制取高纯一氧化碳气体的低、常温脱除有机硫工艺
高纯度一氧化碳的生产

高纯度一氧化碳的生产工艺一氧化碳是C1化学的基础原料,主要用于合成甲醇、甲醛、脂肪酸、脂肪酐、光气、异氰酸酯、碳酸二甲酯以及各种金属羰基化合物。
用于化工合成的高纯度一氧化碳可以从含有一氧化碳的天然气和石油转化的合成气、水煤气、半水煤气以及钢铁厂、电石厂和黄磷厂的尾气中纯化分离;亦可以甲醇为原料,通过催化裂解、变压吸附等工艺制取,同时副产氢气。
一、一氧化碳的生产工艺1 煤炭和天然气法该方法以自然资源煤炭、天然气等为原料通过气化、羰基化等工艺过程来合成一氧化碳,然后根据生产中对一氧化碳的纯度要求进行分离、提纯,得到各种含量的一氧化碳。
该工艺目前广泛应用于甲醇、醋酸等脂肪族化合物以及其衍生物的生产。
2 甲醇裂解制一氧化碳(1)工艺原理甲醇在专用催化剂作用和280℃下发生催化裂解,得到一氧化碳、二氧化碳和氢气等混合气体,经过变压吸附工艺(PSA)分离后可得到高纯度一氧化碳和氢气。
反应式为:CH3OH →CO+2H2 -90.7KJ/mol(2)工艺流程甲醇经预热、汽化、过热后在专用催化剂上进行裂解反应,裂解气经冷却、冷凝后其组成为H2 ~66%,CO2 -4.5%,CO ~31.8%,该裂解气进行压缩后在PSA-I吸附塔上脱碳后得到含氢气、一氧化碳的净化气体,然后在PSA-II吸附塔上分别得到含量≥98%的一氧化碳,并副产氢气。
根据下游产品对一氧化碳纯度的需要,可以通过进一步的变压吸附操作,将一氧化碳的纯度提高至99.99%。
工艺流程可表示如下:二、一氧化碳的提纯工艺无论是用甲醇裂解工艺生产一氧化碳,还是以黄磷尾气、转炉气、高炉气等为原料分离、纯化一氧化碳,其原料气都是若干种气体的混合物,都必须经过提纯后才可以得到各种纯度的一氧化碳以满足下游产品的生产需要。
一氧化碳虽然是C1化学的基础原料气,具有广泛的用途,但提纯方法不多,以往国内采用精馏法或COSORB法提纯CO。
但这两种方法的预处理系统复杂,设备多,投资大,操作成本高,效果不理想。
粗原料气的净化—硫化物的脱除(合成氨生产)

由脱随塔流出的富液,送至脱硫闪蒸槽而后进人H2S提浓塔,塔顶进液 为脱硫贫液,中部进液为脱硫富液。在H2S提浓塔后还有一个闪蒸槽。 闪 蒸气压缩后作为H2S提浓塔的气提气。由H2S提浓塔出来的气体含H2S25% 左右,可直接送至克劳斯法制硫装置。由脱碳闪蒸槽出来的闪蒸气含CO2 99%左右,可作尿素生产原料之用。
本书仅对近年来备受人们关注的Slexol怯(中国称为NHD法)脱硫作简介。此法 1965 年首先由美国Alied Chenical公司采用,至今已有 40多套装置在各国运 行。脱硫剂的主体成分为聚乙二醇二甲醒,商品名为Selexol。它是一种聚乙 二醇二甲醚同系物混合体。分子式为CH3O CH-O- CH2 nCH。 式中n为3-9。 平均相对分子质量为22-242。各种同系物的质量分数,%大致如下。
3、脱硫剂活性好,容易再生,定额消耗低
脱硫剂活性好,容易再生,可以降低生产的费用,符合工业生 产的经济性。
4、不易发生硫堵
硫堵:进脱硫塔气体的成分不好,杂志耗量较高;反应时析出的 硫不能及时排出;脱硫塔淋喷密度不够;再生空气量不足,吹风强度 低等原因造成硫堵。
5、脱硫剂价廉易得
采用最多的是廉价的石灰、石灰石和用石灰质药剂配制的碱性溶 液。以提高生产的经济性。
酞菁钴价格昂贵,但用量很少,脱硫液中PDS含量仅在数十个cm3/ m3左右。PDS的吨氨耗量一般在1.3-2.5g左右,因而运行的经济效益也较 显著。
此法也可脱除部分有机硫。若脱硫液中存在大量的氰化物,仍能导致 PDS中毒,但约经60h靠其自身的排毒作用,其脱硫活性可以逐渐恢复。 PDS对人体无毒,不会发生设备硫堵,无腐蚀性。
再
较高的温度有利于硫磺的分离,使析出的硫易于凝聚,
生
关于天然气脱硫脱碳工艺的选择分析
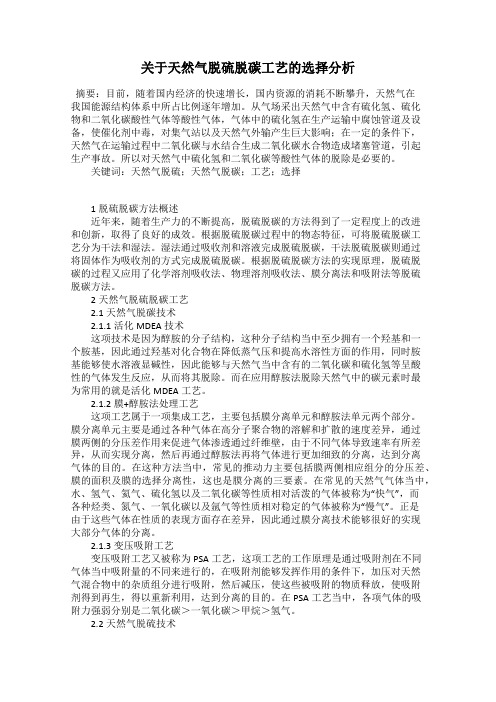
关于天然气脱硫脱碳工艺的选择分析摘要:目前,随着国内经济的快速增长,国内资源的消耗不断攀升,天然气在我国能源结构体系中所占比例逐年增加。
从气场采出天然气中含有硫化氢、硫化物和二氧化碳酸性气体等酸性气体,气体中的硫化氢在生产运输中腐蚀管道及设备,使催化剂中毒,对集气站以及天然气外输产生巨大影响;在一定的条件下,天然气在运输过程中二氧化碳与水结合生成二氧化碳水合物造成堵塞管道,引起生产事故。
所以对天然气中硫化氢和二氧化碳等酸性气体的脱除是必要的。
