CH_w-15-rolling-plate-new
美国特色产品说明:0215型设备中文版说明书

verviewWell-suited for low traffic areas, this unit is similar to the 0210 but reduced capacity to dispense 200 C-fold or 275 multi-fold paper towels without adjustment or adapters and is fitted with tumbler lock and heavy-duty stainless steel piano hinge.American Specialties, I nc. | 441 Saw Mill River Road, Yonkers, NY 10701 | (914) 476-9000 | Model:#0215Issued:11/1/2021Revised:3/10/2023Page:1 of 2Revision :R1uStainability /lEEDPaper Towel Dispenser - Petite (Multi - C-Fold) -Surface MountedToilet Accessories CSI:10 28 13MR 6 (1)EQ 4.1 (1)EQ 4.2 (1)EQ 4.4 (1)661_1O peratiOn & M aintenancet echnical i nfOrMatiOn / p rOduct p rOpertiesi nstallatiOnW arrantySurface mount unit on wall or partition using five #10 self-threading screws (by others) through concealed mounting holes provided. Four mounting holes through back are keyhole slots for ease in hanging unit on pre-installed screws. Center top mounting hole is horizontal slot for ease of adjustment and vandal resistant locking. For compliance with 2010 ADA Accessibility Standars install unit so that centerline of towel dispenser slot is 48" [1219] maximum above finished floor (AFF).Manufacturer reserves the right to make changes to the design, dimensions or functionality of the product without formal notice.Towels are self-feeding as withdrawn by hand until supply is depleted. Unit may be reloaded with a partial load in-place and will continue to feed properly. Low level of towel supply is indicated from 35% capacity to empty. Unit is a reduced-size model and has less capacity than larger models, therefore it is recommended to use this unit in space-restricted or low traffic areas. Locking door prevents unauthorized access or removal.One (1) Y ear from date of InvoiceAmerican Specialties, I nc. | 441 Saw Mill River Road, Yonkers, NY 10701 | (914) 476-9000 | Model:CSI:#021510 28 13Toilet Accessories Issued:11/1/2021Revised:3/10/2023Page:Revision :Type 304 Stainless Steel - Matte Black Powder Coated Concealed multi-staked hinge - 3/16" Dia. [Ø5]200 C-fold or 275 multi-fold paper towelsPropertyValueDimensions Construction 11" [279] W x 8" [203] H x 4" [102] DManual - Pull T ype Surface MountedN/A2 of 2R1Power Operation Mounting Capacity。
Allwinner R8 Datasheet

REVISION HISTORYDECLARATIONTABLE OF CONTENTS5.3. DC Electrical Characteristics2.6.Memory Subsystem&Touch G-SENSORSPI1_CLK UART3_RX42 DDR3_D743 VCC3_DRAM79 AGND80 VRPSDC0_CMD 111PF3PE9 CSI_D6LCD_D10 141PD10PC19 163 VCC4function 0);3)Type: signal directionPC7 Input PC8 InputPE4 Input PE5 InputSignal Name DescriptionOthersVRP Reference voltageV IH High-Level Input Voltage V IL Low-Level Input VoltageFigure 5-1. Power Up Sequence5.5.2.Power Up Reset Sequence RequirementsThe device has a system reset signal to reset the board. When asserted, the following steps give an example of power up reset sequence supported by the R8 device.•AVCC ,VDD_CPU and VCC_DRAM can be powered up simultaneously.•VDD_INT can be powered up after VDD_CPU is powered up, the time difference is T1ms.•VCC can be powered up after VDD_INT is powered up, the time difference is T2ms.Figure 5-2. Power Up Reset Sequence5.5.3.Resume Power Up Sequence from Super Standby ModeTo resume a power up sequence when the device is in Super Standby mode:•VCC_DRAM and AVCC remains powered up always.•VDD_CPU can be powered up firstly.•VDD_INT can be powered up after VDD_CPU is powered up, the time difference is T1ms.•VCC can be powered up after VDD_INT is powered up, the time difference is T2ms.Figure 5-3. Exit Super Standby and Resume Power Up Sequence5.5.4.Power Down Sequence RequirementsTo reduce power consumption,the R8 can be partially powered down.The section lists the power down requirements in each mode.In Super Standby mode,•VCC_DRAM and AVCC must be kept powered up.•VDD_CPU,VDD_INT and VCC are powered down simultaneously.•VCC voltage fall time is more longer than VDD_INT.VDD_CPUVDD_CPU6.PIN ASSIGNMENT6.2.PACKAGE DIMENSIONThe following diagram shows the package dimension of R8.。
CW2015-电量计芯片datasheet

CW2015-DS V2.1
Mob:13510032582 QQ:316224953 Mail:fred@gold-luck.com
CW2015
Low-Cost Fuel Gauge IC with Low-SOC Alert
Features
System-Side or Pack-Side Fuel Gauging 3% Maximum Total SOC Measurement Error 14-bit Delta Sigma ADC for Temperature and Cell
Order Information
Name
CW201erature -20℃ to 70℃ -20℃ to 70℃
Package TDFN8 CSP9
Package Mark 2015CSAD 2015CSAC
Cellwise copyright reserved
UNITS V
V
V
DC Electrical Characteristics
(2.5≤VDD≤4.5, TA= -20 to 70OC, unless otherwise specified.)
PARAMETER
SYMBOL
CONDITIONS
Min. Typ. Max.
Active Current Sleep-Mode Current Time-Based Accuracy ADC input resistor ADC resolution
Cellwise copyright reserved
2
Gas Gauge IC Series
CW2015-DS V2.1
Timex Cr2016 Cell Indiglo Manual

wr50m manual - FixYa need manual gt, timex watch Indiglo WR30M Support /. Timex Cr2016 Cell Wr30m Watches At Timex watch. NEW Mens TIMEX INDIGLO Alarm Quartz Watch with Backlite *. 50M * T19281. Rare Timex Indiglo WR 30M CR2016 Cell Wristwatch /. eBay Instruction Manual.
Timex Expedition Watch Manual Indiglo from our library is free resource for Enter the Changing a CR2016 battery in a Timex Indiglo watch is not a hard task. Get the best deals on Timex Watches for Men when you shop the largest online Timex Ironman T5K790, 30 Lap Sports Watch with, Indiglo Night Light Men's TIMEX Water Resistant Watch w/ New Battery NEW From OLD STOCK Timex big size Men's Manual Wind Day Date Watch Leather Band. Problem with Watches. changed battery in timex indiglo alarm expedition cr2016 cannot restart watch. Where do I find a user manual for a Timex Expedition.
JBC-Tools_CLMU-A8_clmu-a8-lead-free-soldering-meta
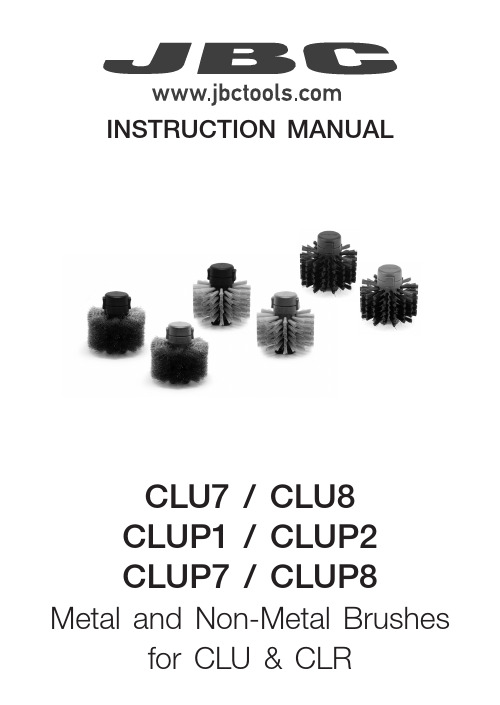
CLUP7 / CLUP8 Non-Metal* / Non-Metal HMP* Gentle
5s
1-2 s
1-2 s
Extended* Black
Extended* Blue
*Only use the non-metal brushes when they are rotating. Incorrect use will damage them.
For CLU pull the locking tab to open the splashguard.
CLR Splashguard
Press the brush buttons (1) to remove the brushes (2).
1
CLU
Align the brush with the axis and push them in until a click is heard. Check if the brush is properly fixed.
