DCS系统介绍
DCS系统简介
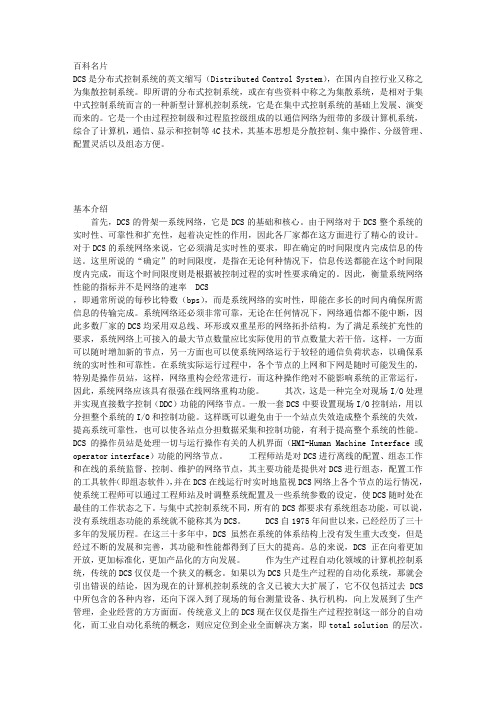
百科名片DCS是分布式控制系统的英文缩写(Distributed Control System),在国内自控行业又称之为集散控制系统。
即所谓的分布式控制系统,或在有些资料中称之为集散系统,是相对于集中式控制系统而言的一种新型计算机控制系统,它是在集中式控制系统的基础上发展、演变而来的。
它是一个由过程控制级和过程监控级组成的以通信网络为纽带的多级计算机系统,综合了计算机,通信、显示和控制等4C技术,其基本思想是分散控制、集中操作、分级管理、配置灵活以及组态方便。
基本介绍首先,DCS的骨架—系统网络,它是DCS的基础和核心。
由于网络对于DCS整个系统的实时性、可靠性和扩充性,起着决定性的作用,因此各厂家都在这方面进行了精心的设计。
对于DCS的系统网络来说,它必须满足实时性的要求,即在确定的时间限度内完成信息的传送。
这里所说的“确定”的时间限度,是指在无论何种情况下,信息传送都能在这个时间限度内完成,而这个时间限度则是根据被控制过程的实时性要求确定的。
因此,衡量系统网络性能的指标并不是网络的速率 DCS,即通常所说的每秒比特数(bps),而是系统网络的实时性,即能在多长的时间内确保所需信息的传输完成。
系统网络还必须非常可靠,无论在任何情况下,网络通信都不能中断,因此多数厂家的DCS均采用双总线、环形或双重星形的网络拓扑结构。
为了满足系统扩充性的要求,系统网络上可接入的最大节点数量应比实际使用的节点数量大若干倍。
这样,一方面可以随时增加新的节点,另一方面也可以使系统网络运行于较轻的通信负荷状态,以确保系统的实时性和可靠性。
在系统实际运行过程中,各个节点的上网和下网是随时可能发生的,特别是操作员站,这样,网络重构会经常进行,而这种操作绝对不能影响系统的正常运行,因此,系统网络应该具有很强在线网络重构功能。
其次,这是一种完全对现场I/O处理并实现直接数字控制(DDC)功能的网络节点。
一般一套DCS中要设置现场I/O控制站,用以分担整个系统的I/O和控制功能。
DCS控制系统讲解

DCS控制系统讲解DCS(分散控制系统)是指通过计算机技术和通信技术将生产过程中的各个控制单元进行连接和协调,实现对整个生产过程的自动控制和监控的系统。
它是以计算机为核心,将各个控制单元分散在不同的位置,并通过通信网络进行连接的控制系统。
DCS系统由硬件和软件两部分组成。
硬件包括主机、输入输出设备、通信设备等。
主机是DCS系统的核心,用于处理各个控制单元发送过来的数据,并根据设定的控制策略进行控制。
输入输出设备用于与现场设备进行数据的交换,如传感器、执行器等。
通信设备用于连接各个控制单元,实现数据的传输和交换。
软件是指对DCS系统进行编程,实现各种控制功能和监控功能的程序。
DCS系统的特点是分布式控制。
各个控制单元可以分散在不同的位置,并通过通信网络进行连接。
这样就可以实现对整个生产过程的全面控制和监控。
此外,DCS系统还具有模块化设计的特点,各个控制单元可以独立工作,互不干扰。
这样就可以方便系统的扩展和维护。
DCS系统可以分为三层结构:生产现场层、控制层和管理层。
生产现场层是指生产过程中的实际控制单元,如传感器、执行器等。
控制层是指各个控制单元之间进行数据通信和控制的计算机集群,包括主机、通信设备等。
管理层是指对整个DCS系统进行监控和管理的计算机,包括人机界面和监控软件等。
DCS系统具有很高的可靠性和可扩展性。
由于各个控制单元可以独立工作,并通过通信网络进行连接,当其中一个控制单元发生故障时,其他控制单元仍然可以正常工作。
同时,当生产过程需要扩展时,只需要添加新的控制单元,而无需对整个系统进行大范围的改造。
DCS系统的应用范围广泛,包括电力、化工、冶金、环保、交通等行业。
在电力行业,DCS系统可以用于对电力系统进行监控和控制,实现电力的调度和分配。
在化工行业,DCS系统可以用于对化工过程中的反应装置、蒸馏装置等进行控制,实现化工生产的自动化。
在冶金行业,DCS系统可以用于对冶炼过程中的各个控制单元进行控制,提高生产效率和质量。
DCS系统

DCS系统一、DCS介绍DCS的硬件系统是通过网络系统将不同数目的现场控制站、操作员站和工程师站连接起来,共同完成各种采集、控制、显示、操作和管理功能。
目前,世界上有名的DCS厂家就有上百家。
不同的系统采用的计算机硬件差别很大。
我在此主要介绍现场控制站。
现场控制站是一个可独立运行的计算机监测与控制系统。
其结构如右图。
