8D手法(一)
8D手法的基本特点

•★团队的工作要有领导层的支持★
书山有路勤为径, 学海无涯苦作舟
•
D2:描述问题 D2: Describe the Problem
将所遭遇的外界/内部客户问题,以量化的和客户能够明 白的术语说明问题的人,事,時,地,如何,为何,及多少 (即所謂5W2H)。
何谓5W2H:
Who-何人 :识別是哪一个客戶在抱怨
和预防的范畴; 3、确立紧急程度,必要时采取紧急应对措施以保护
客户利益。
— 除了重大的异常外,通常可以不采取紧急应对措施; — 产品紧急处理方式通常是隔离或者退回制造厂处理。
书山有路勤为径, 学海无涯苦作舟
•
D1: 建立团队
D1:Establish a Team
1、选择并记录公司内外的所有成员。团队成员由包含与问题密 切相关的技术人员或管理人员、相关的质量工程师组成 ;
☆ 主要特点之三:注重过程的监控及信息的精炼 8D格式用于监控解决问题的过程,它不是一个详尽的报告或 复杂的分析,描述工具,而是一个包含了解决问题的每个步 骤的集合,因而可从其中找到经提炼的基本信息;
☆ 主要特点之四:肯定贡献 8D程序的第“ 8D” 就是管理者要衷心肯定团队及个人的贡献, 予以祝贺。这是使8D能持续开展的保证。
书山有路勤为径, 学海无涯苦作舟
•
8D的主要特点:
☆ 主要特点之一: 团队作战 由一组人来共同对一个问题进行研究,对问题分析更全面、 更透彻,有利于找出根本原因,以彻底纠正,永不再犯;
☆ 主要特点之二:以事实为基础的问题解析技术 强调精确地陈述问题,并使用合理的思考与统计工具来详细 的描述问题。分析测验一切可能原因,找出并验证真因;
•D6:执行永久 •纠正措施
•D7:避免再发生
8D的标准书写与技巧
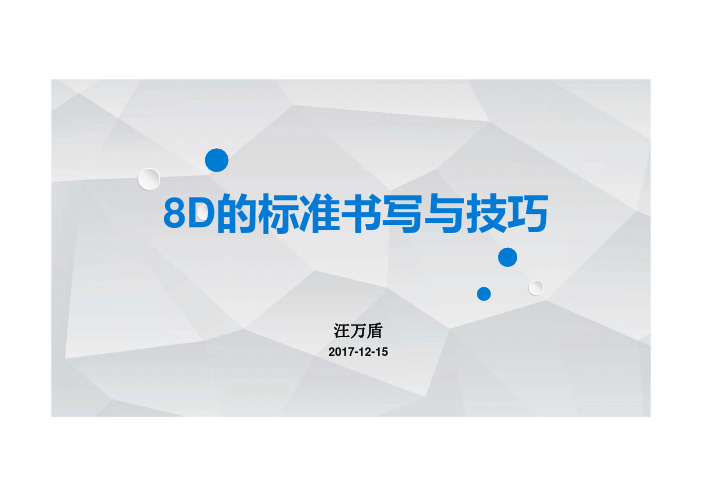
D-1 主题选定及小组成立
D1 D2 D3 D4 D5 D6 D7 D8
目标
建立一个具备产品、流程和专业知识的团队,合理地分配时间和权利去采取必 要的行动以便解决问题
成员 (好的团队成员应该):
• 可为问题提供资源和调解的管理层 • 能诊断问题的症结所在,具备工艺/产品的知识 • 能较快地接受新方法 • 具体有团队意识,而不是独行侠 • 必要时可加入客户并涉及供应商
D-4 确定并验证真因
D1 D2 D3 D4 D5 D6 D7 D8
常见问题: 片面给出表面原因,以至于后续很难执行
只有怀疑的原因,但没有有力的证据证明
• 建议查看是否包含怀疑的理由/证据的结论
经常写到根本原因不清楚,因为不利用分析工具,而只依靠经验值
• 建议列出所有可疑的故障原因
所写产生原因和本身事件没有直接联系
8D的标准书写与技巧
汪万盾
2017-12-15
课堂注意事项
请将手机调至震动状态 如有紧急电话可外出接听 培训结束欢迎交流 离开前请将桌椅归位,爱护公共设施
8D
• 8D发展史 • 8D结构 • 何时采用8D • D1-8介绍
8D 发展史
8D又称团队导向问题解决方法
8D最早是美国福特公司使用的经典质量问题分析手法。
D-2 问题描述
D1 D2 D3 D4 D5 D6 D7 D8
目标 用一种可量化的方法去确定问题的程度和它的影响,由此可以聚焦我们的视野
并且可以为发现问题起因提供必要的信息
1. 尽量以客户的语言描述问题,从客户的角度阐述问题. 2. 使用量化的术语来描述问题。如什么、地点、时间、程度、频率等。 3. 采用5W, 2H“清楚”说明问题
8D问题解决手法

8D (8 Disciplines) 问题解决8步法8D 的原名叫做 8 Disciplines,意思是8 个人人皆知解决问题的固定步骤。
原始是由Ford 公司,全球化品质管制及改善的特殊必备方法,之后已成为QS9000/ ISO TS16949、福特公司的特殊要求。
凡是做 FORD 的零件,必需采用 8D 作为品质改善的工具,目前有些企业并非 FORD 的供应商或汽车业的合作伙伴,也很喜欢用这个方便而有效的方法解决品质问题,成为一个固定而有共识的标准化问题解决步骤。
Discipline 1. 成立改善小组(Form the Team):由议题之相关人员组,通常是跨功能性的,说明团队成员间的彼此分工方式或担任的责任与角色。
