高速切削加工技术的现状和发展
我国高速加工技术现状及发展趋势
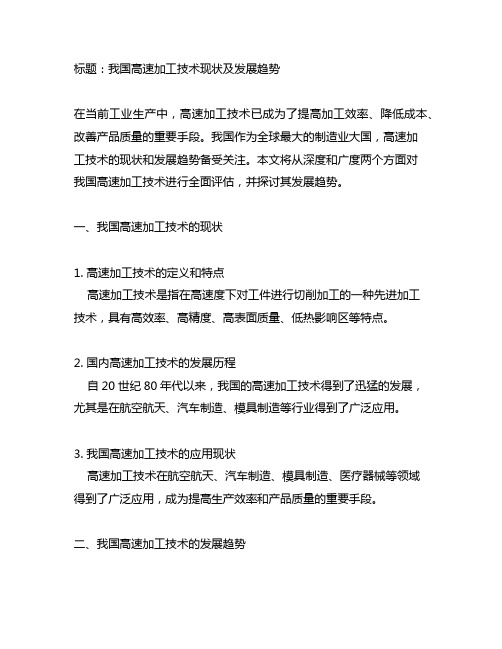
标题:我国高速加工技术现状及发展趋势在当前工业生产中,高速加工技术已成为了提高加工效率、降低成本、改善产品质量的重要手段。
我国作为全球最大的制造业大国,高速加工技术的现状和发展趋势备受关注。
本文将从深度和广度两个方面对我国高速加工技术进行全面评估,并探讨其发展趋势。
一、我国高速加工技术的现状1. 高速加工技术的定义和特点高速加工技术是指在高速度下对工件进行切削加工的一种先进加工技术,具有高效率、高精度、高表面质量、低热影响区等特点。
2. 国内高速加工技术的发展历程自20世纪80年代以来,我国的高速加工技术得到了迅猛的发展,尤其是在航空航天、汽车制造、模具制造等行业得到了广泛应用。
3. 我国高速加工技术的应用现状高速加工技术在航空航天、汽车制造、模具制造、医疗器械等领域得到了广泛应用,成为提高生产效率和产品质量的重要手段。
二、我国高速加工技术的发展趋势1. 技术创新推动高速加工技术的发展随着科技的进步和不断创新,高速加工技术将会更加高效、精密、稳定,能够满足更加复杂的加工需求。
2. 智能制造与高速加工技术的融合智能制造将成为未来高速加工技术发展的重要方向,通过智能化、自动化技术,提高生产效率和产品质量。
3. 绿色制造与高速加工技术的结合高速加工技术在减少碳排放、节能减排方面将会有更大的发展空间,应用于绿色制造领域。
4. 人工智能在高速加工技术中的应用随着人工智能技术的快速发展,其在高速加工技术中的应用将会成为新的发展趋势,将提高生产效率和产品质量。
三、总结与展望我国高速加工技术在不断发展创新的过程中,已经取得了令人瞩目的成绩,但与发达国家相比仍有一定差距。
在未来发展中,需要加大科技投入力度,加强技术研发和创新,培养更多高端技术人才,不断提升我国的高速加工技术水平,推动制造业向高质量发展。
个人观点:高速加工技术作为先进制造技术的代表,将会对我国工业生产产生深远影响。
在未来,我相信随着科技的进步和不断创新,我国的高速加工技术将不断迈向更加高效、精密、稳定的发展方向,并为我国制造业的转型升级和智能制造提供重要支撑。
高速切削加工技术及其进展
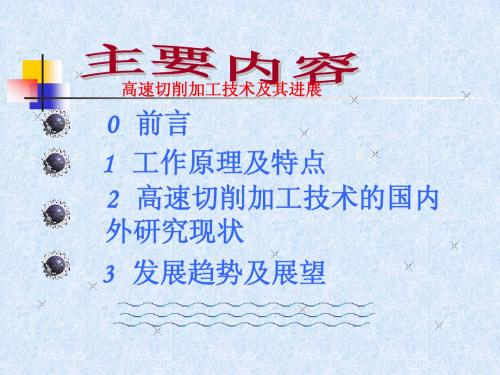
1 工作原理及特点
1.1 高速切削加工的提出
1.高速切削加工技术 于20世纪30年代由德 国 人 Salomon 提 出 。 大量铣削试验发现, 随切削速度不断增加 ,切削温度上升到一 峰值,随着切削速度 进一步提高,切削温 度达到峰值后反而下 降。 2.随上世纪80 年代末 和90 年代初数控机床 和刀具技术的进步, 开始应用并快速发展 到广泛应用。
1 工作原理及特点
1.3 高速切削加工的特点
加工精度高 切削力减少 降低了切削热对 被加工工件的影 响 可以以切代磨 刀具寿命是制约 高速切削进一步 发展的主要因素 之一。
图2 高速加工的一般特征
2 高速切削加工技术的国内外研究现状
2.1 高速切削刀具材料
涂层刀具,主要 有硬涂层、软涂 层和金刚石膜涂 层。 立方氮化硼 聚晶金刚石 金属陶瓷刀具 陶瓷刀具
图3 高速加工技术的研究体系
2 高速切削加工技术的国内外研究现状
2.2 高速切削切屑形成及其变形机理 主要集中在淬硬 的研究
钢、高温高强度 钢、钛合金等难 加工材料高速切 削切屑形成机理 的研究。 锯齿形切屑形成 机理---两大理论 体系,即突变剪 切或绝热剪切理 论和周期性脆性 断裂理论。
图3 高速加工技术的研究体系
高速切削加工技术及其进展
0 前言 1 工作原理及特点 2 高速切削加工技术的国内 外研究现状 3 发展趋势及展望
0 前言
1. 生产力构成中, 制造技术的
作用往往占60% 左右
2. 工业发达国家制造技术发展
计划 ,如美国的先进制造技 术计划(AMT)、关键技术( 制造)计划,日本的智能制造 系统国际合作计划(IMS), 德国的制造 2000 计划等。 3.现代切削加工技术的重要发 展方向 :以高生产率和高加 工精度与表面质量等特点著称 的高速切削技术
高速钻铣切削技术发展趋势及应用展望
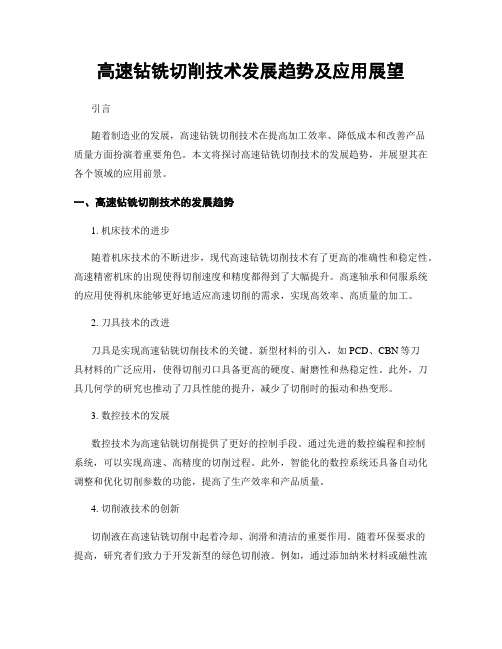
高速钻铣切削技术发展趋势及应用展望引言随着制造业的发展,高速钻铣切削技术在提高加工效率、降低成本和改善产品质量方面扮演着重要角色。
本文将探讨高速钻铣切削技术的发展趋势,并展望其在各个领域的应用前景。
一、高速钻铣切削技术的发展趋势1. 机床技术的进步随着机床技术的不断进步,现代高速钻铣切削技术有了更高的准确性和稳定性。
高速精密机床的出现使得切削速度和精度都得到了大幅提升。
高速轴承和伺服系统的应用使得机床能够更好地适应高速切削的需求,实现高效率、高质量的加工。
2. 刀具技术的改进刀具是实现高速钻铣切削技术的关键。
新型材料的引入,如PCD、CBN等刀具材料的广泛应用,使得切削刃口具备更高的硬度、耐磨性和热稳定性。
此外,刀具几何学的研究也推动了刀具性能的提升,减少了切削时的振动和热变形。
3. 数控技术的发展数控技术为高速钻铣切削提供了更好的控制手段。
通过先进的数控编程和控制系统,可以实现高速、高精度的切削过程。
此外,智能化的数控系统还具备自动化调整和优化切削参数的功能,提高了生产效率和产品质量。
4. 切削液技术的创新切削液在高速钻铣切削中起着冷却、润滑和清洁的重要作用。
随着环保要求的提高,研究者们致力于开发新型的绿色切削液。
例如,通过添加纳米材料或磁性流体来提高切削液的热传导和润滑性能,同时减少对环境的污染。
切削液技术的改进将进一步促进高速钻铣切削技术的发展。
二、高速钻铣切削技术的应用展望1. 航空航天领域航空航天领域对于精密和高效的切削加工是非常关键的。
高速钻铣切削技术的应用可以加快零部件的加工速度,提高生产效率,并且保证零部件的高精度和质量。
此外,高速钻铣切削技术还可以应用于航空航天材料的切削加工,如高强度钛合金、镍基高温合金等。
2. 汽车领域汽车制造行业对于高速、高精度的切削加工也有很高的需求。
高速钻铣切削技术可应用于发动机缸体、汽缸盖和各种复杂曲面件的加工。
借助高速切削,汽车制造商可以提高生产效率,降低成本,并且提供更高质量的汽车零部件。
高速加工的发展趋势
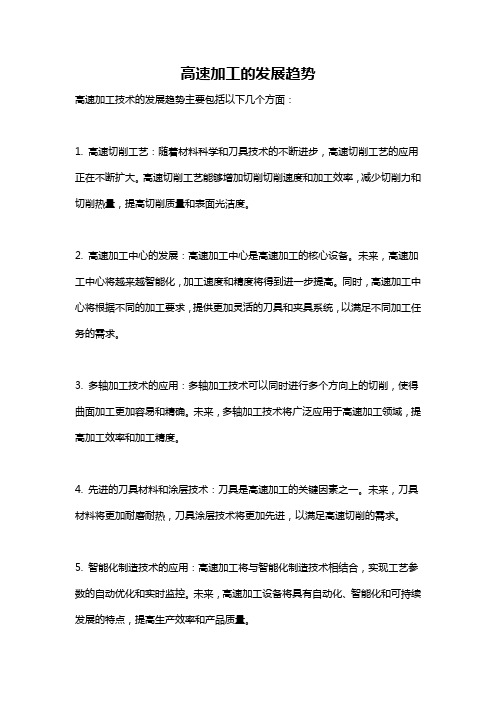
