BS 729 - 1971 Hot Dip GalvanizedCoatings On Iron and Steel Articles
阿联酋系墙铁约束固定装置(TMI)WallTiesRestraintFixings

Technical Metal Industrial Co. L.L.C.Tel: +971 (2) 5502025 Fax: +971 (2) 5502024 P.O. Box: 41558Abu DhabiTel: +971 (4) 8858036Fax: +971 (4) 8858658P.O. Box: 86029DubaiTel: +971 (3) 7224768Fax: +971 (3) 7224769P.O. Box: 99155Al AinTel: +971 (7) 2282332Fax: +971 (7) 2282232P.O. Box: 33239Ras Al khaimahE-mail:*******************:I ntroductionAll wall tie’s manufacturing complies with BS EN 845-1:2003 (formerly BS 1243). A quick quotation and prompt delivery is available from stock of standard tie. As for our custom designed ties, an advanced information submittal is required for quick deliveries.TMI is well equipped for manufacturing wall ties and meeting any challenge in the construction industry. TMI manufactures a wide range of wall ties in galvanized steel and stainless steel of grades S304 and S316.The range of TMI ’s accessories from the standard ties, to its specialty, the custom designed ties are available to suit most engineering applications such as masonry to masonry, masonry to concrete, masonry to overhead structure and masonry to steel structures.TMI has been in the business of manufacturing and supplying a wide range of building accessories for the construction industry since 1997. With continued process improvement and new innovative product development, TMI is proud to deliver any quantity of its high quality and great valued products, with excellent service and punctuality to its customers.Movement ties are designed to restrain masonry against lateral wind loads, allowing a horizontal expansion or contraction. Movement ties are used where masonry restrained to steel work and in longspan masonry where movement joints are required.Movement ties are held in the brick or block work. The debonding sleeve provided on plain end of the tie will serve to allow the movement. TMI recommends the debonding sleeve to be installed with agap of 10mm at the end to allow for expansion or contraction.LPSWwith sleevesDBSLPSW-STL-Plain tie slot withsleevesPTSWwith sleevesFTSW* Debonding sleeve is supplied according to tie measurement.Frame cramps are designed to restrain the masonry with the new or existing vertical structure. LSSB-STLSTendLSSSplit EndCGWTwall tieLSSBLBTu-cut endLPS-STslot tieLPTLPSLSS-STSplit-end LPS-SLSSFThe 06mm hole (as in LPS) or 6mmx18mm slot (as in LPT) in the standard 30mm upstand (other upstand height available upon request) is provided for attaching the frame cramp to the vertical structure and the other end is embedded to the masonry.* Custom designs are available upon request.* Material - Galvanized, Stainless steel, mild steel.* Finish - Hotdip galvanized, Powder coated* Custom designs are available upon request.* Material - Galvanized, Stainless steel, mild steel.* Finish - Hotdip galvanized, Powder coatedThese products are designed to secure two masonry of a cavity wall, allowing them to act as one structure.The tie made of strip (as in FCWT) or wire (as in WTB) is embedded in the inner and outer masonry. Ties having a 06.0mm hole or 6mmx18mm slot in the standard 30mm upstand (as in CWT) will be fixed to the existing vertical structure and the other end is embedded to the outer masonry. The drip feature of the tie can be fabricated according to customer requirements, and should be pointed downside during installation to prevent the moisture from crossing between the masonry.LPS-SCcavity tieCWT-STCWTCavity wall tiebolt/screw-onLS-TL-SlotPCWTLPS-STCcavity tie* Custom designs are available upon request.StripFS2F FCWTFlat two sidewall tieSCTWireEmbedment Length of TieThe tie should be of perfect length so that it should beproperley embeded in mansonry. TMI suggest a minimumembedment of 50 perecentage in each block.WTZZ-Shape WiretieDTW-DDwire tiedouble dripDTW-SDwire tie singledripZWTZ-Wire TieWTB* Custom designs are available upon request.* Material - Galvanized, Stainless steel, mild steel.* Finish - Hotdip galvanized, Powder coatedSlot Details* Custom designs are available upon request.Overhead restraints are designed for restraining the free standing wall with the overhead structure. The sliding tie is fixed to the overhead structure to arrest side movements. The shrinkage or thermalmovement of the wall can be absorbed by the vertical movement of the sliding tie.VM2Vertical movementtie bolt screw onVHM-ST2Vertical horizontalmovement tie slotVHM-ST1Vertical horizontalmovement tie slotVM1Vertical movement tie bolt screw-onWTCWCeiling wall strap tieThe sliding tie is provided with a 06mm hole (as in VM1, VHM-ST1) or 6mmx18mm slot (as in VM2, VHM-ST2) as a standard for fixture to the overhead structure. The other end is held between the brick or block work.Different anchor plates are also available as a simple and economical head restraint system. Anchor Plates are used to attach structural members to concrete structure. Anchor plates and angles can be used to frame openings in concrete walls or as shelf angles.Anchor PlatesASP22 Side screwed punched anchor.AH-2ST2 Side slot anchor horizontalAWSABS1 1 Side bolt anchorAH-1ST1 Side slot anchor horizontalAPPlain anchorAV-1STVerticalASBBolt / slotted anchorAV-2ST2 Side slotanchor - vertical* Material - Galvanized, Stainless steel, mild steel. * Table Shows details about sleeve. Tie will be supplied accordingly to sleeve design.* Custom designs are available upon request.* Material - Galvanized, Stainless steel, mild steel.* Finish - Hotdip galvanized, Powder coated* Finish - Hotdip galvanized, Powder coatedThis system is designed to join and provide lateral support to the newly formed masonry with the existing vertical structure, that is steel section or concrete.The system consist of channel that is fixed to the vertical structure (steel work or a concrete structure) and the tie which slides vertically in the channel embeded to masonry which provides the necessary restraint. The tie can be supplied with or without rubber sleeves.The dove tail Anchor channel is cast-in to the concrete during construction and after setting, the wire or strip tie is mated and embded to the masonry which provides a support to the structure. The dove tail anchor channel to be furnished with form filler inserts to protect channel from filling with DTTDove tail withtriangular channelOCOmega channel* Material - Galvanized, Stainless steel, mild steel.* Finish - Hotdip galvanized, Powder coated FTC FasttrackchannelsWTRC Rectangularchannel with tie* Material - Galvanized, Stainless steel, mild steel.* Finish - Hotdip galvanized, Powder coated* Material - Galvanized, Stainless steel, mild steel.* Finish - Hotdip galvanized, Powder coatedDTCV-WDovetail anchor channelvertical with wire TieDTCV-SDovetail anchor channelvertical with strip TieDTCH-WDovetail anchor channelhorizontal with wire TieSliding anchor system is designed to restrain cavity wall to the overhead structure.SAT-TWSAT-OWSlidding Anchor Tie - One WayThe system has a stem fixed to the overhead structure. It accepts ties which slide to accommodate vertical movement.Tail OptionsBody Options Different combinations is available from the listed head, body and tail options to suit your practical applications.TPE Plain endTSE Split end Stem Specification* Head option as shown and can be fabricated according to customer requirements. SAS-H1 Sliding Anchor Stem - Head One SAS-H2 Sliding Anchor Stem - Head Two SAS-H3 Sliding Anchor Stem - Head Three SAS-H4 Sliding anchor stem - head fourSAS-H5 Sliding anchor stem - head five SAS-H6 Sliding anchor stem - head twistTie Specification* Other length are available upon request.* Material - Galvanized, Stainless steel, mild steel.* Finish - Hotdip galvanized, Powder coated2 - WireManufacturedBS EN 845-1:2003 (formerly BS 1243)BS 1052 (1980), BS 4482 (2005)Mild steel wire Hot dipped GalvanizingStainless steel wireBS EN 10244-2:2001 (formerly BS 1706)ASTM A641/A641MBS EN ISO 1461:1999 (formerly BS 729) ASTM A123/A123MBS EN 10088-3:2005 (formerly BS 1554:1990)ASTM A580/A580MZinc Plated WireBS EN 10346:2009 (formerly BS EN 10142:1991)ASTM A653/A653MPre Galvanized Steel BS EN 845-1:2003 (formerly BS 1243)Manufactured BS EN 10149-3:1996Mild SteelBS EN ISO 1461:1999 (formerly BS 729)ASTM A123/A123M, ASTM A153/A153MHot dipped Galvanizing1 - SheetBS EN 10088-2:2005 (which was direct equivalent formerly BS 1449:Part 2:1983, grade 304 2B finish)ASTM A240/A240M in grade 304 2B finishStainless SteelT echnical SpecificationsPlease follow the below recommendations for storage Conditions:• Store in covered and dry area.• Avoid contact with sand, chemicals & water.S。
SAS Micropile Manual
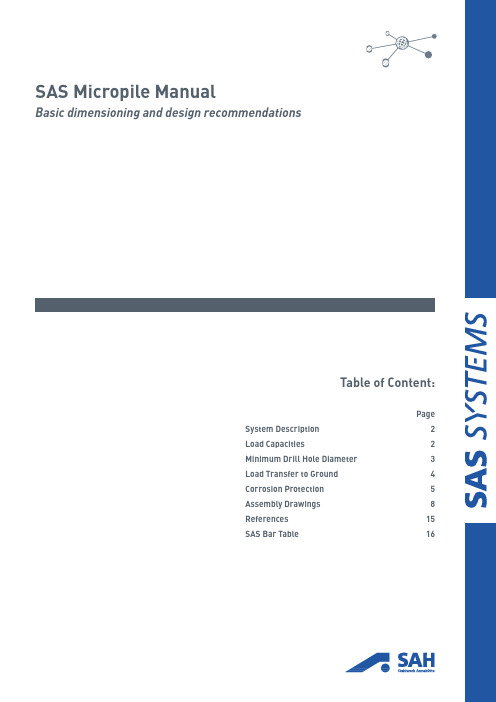
