塑胶模具设计(初级)1
塑料模具设计步骤
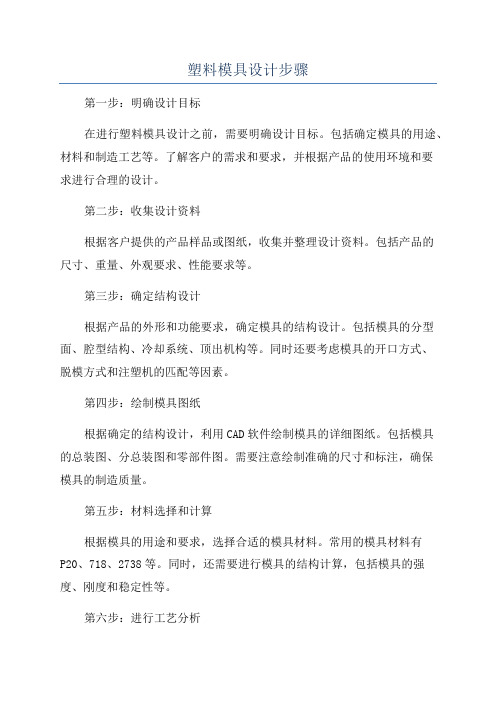
塑料模具设计步骤第一步:明确设计目标在进行塑料模具设计之前,需要明确设计目标。
包括确定模具的用途、材料和制造工艺等。
了解客户的需求和要求,并根据产品的使用环境和要求进行合理的设计。
第二步:收集设计资料根据客户提供的产品样品或图纸,收集并整理设计资料。
包括产品的尺寸、重量、外观要求、性能要求等。
第三步:确定结构设计根据产品的外形和功能要求,确定模具的结构设计。
包括模具的分型面、腔型结构、冷却系统、顶出机构等。
同时还要考虑模具的开口方式、脱模方式和注塑机的匹配等因素。
第四步:绘制模具图纸根据确定的结构设计,利用CAD软件绘制模具的详细图纸。
包括模具的总装图、分总装图和零部件图。
需要注意绘制准确的尺寸和标注,确保模具的制造质量。
第五步:材料选择和计算根据模具的用途和要求,选择合适的模具材料。
常用的模具材料有P20、718、2738等。
同时,还需要进行模具的结构计算,包括模具的强度、刚度和稳定性等。
第六步:进行工艺分析对模具的制造工艺进行分析和确定。
包括分析模具的加工工序、加工工艺和设备要求等。
根据模具的复杂程度和加工难度,合理安排加工顺序,确保模具的制造周期和质量。
第七步:模具制造根据绘制的模具图纸和工艺分析,开始进行模具的制造。
包括模具的零部件加工、热处理、组装和调试等。
在制造过程中,需要严格按照图纸要求进行加工,并进行质量检查和控制,确保模具的精度和质量。
第八步:模具试模和调试在模具制造完成后,进行模具的试模和调试。
将模具安装到注塑机上,进行试模产出。
根据试模的结果进行调整和优化,确保产品的质量和满足客户的要求。
第九步:模具改进和优化根据试模和客户的反馈意见,对模具进行改进和优化。
包括优化注塑工艺参数、改进模具的结构和加工工艺等。
依据改进和优化的方案,进行再次试模和调试,直至满足客户的要求。
第十步:模具交付和使用在模具改进和优化完成后,将模具交付给客户使用。
同时,需要提供合适的模具保养和维护指导,帮助客户正确使用和保养模具,延长模具的使用寿命。
塑胶模具设计手册
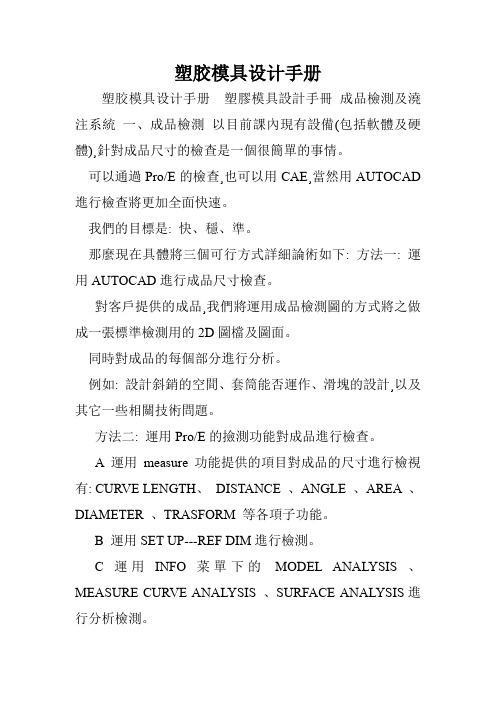
塑胶模具设计手册塑胶模具设计手册塑膠模具設計手冊成品檢測及澆注系統一、成品檢測以目前課內現有設備(包括軟體及硬體)¸針對成品尺寸的檢查是一個很簡單的事情。
可以通過Pro/E的檢查¸也可以用CAE¸當然用AUTOCAD 進行檢查將更加全面快速。
我們的目標是: 快、穩、準。
那麼現在具體將三個可行方式詳細論術如下: 方法一: 運用AUTOCAD進行成品尺寸檢查。
對客戶提供的成品¸我們將運用成品檢測圖的方式將之做成一張標準檢測用的2D圖檔及圖面。
同時對成品的每個部分進行分析。
例如: 設計斜銷的空間、套筒能否運作、滑塊的設計¸以及其它一些相關技術問題。
方法二: 運用Pro/E的撿測功能對成品進行檢查。
A運用measure功能提供的項目對成品的尺寸進行檢視有: CURVE LENGTH、DISTANCE 、ANGLE 、AREA 、DIAMETER 、TRASFORM 等各項子功能。
B 運用SET UP---REF DIM進行檢測。
C 運用INFO菜單下的MODEL ANALYSIS 、MEASURE CURVE ANALYSIS 、SURFACE ANALYSIS進行分析檢測。
方法三:運用CAE功能對成品進行檢測。
二、重量材質部分: 我們知道運用Pro/E的工程計算的功能可以很清楚地計算出成品的體積、重量。
我們運用CAE提供的資料庫將常用塑膠材料的特性進行匯編¸利用方便的塑膠特性選擇注塑成型機的大小。
三、投影面積的大小: 投影面積的大小也可以通過Pro/E 計算¸當然CAE的計算也是可以完成的。
只不過是CAE中投影面積的計算費時太長。
這不是方法上的問題¸而是技巧性的問題。
四、模流分析的結果。
塑膠材料的特性及進膠方式。
一些常見的高份子材料列如下表: 結晶性非結晶性PP 聚丙烯PS(ATACTIC)聚苯乙烯HDPE高密度聚乙烯PV AC 聚酯酸乙烯LDPE低高密度聚乙烯PMMA聚甲基丙烯酸甲酯PA(NYLON) EV A乙烯--醋酸乙烯共聚合物POM聚縮醛A V PTFE EV PEO CHLORINATED PE氯化聚乙烯PETP(PET)聚對苯二甲二乙酯ABS HIPS PPO 賽璐璐(cellulose)纖維素塑膠PC 聚碳酸酯PBT 聚對丁烯二甲二乙酯對一些常見的¸我們公司及客戶們經常使用的塑膠特性做一些簡單的介紹: 一、PC塑料(POLYCARBONATE): PC 兼具有耐熱性、耐沖擊性和透明性。
塑胶模具设计规范-1
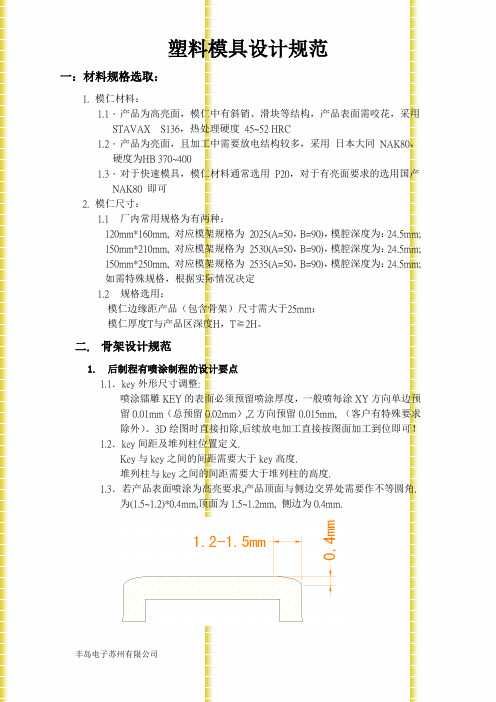
一:材料规格选取:1.模仁材料:1.1.产品为高亮面,模仁中有斜销、滑块等结构,产品表面需咬花,采用STAVAX S136,热处理硬度45~52 HRC1.2.产品为亮面,且加工中需要放电结构较多,采用日本大同NAK80,硬度为HB 370~4001.3.对于快速模具,模仁材料通常选用P20,对于有亮面要求的选用国产NAK80 即可2.模仁尺寸:1.1厂内常用规格为有两种:120mm*160mm, 对应模架规格为2025(A=50,B=90),模腔深度为:24.5mm;150mm*210mm, 对应模架规格为2530(A=50,B=90),模腔深度为:24.5mm;150mm*250mm, 对应模架规格为2535(A=50,B=90),模腔深度为:24.5mm;如需特殊规格,根据实际情况决定1.2规格选用:模仁边缘距产品(包含骨架)尺寸需大于25mm;模仁厚度T与产品区深度H,T≧2H。
二. 骨架设计规范1. 后制程有喷涂制程的设计要点1.1.key外形尺寸调整:喷涂镭雕KEY的表面必须预留喷涂厚度,一般喷每涂XY方向单边预留0.01mm(总预留0.02mm),Z方向预留0.015mm, (客户有特殊要求除外)。
3D绘图时直接扣除,后续放电加工直接按图面加工到位即可!1.2.key间距及堆列柱位置定义.Key与key之间的间距需要大于key高度.堆列柱与key之间的间距需要大于堆列柱的高度.1.3.若产品表面喷涂为高亮要求,产品顶面与侧边交界处需要作不等圆角.为(1.5~1.2)*0.4mm,顶面为1.5~1.2mm, 侧边为0.4mm.2. 后制程有印刷制程的设计要点2.1.不可有任何凸出物高于印刷面,防止凸出物刮伤网板,3.确定进(出)胶方式:按键类产品须有进胶口和出胶口,其方式主要有直接进(出)胶和搭接进(出)胶两种,进胶方式决定于产品结构:①, 产品侧边允许有毛边,或者产品周边有裙边,通常采用直接进胶.②, 产品侧边不允许有毛边,且无裙边的产品通常采用搭接进胶.C.进(出)胶位置及数量:①按键类产品如果进(出)胶选择在长边,长边尺寸小于14mm,尽量做1个进胶1个出胶的方式;(进出胶需错位) 长边尺寸大于14mm,可采用1个进胶2个出胶的方式;②按键类产品如果进(出)胶选择在短边, 采用1个进胶1个出胶的方式即可.(进出胶无需错位)③对于圆环型产品需要做1进3出,分别均匀分布在产品四周.D. 进(出)胶口尺寸:㈠对于直接进出胶:进(出)胶口宽度尺寸设计,视KEY的形状而定,通常进胶比出胶口大0.5~1.0mm。
