高速切削技术及工艺新要求
高速切削关键技术

中心和其他数控机床进给系统采用 1.5 g。它在高速加工中心上的应用 速度达76.2 m/min,进给加速度达
的主要形式。滚珠丝杠副传动系统 仍受到一定的限制。
1~1.5 g。意大利Vigolzone公司生产
采用交流伺服电机驱动,进给加速
采用滚珠丝杠副传动实现的高 的高速卧式加工中心,三轴采用直
46 汽 车 工 艺 与 材 料 AT&M
高速切削机床是实现先进切削工 艺、获得高效加工效益的载体,也 是进行高速切削试验研究的平台。 高速切削的关键技术有高速切削机 理、高速加工技术、高速加工用刀
具技术、高速加工工艺技术以及高 速加工测试技术等,其中高速机床 是实现高速加工的前提和基础条 件。
1 高速主轴单元
高速主轴部件是高速机床最为关 键的部件之一,同时高速主轴单元 的设计是实现高速加工的关键技术 之一。高速主轴在离心力作用下产 生振动和变形,高速运转时产生的 摩擦热和大功率内装电机产生的热 会引起温升和热变形,将直接影响 机床最终的加工性能,因此必须对 其进行严格控制。高速主轴单元的 类型主要有电主轴、气动主轴、水 动主轴。不同类型的主轴输出功率 相差较大。高速主轴要在极短的时 间内完成升降速,并在指定的位置 快速准停,这要求主轴具有很高的 角加速度。主轴的驱动如果通过皮 带等中间环节,不仅会在高速状态 打滑、产生振动和噪声,而且增加 了转动惯量,机床主轴快速准停非 常困难。高速加工机床主轴系统在 结构上几乎都是采用交流伺服电机 直接驱动的集成结构形式。集成化 主轴有两种形式,一种是通过联轴 器把电机与主轴直接联接,另一种 是把电机转子和主轴做成一体。
蚀作用及高速紊流下气泡的产生对 20~25 μm。相对于采用直线电机 本。日本精工已经研制出进给速度
高速切削技术研究
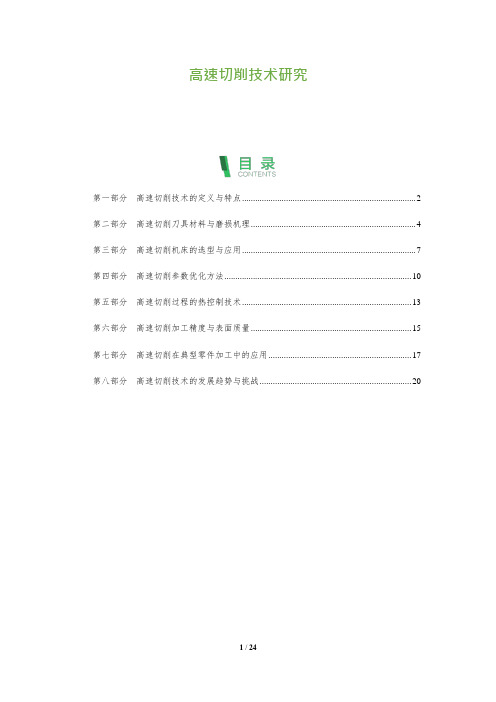
高速切削技术研究第一部分高速切削技术的定义与特点 (2)第二部分高速切削刀具材料与磨损机理 (4)第三部分高速切削机床的选型与应用 (7)第四部分高速切削参数优化方法 (10)第五部分高速切削过程的热控制技术 (13)第六部分高速切削加工精度与表面质量 (15)第七部分高速切削在典型零件加工中的应用 (17)第八部分高速切削技术的发展趋势与挑战 (20)第一部分高速切削技术的定义与特点高速切削技术是一种先进的制造工艺,它通过使用高转速的刀具和优化的切削参数来提高材料去除率、加工精度和表面质量。
该技术的核心在于实现高效率、高质量和高精度的加工过程。
在高速切削过程中,刀具以极高的速度旋转(通常超过每分钟数千转),同时进给速度也相应提高。
这种高速旋转产生的离心力有助于减小切削力和切削热,从而延长刀具寿命并减少工件的热变形。
此外,由于切削力的降低,高速切削还可以减少振动,进一步提高加工精度。
高速切削技术的优势主要体现在以下几个方面:1.高效率:与传统切削相比,高速切削可以显著提高材料去除率,缩短加工时间。
研究表明,高速切削可以提高生产效率达 30%至50%。
2.高精度:高速切削过程中的低切削力可以减少工件的振动,从而提高加工精度。
此外,由于切削热的影响较小,工件的热变形也得到了控制。
3.高质量表面:高速切削产生的切削热较低,这有助于减少工件的烧伤和裂纹,从而获得更好的表面质量。
4.刀具寿命延长:高速切削可以降低切削力,减少刀具磨损,从而延长刀具的使用寿命。
5.节能减排:高速切削技术可以实现更高的材料去除率,从而减少能源消耗和碳排放。
然而,高速切削技术也存在一些挑战,如刀具成本较高、对机床性能要求较高等。
因此,在实际应用中,需要根据具体加工需求和技术条件,合理选择切削参数和刀具,以确保高速切削技术的有效性和经济性。
总之,高速切削技术作为一种先进的制造工艺,具有高效率、高精度、高质量表面等优势,但在实际应用中需充分考虑其成本和设备要求。
高速切削技术简介

1.3 高速切削的研究发展现状
日本:
日本是在20世纪60年代开始高速切削机理的研究。 近些年来吸收了各国的研究成果,现在已后来居上,跃居世 界领先地位。 20世纪90年代研制出了日本第一台卧式加工中心,主轴转速 达到30000r/min,最大进给速度为80m/r,加速度为2g, 重复定位精度为±lµm。 同时他们也致力于高速切削工艺,特别是高速切削工艺数据 库、刀具磨损与破损机理、CAD/CAM系统开发及质量控制等 方面的研究。
1)提高排屑性能,具体措施:
①采用内部供液方式,压力为2~7MPa; ②钻尖角比普通钻头大,易于分断厚型切屑; ③对钻头横刃进行修磨,使之成为中心涡卷形状。
汽车零件孔的高速切削加工
高速钻削加工应注意的问题:
2)提高刀具刚性,具体措施:
①增大钻头芯厚; ②增大倒棱锥度。
汽车零件孔的高速加工
3)防止钻尖过热,具体措施:
1.5.1 汽车工业中的高速切削
汽车工业:
在20世纪20年代主要采用由组合机床组成的刚性生产 线。 在20世纪80年代后,开始采用由加工中心组成的柔性 生产线。 生产的柔性提高了,但生产效率不如组合机床生产线。 怎么办?能否采用高速加工来提高生产率?
