粉末精整液压机送料自动化生产线
630T全自动粉末冶金液压机技术改造

采 用 卸 压 阀 当压 力超 过 5 MP a ~ 7 MP a时 ,卸 压
寸 躲
珀
∞
阀卸 压
,
保 护辅 助 缸 由于超 压 而 损坏 ;二 是 采
上述三点 虽无摩擦 力的计算 和统计 数据 .但 实 践 已反 映 出摩擦 力大 于 螺 栓所 能 承 受 的 最 互 锁 ,充 液 阀不 打 开 ,辅 助 缸 不 动 作 ,
只 M1 6六角 螺栓 。其 中有 两 只被 平头 拉 断 .落
压 、耐 磨 、耐 腐蚀 和 可 在 一 3 0 ℃至 8 0 ℃ 范 围 的 油温 中工 作 的特 点 .选 用 它来 取 代 非 标 准 密封
在 圈压板 面上。其余 螺栓也 因受拉 变形。板面 多
处留下被压 凹 的痕迹 .原用 的普通牌 号铸铁 圈压
牛 皮 圈受 热 膨 胀 增 大
.
工
业
标
准
化 质
量
与
形 成 一个 液 压 密 封 腔 。 当活 塞
下端 由辅 助 缸提 升 ,充 液 阀打 开 油 缸 中 的油 进
入上 油 箱 时 ,压 机 即 回程 。这 里 要 注 意 ,一 是 0
o)
使 缸 体 与 活塞 间 的摩擦 阻 力
投 入使用后 。产 品的质量 、班 产量及 模具 的使用
寿 命 。均得 到提高 。但 使用 时间不长便 相继 出现
压 制 毛 坯 尺 寸 变 高 。压机 脱 模 无 力 ,回程 速 度 慢 。油温升 高 等现 象 。导致机 器 不能 正 常运 行 。 制造 厂家修理 和更换全 套主缸 后 .经调 试恢 复正 常 。但使用 不久 。故 障又依 I 1 9 出现 。此现象 使维
粉末成型机械压机原理

粉末成型机械压机原理粉末成型机械压机是一种常用的成型设备,其原理是利用机械压力将金属粉末或陶瓷粉末等原料在模具中通过挤压成型的工艺。
这种成型方式可以高效地将粉末原料压制成各种形状复杂、密度均匀的成品,广泛应用于汽车零部件、机械零件、粉末冶金制品等领域。
粉末成型机械压机主要由压力系统、转子系统、保压系统和控制系统组成。
压力系统是粉末成型机械压机的重要组成部分,通过电机带动液压泵将液压油送入缸体,形成液压缸的工作压力,从而产生压力作用在模具上。
液压系统的设计需要考虑到对压力的准确控制和平稳输出,以确保成型过程中成品的质量和一致性。
转子系统是粉末成型机械压机的核心部件,通常为双转子结构。
在成型过程中,原料粉末首先被加入到模具腔的一侧,随后随着转子旋转,原料粉末被逐渐挤压填充到整个模具腔中。
转子的设计和精密度对成型品质起着决定性作用,必须保证其旋转平稳、密封性好且耐磨。
保压系统在成型过程中用于维持模具内部的压力,通常采用液压缸或气动缸。
通过保压系统的作用,可以确保原料粉末充分填充模具腔且避免形成气孔或缺陷,进而保证成品的密度和强度。
控制系统是粉末成型机械压机的智能部分,用于监测和控制成型过程中的各个参数。
控制系统可以实现自动调节压力、转速、保压时间等参数,提高生产效率和产品品质的稳定性。
在粉末成型机械压机的操作过程中,操作人员需要熟悉设备的各个部件及其功能,正确操作设备并及时调整参数以确保成品质量。
定期对设备进行维护保养、清洁和润滑也是确保设备长期稳定运行的重要环节。
综上所述,粉末成型机械压机通过机械压力将原料粉末在模具中加工成各种形状的成品,广泛应用于工程领域。
压力系统、转子系统、保压系统和控制系统的协同作用是保证成型质量和生产效率的关键,操作人员的熟练操作和设备的及时维护对设备长期稳定运行也至关重要。
1。
自动化木工生产线