(新)塑胶模具设计(初级)_

`一. 概述二. 塑膠及塑膠製品三. 典型塑膠模胚結構圖四. 一般塑模設計及加工五. 試模與維護六. 模具管理一. 概述1. 塑膠模具定義及在國民經濟中的重要作用:塑膠模就是利用其特定形狀去成型具有一定形狀和尺寸的塑膠製品的工具,它對塑膠零件的製造質量和成本起決定性影響.在我們日常生活及社會各領域,無處不見模具產品的蹤影.現在,我們就概括說說模具工業在國民經濟中的重要作用.在電子、汽車、電機、儀器、電器、儀表、家電和通訊等產品中,60%~80%的零部件都要依靠模具成形。
用模具生產製件所表現出來的高精度、高複雜程度、高一致性、高生產率和低消耗,是其他加工製造方法所不能比擬的。
模具又是“效益放大器”,用模具生產的最終產品的價值,往往是模具自身價值的幾十倍、上百倍。
目前全世界的模具年產值,約有600億美元。
日、美等工業發達國家,其模具工業產值已超過機床工業產值。
從1997年開始,我國模具工業產值也超過了機床工業產值。
模具生產技術水平的高低,已成為衡量一個國家產品製造水平高低的重要標志,在很大程度上決定著產品的質量、效益和新產品的開發能力。
第一,模具工業是高新技術產業的一個組成部分。
例如,屬於高新技術領域的集成電路的設計與製造,不能沒有做引線框架的精密級進沖模和精密的集成電路塑封模;計算機的機殼、接插件和許多元器件的製造,也必須有精密塑膠模具和精密衝壓模具;數位化電子產品(包括通訊產品)的發展,沒有精密模具也不行。
不僅電子產品如此,在航太航空領域也離不開精密模具。
例如,形狀誤差小於0.1~0.3μm的空對空導彈紅外線接收器的非球面反射鏡,就必須用高精度的塑膠模具成型。
因此可以說,許多高精度模具本身就是高新技術產業的一部分。
有些生產高精度模具的企業,已經被命名為“高新技術企業”。
第二,模具工業又是高新技術產業化的重要領域。
模具製造技術水平的提高,模具工業的技術升高,離不開同高新技術的嫁接。
CAD/CAE/CAM技術在模具工業中的應用,快速原型製造技術的應用,使模具的設計製造技術發生了重大變革,就是一個最好的例證。
塑料模具设计1

柱塞式 螺杆式
PPT文档演模板
注射机技术参数:注塑装置参数、合模部件参数、 整机性能参数
2020/11/9
塑料模具设计1
§4.2 注射机有关工艺参数的校核
一、最大注射量校核
注射机每次实际的注射量应在最大注射量的80%以内
PPT文档演模板
注射量以容积表示:
V≤0.8V机 其中:
V塑料≥K压V
V——塑件的总体积(塑件+浇注系统)
重点与难点: 难点:浇注系统尺寸分析 重点:浇注系统各部分尺寸、设计
2020/11/9
塑料模具设计1
高性能模具
一副高性能模具必须具备下列三个高性 能系统的配合:
高性能充填系统 高性能保压系统 高性能冷卻系统
PPT文档演模板
2020/11/9
塑料模具设计1
塑料模具的浇注系统
PPT文档演模板
2020/11/9
2020/11/9
塑料模具设计1
§4.2 注射机有关工艺参数的校核
五、开模行程的校核
单分型面模具:S>=H1+H2+(5~10)mm 双分型面模具:S>=H1+H2+a+(5~10)mm
PPT文档演模板
2020/11/9
塑料模具设计1
§4.2 注射机有关工艺参数的校核
五、开模行程的校核
注射机最大开模行程(S)与模具厚度(Hm)有关
特种模具
瓣合式模具(HALF——哈夫模) 螺纹模具
滑动型芯与哈夫模块相结合模具
其它模具
2020/11/9
塑料模具设计1
§4.1注射模的结构组成与类型
二、注射模的类型
单分型面注射模
001.塑胶模具基本原理和产品结构设计
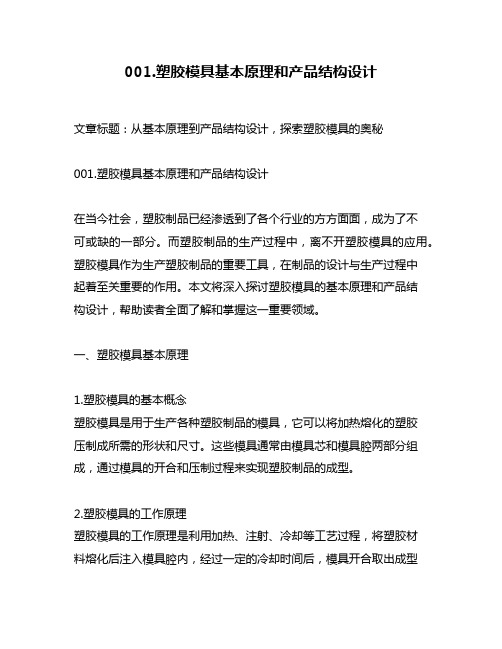
001.塑胶模具基本原理和产品结构设计文章标题:从基本原理到产品结构设计,探索塑胶模具的奥秘001.塑胶模具基本原理和产品结构设计在当今社会,塑胶制品已经渗透到了各个行业的方方面面,成为了不可或缺的一部分。
而塑胶制品的生产过程中,离不开塑胶模具的应用。
塑胶模具作为生产塑胶制品的重要工具,在制品的设计与生产过程中起着至关重要的作用。
本文将深入探讨塑胶模具的基本原理和产品结构设计,帮助读者全面了解和掌握这一重要领域。
一、塑胶模具基本原理1.塑胶模具的基本概念塑胶模具是用于生产各种塑胶制品的模具,它可以将加热熔化的塑胶压制成所需的形状和尺寸。
这些模具通常由模具芯和模具腔两部分组成,通过模具的开合和压制过程来实现塑胶制品的成型。
2.塑胶模具的工作原理塑胶模具的工作原理是利用加热、注射、冷却等工艺过程,将塑胶材料熔化后注入模具腔内,经过一定的冷却时间后,模具开合取出成型的塑胶制品。
这个过程需要严格控制温度、压力、冷却时间等参数,以确保成型的塑胶制品质量。
3.塑胶模具的分类根据不同的成型方法和产品要求,塑胶模具可以分为压缩模具、注射模具和吹塑模具等多种类型,每种类型都有其特定的适用范围和工艺要求。
二、塑胶模具产品结构设计1.产品设计的前期工作在进行塑胶模具产品结构设计之前,需要充分了解产品的使用场景、功能需求、外形尺寸等相关信息,以便为后续的模具设计工作提供有效的参考依据。
2.模具结构设计的要点模具结构设计需要考虑产品的成型过程、模具的制造工艺、使用寿命和维护保养等因素。
合理的模具结构设计可以有效提高模具的使用寿命和成型效率。
3.模具材料的选择模具材料的选择对于模具的使用寿命和成型效果有着至关重要的影响。
合理选择模具材料可以大大提高模具的性能和使用寿命。
三、个人观点与总结回顾通过对塑胶模具的基本原理和产品结构设计进行深入了解,我认为塑胶模具作为塑胶制品生产过程中的重要环节,其工艺和质量对最终成型产品的质量起着决定性的作用。
塑胶模具设计

