欧姆龙PLC系统在昆钢高线PF线的应用
探究 PLC 系统在轧钢生产线自动控制中的应用
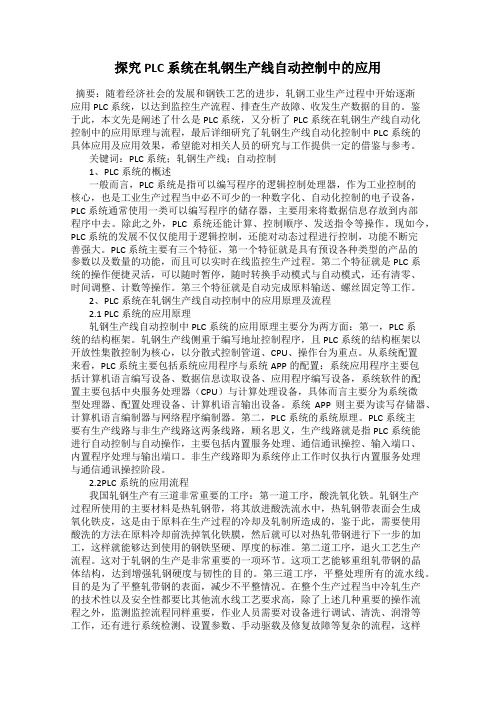
探究 PLC 系统在轧钢生产线自动控制中的应用摘要:随着经济社会的发展和钢铁工艺的进步,轧钢工业生产过程中开始逐渐应用PLC系统,以达到监控生产流程、排查生产故障、收发生产数据的目的。
鉴于此,本文先是阐述了什么是PLC系统,又分析了PLC系统在轧钢生产线自动化控制中的应用原理与流程,最后详细研究了轧钢生产线自动化控制中PLC系统的具体应用及应用效果,希望能对相关人员的研究与工作提供一定的借鉴与参考。
关键词:PLC系统;轧钢生产线;自动控制1、PLC系统的概述一般而言,PLC系统是指可以编写程序的逻辑控制处理器,作为工业控制的核心,也是工业生产过程当中必不可少的一种数字化、自动化控制的电子设备,PLC系统通常使用一类可以编写程序的储存器,主要用来将数据信息存放到内部程序中去。
除此之外,PLC系统还能计算、控制顺序、发送指令等操作。
现如今,PLC系统的发展不仅仅能用于逻辑控制,还能对动态过程进行控制,功能不断完善强大。
PLC系统主要有三个特征,第一个特征就是具有预设各种类型的产品的参数以及数量的功能,而且可以实时在线监控生产过程。
第二个特征就是PLC系统的操作便捷灵活,可以随时暂停,随时转换手动模式与自动模式,还有清零、时间调整、计数等操作。
第三个特征就是自动完成原料输送、螺丝固定等工作。
2、PLC系统在轧钢生产线自动控制中的应用原理及流程2.1 PLC系统的应用原理轧钢生产线自动控制中PLC系统的应用原理主要分为两方面:第一,PLC系统的结构框架。
轧钢生产线侧重于编写地址控制程序,且PLC系统的结构框架以开放性集散控制为核心,以分散式控制管道、CPU、操作台为重点。
从系统配置来看,PLC系统主要包括系统应用程序与系统APP的配置:系统应用程序主要包括计算机语言编写设备、数据信息读取设备、应用程序编写设备,系统软件的配置主要包括中央服务处理器(CPU)与计算处理设备,具体而言主要分为系统微型处理器、配置处理设备、计算机语言输出设备。
PLC在钢铁冶金企业电气自动化控制中的应用

PLC在钢铁冶金企业电气自动化控制中的应用钢铁冶金企业是一个电力、机械和自动化密集度较高的行业,而PLC(Programmable Logic Controller,可编程逻辑控制器)在这个行业的电气自动化控制中扮演着非常重要的角色。
下面将详细介绍PLC在钢铁冶金企业电气自动化控制中的应用。
PLC在钢铁冶金企业中常用于控制和监测生产线的运行。
通过PLC,可以实现对生产线各个设备的控制和监测,例如炼铁炉、炼钢炉、连铸机等设备的开启、停止、自动控温、速度控制等。
PLC可以根据工艺流程的要求,编写相应的控制程序,确保生产线能够按照需要进行工作,同时实现对各个设备运行状态的监测和报警功能,确保生产的安全和稳定。
PLC还可以用于实现钢铁冶金企业的数据采集和远程监控。
通过与传感器和仪表的连接,PLC可以采集各种生产过程中的数据,如温度、压力、流量等参数。
这些数据可以实时传输到上位机,进行数据分析和处理,为企业的生产决策提供依据。
通过PLC可以实现对生产过程的远程监控,监测设备的运行状态,及时调整和处理异常情况,提高生产的效率和质量。
PLC还可以用于实现钢铁冶金企业的能源管理和节能控制。
钢铁冶金企业消耗的能源较大,节能成为企业的重要任务。
通过PLC,可以对各个设备进行能源消耗的监测和控制,实现能源的优化配置和节约利用。
通过对生产过程的监测和数据分析,可以找出能源消耗较大的环节,进行合理调整和控制,降低能源消耗,并且可以实现对能源的实时监测和统计,为企业的能源管理提供支持。
PLC还可以用于实现钢铁冶金企业的安全控制和报警。
钢铁冶金企业往往存在一些危险环境,如高温、高压、有毒气体等,对工人的安全有较大的威胁。
通过PLC,可以实现对这些危险环境的监测和控制,当危险情况发生时,PLC可以自动发出报警信号,并采取相应的安全措施,确保工人的安全。
PLC在钢铁冶金企业电气自动化控制中具有非常重要的应用价值。
它可以用于控制和监测生产线的运行、实现数据采集和远程监控、实现能源管理和节能控制、以及实现安全控制和报警等功能,提高企业的生产效率和质量,降低能源消耗,保障工人的安全,对钢铁冶金企业的发展具有重要意义。
PLC在钢铁冶金企业电气自动化控制中的应用

