高洁净度管线钢中元素的作用与控制
管线钢精炼渣系的开发与钢中磷硫氮全氧的控制

s ew sot l d ( 7 ×0 , t l a cn o e P 0 1 6 S≤2 l3 e rl ≤1 r 0 0 ,N≤5 ×0,t hl0 5 l3 . x 0 l 6 h w o  ̄ 0x0 r e e <
Ke o ds Pi e i e S e l Re n n l g S re ; Ha mf lElme t n r l S c n a y Rei i g y W r : p ln te ; i f igSa eis r u e n s Co to ; e o d r fn n
De eo m e fRe n n l g S re fPi lne St e nd Co t o v lp nto f i g S a e iso pei e la n r l i
P o p o u o e To a y e u f r a d Ni o e si t e h s h r ft t lOx g n S lu n t g n n S e l h r
o epo u t no eiig l eis (0 5 %C 0,6 1% S0 ,2 %- 5 1 3 %- %Mg ). fh rd ci f f n a S r t o R n Sg e 5 %- 5 a %- 0 i2 1 2 %A 2 ,5 8 0 0
Ac o d n ed s n o er f i gsa n i ei es e a r d ce , a d t eh r u l me t e c r i gt t e i f h i n l gma yp p l t l s o u t d n a mf l e n si t oh g t e n n e w p h e nh
21 生产 条件 .
10 双 工 位 L 5t F钢 包 精 炼 炉 、 1台 10 双 工 位 5t R H真 空 精 炼 炉 、 1台 2 0 2mm ̄ 0mm板 坯 连 150 铸 机 、 1台 2 0 mx 1m 板 坯 连 铸 机 、 1 2 m 180 m 台 7机 7流 小 方 坯 连 铸 机 。生 产 主要 原 材 料 见
钢中氧的控制

3MnO. Al2O3.3SiO2(锰铝榴石)的作用
• 熔点低,1400℃;球形易于上浮; • 夹杂物可塑性好(800℃~1300℃); • 钢中无Al2O3析出,钢水可浇性好; • 脱氧良好,铸坯无皮下气泡形成。
脱氧及夹杂物的生成控制-铝镇静钢
形成的脱氧产物: Al2O3,其危害:
• 熔点高,2050℃;固态析出与钢水; • 可塑性差,影响钢材性能;
3、 LD-LF-CC 流程氧的控制
高纯净钢缺陷产生的原因调查
钢种
DI罐用镀锡板 ERW管材 镀锡板 深冲用冷轧钢 板 UO管材 UOE管(厚钢 板) 产品缺陷 飞边裂纹 UT缺陷 US缺陷 炉渣分层 冲压缺陷 夹杂 UT缺陷 US缺陷 引起缺陷夹杂物 最小直径
150um 、60um 150um 220um 400um、150um
[C][O]=0.0027, 炉龄<2500(炉) Ⅱ区: a[O] 远离在C-O平衡线; [C][O]:0.0031~0.0037, 炉龄> 2500(炉) Ⅲ区(其它区域): [C][O]:远离C-O平衡线且波动 较大,复吹效果降低。
转炉终点氧的控制-终点温度的控制
转炉终点温度的控制(生产统计):
[C]=0.02%~0.05%,顶吹终点a[O] = 700ppm~900ppm; 复吹终点a[O] = 250ppm~600ppm。
脱氧及夹杂物的生成控制
连铸钢种脱氧的模式 硅镇静钢:-脱氧剂:Si+Mn 硅-铝镇静钢-脱氧剂:Si+Mn+Al(少量) 铝镇静钢--脱氧剂:过剩Al,[Al]>0.01%。
渣相的吸收
夹杂物的排除(钢包精炼)
连铸过程钢中氧的控制-钢水二次污染的防止 连铸过程氧的控制关键 防止钢的二次氧化 进一步利用连铸中间包、结晶器排除夹杂
X70管线钢洁净度控制

关 键词 : 管线钢
洁净度
夹杂物 过程控制
Co t o f Cla lne s o 0 Pi e i t e n r lo e n i s fX7 p l ne S e l
Ca e e Ca iK s n o Yula i ng W a g Pan e n f ng
前 言
含量 和控制非金属夹杂物的数量 、 形态 和尺寸 , 高 提 钢水 的 纯净 度 , 其 是对 管 线 钢 性 能 危 害 较 大 的 尤 A , Mn 夹 杂 物 的控制 , 变其 形 态 是管 线 钢 1 和 0 S 改 冶炼 的重要任务之一 。 卜 中厚板卷厂 X 0管线钢采用铁水倒 罐一铁水 预 7 处理一转炉冶炼 一 出钢 脱 氧合 金化 一 L F精炼 炉一 R H真空炉一钙处理一连铸生产工艺 流程 , 通过对 冶 炼各工序过程 的研 究和 分析 , 发出各 环节 钢水 洁 开
0 5,n d l r c s o rca k n r n l o ec a k a e fu d o n e l—ie a d a d h n y o oe , . o mid e c a k ,c me rc sa d t a ge z n r c sc n b 0 n .n e d e l n n o e c mb p r s i k
( iePae C iP a t W d lt/ ol ln )
( eh oo y& Qu l yDe a t n ) T c n lg ai p r t me t
Ab ta tT epo eso ieieseli:h tmea rt ame t- sr c :h rc s fpp l te s o tlper t n- ̄B0F ÷rf ig L / n e - — e nn ( F RH) i — C M os l pp l e C t met iei n
X80管线钢冶炼工艺研究
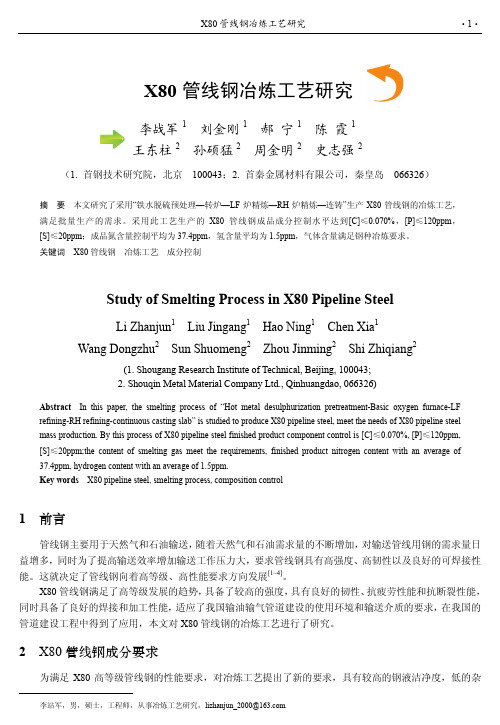
X80管线钢冶炼工艺研究李战军1刘金刚1郝宁1陈霞1王东柱2孙硕猛2周金明2史志强2(1. 首钢技术研究院,北京 100043;2. 首秦金属材料有限公司,秦皇岛 066326)摘 要 本文研究了采用“铁水脱硫预处理—转炉—LF炉精炼—RH炉精炼—连铸”生产X80管线钢的冶炼工艺,满足批量生产的需求。
采用此工艺生产的X80管线钢成品成分控制水平达到[C]≤0.070%,[P]≤120ppm,[S]≤20ppm;成品氮含量控制平均为37.4ppm,氢含量平均为1.5ppm,气体含量满足钢种冶炼要求。
关键词 X80管线钢冶炼工艺成分控制Study of Smelting Process in X80 Pipeline SteelLi Zhanjun1 Liu Jingang1 Hao Ning1Chen Xia1Wang Dongzhu2 Sun Shuomeng2 Zhou Jinming2 Shi Zhiqiang2(1. Shougang Research Institute of Technical, Beijing, 100043;2. Shouqin Metal Material Company Ltd., Qinhuangdao, 066326)Abstract In this paper, the smelting process of “Hot metal desulphurization pretreatment-Basic oxygen furnace-LF refining-RH refining-continuous casting slab” is studied to produce X80 pipeline steel, meet the needs of X80 pipeline steel mass production. By this process of X80 pipeline steel finished product component control is [C]≤0.070%, [P]≤120ppm, [S]≤20ppm;the content of smelting gas meet the requirements, finished product nitrogen content with an average of37.4ppm, hydrogen content with an average of 1.5ppm.Key words X80 pipeline steel, smelting process, composition control1前言管线钢主要用于天然气和石油输送,随着天然气和石油需求量的不断增加,对输送管线用钢的需求量日益增多,同时为了提高输送效率增加输送工作压力大,要求管线钢具有高强度、高韧性以及良好的可焊接性能。
钢的纯净度评测及其控制