高速加工的发展趋势
高速加工技术的发展趋势主要包括以下几个方面:
1. 高速切削工艺:随着材料科学和刀具技术的不断进步,高速切削工艺的应用正在不断扩大。
高速切削工艺能够增加切削切削速度和加工效率,减少切削力和切削热量,提高切削质量和表面光洁度。
2. 高速加工中心的发展:高速加工中心是高速加工的核心设备。
未来,高速加工中心将越来越智能化,加工速度和精度将得到进一步提高。
同时,高速加工中心将根据不同的加工要求,提供更加灵活的刀具和夹具系统,以满足不同加工任务的需求。
3. 多轴加工技术的应用:多轴加工技术可以同时进行多个方向上的切削,使得曲面加工更加容易和精确。
未来,多轴加工技术将广泛应用于高速加工领域,提高加工效率和加工精度。
4. 先进的刀具材料和涂层技术:刀具是高速加工的关键因素之一。
未来,刀具材料将更加耐磨耐热,刀具涂层技术将更加先进,以满足高速切削的需求。
5. 智能化制造技术的应用:高速加工将与智能化制造技术相结合,实现工艺参数的自动优化和实时监控。
未来,高速加工设备将具有自动化、智能化和可持续发展的特点,提高生产效率和产品质量。
总体来说,高速加工的发展趋势是向着高效、智能和精准的方向发展,以满足不断变化的制造需求。
超高速切削现状和趋势
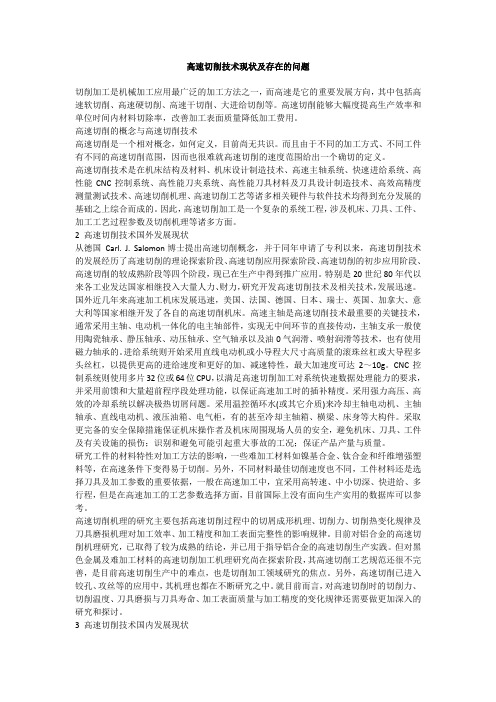
高速切削技术现状及存在的问题切削加工是机械加工应用最广泛的加工方法之一,而高速是它的重要发展方向,其中包括高速软切削、高速硬切削、高速干切削、大进给切削等。
高速切削能够大幅度提高生产效率和单位时间内材料切除率,改善加工表面质量降低加工费用。
高速切削的概念与高速切削技术高速切削是一个相对概念,如何定义,目前尚无共识。
而且由于不同的加工方式、不同工件有不同的高速切削范围,因而也很难就高速切削的速度范围给出一个确切的定义。
高速切削技术是在机床结构及材料、机床设计制造技术、高速主轴系统、快速进给系统、高性能CNC控制系统、高性能刀夹系统、高性能刀具材料及刀具设计制造技术、高效高精度测量测试技术、高速切削机理、高速切削工艺等诸多相关硬件与软件技术均得到充分发展的基础之上综合而成的。
因此,高速切削加工是一个复杂的系统工程,涉及机床、刀具、工件、加工工艺过程参数及切削机理等诸多方面。
2 高速切削技术国外发展现状从德国Carl. J. Salomon博士提出高速切削概念,并于同年申请了专利以来,高速切削技术的发展经历了高速切削的理论探索阶段、高速切削应用探索阶段、高速切削的初步应用阶段、高速切削的较成熟阶段等四个阶段,现已在生产中得到推广应用。
特别是20世纪80年代以来各工业发达国家相继投入大量人力、财力,研究开发高速切削技术及相关技术,发展迅速。
国外近几年来高速加工机床发展迅速,美国、法国、德国、日本、瑞士、英国、加拿大、意大利等国家相继开发了各自的高速切削机床。
高速主轴是高速切削技术最重要的关键技术,通常采用主轴、电动机一体化的电主轴部件,实现无中间环节的直接传动,主轴支承一般使用陶瓷轴承、静压轴承、动压轴承、空气轴承以及油0气润滑、喷射润滑等技术,也有使用磁力轴承的。
进给系统则开始采用直线电动机或小导程大尺寸高质量的滚珠丝杠或大导程多头丝杠,以提供更高的进给速度和更好的加、减速特性,最大加速度可达2~10g。
超高速切削的发展现状
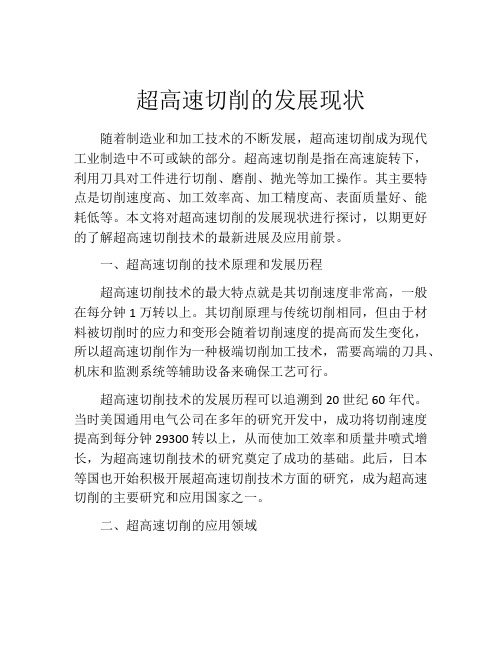
超高速切削的发展现状随着制造业和加工技术的不断发展,超高速切削成为现代工业制造中不可或缺的部分。
超高速切削是指在高速旋转下,利用刀具对工件进行切削、磨削、抛光等加工操作。
其主要特点是切削速度高、加工效率高、加工精度高、表面质量好、能耗低等。
本文将对超高速切削的发展现状进行探讨,以期更好的了解超高速切削技术的最新进展及应用前景。
一、超高速切削的技术原理和发展历程超高速切削技术的最大特点就是其切削速度非常高,一般在每分钟1万转以上。
其切削原理与传统切削相同,但由于材料被切削时的应力和变形会随着切削速度的提高而发生变化,所以超高速切削作为一种极端切削加工技术,需要高端的刀具、机床和监测系统等辅助设备来确保工艺可行。
超高速切削技术的发展历程可以追溯到20世纪60年代。
当时美国通用电气公司在多年的研究开发中,成功将切削速度提高到每分钟29300转以上,从而使加工效率和质量井喷式增长,为超高速切削技术的研究奠定了成功的基础。
此后,日本等国也开始积极开展超高速切削技术方面的研究,成为超高速切削的主要研究和应用国家之一。
二、超高速切削的应用领域随着超高速切削技术的不断发展和完善,其在航空航天、汽车制造、机械制造等领域的应用越来越普及。
目前,超高速切削技术已经广泛应用于以下几个领域:1、航空航天领域在航空航天领域,超高速切削技术被广泛应用于飞机发动机叶片、航空轴承等零部件的加工中。
由于这些零部件具有较高的加工难度和质量要求,而超高速切削技术的高加工效率和高加工质量正好能够满足这些要求。
2、汽车制造领域在汽车制造领域,超高速切削技术被广泛应用于汽车发动机零部件、车轮、减震器等汽车零部件的加工中。
由于该技术具有高效率、高质量、高精度的特点,能够大大提高汽车零部件的生产效率、降低生产成本。
3、机械制造领域在机械制造领域,超高速切削技术被广泛应用于高精度、高难度的零部件加工中。
由于该技术能够大大提高加工效率和精度,能够满足顾客对高精度、高质量零部件的要求,从而提高制造业的竞争优势。
超高速切削的发展现状

超高速切削的发展现状超高速切削是一种先进的切削加工技术,采用高速转速和小切削深度进行切削,能够有效提高切削效率和加工精度。
本文将对超高速切削的发展现状进行详细介绍。
超高速切削技术的发展可以追溯到20世纪60年代,当时由于切削过程容易产生几何形状的误差和表面质量问题,因此一直未能得到广泛应用。
随着计算机数控技术和精密制造技术的快速发展,超高速切削技术在上世纪80年代出现了突破性的进展。
发展初期,超高速切削主要用于加工金属材料,如铝合金、镁合金等,通过提高切削速度和减小切削深度,大大提高了切削效率和表面质量。
随着材料科学和刀具制造技术的进步,超高速切削技术逐渐应用到切削硬度较高的材料,如钢、铁等。
近年来,随着新材料和复杂工件的出现,超高速切削技术迎来了新的发展机遇。
首先是新材料的应用,如高性能陶瓷、纳米材料等,这些材料具有高硬度和高韧性,传统切削技术难以满足对其加工精度和表面质量的要求,而超高速切削技术能够有效解决这一问题。