自动化木工生产线一、引言自动化木工生产线是一种高效、精确且可靠的生产系统,用于加工木材和制造木制品。
该生产线利用先进的机械设备和自动化控制技术,能够实现木材的切割、修整、打磨、组装等工序的自动化操作,大大提高了生产效率和产品质量。
本文将详细介绍自动化木工生产线的组成部分、工作原理、优势以及应用领域。
二、组成部分1. 木材进料系统:木材进料系统是自动化木工生产线的起始部分,用于将原材料木材输送到生产线。
该系统通常包括输送带、传送机械臂和传感器等设备,能够实现木材的自动进料和定位。
2. 切割系统:切割系统是自动化木工生产线的核心部分,用于将木材按照预定的尺寸和形状进行切割。
该系统通常采用数控切割机,能够根据预先设定的程序进行精确的切割操作。
3. 修整系统:修整系统用于对切割好的木材进行修整,使其边缘光滑且符合规格要求。
该系统通常包括修整机、砂轮和刀具等设备,能够实现木材的自动修整和修边。
4. 打磨系统:打磨系统用于对修整好的木材进行表面打磨,使其光滑度和质感更加出色。
该系统通常采用自动化打磨机,能够实现木材的自动定位和精确的打磨操作。
5. 组装系统:组装系统用于将打磨好的木材进行组装,形成最终的木制品。
该系统通常包括组装机、胶水喷涂机和夹具等设备,能够实现木材的自动组装和固定。
6. 检测系统:检测系统用于对加工好的木制品进行质量检测,确保其符合产品标准和要求。
该系统通常包括视觉检测设备、尺寸测量仪和重量检测仪等设备,能够实现木制品的自动检测和分类。
三、工作原理自动化木工生产线的工作原理如下:1. 木材进料:原材料木材通过输送带进入木材进料系统,传感器检测木材的长度和宽度,并将信息传输给控制系统。
2. 切割:控制系统根据预先设定的程序,将木材的尺寸和形状信息发送给切割系统。
数控切割机根据指令进行精确的切割操作,将木材切割成所需的板材。
3. 修整:切割好的板材通过输送带进入修整系统,修整机根据设定进行自动修整和修边操作,使木材边缘光滑且符合规格要求。
喷粉生产线介绍

喷粉生产线介绍Overview of powder spraying production line目录CONTENT 01喷粉生产线概述Overview of powder spraying production line 02喷粉生产线结构介绍Introduction of powder spraying productionline structure03喷粉生产线主要优势Main advantages of powder sprayingproduction line04喷粉生产线应用场景Application scenarios of powderpraying production linePART 01喷粉生产线概述Overview of powder spraying production line喷粉生产线采用粉末喷涂经济性好,无环境污染,效率高,一次喷涂可使涂层厚度达到50μm以上。
喷粉生产线设备主要包括粉末喷涂室、高压静电发生器、静电粉末喷枪、送粉器、粉末回收装置等。
喷粉生产线的六大组成部分主要包括:预处理设备、喷粉系统、烘箱、热源系统、电控系统、悬挂输送链。
喷涂外观美观结实,耐久实用,质量保证。
产品照片产品照片产品照片喷粉生产线总体概述001PART 02喷粉生产线结构介绍Introduction of powder spraying production line structure前处理前处理即涂装前对工件表面之氧化皮、铁锈、油脂、尘土等污垢物进行彻底清洗的工序。
烘干固化烘炉是涂装生产线中的重要设备之一,它的温度均匀性是保证涂层质量的重要指标。
喷粉设备喷粉系统包括粉房,位于粉房内的喷粉装置和粉尘回收装置,所述喷粉装置包括移动支架,喷枪,供粉系统和移动装置。
产品结构介绍热源系统烘干固化喷粉系统前处理电控系统悬挂链001行车式前处理利用电动葫芦将工件吊浸于处理槽完成工件表面的处理,结构简单投资少,适用于表面复杂生锈严重的工件不适合漂浮工件。
年产100万吨超细矿粉生产线技术方案

年产100万吨超细矿粉生产线技术方案100万吨/年矿渣微粉粉磨站工程技术方案--陕西斯达实业有限公司年产100万吨超细矿粉生产线技术方案陕西斯达实业有限公司中国?西安目录序号章节内容页码01第一章企业简介02第二章立式辊磨超细粉磨生产线工艺介绍03第三章革新工艺特点04第四章工艺流程简述05第五章项目规模及经济技术指标06第六章生产线主机设备及建筑物07第七章设备投资及功率概算07><8第八章简易经济效益分析09第九章几个建议10第十章联系方式第一章、企业简介陕西斯达实业有限公司系一家致力于钢铁、电力、冶金建材行业环保节能超细粉磨新工艺技术研发及大型装备制造企业。
1992年创始于历史文化名城西安,2003年入区西安国家民用航天产业基地重建,并被列为省市重点项目,得到了政府的重点扶植和快速发展。
二十余年来在经验丰富的技术专家和高素质管理人才的共同努力下;广开才路积累了一支老中青相结合的专业技术队伍,其中有享受国务院津贴待遇的高级专家为学术带头人,有一批八、九十年代专业院校培养的技术管理骨干,有大量的经历十余年实际工作经验的中坚力量;建立了完善的技术研究、工程设计、工程施工、物流采购、机械制造工厂、质量保障体系、项目推广等企业运行组织机构。
在大型装备开发制造领域,与中冶集团、西重院、国电集团、建材院等科研院所密切合作,应用先进的“料层粉磨”理论开发设计出大型超细矿粉装备-斯达SRM系列立式辊磨系统,产品设计标准采用钢铁、电力行业重型装备制造标准及部分国际标准,经多条生产线实际运行证明斯达立磨粉磨生产线具备工艺简化、投资低、节能、易操作、能安全长期运转、超细粉产量高、比表面积稳定等优点;并获得多项知识产权专利。
我们努力打造服务型企业团队,成立了包括工艺、土建、机械、电气、自动化等各专业技术人员组成售前售后服务队伍,以项目业主诉求为目标,承担项目前期科研、初步设计、施工设计、装备制造、安装调试、达产达标、人员培训、工程总包等一条龙服务。
自动控制液压板料剪切生产线设计