Discipline 2. 描述问题(Describe the Problem):将问题尽可能量化而清楚地表达,并能解决中长期的问题而不是只有眼前的问题。
Discipline 3. 实施及确认暂时性的对策(Contain the Problem):对于解决 D2 之立即而短期行动,避免问题扩大或持续恶化,包含清库存、缩短PM时间、加派人力等。
Discipline 4. 原因分析及验证真因(Identify the Root Cause):发生 D2 问题的真正原因、说明分析方法、使用工具(品质工具)的应用。
Discipline 5. 选定及确认长期改善行动效果(Formulate and Verify Corrective Actions):拟订改善计划、列出可能解决方案、选定与执行长期对策、验证改善措施,清除 D4 发生的真正原因,通常以一个步骤一个步骤的方式说明长期改善对策,可以应用专案计划甘特图(Gantt Chart),并说明品质手法的应用。
Discipline 6. 改善问题并确认最终效果(Correct the Problem and Confirm the Effects):执行 D5 后的结果与成效验证。
《8D手法介绍》

8D手法介绍
3:实施并验证临时措施 目的:
保证在永久纠正措施实施前,将问题与内外部顾客 隔离。
关键要点: ● 评价紧急响应措施 ● 找出和选择最佳“临时抑制措施” ● 决策 ● 实施,并作好记录 ● 验证
8D手法介绍
Discipline4:确定并验证根本原因 目的:
修改现有的管理系统、操作系统、工作惯例、设计 与规程以防止这一问题与所有类似问题重复发生。 关键要点:
● 选择预防措施 ● 验证有效性 ● 决策 ● 组织、人员、设备、环境、材料、文件重新确定
8D手法介绍
Discipline8:小组祝贺 目的:
承认小组的集体努力,对小组工作进行总结并祝贺。 关键要点:
8D手法介绍
8D(8 Disciplines)方法,又称团队导向问题解决 方法,是福特公司处理问题的一种方法,亦适用于过程 能力指数低于其应有值时有关问题的解决,它提供了一 套符合逻辑的解决问题的方法,同时对于统计过程管制 与实际的质量提升架起了一座桥梁。
此手法,是一种企业过程能力偏低时的解决问题方 法,面对顾客投诉及重大不良时,提供解决问题的方法, 以及任何从暴露出来的问题中,找到疾症,正本清源, 提升管理水平。
制定一个实施永久措施的计划,确定过程控制方法 并纳入文件,以确保根本原因的消除。在生产中应用该 措施时应监督其长期效果。 方法:防错、统计控制 关键要点:
● 重新审视小组成员 ● 执行永久纠正措施,废除临时措施 ● 利用故障的可测量性确认故障已经排除 ● 控制计划、工艺文件修改
8D手法介绍
Discipline7:预防再发生 目的:
8D手法介绍
Discipline1:小组成立
8D报告填写及手法运用
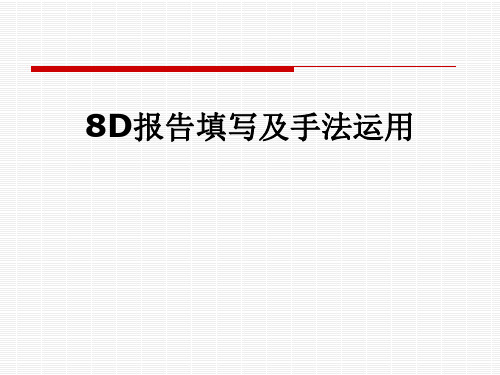
44
写及手法运用
逻辑的决策-改善之道
作出合乎逻辑的决策,不要带有偏见。 当无法用逻辑决策时,使用你的直觉。 对决策产生的效果要进行仔细的斟酌。 多向受到决策影响的人进行咨询 。 决策没有完美的,接受了再去持续改进。 考虑过问题需要的是暂时性解决,还是一劳永逸
41
写及手法运用
作出一个符合逻辑的决策
·权衡抉择,以数值形式打分 这样可以澄清的思路。 ·从列举和评估的方案中选出一些较优方
案,排除其他选择。 ·从剩下的较优方案中,选出最有可能达
到预期结果的方案。
42
写及手法运用
直觉决策法
当缺乏足够的信息时,依靠的是你的本能—— 一种“强烈的反应”即“直觉”。 直觉与严密的逻辑同样非常有效。
数
Yes
据
7. preventive action
(预防措施)
采取临时措施 解决当前异常
No 审核数据以确保纠正措施的有效
8. Congratulate the Team (成果分享)
End
4
写及手法运用
D1:工作小組