其次是复杂工件的加工,如汽车发动机缸体、飞机发动机叶片等,这些工件形状复杂,表面精度要求高,传统加工方法效率低、成本高,而超高速切削技术具有快速、高效的优势。
随着超高速切削技术的不断发展,相关设备和工具也在不断更新迭代。
首先是刀具材料的优化,采用纳米材料、复合材料等先进材料制造刀具,能够提高切削效率和切削质量。
其次是机床的改进,采用高刚性、高速度的数控机床,能够满足高速切削的要求。
同时,先进的控制系统和传感器技术的应用,能够实时监测切削过程中的温度、压力等参数,保证整个加工过程的稳定性和安全性。
超高速切削技术的发展带来了巨大的经济效益和社会效益。
首先是加工效率的提高,相比传统切削技术,超高速切削能够大幅度提高切削速度和加工效率,节约了生产时间和成本。
其次是加工精度和表面质量的提升,超高速切削能够实现微米级的精度和纳米级的表面粗糙度,满足了高精度工件的需求。
此外,超高速切削技术还可以减少切削力和切削温度,降低刀具磨损和能量消耗,从而延长刀具寿命,减少了对自然资源的消耗,对环境保护具有积极意义。
高速切削加工技术的现状和发展
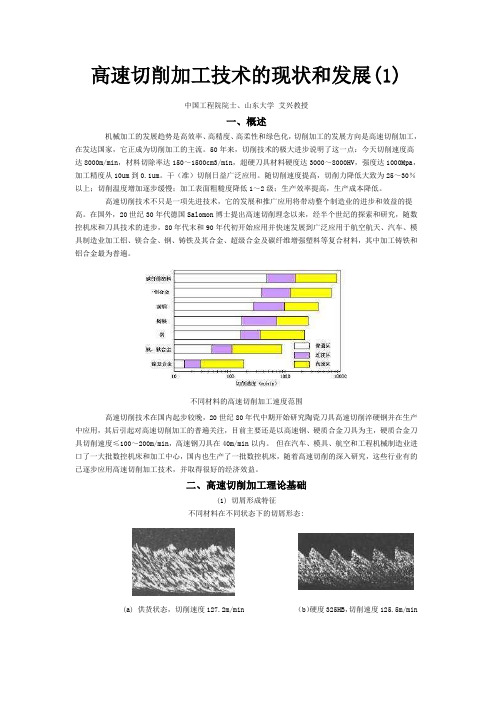
高速切削加工技术的现状和发展(1)中国工程院院士、山东大学艾兴教授一、概述机械加工的发展趋势是高效率、高精度、高柔性和绿色化,切削加工的发展方向是高速切削加工,在发达国家,它正成为切削加工的主流。
50年来,切削技术的极大进步说明了这一点:今天切削速度高达8000m/min,材料切除率达150~1500cm3/min,超硬刀具材料硬度达3000~8000HV,强度达1000Mpa,加工精度从10um到0.1um。
干(准)切削日益广泛应用。
随切削速度提高,切削力降低大致为25~30%以上;切削温度增加逐步缓慢;加工表面粗糙度降低1~2级;生产效率提高,生产成本降低。
高速切削技术不只是一项先进技术,它的发展和推广应用将带动整个制造业的进步和效益的提高。
在国外,20世纪30年代德国Salomon博士提出高速切削理念以来,经半个世纪的探索和研究,随数控机床和刀具技术的进步,80年代末和90年代初开始应用并快速发展到广泛应用于航空航天、汽车、模具制造业加工铝、镁合金、钢、铸铁及其合金、超级合金及碳纤维增强塑料等复合材料,其中加工铸铁和铝合金最为普遍。
不同材料的高速切削加工速度范围高速切削技术在国内起步较晚,20世纪80年代中期开始研究陶瓷刀具高速切削淬硬钢并在生产中应用,其后引起对高速切削加工的普遍关注,目前主要还是以高速钢、硬质合金刀具为主,硬质合金刀具切削速度≤100~200m/min,高速钢刀具在40m/min以内。
但在汽车、模具、航空和工程机械制造业进口了一大批数控机床和加工中心,国内也生产了一批数控机床,随着高速切削的深入研究,这些行业有的已逐步应用高速切削加工技术,并取得很好的经济效益。
二、高速切削加工理论基础(1) 切屑形成特征不同材料在不同状态下的切屑形态:(a) 供货状态,切削速度127.2m/min (b)硬度325HB,切削速度125.5m/min连续带状切屑(D.LEE)锯齿状切屑(c)硬度325HB,切削速度250m/min锯齿状切屑(d)硬度325HB,切削速度2600m/min即将分离的锯齿状切屑高速切削不同状态AISI4340钢(40CrNiMoA)时的切屑形态(纵截面微观照片)((b)、(c)、(d)从komarduri)切削渗碳淬硬20CrMnTi钢(HRC60~62)在100~110m/min时的切屑形貌工件材料及其性能和切削条件对切屑形态起主要作用,其中工件材料及其性能有决定性的影响。
超高速加工技术的现状及发展趋势
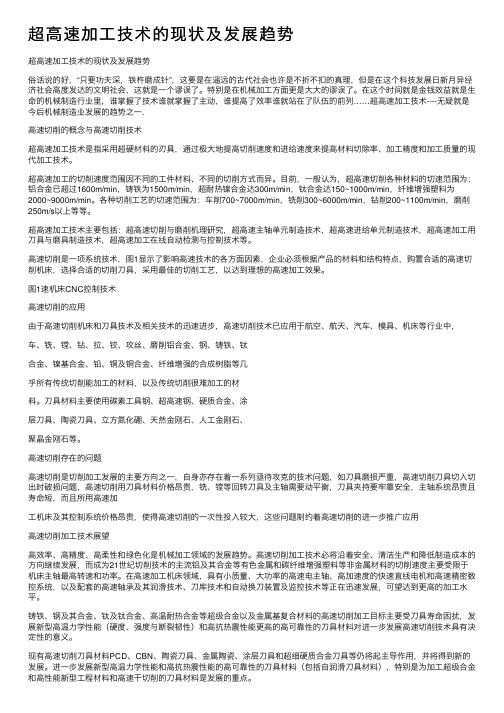
超⾼速加⼯技术的现状及发展趋势超⾼速加⼯技术的现状及发展趋势俗话说的好,“只要功夫深,铁杵磨成针”,这要是在遥远的古代社会也许是不折不扣的真理,但是在这个科技发展⽇新⽉异经济社会⾼度发达的⽂明社会,这就是⼀个谬误了。
特别是在机械加⼯⽅⾯更是⼤⼤的谬误了。
在这个时间就是⾦钱效益就是⽣命的机械制造⾏业⾥,谁掌握了技术谁就掌握了主动,谁提⾼了效率谁就站在了队伍的前列……超⾼速加⼯技术----⽆疑就是今后机械制造业发展的趋势之⼀.⾼速切削的概念与⾼速切削技术超⾼速加⼯技术是指采⽤超硬材料的刃具,通过极⼤地提⾼切削速度和进给速度来提⾼材料切除率、加⼯精度和加⼯质量的现代加⼯技术。
超⾼速加⼯的切削速度范围因不同的⼯件材料、不同的切削⽅式⽽异。
⽬前,⼀般认为,超⾼速切削各种材料的切速范围为:铝合⾦已超过1600m/min,铸铁为1500m/min,超耐热镍合⾦达300m/min,钛合⾦达150~1000m/min,纤维增强塑料为2000~9000m/min。
各种切削⼯艺的切速范围为:车削700~7000m/min,铣削300~6000m/min,钻削200~1100m/min,磨削250m/s以上等等。
超⾼速加⼯技术主要包括:超⾼速切削与磨削机理研究,超⾼速主轴单元制造技术,超⾼速进给单元制造技术,超⾼速加⼯⽤⼑具与磨具制造技术,超⾼速加⼯在线⾃动检测与控制技术等。
⾼速切削是⼀项系统技术,图1显⽰了影响⾼速技术的各⽅⾯因素,企业必须根据产品的材料和结构特点,购置合适的⾼速切削机床,选择合适的切削⼑具,采⽤最佳的切削⼯艺,以达到理想的⾼速加⼯效果。
图1速机床CNC控制技术⾼速切削的应⽤由于⾼速切削机床和⼑具技术及相关技术的迅速进步,⾼速切削技术已应⽤于航空、航天、汽车、模具、机床等⾏业中,车、铣、镗、钻、拉、铰、攻丝、磨削铝合⾦、钢、铸铁、钛合⾦、镍基合⾦、铅、铜及铜合⾦、纤维增强的合成树脂等⼏乎所有传统切削能加⼯的材料,以及传统切削很难加⼯的材料。
中国刀具与切削加工技术的发展现状与趋势
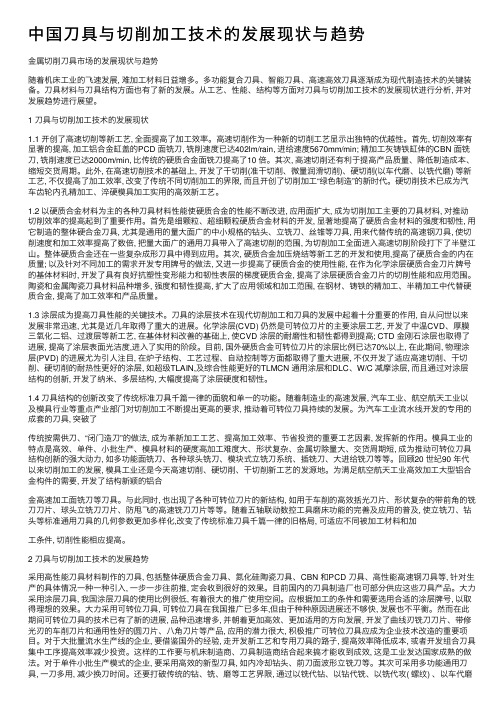
中国⼑具与切削加⼯技术的发展现状与趋势⾦属切削⼑具市场的发展现状与趋势随着机床⼯业的飞速发展, 难加⼯材料⽇益增多。
多功能复合⼑具、智能⼑具、⾼速⾼效⼑具逐渐成为现代制造技术的关键装备。
⼑具材料与⼑具结构⽅⾯也有了新的发展。
从⼯艺、性能、结构等⽅⾯对⼑具与切削加⼯技术的发展现状进⾏分析, 并对发展趋势进⾏展望。
1 ⼑具与切削加⼯技术的发展现状1.1 开创了⾼速切削等新⼯艺, 全⾯提⾼了加⼯效率。
