SMT印制电路板的可制造性设计与审核
SMT印制电路板设计常见问题及解决方法
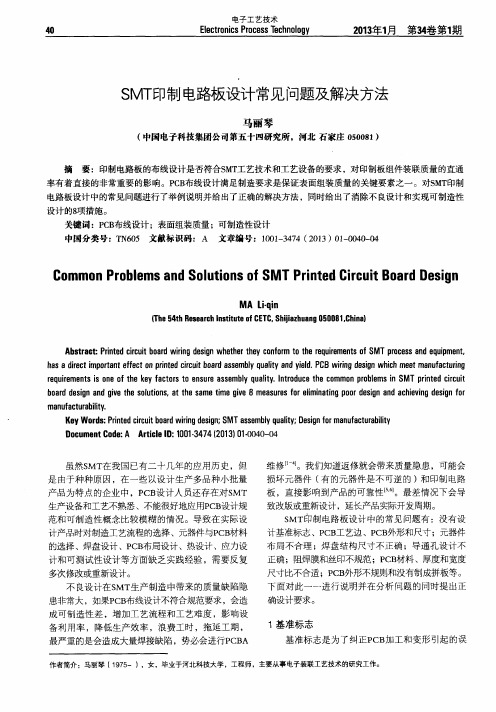
( T h e 5 4 t h R e s e a r c h I n s t i t u t e o f C E T C , S h i j i a z h u a n g 0 5 0 0 8 1 , C h i n a l
A b s t r a c t : P r i n t e d c i r c u i t b o a r d wi r i n g d e s i g n wh e t h e r t h e y c o n f o r m t o t h e r e q u i r e me n t s o f S MT p r o c e s s a n d e q u i p m e n t ,
致改版或重新设计 ,延长产品实际开发周期。 s MT印制 电路 板设计 中的常 见 问题有 :没有 设 计基准标 志 、P C B 工艺边 、P C B  ̄ b 形和尺寸 ;元器件 布 局不合 理 ;焊盘 结构尺寸 不正确 ;导通 孔设 计不
计和可测试性设计等方面缺乏实践经验 ,需要反复
设计 的8 项措施 。
关键词 :P C B 布线设计 ;表 面组装质量 ;可制造性设计 中国分类号 :T N 6 0 5 文献标识码 :A 文章编号 :1 0 0 1 — 3 4 7 4( 2 0 1 3 )0 1 — 0 0 4 0 — 0 4
C o mmo n P r o b l e ms a n d S o l u t i o n s o f S MT P r i n t e d C i r c u i t B o a r d D e s i g n
D o c u me n t C o d e : A A r t i c l e I D : 1 O 0 1 , 3 4 7 4( 2 0 1 3 ) 0 1 . 0 0 4 0 — 0 4
SMT印制板设计规范

SMT印制板设计规范SMT(Surface Mount Technology)印制板设计规范是关于电子产品印制板设计的一系列要求和准则,旨在确保PCB(Printed Circuit Board)的制造过程能够顺利进行,并最终得到高质量的印制板产品。
下面是一些SMT印制板设计规范的重要内容。
1.印制板尺寸和布局:-确定印制板的实际尺寸,包括长度、宽度和厚度,并在设计中使用正确的尺寸参数。
-设计合理的布局,确保所有元件和走线的正确安装和连通,以提高印制板的性能和可靠性。
2.元件安装规范:-元件安装应遵循适当的引脚布局,确保元件安装在正确的位置并正确连接。
-元件的排列应便于制造和维修,并保证元件之间的足够间距和空间。
3.安装孔和固定装置:-印制板上的孔和固定装置应符合标准尺寸和设计规范,并确保能够正确安装印制板。
-孔的位置和尺寸应准确,以确保印制板和配件之间的稳定连接。
4.线宽和间距:-确定正确的线宽和间距参数,以提供足够的电流传输能力,并避免线路之间的干扰或短路。
-确保线宽和间距符合制造商的要求和能力,并能满足所需的电子器件和电流要求。
5.反焊和覆盖层:-在印制板上使用适当的反焊材料,以便在组装过程中保护印制电路和焊点,并提供良好的可焊性。
-配置适当的覆盖层,以保护印制板免受外部环境的影响,并提供适当的绝缘和防护。
6.引脚和焊盘:-准确标记元件引脚的位置和方向,确保正确的引脚连接和组装。
-焊盘的尺寸和形状应适合所使用的元件,并提供良好的焊接质量和可靠性。
7.电源分离和地面规范:-正确的电源分离和地面规范是确保印制电路的稳定性和性能的重要因素。
-确定正确的分离点和连接方式,以确保电源的稳定和地面的良好连接。
8.文件和制造要求:-提供准确和详细的PCB设计文件,包括图纸、尺寸和布局等信息,以供制造商参考。
-了解制造商的要求,并根据实际制造要求进行设计和调整。
总之,遵守SMT印制板设计规范对于确保PCB的制造质量和性能至关重要。
SMT DFM(可制造性设计)检查表

文件编号:LCT-PC-All-QD一、产品基本信息□研发阶段□中试阶段□量产阶段二、SMT技术资料三、PCB制造工艺要求(一)PCB 设计3、PCB之工艺边:定位孔A、定位孔直径(∮=3~4mm);B、定位孔距离板角坐标:X=5mm,Y=5mm。
C、PCB四边均需要工艺边框,其中2个长边宽度应大于8mm以上,短边应大于3mm以上。
D、PCB板顶角成圆弧形。
□□□1、PCB之工艺边定位孔:Ph ilips FCM高速贴装机Carrier传动结构特殊要求。
2、见图示(一)。
4、PCB小板:夹具孔周边1mm内不允许有元器件,以免与夹具干涉。
□□□1、PCB小板夹具孔:通用要求。
2、见图示(一)。
5、PCB焊盘、通孔设计A、同一元件Pad形状、面积要相同;与材料管脚规格匹配。