摘要在机械生产中,钢板卷材展平自动化加工,不仅大大提高了生产率,把人们从繁重的劳动中解脱出来;而且对提高产品质量,降低成本、促进产业结构的合理化起到了积极的作用。
我所做的课题是自动控制液压板料剪切生产线设计——展平机、送料机构设计。
设计方案新颖,结构简单、紧凑,能大大提高生产的效率。
文中详细的介绍了该装置的设计思路及步骤。
并将其分为4大部分:动力部分、传动部分、展平部分和送料部分。
文章主要针对这四个部分进行方案分析、方案选择、零件参数的确定及数据计算、方案验证等。
辊式展平机具有较高的生产效率,在板材校平中,应用最为广泛。
这里着重介绍了辊式展平机的结构形式、使用特点、设计计算等。
关键词:展平机、送料机构、结构设计AbstractIn machinery production, steel coil flattening automated processing, not only greatly increased the productivity of labor people from heavy freed; but also to improve product quality, reduce costs, rationalize the industrial structure has played a positive role. What I did is the subject of automatic control hydraulic plate shear production line design flattening machine, the feed mechanism design. Design of novel, simple, compact, can greatly improve production efficiency. Described in detail the design concept of the device and steps. Were divided into four parts: the feed section, transmission parts and power parts. The article focused on the four parts of the program analysis, program selection, part parameters and data calculation, the program verification. Roll flattening machine with high production efficiency, the school board level, the most widely used. This highlights the roll flattening machine structure, the use of features, design calculation.Keywords: flattening machine, feeding mechanism, structure design目录引言 (3)第1章、钢板卷材整平剪切 (4)§1.1 钢板卷材展平剪切生产线简介 (4)§1.1.1 钢板卷材整平剪切机简介 (4)§1.1.2 钢板卷材整平剪切机的工艺流程 (5)§1.2 钢板卷材整平剪切机的结构及工作原理 (5)第2章、展平机构的总体结构设计 (7)§2.1 整平机构的设计 (7)§2.2 传动系统的设计要点 (7)第3章、平行辊展平机 (8)§3.1 平行辊展平机的工作原理 (8)§3.2 平行辊展平机的参数计算 (11)§3.2.1 结构参数计算 (11)§3.3 参数计算 (16)§3.3.1 辊数的确定 (16)§3.3.2 主要参数的验算 (16)§3.3.3 板材所需的扭矩 (16)§3.3.4 校平机辊子上的压力 (17)§3.3.5 传动功率的确定 (18)§3.3.6 校正辊强度的验算 (18)第4章、电动机及减速器的选择: (19)§4.1 电动机的选择 (19)§4.1.1 电动机选择的一般原则: (19)§4.1.2 电动机选择与计算 (19)§4.2 圆弧蜗杆减速器的选择 (20)第5章、变速箱设计参数 (21)§5.1 变速箱铸造箱体的主要结构尺寸 (21)§5.2 变速箱的功能 (21)第6章、联轴器型号的选择 (22)§6.1 普通联轴器型号的选择 (22)§6.2 万向联轴器型号的选择 (22)第7章、毕业设计总结 (24)第8章、参考文献 (26)第9章、致谢 (27)引言随着国民经济健康快速发展,各种金属板带材在各个行业获得了广泛的应用。
自动化生产线整体联调