在DCS控制系统中,各种现场检测仪表(如各种传感器、变送器等)送来的过程信号均由过程控制级各单元进行实时的数据采集,滤除噪音信号,进行非线性校正及各种补偿运算,折算成相应的工程量。
同时,接受操作站发来的各种手动操作命令对生产过程进行控制。
在过程控制单元根据过程控制组态,还可进行各种闭环控制、批量控制、顺序控制等。
现场控制站分机柜、电源、控制计算机。
电源均采用双交流电源供电,互为冗余。
站内各功能模块所需的直流电源一般有+5V,±15V(或12V),24V等,一般由交流电整成直流电,供给柜内直流母线,也是采用冗余配置。
控制计算机由CPU、存储器、输入输出通道(I/O)等基本部分组成。
其中,种类最多,数量最大的就是各种I/O接口模件。
模拟量输入通道(AI),生产过程中各种连续性的物理量(如温度、压力、压差、位移、转速、电流、电压)和化学量(PH值,浓度等)模拟量输出通道(AO),一般是输出4~20Ma的连续的直流电流信号,用来控制各种直行程或角行程的执行机构,或通过调速装置控制各种电机的转速,也可通过电—气转换器或电—液转换器来控制各种气动或液动执行机构。
开关量输入通道(DI),用来输入各种限位开关、继电器等无源接点。
由DCS提供检测电压(一般为24V)。
开关量输出通道(DO),又称数字量输出通道,用于控制电磁阀门、继电器、指示灯、声报警器等只具有开、关两种状态的设备,开关量输出就是输出无源接点。
上图为一个两位式气动门的控制回路接线。
从图中我们可以看出,我们需要把电源串联进入回路。
DCS控制系统介绍
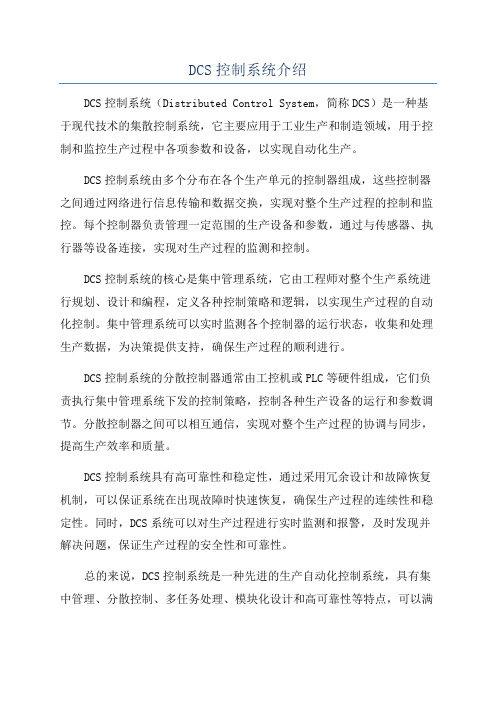
DCS控制系统介绍
DCS控制系统(Distributed Control System,简称DCS)是一种基于现代技术的集散控制系统,它主要应用于工业生产和制造领域,用于控制和监控生产过程中各项参数和设备,以实现自动化生产。
DCS控制系统由多个分布在各个生产单元的控制器组成,这些控制器之间通过网络进行信息传输和数据交换,实现对整个生产过程的控制和监控。
每个控制器负责管理一定范围的生产设备和参数,通过与传感器、执行器等设备连接,实现对生产过程的监测和控制。
DCS控制系统的核心是集中管理系统,它由工程师对整个生产系统进行规划、设计和编程,定义各种控制策略和逻辑,以实现生产过程的自动化控制。
集中管理系统可以实时监测各个控制器的运行状态,收集和处理生产数据,为决策提供支持,确保生产过程的顺利进行。
DCS控制系统的分散控制器通常由工控机或PLC等硬件组成,它们负责执行集中管理系统下发的控制策略,控制各种生产设备的运行和参数调节。
分散控制器之间可以相互通信,实现对整个生产过程的协调与同步,提高生产效率和质量。
DCS控制系统具有高可靠性和稳定性,通过采用冗余设计和故障恢复机制,可以保证系统在出现故障时快速恢复,确保生产过程的连续性和稳定性。
同时,DCS系统可以对生产过程进行实时监测和报警,及时发现并解决问题,保证生产过程的安全性和可靠性。
总的来说,DCS控制系统是一种先进的生产自动化控制系统,具有集中管理、分散控制、多任务处理、模块化设计和高可靠性等特点,可以满
足各种工业生产领域的自动化控制需求,提高生产效率,节约成本,保证生产质量,是工业生产自动化的重要技术手段。
(完整版)DCS系统介绍
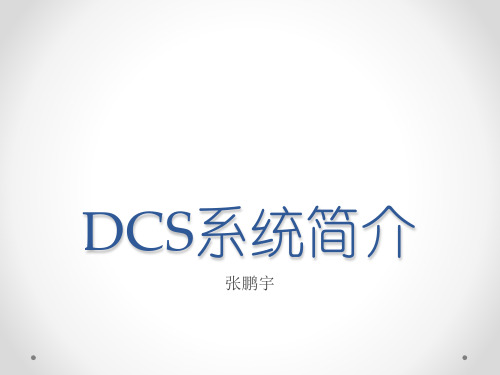
3.2.2过程控制级
• 又称现场控制单元或基本控制器,是DCS系统中的核心部 分。生产工艺的调节都是靠它来实现。比如阀门的开闭调 节、顺序控制、连续控制等等。
3.2.3过程管理级
• DCS的人机接口装置,普遍配有高分辨率、大屏幕的色彩 CRT、操作者键盘、打印机、大容量储存器等。操作员通 过操作站选择各种操作和监视生产情况、这个级别是操作 人员跟DCS交换信息的平台。是DCS的核心显示、操作跟 管理装置。操作人员通过操作站来监视和控制生产过程, 可以通过屏幕了解到生产运行情况,了解每个过程变量的 数字跟状态。
8 TCP/IP配置
• 1、IP地址 • 2、子网掩码 • 3、默认网关 • 4、DNS
8.1 IP地址
• IP地址是指互联网协议地址(英语:Internet Protocol Address, 又译为网际协议地址),是IP Address的缩写。IP地址是IP协议提供 的一种统一的地址格式,它为互联网上的每一个网络和每一台主机分 配一个逻辑地址,以此来屏蔽物理地址的差异。
• 1.DI信号:数字输入信号(Digital Input) • 2.DO信号:数字输出信号(Digital Output) • 3.AI信号:模拟量输入(Analog Input) • 4.AO信号:模拟量输出(Analog Output)