一.总体结构设计1,分模面(Parting surface)为使产品从模具中取出模具必须分成公母模侧两部分此分界面称之为分模面它有分模和排气的作用但因模具精度和成型之差异易产生毛边结线有碍产品外观及精度选择分模面时注意:1.不可位于明显位置而影响产品外观2.开模时应使产品留在有脱模机构的一侧3.位于模具加工和产品后加工容易处4.对于同轴度要求高的产品尽可能将型腔设计在同一侧5.避免长抽芯考虑将其放在公模开模方向如一定要有应将抽芯机构尽量设在公模侧6.一般不采用圆弧部分分模这样会影响产品外观7.对于流动性好易溢边之塑料应采用插破方式分型可防治毛边产生8.对于高度高脱模斜度小之产品可取中间分模型腔分两边以有利于脱模一套模具的分模面可能有一个或多个在确定分模面时还应考虑如下因素:1.产品的形状尺寸壁厚详加研究分析找最佳方向来分模俗称“拆模”2.了解塑料性能和成型性以及浇注系统的布局3.注意排气和脱模简化模具结构操作方便加工容易它的形式有多种:水平阶梯斜面垂直曲面2.脱模斜度(Draft)为使产品容易从模具中脱出模具上必须设置脱模斜度其大小视产品形状塑料模具结构表面精度和加工方式不同而异一般为1—3目前尚无确切数值和公式大多是依经验值在不影响产品外观和性能之情形下脱模斜度愈大愈好1. 箱盒和盖2.栅格:栅格形状尺寸及肉厚不同应有不同的脱模斜度经验公式如下0.5(A---B)/H =1/12-1/14A二大端尺寸B二小端尺寸H二高度栅格节距在4mm以下之场合,脱模斜度为1/10左右,栅格肉厚超过8 mm斜度不可过份加大可在母模侧多留胶位处分模如栅格段胶位加大可考虑加大斜度3. 加强筋:可改善料流防止应力变形并起补强作用a.纵肋:0.5(A-B)/H=1/500—1/200b.底肋:0.5(A-B)/H=1/150—1/100c.凸柱:0.5(大端直径-小端直径)/H = 1/30—1/20 (内外孔在模具同一侧)母模侧:0.5(大端直径-小端直径)/H = 1/50—1/30公模侧:0.5(大端直径-小端直径)/H = 1/100—1/50 (内外孔在模具两侧)注:母模侧脱模斜度可较公模侧大些以利于脱模3. 肉厚(Thickness)产品的肉厚会直接影响到成型周期和生产效率并会因肉厚不均引起缩收下陷和应力产生设计模具时决定肉厚应注意:1.产品机械强度是否充分2.能否均匀分散冲击力和脱模力不发生破裂3.有埋入件时须防止破裂是否会因肉薄产生结合线而影响强度4.尽可能肉厚一致以防缩收下陷5.肉太薄是否会引起充填不足或阻碍料流以下为常见塑料标准肉厚参考:4.凸柱(Boss)一般为产品上凸出之圆柱它可增强孔的周边强度装配孔及局部增高之用必须防止因肉厚增加造成缩水和因聚集空气造成充填不满或烧焦现象设计时注意点:1.其高度以不超过本身直径之两倍为宜否则须增设加强筋2.其位置不宜太接近转角或侧壁以利于加工3.优先选择圆形以利于加工和料流如在底部可高出底面0.3—0.5mm5.孔(Hole)在多数产品上都有孔的存在其主要有三种方法来取得:1.在产品上直接成型2.在产品上先成型预留孔再机加工完成3.成型后完全由机加工钻孔设计时须注意以下几点:1.孔与孔之间距离须孔径2倍以上2.孔与产品边缘之距离应为孔径之3倍以上3. 孔之周边宜增加肉厚4.孔与产品侧壁之距离应为孔径0.75倍以上5.孔之直径在1.5mm以下时很容易产生弯曲变形须注意孔深不宜超过孔径2倍以上6.分模面在中间之通孔为防止偏心可将不重要一侧之孔径加大6.螺纹(scrow)为装配之用产品上有时会有螺纹设计它可以直接成型也可以在成型后再机械加工对于经常拆卸或受力大之螺纹则采用金属螺纹镶件设计时注意如下原则:1.螺距小于0.75mm之螺纹避免使用最大可使用螺纹5mm之螺纹2.因塑料收缩原因避免直接成型长螺纹以防螺距失真3.螺纹公差小于塑料收缩量时避免使用4.如内外螺纹配合须留0.1—0.4mm之间隙5.螺纹部分应有1--3脱模斜度6.螺牙不可延长至产品末端须设0.8mm左右之光杆部位以利于模具加工和螺纹寿命7.在一些类似瓶盖产品上它会设一些竖琨纹其间距宜大最小为1.5mm 一般为3.0mm在分模面设至少0.8mm平坦部位7.镶嵌件(Insert)为了防止产品破裂增加机械强度或作为传导电流之媒体及装饰之用在产品成型时常埋入镶嵌件注意要点:1.保证镶件牢靠性镶件周围胶层不能太薄2.镶件和镶件孔配合时须松紧合适不影响取放3.为使镶件与塑胶结合紧密埋入部分常设计成粗糙或凹凸之形状(压花钻孔冲弯切槽倒扣等)8.其他要点(Other)1.加强筋不可太厚一般不超过肉厚的一半以防缩水2.只要不影响外关和功能光面尽量改为咬花面这样可减少模具加工难度增加美感防止缩水产生3.在凸柱周边可除去部分肉厚以防止收缩下陷4.肉厚较薄之孔应将孔边及高度增加以便补强5.心芯梢受收缩力影响产品顶出时易造成破裂可设置凸边承受顶出力6.转角设区可改善强度防止应力集中有利于料流7.避免锐角薄肉部份易使材料充填不足8.外边有波纹之产品为方便后加工可改为加强边缘9.分模面有阶段形时模具加工不易考虑改为斜线或曲线分模10.贯穿之抽芯易发生故障改为两侧抽芯为佳11.因圆形比其他形状加工更易可降低成本优先选用12.在产品上加蚀文字或图案时如无特殊要求尽量设计凹字便于模具加工二.浇注系统设计浇注系统是塑模设计中一重要环节常分为普通和无流道浇注系统它跟所用塑料产品形状尺寸机台分模面有密切关系设计时注意以下原则:1.流道尽量直尽量短减少弯曲光洁度在Ra=1.6—0.8um之间2.考虑模具穴数按模具型腔布局设计尽量与模具中心线对称3.当产品投影面积较大时避免单面开设浇口以防注射受力不均4.浇口位置应去除方便在产品上不留明显痕迹不影响产品外观5.主流道设计时避免塑料直接冲击小型芯或小镶件以免产生弯曲或折断6.主流道先预留加工或修正余量以便保证产品精度1.主流道设计主流道是连接机台喷嘴至分流道入口处之间的一段通道是塑料进入模具型腔时最先经过的地方其尺寸大小与塑料流速和充模时间长短有密切关系太大造成回收冷料过多冷却时间增长包藏空气增多易造成气泡和组织松散极易产生涡流和冷却不足如流径太小热量损失增大流动性降低注射压力增大造成成型困难一般情况下主流道会制造成单独的浇口套镶在母模板上但一些小型模具会直接在母模板上开设主流道而不使用浇口套主流道设计要点:1.浇口套内孔为圆锥形(2--6 )光洁度在Ra=1.(-0.8um锥度须适当太大造成压力减少产生潮流易混进空气产生气孔锥度过小会使流速增大造成注射困难2.浇口套口径应比机台喷嘴孔径大1—2mm以免积存残料造成压力下降浇道易断3. 一般在浇口套大端设置倒圆角国=1—3mm)以利于料流4.主流道与机台喷嘴接触处设计成半球形凹坑深度常取3—5mm特别注意浇口套半径比注嘴半径大1—2mm 一般取R=19—22mm之间以防溢胶5.主流道尽量短以减少冷料回收料减少压力和热量损失6.主流道尽量避免拼块结构以防塑胶进入接缝造成脱模困难7.为避免主流道与高温塑胶和射嘴反复接触和碰撞一般浇口套选用优质钢材加工并热处理8.其形式有多种可视不同模具结构来选择一般会将其固定在模板上以防生产中浇口套转动或被带出2.