项目六 自动生产线整体联调
联机运行时,可通过触摸屏(触摸屏与传送单元的PLC连 接)发出起动控制信号,运行状态由外部的状态指示灯显示 (红:故障;黄:单机;绿:运行),也可以通过触摸屏的场 景画面显示。
YL-335B自动生产线各工作单元的PLC是通过数据模块进 行网络通信和数据交换的,系统的整体运行采用的是顺序控制 结构,即每个工件由供料开始到分拣结束,按照顺序逐步完成。 其流程为供料—加工—装配—分拣,输送单元负责整体协调, 每个工作命令均由输送单元的PLC发出指令。
项目六 自动生产线整体联调
三、 项目准备
1. 填写自动生产线的设备和器件材料清单
YL-335B自动生产线进行整体联调时, 须先对设备和器件进行清点与物理测试。填 写表6 1中的设备和器件材料的规格、型号、 数量等,并进行物理检查。表中包括电气元 器件清单、气动元器件清单、配电箱元器件 清单和西门子系统设备及元器件清单。
任务一 自动生产线(单机)调试与运行
2)加工单元电气系统功能测试
任务一 自动生产线(单机)调试与运行
3)装配单元电气系统功能测试
任务一 自动生产线(单机)调试与运行
4)分拣单元电气系统功能测试
任务一 自动生产线(单机)调试与运行
5)输送单元电气系统功能测试
任务一 自动生产线(单机)调试与运行
任务一 自动生产线(单机)调试与运行
加工后的成品工件
任务一 自动生产线(单机)调试与运行
控制方案及要求
自动生产线的控制方案是将供料单元料仓内的工件(毛坯件) 送往加工单元的物料台,加工单元对其进行冲压加工后,由输送 单元的机械手把加工好的工件送往装配单元的物料台,然后把装 配单元料仓内的白色或黑色的小圆柱零件嵌入到装配台上的工件 中,完成装配后的成品再由输送单元的机械手送往分拣单元物料 台进行分拣输出。如此完成一个周期。要求控制流程是供料—加 工—装配—分拣,加工后的工件按照不同的材质和颜色分拣后为 一个控制周期。在一个周期中,各工作单元按照顺序控制程序执 行各动作。
自动化灌装生产线操作流程

自动化灌装生产线操作流程一、概述自动化灌装生产线是一种高效、精确的生产工艺,能够实现对液体、粉末、颗粒等物料的快速灌装。
本文将详细介绍自动化灌装生产线的操作流程,包括设备准备、操作步骤、质量控制等内容。
二、设备准备1. 确保自动化灌装生产线设备完好无损,各部件安装坚固。
2. 检查液体、粉末、颗粒等物料的供应情况,确保充足并符合质量要求。
3. 准备好灌装容器、密封材料、标签等辅助材料。
三、操作步骤1. 启动自动化灌装生产线,确保各设备运行正常。
2. 将待灌装物料装入料斗或者料仓,并设置好灌装量。
3. 调整灌装机的参数,包括灌装速度、灌装量精度等,以确保灌装过程的准确性。
4. 将灌装容器放置在传送带上,并确保容器的稳定性和整齐罗列。
5. 启动传送带,容器开始进入灌装区域。
6. 灌装机根据设定的参数,自动对容器进行灌装操作,确保每一个容器的灌装量一致。
7. 灌装完成后,传送带将容器送入密封区域。
8. 根据产品要求,进行密封操作,确保产品的密封性和保质期。
9. 完成密封后,传送带将容器送入标签区域。
10. 进行标签贴附操作,确保产品的标识准确清晰。
11. 检查灌装容器的外观质量,包括容器的整洁度、标签的贴附情况等。
12. 将质量合格的产品送入包装区域,进行包装操作。
13. 完成包装后,产品进入成品区域,等待出库或者下一步工序。
四、质量控制1. 定期对自动化灌装生产线设备进行维护和保养,确保设备的稳定性和工作效率。
2. 对灌装机进行定期校准,确保灌装量的准确性。
3. 对灌装容器进行外观质量检查,包括容器的整洁度、标签的贴附情况等。
4. 抽样检测灌装产品的质量,包括灌装量、密封性等指标,确保产品符合质量要求。
5. 建立完善的质量管理体系,对生产过程进行监控和记录,及时发现和处理质量问题。
五、安全注意事项1. 操作人员需熟悉设备的操作流程和安全规定,并穿戴好相关的个人防护装备。
2. 定期对设备进行安全检查,确保设备的安全性能。
MP-1600热模锻压力机精锻齿轮自动化锻造生产线技术方案

