麻花钻加工精孔的妙招
麻花磨钻头的方法和技巧
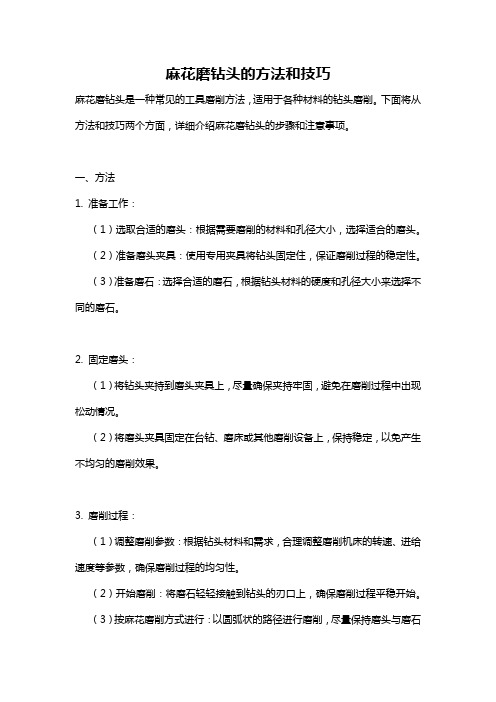
麻花磨钻头的方法和技巧麻花磨钻头是一种常见的工具磨削方法,适用于各种材料的钻头磨削。
下面将从方法和技巧两个方面,详细介绍麻花磨钻头的步骤和注意事项。
一、方法1. 准备工作:(1)选取合适的磨头:根据需要磨削的材料和孔径大小,选择适合的磨头。
(2)准备磨头夹具:使用专用夹具将钻头固定住,保证磨削过程的稳定性。
(3)准备磨石:选择合适的磨石,根据钻头材料的硬度和孔径大小来选择不同的磨石。
2. 固定磨头:(1)将钻头夹持到磨头夹具上,尽量确保夹持牢固,避免在磨削过程中出现松动情况。
(2)将磨头夹具固定在台钻、磨床或其他磨削设备上,保持稳定,以免产生不均匀的磨削效果。
3. 磨削过程:(1)调整磨削参数:根据钻头材料和需求,合理调整磨削机床的转速、进给速度等参数,确保磨削过程的均匀性。
(2)开始磨削:将磨石轻轻接触到钻头的刃口上,确保磨削过程平稳开始。
(3)按麻花磨削方式进行:以圆弧状的路径进行磨削,尽量保持磨头与磨石的接触面积均匀,避免磨削过程中集中在一点,导致刃口不均匀。
(4)掌握磨削时间:根据钻头的材料硬度和磨削需求,合理掌握磨削的时间,避免磨削过度或不足。
4. 磨削后处理:(1)清洁钻头:磨削结束后,用工具清洁钻头的表面,清除刃口上的余渣和铁屑等杂质。
(2)检查钻头质量:通过目视和手感,判断钻头的质量是否符合要求,如刃口是否均匀锋利、孔径是否满足标准等。
(3)记录和整理:将磨削过程中的相关数据记录下来,并整理归档,以备后续参考和分析。
二、技巧1. 磨削应均匀进行:在磨削过程中,麻花磨削方式可以有效保证磨头的均匀磨削,避免出现刃口不均匀的情况。
2. 注意磨削深度:根据磨削需求和钻头的剩余长度,合理控制磨削的深度,避免磨削过度导致钻头的寿命缩短。
3. 磨石的选择和维护:根据材料的硬度选择合适的磨石,定期检查磨石的磨损情况,及时更换磨石。
4. 控制磨削时间:磨削时间过长容易导致钻头过热,影响钻头的质量,因此在磨削过程中应合理控制磨削时间。
钻头刃磨知识总汇-麻花钻及群钻(免费)
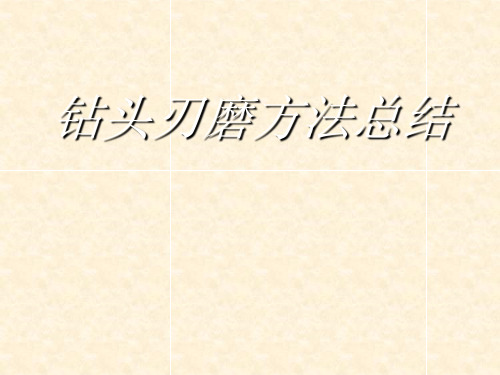
以φ12mm高速钢麻花钻头,刃磨成基本 群钻刃型为例,(这种刃型可钻削低、中、 高碳钢;合金钢及耐酸不锈钢(1Cr18Ni9Ti )等各类黑色和有色金属材料)。
四、基本群钻刃型快速刃磨顺序及方法
1.磨尖高:
要求:从市埸购来的麻花钻头,其外锋角2φ118º±2º,将其钻尖高磨至≈H/2。 目的:减少后续的刃磨量和时间。
5.磨内刃:
要求:内刃宽度磨至弧刃全长≈l/2,同时须产生内刃前角γτ、≈–5º~–10º、内刃斜角 K≈20º~30º、横刃长B≈0.04~0.07mm(图15–1)。 目的:使内刃前角γτ负值减至最小,加之横刃长减短,钻削时轴向力就小得多,从 而给大进给量创造了条件。
方法:钻心前刀面磨削点为砂轮 外圆中心与其侧面相交处。①钻 头尾部抬高与砂轮磨削点呈15º~ 25º夹角;②左手抓住钻尾,其中 指按在砂轮机上某一点定位,右 手拇指和食指抠住钻头前端两螺 旋沟槽;③在摆出以上位置后, 右手将钻头后面的螺旋槽逐渐靠 上砂轮磨削点,与此同时左手微 松,右手扭住钻头作顺时针方向 缓慢转动刃磨,当磨至近横刃时, 观察砂轮磨削点与钻头前刀面呈 ≈15º~20º时,右手将钻心向砂轮 侧面作一直线微量进给,使内刃 斜角τ产生并同时缩短横刃。微松, 将钻头旋转180º,仍在原位置,按 上述动作刃磨另一侧内刃。在刃 磨的全过程中,身体站位与手指 的定位点不变,
3
3、由刃口往后磨后面。 刃口接触砂轮后,要从主切削刃往后面磨,也
就是从钻头的刃口先开始接触砂轮,而后沿着整 个后刀面缓慢往下磨。钻头切入时可轻轻接触砂 轮,先进行较少量的刃磨,并注意观察火花的均 匀性,及时调整手上压力大小,还要注意钻头的 冷却,不能让其磨过火,造成刃口变色,而至刃 口退火。发现刃口温度高时,要及时将钻头冷却。
麻花钻头怎么磨又快又耐用【纯干货经验】
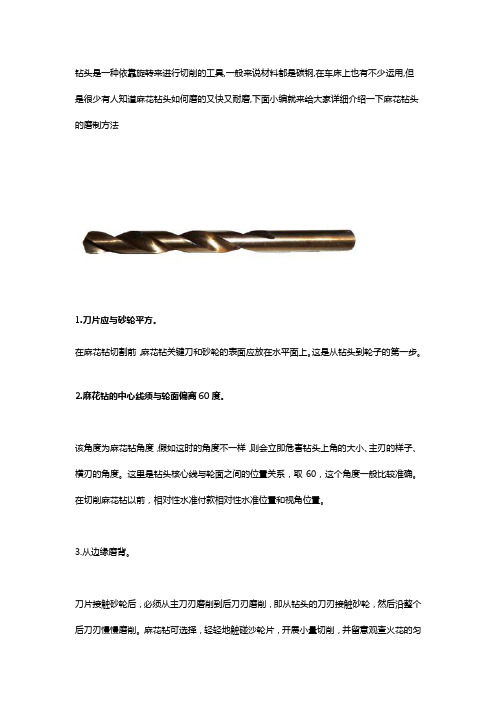
钻头是一种依靠旋转来进行切削的工具,一般来说材料都是碳钢,在车床上也有不少运用,但是很少有人知道麻花钻头如何磨的又快又耐磨,下面小编就来给大家详细介绍一下麻花钻头的磨制方法1.刀片应与砂轮平方。