钢的纯净度估测及其控制<The Evaluation Methods and Control of Steel Cleanliness>1.引言随着社会发展和科技进步, 对钢质量, 尤其对它的纯净度(cleanliness)要求越来越高. 除了要降低钢中非金属氧化物夹杂物(non-metallic oxide inclusions)的含量, 控制其尺寸、形貌和成分外, 就洁净钢(clean steel)而言, 还要求控制其硫(S)、磷(P)、氢(H)、氮(N), 甚至碳(C), 并且要尽可能减少钢中金属杂质元素(metallic impurity elements), 诸如: 砷(AS)、锡(Sn) 、锑(Sb)、硒(Se)、铜(Cu)、锌(Zn)、铅(Pb)、镉(Cd)、碲(Te)、铋(Bi)等.不同钢种因其不同的应用场合和条件,对上述要求也各不相同。
例下表所示:表1 对不同钢种典型的纯净度要求(Typical steel cleanliness requirements for various steel grades)钢中的金属杂质元素(metallic impurity elements)通常被视为残余元素(trace elements).由于它们在炼钢和精炼过程很难去除,所以在钢中不断累积,成为废钢供应的一大问题。
鉴于钢中如存在超量的残余金属元素,会造成晶间偏析(intergranular segregation)、有害析出物和其它一些问题。
目前,在钢的生产过程中为了克服钢中残余元素造成的危害,尤其是电炉炼钢,通常采用严格控制废钢的种类和用量。
近年来世界各国普遍采用高炉铁水、直接还原铁、海绵铁、碳化铁或其它相对纯的铁来替代废钢,旨在降低钢中残余元素含量。
从钢中残余元素角度讨论钢纯净度问题近年来已有不少相关研究的报道和论文发表。
我们今天主要讨论钢厂普遍存在,大家又十分关注并想得到解决的问题:〈低碳铝镇静钢氧化物夹杂对其纯净度的影响〉。
不锈钢管洁净度等级标准

不锈钢管洁净度等级标准一、概述不锈钢是一种常用的结构材料,应用广泛,其中用于洁净环境中的不锈钢更为重要。
不锈钢洁净等级划分标准是指根据洁净环境中的空气、物表等悬浮颗粒物质的浓度和大小等因素,将不锈钢产品按所需洁净度要求划分为不同等级的标准。
二、等级划分不锈钢洁净等级划分标准分为6级,分别为A、B、C、D、E和F级。
其中,A 级要求最高,逐级降低。
等级划分标准的具体要求如下:1. A级:适用于要求最高洁净度的场合,如超净室、特种工业等,要求悬浮颗粒物≤0.5μm/m³,≤5.0 μm/m³,透过颗粒物≤0.01个/每分钟/米²;2. B级:适用于洁净室、电子厂房等场合,要求悬浮颗粒物≤3.5μm/m³,≤35μm/m³,透过颗粒物≤0.1个/每分钟/米²;3. C级:适用于某些需要在相对清洁环境中工作的场合,如实验室等,要求悬浮颗粒物≤3.5μm/m³,≤70μm/m³,透过颗粒物≤0.5个/每分钟/米²;4. D级:适用于某些机械制造、组装、检测等场合,要求悬浮颗粒物≤5.0μm/m ³,≤350μm/m³,透过颗粒物≤5个/每分钟/米²;5. E级:适用于某些场合,如装配车间、铸造车间等,要求悬浮颗粒物≤10.0μm/m³,≤700μm/m³,透过颗粒物≤20个/每分钟/米²;6. F级:适用于较为一般的工业制造场合,要求悬浮颗粒物≤100.0μm/m³,≤10000.0μm/m³,透过颗粒物≤200个/每分钟/米²。
三、检测方法按照ISO 14644-1标准所述的检测方法,可采用激光粒子计数(LPC)或电子显微镜(SEM)等方式进行。
四、适用范围本标准适用于在不同洁净度(大气环境中的悬浮颗粒物)下生产和使用的不锈钢制品。
X80管线钢高洁净度钢水的冶炼实践

转炉出钢脱氧后 , 钢水中 T [ ] . O 一般控制在
2 p 0p m左 右 , 但个 别 炉次 波 动很 大 。通 过钙
处理 、 软吹 、 真空 处理及 中间包 流场作用 上 浮
去除, 同时做 好 全 流程 的 钢 水 保 护 , 以将 可 X 0管线 钢溶解 氧 质量 分 数完 全 控 制在 3— 8 9 p 钢 中全 氧 基 本 上 以夹 配 铝 , 样 形 这
图 4 钢 水 冶 炼 过 程 中 氮含 量 变 化 情 况
25 钢水 氧含 量控 制 .
图 5钢 水 冶炼 过程 中氧 含量 变 化情 况 。
为 了降 低 钢 包 顶 渣 氧含 量 : a 从 转 炉 出钢 ()
挡渣 , 减少 转炉 下 渣 量 ; b 吹 氩 站 到 L () F炉 采用 全程 控 制 钢加 铝 粒 的措 施 , 证 精 炼 过 保 程 中钢 中 [ 1 始终 参 与 对 钢包 顶 渣 的还 原 ; A] ( ) 转 炉 下渣 量 减 少 的 前 提 下 , 当 加 人 c在 适 造渣 料增 大 钢 包顶 渣 量 , 时在 加 热 时 精 确 同 调 整钢包 底 吹流量 , 现加 热过 程 的埋弧 。 实
在 R 真 空 精炼 后 , 钢 水 进 行钙 处理 和钢 H 对
后 的铁水和废钢、 、 铜 镍等兑人顶底复吹转炉
进行 脱碳 、 磷处 理 , 脱 出钢 时 向钢包 中加 入 一
包 底部 软吹 氩 处 理 , 钢 中 固态 的 A: , 将 1 类 O 夹 杂 物 变 性 为 A 一C O类 液 态 夹 杂 物 , 1 O a 以促进 钢 中 的夹 杂 物 上 浮 。 同 时 浇 铸 过 程 中 , 大包 和 中 间包 之 间 以及 中间 包 和浸 人 在
钢洁净度的评定和控制一

