如何消除七大浪费
消除生产现场的七大浪费

消除生产现场的七大浪费引言在现代制造业中,提高生产效率是每个企业都追求的目标之一。
然而,在生产过程中存在着各种浪费现象,这些浪费不仅会降低生产效率,还会增加成本和时间。
为了提高生产效率,我们需要消除这些浪费。
本文将介绍生产现场常见的七大浪费,并提供一些解决方案。
1. 过产量过产量是指生产过程中超出需求的产量。
这种浪费会导致过剩的库存和资金占用。
为了消除过产量的浪费,可以采取以下措施:•优化生产计划,确保生产与需求的平衡。
•精确预测需求,避免产生过多的库存。
•优化生产工艺,提高生产效率,减少不必要的浪费。
2. 传送传送是指产品在生产过程中需要频繁搬运或转移所导致的浪费。
这种浪费不仅增加了生产线的复杂性,还容易引发物料丢失或损坏。
为了减少传送的浪费,可以采取以下措施:•优化生产线布局,缩短物料传送距离。
•使用自动化设备,降低人工传送的需求。
•设计合理的物料存储和取料系统,减少传送过程中的损失。
3. 大量存货大量存货指的是生产过程中大量积压的未完成产品。
这种浪费不仅增加了库存成本,还增加了生产线停机的风险。
为了减少大量存货的浪费,可以采取以下措施:•定期评估生产能力,确保与需求相匹配。
•采用小批量生产,减少未完成产品的库存。
•实施精益生产管理,缩短生产周期,减少存货积压。
4. 等待等待是指生产过程中因为物料或信息的不及时而导致的停机等待时间。
这种浪费会降低生产效率,延长生产周期。
为了消除等待的浪费,可以采取以下措施:•设立高效的沟通渠道,保证信息的及时传递。
•加强供应链管理,确保物料供应的稳定和及时。
•优化生产计划,避免生产资源的闲置。
5. 过度加工过度加工是指对产品进行超出需求或规格要求的加工。
这种浪费会导致资源的浪费和生产效率的降低。
为了消除过度加工的浪费,可以采取以下措施:•监控产品质量,确保符合需求和规格要求。
•优化工艺流程,取消不必要的加工环节。
•加强员工培训,提升其对产品要求的理解和把握。
如何消除七大浪费
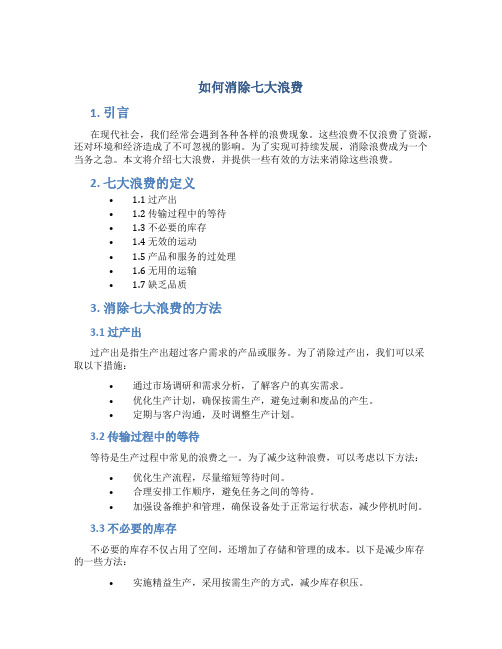
如何消除七大浪费1. 引言在现代社会,我们经常会遇到各种各样的浪费现象。
这些浪费不仅浪费了资源,还对环境和经济造成了不可忽视的影响。
为了实现可持续发展,消除浪费成为一个当务之急。
本文将介绍七大浪费,并提供一些有效的方法来消除这些浪费。
2. 七大浪费的定义• 1.1 过产出• 1.2 传输过程中的等待• 1.3 不必要的库存• 1.4 无效的运动• 1.5 产品和服务的过处理• 1.6 无用的运输• 1.7 缺乏品质3. 消除七大浪费的方法3.1 过产出过产出是指生产出超过客户需求的产品或服务。
为了消除过产出,我们可以采取以下措施:•通过市场调研和需求分析,了解客户的真实需求。
•优化生产计划,确保按需生产,避免过剩和废品的产生。
•定期与客户沟通,及时调整生产计划。
3.2 传输过程中的等待等待是生产过程中常见的浪费之一。
为了减少这种浪费,可以考虑以下方法:•优化生产流程,尽量缩短等待时间。
•合理安排工作顺序,避免任务之间的等待。
•加强设备维护和管理,确保设备处于正常运行状态,减少停机时间。
3.3 不必要的库存不必要的库存不仅占用了空间,还增加了存储和管理的成本。
以下是减少库存的一些方法:•实施精益生产,采用按需生产的方式,减少库存积压。
•优化供应链管理,确保物料的及时供应,避免库存过多或过少的情况。
•提高销售预测的准确性,避免因预测不准确而导致的库存积压。
3.4 无效的运动无效的运动是指在生产过程中没有价值的运动。
以下是减少无效运动的一些方法:•优化工作布局,确保工作流程合理,减少不必要的移动和运输。
•提供良好的工作环境和设备,避免员工因工作环境不好而产生额外的运动。
•增加员工培训,提高工作效率和操作技能,减少无效运动的发生。
3.5 产品和服务的过处理产品和服务的过处理是指过度加工或过度提供服务。
以下是减少产品和服务过处理的一些方法:•优化工艺流程,确保产品加工符合客户要求,避免过度加工。
•确定客户的真实需求,提供符合需求的服务,避免过度提供服务。
精益生产中的七大浪费及改善方法
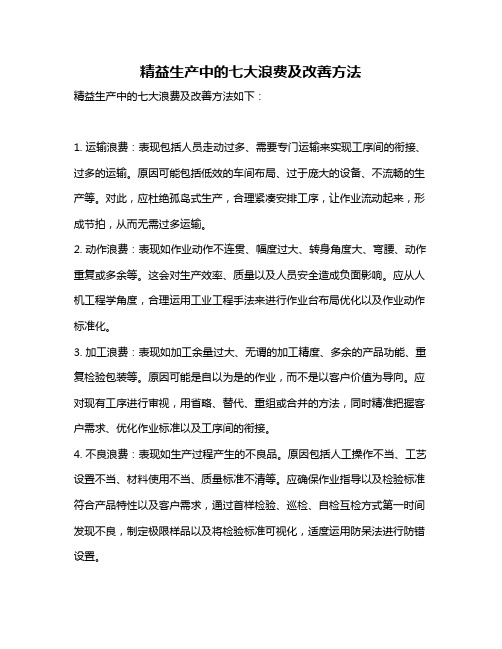
精益生产中的七大浪费及改善方法精益生产中的七大浪费及改善方法如下:1. 运输浪费:表现包括人员走动过多、需要专门运输来实现工序间的衔接、过多的运输。
原因可能包括低效的车间布局、过于庞大的设备、不流畅的生产等。
对此,应杜绝孤岛式生产,合理紧凑安排工序,让作业流动起来,形成节拍,从而无需过多运输。
2. 动作浪费:表现如作业动作不连贯、幅度过大、转身角度大、弯腰、动作重复或多余等。
这会对生产效率、质量以及人员安全造成负面影响。
应从人机工程学角度,合理运用工业工程手法来进行作业台布局优化以及作业动作标准化。
3. 加工浪费:表现如加工余量过大、无谓的加工精度、多余的产品功能、重复检验包装等。
原因可能是自以为是的作业,而不是以客户价值为导向。
应对现有工序进行审视,用省略、替代、重组或合并的方法,同时精准把握客户需求、优化作业标准以及工序间的衔接。
4. 不良浪费:表现如生产过程产生的不良品。
原因包括人工操作不当、工艺设置不当、材料使用不当、质量标准不清等。
应确保作业指导以及检验标准符合产品特性以及客户需求,通过首样检验、巡检、自检互检方式第一时间发现不良,制定极限样品以及将检验标准可视化,适度运用防呆法进行防错设置。