在麻花钻切割前,麻花钻关键刀和砂轮的表面应放在水平面上。
这是从钻头到轮子的第一步。
2.麻花钻的中心线须与轮面偏离60度。
该角度为麻花钻角度,假如这时的角度不一样,则会立即危害钻头上角的大小、主刃的样子、横刃的角度。
这里是钻头核心线与轮面之间的位置关系,取60,这个角度一般比较准确。
在切削麻花钻以前,相对性水准付款相对性水准位置和视角位置。
3.从边缘磨背。
刀片接触砂轮后,必须从主刀刃磨削到后刀刃磨削,即从钻头的刀刃接触砂轮,然后沿整个后刀刃慢慢磨削。
麻花钻可选择,轻轻地触碰沙轮片,开展小量切削,并留意观查火花的匀称性,立即调节手压,也要留意麻花钻的制冷,不容易造成烫伤,造成边沿变色,随后淬火。
当边缘温度较高时,钻头应及时冷却。
4.钻头的边缘应上下摆动,钻头的尾部不能抬高。
这是一种标准的钻头磨削作用,主要是在砂轮上下摆动钻头,即把钻头握在手前,使钻头在砂轮上均匀摆动。
但是,手柄的手不能摆动,还要防止后柄上升,即钻头的末端不能抬高到砂轮的水平中心线以上,否则会使刀片钝化,不能切割。
这是最重要的一步,比特研磨好坏,与它有很大的关系。
当你在研磨时,从边缘开始,轻轻地摩擦后角使干净。
5.确保刀尖与轴线对齐,并缓慢修复两侧的对称性。
当钻头的一边完成时,钻头的另一边必须加工,两边必须是对称的。
经验丰富的主人会在光线中看到钻头的对称性,慢慢地研磨。
钻头的后角一般为1014,后角太薄,钻头边缘太薄,振动大,孔是三角形或五角形,切削纤维形,后角小,钻头轴向力大,钻进困难,切削速度加快,钻头热毛严重,钻头不能钻。
背角适用于磨削,中心至中心,双刃对称,钻头间隙轻,无振动,孔径不会扩大。
6.经过双刃磨后,应仔细磨削直径较大的钻头。
经过双刃磨后,双刃刀尖会有一个平面,影响钻头的中心位置,需要扭转刀刃后面的角落,刀尖平面尽可能小。
麻花钻头的磨法【干货技巧】

麻花钻头的磨法内容来源网络,由“深圳机械展(11万㎡,1100多家展商,超10万观众)”收集整理!更多cnc加工中心、车铣磨钻床、线切割、数控刀具工具、工业机器人、非标自动化、数字化无人工厂、精密测量、3D打印、激光切割、钣金冲压折弯、精密零件加工等展示,就在深圳机械展.麻花钻头在切削工具中是最常用的一种,如果想要麻花钻头磨得锋利,那就得注意下面几点:麻花钻头在机械加工里面,算是最常用的一种钻孔工具,其结构简单,但是要想把钻头的刃磨得锋利,却不是件容易的事。
要想把麻花钻头的刃磨得锋利,那就一定要掌握刃磨的技巧和方法。
下面就是介绍麻花钻头手工刃磨技巧。
1、刃口要与砂轮面摆平首先,在磨钻头之前,找到钻头与砂轮的相对水平位置,也就是说钻头的主切削面与砂轮面的水平面,在刃口接触砂轮面的那一刻,要保证其钻头的整个刃口都能磨到。
钻头与砂轮的位置是磨刃的第一,位置摆放好后,钻头再慢慢地往砂轮上靠近。
2、钻头轴线要与砂轮面斜出60°的角角度不对,对钻头顶角的大小、主切削刃面、横刃斜角面造成最直接的影响。
所以钻头的轴线与砂轮表面取60°的角度即可。
这里有个要注意的事项:钻头刃磨的相对水平面与角度,这两者都要兼顾到,千万不可为了摆平刀刃忽略角度,反之也不行。
3、由刃口往后磨后面磨钻头刃口在接触砂轮后,从主切削面开始,缓慢的向后刀面往下磨,简而言之,就是先从钻头的刃口开始接触砂轮后,由刃头缓慢的向后刀面往下磨。
在开始磨刀刃的时候,可以先轻轻的接触砂轮,进行少量的刃磨,并且要注意观察打磨出来的火花的均匀性,以便调整手部压力,钻头的冷却程度也是不可忽视的,不能打磨的太过,否则会因打磨的太过,而造成刃口色变,至刃口退火。
另外,还值得注意的是,刃口温度太高时,钻头要即时进行冷却,否则将功亏一篑。
4、钻头的刃口要上下摆动,钻头尾部不能起翘在磨削钻头时我们手握钻头顶部,手在砂轮面进行均匀的上下摆动,握在柄部的手不仅不能随意摆动,还要防止后柄往上翘,其意思是,钻头的尾部不可高于砂轮的水平中心线上,否则会磨钝刃口,无法切削。
提高钻孔精度的小窍门
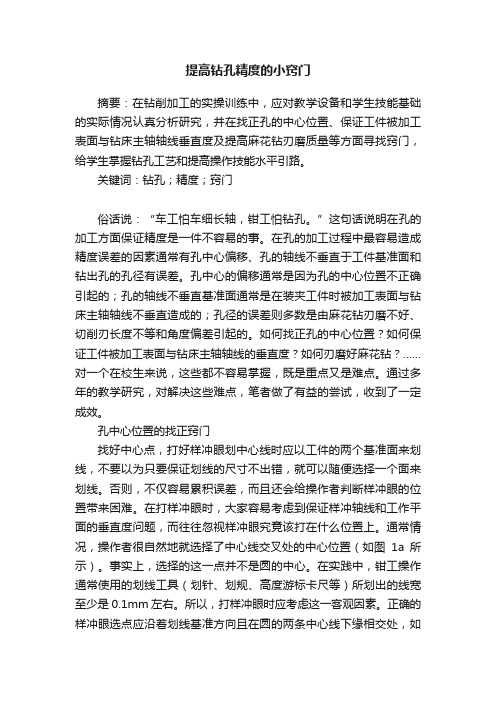
提高钻孔精度的小窍门摘要:在钻削加工的实操训练中,应对教学设备和学生技能基础的实际情况认真分析研究,并在找正孔的中心位置、保证工件被加工表面与钻床主轴轴线垂直度及提高麻花钻刃磨质量等方面寻找窍门,给学生掌握钻孔工艺和提高操作技能水平引路。
关键词:钻孔;精度;窍门俗话说:“车工怕车细长轴,钳工怕钻孔。
”这句话说明在孔的加工方面保证精度是一件不容易的事。