1.5.1 汽车工业中的高速切削
汽车工业: 从20世纪80年代中期开始,在单轴专用加工 中心上,采用高速加工技术,以10倍于普通加工 的速度加工,使加工中心的柔性和生产率得到兼 顾,例如一台高速加工中心在一年中就能加工 40000件变速箱箱体。
汽车零件平面的高速铣削加工
1)铸铁缸体、缸盖端面的高速铣削加工:
如Lamb公司: 缸体、缸盖大平面加工采用高速铣削,用氮化硅 (Si3N4基)陶瓷刀片铣削缸体顶面,切削速度达 1524m/min,进给速度达6350mm/min,生产效率提高了 50%。
先进制造工艺--高速切削技术
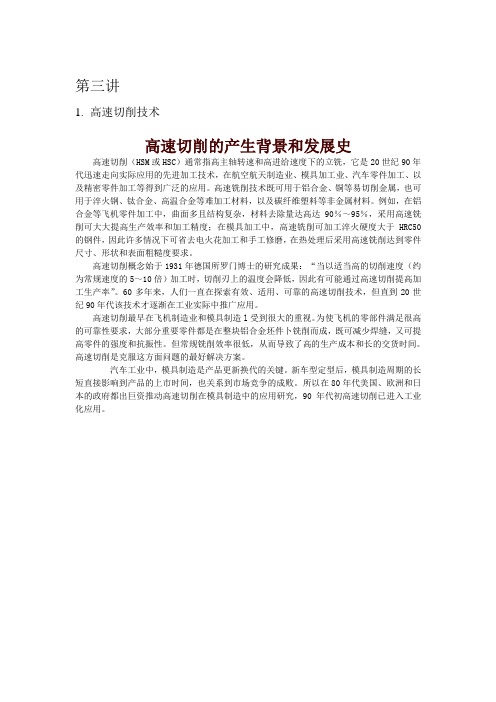
第三讲1.高速切削技术高速切削的产生背景和发展史高速切削(HSM或HSC)通常指高主轴转速和高进给速度下的立铣,它是20世纪90年代迅速走向实际应用的先进加工技术,在航空航天制造业、模具加工业、汽车零件加工、以及精密零件加工等得到广泛的应用。
高速铣削技术既可用于铝合金、铜等易切削金属,也可用于淬火钢、钛合金、高温合金等难加工材料,以及碳纤维塑料等非金属材料。
例如,在铝合金等飞机零件加工中,曲面多且结构复杂,材料去除量达高达90%~95%,采用高速铣削可大大提高生产效率和加工精度;在模具加工中,高速铣削可加工淬火硬度大于HRC50的钢件,因此许多情况下可省去电火花加工和手工修磨,在热处理后采用高速铣削达到零件尺寸、形状和表面粗糙度要求。
高速切削概念始于1931年德国所罗门博士的研究成果:“当以适当高的切削速度(约为常规速度的5~10倍)加工时,切削刃上的温度会降低,因此有可能通过高速切削提高加工生产率”。
60多年来,人们一直在探索有效、适用、可靠的高速切削技术,但直到20世纪90年代该技术才逐渐在工业实际中推广应用。
高速切削最早在飞机制造业和模具制造l受到很大的重视。
为使飞机的零部件满足很高的可靠性要求,大部分重要零件都是在整块铝合金坯件卜铣削而成,既可减少焊缝,又可提高零件的强度和抗振性。
但常规铣削效率很低,从而导致了高的生产成本和长的交货时间。
高速切削是克服这方面问题的最好解决方案。
汽车工业中,模具制造是产品更新换代的关键。
新车型定型后,模具制造周期的长短直接影响到产品的上市时间,也关系到市场竞争的成败。
所以在80年代美国、欧洲和日本的政府都出巨资推动高速切削在模具制造中的应用研究,90年代初高速切削已进入工业化应用。
图16 高速切削在生产应用中的发展历程图17 采用高速切削后产品质量提高的历程a一硬质合金切钢 b一硬质合金切铸铁c—CBN切铸铁图16是德国宝马公司(BMW)采用高速切削的历程。
高速切削加工技术的特点及应用要求

通讯作者简介 : 周进 ( 95 )女 , 16 一 , 湖南南 县人 , 高级 讲师 , 研 究 方向 : 计算机应用 与机电工程 。
E・alx njn u0 6 16 cm;injn u yho cr.n m i i gaw 20 @ 2 .o x gaw @ a o.o c 。 :o i o i n
1 倍 以上的切削加工 叫高速切 削加工。按 加工 0
工艺规定的高速切 削范 围: 车削 ( 0 700 70— 0 )Ⅱ
2 0 年 2 3日收到 06 月 湖 I铁 道职业技 术学 院科研规划项 目 _ } 『 ( 川铁 院办 [ 04 3 2 0 ] 6号 、2 0 ]2 [0 4 7 号) 资助 第 一作者简介 : 熊建武 (94 )男 , 16一 , 湖南 安化 县人 , 工学硕 士 , 高级工程师 、 副教授 , 研究方 向: 模具设计与精 暂切削。
进给丝杠 , 高速 、 高精度的插补系统 , 快速响应数控
系统和高精度 的伺 服系统 。主轴 的轴 向窜 动和径 向跳动小 , 并具有 良好的动平衡性能。 () 3 机床必须配备 实心 的台架 , 有效 消除切削 加工振动, 提高机床的稳定性 。 () 4 机床伺服 电动机 线速度高 , 并且能 提供 恒 定的速率 , 速度变化不超过 0 O %。 .1 () 5 机床数控系统必 须具备程序 预读 、 角 自 转 动减速 、 优化插补 、 可适用 于通用计算平 台等 功能, 如西门子 80 / 4 E F N C 5 i 4 D 80 ,A U I0 等系统 。 32 高速切削加工对刀具的要求 . 高速切削加工刀 具 的结构 必须保证 高速旋转 状态下的刀具动平衡 , 并确保 刀具寿命。为保证高 速旋转状态下刀具能够绕轴线稳定旋转 , 前采用两 目 种办法 , 一是采用带有动平衡装置 的刀具 , 此类刀具 在刀套表面安装了机械滑块或采用流体动平衡设计 ; 另外一种就是采用整体刀具, 刀套与刀体合为一体 ,