PLC在钢铁冶金企业电气自动化控制中的应用PLC是一种专门用于工业控制系统的电子设备,它采用可编程的逻辑控制器,能够根据预设的程序自动执行各种控制操作。
在钢铁冶金生产过程中,PLC可以实现自动化控制的各种功能,包括物料输送、温度控制、测量与检测、安全保护和故障诊断等。
下面就针对这些功能来具体分析PLC在钢铁冶金企业中的应用。
PLC在钢铁冶金企业中的物料输送控制方面发挥着重要作用。
在钢铁冶金生产过程中,原材料、中间产品和成品需要通过输送设备进行运输。
PLC可以通过对输送设备的控制,实现物料的自动化输送,提高生产效率和降低人力成本。
通过PLC控制,可以实现物料输送过程中的自动刹车、速度调节、方向控制等功能,确保物料输送过程的安全和稳定。
PLC在温度控制方面也具有重要作用。
钢铁冶金生产过程中,需要对物料和设备进行精确的温度控制,以确保生产过程的正常进行。
PLC可以通过连接温度传感器和执行器,实现对温度信号的采集和控制。
PLC还可以根据预设的温度控制程序,对加热、冷却设备进行自动控制,确保温度稳定在设定范围内,提高产品质量和生产效率。
PLC在安全保护和故障诊断方面也能够发挥重要作用。
钢铁冶金生产过程中存在各种安全隐患和设备故障问题,需要及时进行处理和解决,以确保生产安全和设备正常运行。
PLC可以通过连接安全传感器和执行器,实现对生产过程中的安全隐患的实时监测和预警。
PLC还可以通过连接故障诊断设备,实现对设备故障的实时诊断和报警。
通过PLC控制,可以实现对生产过程中的安全隐患和设备故障问题的及时处理,确保生产安全和设备正常运行。
PLC在钢铁冶金企业电气自动化控制中的应用非常广泛,可以实现物料输送、温度控制、测量与检测、安全保护和故障诊断等各种功能。
通过PLC控制,可以实现生产过程的自动化和智能化,提高生产效率和产品质量,降低生产成本和人力成本,确保生产安全和设备正常运行。
钢铁冶金企业在电气自动化控制系统的建设和应用中,需要充分重视PLC的应用,发挥其重要作用。
浅谈PLC系统在轧钢产线自动控制中的应用
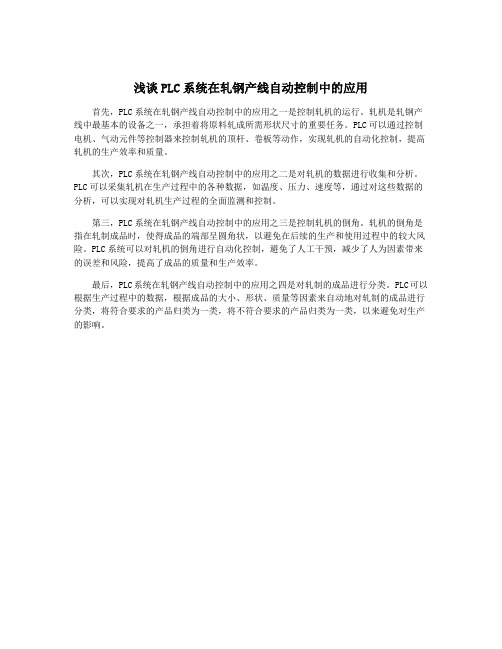
浅谈PLC系统在轧钢产线自动控制中的应用
首先,PLC系统在轧钢产线自动控制中的应用之一是控制轧机的运行。
轧机是轧钢产线中最基本的设备之一,承担着将原料轧成所需形状尺寸的重要任务。
PLC可以通过控制电机、气动元件等控制器来控制轧机的顶杆、卷板等动作,实现轧机的自动化控制,提高轧机的生产效率和质量。
其次,PLC系统在轧钢产线自动控制中的应用之二是对轧机的数据进行收集和分析。
PLC可以采集轧机在生产过程中的各种数据,如温度、压力、速度等,通过对这些数据的分析,可以实现对轧机生产过程的全面监测和控制。
第三,PLC系统在轧钢产线自动控制中的应用之三是控制轧机的倒角。
轧机的倒角是指在轧制成品时,使得成品的端部呈圆角状,以避免在后续的生产和使用过程中的较大风险。
PLC系统可以对轧机的倒角进行自动化控制,避免了人工干预,减少了人为因素带来的误差和风险,提高了成品的质量和生产效率。
最后,PLC系统在轧钢产线自动控制中的应用之四是对轧制的成品进行分类。
PLC可以根据生产过程中的数据,根据成品的大小、形状、质量等因素来自动地对轧制的成品进行分类,将符合要求的产品归类为一类,将不符合要求的产品归类为一类,以来避免对生产的影响。
PLC在钢铁冶金企业电气自动化控制中应用

PLC在钢铁冶金企业电气自动化控制中应用摘要:电气自动化技术在当前的各行各业中都发挥着巨大的作用,特别是在钢铁冶金行业中,而在钢铁冶金行业中采用PLC控制技术能够规范生产流程,提高生产效率,提升整个钢铁冶金企业的自动化控制水平。
基于此,本文首先介绍了PLC的概念以及特点,其次重点分析了PLC技术在钢铁冶金企业中自动化控制中的应用,希望能够为今后的钢铁冶金行业提供参考。
关键词:PLC;钢铁;冶金;电气自动化1 PLC概念与特点1.1概念PLC的组成部分主要包含电源、CPU、存储器等。
它主要是一种能够有效控制工业生产连接的新型先进高科技设备,可以制定相关的程序以运行时。
工业化技术在我国的经济发展中有着不可替代的作用。
PLC技术作为一种自动化控制技术,在整个的工业发展历程中也扮演着重要的角色。
1.2特点PLC主要有以下集中特点:①实用性。
PLC本身具有非常强大的算术和数据处理能力,可以灵活控制工业生产各个环节的系统设置和电气自动化控制需求,增强控制系统的数字化。
②方便。
可编程控制系统将很快主导工业自动化应用。
PLC小巧轻便,端接口设计比较简单,内部结构和编程语言通俗易懂,所以在测试时非常容易操作,无论是传统应用还是维护都非常简单方便。
③防干扰性。
PLC由于其接地系统牢固,对不同环境的适应性强,具有良好的抗干扰性能。
2 PLC技术在钢铁冶金企业电气自动化控制中的优势在钢铁冶金企业自动化控制中应用PLC技术能够实现生产的高度智能化,增加生产环节的技术含量,传统的钢铁冶金控制系统缺乏现代化的运行水准,不仅需要耗费巨大的人力物力财力,还不能满足企业生产的效率。
PLC技术的广泛应用保证了钢铁冶金系统运行的效率,提高了生产的稳定性,降低了企业的生产成本。
PLC技术功能性强使用方便能够适应生产中灵活多变需求。
现代钢铁冶金的技术已经趋于成熟,但是生产的环境依旧需要改良,PLC系统通过控制水箱和控制柜能够有效的降低生产过程中的粉尘系数,使操作工人的生产环境得到极大的改善。
PLC在轧钢生产线的应用
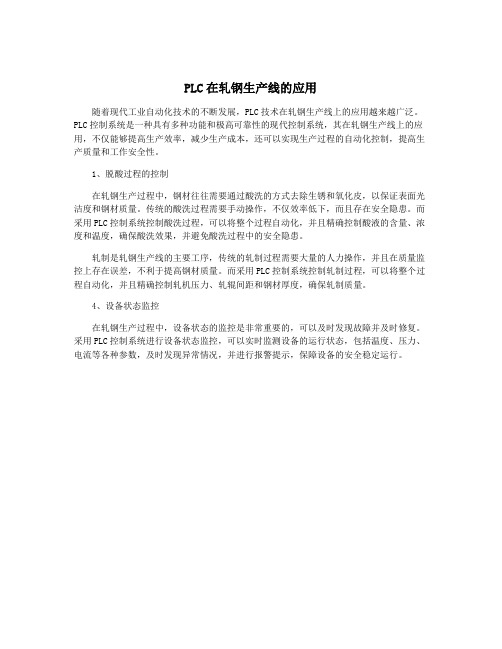
PLC在轧钢生产线的应用
随着现代工业自动化技术的不断发展,PLC技术在轧钢生产线上的应用越来越广泛。
PLC控制系统是一种具有多种功能和极高可靠性的现代控制系统,其在轧钢生产线上的应用,不仅能够提高生产效率,减少生产成本,还可以实现生产过程的自动化控制,提高生产质量和工作安全性。
1、脱酸过程的控制
在轧钢生产过程中,钢材往往需要通过酸洗的方式去除生锈和氧化皮,以保证表面光洁度和钢材质量。
传统的酸洗过程需要手动操作,不仅效率低下,而且存在安全隐患。
而采用PLC控制系统控制酸洗过程,可以将整个过程自动化,并且精确控制酸液的含量、浓度和温度,确保酸洗效果,并避免酸洗过程中的安全隐患。
轧制是轧钢生产线的主要工序,传统的轧制过程需要大量的人力操作,并且在质量监控上存在误差,不利于提高钢材质量。
而采用PLC控制系统控制轧制过程,可以将整个过程自动化,并且精确控制轧机压力、轧辊间距和钢材厚度,确保轧制质量。
4、设备状态监控
在轧钢生产过程中,设备状态的监控是非常重要的,可以及时发现故障并及时修复。
采用PLC控制系统进行设备状态监控,可以实时监测设备的运行状态,包括温度、压力、电流等各种参数,及时发现异常情况,并进行报警提示,保障设备的安全稳定运行。
PLC在钢铁冶金企业电气自动化控制中的应用