建议釆取工作小组方法来编 制8D系统。小组成员应按需要包 括设计、制造、装配、质量、可 靠性、维修、采购、测试、供应 及其他主题的专家
维修保养指引不当 环境保护不够
计算错误
➢ 典型失效机制
变形(yield)
疲劳
材料不稳定 蠕变(creep)
磨损 腐蚀
28
写及手法运用
潜在失效原因/机制
过程 ➢ 当失效模式和原因非相互独立和唯一,可能需考 虑 实验设计(DOE)以明确原因 ➢ 禁止含糊不清的词语(操作工错误,机器失误) ➢ 典型失效原因 扭矩不正确 - 过大,过小 焊接不正确 - 电流,时间,压力不正确 热处理不正确 - 时间,温度有误 测量不精确, 浇口/通风(gating/venting)不正确 润滑不当/无润滑,漏装/错装零件
8D报告过程以及D是指的什么讲解优选稿

8D报告过程以及D是指的什么讲解集团文件版本号:(M928-T898-M248-WU2669-I2896-DQ586-M1988)8D具体是指什么什么样的情况下需出8D报告一般什么样的情况下需出报告?在某一制程由于某种原因影响到下一制程的正常运做时,需要对此种不良原因进行分析,一般我们称为FA,即失效分析。
8D是FA的一种。
它可以完整的描述及分析不良发生的原因。
并且给出临时对策及长期对策。
对特异性原因导致的问题需要回复8D。
以防止此类问题再次发生。
8D最早是福特公司使用的很经典的分析手法1D: 成立团队公司明确团队队长由第一副总亲自担任;质保部负责召集和组织团队的活动;团队成员由包含与问题密切相关的技术人员或管理人员、相关的质量工程师组成。
2D:描述问题为了容易找到问题症结所在防止问题再发生,应使用合理的思考及统计工具来详细地描述问题:发生了什么问题发生地点发生时间问题的大小和广度从这几方面收集关键资料。
3D: 围堵行动为使外部或内部的客户都不受到该问题的影响,制定并执行临时性的围堵措施,直到已采取了永久性的改进。
要确保围堵行动可收到预期的效果。
4D: 找根本原因就问题的描述和收集到的资料进行比较分析,分析有何差异和改变,识别可能的原因,测验每一个原因,以找出最可能的原因,予以证实。
5D: 永久性纠正针对已确认的根本原因制订永久性的纠正措施,要确认该措施的执行不会造成其它任何不良影响。
6D: 验证措施执行永久性的纠正措施,并监视其长期效果7D:预防再发生修正必要的系统,包括方针、运作方式、程序,以避免此问题及类似问题的再次发生。
必要时,要提出针对体系本身改善的建议。
8D: 肯定贡献完成团队任务,衷心地肯定团队及个人的贡献,并加以祝贺。
由最高领导者签署8D的流程D1-第一步骤: 建立解决问题小组若问题无法独立解决,通知你认为有关的人员组成团队。
团队的成员必需有能力执行,例如调整机器或懂得改变制程条件,或能指挥作筛选等。
8D手法(一)

掌握“问题”的要领
• 1)什么是“问题”?
问题是实际与理想之间的差距 (Gap).
• 2)什么是问题的状态? 1.功能性问题 2.结构性问题
• 3)如何发现问题? 把问题视作一座冰山 ( 使用工具: 5 Why..)
Page 5 of 110
先提升制程水准 (Xbar ) 还是降低异常 (σ )?
现象
为什么机器停了? 现在
why
看到的。可感觉,可测量
问题
紧急处理
为什么机器会超载?
过去
为什么轴承润滑不足?
why真因
why
真因
一次因 (近因)
指标对策 (暂时)
改善行动
为什么润滑机器失灵?
why
真因
防呆设计
为什么润滑机器的轮 轴磨损?
why
真因 真因
n 次因
(根因) Page 18 of 110
治本对策 (永久)
客戶Release good Hold reject
Hold Yield 太高不合理
客戶要求作 工程分析
客户一直 未回复
待客户新程序
平面度不佳关联图解
QA未执行 分散抽样
返工产品 未检验
加班 精神不佳
疏忽
多数
熬夜
对规格认 识不够
打带动 作不规范
方法异常
工作不 专心
材料问题
设计不良
人员疏忽
平面效 果不佳
Page 1 of 110
8D 的本质:解决问题的8个程序
当我们观察到或 发现---------时
这种现象是否正常 ? 跟标准或目标相比较时的 差异(偏离程度)? 其差异是否不应该存在 ?