机械加工方面的几种先进工艺

机械加工方面的几种先进工艺机械加工是制造业中重要的一环,随着技术的不断发展,机械加工也在不断创新和改进。
本文将介绍几种先进的机械加工工艺。
一、高速切削技术高速切削技术是近年来发展起来的一种机械加工技术,其特点是切削速度高、切削力小、切削温度低、切削精度高,可以大大提高加工效率和加工质量。
高速切削技术需要使用高速切削机床和高速切削刀具,以及精密的切削参数控制系统。
在高速切削技术中,切削速度可达到每分钟数万转,切削深度和进给量可以在毫米级别内控制。
二、数控加工技术数控加工技术是现代机械加工的主流技术之一,其特点是自动化程度高、加工精度高、加工效率高、加工质量稳定。
数控加工技术需要使用数控机床和数控编程软件,通过编写数控程序,将加工工艺参数输入到数控系统中,实现对工件的自动加工。
数控加工技术可以实现对复杂形状的工件进行高精度加工,广泛应用于航空、汽车、模具等领域。
三、激光加工技术激光加工技术是一种非接触式加工技术,其特点是加工速度快、加工精度高、切割面光滑、不产生切削应力。
激光加工技术需要使用激光切割机和激光加工控制系统,通过控制激光束的焦距和功率,实现对材料的切割、钻孔、雕刻等加工。
激光加工技术应用广泛,包括电子、半导体、医疗、航空等领域。
四、电火花加工技术电火花加工技术是一种将电能转化为热能来加工工件的非传统加工技术,其特点是加工精度高、加工表面质量好、不会产生机械应力和热应力。
电火花加工技术需要使用电火花加工机和电火花加工控制系统,通过控制电极和工件之间的间隙和放电参数,实现对工件的加工。
电火花加工技术广泛应用于精密模具、航空航天、汽车等领域。
五、超声波加工技术超声波加工技术是一种利用超声波振荡来加工材料的加工技术,其特点是加工效率高、加工精度高、加工表面质量好、不会产生热应力和机械应力。
超声波加工技术需要使用超声波振荡器和超声波加工控制系统,通过控制振荡器的频率和振幅,实现对材料的加工。
超声波加工技术应用广泛,包括电子、光学、医疗、航空等领域。
先进制造技术 第2章 高速切削技术2-1
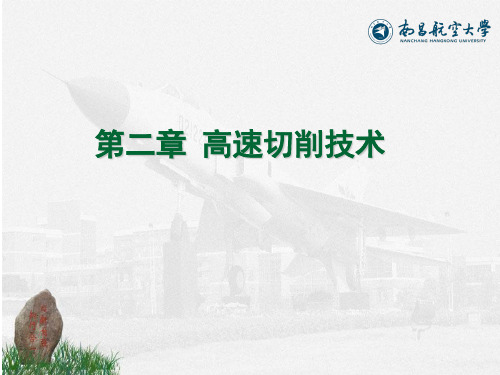
萨洛蒙在l924一1931年间,进行了一系列的高速切削实验: 在非黑色金属材料,如铝、铜和青铜上,用特大直径的刀 盘进行锯切,最高实验的切削速度曾达到14000m/min, 在各种进给速度下,使用了多达20齿的螺旋铣刀。l931年 申请了“超极限速度”专利,随后卖给了“Krupp钢与工 具制造厂”。 萨洛蒙和他的研究室实际上完成了大部分有色金属的切削 试验研究,并且推断出铸铁材料和钢材的相关曲线。 萨洛蒙理论提出了一个描述切削条件的区域或者是范围, 在这个区域内是不能进行切削的。萨洛蒙没有提出可靠的 理论解释,而且他的许多实验细节也没有人知道。
刀具磨损曲线
三、高速切削切屑形成
高速切削试验表明,工件材料及 性能对切屑形态 有决定性影响。
低硬度和高热物理性能的工件材料(铝合金、低碳钢、未 淬硬钢等)易形成连续带状切屑。 高硬度和低热物理性能的工件材料(钛合金钢、未淬硬钢 等)易形成锯齿状切屑。
切削速度对切屑形态有重要影响。对钛合金,在 (1.5~4800)m/min的切削速度范围内形成锯齿状 切屑,随切削速度的增加,锯齿程度(锯齿的齿 距)在增加,直至成为分离的单元切屑。
不同切削速度下车削45钢件的切削形态。
一方面,切削速度增加,应变速度加大,导致脆 性增加,易于形成锯齿状切屑;另一方面,切削 速度增加,切屑温度增加,导致脆性降低,不易 形成锯齿状切屑;
绝热剪切理论(Adiabatic Shear Theory) 周期脆性断裂理论(Periodic brittle fracture theoty)
萨洛蒙(Salomon)曲线
1600
切削温度/℃
钢
1200
青铜
铸铁 硬质合金980℃ Stelite合金850℃ 高速钢650℃ 碳素工具钢450℃
高速切削加工技术
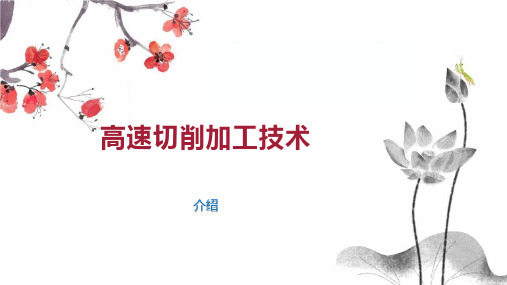
高速切削的适用性
高速切削的适用性
高速加工作为一种新的技术,其优点是显而易见的,它给传统的金属切削理论带来了一种革命性的变化。那 么,它是不是放之四海而皆准呢?显然不行。即便是在金属切削机床水平先进的瑞士、德国、日本、美国,对于这 一崭新技术的研究也还处在不断的摸索研究当中。实际上,人们对高速切削的经验还很少,还有许多问题有待于 解决:比如高速机床的动态、热态特性;刀具材料、几何角度和耐用度问题,机床与刀具间的接口技术(刀具的 动平衡、扭矩传输)、冷却润滑液的选择、CAD/CAM 的程序后置处理问题、高速加工时刀具轨迹的优化问题等等。