0021174-0222
130 mm
INSTRUCTION MANUAL
CLU7 / CLU8 CLUP1 / CLUP2 CLUP7 / CLUP8
Metal and Non-Metal Brushes for CLU & CLR
This manual corresponds to the following references:
CLMU-A7* CLMU-A8* *each ref. incl. 2 brushes
CLMU-P1* CLMU-P2*
Packing List
The following items should be included:
敦泰教程

California Instruments CSW Series 5550-33300 VA AC

InputVoltage Ranges Factory configured 187 to 264 Vrms, 3ø L-L (3 wire), or 342 to 457 Vrms, 3ø L-L (4 wire). A chassis ground is also required. Power Factor PFC Input, 0.99PFFrequency Range47 to 440 HzEfficiency70% min, at full loadRide Through10 ms minimumOutputPower5550 VA: 1ø or 3ø (systems up to 33,000 VA)AC or DC Output Voltage0 to156 Vrms L-N, low range; 0 to 312 Vrms L-N, high rangeCurrent Per Phase16A to 115V in 156V range; 8A to 230V in 312V range per, 1850 VA module.Power Factor of Load0 lagging to 0 leading (0-unity)Crest Factor 3.5:1 (peak output current to rms output current))Frequency Range Specifications apply DC, 40Hz to 5kHz. For output frequencies greater than 1 kHz, the max slew rateallowed is 1 kHz per second.Max Total Harmonic Distortion(Full Linear Load or No Load): 0.25% max, 40 to 100 Hz; 0.5% max to 500 Hz; and 1% max to 1 kHz plus 1%/kHz to 5 kHzAC Noise Level>60 dB rms below full output voltageAmplitude Stability With Remote Sense±0.1% of full scale over 24 hours at constant line, load and temperatureLine Regulation(DC, or 40 Hz to 5 kHz): ±0.015% of full scale for a ±10% input line changeLoad Regulation±0.025% of full scale voltage for a full resistive load to no load; above 1 kHz, add ±0%/kHzVoltage Accuracy±0.1% of range. Above 1 kHz, add 0.2%/kHz. Add ±0.1% of full scale for “AC PLUS DC” mode. Valid for 5 to 156 Vrms and10 to 312 Vrms at 25°CVoltage Resolution1mV (0.1V) Full ScaleFrequency Accuracy±0.01% at 25°C ±0.001%/°CFrequency Resolution40 Hz to 81.91 Hz (0.01 Hz)81.90 Hz to 819 Hz (0.01 Hz)820 Hz to 5000 Hz (1 Hz)Phase Accuracy, Phase-to-PhaseBalanced Linear Resistive Load±1% of Programmed valuePhase Angle Resolution0.1°Remote Output Voltage Sense 5 Vrms total lead drop, maxCSW Series : Product SpecificationsCommon Intput and OutputsRemote Inhibit A logic Low or High contact closure input to inhibit the outputsExternal Amplitude Modulation0 to 5 VRMS provides 0 to 20% output amplitude modulation (±2% of full scale output).External Drive Input Acts as Amplifier, 0 to 5 VRMS (DC to 5 kHz) or ±5 VDC input for zero to full scale programmed voltage output(±2% of full scale output). Individual inputs for an external signal for each of the three phases.Remote Programming Voltage0 to ±7.07 VDC provides zero to full scale programmed voltage output(±2% of full scale output).External Input Impedance40K (ohm symbol) for each of the three inputs.Externaly Sync External Sync allows the output frequency of the AC source to be synchronized to an external TTL level clock signal.LKM Clock and Lock Master. Enables synchronizing outputs of two or more California Instruments sources, one acts as master.LKS Clock and Lock AuxiliaryFront Panel Trigger, BNC Connector Output available at the front panel BNC connector that provides a negative going pulse for any programmed voltage or frequencychange. The trigger can be reassigned as an output when running list transients.Front Panel Phase A, B and C, BNC connectors These three outputs are representive of the programmed output waveform, magnitude and frequency. 0 to 4.86 Vrms represents 0 to a full-scale output voltage.206858.458.0223sales.ppd@CSW Series : Product SpecificationsEnvironmentalOperating Temperature 0°C to 45°C (32°F to 113°F)Storage Temperature -40°C to 70°C (-40°F to 158°F)CoolingAir is drawn in from the top, bottom, and sides and exhausted through the rear Humidity (Non-condensing)0 to 85% at 25°C (77°F); derate to 50% at 40°C (104°F)AltitudeOperating 10,000 ft, non operating 40,000 ftPhysicalDimensionsWidth: 19” (483 mm)Height: 8.75” (222 mm)Depth: 23.5” (597 mm)WeightCSW 5550 - 127 lbs (57.5 kg)Shipping Weight - US CSW - 160 lbs (72 kg)NoteMulti Chassis systems, dimension and weight are approximately x2, x3, x4, x5 and x6 CSW Specifications5550–33300 VAMeasurementsMeasurements - Standard (AC Measurements)Parameter Frequency Phase Voltage (AC)Current (AC rms)Real Power Apparent Power Power Factor Range40-81.91 Hz 82.0-819.1 Hz > 819 Hz 40-100 Hz 100-1000 Hz0-300 V0-50 A0-6 kW0-6 kVA0.00-1.00Accuracy* (±)1 ø mode (-1) 0.1% + 1 digit 0.5°0.5% + 250 mV 0.1% + 150 mA0.15% + 9 W0.15% + 9 VA 0.033 ø mode (-3)2°0.1% + 50 mA0.15% + 3 W 0.15% + 3 VA 0.01Resolution*.01 Hz / 0.1 Hz / 1 Hz0.1° / 1°10 mV 1 mA 1 W 1 VA 0.01* Accuracy specifications are in % of reading and apply above 100 counts. For multi-chassis configurations, current, power range and accuracy specifications are times three. Power factor accuracy applies for PF > 0.5 and VA > 50% of max. Frequency measurement specification valid for output > 30 Vrms.Constant Power AC ModeRMS VoltageR M S C u r r e n t5550 CSW Operating Areaper PhaseLow Range High Range16.0A11.8A8.0A 5.9A115V 156V 230V 312VHarmonic MeasurementsParameterRange Accuracy ( ± )Resolution Frequency fundamental 16.00 - 1000 Hz 2 counts 0.01 Hz to 1 Hz Frequency harmonics 32.00 Hz - 16 kHz 2º typ.0.5ºVoltage Fundamental 0.25V0.01V Harmonic 2 - 500.25V + 0.1% + 0.1%/kHz 0.01V CurrentFundamental 0.05A0.01A Harmonic 2 - 500.05A + 0.1% + 0.1%/kHz0.01AHarmonics frequency range in three-phase mode is 32 Hz - 16 kHz. Accuracy specifications are multiplied by the number of power sources in multi-source systems with the 3-phase (3Ø) or the number of sources times 3 in the 1-phase (1Ø) mode . Measurement bandwidth is limited to 16 Khz.ModelCSW5550CSW11100CSW16650CSW22200CSW17750CSW33300Multiplier 3Ø/1 Ø1/32/63/94/125/156/18CSW Series : Product SpecificationsProtection And SafetyOvervoltage Shutdown Programmable for 15V to 255V peak, 156V range; 30V to 510V peak, 312V range Programmable Current Limit Shutdown Settable to 0.01 ARMS ResolutionSettable to 1% of range: the timeout is settable from 100 ms to 10s.Programmable Current Limitwith Timed ShutdownOver temperature Shutdown Automatic, not programmableRegulatory Compliance• EN 61010• EN 55011• UL 3111• EN 50082-2• EN 61000-4-3, EN 61000-4-4• FCC Part 15, Class A• CE MarkDesigned to meet:• EN 61010• EN 55011• UL 3111• EN 50082-2• EN 61000-4-3, EN 61000-4-4• FCC Part 15, Class A208858.458.0223sales.ppd@CSW Series : Product Diagram8.620”Front View16.90”Rear View16.90”21.069”2.371”Top View 23.440”8-32UNC-2B A =ACCURIDE SLIDE MOUNTINGAAA4.10013.2504.8755.3301.8108.620Side View2.6801.065 DIA FOR INPUT WIRING .875 DIA FOR SENSE WIRING 1.063 DIA FOR OUTPUT WIRING6.32519” (483mm)8.71”(221 mm)5550–33300 VA210CSW Series© 2011 AMETEK Programmable Power All rights reserved. AMETEK Programmable Power is the trademark of AMETEK Inc., registered in the U.S. and other countries. Elgar, Sorensen, California Instruments, and Power Ten are trademarks of AMETEK Inc., registered in the U.S.Model Number DescriptionCSW5550208Power LevelInput PowerXXXOptionsXXX Input Options -400342-457 Volt Line to Line AC input.Output Options -LFLimits output frequency to 500 Hz.Cabinet Options -RMS Rackmount Slides. Recommended for rack mount applications.C prefixCabinet System. Installed and pre-wired in 19” cabinet.OptionsOptions Code Description-160RTCA/DO-160D, Change 2, EuroCAE-14D and Airbus test firmware.-704F Mil. Std. 704A-F tests -ABD Airbus Directive 0100.1.8 tests.-AMD Airbus AMD24 tests.-A350Airbus A350 tests.-B787Boeing 787B3-0147 tests.-AIRB Airbus ABD0100.1.8, AMD 24 and A350 combination test software suite -LAN LXI Ethernet LAN Interface (Rj45 Connector)-LKM Clock/Lock Master -LKS Clock/Lock Auxiliary-413IEC61000-4-13 Harmonics and Interharmonics test firmware and hardware.-411IEC61000-4-11 test firmware. See also EOS1/3.-WHM Watt-Hour Measurement option.-MB Multi-Box. Adds controller to auxiliary chassis of multi-chassis systems-SWSCPI Command Firmware (Simulates the Elgar SW Series) Not all commands are supported. Please contact factory for details.。
电镀标准对照

252
ESA-M21P2-A4-Black WSD-M21P13-A2 Black
GM6173 Black
PS5873 Black
Black.