8D报告过程以及8D是指的什么讲解
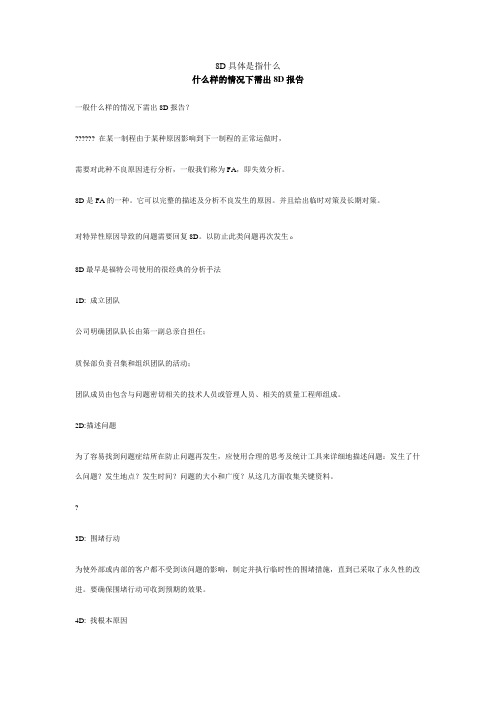
8D具体是指什么什么样的情况下需出8D报告一般什么样的情况下需出8D报告?在某一制程由于某种原因影响到下一制程的正常运做时,需要对此种不良原因进行分析,一般我们称为FA,即失效分析。
8D是FA的一种。
它可以完整的描述及分析不良发生的原因。
并且给出临时对策及长期对策。
对特异性原因导致的问题需要回复8D。
以防止此类问题再次发生。
8D最早是福特公司使用的很经典的分析手法1D: 成立团队公司明确团队队长由第一副总亲自担任;质保部负责召集和组织团队的活动;团队成员由包含与问题密切相关的技术人员或管理人员、相关的质量工程师组成。
2D:描述问题为了容易找到问题症结所在防止问题再发生,应使用合理的思考及统计工具来详细地描述问题:发生了什么问题?发生地点?发生时间?问题的大小和广度?从这几方面收集关键资料。
3D: 围堵行动为使外部或内部的客户都不受到该问题的影响,制定并执行临时性的围堵措施,直到已采取了永久性的改进。
要确保围堵行动可收到预期的效果。
4D: 找根本原因就问题的描述和收集到的资料进行比较分析,分析有何差异和改变,识别可能的原因,测验每一个原因,以找出最可能的原因,予以证实。
5D: 永久性纠正针对已确认的根本原因制订永久性的纠正措施,要确认该措施的执行不会造成其它任何不良影响。
6D: 验证措施执行永久性的纠正措施,并监视其长期效果7D:预防再发生修正必要的系统,包括方针、运作方式、程序,以避免此问题及类似问题的再次发生。
必要时,要提出针对体系本身改善的建议。
8D: 肯定贡献完成团队任务,衷心地肯定团队及个人的贡献,并加以祝贺。
由最高领导者签署8D的流程D1-第一步骤: 建立解决问题小组若问题无法独立解决,通知你认为有关的人员组成团队。
团队的成员必需有能力执行,例如调整机器或懂得改变制程条件,或能指挥作筛选等。
D2-第二步骤: 描述问题向团队说明何时、何地、发生了什么事、严重程度、目前状态、如何紧急处理、以及展示照片和收集到的证物。
8D分析方法

8D分析方法
do
something
8D的由来
8D(8 Disciplines)即问题解决8步法,最早是福特公司使用的经典质量问题分析手法,对于解决工厂中存在的问题是一个很有用的工具,尤其在面对重大不良时,它能建立一个体系,让整个团队共享信息,并引导团队提供解决问题的方法。
工作中有过这样的感触
8D方法由8个步骤和1个准备步骤组成,客观地确定、定义和解决问题并防止相似问题的再次发生。
8D方法应用流程
D1组建问题解决团队
8D原名就是叫团队导向问题解决步骤,8D小组需要由具备产品及制程知识,能支配时间且拥有职权及技能的人士组成,必须指定一名8D团队组长。
不具备以上条件的8D是失败的8D,它没法在你需要资源解决问题时提供帮助。若一个体系出现了质量异常,绝非单一部门职能失效,否则整个体系需要重新进行完善。
十二项工作原则之解决问题4步骤
1. 解决问题2. 修改相关程序文件3. 相关人员培训4. 相关问题追溯
D8 8D过程总结
恭贺小组的每一成员,问题解决完成,对小组成员的努力予以肯定。8D项目正式关闭文件定案和存档
记录过程中学到的教训
提交8D问题分析报告表达对成员的感谢
感谢阅读
感谢阅读
D2描述问题
以客户的角度和观点详细描述其所感受到的问题现象,将所遭遇的问题,以量化的方式,明确出所涉及的人、事、时、地、为何、如何、多少。
如何进行问题描述?
要找到问题的根源而不是表现症状的简单描述;要定义问题的边界(不要将问题范围扩大到不可控的范围之外
5W2H方法
Who~谁发现的问题?When~什么时间发现的问题?Where~在何处发现的问题?What~有什么问题发生?Why~为何问题此时发生?How~问题如何发生?How many~问题发生的程度(多大?范围?比例?)