5. 等待浪费:表现如人员(以及设备)在等待,或者有时忙、有时闲的不均衡现象。
原因如生产线品种切换、工作量少、时常缺料、设备闲置等。
应实施生产均衡化,快速换模技术的运用,全员生产性防护,多技能工,消除不良浪费,提升供应商水准。
6. 过量生产:这是常被视为最大的浪费。
其结果导致库存、资金的占用以及潜在的报废风险。
应形成一个流、节拍化生产。
“一个流生产”是指从毛坯投入成品产出的整个制造加工过程,零件始终处于不停滞、不堆积、不超越的状态。
每道工序加工完一个制件后立即流到下一工序;工序间的在制品数量不超过前工序的装夹数量。
零件的运动不间断、不超越、不落地。
只有合格的产品才允许往下一道工序流。
节拍化生产要求是需求节拍与生产节拍平衡。
七大浪费消除方法
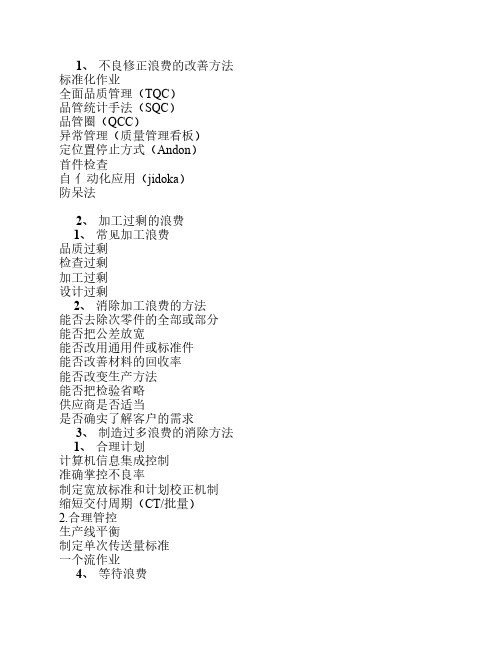
全额百分比 70%-75% 15%-25% 10%以下
1、 不良修正浪费的改善方法 标准化作业 全面品质管理(TQC) 品管统计手法(SQC) 品管圈(QCC) 异常管理(质量管理看板) 定位置停止方式(Andon) 首件检查 自 亻动化应用(jidoka) 防呆法
2、 加工过剩的浪费 1、 常见加工浪费 品质过剩 检查过剩 加工过剩 设计过剩 2、 消除加工浪费的方法 能否去除件 能否改善材料的回收率 能否改变生产方法 能否把检验省略 供应商是否适当 是否确实了解客户的需求 3、 制造过多浪费的消除方法 1、 合理计划 计算机信息集成控制 准确掌控不良率 制定宽放标准和计划校正机制 缩短交付周期(CT/批量) 2.合理管控 生产线平衡 制定单次传送量标准 一个流作业 4、 等待浪费
消除方法
1、 cell生产 2、 线平衡 3、 人机作业分离 4、 全员生产性维护(TPM) 5、 快速切换(SMED) 5、 消除库存浪费的方法 1、 ABC分类管理法
类别
品种比分比
A
5%-15%
B
15%-40%
C
40%以上
2、 JIT生产方式 3、 控制在库全额 4、 定期盘点 5、 库存警示法 6、 搬运浪费消除方法 1、 全球化布局 SLP 2、 搬运手段合法化 Conveyor AGA(Antomation Guided vehicle) 定量搬运和定时搬运 集中配料和集中包装
精益生产:减少七大浪费的综合途径
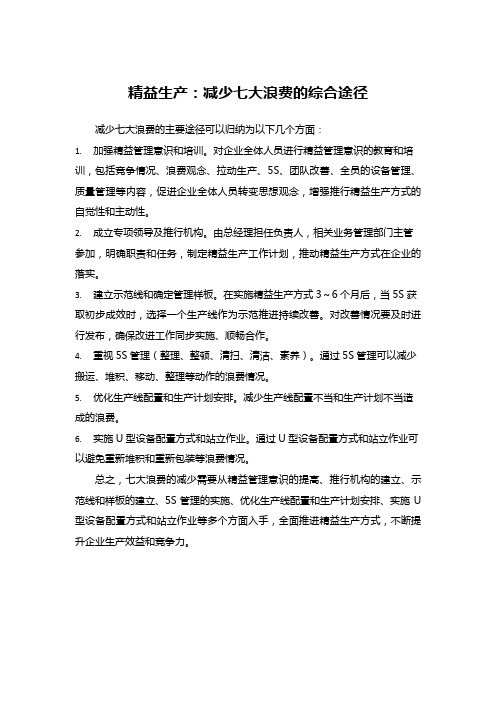
精益生产:减少七大浪费的综合途径减少七大浪费的主要途径可以归纳为以下几个方面:
1.加强精益管理意识和培训。
对企业全体人员进行精益管理意识的教育和培训,包括竞争情况、浪费观念、拉动生产、5S、团队改善、全员的设备管理、质量管理等内容,促进企业全体人员转变思想观念,增强推行精益生产方式的自觉性和主动性。
2.成立专项领导及推行机构。
由总经理担任负责人,相关业务管理部门主管参加,明确职责和任务,制定精益生产工作计划,推动精益生产方式在企业的落实。
3.建立示范线和确定管理样板。
在实施精益生产方式3~6个月后,当5S获取初步成效时,选择一个生产线作为示范推进持续改善。
对改善情况要及时进行发布,确保改进工作同步实施、顺畅合作。
4.重视5S管理(整理、整顿、清扫、清洁、素养)。
通过5S管理可以减少搬运、堆积、移动、整理等动作的浪费情况。
5.优化生产线配置和生产计划安排。
减少生产线配置不当和生产计划不当造成的浪费。
6.实施U型设备配置方式和站立作业。
通过U型设备配置方式和站立作业可以避免重新堆积和重新包装等浪费情况。
总之,七大浪费的减少需要从精益管理意识的提高、推行机构的建立、示范线和样板的建立、5S管理的实施、优化生产线配置和生产计划安排、实施U 型设备配置方式和站立作业等多个方面入手,全面推进精益生产方式,不断提升企业生产效益和竞争力。
精益生产之如何消除七大浪费

精益生产之如何消除七大浪费精益生产是一种管理理念,旨在最大限度地减少浪费,提高生产效率。
其中,被称为七大浪费的问题是影响生产效率的关键因素,它们分别是:过剩生产、等待时间、运输、过程中的存储、过度加工、不合格品、及其它不必要的动作。
下面将讨论这七大浪费以及如何消除它们。
首先,过剩生产是指生产超过需求量的产品或服务。
这会导致库存积压、资金浪费和资源浪费。
为了消除过剩生产,企业可以采取一种名为“拉动生产”的方法,即根据市场需求,只在需要时进行生产。
这种方法可以最大程度地减少库存,并确保产品总是按需生产。
另一个浪费是等待时间。
当产品在生产过程中遇到等待时间,生产效率就会降低。
为了消除等待时间,企业可以通过优化生产线布局、减少换线时间和优化生产计划来提高生产效率。
运输也是一个浪费,它指的是物流过程中的资源浪费。
为了避免浪费,企业可以优化物流流程,减少运输中的空载、半载等情况。
此外,通过提高仓储和物流设施的效率,也可以减少运输浪费。
过程中的存储是指在生产过程中积压的产品或原材料。
过多积压会导致浪费,减少存储也是消除浪费的关键。
为了解决该问题,企业可以通过实施精细化的供应链管理,及时补充原材料,以及优化生产线的布局,减少存储空间。
过度加工是指对产品进行不必要的处理或加工。
这不仅浪费时间和资源,还会增加成本。
为了解决这个问题,企业可以通过准确定义产品要求,避免不必要的加工。
同时,通过培训员工,提高其技能水平,也能帮助减少过度加工。
不合格品是指在生产过程中产生的不符合要求的产品。