B、焊盘相邻边间隙要求大于8Mil;若无法达到8Mil,则不能小于6Mil(且须在Gerber文件中指出其位置)。
C、PCB上通孔(via hole)需要密封。
D、Pad上via尽可能小,且必须全部密封。
E、零件间距不会造成放置时互相干涉。
F、BGA焊盘间面积要相等;焊盘上通孔(via hole)尽可能引至边缘或焊盘外。
□□□1、间隙太小,仅0.1mm。
2、间隙要大于8Mil(0.2mm)。
1、BGA焊盘面积不相同。
2、焊盘上通孔移至边缘或焊四、SMT制程控制要求4.1. 锡膏管控1、锡膏选择。
2、运输、存放。
3、生产使用管制。
4.2. 钢板及刮刀、治具管控4.3. 元件选择4.4. 材料Profile 参数设定1、 Profile 量测位置选取原则:大组件、BGA 、QFP 、屏蔽盖内等。
2、 Profile 参数:1) 有铅: 峰值温度为215℃~225℃;179℃~183℃回流时间60~90 S ;上升斜率<3℃/ S 。
2) 局部无铅:Peak 为225℃~230℃;220℃以上30~40S ;回流时间80~110S 。
SMT贴片流程及可制造性
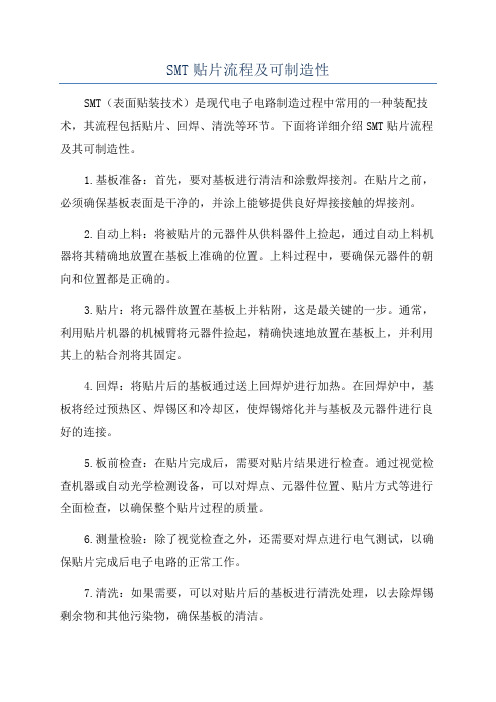
SMT贴片流程及可制造性SMT(表面贴装技术)是现代电子电路制造过程中常用的一种装配技术,其流程包括贴片、回焊、清洗等环节。
下面将详细介绍SMT贴片流程及其可制造性。
1.基板准备:首先,要对基板进行清洁和涂敷焊接剂。
在贴片之前,必须确保基板表面是干净的,并涂上能够提供良好焊接接触的焊接剂。
2.自动上料:将被贴片的元器件从供料器件上捡起,通过自动上料机器将其精确地放置在基板上准确的位置。
上料过程中,要确保元器件的朝向和位置都是正确的。
3.贴片:将元器件放置在基板上并粘附,这是最关键的一步。
通常,利用贴片机器的机械臂将元器件捡起,精确快速地放置在基板上,并利用其上的粘合剂将其固定。
4.回焊:将贴片后的基板通过送上回焊炉进行加热。
在回焊炉中,基板将经过预热区、焊锡区和冷却区,使焊锡熔化并与基板及元器件进行良好的连接。
5.板前检查:在贴片完成后,需要对贴片结果进行检查。
通过视觉检查机器或自动光学检测设备,可以对焊点、元器件位置、贴片方式等进行全面检查,以确保整个贴片过程的质量。
6.测量检验:除了视觉检查之外,还需要对焊点进行电气测试,以确保贴片完成后电子电路的正常工作。
7.清洗:如果需要,可以对贴片后的基板进行清洗处理,以去除焊锡剩余物和其他污染物,确保基板的清洁。
1.元器件封装:不同的元器件封装形式对贴片工艺的要求不同。
例如,表面贴装元器件(SMD)和裸露芯片元器件(BGA)的封装形式对焊接技术和贴片机的要求不同,需要根据不同封装形式进行不同的工艺调整。
2.设计规范:良好的设计规范对贴片工艺的可制造性至关重要。
例如,元器件的布局和间距、组件的定位标记、焊盘和针孔的设计等都需要满足贴片机的要求,以确保贴片的精确度和质量。
3.设备能力:贴片机的性能和能力对贴片工艺的可制造性具有重要影响。
例如,贴片机的速度、精度和稳定性都需要满足生产要求,以确保贴片的质量和效率。
4.材料选择:选择适合贴片工艺的材料也是关键因素。
SMT与AI可制造性标准20101209

须考虑机器轨
5 2、PCB 的 BOT 面上,焊盘至“非轨道便”距离要求:(仅针对双面回流 PCB)
道传输和装夹
定位所要求的 工 元件离板边的 艺
最小距离,必要 组
说明:PCB 下板,所有需印刷锡膏的元件、焊盘等,至“非轨道边”距离要求大于 5.0MM;
序 列
项目
1.1 SMT 可生产 PCB 尺寸要求(如图 A1.1)(依据 SMT 车间机器性能要求) 1、点胶制程(单层板)PCB 的可生产尺寸范围: 最小极限尺寸:X 方向:50MM Y 方向:55MM 最大极限尺寸:X 方向:410MM Y 方向:360MM 2、锡膏制程(多层板)PCB 的可生产尺寸范围: 最小极限尺寸:X 方向:80MM Y 方向:55MM 最大极限尺寸:X 方向:450MM Y 方向:350MM 3、SMT 推荐的 POWRE 板、LCD 主板及 TV 主板尺寸范围:
1、板材的使用应和制程相对应 说明:
边缘有毛刺易 工
造成机器轨道 艺
送板不顺畅或 轨道卡板
组
1) SMT 不同的回流焊制程,其焊接温度不一样,无铅(峰值温度:235-250℃)、点胶(固 化温度 120℃)。
2) 不同板材的 PCB,其耐焊接热性能不一样,这与不同板材 TG 点有关,FR-1 纸基板的 TG 点只有 80℃左右,二 FR-4 玻璃布基板 TG 点位 125℃。因此,为防止 PCB 板砖焊接 过程中产生是产生较大的热应点和变形,选择电子产品的 PCB 集采时应综合成本和性能
<100
≤1.5 ≤2.0 ≤2.5
≤3.0
100-200 ≤1.5 ≤2.5 ≤3.5
SMT与DFM汇总

• (4) 元器件布局不合理
•
a 没有按照再流焊要求设计,再流焊时造成温度不均匀。