8D方法

Problem solving process (8-D method)问题解决过程 (8-D方法)“8D”是一种通过8个步骤解决问题的方法。
“8D” 是通过以下三个途径解决问题并防止问题(投诉)的重复发生:●快速地,持久地,系统地处理内外部的投诉,分析定位并消除根本原因。
●把经验教训应用到相似的过程及产品上。
●制定并不断完善解决问题过程的文档。
D1: Problem solving team问题解决小组:成立的解决小组成员需要对产品和过程比较熟悉并且有经验,且至少包含技术,质量和生产部门。
D2: Problem description 问题描述:问题描述是指详细的描述出不良现象、问题零件以及出现什么样的影响。
描述必须清楚易懂,如果有必要,可以提供一些样品(例如不良零件,图片,图纸等)进一步说明不良现象,以便于简单化分析。
D3:Containment actions围堵措施:一旦发现不良,即时遏制措施必须实行,以保护客户的不接收,不使用或不生产不合格产品。
因此,遏制行动,仅仅是一种保护措施,往往与问题的原因是没有关系的。
例如:挑选,返工,报废,等围堵措施都是与问题的原因没有关系。
D4:Root cause analysis根本原因分析●根本原因分析应确定:为什么发生了不合格和为什么不合格产品没有被探测到●必须对受影响的产品及其加工过程进行调查和因果关系分析(哪一个组件/产品导致不良,哪一个过程导致不良)●所有导致不良的可能情况必须都要被考虑●必须由适当的方法和工具来支持这种分析(如QC七大手法, FMEA ,鱼骨图, 5why)●评估与问题相关的潜在风险(不良品所影响的时间和数量)。
●D5:Corrective actions and proof of effectiveness改善措施和验证有效性:●根据D4定义可能的改善措施来消除根本的不良。
●所有能解决和最终消除问题的方法必须可实施的,可评估的。
品质七大手法及8D报告(一)
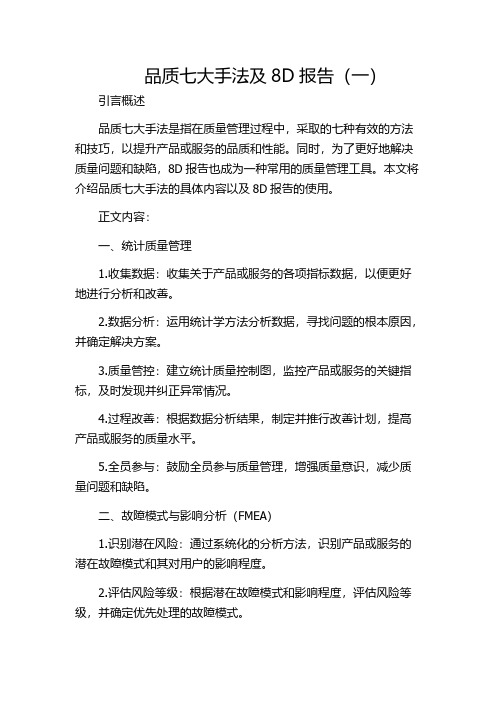
品质七大手法及8D报告(一)引言概述品质七大手法是指在质量管理过程中,采取的七种有效的方法和技巧,以提升产品或服务的品质和性能。
同时,为了更好地解决质量问题和缺陷,8D报告也成为一种常用的质量管理工具。
本文将介绍品质七大手法的具体内容以及8D报告的使用。
正文内容:一、统计质量管理1.收集数据:收集关于产品或服务的各项指标数据,以便更好地进行分析和改善。
2.数据分析:运用统计学方法分析数据,寻找问题的根本原因,并确定解决方案。
3.质量管控:建立统计质量控制图,监控产品或服务的关键指标,及时发现并纠正异常情况。
4.过程改善:根据数据分析结果,制定并推行改善计划,提高产品或服务的质量水平。
5.全员参与:鼓励全员参与质量管理,增强质量意识,减少质量问题和缺陷。
二、故障模式与影响分析(FMEA)1.识别潜在风险:通过系统化的分析方法,识别产品或服务的潜在故障模式和其对用户的影响程度。
2.评估风险等级:根据潜在故障模式和影响程度,评估风险等级,并确定优先处理的故障模式。
3.制定预防措施:在风险等级高的故障模式上,制定相应的预防措施,减少潜在风险的发生。
4.纠正措施:对已发生的故障模式,制定纠正措施,确保问题不再发生,并进行持续改进。
5.验证效果:对预防和纠正措施进行验证,确保其有效性和实施情况。
三、质量成本管理1.成本分析:对质量过程中产生的各项成本进行深入分析,包括预防成本、评价成本、内部失败成本和外部失败成本。
2.成本控制:通过制定合理的质量控制措施,减少质量问题和缺陷的发生,降低质量成本。
3.经济批量选择:在制定生产计划时,综合考虑成本和质量要求,选择适当的经济批量。
4.质量成本效益分析:对质量改进措施的成本与效益进行评估和分析,以便决策者做出合理的决策。
5.全员节约:倡导全员以经济节约的思想,降低质量成本,提高公司整体竞争力。
四、质量标准化管理1.制定标准:在产品或服务的设计阶段,制定相应的质量标准,以指导后续的生产和服务过程。
8D培训讲义

四、8D 精神
为什么要成立8D小组 “D1 成立8D小组” 为8D过程的真正开始。 成立8D小组是8D过程的基本部分。极少有一个人具有所有需要的资源、资料和技能来解决一个复杂的问题。另一方面,一组合适的人员能够包括所有必须的资源和聚集每一个人所具有的技能。
D3:临时措施
立即对线上品、库存品、在途品及发运给客户的产品采取紧急处理对策。 说明目前如何控制该项不合格,同时防止上述不良品再度流出。 由成本、交期及引发其他不合格可能性来评估紧急对策的有效性。 应明确执行临时措施的责任者。 临时措施是否会引起其它问题。
什么是根本原因 不同类型的原因。 #可能原因:在因果图上被确定的描述一种结果可能发生的任何原因 #最有可能原因:以可得到的数据为基础,最能描述问题的原因 #根本原因:验证过的产生问题的真正原因 D4过程能够帮助慢慢减小调查范围
D2: 问题描述
要想成为一个有效的问题解决者,必须在采取行动前知道尽可能多的关于问题的描述。在D2阶段的任何不清楚和不准确都会导致小组得到错误的原因和采取错误的纠正行动。 采用标准的语言,从客户观点来描述问题 描述尽量具体,事实清楚,证据充分,能 量化以量化表示. 所报告的应是真实、客观的问题 采取5W2H描述
8D培训讲义
内 容 一、什么是8D 二、8D有什么作用 三、何时采用8D 四、8D 精神是什么 五、怎么做8D
一、什么是8D?