SAS Micropile ManualBasic dimensioning and design recommendationsTable of Content:PageSystem Description 2Load Capacities 2Minimum Drill Hole Diameter 3Load Transfer to Ground 4Corrosion Protection 5Assembly Drawings 8References 15SAS Bar Table 16System DescriptionMicropiles are small diameter piles; transferring compression, tension, and alternating loads mainly through skin friction to the surrounding ground. This concept of micropiles was developed in the 1950’s. The use of con-tinuous threaded bars as single, double, and triple bar micropiles was introduced in the 1970’s.The SAH micropiles comprises of a thread-bar as the principal load carrying element inside a pressure-grout-ed cement body. This continuous coarse SAH thread-bar allows the micropile to be installed in single sections, or in multiple sections, coupled together to any desired length.Various corrosion protection systems are available to cope with environmental impact and performance life expectations.Load Capacities of PileIn accordance with EN1537 and PTI Recommendations for Ground Anchors, the following listed working load capacities for mircopiles are based on a factor of 0.60 x Ptk (0.60 x UTS), that is 60 % of the nominal ultimate tensile strength.Working Load Capacities for S 670/800 (grade 97) bar:Working Load Capacities for B 500/550 (grade 75 and grade 80) bar:1) Diameter 63.5 mm bar is of grade 555/700 N/mm² (grade 80).Minimum Drill Hole DiameterRequired drill hole diameter for single corrosion protected (SCP) and double corrosion protected (DCP) micro-pile depends on the ground conditions and drilling equipment setup, e.g. fully cased drill hole. The following are minimum internal hole diameters at which the piles do fit and do meet required cement grout coverage according EN 1537 for DCP micro piles.Minimum drill hole diameter for single bar micropile:Load Transfer to GroundMicropiles transfer load mainly through skin friction into the surrounding ground. For pressure-grouted micro-piles the minimum load transfer length can be presumed to equal an anchors bond length along the drill hole surface:L b= P/(π x t x d x g p)L b= load transfer lengthP= design load of micro piled= drill hole diametert= bond stress at soil to cement grout interfaceg= safety factorpEmpirical bond stress values at soil to cement grout interface for pressure grouted micro piles according to DIN 1054, Subsoil - Verification for earthworks and foundations:SAS thread-bar has a relative rib area of 0.075 to 0.080, which exceeds that of standard thread-bars. For ce-ment grout strength in excess of 40 N/mm2 a bond stress of t w= 5 N/mm2 for the serviceability limit state can be assumed between SAS thread-bar and surrounding cement grout.According to PTI Recommendations for permanent ground anchors a safety factor of 2.0 should be applied to the bond stress value at the grout/ground interface. DIN 1054 is differentiating the safety factor to load condi-tions and source of bond stress value used.Safety factors on bond stress values for micropiles according to DIN 1054 Subsoil - Verification for Earthworksand Foundations:Local standards and particular project-related safety factors on load capacities as well as allowable bond stress of soils have to be observed.Corrosion Protection SystemsThe pace of corrosion of steel members in the ground is largely depending on the aggressiveness of the sur-rounding environment. For the SAS Micropile system the following protection against corrosion can be applied:sacrificial steelbare bar in cement grout(SCP) single corrosion protectionhot dip galvanized bar in cement grout epoxy coated bar in cement grout bare bar in pre-grouted PE sheathing(DCP) double corrosion protectionMicropiles with a performance-life expectation of less than 2 years are temporary piles. A performance life-span of 2 to 7 years can be considered for semi permanent. Micropiles with a performance-life of more than 7 years are permanent piles.•••••Corrosion of bare steel in the ground:Steel elements can be oversized to allow for loss of cross sectional area due to corrosion. Depending on the ground conditions, the European standard for micropiles, EN 14199, is suggesting the following loss of thick-ness of bare steel in the ground:The values above are for guidance only. Local conditions should be considered and suitable values taken into account.SCP - Single Corrosion Protection:Bare thread-bars, inside a column of cement-grout are considered having single corrosion protection. This single corrosion protection is adequate for temporary piles as well as permanent piles loaded with compres-sion only. EN 1537 for Ground Anchors as well as the American PTI Anchor Recommendations is considering a service live of less than 24 month as temporary.Hot Dip Galvanizing:Micropiles in less aggressive environment can be protected semi-permanent by hot dip galvanizing of the thread-bars in accordance to EN 1461, BS 729, or ASTM A 153.Epoxy coating:Micropiles in less agressive environment can be protected semi-permanent by epoxy coating of the thread-bars in accordance to BS 7295, ASTM A 934, or A 775.DCP - Double Corrosion Protection:Permanent piles, tensile loaded piles, or piles in aggressive media (such as seawater), should have double corrosion protection applied. This is provided by centralizing the thread-bar in a corrugated plastic sleeve and by filling the annulus between the bar and the sleeve with a non-shrink cement grout, preferably in a qualified workshop.Corrosion Protection Matrix:For the following suitability matrix on corrosion protection systems a soil corrosiveness according to DIN EN 12501 was considered. Further the performance life was classified to temporary (less than 2 years), semi per-manent (two to 7 years), and permanent (more than 7 years.Recommended corrosion protection systems in light of performance life and soil corrosiveness:1) In accordance with DIN EN 12501.2) Suitable for micropiles loaded by compression only.SAS Micropile Assembly DrawingsAs mentioned at the very beginning, micropiles transfer compression, tension, or alternating loads to the sur-rounding ground. At the pile head and coupler units the path of force is different for tension vs. compression loaded micropiles. Following sketches show micropile coupler units, matching the path of load transfer:Compression Load Tension Load Alternating Load[compression load cycle]The following micropile assembly drawings reflect this fact by altering the anchor and coupler units for single corrosion protected (SCP ) and double corrosion protected (DCP ) systems:SCP Pile for Tension and Compression Load Page 9SCP Pile for Compression Load Page 10SCP Pile for Tension LoadPage 11DCP Pile for Tension and Compression Load Page 12DCP Pile for Compression Load Page 13DCP Pile for Tension LoadPage14Coupler 3006Lock Nut 2040Coupler 3003Anchor Nut 2002Anchor Nut 2002Lock Nut 2040Coupler 3003Notes and DetailsNotes and DetailsNotes and DetailsApprovalsZ-1.1-1 SAS 555 Thread-Bar (S555/700) as load bearing element for micro-piles andsoil nailsETA request No. 01.03/10 Application for European Technical Approval “Kit For Micropiles” in progressat EOTA TBStandardsEN 445 Grout for prestressing tendons – Test methodsEN 447 Grout for prestressing tendons – Specification for common groutEN 1537 Execution of special geotechnical works – Ground anchorsEN 12501-1 & 2 Protection of metallic materials against corrosion. Corrosion likelihood in soil. Pr EN 14199 Execution of special geotechnical works – MicropilesEN ISO 15630-1 Steel for the reinforcement and prestressing of concrete – Test methods ETAG 013 Post Tensioning Kits for prestressing of StructuresISO/CD 15835-1 Steel for reinforcement of concrete – Mechanical splices for bars – Part 1:RequirementsISO/CD 15835-2 Steel for reinforcement of concrete – Mechanical splices for bars – Part 2:Test methodsPublicationsRecommendations for Prestressed Rock and Soil Anchors – Post-tensioning Institute, 2004For more detailed information and queries please directly contact the R&D department at Stahlwerk Annahütte.Stahlwerk Annahütte Max Aicher GmbH & Co. KG, D-83404 Hammerau / Germany Tel. +49 (0)86 54 / 4 87-0 • Fax +49 (0)86 54 / 4 87-964stahlwerk@ • 。
冠凯帕蒂柔软清洗涂层液说明书
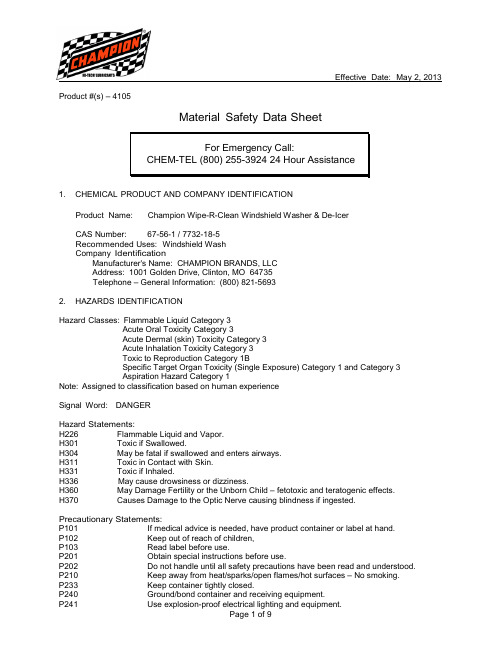
Product #(s) – 4105Material Safety Data SheetFor Emergency Call:CHEM-TEL (800) 255-3924 24 Hour Assistance1. CHEMICAL PRODUCT AND COMPANY IDENTIFICATIONProduct Name: C hampion Wipe-R-Clean Windshield Washer & De-IcerCAS Number: 67-56-1 / 7732-18-5Recommended Uses: Windshield WashCompany IdentificationManufacturer's Name: CHAMPION BRANDS, LLCAddress: 1001 Golden Drive, Clinton, MO 64735Telephone – General Information: (800) 821-56932. HAZARDS IDENTIFICATIONHazard Classes: Flammable Liquid Category 3Acute Oral Toxicity Category 3Acute Dermal (skin) Toxicity Category 3Acute Inhalation Toxicity Category 3Toxic to Reproduction Category 1BSpecific Target Organ Toxicity (Single Exposure) Category 1 and Category 3Aspiration Hazard Category 1Note: Assigned to classification based on human experienceSignal Word: DANGERHazard Statements:H226 Flammable Liquid and Vapor.H301 Toxic if Swallowed.H304 May be fatal if swallowed and enters airways.H311 Toxic in Contact with Skin.H331 Toxic if Inhaled.H336 May cause drowsiness or dizziness.H360 May Damage Fertility or the Unborn Child – fetotoxic and teratogenic effects.H370 Causes Damage to the Optic Nerve causing blindness if ingested. Precautionary Statements:P101 If medical advice is needed, have product container or label at hand.P102 Keep out of reach of children,P103 Read label before use.P201 Obtain special instructions before use.P202 