工人和技术人员的共同努力,十几年来,5号高炉的主要技术经济指标得到了显著提高。
2009年2月,5号高炉炼铁生产创造了又一项全新的纪录:生铁产量万吨,超目标计划万吨;高炉利用系数t/m3·d,日利用系数t/m3·d 。
表3.1示出了5号高炉投产以来部分技术经济指标的变化情况。
5号高炉近几年创造的相关纪录见表3.2 。
图3.1直观地给出了5号高炉投产以来的年产量变化趋势,同时也反映出武钢炼铁技术日趋成熟,管理水平逐渐提高。
图3.2反映了随着煤比的增加,焦比逐渐降低,炼铁生产的单位成本也相应减少。
表3.1 5号高炉投产以来部分经济技术指标指标1994199519961997199819992000200120022003产量/万t 213.2 192.2 183.5 233.0 245.2 241.9 245.4 249.7 259.0 248.1利用系数/t·m-3·d-1入炉焦比/kg·t-1471.6 478.0 478.5 429.1 412.8 405.9 398.7 396.1 386.7 376.2煤比/ kg·t-177.9 82.8 79.5 99.5 108.2 120.0 122.1 123.3 124.1 136.2 风量/m-3·min-15902 6001 5313 6133 6224 6274 6283 6285 6367 6138风温/℃1130 1133 1075 1136 1130 1125 1102 1104 1107 1104风速/m·s-1211 228 212 213 214 234 236 237 239 236矿品位/%孰料率/%煤气CO2/% 18.3 18.4 17.6 19.4 19.3 19.2 19.0 18.8 18.8 18.8 休风率/%炉渣碱度焦负荷/(t·t-1) 28 5 1综合冶强/t·m-3·d-1顶压/MPa富氧率/% 9表3.2 5号高炉近几年创造的相关纪录项目纪录单位时间焦炭原料纪录(%)利用系数t/m3•d2009年2月灰分入炉焦比299 kg/t 2009年1月M40 82.7煤比190.7 kg/t 2006年8月M10燃料比458.4 kg/t 2006年10月图3.1 5号高炉年生铁产量趋势图图3.2 5号高炉入炉焦比、煤比趋势图4 炼铁生产主要技术措施武钢5号高炉通过采取一系列措施:优化高炉设计与炉料结构,提高入炉原燃料质量,选择合适的高炉内衬、改良炉底结构与材质,注重开炉前的基础工作与开炉初期的长寿准备,加适量的钒钛矿护炉,开发冷却壁垂直水冷管修补换新技术,维护好炉体与冷却壁,选择合理的装料制度与风口布局,强化软水密闭循环冷却系统的日常管理等,实现了高炉强化冶炼与长寿生产。
4.1 贯彻精料方针,改善炉料质量(1)优化配矿结构、提高入炉料品位与熟料率5号高炉所用的烧结矿含铁量逐步提高到58%左右;1993年开始使用进口球团矿,此后球团配比几经变化,但总的趋势是增加的。
2002年7月开始,进口球团矿的配比由原来的16%提高到24%,最高用至27 ;2001年、2002年、2003年高炉年均入炉品位分别达到、、。
熟料率也从开炉期的80%左右增加到2003年的90%,入炉料的物化冶金性能也有了较明显的改善。
(2)强化筛分、减少入炉粉末原燃料粉末多,不仅不利炉况顺行,同时粉末易向炉墙边缘偏聚,随高速煤气流上升,炉墙容易被冲蚀,对长寿构成负面影响。
烧结矿的筛由2001年以前单层“人字”式椭圆形筛网逐步更换为“梳齿”形筛网,接着改为筛分效率更高的振打式棒条筛,入炉粉末进一步降低,基本控制在以内,高炉料柱的透气性得到了有效改善。
(3)增加球团矿比例,改善炉料结构。
长期以来,武钢高炉的炉料结构由75%烧结矿和25%块矿(其中有15%为进口矿)组成,熟料率比国内其他厂低10~15%,为了改善炉科结构,技术人员不断提高球团矿配比,最高时达25%。