• b 没有按照波峰焊要求设计,波峰焊时造成阴影效应。
• (5) 基准标志(Mark)、PCB外形和尺寸、PCB定位孔和夹持边的设 置不正确 • a 基准标志(Mark)做在大地的网格上,或Mark图形周围有阻焊
—印制板电路设计——————测试点
—可靠性设计
—降低生产成本
—焊盘与导线的连接
—阻焊 —散热、电磁干扰等
•
可制造性设计DFM(Design For Manufacture)
是保证PCB设计质量的最有效的方法。DFM就是从产
品开发设计时起,就考虑到可制造性和可测试性,
使设计和制造之间紧密联系,实现从设计到制造一
• → 首批投料
→ 小批试生产
→ 正式投产
传统的设计方法与现代设计方法比较
• •
•
传统的设计方法
串行设计
重新设计 1#
重新设计 n#
生产
•
现代设计方法
并行设计CE 及DFM 重新设计 1# 生产
• •
•
SMT工艺与传统插装工艺有很大区别,对PCB 设计有专门要求。除了满足电性能、机械结构、 等常规要求外,还要满足SMT自动印刷、自动贴装、 自动焊接、自动检测要求。特别要满足再流焊工 艺的再流动和自定位效应的工艺特点要求。 • SMT具有全自动、高速度、高效益的特点,不 同厂家的生产设备对PCB的形状、尺寸、夹持边、
定位孔、基准标志图形的设置等有不同的规定。
•
不正确的设计不仅会导致组装质量下降,还会造成贴
装困难、频繁停机,影响自动化生产设备正常运行,影响
贴装效率,增加返修率,直接影响产品质量、产量和加工
SMT印制板可制造性设计(工艺性)审核
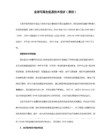
3.4 是否符合SMT工艺对PCB设计的要求
a. 基板材料、元器件及元器件包装的选用是否符合要求;
b. 焊盘(形状、尺寸、间距)是否符合DFM规范;
c. 引线宽度、形状、间距、引线与焊盘的连接是否符合要求;
d. 元器件整体布局、元器件之间最小间距是否符合要求,大器件周围是否考虑了返修尺寸;
(2)为了要满足SMT自动贴装、自动检测的要求
SMT具有全自动、高速度、高效益的特点,不同厂家的生产设备对PCB的形状、尺寸、夹持边、定位孔、基准标志图形设置等有不同的规定,如果设计不正确会导致组装质量下降,会造成贴装困难、频繁停机,影响自动化生产设备正常运行,影响贴装效率;增加返修率,直接影响产品质量和成品率,严重时还会造成印制板报废等质量事故。
e. 再流焊面元器件排布方向是否符合要求;
f. 波峰焊时元器件排布方向是否符合要求;
g. 插装元器件的孔径、焊盘设计是否符合DFM规范;
h. 元器件的极性排列方向是否尽量一致;
i. 阻焊膜及丝网图形是否正确,元件极性与IC第1脚是否标出;
j. 轴向元件插装孔跨距是否合适(或元件成形是否正确);
SMT印制板可制造性设计(工艺性)审核
1. SMT印制电路板可制造性设计审核的目的
2.审核程序
3. PCB可制造性设计审核审核内容
4. PCB可制造性设计审核标准和依据
5. PCB可制造性设计审核方法
6.完成审核后要写出审核报告
(1)为了满足SMT工艺要求
SMT工艺与传统插装工艺有很大区别,对PCB设计有专门要求。
2.审核程序
首先是设计人员自审;
然后由工艺人员逐项审核;
印制电路板可制造性设计审核要点

A面 混 装 B 一 面 既 装 S D 又 装 有 T C M, H 面 仅 贴 简 单 另 二 次 回 流 焊加 一 次 面 仅 装 有 C i 元 h p类 波 峰 焊
一
足够的机械 强度 , 能够承受 组装工 艺中的热处 理和冲击 , 足够 的平整度 以适合 自动化的组装工艺 , 能承受多次的返修 ( 接) 焊
技术市场
印制 电路板 可 制造 性设 计 审核要 点
管 良梅 张卫 民 吕文 锋
( 国电南瑞科技 股份有 限公 司, 江苏 南京 2 6 ) 1 0 1 0 【 摘 要】印制 电路板可 制造性设计 (F ) DM 是提 高加工质 量、 高生产效率 、 高电子产品可靠性 、 提 提 降低 成本 的重要措施。 述 叙
等 。 有 能力 的情 况 下 , 计 人 员 应 该 尽 量 做 到 以 下 的布 局 法 : 在 设 对 于 背 景有 较 高 的反 差 。 光 学 定 位 基 准 中 心 3m以l 要 设 在 m 内不 错 。一 般 采 用 直 径 1 5m的实 心 圆 焊 盘 作 为光 学基 准 。光 学 定 .m
称为 D M 印制板详细 阶段设计完成后, F。 设计者按 以下条 目进行
一
次全面的 自我审查非常必要 , 有助于减少一些显而 易见 的问
基 板 的 选 择
题 , 艺 工 程 人 员 进 行 复 审将 尽 可 能地 提 高 设 计 质 量 。 工
一
S D 又有 T C M, H
、
基板 的作用 , 了提供 组装所需 的架构外 , 除 也提供 电源和
工 作 , 合 P B的制 造 工 艺 , 适 C 良好 的 电气 性 能 ( 阻 抗 、 质 常 如 介