6.1.1 DI信号典型回路图
• 设备状态信号、阀门反馈、盘车开关、急停按钮……
8.4 DNS
• DNS(Domain Name Service)域名服务,我们都知道在网络 上传输信息用的地址是IP地址,但是因为IP没有规律难以 记忆,所以就有了域名,当我们访问drop160时,网络上 的路由器是不知道drop160怎么走的,所以我们需要把 drop160转化成drop160的IP地址,这就是DNS服务。
DCS系统的介绍

第三章 DCS系统的介绍多级计算机分布控制系统又称集散控制系统(DCS,distributed control system),是网络技术和控制技术结合的产物。
它是根据分布设计的基本思想,实现功能上分离,位置上分散,达到以分散控制为主,集中管理为辅。
3.1 DCS系统的定义DCS是分布式控制系统的英文缩写(Distributed Control Systerm),在国内自控行业又称为集散控制系统。
即所谓的分布式控制系统,或在有些资料中称之为集散系统,是相对于集中式控制系统而言的一种新型计算机控制系统,它是在集中式控制系统的基础上发展、演变而来的。
在系统功能方面,DCS和集中式控制系统的区别不大,但在系统功能的实现方法上却完全不同。
3.2 DCS的组成集散控制系统DCS(Distributed Control Systerm)是基于“4C”技术(Computer Control Communicatiao CRT)在20世纪70年代中期出现的新型工业控制系统。
采用分布式的计算机系统结构,目的是为了减少风险,提高系统可靠性。
它将整个控制系统按照区域、功能和回路作适当分解,再通过总线或通讯网络将它们连接为有机整体。
1975年Honey-well公司推出了第一套DCS 控制系统,首先被应用于石油化工行业。
自1975年以来,DCS控制系统的硬件和软件功能不断完善和强化,已经经历了三代,但从基本结构来看特性相同,可分解为三大基本部分。
(1)过程控制站过程控制站是集散控制系统与生产过程之间的界面,生产过程的各种过程变量和状态信息通过过程控制站转化为操作监视的数据,而操作的各种信息业通过过程控制站送到执行机构。
在过程控制装置内,进行模拟量与数字量的相互转换,完成各种控制算法的运算,以及对输入和输出量的数据处理等运算。
(2)操作站操作站是操作人员与集散控制系统的界面,操作人员通过操作站了解生产过程的运行状况,并通过他发出操作指令。
DCS控制系统介绍三篇

DCS控制系统介绍三篇篇一:DCS控制系统介绍集散控制系统的英文原名为:DistributedControlSystem,简称DCS,通常也称为集散控制系统。
集散控制系统的控制功能,主要由计算机技(computer)、控制技术(Control)、显示技术(CRT)和通信技术(communicate)来完成,一般也称为4C技术,4C技术是DCS系统的四大支柱。
DCS中通信技术更为重要,操作员站的操作、工程师站系统的组态以及现场设备信息的交换都依靠通信技术来完成。
第一节集散控制系统的构成一集散控制系统的构成方式如图是集散控制系统典型结构。
功能分层是集散控制系统的体系特征反映了集散控制系统的“分散控制、集中管理”的特点。
从功能上看可以分为:四个层次,分别是现场控制级的功能;过程装置控制级;车间操作管理级;全厂优化和调度管理级。
从结构看分为:三大块,分别是分散过程控制装置;集中操作和管理系统;通信系统。
图4.1DCS结构(一)集散控制系统的各层功能1、现场控制级的功能(1)微处理器进入现场变送器、传感器和执行器;现场总线的应用。
部分或完全完成过程控制级的功能;(2)采集过程数据,对数据进行数据转换;(3)输出过程操作命令;(4)进行直接数字控制;(5)完成与过程装置控制级的数据通信;(6)对现场控制级的设备进行检测和诊断。
2、过程装置控制级的功能过程装置控制级的结构采用过程控制设备+I/O卡件,其功能是:(1)采集过程数据,进行数据转换和处理;(2)数据的监视和存储;(3)实施连续、批量或顺序控制的运算和输出控制作用;(4)数据和设备的自诊断;(5)数据通信。
3、车间操作管理级的功能车间操作管理级设备有中央控制室操作站、打印机、拷贝机、工程师站、计算站,能完成功能是:(1)数据显示与记录(2)过程操作(含组态操作、维护操作)(3)数据存储和压缩归档(4)报警、事件的诊断和处理(5)系统组态、维护和优化处理(6)数据通信;(7)报表打印和画面硬拷贝。
DCS系统介绍
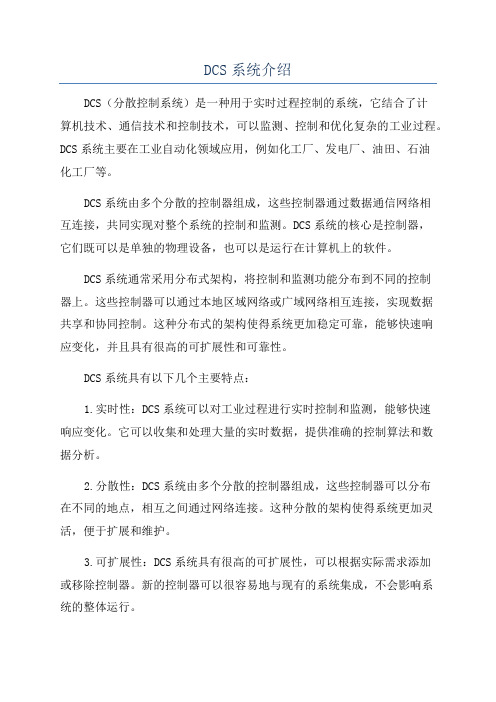