Yes
NOTE: The following electroplate finishes are limited to only a few parts, such as Tubular Type clips and Tube Clamps. Please do not specify these
5% solution at 95 degrees Fahrenheit. End point (1/16" rust spots) after 400 hours. 5% solution at 95 degrees Fahrenheit. End point (1/16" rust spots) after 400 hours.
No
5% solution at 95 degrees Fahrenheit. End point (red rust) after 24 hours.
Zinc Electroplate PS4220 Code 15
Silver Color. Parts are zinc Slight electroplated from discoloration .00015" to .0002" thick and baked to reduce from baking may occur hydrogen embrittlement. 5% solution at 95 degrees Fahrenheit. End point (red rust) after 24 hours.
SwirlFlo
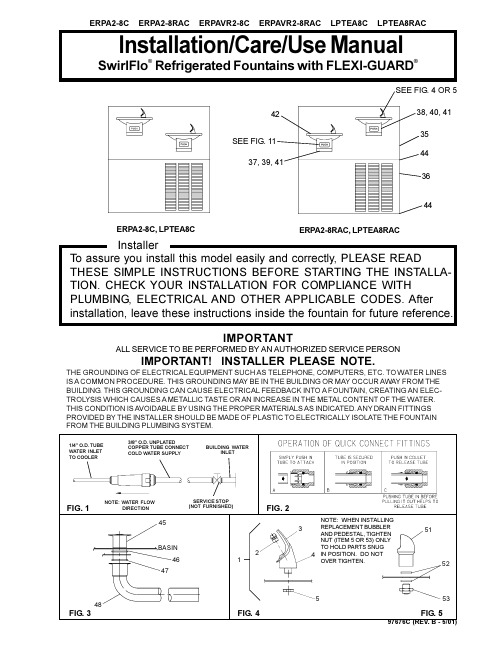
97676C (REV. B - 5/01)Installation/Care/Use ManualSwirlFlo ® Refrigerated Fountains with FLEXI-GUARD ®IMPORTANTALL SERVICE TO BE PERFORMED BY AN AUTHORIZED SERVICE PERSONFIG. 2FIG. 1THE GROUNDING OF ELECTRICAL EQUIPMENT SUCH AS TELEPHONE, COMPUTERS, ETC. TO WATER LINES IS A COMMON PROCEDURE. THIS GROUNDING MAY BE IN THE BUILDING OR MAY OCCUR AWAY FROM THE BUILDING. THIS GROUNDING CAN CAUSE ELECTRICAL FEEDBACK INTO A FOUNT AIN, CREATING AN ELEC-TROLYSIS WHICH CAUSES A MET ALLIC T ASTE OR AN INCREASE IN THE MET AL CONTENT OF THE WATER.THIS CONDITION IS AVOIDABLE BY USING THE PROPER MATERIALS AS INDICATED. ANY DRAIN FITTINGS PROVIDED BY THE INST ALLER SHOULD BE MADE OF PLASTIC TO ELECTRICALLY ISOLATE THE FOUNT AIN FROM THE BUILDING PLUMBING SYSTEM.IMPORTANT! INSTALLER PLEASE NOTE.NOTE: WATER FLOW DIRECTIONBUILDING WATER INLETSERVICE STOP (NOT FURNISHED)1/4" O.D. TUBE WATER INLET TO COOLER3/8" O.D. UNPLATEDCOPPER TUBE CONNECT COLD WATER SUPPLYNOTE: WHEN INSTALLING REPLACEMENT BUBBLER AND PEDESTAL, TIGHTEN NUT (ITEM 5OR 53) ONLY TO HOLD PARTS SNUG IN POSITION. DO NOT OVER TIGHTEN.FIG. 3234513635SEE FIG. 4 OR 537, 39, 4138, 40, 4142SEE FIG. 114444FIG. 44546BASIN4748ERPA2-8RAC, LPTEA8RACFIG. 5515253ERPA2-8C, LPTEA8C97676C (REV. B - 5/01)FIG. 6PAGE 2L E G E N D A = 3/8" O .D . T U B E C O N N E C T (C H I L L E R W A T E R O U T L E T )B = 3/8" O .D . T U B E C O N N E C T (C H I L L E R W A T E R I N L E T ) S H U T O F F V A L V E B Y O T H E R S C = 1-1/4" T R A P N O T F U R N I S H E D D = E L E C T R I C A L I N L E TL P T E A 8C L P T E A 8R A C97676C (REV. B - 5/01)PAGE 3FIG. 7ERPA2-8C /ERPA2-8RAC TUBE ROUTINGINST ALLATION INSTRUCTIONS1. Install remote chiller. Remove front panel of chiller. Remove and discard cardboard inner pack from between compressor and side panel. Slide chiller onto the shelf and position it to the left side of shelf. (See Figure 6)NOTE: Building construction must allow for adequate air flow on both sides, top, and back of chiller. See chiller instructions for additional instructions.2. Make water supply connections. Install a shut-off valve and union connection to building water supply (valve and union not provided). Turn on the water supply and flush the line thoroughly.3. ERPA MODELS: Make connection between remote chiller and building supply line. Inlet port is marked on the chiller (1/4" O.D. copper tube). Bend the copper tube (provided) at an appropriate length from chiller to opening in frame. Install a 1/4" x 3/8" union (provided) on the marked chiller inlet port. Connect building supply line to union. (See Figure 7)LPTEA MODEL: Mount filter head assembly to side of chiller (See Figure 9). Make connection between filter and building supply line (3/8" O.D. tube not provided). Inlet port is marked on the chiller (1/4" O.D. copper tube). Install a 1/4" x 1/4" union (provided). Bend the copper tube (provided) at an appropriate length from the filter and connect to the union on the chiller. (See Figure 8). 4. Hang the upper panel on the mounting frame hanger. Align holes in the panel with the holes in the mounting frame. Be sure that panel is engaged with hanger at top of frame before releasing it.5. Install the fountain. Remove access cover plate on underside of fountains and save the screws. Mount the fountain to theupper panel and the wall frame with (4) 5/16" x 1 3/4" (44mm) long bolts and nuts (provided). Install spacers on bottom two bolts. Tighten securely.6. Attach waste tube (1 1/4" OD) to 1 1/4" OD slip trap (provided by others).7. ERPA MODELS: Make connections between remote chiller outlet tube and fountain strainer. Outlet port is marked on the chiller (3/8" O.D. copper tube). Install a 3/8" x 3/8" union (provided) on the marked chiller outlet port. Insert the 3/8" unplated copper water line (provided) into the union and the inlet side of the strainer by pushing it in until it reachs a positive stop, approximately 3/4" (19mm). Connect 1/4" copper tubing coming from fountain to the strainer. Turn on water supply and check for leaks. DO NOT SOLDER TUBES INSERTED INTO THE STRAINER AS DAMAGE TO THE O-RINGS MAY RESULT . (See Figure 6).LPTEA MODEL: Make connections between remote chiller and fountain. Outlet port is marked on the chiller (3/8" O.D. copper tube). Install a 3/8" x 3/8" union (provided) on the marked chiller outlet port. Insert the 3/8" unplated copper water line (provided) into the union. Install a 1/4" x 3/8" union (provided) on the 3/8" copper tube and connect to the 1/4" copper tubing coming from the fountain. Turn on water supply and check for leaks. DO NOT SOLDER TUBES INSERTED INTO THE UNIONS AS DAMAGE TO THE O-RINGS MAY RESULT . (See Figure 8).8. These products are designed to operate on 20-105 PSIG supply line pressure. If inlet pressure is above 105 PSIG , a pressure regulator must be installed in the supply line. Any damage caused by reason of connecting these products to supply line pressures lower than 20 PSIG or higher than 105 PSIG is not covered by warranty. 9. Make electrical connections to the chiller. See chiller instructions.10. Check stream height from bubbler. Stream height is factory set at 35 PSI. If supply pressure varies greatly from this, turn adjustment screw on regulator (Item 12). Clockwise adjustment will raise stream height and counter-clockwise will lower stream height. For best adjustment stream should hit basin approximately 6 1/2" from the bubbler.11. Mount lower panel. Loosen the (2) #10-24 x 5/8" (16mm) screws at frame bottom lip. Slide upper tongue of lower panel under lower edge of already installed upper panel. Tighten previously loosened screws securely.12. Replace bottom access panel to fountain basin using screws provided. Tighten securely.TROUBLE SHOOTING AND MAINTENANCE1. Orifice Assy: Mineral deposits on orifice can cause water flow to spurt or not regulate. Mineral deposits may be removed from orifice with a small round file not over 1/8" diameter or a small diameter wire. CAUTION: Do not file or cut orifice materials.2. Stream Regulator: If orifice is free of material deposits, regulate flow according to instruction 10 stated above.3. Actuation of Quick Connect Water Fittings: Cooler is provided with lead-free connectors which utilize an o-ring water seal. T o remove tubing from the fitting, relieve water pressure, push in on the gray collar while pulling on the tubing (See Fig. 2) T o insert tubing, push tube straight into the fitting until it reaches a positive stop, approximately 3/4".4. Caution: Cleaning of Bronzetone Models requires special care. Outer surfaces must be cleaned with a mild detergent or mixture of vinegar and water only, rinsed and wiped dry. Abrasive and acidic cleaners may eventually damage the Bronzetone finish.CHILLER INLETCHILLER OUTLET324333TO BUBBLERTO BUBBLERW ATER INLETCHILLER OUTLET3234LPTEA8C /LPTEA8RAC TUBE ROUTINGFIG. 