Do not handle until all safety precautions have been read and understood. P210 Keep away from heat/sparks/open flames/hot surfaces – No smoking.P233 Keep container tightly closed.P240 Ground/bond container and receiving equipment.P241 Use explosion-proof electrical lighting and equipment.Product #(s) – 4105P242 Use only non-sparking tools.P243 Take precautionary measures against static discharge.P261 Avoid breathing vapors.P264 Wash thoroughly after handling.P270 Do not eat, drink or smoke when using this product.P271 Use only outdoors or in a well-ventilated area.P280 Wear protective gloves / protective clothing / eye protection.P301 + P310 If SWALLOWED: Immediately call a POISON CENTER or doctor/physician.P331 D o NOT induce vomiting.P330 Rinse mouth.P303 + P361 + P353 If ON SKIN (or hair): Remove/Take of immediately all contaminated clothing.Rinse skin with water/shower.P304 + P340 IF INHALED: Remove victim to fresh air and keep at rest in a positioncomfortable for breathing.P308 + P311 IF exposed or concerned: Call a POISON CENTER or doctor/physicianP361 + P378 Take off immediately all contaminated clothing and wash it before reuse.P370 + P378 In case of fire: Use dry chemical, CO2, alcohol-resistant foam, and water spray for extinction.P403 + P235 Store in well-ventilated place. Keep cool.P501 Disposal: Dispose of contents/container to a specialized waste disposal plant in accordance with local/regional regulationsHazard Pictograms:3. COMPOSITION/INFORMATION ON INGREDIENTSCAS Num b erComponents Typical WeightPercentageMethanol 22-36% 67-56-1Water 64-78% 7732-18-54. FIRST AIDEyes: If irritation or redness develops, move victim away from exposure and into fresh air. Flush eyes with clean water. If symptoms persist, seek medical attention.Skin: Remove contaminated shoes and clothing and cleanse affected area(s) thoroughly bywashing with mild soap and water. If irritation or redness develops, seek medical attention.Inhalation: If respiratory symptoms develop or other symptoms of exposure develop, move victim away from source of exposure and into fresh air. If symptoms persist, seek medical attention. If victim is not breathing, clear airway and immediately begin artificial respiration. If breathingdifficulties develop, oxygen should be administered by qualified personnel. Seek immediate medical attention.Product #(s) – 4105Ingestion: Aspiration hazard. Do not induce vomiting or give anything by mouth because thismaterial can enter the lungs and cause severe lung damage. If victim is drowsy or unconscious and vomiting, place on the left side with the head down. If possible, do not leave victim unattended and observe closely for adequacy of breathing. Seek immediate medical attention.Note to Physicians: Ethanol significantly decreases the toxicity of methanol because it competes for the same metabolic enzymes, and has been used to treat methanol poisoning.Epinephrine and other sympathomimetic drugs may initiate cardiac arrhythmias in persons exposed to high concentrations of hydrocarbon solvents (e.g., in enclosed spaces or with deliberate abuse).The use of other drugs with less arrhythmogenic potential should be considered. If sympathomimetic drugs are administered, observe for the development of cardiac arrhythmias.Medical Conditions: Exposure to high concentrations of this material may increase the sensitivity of the heart to certain drugs. Persons with pre-existing heart disorders may be more susceptible to this effect (see Note to Physician above).5. FIRE FIGHTING MEASURESSuitable Extinguishing Media: Dry chemical, CO2, water spray or alcohol-resistant foam. .Water spray is recommended to cool or protect exposed materials or structures. Water may be ineffective for extinguishment, unless used under favorable conditions by experienced fire fighters. Carbon dioxide can displace oxygen. Use caution when applying carbon dioxide in confined spaces.Specific Hazards: This material is flammable and can be ignited by heat, sparks, flames or other sources of ignition (e.g., static electricity, pilot lights or mechanical/electrical equipment). Flame is invisible in daylight. Vapors may travel considerable distances to a source of ignition where they can ignite, flashback or explode. May create vapor/air explosion hazard indoors, in confined spaces, outdoors or in sewers. If container is not properly cooled, it can rupture in the heat of a fire. Vapors are heavier than area and can accumulate in low areas.Hazardous Combustion Products: Toxic gases and vapors; oxides of carbon and formaldehyde.Special Firefighting Procedures: For fires beyond the initial stage, emergency responders in the immediate hazard area should wear bunker gear. When the potential chemical hazard is unknown, in enclosed or confined spaces, or when explicitly required by DOT, a self-contained breathingapparatus should be worn. In addition, wear other appropriate protective equipment as conditions warrant (see Section 8). Isolate immediate hazard area and keep unauthorized personnel out. Stop spill/release if it can be done with minimal risk. Move undamaged containers from immediatehazard area if it can be done with minimal risk. Water spray may be useful in minimizing ordispersing vapors and to protect personnel. Cool equipment exposed to fire with water, if it can be done with minimal risk. Avoid spreading burning liquid with water used for cooling purposes.6. ACCIDENTAL RELEASE MEASURESPersonal Precautions: Flammable. Spilling of liquid product will create a fire hazard and may form an explosive atmosphere. Keep all sources of ignition and hot metal surfaces away fromspill/release if safe to do so. The use of explosion-proof equipment is recommended. Stay upwind and away from spill/release. For large spills, notify people down-wind of spill/release, isolateimmediate hazard area and keep unauthorized personnel out. Wear appropriate protectiveequipment including respiratory protection as conditions warrant (see Section 8). See Sections 2 and 7 for additional information on hazards and precautionary measures.Product #(s) – 4105Environmental Precautions: Stop spill/release if it can be done with minimal risk. Prevent spilled material from entering sewers, storm drains, other unauthorized treatment drainage systems, and natural waterways. Use foam on spills to minimize vapors. Use water sparingly to minimizeenvironmental contamination and reduce disposal requirements. If spill occurs on water, notify appropriate authorities. Spills into or upon navigable waters, the contiguous zone, or adjoiningshorelines that cause a sheen or discoloration on the surface water, may require notification of the National Response Center (phone number 800-424-8802).Methods for Containment and Clean-Up: Notify relevant authorities in accordance with allapplicable regulations. Immediate cleanup of any spill is recommended. Dike far ahead of spill for later recovery or disposal. Absorb spill with inert material such as sand, earth or other non-combustible material, and place in suitable container for disposal. If spilled on water remove with appropriate methods (e.g., skimming, booms or absorbents). In case of soil contamination, remove contaminated soil for remediation or disposal, in accordance with local regulations.7. HANDLING AND STORAGEPrecautions for Safe Handling: Keep away from ignition sources such as heat/sparks/open flames – No smoking. Take precautionary measures against static discharge. Non-sparking tools should be used. Wear protective gloves/clothing and eye/face protection. Wash thoroughly after handling.Use good personal hygiene practices and wear appropriate personal protective equipment (see Section 8).Flammable. May vaporize easily at ambient temperatures. The vapor is heavier than air and may create an explosive mixture of vapor and air. Beware of accumulation in confined spaces and low lying areas. Open container slowly to relieve any pressure. Electrostatic charge may accumulate and create a hazardous condition when handling or processing this material. To avoid fire orexplosion, dissipate static electricity during transfer by bonding and grounding containers andequipment before transferring material. The use of explosion-proof equipment is recommended and may be required (see appropriate fire codes). Refer to NFPA-77 and/or API RP 2003 for specific bonding/grounding requirements. Do not enter confined spaces such as tanks or pits withoutfollowing proper entry procedures such as ASTM D-4276 and 29CFR 1910.146. Do not wearcontaminated clothing or shoes. Keep contaminated clothing away from sources of ignition such as sparks or open flames. Use good personal hygiene practice.Conditions for Safe Storage: Keep container(s) tightly closed. Use and store this material in cool, dry, well-ventilated areas away from heat and all sources of ignition. Post area “No Smoking or Open Flame.” Store only in approved containers. Keep away from any incompatible material (see Section 10). Protect container(s) against physical damage. Outdoor or detached storage ispreferred. Indoor storage should meet OSHA standards and appropriate fire codes.8. EXPOSURE CONTROLS/PERSONAL PROTECTIONExposure