在孔的加工过程中最容易造成精度误差的因素通常有孔中心偏移、孔的轴线不垂直于工件基准面和钻出孔的孔径有误差。
孔中心的偏移通常是因为孔的中心位置不正确引起的;孔的轴线不垂直基准面通常是在装夹工件时被加工表面与钻床主轴轴线不垂直造成的;孔径的误差则多数是由麻花钻刃磨不好、切削刃长度不等和角度偏差引起的。
如何找正孔的中心位置?如何保证工件被加工表面与钻床主轴轴线的垂直度?如何刃磨好麻花钻?……对一个在校生来说,这些都不容易掌握,既是重点又是难点。
通过多年的教学研究,对解决这些难点,笔者做了有益的尝试,收到了一定成效。
孔中心位置的找正窍门找好中心点,打好样冲眼划中心线时应以工件的两个基准面来划线,不要以为只要保证划线的尺寸不出错,就可以随便选择一个面来划线。
否则,不仅容易累积误差,而且还会给操作者判断样冲眼的位置带来困难。
在打样冲眼时,大家容易考虑到保证样冲轴线和工作平面的垂直度问题,而往往忽视样冲眼究竟该打在什么位置上。
通常情况,操作者很自然地就选择了中心线交叉处的中心位置(如图1a所示)。
事实上,选择的这一点并不是圆的中心。
在实践中,钳工操作通常使用的划线工具(划针、划规、高度游标卡尺等)所划出的线宽至少是0.1mm 左右。
所以,打样冲眼时应考虑这一客观因素。
正确的样冲眼选点应沿着划线基准方向且在圆的两条中心线下缘相交处,如图1b所示。
选择有正确锥度的样冲打眼保证所使用的样冲有正确的锥度对初钻时的钻头定位是十分重要的。
在打样冲眼时千万别小看这个问题,更不应该随便在砂轮机上刃磨几下样冲就打眼了。
麻花钻加工方法
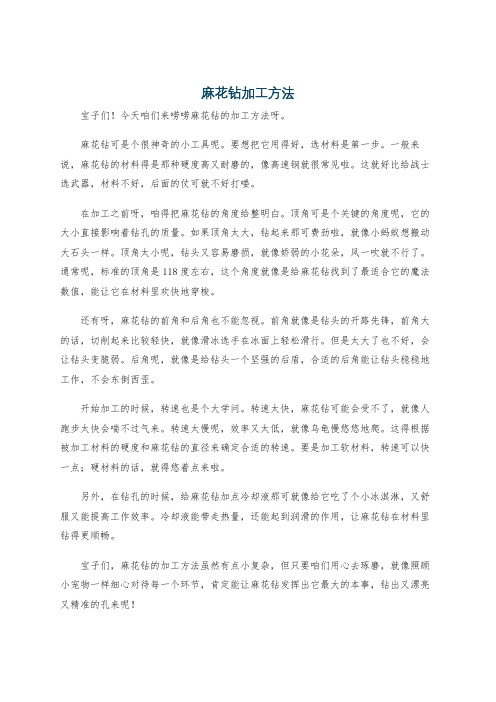
麻花钻加工方法宝子们!今天咱们来唠唠麻花钻的加工方法呀。
麻花钻可是个很神奇的小工具呢。
要想把它用得好,选材料是第一步。
一般来说,麻花钻的材料得是那种硬度高又耐磨的,像高速钢就很常见啦。
这就好比给战士选武器,材料不好,后面的仗可就不好打喽。
在加工之前呀,咱得把麻花钻的角度给整明白。
顶角可是个关键的角度呢,它的大小直接影响着钻孔的质量。
如果顶角太大,钻起来那可费劲啦,就像小蚂蚁想搬动大石头一样。
顶角太小呢,钻头又容易磨损,就像娇弱的小花朵,风一吹就不行了。
通常呢,标准的顶角是118度左右,这个角度就像是给麻花钻找到了最适合它的魔法数值,能让它在材料里欢快地穿梭。
还有呀,麻花钻的前角和后角也不能忽视。
前角就像是钻头的开路先锋,前角大的话,切削起来比较轻快,就像滑冰选手在冰面上轻松滑行。
但是太大了也不好,会让钻头变脆弱。
后角呢,就像是给钻头一个坚强的后盾,合适的后角能让钻头稳稳地工作,不会东倒西歪。
开始加工的时候,转速也是个大学问。
转速太快,麻花钻可能会受不了,就像人跑步太快会喘不过气来。
转速太慢呢,效率又太低,就像乌龟慢悠悠地爬。
这得根据被加工材料的硬度和麻花钻的直径来确定合适的转速。
要是加工软材料,转速可以快一点;硬材料的话,就得悠着点来啦。
另外,在钻孔的时候,给麻花钻加点冷却液那可就像给它吃了个小冰淇淋,又舒服又能提高工作效率。
冷却液能带走热量,还能起到润滑的作用,让麻花钻在材料里钻得更顺畅。
宝子们,麻花钻的加工方法虽然有点小复杂,但只要咱们用心去琢磨,就像照顾小宠物一样细心对待每一个环节,肯定能让麻花钻发挥出它最大的本事,钻出又漂亮又精准的孔来呢!。
麻花钻的磨法

如果有这方面的资料,特别是视频,就更好了!!
麻花钻对于机械加工来说,它是一种常用的钻孔工具。结构虽然简单,但要把它真正刃磨好,也不是一件轻松的事。关键在于掌握好刃磨的方法和技巧,方法掌握了,问题就会迎刃而解。我这里介绍一下对麻花钻的手工刃磨技巧。
麻花钻的顶角一般是118°,也可把它当作120°来看待。刃磨钻头主要掌握几个技巧:
1、刃口要与砂轮面摆平。
磨钻头前,先要将钻头的主切削刃与砂轮面放置在一个水平面上,也就是说,保证刃口接触砂轮面时,整个刃都要磨到。这是钻头与砂轮相对位置的第一步,位置摆好再慢慢°的角度。
3、由刃口往后磨后面。
刃口接触砂轮后,要从主切削刃往后面磨,也就是从钻头的刃口先开始接触砂轮,而后沿着整个后刀面缓慢往下磨。钻头切入时可轻轻接触砂轮,先进行较少量的刃磨,并注意观察火花的均匀性,及时调整手上压力大小,还要注意钻头的冷却,不能让其磨过火,造成刃口变色,而至刃口退火。发现刃口温度高时,要及时将钻头冷却。
当然,磨钻头没有一定的定式,需要在实际操作中积累经验,通过比较、观察、反复试验,定会把钻头磨得更好。
?