pcb可制造性设计与smt工艺技术
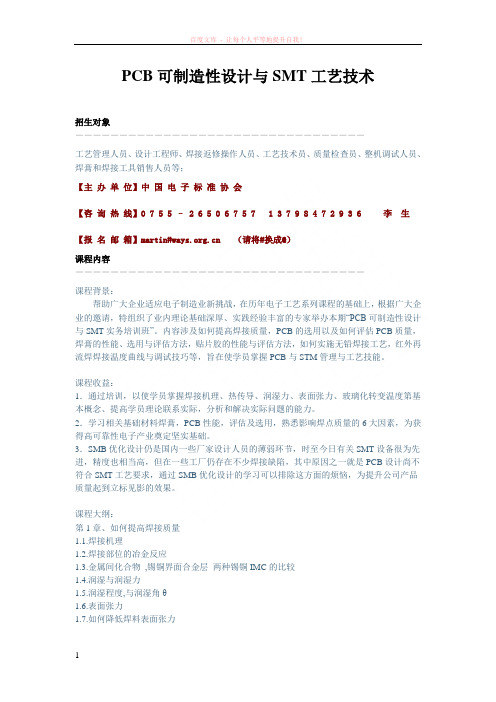
PCB可制造性设计与SMT工艺技术招生对象---------------------------------工艺管理人员、设计工程师、焊接返修操作人员、工艺技术员、质量检查员、整机调试人员、焊膏和焊接工具销售人员等;【主办单位】中国电子标准协会【咨询热线】0 7 5 5 – 2 6 5 0 6 7 5 7 1 3 7 9 8 4 7 2 9 3 6 李生【报名邮箱】martin# (请将#换成@)课程内容---------------------------------课程背景:帮助广大企业适应电子制造业新挑战,在历年电子工艺系列课程的基础上,根据广大企业的邀请,特组织了业内理论基础深厚、实践经验丰富的专家举办本期“PCB可制造性设计与SMT实务培训班”。
内容涉及如何提高焊接质量,PCB的选用以及如何评估PCB质量,焊膏的性能、选用与评估方法,贴片胶的性能与评估方法,如何实施无铅焊接工艺,红外再流焊焊接温度曲线与调试技巧等,旨在使学员掌握PCB与STM管理与工艺技能。
课程收益:1.通过培训,以使学员掌握焊接机理、热传导、润湿力、表面张力、玻璃化转变温度第基本概念、提高学员理论联系实际,分析和解决实际问题的能力。
2.学习相关基础材料焊膏,PCB性能,评估及选用,熟悉影响焊点质量的6大因素,为获得高可靠性电子产业奠定坚实基础。
3.SMB优化设计仍是国内一些厂家设计人员的薄弱环节,时至今日有关SMT设备很为先进,精度也相当高,但在一些工厂仍存在不少焊接缺陷,其中原因之一就是PCB设计尚不符合SMT工艺要求,通过SMB优化设计的学习可以排除这方面的烦恼,为提升公司产品质量起到立标见影的效果。
课程大纲:第1章、如何提高焊接质量1.1.焊接机理1.2.焊接部位的冶金反应1.3.金属间化合物,锡铜界面合金层两种锡铜IMC的比较1.4.润湿与润湿力1.5.润湿程度,与润湿角θ1.6.表面张力1.7.如何降低焊料表面张力1.8.润湿程度的目测评估,什么是优良的焊点第2章、PCB的选用以及如何评估PCB质量?2.1.PCB基材的结构2.2.有机基材的种类2.3.复合基CCL2.4.高频板,微波板2.5.评估印制板质量的相关参数2.5.1.PCB不应含有PBB和PBDE2.5.2.PCB的耐热性评估①.玻璃态、皮革态、Tg、②.Td、③.T260、T288、T300④.CET、Z轴CTE、α1-CTE、α2-CTE、2.6.无铅焊接中SMB焊盘的涂镀层①.热风整平工艺(HASL)②.涂覆Ni/Au工艺③.浸Ag(I—Ag)工艺④.浸Sn(I—Sn)工艺⑤.OSP/HT-OSP第3章、锡膏的性能、选用与评估3.1.锡膏成分与作用3.1.1.合金粉的技术要求3.1.2.焊剂的技术要求3.1.3.焊锡膏的流变行为黏度、牛顿流体、非牛顿流体、触变性3.2 焊锡膏的评价3.3.几种常见的焊锡膏、无铅焊锡膏第4章、贴片胶的性能与评估4.1.贴片胶的工艺要求4.2.贴片胶种类①.环氧型贴片胶,②.丙烯酸类贴片胶4.3.贴片胶的流变行为4.4.影响黏度的相关因素4.5贴片胶的力学行为4.6.贴片胶的评估4.7.点胶工艺中常见的缺陷第5章、红外再流焊焊接温度曲线与调试①.RTR型红外再流焊接温度曲线解析②.各个温区的温度以及停留时间④.不同PCB焊盘涂层峰值温度需适当调整③.SN63峰值温度为何是215-230℃?⑤.直接升温式红外再流焊焊接温度曲线⑥.焊接工艺窗口⑦.新炉子如何做温度曲线⑧.常见有缺陷的温度曲线第6章、如何实施无铅焊接工艺①.元器件应能适应无铅工艺的要求a.电子元器件的无铅化标识b.引线框架的功能与无铅镀层②无铅工艺对PCB耐热要求③应选好无铅锡膏④无铅再流焊工艺中PCB设计注意事项⑤无铅锡膏印刷模板窗口的设计⑥贴片工艺⑦焊接工艺⑧氮气再流焊⑨为什么无铅焊点不光亮SnPb焊料焊接无铅BGA第7章、为什么无铅焊料尚存在这么多的缺陷、如何改进?①.无Pb焊料尚存在的缺点②.焊料元素在元素周期表中的位置③.元素周期表—物质的“基因图谱”④.无铅焊料中添加微量稀土金属⑤.使用低Ag焊料⑥.Sn0.7CuNi+Ge第8章、PCB可靠性设计1.常见的焊盘设计缺陷2.为什会岀现会岀现这些缺陷3.SMT焊接特点.4.电子产品的板级热设计5.QFN散热设计6.PCB空面积的散热设计,7.焊点的隔热性设计8.工艺边,基准点,拼板9.S0C焊盘设计要求10.QFP焊盘设计要求11.PLCC焊盘设计要求12.BGA焊盘设计要求第9章.焊点检验中如何选用X光机?1.X射线产生及的基本特性2.什么是闭管?什么是开管?各有何特点3.X光机结构4.选用X光机的相关参数第10章BGA常见焊接缺陷分析(案例)10.1 BGA常见焊接缺陷电镜图10.2.虚焊产生原因及处理办法10.3.立碑产生原因及处理办法10.4.焊球产生原因及处理办。