分流道设计分流道是主流道的连接部分介于主流道和浇口之间起分流和转向作用分流道必须在压力损失最小的情况下将熔融塑胶以较快速度送到浇口处充模其截在截面积相等的条件下正方形之周长最长圆形最短面积如太小会降低塑料流速延长充模时间易造成产品缺料烧焦银线缩水如太大易积存过多气体增加冷料延长生产周期降低生产效率对于不同塑胶材质分流道会有所不同但有一个设计原则:必须保证分流道的表面积与其体积之比值最小即在分流道长度一定的情况下要求分流道的表面积或侧面积与其截面积之比值最小分流道型式有多种它因塑胶和模具结构不同而异常用型式有圆形半圆形矩形梯形U形正六边形如图设计时基本原则:1.在条件允许下分流道截面积尽量小长度尽量短2.分流道较长时应在末端设置冷料穴以容纳冷料和防止空气进入而冷料穴上一般会设置拉料杆以便于胶道脱模3.在多型腔模具中各分流道尽量保持一致长度尽量短主流道截面积应大于各分流道截面积之和4.其表面不要求过份光滑(Ra=1.6左右)有利于保温5.如分流道较多时应考虑加设分流锥可避免熔融塑胶直接冲击型腔也可避免塑料急转弯使塑胶平稳过渡6.分流道一般采用平衡式方式分布特殊情况可采用非平衡方式要求各型腔同时均衡进胶排列紧凑流程短以减少模具尺寸7.流道设计时应先取较小尺寸以便于试模后有修正余量一般的流道直径(尺寸)3.浇口设计浇口是指流道末端与型腔之间的连接部分是浇注系统的最后部分其作用是使塑料以较快速度进入并充满型腔它能很快冷却封闭防止型腔内还未冷却的热胶倒流设计时须考虑产品尺寸截面积尺寸模具结构成型条件及塑胶性能有关浇口尽量短小与产品分离容易不造成明显痕迹其类型多种多样主要有:浇口的种类及其特微9. 盘形浇口:沿产品外圆周而扩展进料其进料点对称充模均匀能消除结合线有利于排气水口常用冲切方式去除设计时注意冲切工艺10.扇形浇口:从分流道到模腔方向逐渐放大呈扇形适用于长条或扁平而薄之产品可减少流纹和定向应力扇形角度由产品形状决定浇口横面积不可大于流道断面积11.环形浇口:延产品整个外圆周扩展进胶它能使塑胶绕型芯均匀充模排气良好减少结合线但浇口切除困难它适用于薄壁长管状产品12.点浇口:是一种截面积小如针状之浇口一般用于流动较好之塑胶其浇口长度一般不超过其直径所以脱模后浇口自动切断不须再修正而浇口残痕不明显在箱罩盒壳体及大面积产品中应用相当广泛它可以使模具增加一个分模面便于水口脱模其缺点是因进浇口较小易造成压力损耗成型时产生一些不良(流痕烧焦黑点)其形状有菱形单点形双点形多点形13.侧浇口: 一般开设在模具一边分模面上由内侧或外侧进胶截面多为矩形适用于一模多穴14.直接浇口:直接由主流道进入模腔适用于单穴深腔壳形箱形模具其流道流程短压力损失少有利于排气但浇口去除不便会留明显痕迹15.潜伏浇口:其浇口呈倾斜状潜伏在分模面一方在产品侧面或里面进胶脱模时可自动切断针点浇口适用自动化生产设计要点:1.进胶口应开设在产品肉厚部分保证充模顺利和完全2.其位置应选在使塑胶充模流程最短处以减少压力损失有利于模具排气3.可通过模流分析或经验判断产品因浇口位置而产生之结合线处是否影响产品外观和功能可加设冷料穴加以解决4.在细长型芯附近避免开设浇口以免料流直接冲击型芯产生变形错位或弯曲5.大型或扁平产品建议采用多点进浇可防止产品翘曲变形和缺料6.尽量开设在不影响产品外观和功能处可在边缘或底部处7.浇口尺寸由产品大小几何形状结构和塑胶种类决定可先取小尺寸再根据试模状况进行修正8. 一模多穴时相同的产品采用对称进浇方式对于不'同产品在同一模具中成型时优先将最大产品放在靠近主流道的位置9.在浇口附近之冷料穴尽端常设置拉料杆以利于浇道脱模4.热流道目前浇注系统发展和改进的一个重要方向就是开发热流道模具它与一般注射模具的主要区别就是注射成型过程中浇注系统内之塑胶不会冷却拟固也不会形成浇道与产品一起脱模[[因此也称无流道模具在大型和精密模具设计中应用已越来越广泛它有以下优点:1.缩短成型周期省去剪浇口修整产品破碎回收等工序节约人力物力提高生产效率2.因无冷胶可减少材料消耗3.因生产中温度严格控制显著提高产品质量降低次品产生4.因浇注系统中塑胶始终处于融熔状态有利于压力传递可降低注射压力利于成型5.因无浇道产生所以可缩短开模行程有利于模具和机台寿命但热流道模具结构复杂温度控制要求严格需要精密的温控系统制造成本较高不适合小批量生产根据不同塑胶特性对热流道模具有不同要求见下表:三.顶出系统设计产品完成一个成形周期后开模产品会包裹在模具的一边必须将其从模具上取下来此工作必须由顶出系统来完成它是整套模具结构中重要组成部分一般由顶出复位和顶出导向等三部分组成一.按动力来分1.手动顶出:当模具开模后由人工操纵顶出系统顶出产品它可使模具结构简化脱模平稳产品不易变形但工人劳动强度大生产率低适用范围不广一般在手动旋出螺纹型芯时使用2.机动顶出:通过注射机动力或加设之马达来推动脱模机构顶出产品它可通机台上的顶杆\推顶针板来达到脱模目的也可在公母模板上安装定距拉杆或链条靠开模力拖动顶出机构顶出产品调模时必须注意控制开模行程适用于顶出系统在母模侧之模具3.液压顶出:在模具上安装专用油缸由注射机控制油缸动作其顶出力速度和时间都可通过液压系统来调节可在合模之前顶出系统先回位4.气动顶出:利用压缩空气在模具上设置气道和细小的顶出气孔直接将产品吹出产品上不留顶出痕迹适用于薄件或长筒形产品二.按模具结构分一次顶出机构二次顶出机构母模顶出机构浇注系统顶出机构螺纹顶出机构等设计原则:1.选择分模面时尽量使产品留在有脱模机构的一边2.顶出力和位置平衡确保产品不变形不顶破3.顶针须设在不影响产品外观和功能处4.尽量使用标准件安全可靠有利于制造和更换顶出系统形式多种多样它与产品之形状结构和塑胶性能有关一般有顶杆顶管推板顶出块气压复合式顶出等一.顶杆它是顶出机构中最简单最常见的一种形式其截面积形式主要有如下1.圆形因圆形制造加工和修配方便顶出效果好在生产中应用最广泛但圆形顶出面积相对较小易产生应力集中顶穿产品顶变形等不良在脱模斜度小阻力大等管形箱形产品中尽量避免使用当顶杆较细长时一般设置成台阶形的有托顶针以加强刚度避免弯曲和折断设计要点:1.顶出位置应设置在阻力大处不可离镶件或型芯太近对于箱形类等深腔模具侧面阻力最大应采用顶面和侧面同时顶出方式以免产品变形顶破2.产品阻力均衡时顶杆应对称设置使受力平衡3.当有细而深之加强筋时一般在其底部设置顶杆4.若模具上有镶件顶针设在其上效果更佳5.在产品进胶口处避免设置顶针以免破裂6.当产品表面不允许有顶出痕迹时可设置顶出耳再剪除7.对于薄肉产品在分流道上设置顶针即可将产品带出8.顶针与顶针孔配合一般为间隙配合如太松易产生毛边太紧易造成卡死为利于加工和装配减少摩擦面一般在模仁上预留10—15mm之配合长度其余部分扩孔0.5—1.0mm成逃孔9.为防止顶针在生产时转动须将其固定在顶针板上其形式多种多样须根据顶针大小形状位置来具体确定在此不一一列举10. 顶出系统托模以后在进行下一周期生产时必须退回原处其形式主要有强制回位拉杆回位弹簧回位油缸二.顶管又叫司筒或套筒顶针它适用于环形筒形或带中心孔之产品顶出由于它是全周接触受力均匀不会使产品变形也不易留下明显顶出痕迹可提高产品同心度但对于周边肉厚较薄之产品避免使用以免加工困难和强度减弱造成损坏三.推板此形式适用于各种容器箱形筒形和细长带中心孔之薄件产品它顶出平稳均匀顶出力大不留顶出痕一般会有固定连接以免生产中或托模时将推板推落但只要导柱足够长严格控制托模行程推板也可不固定.。