钢洁净度的评定和控制!一"关键词钢洁净度夹杂物尺寸分布形态#$%&’吸氮(前言市场对洁净钢的需求逐年增加)除了要求降低钢中非金属氧化物夹杂含量和控制其形态*化学成分及尺寸分布外)还要求降低钢中杂质元素!如+,*-*.*/*甚至0"和痕量元素!如+12*,3*,4*,5*06*-4及78"含量9表(为普通用钢内杂质元素对其机械性能的影响9表(钢中杂质元素对其机械性能的影响元素存在形式对机械性能的影响, #$&硫化物和氧化物夹杂延性)冲击值)各向异性可成型性!延伸率)断面收缩率和弯曲性能"深冲和冷拔性能低温韧性疲劳强度0 /固溶体沉积位移珠光体和渗碳体碳化物和氮化物析出固溶度!增加")淬透性变形老化!增加")延性和韧性!降低"位移!增加")延性和韧性!降低"沉淀)晶粒细化!增加")韧性!增加"碳化物和氮化物在晶间析出致脆裂-固溶体固溶度!增加")淬透性!增加"回火脆性析出)二次加工脆化钢材中的夹杂物可引起许多缺陷)例如)美国国家钢公司:8;<52=厂低碳铝镇静钢发生边部裂纹)经鉴定)该裂纹是由脱氧和二次氧化产物1>?&@夹杂*来自中间包覆盖剂的铝酸钙和夹带的结晶器保护渣而引起9纵向裂纹发生在带钢表面平行于轧制方向)裂纹可导致低碳铝镇静钢汽车板表面缺陷和可成型性问题)正如美国内陆钢公司A号7&B车间和国家钢公司大湖厂多项研究论文所述)钢中的铝酸盐夹杂物来自裹入结晶器的脱氧产物和复合非金属夹杂物9钢的洁净度取决于钢中非金属夹杂物的数量*形态和尺寸分布)因钢种及其用途不同而定义不同)如表?所示9表?各类钢种对钢洁净度的要求钢种夹杂物含量C D(E F A G夹杂物最大尺寸C H I J B钢汽车板和深冲钢%0’K@E)%/’KA E)#$%&’KA E%0’K(E)%/’KL E%0’K@E)%/’K@E(E EM J罐%0’K@E)%/’K@E)#$%&’K?E?E压力容器用合金钢%-’KN E合金钢棒材%.’K?)%/’K(E O?E)#$%&’K(E抗.J0钢!酸性介质油气管"%-’KL E)%,’K(E管线钢%,’K@E)%/’K@L)#$%&’K@E)%/’KL E(E E 连续退火薄板%/’K?E焊接厚板%.’K($L轴承钢#$%&’K(E(L轮胎钢芯线%.’K?)%/’KA E)#$%&’K(L(E晶粒未取向电磁钢板%/’K@E厚板%.’K?)%/’K@E OA E)#$%&’K?E单个夹杂+(@)夹杂物簇+?E E 线材%/’KP E)#$%&’K@E?E由于大型宏观夹杂对钢的机械性能危害最大)其尺寸分布非常重要9据报道)(Q R典型的低碳铝镇静钢含(E N O(E S个夹杂物!其中)仅含T E O(@E H I夹杂物A E E个)(@E O?E E H I夹杂物(E 个)?E E O?N E H I夹杂物少于(个"9显然)检测少量大型夹杂物是非常困难的9尽管大型夹杂物在数量上比小型夹杂物少得多)但其总体积分数可能较大)有时一个大型夹杂物能引起整个一炉钢的灾难性缺陷9因此)洁净钢不仅要控制钢中夹杂物平均含量)而且还要避免夹杂物尺寸超过对产品有害的临界尺寸9由此)表?中列出了许多钢材对夹杂物最大尺寸的限定值9夹杂物尺寸分布的UVWU?E E A年第(期鞍钢技术1/X1/X#Y0./&Z&X[重要性在图!中得到了进一步解释"测试结果表明#大于$%&’的夹杂物由钢包内的!()!*!%+,-降到中间包的%(./*!%+,-"因此#尽管钢包内钢水总氧含量稍高且夹杂物总量较多#中间包内的钢水还是较洁净的"图!钢包和中间包内0123$夹杂物尺寸分布非金属夹杂物来源很多#包括45!6脱氧产物"例如低碳铝镇静钢内的主要夹杂物是0123$#该夹杂物因钢中溶解氧与加入的脱氧剂5如016化学反应而产生#0123$夹杂在富氧环境下生成#形状呈树枝状#其中可能也包括一些较小的0123$颗粒碰撞聚集物"526二次氧化产物"例如钢水中残留的7018被渣中9:3氧化或暴露在大气中氧化生成0123$"5$6出钢时带入的冶金炉渣"通常为球形液态夹杂"5,6其它来源的外来夹杂物"如飞灰;剥落的耐火砖衬和陶瓷炉衬颗粒"这类夹杂物通常尺寸大且形状不规则"它们常常作为0123$非均质形核的晶核并夹带某些颗粒"5.6化学反应产物"如用<=改质处理夹杂物时#反应进行不正常时出现的产物"控制钢的洁净度贯穿炼钢工艺的各项操作#内容包括4脱氧和合金化的时间及地点;炉外精炼的程度和顺序;搅拌和倒包操作;保护浇铸装置;中间包几何形状及操作;各种冶金熔剂的吸收能力以及浇铸操作"钢的洁净度问题在各类相关文献中都是备受关注的"!>/%年?@:A A 1@B C首次全面综述了关于钢锭内夹杂物和痕量元素的控制及评价方法"最近#这一学术领域由D E ;F G 1=H H =和<I =’J提出最新论述#内容增加了热力学条件"本文介绍了钢洁净度技术的最新进展#首先回顾了钢的洁净度的评价方法#接着概述了世界许多钢厂对低碳铝镇静钢的洁净度;总氧含量K (738和吸氮的间接测量"最后叙述了钢包;中间包和连铸操作中#提高钢的洁净度的操作实践"本文收集了许多关于钢的洁净度的数据#目的是为洁净钢生产提供有用的信息#焦点是控制0123$夹杂"2钢洁净度的评价方法研究和控制钢的洁净度的关键是其精确的评价方法#在炼钢生产的各个阶段测定夹杂物的数量;尺寸分布;形状和化学成分"尽管测定技术有多种5有精确而昂贵的直接测定法#还有快速而廉价的间接测定法6#只有可靠性是相对的选择依据"2(!直接测定法钢的洁净度的一些直接测定法概述如下45!6金相显微镜观测5D D 36"这是一种传统的方法#用光学显微镜检测二维钢样薄片#并且用肉眼定量"整理整个试样复合型夹杂物检验结果时#提出问题"例如#由于较小的一簇夹杂物在整理试验结果时可被忽略"但是#用这种方法数小夹杂物太浪费时间#而大型夹杂物又太少"尽管有些方法二维结果与三维实际情况相关#问题还是很多"526图像扫描5L 06法"该法采用高速计算机计算显微镜视频扫描图像"根据灰度的断续分辨明暗区#比肉眼观测的D D 3法大有改进#很容易测定较大面积和较多数量的夹杂物"但是#有时容易将非金属夹杂物引起的划痕;麻点和凹坑弄错"5$6硫印法"这种方法通用而廉价"通过对富硫区进行腐蚀#区分宏观夹杂和裂纹"该法的问题与其他二维方法相同"5,6电解5蚀6法"这种方法精确度高但费时"较大的钢样52%%C M 2N C 6完全被酸5F <16溶解#然后收集残留的非金属夹杂物#以便计算和进一步分析"另外#为了保留非金属夹杂物9:3#将浸入9:<12或9:O 3,溶液的钢样通电溶解"这种方法适合观测单个且完整的夹杂物"5.6电子束熔炼5P Q 6法"在真空条件下#用电子束熔化钢样#夹杂物上浮到钢水表面"通常电子RS T R U 鞍钢技术V 2%%,年第!期束熔炼查找的是上浮夹杂物特定区域!目前已开发出了电子束熔炼的升级法"#$%#&’(用来评估夹杂物尺寸分布!此法靠测定几个区域的上浮夹杂物尺寸(推断所有夹杂物的上浮结果(从而计算夹杂物尺寸分布指数!")’水冷坩埚熔炼法"**’!在电子束熔炼的条件下(先将熔融钢样表面的夹杂物浓缩(再冷却后(样品被分解(夹杂物被分离出来!这种方法靠减少溶解金属的体积分离夹杂物!"+’扫描电子显微术",#-’!这种方法可清晰地观测到每种夹杂物的三维组织结构和化学成分(用电子探针分析仪"#.-/’检测化学成分!"0’脉冲鉴别分析光谱测量法"1#,%.2/’!光学发射光谱测量法是分析钢中溶解元素的传统方法!13456钢公司采用这一技术在取样789:;之内分析出总氧含量<微小夹杂物尺寸分布和化学成分!为了检测固态夹杂物(作发射火花的闪光记录!为了优化铁元素的基础发光信号和夹杂物的干扰发光信号比值(定义了电信号的特征曲线!高强度=/>?火花峰值就是脉冲鉴别分析指数!"@’曼内斯曼夹杂物检测法"-A2/,’!先使钢样波动(以排除气泡(然后超声扫描检测固态夹杂物和固<气复合夹杂物(这一方法最近被重新发现(命名为B,C.法!"78’激光衍射颗粒尺寸分析法"B2.,/’!采用这项激光技术检测其他方法"如淀泥法’检测出的夹杂物的尺寸分布!"77’常规的超声波法"*D,’!该法可以确定固态钢样内大于E8F9的夹杂物尺寸分布!"7E’锥形样品扫描法!此法用螺旋运动检测仪"如超声系统’自动扫描连铸产品的圆锥形样品表面每个位置的夹杂物!"7G’分级热分解法"H I2’!