⾼速切削作为⼀种新的切削⼯艺显⽰出独特的优越性。
⾸先, 切削效率有显著的提⾼, 加⼯铝合⾦缸盖的PCD ⾯铣⼑, 铣削速度已达402lm/rain, 进给速度5670mm/min; 精加⼯灰铸铁缸体的CBN ⾯铣⼑, 铣削速度已达2000m/min, ⽐传统的硬质合⾦⾯铣⼑提⾼了10 倍。
其次, ⾼速切削还有利于提⾼产品质量、降低制造成本、缩短交货周期。
此外, 在⾼速切削技术的基础上, 开发了⼲切削(准⼲切削、微量润滑切削)、硬切削(以车代磨、以铣代磨) 等新⼯艺, 不仅提⾼了加⼯效率, 改变了传统不同切削加⼯的界限, ⽽且开创了切削加⼯“绿⾊制造”的新时代。
硬切削技术已成为汽车齿轮内孔精加⼯、淬硬模具加⼯实⽤的⾼效新⼯艺。
1.2 以硬质合⾦材料为主的各种⼑具材料性能使硬质合⾦的性能不断改进, 应⽤⾯扩⼤, 成为切削加⼯主要的⼑具材料, 对推动切削效率的提⾼起到了重要作⽤。
⾸先是细颗粒、超细颗粒硬质合⾦材料的开发, 显著地提⾼了硬质合⾦材料的强度和韧性, ⽤它制造的整体硬合⾦⼑具, 尤其是通⽤的量⼤⾯⼴的中⼩规格的钻头、⽴铣⼑、丝锥等⼑具, ⽤来代替传统的⾼速钢⼑具, 使切削速度和加⼯效率提⾼了数倍, 把量⼤⾯⼴的通⽤⼑具带⼊了⾼速切削的范围, 为切削加⼯全⾯进⼊⾼速切削阶段打下了半壁江⼭。
整体硬质合⾦还在⼀些复杂成形⼑具中得到应⽤。
其次, 硬质合⾦加压烧结等新⼯艺的开发和使⽤,提⾼了硬质合⾦的内在质量; 以及针对不同加⼯的需求开发专⽤牌号的做法, ⼜进⼀步提⾼了硬质合⾦的使⽤性能, 在作为化学涂层硬质合⾦⼑⽚牌号的基体材料时, 开发了具有良好抗塑性变形能⼒和韧性表层的梯度硬质合⾦, 提⾼了涂层硬质合⾦⼑⽚的切削性能和应⽤范围。
超高速切削的发展现状

超高速切削的发展现状金属切削加工已进入了一个以高速切削为代表的新的发展阶段,由于高速切削加工能极大地提高材料的切除率和零件的加工质量,降低加工成本,因而成为当今金属切削加工的发展方向之一。
高速切削刀具技术是高速切削加工的一个关键技术,它包括高速切削刀具材料、刀柄系统、刀具系统动平衡技术、刀具监测技术等。
本文就作一概述。
1.高速切削加工对刀具系统的要求所谓刀具系统是指由刀柄、夹头和切削刀具所组成的完整的刀具体系,刀柄与机床主轴相连,切削刀具通过夹头装入刀柄之中。
要使刀具系统能在高速下进行切削加工,应满足以下基本条件:较高的系统精度系统精度包括系统定位夹持精度和刀具重复定位精度,前者指刀具与刀柄、刀柄与机床主轴的连接精度;后者指每次换刀后刀具系统精度的一致性。
刀具系统具有较高的系统精度,才能保证高速加工条件下刀具系统应有的静态和动态稳定性。
较高的系统刚度刀具系统的静、动刚度是影响加工精度及切削性能的重要因素。
刀具系统刚度不足会导致刀具系统振动,从而降低加工精度,并加剧刀具的磨损,降低刀具的使用寿命。
较好的动平衡性高速切削加工条件下,微小质量的不平衡都会造成巨大的离心力,在加工过程中引起机床的急剧振动。
因此,高速刀具系统的动平衡非常重要。
2.传统实心长刀柄结构存在的问题目前,在数控铣床、数控镗床和加工中心上使用的传统刀柄是标准7:24锥度实心长刀柄。
这种刀柄与机床主轴的连接只是靠锥面定位,主轴端面与刀柄法兰端面间有较大间隙。
这种刀柄结构在高速切削条件下会出现下列问题:刀具动、静刚度低刀具高速旋转时,由于离心力的作用,主轴锥孔和刀柄均会发生径向膨胀,膨胀量大小随旋转半径和转速的增大而增大。
这就会造成刀柄的膨胀量小于主轴锥孔的膨胀量而出现配合间隙,使得本来只靠锥面结合的低刚性连接的刚度进一步降低。
动平衡性差标准7:24锥度柄较长,很难实现全长无间隙配合,一般只要求配合前段70%以上接触,而后段往往会有一定间隙。
高速切削加工的发展及需求

高速切削加工的发展及需求高速切削加工是当代先进制造技术的重要组成部分,拥有高效率、高精度及高表面质量等特征。
本文介绍此技术的定义、发展现状、适用领域以及中国的需求情况。
高速切削加工的定义高速切削加工是面向21世纪的一项高新技术,它以高效率、高精度和高表面质量为基本特征,在汽车工业、航空航天、模具制造和仪器仪表等行业中获得了愈来愈广泛的应用,并已取得了重大的技术经济效益,是当代先进制造技术的重要组成部分。
高速切削是实现高效率制造的核心技术,工序的集约化和设备的通用化使之具有很高的生产效率。
可以说,高速切削加工是一种不增加设备数量而大幅度提高加工效率所必不可少的技术。
高速切削加工的优点主要在于:提高生产效率、提高加工精度及降低切削阻力。
有关高速切削加工的含义,目前尚无统一的认识,通常有如下几种观点:切削速度很高,通常认为其速度超过普通切削的5-10倍;机床主轴转速很高,一般将主轴转速在10000-20000r/min 以上定为高速切削;进给速度很高,通常达15-50m/min,最高可达90m/min;对于不同的切削材料和所釆用的刀具材料,高速切削的含义也不尽相同;切削过程中,刀刃的通过频率(Tooth Passing Frequency)接近于“机床-刀具-工件”系统的主导自然频率(Dominant Natural Frequency)时,可认为是高速切削。
可见高速切削加工是一个综合的概念。
1992年,德国Darmstadt工业大学的H. Schulz教授在CIRP上提出了高速切削加工的概念及其涵盖的范围。
认为对于不同的切削对象,过渡区(Transition)即为通常所谓的高速切削範围,这也是当时金属切削工艺相关的技术人员所期待或者可望实现的切削速度。
高速切削加工技术现状高速切削加工对机床、刀具和切削工艺等方面都有一些具体的要求。
下面分别从这几个方面阐述高速切削加工技术的发展现状和趋势。
机床设备现阶段,为了实现高速切削加工,一般釆用高柔性的高速数控机床、加工中心,也有釆用专用的高速铣、钻床。
高速高效切削加工技术的现状及发展趋势

高速高效切削加工技术的现状及发展趋势一、前言目前,我国已成为世界飞机零部件的重要转包生产国,波音、麦道、空客等世界著名飞机制造公司都在我国转包生产从尾翼、机身、舱门到发动机等各种零部件,这些飞机零部件的加工生产必须采用先进的加工装备和加工工艺。
为此,国内各飞机制造公司均进行了大规模的技术改造,引进了大量国外先进的加工装备,使我国的飞机制造业设备的数控化率越来越高。
与此同时,大量高速、高效、柔性、复合、环保的国外切削加工新技术不断涌现,使切削加工技术发生了根本的变化。