DCS系统介绍DCS(分散控制系统)是一种用于实时过程控制的系统,它结合了计算机技术、通信技术和控制技术,可以监测、控制和优化复杂的工业过程。
DCS系统主要在工业自动化领域应用,例如化工厂、发电厂、油田、石油化工厂等。
DCS系统由多个分散的控制器组成,这些控制器通过数据通信网络相互连接,共同实现对整个系统的控制和监测。
DCS系统的核心是控制器,它们既可以是单独的物理设备,也可以是运行在计算机上的软件。
DCS系统通常采用分布式架构,将控制和监测功能分布到不同的控制器上。
这些控制器可以通过本地区域网络或广域网络相互连接,实现数据共享和协同控制。
这种分布式的架构使得系统更加稳定可靠,能够快速响应变化,并且具有很高的可扩展性和可靠性。
DCS系统具有以下几个主要特点:1.实时性:DCS系统可以对工业过程进行实时控制和监测,能够快速响应变化。
它可以收集和处理大量的实时数据,提供准确的控制算法和数据分析。
2.分散性:DCS系统由多个分散的控制器组成,这些控制器可以分布在不同的地点,相互之间通过网络连接。
这种分散的架构使得系统更加灵活,便于扩展和维护。
3.可扩展性:DCS系统具有很高的可扩展性,可以根据实际需求添加或移除控制器。
新的控制器可以很容易地与现有的系统集成,不会影响系统的整体运行。
4.可靠性:DCS系统具有很高的可靠性,它可以实现冗余配置,以确保系统在控制器故障或通信故障的情况下仍然正常运行。
此外,DCS系统还可以进行故障诊断和预测,及时发现和修复故障,减少停机时间。
5.开放性:DCS系统采用开放的标准和协议,可以与其他系统和设备进行集成。
例如,它可以与企业资源计划(ERP)系统、质量管理系统、人机界面(HMI)等系统相连接,实现数据共享和协同工作。
DCS系统可以实现多种控制策略,例如PID控制、模型预测控制、优化控制等。
它可以对工业过程进行自动化控制,提高生产效率和产品质量,减少能源消耗和废品产生。
DCS控制系统介绍
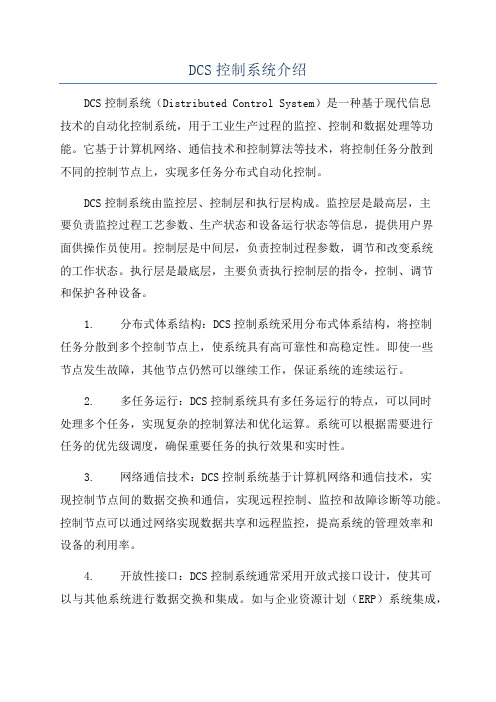
DCS控制系统介绍DCS控制系统(Distributed Control System)是一种基于现代信息技术的自动化控制系统,用于工业生产过程的监控、控制和数据处理等功能。
它基于计算机网络、通信技术和控制算法等技术,将控制任务分散到不同的控制节点上,实现多任务分布式自动化控制。
DCS控制系统由监控层、控制层和执行层构成。
监控层是最高层,主要负责监控过程工艺参数、生产状态和设备运行状态等信息,提供用户界面供操作员使用。
控制层是中间层,负责控制过程参数,调节和改变系统的工作状态。
执行层是最底层,主要负责执行控制层的指令,控制、调节和保护各种设备。
1. 分布式体系结构:DCS控制系统采用分布式体系结构,将控制任务分散到多个控制节点上,使系统具有高可靠性和高稳定性。
即使一些节点发生故障,其他节点仍然可以继续工作,保证系统的连续运行。
2. 多任务运行:DCS控制系统具有多任务运行的特点,可以同时处理多个任务,实现复杂的控制算法和优化运算。
系统可以根据需要进行任务的优先级调度,确保重要任务的执行效果和实时性。
3. 网络通信技术:DCS控制系统基于计算机网络和通信技术,实现控制节点间的数据交换和通信,实现远程控制、监控和故障诊断等功能。
控制节点可以通过网络实现数据共享和远程监控,提高系统的管理效率和设备的利用率。
4. 开放性接口:DCS控制系统通常采用开放式接口设计,使其可以与其他系统进行数据交换和集成。
如与企业资源计划(ERP)系统集成,实现生产计划和物料管理的统一、同时,也可以与其他自动化系统集成,如SCADA系统、MES系统等,实现全面的生产过程控制和管理。
5. 可扩展性:DCS控制系统具有较好的可扩展性,可以根据生产工艺的变化和需求的变化进行扩展和改造。
可以增加新的控制节点,增加新的功能模块,实现对系统的功能和性能的扩展,提高系统的灵活性和适应性。
DCS控制系统在工业生产中有着广泛的应用,包括化工、石油、电力、冶金、食品、制药等行业。
DCS系统的介绍

DCS系统的介绍DCS(分布式控制系统)是一种集成了过程控制、数据采集、通信、运算和显示等功能的自动化控制系统。
它主要应用于诸如发电厂、化工厂、石油化工、冶金、制药、水处理、水电站等领域。
DCS系统通过集中控制器、工作站、输入/输出子系统、通信网络等构成,实现对整个系统的实时监控和自动控制。
1.集中控制器(CPU):集中控制器是DCS系统的核心,负责实时监控和控制系统的各种参数。
它可以处理来自传感器和执行器的输入和输出信号,执行控制算法,并向操作员提供实时数据。
2.工作站:DCS系统通常包括一台或多台工作站,用于操作员监控和操纵系统。