不同氧化物夹杂在不同温度还原(如氧化铝基氧化物还原温度为7J88K或7)88K(耐火材料夹杂物还原温度为7@88K(总氧含量为每个加热步骤测出的氧含量之和!"7J’激光显微探针质谱分析法"B/--,’!用脉冲激光束照射每个颗粒(选择电离临界值之上最低激光强度值作为其化学状态特征光谱图!通过与标样比较(激光显微探针质谱分析的强度峰值与每个化学元素对应!"7L’M N射线光电子光谱法"M.,’!此法采用M N射线检测尺寸大于78F9的夹杂物化学状态!"7)’俄歇电子光谱法"/#,’!采用电子束检测夹杂物化学状态!"7+’光电扫描法!分析用其他方法分离出来的夹杂物的光电扫描信号(以监测其尺寸分布!"70’库尔特计数分析法!这种方法与B A-*/法相似(可检测电蚀法分离出的夹杂物尺寸分布!"7@’液态金属洁净度分析法"B A-*/’!这种方法用传感器在线直接检测钢液中的夹杂物!由于穿过空隙进入传感器的夹杂物颗粒能改变空隙断面的电导率(检测电导率的变化便可检测夹杂物!"E8’钢水超声技术!此法吸收超声脉冲反射信号(在线检测钢中夹杂物!E O E间接方法根据成本<时间要求和取样的难度(钢铁工业通常采用检测钢中总氧<吸氮和其他的间接方法测量钢的洁净度!E O E O7定氧钢的总氧含量是溶解氧和非金属氧化物夹杂结合的氧之和!用定氧传感器很容易测定溶解氧=1?(用脱氧元素"如铝’化学反应平衡热力学控制钢中的总氧!铝和氧反应平衡条件如下P>6Q R S>6Q"=/>?E=1?G’S%)E+08T U"R’VE8O L J"7’例如P70+G W"7)88K’时(RS7O8L X78%7G(如果=/>?S8O8G YZ8O8)Y(溶解氧=1?为"8[888G YZ8O888L Y’!由于溶解氧含量不是很多(可间接地测定钢中氧化物夹杂的氧含量(以其代替总氧含量!钢中大夹杂物占少数(且定氧用钢样尺寸太小"约E8Q’(样品内几乎无大的夹杂物(既使一个样品内有一个大夹杂物(由于读数异常地高(数据很可能大打折扣!因此(总氧含量实际上代表小型氧化物夹杂中的氧含量(而不是大型氧化物夹杂含量!然而(总氧含量低会降低大型氧化物夹杂存在的可能性(如图E所示!可见(总氧含量指标仍非常重要(且通常标志着钢的洁净度!如图G所示(检测到的钢水样内的总氧含量与产品的裂纹发生率明显有关!尤其是中间包取样成分标志着处理板坯的洁净度!如日本川崎钢公司要求中间包钢水样I O=1?低于8O88G Y的条\]^\钢洁净度的评定和控制"一’件下!可保证冷轧薄板供货免检"#$##%&’#$##((&为要求检验的临界值"#$##((&以上的炉次要改判)一些钢厂生产低碳铝镇静钢各工序钢中*+,-.控制水平如表%所示/表%空格部分意味着参考文献中无合适的数据0)图1钢中总氧含量和宏观夹杂之间的关系图%中间包内总氧含量与产品裂纹指数间的关系从表%可以得出下述结论2/30随着新技术的实现!低碳铝镇静钢中*+ ,-.含量逐年降低)例如!新日铁钢中*+,-.从345#年的#+##6&’#+##(&降低到344#年的#+##1&)/1078处理的钢水*+,-./#$##3&’#$##%&0比钢包气体搅拌*+,-./#$##%(&’#$##6(&0含量低)/%0随着工序的进行!*+,-.逐步降低!依次为2钢包#$##6&9中间包#$##1(&9结晶器#$##1&及板坯内#$##3(&)1+1+1吸氮检测表%国内外先进钢铁厂生产纯净钢各工序钢中全氧量:;3#<6&钢厂精炼方法钢水包中间包结晶器板坯时间美洲内陆钢公司6号=->?@>%#16133(344#阿姆克@A B B C D E F G H厂78I#’3#(3(’6#/1(03I+4’1%+J3443 K+L钢公司?F M N A H厂=-O真空脱气3%’353443北美某厂1#’%(1#’%#3#’3(3443 *A P Q D H公司8N M M A R F H厂1#’%#3443加拿大多法斯科厂?>S78343%3%+134413446 ?*T钢公司克力夫兰厂13’15344(阿特莱斯不锈钢厂气体搅拌%I’6(%#’%J344(美国UD A M E F H炼钢车间V M N W F<781%X3#11X31344(巴西K R A P A H N R厂3%344%欧洲芬兰劳塔鲁基拉赫钢厂6J X31%1%J35344%芬兰Y F D M Z N M厂/高碳钢0气体搅拌%11%1###德国V A C C A H[D M厂3#’3(3#\3(3446荷兰霍戈文艾莫伊登厂真空脱气]^]Y3(’%1_>钢1#’%#34463446法国索拉克V‘H Q A M Q厂78<V=1#’(#3445英钢联78a3#3446奥钢联林茨厂3I3446亚洲川崎制铁千叶厂786#1#34J4川崎制铁水岛厂Y*=/b c^N-:]C1-%0a1(/3+J0a%(/3+10a6#/#+J0a((344Id Y Y!传统787835344% d Y Y!78加喷粉78喷粉5344% d Y Y!传统T-V T-V%%+J344% d Y Y!T-V加喷粉T-V喷粉1(+3344% d Y Y京滨厂3号炉a1#3443新日铁8Ne Z A P N H厂1I34J4韩国浦项钢公司781(’%3a15a3#344%34433443台湾中钢公司?>S78a%#313446中国宝钢集团公司^]L<-=78351+(5#4%(513’1(6J+J3%+J’35+(3441344(中国武钢集团公司78S?>53’5%36+51##1注2/0内数据为平均值)fghf i鞍钢技术j1##6年第3期不同炼钢容器内!尤其是钢包和中间包"#钢中含氮量不同说明倒包过程吸氮$例如#%&’()*钢厂洁净钢生产要求从钢包到中间包吸氮上限为+,++-.$脱氧后#钢中溶解的氧含量低使其迅速吸氮#因此#通过检测吸氮#可以间接粗略检测吸氧$二次氧化导致的钢的洁净度和产品质量问题如图/01所示$值得注意的是#硫是减少吸氮和氧化的表面活性元素$图1吸氮和总氧含量与钢的质量指数的关系表1总结了几个钢厂生产低碳铝镇静钢时每道工序的吸氮情况#由表/01可以得出如下结论2 !-"通过采用新技术和改进操作#吸氮逐年降低$如法国索拉克钢公司敦刻尔克厂#中间包到结晶器钢水吸氮从-344年的+,+++3.降低到-335年的+,+++-.$!5"一般而言#钢包到结晶器钢水吸氮可控制在+6+++-.7+6+++/.#通过优化倒包操作可减少浇铸期间吸入的空气#将吸入空气控制在+6+++-.以下#保护浇铸对吸氮的作用将在下文讨论$!/"多数钢厂将低碳铝镇静钢的氮含量控制在+6++/.7+6++1.#主要靠炼钢转炉或电炉操作加以控制#但也受炉外精炼和保护浇铸操作的影响$表1国内外先进钢铁厂各工序钢中吸氮情况!89:;<=-+>1."钢厂工艺89:;时间多法斯科钢公司钢包?中间包中间包?结晶器中间包?结晶器中间包?结晶器@--,4+,/+,A5-335-33A 威尔顿钢公司钢包?结晶器中间包?结晶器17-+@A-33/前-33/后阿姆克钢公司阿什兰厂中间包?结晶器5-33/内陆钢公司1号B C D钢包?中间包/-33+美钢联费尔菲尔德厂钢包?中间包1E,A-33A-33A前法国索拉克钢公司敦刻尔克厂钢包?中间包中间包?结晶器钢包?中间包中间包?结晶器+,A7-,/-/3-33A-335-33A前-344墨西哥钢公司钢包?结晶器A-33F 德国迪林根厂钢包?中间包钢包?结晶器AA-33/-33/中国宝钢钢包?中间包-7A-33A中国武钢钢包?结晶器/,473,/-33A5,5,/溶解铝减少值的检测对低碳铝镇静钢而言#钢中溶解铝的减少意味着发生了二次氧化$然而#由于铝也能被炉渣二次氧化#所以检测溶解铝的降低值比检测吸氮精度低$5,5,1炉渣成分检测分析每项操作前后炉渣成分的变化#可检测出夹杂物被炉渣吸收的情况$另外#通过观测渣中痕量元素变化和夹杂物成分#可检测出每炉钢炉渣中夹杂物$5,5,A检测浸入式水口结瘤因结瘤引起的浸入式水口寿命缩短#一般说明钢水的洁净度低$众所周知#低碳铝镇静钢内少量G H5C/夹杂就能引起水口堵塞$连铸低碳铝镇静钢结瘤物典型成分为2G H5C/A-,E.#D&11.# I*C5,/.#J’C5-,1.#K L C+,F.$!待续"潘秀兰编译!编辑许平静"收稿日期25++/>+E>-5MNOM钢洁净度的评定和控制!一"。
不锈钢中氮的作用