84343TO BUBBLER4397676C (REV. B - 5/01)PAGE 4P ART NO.ITEM NO.PARTS LISTBubbler AssyBubbler Assy (Bronzetone)Orifice AssyOrifice Assy (Bronzetone)Housing Assembly PedestalPedestal (Bronzetone)Bubbler LocknutPush Bar Mounting Bracket Push Bar AssyPush Bar Assy (Bronzetone)Regulator Activator Arm Screw - #8-32 X .25 THMS Holder-Regulator Hex Nut Regulator Retaining Nut ClipBushing - Nylon Rod - Pivot Rod - Pivot Rod - Push Clip - Push RodScrew - #10 X .50 HHSM Pivot Rod Bracket RetainerScrew - #10-24 X .37 PHTC Filter Mounting Bracket Filter Head Assy Filter AssyRegulator Mounting Bracket Screw - #8-18 x .75" PH Elbow - 3/8" (10mm)Fitting - Superseal 1/4" (6mm)Fitting - Superseal 3/8" (10mm)T ee - 3/8Union - 3/8 X 1/4Union - 1/4 X 1/4Back Panel RH ADABack Panel RH ADA (Bronzetone)Back Panel LH ADABack Panel LH ADA (Bronzetone)Lower PanelLower Panel (Bronzetone)Ftn Body & Shell-ShortFtn Body & Shell-Short (Bronzetone)Ftn Body & Shell-LongFtn Body & Shell-Long (Bronzetone)Cover Plate-ShortCover Plate-Short (Bronzetone)Cover Plate-LongCover Plate-Long (Bronzetone)Speed NutBasin-SwirlflowBasin-Swirlflow (Bronztone)StrainerScrew - #10-24 X .62 HHMS Strainer & Ferrule AssemblyStrainer & Ferrule Assy (Bronzetone)Gasket - T ailpipe Gasket - T ailpipe Waste Arm Tube - Water InPoly Tubing 48" (Cut T o Length)Bubbler-(VR Model Only)Gasket-(VR Model Only)Bubbler-Nipple-(VR Model Only)Bolt - 5/16-18 x 1.75 Lg.Nut - Hex 5/16-18Spacer51349C 56044C 40322C 45383C 50934C 50168C 56042C 75580C 21804C 21810C 21833C 21806C 70426C 50986C 40045C 61313C 15005C 75555C 50198C 70410C 70425C 70378C 21705C 70002C 21844C 4020600011262754389022490C 51294C 51299C 21803C 70792C 70818C 70822C 70823C 70852C 70745C 70683C 28185C 28186C 28187C 28188C 27026C 28264C 21822C 21831C 21823C 21832C 21845C 21835C 21846C 21836C 70055C 5500102621827C 55996C 11100834389045336C 45337C 50074C 50377C 45330C 62086C 56092C 45392C 10032274056015009C 70199C 70020C 740800531234567891011121314151617181920212223242526272829303132333435363738394041424344454647484950515253NS NS NSDESCRIPTIONFIG. 925242829312630FIG. 10141561697151918222010212017152315271511121315822FIG. 114950RH ADALH ADA 800-518-5388。
Sputter IAT_FAT Check list

檢查項目 Items 檢驗內容 Inspection content 判 定 基準 Acceptance Criterial 各裝置、外形尺寸(根據圖面 外形尺寸 ± 10mm以內) All Equipment's Dimensions are According to the Latest Drawing, the Max incorrect that we can allow is ± 10mm. 裝置長度的誤差為± 10mm內 The Max incorrect of Equipment`s Length is ± 10mm 干涉區域確認・・・搬入口/受渡部 (± 10mm) To confirm whether the open area is interfered with upstream/downstream. Pass line高度: 1,300± 10mm Pass Line height: 1,300± 10mm Hook up 位置是否與仕樣相符 To confirm whether the hook up position is the same as lay out. 是否接近樣本的顏色(Ivory or 3.5Y-8.5/0.5) To confirm whether the machine's color is close to our spec 机台之涂装是否有脱落 Does the painting of machine has any peeled off? 確認操作側位置触控面板是否正確 To confirm the Operation Site Position 触控面板位置及按键大小是否适当 Is the position and size of button of touch panel suitable? 机台外观是否有损伤或变形 Does machine has any damaged and deformed? 無毛邊生鏽 No any Burr and rust 腳座數量是否與仕樣相符 Is the total amount of footing the same as Spec ? 腳座安裝位置是否與圖面相符 Is the position of footing the same as Lay-out? 机台是否有加装防震脚座 Does machine intall anti-vibration support foot? 危險部是否裝有Cover(驅動部、回轉部) Dangerous Device need to be added Cover, just like driving device or rotation device 發塵部和grease、oil部分的Cover是否為透明PVC Cover,必 要時進行強制排氣 The particle causing area, grease and oil area need to be covered by transparent PVC cover,if it is need. 測試方法 Method 尺量測 (By tape-measure) 尺量測 (By tape-measure) 尺量測 (By tape-measure) 尺量測 (By tape-measure) 尺量測 (By tape-measure) 目視 (Visual Inspection) 目視 (Visual Inspection) 目視 (Visual Inspection) 功能測試 (Function test) 目視 (Visual Inspection) 目視 (Visual Inspection) 目視 (Visual Inspection) 目視 (Visual Inspection) 目視 (Visual Inspection) 目視 (Visual Inspection) 目視 (Visual Inspection) Priority A/B/C A A A A A A A A A A A A A A A 確認時機 A/B A/B A/B A/B A/B A/B A/B A/B A/B A/B A/B A/B A/B A/B A/B A/B add fig IAT 結果 Result 判定 Judge FAT 結果 Result 判定 Judge
ST原厂内部指令资料

DIAGNOSTIC COMMANDS Compatible with Drives with >64k CylindersJanuary 13, 2003SERIAL PORT INPUT PARAMETER REPRESENTATIONCommand parameters in this document are represented with single letters, separated by commas.e.g. Sx,y,z - This signifies a serial port command, “S”, that takes in three parameters. Exception: When one parameter is used to input two different values to the command, field width of each parameter will be shown.e.g. Dxxyy – This signifies a serial port command, “D”, that takes in one parameter. Thehigh byte of this parameter (xx) is used to pass one value to the command and the lowbyte (yy) is used to pass a second value to the command.The serial port will accept a max of up to one word (ffffh) for each parameter. For drives with greater than 64k cylinders, the serial port will accept up to a double word (ffff ffffh) for each parameter. S ee the appropriate command description to determine the valid size of a particular parameter.Unless otherwise noted, leading zeros are NOT required.SERIAL PORT OUTPUT DISPLAY REPRESENTATIONOutput display values in this document are represented with either letters or numbers and will show exact field width to aid in the creation and maintenance of serial port parsing software.e.g.When the log is displayed the output to the screen is formatted as shown below.(Log Type 2) (Log Type 4)___x_______Head___x_______Headvv wwww.xxx yyy zz vv wwww.xxx yyy zzwhere wwww is physical cylinder where wwww is physical cylinderLog format for drives with >64k cylinders:(Log Type 2) (Log Type 4)___Head___x_________x_________Headvv wwwww.xxx yyy zz vv wwwww.xxx yyy zzwhere wwwww is physical cylinder where wwwww is physical cylinderor output formatted as follows:Zone0:0006-0B4F800389.020Output format for drives with >64k cylinders:Zone00:0CC84-0DE36884414.1017TABLE OF CONTENTSON-LINE COMMANDS (10)I NTERFACE-S PECIFIC C OMMANDS (10)^E Interface State: Error codes, Max C.H.S, Current transfer mode settings (10)^F Read Segment Record(s) (10)^G Write Queue (10)^I Controller Register Dump (10)^K Niwot RdWr State (10)^Q Resume after ^S (age 50 only) (10)^S Pause intf task and swap to diag monitor (10)^U Currently unused (10)^V Interface Command Echo and Activity Trace Toggle (10)^X Interface and Niwot Command History (10)^Y Display Raw SMART DST Values (for Serial Port running of DST) (10)‘~’Interface Command State (10)G ENERAL C OMMANDS (10)^A Send Certification Code Rev (10)^B(Reserved for Servo Use) (10)^C Firmware Reset (10)^D, ^N Retry Activity Display Toggle. (See Appendix B. for Retry Display Characters.) (10)^L Display Sign-on Message, including firmware version. ** (10)^O, ^]Advance Servo Tracing (10)^P Power Chop enable/disable toggle (11)^Q Cert Display Debug enable/disable toggle ( not age 50 ) (11)^R Restart the Diagnostic Monitor, load overlay from disc (11)^T Restart testing at the current age (11)^W Read/Write