MP-1600热模锻压力机精锻齿轮自动化锻造生产线技术方案一、生产线整体工艺方案:根据精锻齿轮生产特点,推荐MP1600热模锻压力机生产线,主要包含MP-1600热模锻压力机、自动送料装置(步进梁)、YKT-630热模锻压力机、传送带等。
用于精锻齿轮锻件的多工位自动化锻造生产,采用四工位温热精锻加冷精整的方式,热锻频率为每分钟8-10次,工艺技术方案如下:1、精密下料后的棒料成箱用叉车放入中频感应加热炉的料箱翻斗内,传送至步进式自动上料机,自动地把坯料输送到出料输送链上,进入夹辊轮进料系统,棒料以连续均匀的预定速度通过加热感应线圈加热至设定温度;通过温度分选机构,不合格棒料排除,合格棒料通过快速出料机构送入红件输送带。
2、红件输送带将棒料送入自动输送装置始端的翻转料槽,使棒料直立,便于输送装置的夹爪夹持。
3、自动输送装置(机械手)安装在MP热模锻压力机两侧,负责锻件的自动传送工作。
4、MP热模锻压力机具有四个锻造工位:镦粗、预锻、终锻、切边。
5、模具和模架安装在热模锻压力机上,通过自动喷雾装置进行润滑和冷却。
6、锻造完成后,锻件通过输送带传送至指定料框。
7、半轴齿轮:目前锻造工艺,Ø55X90,1.67kg ,压力机上工步为:镦粗—预锻—终锻—切边。
8、行星齿轮:目前锻造工艺,Ø35X64,0.48kg ,压力机上工步为:镦粗—预锻—终锻—切边。
9、锻件冷却后进行喷砂清理去除氧化皮,表面上油后在YKT-630热模锻压力机上进行冷精整达到需要锻件精度。
(下料、喷砂清理、上油设备和装置不含在以上方案中)以上工艺为理论计算,实际生产过程会稍有变化,根据生产情况可以进行完善和调整。
生产线外形布置图如下:二、MP-1600热模锻压力机和YKT-630冷挤压机:(一)压力机主要技术参数MP-1600YKT-630(二)MP热模锻压力机主要特点1、机架:采用整体式铸造机身。
机架两侧开有侧窗口,方便横向送料。
立式数控加工中心的自动化生产线设计和布局
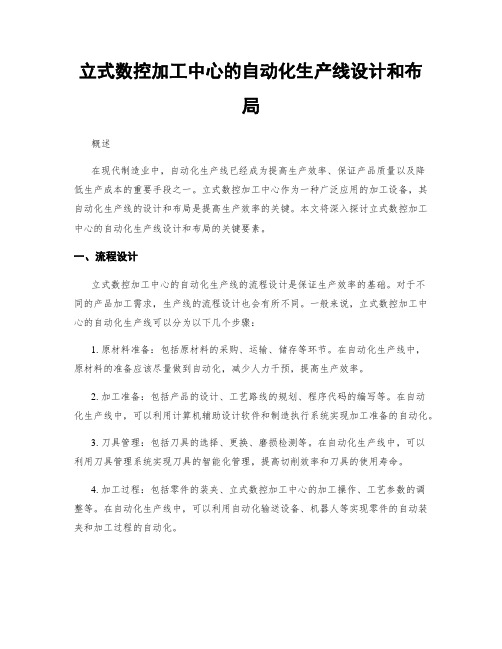
立式数控加工中心的自动化生产线设计和布局概述在现代制造业中,自动化生产线已经成为提高生产效率、保证产品质量以及降低生产成本的重要手段之一。
立式数控加工中心作为一种广泛应用的加工设备,其自动化生产线的设计和布局是提高生产效率的关键。
本文将深入探讨立式数控加工中心的自动化生产线设计和布局的关键要素。
一、流程设计立式数控加工中心的自动化生产线的流程设计是保证生产效率的基础。
对于不同的产品加工需求,生产线的流程设计也会有所不同。
一般来说,立式数控加工中心的自动化生产线可以分为以下几个步骤:1. 原材料准备:包括原材料的采购、运输、储存等环节。
在自动化生产线中,原材料的准备应该尽量做到自动化,减少人力干预,提高生产效率。
2. 加工准备:包括产品的设计、工艺路线的规划、程序代码的编写等。
在自动化生产线中,可以利用计算机辅助设计软件和制造执行系统实现加工准备的自动化。
3. 刀具管理:包括刀具的选择、更换、磨损检测等。
在自动化生产线中,可以利用刀具管理系统实现刀具的智能化管理,提高切削效率和刀具的使用寿命。
4. 加工过程:包括零件的装夹、立式数控加工中心的加工操作、工艺参数的调整等。
在自动化生产线中,可以利用自动化输送设备、机器人等实现零件的自动装夹和加工过程的自动化。
5. 检测与质量控制:包括产品的尺寸检测、表面质量检测、工序合格率统计等。
在自动化生产线中,可以利用自动检测设备、数据库管理系统等实现产品的自动检测和质量数据的实时监控。
6. 成品包装与发货:包括产品的包装、装运、发货等。
在自动化生产线中,可以利用自动包装机、物流管理系统等实现成品包装的自动化和发货的高效率。
二、设备布局设备布局是立式数控加工中心的自动化生产线设计的关键环节,它直接影响生产效率和生产质量。
合理的设备布局应考虑以下几个方面:1. 原材料进出口:原材料的进出口应尽量短,减少物料的运输时间,提高生产效率。
同时,应避免不同种类原材料的混淆,以免影响产品质量。
SMT自动化生产线方案