DFM-checklist-for-SMT

3 TUBE(支装) 不允许 不允许
不允许
Yes
No
N/A
Yes
No
N/A
19
ME
Mark点不能放于夹板边,且mark点中心露铜需离开上下板边外沿 5mm以上。
Yes
No
N/A
Mark点能良好地识别,形状规则,表面平整,直径d=1.2mm,且有周
20
EE
围有一圈直径大于2.5mm的完整空旷区,无绿油区离板边1mm, Mark点周围5mm内无相似尺寸的方块或圆干扰;需考虑线上所有设
17
EE
带半圆孔贴片焊盘的(模块PCB),选用FR4+沉金工艺( Tg≧170 ℃),其它的表面处理工艺不推荐选用;
需要考虑ESD静电泄放要求的PCB(如SD卡等等),可以考虑沉金
工艺。(来源:SQM主导的 定制件质量管理及系统精益供应链)
18
元件的包装首选卷装,次选硬质盘装(常用220*330,120*300≤a PP ≤230*330),外包装不能接受纸制,不能使用支装,如果不满足
BGA、IC等器件极性、丝印标识与器件封装一致、不错位,丝印字
迹清晰。
16
EE PCB上的细小通孔用绿油填塞,不允许漏白光。
Yes
No
N/A
Yes
No
N/A
Yes
No
N/A
Yes
No
N/A
带BGA板采用FR4+沉金工艺(Tg≧150℃),其次考虑用FR4+沉锡工艺
( Tg≧150℃);其它普通板可以考虑OSP。
PCB供应商制作时需要使用锣板方式,PCB 外观一致性好,无毛刺
、四周光滑;阻焊层、绿漆均匀,无脱落或剥离现象。
印制电路板可制造性设计规范共11页word资料

1范围1.1主题内容本标准规定了电子产品中印制电路板设计时应遵循的基本要求。
1.2适用范围本标准适用于以环氧玻璃布层压板为基板的表面组装印制板设计,采用其它材料为基板的设计也可参照使用。
2引用标准GB 2036-94 印制电路术语GB 3375-82 焊接名词术语SJ/T 10668-1995 表面组装技术术语SJ/T 10669-1995 表面组装元器件可焊性试验Q/DG 72-2019 PCB设计规范3定义3.1术语本标准采用GB 3375、GB2036、SJ/T 10668定义的术语。
3.2缩写词a. SMC/SMD(Surface mounted components/ Surface mounted devices):表面组装元器件;b. SMT(Surface mounted technology):表面组装技术;c. SOP(Small outline package):小外形封装,两侧具有翼形或J形短引线的一种表面组装元器件封装形式;d. SOT(Small outline transistor):小外形晶体管;e. PLCC(Plastic leaded chip carrier):塑封有引线芯片载体,四边具有J形短引线,典型引线间距为1.27mm,采用塑料封装的芯片载体,外形有正方和矩形两种形式f.;QFP(Quad flat package):四边扁平封装,四边具有翼形短引线,引线间距为1.00mm,0.80mm,0.65mm,0.50mm,0.30mm等;g. DIP (Dual in-line package):双列直插式封装h.;BQFP (QFP with buffer):带缓冲垫封装的Q FP;i. PCB (Printed circuit board):印制板。
J.BGA(Ball Grid Array):球形栅格列阵4一般要求4.1印制电路板的尺寸厚度4.1.1印制板最小尺寸L×W为80mm×70mm,最大尺寸L×W为457mm×407mm4.1.2印制板厚度一般为0.8~2.0mm。
2-SMT印制板DFM设计及审核

A面施加焊膏 翻转PCB
贴装SMD
再流焊
A B
B面施加贴装胶
翻转PCB A面插装THC
贴装SMD
胶固化
B面波峰焊
B面插装件后附。
1.3 选择表面贴装工艺流程应考虑的因素
1.3.1 尽量采用再流焊方式,再流焊比波峰焊具有以下优越性; (1)元器件受到的热冲击小。 (2)能控制焊料量,焊接缺陷少,焊接质量好,可靠性高;
(3)焊料中一般不会混入不纯物,能正确地保证焊料的组分;
• 有自定位效应(self alignment)
(4)可在同一基板上,采用不同焊接工艺进行焊接;
(5)工艺简单,修板量极小。从而节省了人力、电力、材料。
1.3.2 一般密度的混合组装时
• 尽量选择插装元件、贴片元件在同一面。
波峰焊工艺;(必须双面板) • 当THC在PCB的A面、SMD 在PCB的B面时,采用B面点胶、波峰焊工 艺。(单面板)
3. 增加工艺流程,浪费材料、浪费能源。
4. 返修可能会损坏元器件和印制板。
5. 返修后影响产品的可靠性
6. 造成可制造性差,增加工艺难度,影响设备利用率,
降低生产效率。
7.最严重时由于无法实施生产需要重新设计,导致整个 产品的实际开发时间延长,失去市场竞争的机会。
二. 目前国内SMT印制电路板设计中的