塑胶模具设计指引
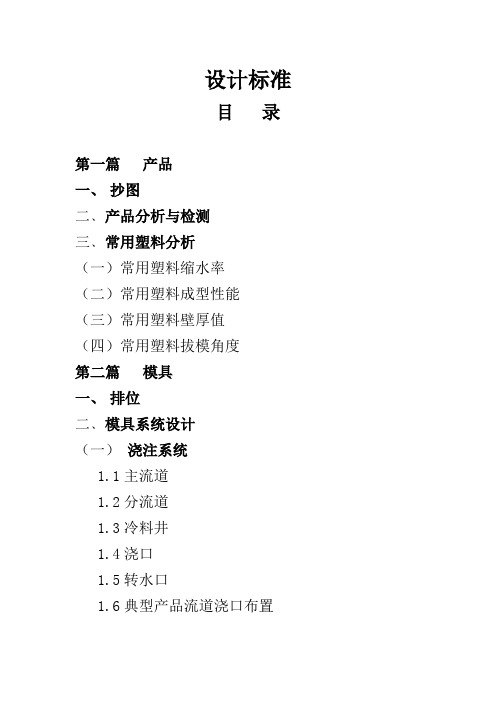
设计标准目录第一篇产品一、抄图二﹑产品分析与检测三﹑常用塑料分析(一)常用塑料缩水率(二)常用塑料成型性能(三)常用塑料壁厚值(四)常用塑料拔模角度第二篇模具一、排位二﹑模具系统设计(一)浇注系统1.1主流道1.2分流道1.3冷料井1.4浇口1.5转水口1.6典型产品流道浇口布置(二)成形系统2.1行位系统行位斜顶2.2镶件(三)顶出系统4.1顶出系统设计要点4.2顶出机构的基本方式 4.2.1顶针4.2.2司筒4.2.3扁顶针4.2.4直顶4.2.5推板4.3先复位机构(四) 冷却系统5.1.运水位置5.2.水路大小5.3.水路与模胚位置关系5.4.水井(五) 导向定位系统(六) 排气系统7.1产品排气7.2导套排气槽7.3尼龙螺丝排气孔(七)模胚结构件(支撑)及周边辅助件 7.1撑头7.2垃圾钉7.3锁模机构7.4温控箱、水管、紧固件三﹑细水口模设计四、模具零部件材料选择六、分模(一)模具档分模(二)组立档分模七、注射机选择第三篇图档一、出图要求1.排位图2.装配图3.顶针图4.线割图5.零件图6.分模图7.爆炸图二、图纸管理与进度控制(一)图纸管理(二)审图(三)进度三、电脑图档管理第四篇附录一、标准件二、工程表格产品篇抄图一.抄图前,先要看懂,看透产品线图,然后班顺思路,特别是外形面的画法。
抄好产品图要转为2D线图与设计部提供的平面线图套。
要保证主要的视图和边界线完全重合一致。
若有不重合、不一致的情况,首先分析是2D线图本身表达有问题,还是抄图时造成的。
若为2D线图表达问题则应及时标明,并与设计部沟通、反映;若为抄图问题,及时修改。
二.一个产品通常要多次转图与标题栏对上几次逐步确认(看版本),避免最后的问题堆积。
三.在抄图的整个过程中,最为重要的是基体外形面的控制和核对。
四.抄好的UG尽可能保证可以再生,以实现UG的参数设计功能。
五.通常抄图应先抄好影响模具结构之处,如外形面、行位处倒勾、前后模基面加减胶。
塑料成型模具设计课件1
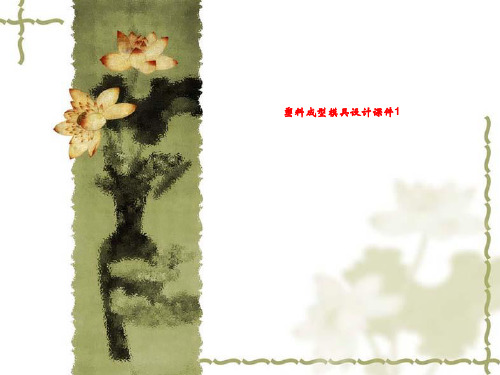
课程情况总体介绍:
授课学时:40学时(课堂讲解32学时、上机8学时)
课程性质: 高分子加工专业的一门主干专业技术课, 是一门实践性、综合性很强的课程。
课程目录:
第一章 绪论 第二章 注射成型模具结构 第三章 注射成型模具设计 第四章 计算机辅助设计软件简介(上机操作)
材化学院高分子系
材化学院高分子系
第一章 绪论 1.1 模具及模具的发展概况
1. 模具(基本概念1):——是指利用其本身特定 形状去成型具有一定形状和尺寸的制品的工具。
材化学院高分子系
第一章 绪论 1.1模具及模具的发展概况
特点: 1)模具----是一种工具; 2)模具与塑件-----“一模一样” ; 3)模具生产制件所具备的高精度、高复杂程度、 高一致性、高生产率和低消耗,是其他加工制造 方法所不能比拟的。
第一章 绪论
压缩成型机
压缩模具
材化学院高分子系
压缩成型产品
压注成型机
第一章 绪论
压注原理
材化学院高分子系
压注成型产品
挤出机头
第一章 绪论 挤出成型产品
材化学院高分子系
挤出成型过程
注射成型机
第一章 绪论
注射成型产品
注射原理
材化学院高分子系
吹塑成型机
第一章 绪论
吹塑原理
材化学院高分子系
吹塑成型产品
液压系统
模具安 装空间
材化学院高分子系
产品出口
电路控 制系统
报警器
第一章 绪论
小结:
模具及模具的发展概况; 塑料的成型工艺方法与成型模具 塑料模塑成型及模具技术的发展动向 本课程的学习目的与要求。
材化学院高分子系
塑胶模具设计_初级_

`一. 概述二. 塑膠及塑膠製品三. 典型塑膠模胚結構圖四. 一般塑模設計及加工五. 試模與維護六. 模具管理一. 概述1. 塑膠模具定義及在國民經濟中的重要作用:塑膠模就是利用其特定形狀去成型具有一定形狀和尺寸的塑膠製品的工具,它對塑膠零件的製造質量和成本起決定性影響.在我們日常生活及社會各領域,無處不見模具產品的蹤影.現在,我們就概括說說模具工業在國民經濟中的重要作用.在電子、汽車、電機、儀器、電器、儀表、家電和通訊等產品中,60%~80%的零部件都要依靠模具成形。
用模具生產製件所表現出來的高精度、高複雜程度、高一致性、高生產率和低消耗,是其他加工製造方法所不能比擬的。
模具又是“效益放大器",用模具生產的最終產品的價值,往往是模具自身價值的幾十倍、上百倍。
目前全世界的模具年產值,約有600億美元。
日、美等工業發達國家,其模具工業產值已超過機床工業產值。
從1997年開始,我國模具工業產值也超過了機床工業產值。
模具生產技術水平的高低,已成為衡量一個國家產品製造水平高低的重要標志,在很大程度上決定著產品的質量、效益和新產品的開發能力。
第一,模具工業是高新技術產業的一個組成部分。
例如,屬於高新技術領域的集成電路的設計與製造,不能沒有做引線框架的精密級進沖模和精密的集成電路塑封模;計算機的機殼、接插件和許多元器件的製造,也必須有精密塑膠模具和精密衝壓模具;數位化電子產品(包括通訊產品)的發展,沒有精密模具也不行。
不僅電子產品如此,在航太航空領域也離不開精密模具。
例如,形狀誤差小於0.1~0.3μm的空對空導彈紅外線接收器的非球面反射鏡,就必須用高精度的塑膠模具成型。
因此可以說,許多高精度模具本身就是高新技術產業的一部分。
有些生產高精度模具的企業,已經被命名為“高新技術企業"。
第二,模具工業又是高新技術產業化的重要領域。
模具製造技術水平的提高,模具工業的技術升高,離不開同高新技術的嫁接。
CAD/CAE/CAM技術在模具工業中的應用,快速原型製造技術的應用,使模具的設計製造技術發生了重大變革,就是一個最好的例證。
塑料模具设计教学(精选)
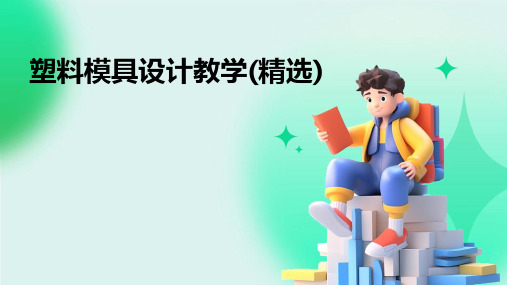
设计需求分析
03
研究仪表盘的形状、尺寸、功能等要求。
典型案例分析讨论
模具结构设计
探讨大型复杂模具的设计思路,如多 型腔布局、侧向抽芯等。
制造工艺及装配
分析模具的加工难点、热处理及装配 调试技巧。
学生实践操作指导建议
实践操作前准备 熟悉常用塑料模具设计软件,如UG、Pro/E等。