GuidelinesComponent ACGIH TLV ACGIH STEL OSHA PEL OSHA STELMethanol 200 ppm(Skin) 250 ppm(Skin)200 ppm(Skin)250 ppm(Skin)Product #(s) – 4105Engineering Controls: If current ventilation practices are not adequate to maintain airborneconcentrations below the established exposure limits, additional ventilation or exhaust systems may be required.Specific Personal Protective EquipmentEye/Face Protection: The use of eye protection that meets or exceeds ANSI Z.87.1 isrecommended to protect against potential eye contact, irritation or injury. Depending on conditions of use, a face shield may be necessary.Skin: The use of gloves impervious to the specific material handled is advised to prevent skin contact. Users should check with manufacturers to confirm the breakthrough performance of their products. Depending on exposure and use conditions, additional protection may be necessary to prevent skin contact including use of items such as chemical resistant boots, aprons, arm covers, hoods, coveralls or encapsulated suits. Suggested protective materials: butyl and nitrile rubbers.Respiratory Protection: Where there is potential for airborne exposure above the exposure limits,a NIOSH approved air purifying respirator with an organic vapor cartridge may be used.A respiratory protection program that meets OSHA's 29 CFR 1910.134 and ANSI Z88.2requirements must be followed whenever workplace conditions warrant a respirator's use. Air- purifying respirators provide limited protection and cannot be used in atmospheres that exceed the maximum use concentration as directed by regulation or the manufacturer’s instructions, in oxygen deficient (less than 19.5% oxygen) situations or under conditions that are immediately dangerous to life and health (IDLH).Use a positive pressure air supplied respirator if there is potential for uncontrolled release, exposure levels are unknown, or any other circumstances where air-purifying respirators may not provide adequate protection.Other Protective Equipment: Eye wash and quick-drench shower facilities should be available in the work area. Thoroughly clean shoes and wash contaminated clothing before reuse.Suggestions provided in this section for exposure control and specific types of protectiv e equipment are based on readily available information. Users should consult with the specific manufacturer to confirm the performance of their protective equipment. Specific situations may require consultation with industrial hygiene, safety, or engineering professionals.9. PHYSICAL AND CHEMICAL PROPERTIES (approximate v a lues)Appearance: Clear, blue liquidOdor: Mild alcoholOdor threshold: 4.2-596 ppmpH: Not applicableMelting/Freezing Point: -97.8˚C /208˚FBoiling point (at 1 atm): 64.7˚C / 148 ˚FFlash Point: 35 ˚C / 9 ˚F (Closed Cup)Auto-Ignition Temperature: 470 ˚C / 878 ˚FEvaporation rate (butyl acetate = 1): 4.1Flammability (solid, gas): Not applicableExplosive Limits: Lower – 6%/ Upper – 36%Vapor Pressure: 92 mmHg @ 20 ˚C / 68 ˚FProduct #(s) – 4105Vapor Density (air = 1): 1.1 @ 15 ˚C / 59 ˚FSpecific gravity (H20 = 1): 0.79 @ 20˚C / 68 ˚FSolubility in water: SolublePartition Coefficient: n-octanol/water: Log P = -0.77Decomposition Temperature: No dataViscosity: 5.81 x 10-7 m2/s @ 40 ˚C / 104 ˚F10. STABILITY AND REACTIVITYStability (thermal, light, etc.): Stable under normal conditions of storage and handling.Conditions to Avoid: Avoid all possible sources of ignition (see Sections 5 and 7).Incompatibility (materials to avoid): Avoid contact with strong acids, bases and oxidizers such as liquid chlorine and oxygen. Contact with these materials may cause a violent or explosive reaction.May be corrosive to lead, aluminum, magnesium and platinum. May react with metallic aluminum or magnesium and generate hydrogen gas. May attack some forms of plastic, rubber and coatings.Hazardous Decomposition Products: Thermal decomposition may release carbon monoxide, carbon dioxide, and formaldehyde.Hazardous Polymerization: Will not occur.11. TOXICOLOGICAL INFORMATIONAcute Toxicity:Product/Ingredient Name Result Species DoseMethanol (major ingredient) LD50 OralLD50 DermalLC50 Inhalation (vapor) RatRabbitRat>2528 mg/kg17,100 mg/kg13.3 mg/l – 6hrNote: Assigned to classification based on human experience and not animal data.Skin Corrosion/Irritation: Causes mild irritation. Repeated exposure may cause dryness orcracking.Serious Eye Damage/Irritation: Causes mild irritation.Signs and Symptoms: High concentrations can cause minor respiratory irritation, headache,drowsiness, dizziness, loss of coordination, disorientation and fatigue. Ingestion can causeirritation of the digestive tract, nausea, abdominal pain, vomiting and visual disturbances ranging from blurred vision to light sensitivity, blindness or death.Skin Sensitization: None reportedRespiratory Sensitization: None reportedGerm Cell Mutagenicity: There is insufficient information available to conclude that methanol is mutagenic.Carcinogenicity: Methanol did not demonstrate carcinogenic effects in rats and mice treated via whole body inhalation at concentrations > 1.3 mg/l in air. There is insufficient informationavailable to conclude that methanol is carcinogenic. It is not listed by NTP, IARC or OSHA.Product #(s) – 4105Reproductive Toxicity: Methanol has produced fetotoxicity in rats and teratogenicity in miceexposed by inhalation to high concentrations of methanol vapors.Specific Target Organ Toxicity (Single Exposure): Methanol ingestion causes damage to the optic nerve causing blindness. May cause drowsiness and dizziness.Specific Target Organ Toxicity (Repeated Exposure): There is insufficient informationavailable to conclude that methanol causes target organ effects from repeated exposure.Aspiration Hazard: May be fatal if swallowed and enters airways.12. ECOLOGICAL INFORMATIONToxicity:Ingredient Name Result Species ExposureMethanol (major ingredient) Acute EC50 = 16.912 mg/L Marine WaterAcute LC50 = 2500000 ug/L Marine WaterAcute LC50 = 3289 mg/L Fresh WaterAcute LC50 > 100000 ug/L Fresh WaterAlgaeCrustaceansDaphniaFish96 hours48 hours48 hours96 hoursPersistence and Degradability: Methanol biodegrades easily in water and soil.BOD5 = 1.1COD = 1.05 – 1.55, 99%Bioaccumulative Potential: Risk of bioaccumulation is low (BCF <500 and low log K ow <4). BCF =0.2 - <10 Log K ow = -0.77Mobility in Soil: Methanol is highly mobile. Adsorption coefficient (K oc) solid phase/liquid phase = 1 Other Adverse Effects: None known13. DISPOSAL CONSIDERATIONSThe generator of a waste is always responsible for making proper hazardous waste determinations and needs to consider state and local requirements in addition to federal regulations.Recycle wherever possible. Large volumes may be suitable for re-distillation or, if contaminated, incinerated. Can be disposed of in a sewage treatment facility.This material, if discarded as produced, would not be a federally regulated RCRA “listed” hazardous waste. However, it would likely be identified as a federally regulated RCRA hazardous waste for the following characteristic of ignitability (D001). See Sections 7 and 8 for information on handling,storage and personal protection and Section 9 for physical/chemical properties. It is possible that the material as produced contains constituents which are not required to be listed in the MSDS but could affect the hazardous waste determination. Additionally, use which results in chemical orphysical change of this material could subject it to regulation as a hazardous waste.14. TRANSPORT INFORMATIONDOT/TDG Proper Shipping Name: Flammable Liquid n.o.s. (Methanol)Product #(s) – 4105DOT/TDG Identification Number: UN1993DOT Hazard Class: 3 / TDG Hazard Class: 3(6.1)DOT/TDG Packing Group: IIERG Guide Number: 131Marine Pollutant: No15. REGULATORY INFORMATIONTSCA: Methanol is listed on the TSCA inventory.DSL: Methanol is listed on the DSL inventory.OSHA (Occupational Safety and Health Administration): This material is considered to be hazardous as defined by the OSHA Hazard Communication Standard.This material has not been identified as a carcinogen by NTP, IARC or OSHACERCLA/SARA – Section 302 Extremely Hazardous Substances and TPQ (in pounds): This material does NOT contain chemicals subject to the reporting requirements of SARA 302 and 40 CFR 355 Appendix A and B.EPA (CERCLA) Reportable Quantity (in pounds): This material contains the following chemicals subject to the reporting requirements of 40 CFR 302.4.Component Concentration RQMethanol 22-36% 500 lbs CERCLA/SARA - Sections 311/312 (Title III Hazard Categories):Acute: Yes Chronic: Yes Fire: Yes Reactivity: NoCERCLA/SARA – Section 313 and 40 CFR 372: This material contains the following chemicals subject to the reporting requirements of SARA 313 and SARA Title III and 40 CFR:Component Concentration de minimisMethanol 22-36% 1% California Safe Drinking Water and Toxic Enforcement Act of 1986 (Proposition 65): This material contains detectable chemicals known to the State of California to cause cancer and/or reproductive toxicity.Component Concentration EffectMethanol 22-36% Developmental Canada:This product has been classified in accordance with the hazard criteria of the Controlled Products Regulations (CPR) and the SDS contains all the information required by the Regulations.WHMIS Hazard Class: B2, D1B, D2A, D2B16. OTHER INFORMATIONIssue Date: May 2, 2013Previous Issue Date: May 2, 2013Change: Updated to new GHS compliant HCS 2012 criteriaProduct #(s) – 4105DISCLAIMER OF EXPRESSED AND IMPLIED WARRANTIESThe information in this document is believed to be correct as of the date issued. HOWEVER, NO WARRANTY OF MERCHANTABILITY, FITNESS FOR ANY PARTICULAR PURPOSE, OR ANY OTHER WARRANTY IS EXPRESSED OR IS TO BE IMPLIED REGARDING THE ACCURACY OR COMPLETENESS OF THIS INFORMATION, THE RESULTS TO BE OBTAINED FROM THE USE OF THIS INFORMATION OR THE PRODUCT, THE SAFETY OF THIS PRODUCT, OR THEHAZARDS RELATED TO ITS USE. This information and product are furnished on the condition that the person receiving them shall make his own determination as to the suitability of the product for this particular purpose and on the condition that he assumes the risk of his use thereof.。