b 导轨传输时,由于PCB外形异形、PCB尺寸过大、过小、或由 于PCB定位孔不标准,造成无法上板,无法实施机器贴片操作。
c 在定位孔和夹持边附近布放了元器件,只能采用人工补贴。
d 拼板槽和缺口附近的元器件布放不正确,裁板时造成损坏元器 件。
(6) PCB材料选择、PCB厚度与长度、宽度尺寸比不合适
表面组装技术SMT及印制板可制造性设计

SMT(Surface Mount Technology,表面组装技术)是一种将电子元件直接贴装在印 制板表面上的组装技术。它通过使用小型化的封装和精细的焊盘,实现了电子元件与印 制板之间的微型化连接。SMT具有高密度、高可靠性的特点,能够大幅度提高电子产
品的性能和稳定性。
SMT的发展历程
04
CATALOGUE
SMT质量与可靠性
SMT质量检测
01
02
03
检测方法
通过目视检查、X射线检 测、自动光学检测等方法 对SMT贴片质量进行检测 。
检测内容
检查焊点质量、元件位置 精度、焊盘完整性等,确 保贴片符合工艺要求。
检测标准
依据IPC标准(国际电子 工业联合会标准)进行检 测,确保产品符合行业标 准。
无铅焊接技术
随着环保意识的增强,无 铅焊接技术将逐渐取代传 统含铅焊接技术,降低环 境污染。
微型化组件应用
随着电子设备小型化趋势 ,微型化组件在SMT中应 用将更加广泛,提高组装 密度。
SMT与其它制造技术的结合
SMT与激光技术结合
利用激光技术进行精确打标、切割和焊接,提高生产效率和精度 。
SMT与机械加工技术结合
选用符合标准的元件、焊料和基材,确保 产品质量。
加强过程控制
培训与提高
建立严格的生产过程控制体系,确保每个 环节的质量稳定。
对操作人员进行定期培训,提高其技能水 平,确保生产质量。
05
CATALOGUE
SMT未来发展趋势
新型SMT技术
3D-SMT
通过在多层印制板上实施 表面组装,实现立体集成 ,提高组装密度和可靠性 。
智能检测与监控
利用传感器和机器视觉技术对SMT生 产过程进行实时检测和监控,确保产 品质量。
SMT印制电路板的可制造性设计及审核

SMT印制电路板的可制造性设计及审核一、引言1.背景介绍在电子产品制造过程中,可制造性设计及审核是确保电路板能够高效、精确地完成组装的重要环节。
特别是对于SMT印制电路板而言,设计人员需要考虑许多因素,以确保电路板的可制造性和品质。
2.目的和重要性本文的目的是介绍SMT印制电路板的可制造性设计及审核,以帮助设计人员了解如何进行合理设计和审核,提高产品的制造效率和品质。
二、可制造性设计原则1.布局设计原则合理的布局设计能够提高组装过程的效率,减少错误和修正的机会。
设计人员应尽量考虑以下原则:-分组布局:将相似的元件归为一组,减少线路走线的复杂度。
-元件位置:考虑元件的尺寸和位置,确保组装工人容易识别和安装。
-连接器布局:合理选择连接器位置,以方便连接和维护。
2.走线设计原则良好的走线设计可以减少电路板上的噪声干扰、交叉干扰等问题。
设计人员应考虑以下原则:-信号通道与电源通道分离:避免信号与电源干扰,使用地线隔离。
-差分线对称布局:减少差分线长度不平衡引起的问题。
-黄金分割比例:在走线时考虑几何比例。
三、可制造性审核方法1.设计规范检查在设计阶段,可以根据工厂的制程要求和标准对电路板进行设计规范检查,以确保设计满足制程要求。
2.DFM分析DFM(Design for Manufacturability)分析是对设计进行全方位的可制造性分析,主要包括以下内容:-元件封装选型:选用适合的SMT封装,避免占用过多空间和复杂的组装工艺。
-元件位置布局:考虑元件之间的电路连接,减少走线复杂度。
-宽度和间距要求:考虑电路板的制造限制,设定合适的宽度和间距。
3.信号完整性分析在测试阶段,可以进行信号完整性分析,以确保设计满足信号传输和抗干扰的要求。
四、结论本文介绍了SMT印制电路板的可制造性设计及审核的相关内容。
通过合理的布局设计和走线设计,可以提高制造效率和品质。
同时,通过设计规范检查、DFM分析和信号完整性分析等方法,可以确保设计满足制程要求和信号传输要求。
SMT组装中的实用可制造性设计

D M设计修 改请 求程 序等。 F
T e c u s s amig t r vd y t mai riig o M ( sg o n f c u a _ V n SMT h o r e i i n o p o ie a s s e t tann n DF c De in f r Ma u a t rb l )i i t
维普资讯
_中国 电子专用设备 工业协 会 _ 美 国S A MT 深圳办事处
大 力发展面 向 “ 世界工厂 ’ ’的职业教育和培训
Sr _r V 组装中的实用可制造性设计
前 言 本课 程就S 的 可制造 性 设计 ( M ) 行 系统培 训 ,使 受训 者 掌握 用 经济 有效 的方法 ,设计 出多 MT DF 进
