sa非传统加工及特殊加工技术
特种加工

特种加工亦称“非传统加工”或“现代加工方法”,泛指用电能、热能、光能、电化学能、化学能、声能及特殊机械能等能量达到去除或增加材料的加工方法,从而实现材料被去除、变形、改变性能或被镀覆等。
与传统机械加工方法相比具有许多独到之处:(1)加工范围不受材料物理、机械性能的限制,[1]能加工任何硬的、软的、脆的、耐热或高熔点金属以及非金属材料。
(2)易于加工复杂型面、微细表面以及柔性零件。
(3)易获得良好的表面质量,热应力、残余应力、冷作硬化、热影响区等均比较小。
(4)各种加工方法易复合形成新工艺方法,便于推广应用。
特种加工技术的主要应用领域是:难加工材料,如钛合金、耐热不锈钢、高强钢、复合材料、工程陶瓷、金刚石、红宝石、硬化玻璃等高硬度、高韧性、高强度、高熔点材料。
难加工零件,如复杂零件三维型腔、型孔、群孔和窄缝等的加工。
低刚度零件,如薄壁零件、弹性元件等零件的加工。
以高能量密度束流实现焊接、切割、制孔、喷涂、表面改性、刻蚀和精细加工。
电加工技术原理电火花加工是利用浸在工作液中的两极间脉冲放电时产生的电蚀作用蚀除导电材料的特种加工方法,又称放电加工或电蚀加工电火花加工特点1:电火花加工速度与表面质量模具在电火花机加工一般会采用粗、中、精分档加工方式。
粗加工采用大功率、低损耗的实现,而中、精加工电极相对损耗大,但一般情况下中、精加工余量较少,因此电极损耗也极小,可以通过加工尺寸控制进行补偿,或在不影响精度要求时予以忽略。
2:电火花碳渣与排渣电火花机加工在产生碳渣和排除碳渣平衡的条件下才能顺利进行。
实际中往往以牺牲加工速度去排除碳渣,例如在中、精加工时采用高电压,大休止脉波等等。
另一个影响排除碳渣的原因是加工面形状复杂,使排屑路径不畅通。
唯有积极开创良好排除的条件,对症的采取一些方法来积极处理。
3:电火花工件与电极相互损耗电火花机放电脉波时间长,有利于降低电极损耗。
电火花机粗加工一般采用长放电脉波和大电流放电,加工速度快电极损耗小。
《特种加工技术》教案_

特种加工技术教案绪论1.1 特种加工的概念一、引入课题:特种加工产生的条件,之所以产生特种加工普通机械加工满足不了加工的要求。
一些难加工的材料、一些有特殊要求的零件、加工效率(生产率)、生产成本等等都需要特种加工。
比较普通加工与特种加工的区别来引入课题。
二、讲课内容1、特种加工的产生及定义随着社会生产的需要和科学技术的进步,20世纪40年代,前苏联科学家拉扎连柯夫妇研究开关触点遭受火花放电腐蚀损坏的现象和原因,发现电火花的瞬时高温可使局部的金属熔化、气化而被腐蚀掉,开创和发明了电火花加工。
后来,由于各种先进技术的不断应用,产生了多种有别于传统机械加工的新加工方法。
这些新加工方法从广义上定义为特种加工(NTM,Non-Traditional Machining),也被称为非传统加工技术,其加工原理是将电、热、光、声、化学等能量或其组合施加到工件被加工的部位上,从而实现材料去除。
©可播放特种加工的一些视频。
三、作业1.2 特种加工的特点及发展1.3 特种加工的分类一、复习旧课:特种加工产生的原因及定义。
二、引入新课:特种加工范围广但有一些共性。
与机械加工比起来有以下的一些特点。
三、讲课内容1、与传统的机械加工相比,特种加工的不同点是:(1) 不是主要依靠机械能,而是主要用其他能量(如电、化学、光、声、热等)去除金属材料。
(2) 加工过程中工具和工件之间不存在显著的机械切削力,故加工的难易与工件硬度无关。
(3) 各种加工方法可以任意复合、扬长避短,形成新的工艺方法,更突出其优越性,便于扩大应用范围。
正因为特种加工工艺具有上述特点,所以就总体而言,特种加工可以加工任何硬度、强度、韧性、脆性的金属或非金属材料,且专长于加工复杂、微细表面和低刚度的零件。
2、特种加工技术的研究主要表现在以下几个方面:(1) 微细化。
(2) 特种加工的应用领域正在拓宽。
(3) 广泛采用自动化技术。
3、我国特种加工技术的发展情况我国的特种加工技术起步较早。
特种加工技术

• 2. 超声波加工的特点和应用 • (1) 超声波加工主要适于加工各种硬脆材料,特别是不导
• 图是利用固体激光器加工的原理示意图。当激 光工作物质(如红宝石、钕玻璃和掺钕钇铝石 榴石等)受到光泵(即激励脉冲氙灯)的激发后, 吸收特定波长的光,在一定条件下可形成工作 物质中的亚稳态粒子数大于低能级粒子数的状 态,这种现象称为粒子数反转。此时,一旦有 少数激发粒子自发辐射发出光子,即可感应所 有其它激发粒子产生受激辐射跃迁,造成光放 大。并通过谐振腔的反馈作用产生振荡,由谐 振腔一端输出激光。通过透镜将激光束聚焦到 待加工表面上,即可对工件进行加工。
好、无残余应力和毛刺; • (5) 加工中阴极损耗小,一般可加工上千个零件; • (6) 因影响电解加工的因素很多,故难于实现高
精度的稳定加工。尺寸精度低于电火花加工,且 不易控制,一般型孔加工为:0.03~0.05mm,型 腔加工为0.05~0.2mm; • (7) 电解液对机床有腐蚀作用,设备费用高,电 解产物的处理和回收较困难,污染较严重。
砂带磨削
• 利用高速运转的环形砂带加工工件表面的 磨削。一般在砂带磨床上进行。 砂带围绕 在具有一定弹性的压轮和张紧轮上,由压 轮驱动回转作连续切削运动,工件放在传 送带或工作台上作进给运动。当工件接触 砂带或通过压轮下的磨削区时,即被砂带 磨去表面的一层材料
• 砂带磨削具有许多其它磨削加工方式所不 具备的优势:①磨削效率高达96%,是所 有磨削加工方式中最高的;②磨削比高(比 砂轮磨削高10倍以上);③可实现磨削、研 磨、抛光等多重加工效果,加工精度高,
机械加工方面的几种先进工艺