这不仅浪费了原材料和劳动力,还会降低产品质量。
为了减少不合格品,企业可以实施严格的质量控制措施,优化生产过程,并确保员工具备所需的技能和知识。
最后,还有许多与生产过程无关的不必要动作,如繁琐的文件处理、冗余的流程等。
为了消除这些不必要的动作,企业可以通过简化流程、减少文档处理、引入自动化技术等方式来提高效率。
综上所述,消除七大浪费是精益生产的核心内容之一。
如何消除七大浪费
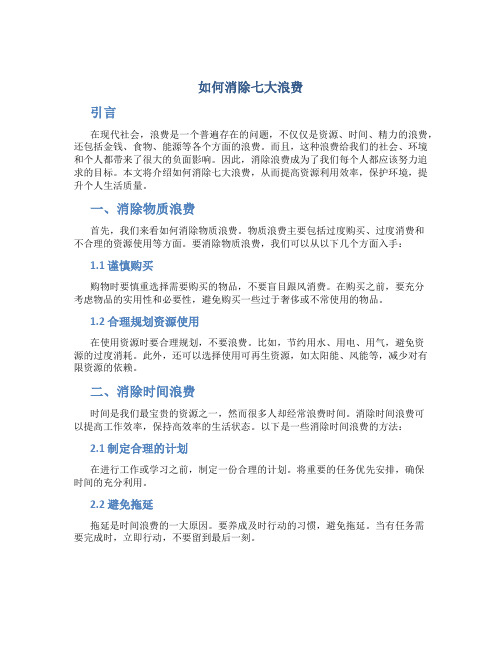
如何消除七大浪费引言在现代社会,浪费是一个普遍存在的问题,不仅仅是资源、时间、精力的浪费,还包括金钱、食物、能源等各个方面的浪费。
而且,这种浪费给我们的社会、环境和个人都带来了很大的负面影响。
因此,消除浪费成为了我们每个人都应该努力追求的目标。
本文将介绍如何消除七大浪费,从而提高资源利用效率,保护环境,提升个人生活质量。
一、消除物质浪费首先,我们来看如何消除物质浪费。
物质浪费主要包括过度购买、过度消费和不合理的资源使用等方面。
要消除物质浪费,我们可以从以下几个方面入手:1.1 谨慎购买购物时要慎重选择需要购买的物品,不要盲目跟风消费。
在购买之前,要充分考虑物品的实用性和必要性,避免购买一些过于奢侈或不常使用的物品。
1.2 合理规划资源使用在使用资源时要合理规划,不要浪费。
比如,节约用水、用电、用气,避免资源的过度消耗。
此外,还可以选择使用可再生资源,如太阳能、风能等,减少对有限资源的依赖。
二、消除时间浪费时间是我们最宝贵的资源之一,然而很多人却经常浪费时间。
消除时间浪费可以提高工作效率,保持高效率的生活状态。
以下是一些消除时间浪费的方法:2.1 制定合理的计划在进行工作或学习之前,制定一份合理的计划。
将重要的任务优先安排,确保时间的充分利用。
2.2 避免拖延拖延是时间浪费的一大原因。
要养成及时行动的习惯,避免拖延。
当有任务需要完成时,立即行动,不要留到最后一刻。
2.3 高效利用碎片时间生活中有很多碎片化的时间,如等车、排队等,这些时间可以利用起来做一些小事,如读书、回复邮件等,以此来减少时间的浪费。
三、消除能源浪费随着能源资源的日益枯竭,消除能源浪费变得尤为重要。
以下是一些消除能源浪费的方法:3.1 提高能源利用效率在使用能源时,要注意提高能源利用效率。
比如,选择能效等级高的家电产品,控制空调、暖气的使用时间和温度,避免不必要的能源浪费。
3.2 推广可再生能源的使用可再生能源是未来能源的发展方向,可以通过推广可再生能源的使用,减少对化石能源的依赖,从而达到减少能源浪费的目的。
7大浪费及消除方法
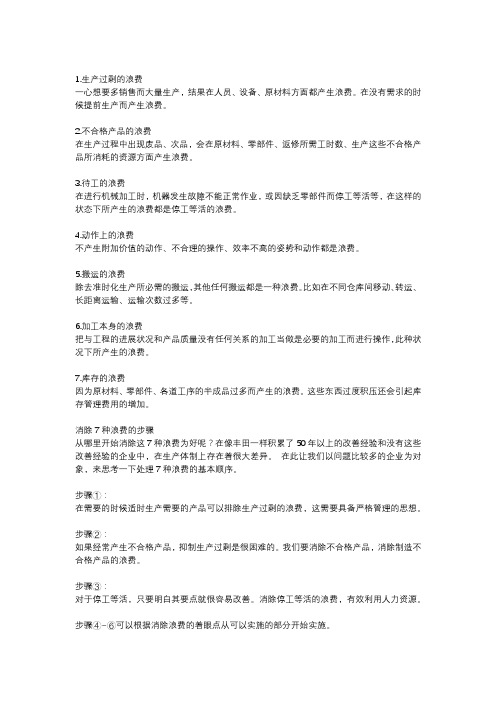
1.生产过剩的浪费一心想要多销售而大量生产,结果在人员、设备、原材料方面都产生浪费。
在没有需求的时候提前生产而产生浪费。
2.不合格产品的浪费在生产过程中出现废品、次品,会在原材料、零部件、返修所需工时数、生产这些不合格产品所消耗的资源方面产生浪费。
3.待工的浪费在进行机械加工时,机器发生故障不能正常作业,或因缺乏零部件而停工等活等,在这样的状态下所产生的浪费都是停工等活的浪费。
4.动作上的浪费不产生附加价值的动作、不合理的操作、效率不高的姿势和动作都是浪费。
5.搬运的浪费除去准时化生产所必需的搬运,其他任何搬运都是一种浪费。
比如在不同仓库间移动、转运、长距离运输、运输次数过多等。
6.加工本身的浪费把与工程的进展状况和产品质量没有任何关系的加工当做是必要的加工而进行操作,此种状况下所产生的浪费。
7.库存的浪费因为原材料、零部件、各道工序的半成品过多而产生的浪费。
这些东西过度积压还会引起库存管理费用的增加。
消除7种浪费的步骤从哪里开始消除这7种浪费为好呢?在像丰田一样积累了50年以上的改善经验和没有这些改善经验的企业中,在生产体制上存在着很大差异。
在此让我们以问题比较多的企业为对象,来思考一下处理7种浪费的基本顺序。
步骤①:在需要的时候适时生产需要的产品可以排除生产过剩的浪费,这需要具备严格管理的思想。
步骤②:如果经常产生不合格产品,抑制生产过剩是很困难的。
我们要消除不合格产品,消除制造不合格产品的浪费。
步骤③:对于停工等活,只要明白其要点就很容易改善。
消除停工等活的浪费,有效利用人力资源。
步骤④~⑥可以根据消除浪费的着眼点从可以实施的部分开始实施。
步骤④:对于动作的浪费,如果减少工时数(人数×时间)将会对消除浪费产生很大影响。
但是,即使是进行动作分析,清除了一些细小的浪费,也会被其他的问题所掩盖,所以必须注意。
步骤⑤:要消除搬运的浪费,就要在搬运距离和搬运次数等方面加以改进。
步骤⑥:对于加工过程中本身的浪费,要认识到不产生附加价值的一切东西都是浪费。
如何消除生产现场的七大浪费

现场活动包括“有附加价值的”和“没有附加价值的”活 动,那些不产生附加价值的活动应坚决予以消除
1.制造过多的浪费 2.等待的浪费 3.搬运的浪费 4.加工的浪费 5.库存的浪费 6.动作的浪费 7.制作不良的浪费
1.制造过多的浪费
消除“七大浪费”
竞争力提升
改善 消除浪费 标准化 现场5S
动作改善、作业流程改善、物流改善、设 备模夹治具改善、品质改善、管理改善等
七大浪费
动作标准化、作业流程标准化、操作流程 标准化、包装运输标准化等
整理、整顿、清扫、清洁、素养等
成本管理看板
何谓浪费:
不产生任何附加价值的 动作、方法、行为和计划