statistics gathering enable/disable toggle (11)^Z Restart the Diagnostic Monitor, do not load overlay from disc (11)!Display Current R/W Channel Settings (11)%Show Mux Status. ** (See Appendix B for Description) (11)‘Display Transfer Status (See Appendix B Description) (11).Display Active Status. ** (See Appendix B for Description) (11);Display Machine Status. ** (See Appendix B for Description) (11)<Decrement read/write scope synchronization pulse position (11)>Increment read/write scope synchronization pulse position (11)?Show Buffer Allocation. ** (See Appendix B for Description) (11)^Show Elapsed Time since start of cert test or last ^Z (11)`Show Read/Write Statistics. (See Appendix B for Description) (11){(Reserved for Servo Diagnostic Use) (11)}(Reserved for Servo Diagnostic Use) (11)ESC Interrupt Loop, Batch file or SeaDex script execution (11)COMMON COMMANDS: (AVAILABLE FROM ALL LEVELS EXCEPT LEVEL 8).12 /x Change Level to Diagnostic Monitor Level x (12)CR Loop Break (12)*Special Function for batch file: (12)@x Batch File Label (12)|Batch file terminator (12)+x,y Peek Byte. Display the byte data content of the specified memory address: (12)=x,y,z Poke Byte. Replace the contents of the specified address with the specified data (12)-x,y Peek Word. Display the word contents of the specified address (12)A x,y,z Set Test Space (13)L x,y Loop. Causes the next command to repeat execution, subject to controls specified by x: (13)LEVEL T COMMANDS: CERT PROCESS / TEST (14)A Enable/Disable throttling of drive messaging (14)B x,y Set Baud Rate (14)*** C,,z Reset Certification Test. (available only when overlay is valid) (14)*** D x,y,z Display Cert Logs sequentially from Log x. (available only when overlay is valid) (14)E x,y,z Display/Edit Cert Log(s) (14)F Set Stuff 14*** H x,y,z Display/Reset Health Status Bits. (available only when overlay is valid) (15)*** I,y,z Initialize System Region. (available only when overlay and cert table are valid) (15)J x,y Set Scope Sync from Cert Log entries: (15)K Download Congen file (15)N x,y,z Set Drive Age to x (15)R Read System Sector into System RAM (15)S Check User Slip List for empty or unordered slip list (15)T x Run Factory Test x (15)*** V x,y Display Defect List(s) to screen and add to active log (15)W x,y,z Save System RAM into System Sector (15)Y x,y Set Drive Type (16)a Drive messaging pause toggle switch (16)b,,z Initialize the overlay area of the disc (16)c Write overlays to the disc (16)d x,y,z Download Cert Code (for automated use only) (16)e x,y Download overlay (for automated use only) (16)f Burn new serial flash code that is already downloaded to the buffer and transition to it (16)g x,y,z Call overlay function (16)h Download cert table (for automated use only) (17)*** i x,y,z Initialize/Reset Defect List(s) (available only when overlay is valid) (17)*** j Download SeaDex script (for automated use only) (available only when overlay is valid) (17)k x,y,z Initialize what head to depop (17)*** l x Initialize and write zone buffers in the overlay to RAM (17)*** m,,z Defect Map System Area (available only when overlay is valid) (17)r Reload Cert from Disc and report version number (17)*** s x,y,z Save Defect List(s) (available only when overlay is valid) (17)w x,y Write (Save) Overlay code to Disc (for automated use only) (18)*** x ll,ss,nn Page Log To Host (available only when overlay is valid) (18)#,,z Enter HDA Serial Number (18)$Enter PCBA Serial Number (18)[x,y ASCII Log Control: (18)LEVEL ONE COMMANDS: MEMORY MANIPULATION COMMANDS (19)B x,y Buffer Display (19)D x,y,z Display Memory (19)F Enable Forced Write Bit (19)M Show Flash ROM Information (19)N x,y,z SMART Serial Port Control (19)P Display PCBA Information (19)S x,y,z Edit Memory Byte (20)U x,y,z Edit Buffer Byte (20)*** Y x Converts desired cylinder number to gray code and display the result (20)*** c x,y,z Compare Buffers (available only when overlay is valid) (20)d x Clear overlay code from disc (for automated use only) (20)m x,y,z Edit memory word. Operates same as level 1 ‘S’ command, except operates on words (20)r Read cert code from disc (20)s Send Drive Information (20)t Read cert table from disc (20)u Read SeaDex script from disc (20)*** y x Converts desired gray code to a cylinder number and displays the result (20)LEVEL TWO COMMANDS: NIWOT READ/WRITE COMMANDS (21)B x,y Display Buffer (21)C x,y,z Copy Buffers (21)E x,y,z Display/Edit Cert Log(s) (21)F x,y,z,a Modify Track Defect List (21)G x,y,z,a,b,c MRT Test (available only when overlay is valid) (22)H x Select Head (23)I x,y,z Display/Modify Adaptive Settings (23)J x,y Scope Sync from Log (23)K x,y Set Tracking Offset (23)M x,y,z,w Quick Margin Test (23)N x Adaptive Test for all Heads in Specified Zone (23)O x,y,z Seek-Seek on current head: (23)P x,y,zzww Set Buffer Pattern: (23)Q x,y,,a Write/Read/Read Data (23)R x,y,z,a Read Data (24)S x,y,z Seek Cyl/Head (24)*** T x,y,z Measure Throughput. (available only when overlay is valid) (24)U x,y Spin-Up (25)*** V x,y,z Read/Compare against corresponding write buffer (25)W x,y,z,a Write Data (25)*** X x,y,z Display Data IDs on current track. (available only when overlay is valid) (25)Y x,y,zzaa,b Show/Set Retry Controls (26)Z Spin-Down (26)*** c x,y,z Compare Buffers (available only when overlay is valid) (26)*** d x,y,z,a R e-assign Errors from Log. (available only when overlay is valid) (26)*** e x,y Save Log to Cert Log y. (available only when overlay is valid) (26)*** f x,y,z Wedge Defect Map Current Track(available only when overlay is valid) (26)*** g x,y Slip Servo Wedge (available only when overlay is valid) (27)*** h x Translate Physical sector to Logical sector (27)*** i x,y Show Track Defect List in Active Log (27)*** j,y Read Wedge (27)*** l x Translate Logical sector to Physical sector (27)p x Full Pack Read Or Write (available only when overlay is valid) (28)r x,y,z,a Read Long from current track (28)s x,y,z Seek to Physical Cyl/Head (29)*** t c,hhss,o Translate Physical Cylinder, Servo Sector, Byte offset to LPL (29)u x,y,z Enable display of channel and preamp registers during retry (29)w x Write Long to current track (29)x Show Zone Boundaries and system cylinders as well as the last LBA of the drive (31)y x,z Set Direct Write Mode (31)*** z,y Write Wedge (31)LEVEL THREE COMMANDS: SERVO SEEKING COMMANDS (33)C x,y Acceleration Constant Measurement Test (33)D x,y,z,a,b,c Seek Access Times (33)E x,y,z Display/Edit Certification Test Log(s) (33)*** G x Translate Hex Cylinder to Gray Code (available only when overlay is valid) (33)H x Head Select (33)*** J x Head Switch Offsets (available only when overlay is valid) (33)*** M x,y Actuator Open-loop Move (available only when overlay is valid) (33)O x,y,z Seek-Seek on current head: (33)P x,y,z Position Error Display (33)Q xx,yy Certification Write/Read (34)*** R x,y,z Read Grey Code (available only when overlay is valid) (34)S x,y,z Seek Cyl/Head (34)T Servo Transducer Calibrations (34)U x Spin-Up 34V x,y,z Read GC123 registers (available only when overlay is valid) (34)*** W Read physical Grey Code (available only when overlay is valid) (34)*** Y Hysteresis (available only when overlay is valid) (34)Z Spin-Down (34)*** c Test Air Latch Closed (available only when overlay is