E-TP-100(伊朗标准)

ENGINEERING STANDARDFORPAINTSORIGINAL EDITIONJULY 1994This standard specification is reviewed andupdated by the relevant technical committee onOct. 2000(1), Feb. 2004(2) and Nov. 2006(3). Theapproved modifications are included in thepresent issue of IPS.This Standard is the property of Iranian Ministry of Petroleum. All rights are reserved to the owner. Neither whole nor any part of this document may be disclosed to any third party, reproduced, stored in any retrieval system or transmitted in any form or by any means without the prior written consent of the Iranian Ministry of Petroleum.CONTENTS : PAGE No.1. SCOPE AND FIELD OF APPLICATION (2)2. REFERENCE STANDARDS (2)3. DEFINITIONS (4)4. THE NEED FOR STANDARD (6)5. CORROSIVE ENVIRONMENTS (6)6. ADHESION OF PAINT TO THE SUBSTRATE (8)7. FACILITIES FOR APPLICATION OF COATINGS (9)8. REQUIREMENTS (9)8.1 General (9)8.2 Surface Preparation (10)8.3 Paint Application (12)8.4 Priming and Painting (see IPS-C-TP-102) (14)9. PAINT SCHEDULE (23)10. PAINT SYSTEMS (28)11. PAINT COLOR SCHEDULE (36)APPENDICES:APPENDIX A BASIC PRINCIPLES (45)A.1 CORROSION PREVENTION BY PAINT COATINGS (45)A.2 BARRIER CHARACTERISTICS (45)A.3 ELECTRICAL METHODS (45)A.4 CHEMICAL INHIBITION (46)APPENDIX B (47)B.1 CHARACTERISTIC OF PROTECTIVE SYSTEMS (47)B.2 CHARACTERISTICS OF METALLIC COATINGS (50)SOME OTHER PROTECTIVE SYSTEMS (51)B.3 CHARACTERISTICSOFAPPENDIX C INTERNAL PAINTING OF ABOVE GROUND STEELTANKS, LPG SPHERES AND VESSELS (57)C.1. GENERAL (57)C.2 HORIZONTAL TANKS / VESSELS (57)C.3 SPHERES AND CYLINDRICAL VESSELS FOR LIQUEFIEDPETROLEUM GASES UNDER PRESSURE (57)C.4 VERTICAL TANKS (58)APPENDIX D TYPICAL REFINERY PAINTING SYSTEMS (64)APPENDIX E TYPICAL PAINTING SYSTEMS FOR FRESH WATER VESSELS (68)APPENDIX F TYPICAL SHIP PAINT SYSTEMS (69)1. SCOPE AND FIELD OF APPLICATIONThis Engineering Standard gives the minimum requirements mainly for initial construction and also maintenance painting of metal surfaces. The standard also gives minimum requirements for surface preparation and painting of piping, plant, equipment, storage tank, building etc. which will be exposed to different corrosive environments. Painting schedule, paint systems and paint color schedules are included in this respect.The standard is intended for corrosion protection of steel structures of oil, gas and petrochemical industries mainly for refineries, chemical and petrochemical plants, gas plants, above ground facilities of gas transmission and distribution systems, marine structures and where applicable, in exploration, production and new ventures. This engineering standard is limited mainly to the liquid applied paints (usually by brush or spray), metallic coating materials that are commonly used for corrosion protection in atmospheric or immersion service is also included. The rate of base metal corrosion where such coatings are used should not exceed approximately 1.3 mm/year (50 mils/year). For corrosion rate above this, both in atmospheric and immersion service, or where catastrophic failure is of concern, these coatings shall not be used, and corrosion-protective measures shall include the use of more corrosion-resistant alloys, cladding and special coatings and linings (see IPS-E-TP-270, IPS-E-TP-350 and IPS-E-TP-820) shall apply.In addition, internal protection of pipes for water supply and external protection of underground structures are not covered.It should be noted that ten different paint groups including 54 paint systems are indicated for a number of applications in section 9 (paint schedule). The user shall therefore decided at the design stage or at the start of a project, which paint system is to be used.Definitions, types of corrosion environments and standards of surface preparation are also specified herein this standard.The basic principles of corrosion prevention by paints are discussed in Appendix A while Appendix B gives the characteristic of some paint systems. Appendices C, D, E and F introduce typical painting systems for storage tanks, refinery, fresh water vessels and ships respectively.Note 1:This standard specification is reviewed and updated by the relevant technical committee on Oct. 2000. The approved modifications by T.C. were sent to IPS users as amendment No. 1 by circular No. 133 on Oct. 2000. These modifications are included in the present issue of IPS.Note 2:This standard specification is reviewed and updated by the relevant technical committee on Feb. 2004. The approved modifications by T.C. were sent to IPS users as amendment No. 2 by circular No 256 on Feb. 2004. These modifications are included in the present issue of IPS.Note 3:This standard specification is reviewed and updated by the relevant technical committee on Nov. 2006. The approved modifications by T.C. were sent to IPS users as amendment No. 3 by circular No 311 on Nov. 2006. These modifications are included in the present issue of IPS.2. REFERENCE STANDARDSThroughout this Standard the following dated and undated standards/codes are referred to. These referenced documents shall, to the extent specified herein, form a part of this standard. For dated references, the edition cited applies. The applicability of changes in dated references that occur after the cited date shall be mutually agreed upon by the Company and the Vendor. For undated references, the latest edition of the referenced documents (including any supplements and amendments) applies.AWWA (AMERICAN WATER WORKS ASSOCIATION)C210BSI (BRITISH STANDARDS INSTITUTION)BS EN 1089 "Transportable Gas Cylinder"3PartBS 381C "Colors for Identification, Coding and Special Purposes"BS 534 "Specification for Steel Pipes, Joints and Specials for Water, and Sewage"BS 729 "Hot-Dip Galvanized Coatings on Iron and Steel Articles"Code"BS1133 "PackagingBS 1319 "Specification for Medical Gas Cylinders, Valves and Yoke Connections"BS 1706 "Electroplated Coatings of Cadmium and Zinc on Iron and Steel"BS 1710 “Preparation of Steel Sub Surface before Application of Paint and Related Products”Identification”7079 “ColorBSBS 2015 "Glossary of Paint Terms"BS 2569 "Sprayed Metal Coatings"BS 3294 "The Use of High Strength Friction Grip Bolts in Structural Steel work"BS 3382 "Electroplated Coatings on Threaded Components"BS 3698 "Calcium Plumbate Priming Paints"BS 4147 "Hot Applied Bitumen Based Coating for Ferrous Products"BS 4164 "Coal Tar Based Hot Applied Coating Materials for Protecting Iron and Steel, Including Suitable Primers where Required"BS 4604 "The use of High Strength Friction Grip Bolts in Structural Steel Work, Metric Series"BS 4652 "Metallic Zinc-Rich Priming Paint (Organic Media)"BS 4800 "Specification for Paint Colors for Building Purposes"BS 4921 "Sherardized Coatings on Iron and Steel Articles"BS 5493 "Code of Practice for Protective Coating of Iron and Steel Structures against Corrosion"CP (CODES OF PRACTICE)CP 110 "Structural use of Concrete"CP 114 "Structural use of Reinforced Concrete in BuildingsCP 117 "Composite Construction in Structural Steel and Concrete"CP 1021 "Cathodic Protection"DIN (DEUTSCHES INSTITUTE FUR NORMUNG EV.)DIN 18364 "Works for Protection against Corrosion of Steel and Aluminum"IPS (IRANIAN PETROLEUM STANDARDS)NACE (NATIONAL ASSOCIATION OF CORROSION ENGINEERS)Practice, Repair of Lining Systems"RP-01-84 "RecommendationSSPC (STEEL STRUCTURES PAINTING COUNCIL)"Manual, Volume 1 and Volume 2"3. DEFINITIONSAcid PicklingIs a treatment for removal of rust and mill scale from steel by immersion in an acid solution containing an inhibitor. Pickling should be followed by thorough washing and drying before painting.Blast CleaningCleaning and roughening of a surface (particularly steel) by the use of metallic grit or nonmetallic grit (sand) or metal shot (usually steel), which is projected against a surface by compressed air, centrifugal force, or water.CoatingGeneric term for paints, lacquer, enamels, etc. A liquid, liquefiable or mastic composition that has been converted to a solid protective, decorative, or functional adherent film after application as thin layer.ColorA phenomenon of light or visual perception that enables one to differentiate otherwise identical objects.Corrosion