6、两刃磨好后,对直径大一些的钻头还要注意磨一下钻头锋尖。
钻头两刃磨好后,两刃锋尖处会有一个平面,影响钻头的中心定位,需要在刃后面倒一下角,把刃尖部的平面尽量磨小。方法是将钻头竖起,对准砂轮的角,在刃后面的根部,对着刃尖倒一个小槽。这也是钻头定中心和切削轻快的重要一点。注意在修磨刃尖倒角时,千万不能磨到主切削刃上,这样会使主切削刃的前角偏大,直接影响钻孔。
用一支过大后角的钻头和另一支过小后角的钻头让学生在台钻上试钻。学生会发现,过大后角的钻头在钻削时,孔口呈三
麻花钻钻孔中常见问题的原因和解决办法
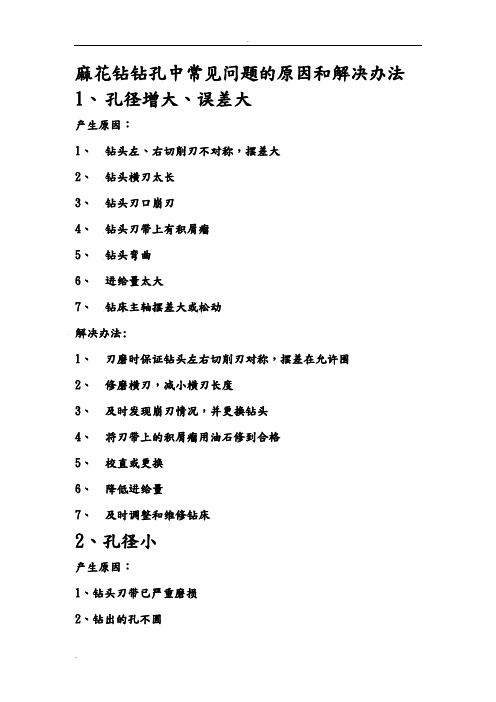
麻花钻钻孔中常见问题的原因和解决办法1、孔径增大、误差大产生原因:1、钻头左、右切削刃不对称,摆差大2、钻头横刃太长3、钻头刃口崩刃4、钻头刃带上有积屑瘤5、钻头弯曲6、进给量太大7、钻床主轴摆差大或松动解决办法:1、刃磨时保证钻头左右切削刃对称,摆差在允许围2、修磨横刃,减小横刃长度3、及时发现崩刃情况,并更换钻头4、将刃带上的积屑瘤用油石修到合格5、校直或更换6、降低进给量7、及时调整和维修钻床2、孔径小产生原因:1、钻头刃带已严重磨损2、钻出的孔不圆解决办法:1、更换合格钻头2、3、钻孔时产生振动或不圆产生原因:1、钻头后角太大2、无导向套或导向套与钻头配合间隙过大3、钻头左右切削刃不对称,摆差大4、主轴轴承松动5、工件夹紧不牢6、工件表面不平整,有气孔沙眼7、工件部有缺口,交叉孔解决办法:1、减小钻头后角2、钻杆伸出过长时必须有导向套,采用合适间隙的导向套或先大中心孔在钻孔3、刃磨时保证钻头左右切削刃对称,摆差在允许围4、调整或更换轴承5、改进夹具与定位装置6、更换合格毛坯7、改变工序顺序或改变工件结构4、孔位超差,孔歪斜产生原因:1、钻头的钻尖已磨钝2、钻头左右切削刃不对称,摆差大3、钻头横刃太长4、钻头与导向套配合间隙过大5、主轴与导向套中心线不同心,主轴与工作台面不垂直6、钻头在切削时振动7、工件表面不平整,有气孔砂眼8、工件部有缺口、交叉孔9、导向套低端面与工件表面间的距离远,导向套长度短10、工件夹紧不牢11、工件表面倾斜12、进给量不均匀解决办法:1、重磨钻头2、刃磨时保证钻头左右切削刃对称,摆差在允许围3、修磨横刃,减小横刃长度4、采用合适间隙的导向套5、校正机床夹具位置。
检查钻床主轴的垂直度6、先打中心孔再钻孔,采用导向套或改为工件回转的方式7、更换合格毛坯8、改变工序顺序或改变工件结构9、加长导向套长度10、改进夹具与定位装置11、正确定位安装12、使进给量均匀5、钻头折断产生原因:1、切削用量选择不当2、钻头崩刃3、钻头横刃太长4、钻头已钝,刃带严重磨损呈正锥形5、导向套底端面与工件表面间的距离太近,排屑困难6、切削液供应不足7、切屑堵塞钻头的螺旋槽,或切屑卷在钻头与导向套之间8、导向套磨损或成倒锥形,退刀时,钻屑夹在钻头与导向套之间9、快速行程终了位置距工件太近,快速行程转向工件进给时误差大10、孔钻通时,由于进给阻力迅速下降而进给量突然增加11、工件或夹具刚性不足,钻通孔时弹性恢复,使进给量突然增加12、进给丝杠磨损,动力头重锤重量不足。
锥柄麻花钻操作方法

锥柄麻花钻操作方法
锥柄麻花钻是一种常用的钻孔工具,主要用于木工、金属加工等行业。
下面是其基本操作方法:
1. 准备工作:选择适当的锥柄麻花钻头,并确认其长度和直径是否符合需求。
同时,确保工作台面平整、夹持工件稳固。
2. 固定麻花钻头:将麻花钻头的锥柄插入钻头夹持装置(如电钻等),并用扳手固定好。
3. 调节转速:根据工作材料的不同,选择合适的转速。
通常来说,对于木材而言,转速可适当较低;对于金属材料,转速则可适当较高。
4. 定位孔位:在工件上标出所需孔位,并用工具(如铅笔、刻线刀等)画出精确定位的线条。
5. 开始钻孔:将锥柄麻花钻头的刃部对准定位线条,用少量力气开始切入,保持垂直钻孔。
逐渐增加力度,用旋转的方式深入孔内。
6. 清理碎屑:钻孔时会产生大量木屑或金属屑,为保持进一步操作的清晰度,需要及时清理掉。
7. 钻孔完毕:当钻孔达到所需深度后,停止钻孔操作,等待钻头完全停止旋转。
将钻头缓慢从孔中拔出,避免损坏工件或钻头。
8. 锥孔处理:锥柄麻花钻钻孔后容易出现倒径现象,可使用锥形孔钻进行倒径修整,使钻孔底部成锥形,增加螺栓或螺钉的握力。
注意事项:
- 使用麻花钻时要佩戴工作手套和护目镜等个人防护设备,以免发生危险。
- 钻孔前要检查麻花钻头是否完好,如有损坏或变形应及时更换。
- 钻孔时要保持稳定的手部姿势和适当的力度,以免引起倒钻或其他安全问题。