不锈钢中氮的作用不锈钢是一种具有耐腐蚀性能的金属材料,通常由铁、铬和镍等元素组成。
在不锈钢中,氮是一种重要的合金元素,它对不锈钢的性能有着重要的影响。
氮在不锈钢中起到了强化作用。
氮原子的大小与碳原子相似,但是它的电负性更大。
当氮原子取代部分铬原子或铁原子时,可以形成一种强化的固溶体。
这种固溶体可以提高不锈钢的强度和硬度,增加其耐磨性和耐冲击性能。
因此,氮的加入可以使不锈钢更加坚固耐用。
氮在不锈钢中还起到了抑制晶间腐蚀的作用。
晶间腐蚀是指不锈钢在高温或焊接等条件下,由于铬元素与碳元素结合形成的碳化物过多而导致的腐蚀现象。
而氮的加入可以抑制碳化物的形成,从而减少晶间腐蚀的风险。
这对于一些特殊环境下使用的不锈钢制品尤为重要,可以提高其使用寿命和安全性能。
第三,氮还可以改善不锈钢的加工性能。
不锈钢是一种难以加工的材料,但是适量的氮的加入可以使其变得更易加工。
氮的加入可以改善不锈钢的塑性和可锻性,降低其加工硬化倾向,从而使不锈钢更容易进行成型、冷加工和热处理等工艺。
氮还可以提高不锈钢的耐腐蚀性能。
不锈钢的耐腐蚀性是其最重要的性能之一,而氮的加入可以进一步提高其耐腐蚀性能。
氮原子与铬元素结合形成一种稳定的氮化铬化合物,这种氮化铬化合物可以阻止氧气和其他腐蚀介质的进入,从而提高不锈钢的耐腐蚀能力。
在工业领域中,氮的加入对不锈钢的性能有着重要的影响。
通过调整氮的含量和添加方式,可以获得不同性能要求的不锈钢材料。
例如,在高温高压环境下使用的不锈钢管道中,氮的加入可以提高其抗氧化和耐腐蚀性能,延长使用寿命。
而在制造高硬度不锈钢刀具和模具时,氮的加入可以提高其硬度和耐磨性,提高切削和模具寿命。
氮在不锈钢中具有重要的作用。
它可以强化不锈钢材料,抑制晶间腐蚀,改善加工性能,提高耐腐蚀性能。
氮的加入可以使不锈钢更加坚固耐用,并且适应不同工业领域的需求。
因此,在不锈钢材料的研发和应用中,氮的作用不可忽视。
RHLF和LFVD工艺生产管线钢洁净度的比较