SMT自动化生产线方案引言概述:随着科技的不断发展,SMT(表面贴装技术)自动化生产线在电子制造行业中得到了广泛应用。
该方案通过引入自动化设备和系统,提高了生产效率和质量,降低了成本和人力投入。
本文将详细介绍SMT自动化生产线的方案,并分为五个部分进行阐述。
一、自动化设备的引入1.1 选择合适的贴片机:贴片机是SMT生产线的核心设备,可以实现高速、高精度的元件贴装。
在选择贴片机时,需要考虑生产规模、产品种类和贴装速度等因素。
1.2 引入自动上下料机:自动上下料机可以实现对元件的自动供给和回收,提高了生产效率和减少了人力投入。
1.3 引入自动检测设备:自动检测设备可以对贴片过程中的错误进行实时监测和纠正,确保产品质量。
二、生产线布局优化2.1 合理规划工作站:根据生产流程和设备的功能,合理规划工作站的布局,使得各个工作站之间的物料流动更加顺畅,减少生产过程中的等待时间。
2.2 引入自动输送系统:自动输送系统可以将物料和产品在各个工作站之间进行快速、准确的传送,提高生产效率。
2.3 设立合理的仓储区域:在生产线上设置合理的仓储区域,方便存放和管理物料,减少物料的损耗和混乱。
三、数据管理与追溯系统3.1 引入MES系统:制造执行系统(MES)可以实现对生产过程的实时监控和数据管理,包括生产计划、物料管理、质量管理等,提高生产线的可控性和透明度。
3.2 实施追溯系统:通过在生产过程中对每个产品进行标识和追溯,可以追踪产品的生产过程和质量问题,提高产品质量和售后服务。
3.3 数据分析与优化:通过对生产数据的分析,可以发现生产线中存在的问题和瓶颈,并进行优化,提高生产效率和质量。
四、人员培训与管理4.1 培训操作人员:引入自动化生产线后,需要对操作人员进行培训,使其熟悉设备的操作和维护,提高工作效率和生产线的稳定性。
4.2 设立标准操作规程:制定标准的操作规程,明确每个工作站的操作流程和质量要求,确保生产过程的一致性和产品的稳定性。
机械制造业自动化生产线应用案例

机械制造业自动化生产线应用案例自动化生产线在机械制造业中的应用已经成为一种趋势。
通过引入自动化设备和技术,企业可以提高生产效率、降低生产成本、改善产品质量,并且能够适应市场的快速变化。
本文将介绍几个机械制造业中自动化生产线的应用案例,以展示其重要性和益处。
1. CNC机床生产线CNC机床是一种广泛应用于机械制造业的自动化设备。
传统的机床需要操作工人手动操纵,而CNC机床通过计算机程序控制,实现对工件的精密加工。
一条CNC机床生产线通常包括机床、自动上下料系统、自动测量系统和自动化控制系统等组成部分。
工件通过自动上下料系统进入机床进行加工,然后通过自动测量系统进行质量检测,最后通过自动化控制系统进行排出。
这种自动化生产线大大提高了加工效率和产品质量。
2. 机械装配生产线机械装配是机械制造业的重要环节。
传统的机械装配通常需要操作工人手工进行,但是由于人为因素和繁琐的工序,容易出现错误和质量问题。
自动化装配生产线通过引入机器人和自动化设备,实现对零部件的自动化组装。
机器人可以根据预先设定的程序进行操作,精确快速地完成装配任务。
同时,自动化装配生产线还可以通过视觉系统和传感器等技术,进行质量检测和故障排除,确保产品质量和生产效率。
3. 智能仓储生产线智能仓储是现代机械制造业中的重要环节。
传统的仓储通常需要人工进行货物的储存和管理,容易造成错误和浪费。
自动化仓储生产线通过引入自动化设备和物流系统,实现对货物的自动化存储和管理。
例如,AGV(自动引导车)可以根据预先设定的路径和程序,将货物从生产线上取出并运送到指定的仓库区域进行储存。
而自动化堆垛机可以根据需求,对货物进行高效、精确的定位和堆垛。
4. 进一步发展趋势随着科技的发展,人工智能、大数据和云计算等技术在机械制造业中的应用也越来越广泛。
未来的自动化生产线将更加智能化、自动化和灵活化。
例如,自动化生产线可以通过人工智能和机器学习技术,实现对生产过程的自动监控和优化,以及对故障和问题的预警和处理。
制造业自动化生产线方案