(1)CAM系统应具有很高的计算编程速度
高速加工中采用非常小的切给量与切深,故高速加工的NC程序比对传统数控加工程序要大得多,因而要求计 算速度要快,要方便节约刀具轨迹编辑,优化编程的时间。
(2)全程自动防过切处理能力及自动刀柄干涉检查能力
高速加工以传统加工近10倍的切削速度进行加工,一旦发生过切对机床、产品和刀具将产生灾难性的后果, 所以要求其CAM系统必须具有全程自动防过切处理的能力。高速加工的重要特征之一就是能够使用较小直径的刀 具,加工模具的细节结构。系统能够自动提示最短夹持刀具长度,并自动进行刀具干涉检查。
如此看来,主轴转速为10~r/min这样的高速切削在实际应用时仍受到一些限制: (1)主轴转速10~r/min时,刀具必须采用 HSK 的刀柄,外加动平衡,刀具的长度不能超过120mm,直径不 能超过16mm,且必须采用进口刀具。这样,在进行深的型腔加工时便受到限制。 (2)机床装备转速为10~r/min的电主轴时,其扭矩极小,通常只有十几个N·m,最高转速时只有5~6N·m。 这样的高速切削,一般可用来进行石墨、铝合金、淬火材料的精加工等。 (3)MIKRON公司针对这些情况开发了一些主轴最高转速为r/min、r/min、r/min和r/min的机床,尽力提高 进给量(~mm/min),以保证机床既能进行粗加工,又能进行精加工,既省时效率又高。
高速加工技术及应用
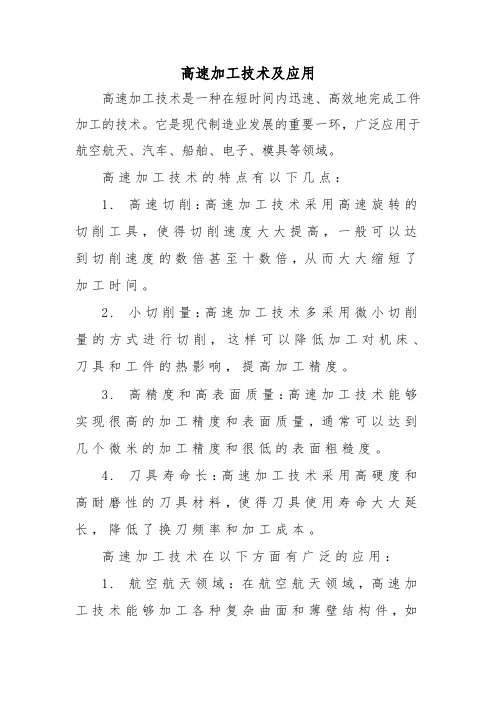
高速加工技术及应用高速加工技术是一种在短时间内迅速、高效地完成工件加工的技术。
它是现代制造业发展的重要一环,广泛应用于航空航天、汽车、船舶、电子、模具等领域。
高速加工技术的特点有以下几点:1.高速切削:高速加工技术采用高速旋转的切削工具,使得切削速度大大提高,一般可以达到切削速度的数倍甚至十数倍,从而大大缩短了加工时间。
2.小切削量:高速加工技术多采用微小切削量的方式进行切削,这样可以降低加工对机床、刀具和工件的热影响,提高加工精度。
3.高精度和高表面质量:高速加工技术能够实现很高的加工精度和表面质量,通常可以达到几个微米的加工精度和很低的表面粗糙度。
4.刀具寿命长:高速加工技术采用高硬度和高耐磨性的刀具材料,使得刀具使用寿命大大延长,降低了换刀频率和加工成本。
高速加工技术在以下方面有广泛的应用:1.航空航天领域:在航空航天领域,高速加工技术能够加工各种复杂曲面和薄壁结构件,如发动机叶片、航空航天零件等,提高了零件的精度和表面质量。
2.汽车领域:高速加工技术在汽车制造中主要用于零部件的加工,如发动机缸体、座椅滑块等,能够提高加工效率和产品质量。
3.船舶领域:高速加工技术在船舶制造中主要用于船体结构和轴承加工,如船体钢板切割、轴承的外圈和内圈加工等,提高了加工速度和质量。
4.电子领域:高速加工技术在电子领域主要用于半导体器件的切割和加工,如芯片切割、光纤连接器加工等,提高了加工精度和产品性能。
5.模具领域:高速加工技术在模具制造中主要用于模具的精细加工,如模具的深孔加工、细小结构的加工等,提高了模具的加工精度和寿命。
高速加工技术的发展对于提高制造业的竞争力和产品质量具有重要意义。
随着材料科学和机械加工技术的不断发展,高速加工技术将在更多领域得到应用,并不断推动制造业的发展。
高速切削加工技术介绍

美国于 1960 年前后开始进行超高速切削试验。试验将刀具装在加农炮里,从滑台上射向工件;或将工件当作子弹射向固定的刀具。 1977 年美国在一台带有高频电主轴的加工中心上进行了高速切削试验,其主轴转速可以在 180 ~ 18000r / min 范围内无级变速,工作台的最大进给速度为 7 . 6m / min。
1979 年美国防卫技术研究总署( DARPA )发起了一项“先进加工研究计划”,研究切削速度比塑性波还要快的超高速切削,为快速切除金属材料提供科学依据。