PLC在钢铁冶金企业电气自动化控制中的应用PLC(可编程逻辑控制器)是一种专门用于工业自动化控制的计算机控制系统,它广泛应用于钢铁冶金企业的电气自动化控制中。
以下是PLC在钢铁冶金企业电气自动化控制中的常见应用。
PLC用于控制生产线的动作。
钢铁冶金企业的生产线通常包括生产设备、运输设备和处理设备等,PLC可以通过控制这些设备的运行,实现生产线的自动化运作。
通过编程PLC,可以实现对设备的开关控制、运动控制和速度控制等功能,提高生产线的运行效率和稳定性。
PLC用于数据采集和处理。
在钢铁冶金企业中,需要实时监测和记录生产过程的关键数据,如温度、压力、流量等。
PLC可以通过与传感器和仪表等设备的连接,实时采集这些数据,并通过编程对数据进行处理和分析。
通过PLC,可以实现自动化监测和报警功能,及时发现和处理异常情况,确保生产过程的稳定和安全。
PLC还被广泛应用于钢铁冶金企业的能源管理和成本控制方面。
钢铁冶金企业是能源消耗较大的行业,PLC可以通过控制和管理设备的运行,实现对能源的合理利用和节约。
通过编程PLC,可以实现设备的启停控制、能源消耗的监测和分析,提高能源利用率,并通过数据分析和优化控制,降低生产成本。
PLC还可以与其他自动化设备和系统进行集成。
钢铁冶金企业中的自动化控制系统通常包括多个子系统,如物料输送系统、燃烧系统和气体净化系统等。
PLC可以通过与这些系统的通信和集成,实现对整个生产过程的全面控制和监测。
通过编程PLC,可以实现不同系统之间的数据传输和交互,提高系统的整体效率和性能。
PLC在钢铁冶金企业的电气自动化控制中具有重要的应用价值。
它可以实现对生产线的智能化控制,实时监测和处理生产过程中的关键数据,实现能源管理和成本控制,实现不同系统之间的集成和协调。
通过PLC的应用,可以提高钢铁冶金企业的生产效率、质量和安全性,降低生产成本,提升企业竞争力。
PLC技术在钢铁冶金企业电气自动化控制中的应用

PLC技术在钢铁冶金企业电气自动化控制中的应用吕梁建龙实业公司摘要:PLC(可编程逻辑控制器)技术在钢铁冶金企业的电气自动化控制中具有重要作用。
本文将探讨PLC技术在该领域的应用。
首先,我们介绍了钢铁冶金产业的现代化挑战,包括提高生产效率、降低能耗、确保产品质量等。
然后,我们详细讨论了PLC技术在生产过程中的多个应用领域,包括冶炼过程控制、质量控制和能源管理。
最后,我们探讨了未来发展趋势,包括工业互联网、数据分析和安全性考虑,这些趋势将继续推动PLC技术在钢铁冶金企业中的创新应用。
通过本文的研究,我们可以更好地理解PLC技术如何改善钢铁冶金工业的自动化控制,提高效率和可持续性。
关键词:PLC技术;钢铁冶金;电气自动化控制引言随着工业化的不断发展,钢铁冶金企业在全球经济中扮演着关键的角色。
为了满足不断增长的需求,这些企业需要不断提高生产效率、降低能源消耗、确保产品质量以及提升安全性。
在实现这些目标方面,电气自动化控制技术起着至关重要的作用,而PLC(可编程逻辑控制器)技术则是其中的重要组成部分。
一、PLC技术在钢铁冶金企业电气自动化控制中的重要性与背景在钢铁冶金企业中,电气自动化控制发挥着至关重要的作用。
首先,电气自动化帮助企业提高生产效率和质量,通过自动化的生产线和设备控制,可以更加精确地管理冶炼和生产过程,减少了人为干预的错误。
其次,电气自动化还提供了更好的安全性,降低了事故和操作风险。
此外,它也有助于资源的节约,通过智能化控制,可以更有效地利用原材料和能源,降低了生产成本。
PLC(可编程逻辑控制器)技术作为电气自动化的核心组成部分,具有高度的灵活性和可编程性。
PLC系统可以根据不同的生产需求进行编程和调整,适用于各种钢铁冶金工艺。
此外,PLC系统还能够与其他控制设备和传感器实现无缝集成,提供全面的控制和监测。
然而,钢铁冶金企业在实现电气自动化时面临一些挑战。
首先,由于冶金工艺的复杂性,需要高度定制化的PLC编程和控制系统,这增加了部署和维护的难度。
欧姆龙PLC系统在昆钢高线PF线的应用