工作站提供了人机界面,使操作员能够查看关键数据、趋势图、报警信息等。
通过工作站,操作员可以对系统进行调整和优化,实现最佳控制效果。
3.输入/输出子系统:输入/输出子系统负责将传感器和执行器与DCS系统进行连接。
它包括模拟输入、模拟输出、数字输入、数字输出等接口模块,用于将各种信号转换为数字信号,以便于集中控制器的处理。
4.通信网络:DCS系统中的各个组件通过通信网络进行连接。
通信网络是实现数据传输和交换的重要一环,它可以是以太网、现场总线、红外线通信等。
通信网络高效稳定的运行是确保DCS系统正常运行的关键。
1.高度集成:DCS系统集成了过程控制、数据采集、通信、运算和显示等功能,可以实现对整个系统的一体化管理,提高工作效率和生产效益。
2.实时监控:DCS系统可以提供实时的数据和趋势图,使操作员对系统状态进行实时监控和分析。
这样,操作员可以及时发现和处理潜在问题,保证生产过程的稳定性和安全性。
3.灵活可扩展:DCS系统可以根据实际需要进行灵活扩展和升级。
用户可以根据生产线的变化进行系统配置和改造,以适应新的生产要求。
4.可靠性高:DCS系统采用了分布式架构,其中集中控制器、工作站和输入/输出子系统等可以实现冗余备份,提高了系统的可靠性和稳定性。
5.易于操作:DCS系统提供了友好的用户界面和操作方法,使操作员能够轻松地操作和管理系统。
DCS系统简介DCS系统
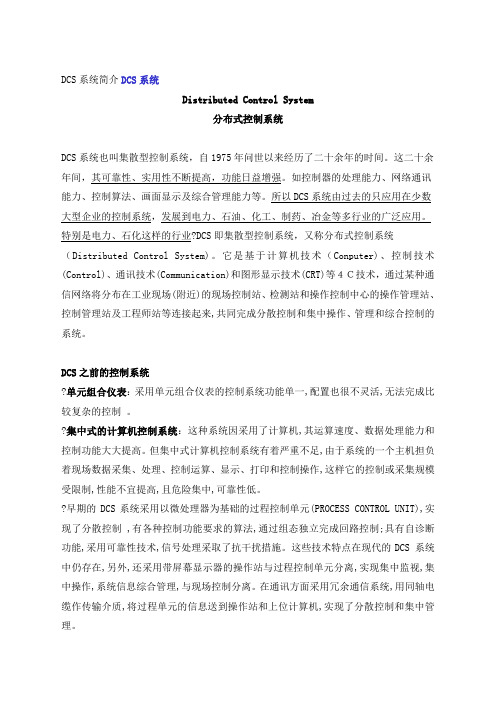
DCS系统简介DCS系统Distributed Control System分布式控制系统DCS系统也叫集散型控制系统,自1975年问世以来经历了二十余年的时间。
这二十余年间,其可靠性、实用性不断提高,功能日益增强。
如控制器的处理能力、网络通讯能力、控制算法、画面显示及综合管理能力等。
所以DCS系统由过去的只应用在少数大型企业的控制系统,发展到电力、石油、化工、制药、冶金等多行业的广泛应用。
特别是电力、石化这样的行业?DCS即集散型控制系统,又称分布式控制系统(Distributed Control System)。
它是基于计算机技术(Conputer)、控制技术(Control)、通讯技术(Communication)和图形显示技术(CRT)等4C技术,通过某种通信网络将分布在工业现场(附近)的现场控制站、检测站和操作控制中心的操作管理站、控制管理站及工程师站等连接起来,共同完成分散控制和集中操作、管理和综合控制的系统。
DCS之前的控制系统单元组合仪表:采用单元组合仪表的控制系统功能单一,配置也很不灵活,无法完成比较复杂的控制。
集中式的计算机控制系统:这种系统因采用了计算机,其运算速度、数据处理能力和控制功能大大提高。
但集中式计算机控制系统有着严重不足,由于系统的一个主机担负着现场数据采集、处理、控制运算、显示、打印和控制操作,这样它的控制或采集规模受限制,性能不宜提高,且危险集中,可靠性低。
早期的DCS系统采用以微处理器为基础的过程控制单元(PROCESS CONTROL UNIT),实现了分散控制 ,有各种控制功能要求的算法,通过组态独立完成回路控制;具有自诊断功能,采用可靠性技术,信号处理采取了抗干扰措施。
这些技术特点在现代的DCS 系统中仍存在,另外,还采用带屏幕显示器的操作站与过程控制单元分离,实现集中监视,集中操作,系统信息综合管理,与现场控制分离。
在通讯方面采用冗余通信系统,用同轴电缆作传输介质,将过程单元的信息送到操作站和上位计算机,实现了分散控制和集中管理。
(完整版)DCS系统介绍
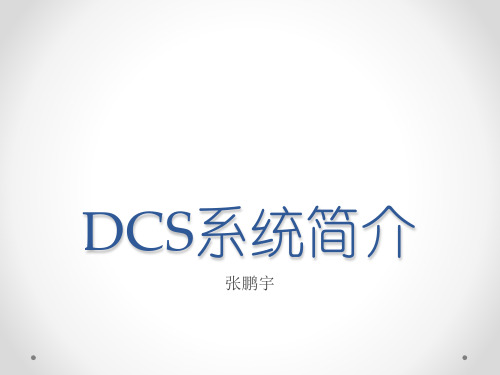
5.2 监控画面组态
5.3 工作站组态
• 用于监视控制显示画面及部分组态功能。
5.4 通讯组态
• 用于组态工作站,打印机及第三方控制器。
六、DCS的基础知识
• I/O信号 • 系统冗余 • DCS系统的特点
6.1 IO信号
• I/O:控制系统需要建立信号的输入和输出通道,这就是 I/O。DCS中的I/O一般是模块化的,一个I/O模块上有一 个或多个I/O通道,用来连接传感器和执行器。
2.2 1940~1970年
• 第三次科技革命开始后,随着计算机技术的发展,人们开 始尝试将计算机用于过程控制。但当时采用的办法是用一 台计算机控制几十甚至上百个回路,这样做的危险性很高, 如果计算机出现故障,会导致很严重的后果,这造成了危 险集中。
2.3 1970~1990年
• 直到上世纪70年代,随着计算机技术的日渐成熟,人们才 开始将危险分散。就是原来靠一台大计算机完成的任务, 现在用几十台微处理器来完成,从而大大降低了危险系数。 至此DCS就诞生了。