刀具在航空航天加工领域的应用技术进入了以发展高速切削、开发新的切削工艺和加工方法、提供成套技术为特征的新阶段。
与此形成鲜明对比的是,我国的装备制造业和以制造业为主要服务对象的传统的工具工业却无法满足航空航天工业对现代制造装备和先进加工工艺的要求。
下面结合我国航空航天工业加工技术的现状及发展趋势,着重介绍我国高效、高速切削刀具的生产应用情况,对我国工具工业的发展现状和存在的问题提出自己的看法。
二、航空航天工业加工技术的现状及发展趋势1.航空结构件材料的发展趋势及其特点①以整体件为代表的铝合金结构件为了提高零件的可靠性、降低成本和减轻重量,传统的铆接结构逐步被整体薄壁的机加工结构件所代替。
这类零件由于大部分是用整体实心铝合金材料制成的薄壁、细筋结构件,70%~95%的材料要在加工中去除掉,而高速切削产生的热量少、切削力小、零件变形小,因此提高生产效率的唯一途径是采用四轴或五轴联动机床进行高速铣削加工。
②以钛基和镍基合金零件为代表的难切削材料零件由于钛(镍)合金具有比强度高、热强度好、化学活性大等特点,目前飞机发动机重要部件采用钛基和镍基合金材料的逐渐增多。
采用高速切削后,其切削速度可提高到100m/min以上,为常规切削速度的10倍。
这类材料的加工特点是:切削力大、切削温度高、加工硬化和粘刀现象严重、刀具易磨损。
③以碳纤维复合材料零件为代表的复合材料结构件复合材料现已成为新一代飞机机体结构主要材料之一,如飞机上的大型整体成形的翼面壁板、带纵墙的整体下翼面等。
超快速切削技术的挑战与前景展望
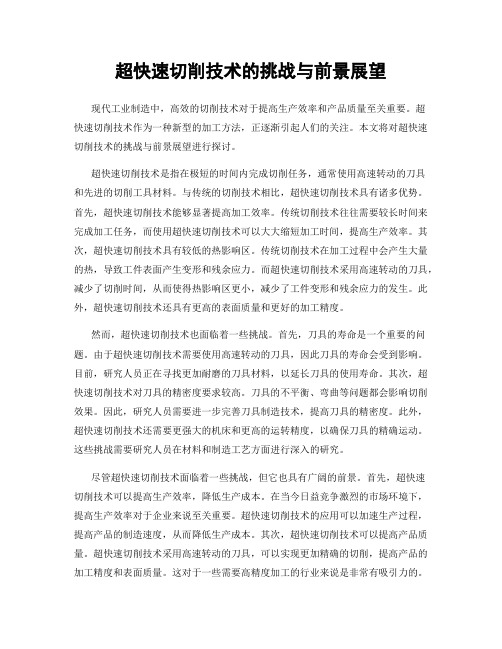
超快速切削技术的挑战与前景展望现代工业制造中,高效的切削技术对于提高生产效率和产品质量至关重要。
超快速切削技术作为一种新型的加工方法,正逐渐引起人们的关注。
本文将对超快速切削技术的挑战与前景展望进行探讨。
超快速切削技术是指在极短的时间内完成切削任务,通常使用高速转动的刀具和先进的切削工具材料。
与传统的切削技术相比,超快速切削技术具有诸多优势。
首先,超快速切削技术能够显著提高加工效率。
传统切削技术往往需要较长时间来完成加工任务,而使用超快速切削技术可以大大缩短加工时间,提高生产效率。
其次,超快速切削技术具有较低的热影响区。
传统切削技术在加工过程中会产生大量的热,导致工件表面产生变形和残余应力。
而超快速切削技术采用高速转动的刀具,减少了切削时间,从而使得热影响区更小,减少了工件变形和残余应力的发生。
此外,超快速切削技术还具有更高的表面质量和更好的加工精度。
然而,超快速切削技术也面临着一些挑战。
首先,刀具的寿命是一个重要的问题。
由于超快速切削技术需要使用高速转动的刀具,因此刀具的寿命会受到影响。
目前,研究人员正在寻找更加耐磨的刀具材料,以延长刀具的使用寿命。
其次,超快速切削技术对刀具的精密度要求较高。
刀具的不平衡、弯曲等问题都会影响切削效果。
因此,研究人员需要进一步完善刀具制造技术,提高刀具的精密度。
此外,超快速切削技术还需要更强大的机床和更高的运转精度,以确保刀具的精确运动。
这些挑战需要研究人员在材料和制造工艺方面进行深入的研究。
尽管超快速切削技术面临着一些挑战,但它也具有广阔的前景。
首先,超快速切削技术可以提高生产效率,降低生产成本。
在当今日益竞争激烈的市场环境下,提高生产效率对于企业来说至关重要。
超快速切削技术的应用可以加速生产过程,提高产品的制造速度,从而降低生产成本。
其次,超快速切削技术可以提高产品质量。
超快速切削技术采用高速转动的刀具,可以实现更加精确的切削,提高产品的加工精度和表面质量。
超高速切削的发展现状整理

超高速切削的发展现状整理超高速切削的进展现状金属切削加工已进入了一个以高速切削为代表的新的进展阶段,由于高速切削加工能极大地提高材料的切除率和零件的加工质量,降低加工成本,因而成为当今金属切削加工的进展方向之一。
高速切削刀具技术是高速切削加工的一个关键技术,它包括高速切削刀具材料、刀柄系统、刀具系统动平衡技术、刀具监测技术等。
本文就作一概述。
1. 高速切削加工对刀具系统的要求所谓刀具系统是指由刀柄、夹头和切削刀具所组成的完整的刀详细系,刀柄与机床主轴相连,切削刀具通过夹头装入刀柄之中。
要使刀具系统能在高速下进行切削加工,应满意以下基本条件:较高的系统精度系统精度包括系统定位夹持精度和刀具重复定位精度,前者指刀具与刀柄、刀柄与机床主轴的连接精度;后者指每次换刀后刀具系统精度的全都性。
刀具系统具有较高的系统精度,才能保证高速加工条件下刀具系统应有的静态和动态稳定性。
较高的系统刚度刀具系统的静、动刚度是影响加工精度及切削性能的重要因素。
刀具系统刚度不足会导致刀具系统振动,从而降低加工精度,并加剧刀具的磨损,降低刀具的使用寿命。
较好的动平衡性高速切削加工条件下,微小质量的不平衡都会造成巨大的离心力,在加工过程中引起机床的急剧振动。
因此,高速刀具系统的动平衡特别重要。
2. 传统实心长刀柄结构存在的问题目前,在数控铣床、数控镗床和加工中心上使用的传统刀柄是标准7:24锥度实心长刀柄。
这种刀柄与机床主轴的连接只是靠锥面定位,主轴端面与刀柄法兰端面间有较大间隙。
这种刀柄结构在高速切削条件下会消失下列问题:刀具动、静刚度低刀具高速旋转时,由于离心力的作用,主轴锥孔和刀柄均会发生径向膨胀,膨胀量大小随旋转半径和转速的增大而增大。
这就会造成刀柄的膨胀量小于主轴锥孔的膨胀量而消失协作间隙,使得原来只靠锥面结合的低刚性连接的刚度进一步降低。
动平衡性差标准7:24锥度柄较长,很难实现全长无间隙协作,一般只要求协作前段70%以上接触,而后段往往会有肯定间隙。
高速切削加工技术的现状和发展
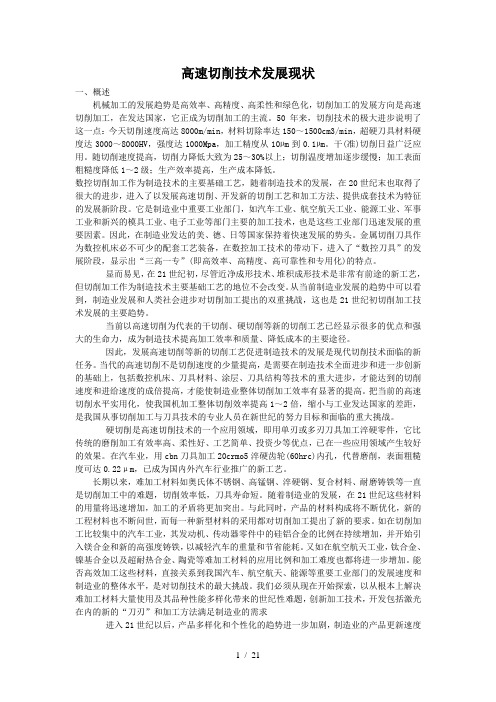
高速切削技术发展现状一、概述机械加工的发展趋势是高效率、高精度、高柔性和绿色化,切削加工的发展方向是高速切削加工,在发达国家,它正成为切削加工的主流。
50年来,切削技术的极大进步说明了这一点:今天切削速度高达8000m/min,材料切除率达150~1500cm3/min,超硬刀具材料硬度达3000~8000HV,强度达1000Mpa,加工精度从10µm到0.1µm。
干(准)切削日益广泛应用。
随切削速度提高,切削力降低大致为25~30%以上;切削温度增加逐步缓慢;加工表面粗糙度降低1~2级;生产效率提高,生产成本降低。