( 2 ) 从 开 发 者 的 视 角 而言 : 一些 需 要 访 从而 使 软 件 开 发 能够 适应 于 可 累复 杂 护 着
化结构 , 因此 系 统 分 属 于 不 同 层 次 的 组 件 互相独立 , 能够 方 便 地 增 加 、 更 新。 这 个 特 点为系统 的维护带 来许多方便 。 此 外 因 为 不同组件 之间的 关系是互相独立 的 , 假 如 需要更换 组件 , 并 不 会 对 系 统 另外 部 分 的 组件产生 任何影 响 , 所 以 对 系 统 进 行 更 新 或者维 护的时候 就会安全和 可靠。 此外 由
软件 开发情况 。
( 3 ) 本 研 究 所开 发 的 系 统 之 中所 存 在 的 业 务逻 辑 可以 全 部 以 第 三方 提 供 的 服 务 来 实 现 具 体 的功 能 。 相 关 的 业 务 逻辑 服 务 组 件 由 服 务 提 供 者进 行 开 发 之 后 , 可 以 给 整
社, 2 0 2.
结 合 前 文 所 述 的 基 于 M VC的 结 构 特 征, 本 设 计 在 信 息 系 统 引 入MVC 结 构 所具 有的优势 包括。 ( 1 ) 在软件用 户的视角 : 客 户 的需 求 可 以 通 过 将 不 一 样 的 服 务 组 合 起 来 进 行 实 现。 举例来讲 , 一 个 客 户 在查 询 服 务 的 时 候 还要 另外提供一些服 务 , 则 此 时 客 户 可 以 把这部分 服务进行组 合 , 从 而 形 成 新 的 可 供调用 的服务 。 通 过 这 样 的 方 法 就 能 够 使 得 在 并 发 请 求 数 目比 较 多 的 时 候 , 不 至 于
户解决需求模 糊的问题 。 在 基 于 敏 捷 管 理 理念的软件开 发实施 中, 对 开 发 流 程 和 开
PLC 在煤矿胶带输送机上的应用分析

PLC 在煤矿胶带输送机上的应用分析0 引言在矿井煤炭运输中,煤矿皮带运输机是最为重要的设备之一,通过应用该设备能快速的将开采的煤炭从矿井中运出,降低了人力资源投入,并节约了大量时间,保证了开采量。
但由于长期使用,一些皮带运送机会出现不同程度的问题,而通过引入PLC 控制系统,采用PLC 作为煤矿胶带运送机的控制核心,能极大程度的提升系统的可靠性以及工作效率,减少设备出现故障的概率,降低工作人员的工作量,对于保证采煤效率和采煤安全有着重要的作用。
1 PLC 可编程逻辑控制器概述PLC 控制系统是一种以微型处理器为基础核心来实现自动控制的系统,由于其结合了现代计算机技术,自动控制集1/4 控技术和信息化技术,使得其具有体积小、操作便捷、维护简单、可靠性高、功能性强等优点。
现如今该系统已经被大量使用于工业生产之中,采矿业自然也是重点应用领域。
PLC 系统软件采用的是梯形图编程,其具有模块化特点,这使得系统具有较强的独立功能性。
当工作人员启动设备后,首先要对设备情况进行检测,当检测确定设备处于正常状态时,设备就会正常启动,如果出现异常,设备就会转入其他相应的功能之中。
设备还设置有急停按钮,只要按下急停按钮就能让设备完全停下,并且该系统还具有远程操作功能,只需要在远程工作站中设定相应的条件,就能对设备运行状态进行监控,对设备进行控制[1]。
2 PLC 系统的主要功能PLC 系统需要设置大量的功能,才能确保系统发挥实际效果。
当将该系统应用到煤矿胶带输送机上时,能满足皮带运输控制系统和皮带运输保护系统2 个方面的现场功能实现。
控制系统的重点是对操控系统进行整合,通过构建完整统一的控制系统来帮助工作人员更好地对设备进行管理控制,其工作方式一般被分为自动状态和维修状态。
在建立控制系统后,工作人员可以在总控台通过几个开关轻易的实现设备的启停、改变设备运行状态等行为。
而保护系统则能对煤矿胶带输送机实施六大保护,一旦出现了堆煤、烟雾、跑偏等动作时,皮带就能迅速识别随后自动停止,这能极大程度的保证人员和设备的安全,避免出现故障和意外,保证采煤安全和采煤效率。
钢铁企业电气自动化控制中PLC技术运用分析

钢铁企业电气自动化控制中PLC技术运用分析摘要:钢铁企业电气自动化控制中,PLC技术的应用不仅可以保障生产环节的稳定,也有利于提高生产效率,控制生产成本,对钢铁企业发展具有重要意义。
PLC技术在钢铁企业的炼铁除尘、故障响应、配料系统以及电机变频调速方面发挥良好的作用,有利于精准的管控生产材料、强化生产工序监督,节约生产中的各类资源,能够有效提升钢铁企业自动化控制水平,助力钢铁行业发展。
关键词:钢铁企业;电气自动化控制;PLC技术PLC技术是工业生产电气自动化控制中极为重要的技术条件,通过数字运算操作电子系统的应用,能够将各种逻辑运算、顺序控制指令汇总到储存器内,实现对工业生产的有效控制。
钢铁企业的电气自动化控制中应用PLC技术,也能够极大的提升其控制水平,保障生产质量。
在钢铁企业实际应用PLC技术时,需要注意分析PLC技术的特点,接合其基本结构和工作原理,客观探讨提升自动化控制水平的条件,保证钢铁企业的工业生产得以有序开展,提升生产质量。
一、钢铁企业电气自动化控制中PLC技术应用意义1、保证生产环节稳定钢铁企业电气自动化控制中应用PLC技术有利于保障生产环节稳定。
PLC技术是一种简单、便捷并且优质的编程技术,能够通过储存器内的各种逻辑运算和控制指令的应用,实现工业生产的有效控制,在钢铁企业生产过程中,PLC技术可以实现电气自动化控制,对冶金过程中的除尘系统、配料系统、故障响应等进行科学管控,加强了工业生产中各环节的监控和管理。
相较于人工控制,PLC技术的自动化控制依托于计算机技术能够实现更加稳定的调控,避免了人为操作中可能出现的失误,能够提供更加稳定、可靠的生产条件,保证其生产质量[1]。
2、提高工业生产效率PLC技术用于钢铁企业电气自动化控制也很好的提升了工业生产效率。
PLC技术是一种简单、高效的控制技术,编程入门相对简单,实际控制效果较好,可以消耗较少资源的前提下,对工业各工序进行有效的管控。
浅谈PLC系统在轧钢产线自动控制中的应用