关键词:天然气脱硫;天然气脱碳;工艺;选择1脱硫脱碳方法概述近年来,随着生产力的不断提高,脱硫脱碳的方法得到了一定程度上的改进和创新,取得了良好的成效。
根据脱硫脱碳过程中的物态特征,可将脱硫脱碳工艺分为干法和湿法。
湿法通过吸收剂和溶液完成脱硫脱碳,干法脱硫脱碳则通过将固体作为吸收剂的方式完成脱硫脱碳。
根据脱硫脱碳方法的实现原理,脱硫脱碳的过程又应用了化学溶剂吸收法、物理溶剂吸收法、膜分离法和吸附法等脱硫脱碳方法。
2天然气脱硫脱碳工艺2.1天然气脱碳技术2.1.1活化MDEA技术这项技术是因为醇胺的分子结构,这种分子结构当中至少拥有一个羟基和一个胺基,因此通过羟基对化合物在降低蒸气压和提高水溶性方面的作用,同时胺基能够使水溶液显碱性,因此能够与天然气当中含有的二氧化碳和硫化氢等呈酸性的气体发生反应,从而将其脱除。
而在应用醇胺法脱除天然气中的碳元素时最为常用的就是活化MDEA工艺。
2.1.2膜+醇胺法处理工艺这项工艺属于一项集成工艺,主要包括膜分离单元和醇胺法单元两个部分。
膜分离单元主要是通过各种气体在高分子聚合物的溶解和扩散的速度差异,通过膜两侧的分压差作用来促进气体渗透通过纤维壁,由于不同气体导致速率有所差异,从而实现分离,然后再通过醇胺法再将气体进行更加细致的分离,达到分离气体的目的。
在这种方法当中,常见的推动力主要包括膜两侧相应组分的分压差、膜的面积及膜的选择分离性,这也是膜分离的三要素。
高纯一氧化碳的制造方法
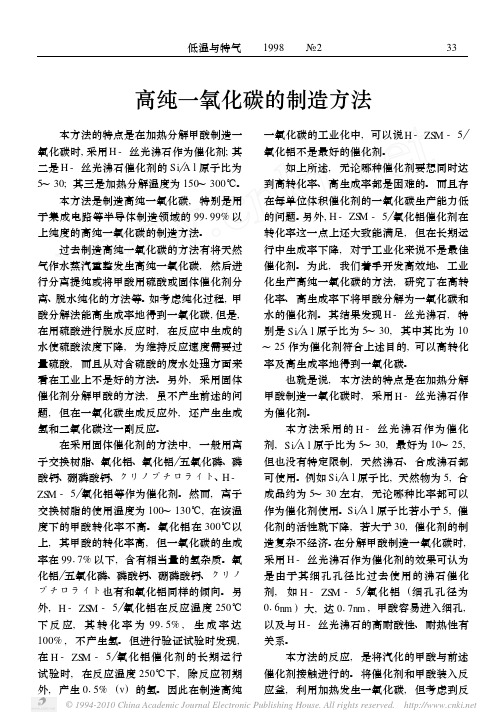
子交换树脂、氧化铝、氧化铝 五氧化磷、磷 但也没有特定限制, 天然沸石、 合成沸石都
酸钙、硼磷酸钙、
•
、H -
可使用。例如 Si A l 原子比, 天然物为 5, 合
ZSM - 5 氧化铝等作为催化剂。然而, 离子 成品约为 5~ 30 左右, 无论哪种比率都可以
交换树脂的使用温度为 100~ 130℃, 在该温 作为催化剂使用。Si A l 原子比若小于 5, 催
6 结 论
含 量
991999 0127 019 110 019 < 011 < 011 019
本方法是从含有低沸点和高沸点成分的 粗 B 2H 6 中制取高纯 B 2H 6, 通过选择吸附与 B 2H 6 沸点接近的难以用蒸馏法分离的微量 CO 2、C2H 6 等杂质和蒸馏法组合, 制取高纯 B 2H 6。
在本反应生产的一氧化碳中含有水及微 量氢、 二氧化碳杂质, 可用众所周知的方法 的组合对该气体进行提纯得到高纯一氧化 碳。 如用稀释的氢氧化钠溶液洗净除去残留 的微量未反应的甲酸和二氧化碳后, 再经干 燥除水可得到高纯一氧化碳。 其纯度可达到 99199% 以上, 可用在半导体制造领域及其它 用途。 本方法使用的反应器的材质一定要不 受甲酸及一氧化碳的腐蚀, 而且对反应没有 影响。 可使用满足该要求的铝、 钛、 锆、 碳 等材质。
焦炉气制甲醇工艺中硫化物的脱除
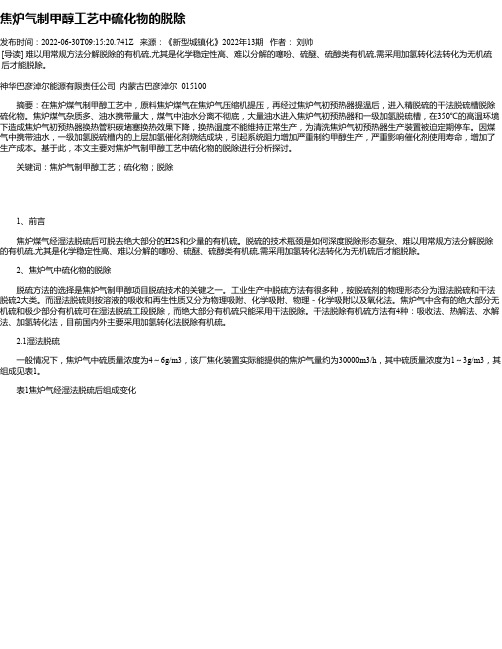
焦炉气制甲醇工艺中硫化物的脱除发布时间:2022-06-30T09:15:20.741Z 来源:《新型城镇化》2022年13期作者:刘帅[导读] 难以用常规方法分解脱除的有机硫,尤其是化学稳定性高、难以分解的噻吩、硫醚、硫醇类有机硫,需采用加氢转化法转化为无机硫后才能脱除。
神华巴彦淖尔能源有限责任公司内蒙古巴彦淖尔 015100摘要:在焦炉煤气制甲醇工艺中,原料焦炉煤气在焦炉气压缩机提压,再经过焦炉气初预热器提温后,进入精脱硫的干法脱硫槽脱除硫化物。
焦炉煤气杂质多、油水携带量大,煤气中油水分离不彻底,大量油水进入焦炉气初预热器和一级加氢脱硫槽,在350℃的高温环境下造成焦炉气初预热器换热管积碳堵塞换热效果下降,换热温度不能维持正常生产,为清洗焦炉气初预热器生产装置被迫定期停车。
因煤气中携带油水,一级加氢脱硫槽内的上层加氢催化剂烧结成块,引起系统阻力增加严重制约甲醇生产,严重影响催化剂使用寿命,增加了生产成本。
基于此,本文主要对焦炉气制甲醇工艺中硫化物的脱除进行分析探讨。
关键词:焦炉气制甲醇工艺;硫化物;脱除1、前言焦炉煤气经湿法脱硫后可脱去绝大部分的H2S和少量的有机硫。
脱硫的技术瓶颈是如何深度脱除形态复杂、难以用常规方法分解脱除的有机硫,尤其是化学稳定性高、难以分解的噻吩、硫醚、硫醇类有机硫,需采用加氢转化法转化为无机硫后才能脱除。
2、焦炉气中硫化物的脱除脱硫方法的选择是焦炉气制甲醇项目脱硫技术的关键之一。