数控切削加工作为制造技术的主要基础工艺,随着制造技术的发展,在20世纪末也取得了很大的进步,进入了以发展高速切削、开发新的切削工艺和加工方法、提供成套技术为特征的发展新阶段。
它是制造业中重要工业部门,如汽车工业、航空航天工业、能源工业、军事工业和新兴的模具工业、电子工业等部门主要的加工技术,也是这些工业部门迅速发展的重要因素。
因此,在制造业发达的美、德、日等国家保持着快速发展的势头。
金属切削刀具作为数控机床必不可少的配套工艺装备,在数控加工技术的带动下,进入了“数控刀具”的发展阶段,显示出“三高一专”(即高效率、高精度、高可靠性和专用化)的特点。
显而易见,在21世纪初,尽管近净成形技术、堆积成形技术是非常有前途的新工艺,但切削加工作为制造技术主要基础工艺的地位不会改变。
从当前制造业发展的趋势中可以看到,制造业发展和人类社会进步对切削加工提出的双重挑战,这也是21世纪初切削加工技术发展的主要趋势。
当前以高速切削为代表的干切削、硬切削等新的切削工艺已经显示很多的优点和强大的生命力,成为制造技术提高加工效率和质量、降低成本的主要途径。
因此,发展高速切削等新的切削工艺促进制造技术的发展是现代切削技术面临的新任务。
当代的高速切削不是切削速度的少量提高,是需要在制造技术全面进步和进一步创新的基础上,包括数控机床、刀具材料、涂层、刀具结构等技术的重大进步,才能达到的切削速度和进给速度的成倍提高,才能使制造业整体切削加工效率有显著的提高。
高速切削技术在金属加工中的应用与未来发展趋势
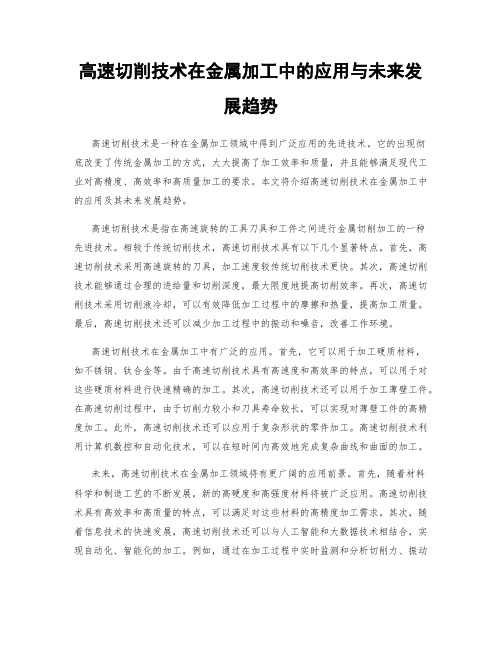
高速切削技术在金属加工中的应用与未来发展趋势高速切削技术是一种在金属加工领域中得到广泛应用的先进技术。
它的出现彻底改变了传统金属加工的方式,大大提高了加工效率和质量,并且能够满足现代工业对高精度、高效率和高质量加工的要求。
本文将介绍高速切削技术在金属加工中的应用及其未来发展趋势。
高速切削技术是指在高速旋转的工具刀具和工件之间进行金属切削加工的一种先进技术。
相较于传统切削技术,高速切削技术具有以下几个显著特点。
首先,高速切削技术采用高速旋转的刀具,加工速度较传统切削技术更快。
其次,高速切削技术能够通过合理的进给量和切削深度,最大限度地提高切削效率。
再次,高速切削技术采用切削液冷却,可以有效降低加工过程中的摩擦和热量,提高加工质量。
最后,高速切削技术还可以减少加工过程中的振动和噪音,改善工作环境。
高速切削技术在金属加工中有广泛的应用。
首先,它可以用于加工硬质材料,如不锈钢、钛合金等。
由于高速切削技术具有高速度和高效率的特点,可以用于对这些硬质材料进行快速精确的加工。
其次,高速切削技术还可以用于加工薄壁工件。
在高速切削过程中,由于切削力较小和刀具寿命较长,可以实现对薄壁工件的高精度加工。
此外,高速切削技术还可以应用于复杂形状的零件加工。
高速切削技术利用计算机数控和自动化技术,可以在短时间内高效地完成复杂曲线和曲面的加工。
未来,高速切削技术在金属加工领域将有更广阔的应用前景。
首先,随着材料科学和制造工艺的不断发展,新的高硬度和高强度材料将被广泛应用。
高速切削技术具有高效率和高质量的特点,可以满足对这些材料的高精度加工需求。
其次,随着信息技术的快速发展,高速切削技术还可以与人工智能和大数据技术相结合,实现自动化、智能化的加工。
例如,通过在加工过程中实时监测和分析切削力、振动等参数,可以实现工艺优化和故障预测,提高加工效率和质量。
此外,高速切削技术还可以与增材制造技术相结合,实现复合加工,进一步拓展应用领域。
高速切削加工工艺的现状与优化趋势
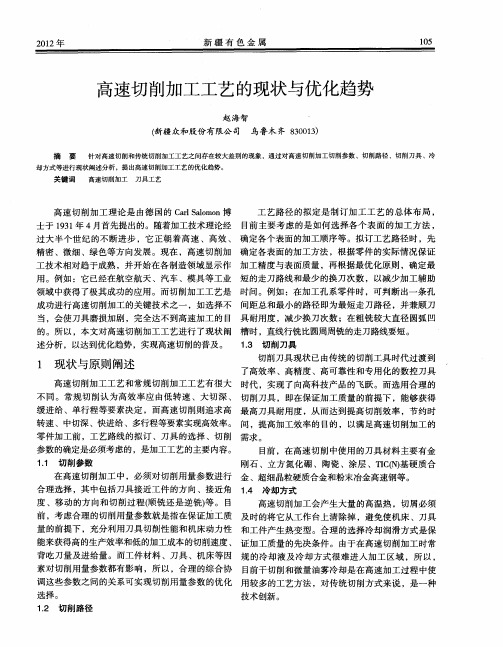
精密、微细 、绿色等方 向发展 。现在 ,高速切削加 确定各表面的加工方法 ,根据零件的实际情况保证 工技术相对趋于成熟 ,并开始在各制造领域显示作 加工精度与表面质量 ,再根据最优化原则 ,确定最 用。例如 :它已经在航空航天 、汽车、模具等工业 短 的走刀路线和最少 的换刀次数 ,以减少加工辅助
热冲击性等优化性能要求 。高速切削要求刀具结构 吃刀量等参数 的选择 。而进给量是精加工时决定生 和刀具夹紧机构具有更严格的要求 ,以确保生产安 产 率 的主要 因素 ,增 大进 给 量将 会 增 大加 工 表 面 的 全的可靠性 。可综合以下几个要点进行考虑 : 粗 糙度数 值 ,所 以要 慎重 选择 与协调 。 首先选择刀具材料 :在高速切削加工系统 中优 主要 考 虑 刀具 的影 响 ,考虑 工 件 材料 的 加工 性 先选 用 硬质 合金 ,甚 至超 细粒 度 硬质 合 金 或具 有 涂 能 。在确 定切 削用 量 参数 时 ,首 先 应 采用 尽 可 能大 层技 术等 材料 的高性 能刀具 ,以提 高使 用 的可靠性 。 的背吃刀量 ,其次选用较大 的进给量 ,最后确定合 其 次 选择 刀 具结 构 :根 据 零 件 的结 构 和尺 寸选 理 的切 削速度 。 择合适的刀具与其相适应 ,优先选用机夹式可转位 总之 ,无论在何种加工场合 ,都应在保证加工 结构 ,甚 至复合 结构 或专用 结构 刀具 ,以减 少换 刀 、 质 量 的前 提下 ,认 真 选 择切 削参 数 ,并兼 顾 切 削效 对 刀和刃磨 的时间 。 率 、经济性和加工成本。而具体数值的确定 ,可根 最后选择刀柄结构 :保证刀具能够迅速 、准确 据 实 际情 况及 机 床说 明 书 、切 削用 量 手册 ,并结 合 地安装到机床主轴或刀库 中去 ,优先选用标准化或 加工经验而确定 。综合协调这些参数之间的关系可 系 列化 刀柄 ,并 且尽 可能 选用 短 刀柄 ,以提 高刀 具 实 现切 削用 量参数 的优 化选择 。 的 刚性 。 22 切 削路径 优化 . 般 情 况下 ,选 用 高 耐用 度 、高精 度 和专 用 化 切削路径的选择与优化在高速切削加工 中,除 的刀具 ,会增加刀具使用成本 ,但是 ,它却提高 了 了刀具 材 料 和刀 具几 何参 数 的选 择 外 ,还 要 采取 不 零件 的加工 效率 和加 工 质 量 ,可 以使 整 个 加 工成 本 同的切 削路径 才能 得到 较好 的切削效 果 。 大大降低。因此 ,在加工系统 中选择合理的切削刀 切削路径优化 的目的是提高刀具耐用度 ,提高 具 ,利用刀具 自身优势来完成高速切削加工。 切削效率 ,获得最小的加工变形 ,提高机床走刀利 24 冷却 方式优 化 . 