8D:所谓8D方法(eight disciplines),又称团队导向问题解决对策TOPS(Team Oriented Problem Solving) ,是福特公司处理问题的一种方法,共分8个步骤。
不要忘记总结团队作战的经验 完成小组任务,衷心地肯定小组和个人的集体努力和贡献,并加以祝贺。由最高领导者签署。
8D手法

第十一章 8D手法第一节.8D手法概述1.1.8D(8 Discipline in Problem Solving)的改善方法強調利用團隊合作,來達成 問題分析與改善的目的. 英文稱為 Team Oriented Problem Solving (TOPS);1.2.8D是福特汽車所發展出來的方法: 透過團隊合作,用以分析與改善製程能 力(capability)和客戶抱怨,進而提昇製程能力及顧客滿意.第二节 : 8D手法的特点2.1.提供一套井然有序的團隊合作方法,注重事實證據與數據解析,減少因人而異的處理方式,達成問題的分析與改善.2.2.為了找尋及建立長治久安的作業方法, 我們需要來自各方面的意見與建議.2.3.應用於任何問題或改善活動: 在共同目標下,達成部門間之有效溝通,減少各單位之本位主義的籓籬.2.4.所有相關的分析報告,均需文件化.2.5.每一個問題的原由與改善的 方法, 將之文件化是必要的.然而解決與改善的步驟可能會依個 別問題的困難或複雜程度而採取不同的步驟與次序.2.6.一個問題發生之後,製造部立即採取暫時的應付措施避免問題惡化.但是徹底的改善與避免再 發生的長遠對策, 仍需要配合組織相關部門人員,透過團隊合作,解決問題的根源.要點﹕1:組隊;團隊合作 2:問題描述 3:暫時的保固措施 4:真因的找尋及驗證 5.驗證改善方案 6:實行徹底的改善行動 7:預防再發生;標準化 8:慶賀您的團隊成功第三节 8D手法中8大步骤讲解3.1.組隊; 團隊合作; Use Team Approach召集擁有製程或產品相關技術人員組成 一個團隊小組, 付與改善的權力, 並給與小組成员足夠的時間及資源, 來解決問題和執 行改善措施.這個團隊小組必需指定一人擔任小組長.3.2.問題描述 ; Describe the Problem指出內部或外在顧客的問題所在.使用5W2H讓清楚描述問題:WHO: 顧客是誰WHAT: 產品是什麼WHEN: 何時製造生產的WHERE: 問題發生在那裏WHY: 為何發生問題 (人, 機器, 材料, 維修保養,或量測工具與方法)HOW: 問題是如何產生(未遵守TCM規定,或未規定完整)HOW MANY: 有多少數量的產品被影響品质理念﹕持续改进,企业发展的永动机 第 133 页,共164页3.2.3. 暫時的保固措施;Implement and Verify Containment Actions找尋並且實行暫時的保固措施來隔離問 題對任 何內部或外部顧客的影響, 直到改善措施實行為止.確定保固措施能有效的控制問題, 使之不再影響顧客滿意.3.4.真因的找尋及驗證;Define and Verify Root Causes驗證所有可能造成該問題的因素.藉由實驗研究每一個可能的因子, 尋找及確認問題 的真因.再尋求各種改善方案, 來去除真因.3.5.驗證改善方案; Verify Corrective Actions經由試產/試作確認所選擇的改善方案能有效的徹底解決顧客的問題. 並且不會有其它不可預期的負作用.(必要的時, 可以風險評估方式為之)3.6.實行徹底的改善行動; Implement Permanent Corrective Actions決定及實行最有效的的各個改善行動. 選擇控制因子,以確定真因 已被排除. 當大量生產時,觀察長期效應. 必要時, 可以再施行一些補強措施.3.7.預防再發生;標準化 Prevent Recurrence修定管理/管制系統 , 作業系統, 將它們徹底實行並且標準化 ,來預防相同或類似問題的再發生.3.8.慶賀您的團隊成功; Congratulate your team讚揚的整個團隊的各項努力與成功.注: 這些步驟並沒有一定的先後次序,它們是可以隨著問題的不同而作調整的. 例如問題剛被發現和組隊,而暫時的保固措施已被生產線上的領班和作業人員所實行.附:8D手法执行流程图品质理念﹕一丝之差, 优劣分家 第 134 页,共164页第四节 8D手法运作4.1.並不是要求每一件发生的问题都必须采取8D方法,而是针对重复发生的,一直没有解决的比 较重大的问題,针对客戶要求回覆的客訴抱怨.4.2.执行和验证临时措施:根据问题的性质,确定并执行相应的临时措施,以控制外界/內部客戶问題发生的效应不致扩 大,直到永久措施執行.验证所采取临时措施的效果。
8D问题改善手法
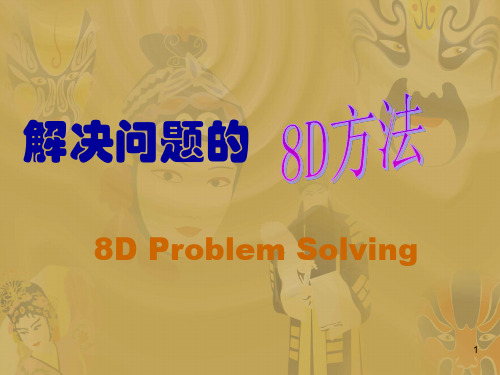
针对选定的纠正措施
修正衡量指标以及 对现行的质量控制 模式进行工程变更
利用三十天的数据 (如SPC或推移图)
来进行确认
建立纠正措施 执行计划
审核改版的 设计FMEA
识别设计或生产过程 中的主要、安全、
关键特性
经过推移图和初次的 测量来停止临时措施
审核改版的 过程FMEA
开发或修正控制计划 以及过程窗体以监控
为一根本原因
列出所有可能的原因 收集适当的资料信息
根据资料显示 确定根本原因
智联培训30
root cause
root cause就是只要解决它就可以解
决失效模式。
使用方法:Why, Why, Why, Why, Why 丰田员工提出“5个为什么”。要找 出问题的根本原因,必须至少依次提 出5个“为什么?”这就象一层层剥洋 葱一样。