・54・特殊钢第30卷晕、■缸簟壬墨冶炼流程备工位图3RH—LF(a)和LF・VD(b)流程钢中磷含量Fig.3Avergephosphorou8contentinsteelduringRH—LF(a)andLF-VD(b)process磷含量平均为0.0090%。
RH—LF精炼流程LF吊包时渣碱度平均为3.73,LF—VD过程渣碱度高,出VD时渣碱度平均为9.02,有利于控制合金中带入的磷,连铸时LF.VD工艺比RH—LF工艺磷含量平均低0.001O%,LF-VD过程磷含量控制要优于RH—LF精炼过程。
2.4夹杂物控制管线钢对钢中夹杂物控制要求较高,LF-VD流程中夹杂物在VD处理后期弱搅拌上浮去除;RH-LF工艺流程中RH循环搅拌提高了夹杂物去除的动力学条件,在Lf'流程钙处理有效地促进了夹杂物球化;LF・VD精炼工艺流程钢中夹杂物总量可以控制到2mg/10kg,RH-LF精炼工艺钢中夹杂物总量可以控制到4.5rag/10kg。
RH-LF精炼工艺夹杂物偏高,因为Ⅱ’・VD流程LF、VD能弱搅拌以促进夹杂物上浮,而RH-LF精炼工艺中,LF脱氧生成的夹杂物仅在Ⅱ.流程弱搅拌后就进人连铸工序,上浮去除的时间比LF-VD工艺少了VD处理时间。
图4(a,b)为夹杂物类型分布图,由图4(a,b)中可知,RH—LF和LF-VD工艺钢中夹杂物以钙铝酸盐或钙铝酸盐的复合物为主,RH-LF工艺有部分二氧化硅,LF—VD工艺有部分氧化铝夹杂物。
图4(C,d)为显微夹杂物尺寸分布图,由图4(C,d)中可知,RH-LF夹杂物尺寸主要为5~10岬,而LF—VD工艺显微夹杂物尺寸偏大一些主要集中在5—20岬。
图4RH—LF(a)和LF・VD(b)工艺钢中夹杂物分布;RH.LF(c)和LF-VD(d)工艺钢中夹杂物尺寸分布Fig.4DistributionofinclusionsinsteelrefinedbyRH—LF(a)andLF・VD(b)process;distributionofsizesofinclusioninsteelre-finedbyRH—LF(C)andLF—VD(d)process3结论(1)LF.VD流程控制钢中氮的效果稍优于RH-LF流程,钢中全氧含量均能控制在0.001O%内。
钢材合金元素硫磷控制

钢材合金元素硫磷控制
钢材中的硫和磷是常见的合金元素,对钢材的性能和质量有重要影响。
下面我将从多个角度来全面回答你关于钢材合金元素硫磷控制的问题。
1. 硫控制:
硫是钢材中的一种杂质元素,对钢材的性能有负面影响。
硫会降低钢材的塑性和韧性,使其易于产生冷脆性,并对焊接性能产生不利影响。
因此,控制钢材中的硫含量是非常重要的。
硫的控制方法包括:
- 选择低硫含量的原材料:在钢铁生产过程中,选择低硫含量的铁矿石和废钢等原材料,以降低硫的含量。
- 炼钢过程中的脱硫:通过在炼钢过程中添加石灰、氧化铁等脱硫剂,将硫与脱硫剂反应生成易挥发的硫化物,从而降低硫含量。
- 控制炉渣中的硫含量:合理控制炉渣中的硫含量,可以减少硫在钢水中的传递。
2. 磷控制:
磷是钢材中常见的合金元素之一,但高磷含量会对钢材的性能产生不利影响。
高磷钢材易于产生冷脆性,并且对焊接性能和塑性有负面影响。
因此,磷的控制也是非常重要的。
磷的控制方法包括:
- 选择低磷含量的原材料:在钢铁生产中选择低磷含量的铁矿石和废钢等原材料,以降低磷的含量。
- 炼钢过程中的磷去除:通过添加磷化渣或者进行磷化渣还原等方法,将磷与
炉渣分离,从而降低钢材中的磷含量。
- 精炼处理:采用精炼方法,如氧气顶吹、真空处理等,可以进一步降低钢材中的磷含量。
总结起来,钢材中的硫和磷是需要进行控制的合金元素。
通过选择低含硫、磷的原材料,采取脱硫、磷去除等措施,在钢铁生产过程中可以有效降低硫和磷的含量,提高钢材的质量和性能。
这样能够确保钢材具备良好的塑性、韧性和焊接性能,满足不同工程和应用的要求。
洁净钢冶炼及质量控制

• 脱氧与夹杂物
• 复吹
炉外精炼
• 含义:把炼钢炉炼出的成品钢或半成品钢,
在炉外设备中进行脱硫、脱氧、脱碳、去气、 去夹杂、调整化学成分和温度等处理,进一 步提高钢的质量和品质的工艺方法。 • 功能 • 手段 • 方法
连铸
• 连铸过程
• 二次氧化与保护浇注
• 中间包冶金
• 保护渣
夹杂物控制
• 非金属夹杂物:在冶炼和浇注过程中产生或混入钢中,
经加工或热处理后仍不能消除而且与钢基体无任何联系而 独立存在的氧化物、硫化物、氮化物等非金属相,统称为 非金属夹杂物,简称夹杂物。 • 非金属夹杂物是指其存在状态不受一般热处
理的显著影响的非金属化合物。
补充:夹杂物分类
• 按化学成分分类
• 按夹杂物的来源分类
钢中微量元素(Pb 、As 、Sb 、Bi 、Cu 、Sn) 的含量
也很低
纯净钢与洁净钢概念
• 洁净钢( clean steel) :指对钢中非金属夹杂物(主要是
氧化物、硫化物) 进行严格控制的钢种,要求夹杂物对钢 的性能无害。 这主要包括:钢中总氧含量低,非金属夹杂物 • 数量少 ;尺寸小
• 分布均匀;形状合适
• 钢材的断裂过程是裂纹的不断发生和发展的过程,而夹 杂物往往作为显微裂纹的起点而起重要的作用。因此,
夹杂物对金属材料与断裂过程有关的性能指标如延伸率
﹑断面收缩率等影响很大。当夹杂物的数量增加时,钢 的塑性下降。
• 夹杂物对钢的疲劳寿命有不利的影响,按降低疲劳寿命
的程度从强到弱排列:刚玉﹑球状不变性夹杂﹑半塑性
• 按夹杂物的颗粒大小分类
• 按加工时夹杂物的变形性能来分类
夹杂物控制
nb元素在钢中的作用