valid) (34)*** g x Translate Gray to Hex (available only when overlay is valid) (34)j x,y,z Ramp Test. (Ramp Load drives only – currently Saturn) (35)k Measure Head Position (35)*** m Servo Actuator Geometry Test for MDW (available only when overlay is valid) (35)*** o Test Air Latch Open (available only when overlay is valid) (35)*** p x,y Translate Physical sector to Logical sector. (available only when overlay is valid) (35)*** q x,y Translate Logical sector to Physical sector. (available only when overlay is valid) (35)s x,y,z Seek to Physical Cyl/Head (35)LEVEL FOUR COMMANDS: SERVO TRACKING COMMANDS (36)C xxyy,z,a,b Tracking Test. (available only when overlay is valid) (36)D x,y,z,a,b,c Seek Access Times (36)E x,y,z Display Active Log (36)*** G x Set Tracking/Seek Gain (available only when overlay is valid) (36)H x Select Head x (36)*** I x,y,z Head Stability Test for Heads (default is All Heads) (available only when overlay is valid) (36)K x Servo Offset (37)*** M x,y Actuator Open-loop Move (available only when overlay is valid) (37)N x Napa Servo Adaptive Test for all Heads in Specified Zone (37)O Show MR Head Offset (for current head) (37)P x,y,z Position Error Display for current track (37)S x,y,z Seek Cyl/Head (37)T x,y,z Napa Servo Adaptive Test at the Specified Track (37)*** W Read physical Grey Code (available only when overlay is valid) (37)X x Display 1 rev of servo burst information for current track (37)*** Z x Zap Servo Burst x of the current track. (available only when overlay is valid) (37)*** a Slip error code 90's from the log (available only when overlay is valid) (37)*** c x Track 0 Cal for MDW (available only when overlay is valid) (38)d x Disable/Enable servo from using the ZAP coefficients in the ZAP table (38)*** f Fill Skipped Cylinders (NOT IMPLEMENTED) (available only when overlay is valid) (38)i x Enable/disable ZAP reads (available only when overlay is valid) (38)j,x Adaptive Coherent Feedforward Compensator (ACFC) calibration (MDW only) (38)k Skip MDW serial number cylinders (available only when overlay is valid) (MDW only) (38)l xx Will scan the current position for servo defects and zap the track (38)*** m RRO ZAP System cylinders (available only when overlay is valid) (38)n y,,x Calculate the zap coefficients at the current position (38)p x,y,z Display Spin Error (39)*** q x Change Spin Speed (available only when overlay is valid) (39)r x Reads and displays the specific Track ID contents (39)***s x,y,z Show error count for given log (available only when overlay is valid) (39)t x,y Modifies and views the ZAP RAM table (39)v x,y,z,a ButterFlySeekTest (39)w x Writes the ZAP values in the ZAP RAM table to the Track Ids of the current track (39)x c,,z Skip Cylinder (40)y Show Skipped Cylinders (40)z c,,z Unskip Skipped Cylinder(s) (40)LEVEL SIX COMMANDS: BATCH FILE COMMANDS (41)B x Run Batch File (41)D x List Batch File (41)E x Enter Batch File (41)*Special Function for batch file: (41)@x Batch File Label (41)|Batch file terminator (41)LEVEL SEVEN COMMANDS: READ CHANNEL ADAPTIVE COMMANDS (42)B x,y Display Buffer (42)C x,y,z Copy Buffers (42)D x Display Temperature Diode Values (42)E x,y Display Log(s) (42)F x,y Format Sector/Track (42)G x,y,z Toggle ECC Seed Finder tool (42)H x Select Head x (42)I x,y,z,a Display/Modify Adaptive Settings for the Current Head (42)M x,y,z Napa Single Adaptive Parameter Test (42)N x Napa Data Adaptive Test for all Heads in Specified Zone (43)O h,z, s Read/Write Coarse Offset Calibration (43)P x,y,zzww Set Buffer Pattern: (44)Q x,y Write/Read/Read Data (44)R x,y Read Data (44)S x,y,z Seek Cyl/Head (44)T x,y,z Napa Data Adaptive Test at the Specified Track (44)U x,y Spin-Up (44)V f Set MR Head Read Bias Current for all Heads (44)W x,y Write Data (44)Y x,y,zzaa,b Show/Set Retry Controls (44)Z Spin Down Command (45)a x,y,z MR Bias Backoff (45)b x,y PE and OTC measurements (45)c x,y,z Generate OTC bath tubs by sector (47)d x,y,f Reset Adaptives to the Default Settings (47)e Show diagnostic error counter in the Valiant (DIAGERRCNT) (47)f f Shows the number of TAs/ data retries done (47)g xxxx,yyyy,zz Does Error Rate by sector command (47)i x Issue read / write command (use after p) (47)j Ramp unload without spin-down (Ramp drives only – currently Saturn) (47)n Run the read channel noise calibration at the current track (47)o x,y,z OTC command (48)p Set parameters for Read / Write operation (precedes i command) (48)r Read Adaptives from the System Sectors (48)s xy,z,a Send Byte to Read Channel or Preamp (48)t x,z Get Data from Read Channel or Preamp (48)u Write Unsafe Enable Toggle (48)v,f VCO calibration / display (48)w x,y,z Save System RAM into System Sector (48)x Show Zone Boundaries (49)y x,z Set Direct Write Mode (49)z Toggle Data Randomizer (49)7x,y,z Generate 747 curve (49)9x,y,z Adapt Write Delay (50)LEVEL EIGHT COMMANDS: SERVO TRACK WRITER COMMANDS (53)A Abort any pending servo diagnostic command (53)B Set the read head bias to the serial preamp (53)C x,y,z Execute the servo diagnostic sub commands (53)D Dump Drive Configuration (55)E Lock Spindle Motor (56)F Write Pack-writer Auto Stamp (56)G x Set Spin Gain (56)H x Select head directly (57)I x Push-Inward Actuator (57)J x Spin Speed Adjust (57)K x Added track offset in track follow state (57)Lx Load Head Mask (57)M Increment Head (current head + 1) (57)N Report Logical Spin State (57)O x Message Display (57)P x Push-Out Actuator (57)Q x Read channel (57)R x Read Gray Code (57)S x,y,z Seek Cyl/Head (58)U x Spin-Up Motor (58)Vx Spin-Up 58W x Set Write Current (58)Z Spin-Down (58)c Crash test the Actuator/Crashstops/HDA (58)fx,y Set bank write mode (58)g IMRON signal polarity (58)LEVEL A COMMANDS: NIWOT READ/WRITE LBA COMMANDS(FULLSLIP) (59)C x,y Convert LBA to LPL and display to screen (59)D x,y Convert LBA to PCHS and display to screen (59)E x,y Display Log(s) (59)M x,y Set GrandB Test ports (59)Q,x Write/Read/Read LBA (59)R,x Read LBA Command (59)S x,y,z Seek LBA Command (59)W,x Write LBA Command (59)Y x,y,za Show/Set Retry Controls (59)c x,y,z Convert LPL to LBA and display to screen (59)d x,y,z Convert PCHS to LBA and display to screen (59)l x,y,z Display # of unslipped sectors for LPL to screen (60)LEVEL C COMMANDS: CERT DIAGNOSTIC CTS COMMANDS (61)D Display the Cert Test sequence (61)F vvww,x,yyzz Run Cert CTS Test F with input parameters (61)***P Load Buffers 10-1A with NAPA specific 127 bit pattern, load buffers 1B-1F with 0’s (available only when overlay is valid) (61)***l xxxxx,yPerform Lazy Write / On-Track-Erasure Screen. (available only when overlay is valid) (61)*** p xx,yy Parse Cert Log for Errors by Head (available only when overlay is valid) (62)*** s x,y,z,a CTSSpinUpandDn (available only when overlay is valid) (63)LEVEL D COMMANDS: SEADEX COMMANDS (64)E x,y,z Display SeaDex Log, level-T E-command style (64)I x SeaDex Information tables (64)S x Single Step SeaDex script (64)T x,y,...SeaDex Test Step. (64)b x,y,z Script assembly Breakpoint (65)c x SeaDex Checkpoint (65)l x,y Display SeaDex Log (65)p x Display SeaDex Tune Parameter (65)s x,y Set or Display SeaDex System Variable (65)t x SeaDex Trace Levels (66)v Verify SeaDex Script (66)w x,y,z,a Set or Display SeaDex Word (67)LEVEL E COMMANDS:DRIVE ZONE AND FORMAT