工业生产中脱硫方法有很多种,按脱硫剂的物理形态分为湿法脱硫和干法脱硫2大类。
而湿法脱硫则按溶液的吸收和再生性质又分为物理吸附、化学吸附、物理-化学吸附以及氧化法。
焦炉气中含有的绝大部分无机硫和极少部分有机硫可在湿法脱硫工段脱除,而绝大部分有机硫只能采用干法脱除。
干法脱除有机硫方法有4种:吸收法、热解法、水解法、加氢转化法,目前国内外主要采用加氢转化法脱除有机硫。
2.1湿法脱硫一般情况下,焦炉气中硫质量浓度为4~6g/m3,该厂焦化装置实际能提供的焦炉气量约为30000m3/h,其中硫质量浓度为1~3g/m3,其组成见表1。
化工工艺学教学课件--第五章 脱硫与脱碳

(4)聚乙二醇二甲醚法
使用的吸收溶剂是经筛选后的聚乙二醇二甲 醚n=的2~同9。系该物同,系分物子能式选为择CH性3O地(C脱2H除4O气)n体CH中3,式的中 CO2和H2S,无毒且能耗较低。
2、化学吸收法
(1)氨水法
是最原始的一种方法,在我国小氮肥厂,用 浓氨水吸收二氧化碳生产碳酸氢铵,因工艺简 单,脱碳成本低,还有不少小化肥厂使用此法。
活性成分为MoS2,其次
Co9S8
(3)干法脱硫的优缺点
优点:具有极强的脱除有机硫和无机硫能力, 气体净化度高。
缺点:脱硫剂再生困难或不能再生,不适用于 脱除大量无机硫,所以只能用于气态烃、石脑 油及合成气的精细脱硫。
4、湿法脱硫
湿法脱硫是在吸收塔中用液体吸收剂(脱硫剂)吸 收煤气中的硫化氢,而后再将吸收剂再生,再生后的吸 收剂再送回吸收塔中循环使用。
第五章 脱硫与脱碳
各种方法制得的原料气在送去合成氨之前都需经过 净化,以出去其中的有害杂质,如硫化物、CO和CO2等。 净化过程主要包括脱硫、CO变换和脱除CO2和少量CO。 一、脱硫 二、二氧化碳脱除 三、少量一氧化碳脱除
一、脱硫
按分子结构
硫
无机硫 有机硫
存在形式
硫铁矿硫
硫化氢
无机硫90%
硫酸盐硫 脂肪硫 芳香硫
③特点
★溶剂在低温下对CO2、H2S、COS等酸性气体吸收能力 极强,溶液循环量小,功耗少。 ★溶剂不氧化、不降解,有很好的化学和热稳定性。 ★净化气质量好,净化度高,CO2<20ppm,H2S<0.1ppm。 ★溶剂不起泡。 ★具有选择性吸收H2S、COS和CO2的特性,可分开脱除 和再生。 ★溶剂廉价易得,但甲醇有毒,对操作和维修要求严格。 ★该工艺技术成熟,目前全世界约有87套大中型工业化 装置。
制备高纯一氧化碳的新方法

工艺与设备制备高纯一氧化碳的新方法姚永纯(化工部光明化工研究设计院 大连 116031)介绍了三种较新的高纯一氧化碳制备方法及其特点,展望了今后的发展趋势。
关键词:一氧化碳 制备 催化剂1 前 言如今,CO已成为合成多种化工产品的重要原料,尤其是以CO为基本原料的有机合成化学的研究已引起人们的极大关注。
由高纯CO合成的产品包括甲醇、甲醛、醋酸、醋酸酐、异氰酸酯、碳酸二甲酯、草酸二乙酯、二甲基甲酰胺和农药除草剂等。
有些正以工业规模生产,有些已列入计划,准备生产。
由于工业发展和羰基合成的需要,对CO 的需求,无论在数量上还是在质量上都有了更高的要求,高效经济地合成高纯CO的方法对C1化学及羰基合成工业的发展具有十分重要的理论意义和现实意义。
传统的合成方法已不能满足现代工业的要求,以浓H2SO4作脱水剂的甲酸分解法〔1〕虽产品纯度较高,但设备腐蚀严重,废酸处理麻烦;焦炭不完全燃烧法和木炭干冰法〔2〕虽成本较低,但产品纯度低,杂质成分复杂,难以得到高纯产品。
近年来,在CO领域,各国科学工作者做了大量工作,新的生产方法也不断涌现。
2 制备新方法〔3~5〕2.1 甲酸催化法该法采用H-丝光沸石作为催化剂(Si/ Al原子比为5~30,最好为10~25)在150~300℃温度条件下,将甲酸蒸气通入充填催化剂的塔内进行反应。
得到的一氧化碳中含有水及微量氢、二氧化碳杂质,用氢氧化钠溶液洗净,除去微量残存的未反应的甲酸和二氧化碳后,再经干燥除水可得到99.99%的高纯CO。
本法的甲酸的转化率达99.9%,一氧化碳的生成率为99.99%。
特点:催化剂H-丝光沸石的活性可长期保持,反应在较低的温度下进行,可得到高生成率、氢含量低的高纯一氧化碳;并有利于工业化。
与现有方法相比,有显著的优点。
1.与硫酸催化的甲酸脱水法相比,没有废酸处理问题。
2.与其它固体催化法〔6〕相比,一氧化碳的产率高,氢杂质含量低,单位体积催化剂的一氧化碳生产能力高。
脱碳的几种方法的优缺点和比较..