机械加工方面的几种先进工艺机械加工是制造业中重要的一环,随着技术的不断发展,机械加工也在不断创新和改进。
本文将介绍几种先进的机械加工工艺。
一、高速切削技术高速切削技术是近年来发展起来的一种机械加工技术,其特点是切削速度高、切削力小、切削温度低、切削精度高,可以大大提高加工效率和加工质量。
高速切削技术需要使用高速切削机床和高速切削刀具,以及精密的切削参数控制系统。
在高速切削技术中,切削速度可达到每分钟数万转,切削深度和进给量可以在毫米级别内控制。
二、数控加工技术数控加工技术是现代机械加工的主流技术之一,其特点是自动化程度高、加工精度高、加工效率高、加工质量稳定。
数控加工技术需要使用数控机床和数控编程软件,通过编写数控程序,将加工工艺参数输入到数控系统中,实现对工件的自动加工。
数控加工技术可以实现对复杂形状的工件进行高精度加工,广泛应用于航空、汽车、模具等领域。
三、激光加工技术激光加工技术是一种非接触式加工技术,其特点是加工速度快、加工精度高、切割面光滑、不产生切削应力。
激光加工技术需要使用激光切割机和激光加工控制系统,通过控制激光束的焦距和功率,实现对材料的切割、钻孔、雕刻等加工。
激光加工技术应用广泛,包括电子、半导体、医疗、航空等领域。
四、电火花加工技术电火花加工技术是一种将电能转化为热能来加工工件的非传统加工技术,其特点是加工精度高、加工表面质量好、不会产生机械应力和热应力。
电火花加工技术需要使用电火花加工机和电火花加工控制系统,通过控制电极和工件之间的间隙和放电参数,实现对工件的加工。
电火花加工技术广泛应用于精密模具、航空航天、汽车等领域。
五、超声波加工技术超声波加工技术是一种利用超声波振荡来加工材料的加工技术,其特点是加工效率高、加工精度高、加工表面质量好、不会产生热应力和机械应力。
超声波加工技术需要使用超声波振荡器和超声波加工控制系统,通过控制振荡器的频率和振幅,实现对材料的加工。
超声波加工技术应用广泛,包括电子、光学、医疗、航空等领域。
八大特种加工技术

非常工艺:八大特种加工技术特种加工亦称“非传统加工”或“现代加工方法”,泛指用电能、热能、光能、电化学能、化学能、声能及特殊机械能等能量达到去除或增加材料的加工方法,从而实现材料被去除、变形、改变性能或被镀覆等。
一、特种加工的发展和定义传统的机械加工已有很久的历史,它对人类的生产和物质文明起了极大的作用。
目前我们的大部分产品还是依靠传统的方法加工和装配得到的,如我们的家用电器:电冰箱、洗衣机、空调等;我们的交通工具:如汽车、火车、飞机等,以及各种武器装备:枪、炮、坦克、火箭等。
传统的机械加工方法是用机械能量和切削力切除多余的金属,使零件具有一定的几何形状、尺寸和表面粗糙度。
它要求刀具材料比工件材料硬。
随着科学技术的发展,特别是上个世纪50年代以来,随着生产发展和科学实验的需要,很多工业部门,尤其是国防工业部门的要求尖端科学技术产品向高精度、高速度、高温、高压、大功率、小型化等方向发展,它们使用的材料越来越难加工,零件的形状越来越复杂,尺寸精度、表面粗糙度和某些特殊要求也越来越高,因而对机械制造部门提出一些新的要求:•解决各种难切削材料的加工问题。
如硬质合金、钛合金、耐热钢、不锈钢、淬火钢、金刚石、宝玉石、石英以及锗、硅等各种高硬度、高强度、高韧性、高脆性的金属及非金属材料的加工。
•解决各种特殊复杂表面的加工问题。
如喷汽涡轮机叶片、整体涡轮、发动机机匣、锻压模和注射模的立体成型表面,各种冲模、冷拔模上特殊断面的型孔,炮管内膛线,喷油咀、栅网、喷丝头上的小孔、窄缝等的加工。
•解决各种超精、光整或具有特殊要求的零件的加工问题。
如对表面质量和精度要求很高的航天、航空陀螺仪、伺服阀,以及细长轴、薄壁零件、弹性元件等低刚度零件的加工。
要解决上述一系列工艺问题,仅仅依靠传统的切削加工方法就很难实现,甚至根本无法实现。
人们相继探索研究新的加工方法,特种加工就是在这种前提条件下产生和发展起来的。
特种加工,国外称作非传统加工(Non - Traditional Machining, NTM)或非常规加工(Non –ConventionalMachining,NCM),是一种采用不同于传统切削磨削加工工艺及装备的加工技术,是将电、磁、声、光、热等物理能量及化学能量或其组合乃至与机械能组合直接施加在被加工的部位上,从而使材料被去除、变形及改变性能等。
“机械制造技术基础”课程 学习指南