在德国, 1984 年国家研究技术部组织了以 Darmstadt 工业大学的生产工程与机床研究所 PTW )为首,包括 41 家公司参加的两项联合研究计划,全面而系统地研究了超高速切削机瓜刀具、控制系统以及相关的工艺技术,分别对各种工件材料(钢、铸铁、特殊合金、铝合金、铝镶铸造合金、铜合金和纤维增强塑料等)的超高速切削性能进行了深入的研究与试验,取得了切削热的绝大部分被切屑带走国际公认的高水平研究成果,并在德国工厂广泛应用,获得了好的经济效益。日本于 20 世纪 60 年代就着手超高速切削机理的研究。日本学者发现在超高速切削时,工件基本保持冷态,其切屑要比常规切屑热得多。日本工业界 35善于吸取各国的研究成果并及时应用到新产品开发中去,尤其在高速切削机床的研究和开发方面后来居上,现已跃居世界领先地位。进人 20 世纪 90 年代以来,以松浦( Matsuora )、牧野 ( Makino )、马扎克( Mazak )和新泻铁( Niigata )等公司为代表的一批机床制造厂,陆续向市场推出不少超高速加工中心和数控铣床,日本厂商现已成为世界上超高速机床的主要提供者.
2 高速切削刀具
刀具是实现高速加工的关键技术之一。生产实践证明,阻碍切削速度提高的关键因素是刀具能否承受越来越高的切削温度在萨洛蒙高速切理研究和高速切削试验的不断深人,证明高速切削的最关键技术之一就是所用的刀具。舒尔兹教授在第一届德国 ― 法国高速切削年会( 1997 年)上做的报告中指出:目前,在高速加工技术中有两个基本的研究发展目标,一个是高速引起的刀具寿命问题,另一个是具有高精度的高速机床.
智能化加工中高速切削技术的研究

智能化加工中高速切削技术的研究随着智能化加工技术的不断发展,高速切削技术的研究和应用也成为了当前制造业领域的热点之一。
高速切削技术,是指在高转速和高进给率的条件下进行切削加工的技术。
这种方法不仅可以提高生产效率,降低生产成本,还可以大大提高加工质量和工件精度。
下面将分别从高速切削技术的优势、研究现状和发展趋势三个方面来谈一下高速切削技术在智能化加工中的应用。
一、高速切削技术的优势1. 提高生产效率高速切削技术可以大大提高生产效率。
由于高速切削的进给率更高,每分钟加工量也随之提高,因此可以在保证加工质量的情况下大幅缩短加工时间。
另外,由于高速切削能够更好地控制温度,这种方法也可以有效地避免加工过程中因温度过高而导致的加工时间延长。
2. 提高加工精度高速切削技术在保证生产效率的同时还可以提高加工精度。
由于高速切削技术具有更高的进给率和更快的切削速度,因此可以使加工后的工件表面更加光滑,同时还可以提高切削刀具的寿命和稳定性。
这也是为什么在半导体、电子、航空航天等行业中普遍采用高速切削技术的原因。
3. 降低生产成本高速切削技术可以降低生产成本。
由于高速切削技术可以更快地完成加工过程,因此可以大幅缩短加工时间,从而降低加工成本。
另外,由于高速切削技术可以提高加工精度,因此可以减少加工中因误差造成的废品率,进一步降低生产成本。
二、高速切削技术的研究现状在高速切削技术的研究方面,国内外学者们进行了大量的工作。
目前主要研究方向包括切削力、加工表面质量、切削温度、刀具磨损等多个方面。
其中,切削力与加工表面质量是当前主要研究方向。
1. 切削力切削力是高速切削过程中的重要参数之一。
国内外学者们通过理论计算、仿真模拟、实验验证等多种方法来研究高速切削过程中的切削力变化规律和影响因素,为高速切削过程的稳定性和加工效果的提升提供了有力的支持。
2. 加工表面质量加工表面质量是衡量高速切削技术优劣的关键指标之一。
国内外学者们通过改进刀具结构、刀具材料和切削参数等多种措施来提高高速切削加工表面质量,研究表明在高速切削过程中使用更硬的刀具材料和更合理的切削参数可以有效地提升加工表面质量。
高速切削加工技术
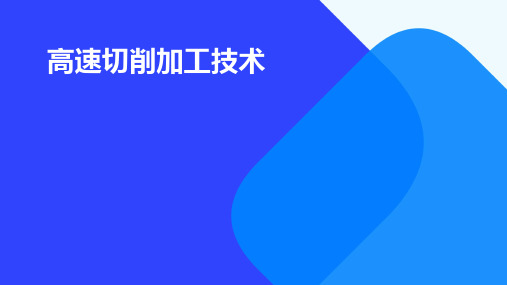
在通用机械制造业中,高速切 削加工技术广泛应用于机床、 泵阀、压缩机和液压传动装置 等产品的制造。
05
高速切削加工技术的发 展趋势与挑战
高效稳定的高速切削技术
高效稳定的高速切削技术是未来发展 的关键,需要不断提高切削速度和加 工效率,同时保持加工过程的稳定性 和可靠性。
高效稳定的切削技术还需要不断优化 切削参数和刀具设计,以适应不同材 料和加工需求的挑战。
高速切削工艺技术
切削参数选择
根据不同的加工材料和切削条件, 选择合适的切削速度、进给速度 和切削深度等参数,以实现高效
切削和高质量加工。
切削液使用
合理选用切削液,如乳化液、极 压切削油等,以提高切削效率和 工件表面质量,同时减少刀具磨
损和热量产生。
加工路径规划
采用合理的加工路径和顺序,以 减少空行程和换刀次数,提高加
高效稳定的切削技术需要解决切削过 程中的振动和热变形问题,提高加工 精度和表面质量。
高性能刀具材料的研发
高性能刀具材料是实现高速切削 的关键因素之一,需要具备高硬 度、高强度、高耐磨性和良好的
抗热震性等特点。
研发新型高性能刀具材料,如超 硬材料、陶瓷材料等,能够提高 切削速度和加工效率,同时减少
刀具磨损和破损。
改善加工质量