- 钻孔前应先确定工件的材料和硬度,选择合适的转速和麻花钻头。
提高钻孔位置精度的方法
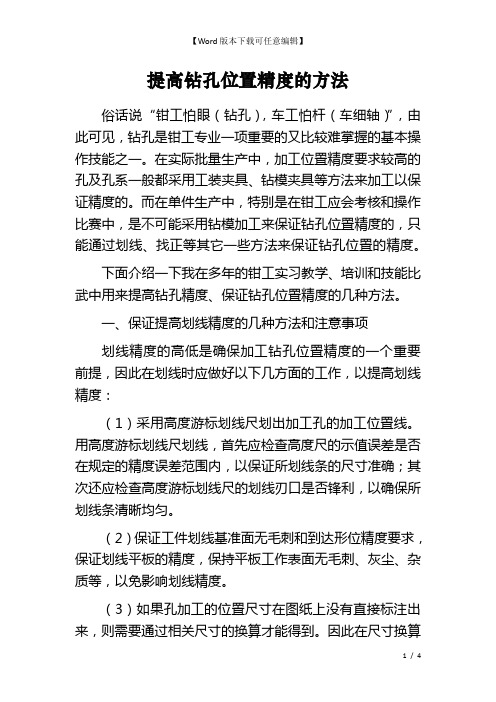
提高钻孔位置精度的方法俗话说“钳工怕眼(钻孔),车工怕杆(车细轴)”,由此可见,钻孔是钳工专业一项重要的又比较难掌握的基本操作技能之一。
在实际批量生产中,加工位置精度要求较高的孔及孔系一般都采用工装夹具、钻模夹具等方法来加工以保证精度的。
而在单件生产中,特别是在钳工应会考核和操作比赛中,是不可能采用钻模加工来保证钻孔位置精度的,只能通过划线、找正等其它一些方法来保证钻孔位置的精度。
下面介绍一下我在多年的钳工实习教学、培训和技能比武中用来提高钻孔精度、保证钻孔位置精度的几种方法。
一、保证提高划线精度的几种方法和注意事项划线精度的高低是确保加工钻孔位置精度的一个重要前提,因此在划线时应做好以下几方面的工作,以提高划线精度:(1)采用高度游标划线尺划出加工孔的加工位置线。
用高度游标划线尺划线,首先应检查高度尺的示值误差是否在规定的精度误差范围内,以保证所划线条的尺寸准确;其次还应检查高度游标划线尺的划线刃口是否锋利,以确保所划线条清晰均匀。
(2)保证工件划线基准面无毛刺和到达形位精度要求,保证划线平板的精度,保持平板工作表面无毛刺、灰尘、杂质等,以免影响划线精度。
(3)如果孔加工的位置尺寸在图纸上没有直接标注出来,则需要通过相关尺寸的换算才能得到。
因此在尺寸换算时,必须保存小数点后三位数,保证尺寸换算的准确性,提高划线精度。
(4)正确使用样冲。
样冲眼的作用是为钻孔或划圆弧起定心作用的,因此,对刃磨样冲的要求是非常高的,要求样冲头必须磨得圆而尖和有足够的硬度。
在敲击样冲眼时,首先是轻轻敲打,然后从多个方向观察所敲击的样冲眼是否偏离孔的十字中心线的交点,判断无误后,再将样冲眼加大,以保证钻孔时标准麻花钻准确地定心。
(5)划出检查孔位置精度的“检查圆”和“检查框”。
在孔加工时,可以根据工作实际需要选择这两种找正基准。
钻孔划线完毕后,一般都要划出比需要加工孔的直径大的“检查圆”,作为钻孔时的找正基准。
但是用划规划“检查圆”时容易产生误差,因此,可采用高度尺将孔的“检查圆”划成“检查框”,“检查框”的方格与孔的十字中心线的四个交点即为孔的找正基准点,这样可以保证钻孔的中心与样冲眼定位的中心重合,保证划线精度,也防止了划“检查园”的误差。
麻花钻钻孔参数

麻花钻,又称普通麻花钻,是一种常见的钻孔切削工具。
在加工过程中,选择合适的钻孔参数对于保证钻孔质量和效率具有重要意义。
以下是一些建议的麻花钻钻孔参数:
1. 切削液:选择合适的切削液可以降低摩擦、冷却钻头和工件,减少钻头磨损和热量积累。
常用的切削液有水基、油基和乳化液等。
2. 钻头材料:麻花钻的切削部分通常由高速钢、硬质合金或其他高性能材料制成。
不同材料的钻头适用于不同的工作条件和加工材料。
3. 钻头几何参数:
-前角γ:前角γ的大小会影响钻头的切削性能和耐用度。
通常,γ在15°-30°之间。
-后角ψ:后角ψ用于减少切削力和热量积累。
ψ在10°-15°之间。
-切削刃长度:切削刃长度影响钻孔质量和切削力。
根据加工条件和工件材料选择合适的切削刃长度。
4. 钻头直径:钻头直径是影响钻孔质量和切削力的关键参数。
根据工件的厚度和加工要求选择合适的钻头直径。
5. 转速:钻头的转速会影响切削力、热量积累和钻头磨损。
较高的转速可以提高切削效率,但容易导致钻头磨损。
根据工件材料和钻头性能选择合适的转速。
6. 进给速度:进给速度对钻孔质量和切削力有重要影响。
较高的进给速度可以提高加工效率,但容易导致钻头磨损和振动。
根据工件材料和钻头性能选择合适的进给速度。
7. 切削深度:切削深度会影响钻孔质量和切削力。
较小的切削深度可以提高钻孔质量,但降低加工效率。
根据工件厚度和加工要求选择合适的切削深度。
麻花钻头磨法图解
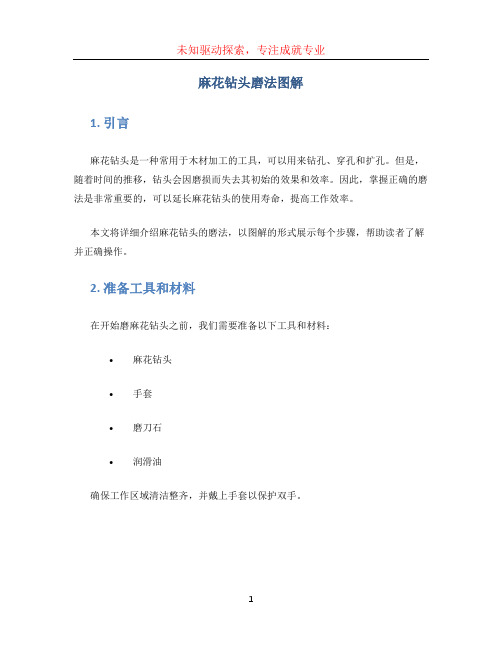
麻花钻头磨法图解1. 引言麻花钻头是一种常用于木材加工的工具,可以用来钻孔、穿孔和扩孔。
但是,随着时间的推移,钻头会因磨损而失去其初始的效果和效率。
因此,掌握正确的磨法是非常重要的,可以延长麻花钻头的使用寿命,提高工作效率。
本文将详细介绍麻花钻头的磨法,以图解的形式展示每个步骤,帮助读者了解并正确操作。
2. 准备工具和材料在开始磨麻花钻头之前,我们需要准备以下工具和材料:•麻花钻头•手套•磨刀石•润滑油确保工作区域清洁整齐,并戴上手套以保护双手。
3. 磨法步骤步骤1:清洁钻头使用清洁剂和刷子清洁钻头的表面,将灰尘和污垢清除干净。