“机械制造技术基础”课程学习指南一、课程目的和要求学习并牢固掌握机械制造技术的基础知识、基本理论和基本方法。
通过课程学习及生产实习、课程设计等实践环节训练,培养分析和解决机械制造工程问题的基本能力,包括:1)制订机械加工工艺规程的初步能力;2)分析和解决现场工艺问题初步能力;3)机床夹具初步设计能力。
了解机械制造领域的最新成就和发展趋势。
二、课程特点实践性:机械制造技术本身是机械制造生产实践的总结和升华,反过来要接受实践的检验,并用以对生产活动进行指导和约束。
学习本课程应注意理论联系生产实际,在实践中学习、总结和提升,同时用理论指导实践。
综合性:机械制造是一门综合性很强的技术,涉及多种学科理论和方法。
现代机械制造技术与其他高技术互相依赖,共同发展。
学习本课程应注意联系和综合应用以往所学知识,注意应用其他学科理论和方法解决制造问题。
灵活性:机械制造技术应用于具体企业要充分考虑企业具体情况。
对于不同的生产条件和企业内、外部环境,所采用的制造方法和生产模式可能完全不同。
学习本课程重在理解和掌握机械制造技术的基本理论和方法,以及这些理论和方法的灵活应用。
三、建议学习方法课堂讲授:讲授重点、难点。
自学:课程内容15%~20%自学,通过作业、答疑保证效果。
课堂讨论与习题讲解:针对重点内容和疑难问题及作业中的共性问题,适当安排。
实践环节:作业、练习、(生产实习、课程设计)。
四、各章要点与学习指南1. 第1章机械制造技术概论本章要点:本章首先从大制造的概念出发,介绍关于生产、制造、制造技术、制造系统等基本概念,机械制造业的发展简况及其在国民经济中的地位,然后重点介绍与现代制造技术密切相关的制造哲理和生产模式,最后对机械制造方法从宏观上进行说明。
本章旨在使学习者建立一个系统的观点,并能从全局上把握住制造技术的基本问题。
学习本章内容,应深刻理解“大制造”概念的内涵和实质,正确认识“大制造”与“小制造”之间的关系,了解现代制造哲理,并学会用系统的观点和方法分析和解决机械制造中的实际问题。
特种加工课程教学大纲
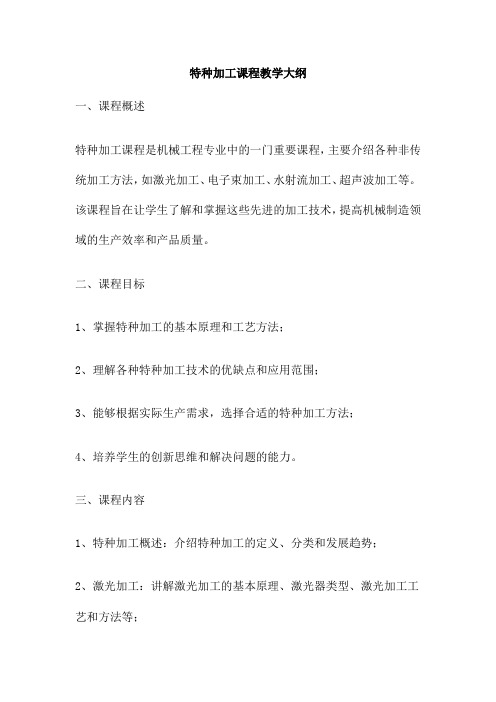
特种加工课程教学大纲一、课程概述特种加工课程是机械工程专业中的一门重要课程,主要介绍各种非传统加工方法,如激光加工、电子束加工、水射流加工、超声波加工等。
该课程旨在让学生了解和掌握这些先进的加工技术,提高机械制造领域的生产效率和产品质量。
二、课程目标1、掌握特种加工的基本原理和工艺方法;2、理解各种特种加工技术的优缺点和应用范围;3、能够根据实际生产需求,选择合适的特种加工方法;4、培养学生的创新思维和解决问题的能力。
三、课程内容1、特种加工概述:介绍特种加工的定义、分类和发展趋势;2、激光加工:讲解激光加工的基本原理、激光器类型、激光加工工艺和方法等;3、电子束加工:介绍电子束加工的基本原理、设备类型、工艺和方法等;4、水射流加工:讲解水射流加工的基本原理、设备类型、工艺和方法等;5、超声波加工:介绍超声波加工的基本原理、设备类型、工艺和方法等;6、其他特种加工方法:如离子束加工、电化学加工等。
四、教学方法1、理论教学:通过课堂讲解、图片、视频等方式,使学生了解特种加工的基本原理和工艺方法;2、实验教学:通过实验操作,让学生亲身体验各种特种加工方法,加深对理论知识的理解;3、项目实践:学生分组进行项目实践,运用所学知识解决实际问题,培养创新思维和解决问题的能力;4、案例分析:通过分析实际生产中的案例,让学生了解各种特种加工方法的应用和实际效果。
五、考核方式1、平时成绩:包括课堂表现、作业完成情况等;2、期中考试:考核学生对基本理论和方法的掌握程度;3、实验成绩:根据实验操作和实验报告评定;4、项目实践成绩:根据项目完成情况、报告撰写等评定;5、期末考试:综合考核学生对课程内容的理解和应用能力。
六、教学评估1、通过学生评教、教师评教等方式,对教学质量进行评估;2、通过考试成绩分析,评估学生的学习效果;3、通过项目实践报告评估,检验学生对所学知识的应用能力。
七、教学资源1、教材和参考书:选用优秀的教材和参考书,为学生提供充足的学习资源;2、网络资源:提供相关的网络链接和资料下载,方便学生自主学习;3、实验设备:提供先进的实验设备,满足学生的实验需求;4、项目实践场地:提供良好的实践环境,帮助学生完成项目实践。
特种加工技术

定义与概念
特种加工亦称“非传统加工”或“现代加工方法”,泛指用电 能、热能、光能、电化学能、化学能、声能及特殊机械能等能 量达到去除或增加材料的加工方法,从而实现材料被去除、变 形 、改变性能或被镀覆等。
特种加工技术是直接利用电能、热能、声能、光能、电化学能、 化学能及特殊机械能等多种能量或其复合能量以实现材料切除 的加工方法。其研究范围是电加工、高能束流(激光束、电子束、 离子束、高压水束)加工、超声波加工及多能源复合加工。
离子束加工技术
它是一种微细加工技术,成为航空电子设备和精密机载设备的 关键制造技术之一。它是应用离子蚀刻技术、离子溅射技术、 离子镀膜技术和离子注入技术完成精密零件的精密成形加工和 特殊表面层的制备。 离子束加工技术在航空电子设备和高精密机载设备的微细加工 和超精密加工中具有至关重要的作用,工业发达国家的航空工 业界高度重视此项技术的发展与应用。离子束加工技术主要发 展方向是实现计算机数控自动化、超精密化、经济与高效化。
特种技术的特点
加工范围不受材料物理 、机械性能的限制,能加工任何硬的、 软的、脆的、耐热或高熔点金属以及非金属材料。 易于加工复杂型面、微细表面以及柔性零件。 易获得 良好的表面质量,热应力、残余应力、冷作硬化、热影 响区等均比较小。 各域
特种加工技术在国际上被称为21世纪的技术 难加工材料,如钛合金、耐热不锈钢、高强钢、复合材料、工 程陶瓷、金刚石、红宝石、硬化玻璃等高硬度、高韧性、高强 度、高熔点材料。 难加工零件,如复杂零件三维型腔、型孔、群孔和窄缝等的加 工。 低刚度零件,如薄壁零件、弹性元件等零件的加工。 以高能量密度束流实现焊接、切割、制孔、喷涂、表面改性、 刻蚀和精细加工。
电加工技术
目前电解加工机床最大容量已达到5万安培,并已实现CNC控制 和多参数自适应控制。电火花加工气膜孔采用多通道、纳秒级 超高频脉冲电源和多电极同时加工的专用设备,加工效率2~3 秒/孔,表面粗糙度Ra0.4μm,通用高档电火花成型及线切割已 能提供微米级加工精度,可加工3μm的微细轴和5μm的孔。精 密脉冲电解技术已达10μm左右。电解与电火花复合加工,电 解磨削、电火花磨削已用于生产。
特种加工技术