maa e S rc s n ie r n e h ia DF s e ilt maei rjc n g r CBd sg e n g r MT po ese gn e dtc nc n a i t M p c i t tr l oe tma a e P e in r as ap
F coy e gn e i n g rfco p rt n ma a e , rjc p r in ma a e, rd c rga at r n i r g ma a e, a t r o eai n g r po to ea o n g r po u tpo rm e n y o e t
a s m by n o d rt u e c s fe t e m e h d o a he e m a u a t be d sg i e t rq ai , se l i r e o s o t e f c i t o s t c iv v n f c ua l e in w t b te u ly r h t q ik i e o uc er m —t —m a k t o e b ra d m ae il o ta d s o t h o g p tt e W i on iu u M t re lw rl o n t r s n h r t r u hБайду номын сангаасu i . t c t o s DF a ac er m h n
印制电路板可制造性设计技术要求

科成公司印制板可制造性设计技术要求本要求涉及了单双面、多层印制电路板可制造性设计的通用技术要求,包括材料、尺寸和公差叠层、印制导线和焊盘、金属化孔、导通孔、安装孔、镀层、涂敷层、字符和标记等。
作为印制板设计人员设计单双、多层面板时参考:1 一般要求1.1 本标准作为PCB设计的通用要求,规范PCB设计和制造,实现CAD与CAM的有效沟通。
1.2 我公司在文件处理时优先以设计图纸和文件作为生产依据。
1.3 可接收文件格式为:PROTEL系类(优先)、PADS系列、autocad系列、gerber文件。
2 PCB材料2.1 基材PCB的基材一般采用环氧玻璃布覆铜板,即FR4。
2.2 铜箔双层板成品表面铜箔厚度≥18µm(0.5OZ);有特殊要求时,在图样或文件中指明。
3 PCB结构、尺寸、公差和叠层3.1 结构a)构成PCB的各有关设计要素应在设计图样中描述。
外型应统一用Mechanical 1 layer (优先)或Keep out layer 表示。
若在设计文件中同时使用,一般keep out layer 用来屏蔽,不开孔,而用mechanical 1表示成形。
b)在设计图样中表示开不金属化槽的,用Mechanical 1 layer 画出相应的形状即可。
3.3 外形尺寸公差PCB外形尺寸应符合设计图样的规定。
当图样没有规定时,外形尺寸公差为±0.2mm。
(V-CUT产品除外)3.4 平面度(翘曲度)公差3.5多层叠层多层板应在附件中标注明叠层方式,不标注的我公司按PCB设计叠层加工。
用户提供GERBER制版的必须标明叠层,否则无法加工。
4 印制导线和焊盘4.1 布局a)印制导线和焊盘的布局、线宽和线距等原则上按设计图样的规定。
但我公司会有以下处理:适当根据工艺要求对线宽、PAD环宽进行补偿,单面板一般我公司将尽量加大PAD,以加强客户焊接的可靠性。
b)当设计线间距达不到工艺要求时(太密可能影响到性能、可制造性时),我公司根据制前设计规范适当调整。
- 1、下载文档前请自行甄别文档内容的完整性,平台不提供额外的编辑、内容补充、找答案等附加服务。
- 2、"仅部分预览"的文档,不可在线预览部分如存在完整性等问题,可反馈申请退款(可完整预览的文档不适用该条件!)。
- 3、如文档侵犯您的权益,请联系客服反馈,我们会尽快为您处理(人工客服工作时间:9:00-18:30)。
A面再流焊,B面波峰焊工艺时, BGA的导通孔应设计盲孔
A面再流焊
B面波峰焊 由于二次熔锡 造成BGA焊点失效
(8) 元器件和元器件的包装选择不合适 由于没有按照贴装机供料器配置选购元器件和元器 件的包装,造成无法用贴装机贴装。
• 1994年SMTA首次提出DFX概念。1995年DFX是表面贴装国际会议 的主题,1996年SMTA发表了6篇相关性文章。 作为一种科学的方法,DFX将不同团队的资源组织在一起,共同 参与产品的设计和制造过程。通过发挥团队的共同作用,实现缩短 产品开发周期,提高产品质量、可靠性和客户满意度,最终缩短从 概念到客户手中的整个时间周期。
环保设计
• DFF: Design for Fabrication of the PCB PCB可加工性设计
• DFS: Design for Sourcing
物流设计
• DFR: Design for Reliability 可靠性设计
• HP公司DFM统计调查表明:产品总成本 60%取决于产品的最初设计,75%的制造成 本取决于设计说明和设计规范,70-80%的 生产缺陷是由于设计原因造成的。