• 3.2管理级别分类:现场控制级、过程控制级、过程管理 级、经营管理级
• 3.3网络结构分类:一级网络、二级网络、三级网络
3.1硬件组成
3.2.1现场控制级
• 又称数据采集装置,主要是将过程非控变量进行数据采集 和预处理,而且对实时数据进一步加工处理,供操作站显 示和打印,从而实现开环监视,并将采集到的数据传输到 监控计算机。输出装置在有上位机的情况下,能以开关量 或者模拟量信号的方式,向终端元件输出计算机控制命令。 这一个级别直接面对现场,跟现场过程相连。比如阀门、 电机、各类传感器、变送器、执行机构等等。
3.2.2过程控制级
DCS系统介绍
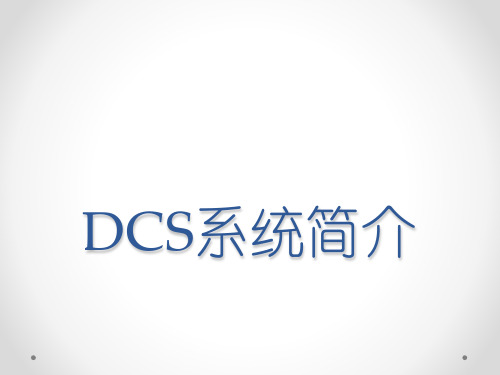
2.1 1930~1940年
• 上世纪三四十年代,工业自动化装置采用的是分散性控制 系统。也就是所有设备都是独立运行,不联网控制。操作 员根据生产需求进行计算后,将独立设备的特性调节到适 合的程度,然后就开始工作。之后采用了气动、电动模拟 仪表组成过程控制系统,实现了一定程度上的集中监视、 操作和分散控制。
4.1.1 早期的DCS机柜
4.1.2系统柜
控制防火墙 冗余数字与模拟 I/O 电源系统 C300 控制器
现场总线接口模件
4.1.3辅助柜
4.1.4 辅操台
4.2 操作站
4.3 网络设备
4.4 可编程控制器PLC
• 可编程逻辑控制器是种专门为在工业环境下应用而设计的 数字运算操作电子系统。它采用一种可编程的存储器,在 其内部存储执行逻辑运算、顺序控制、定时、计数和算术 运算等操作的指令,通过数字式或模拟式的输入输出来控 制各种类型的机械设备或生产过程。
3.2.4经营管理级
• 又称上位机,功能强、速度快、容量大。通过专门的通信 接口与高速数据通路相连,综合监视系统各单元,管理全 系统的所有信息。这是全厂自动化系统的最高一层。只有 大规模的集散控制系统才具备这一级。
3.3网络结构
四、DCS系统的硬件结构
• 现场控制单元:系统柜、辅助柜、辅操台…… • 操作站:服务器、工程师站、操作站……
• 3.2管理级别分类:现场控制级、过程控制级、过程管理 级、经营管理级
• 3.3网络结构分类:一级网络、二级网络、三级网络
3.1硬件组成
3.2.1现场控制级
• 又称数据采集装置,主要是将过程非控变量进行数据采集 和预处理,而且对实时数据进一步加工处理,供操作站显 示和打印,从而实现开环监视,并将采集到的数据传输到 监控计算机。输出装置在有上位机的情况下,能以开关量 或者模拟量信号的方式,向终端元件输出计算机控制命令。 这一个级别直接面对现场,跟现场过程相连。比如阀门、 电机、各类传感器、变送器、执行机构等等。
DCS控制系统介绍
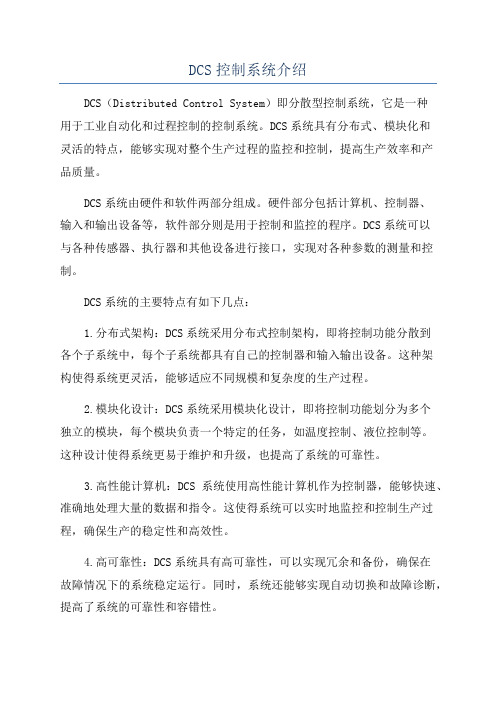
DCS控制系统介绍DCS(Distributed Control System)即分散型控制系统,它是一种用于工业自动化和过程控制的控制系统。
DCS系统具有分布式、模块化和灵活的特点,能够实现对整个生产过程的监控和控制,提高生产效率和产品质量。
DCS系统由硬件和软件两部分组成。
硬件部分包括计算机、控制器、输入和输出设备等,软件部分则是用于控制和监控的程序。
DCS系统可以与各种传感器、执行器和其他设备进行接口,实现对各种参数的测量和控制。
DCS系统的主要特点有如下几点:1.分布式架构:DCS系统采用分布式控制架构,即将控制功能分散到各个子系统中,每个子系统都具有自己的控制器和输入输出设备。
这种架构使得系统更灵活,能够适应不同规模和复杂度的生产过程。
2.模块化设计:DCS系统采用模块化设计,即将控制功能划分为多个独立的模块,每个模块负责一个特定的任务,如温度控制、液位控制等。
这种设计使得系统更易于维护和升级,也提高了系统的可靠性。
3.高性能计算机:DCS系统使用高性能计算机作为控制器,能够快速、准确地处理大量的数据和指令。
这使得系统可以实时地监控和控制生产过程,确保生产的稳定性和高效性。
4.高可靠性:DCS系统具有高可靠性,可以实现冗余和备份,确保在故障情况下的系统稳定运行。
同时,系统还能够实现自动切换和故障诊断,提高了系统的可靠性和容错性。
5. 开放性:DCS系统是一个开放系统,可以与其他系统进行连接和通讯,如MES(Manufacturing Execution System)、ERP(Enterprise Resource Planning)等。
这种开放性使得系统更加灵活,可以实现工厂级别的集成和管理。
DCS系统主要应用于工业生产过程控制,如化工、电力、石油、制药等行业。