掌握基本的模具设计理论知识,如分型面设计原则、浇注系统设计方法等。
加工。
装配调试过程及注意事项
装配前准备
清洗零件、检查尺寸精度和形 位公差,准备好所需的装配工
具和材料。
组件装配
按照装配图纸要求,将各个零 件组装成完整的模具结构,注 意配合精度和紧固力矩。
总装调试
在专用设备上对模具进行合模 、开模、顶出等动作调试,确 保模具动作顺畅、无卡滞现象 。
试模与验收
在试模机上进行试模生产,检 查产品尺寸精度、外观质量等 是否符合要求,对模具进行最
注射成型设备
包括注射机、合模装置、注射装置、液压和电气控制系统等 。注射机是注射成型的主要设备,其类型、规格和结构对塑 料制品的质量、生产效率及成本等均有直接影响。
分型面设计与浇注系统
分型面设计
分型面是模具中用以取出塑件和浇注系统凝料的可分离的接触表面。分型面的位 置和形状对模具结构、制造精度、排气状况、操作方便程度以及塑件的外观质量 都有很大影响。
产品的污染和变形等问题。
05 塑料模具材料选 择与热处理
常用塑料模具材料介绍
01
02
03
碳素钢
用于制造形状简单、精度 要求不高的塑料模具,如 小型模具、试制模具等。
合金钢
具有较高的强度、韧性和 耐磨性,适用于制造大型 、复杂、高精度的塑料模 具。
模具设计教程(1)
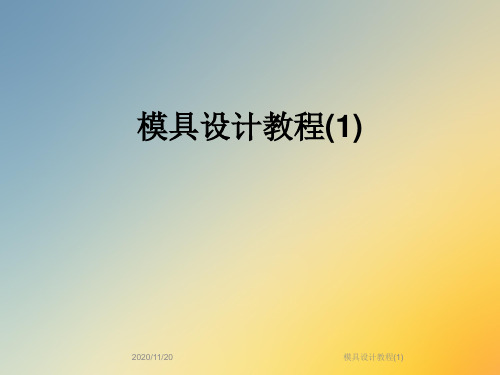
模具设计教程(1)
模具设计
概论2、模具的分类 按制品的材质分类: 金属模:锻造模(冷<温>锻,热锻);铸造模;冷冲 压铸模;粉末压制模;注射模;挤出模… 橡胶模:热压模;注射模…… 塑料模:注射模;挤出模;压制模;吹塑模;吸塑模 模…… 其 他:蜡模;石膏模;玻璃模……
模具的概述
概论
合理的模具设计,主要体现在所成型的塑料制品的
质量(外观质量及尺寸稳定性),使用时的安全可靠和
便于维修,在注塑成型时有较短的成型周期和较长的使
用寿命以及具有合理的模具制造工艺性等方面。
在做模具设计时须知,一个产品它可以同时拥有几
种不同的设计方法,衡量每一种方法的优缺点,再选择 最理想的方法进行设计。对于一些重开模,也必须考虑 在原来的基础上是否做改善。
模具设计教程(1)
• 成型零件的结构形式与设计
型腔的结构形式: 1.整板式型腔 2. 整体式型腔 3. 局部镶拼式型腔 4. 拼块式
5. 瓣合式型腔
模具设计教程(1)
采用镶拼式型腔的优点: 简化了复杂型腔的加工工艺 减少了热处理变形 有利于排气 节约了贵重的模具钢。 缺点: 型腔的精度、装配的牢固性会受影响 在产品上留下镶拼的痕迹
模具设计教程(1)
• 细水口模架
导套 Guide Bush
拉杆 Support Pin
水口推板 Stripper Plate
模具设计教程(1)
• 大水口与细水口模架的不同
相同之处:动模部分 不同之处:顶板和A板之间无固定用的螺钉。
顶板和A板之间可移动一定的距离。 顶板要比底板厚。
定模部分有拉杆导柱和拉杆导套。
模具设计基础知识(新手必看)

模具设计基础知识(新手必看)-CAL-FENGHAI-(2020YEAR-YICAI)_JINGBIAN1. 塑胶材料常用收缩率ABS PC PMMA PS POM PVC PE PP 塑胶件常出现的瘕疵?缺胶、披风、气泡、缩水、熔接痕、黑点、气泡、条纹、翘曲、分层、脱皮等 .3. 常用的塑胶模具钢材?718 738 S136 NAK80 SKH51 SKD61 2344 84074. 高镜面抛光用哪种钢材?常用高硬热处理钢材,如 SKD61 、 8407 、 S136 等!5 . 什么是 2D 什么是 3D ?2D 是指二维平面, 3D 是指三维空间。
在模具部分, 2D 通常是指平面图,即 CAD 图; 3D 通常是指立体图,即 PRO/E 、 UG 或其他 3 D 软件的图档。
6 . UG 的默认精度是多少?UG 的默认精度是7 . 什么是碰穿什么是插穿?与 PL 面平行的公母模贴合面叫碰穿面;与 PL 面不平行的公母模贴合面叫插穿面!8 . 条和丝的关系?条和丝都是长度单位。
条为台湾用语, 1 条 = ;丝为香港用语, 1 丝 = ,所以, 1 条 =1 丝9 . 枕位是什么?外壳类塑件的边缘常开有缺口,用于安装各类配件,此处形成的枕状分型部分称为枕位 .10 . 火山口是什么?BOOS 柱根部减胶部分反映在模具上的类似于火山爆发后的形状叫做模具火山口。
深的骨位上也常做,目的是为了防止缩水。
11 . 呵是指什么?呵就是模仁,香港习惯用语,镶呵的意思就是镶模仁。
12 . 什么是虎口?虎口,又称管位,即用来限位的部分。
常用在模仁的四个角上,起前后模仁一个精定位的作用,常用 CNC 或模床加工。
13 . 什么叫排位?模具上的产品布局称为排位。
往往由进胶式样与模具结构及产品本身来决定的。
14. 什么叫胶位?模具上产品的空穴称为胶位。
也就是你需要的塑胶件15 . 什么叫骨位?产品上的筋称为骨位。
多是起连结或限位作用的16 . 什么叫柱位?产品上的 BOSS 柱称为柱位。
塑料模具设计课程标准(1)

塑料模具设计课程标准(1)塑料模具设计课程标准目的:本课程旨在为学生提供一系列有关塑料模具设计的知识和技能。
经过学习本课程,学生将能够掌握塑料模具的设计原理、工艺流程、材料选择、机械加工过程等方面的知识,获得一定的创新思维能力和实践操作技能。
课程重点:1. 塑料模具的基本概念和工艺原理2. 塑料模具的设计流程和标准3. 塑料模具所涉及的材料及其选择原则4. 塑料模具的机械加工和制造技术5. 塑料模具的质量检验与维护课程内容:1. 塑料模具的基本概念和工艺原理(1)塑料模具的定义和分类;(2)塑料模具的工艺流程和工作原理;(3)塑料模具所涉及的材料及其特点。
2. 塑料模具的设计流程和标准(1)塑料模具的设计步骤和标准;(2)塑料模具设计中常用的工具和软件;(3)塑料模具设计中的实践操作。
3. 塑料模具所涉及的材料及其选择原则(1)塑料模具的主要材料及其基本特性;(2)塑料模具材料的选择原则和技巧。
4. 塑料模具的机械加工和制造技术(1)塑料模具的机械加工方法和工艺;(2)塑料模具的制造技术和挑选厂家的原则和方法。
5. 塑料模具的质量检验与维护(1)塑料模具的检验和测试方法;(2)塑料模具维护中常见故障和处理方法。
教学方法:1. 以案例为基础,加强实践操作;2. 以多媒体教学方式,提高学生的视听体验;3. 采用小组讨论或课程策划等形式,增加学生之间的相互交流及创新思维。
考核与评价:1. 平时教学表现;2. 课堂测试和参考书单;3. 设计项目与报告、产品展示等综合考核。
塑料模具设计基础

上一页 下一页 返回
3.1 塑件的工艺性
• 应采取的预防措施,是将塑件侧壁设计得稍微外凸,待内凹后刚