造成ALT-5检测器包装工作进度延误,
要求派人处理。
智联培训48
1.成立小组
按问题涉及范围确定小组成员: 责属单位: 生管课、销售课、库管课、品保课 责属人员: 王文新、李小朋、庄子清、张春明
智联培训49
2.描述问题
何时:1999年11月4日; 何人:浙江精密机械厂; 何地:浙江精密机械厂—包装车间; 何事:包装ALT-5检测器时,使用20μMHT
智联培训20
D2:描述问题
目的:
用量化的术语详细说明与该问题有 关的内/外部顾客问题,确认该问题 的人、事、时、地、为何、如何及 多少(5W2H)和程度、频率等。
“什么东西出了什么问题”
方法:
质量风险评定,FMEA分析
智联培训21
关键要点:
收集和组织所有有关数据以说明问题 问题说明是所描述问题的特别有用的数据 的总结 审核现有数据,识别问题、确定范围 细分问题,将复杂问题细分为单个问题 问题定义,找到和顾客所确认问题一致的 说明,“什么东西出了什么问题”,而原 因又未知 风险等级
- 1、下载文档前请自行甄别文档内容的完整性,平台不提供额外的编辑、内容补充、找答案等附加服务。
- 2、"仅部分预览"的文档,不可在线预览部分如存在完整性等问题,可反馈申请退款(可完整预览的文档不适用该条件!)。
- 3、如文档侵犯您的权益,请联系客服反馈,我们会尽快为您处理(人工客服工作时间:9:00-18:30)。
A P C D
(-)
列出问题点
Page 29 of 110
PDCA 与CA-PDCA实施步骤
PDCA
活动计划的制定 2. 课题明确化 3. 拟定对策 4. 最恰当对策的检讨 5. 最恰当对策的实施 6. 效果确认 7. 效果维持 8. 检讨及计划
Page 30 of 110
1.选定主题 使用 何种 QC STORY 的判定
方法异常 平面效 果不佳
材料问题
人员疏忽
检查不够
工作不 专心
岗前培 训不足 模具异常
设备问题
设计不良 产品定 位不良 机台操作 不熟悉
磨损
PDCA 的介紹
什么是管理?
ACTION PLAN计划 改善行动
CHECK
检讨
DO执行
QUALITY CONSCIOUSNESS品质意识 .The PDCA cycle is a series of activities pursued for improvement PDCA循环为一系列持续改善的活动
Page 34 of 110
不良率的 p-Chart 趋势图
0.250 0.200
0.150 UCL=0.1253 0.100 Avg=0.0704 0.050 LCL=0.0155 0.000 Lot
Sigma Rule
99-100%
90-98%
60-75%
μ-3σ
μ-2σ
μ-σ
μ
μ+σ
μ+2σ
Page 39 of 110
D0: Symptom(s)
• Symptom(s) 征兆 • 將客戶端所发生抱怨的征兆加以定性及定 量化 • 针对此征兆决定是否使用 8D 及8D应该处 理及应用的范畴 • 用以确认 征兆 的工具图表 – Trend Charts(趋势图)/ Pareto(柏拉图)
把问题看成一座冰山
現象
看到的,可感觉,可测量
现在
why
why
问题 一次因 (近因)
why
紧急处理
真因
过去
why
真因
治标对 策 (暂 时)
真因
真因
why
真因
n 次因 (遠因根源)
治本对策 (永久)
5 Why 1H 工具
• • • • • • 丰田生产方式: “反复提出五次为什么” 垂直式思考,针对问题一层一层的深入 通常第一个答案不会是真正的答案 5 Why 可以找出真正的原因 找原因用5Why+想方法用1How 简单的案子可能4W,3W或2W即找出问题, 原因 ,但复杂的问题或许要5 Why, 6 Why, 7 Why…Î最后要加 1H(How to fix it).
Page 23 of 110
PDCA 循环论
7.效果维持
1.选定主题 2.课题明确化与设定目标
A P 管理人員 管理人員
6.效果确认
3.拟定对策 4.最终对策
C D 检验人员 作业人员
5.最终对策的实施
8.检讨及今后的计划
Page 24 of 110
C-A-P-D-C-A
• • • • 检讨现状-再对策-计划-实行-检查-改善 是问题解决型QC改善过程 注重于已发生问题的处理 PDCA循环注重与做Do, 所以Do的內部还有 小型的PDCA循环,指导问题改善为止 • 是小规模的改进,不是大刀阔斧的改革
μ+3σ
异常的定义
0.27%/2= 0.135%
99.73%
0.27%/2= 0.135%
6σ
Excursions 对整体良率的影响
未去除 Excursions 的良率% 移除 Excursions的 良率%
相差多少 ppm 68
LQFP 14x20
99.8903
99.8971
QFP 28x28
异常很小,但却不准确
Page 7 of 110
准确,但变异很大
Page 8 of 110
Cpk=0.816
Cpk=0.852
0
10 20 30 40 50 60
-6
4 14 24 34 44 54 64 74
Cpk=1.694
Cpk=0.852
-5
5
15 25 35 45 55 65
-6
4 14 24 34 44 54 64 74
掌握“问题”的要领
• 1)什么是“问题”? 问题是实际与理想之间的差距 (Gap). • 2)什么是问题的状态? 1.功能性问题 2.结构性问题 • 3)如何发现问题? 把问题视作一座冰山 ( 使用工具: 5 Why..)