它可以实现对生产参数的实时监测和调节,确保产品的质量和安全,提高工艺的稳定性和效率。
总之,DCS控制系统是一种分散型、模块化和灵活的控制系统,能够实现对工业生产过程的监控和控制,提高生产效率和产品质量。
DCS系统介绍

DCS 发展历史
第二阶段:1980—1985.,在这个时期集散控 制系统的技术特点表现为: 1)微处理器的位数提高,CRT显示器的分辨 率提高 2)强化的模块化系统 3)强化了系统信息管理,加强通信功能
DCS 发展历史
第三阶段,1985年以后,集散系统进入第三 代,其技术特点表现为: 1)采用开放系统管理 2)操作站采用32位微处理器 3)采用实时多用户多任务的操作系统
DCS 发展历史
第一阶段:1975-1980年,在这个时期集散控 制系统的技术特点表现为: 1)采用微处理器为基础的控制单元,实现 分散控制,有各种各样的算法,通过组态独立 完成回路控制,具有自诊断功能 2)采用带CRT显示器的操作站与过程单元分 离,实现集中监视,集中操作 3)采用较先进的冗余通信系统
DeltaV I/O Card Types
Outputs
- AO, 8 Channel, 4 to 20 mA, HART – AO, 8 Channel, 4 to 20 mA – I.S. AO, 8 Channel, 4 to 20 mA – DO, 8 Channel, 120/230 VAC, Isolated – DO, 8 Channel, 120/230 VAC, High Side – DO, 8 Channel, 24 VDC, Isolated – DO, 8 Channel, 24 VDC, High Side – High Density DO, 32 Channel, 24 VDC, High Side – I.S. DO, 4 Channel, 12 VDC I.S. Power
DCS 特点
1) 高可靠性。由于DCS将系统控制功能分散在各台计 算机上实现,系统结构采用容错设计,因此某一台计算 机出现的故障不会导致系统其他功能的丧失。此外,由 于系统中各台计算机所承担的任务比较单一,可以针对 需要实现的功能采用具有特定结构和软件的专用计算机, 从而使系统中每台计算机的可靠性也得到提高。 2) 开放性。DCS采用开放式,标准化、模块化和系列 化设计,系统中各台计算机采用局域网方式通信,实现 信息传输,当需要改变或扩充系统功能时,可将新增计 算机方便地连入系统通信网络或从网络中卸下,几乎不 影响系统其他计算机的工作。
DCS控制系统

第三章 DCS的控制站
功能 控制站是DCS的核心,直接与生产过程的 信号传感器,变送器和执行器连接,具有 信号输入,输出,运算,控制和通信功能
DCS控制站硬件
◆输入输出单元(IOU) 直接与生产过程的输入输出信号连接,主要 由输入输出处理器板(IOP),信号调理板和端 子板(FTA)组成. ◆过程控制单元(PCU) 是控制站的核心,主要由控制处理器,输入 输出接口处理器,通信处理器和冗余处理器组成. 一般都有两个PCU,互为冗余热备用,具有自动诊 断和自动切换功能. ◆电源:一般都有两个电源,互为冗余
DCS的主要特点 的主要特点
(4)适应性,灵活性和易扩展性 DCS硬件采用积木式结构,可灵活配置成小,中,大 各类系统,还可根据生产要求,逐步扩展系统,改变系统 配置. 软件采用模块化设计,提供各类功能模块,可灵活组 态. (5)自治性和协调性 DCS自治性是指系统中各个控制站,操作站均可独立 地工作. DCS协调性指系统中各台计算机用通信网络互连在一 起,相互传送信息,相互协调工作. (6)界面友好性
DCS工程师站
DCS的工程师站功能 工程师站的主要功能就是组态,建立 DCS系统,控制系统和人机界面. ★作为DCS控制工程师的人机界面,工程师 站组态的主要内容包括系统设备组态,控 制功能组态和操作画面组态
�
集散控制系统( 第二篇 集散控制系统(DCS) )
第一章 DCS概述 第二章 DCS的体系结构 第三章 DCS的控制站 第四章 DCS的操作站和工程师站
第一章 DCS概述
概念 DCS(Distributed Control System)分散控 制系统,也称集散控制系统.是以应用微处 理器为基础,结合计算机技术,信号处理技 术,测量控制技术,通信网络技术和人机接 口技术,实现过程控制和工厂管理的控制系 统. 也可以说综ห้องสมุดไป่ตู้了计算机(Computer),通信 (Communication),屏幕显示(CRT)和 控制(Control)技术,简称"4C"技术.