特种加工技术特种加工亦称“非传统加工”或“现代加工方法”,泛指用电能、热能、光能、电化学能、化学能、声能及特殊机械能等能量达到去除或增加材料的加工方法,从而实现材料被去除、变形、改变性能或被镀覆等。
中文名特种加工外文名Special Machining 普及时间二十世纪四十年代目录一概述二发展三特点四运用领域五独到之处六加工工艺七加工技术1、电火花2、激光3、电子束4、离子束5、电加工6、超声波7、数控八发展方向一、概述:特种加工是指那些不属于传统加工工艺范畴的加工方法,它不同于使用刀具特种加工:特种加工、磨具等直接利用机械能切除多余材料的传统加工方法。
特种加工是近几十年发展起来的新工艺,是对传统加工工艺方法的重要补充与发展,目前仍在继续研究开发和改进。
直接利用电能、热能、声能、光能、化学能和电化学能,有时也结合机械能对工件进行的加工。
特种加工中以采用电能为主的电火花加工和电解加工应用较广,泛称电加工。
20世纪40年代发明的电火花加工开创了用软工具、不靠机械力来加工硬工件的方法。
50年代以后先后出现电子束加工、等离子弧加工和激光加工。
这些加工方法不用成型的工具,而是利用密度很高的能量束流进行加工。
对于高硬度材料和复杂形状、精密微细的特殊零件,特种加工有很大的适用性和发展潜力,在模具、量具、刀具、仪器仪表、飞机、航天器和微电子元器件等制造中得到越来越广泛的应用。
特种加工的发展方向主要是:提高加工精度和表面质量,提高生产率和自动化程度,发展几种方法联合使用的复合加工,发展纳米级的超精密加工等。
二、发展:特种加工是20世纪40年代发展起来的,由于材料科学、高新技术的发展和激烈的市场竞争、发展尖端国防及科学研究的急需,不仅新产品更新换代日益加快,而且产品要求具有很高的强度重量比和性能价格比,并正朝着高速度、高精度、高可靠性、耐腐蚀、高温高压、大功率、尺寸大小两极分化的方向发展。
为此,各种新材料、新结构、形状复杂的精密机械零件大量涌现,对机械制造业提出了一系列迫切需要解决的新问题。
特种加工

特种加工:特种加工亦称“非传统加工”或“现代加工方法”,泛指用电能、热能、光能、电化学能、化学能、声能及特殊机械能等能量达到去除或增加材料的加工方法,从而实现材料被去除、变形、改变性能或被镀覆等。
电火花加工:利用浸在工作液中的两极间脉冲放电时产生的电蚀作用蚀除导电材料的特种加工方法,又称放电加工或电蚀加工极性效应:电火花加工时,相同材料两电极的被腐蚀量是不同的。
其中一个电极比另一个电极的蚀除量大,这种现象叫做极性效应。
电火花线切割:在电火花加工的基础上发展的一种工艺,是用线状电极靠火花放电对工件进行切割,故称为电火花线切割。
极间介质消电离:极间介质的消电离在电火花放电加工过程中产生的电蚀产物如果来不及排除和扩散,那么产生的热量将不能及时传出,使该处介质局部过热,局部过热的工作液高温分解,结碳,使加工无法进行,并烧坏电极混气电解加工:是将具有一定压力的气体与电解液按一定比例混合在一起,然后将这种混合物加入到工件的加工间隙中去进行电解加工的一种方法。
P101电化学加工:利用电化学反应(或称电化学腐蚀)对金属材料进行加工的方法。
阳极溶解:阳极被氧化而溶解的现象p4阴极沉淀:p4 电极极化:p83电化学钝化:在金属表面形成一层薄的氧化物层,使金属腐蚀速率大大降低的过程。
电解加工:是利用金属在电解液中的电化学阳极溶解,将工件加工成型的。
电解抛光:是利用金属在电解液中的电化学阳极溶解对工件表面进行腐蚀抛光的,他只是一种表面光整得加工方法,用于降低工件的表面粗糙度和改善表面物理力学性能,而不用于对工件进行形状和尺寸加工。
P109电解磨削:电解加工与机械磨削相结合的特种加工。
P111电铸加工:利用金属的电解沉积原理来精确复制某些复杂或特殊形状工件的特种加工方法。
P120涂镀加工:在金属工件表面局部快速电化学沉积金属的技术。
P123激光加工:是利用光的能量,经过透镜聚焦,在焦点上达到很高的能量密度,靠光热效应来加工各种材料。
特种加工技术 习题集 附答案

补充资料《特种加工技术》习题集0总论1.特种加工在国外也叫做“非传统加工技术”,其“特”在何处?2.试述特种加工技术与传统加工技术的并存关系,并说明特种加工技术对现代制造业存在的必然性和影响。
3.人们常言“打破传统,锐意创新”,特种加工技术的产生和发展对于科研和工程技术人员从事发明创新工作有何启迪?试举例说明生产、生活中还有哪些可以变害为利产生发明和创新的例子?第1章电火花成形加工(EDM SINKING)一、简答题4.试述电火花加工的工作原理及工艺特点。
5.电火花加工机床有哪些附件?其各自的用途如何?6.电火花工作液有哪些供液方式?各自的优缺点如何?7.常用的电火花工具电极材料有哪些?8.电火花磨削与传统机械磨削有何差异?9.试述电火花铣削的工作原理、特点及工艺实施形式。
10.“反拷法”是何含义?其应用场合如何?11.“群电极”是什么含义?如何制备?应用于何种场合?12.简述共轭回转电火花加工的工作原理及特点。
13.超大深径比的深小孔加工的难点何在?对策如何?二、选择题1.电火花深小孔加工应当选择以下作为工作液;A.自来水;B.煤油;C.去离子水(工业纯水) ;D.乳化液2.电火花共轭回转加工的最早发明人是:A.中国人;B.美国人C.俄国人D.德国人3. 欲将小型交叉孔口毛刺去除彻底干净,最好采用加工方法来完成。
A.锉刀;B.砂带磨削C.砂轮磨削D.电火花工艺4.欲保证最高的加工精度,电火花加工中工作液供给方式最好采用。
A.静态淹没工件;B.侧面冲液C.工具电极内部抽吸D.工具电极内部射出5.对于象筛网零件有成千上万个小孔需要加工,为保证生产率,电火花加工宜采用以下工具电极.A.单个实心电极逐个加工;B.单个空心电极逐个加工C. 实心群电极D.空心管群电极三、判断题1.电火花加工中的吸附效应都发生在正极上。
(F )2.电火花成型加工时,电极在长度方向上损耗后无法得到补偿,需要更换电极。
(F)3.电火花成型加工中的自动进给调节系统应保证工具电极的进给速度等于工件的蚀除速度;(T)4.电火花成型加工和穿孔加工相比,前者要求电规准的调节范围相对较小。
特种加工技术