ProtectionCorrosion protection is the separation of the metallic material from the attacking medium by paint or coating.Hand CleaningSurface preparation using hand tools such as wire brushes, scrapers, and chipping hammers.ImmersedIs defined as permanent immersion such as submerged structures, offshore drilling rigs, etc.Intermediate Coat (Undercoat)The paint intended to be used between primer and top coat in a paint system.Manual CleaningIncludes hand cleaning and power tool cleaning.Marine AtmosphereIs defined by frequent and relatively high concentration of salt mist, but it does not imply direct contact with salt spray or splashing waves; it contains a high concentration of chloride in contrast to the high concentration of sulphur dioxide in the industrial environment.Metallic CoatingA metallic coating means one or more layers of metal on a metal substrate (base material).Non Saline WaterIs defined as potable and non-potable water applicable to river installations, sewage treatment tanks, water tanks, and domestic water systems.Paint (or Coating)Is defined one or more separate, coherent layers consisting of non-performed materials and a binder normally of organic nature.Power Tool CleaningUse of pneumatic and electric portable power tools to prepare a substrate for painting.PrimerIs a mixture of binder, inhibitive pigment and solvent? It is used as a first coat on a steel base (base material).Note: Swedish standard SIS 055900 include…..Sea WaterIs defined as sea and other saline waters and estuary water.ShadeMeans a color produced by a pigment or dye mixture having some black in it.Splash ZoneIs defined as wind and water area of floating and tidal structures, such as wharfs, piers, sea walls, platforms, etc. or frequent salt spray.Surface PreparationAny method of treating a surface in preparation for painting. Swedish standards include photographic depictions of surface appearance of hand and power tool cleaning and various grades of blast cleaning over four initial mill scale and rust conditions of new steel.Surface ProfileSurface profile is a measurement of the roughness of the surface which results from abrasive blast cleaning. The height of the profile produced on the surface is measured from the bottoms of the lowest valleys to the tops of the highest peaks.TintMeans a color slightly different from the one under consideration.Top Coat (Finish)The paint intended to be the last coat applied in a coating system; usually applied over a primer, or intermediate coat.Tie CoatIntermediate coat used to bond different types of paint coats. Coating used to improve the adhesion of succeeding coatings.Note: For glossary of paint terms see also BS 2015.4. THE NEED FOR STANDARDThe potential life of a protective system is unlikely to be realized unless:a) The correct choice of system is made;b) the materials used in the system can be supplied when required and with the propertiesattributed to them when making the choice;c) the materials are applied in conditions and with standards of workmanship described in theIPS-C-TP-102.d) the handling, transportation and storage (over which the main contractor has minimal control)of all materials and coated components results in no damage to the integrity of the materials or coating that cannot be completely restored;e) the erection procedures cause no damage to the coatings that can not be completelyrestored;f) such restoration of damaged areas results in a protection at least as good as that of theundamaged areas.There are many variable factors(both natural and otherwise) which can influence the fulfillment of all these conditions for success, and it follows that no two projects can be exactly similar, this is one reason why a "standard" specification shall always be included in a set of contract documents.5. CORROSIVE ENVIRONMENTS5.1 Rural EnvironmentAn interior and exterior atmospheric exposure that is virtually un-polluted by smoke and sulphur gases, and which is sufficiently inland to be unaffected by salt contaminations or the high humidities of coastal areas.5.2 Industrial EnvironmentAtmospheric exposures that include urban communities, manufacturing centers, and industrial plants (but would not include heavy industrial environments such as coke plants, which fall under chemical environments). The atmosphere contains a considerable amount of gas containing sulfur and industrial fumes that increase the rate of corrosion and adversely affect the paint life. This type of environment is categorized to three different zones as follows:Consists of normal indoor and outdoor weathering where light concentration of chemical fumes and light humidity conditions exist.5.2.2 Moderate industrial environmentConsists of:- industrial environment where moderately aggressive chemical, acid or caustic fumes exist;- un-polluted coastal atmosphere;- area where moderate humidity is found;- area where there is condensation, splash, spray, spillage and frequent immersion of fresh water in intermediate temperatures up to 80°C.5.2.3 Severe industrial environmentConsists of:- coastal polluted atmosphere;- severe industrial environment where manufacturing center and industrial plants exist (but not heavy industrial environments, which falls under chemical environments). And the atmosphere of which contains a considerable amount of gas containing sulfur and industrial fumes.- area of high humidity;- area where there is condensation, splash, spray, spillage and frequent immersion of salt water and mild corrosive products.5.3 Water Immersion Environment (for protection of substrate see also IPS-E-TP-270)5.3.1 Non saline waterPermanent immersion in fresh and potable water.5.3.2 Sea waterPermanent immersion in sea water and other saline water and estuary water.5.4 Chemical Environment (or Heavy Industrial Environment)An exposure in which strong concentrations of highly corrosive gases, fumes, or chemicals either in solutions or as solids or liquids contact the surface. The severity may vary tremendously from mild concentrations in yard areas to immersion in chemical. So, this type of environment is categorized to three different zones as follows:5.4.1 Mild chemical environmentChemical exposure to acidic, neutral and alkaline environment. (PH. 2 to 12).5.4.2 Moderate chemical environmentChemical exposure to mild chemical solvents and intermittent contact with aliphatic hydrocarbons (mineral, spirits, lower alchohols, glycols, etc.).Severe chemical exposure to oxidizing chemicals, strong solvents, extreme PH., or contamination of these with high temperature.Note:Protection of substrate in contact with severe chemical environment needs special lining which is beyond the scope of this standard (see table B.1 and IPS-E-TP-270, IPS-E-TP-350, IPS-E-TP-820).5.5 Marine EnvironmentConsists of three different corrosive environments:5.5.1 Atmospheric zoneThe zone of the platform which extends upward from the splash zone and is exposed to sun, wind, spray, and rain.5.5.2 Splash zoneThe zone of the fixed or floating offshore or onshore structure such as platforms, which is alternately in and out of the water because of the influence of tides, winds, and seas. Excluded from this zone are surfaces that are wetted only during major storms.5.5.3 Submerged zoneThe zone which extends downward from the splash zone and includes the position of the platform below the mudline (see water environment).5.6 Underground EnvironmentAll buried surfaces in direct contact with soil (inland, onshore, subsea) which is defined as earth, sand, rock, etc.Note:For protection of underground structures proper systems of coating shall be used which is beyond the scope of this standard (see Appendix B and IPS-E-TP-270).6. ADHESION OF PAINT TO THE SUBSTRATEThe primer is the critical element in most coating systems because it is most responsible for preserving the metallic state of the substrate, and it must also anchor the total system to the steel. This it may do in one of two ways, depending upon the nature of the primer vehicle. Most coatings adhere to metal via purely physical attractions (e.g. hydrogen bonds) that develop when two surfaces are brought closely together.Paint vehicles with polar groups(-OH,-COOH, etc.) have good wetting characteristics and show excellent physical adhesion characteristics (epoxies, oil paints, alkyds, etc.). Much stronger chemically bonded adhesion is possible when the primer can actually react with the metal, as in the case of wash primer pretreatment, or a phosphate conversion coating.For adhesion to take place, the coating and substrate must not be separated from one another. Any contaminant on the steel will increase the separation and decrease paint film adhesion.Moreover, reactive sites on steel at which adhesion can occur are masked not only by contamination, but also by chemically bound species which may themselves satisfy sites on the steel that would otherwise be available for reaction with the paint vehicle. Thorough surface preparation removes such contamination, and exposes many more reactive sites ,there by dramatically increasing the amount of surface area where adhesion can occur.7. FACILITIES FOR APPLICATION OF COATINGSSurface