Page 5 of 110
先提升制程水准 (Xbar ) 还是降低异常 (σ )?
99.8363
99.8393
Page 38 of 110
30
如何管理异常不良率
• 有效管理异常可以 – 將干扰降低 – 提升 Xbar 水准水準 (幫助不大, 因为属于少数) • 暫時管制措施是重要的 – 第一件事就是将產品 “Hold” – 再來才是解決問題, 預防問題的再发生 • 异常管理 – 三现: 现时、现地、现物 – 以Problem 7 Steps 来解决及预防问题 – SDCA
n 次因 (根因)
治本对策 (永久)
5 Why & 关联图
PC/MFG满载 排不上先测试 工程师未 被通知 工程师不知 有Hold Lot 工程师太忙 没时间处理 工程师请 假或外出 L/B,P/C,Tester Hander 问题 系统通知到 别的工程师 产品待 重测
ON HOLD LOT 太多
8D:8 DISCIPLINES
• 8D: 8 Discplines of Problem Solving 解决问题的8个步骤 • 8D是解决问题的一种工具,通常是客户所 抱怨的问题要求公司分析,并提出永久解 决及改善的方法 • 比普通的改善行动报告 (Corrective Action Report) 更加严谨,要求改善的更加完善
5 Why 范例:为何停机
• 问1:为什么停机了? • 问2:为什么用电超载? • 问3:为什么轴承的润 滑不足 • 问4:为什么润滑器失 灵? • 问5:为什么润滑器的 轮轴磨损了? • 答1:因为用电超载, 保险丝烧断了 • 答2:因为轴承的润滑 不足 • 答3: 因为润滑机器失 灵 • 答4: 因为润滑器的轮 轴磨损了 • 答5: 因为杂质跑到里 面去了
目標=100元
-20元 -10元
102 90 101
第一周
第二周
第三周
第四周
Page 33 of 110
两种不同类型的良率损失
• 异常良率损失 Excursions: 良率损失的独立 跳升,由突然且严重的良率损失引起,影 响范围导致特别低良率的有限批数 • 水准不足良率损失Chronics: 良率水准不 足。发生众多批数,其良率相对低于水准 内的良率。
例如: 人員出勤率93%
问
题
分析原因 WHY
原
因
确定改善目标并 形成解决方案
人员出勤率的目标为95%, 低了2个百分比,而此差异 幅度根据以往资料判断差异 大,为异常状况。 请假人数太多
如何改善异常 ? 如何控制发生异 常的原因 ?
对
策
处理:问题发生时立即采取 公布人员出勤状况采取的措施 治标:解决问题的手段 强化请假管制 治本:避免问题再发生 加强员工向心力的方法
Page 12 of 110
5 Why 范例: 为何停机
• 问1:为什么停机了? • 答1:因为用电超载, 保险丝烧断了
5 Why 范例: 为什么停机
• 问1:为什么停机了? • 问2:为什么用电超载? • 答2: 因为轴承的润滑 不足 • 答1:因为用电超载, 保险丝烧断了
5 Why 范例: 为什么停机
D0 D1 D2 D3 D4 D5 D6 D7 D8
征兆/紧急反应措施 成立改善小組 问题描述 暂时对策及对策对策实施确认 原因分析及确认 永久改善行动效果确认 永久改善行动对策的实施及实施验证 避免再发生/系统性的预防行动 完成 % Effective有效率 % Contribution比率 % Effective有效率 Validation确认 % Effective有效率
Page 22 of 110
P-D-C-A
• 计划Plan-实行Do-检讨Check-行动Action • 是项目达成的改善过程 • 是一种对新的作业标准不断挑战、修正, 并以更新的标准替代的过程 • 运用PDCA改善前,应以SDCA来做标准化 • 四个步骤是一体的,连续的.由相同的人或 单位所负责,否则常会导致无法衔接 • 改善行动要求有“有效性”验证
Page 25 of 110
CA-PDCA 循环论
3.原因分析 7.效果维持
2.现状的把握
A Action C Check
P Plan D A P C D
8.反省及今后计划
1.选定主题 6.效果确认
4.拟定对策
5.对策实施
Page 26 of 110
S-D-C-A
• 标准化Standardization-实行-检查-行动 • 所有制程在开始运作时都会不稳定, 在这个 阶段, 稳定制程使产量固定是很重要的 • 待标准建立并且制程稳定了, 则用PDCA来 改变制程提升水准.但是一旦制程一改变, 又 会马上变得不稳定, 需要以SDCA加以稳定 化
5 Why 的分布层次
现象
为什么机器停了?
现在 看到的。可感觉,可测量
why
问题
why
紧急处理
为什么机器会超载? 为什么轴承润滑不足? 为什么润滑机器失灵?
过去
真因