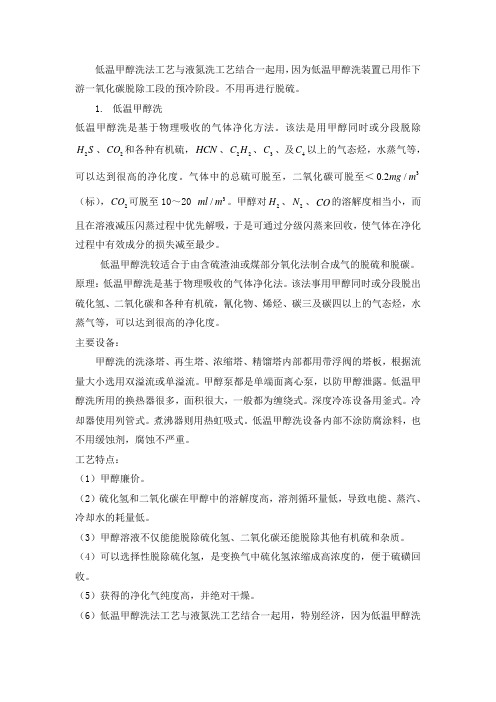
低温甲醇洗法工艺与液氮洗工艺结合一起用,因为低温甲醇洗装置已用作下游一氧化碳脱除工段的预冷阶段。
不用再进行脱硫。
1. 低温甲醇洗低温甲醇洗是基于物理吸收的气体净化方法。
该法是用甲醇同时或分段脱除2H S 、2CO 和各种有机硫,HCN 、22C H 、3C 、及4C 以上的气态烃,水蒸气等,可以达到很高的净化度。
气体中的总硫可脱至,二氧化碳可脱至<30.2/mg m (标),2CO 可脱至10~20 3/ml m 。
甲醇对2H 、2N 、CO 的溶解度相当小,而且在溶液减压闪蒸过程中优先解吸,于是可通过分级闪蒸来回收,使气体在净化过程中有效成分的损失减至最少。
低温甲醇洗较适合于由含硫渣油或煤部分氧化法制合成气的脱硫和脱碳。
原理:低温甲醇洗是基于物理吸收的气体净化法。
该法事用甲醇同时或分段脱出硫化氢、二氧化碳和各种有机硫,氰化物、烯烃、碳三及碳四以上的气态烃,水蒸气等,可以达到很高的净化度。
主要设备:甲醇洗的洗涤塔、再生塔、浓缩塔、精馏塔内部都用带浮阀的塔板,根据流量大小选用双溢流或单溢流。
甲醇泵都是单端面离心泵,以防甲醇泄露。
低温甲醇洗所用的换热器很多,面积很大,一般都为缠绕式。
深度冷冻设备用釜式。
冷却器使用列管式。
煮沸器则用热虹吸式。
低温甲醇洗设备内部不涂防腐涂料,也不用缓蚀剂,腐蚀不严重。
工艺特点:(1)甲醇廉价。
(2)硫化氢和二氧化碳在甲醇中的溶解度高,溶剂循环量低,导致电能、蒸汽、冷却水的耗量低。
(3)甲醇溶液不仅能能脱除硫化氢、二氧化碳还能脱除其他有机硫和杂质。
(4)可以选择性脱除硫化氢,是变换气中硫化氢浓缩成高浓度的,便于硫磺回收。
(5)获得的净化气纯度高,并绝对干燥。
(6)低温甲醇洗法工艺与液氮洗工艺结合一起用,特别经济,因为低温甲醇洗装置已用作下游一氧化碳脱除工段的预冷阶段。
不用再进行脱硫。
(7)过剩的只含很少硫化物的二氧化碳可放空,不存在环保问题。
低温甲醇洗的优缺点优点(1)甲醇在低温高压下,对2CO ,2H S ,COS 有极大的溶解度。
一氧化碳的制备
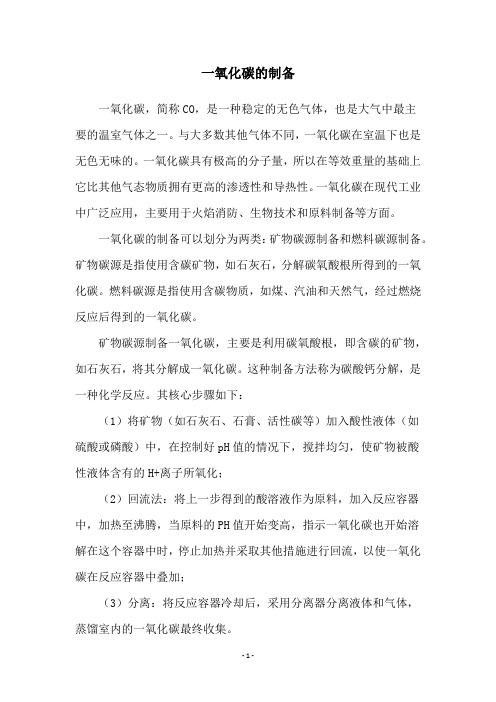
一氧化碳的制备一氧化碳,简称CO,是一种稳定的无色气体,也是大气中最主要的温室气体之一。
与大多数其他气体不同,一氧化碳在室温下也是无色无味的。
一氧化碳具有极高的分子量,所以在等效重量的基础上它比其他气态物质拥有更高的渗透性和导热性。
一氧化碳在现代工业中广泛应用,主要用于火焰消防、生物技术和原料制备等方面。
一氧化碳的制备可以划分为两类:矿物碳源制备和燃料碳源制备。
矿物碳源是指使用含碳矿物,如石灰石,分解碳氧酸根所得到的一氧化碳。
燃料碳源是指使用含碳物质,如煤、汽油和天然气,经过燃烧反应后得到的一氧化碳。
矿物碳源制备一氧化碳,主要是利用碳氧酸根,即含碳的矿物,如石灰石,将其分解成一氧化碳。
这种制备方法称为碳酸钙分解,是一种化学反应。
其核心步骤如下:(1)将矿物(如石灰石、石膏、活性碳等)加入酸性液体(如硫酸或磷酸)中,在控制好pH值的情况下,搅拌均匀,使矿物被酸性液体含有的H+离子所氧化;(2)回流法:将上一步得到的酸溶液作为原料,加入反应容器中,加热至沸腾,当原料的PH值开始变高,指示一氧化碳也开始溶解在这个容器中时,停止加热并采取其他措施进行回流,以使一氧化碳在反应容器中叠加;(3)分离:将反应容器冷却后,采用分离器分离液体和气体,蒸馏室内的一氧化碳最终收集。
燃料碳源制备一氧化碳,主要是通过燃烧反应产生气态物质,如液体燃料、煤、汽油和天然气,当温度和压力满足要求时,反应产物中就会含有一氧化碳。
其制备过程如下:(1)燃料碳源的进料带入反应炉,燃料碳源由氧化剂(如空气)燃烧产生热;(2)把所需的温度和压力控制在一定范围内;(3)燃料碳源反应完成后,通过搅拌器将反应物打散,然后通过催化剂把部分气体吸收,使反应物流动变慢;(4)反应液经过凝析减少温度,蒸发器进行蒸馏,分离释放出来的一氧化碳,得到所需的一氧化碳。
以上是一氧化碳的制备方法,两者都是可行的。
但这两种方法都存在一定的局限性,比如矿物碳源需要花费大量的能源,而燃料碳源制备的一氧化碳污染性较大,有害物质的释放量较高。
除硫工艺流程

除硫工艺流程除硫工艺流程是指在煤炭、石油、天然气等能源生产和利用过程中,将产生的二氧化硫进行去除的一种技术方法。
除硫工艺流程的目的是减少大气中二氧化硫的排放,保护环境和人体健康。
除硫工艺流程一般包括燃烧前除硫和燃烧后除硫两个阶段,下面将对这两个阶段进行介绍。
首先,燃烧前除硫是指在燃烧燃料之前采用一些物理或化学方法将燃料中的硫分离出去。
常用的燃烧前除硫方法有洗煤、破碎煤、脱硫加氢等。
洗煤是通过水洗煤炭,除去其中的杂质和硫。
破碎煤是将煤炭颗粒化,提高煤炭表面积,使硫分解更充分。
脱硫加氢是将煤炭在高温下与氢气反应,使硫分离出来,生成硫化氢。