COMMANDS (68)a x,y Displays / modifies drive zone parameters. (available only when overlay is valid) (68)b x,y,z Displays / modifies frame format information. (available only when overlay is valid) (69)BOOT CODE DIAGNOSTIC COMMANDS (70)ONLINE COMMANDS, BOOT CODE (70)^D, ^N Retry Activity Display Toggle. ** (See Appendix B. for Retry Display Characters.) (70)^L Display Sign-on Message, including firmware version (70)^O, ^]Advance Servo Tracing (70)^Z Restart the Diagnostic Monitor, do not load overlay from disk (70)!Display Current R/W Channel Settings (70)%Show Mux Status. ** (See Appendix B for Description) (70)‘Display Transfer Status (See Appendix B Description) (70).Display Active Status. ** (See Appendix B for Description) (70);Display Machine Status. ** (See Appendix B for Description) (70)<Decrement read/write scope synchronization pulse position (70)>Increment read/write scope synchronization pulse position (70)LEVEL F COMMANDS:LIMITED BOOT CODE DEBUG SUPPORT (71)+x,y Peek Byte. Display the byte data content of the specified memory address: (71)=x,y,z,w Poke memory. Replace the contents of the specified address with the specified data (71)-x,y Peek Word. Display the word contents of the specified address (71)B x,y Display Buffer (71)C x,y,z Copy Buffers (71)D x,y,z Display Memory (71)P x,y,zzww Set Buffer Pattern: (71)R x Read system sectors information (72)U x Spin-Up 72Z Spin-Down (72)b x,y Set Baud Rate (72)d x,y Download code, used in conjunction with SDLD (72)e x,y,z,w Serial flash access routines (73)r,y,z Reserve tracks read (73)s x Seek to Physical Cyl (FULLSLIP) (73)t x,y,z Write to serial device (73)APPENDIX A: ERROR CODES (74)APPENDIX B: SPECIAL AND RETRY DISPLAY CHARACTERS (75)APPENDIX C: ONLINE COMMAND DISPLAY DESCRIPTIONS (76)S TATISTICS D ISPLAY D ESCRIPTION(`) (76)M UX S TATUS D ISPLAY D ESCRIPTION(%) (78)T RANSFER S TATUS D ISPLAY D ESCRIPTION(‘) (79)A CTIVE S TATUS D ISPLAY D ESCRIPTION(.) (81)M ACHINE S TATUS D ISPLAY D ESCRIPTION(;) (82)B UFFER A LLOCATION D ISPLAY D ESCRIPTION(?) (83)H EALTH B ITS D EFINITIONS: (84)E RROR L OG D ISPLAY (85)Header Format: (85)Defect List Format: (85)ON-LINE COMMANDSThe On-Line commands may be initiated at any time. For the Interface-specific commands, the Interface code must be present in the current memory map for successful execution; the General commands are always avail-able.Interface-Specific CommandsCommand Description(AT)^E Interface State: Error codes, Max C.H.S, Current transfer mode settings^F Read Segment Record(s)Queue^G Write^I Controller Register Dump^K Niwot RdWr State^Q Resume after ^S (age 50 only)^S Pause intf task and swap to diag monitorunused^U Currently^V Interface Command Echo and Activity Trace Toggle^X Interface and Niwot Command History^Y Display Raw SMART DST Values (for Serial Port running of DST)‘~’ Interface Command StateGeneral CommandsCommand Description^A Send Certification Code Rev^B(Reserved for Servo Use)Reset^C Firmware^D, ^N Retry Activity Display Toggle. (See Appendix B. for Retry Display Characters.)^L Display Sign-on Message, including firmware version. **^O, ^] Advance Servo TracingOnline General Commands (Continued)Command Description^P Power Chop enable/disable toggle.^Q Cert Display Debug enable/disable toggle ( not age 50 )^R Restart the Diagnostic Monitor, load overlay from disc.^T Restart testing at the current age.^W Read/Write statistics gathering enable/disable toggle.^Z Restart the Diagnostic Monitor, do not load overlay from disc!Display Current R/W Channel Settings% Show Mux Status. ** (See Appendix B for Description)‘ Display Transfer Status (See Appendix B Description). Display Active Status. ** (See Appendix B for Description); Display Machine Status. ** (See Appendix B for Description)< Decrement read/write scope synchronization pulse position.>Increment read/write scope synchronization pulse position.? Show Buffer Allocation. ** (See Appendix B for Description)^Show Elapsed Time since start of cert test or last ^Z.`Show Read/Write Statistics. (See Appendix B for Description){ (Reserved for Servo Diagnostic Use)} (Reserved for Servo Diagnostic Use)ESC Interrupt Loop, Batch file or SeaDex script execution.** - Standardized and documented in Test Engineering’s Internal Reference Manual, “Microcode Command Set”.COMMON COMMANDS: (Available from All Levels except Level 8) The Common Commands may be executed whenever the diagnostic monitor prompt is present and the monitor is waiting for a command request, except at level 8. The level 8 commands take precedence over the com-mon commands.Command Description/x Change Level to Diagnostic Monitor Level x.Break.CR Loop* Special Function for batch file:*1 Pause batch file execution until input*2,x Delay x milliseconds*3,x Branch to Label x*4,x Increment head and branch to Label x*5 Clear monitor screen*6 Stop on error*7,x Load batch loop counter with x.*8,x Decrement batch loop counter, Branch to Label x if 0.@x Batch File Label.During batch file entry, define this location as Label x.x - Single digit numeric label specification.|Batch file terminatorTerminates the entry of batch files.+x,y Peek Byte. Display the byte data content of the specified memory address:x - upper bits of a greater-than-16 bit addressy - lower 16 bits of a greater-than-16 bit address or the 16 bit address=x,y,z Poke Byte. Replace the contents of the specified address with the specified data.x - upper bits of a greater-than-16 bit addressy - lower 16 bits of a greater-than-16 bit address or the 16 bit addressz - byte data content to be written at the specified address.-x,y Peek Word. Display the word contents of the specified address.x - upper bits of >16 bit addressy - lower 16 bits of >16 bit address or the 16 bit addressCommon Commands (Continued)Command DescriptionA x,y,z Set Test Space x Bit Meanings:Bit # If x = 1 If x = 07 Random Data Existing Buffer Data6 Sequential Out Sequential In5 Odd Cylinders All Cylinders4 Even Cylinders All Cylinders3 (unspecified) (unspecified)2 Random Cylinder/Head Sequential Cylinder/Head1 All Cylinders Current Cylinder0 All Heads Current HeadSpecial ValuesA8,y Set Minimum Cylinder to y >64k cyl compatible* A9,y Set Maximum Cylinder to y >64k cyl compatible* AA,y Set Maximum Head to yAD Set Mins/Maxs to DefaultsA87 Sets random data, random cylinder, random head, all cyls & hds AC7 Randomly select 80% Sequential In, 20% Random addresses IF (Random_Start = TRUEA,,z Select Random start and lengthBit0 set = random start sectorBit1 set = random lengthBit0 set = Display aboveL x,y Loop. Causes the next command to repeat execution, subject to controls specified by x: x Bit Meanings:Bit # If = 1 If = 07 Looping active (internal use) Looping not active (internal use)6 Looping primed (internal use) Looping not primed (internal use)5 Stop on Error Code = y Do Loop Count (y<>0)4 Inhibit Error Message on error Display Error Message on error3 (unspecified) (unspecified)2 Spin Down on Error Remain spinning on error1 Stop on No Error0 Continue on error Stop on errory: Error Code to stop on (if Stop on Error Code is enabled.)Loop Count (default is forever.)