•搬运距离很远的地方,小批量的运输 •主副线中的搬运 •出入库次数多的搬运 •破损、刮痕的发生
3.搬运的浪费
原因:
•生产线配置不当 •未均衡化生产 •坐姿作业 •设立了固定的半成品放置区 •生产计划安排不当
对策:
•U型设备配置 •一个流生产方式 •站立作业 •避免重新堆积、重新包装
注意:
•工作预置的废除 •生产线直接化 •观念上不能有半成品放置区 •人性考虑并非坐姿才可以
注意:
•了解同行的技术发展 •公司各部门对于改善的共同 参与及持续不断的改善
4.加工上的浪费
产品的飞边太多,如果 通过修整模具能够使修边更 容易,则可节省人力
5.库存的浪费
不良所造成的库存,半成品所造成 的库存,制造过多所造成的库存
材料、零件、组合件等物品的停滞状 态,包括库存及在制品
表现形式:
5.库存的浪费
过多的库存会隐藏的问题点:
管理基础-消除“七大浪费”

管理基础-消除“七大浪费”引言在企业管理中,有效地消除浪费是提高生产力和效率的重要一环。
其中,被广泛认可的“七大浪费”模型为企业提供了一个框架,帮助管理者辨识和消除浪费,以提高运营效率和盈利能力。
本文将介绍七大浪费的定义和来源,并提供一些具体的消除浪费的方法。
七大浪费的定义1.过度生产:指的是生产过多、过早或过快,超过了市场需求。
这会导致产品积压、库存增加,最终造成资源的浪费。
2.待机与等待:指的是由于生产线的不协调和工序之间的时序问题,导致生产过程中长时间的待机和等待。
这会降低生产效率,增加产品的制造时间和成本。
3.过度加工:指的是对产品或工序进行超出需求范围的加工,导致额外的时间、人力和物力的浪费。
4.在运输和搬运中发生的浪费:指的是产品在运输和搬运过程中的损耗、污损和丢失。
这会增加企业的成本,降低生产效率。
5.库存过剩:指的是过多的库存积压,包括原材料、半成品和成品。
这会增加储存和管理的成本,并增加产品变质和过时的风险。
6.动作浪费:指的是生产过程中不必要的动作、重复的操作和不标准的动作,造成劳动力的浪费和生产效率的降低。
7.不合格品和修复:指的是生产过程中产生的次品和不合格品,以及为了修复次品而进行的额外操作。
这会浪费人力、物力和时间,并增加生产成本。
消除七大浪费的方法1. 过度生产的消除方法•设定合理的生产目标和计划,根据市场需求进行精确的预测和调整。
•实施“Just in Time”(准时生产)的生产模式,以减少过量库存和积压。
•实施灵活的生产线配置,可以随时调整生产速度和生产量。
2. 待机与等待的消除方法•通过流程分析和时间研究,找到生产过程中的瓶颈环节,并优化其生产速度和能力。
•实施自动化和智能化技术,减少人为因素引起的不协调和延迟。
•提供员工培训,提高操作的熟练度和效率。
3. 过度加工的消除方法•定期进行产品需求和工艺流程的评估,将加工范围控制在合理的范围内。
•优化生产线,减少并合并冗余工序。
如何消除七大浪费
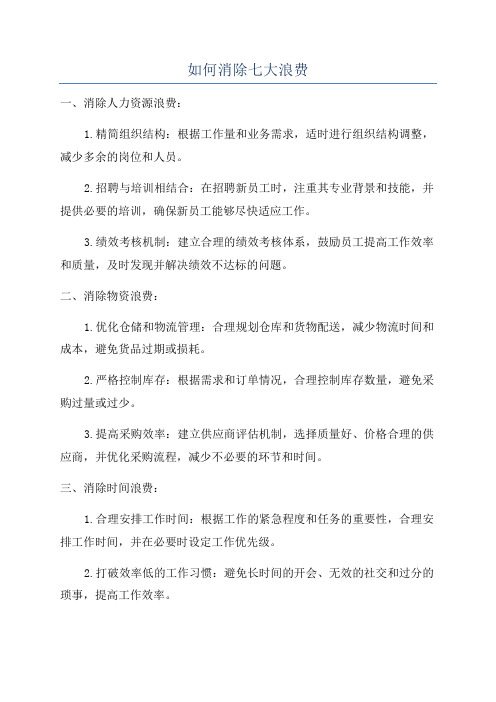
如何消除七大浪费一、消除人力资源浪费:1.精简组织结构:根据工作量和业务需求,适时进行组织结构调整,减少多余的岗位和人员。
2.招聘与培训相结合:在招聘新员工时,注重其专业背景和技能,并提供必要的培训,确保新员工能够尽快适应工作。
3.绩效考核机制:建立合理的绩效考核体系,鼓励员工提高工作效率和质量,及时发现并解决绩效不达标的问题。
二、消除物资浪费:1.优化仓储和物流管理:合理规划仓库和货物配送,减少物流时间和成本,避免货品过期或损耗。
2.严格控制库存:根据需求和订单情况,合理控制库存数量,避免采购过量或过少。
3.提高采购效率:建立供应商评估机制,选择质量好、价格合理的供应商,并优化采购流程,减少不必要的环节和时间。
三、消除时间浪费:1.合理安排工作时间:根据工作的紧急程度和任务的重要性,合理安排工作时间,并在必要时设定工作优先级。
2.打破效率低的工作习惯:避免长时间的开会、无效的社交和过分的琐事,提高工作效率。
3.制定明确的工作计划:在工作开始前制定明确的工作计划,有条不紊地完成任务,避免时间的浪费和拖延。
四、消除能源浪费:1.提高能源利用效率:采用节能设备和技术,优化能源使用结构,减少能源浪费。
2.建立能源监测系统:通过实时监测能源使用情况,发现并解决能源浪费问题,促进能源的节约和合理利用。
五、消除技术浪费:1.定期更新和维护技术设备:及时更新技术设备,定期进行维护和保养,降低因技术设备故障造成的浪费。
2.提供必要的技术培训:确保员工能够熟练掌握和运用所需的技术设备,减少由于技术操作不当导致的浪费。
六、消除人员浪费:1.建立合理的工作分配机制:根据员工的技能和能力,合理分配工作任务,避免人员过度或不足。
2.培养多岗位能力:鼓励员工尝试不同的工作岗位,提高他们的多岗位能力,减少人员流动导致的浪费。
七、消除质量浪费:1.加强质量管理:建立完善的质量管理体系,加强对产品和服务的质量监控。
2.培养质量意识:加强员工的质量意识培养,促使员工注重细节和注重质量,减少因质量不达标造成的浪费。
如何识别与消除七大浪费
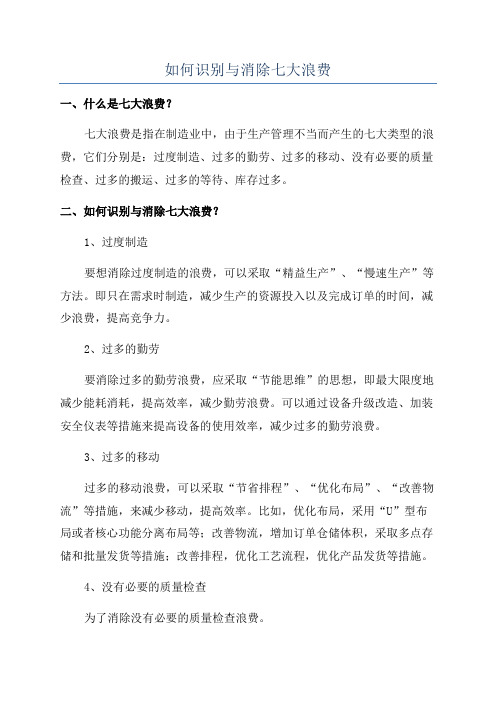
如何识别与消除七大浪费
一、什么是七大浪费?
七大浪费是指在制造业中,由于生产管理不当而产生的七大类型的浪费,它们分别是:过度制造、过多的勤劳、过多的移动、没有必要的质量检查、过多的搬运、过多的等待、库存过多。
二、如何识别与消除七大浪费?
1、过度制造