01
高速切削加工技术能够减少切削 力,降低切削热,从而减小了工 件的热变形和残余应力,提高了 加工精度和表面质量。
02
由于切削力减小,工件不易产生 振动,减少了振纹和表面粗糙度 ,进一步提高了加工质量。
降低加工成本
高速切削加工技术能够显著提高加工效率,缩短了加工周期,从而降低了单件成 本。
高速切削加工技术
目 录
• 高速切削加工技术概述 • 高速切削加工技术的优势 • 高速切削加工的关键技术 • 高速切削加工的实践应用 • 高速切削加工技术的发展趋势与挑战 • 高速切削加工技术的未来展望
高速切削对数控编程的具体要求

高速切削对数控编程的具体要求
1. 切削参数要求,高速切削对数控编程要求合理选择切削速度、进给速度和切削深度等参数。
切削速度要保持在合适的范围内,以
确保切削效率和刀具寿命的平衡。
进给速度要根据材料的硬度、切
削力和刀具的性能等因素进行调整,以实现高效的切削。
切削深度
要根据工件的要求和刀具的稳定性来确定。
2. 刀具选择要求,高速切削要求选择合适的刀具。
刀具的材料、刃数、刃角、刃长等参数需要根据切削材料、切削条件和加工要求
进行选择。
高速切削一般需要使用硬质合金刀具或涂层刀具,以提
高切削速度和刀具寿命。
3. 编程技巧要求,高速切削对数控编程的要求包括合理的刀具
路径规划、平滑的切削轨迹和精确的切削参数控制。
刀具路径要避
免多余的刀具运动,减少空程时间,提高切削效率。
切削轨迹要尽
量平滑,避免急剧的变化和过大的加速度,以减少振动和刀具的应力。
切削参数的控制要准确,包括切削速度、进给速度、切削深度、切削角度等,以保证加工质量和刀具寿命。
4. 程序调试要求,高速切削对数控编程的程序调试要求严格。
需要对程序进行充分的模拟和验证,确保刀具路径和切削参数的准确性。
同时,还需要进行切削试验和切削力的监测,以调整和优化切削参数,提高切削效率和加工质量。
综上所述,高速切削对数控编程的具体要求包括合理选择切削参数、选择合适的刀具、掌握编程技巧和进行程序调试等方面。
这些要求的达成可以提高加工效率、降低成本和提高产品质量。
高速切削加工技术的概念

高速切削加工技术的概念高速切削加工技术是一种在机械加工中使用高速旋转刀具来去除材料的工艺。
它可以提高加工效率、减少加工成本,提高切削质量,并延长刀具寿命。
在高速切削加工技术中,切削速度通常比传统切削速度高出几倍,达到可达到切削极限的速度。
高速切削加工技术的基本原理是通过尽可能高的转速来提高切削速度,以减小切削过程中的切削时间。
高速切削加工技术的发展需要满足以下几个条件:高速切削的刀具材料需要具备良好的硬度、热稳定性和刚性;高速切削需要使用高速转子以提供所需的切削速度;高速切削需要使用高速切削液以冷却和润滑刀具和切削床面。
高速切削加工技术的优点主要体现在以下几个方面:1. 高加工效率:高速切削加工可以提高切削速度,减少切削时间,从而提高加工效率。
与传统切削相比,高速切削可以将加工时间减少50%以上。
2. 高表面质量:高速切削加工可以减小切削过程中的机床振动和切削力,从而获得更高的表面质量。
切削过程中,高速转子产生的离心力可以抑制刀具的振动,提高切削表面的光洁度。
3. 刀具寿命长:高速切削加工可以减小切削温度,减小切削热对刀具的影响,从而延长刀具的使用寿命。
高速切削可以在减小切削温度的同时提高切削速度,从而有效地降低刀具的受热面积,减小刀具的磨损。
4. 减少加工成本:高速切削加工可以提高加工效率,减少切削时间,从而减少加工成本。
高速切削还可以减小切削力和切削温度,减少切削液的消耗,降低切削液的成本。
高速切削加工技术的应用范围广泛,包括航空航天、汽车制造、模具制造、电子制造等领域。
例如,在航空航天制造中,高速切削可以快速精确地加工复杂的零部件;在汽车制造中,高速切削可以提高发动机零部件的加工效率和精度;在模具制造中,高速切削可以提高模具的加工效率和精度;在电子制造中,高速切削可以提高电路板的加工效率和精度。
总之,高速切削加工技术是现代制造业的一个重要发展方向。
通过提高切削速度,高速切削加工可以提高加工效率、减少加工成本,并提高切削表面的质量。
模具加工中的高速切削技术

摘 要: 高速切 削是 一项 复杂 的 系统 工程 。 高速切 削不 只是切 削速 度 的提 高 , 的发展 涉及 到 机床 、 它 刀具 、 艺和 材料 等诸 多领域 的 工 技 术 配合 和技 术创新 。 关键 词 : 模具 加工 ; 高速切 削 ; 用 应
1模 具加工 的特 点
2 . 2高速 进 给系统
瞄国陆盈口团困
丽UNI Z I … d U U 'l I .