制造业自动化生产线方案第一章概述 (2)1.1 项目背景 (2)1.2 项目目标 (2)1.3 项目范围 (3)第二章生产线规划 (3)2.1 生产线布局 (3)2.2 设备选型 (3)2.3 生产线流程设计 (4)第三章系统 (4)3.1 类型选择 (4)3.1.1 负载能力 (4)3.1.2 运动范围 (4)3.1.3 精度 (5)3.1.4 控制方式 (5)3.1.5 编程与维护 (5)3.2 编程与调试 (5)3.2.1 编程 (5)3.2.2 调试 (5)3.3 视觉系统 (5)3.3.1 图像采集 (5)3.3.2 图像处理 (5)3.3.3 目标定位 (5)3.3.4 控制 (6)3.3.5 视觉系统标定 (6)3.3.6 视觉系统维护 (6)第四章传感器与检测系统 (6)4.1 传感器选型 (6)4.2 检测系统设计 (6)4.3 数据采集与处理 (7)第五章自动化控制系统 (7)5.1 控制系统设计 (7)5.2 通信协议 (8)5.3 系统集成 (8)第六章生产线安全与防护 (9)6.1 安全防护措施 (9)6.2 防护设备选型 (9)6.3 安全监控系统 (9)第七章质量保证与检测 (10)7.1 质量控制流程 (10)7.2 检测设备选型 (11)7.3 数据分析与优化 (11)第八章生产效率优化 (12)8.1 生产线瓶颈分析 (12)8.2 生产线平衡优化 (12)8.3 效率提升策略 (12)第九章培训与技术支持 (13)9.1 员工培训计划 (13)9.2 技术支持体系 (13)9.3 持续改进与升级 (14)第十章项目实施与验收 (14)10.1 项目实施计划 (14)10.1.1 实施目标 (14)10.1.2 实施步骤 (15)10.2 项目进度管理 (15)10.2.1 进度计划 (15)10.2.2 进度控制 (15)10.3 验收标准与流程 (16)10.3.1 验收标准 (16)10.3.2 验收流程 (16)第一章概述1.1 项目背景科技的飞速发展,制造业正面临着转型升级的压力。
粉末精整液压机送料自动化生产线

粉末精整液压机送料自动化生产线粉末精整液压机送料自动化生产线粉末精整液压机送料自动化生产线【摘要】针对目前在许多粉末制品厂中以手工取送工件的操作来进行产品的精整加工存在的操作不便、精度低等问题,本文介绍了一种500吨粉末精整液压机自动送料装置,并具体阐述了该装置数控系统的控制原理。
自动送料装置的开发对发展我国粉末液压机及配套辅机研究,提升我国粉末冶金产业技术水平具有显著意义。
【关键词】粉末精整液压机送料自动化500吨粉末液压机的自动上下料装置。
本装置主要由上料输送装置、抓取装置、旋转角度检测定位装置、旋转浸油装置、多工位机械手、下料输送装置、气动系统和电气控制系统等组成。
本装置具有自动化程度高、安全、可靠的特点。
工件参数:直径Φ30mm~Φ130mm;高度≤50mm(一般30~40mm),最小高度20mm;壁厚4~20 mm;重量:70g~400g;材料为以铁基为主的金属零件。
生产节拍:自动上下料装置单次的循环时间需小于2秒,与压机配合节拍可达到10次/min。
工作时间:330天/年,3班/天。
设备主要包含:上料输送装置、抓取装置、旋转角度检测定位装置、旋转浸油装置、多工位机械手、下料输送装置、气动系统和电气控制系统等。
总布置图见下图1所示。
图1总布局1 上料输送装置此装置采用柔性输送链,对工件进行传输,主要由架体、链板、电机减速机等组成,传送链最大有效宽度为130mm(能够保证最大工件平稳、顺利的通过)。
输送方式由电机减速机带动链板沿水平运动,从而实现对工件的水平输送。
输送链两侧有导向装置,防止工件在输送过程中掉下传送带,并且此导向装置可以根据工件的大小调节角度,用于将工件逐个导向到输送链末端的定位装置处。
在传送链末端装有工件定位装置及定位发信开关,用以工件定位及定位检测,且此工件定位装置可以根据工件的大小来调整以达到工件的中心与抓取装置的气爪中心相匹配,为下一步送料机械手抓工件做准备。
输送链与机身之间设有连接支架,以提高整体刚性。
自动化生产线认识

它不仅要求线体上各种机械加工装置能自动地完 成预定的各道工序及工艺过程,使产品成为合格 的制品,而且要求在装卸工件、定位夹紧、工件 在工序间的输送、工件的分拣甚至包装等都能自 动地进行。使其按照规定的程序自动地进行工作 。——我们称这种自动工作的机械电气一体化系 统为自动生产线(简称自动线)
谢谢大家!
202042自动线安装与调试ltsylei126com2014年10月20日202042自动线安装与调试ltsylei126com雷声勇主编2014年学校重点教材立项项目机械工业出版社出版202042自动线安装与调试ltsylei126com202042自动线安装与调试ltsylei126com202042自动线安装与调试ltsylei126com1项目一yl335b自动线认识2项目二供料站安装与调试3项目三加工站安装与调试4项目四装配站安装与调试5项目五分拣站安装与调试6项目六输送站安装与调试7项目七基于ppi网络的整体安装与调试202042自动线安装与调试ltsylei126com202042自动线安装与调试ltsylei126com202042自动线安装与调试ltsylei126com202042自动线安装与调试ltsylei126comyl335b4学时2学时理论2学时实践教学目的
项目一、 YL-335B自动线认识
液体灌装机
全自动的伊利奶粉生产线
项目一、 YL-335B自动线认识
蛋糕生产线
项目一、 YL-335B自动线认识
走进富士康IPAD生产线
项目一、 YL-335B自动线认识
德国宝马自动化生产线
项目一、 YL-335B自动线认识
全新奔驰S级生产线
项目一、 YL-335B自动线认识
粉末成型机械压机