要想消除过度制造的浪费,可以采取“精益生产”、“慢速生产”等方法。
即只在需求时制造,减少生产的资源投入以及完成订单的时间,减少浪费,提高竞争力。
2、过多的勤劳
要消除过多的勤劳浪费,应采取“节能思维”的思想,即最大限度地减少能耗消耗,提高效率,减少勤劳浪费。
可以通过设备升级改造、加装安全仪表等措施来提高设备的使用效率,减少过多的勤劳浪费。
3、过多的移动
过多的移动浪费,可以采取“节省排程”、“优化布局”、“改善物流”等措施,来减少移动,提高效率。
比如,优化布局,采用“U”型布局或者核心功能分离布局等;改善物流,增加订单仓储体积,采取多点存储和批量发货等措施;改善排程,优化工艺流程,优化产品发货等措施。
4、没有必要的质量检查
为了消除没有必要的质量检查浪费。
精益生产之消除七大浪费并实现价值流改善的方法

精益生产之消除七大浪费并实现价值流改善的方法消除七大浪费并实现价值流改善的方法可以包括以下步骤:1.理解和识别浪费:首先,需要理解和识别七大浪费,包括过量生产、运输、库存、动作、等待、废品和过多品种。
这些浪费都会导致生产效率下降,成本增加,同时也可能导致产品质量下降。
2.精益生产:实施精益生产方式,例如通过5S管理(整理、整顿、清扫、清洁和素养)等,来改进现场管理,提高生产效率及产品质量。
同时,建立一个项目领导和项目推行小组来指导和监督精益生产的实施。
3.价值流图析:使用价值流图析工具,将生产过程中的所有步骤和浪费都展示出来。
这有助于发现哪些步骤是不增值的,哪些步骤是导致浪费的关键点。
4.消除浪费:根据价值流图析的结果,制定消除浪费的策略。
例如,对于过量生产,可以改进生产计划和生产排程,实施小批量生产和拉动生产方式;对于运输,可以优化生产线布局和物料搬运方式,减少运输距离和次数;对于库存,可以实施准时制生产和零库存管理策略;对于动作和等待,可以改进工作流程和设备布局,减少员工动作和等待时间;对于废品和过多品种,可以改进产品设计、生产计划和物料管理,减少废品和过多品种的产生。
5.持续改进:在消除浪费的过程中,需要持续改进和优化生产过程。
这可以通过实施持续改进小组、鼓励员工提出改进意见、定期评估生产过程等方式实现。
6.价值流管理:通过信息集成和共享,将价值流管理应用于整个供应链。
这可以帮助企业更好地管理和协调供应商、制造商和分销商之间的合作关系,实现更高效的生产和更低的成本。
7.创新和能力提升:通过创新和能力提升,不断改进生产过程和技术,以适应市场的变化和需求。
这可以通过引入新技术、新工艺、新设备和新管理方法来实现。
总之,消除七大浪费并实现价值流改善需要一个长期的过程,需要企业不断地改进和创新。
通过实施上述策略和方法,企业可以逐步消除七大浪费,提高生产效率和质量,降低成本,并实现可持续发展。
七大浪费认知与消除
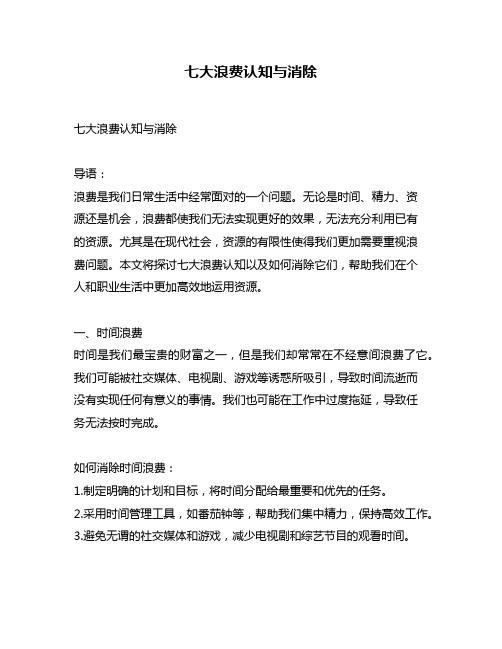
七大浪费认知与消除七大浪费认知与消除导语:浪费是我们日常生活中经常面对的一个问题。
无论是时间、精力、资源还是机会,浪费都使我们无法实现更好的效果,无法充分利用已有的资源。
尤其是在现代社会,资源的有限性使得我们更加需要重视浪费问题。
本文将探讨七大浪费认知以及如何消除它们,帮助我们在个人和职业生活中更加高效地运用资源。
一、时间浪费时间是我们最宝贵的财富之一,但是我们却常常在不经意间浪费了它。
我们可能被社交媒体、电视剧、游戏等诱惑所吸引,导致时间流逝而没有实现任何有意义的事情。
我们也可能在工作中过度拖延,导致任务无法按时完成。
如何消除时间浪费:1.制定明确的计划和目标,将时间分配给最重要和优先的任务。
2.采用时间管理工具,如番茄钟等,帮助我们集中精力,保持高效工作。
3.避免无谓的社交媒体和游戏,减少电视剧和综艺节目的观看时间。
二、精力浪费精力是我们完成任务和克服困难的动力来源。
然而,不良的生活习惯和压力过大可能会导致我们浪费精力。
长时间熬夜、不合理的饮食和缺乏锻炼,都会降低我们的精力水平。
如何消除精力浪费:1.保持规律的作息时间,确保充足的睡眠。
2.均衡饮食,摄入适量的维生素和营养物质。
3.每天进行适量的运动,让身体和大脑得到充分的休息和恢复。
三、物质浪费现代社会给我们带来了极大的物质便利,但也促使我们对物质产生浪费的心理。
我们可能买更多的衣物、电子产品或食品,但很少充分利用它们。
我们也可能在不需要的东西上花费过多的金钱。
如何消除物质浪费:1.在购买物品前,慎重考虑自己是否真的需要它们,并尽量减少冲动消费。
2.购买耐用品,确保其质量和实用性,避免频繁更换和浪费。
3.合理规划食物,减少食物的浪费。
四、机会浪费机会浪费是指我们错过了可以用来发展个人和职业的机会。
无论是一次重要的会议、一个有意思的活动,还是一个能够提升自己的培训课程,我们可能因为各种原因而错过了这些机会。
如何消除机会浪费:1.保持敏锐的观察力,了解并抓住可能出现的机会。
七大浪费及改善七大步骤

七大浪费及改善七大步骤随着生活水平的提高,人们的消费水平也越来越高。
然而,随之而来的是资源的浪费和环境的破坏。
在日常生活中,我们可能会犯下七大浪费,这些浪费不仅影响我们的生活质量,也会对环境造成不良影响。
接下来,本文将介绍七大浪费及改善七大步骤。
一、能源浪费能源浪费是指在生活和工作中,对能源的不合理使用和浪费。
比如,开着空调却打开窗户、长时间使用电脑等。
这些行为不仅浪费能源,也会增加能源成本,对环境造成不良影响。
改善步骤:采用节能环保的家电、合理使用空调、注意用电安全等。