特种加工技术的发展及其应用特种加工是指那些不属于传统加工工艺范畴的加工方法,它不同于使用刀具、磨具等直接利用机械能切除多余材料的传统加工方法。
特种加工是近几十年发展起来的新工艺,是对传统加工工艺方法的重要补充与发展,目前仍在继续研究开发和改进。
直接利用电能、热能、声能、光能、化学能和电化学能,有时也结合机械能对工件进行的加工。
特种加工中以采用电能为主的电火花加工和电解加工应用较广,泛称电加工。
特种加工亦称“非传统加工”或“现代加工方法”,泛指用电能、热能、光能、电化学能、化学能、声能及特殊机械能等能量达到去除或增加材料的加工方法,从而实现材料被去除、变形、改变性能或被镀覆等。
20世纪40年代发明的电火花加工开创了用软工具、不靠机械力来加工硬工件的方法。
50年代以后先后出现电子束加工、等离子弧加工和激光加工。
这些加工方法不用成型的工具,而是利用密度很高的能量束流进行加工。
对于高硬度材料和复杂形状、精密微细的特殊零件,特种加工有很大的适用性和发展潜力,在模具、量具、刀具、仪器仪表、飞机、航天器和微电子元器件等制造中得到越来越广泛的应用。
特种加工技术的特点加工范围上不受材料强度、硬度等限制。
特种加工技术主要不依靠机械力和机械能去除材料,而是主要用其他能量(如电、化学、光、声、热等)去除金属和非金属材料,完成工件的加工。
故可以加工各种超强硬材料、高脆性及热敏材料以及特殊的金属和非金属材料。
以柔克刚。
特种加工不一定需要工具,有的虽使用工具,但与工件并不接触,加工过程中工具和工件间不存在明显的强大机械切削力,所以加工时不受工件的强度和硬度的制约,在加工超硬脆材料和精密微细零件、薄壁元件、弹性元件时,工具硬度可以低于被加工材料的硬度。
加工方法日新月异,向精密加工方向发展。
当前已出现了精密特种加工,许多特种加工方法同时又是精密加工方法、微细加工方法,如电子束加工、离子束加工、激光束加工等就是精密特种加工;精密电火花加工的加工精密度可达微米级0.51μm,表面粗糙度可达镜面 Ra0.02μm。
特种加工技术的定义
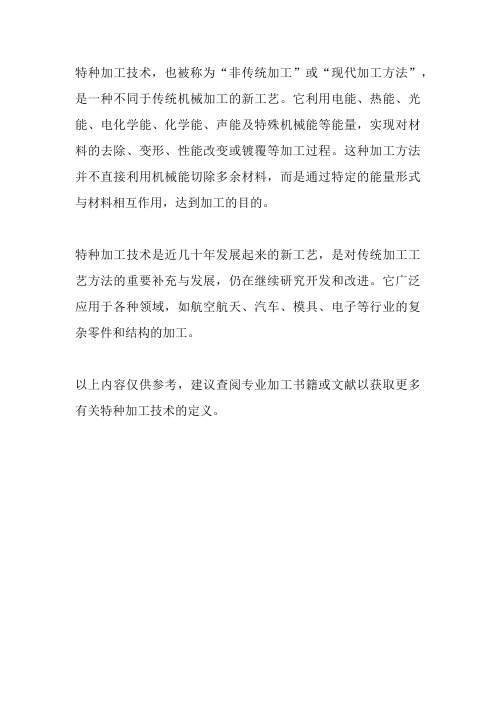
特种加工技术,也被称为“非传统加工”或“现代加工方法”,是一种不同于传统机械加工的新工艺。
它利用电能、热能、光能、电化学能、化学能、声能及特殊机械能等能量,实现对材料的去除、变形、性能改变或镀覆等加工过程。
这种加工方法并不直接利用机械能切除多余材料,而是通过特定的能量形式与材料相互作用,达到加工的目的。
特种加工技术是近几十年发展起来的新工艺,是对传统加工工艺方法的重要补充与发展,仍在继续研究开发和改进。
它广泛应用于各种领域,如航空航天、汽车、模具、电子等行业的复杂零件和结构的加工。
以上内容仅供参考,建议查阅专业加工书籍或文献以获取更多有关特种加工技术的定义。
精密加工和特种加工简介

生产率较低。 (3) 生产率较低。 研磨零件的材料广泛。 (4)研磨零件的材料广泛。
可研磨加工钢件、铸铁件、 可研磨加工钢件、铸铁件、铜、铝等有色金属件和高硬度的淬火钢件、 钢件 铝等有色金属件和高硬度的淬火钢件、 硬质合金及半导体元件、陶瓷元件等 硬质合金及半导体元件、陶瓷元件等。
应用: 应用:
应用: 应用:
珩磨主要用于孔的精整加工,加工范围很广, 加工直径为5mm~ 珩磨主要用于孔的精整加工,加工范围很广,能加工直径为5mm~500mm 或更 孔的精整加工 5mm 大的孔,并且能加工深孔 珩磨还可以加工外圆 平面、球面和齿面等 加工深孔。 加工外圆、 大的孔,并且能加工深孔。珩磨还可以加工外圆、平面、球面和齿面等。
(二)珩磨
珩磨是利用带有磨条(由几条粒度很细的磨条组成) 珩磨是利用带有磨条(由几条粒度很细的磨条组成)的珩磨 是利用带有磨条 对孔进行精整加工的方法 的方法。 头对孔进行精整加工的方法。
1、珩磨精度和表面粗糙度
公差等级IT7~ 以上,表面粗糙度可达 0.1μm~0.008μm。 公差等级IT7~IT5 以上,表面粗糙度可达Ra为0.1μm~0.008μm。 IT7
(四)抛光
抛光是在高速旋转的抛光轮上涂以抛光膏, 抛光是在高速旋转的抛光轮上涂以抛光膏,对零件表面进 是在高速旋转的抛光轮上涂以抛光膏 行光整加工的方法。 行光整加工的方法。
抛光轮一般是用毛毡、橡胶、皮革、棉制品或压制纸板等材料叠制而成, 抛光轮一般是用毛毡、橡胶、皮革、棉制品或压制纸板等材料叠制而成, 一般是用毛毡 是具有一定弹性的软轮。 是具有一定弹性的软轮 抛光膏由磨料(氧化铬、氧化铁等)和油酸、软脂等配制而成。 抛光膏由磨料(氧化铬、氧化铁等)和油酸、软脂等配制而成。 由磨料
非传统加工方法讲解课件