这些方法可以有效地降低燃料中硫的含量,减少燃烧过程中二氧化硫的排放。
其次,燃烧后除硫是指在燃烧燃料之后,通过一些物理或化学方法将燃烧产生的二氧化硫进行去除。
常用的燃烧后除硫方法有湿法烟气脱硫和干法烟气脱硫两种。
湿法烟气脱硫是指将燃烧产生的烟气通过一种含有吸收剂的吸收塔,使二氧化硫被吸收剂吸收,形成硫化物,并从烟气中去除。
常用的吸收剂有石灰石、石灰浆、氨水等。
干法烟气脱硫是指将燃烧产生的烟气中的二氧化硫与一种可吸收二氧化硫的材料反应,将硫吸收剂中的二氧化硫氧化为硫酸气体,然后通过过滤或洗涤等方法对硫酸气体进行去除。
常用的硫吸收剂有活性炭、氧化钙、氧化钠等。
除硫工艺流程的选择取决于燃料的特性、产量要求、环保标准等因素。
不同的工艺流程有不同的优缺点,需要根据实际情况进行选择。
除硫工艺流程在能源生产和利用过程中发挥了重要的作用。
通过有效地除去燃料中的硫和燃烧产生的二氧化硫,可以减少大气中硫的排放,降低酸雨的发生,减少对环境和人体健康的危害。
同时,除硫工艺流程也可以提高燃料的利用效率,降低能源消耗。
因此,对于能源生产和利用过程中的除硫工艺流程的研究和应用具有重要意义。
高纯一氧化碳的制造方法
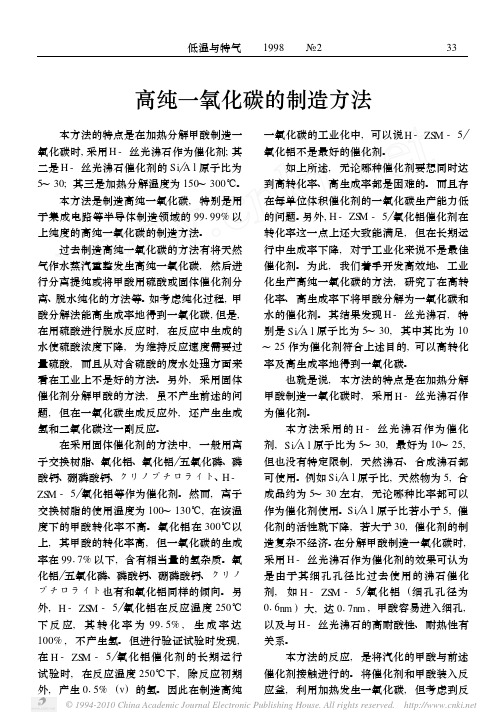
度下的甲酸转化率不高。 氧化铝在 300℃以 化剂的活性就下降, 若大于 30, 催化剂的制
上, 其甲酸的转化率高, 但一氧化碳的生成 造复杂不经济。在分解甲酸制造一氧化碳时,
率在 9917% 以下, 含有相当量的氢杂质。氧 采用 H - 丝光沸石作为催化剂的效果可认为
化铝 五氧化磷、磷酸钙、硼磷酸钙、
看在工业上不是好的方法。 另外, 采用固体
也就是说, 本方法的特点是在加热分解
催化剂分解甲酸的方法, 虽不产生前述的问 甲酸制造一氧化碳时, 采用 H - 丝光沸石作
题, 但在一氧化碳生成反应外, 还产生生成 为催化剂。
氢和二氧化碳这一副反应。 在采用固体催化剂的方法中, 一般用离
本方法采用的 H - 丝光沸石作为催化 剂, Si A l 原子比为 5~ 30, 最好为 10~ 25,
浓缩的低沸点气体, 分析纯化的液态B 2H 6, 当 CH 4 浓度达到 10 ×10- 6 时, 将纯化的液态 B 2H 6 排放到产品接受器 8。 纯化产品的质量 如表 3 所列。
表3
成 分
B 2H 6 % CH 4 10- 6 C2H 6 10- 6 CH 3C l 10- 6 CO 2 10- 6 B 4H 10 10- 6 B 5H 9 10- 6 B 5H 11 10- 6
实例 1 将 H - 丝光沸石 (Si A l 原子比为 1514) 充填至内径为 215cm、 长为 60cm 的柱内达 11cm , 所用催化剂为 50mL。在该柱的前面设 甲酸汽化器。用市售的 88% 纯度的甲酸为原 料, 通过汽化器产生 130℃的甲酸蒸汽以 45g h 的速度送入反应器上部。 将反应器外 部加热至 250℃, 由反应器下部取出反应气 进行分析, 决定反应的转化率、 生成率。 甲 酸的转化率由对未反应的甲酸进行酸碱平衡 滴定来求得, 一氧化碳的生成率用气相色谱 质量分析仪 (GC- M S) 定量生成的氢的量来
一氧化碳低温变换工艺及应用
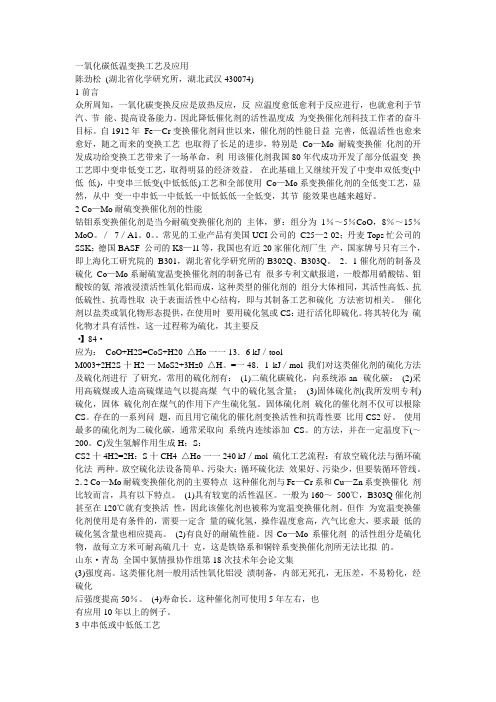
一氧化碳低温变换工艺及应用陈劲松(湖北省化学研究所,湖北武汉430074)1前言众所周知,一氧化碳变换反应是放热反应,反应温度愈低愈利于反应进行,也就愈利于节汽、节能、提高设备能力。
因此降低催化剂的活性温度成为变换催化剂科技工作者的奋斗目标。
自1912年Fe—Cr变换催化剂问世以来,催化剂的性能日益完善,低温活性也愈来愈好,随之而来的变换工艺也取得了长足的进步,特别是Co—Mo耐硫变换催化剂的开发成功给变换工艺带来了一场革命,利用该催化剂我国80年代成功开发了部分低温变换工艺即中变串低变工艺,取得明显的经济效益。
在此基础上又继续开发了中变串双低变(中低低),中变串三低变(中低低低)工艺和全部使用Co—Mo系变换催化剂的全低变工艺,显然,从中变一中串低一中低低一中低低低一全低变,其节能效果也越来越好。
2 Co—Mo耐硫变换催化剂的性能钴钼系变换催化剂是当今耐硫变换催化剂的主体,萝:组分为1%~5%CoO,8%~15%MoO。
/7/A1。
0。
常见的工业产品有美国UCI公司的C25—2-02;丹麦Tops忙公司的SSK;德国BASF 公司的K8—1l等,我国也有近20家催化剂厂生产,国家牌号只有三个,即上海化工研究院的B301,湖北省化学研究所的B302Q、B303Q。
2.1催化剂的制备及硫化Co—Mo系耐硫宽温变换催化剂的制备已有很多专利文献报道,一般都用硝酸钴、钼酸铵的氨溶液浸渍活性氧化铝而成,这种类型的催化剂的组分大体相同,其活性高低、抗低硫性、抗毒性取决于表面活性中心结构,即与其制备工艺和硫化方法密切相关。