第一篇DCS介绍

第一章DCS系统概述1-1-1 #1机组控制系统采用了上海福克斯波罗公司制造的I/A’S系列DCS系统。
整套DCS 系统包括数据采集系统DAS、协调控制系统MCS、炉膛安全与监控系统FSSS、顺序控制系统SCS。
#1机组DEH系统和NCS系统,为新华公司产品。
改造后的#1机组采用以CRT为中心的操作和控制方式。
1-1-2 DAS系统包括锅炉、汽机、电气流程图,趋势图,成组显示,棒状图,机组日报表,事故追忆报表,SOE报表等等。
其流程图上具备实时运行参数、报警状态显示以及操作画面的调出。
1-1-3 MCS系统包括协调控制主控画面,成组操作器画面以及分布在流程图中的给水控制系统,引、送风控制系统,燃烧控制系统,主汽、再热汽温控制系统,一次风机控制系统,除氧器水位控制系统,除氧器压力控制系统,凝器水位控制系统,高加水位控制系统等等。
各子系统的自动投用可在相应的操作器上进行,协调控制方式的选择和投用在主控画面上进行。
1-1-4:FSSS系统包括燃油系统、燃煤系统、公用逻辑三大部分。
它们均分布在锅炉流程图中。
公用逻辑部分包含锅炉保护的主要内容,即炉膛吹扫、主燃料跳闸与首出原因记忆、点火条件、RUNBACK等。
燃油系统包含油层及油枪的投、切控制。
燃煤系统包含各制粉系统的控制。
1-1-5 SCS系统包括了锅炉、汽机的主要辅机、设备和系统的控制、联锁、保护和操作功能。
对重要的辅机设置了启动允许条件“P”、跳闸首出原因“T”、电气跳闸原因“F”。
1-1-6 DEH系统包括汽机控制系统DEH、小汽机控制系统MEH、旁路控制系统BPC三部分。
这三部分均可在两台DEH CRT上调出监视、操作。
1-1-7 NCS系统包括500KV、220KV和机组的公用系统三部分。
500KV升压站和220KV升压站的倒闸操作均可在NCS CRT上进行,公用系统的操作也在NCS CRT上操作。
第二章DCS系统硬件介绍I/A’S的系统结构是按节点(NODE)概念来构成的。
全面的DCS系统基础入门

全⾯的DCS系统基础⼊门什么是DCS?集散控制系统(Distributed Control System):以微处理器为基础,对⽣产过程进⾏集中监视、操作、管理和控制,简称DCS系统。
DCS系统的主要特点归结为⼀句话就是:“分散控制,集中管理”。
DCS与PLC的区别:DCS PLC硬件上位机、⽹络、控制器、I/O接⼝、现场仪表等;单⼀的控制器;软件上位机组态软件、控制器编程软件、通讯接⼝软件、操作及设计画⾯⼈机接⼝软件等;控制器编程软件;运算周期相对长;由于点数少,周期快;特点分布式控制,全局性,控制回路⼤;顺序扫描机制,以时间基准的控制,⽤于单⼀控制单元⼩系统;PLC可以说只是DCS系统的⼀个控制器。
现场控制如何实现?DCS输⼊信号:热电阻;热电偶;0~10mA、4~20mA电流;0~5V、1~5V电压;开关量(数字量)输⼊;即现场⼲触点或电平信号;其他信号;DCS输出信号:开关量(数字量)输出;即对外提供触点,DCS通过触点的通断控制现场设备。
4~20mA输出。
过程控制基本原理:DCS控制简单实例:加热炉温度控制系统:温度变送器控制器⽓动调节阀负反馈:Gc(s):控制器;Gv(s):调节阀;Gm(s):测量变送Gp(s):控制通道;Gd(s):⼲扰通道。
⼏个专业术语:被控变量;操作变量;被控对象;PV:Process Value/Present Value,实时测量值;SV:SetPoint (SP)/SetPoint Value,⽬标值/设定值MV:Manipulated Value,操作输出值。
⽬标:⽬标通过调节燃料流量(操纵变量),使进料温度(被控变量)保持在其设定值;安全性:确保⽣产过程中⼈⾝及设备安全,保护或减少⽣产过程对环境的影响;稳定性:确保产品质量及产品的长期稳定,抑制外部的⼲扰;经济性:实现效益最⼤化及成本最⼩化。
过程控制系统的分类:反馈控制系统--反馈控制系统是根据系统被控量与给定位的偏差进⾏⼯作的,最后达到消除或减⼩偏差的⽬的,偏差值是控制的依据。
DCS系统

DCS为分散控制系统的英文(TOTAL DISTRIBUTED CONTROL SYSTEM)简称。
指的是控制危险分散、管理和显示集中。
60年代末有人研制了作逻辑运算的可编程序控制器(Programmable Logic Controller)。
简称PLC。
主要应用于汽车制造业。
70年代中期以完成模拟量控制的DCS推向市场,代替以PID运算为主的模拟仪表控制。
首先提出DCS这样一种思想的是原制造仪表的厂商,当时主要应用于化工行业。
后又有计算机行业从事DCS的开发。
70年代微机技术还不成熟,计算机技术还不够发达。
操作站、控制器、I/O板和网络接口板等都是DCS生产厂家自行开发的,也就是所有部件都是专用的。
70年代初,有人用如PDP/1124这样的小型机代替原来的集中安装的模拟仪表控制。
连接到中央控制室的电缆很多。
如用小型机既作为控制器、同时把连接小型机的CRT又作为显示设备(即人机界面)。
一台小型机需接收几千台变送器或别的传感器来的信号,完成几百个回路的运算。
很显然其危险有点集中。
和模拟仪表连接的电缆一样多,并且一旦小型机坏了,控制和显示都没有了。
数字控制没有达到预期的目的。
后有人提出把控制和显示分开。
一台计算机完成控制计算任务,另一台计算机完成显示任务。
另外,一个工艺过程作为被控对象可能需要显示和控制的点很多,其中有一些还需要闭环控制或逻辑运算,工艺过程作为被控对象的各个部分会有相对独立性,可以分成若干个独立的工序,再把在计算机控制系统中独立的工序上需要显示和控制的输入、输出的点分配到数台计算机中去,把原来由一台小型机完成的运算任务由几台或几十台计算机(控制器)去完成。
其中一台机器坏了不影响全局。
所谓“狼群代替老虎”的战术,这就是危险分散的意思。
把显示、操作、打印等管理功能集中在一起,用网络把上述完成控制和显示的两部分连成一个系统。
当时有人把这种系统称为集散系统。
危险究竟要分散到多少算合适呢?这与当时的计算机技术的发展水平有关。