水射流加工
水射流原理
水射流加工是利用高压水流对材料进行冲击和磨削的过程 。通过将水加压到非常高的水平,可以产生高速水流,从 而实现材料的切割、磨削和抛光等操作。
应用领域
水射流加工广泛应用于各种行业,如石油、采矿、建筑、 机械制造等。它可以用于切割各种硬脆材料,还可以用于 清除积垢和除锈等。
优点与局限
非传统加工方法讲解课件
目录
• 非传统加工方法概述 • 非传统加工方法分类 • 非传统加工方法原理与技术特点 • 非传统加工方法应用案例
01
非传统加工方法概述
定义与特点
定义
非传统加工方法是指区别于传统 机械加工方法的新型加工技术, 如激光加工、等离子加工、超声 波加工等。
特点
高效、高精度、非接触式、环保 等。
水射流加工应用案例
总结词
高效、低成本、环保
详细描述
水射流加工是利用高压水流的冲击力,使工 件表面材料局部剥离或破碎,从而达到加工 目的的一种方法。它具有高效、低成本、环 保等优点,广泛应用于切割、清洗、磨削等 领域。
THANK YOU
感谢各位观看
与传统加工方法的区别
技术原理
加工效果
传统加工方法主要依靠机械能,而非 传统加工方法则利用光、热、声、电 等物理或化学能量。
非传统加工方法可以实现高精度、微 细加工,而传统加工方法的精度和加 工范围相对有限。
应用范围
非传统加工方法适用于复杂形状、高 硬度、高韧性材料的加工,而传统加 工方法在某些情况下可能受到限制。
在加工效率相对较低等局限。
电火花加工
电火花原理
电火花加工是一种利用电火花腐 蚀材料的过程。通过工具和工件 之间的脉冲放电,将工件表面材
大学机械基础试题及答案

大学机械基础试题及答案一、选择题(每题2分,共20分)1. 机械设计中,通常采用哪种方法来提高零件的疲劳强度?A. 增加材料的硬度B. 增加零件的尺寸C. 改善零件的表面质量D. 增加零件的重量答案:C2. 以下哪种材料不属于金属材料?A. 钢B. 铝C. 塑料D. 铜答案:C3. 在机械传动中,哪种传动方式的效率最高?A. 皮带传动B. 齿轮传动C. 链传动D. 蜗杆传动答案:B4. 以下哪种加工方式属于非传统加工?A. 车削B. 铣削C. 激光加工D. 磨削答案:C5. 机械加工中,用于测量工件直径的量具是:A. 卡尺B. 千分尺C. 百分表D. 塞尺答案:B6. 以下哪种材料最适合用于制造轴承?A. 铸铁B. 铜合金C. 钢D. 塑料答案:C7. 机械设计中,为了减少振动和噪音,通常采用哪种方法?A. 增加零件的重量B. 增加零件的刚度C. 增加零件的阻尼D. 减少零件的尺寸答案:C8. 以下哪种润滑方式适用于高速旋转的轴承?A. 油浴润滑B. 油环润滑C. 油雾润滑D. 油脂润滑答案:C9. 机械加工中,用于测量工件长度的量具是:A. 游标卡尺B. 千分尺C. 百分表D. 塞尺答案:A10. 以下哪种材料最适合用于制造齿轮?A. 铸铁B. 铜合金C. 钢D. 塑料答案:C二、填空题(每空1分,共20分)1. 机械设计中,_________是影响零件疲劳强度的重要因素之一。
答案:表面质量2. 金属材料的硬度可以通过_________来测定。
答案:硬度计3. 在机械传动中,_________传动具有自锁功能。
答案:蜗杆4. 非传统加工技术包括_________、电火花加工等。
答案:激光加工5. 机械加工中,_________用于测量工件的外径。
答案:千分尺6. 轴承材料的选择需要考虑_________、耐磨性和抗疲劳性。
答案:承载能力7. 为了减少机械振动,可以采用_________来吸收振动能量。
机械制造与自动化课程