催化剂以盐类或氧化物形态提供,在使用时要用硫化氢或CS:进行活化即硫化。
将其转化为硫化物才具有活性,这一过程称为硫化,其主要反·】84·应为:CoO+H2S=CoS+H20 △Ho一一13.6 kJ/toolM003+2H2S十H2一MoS2+3Hz0 △H。
=一48.1 kJ/mol 我们对这类催化剂的硫化方法及硫化剂进行了研究,常用的硫化剂有:(1)二硫化碳硫化,向系统添an--硫化碳;(2)采用高硫煤或人造高硫煤造气以提高煤气中的硫化氢含量;(3)固体硫化剂(我所发明专利)硫化,固体硫化剂在煤气的作用下产生硫化氢。
低温甲醇洗脱硫脱碳工艺

低温甲醇洗脱硫、脱碳工艺一、工艺介绍低温甲醇洗是50 年代初德国林德公司和鲁奇公司联合开发的一种气体净化工艺。
该工艺以冷甲醇为吸收溶剂,利用甲醇在低温下对酸性气体溶解度极大的优良特性,脱除原料气中的酸性气体。
该工艺气体净化度高,选择性好,气体的脱硫和脱碳可在同一个塔内分段、选择性地进行。
低温甲醇洗工艺技术成熟,在工业上有着很好的应用业绩,被广泛应用于国内外合成氨、合成甲醇和其他羰基合成、城市煤气、工业制氢和天然气脱硫等气体净化装置中。
在国内以煤、渣油为原料建成的大型合成氨装置中也大都采用这一技术。
低温甲醇洗脱硫、脱碳技术特点如下:1. 溶剂在低温下对CO、H2S COS等酸性气体吸收能力极强,溶液循环量小,功耗少。
2. 溶剂不氧化、不降解,有很好的化学和热稳定性。
3. 净化气质量好,净化度高,CO2<20ppm,H2S<0.1ppm。
4. 溶剂不起泡。
5. 具有选择性吸收H2S、COS和CO的特性,可分开脱除和再生。
6. 溶剂廉价易得,但甲醇有毒,对操作和维修要求严格。
7. 该工艺技术成熟,目前全世界约有87 套大中型工业化装置。
该工艺需从国外引进。
由于操作温度低,设备、管道需低温材料,且有部分设备需国外引进,所以投资较高。
目前,国外低温甲醇洗工艺国外有林德工艺和鲁奇工艺二种流程,二者在基本原理上没有根本区别,而且技术都很成熟。
两家专利在工艺流程设计、设备设计和工程实施上各有特点。
国内大连理工大学经过近20 年的研究,也开发成功了低温甲醇洗工艺软件包,并获得了国内两项专利。
林德低温甲醇洗工艺流程:采用林德的专利设备一一高效绕管式换热器,提高换热效率,特别是多股物流的组合换热,节省占地、布置紧凑,能耗较省;但高效绕管式换需要国外设计(可国内制造)。
原料气进入低温甲醇洗装置后,喷入少量循环甲醇,防止气体结冰,避免系统阻塞在甲醇溶剂循环回路中设置甲醇过滤器,除去FeS、NiS 等固体杂质,防止其在系统中积累而堵塞设备和管道。
一氧化碳变换反应工艺流程-

一氧化碳变换反应工艺流程一氧化碳变换流程有许多种,包括常压、加压变换工艺,两段中温变换(亦称高变、三段中温变换(高变、高-低变串联变换工艺等等。
一氧化碳变换工艺流程的设计和选择,首先应依据原料气中的一氧化碳含量高低来加以确定。
一氧化碳含量很高,宜采用中温变换工艺,这是由于中变催化剂操作温度范围较宽,使用寿命长而且价廉易得。
当一氧化碳含量大于15%时,应考虑将变换炉分为二段或多段,以使操作温度接近最佳温度。
其次是依据进入变换系统的原料气温度和湿度,考虑气体的预热和增湿,合理利用余热。
最后还要将一氧化碳变换和残余一氧化碳的脱除方法结合考虑,若后工序要求残余一氧化碳含量低,则需采用中变串低变的工艺。
一、高变串低变工艺当以天然气或石脑油为原料制造合成气时,水煤气中CO含量仅为10%~13% (体积分数,只需采用一段高变和一段低变的串联流程,就能将CO含量降低至0.3%,图2-1是该流程示意图。
图2-1一氧化碳高变-低变工艺流程图1-废热锅炉2-高变炉3-高变废热锅炉4-预热器5-低变炉6-饱和器7-贫液再沸器来自天然气蒸气转化工序含有一氧化碳约为13%~15%的原料气经废热锅炉1降温至370℃左右进入高变炉2,经高变炉变换后的气体中一氧化碳含量可降至3%左右,温度为420~440℃,高变气进入高变废热锅炉3及甲烷化进气预热器4回收热量后进入低变炉5。
低变炉绝热温升为15~20℃,此时出低变炉的低变气中一氧化碳含量在0.3%~0.5%。
为了提高传热效果,在饱和器6中喷入少量软水,使低变气达到饱和状态,提高在贫液再沸器7中的传热系数。
二、多段中变工艺以煤为原料的中小型合成氨厂制得的半水煤气中含有较多的一氧化碳气体,需采用多段中变流程。
而且由于来自脱硫系统的半水煤气温度较低,水蒸气含量较少。
气体在进入中变炉之前设有原料气预热及增湿装置。
另外,由于中温变换的反应放热多,应充分考虑反应热的转移和余热回收利用等问题。
高效CO去除剂设备工艺原理

高效CO去除剂设备工艺原理什么是CO去除剂CO去除剂是一种用于净化工业尾气中的一氧化碳(CO)的化学物质。
它通常由银和其他金属组成,以吸收和化学反应来减少CO的浓度。
CO是一种有毒无色气体,会对人体造成严重的健康影响,并对环境产生不良影响。