用 率 ,充 分发 挥 高速 加工 的优 势 。 传 统 切 削加 工 的冷 却方 式 一 般采 用 冷却 液 ,这 ( 走刀方 向的优化在走刀方 向的选择上 ,以曲 1 ) 对加 工环境 带来危 害 ,不符 合绿 色加工 的概 念范 畴 。 面平坦 性 为评 价 准则 ,确定 不 同 的走刀 方 向选 取方 而 高速 切 削 加 工 可采 用 干 式 ( 干 式 ) 削 技 术 ,不 准 切 案 ;对于 曲率变化大的曲面 以最大 曲率半径方向为 采用 切 削液 或采 用微 量 的切削 液 ,这可 以提 高切 屑 最 优进 给 方 向 ,对 曲率 变化 小 的面 , 以单 条 刀 轨平 的回收利用率 ,降低切削成本 、降低切削过程对环 均 长度最 长 为原则选 择走 刀方 向。 境的危害 、提高切屑的回收利用率等。 () 位轨 迹 生成按 照 刀位路 径 尽可 能简 化 ,尽 2刀 25 研究 与展 望 . 量走直线 ,路径尽量光滑的要求选择加工策略 ,选 高速切削加工技术系统而复杂 ,离不开机床 、 择合适 的插补方 法 ,保证加工面残 留高度 的要求 , 刀具 、夹具 及其 控制 软件 的配 合 。该 工 艺 的许 多 问 采 用过 渡 圆弧 的 方法处 理 加 工 干涉 区 ,样 在 加工 时 题现在 并没 有得 到充分 解决 ,其发 展前 景十 分广 阔 。 就不需要减速 ,提高加工效率 。 随着 技术 的 日益 成熟 ,特 别是 高 速 主轴 的 出 现 ,切 () 性加 减速 和 断刀 的几率 。选取 合适 的加减 3柔 削速度将进一步提高。但也要追求高速切削转速和 速方式 ,减少启动冲击 ,保持机床 的精度 ,减少刀 进给速度 的最佳参数 ,简化工序 ,这样高速切削的 具 颤振 。 “ 高速 ”才 能充分 发挥 出来 。刀具 的磨 损 以及 轴承 技 23 切 削刀具 优化 . 术将会是今后一段时间内制约高速切削发展的关键 高 速切 削 刀具 是 高速 加 工工 艺 系 统 中最 活跃 的 因素 。 要素 ,是实现高速加工 的关键技术之一 。高速切削
- 1、下载文档前请自行甄别文档内容的完整性,平台不提供额外的编辑、内容补充、找答案等附加服务。
- 2、"仅部分预览"的文档,不可在线预览部分如存在完整性等问题,可反馈申请退款(可完整预览的文档不适用该条件!)。
- 3、如文档侵犯您的权益,请联系客服反馈,我们会尽快为您处理(人工客服工作时间:9:00-18:30)。
高速切削加工技术的现状和发展(1)中国工程院院士、山东大学艾兴教授一、概述机械加工的发展趋势是高效率、高精度、高柔性和绿色化,切削加工的发展方向是高速切削加工,在发达国家,它正成为切削加工的主流。
50年来,切削技术的极大进步说明了这一点:今天切削速度高达8000m/min,材料切除率达150~1500cm3/min,超硬刀具材料硬度达3000~8000HV,强度达1000Mpa,加工精度从10um到0.1um。
干(准)切削日益广泛应用。
随切削速度提高,切削力降低大致为25~30%以上;切削温度增加逐步缓慢;加工表面粗糙度降低1~2级;生产效率提高,生产成本降低。
高速切削技术不只是一项先进技术,它的发展和推广应用将带动整个制造业的进步和效益的提高。
在国外,20世纪30年代德国Salomon博士提出高速切削理念以来,经半个世纪的探索和研究,随数控机床和刀具技术的进步,80年代末和90年代初开始应用并快速发展到广泛应用于航空航天、汽车、模具制造业加工铝、镁合金、钢、铸铁及其合金、超级合金及碳纤维增强塑料等复合材料,其中加工铸铁和铝合金最为普遍。
不同材料的高速切削加工速度范围高速切削技术在国内起步较晚,20世纪80年代中期开始研究陶瓷刀具高速切削淬硬钢并在生产中应用,其后引起对高速切削加工的普遍关注,目前主要还是以高速钢、硬质合金刀具为主,硬质合金刀具切削速度≤100~200m/min,高速钢刀具在40m/min以内。
但在汽车、模具、航空和工程机械制造业进口了一大批数控机床和加工中心,国内也生产了一批数控机床,随着高速切削的深入研究,这些行业有的已逐步应用高速切削加工技术,并取得很好的经济效益。
二、高速切削加工理论基础(1) 切屑形成特征不同材料在不同状态下的切屑形态:(a) 供货状态,切削速度127.2m/min (b)硬度325HB,切削速度125.5m/min连续带状切屑(D.LEE)锯齿状切屑(c)硬度325HB,切削速度250m/min锯齿状切屑(d)硬度325HB,切削速度2600m/min即将分离的锯齿状切屑高速切削不同状态AISI4340钢(40CrNiMoA)时的切屑形态(纵截面微观照片)((b)、(c)、(d)从komarduri)切削渗碳淬硬20CrMnTi钢(HRC60~62)在100~110m/min时的切屑形貌工件材料及其性能和切削条件对切屑形态起主要作用,其中工件材料及其性能有决定性的影响。
一般低硬度和高热物理性能KρC(导热性K、密度ρ和比热容C的乘积)的工件材料如铝合金、低碳钢和未淬硬的钢与合金钢等,在很大切削速度范围内容易形成连续带状切屑。
硬度较高和低热物理特性KρC的工件材料,如热处理的钢与合金钢、钛合金和超级合金,在很宽的切削速度范围均形成锯齿状切屑,随切削速度的提高,锯齿化程度增高,直至形成分离的单元切屑。
(2) 切削力学图中Fs为剪切力,Fm为高速切削时切屑动量改变所需的作用力;Ff为作用在后刀面上的摩擦力。
直角切削时剪切角和前刀面受力简图剪切角φ和摩擦系数μ(=tgβ)的关系可用Merchant公式估算实验证明在高速切削时计算的φ角与测量的结果有良好的一致性高速切削4340钢(40CrNiMoA)时剪切角φ的计算值与测量值的比较(Recht)在高速切削范围内,随切削速度提高,摩擦系数减少,剪切角φ增大,切削力降低。
Al2O3基陶瓷刀具端铣调质45#钢时的切削力(3)切削热和切削温度切削时的热量主要来自剪切变形功、刀-屑和刀-工件摩擦功。
干切时,切削热主要由切屑、工件和刀具传出去,周围介质传出小于1%。
切削时热的产生与传出立铣铝合金时,流入各部分的切削热量Al2O3基陶瓷刀具端铣淬硬钢T10A(HRC58~65)时的切削温度切削速度对切削温度的影响试验结果。
随切削速度的提高,开始切削温度升高很快,但达到一定速度后,切削温度的升高逐渐缓慢,甚至很少升高。
(4)表面粗糙度随V增加,加工表面粗糙度有所减少。