机械制造与自动化课程一、机械制造与自动化课程简介机械制造与自动化课程是机械工程专业的核心课程之一,旨在培养学生掌握机械制造和自动化技术的基本理论、知识和技能,以及具备设计、制造、调试和维护各种机械设备的能力。
本课程涵盖了机械加工、数控技术、自动化控制等方面的内容,是培养高素质机械工程人才的重要课程之一。
二、机械加工1. 传统加工技术传统加工技术包括车削、铣削、钻孔等,是最基础也是最常用的加工方法。
学生需要学习各种切削刀具的使用方法,了解不同材料对切削刃口磨损和断裂的影响,并掌握如何选择合适的切削参数。
2. 非传统加工技术非传统加工技术包括电火花加工、激光切割等,这些方法可以加工出形状复杂或硬度高的零件。
学生需要了解各种非传统加工方法的原理、特点和应用范围,并能够根据零件的要求选择合适的加工方法。
三、数控技术1. 数控机床数控机床是利用计算机控制系统来实现自动化加工的设备,具有高精度、高效率等优点。
学生需要了解数控机床的组成、工作原理和编程方法,以及如何进行数控加工。
2. CAD/CAM技术CAD/CAM技术是将计算机辅助设计和计算机辅助制造相结合,实现数字化设计和加工的一种技术。
学生需要学习CAD/CAM软件的使用方法,能够进行零件三维建模、刀具路径规划等操作,并能够生成G 代码进行数控加工。
四、自动化控制1. 传感器技术传感器是自动化控制系统中最基础也最重要的部件之一,可以将物理量转换为电信号,并通过电路传输到控制器中。
学生需要了解各种传感器类型、特点和应用范围,并能够选择合适的传感器进行测量。
2. PLC编程PLC(可编程逻辑控制器)是一种专门用于自动化控制的计算机设备,可以实现逻辑控制、运动控制、数据处理等功能。
学生需要了解PLC 的组成、工作原理和编程方法,能够进行简单的PLC编程和调试。
五、机械制造与自动化课程实践机械制造与自动化课程中实践环节非常重要,可以帮助学生巩固理论知识、提高技能水平。
特种加工和线切割
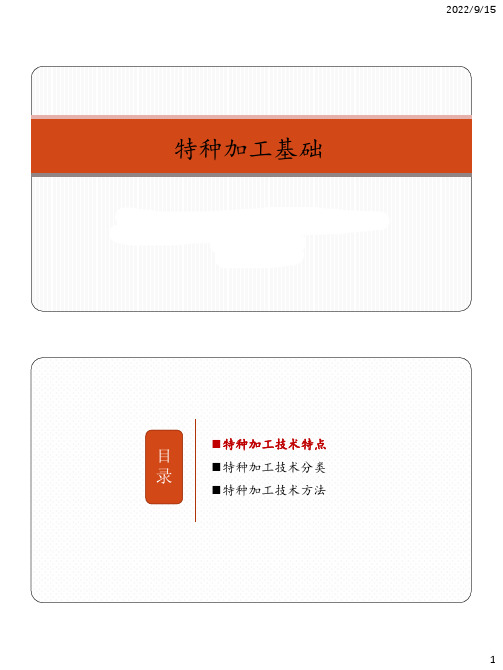
特种加工基础北京航空航天大学工程训练中心陈娇娇目录◼特种加工技术特点◼特种加工技术分类◼特种加工技术方法一、特种加工技术特点随着科学技术的发展,新型材料层出不穷,各种产品逐渐向高精度、高速度、高温、高压、大功率、小型化等方向发展,由此对机械加工提出了新的要求,从而产生了不是主要依靠机械能,而是利用光、电、化学等非机械能进行加工的方法。
特种加工非传统加工非常规机械加工3一、特种加工技术特点1.特种加工的产生生产的发展和科技的进步,对机械制造部门提出了新的要求:1)解决各种难切削材料的加工问题硬质合金、钛合金、耐热钢、不锈钢、淬火钢、金刚石等高硬度、高强度、高韧性、高脆性2)解决各种特殊复杂表面的加工问题3)解决各种超精、光整或具有特殊要求的零件的加工问题4一、特种加工技术特点2.特种加工的特点特种加工产生和发展的原因,在于它具有切削加工所不具有的本质和特点。
切削加工的本质和特点:一是靠刀具材料比工件更硬;二是靠机械能把工件上多余的材料切除。
与切削加工的不同点如下:1)不是主要依靠机械能,而是主要用其他能量(如电、化学、光、声、热等)去除材料。
2)工具硬度可以低于被加工材料的硬度。
3)加工过程中工具和工件之间不存在显著的机械切削力。
可获得很低的表面粗糙度。
5一、特种加工技术特点3.特种加工对机械制造的影响特种加工可以加工任何硬度、强度、韧性、脆性的金属或非金属材料,且专长于加工复杂、微细表面和低刚度零件。
同时,有些方法还可用以进行超精加工、镜面光整加工和纳米级加工。
1)提高了材料的可加工性材料的可加工性不再与硬度、强度、韧性、脆性等成直接、正比关系;加工范围从普通材料发展到硬质合金、超硬材料和特殊材料。
2)改变了零件的典型工艺路线通常切削加工、成型加工等都必须安排在淬火热处理工序之前。
特种加工的出现,改变了这种一成不变的程序格式。
6一、特种加工技术特点3)特种加工改变了试制新产品的模式。
如采用数控电火花线切割,可以直接加工出各种特殊、复杂的二次曲面体零件。
中国造船整体与世界先进水平有较大差距
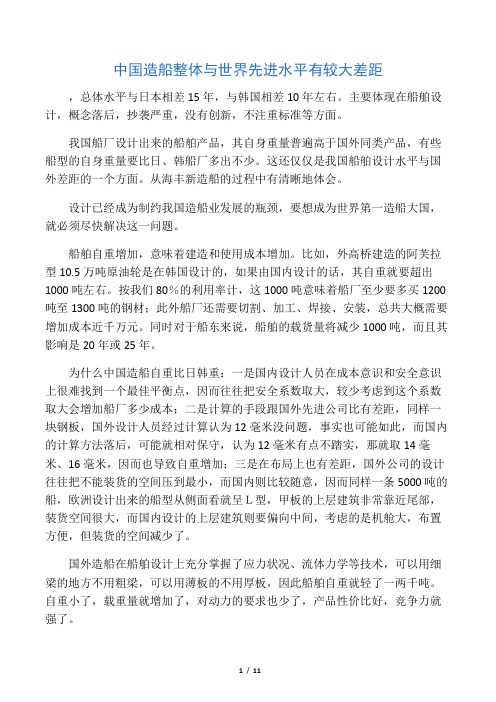
中国造船整体与世界先进水平有较大差距,总体水平与日本相差15年,与韩国相差10年左右。
主要体现在船舶设计,概念落后,抄袭严重,没有创新,不注重标准等方面。
我国船厂设计出来的船舶产品,其自身重量普遍高于国外同类产品,有些船型的自身重量要比日、韩船厂多出不少。
这还仅仅是我国船舶设计水平与国外差距的一个方面。
从海丰新造船的过程中有清晰地体会。
设计已经成为制约我国造船业发展的瓶颈,要想成为世界第一造船大国,就必须尽快解决这一问题。
船舶自重增加,意味着建造和使用成本增加。
比如,外高桥建造的阿芙拉型10.5万吨原油轮是在韩国设计的,如果由国内设计的话,其自重就要超出1000吨左右。
按我们80%的利用率计,这1000吨意味着船厂至少要多买1200吨至1300吨的钢材;此外船厂还需要切割、加工、焊接、安装,总共大概需要增加成本近千万元。
同时对于船东来说,船舶的载货量将减少1000吨,而且其影响是20年或25年。
为什么中国造船自重比日韩重:一是国内设计人员在成本意识和安全意识上很难找到一个最佳平衡点,因而往往把安全系数取大,较少考虑到这个系数取大会增加船厂多少成本;二是计算的手段跟国外先进公司比有差距,同样一块钢板,国外设计人员经过计算认为12毫米没问题,事实也可能如此,而国内的计算方法落后,可能就相对保守,认为12毫米有点不踏实,那就取14毫米、16毫米,因而也导致自重增加;三是在布局上也有差距,国外公司的设计往往把不能装货的空间压到最小,而国内则比较随意,因而同样一条5000吨的船,欧洲设计出来的船型从侧面看就呈L型,甲板的上层建筑非常靠近尾部,装货空间很大,而国内设计的上层建筑则要偏向中间,考虑的是机舱大,布置方便,但装货的空间减少了。
国外造船在船舶设计上充分掌握了应力状况、流体力学等技术,可以用细梁的地方不用粗梁,可以用薄板的不用厚板,因此船舶自重就轻了一两千吨。
自重小了,载重量就增加了,对动力的要求也少了,产品性价比好,竞争力就强了。