浅谈PLC系统在轧钢产线自动控制中的应用随着科技的进步和不断更新,PLC系统在轧钢产线自动控制中的应用越来越广泛。
PLC 系统实现了轧钢产线的自动化控制,大大提高了产线的生产效率,减少了生产成本。
下面就来谈谈PLC系统在轧钢产线自动控制中的应用。
一、PLC系统的基本结构PLC系统是由CPU、存储器、输入输出模块组成的。
CPU是PLC系统的核心部分,硬件上主要由中央处理器组成,软件上主要由两部分组成:系统程序和用户程序。
存储器主要用于存储系统程序和用户程序,输入输出模块负责将设备的输入信号和输出信号转换为数字信号,供CPU处理。
在轧钢产线中,PLC系统主要用于控制轧机和轧钢设备,完成轧钢产线的自动控制。
传统的轧钢机是由机械驱动的,需要操作员手动控制,人工操作不仅费时费力,而且易产生疲劳,容易出现质量问题。
而PLC系统的应用可以实现轧机的自动化控制。
PLC系统可以根据工艺要求,自动调整轧机的速度、力度和压力等参数,保证轧出的产品质量稳定。
PLC系统还可以记录轧机的工作状态和参数,方便生产管理和保养维护。
轧钢设备有冷却、切割、钢板站和铸坯站等,PLC系统可以对这些设备进行自动控制。
比如冷却设备可以根据钢板的温度自动调整冷却水量,确保钢板的温度控制在合理范围内。
切割设备可以根据轧制的尺寸要求进行快速切割,提高了生产效率。
钢板站和铸坯站可以通过PLC系统实现精准的控制,保证钢板的尺寸和体积达到要求。
1、提高轧钢产线的生产效率,减少生产成本。
2、保证轧出的产品质量稳定。
3、降低了人工操作的劳动强度和劳动成本。
4、提高了生产车间的安全性和可靠性。
5、方便了生产管理和保养维护。
综上所述,PLC系统在轧钢产线自动控制中的应用已经成为了必不可少的一部分。
PLC 系统的应用,不仅提高了产线的生产效率,降低了生产成本,还能保证产品的质量稳定,提高了生产车间的安全性和可靠性。
PLC在钢铁工业中的应用与生产过程优化

PLC在钢铁工业中的应用与生产过程优化概述:PLC(可编程逻辑控制器)是钢铁工业中一种重要的自动化控制设备,其应用已经在生产过程中展现出了巨大的优势。
本文将详细介绍PLC在钢铁工业中的应用领域以及如何利用其功能优化生产过程。
第一节:PLC在钢铁工业中的应用领域PLC作为一种高度灵活且可扩展的自动化控制设备,广泛应用于钢铁工业的多个领域。
以下是几个典型的应用领域:1. 原料处理在钢铁工业中,原料处理是生产过程中的第一步。
PLC可以通过控制输送带、传感器和阀门等设备来实现原料的自动化处理,提高生产效率和精确度。
同时,PLC还可以监测和控制温度、湿度等关键参数,确保原料处理的稳定性和安全性。
2. 高炉控制高炉是钢铁工业中最核心的设备之一。
PLC可以通过对高炉的自动控制,实现温度、压力和流量等参数的实时监测和调节。
这种精确的控制可以提高生产效率,降低能耗,并确保产品质量的稳定性。
3. 连铸控制连铸是钢铁生产过程中的关键环节,直接影响最终产品的质量。
PLC可以通过控制连铸机的运行和流程,以及调节铸坯的冷却速度、铸坯形状等关键参数,实现连铸过程的自动化控制和优化。
4. 成品检测与质量控制PLC在钢铁工业中也常用于成品检测及质量控制。
通过设定合适的传感器和控制逻辑,PLC可以实时监测钢铁产品的尺寸、硬度、重量等关键参数。
一旦检测到异常,PLC可以自动触发报警机制,并采取相应的纠正措施,保证产品质量的稳定性。
第二节:PLC在钢铁生产过程中的优化作用除了应用于特定领域,PLC还可以对整个钢铁生产过程进行优化,从而提高生产效率和降低资源消耗。
以下是几个常见的优化方法:1. 自动化生产流程PLC可以自动化控制和优化钢铁生产过程。
通过与其他设备的联动和实时监控,PLC可以自动判断和调整相关参数,从而实现整个生产流程的高效运行。
这种自动化的生产流程不仅降低了人工干预的风险,还减少了生产成本。
2. 数据采集与分析PLC可以实时采集和记录钢铁生产过程中的各种数据,例如温度、压力、流量等参数。
PLC在钢铁冶金企业电气自动化控制中的应用

PLC在钢铁冶金企业电气自动化控制中的应用PLC(可编程逻辑控制器)在钢铁冶金企业电气自动化控制中起着非常重要的作用。
钢铁冶金企业通常由多个工序和设备组成,如原料处理,炼铁,炼钢,轧钢等,这些工序需要准确的控制和协调。
PLC的应用可以实现对这些过程的自动化控制,提高生产效率和产品质量。
PLC在原料处理过程中的应用非常重要。
原料处理是指通过对原料进行破碎、分级、筛分、除尘等工序,使原料达到炼铁和炼钢的要求。
PLC可以对这些工序进行自动控制,根据传感器反馈的信息,实时调节原料处理设备的运行状态和参数,确保原料处理的准确性和稳定性。
PLC在炼铁和炼钢过程中的应用也非常重要。
炼铁过程包括高炉的操作和控制,喷吹操作,出铁过程等。
PLC可以实现对这些工序的自动控制和监控,实时调节各种操作参数,如鼓风量,喷吹速度,炉温,煤气含量等,确保炼铁过程的稳定性和高效性。
同样,炼钢过程中PLC的应用也非常广泛,可以实现对炉前设备和炉后设备的自动控制和监控,确保炼钢过程的稳定和安全。
PLC在钢铁轧钢过程中的应用也非常重要。
轧钢是将铁水或钢坯通过钢轧机进行连续轧制而得到不同形状和规格的钢材的过程。
PLC可以实现对轧钢设备的自动控制和协调,控制轧机的开闭,调节轧制力和速度,实时监测轧制过程中的温度和形状,实现对轧制过程的精确控制。
PLC在炉温控制,环境监测和报警,设备故障监测和维修等方面也有广泛的应用。
PLC 可以实时监测和调节炉温,确保炉温的稳定和均匀性。
PLC可以监测环境中的温度,湿度,氧气含量等参数,根据预先设定的阈值进行报警,保证生产环境的安全和稳定。
PLC还可以监测设备的运行状态和故障情况,及时发出警报并提供相关的维修信息,提高设备的可靠性和维护效率。
PLC在钢铁冶金企业电气自动化控制中的应用十分广泛。
它能够实现对钢铁生产过程中的各个环节进行自动化控制和监控,提高生产效率,保证产品质量,降低能源消耗和环境污染。
随着技术的不断发展,PLC的应用将会越来越广泛,为钢铁冶金企业带来更多的优势。
PLC在钢铁冶金企业电气自动化控制中的应用