二、食物浪费食物浪费是指在生活中对食物的不合理使用和浪费。
比如,买了很多食物但不吃或者吃不完、过期食品等。
这些行为不仅浪费食物,也会增加浪费成本,对环境造成不良影响。
改善步骤:合理规划食物的购买和使用、注意食品保质期、剩余食物能够捐赠等。
三、水资源浪费水资源浪费是指在生活和工作中对水的不合理使用和浪费。
比如,洗衣服时不注意节水、洗澡时间过长等。
这些行为不仅浪费水资源,也会增加水资源成本,对环境造成不良影响。
改善步骤:合理使用水资源、注意节水、修复漏水等。
四、纸张浪费纸张浪费是指在生活和工作中对纸张的不合理使用和浪费。
比如,打印太多不必要的文件、写字时习惯浪费纸张等。
这些行为不仅浪费纸张,也会增加浪费成本,对环境造成不良影响。
改善步骤:合理使用纸张、尽量使用电子文档、回收废纸等。
五、塑料浪费塑料浪费是指在生活和工作中对塑料制品的不合理使用和浪费。
比如,购物时使用过多的塑料袋、习惯使用一次性塑料餐具等。
这些行为不仅浪费塑料资源,也会增加浪费成本,对环境造成不良影响。
改善步骤:使用环保袋、减少使用一次性塑料餐具、回收废弃塑料等。
六、时间浪费时间浪费是指在生活和工作中对时间的不合理使用和浪费。
比如,习惯拖延时间、没有合理规划时间等。
这些行为不仅浪费时间,也会增加浪费成本,对生活和工作造成不良影响。
改善步骤:合理规划时间、养成良好的时间管理习惯等。
识别消除生产中的七大浪费
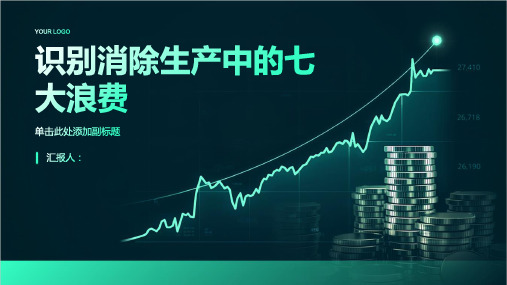
实施精益采购管理:通 过精确的需求预测、合 理的供应商选择和采购 策略制定,降低采购成
本和库存水平。
实施精益生产管理:通 过优化生产计划、提高 生产效率和减少生产过 程中的变异,降低生产
成本和库存水平。
实施精益质量管理:通 过加强质量管理和控制、 提高产品质量和客户满 意度,减少因质量问题
实施消除七大浪费需要全员 参与,从基层员工到高层领
导都要积极投入。
费
目视化管理:通过可视 化手段,及时发现和解 决问题,提高生产效率
防错法:通过设计容错 机制,避免生产过程中
的人为错误和浪费
精益培训:提高员工精 益管理意识和技能,促 进全员参与和减少浪费
优化生产计划,减少过量生产
制定合理的生产计划,根据市场需求和产能进行平衡 引入精益生产理念,减少生产中的浪费 引入生产管理系统,实现生产过程的可视化与可控制 引入生产调度系统,实现生产计划的动态调整与优化
定义:等待时间浪费是指生产过 程中由于生产计划安排不合理、 生产设备故障等原因导致生产停 滞或等待时间过长。
原因:生产计划安排不合理、生 产设备故障、原材料供应不及时、 员工技能不足等。
添加标题
添加标题
添加标题
添加标题
影响:等待时间浪费会导致生产 效率下降、生产成本增加,同时 也会影响员工的工作积极性和生 产情绪。
单击添加标题
识别七大浪费的 方法
实施消除七大浪 费的注意事项
生产中的七大浪 费
消除七大浪费的 措施
过量生产浪费
定义:生产过多的产品或提前 生产产品
影响:导致库存成本的增加、 占用资金、降低生产效率等
原因:需求不明确、计划不准 确、生产控制不当等
七大浪费认知与消除

七大浪费认知与消除七大浪费是指在生产和运营过程中常见的浪费现象,该概念源于精益生产和精益管理的原则。
以下是七大浪费以及相应的认知和消除方法:1.过产出(Overproduction):指在没有需求或超出需求的情况下生产产品。
认知:了解真实需求以避免过度生产。
消除:实施精确的预测和生产计划,并实时调整以适应市场需求。
2.待料(Waiting):指在生产过程中由于缺乏所需材料或信息而导致工作停滞。
认知:审查供应链和内部流程,消除物料短缺和信息传递障碍。
消除:通过改进供应链管理、有效库存控制和沟通流程来减少等待时间。
3.运输(Transportation):指在生产和供应链过程中不必要的物料或产品移动。
认知:通过简化物流和布局来减少物料或产品的运输。
消除:重新设计流程以最小化移动和处理步骤,优化物流路径,减少运输成本和时间。
4.不良品(Defects):指生产中出现的缺陷、错误或不符合质量要求的产品。
认知:意识到质量问题的成本和影响。
消除:实施严格的质量控制和管理措施,改进生产工艺和技术,并进行员工培训。
5.过度加工(Overprocessing):指过度处理、加工超过产品要求的过程。
认知:理解产品和客户需求,避免不必要的工艺和加工。
消除:通过精益工程和价值流映射来优化生产工艺,去除冗余步骤和不必要的复杂性。
6.人员运动(Motion):指由于不必要的动作、移动或步骤而浪费时间和能量。
认知:意识到不必要的动作和移动的低效性。
消除:优化工作站布局和生产流程,减少人员不必要的运动和交通。
7.多余库存(Inventory):指超过所需量的物料或产品库存。
认知:明白多余库存的成本和风险。
消除:实施精确的库存控制和管理,最小化库存持有成本,并与供应链合作伙伴优化库存水平。
通过认知和消除这七大浪费,企业可以提高生产效率,降低成本,提供更好的顾客满意度,并提升整体业绩。
这需要持续的改进和精益管理的原则在企业内部实施和推动。
消除浪费的七种办法

浪费是“除对生产不可缺少的最小数量的设备、原材料、零件部和工人(工作时间)外的任何东西”。
包括:1)过量生产的浪费,2)等待时间的浪费,3)运输的浪费,4)库存的浪费,5)过程(工序)浪费,6)动作的浪费,7)产品缺陷的浪费。