preparation is normally done by the contractor applying the coating.If blast cleaning is not available and it is necessary to use a surface preparation method that is inferior to blast cleaning, it is advisable to choose a paint which is compatible with that surface preparation; the advantages of some chemical resistant paints are lost if they are applied over inadequately prepared surfaces. When programming the work, factors to be considered include the following:a) The sequence of operations (e.g. blast-cleaning before fabrication is normally cheaper thanblast-cleaning after fabrication).b) The application time (e.g. length of a drying or curing time for coating).c) Methods of application (e.g. airless spray, or brush).d) The possible advantage or disadvantage of applying the final coat(s) on site. Some coatings(e.g. galvanizing) cannot be applied on site.8. REQUIREMENTS8.1 General8.1.1 The general technique of surface preparation shall be as recommended in IPS-C-TP-101 and the prepared surface before the application of the primer coat shall be in accordance with the applicable grade as specified in Table 1 (paint schedule).Unless otherwise stated, the prepared surface shall be in accordance with the applicable grade as specified in Swedish Standard, SIS 055900 or SSPC, or BS 4232, or DIN 18364 Standards.8.1.2 The painting system in general shall be specified in accordance with Table 1 (paint schedule).8.1.3 Color schemes shall comply with the color schedule in current use at the particular center and/or tables 3, 4 and 5 (paint color schedule) in clause 11.8.1.4 Paint systems are generally specified by dry film thickness of coat(s) and total dry film thickness of primer, intermediate and top coat rather than by the number of coats.8.1.5 Unless otherwise stated in the schedule the total dry film thickness of paint systems shall be 150 microns minimum. All paints and paint materials used shall comply with the specification given in IPS Standards for Paint Materials and they shall be obtained from approved manufacturers only. 8.1.6 All materials shall be supplied in the manufacturer’s original containers, durably and legibly marked with the description of the contents. This shall include the specification number, the color reference number, the method of application for which it is intended, the batch number, date of manufacture and the manufacturer’s name, initials, or recognized trade mark. No intermixing of different brands or types of paints will be permitted. The storage and preparation of paints and other coating materials shall be in accordance with the manufacturer’s instructions. For further information see IPS Standards for Paint Materials.8.1.7 The products of only a single paint manufacturer shall be used for each complete paint system. The use of different paint manufacturers’ products for successive coats on a single surface, or piece of equipment, is not permitted.8.1.8 The characteristics of paint systems are described in Appendix B.8.2 Surface Preparation8.2.1 General8.2.1.1 Paint life depends primarily on surface preparation. Surface preparation shall remove enough foreign bodies to allow the type of priming paint used to wet the surface thoroughly and develop adequate adhesion.8.2.1.2 For surface preparation reference is made to IPS-C-TP-101, following are some general requirements for surfaces to be painted.8.2.1.3 Steel surfaces shall be free from rust, mill scale, salts, oil, grease, moisture, etc. by the methods specified in IPS-C-TP-101.8.2.1.4 The use of so-called rust converters, rust stabilizers and similar means for chemically converting the corrosion products of the iron into stable iron compounds, is not permissible for steel structures. This also applies to penetrating agents intended to inhibit rust.8.2.1.5 After the surface preparation of the substrate, the grit, dust, etc. shall be removed and a layer of primer applied, before any detrimental corrosion or recontamination occurs.8.2.1.6 The priming paint is a good "wetting" type such as blast primer and is normally applied by brush (see Appendix B table 2).8.2.1.7 Fabrication should preferably be complete before surface preparation begins.8.2.1.8 If hot-dip galvanized steel, stainless steel and non-ferrous metal surfaces are to be painted,a suitable pretreatment in the form of a light blast cleaning with a suitable abrasive such as aluminum oxide shall be given to ensure proper adhesion of the subsequently applied paint system (see Table 6).8.2.1.9 Wood for woodwork should be treated with a shop-applied wood preservative, to prevent conditions under which organisms are likely to damage the wood.This preservative treatment shall not have any adverse effect on the subsequent paintwork. Wood to be painted or varnished shall be made free from contamination. If necessary, a stopping putty (paste filler) shall be used for the stopping of holes for unevenness in the woodwork.8.2.1.10 Concrete surfaces to be painted shall be clean, dry, structurally sound and be of adequate strength, free from laitance, and have some roughness to ensure proper paint adhesion. This surface preparation shall be obtained by blast cleaning, wire brushing with power tools, or etching with very dilute hydrochloric acid followed by rinsing with an excess of water. Mechanical cleaning is preferred to etching with hydrochloric acid and an excess of water, because concrete surfaces shall be dry to a humidity of not more than 4% wt. before paint is applied.8.2.2 Selection of cleaning method (s) (see IPS-C-TP-101 subsection 4.2)The cleaning method(s) shall be selected with reference to the following consideration. The choice between blast cleaning, acid-pickling, flame cleaning and manual cleaning is partly determined by the nature of the paint to be applied. It should be appreciated, however , that paint applied to a properly prepared (e.g. blast cleaned) surface always last longer than similar paint applied to flame cleaning or manual cleaned surfaces.8.2.2.1 Initial condition of surface (rust grade)8.2.2.2 New construction (uncoated surfaces)8.2.2.3 Maintenance (coated surfaces)8.2.3 Standards of surface preparation (see 4. 3. 2. 2 of IPS-C-TP-101)8.2.3.1 Blast cleaningThe following grades of surface finish are defined in accordance with SIS 055900.a) SA 3, blast cleaning to pure metal: Mill scale, rust and foreign matter shall be removedcompletely. Finally, the surface shall be cleaned with a vacuum cleaner, clean dry compressed air or a clean brush. It shall then have a uniform metallic color.b) SA 2½, very thorough blast cleaning: Mill scale, rust and foreign matter shall be removed tothe extent that the only traces remaining are slight stains in the form of spots or stripes. Finally, the surface shall be cleaned with a vacuum cleaner, clean dry compressed air or a clean brush.c) SA 2, thorough blast cleaning: Almost all mill scale, rust and foreign matter shall be removed,finally, the surface shall be cleaned with vacuum cleaner, clean dry compressed air or a clean brush. It shall then be grayish in color.d) SA 1, light blast cleaning: Loose mill scale, rust and foreign matter shall be removed.The grade of surface finish compares as follows with some other internationally recognized standards:STANDARD LEVEL OF CLEANLINESS IN DIFFERENT STANDARDSTYPE OFSURFACE PREPARATIONSIS 055900SWEDENSSPC &NACEUSABS 4232UKDIN 18364GERMANY REMARKSSt 2THOROUGHSCRAPING, BRU-SHING, GRINDINGETC.SP 2---HANDTOOLCLEANING--- --- ST2 OR SP2ANDHAND TOOLCLEANING ISRECOMMENDEDONLY FOR SPOTCLEANINGMANUAL CLEANINGSt 3VERY THOROUGH SCRAPING, BRU- SHING, GRINDINGETC.SP 3---POWER-TOOLCLEANING--- ---Sa 3 PURE METALSP 5TMO1-70-NO1WHITE METALFIRSTQUALITY---Sa 2 1/2 VERY THOROUGHSP 10TMO1-70-NO2NEAR WHITESECONDQUALITYENTROSTU-NGSGRAD 2Sa 2 THOROUGHSP 6TMO1-70-NO3COMMERCIALTHIRDQUALITYENTROSTU-NGSGRAD 3BLAST CLEANINGSa 1 LIGHTSP 7TMO1-70-N04BRUSH-OFF--- ---ACID PICKLING SP 8------ ---CHEMICALCLEANING SP 1SOLVENT CLEANING BS 5493 CP 30128.2.3.2 Manual cleaningManual cleaning using mechanical cleaning tools to remove mill scale and rust is the least satisfactory method of surface preparation and is used where blast cleaning is impractical or not economical. The surface produced shall be in accordance with IPS-C-TP-101 or SIS 055900 st3 orSSPC-SP 3.The manual cleaning methods shall not be used for the preparation of steel where high quality long-life systems are to be used.8.2.3.3 Chemical cleaninga) Acid pickling: Pickling shall be carried out in the workshop.The surface produced shall be in accordance with IPS-C-TP-101 Section 6. The process normally comprise:- Immersion in a bath of warm dilute sulphuric acid or phosphoric acid both to remove mill scale and rust.- Washing in a bath of warm water to remove all traces of sulphuric acid. This water wash may be omitted when phosphoric acid pickling is used.