nb元素在钢中的作用NB元素在钢中的作用1. 引言钢是一种重要的结构材料,广泛应用于建筑、桥梁、船舶等领域。
为了提高钢的性能和使用寿命,我们经常向钢中添加合金元素。
其中,Nb元素作为一种重要合金元素,在钢中发挥着重要的作用。
2. Nb元素的特性•Nb元素具有高熔点、高热稳定性的特点;•Nb元素可以与C、N等元素形成强盐类化合物,提高钢的强度和硬度;•Nb元素能够稳定碳化物的形成,抑制晶界腐蚀和晶内腐蚀,提高钢的耐蚀性。
3. Nb元素在钢中的作用•提高钢的强度:Nb元素能够与C形成高硬度的碳化物,增强钢的强度和硬度,提高钢的耐磨性和抗拉强度。
•抑制晶界腐蚀:Nb元素能够稳定碳化物的形成,限制了晶界处的腐蚀和氢致开裂现象,提高了钢的抗腐蚀能力和耐候性。
•改善焊接性能:Nb元素能够减少钢的碳当量,改善焊接性能和可焊性,降低焊接变形和裂纹的风险。
•提高钢的高温强度:Nb元素能够形成细小的碳化物颗粒,细化晶粒,提高钢的高温强度和抗蠕变性能。
•增加钢的稀土能力:Nb元素对钢的钝化膜具有稀土能力,能够提高钢的耐蚀性和抗疲劳性能。
4. 结论以Nb元素为合金化添加剂的钢具有较高的强度、耐蚀性和耐磨性,适用于各种高强度、高耐磨、高耐蚀的工程结构。
然而,Nb元素的添加量和加工工艺条件需要合理控制,以充分发挥其作用,同时避免过量导致成本增加和钢的脆性增加。
参考文献:•Smith, W. F., & Hashemi, J. (2006). Foundations of materials science and engineering. McGraw-Hill.•Gu, J., Zambaldi, C., & Somani, M. (2018). Nb-alloying effects on the microstructure and mechanical propertiesof Ti-6Al-4V. Materials & Design, 143, .。
高洁净管道工艺流程

高纯管道技术1、公司产品简介:用途:不锈钢洁净管道用于输送半导体业中高纯或超纯洁净气体,及生物制药产业中洁净管道(各种水)。
大宗气体:CDA N2H2 O2A r∙∙∙∙∙∙必须用于管道之介质特殊气体:具腐蚀性:HCL 等等有毒气体:SiF4PF3B2F6等等生物制药:注射水,蒸馏水,去离子水∙∙∙∙∙∙气体技术要求参数包括:纯度,颗粒含量,油脂,氧化物含量,含水量∙∙∙∙∙∙3、不锈钢管道系统的表面处理方式:AP(Annealed & Pickled):即酸洗钝化,管道内表面经过酸洗钝化、清洗,不会提高表面粗糙度,但可去除表面残存的颗粒和油脂,降低能量水平,但不会减少介层数量。
(没有腐蚀性的特气&PN2/PH2)BA(Bringt Annealed):即光亮退火,在加氢或真空状态高温处理,一方面消除内部应力,另一方面在管道表面形成一层钝化膜,以改善形态结构,减少能量水平,在一定程度上提高了表面粗糙度。
(特气的排放管和一般氮气)EP(Electro—Polished):即电化抛光,通过电化学抛光,可以极大地提高表面形态及结构,使表层实际面积得到最大程度的减少。
表面是一层封闭的、厚厚的氧化铬膜,能量接近合金的正常水平,同时介质数量也会降为最少。
(腐蚀性气体用管)微电子、光电子和生物制约等行业对传输敏感或腐蚀性介质的高纯、洁净管道系统一般都采用BA、EP产品。
4、管道材质:304 304L 316 316L 321 904L(按不锈钢化学成分及杂质含量分)(业内最常见的是316L它的焊接性、耐腐蚀性、机械处理性能相对于304 304L 316来说更好些)316L(1.4404/1.4435)VOD(一次熔炼):低C:焊接性能好,硬度小低S、P:焊接性能好Cr:耐腐蚀性能好。
316L VIM+VAR(再次熔炼):低锰材料,耐腐蚀性能得到更大提高。
其他有害物质也更低。
参考管道技术资料,各种化学元素对不锈钢性能的影响。
管线钢L450MB硫、磷含量的控制

当钢 中硫 含量 低 于 0 0 2 时 , I .0 % H C明显 降低 , 甚
至可 以忽 略 。另 外 , 还影 响管 线钢 的低 温 冲击 硫
更高 的要 求 J 。衡 量 管 线 钢 产 品质 量 的 一 个 重 要指 标 就是 钢 中的硫 、 含 量 , 此 , 磷 因 降低 钢 中 的
( 唐山钢铁有 限责任公司 )
摘
要
简要分析 了硫 、 磷对管线钢性能 的影 响以及脱降硫 、 磷的工艺条件。结 合唐钢中厚板公司管线用
钢 L 5 MB冶炼 的生产实践 , 40 分析 了“ 顶底 复吹转炉 一L F精炼 一板坯连铸 ” 工艺流 程 中硫 、 磷含量 的变化规律
和控制技术 , 出转炉脱磷 和 L 指 F精炼脱硫 是冶炼 的关键技术 。 关键词 管线钢 脱硫 脱磷
虽然本次生产的脱硫效果明显, 但没有达到
最佳 效果 , 主要 表 现为 终 渣 的 氧 化 性 高 和 A 1O
含量低 , 了渣的硫容。此外 , 降低 转炉的脱硫能力
有限, 要生 产更低 硫钢 比较 困难 , 有必 要 配备铁 水
预 处理 。
3 3 钢中磷含量的控制 . 管线 钢 L5 M 40 B成 品要 求 [ ] . 1%。 P ≤0 05 L 精炼终渣 的碱度 控制在 4~ , FO+ F 7 ∑( e
好、 良好 的搅拌 条 件等 ] 。
2 2 脱磷 .
转炉造 的碱性 氧化渣具有 良好 的脱磷效果 , 而转炉出钢下渣易使 L 精炼过程钢水 回磷 。因 F
此 , 炉承 担着 脱磷 任务 。转 炉 内的脱 磷 反应 为 : 转
不锈钢管材按照洁净等级分为三级
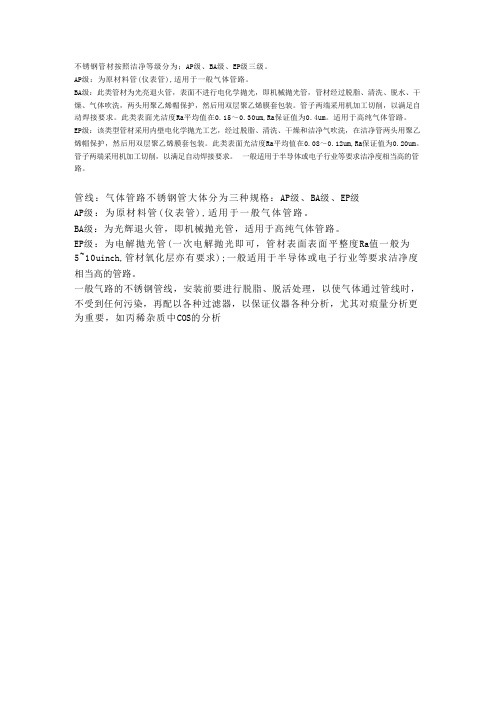
不锈钢管材按照洁净等级分为;AP级、BA级、EP级三级。
AP级:为原材料管(仪表管),适用于一般气体管路。
BA级:此类管材为光亮退火管,表面不进行电化学抛光,即机械抛光管,管材经过脱脂、清洗、脱水、干燥、气体吹洗,两头用聚乙烯帽保护,然后用双层聚乙烯膜套包装。
管子两端采用机加工切削,以满足自动焊接要求。
此类表面光洁度Ra平均值在0.15~0.30um,Ra保证值为0.4um。
适用于高纯气体管路。
EP级:该类型管材采用内壁电化学抛光工艺,经过脱脂、清洗、干燥和洁净气吹洗,在洁净管两头用聚乙烯帽保护,然后用双层聚乙烯膜套包装。
此类表面光洁度Ra平均值在0.08~0.12um,Ra保证值为0.20um。
管子两端采用机加工切削,以满足自动焊接要求。
一般适用于半导体或电子行业等要求洁净度相当高的管路。
管线:气体管路不锈钢管大体分为三种规格:AP级、BA级、EP级
AP级:为原材料管(仪表管),适用于一般气体管路。
BA级:为光辉退火管,即机械抛光管,适用于高纯气体管路。
EP级:为电解抛光管(一次电解抛光即可,管材表面表面平整度Ra值一般为
5~10uinch,管材氧化层亦有要求);一般适用于半导体或电子行业等要求洁净度相当高的管路。
一般气路的不锈钢管线,安装前要进行脱脂、脱活处理,以使气体通过管线时,不受到任何污染,再配以各种过滤器,以保证仪器各种分析,尤其对痕量分析更为重要,如丙稀杂质中COS的分析。
金属冶炼中的原料成分控制