- 1、下载文档前请自行甄别文档内容的完整性,平台不提供额外的编辑、内容补充、找答案等附加服务。
- 2、"仅部分预览"的文档,不可在线预览部分如存在完整性等问题,可反馈申请退款(可完整预览的文档不适用该条件!)。
- 3、如文档侵犯您的权益,请联系客服反馈,我们会尽快为您处理(人工客服工作时间:9:00-18:30)。
放電原理
單發放電狀況
電鍍之定義
電鍍(electroplating)被定義為一種電沈積過程 (electrodepos- ition process), 是利用電極 (electrode)通過電流,使金屬附著於 物體表面 上, 其目的是在改變物體表面之特性或尺寸。
電鍍之目的 :
在基材上鍍上金屬鍍層(deposit),改變基材表面 性質或尺寸。
電鍍的基本知識 :
電鍍大部份在液體 (solution) 下進行,又絕大部 份是由水溶 液 (aqueous solution)中電鍍,約有 30 種的金屬可由水溶液進行電鍍
鍍金的方法 :
電鍍法(electroplating) 無電鍍法(electroless plating) 熱浸法(hot dip plating) 熔射噴鍍法(spray plating) 塑膠電鍍(plastic plating) 浸漬電鍍(immersion plating) 滲透鍍金(diffusion plating) 陰極濺鍍(cathode supptering) 真空蒸著鍍金(vacuum plating) 合金電鍍 (alloy plating) 複合電鍍 (composite plating 局部電鍍 (selective plating) 穿孔電鍍 (through-hole plating) 筆電鍍(pen plating) 電鑄 (electroforming)
非傳統加工及特殊加工技術
何昱廷94114208 張耀之94114218 胡澤群94114229 李冠毅94114253
林緯彬94114222 胡育文94114225 江家興94114249
雷射加工的原理
雷射加工(Laser Beam Machining, 簡稱 LBM)
是以種高熱的加工法,被加工之工件材料一部 分是在液態下以高速除去,但主要是由於高熱 直截揮發成汽態離開工件。加工法是激發紅寶 石中鉻離子放出能量,加強加速光束。
(一)電子束切削:
利用前述原理產生的電子束,若以高速度地撞擊工件,可將 動能轉為熱能,藉著高熱能強度(即能量高度聚集),即有足 夠的熱能來揮發局部的工件材料,達到切削目的。
優點: 1. 精度高,適合需要高精度 的細微切削。 2. 電子束甚集中 (直徑 0.0012mn),工件上的熱影 響區域或壓力幾乎難以發現, 可得很精確的公差。
超音波加工Fra bibliotek超音波是一種頻率超過可聽到聲音的振動波,視其應用而可分為超音 波切削、超音波熔接與超音波檢驗等主要用途。超音波的產生是利用 一種介質,如石英晶體等,將電氣信號轉變為一種高頻振動波而得者。 優點計有:
1.沒有熱應力存在。
2.低工具模造成本。 3.可僱用較低技術工人從事高技術性的精密加工。 4.可穿出治夾具中的非圓孔或任何形狀的內孔。
缺點: 1.設備成本高。 2.須熟練的技術。 3.須在真空中操作,工件大 小較受限制。
(二)熔接:
亦是利用密集且高速的電子束撞擊工件而得局 部高熱能,以熔接工件者。 熔接方式可利用溶化工件的對接或穿透工件而 達到熔接效果,一般都需要填充金屬。 由於加入熔接點的熱量遠大於其發散量,故可 以得到相當大的深度/寬度比值。 不但可用於熔接普通金屬,尚可用於耐高溫、 易氧化的金屬,以及不易熔接之合金 如鋁合 金等。
電子束加工
電子束是其物體受激振後所產生的眾多電子, 若利用導引或約束裝置將其集結成束後,然後 高速撞擊於工件上,將其動能轉換為熱能,即 可進行切削或熔接,然而若是將電子撞擊到工 件材料後,依工件材料受激發出來的二次電子 或波長等特徵,即可進行檢驗工件。 以執行所須的操作---如切削、熔接或檢驗。
(3) 加工液急速氣化膨脹因而對熔融 的工件及電極產生壓力的作用。這種 液體氣化的壓力是放電加工過程中不 可缺少的。若以巨觀來看放電壓是非 常的小,若以單位面積來考慮的話, 加工液的氣化膨脹壓力不可忽視。
(4) 熔融的金屬飛散於加工 液中形成加工屑。
(5) 加工液中流入放電間隙 中將殘餘的熱量帶走,並恢 復絕緣狀態。
基本的放電原理及理論
(1) 電極與工件之間距小到數 微米(μm)的距離時,首先距 離最短的地方,產生火花放電, 此時電流密度極高的電子流, 衝擊被加工物,由於電子流急 速衝擊,被加工物急劇受到熱 的作用到達熔點。同時陽離子 流向陰極,電極(工具)也同 時被加熱。
(2) 由於放電電壓及熱的作用,放電 點周圍的加工液急速氣化。
利用雷射來加工的項目包括︰
切割、雕刻、打洞、焊接、鑽孔、模板修補、 標記、表面處理等,使用的雷射則分氣體雷射 及固體雷射兩種。氣體雷射以二氧化碳為主, 固體雷射則以加工用的YAG雷射為代表。
非傳統加工(Nontraditional Machining )
指傳統車、鉗、銑、鉋、磨等加工以外,新的 機械加工方法之總稱,主要是指不直接利用機 械能,而利用電能、熱能、光能、聲能、化學 能等,其他能量來對工件進行尺寸、形狀變更 或表面處理加工的方法。除了這些單獨的加工 方法使用外,亦可結合兩種或多種加工方法的 應用而得到複合加工方法,來達到截長補短之 功效。
放電加工
放電加工原理簡單而言是利用電能轉換成工件熱 能,使工件急速融熔的一種熱性加工方法。換言 之,放電加工時,液中在電極與工作極微細的間 隙中產生過渡電弧放電現象,進而對工件產生熱 作用,同時,加工中液體由於受到放電壓力及熱 作用產生氣化爆發現象,此時工件的融熔部份, 將伴隨液體氣化現象熔入加工液中,工件因放電 的作用產生放電痕,如此反覆進行,我們所希望 的形狀便可加工完成
(三)檢驗:
例如電子顯微鏡即是利用前述的電子束產生裝 置,經導引並撞擊到待測工件後,檢測其受激 發而產生的二次電子、x射線,以及其他可用 以判定其特性的射線或電子、中子等等,由於 每種元素的二次電子等等,都具有不同的特性, 因之,可由檢測到的二次電子等,而判定待測 工件中所含的元素以及其表面特性等有關性質。