粉末成型机械压机现代工业领域中,粉末冶金技术作为一种重要的加工方法,在各个领域得到了广泛的应用。
而粉末成型机械压机则是粉末冶金技术中不可或缺的关键设备之一,其在粉末成型过程中扮演着至关重要的角色。
粉末成型机械压机可以简单地理解为通过机械压力将金属粉末等原料压制成所需形状的设备。
其工作原理主要包括给料、压制和出料三个基本步骤。
首先,将预先混合好的金属粉末放入粉末仓中,通过给料系统将粉末输送至模具腔室;接着,通过机械压力对粉末进行压制,使其在模具中形成所需形状;最后,完成压制后,打开模具取出成型件,完成整个成型过程。
粉末成型机械压机的工作过程中有几个关键要素需要注意。
首先是粉末的配比和混合均匀度,这直接影响到成型件的密度和力学性能。
因此,在生产过程中需要精确控制原料的比例,并通过混合设备确保各种原料混合均匀。
其次是压制过程中的压力控制,不同形状和尺寸的成型件需要的压力也会有所不同,因此需要根据具体情况调整机械压力保证成型件的质量。
此外,模具的设计和加工精度也对成型件的质量起着至关重要的作用,合理设计模具结构并保证模具精度对提高成型效率和产品质量具有重要意义。
粉末成型机械压机的应用领域非常广泛,例如在汽车制造、航空航天、电子通讯等行业中都有着重要的应用。
通过粉末成型技术可以制造出形状复杂、尺寸精度高的零部件,为现代工业的发展提供了重要支持。
而且与传统加工方法相比,粉末成型机械压机具有资源利用率高、生产效率高、能耗低等优点,符合现代工业对绿色制造的要求。
总的来说,粉末成型机械压机作为粉末冶金技术中一种关键设备,在现代工业生产中发挥着重要作用。
通过不断创新和优化,粉末成型技术将会在更多领域展现出其巨大潜力,为工业制造的发展带来新的机遇和挑战。
1。
全自动粉末成型机操作规程

全自动粉末成型机操作规程1. 引言本文档是针对全自动粉末成型机的操作规程,为操作人员提供简明扼要的操作指导。
全自动粉末成型机是一种高效、精确的成型设备,有效地提高了工作效率和产品质量。
正确操作全自动粉末成型机不仅可以保证生产过程的安全、稳定和高效,还有助于延长设备的使用寿命。
2. 设备概述全自动粉末成型机主要由以下几部分组成:•控制系统:负责设备的整体运行和各种参数的调节。
•运动系统:包括电机、传动轴和传动带等,负责实现各个部件的动作。
•成型模具:根据产品需求,提供不同形状和尺寸的模具。
•加料系统:将原料粉末按照一定比例加入到成型模具中。
•粉末压制系统:将原料粉末在高压下进行压制。
•成型系统:完成原料的压制和成型工艺。
•出料系统:将成品从模具中取出。
3. 操作流程3.1 开机准备在开机之前,操作人员需要进行以下准备工作:•检查设备各部分是否正常运转及各传动部位是否润滑良好。
•根据产品要求,准备好相应的成型模具和原料粉末。
•检查电源和供气系统是否正常工作。
3.2 开机操作1.打开电源开关,启动控制系统。
2.按照设备要求,正确设置各种参数,如温度、压力等。
3.检查加料系统和出料系统是否正常运作。
4.按下启动按钮,启动运动系统,设备开始运行。
3.3 粉末加料操作1.将原料粉末按照一定比例加入到加料系统中。
2.通过控制系统设置加料的速度和量程。
3.操作人员需密切观察加料过程,确保加料的均匀和准确性。
4.加料结束后,关闭加料系统。
3.4 粉末压制操作1.将已加料的模具放入成型系统中。
2.通过控制系统设置所需的压力和成型时间。
3.按下启动按钮,开始进行压制操作。
4.操作人员需密切观察压制过程,确保压制的均匀和稳定。
5.压制结束后,停止运动系统。
3.5 成品取出操作1.将完成成型的模具取出,并将模具放在专门的区域进行冷却。
2.将成品从模具中取出,检查是否满足产品质量要求。
3.将合格的产品进行记录和包装。
3.6 关机操作1.停止运动系统和控制系统的运行。