好平直,如图3-10(b)所示。图3-10(c)则是在不影响塑件使用要求的 前提下将塑件各边均设计成弧形,从而使塑件不易产生翘曲变形。 • 此外,塑件的形状还应考虑分型面位置,有利于飞边和毛刺的去除。 • 综上所述,塑件的形状必须便于成型的顺利进行,简化模具结构, 有利于生产率的提高和确保塑件质量。 • 2.塑件壁厚 • 塑件壁厚是否合理直接影响塑件的使用及成型质量。壁厚不仅要满 足在使用上有足够的强度和刚度,在装配时能够承载紧固力,而且要 在满足成型时熔体能够充满型腔,在脱模时能够承受脱模机构的冲击 和振动。
上一页 下一页 返回
3.1 塑件的工艺性
• 按此标准,塑件的精度分为8个等级,其中1,2级属于精密技术级, 只有在特殊要求下使用,对于未注公差要求的自由尺寸,建议采用标 准中的8级精度,表3-1中只列出标准公差值,其基本尺寸的上、下偏 差可根据塑件的配合性质进行分配。塑件上孔的公差采用基孔制,取 表中数值并冠以“十”号。塑件上轴的公差采用基孔制,取表中数值 并冠以“一”号,中心距及其他位置尺寸公差采用双向等值偏差。
上一页 下一页 返回
3.1 塑件的工艺性
• ②加强筋厚度小于壁厚,否则壁面会因筋根部的内切圆处的缩孔
而产生凹陷。 • ③加强筋的高度不宜过高,以免筋部受力破损。为了得到较好的增
强效果,以设计矮一些、多一些为好,若能够将若干个小肋连成栅格, 则强度能显著提高。 • ④加强筋的设置方向除应与受力方向一致外,还应尽可能与熔体流 动方向一致,以免料流受到搅乱,使塑件的韧性降低。 • ⑤加强筋之间中心距应大于两倍壁厚,且加强筋的端面不应与塑件 支承面平齐,应留有一定间隙,否则会影响塑件使用,如图3-17所示。
- 1、下载文档前请自行甄别文档内容的完整性,平台不提供额外的编辑、内容补充、找答案等附加服务。
- 2、"仅部分预览"的文档,不可在线预览部分如存在完整性等问题,可反馈申请退款(可完整预览的文档不适用该条件!)。
- 3、如文档侵犯您的权益,请联系客服反馈,我们会尽快为您处理(人工客服工作时间:9:00-18:30)。
一. 塑膠及塑膠製品塑膠模具是用來生產塑膠製品的工具,在設計製造模具之前.必須對各種常用塑膠的特性有充分瞭解和掌握.才能精確控制模具尺寸與塑膠件尺寸及成型條件之間的內在關係.才能設計出優秀的模具,常用熱塑性塑膠之特性如下:在實際研發和生產中,產品設計師與模具設計師往往不屬於同一人,這就造成各人會按自己的立場去設計完美自己的產品.如果兩者在各自領域不是很瞭解,將有可能設計出來的產品在模具結構和製造工藝上造成不可行性.塑膠製品的設計不僅要滿足使用要求,而且要符合塑膠的成型工藝特點,並且盡可能使模具結構減化.這樣可使成型工藝穩定,保證塑膠製品的質量,又可使生產成本降低,設計時考慮如下:1.塑膠的性能塑膠的物理力學性能和工藝性能2.成型方法要視具體的成型工藝來確定設計方案3.模具結構和製造工藝有利於模具結構的簡化和製造設計內容主要包括: 幾何形狀尺寸精度表面質量幾何形狀: 形狀肉厚脫模斜度加強肋支撐面圓角孔螺紋嵌件1.形狀盡量避免側壁凹槽或脫模方向垂直的孔,設計成球面或帶击緣形狀可提高強度與剛性.2.肉厚滿足使用和成型條件,力求勻稱,以防內應力.3.脫模斜度為便於脫模,其大小與塑膠性能,縮水率,形狀,肉厚有關.注意:(1)精度要求高,尺寸較高部位脫模斜度較小.(2)形狀復雜,不易脫模處脫模斜度較大.(3)一般母模側斜度比公模側脫模斜度大.方向: 內孔以小端為准,外形以大端為准,脫模斜度不包括在產品公差範圍內.4.加強肋可確保產品的強,度剛度,又不至於使產品的厚度過大.在適當位置設置可避免塑件變形改善料流方向.5.支撐面凸邊或凸點為支撐面,可增加產品剛度和平穩度.6.圓角在轉角處盡可能採用圓弧過渡,可避免應力集中,提高產品強度,改善料流狀況及便於脫模.一般外半徑R1=1.5肉厚,內半徑R=0.5肉厚.7.孔通孔,盲,螺紋孔,不影響產品強度,形狀簡單,簡化模具製造工藝.須注意孔與孔,孔與壁之間間距.8.螺紋可直接成型,也可成型後機械加工.對經常裝卸或受力較大之螺紋採用金屬鑲嵌件.注意:外螺紋牙型不宜過細,直徑不宜小於4MM,內螺紋牙型不宜小於2MM,牙距須考慮收縮率.螺紋始端和末端須設計過渡長度,以防崩裂變形.9.嵌件在產品中鑲入金屬或其他材料形成不可卸連接,可提高機械強度及耐磨性,保證電氣性能,增加產品形狀及尺寸的穩定性,提高精度.注意:包裹層不可太薄,必須保證鑲件在模具內固定的牢靠性.尺寸精度: 材料縮水率和模具製造誤差是主要因素1.成形材料成形條件2塑件形狀3模具主流道尺寸料流方向分型面模具製造誤差及磨損4成型後的條件測量誤差存放條件表面質量: 黑點白點條紋縮水氣泡色差光澤性行(鏡面) 粗糙度(蝕紋) 文字二. 一般塑模設計及加工塑膠模具之設計與製造,是一種高度專門化的技術範圍.一個模具師在他的工作範圍內要熟練的話,需要經過幾年的刻苦磨練.在塑膠工業開始要蓬勃發展之時,熟練模具人才之缺乏就已經是一個嚴重的問題.現在想要在這方面一展抱負之模具人才,依然有多數就業機會在等他.因模具是一精密昂貴的設備,同時從設計到加工完成.須數月時間.而每一套模具的設計,都要因產品的需要而作靈活運用,因此其結構上的每一細節,都須仔細考量和詳加研究.假如現在我們接到一項開模通知單,將如何來展開開模動作呢?下面我們就一起一步一步來學習:1.一般塑模結構簡介:首先讓我們來瞭解一下一套模具的基本結構(附模型)及作用(口述),如下圖:模具的幾個常用名詞:1.溶注口或水口(sprue)塑膠由此進入模腔內,亦稱主流道.溶注口瀙套連接噴嘴與模具,已形成標準件.有些母模板較薄的模具,不須瀙套,直接在模具上鑽出溶注口.2.冷料穴(cold-slug well)噴嘴最前端的熔融塑膠溫度較低,形成冷料渣.在進料口的末端公模仁上開設洞穴,以防止冷料渣進入模腔,造成堵塞流道.減緩料流速度,產品上形成冷料痕結合線.為了開模時從瀙套內拉出冷凝料,一般在冷料穴末端設置拉料桿(頂針上).3. 分流道(runne)分流道是主流道的連接部分,是塑膠流入模腔的通道,它可在壓力損失最小的條件下,將主流道內的塑膠以較快的速度送到澆口處,其主要類型有:圓形.半圓形.矩形.梯形. 要求分流道的表面積或側面積與其截面積的比值為最小.4.柵門(gates)亦稱澆口,是分流道和型腔之間連接部分,也是澆注系統的最後部分.其作用是使流道內熔融塑膠以較快速度進入模腔.型腔充滿後澆口能很快冷卻封閉,防止型腔內未冷卻料回流.其類型.位置.形狀.多種多樣.主要有:盤形.扇形.環形.點狀.側進膠.直接進膠.潛伏進膠.5.排氣槽(vent)當模具完全閉合時,模腔與澆道內充滿空氣.注射時必須將空氣排出模具以外,否則將產生燒焦,填充不滿,毛邊,氣泡,銀線等不良.排氣槽的形式,大小.