CO去除剂设备原理设备介绍CO去除剂设备通常由吸附剂、银催化剂和空气预热器组成。
尾气中的CO会首先进入吸附剂中,吸附剂会吸收CO的一部分并将其储存,然后进入银催化剂中。
银催化剂通过化学反应将CO氧化为二氧化碳(CO2)和水蒸气,然后通过排气管排放到大气中。
此过程中催化剂也会被还原,以便继续使用。
空气预热器主要起到预热进入设备的尾气的作用,以确保化学反应能够正常进行,并提高催化剂的效率。
设备工艺原理CO去除剂设备的工艺原理包括吸附、催化和氧化三个过程。
•吸附过程中,废气中的CO进入吸附剂中,部分被吸附并储存起来。
吸附过程通常在100℃-200℃下进行,时间较短。
•催化过程中,吸附后的CO进入银催化剂中。
银催化剂的作用是将CO氧化为CO2和水蒸气,同时催化剂也会被还原,以便继续使用。
催化过程通常在150℃-250℃之间进行。
•氧化过程中,CO2和水蒸气经过排气管排放到大气中。
该过程通常在200℃以上的高温下进行。
CO去除剂设备的工艺原理是一种高效、可靠的工艺,既可减少CO 的浓度,又可避免CO带来的健康和环境危害。
在工业尾气处理中得到广泛应用。
CO去除剂设备的优缺点CO去除剂设备的优点主要包括:•处理效率高,一次性可处理大量CO尾气。
•设备结构简单,易于维护和操作。
•设备自动化程度高,减少了人工干预。
CO去除剂设备的缺点主要包括:•设备成本较高,对于一些小型工厂来说可能无法承担。
•银催化剂是一种昂贵的化学物质,必须进行定期更换,增加了运营成本。
总结CO去除剂设备是一种高效、可靠的工业尾气处理工艺,其工艺原理主要包括吸附、催化和氧化三个过程。
该设备具有处理效率高、易于操作等优点,同时也存在一定的成本和运营成本。
焦炭纯氧法生产高品质一氧化碳的研究

焦炭纯氧法生产高品质一氧化碳的研究摘要:本文介绍了采用以焦炭和纯氧为原料生产CO的过程中如何做到清除CO中的灰尘及CO除水干燥技术,使得处理后的CO洁净度和干燥度能够满足生产光气时对CO品质的特殊要求,高品质CO大大增加了生产光气设备及其相关管路的使用寿命。
关键词:CO清净CO除水分子筛吸附干燥1、前言在光气生产过程中,由于使用的原料气为CO和氯气,两者的水份是影响光气质量的重要因素。
因为光气遇到水后会生成HCL,腐蚀光气合成器、清净反应器(两者均为合成光气的设备)和与其相连的管路,而腐蚀后造成的泄露危害是相当大的。
同时,CO的洁净度对后续光化产品的外观质量有着很大影响。
因此,降低原料CO气体中的水份含量和提高洁净度,是保护后系统设备维持正常生产和提高产品质量的关键。
我单位生产光气过程使用的氯气为钢瓶液氯,其含水量小于400ppm(wt),不会对生产造成影响;而另一原料气CO为本单位自产,需要进行除尘和除水处理。
我单位生产CO的工艺为采用冶金焦和纯氧为原料,在CO发生炉中发生氧化还原反应,生成的CO要经过水洗、泡沫水洗和碱洗后达至洁净度的要求送入气柜备用。
在上述过程后,CO的含水量逐步升高,所对必须要经过压缩、冷冻和分子筛吸附等过程的处理,使得最终CO的水份降至100ppm(V)以下。
2、工艺流程及原理2.1工艺流程简述由CO发生炉出来的气体经水洗、泡沫水洗及碱洗等步骤除尘净化后得≥96%(V)(气体吸收法),含水量达到饱和的CO气体,该含水量饱和的CO气体在20℃时,其含水量约为20000ppm。
为使其含水量降至100ppm以下,我们选用13X型沸石分子筛进行深度干燥。
但如果单一采用分子筛干燥,势必加大分子筛的干燥与再生负荷,该工艺显然不完善。
所以,必须在分子筛干燥之前进行预脱水,使大部分水分预先脱去,减轻分子筛干燥与再生的负荷。
从而达到深度干燥的目的。
根据一般气体所固有的物性,采用对CO气体加压降温使所含水份达到饱和而析出的方法,则可达此目的,故所拟定的工艺流程是:首先压缩冷冻预脱水,然后进行分子筛深度干燥,进而得到含水量≤100ppm,合格的CO气体。
- 1、下载文档前请自行甄别文档内容的完整性,平台不提供额外的编辑、内容补充、找答案等附加服务。
- 2、"仅部分预览"的文档,不可在线预览部分如存在完整性等问题,可反馈申请退款(可完整预览的文档不适用该条件!)。
- 3、如文档侵犯您的权益,请联系客服反馈,我们会尽快为您处理(人工客服工作时间:9:00-18:30)。
硫 化氢 以及 因过 短 的浓混合气 时 间导致 的较慢 的脱
硫 处理 。
主 权 项 :、 1 在一 种具 有 内燃 机 以及 用 于 处 理 来 自所 述 内燃 机 的排 放 的催化 NOx存 储 和转 化 装
摘 要 : 一种制取高纯一氧化碳气体的低、 常 温脱 除有机 硫 工艺 。 以氧 、 氧化 碳 气 化焦 炭 制 得 二
组 成 为 C 1 ~ 9 、 O 0 ~ 9 、 O O 9 C 2 .1 O O
0 0 1 ~ 2 、COS ( 0~ 9 0 )× 1 ~ 、 S ( 0 . 0 5 O0 0 H2 1