实验用的ACE-V500加工中心最高转数为10000r/min,其一段和二阶固有频率分别为50Hz(3000r/min)和113Hz(6780r/min)。
涂层立铣刀铣削沟槽时转速对加工粗糙度的影响高速切削加工技术的现状和发展(2)中国工程院院士、山东大学艾兴教授三、高速切削刀具材料(1) 高速切削刀具材料∙金刚石∙天然金刚石∙聚晶金刚石(PCD)∙人工合成单晶金刚石∙金刚石涂层∙立方氮化硼(PCBN)∙陶瓷刀具:有氧化铝(Al2O3)基和氮化硅(Si3N4)基两大类∙TiC(N)基硬质合金(金属陶瓷)∙涂层刀具——优异的高速钢、WC基、TiC(N)基硬质合金和陶瓷为基体。
复合涂层。
a)硬涂层:CVD的TiCN+Al2O3+TiN;TiCN+Al2O3;TiCN+Al2O3+HfN,TiN+Al2O3和TiCN、TiB2等。
PVD的TiAlN/TiN、TiAlN等b)软涂层:硫族化合物(MoS2,WS2)涂层的高速钢刀具∙超细晶粒硬质合金:细晶粒(0.2-0.5um)的WC基硬质合金,添加TaC、NbC等∙粉末冶金高速钢(PM HSS)和高性能高速钢HSS-E(2) 高速切削刀具材料的合理应用高速切削时对不同工件材料要选用与其合理匹配的刀具材料和适应的加工方式等切削条件,才能获得最佳的切削效果。
没有万能的刀具材料。
刀具材料性能硬度大小:金刚石PCD>立方氮化硼 PCBN>Al2O3基>Si3N4基>TiC(N)基硬质合金>WC基超细晶粒硬质合金>高速钢HSS。
抗弯强度大小:HSS>WC基>TiC(N)基>Si3N4基>Al2O3基>PCD>PCBN。
断裂韧性大小:HSS>WC基>TiC(N)基>PCBN>PCD>Si3N4基>Al2O3基。
耐热性:PCD700℃-800℃;PCBN1400℃-1500℃;陶瓷1100℃-1200℃;TiC(N)基900℃-1100℃;超细晶粒硬质合金WC基800℃-900℃;HSS600℃-700℃。
高速切削刀具材料合理应用加工铝合金:金刚石最适于高速切削。
但复杂刀具可用整体超细晶粒硬质合金及其涂层刀具高速加工结构铝及其合金。
加工钢和铸铁及其合金:Al2O3基陶瓷刀具适于软、硬高速切削;PCBN适于45-65HRC以上高硬钢的高速切削;Si3N4和PCBN更适于铸铁及其合金的高速切削,但不宜于切削以铁素体为主的钢铁;WC基超细硬质合金及其TiCN、TiAlN、TiN涂层刀具和TiC(N)基硬质合金刀具,特别是整体复杂刀具可加工钢和铸铁。
加工超级合金:增韧补强的氧化铝基和Si3N4基陶瓷刀具(如SiC晶须增韧)和Sialon陶瓷刀具适于加工这类合金。
PCBN刀具可以100-200m/min的切削速度加工。
复杂刀具可用超细晶粒硬质合金及其涂层刀具。
加工钛合金:一般可用 WC基超细晶粒硬质合金和金刚石刀具。
采用润滑性能良好的切削液,可获得较好的结果。
四、高速切削加工的刀柄系统BT系统:刀柄锥度7:24,单面接触。
HSK系统:刀柄锥度1:10,双面接触。
BT刀柄(7:24)BT刀柄与主轴接合图HSK刀柄(1:10)HSK刀柄与主轴接合图刀柄与主轴接触不同刀柄系统,高速加工时,离心力有很大影响。
BT主轴/刀柄联结主轴转速达到某一极限值(n=15000r/min,F=15kN) 时,主轴/刀柄联接处大端的分离导致刀柄在切削力的作用下以刀柄为支承发生摆动,极大地降低了刀柄在主轴锥孔内的定位精度和重复定位精度,无法保证联结的可靠性。
(a)联结面间的间隙(单位:m) (b)联结面间的接触应力(单位:N/m2)BT刀柄与主轴的联结(转速n=15000r/min, 轴向拉力F=15kN)(a)联结面间的间隙(单位:m) (b)联结面间的接触应力(单位:N/m2)HSK-A63主轴/刀柄的联结(n=10000r/min)(a) BT 40(b) HSK-A63旋转速度对径向间隙的影响BT40联结的最佳转速范围为0~12,000r/min,12,000~15,000r/min仍可使用,15,000r/min以上,由于精度降低,无法使用。
HSK-63A刀柄系统最佳转速范围为0-30000r/min,超过这个范围精度降低。
高速切削加工技术的现状和发展(3)中国工程院院士、山东大学艾兴教授五、高速切削加工的安全技术(1)高速旋转刀具的平衡高速切削旋转刀具系统必须平衡,但应根据其使用速度范围予以平衡,以达到最佳经济条件。
一般在6000rpm以上必须平衡,以保证安全。
要求G≤2.5, G为平衡品质(mm/s),即反映刀具平衡量与转速关系的参数。
e-偏心(g×mm/Kg) M-刀体质量(Kg)ω-角速度(r/s)m-不平衡量(g)N-转速(rpm) r-不平衡半径(mm)U-残余不平衡量(g×mm)残余不平衡量U= m ×r动平衡线图SHENCK动平衡仪高速切削刀具的安全性:防止离心力造成刀体与夹紧零件破坏和刀片的夹紧不可靠。
高速切削刀具破坏实例:在5000 rpm时刀片甩出的面铣刀在36700 rpm时爆碎的面铣刀36000 rpm时弯曲与折断的直径12 mm的带柄立铣刀(2)可转位刀具安全性(a)立装可转位铣刀(b)平装可转位铣刀螺钉分析可转位面铣刀刀片外移和螺钉弯曲旋转速度对刀具变形的影响金属去除率对螺钉最大等效应力的影响不同装夹方式下的螺钉极限转速分析结果表明:从安全性看,对可转位面铣刀刀具,旋转离心力造成刀片夹紧,螺钉的破坏和刀体的变形有最主要的影响,立装铣刀优于平装铣刀。
(3)整体硬质合金(<0.5um)立铣刀的安全性φ10mm立铣刀(三齿)仅受离心力作用的应力图(n=10,000r/min)φ10mm立铣刀(三齿)刀具受离心力、切削力作用的应力图(n=10,000r/min,Q=39 cm3/min)金属去除率对φ10mm刀具应力的影响对于小直径整体式硬质合金铣刀而言,旋转离心力对刀具的变形、应力分布影响很小,完全可以忽略不计。
其应力水平的高低是由切削力决定的。
六、高速切削加工技术的应用实例陶瓷刀具车削淬硬钢(HRC60~62)30D箱体加工示意图七、高速切削加工技术展望高效率、高精度、高柔性和绿色化是机械加工领域的发展趋势。
高速切削加工技术必将沿着安全、清洁生产和降低制造成本的方向继续发展,而成为21世纪切削技术的主流切削速度目标:铣加工铝及其合金10000m/min;铣加工铸铁5000m/min;铣加工普通钢2500m/min。
钻削铝及其合金30000r/min,钻削铸铁20000r/min,钻削普通钢10000r/min。