PLC在钢铁冶金企业电气自动化控制中的应用PLC(可编程逻辑控制器)在钢铁冶金企业的电气自动化控制中起着重要的作用。
由于钢铁冶金企业的生产过程复杂,涉及到多个步骤和大量的设备,如果完全依靠人工操作,不仅工作效率低下,还容易出现人为错误。
而PLC可以通过编制逻辑控制程序,实现对设备的自动控制,提高生产效率和产品质量。
以下将详细介绍PLC在钢铁冶金企业电气自动化控制中的应用。
PLC在钢铁冶金企业中广泛应用于生产线的控制。
钢铁冶金企业的生产线通常包括多个工位或工序,每个工序包括一系列的操作和控制步骤。
PLC可以根据生产线的工艺流程编程,实现对各个工序的控制和调度。
在炼铁工序中,PLC可以控制高炉的加料、送风、出铁等操作,实现自动化控制,减少人工干预,提高生产效率和炼铁质量。
PLC还可以用于设备的监控和故障诊断。
钢铁冶金企业通常拥有大量的设备,如卷板机、轧机、热处理炉等。
这些设备的正常运行对于生产线的顺利进行至关重要。
PLC可以通过连接传感器和执行器,实时监测设备的运行状态,并根据设定的逻辑控制程序对设备进行控制。
当设备出现异常情况或故障时,PLC可以发出报警信号,并通过界面显示出错信息,方便操作人员进行故障诊断和维修。
这样既提高了设备的可靠性和稳定性,又减少了生产停机时间和维护成本。
PLC还可以实现钢铁冶金企业的生产数据采集和处理。
钢铁冶金企业的生产过程中产生大量的数据,如温度、压力、电流、流量等。
这些数据对于生产流程的控制和质量的监测非常重要。
PLC可以通过连接传感器和数据采集模块,实时采集和记录生产数据,并通过通信接口将数据传输到上位机或云平台进行进一步的处理和分析。
这样可以及时监测生产过程中的异常情况,提前做出调整,保证产品的质量和生产的效率。
PLC在钢铁冶金企业电气自动化控制中的应用非常广泛。
它能够实现对生产线的自动控制,提高生产效率和产品质量;可以监控设备的运行状态,及时发现并处理故障;还可以采集和处理生产数据,实现对生产过程的监控和优化。
浅谈PLC系统在轧钢产线自动控制中的应用

浅谈PLC系统在轧钢产线自动控制中的应用PLC系统(可编程逻辑控制器)是一种专门用于工业自动化控制的设备,其在轧钢产线的应用是非常广泛的。
轧钢产线是一个复杂的工业生产系统,需要对温度、压力、速度等多个工艺参数进行精密控制,而PLC系统能够实现对这些参数的快速、准确的控制,提高生产效率,降低成本,确保轧钢产线的安全稳定运行。
本文将从PLC系统的基本原理、在轧钢产线中的具体应用以及未来发展趋势等方面进行探讨。
一、PLC系统的基本原理PLC系统是一种现代工业控制系统,其基本原理是通过对输入信号进行逻辑运算,输出控制信号,实现对工业生产过程的控制。
PLC系统主要由中央处理器、输入/输出模块、存储器和编程键盘等部分组成。
其中中央处理器主要负责对输入信号进行逻辑处理,根据编程逻辑进行控制,输出相应的控制信号;输入/输出模块负责与外部设备进行信号交换;存储器则用于存储程序和数据。
通过编程键盘可以编写控制程序,对PLC系统进行编程。
PLC系统在工业自动化控制中具有如下特点:1. 稳定可靠:PLC系统采用现代化的数字电子技术,具有较高的可靠性和稳定性;2. 灵活多变:PLC系统的编程语言丰富多样,可以根据不同的控制需求进行编程;3. 易于维护:PLC系统采用模块化设计,故障时可以快速更换故障模块,方便维护;4. 易于扩展:PLC系统可以根据生产需求进行扩展,添加新的输入/输出模块和功能模块。
二、PLC系统在轧钢产线中的具体应用1. 温度控制:在轧钢产线中,控制板坯和卷板的温度是非常重要的。
PLC系统可以根据轧制工艺要求,实时监测板坯和卷板的温度,并通过控制加热炉、冷却设备等进行温度调节,保证板坯和卷板的温度符合要求。
2. 压力控制:轧钢产线中,需要对轧制机的压力进行精确控制,以保证轧制板坯和卷板的厚度精度。
PLC系统可以实时监测轧制机的压力,并通过控制液压系统、气动系统等设备进行压力调整,保证轧制质量。
4. 故障诊断:轧钢产线是一个复杂的系统,随时可能发生各种故障。
PLC在高速线材中的应用