1 g吸 附剂/ 0 L水 相 的 比例 加 入 水 相 , 加 入油 相 , 再
气和稀混合气排气流暴露所述催化 N 存储 和转 Ox
化装 置达第 一间 隔 } 及在所 述第一 间 隔之后 , 向连续 浓混合 气排 气流暴 露 所 述催 化 NOx存 储 和 转 化装
置达第 二 间隔 。
发 明名称 : 制取 高纯 一氧化碳 气 体的低 、 常温脱
除有 机硫 工艺
编 号 : . H2 0 0 0 Q J 0 667 T
申 请 人 : 省化 学研究 院 l 海化工 设计 院 湖北 上
有 限公 司
油相与水 相体积 比为 l 0 1:1 将 混合 体 系在 ~ . ,
3 ℃反 应 3 4小 时 , 出吸 附剂 , 6 " 1 0 O ~2 滤 于 0- 2 ℃干 - - 燥后 , 5 0 在 0 C焙烧 , 得到再 生 的脱 硫 吸 附剂 ;所 述 的水相 为含 有 微 生 物 的生 理 盐 水 、 H一 6 0 7 0 p . ~ .
隔, 浓混合 气循环 可 以 对脱 硫 处 理期 间的 每个 浓 混
合气/ 稀混合气脱硫循环进行优化 。以此方式 , 可以
同时避免 因使用 过长 的浓混 合气循 环产 生的过 多 的
申 请 人: 中国科 学 院过程 工程 研究所 摘 要 : 发 明 涉及 一 种脱 硫 吸 附剂 的再 生 本 方法 。其 为将吸 附 了硫 的脱硫 吸 附剂加 入一定 比例 的水 相和油 相 的混合体 系 , 混 合 体 系在 3 " 应 将 0C反
热 后 , 入 内装 净 化 保 护 剂 A、 的 净 化 塔 , 除 进 B 脱
NOx As 、 H3 HC 、 N、OX 和 H2 害物 、 H3P 、 1HC S S有
质, 进入 内装 C s水 解 催 化 剂 的 脱 有 机 硫 塔 , O 将 8 " 9 的 C s 水解 转化 为 H。 此 过程 在 2 5 - 5, - 9 6 O s, O
~
的磷酸 缓 冲溶液 或基 础 培 养基 } 中微 生 物 细胞 在 其 水相 中的浓 度为 1  ̄5g L;所述 的微 生物 为专 一 0 0/ 性 生物 脱硫 催化 剂 ;所 述 的油 相 为正辛烷 、 甲苯 、 汽
油或 柴油 。
100 ×1 的原 料 气体 经过 储气 柜 、 压 和加 00 ) 0 增
1 ,5g L微 生物 的生 理盐 水 、 酸 缓 冲 溶液 或 培 0- 0/ -  ̄ 磷
养基 ; 所述 的微 生物 为 专一 性 生 物脱 硫 催 化 剂短 芽
置 的装 置 中 , 一种对 所述催 化 NOx存储 和转化 装置 进 行脱 硫 的方 法 , 述方 法包 括 :将 所 述催 化 NOx 所 存 储 和转化装 置加 热到脱硫 温度 }向交替 的浓混合
常温 脱除有 机硫工 艺 , 以氧 、 氧化碳 气化 焦碳 制得 二 粗一 氧化碳 原料气 . 组 成 为 C O ~9 、C 其 O1 9 O
维普资讯
20 0 6年第 6卷第 6期
气 体净 化
・ 3 3 ・
可溶 于水 的铵 化合 物 。
发 明名 称 : 一种脱 硫 吸 附剂 的再 生方 法
编 号 : J 0 665 QT H2 0 0 0
然 后基 于所确定 的硫 量选择 预定 的浓混合 气循 环 间
孢杆 菌 、 氏假 单胞 茵 、 球 诺 卡 氏菌 、 登 氏菌 和 德 小 戈
红平红球菌。该方法方便 、 高效, 不会影响吸附剂的
性质, 使得 脱硫 吸 附剂可 以多次 循环使 用 } 免 子使 避 用 高温焙 烧再 生脱 硫 吸 附 剂 时不 能彻 底 脱 硫 、 造 会 成 油 品燃 烧值 损失 的 缺 陷 ; 以脱 除 使用 加 氢脱 硫 可 方 法很难 脱 除的有 机硫 化 物 ; 实现 了 油 品 的超低 硫 生产 , 以将硫 含 量 降低 到 3 × l 以 下 } 可 O O 而且 能 耗小, 生产过 程 中不 产生 有毒 害的物 质 。 主 权 项 :、 种脱硫 吸 附剂 的再 生方 法 , 括 1一 包 如下 的 步 骤 :将 吸 附 了硫 的脱 硫 吸 附荆 按 2 5 . ~
~
发明 名称 : NOx存储 和转化 装置 进行脱 硫 的 对
方法 编 号 : T H2 0 0 0 Q J 066 6
10 5 ℃及 0I ,0 a的条 件下 进行 , 原料气 经 . ̄ 1MP 该
精 制处理 后供 下游 醋 酸 、 甲基 甲酰胺 、 甲醚 、 二 二 甲 苯 二异 腈酸醑 或二苯 基 甲烷 二异腈 酸酯 等精细 化工 生产 使 用 。本 工 艺 将 C S的 8 ~ 9 转 化 为 O 5, 9 6 5 H。 , s 可采 用常规 的湿 法 脱 硫代 替 聚 乙二 醇 二 甲醚 脱 硫 , 使 聚 乙二醇 二 甲醚 脱碳 解 吸气 C + C 可 O。 OS 实现 循环利 用 , 做到 有 毒 物质 C 0s的零 排放 , 利 有 于保 护环境 。 主 权 项 :、 种制 取高纯 一氧化 碳气体 的 低 、 1一