工 业 技 术
模具 ] c m- 中的高速切 削技术
郑 华 新 张 清 胜
(、 1 海马郑州汽车有限公司 , 河南 郑州 4 0 1 2 河南安飞 电子玻璃有限公 司 506 、 河南 郑州 40 1 ) 5 0 6
—
高速 切 削要 求 刀 具材 料具 有 如 下 性 能 : 由曲面组成。 所用的材料硬度高, 一般模具都 高硬 度 、 强 度 和耐 磨性 : 高 高韧 度 、 良好 的耐 是由淬火工具钢或硬质合金制成 ,运用传统 热冲击性 ; 高热硬性、 良好的化学稳定性。日 的加 工方法 加工较 为 困难 。 目前 在模 具加 工 前, 高速切削加工常用的刀具材料有 : 涂层刀 制造 过程 中 ,主要 以普通 机 加工 和 电火花 加 具 、 瓷刀 具 、 方 氮 化硼 (B ) 陶 立 C N材料 和聚 品 工为 主 。 要缩 短制造 周期 并降低 成本 , 广 金刚 石(C ) 等 。 必须 P D材料 泛采 用先进 切削加 工技 术加 工模 具 。而作 为 3 高速 切 削刀具 系统 . 2 先进 制造技 术 的高速切 削技 术 的 出现 ,正 是 刀具几 何 参数对加 工 质量 和刀具 耐用 度 满 足了模具 加工 这些要 求和特 点 。 有很 大影 响 ,一般 高速切 削刀 具 的前角 比普 2高速 切削机 床技术 通 切 削刀具 约 小 1。后 角 约大 5一。 刀具 O, o8。 性能 良好 的高速切 削机 床是 实现 高速 切 在 高速旋 转时 , 会承受 很大 的离 心力 , 大小 其 削 的前提 和关键 ,而具 有 高精度 的 高速 主轴 远 远超过 切削 力 , 为刀具 的 主要 载荷 , 以 成 足 和 控制精 度高 的高速 进给 系统 ,则 是高 速切 导致 刀体 破碎 , 造成重 大事 故 。
高速切削(HSC)技术
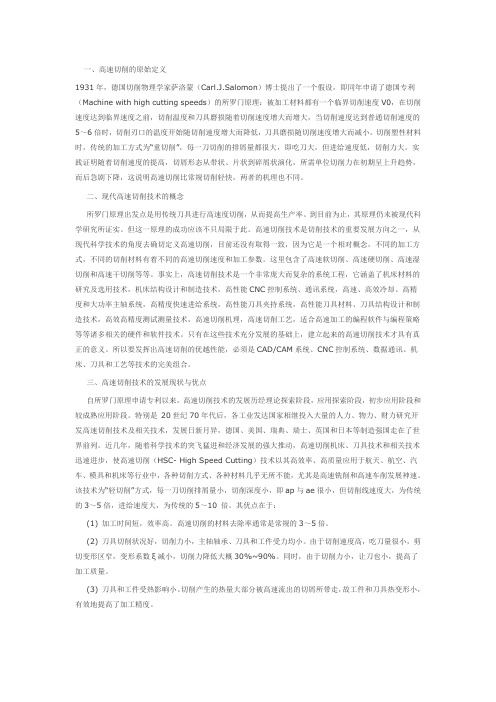
一、高速切削的原始定义1931年,德国切削物理学家萨洛蒙(Carl.J.Salomon)博士提出了一个假设,即同年申请了德国专利(Machine with high cutting speeds)的所罗门原理:被加工材料都有一个临界切削速度V0,在切削速度达到临界速度之前,切削温度和刀具磨损随着切削速度增大而增大,当切削速度达到普通切削速度的5~6倍时,切削刃口的温度开始随切削速度增大而降低,刀具磨损随切削速度增大而减小。
切削塑性材料时,传统的加工方式为“重切削”,每一刀切削的排屑量都很大,即吃刀大,但进给速度低,切削力大。
实践证明随着切削速度的提高,切屑形态从带状、片状到碎屑状演化,所需单位切削力在初期呈上升趋势,而后急剧下降,这说明高速切削比常规切削轻快,两者的机理也不同。
二、现代高速切削技术的概念所罗门原理出发点是用传统刀具进行高速度切削,从而提高生产率。
到目前为止,其原理仍未被现代科学研究所证实。
但这一原理的成功应该不只局限于此。
高速切削技术是切削技术的重要发展方向之一,从现代科学技术的角度去确切定义高速切削,目前还没有取得一致,因为它是一个相对概念,不同的加工方式,不同的切削材料有着不同的高速切削速度和加工参数。
这里包含了高速软切削、高速硬切削、高速湿切削和高速干切削等等。
事实上,高速切削技术是一个非常庞大而复杂的系统工程,它涵盖了机床材料的研究及选用技术,机床结构设计和制造技术,高性能CNC控制系统、通讯系统,高速、高效冷却、高精度和大功率主轴系统,高精度快速进给系统,高性能刀具夹持系统,高性能刀具材料、刀具结构设计和制造技术,高效高精度测试测量技术,高速切削机理,高速切削工艺,适合高速加工的编程软件与编程策略等等诸多相关的硬件和软件技术。
只有在这些技术充分发展的基础上,建立起来的高速切削技术才具有真正的意义。
所以要发挥出高速切削的优越性能,必须是CAD/CAM系统、CNC控制系统、数据通讯、机床、刀具和工艺等技术的完美组合。
- 1、下载文档前请自行甄别文档内容的完整性,平台不提供额外的编辑、内容补充、找答案等附加服务。
- 2、"仅部分预览"的文档,不可在线预览部分如存在完整性等问题,可反馈申请退款(可完整预览的文档不适用该条件!)。
- 3、如文档侵犯您的权益,请联系客服反馈,我们会尽快为您处理(人工客服工作时间:9:00-18:30)。
称为高速切削。在此速度下,切削温度可以越过所 谓的 “ 死区” ( ae o da ) V ly t ,刀具反而可以正常 l eh f 切削。图 1 是德国 D rs d 工业大学生产工程与机 a tt ma 床研究所 (1 PW)做出的不 同材料高速切削范围的
摘要 :概述 高速切削技术的优点及前景展望 ,结合 实际加工中的经验提 出了对工艺方法特别
是对 数控 编程 的新要 求 。
关键词:高速切 削; 削速度;每齿进给量 切
中图分类 号 :T S 6・ G0 l 文献标 识码 :B 文章编 号 :17 4 5 (06)1— 0 3— 3 6 2— 50 20 0 0 2 0