PLC在高速线材中的应用摘要:PLC是一种专门为在工业环境下应用而设计的数字运算操作的电子装置。
它采用可以编制程序的存储器,用来在其内部存储执行逻辑运算、顺序运算、计时、计数和算术运算等操作的指令,并能通过数字式或模拟式的输入和输出,控制各种类型的机械或生产过程。
在现代轧钢上产中,自动化高度集中,PLC 应用尤为重要。
关键词:PLC S7400协议网络1.PLC技术发展呈现新的动向1.产品规模向大、小两个方向发展大:I/O点数达14336点、32位为微处理器、多CPU并行工作、大容量存储器、扫描速度高速化。
小:由整体结构向小型模块化结构发展,增加了配置的灵活性,降低了成本。
2.PLC在闭环过程控制中应用日益广泛。
3:不断加强通讯功能。
4..新器件和模块不断推出高档的PLC除了主要采用CPU以提高处理速度外,还有带处理器的EPROM或RAM的智能I/O模块、高速计数模块、远程I/O 模块等专用化模块。
5.编程工具丰富多样,功能不断提高,编程语言趋向标准化有各种简单或复杂的编程器及编程软件,采用梯形图、功能图、语句表等编程语言,亦有高档的PLC指令系统。
6.发展容错技术采用热备用或并行工作、多数表决的工作方式。
7.追求软硬件的标准化。
2. PLC在高速线材生产线的应用现以宣钢集团二高线为例,其基础自动化系统采用西门子公司最新型PLC S7-400和PLC S7-300系列产品。
2.1.SIEMENSS7系列产品功能强大,配置灵活,有如下突出特点高速在程序执行方面,极短的指令执行时间使S7-400和S7-300在竞争中脱颖而出。
坚固即使在恶劣、不稳定的工业环境下,全封闭的模板依然可正常工作;无风扇操作降低了安装费用。
功能完善、强大允许多CPU配置,功能更强、速度更快。
同时,配有品种齐全的功能模板,充分满足用户各种类型的现场需求。
强通讯能力分布式的内部总线允许在CPU与中央I/O间进行非常快的通讯,P总线与输入/输出模板进行数据交换。
欧姆龙高速脉冲指令
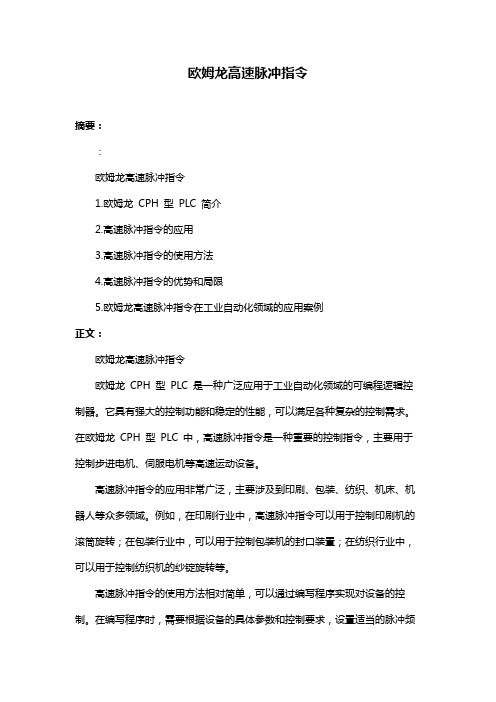
欧姆龙高速脉冲指令摘要::欧姆龙高速脉冲指令1.欧姆龙CPH 型PLC 简介2.高速脉冲指令的应用3.高速脉冲指令的使用方法4.高速脉冲指令的优势和局限5.欧姆龙高速脉冲指令在工业自动化领域的应用案例正文:欧姆龙高速脉冲指令欧姆龙CPH 型PLC 是一种广泛应用于工业自动化领域的可编程逻辑控制器。
它具有强大的控制功能和稳定的性能,可以满足各种复杂的控制需求。
在欧姆龙CPH 型PLC 中,高速脉冲指令是一种重要的控制指令,主要用于控制步进电机、伺服电机等高速运动设备。
高速脉冲指令的应用非常广泛,主要涉及到印刷、包装、纺织、机床、机器人等众多领域。
例如,在印刷行业中,高速脉冲指令可以用于控制印刷机的滚筒旋转;在包装行业中,可以用于控制包装机的封口装置;在纺织行业中,可以用于控制纺织机的纱锭旋转等。
高速脉冲指令的使用方法相对简单,可以通过编写程序实现对设备的控制。
在编写程序时,需要根据设备的具体参数和控制要求,设置适当的脉冲频率、脉冲数量等参数。
此外,还需要注意避免脉冲信号的干扰,确保控制信号的稳定性和可靠性。
欧姆龙高速脉冲指令具有以下优势:1.高速:高速脉冲指令可以实现快速、精确的控制,提高设备的运行效率和精度;2.稳定:高速脉冲指令具有较强的抗干扰能力,可以保证控制信号的稳定性和可靠性;3.灵活:高速脉冲指令可以适应不同设备的控制需求,具有较强的灵活性。
然而,欧姆龙高速脉冲指令也存在一定的局限性,如对脉冲信号的频率、幅值等参数有一定的要求,需要根据具体的设备参数进行调整。
在工业自动化领域,欧姆龙高速脉冲指令的应用案例众多。
例如,在印刷行业中,可以用于控制印刷机的滚筒旋转,实现高速、精确的印刷;在包装行业中,可以用于控制包装机的封口装置,实现高速、精确的包装;在纺织行业中,可以用于控制纺织机的纱锭旋转,实现高速、精确的纺织等。
欧姆龙PLC系统在昆钢高线PF线的应用

高速线材生产线的PF线是高线盘卷的运输线。
昆钢高线的PF线有60个C型钩、2个合流道岔、2个分流道岔、34个工位。
由2台11kW的交流变频电机和2台减速机分别组成2个传动站,通过2根传动链带动C型钩形成盘卷输送线,由集卷站将盘卷送至卸卷站,运送过程中盘卷自然冷却后经打包机打包,然后称重,挂牌。
1 原控制系统存在的问题(1)对操作人员的要求比较高:PF线的原控制系统采用了日本欧姆龙S Y M S C C500系列PL C和一个与PL C连接的用发光二极管、七段译码器、蜂鸣器制作的工艺流程模拟屏组成。
且其小监控面板要通过输入不同的指令和地址来监控和强制模块的输入输出点、保持继电器、计数器等。
操作人员必须特别熟悉工艺流程、操作指令、每个工位的输入输出点的地址和强制方法、保持继电器和计数器的复位方法方可操作,这样导致操作人员培训时间长。
(2)监控点比较少:虽然发光二极管用来监控每个工位的占位信号、到位信号、电磁阀线圈的工作状态。
七段译码器用来显示工位间的存钩数。
蜂鸣器用来故障报警。
但小监控面板的液晶屏每次最多只可以监控三个输入输出点或保持继电器、计数器等。
要查看更多的点的状态,只能清除屏幕后再输入指令和地址。
(3)操作繁琐:想要强制某个工位的输入输出点或者调整存钩数等操作,要先输入功能指令,再对照贴在PL C柜门上的地址图表来输入地址,方可执行强制。
(4)故障报警不准确,查询不方便:工艺流程模拟屏虽然可以根据发光二极管的状态来监控每个工位的状态、存钩数、故障报警等,但PF线故障停链时,模拟屏上的故障报警的点多,难以判断故障工位,需要依次排查,比较费时。
(5)原系统在运行过程中出现的故障:P F 线的15#、18#工位后面是一个合流道岔。
由于占位信号不准确易导致撞钩故障,C型钩卡在一起把PF 线传动链卡死,引起过载停链。
随着生产节奏加快,只要PF线故障停链几分钟,就会造成轧制好的成品因无法运送而停轧。
严重影响生产的顺利进行,是制约产量完成的一个“瓶颈”。
PLC在钢管生产线追剪伺服控制系统中的应用