确保钻头表面干净整洁,以便更容易进行磨削。
步骤1步骤1步骤2:确定刃口角度使用螺旋测微器测量钻头的刃口角度。
刃口角度是钻头切削效果的关键因素,不同的材料需要不同的刃口角度。
根据材料的硬度和钻孔要求来选择合适的刃口角度。
步骤2步骤2步骤3:开始磨削将麻花钻头定位于磨刀石上,用手握住钻头的柄部,以适当的角度将钻尖轻轻放在磨刀石上开始磨削。
确保钻尖与磨刀石保持稳定的接触,并用适度的力度进行磨削。
步骤3步骤3步骤4:创造新的尖角通过转动手腕,逐渐将钻头从磨刀石上移动,以创造一个新的尖角。
注意保持持续的刀尖接触,并控制好磨削的速度和力度。
步骤4步骤4步骤5:磨削两侧将钻头磨削至两侧呈对称形状。
使用相同的磨削技术,分别按图所示磨削钻头的两侧,以保持均匀的形状和尖锐的刃口。
步骤5步骤5步骤6:润滑擦拭使用润滑油和干净的布擦拭麻花钻头的表面,以去除磨削过程中产生的金属屑和残留物。
确保钻头表面干净,以防止金属屑对下次使用产生影响。
步骤6步骤64. 注意事项•在磨削钻头之前,要确保钻头的柄部没有损坏或变形,以免影响使用和磨削结果。
•磨刀石的选择很重要,应根据钻头的材料和硬度选择合适的磨刀石,以获得最佳的磨削效果。
•磨削过程中要均匀施加力量,以保持钻头的均匀磨削,避免过度磨削或不足磨削。
•定期检查和维护麻花钻头,包括清洁和磨削,以保持其最佳的使用寿命和工作效率。
麻花钻头磨法技巧
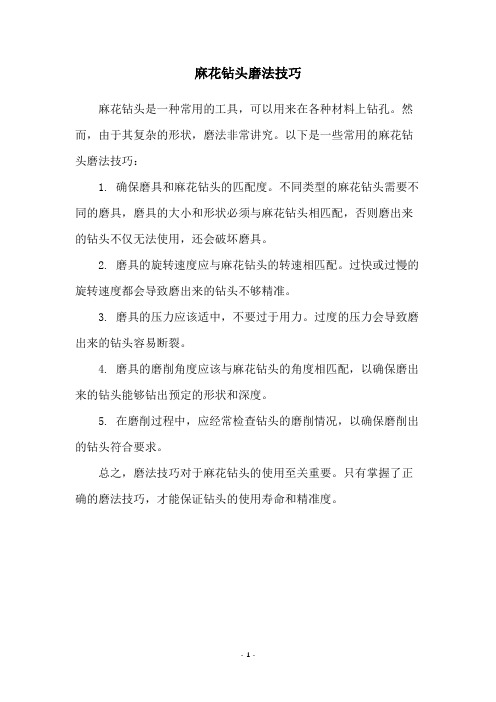
麻花钻头磨法技巧
麻花钻头是一种常用的工具,可以用来在各种材料上钻孔。
然而,由于其复杂的形状,磨法非常讲究。
以下是一些常用的麻花钻头磨法技巧:
1. 确保磨具和麻花钻头的匹配度。
不同类型的麻花钻头需要不同的磨具,磨具的大小和形状必须与麻花钻头相匹配,否则磨出来的钻头不仅无法使用,还会破坏磨具。
2. 磨具的旋转速度应与麻花钻头的转速相匹配。
过快或过慢的旋转速度都会导致磨出来的钻头不够精准。
3. 磨具的压力应该适中,不要过于用力。
过度的压力会导致磨出来的钻头容易断裂。
4. 磨具的磨削角度应该与麻花钻头的角度相匹配,以确保磨出来的钻头能够钻出预定的形状和深度。
5. 在磨削过程中,应经常检查钻头的磨削情况,以确保磨削出的钻头符合要求。
总之,磨法技巧对于麻花钻头的使用至关重要。
只有掌握了正确的磨法技巧,才能保证钻头的使用寿命和精准度。
- 1 -。
麻花钻头的磨法麻花钻头磨法图解

麻花钻头的磨法麻花钻头磨法图解.标准麻花钻的修磨方法1、修磨横刃(1)磨去横刃,形成新的切削刃(鱼嘴形)。
修磨后加大该处前角,使轴向力大大降低。
但这种刃形切削时定心不好,钻孔精度差;且钻心强度减弱,易崩刃。
只用于钻铸铁等强度低的材料,一般少用。
(2)十字形刃磨,横刃长度不变,修磨处加大横刃前角,但钻心强度减弱,不宜加工硬质材料,主要用于钻深孔。
它须用专用夹具刃磨。
法。
麻花钻头的磨法:1.“刃口摆平轮面靠。
”这是钻头与砂轮相对位置的第一步,往往有学生还没有把刃口摆平就靠在砂轮上开始刃磨了。
这样肯定是磨不好的。
这里的“刃口”是主切削刃,“摆平”是指被刃磨部分的主切削刃处于水平位置。
“轮面”是指砂轮的表面。
“靠”是慢慢靠拢的意思。
此时钻头还不能接触砂轮。
2.“钻轴斜放出锋角。
”这里是指钻头轴心线与砂轮表面之间的位置关系。
“锋角”即顶角118°±2o的一半,约为60°这个位置很重要,直接影响钻头顶角大小及主切削刃形状和横刃斜角。
要提示学生记忆常用的一块30°、60°、90°三角板中60°的角度,学生便于掌握。
口诀一和口诀二都是指钻头刃磨前的相对位置,二者要统筹兼顾,不要为了摆平刃口而忽略了摆好斜角,或为了摆好斜放轴线而忽略了摆平刃口。
在实际操作中往往很会出这些错误。
此时钻头在位置正确的情况下准备接触砂轮。
3.“由刃向背磨后面。
”这里是指从钻头的刃口开始沿着整个后刀面缓慢刃磨。
这样便于散热和刃磨。
在稳定巩固口诀一、二的基础上,此时钻头可轻轻接触砂轮,进行较少量的刃磨,刃磨时要观察火花的均匀性,要及时调整压力大小,并注意钻头的冷却。
当冷却后重新开始刃磨时,要继续摆好口诀一、二的位置,这一点往往在初学时不易掌握,常常会不由自主地改变其位置的正确性。
4.“上下摆动尾别翘。
”这个动作在钻头刃磨过程中也很重要,往往有学生在刃磨时把“上下摆动”变成了“上下转动”,使钻头的另一主刀刃被破坏。
钻削精孔的方法
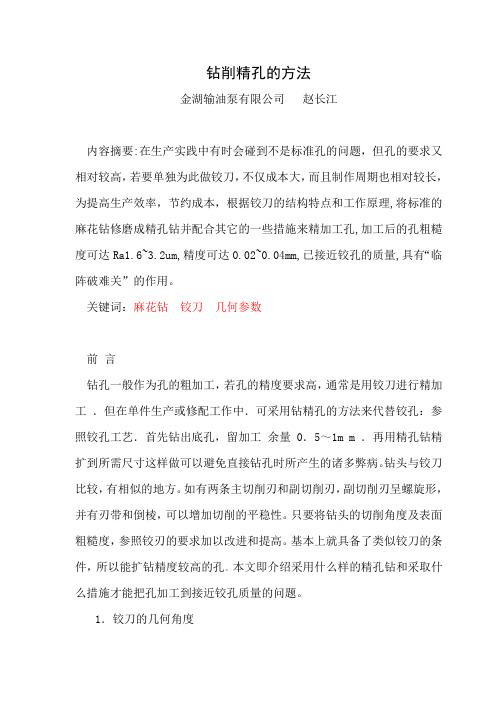