Ab ta t T i at l r f tea v na e n r s e t ihs e dc tn c n q e n us sr c : hs r ceb esh d a tg sa dp op c hg p e ut gt h i u ,a d p t i i f o i e
高速带走 ,传给工件的热大量减少 ,减少 了零件的
内应力和热变形 ,提高了加工精度。 ( )高速切 削中的激振频率 特别高 ,它远远 4
离开了 “ 机床 一刀具 一工件 ”系统 的低 阶固有 频
・
. .
[ 收稿 日 期]20 - 8 2 05 0 — 5 [ 作者简介]邓螈援 (9 1 , 18一) 女,助教,主要从事机械设计制造及其 自 动化、数控技术课程教学 及研究。
业等行业 。近年来 ,由于我 国航天、航空 、模具和 汽轮机等行业装备水平的迅速提高和激烈的市场竞
争 ,也开始不同程度地利用高速切削 了。 通常人们按照德国 Dr s d 工业大学研究人员 a tt ma
的定义,把高出 5— O 1 倍常规切削速度的切削加工
壁、细肋件等刚性差的零件 的表面质量 ,包括降低
1 引言
高速切削 ( i pe u i )是 2 Hg S edC t g h t n O世纪 9 O
实验数据。该研究结果得到了国际上的公认 。 和常规切削相 比,高速切削具有如下优点:
( ) 由于切 削速度大幅度提高 ,为保持每齿 1
进 年代初才开始实际应用 的一项先进制造技术 ,由于 进给量不变 , 给率也相应大幅提高。单位时问内 能显著提高加工效率和切削质量 ,在短短的十几年 材料切除率增加 , 切削时间减少。极大地提高了生
fr ad n w rq eto c n lg ,ep cal en meal o to e rga ow r e e u s ft h oo y s e il t u r l cnrl d p o rmmig e yh y l n ,wi ep c o te t rs e tt h h
Hih S e d Cu tn c n q ea d g p e ti g Te h i u n
Ne Re u s fTe h oo y w q e to c n l g
D n a y a Ya e L o Yi g e g Yu n u n , nL i, u n
(1 C eg uU i r t C e gu 6 0 0 ;2 C e g uY n e P w r O. T C eg u 6 0 8 ; . hn d nv sy h nd 1 16 . h n d u ni o e e i C ,L D hn d 10 2
3 T eTnhR sac ntueo hn l tnc ehooyGopCroao C egu 10 6 . h et eerhIstt f iaEe r i Tcnl ru o rtn hnd 60 3 ) i C co s g p i
维普资讯 http://www.Hale Waihona Puke
2 o 12月 0 6年期 第
实 验
科
学
与 技
术
高速切 削技术及工艺新要求
邓螈媛 ” 严 磊 罗 颖
(. 1 成都大学 成都 600 ;2 成都云内动力有限公司 成都 60 8 ; 116 . 10 2 3 .中国电子科技集 团公司第十研究所 成都 603 ) 106
这层熔化面起到了一定的润滑作用 ,这是高速切削 刀具不易产生积屑瘤 的原 因之一。所以在确定高速 切削参数时,一般都要提高切削速度 同时减少轴向
往往 比常规切削好许多。
纤维塑料
铝合金 黄铜
切削深度和提高进给率以保持一定 的切屑厚度 ,这
样有利于切屑带走大量的切削热 ,同时有利于切屑 在刀具前刀面上的快速移动。笔者在实际切削铝合
一
2 — 3
维普资讯
E pr et cec T cnlg xei n i e& eh o y m S n o
2o 0 6年 2月 第 1 期
率范围 ,加工平稳 、振动小 。而工件的加工表面粗
糙度对低阶固有频率最敏感 ,加工出的表面粗糙度
以熔化切屑上一层极薄的接触面 ,切屑高速移动时
中迅速成为欧美 日本等主要工业 国切削加 工的主 流 ,广泛应用于模具 、航空 、航天、机车和汽车工
产效率 ,降低了生产成本 。 ( )从高速切削大量实 践中得知 ,在切 削速 2 度达到一定值后 ,切削力可降低 3 % 以上,尤其 O 是径向切削力 的大幅度减少 ,这特别有利于提高薄
a t a c ie p c s i g e p r n e c u lma h n r e sn x e e c . o i
Ke r s: hg p e ut g ut gs e d e dn mo n e oh y wo d ih s e d c t n ,c t n p e ,fe iga u tp rt t i i o