消除浪费的方法如下:1.集中工厂网络按照统一目标设计的多家工厂可以更好的组织起来,并使经营更加经济。
一般是建立小规模专业化工厂而不是大型纵向一体化的制造厂。
2.成组技术与将工作从一个部门转移到另一个部门交给专业化员工操作不同,成组技术考虑了制作一个零件的所有操作,并将完成这些操作的机器放在一起。
成组技术单元减少了不同操作间的移动、等待时间和在制品库存,也减少了所需员工的人数。
然而,员工必须具有充分的柔性以便能够操作工作中的集中设备,完成工件的加工过程。
由于供人们具有先进的技术水平,因此工作的安全性也得到了保证和提高。
3.源头质量的控制控制源头质量意味着在工作之初就要做得十分正确。
当出现错误时立即停止该工序或装配线。
工人成为自己工作的检查者,独自对其产品质量负责。
由于工人一次只注意工作的一部分,因此就容易发现工作中存在的质量问题。
源头质量包括自动化或称为自动检测。
自动设备或机器人进行质量检查,更快捷、容易、可重复性强,适合规模太大太复杂,不能由人工完成的工作。
4. JIT生产JIT意味着在必要的时候生产必要的产品,不要过量生产。
超过所需最小数量的任何东西都将被看成是浪费,因为现在再不需要的事物上投入的精力和原材料都不能在现在被使用。
JIT 已被用于重复性生产企业。
尽管工作站间可能区别很大,但还是可以实现过渡时间的最小化,同时保持运送数量最小--通常是把每日生产总数的1/10作为单位运送批量规模。
供应商有时甚至要每日供应多次物料,以保持小批量规模和低库存。
当所有等待数量变为零时,库存投资实现最小化,提前期大大缩短,企业对需求变化快速反应,质量问题也得以迅速曝光。
5.均衡生产负荷平衡生产流可以减少通常情况下由于计划不均衡所带来的反应,成为均衡车间生产负荷.当总装线发生变化时,这种变化就在整条生产线上和供应链上被放大了。
识别消除生产中的七大浪费经典

识别消除生产中的七大浪费经典引言生产中的浪费是指在生产过程中没有为最终产品增加价值或效率的活动或使用资源。
识别和消除这些浪费是持续改进生产效率和质量的关键。
本文将介绍生产中的七大经典浪费,以及如何识别和消除它们。
1. 运输浪费运输浪费是指在生产过程中物料或产品的移动过程中产生的浪费。
这包括长距离的运输、频繁的运输和不必要的运输。
运输浪费会增加生产成本并延长生产周期。
如何识别运输浪费•检查生产过程中物料或产品的运输路径;•分析是否存在频繁的物料或产品运输;•观察是否存在长距离的物料或产品运输;如何消除运输浪费•优化物料或产品运输路径,减少距离;•合并运输批次,减少频繁的运输;•在生产线上设置等待区域,避免长距离的运输;2. 库存浪费库存浪费是指在生产过程中存放大量物料或产品而没有产生价值的浪费。
过多的库存会增加仓储成本,并且可能导致过时或损坏的物料或产品。
如何识别库存浪费•检查库存数量是否过多;•观察是否存在过时或损坏的物料或产品;•分析是否存在生产过程中的停滞点;如何消除库存浪费•优化生产计划,减少库存数量;•定期检查并处理过时或损坏的物料或产品;•减少生产过程中的停滞点,提高生产效率;3. 过程浪费过程浪费是指在生产过程中存在的无效操作或步骤。
这可能包括重复的步骤、不必要的检查、等待时间等。
过程浪费会降低生产效率并增加生产周期。
如何识别过程浪费•观察生产过程中是否存在重复的操作步骤;•分析是否存在不必要的检查;•检查生产过程中是否存在等待时间;如何消除过程浪费•重新设计生产过程,消除重复的操作步骤;•优化检查过程,减少不必要的检查;•减少生产过程中的等待时间,提高生产效率;4. 超生产浪费超生产浪费是指在生产过程中生产超过实际需求的产品的浪费。
这会导致过多的库存和资金占用。
如何识别超生产浪费•检查生产计划和实际需求之间的差异;•观察是否存在未经授权的生产;•分析是否存在过多的库存;如何消除超生产浪费•根据实际需求调整生产计划;•确保所有生产都经过授权和计划;•减少库存数量,以及库存周转周期;5. 待料浪费待料浪费是指在生产过程中等待物料或工具到位而产生的浪费。
- 1、下载文档前请自行甄别文档内容的完整性,平台不提供额外的编辑、内容补充、找答案等附加服务。
- 2、"仅部分预览"的文档,不可在线预览部分如存在完整性等问题,可反馈申请退款(可完整预览的文档不适用该条件!)。
- 3、如文档侵犯您的权益,请联系客服反馈,我们会尽快为您处理(人工客服工作时间:9:00-18:30)。
生产的浪费
1.过量生产 2.缺陷 3.多余加工 4.库存
5.搬运 6.多余动作 7.等待
定义 • 任何超过单件流
的供应
对策
• 意识改变 • U型生产 • 看板管理
原因
• 先行生产 • 库存越多越好意识 • 工艺,设备不稳定
问题
• 空间浪费 • 隐藏生产问题 • 压制改善欲望 • 周转奖金增加
生产的浪费
总装厂
原材料 发货
零件生产 客户
价值流程图 (VSM) 是一个手工方法通过用特定的图标绘画来表现整个价值流的 过程,包括物流,信息流和过程流。
• 价值流图可以帮助我们直接观察到: – 整体的作业流动 – 材料和信息流之间的连接 – 7种浪费 – 引起浪费的系统问题 – 影响大的改进区域 – 将不同部门或职能的问题联系在 一起
价值 流
过
程
冲压
过
程
焊接
过
程
总装单元
原材料
成品
也可以用价值流的方法来绘制业务过程。
价值流程图
信息流
过程流 物料流
★ 价值流的绘制是帮助你找到浪费,观察到整个流程状 态的简单工具。注意整个流程,目的在于消除浪费!