一. 不良设计在SMT生产制造中的危害
1. 造成大量焊接缺陷。 2. 增加修板和返修工作量,浪费工时,延误工期。 3. 增加工艺流程,浪费材料、浪费能源。 4. 返修可能会损坏元器件和印制板。 5. 返修后影响产品的可靠性 6. 造成可制造性差,增加工艺难度,影响设备利用率,
降低生产效率。 7.最严重时由于无法实施生产需要重新设计,导致整个
• 新产品研发过程
方案设计 → 样机制作 → 产品验证 •
→ 小批试生产 → 首批投料 → 正式投产
传统的设计方法与现代设计方法比较
•
传统的设计方法
•
串行设计 重新设计 重新设计
生产
•
1#
n#
•
现代设计方法
•
•
并行设计CE 重新设计 生产
•
及DFM
1#
内容
一. 不良设计在SMT生产制造中的危害 二. 目前国内SMT印制电路板设计中的常见问题及解决措施 三. SMT工艺对PCB设计的要求 四. SMT设备对PCB设计的要求 五. 提高PCB设计质量的措施 六. SMT印制板可制造性设计(工艺性)审核 七. 产品设计人员应提交的图纸、文件 八. 外协加工SMT产品时需要提供的文件 九. IPC-7351《表面贴装设计和焊盘图形标准通用要求》简介
现代设计DFX系列介绍
• DFM: Design for Manufacturing 可制造性设计
• DFT: Design for Test
可测试性设计
• DFD: Design for Diagnosibility 可分析性设计
• DFA: Design for Aseembly
可装配性设计
• DFE: Desibn for Enviroment
b 导轨传输时,由于PCB外形异形、PCB尺寸过大、过 小、或由于PCB定位孔不标准,造成无法上板,无法实 施机器贴片操作。
c 在定位孔和夹持边附近布放了元器件,只能采用人 工补贴。
d 拼板槽和缺口附近的元器件布放不正确,裁板时造 成损坏元器件。
(6) PCB材料选择、PCB厚度与长度、宽度尺寸比不合适 a 由于PCB材料选择不合适,在贴片前就已经变形,
• DFM具有缩短开发周期、降低成本、提高产品质 量等优点,是企业产品取得成功的途械行业用于简化产品结构和减少加工成本。 • 1991年,DFM的应用对美国制造业竞争优势的形成做出贡献,美
国总统布什给创始人G.布斯劳博士和P.德赫斯特博士颁发了美国国 家技术奖。DFM很快被汽车、国防、航空、计算机、通讯、消费类 电子、医疗设备等领域的制造企业采用。
SMT印制电路板的 可制造性设计及审核
• 印制电路板(以下简称PCB)设计是表面组装技术 的重要组成之一。PCB设计质量是衡量表面组装技术水平 的一个重要标志,是保证表面组装质量的首要条件之一。
PCB设计包含的内容:
—基板材料选择
—布线
—元器件选择
—焊盘
—印制板电路设计——————测试点
PCB设计——可制造(工艺)性设计 —导线、通孔
—可靠性设计 —降低生产成本
—焊盘与导线的连接 —阻焊
—散热、电磁干扰等
• 可制造性设计DFM(Design For Manufacture) 是保证PCB设计质量的最有效的方法。DFM就是从产 品开发设计时起,就考虑到可制造性和可测试性, 使设计和制造之间紧密联系,实现从设计到制造一 次成功的目的。
制造加工精度差造成的。其结果造成虚焊或电气断路。
• (4) 元器件布局不合理 • a 没有按照再流焊要求设计,再流焊时造成温度不均匀。
• b 没有按照波峰焊要求设计,波峰焊时造成阴影效应。
(5) 基准标志(Mark)、PCB外形和尺寸、PCB定位孔和夹 持边的设置不正确
a 基准标志(Mark)做在大地的网格上,或Mark图形周 围有阻焊膜,由于图象不一致与反光造成不认Mark、 频繁停机。
产品的实际开发时间延长,失去市场竞争的机会。
二. 目前国内SMT印制电路板设计中的 常见问题及解决措施
1. PCB设计中的常见问题(举例)
(1) 焊盘结构尺寸不正确(以Chip元件为例)
a 当焊盘间距G过大或过小时,再流焊时由于元件焊端不能与焊 盘搭接交叠,会产生吊桥、移位。
•
焊盘间距G过大或过小
b 当焊盘尺寸大小不对称,或两个 元件的端头设计在同一个焊盘上时, 由于表面张力不对称,也会产生吊 桥、移位。
• (2) 通孔设计不正确
•
导通孔设计在焊盘上,焊料会从导通孔中流出,会造
成焊膏量不足。
•
不正确
•
正确 印制导线
• (3) 阻焊和丝网不规范
•
阻焊和丝网加工在焊盘上,其原因:一是设计;二是PCB
造成贴装精度下降。 b PCB厚度与长度、宽度尺寸比不合适造成贴装及再
流焊时变形,容易造成焊接缺陷,还容易损坏元器件。 特别是焊接BGA时容易造成虚焊。 • • 虚焊
(7) BGA的常见设计问题
a 焊盘尺寸不规范,过大或过小。 b 通孔设计在焊盘上,通孔没有做埋孔处理 c 焊盘与导线的连接不规范 d 没有设计阻焊或阻焊不规范。