钻削精孔的方法金湖输油泵有限公司赵长江内容摘要:在生产实践中有时会碰到不是标准孔的问题,但孔的要求又相对较高,若要单独为此做铰刀,不仅成本大,而且制作周期也相对较长,为提高生产效率,节约成本,根据铰刀的结构特点和工作原理,将标准的麻花钻修磨成精孔钻并配合其它的一些措施来精加工孔,加工后的孔粗糙度可达Ra1.6~3.2um,精度可达0.02~0.04mm,已接近铰孔的质量,具有“临阵破难关”的作用。
关键词:麻花钻铰刀几何参数前言钻孔一般作为孔的粗加工,若孔的精度要求高,通常是用铰刀进行精加工.但在单件生产或修配工作中.可采用钻精孔的方法来代替铰孔:参照铰孔工艺.首先钻出底孔,留加工余量 0.5~1m m .再用精孔钻精扩到所需尺寸这样做可以避免直接钻孔时所产生的诸多弊病。
钻头与铰刀比较,有相似的地方。
如有两条主切削刃和副切削刃,副切削刃呈螺旋形,并有刃带和倒棱,可以增加切削的平稳性。
只要将钻头的切削角度及表面粗糙度,参照铰刃的要求加以改进和提高。
基本上就具备了类似铰刀的条件,所以能扩钻精度较高的孔。
本文即介绍采用什么样的精孔钻和采取什么措施才能把孔加工到接近铰孔质量的问题。
1.铰刀的几何角度(1)主偏角κr 主偏角愈小,铰刀受到的轴向力愈小,导向性愈好,但κr过小时,铰削时挤压摩擦较大,铰刀耐用度低,切入、切出时间长。
故手用铰刀选择较小的主偏角,以减轻工人劳动强度和获得良好导向性,而机用铰刀选择较大的主偏角,以减少切削刃长度和机动时间,加工铸铁取κr=3°~5°;加工钢料取κr=12°~15°;加工盲孔取κr=45°。
(2)前角γр铰刀的前角规定在切深剖面(即铰刀的端剖面)内表示。
铰削时,由于切屑与前面在切削刃附近处接触,切削厚度较小,故前角对切削变形的影响并不显著。
为便于制造,通常高速钢铰刀在精加工时取γр=O°;粗铰塑性材料时取γр=5°~10°。
谈巧用麻花钻加工精孔的操作

刃。
成粗 、 精加 工 的联合 切 削刃 , 少 切 削厚 度 和 切 削 变 减
麻 花钻 钻扩 孔 是经 改磨 过 的钻 头 在 已有 孔 的基
础 上 , 经扩 钻 加工 的 一种 精加 工 孔 的操作 , 再 简称 钻
形 , 高修 光 能 力 , 善 散 热 条 件 , 利 于 提 高 孔 的 提 改 有
麻花钻加工精孔的探索与研究
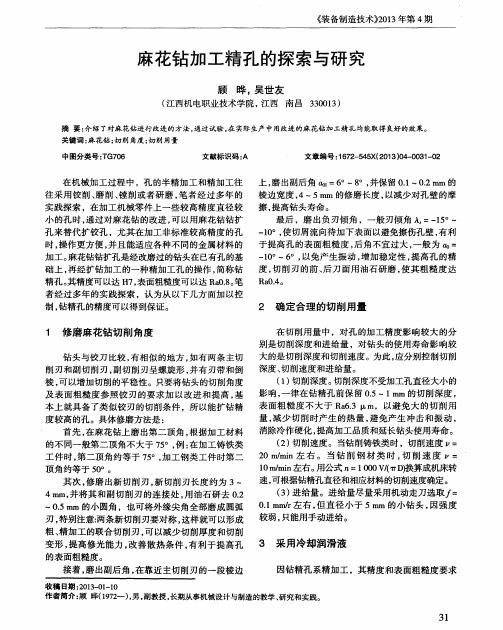
在切 削用 量 中 ,对孔 的加 工 精度 影 响 较 大 的分
别是切削深度和进 给量 ,对钻头 的使用寿命影响较 大 的是切 削深 度和 切 削速 度 。为此 , 应 分别 控制 切 削 深度 、 切 削 速度 和进 给量 。 ( 1 ) 切削深度。 切削深度不受加工孔直径大小 的 影响 , 一律在钻精孔前保 留 0 . 5 1 r f l n l 的切削深度 , 表面粗糙度不 大于 R a 6 - 3 m,以避免大 的切 削用 量, 减少切削时产生 的热量 , 避免产生冲击和振 动 , 消除冷作 硬化 , 提高加工品质和延长钻头使用寿命 。 ( 2 ) 切削速度。当钻削铸铁类时 ,切削速度 = 2 0 m / mi n左 右 。 当 钻 削 钢 材 类 时 , 切 削 速 度 = 1 0 m / m i n 左右 。 用公式 n =1 0 0 0 V D 腆 算成机床转 速, 可 根据钻 精孔 直径 和相应材料 的切削 速度确定 。
关键词 : 麻花钻 ; 切 削角度 ; 切 削 用量
中图分类号 : T G 7 0 6
文献标 识码 : A
文章编号 : 1 6 7 2 — 5 4 5 X( 2 0 1 3) 0 4 - 0 0 3 1 — 0 2
在机械加工过程 中,孔的半精加工和精加工往 上, 磨 出副后角 a o 。 =6 。 ~8 。, 并保 留 0 . 1 — 0 . 2 m m的 往采用铰 削、 磨削 、 镗削或者研磨 , 笔者经过多年 的 棱边宽度 , 4 —5 n l l n的修磨长度 , 以减少对孔 壁的摩 实践探索 ,在加工机械零件上一些较高精度直径较 擦 , 提高钻头寿命 。 小 的孔 时 , 通 过 对麻 花钻 的改 进 , 可 以用麻 花 钻 钻 扩 最后 ,磨 出负刃倾角 ,一般刃倾角 A =一 1 5 。 ~ 孔来替代扩铰孔 ,尤其在加工非标准较高精度的孔 1 o o, 使切屑流向待加下表面以避免擦伤孔壁 , 有利 时, 操作更方便 , 并且能适应各种不同的金属材料 的 于提 高 孔 的 表 面 粗 糙 度 , 后角不宜过大 , 一般为 a o = 加工 。 麻 花钻 钻扩孔 是 经改磨 过 的钻 头在 已有孔 的基 1 0 。 ~ 6 。, 以免产生振动 , 增加稳定性 , 提高孔的精 础上 , 再经扩钻加工的一种精加工孔 的操作 , 简称钻 度 , 切削刃 的前 、 后刀面用油石研磨 , 使其粗糙度 达 O. 4 精孔 。 其精度可以达 H 7 , 表面粗糙度可 以达 R a 0 . 8 。 笔 Ra 者经过多年的实践探索 ,认为从 以下几方面加以控 制, 钻精 孔 的精度 可 以得 到保 证 。 2 确定合理 的切削用量