价值流包含的是特定产品从进公司到发货至客户的所有要素 (包括增值的和非增值的)。
需求
设计
2.缺陷 3.多余加工 4.库存 5.搬运 6.多余动作 7.等待
定义 • 生产的数量或速
度超客户需要
对策
• 单件流 • 看板拉动生产 • 少人化,均衡化
原因
• 过剩人员,设备 • 不停线 • 批量生产
问题
• 搬运 • 妨碍物流 • 长期再库,不良 • 压缩生产空间
制造的浪费 1.过量生产 2.缺陷
操作者
价值流程图-过程流绘制
供应商
生产计划
客户
加工
THM1-100 人力:5
C/T:15 s 总装:68s OEE:65%
报废率:5%
1班/天
装配
… …
.. .. .. ..
..
包装
… …
.. .. .. ..
..
价值流程图-物料流绘制
价值流程图-物料流绘制
供应商
生产计划
客户
I 2.0d
加工
THM1-100 人力:5
1.过量生产 2.缺陷 3.多余加工 4.库存 5.搬运
6.多余动作 7.等待
定义 • 任何不是为了及
时生产的搬运
对策
•U字型布局 •流动生产方式 •多技能化、站着作 业
原因
• 布局不好 • 工程间批量生产
问题
• 增加搬运人员及工 具
• 因搬运造成作业等 待
生产的浪费
1.过量生产 2.缺陷 3.多余加工 4.库存 5.搬运 6.多余动作
生产的浪费
1.过量生产 2.缺陷 3.多余加工
4.库存 5.搬运 6.多余动作 7.等待
定义
• 没有对产品增加 价值的工艺加工!
对策
• 品质要求标准化 • 作业内容标准化 • 工具改善
原因
• 提高不必要加工的 精度
• 工具不好使 • 原材料标准不一致
问题
• 不必要的操作,人员
• 不良品的增加 • 低效率
试计算该产线的时间稼动率、开动率?
总劳动时间 = 日历时间–无排程时间-用餐时间 = 720-120-90=510(min)
稼动时间 = 总劳动时间–计划停止时间-非计划停止时间 =510-10-10-30-30-30-20=340(min)
时间稼动率 = 稼动时间/总劳动时间 * 100% = 340 / 510 *100% = 66.7%
从产品整个流程角度思考!
流程中”产品”涉及的 4 项活 动!
1. 运输 2. 存放 Байду номын сангаас. 检验 4. 加工
我们的现状
10% 0.5d 70-80% 4.0d 5-10% 4.0H
1-5% 1.0H
世界级水平
<2% <18%
0 >80%
您的流程为何不能流动起来?现在开始识别浪费源!
七种浪费形式
生产的浪费 1.过量生产
C/T:15 s 总装:68s OEE:65%
报废率:5%
1班/天
I 0.5d
装配
… …
.. .. .. ..
..
包装
…
…
I ..
2.0d
.. ..
..
..
1次/d
I 1.0d
价值流程图-信息流绘制
价值流程图-信息流绘制
供应商
采购单 3d
生产计划
每周
月订单 7d
每日
客户
20,000台 交期:30d
= 41.6%
提示:操作时间=总花费时间-无排程时间-用餐-计划停止时间
时间稼动率
时间稼动率
=
稼动时间 总劳动时间
×100%
总劳动时间=日历时间-无排程时间-用餐时间(即有薪时间) 稼动时间=总劳动时间-计划停止时间-非计划停止时间
=日历时间-无排程时间-用餐-计划停止时间-非 计划停止时间 开动率=稼动时间/日历时间*100%
定义 • 工序之间的空闲
对策
•标准化生产 •防止失误装置 •Cycle内准备交换
原因
• 熟练工与非熟练工的 差异
• 作业量的差异 • 突发的品质事故
问题
• 作业者之间产生不满
• 人,作业,时间,机 械的浪费提供,再 库的增大
消灭浪费的顺序
1 •认识浪费 2 •生产效率 3 •价值流图
传统效率
165s
1.0d 5.5d
价值流程图-改善点绘制
改善点
价值流程图-改善点
供应商
在线 库
I 2.0d
2.0d
采购单 3d
生产计划
拉动 生产
每周
周期 过长
月订单 7d
每日
客户
20,000台 交期:30d
T/T:28.8s/台
人员, 设备,
闲加置工
THM1-100 人力:5
C/T:15 s 总装:68s OEE:65%
T/T:28.8秒/台
I 2.0d
2.0d
加工
THM1-100 人力:5
C/T:15 s 总装:68s OEE:65%
报废率:5%
1班/天
68 s
I 0.5d
0.5d
装配
… …
.. .. .. ..
..
120s
I 2.0d
2.0d
包装
… …
.. .. .. ..
..
50s
1次/d
I 1.0d
0.1%
=
600 600 + 50
×100%
= 92.3%
设备综合利用率(OEE: Overall Equipment Effectiveness)
OEE = 时间稼动率× 性能稼动率×良率 稼动时间 标准加工时间 良品数
= 总劳动时间 × 稼动时间 × 总产出数 稼动时间 总产出数× C/T 良品数
= 总劳动时间 × 稼动时间 × 总产出数 良品数× C/T
Manufacturing Process
Scrap
Kaizen闪光点/ 爆炸点
外部资源/ 客户
缓冲区/ 安全库存
数据盒
I
库存
o oo
卡车运输
手工的 信息流
Electronic Information Flow
Production Kanban
成品至客户
Withdrawal Kanban
推动箭头
Signal Kanban
报废率:5%
1班/天
68.0 s
连续 流
I 0.5d
0.5d
装配
… …
.. .. .. ..
..
120s
连续 流
I 2.0d
2.0d
包装
… …
.. .. .. ..
..
50s
1次/d
I 1.0d
0.1%
165.0s
1.0d 5.5d
价值流程图-未来流程
供应商
采购单 3d
生产计划
月订单 3d
客户
20,000台 交期:30d
操作效率
=
标准时间 操作时间
×100%
IE效率=? 操作效率=? (宽放系数15%)
IE效率
=
增值时间 总花费时间
128× 600 = 12× 60× 60× 8 = 22.2%
操作效率
=
标准时间 操作时间
(128 + 25)× (1+15%)× 600 = (12× 60 −120 − 90 −10 -10 - 30)× 60× 8
制造周期缩短80%,生产效率提升25%,WIP降低85%, 面积减少30%
价值流图析
实施精益系统,消除过程浪费的基础与关键点,是企业全观 自身问题点及设定改善目标的工具,是企业把握命脉-交货期的唯一 有效工具:
☆建立人员精益的概念,识别精益的改进机会; ☆帮助人们容易发现过程中何处产生浪费; ☆认识价值的构成因素与重要性; ☆掌握实际绘制”价值流图”的能力,成为一位称职的经营管理者; ☆通过价值流图示中的应用,通过数据,量化改善机会的次序; ☆通过价值流图示技巧,设定改善机会,改善目标; ☆利用价值流解决企业制造系统问题的专业工具和管理技能 。
= 总劳动时间
OEE=时间稼动率*性能稼动率*良率 =66.7%*82.8%*92.3%=51.0%