- Immersion in a bath of hot dilute phosphoric acid to provide a passivated surface suitable for painting. The contents of the baths shall be discarded when the concentration is below that indicated specifically for the bath or if accumulation of sediment causes staining of the work.b) Solvent cleaning: Solvent cleaning should be used prior to the application of paint and inconjunction with surface preparation methods specified above for the removal of rust, mill scale or paint, etc. Petroleum solvents such as kerosene, mineral spirits, or chlorinated solvents such as trichloroethylene or 1.1.1 trichloroethene can be used to dissolve and remove soil.Chlorinated solvents are also effective in removing heavy oils, greases and waxes (see IPS-C-TP-101 Section 5).8.2.4 Surface preparation for maintenanceInitially all areas of loosened paint and scale and all points of rusting should be located and treated in a manner essentially similar to the preparation detailed in the previous section. If such areas are sufficiently numerous as to make exact location and definition a difficult proposition, then whole paintwork should be prepared overall by sand-blasting, chipping, scraping and power wire brushing to the standards detailed in the previous section.All prepared areas shall then be degreased where necessary by solvent cleaning method. Surface preparation for maintenance shall be in accordance with IPS-C-TP-101 Section 13.8.3 Paint ApplicationPaint application shall be in accordance with IPS-C-TP-102, here are some general requirements for painting.8.3.1 GeneralAll surfaces shall receive an appropriate paint system as specified in Table 1, with the following exceptions:- any equipment furnished completely painted by the manufacturer unless it is specially required to match a color scheme or to repair damage to the paint film;- hot-dip galvanized steel, weathering steel, stainless steel and non-ferrous metals, monel, brass, copper, aluminum jacketing unless it is specially required;- nonmetallic surfaces;- nameplates, code stampings and push-buttons;- surfaces to be fireproofed;- concrete, brickwork, tile, glass and plastics,unless specially required;。
热镀锌钢白锈产生原因分析及预防
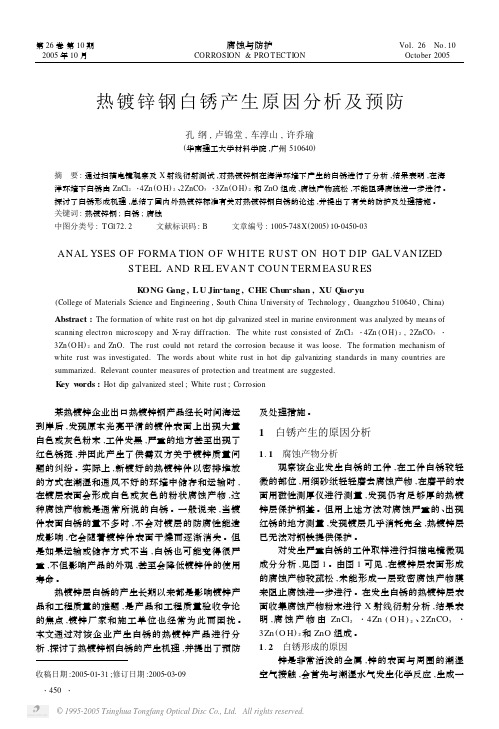
热镀锌钢白锈产生原因分析及预防孔纲,卢锦堂,车淳山,许乔瑜(华南理工大学材料学院,广州510640)摘 要:通过扫描电镜观察及X 射线衍射测试,对热镀锌钢在海洋环境下产生的白锈进行了分析,结果表明,在海洋环境下白锈由ZnCl 2・4Zn (O H )2、2ZnCO 3・3Zn (O H )2和ZnO 组成,腐蚀产物疏松,不能阻碍腐蚀进一步进行。
探讨了白锈形成机理,总结了国内外热镀锌标准有关对热镀锌钢白锈的论述,并提出了有关的防护及处理措施。
关键词:热镀锌钢;白锈;腐蚀中图分类号:T G172.2 文献标识码:B 文章编号:10052748X (2005)1020450203ANAL YSES O F FORMA TION O F W H ITE RU ST ON HO T DIP GAL VAN IZEDSTEEL AND R EL EVAN T COUN TERM EASU R ESK ONG G ang ,L U Jin 2tang ,CHE Chun 2shan ,XU Q iao 2yu(College of Materials Science and Engineering ,South China University of Technology ,Guangzhou 510640,China )Abstract :The formation of white rust on hot dip galvanized steel in marine environment was analyzed by means ofscanning electron microscopy and X 2ray diffraction.The white rust consisted of ZnCl 2・4Zn (O H )2,2ZnCO 3・3Zn (O H )2and ZnO.The rust could not retard the corrosion because it was loose.The formation mechanism of white rust was investigated.The words about white rust in hot dip galvanizing standards in many countries are summarized.Relevant counter measures of protection and treatment are suggested.K ey w ords :Hot dip galvanized steel ;White rust ;Corrosion 某热镀锌企业出口热镀锌钢产品经长时间海运到岸后,发现原本光亮平滑的镀件表面上出现大量白色或灰色粉末,工件发黑,严重的地方甚至出现了红色锈斑,并因此产生了供需双方关于镀锌质量问题的纠纷。
核心筒结构填充墙面层产生裂缝的质量控制措施
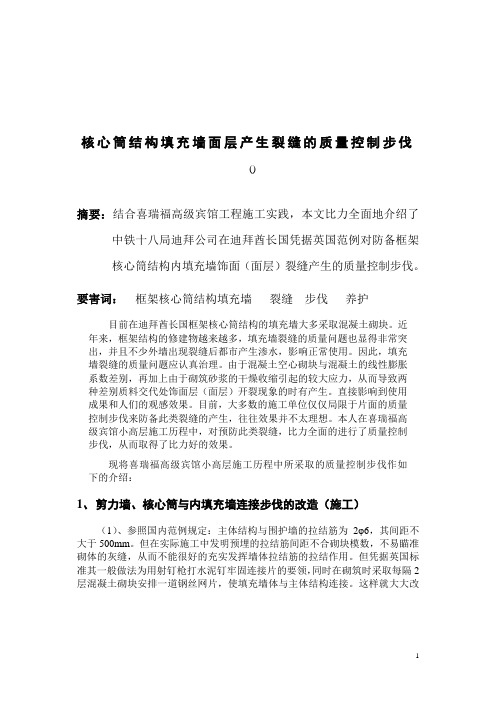
核心筒结构填充墙面层产生裂缝的质量控制步伐()摘要:结合喜瑞福高级宾馆工程施工实践,本文比力全面地介绍了中铁十八局迪拜公司在迪拜酋长国凭据英国范例对防备框架核心筒结构内填充墙饰面(面层)裂缝产生的质量控制步伐。
要害词:框架核心筒结构填充墙裂缝步伐养护目前在迪拜酋长国框架核心筒结构的填充墙大多采取混凝土砌块。
近年来,框架结构的修建物越来越多,填充墙裂缝的质量问题也显得非常突出,并且不少外墙出现裂缝后都市产生渗水,影响正常使用。
因此,填充墙裂缝的质量问题应认真治理。
由于混凝土空心砌块与混凝土的线性膨胀系数差别,再加上由于砌筑砂浆的干燥收缩引起的较大应力,从而导致两种差别质料交代处饰面层(面层)开裂现象的时有产生。
直接影响到使用成果和人们的观感效果。
目前,大多数的施工单位仅仅局限于片面的质量控制步伐来防备此类裂缝的产生,往往效果并不太理想。
本人在喜瑞福高级宾馆小高层施工历程中,对预防此类裂缝,比力全面的进行了质量控制步伐,从而取得了比力好的效果。
现将喜瑞福高级宾馆小高层施工历程中所采取的质量控制步伐作如下的介绍:1、剪力墙、核心筒与内填充墙连接步伐的改造(施工)(1)、参照国内范例规定:主体结构与围护墙的拉结筋为2φ6,其间距不大于500mm。
但在实际施工中发明预埋的拉结筋间距不合砌块模数,不易瞄准砌体的灰缝,从而不能很好的充实发挥墙体拉结筋的拉结作用。
但凭据英国标准其一般做法为用射钉枪打水泥钉牢固连接片的要领,同时在砌筑时采取每隔2层混凝土砌块安排一道钢丝网片,使填充墙体与主体结构连接。
这样就大大改进了墙体与主体框剪结构的联系,使墙体抵抗竖向变形的能力提高了约50%左右。
消除了主体与填充墙体竖向裂缝的产生(具体做法见下图1)。
图1 填充墙墙体与主体结构的连接(2)、在施工历程中,为了制止窗台与窗台墙交代处因受力不均及墙体压缩变形而产生裂缝现象,故在窗台处设置了2φ12,C20钢筋混凝土现浇带与主体领悟以抵抗变形缝的产生。
郡士辅料编号

郡士辅料编号,特征,说明及各类漆色表(纯文字版)分享 |2010-09-15 12:18:02 作者:张春宇来源:上上模型浏览次数:1414 网友评论 0 条郡士辅料编号名称特征说明B501 水性罐喷-光油 86ml 涂装后增加模型整体的光泽 (多用于民用车辆)B502 水性罐喷-半光油 86ml 涂装后的模型整体光泽统一 (多用于飞机)B503 水性罐喷-消光 86ml 涂装后的模型降低光泽度 (多用于军事模型)B504 金属打底补土罐喷 100ml 在金属\电镀件\蚀刻片表面增强漆的附着力B505 罐喷补土-1000 100ml 在模型图装前打底、统一底色 1000目B506 罐喷补土-500 100ml 在模型图装前打底、统一底色 500目B511 罐喷白补土-1000 180ml 在模型图装前打底、统一底色 1000目白色B513 罐喷罩光漆 170ml 涂装后增加模型整体的光泽(多用于民用车辆)B514 罐喷消光漆 170ml 涂装后的模型降低光泽度(多用于军事模型)B515 罐喷补土-1200 180ml 在模型图装前打底、统一底色 1200目B516 罐喷半光油 170ml 涂装后的模型整体光泽统一(多用于飞机)B517 罐喷树脂/金属专用补土 180ml 在金属\电镀件\蚀刻片表面增强漆的附着力B518 罐喷白补土-1000 180ml 在模型图装前打底、统一底色 1000目白色B519 罐喷补土-1000 170ml 在模型图装前打底、统一底色 1000目Cxxx 油性漆 10mlC030 消光剂 10ml 降低油性漆光泽度的添加剂C046 透明漆-光泽 10ml 涂装后增加模型整体的光泽(多用于民用车辆) CL184 超级光油 40ml 光泽度更高的罩光漆CS107 新世纪福音战士套装漆特定机体颜色套装CS108 新世纪福音战士套装漆特定机体颜色套装D173 模型调漆皿 11个模型漆调色时使用的小器皿GUGM01 高达画线笔(分涂装用、勾线用) 用于高达模型的上色Hxxx 水性漆 10mlHS13 水性涂料套装(10色、笔及调漆皿) 内含基本颜色,可自行配色HS21 模型旧化漆套装模型旧化专用涂料M131 喷涂彩绘用蓝色遮盖液 25ml 用于分色涂装时遮挡M132 喷涂彩绘用透明遮盖液 25ml 用于分色涂装时遮挡MC124 胶水 25ml 用于粘接模型零件MC127 胶水 40ml 用于粘接模型零件MCxxx 金属系油性漆 10mlMS231 贴纸软化剂 40ml 使贴纸和模型贴合更紧密MS232 贴纸软化剂接着剂 40ml 不仅起软化作用还带有背胶成分P118 管装补土 25g 用于模型表面的补缝、添洞PA142 喷笔专用气罐 170ml 代替气泵为喷笔提供高压气源PS152 简易喷笔MK-1型 0.4mm 气罐及喷笔PS153 简易喷笔MK-2型气罐及喷笔口径0.2,0.4mmPS154 简易喷笔MK-3型大气罐及喷笔(含笔架) 口径0.2,0.4mmPS257 喷笔清洁用稀料防扩散收集罐PS261 高级金属喷笔(单动) 0.3mm 模型图装用喷笔PS262 高级金属喷笔(双动) 0.3mm 模型图装用喷笔RP261 瓶装树脂/金属专用补土 40ml 在金属\电镀件\蚀刻片表面增强漆的附着力SB222 调漆瓶模型漆调配专用的玻璃瓶SF242 金属底漆 40ml 在金属表面增强漆的附着力(多用于蚀刻片)SF283 瓶装白补土-1000 40ml 在模型图装前打底、统一底色(强遮盖型)SF284 瓶装补土-1000 40ml 在模型图装前打底、统一底色 1000目SF285 瓶装补土-500 40ml 在模型图装前打底、统一底色 500目SM01 超级银 18ml 超级金属漆,覆盖力强,颗粒极细SM02 超级金 18ml 超级金属漆,覆盖力强,颗粒极细SM03 超级铁 18ml 超级金属漆,覆盖力强,颗粒极细SM04 超级不锈钢 18ml 超级金属漆,覆盖力强,颗粒极细T101 超级溶剂 50ml 可稀释水性、油性漆,图装必备T102 超级溶剂 110ml 可稀释水性、油性漆,图装必备T103 超级溶剂 250ml 可稀释水性、油性漆,图装必备T104 超级溶剂 400ml 可稀释水性、油性漆,图装必备T105 笔痕消除剂 40ml 添加到漆中,能减少手涂产生的笔痕T106 超级溶剂-高纯 110ml 可稀释水性、油性漆,高纯度型T107 工具专用清洁液 80ml 涂装工具清洗专用,溶解力强T108 超级溶剂-高纯 400ml 可稀释水性、油性漆,高纯度型T109 涂料清洗剂 450ml 涂装工具清洗专用,溶解力强君仕硝基涂料---Mr.COLOR"哑"指无光泽"IJA","IJN","RLM"," FS","BS"是各国制定的不同色表的色系名称"RAF"是皇家空军(Royal Air Force)的缩写"RN"是皇家海军(Royal Navy)的缩写1 光泽白2 光泽黑3 光泽红4 光泽黄5 光泽蓝6 光泽绿7 棕8 银9 金10 铜11 淡海鸥灰12 橄榄褐113 半光中灰14 半光海军蓝15 半光IJN中岛绿16 半光IJA绿17 RLM71暗绿18 半光RLM70黑绿19 半光沙褐20 半光淡蓝21 半光中石22 半光暗土23 暗绿224 天25 暗海灰26 鸭蛋绿27 内部绿28 钢/黑铁29 半光舰底红30 消光剂/哑色添加剂31 暗灰132 战舰暗灰233 哑黑34 光泽天蓝35 三菱IJN灰36 半光RLM74灰绿37 RLM75紫灰38 橄榄褐239 暗黄/沙黄40 德国灰41 红褐42 红木43 木棕44 甲板革45 帆布46 罩光漆/透明色47 光泽透明红48 透明黄49 光泽透明橙50 透明蓝51 半光肉52 田野灰254 哑卡其绿55 卡其56 IJA灰/明灰白257 金属蓝绿/青竹58 半光橙黄59 光泽橙60 半光RLM02灰61 烧铁62 哑白63 光泽粉64 光泽黄绿65 光泽亮蓝66 光泽亮绿67 光泽紫68 光泽洋红69 光泽降白70 暗绿71 午夜蓝72 半光中蓝73 光泽飞机灰74 空军蓝75 金属红76 金属蓝77 金属绿78 金属黑79 光泽明红80 半光钴蓝81 苹果褐90 明银92 半光黑100 葡萄酒红/栗色101 烟灰102 烟蓝107 人型白108 人型红109 人型黄110 人型蓝111 人型肉1112 人型肉2113 RLM04黄114 RLM23红115 RLM65淡蓝116 RLM66黑灰117 RLM76淡蓝118 RLM78淡蓝119 RLM79沙黄120 RLM80橄榄绿121 RLM81紫褐122 RLM82淡绿123 RLM83暗绿124 三菱暗绿125 引擎罩126 三菱仪表板127 中岛仪表板128 灰绿129 中岛暗绿130 川崎暗绿131 螺旋桨132 土绿133 土134 草绿135 俄国绿136 俄国绿2 151 珠光白152 珠光绿153 珠光红154 珠光蓝155 特级罩光漆/透明色156 特级白4157 特级黑158 特级意大利灰159 特级银160 珠光橙红201 荧光红202 荧光黄203 荧光橙204 荧光粉207 荧光绿301 灰FS36081302 绿FS34092303 绿FS34102304 橄榄褐FS34087 305 灰FS36118306 灰FS36270307 灰FS36320308 灰FS36375309 绿FS34079310 棕FS30219311 灰FS36622312 绿FS34227313 黄FS33531314 蓝FS35622315 灰FS16440316 光泽白FS17875 317 灰FS36231318 雷达罩319 淡绿320 暗绿321 淡褐322 氰蓝323 淡蓝324 淡灰325 灰FS26440326 蓝FS15044327 红FS11136328 蓝FS15050329 黄FS13538330 暗绿BS381C/641331 暗海灰BS381C/638 332 淡飞机灰BS381C/627 333 暗海灰BS381C/640 334 麦灰BS4800/18B21 335 中海灰BS381C/637 336 麻BS4800/10B21337 灰蓝FS35237338 淡灰FS36495339 引擎灰FS16081340 田野绿FS34097郡仕水溶性涂料---Hobby Color H1 白H2 黑H3 红H4 黄H5 蓝H6 绿H7 棕H8 银H9 金H10 铜H11 哑白H12 哑黑H13 哑红H14 橙H15 亮蓝H16 黄绿H17 Cocoa棕H18 钢/黑铁H19 粉H20 消光漆/哑色H21 降白H22 灰H23 明红H24 橙黄H25 天蓝H26 亮绿H27 革H28 金属黑/青铁H29 鲑粉H30 罩光漆/透明色H31 白绿H32 田野灰1H33 苹果褐H34 奶黄H35 钴蓝H36 暗绿H37 木棕H38 铁红/赤铁H39 紫H40 消光剂/哑色添加剂H41 苍绿H42 蓝灰H43 葡萄酒红/栗色H44 肉H45 淡蓝H46 翠绿H47 红棕H48 田野灰2H49 紫罗兰H50 莱姆绿H51 淡海鸥灰/浅海灰H52 橄榄褐1H53 中灰H54 海军蓝H55 午夜蓝H56 中蓝H57 飞机灰H58 内部绿H59 IJN绿/浓绿1H60 IJA绿/浓绿2H61 IJN灰/明灰白1 H62 IJA灰/明灰白2 H63 金属蓝绿/青竹H64 RLM71暗绿H65 RLM70黑绿H66 RLM79沙褐H67 RLM65淡蓝H68 RLM74暗灰H69 RLM75灰H70 RLM02灰H71 中石(RAF)H72 暗土(RAF)H73 暗绿(RN/RAF)H74 天/鸭蛋绿(RN/RAF) H75 暗海灰(RAF)H76 烧铁H77 胎黑H78 橄榄褐2H79 沙黄H80 卡其绿H81 卡其H82 军舰暗灰1 H83 军舰暗灰2 H84 红木H85 帆布H86 洋红H87 金属红H88 金属蓝H89 金属绿H90 透明红H91 透明黄H92 透明橙H93 透明蓝H94 透明绿H95 烟灰H96 烟蓝H97 荧光黄H98 荧光橙H99 荧光粉H100 荧光绿H301 灰FS36081H302 绿FS34092H303 绿FS34102H304 橄榄褐FS34087 H305 灰FS36118H306 灰FS36270H307 灰FS36320H308 淡鬼灰FS36375 H309 暗绿FS34079 H310 暗革FS30219 H311 伪装灰FS36622 H312 苍绿FS34227 H313 沙FS33531H314 鸭蛋蓝FS35622H315 灰FS16440H316 光泽白FS17875H317 暗海鸥灰FS36231 H318 雷达罩H319 淡绿/淡松叶H320 暗绿/浓松叶H321 淡棕/黄土H322 氰蓝H323 淡蓝H324 淡灰H325 灰FS26440H326 蓝FS15044H327 红FS11136H328 蓝FS15050H329 黄FS13538H330 暗绿BS381C/641H331 暗海灰BS381C/638H332 飞机灰BS381C/627H333 暗海灰BS381C/640H334 麦灰BS4800/18B21H335 中海灰BS381C/637H336 麻BS4800/10B21H337 灰蓝FS35237H338 淡灰FS36495H339 引擎灰FS16081H340 田野绿FS34097H341 黄沙H342 油污H343 煤灰H344 锈红H345 颗粒蓝H346 颗粒沙郡仕硝基金属漆---Mr.Metal Color211 铬银212 生铁213 不锈钢214 熟铁215 铜216 青铜217 金219 黄铜郡仕高达漆笔---Gundam Marker GM01 渗线黑GM02 渗线灰GM03 渗线棕GM04 金GM05 银GM06 高达蓝GM07 高达红GM08 高达黄GM09 高达绿GM10 高达黑GM11 高达白GM12 高达灰GM13 高达金属灰GM14 高达荧光粉GM15 高达荧光绿GM16 高达金属红GM17 高达金属蓝GM18 高达金属绿GM19 高达金属紫GM20 圆头渗线黑。