谈巧用麻花钻加工精孔的操作

振动 , 消除冷作硬化 , 提高加工质量 和延 长钻头使用寿
命。
切削速 度 : 削铸铁类 时 , 削速度 V= 0 m mn 钻 切 2m / i 左右 。钻削 钢材类 时 , 削速度 V:1m / i 右。 切 0 m m n左
全部磨成圆弧刃 。 特别注意 : 条新切 削刃要对 称 , 两 这 样 就可以形成粗 、 加工的联合切削刃 , 精 减少切 削厚度 和切削变形 , 提高 修光 能力 , 善散热 条件 , 改 有利 于提
Ra 4 0.
2 确 定合 理 的切 削用量
在切 削用量中 , 对孔 精度 影响较 大 的分别 是切 削 深度 和进 给量 , 对钻 头 的使 用 寿命 影 响较大 的是切 削
深度 和切 削速度 。为此 , 分别控 制切削深度 、 削速 应 切 度 和进 给量 。 切削深度 : 受加工 孔 直径 大小 的影 响 , 不 一律在 钻精 孔前保 留 0 5~1 m的切 削深度 , . m 粗糙度 不大 于 R . , a 3 以避免 大切 削量 , 6 减少 热量 , 避免 产生 冲击 和
高钻 头寿命 。 磨 出负刃倾 角。一般 刃倾 角 l …1 1 。使 = 0 5, 切 屑流向待加 工表 面 以避 免擦 伤孔壁 , 有利于 提高孔 的表 面粗糙 度。后 角不宜过 大 , 一般 为 a 6 一一1。 =。 O, 以免 产生振 动 , 增加稳定性 , 提高孔的精度 。 切削刃的前 、 刀 面用 油 石研 磨 , 后 使其 粗 糙 度 达
作者简 介: 刘真水 , , 男 山东济宁人 , 现任济宁市太平煤 矿开拓 一 区
机 电 区长 。
为新风 门密 闭好 漏风 量小 , 效 的保证 了 3 1采煤 工 有 0 作面正常生产 , 个 月累计 多出原煤 12万 t 8 . 。
- 1、下载文档前请自行甄别文档内容的完整性,平台不提供额外的编辑、内容补充、找答案等附加服务。
- 2、"仅部分预览"的文档,不可在线预览部分如存在完整性等问题,可反馈申请退款(可完整预览的文档不适用该条件!)。
- 3、如文档侵犯您的权益,请联系客服反馈,我们会尽快为您处理(人工客服工作时间:9:00-18:30)。
想知道麻花钻加工精孔的妙招吗?
在加工机械零件上的一些较高精度的孔时,可以用麻花钻钻扩孔来替代扩铰孔,尤其在加工非标准精孔时,就显得操作更方便,能适应各种不同的金属材料的加工。
麻花钻钻扩孔是经改磨过的钻头在已有孔的基础上,再经扩钻加工的一种精加工孔的操作,简称钻精孔。
其精度达H7,表面粗糙度达Ra0.8。
一般由于操作者在操作时不得法,钻出的孔精度偏低。
笔者经过多年的实践操作,至佳刀具认为从以下几方面加以控制。
钻精孔的精度会得以保证。
1、正确刃磨切削角度及提高表面粗糙度:麻花钻与铰刀比较,有相似的地方。
如有两条主切削刃和副切削刃,副切削刃呈螺旋形,并有刃带和倒棱,可以增加切削的平稳性。
只要将钻头的切削角度及表面粗糙度,参照铰刃的要求加以改进和提高。
基本上就具备了类似铰刃的条件,所以能扩钻精度较高的孔。
磨出第二顶角(22)。
根据加工材料的不同一般2≤75°。
2、确定合理的切削用量在切削用量中,对孔精度影响较大的分别是切削深度和进给量,对麻花钻的使用寿命影响较大的是切削深度和切削速度。
为此,应分别控制切削深度、切削速度和进给量。
切削深度:不受加工孔直径大小的影响,一律在钻精孔前保留0.5~1mm的切削深度,粗糙度不大于Ra6.3,以避免大切削量,减少热量,避免产生冲击和振动,消除冷作硬化,提高加工质量和延长钻头使用寿命。
3、冷却润滑液:因钻精孔系精加工,其精度和表面粗糙度都较高,并且切削负荷小,故应选择以润滑为主的冷却润滑液。
采用10%~20%的乳化油水溶液。
4、其它要求:选用精度比较高的钻床,若钻床主轴径向圆跳动误差较大时,可采用浮动夹头来装夹钻头加工。
使用较新或各部分尺寸精度接近公差要求的麻花钻。
因钻头多次使用后会磨损,而影响孔径精度。
钻头的两个切削刃需尽量修磨对称,两刃的轴向摆差应控制在0.05mm范围内,使两刃负荷均匀,以提高切削稳定性,钻头的径向摆差应小于0.03mm。