03 原料成分的调整与优化
根据产品要求调整
目标产品纯度
根据所需金属产品的纯度要求,对原料中的 杂质含量进行严格控制,确保产品纯度达标 。
金属冶炼中的原料成 分控制
目录
• 原料成分控制的重要性 • 原料成分的检测方法 • 原料成分的调整与优化 • 原料成分控制的实际应用 • 未来展望与挑战
原料成分控制的重要性
01
保证产品质量
01
精确控制原料成分
在金属冶炼过程中,精确控制原料成分是保证产品质量 的关键。通过确保原料中各元素的含量符合标准,可以 生产出具有一致物理和化学性质的金属或合金。
环保法规的影响
1 2
环保标准提高
随着环保法规的日益严格,金属冶炼企业需要不 断改进工艺和设备,降低污染排放,满足更高的 环保标准。
废物处理成本增加
环保法规对废弃物的处理和处置提出了更高要求 ,导致金属冶炼企业需要增加相关成本投入。
3
技术创新推动
环保法规的倒逼效应促使金属冶炼企业加大技术 研发和创新投入,推动行业绿色发展。
提高金属回收率
减少废品和次品
有效的原料成分控制可以减少废品和 次品的产生,提高产品的合格率,进 一步提高了生产效率。
通过精确控制原料成分,可以提高金 属回收率,从而降低生产成本。
降低能耗和排放
减少能源消耗
精确控制原料成分可以降低冶炼 过程中的能源消耗,从而减少对 环境的负担。
降低排放
通过优化原料成分,可以降低有 害物质的排放,减轻对环境的污 染。例如,减少硫、磷等有害元 素的含量可以降低烟尘和废水的 排放。
钢中加入CR与NI的作用
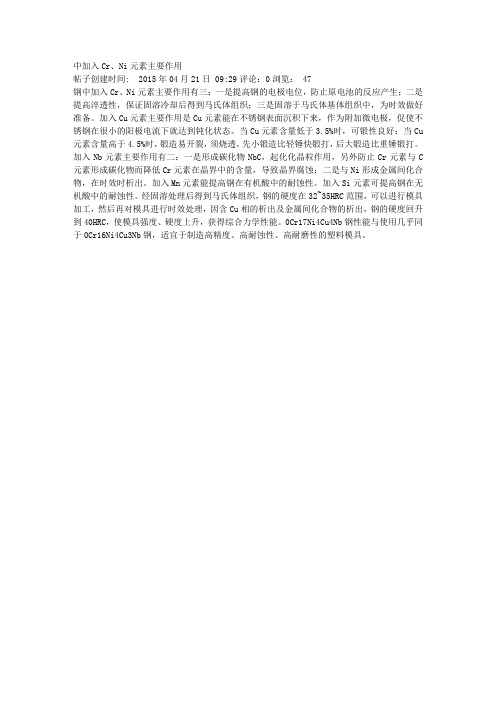
中加入Cr、Ni元素主要作用
帖子创建时间: 2015年04月21日 09:29评论:0浏览: 47
钢中加入Cr、Ni元素主要作用有三:一是提高钢的电极电位,防止原电池的反应产生;二是提高淬透性,保证固溶冷却后得到马氏体组织;三是固溶于马氏体基体组织中,为时效做好准备。
加入Cu元素主要作用是Cu元素能在不锈钢表面沉积下来,作为附加微电极,促使不锈钢在很小的阳极电流下就达到钝化状态。
当Cu元素含量低于3.5%时,可锻性良好;当Cu 元素含量高于4.5%时,锻造易开裂,须烧透,先小锻造比轻锤快锻打,后大锻造比重锤锻打。
加入Nb元素主要作用有二:一是形成碳化物NbC,起化化晶粒作用,另外防止Cr元素与C 元素形成碳化物而降低Cr元素在晶界中的含量,导致晶界腐蚀;二是与Ni形成金属间化合物,在时效时析出。
加入Mn元素能提高钢在有机酸中的耐蚀性。
加入Si元素可提高钢在无机酸中的耐蚀性。
经固溶处理后得到马氏体组织,钢的硬度在32~35HRC范围,可以进行模具加工,然后再对模具进行时效处理,因含Cu相的析出及金属间化合物的析出,钢的硬度回升到40HRC,使模具强度、硬度上升,获得综合力学性能。
0Cr17Ni4Cu4Nb钢性能与使用几乎同于0Cr16Ni4Cu3Nb钢,适宜于制造高精度、高耐蚀性、高耐磨性的塑料模具。
- 1、下载文档前请自行甄别文档内容的完整性,平台不提供额外的编辑、内容补充、找答案等附加服务。
- 2、"仅部分预览"的文档,不可在线预览部分如存在完整性等问题,可反馈申请退款(可完整预览的文档不适用该条件!)。
- 3、如文档侵犯您的权益,请联系客服反馈,我们会尽快为您处理(人工客服工作时间:9:00-18:30)。
于 ’53 6 时, 腐蚀速度基本不受影响, 当铜达到 ’5. 腐蚀速度明显加快。 6 时, # 管线钢中夹杂物的作用与控制 在大多数情况下, 钢中的 ":/ 都起源于夹杂物, 塑性夹杂物和脆性夹杂物是产生 ":/ 的主要根源。 分析表明, ":/ 端口表面有延伸的 NG1 和 OP3 K> 点 链状夹杂, 而 11/ 的形成与 ":/ 的形成密切相关。 因此, 为了提高抗 ":/ 和抗 11/ 能力, 必须尽量减少 钢中的夹杂物、 精确控制夹杂物的形态。 钙处理可以很好地控制钢中夹杂物的形态, 从
, 成品中 [ $] - &. ( &’
)*
。
其 +, 分段精炼工艺要点如下: !转炉脱磷出钢 后, 在 +, 中吹入气体, 进行强搅拌脱磷; "完全去除 脱磷渣, 防止回磷, 然后进行还原精炼; # 喷吹 /012 粉剂, 获得超低磷钢。 ! 管线钢中锰的作用与控制 由于高级管线钢要求较低的碳含量, 因此通常 靠提高锰含量来保证其强度
的增加, !"# 的敏感性显著增加。当钢中硫含量小 于 $%$$J ’ 时, 甚至可以忽略此时的 !"# 明显降低, 当 :.J 等低强度管线 !"#。日本 P% Q464R4 等认为: 钢中硫含量低于 $%$$J ’ 时, 裂纹长度比接近于零。 然而由于硫易与锰结合生成 GDF 夹杂物, 当 GDF 夹 杂变成粒状夹杂物时, 随着钢强度的增加, 单纯降低 硫含量不能防止 !"#。如 :/( 管线钢, 当硫含量降 T/ 到 J$ S &$ 时, 其裂纹长度比仍高达1$ ’ 以上。硫 还影响管线钢的低温冲击韧性。从图 J 可见, 降低 硫含量可显著提高冲击韧性
线钢中的氢含量越高, 腐蚀率 89: 产生的几率越大, 越高, 平均裂纹长度增加越显著 (图 6) 。
线性增加; 而含 G%GJ MG%G! M : 的管线钢, 当 J& K 管线钢硬度的增加趋势明显减 :/L 大于 G%7 M 时, 缓 (图 E) 。
图6 "#$%6
可扩散的氢含量与平均裂纹长度的关系 ;/23,#(- </,4//- 3=/’3$/ +’3+> 2/-$,? 3-) 3@(*-, (1 )#11*0#<2/ ?A)’($/-
表& ;4<=> & :5$ 级管线钢的化学成分 #8>6?@4= @A6BAC?)?AD AE :5$ B?B>=?D> C)>>=
# $%$/ F? $%$I GD &%I0 3 $%$$0 F $%$$1 H< $%$. GA $%J.
图J W?X%J
横向冲击韧性与硫含量的关系 T J$ Z , 9>=4)?AD <>)[>>D =4)>N4= ?6B4@) RK@)?=?)O 4) T J$ Z 4DR CK=B8KN @AD)>D)
过 ’53 6 时, 能在钢的表面形成致密保护层, ":/ 会 显著降低, 钢板的平均腐蚀率明显下降, 平均裂纹长 度几乎接近于零。 但是, 对于耐 /K3 腐蚀的管线钢, 添加铜会增加
[L] 。当钢中不添加铬时, 添加 ’5. 6 /M 会 腐蚀速度 使腐蚀速度提高 3 倍。而添加 ’5. 6 /I 以后, 铜小
表J ;4<=> J 国外炉外精炼的 ; [-] 水平 [-]?D C)>>= 4E)>N C>@ADR4NO ; N>E?D?DX ?D A]>NC>4C
钢厂 新日铁君津制铁所 室兰制铁所 日本其他厂 日本 HPP 工艺 9! ^ P"3 (碱性钢包) *LP"3 YWL9! 或 YWL*-, 9! 9! 改进的 HPL3_9G [ -] ; 7 &$ T / J0 &( &$ J$ (
T/ !( S &$ 的管线钢。日本某厂采用图 1 改进的工 艺脱硫, 喷粉 &$ 6?D 后, [ F] 由 1$ S &$ T / 降到 &$ S 脱硫效率显著提高。 &$ T / 以下,
!
管线钢中硫的作用与控制 硫是管线钢中影响钢的抗 !"# 能力和抗 FF# 能
[1, .]
"
管线钢中氧的作用与控制 钢中氧含量过高, 氧化物夹杂以及宏观夹杂增
力的主要元素
。法国 M% G% 3N>CCAKON> 等研究表 明: 当钢中硫含量大于 $%$$( ’ 时, 随着钢中硫含量
加, 严重影响管线钢的洁净度。钢中氧化物夹杂是 管线钢产生 !"# 和 FF# 的根源之一, 危害钢的各种 性能, 尤其是当夹杂物直径大于 ($ # 严重恶化 6 后, 钢的各种性能。为了防止钢中出现直径大于 ($ # 6 的氧化物夹杂, 减少氧化物夹杂数量, 一般控制钢中 氧含量小于 $%$$&( ’ 。 采用炉外精炼可获得较低的氧含量, 国外的精 炼工艺及 ; [-] 的控制水平见表 J。
图I Q,*GI 热轧钢板氢致裂纹敏感性与碳含量关系 53A1:,() R3:S33) !"# (> /(:F9(AA,)* 8:33A +A1:3 1)@ ?19R() ?():3):
[L] 和磷的偏析加剧 。当碳含量小于 HGHO K 时, 可防 ( 图 I) 。对 于 寒 冷 状 态 下 含 硫 环 境 的 止 !"#
[6, 7] 钢中氢是导致白点和发裂的主要原因 。管
量。 " 管线钢中磷的作用与控制 由于磷在管线钢中是一种易偏析元素, 在偏析 区其淬硬性约为碳的 J 倍。由 J 倍磷含量与碳当量
[J] (J& K :/L) 对管线钢硬度的影响可知 : 随着 J& K 含 G%DJ MG%JJ M : 的管线钢的硬度呈 :/L 的增加,
第7期
战东平等: 高洁净度管线钢中元素的作用与控制
・ $# ・
图! "#$%!
超低硫钢的生产工艺流程
&’()*+,#(- .’(+/00 (1 *2,’3 2(4 5 0,//2
另外, 由于耐火材料供氧, 钢水在运输和浇注过 程中应尽量减少二次氧化。通过改进中间包挡墙和 坝结构以及选择良好的中间包覆盖渣和连铸保护 渣, 可取得较好的效果。 ! 管线钢中氢的作用与控制
图E "#$%E
偏析区管线钢硬度和淬硬性的关系 ;/23,#(- </,4//- ?3’)-/00 3-) ?3’)/-3<#2#,A #- ,A.#+32 0/$’/$3,#(- N(-/
磷还会恶化焊接性能, 对于严格要求焊接性能 的管线钢, 应将磷限制在 G%G6 M 以下。磷能显著降 低钢的低温冲击韧性, 提高钢的脆性转变温度, 使钢 管发生冷脆。而且低温环境用的高级管线钢, 当磷 含量大于 G%GDE M 时, 磷的偏析也会急剧增加。 在炼钢整个过程中均可脱磷, 如铁水预处理、 转
[(]
。
管线钢中硫的控制通常是在炉外精炼时采用喷 粉、 加顶渣或使用钙处理技术完成的。采用 9!L3U T/ 法可以将钢中硫含量控制在 [ F] 新日铁 !&$ S &$ , 大分 厂 采 用 9!L"DV>@)?AD 法 喷 吹 #4-L#4WJ 粉 剂 .( 钢 中 硫 稳 定 在 ( S &$ T / 左 右。君 津 制 铁 2X 7 ) 后, 所单 独 采 用 YW 精 炼 , 钢中硫含量最低降到 万方数据
!""!#$ %&’ #(&$)(* (" !*!+!&$, -& .-/. #*!%&*-&!,, 0-0!*-&! ,$!!*
$!%& ’()*+,)* -"%&. $/(0/01 2%&. 23)4/()* 56" 7/083)
(&(9:/318:39) 6),;398,:<) %1,$)%#$ =>>3?: 1)@ ?():9(A (> 80?/ 3A3B3):8 18 #, C, 7, D, !, E) ,) +,+3A,)3 8:33A +19:,?0A19A< 3>F
’
其他 #KLH?L;?
而采用 -P3 (铁水预处理) ( 顶底复 &$ S &$ T / , LY,L-U 吹转炉) 在 *LP"3 L*LP"3L## 生产极低硫管线钢时, 中保持 #4- 7 +=J -1 "&%5, 吹入脱硫粉剂 &1 2X 7( ) #4, 可以生产出 [ F] \ /( ’ , +=J -1 \ 1$ ’ , F?-J \ ( ’ )
万方数据 和同一保护套管的反复使用可明显降低钢液的吸氢
・ "% ・
钢
铁
第 >* 卷
炉以及炉外精炼, 但最终脱磷都是采用炉外精炼来 完成。名古屋厂采用 !"#$% 脱磷将 [ $] 降到 &’ ( )* 脱磷 &’ 。鹿岛制铁所采用 +, 分段工艺进行精炼, 终了时 [ $] - &’ ( &’
)*
>3?: (> :/383 3A3B3):8 () !"# 193 @,8?0883@G 7(B3 80**38:,()8 193 B1@3 () :/3 ?/(,?3 (> B3:1AA09*,?1A +9(F ?388 1)@ ?():9(A B3:/(@ (> :/383 3A3B3):8 >(9 /,*/ ?A31)A,)388 +,+3A,)3 8:33AG 2!3 4()’, +,+3A,)3 8:33A , ?A31)A,)388 8:33A, 83?()@19< 93>,),)*, !"# 随着石油和天然气输送用管线钢需求量的不断 增加, 服役条件的日趋恶化, 对管线钢的质量要求也 越来越高。对厚壁管除要求高强度、 高韧性, 还对其 抗氢致裂纹 ( !"#) 和抗硫应力致裂纹 ( 77#) 以及良 好的野外可焊接性能提出了更高的要求。由于 !"# 是目前管线钢失效和发生事故的主要原因, 研究各 成分对 !"# 的影响就变得很重要。只有深入了解各 成分的作用及对性能的影响, 选择合理的冶炼工艺 进行精确的成分控制和夹杂物形态控制, 才会冶炼 出高洁净度的管线钢, 满足高品质、 高性能的要求。 5 管线钢中碳的作用与控制 按照 %D" 标准规定, 管线钢中的碳含量通常为 但实际生产的管线钢中的碳含量却 HGIJ KHGLJ K , 在逐渐降低, 尤其是高等级的管线钢, 如表 I 所示的 [I] 其碳含量仅为 HGHN K 。对于低温条 MJH 管线钢, 件使用的管线钢, 当钢中碳含量超过 HGHO K 时, 继 续增加碳含量将导致管线钢抗 !"# 能力下降, 使裂 纹率突然增加。当碳含量超过 HGHP K 时, 将导致锰