深度因材料和模具結構不同而異(如上表),其方法主要有:分模面排氣法,頂針排氣法,鑲件排氣法,水路排氣法,真空排氣法.6.頂出系統(Ejection device)是將產品從模具上脫出之裝置,亦稱脫模機構.是模具的重要組成部分,其形式和推出方式因產品形狀,結構和塑膠特性有關,其零件有頂針,推板,頂出塊,斜梢,司筒,油缸或氣缸,齒輪等,它與模仁之間是間隙配合,表面積盡可能大,設在不影響外觀和功能處,注意脫模平衡.7.模穴模仁(Mold cavity)模穴是在模板上挖框,,以便埋入模仁,主要是節省材料和加工方便方面考慮.有些分模面斷差大的模具母模側,會不挖模穴直接在模板上加工產品部分.模仁主要指模具的產品部分,其精度,材質要求比模胚部分要高,其形狀,形式對不同的模具有不同的要求,為整套模具最重要部分.8.模具鋼(Mold Steel)一套模具外觀看似乎都是一樣的鋼鐵,其實它的各部位因要求不同必須使用不同之材質,模具鋼之選擇對模具壽命,加工性,精度等影響很大.模具鋼材料因模具之構造塑膠產品要求不同而異.選材要求主要如下:1.采購容易2.機械加工性優良3.耐磨,耐腐蝕,耐熱性好4.組織細密一致,無針孔等內部缺陷5.適合熱處理變形小6.經濟,降低成本又能滿足使用要求模具與成型設備之關係模具要生產,必須架設在相應的成型設備上才能發揮其作用.所以從廣義上講,模具也是成型機的一個組成部分.兩者之間相輔相成,互為關聯.在模具設計中必須瞭解此模具生產中適用機台之相關規格.才能設計出符合要求之模具:1.注射機型號及生產廠商2.最大注射量3.最大鎖模力4.噴嘴球面半徑及噴嘴孔徑5.定位孔直徑6.頂桿間距座標7.閉合高度(最大最小)8.注塑機能配合的脫模方式9.注塑機開模行程及開距10.其他相關要求模具設計思路一套模具的好壞,可以說一半取決於設計.而一套模具設計的好壞,牽涉面極廣,除了要求設計者有豐富的模具方面理論知識和經驗外,對設計前的周詳檢討與思考也同樣重要:1.瞭解產品圖----是否具備開模條件:脫模斜度,收縮變形,能否頂出.2.確認產品材質----塑膠材料種類繁多,確定材質以決定收縮率,瞭解流動性以決定注口及澆道設計.3.模具材質----根據不同之塑膠及產品要求,來正確選擇模具鋼,以便達到品質及模具壽命要求,這要求設計者對塑膠和鋼材有足夠瞭解.4.成型機規格----瞭解夾模壓力,注射容量,裝模高度,定位環尺寸,噴嘴半徑,托模孔位置.5.模穴及其排列----由產品的投影面積,形狀,精度,產量及效益來確定.各方面互相協調制約,多方面考慮來達到一最佳組合,並確定模胚和標準件.6.澆道方式----熱澆道,絕熱澆道,無澆道,直接進膠(二板模),間接進膠(三板模)及其他方式.7.澆口方式----種類繁多,因需求而異,須注意澆口是否有外觀要求及流動,平衡,結合線,排氣等問題,.澆口型號尺寸是否足以充滿整個產品.8.分模面----為模具設計重要環節,由設計師靈活運用,須考慮產品外觀,頂出方式,模具加工等9.模仁----須考慮外觀,加工方式,模具強度,脫模方式,冷卻方式,流動性,排氣等問題.10.側凹----有滑塊,油(氣)缸,馬達,斜梢,強行脫模及其他特殊方式,此部分變化最多,最復雜之設計.11.頂出----多種方式,頂針.扁梢.司筒.托板.滑塊.二段頂出.油(氣)壓.注意脫模平衡,模具強度,外觀,功能,冷卻效果.12.排氣----對保證產品品質至關重要,利用多種形式進行排氣,注意防止產品真空吸附及模具拉不開.13.冷卻----冷卻對模具生產影響很大,而設計工作較繁雜,既要考慮冷卻效果及冷卻一致性,又要考慮冷卻系統對模具整體結構的影響.14.加工方式----所有模具設計都須確實考慮模具加工可行性,才有實用價值.否則將脫離現場模具製造經驗而成為一次失敗的設計.15.模具圖----按上述構思進行繪製模具圖,含組立圖,零件圖及相關之加工用圖.在繪製過程中進一步完善模具各系統之間協調,以趨完美.16.校對審核----模具設計完成,必須協同客戶及相關人員進行校對審核,以對總體結構,加工可行性及繪圖過程中的疏漏作一全面檢查,徵求客戶意見,避免因設計失誤造成模具製造和使用困難,甚至報廢.模具加工常識一套設計再好的模具,如果在加工時不能達到設計要求,將嚴重影響整套模具之質量和壽命.這是現場模具師的責任,也是設計者必須瞭解的加工可行性重點.根據模具的難易程度,我們必須選擇不同的加工方法來達到加工效果,總體來說,可分為傳統加工和特殊加工:傳統加工銑削,車削,磨削,鑽削,氬焊,鉗工,一般熱處理等.特殊加工火花放電,線切割,CNC加工,化學腐蝕,雕刻,鐳射,特殊熱處理,表面處理電鑄電鍍壓鑄等.模具的加工過程,要靠加工者豐富的現場經驗和熟練的操作技巧及先進的設備來保證.它可以引深為另一門專業學科,對於我們設計者來說,不要求精通每一個加工過程和細節,但必須結合工廠實際,清楚每一種加工工序,充分瞭解加工可行性,才可在低成本下設計出符合要求之模具.避免因模具設計缺陷造成模具質量問題.模具設計規範表模具設計檢查表模具檢查表三, 試模與維護試模產品的品質與成型機性質,模具設計及加工成型條件有關,其中一項不當時, 便得不到良好的產品.以現有的成型機,預估成型條件,來設計模具.若不實際成型,也很難保證其效果好壞.通常是模具加工完成後,進行試模,以檢討產品外觀,尺寸,功能是否適合設計和使用要求.試模或產品中的不良原因,可能由模具本身或成型條件聯合引起所致,須充分檢討後再修改,一般情況下成型條件較易變更,故先調整成型條件,無法解決時再修正模具,模具設計人員應參加試模工作,以便發現問題及提出修改意見.1.試模前必須對成型機進行全面檢查,確保機台工作正常.2.確認原料正確,並正確加熱到注射溫度.3.開始試模時原則上先低壓,低溫和較長時間條件下成型,然後按壓力,時間,溫度這樣的順序變動.最好不要同時變動2個或3個工藝條件.以便分析判斷情況.4.可選用高速和低速兩種工藝,壁薄大面積宜用高速注射,壁厚小面積者宜用低速注射.優先採用低速成型,5.對於粘度高和熱穩定性差之塑膠,注意螺桿轉速及背壓,噴嘴溫度太低太高時採用每成型一模座後移之方式.以防斷澆道及流涎.試模過程中應作詳細記錄,填寫試模記錄卡,檢討模具問題點,提出還修意見,在樣品上作相應標示.以作修模參考.維護模具在生產過程中會產生磨損和不正常之損壞,而其中操作不當引起的模具故障占大多數,如夾模,碰傷,生銹,鑲嵌件未放好等.1.鑲柱或導柱碰彎.2.產品部分局部受傷,大部分還是好的.3.模具鋼材硬度太低,零件精度太差,使用一段時間後長毛邊,尺寸偏差.4.模具生產一段時間後,客戶提出工程變更,在原有基礎上作外觀和尺寸修改.在這種情況下,並不須要將整套模具報廢,只須局部修復既可,修模之前,必須充分研究模具圖紙,模具結構,材質,熱處理狀態及模具損傷原因,考慮各種修模方案,取最佳方案實施.最重要的是杜絕同樣的故障再次出現,切忌腳痛醫腳頭痛醫頭.。