【120】 第37卷 第2期 2015-02(下)PLC 在钢管生产线追剪伺服控制系统中的应用Application of PLC in the steel pipe production line after shear servo control system雷慧杰1,陈彦涛1,张艳伟2LEI Hui-jie 1, CHEN Yan-tao 1, ZHANG Yan-wei 2(1.安阳工学院 电子信息与电气工程学院,安阳 455000;2.安阳钢铁集团公司,安阳 455000)摘 要:为了提高钢管同步定长切割的精度和系统的稳定性,提出了基于PlC和伺服系统的追剪自动控制方案。
结合系统的工作原理,分析了追剪的运动过程,基于PlC和伺服驱动器对系统进行了硬件设计,搭建了计算启动残长的数学模型,对软件进行了设计。
应用结果表明,该系统切割精度高,工作可靠稳定,提高了企业的生产效益,具有很好的应用前景。
关键词:PlC;追剪;伺服控制系统中图分类号:TP273 文献标识码:B 文章编号:1009-0134(2015)02(下)-0120-03Doi:10.3969/j.issn.1009-0134.2015.02(下).37收稿日期:2014-10-20基金项目:2014年度河南省教育厅科学技术研究重点项目(14A510002);安阳工学院2014年度青年科研基金项目(QJJ2014016)作者简介:雷慧杰(1981 -),女,讲师,硕士,研究方向为电气传动与自动控制。
0 引言安钢某钢管生产线生产的国标无缝钢管规格为Φ60mm~108mm ,壁厚3.0mm~4.0mm ,定尺10m ,允许误差≤5mm ,过去传统机械定尺的飞剪已经不能满足生产的精度要求。
现在冶金企业中各种型材、管材等连续轧制生产线进行物料剪切的重要设备是追剪,追剪控制系统能够将连续延伸的型材、管材在线动态切割成客户要求的长度,定长精度高[1]。
- 1、下载文档前请自行甄别文档内容的完整性,平台不提供额外的编辑、内容补充、找答案等附加服务。
- 2、"仅部分预览"的文档,不可在线预览部分如存在完整性等问题,可反馈申请退款(可完整预览的文档不适用该条件!)。
- 3、如文档侵犯您的权益,请联系客服反馈,我们会尽快为您处理(人工客服工作时间:9:00-18:30)。
欧姆龙PLC系统在昆钢高线PF线的应用作者:徐丽梅
来源:《科技资讯》2013年第11期
摘要:本文通过对欧姆龙PLC控制系统在昆钢高线PF线的应用,说明随着科技进步,PLC控制系统的更新,不仅能提高生产效率,而且监控全面,操作简便,便于维护。
关键词:PF线改造效果
中图分类号:TP273 文献标志码:A 文章编号:1672-3791(2013)04(b)-0000-01
高速线材生产线的PF线是高线盘卷的运输线。
昆钢高线的PF线有60个C型钩、2个合流道岔、2个分流道岔、34个工位。
由2台11KW的交流变频电机和2台减速机分别组成2个传动站,通过2根传动链带动C型钩形成盘卷输送线,由集卷站将盘卷送至卸卷站,运送过程中盘卷自然冷却后经打包机打包,然后称重,挂牌。
1 原控制系统存在的问题
(1)对操作人员的要求比较高:PF线的原控制系统采用了日本欧姆龙SYMSC C500系列PLC和一个与PLC连接的用发光二极管、七段译码器、蜂鸣器制作的工艺流程模拟屏组成。
且其小监控面板要通过输入不同的指令和地址来监控和强制模块的输入输出点、保持继电器、计数器等。
操作人员必须特别熟悉工艺流程、操作指令、每个工位的输入输出点的地址和强制方法、保持继电器和计数器的复位方法方可操作,这样导致操作人员培训时间长。
(2)监控点比较少:虽然发光二极管用来监控每个工位的占位信号、到位信号、电磁阀线圈的工作状态。
七段译码器用来显示工位间的存钩数。
蜂鸣器用来故障报警。
但小监控面板的液晶屏每次最多只可以监控三个输入输出点或保持继电器、计数器等。
要查看更多的点的状态,只能清除屏幕后再输入指令和地址。
(3)操作繁琐:想要强制某个工位的输入输出点或者调整存钩数等操作,要先输入功能指令,再对照贴在PLC柜门上的地址图表来输入地址,方可执行强制。
(4)故障报警不准确,查询不方便:工艺流程模拟屏虽然可以根据发光二极管的状态来监控每个工位的状态、存钩数、故障报警等,但PF线故障停链时,模拟屏上的故障报警的点多,难以判断故障工位,需要依次排查,比较费时。
(5)原系统在运行过程中出现的故障:PF线的15#、18#工位后面是一个合流道岔。
由于占位信号不准确易导致撞钩故障,C型钩卡在一起把PF线传动链卡死,引起过载停链。
随着生产节奏加快,只要PF线故障停链几分钟,就会造成轧制好的成品因无法运送而停轧。
严重
影响生产的顺利进行,是制约产量完成的一个“瓶颈”。
且随着科技的不断进步,系统备件已很难购置,因此只有对原系统进行升级改造。
2 新系统的选型及应用
2.1 新系统的选型
新系统的初期选型过程中决定先试用西门子S7-300PLC系统,但是在试验过程中却发现原来使用的光电开关和接近开关,电压为AC220V,在还没有检测到信号时,西门子S7-
300PLC的6ES7 321-1FF10-0AA0和6ES7 321-1FH00-0AA0这两种数字输入模块就已经有高电平信号了。
经对光电开关和接近开关实际测量有78V的漏电,而西门子的数字输入模块只要70V就高电平有效。
若要使用西门子的S7-300PLC系统,就要更换现有的检测元件。
为了节约成本,便于操作,选用欧姆龙SYSMSC CS1G-CPU42H型的PLC系统。
配用现有检测元件,该PLC数字输入模块能正常接收信号,有960个输入输出点,具有处理速度快,通讯能力强的优点。
2.2 新系统的组成和应用
欧姆龙SYSMSC CS1G-CPU42H型的PLC系统,使用计算机与PLC连接,应用GE的IFIX软件制作了工艺流程图、点位表、夹紧器图表、存钩数图表、故障报警。
2.2.4 故障报警
3 新老系统的比较
3.1 降低了对操作人员的要求
改造前对PF线操作工的技能要求较高,要有两年以上的操作经验才能熟练操作。
改造后只需培训两个月就可以对PF线进行熟练操作。
3.2 监控点全面
可以对整个PF线的工艺流程、所有工位的信号状态、存钩数、故障报警等起到全面的监控作用。
比较起老系统来更全面、更直观。
3.3 操作更简便
只需要切换显示器画面就能对PF线进行监控和操作,操作变得更简便、快捷、准确。
3.4 故障报警准确
操作人员只要根据故障报警的内容就可以准确的判断和处理故障。
比较起老系统来,故障报警更容易查找。
有效避免了撞钩故障的发生,提高了生产效率。
4 结语
实际生产应用中,设备升级应结合现场实际,设备选型过程中不应盲从,要多方考虑,在节能降耗的前提下,也应兼顾生产成本及人员素质。
如何实现生产效益最大化,是我们在每一次对设备升级改造过程中要考虑和解决的问题,只有本着节约资金能源的前提下,才能实现性价比最优化。