* Will accept up to 8 digits for drives with >64k cylindersLEVEL T COMMANDS: Cert Process / TestCommand DescriptionA Enable/Disable throttling of drive messaging.Toggles the state of the drive messaging toggling. Power-up state is throttled - oncebuffer is full, drive messaging system will wait for characters to be transmittedbefore processing further output informationB x,y Set Baud Ratex = 0 Set baud rate to POR default, typically 9600x = 1 Display supported baud rates in the format: =xxxxx > 1 Set supported baud rateTypical baud rates (xxxx leading zeros may be omitted)ratex baud1228 1,228,000921,000921625 625,000460,000460230 230,000115,00011557,60057619,20019296 9,60048 4,80024 2,400y - if entered y contains the delay time in milliseconds. Default isdo not wait for host to return CR, just set new baud rate. If y is enteredthe code will check every millisecond up to y milliseconds for a carriagereturn to be sent back from the host at the new baud rate. If no CR is seen thedrive will default back to 9600 baud.*** C,,z Reset Certification Test. (available only when overlay is valid)Resets health bits and sets age to 1. Clears Scratch Fill Done flag.z - if z = 22h then reset certification test.- if z <> 22 then ignore this command.*** D x,y,z Display Cert Logs sequentially from Log x. (available only when overlay is valid)x - Log to start sequential display; if blank, display only logs of failed tests.y - Displays only log entries with this error codez - Special function:= 40 - Enable fast dump capability for data cataloger capture. Inhibits time delaybetween log dumps and enables fast, unformatted log dump.E x,y,z Display/Edit Cert Log(s)See /2 E for further detail.StuffF SetThe Set Stuff data may be up to 512 characters long. The Set Stuff data format is de-fined by the Seagate-Longmont ATA Vendor Specific Stuff document.。
Electro-Voice ZLX-15BT 15 2-way powered speaker B

▪High-quality Bluetooth® audio streaming for background music or musical accompaniment. Bluetooth® connectivity is available in select countries.▪Quick Smart DSP features best-in-class processing. Easy setup via four presets, sub/top system-match, two-band EQ, five user-programmable presets, visual monitoring of limiter status, input level control and meters, and master volume control to optimize gain structure, all via LCD.▪High-efficiency 1000 W Class-D power amplifier delivers us to 127 dB peak SPL utilizing transducers designed and engineered by EV.▪EV-patented Signal Synchronized Transducers (SST) waveguide design provides precise and consistent coverage, minimal distortion, and maximized acoustical loading.▪Three optimally located handles combined with a rugged composite structure provides the most portable professional sound speaker on the market.NOW STREAMING: Cut through the competition with Bluetooth® enhanced ZLX portableloudspeakersZLX portable loudspeakers offer the best performance and reliability in their class - with components and engineering that work together to make it quicker and easier than ever to take control of your sound, whatever the gig. Now with Bluetooth® enabled wireless audio streaming, legendary ZLX performance becomes even more convenient with the ability to connect to any mobile device for streaming your music library.Featuring custom drivers housed in an innovative cabinet design, the two new wireless, compact, and versatile ZLX models make EV's renowned sound quality and rugged reliability more accessible than ever before.Bluetooth® is available in select countries.Technical specificationspreset.2.Maximum SPL is measured at 1 m using broadband pink noise at maximum output.3.Current rating is specified at 1/8 full output power.Frequency response:Dimensions:System overviewFull-Range loudspeaker control and monitoring interface1253 4876Full-Range loudspeaker amplifier panel1.LCD - DSP control and monitoring interface.2.MASTER VOL - Adjusts the sound level.DSP - Scroll through the menu and select theavailable choices. Push the MASTER VOL knob toenter the DSP menu.3.INPUT LEVEL - Level control for adjusting theindividual inputs’ level. The 12 o’clock position isunity gain (no gain or attenuation), the range to theleft of zero is for adjusting line level sources, and the range to the right of zero (0) is for adjustingmicrophone levels. LINE and MIC input level control is available for both INPUT 1 and INPUT 2.4.POWER - AC switch or switching the power ON orOFF. The LCD screen lights up when the power isturned ON, after approximately 3 seconds.5.MAINS IN - AC connection is established via an IEC-connector.6.INPUT - Balanced input for the connection of signalsources like mixing consoles, instruments, ormicrophones. Connections can be established using¼ inch TRS or XLR connectors.7.OUTPUT - XLR output sends the mix of all inputsignals to another loudspeaker or subwoofer. INPUTLEVEL controls the signal level to OUTPUT. TheMASTER VOL or DSP control settings do not affectOUTPUT. This is also the output for the BT signalwhich is configurable via the MIX OUT setting.8.AUX IN - 3.5 mm audio jack input for connectingexternal audio media devices, such as MP3 players. For more information, see the ZLX Powered Loudspeaker Series Installation manual (F.01U.349.854).Ordering informationZLX-15BT-EU 15" 2-way powered speaker BT EUcord Powered 15-inch 2-way loudspeaker with Bluetooth®and EU cord, blackOrder number ZLX-15BT-EUZLX-15BT-US 15" 2-way powered speaker BT UScord Powered 15-inch 2-way loudspeaker with Bluetooth®and US cord, blackOrder number ZLX-15BT-USAccessoriesZLX-BRKT ZLX Wall Mount BracketWall mount bracket for ZLX-12/12P/12BT andZLX-15/15P/15BT, blackOrder number ZLX-BRKTZLX-15-CVR ZLX Padded Cover for ZLX-15/P - EV Logo Padded cover for ZLX-15/15P/15BT, EV logo, black Order number ZLX-15-CVRRepresented by: Germany:Bosch Sicherheitssysteme GmbH Robert-Bosch-Ring 585630 GrasbrunnGermany Bosch Security Systems, Inc. 12000 Portland Avenue South Burnsville MN 55337USA© Bosch Security Systems 2018 | Data subject to change without notice Document Number | Vs1 | 11. Apr 2018。
Eaton Aerospace产品说明书

Manual (ATA Number)CurrentRevisionRevisionDateEaton PartNumberDescription OEM Application63-41-10Rev 1Mar 31/981H118-45QDM Signal Conditioner Agusta Westland EH10163-41-20Initial Feb 15/02S247-4Sight Gauge Agusta AB13979-22-06Rev 2Jul 30/991A475Chip Collector GE CF679-24-01Reissue Apr 15/94A693Full Flow Debris Monitor Textron Lycoming ALF502/ LF507 79-22-06Rev 2Jul 30/991A1869Chip Collector GE CF679-24-01Reissue Apr 15/941D1934Full Flow Debris Monitor Textron Lycoming ALF502/ LF507 79-24-01Reissue Apr 15/941D2316Full Flow Debris Monitor Textron Lycoming ALF502/ LF507 79-22-11Initial Feb 1/941J2496Power Module Israel Cobra79-23-00Initial Feb 28/941F2870-3Lubriclone Allison AE210079-21-39Rev 2Sep 30/991F2976SeriesDMS Separator Hispano-Suiza GE9079-21-38Rev 1Aug 31/991G2977SeriesDMS Sensor Hispano-Suiza GE9079-21-41Rev 1Apr 30/991H2983-3DMS Conditioner Hispano-Suiza GE9049-90-30Initial Jan 18/082E3249Level Sensor Honeywell36-150 APU79-21-03Rev 1May 24/96VB3447Chip Detector Rolls-Royce RB21179-21-04Rev 1May 10/96VA3503Chip Detector Rolls-Royce RB21179-21-05Rev 2Feb 15/01VA3508Chip Detector Rolls-Royce BR710, TRENT700/80079-22-45Rev 3Nov 1/99VB3521-2Chip Detector Rolls-Royce V250079-22-06Rev 2Jul 30/99B4354-1Chip Detector GE CF679-22-08Rev 1Mar 31/99B4901Chip Detector w/Self-ClosingValve Pratt & Whitney PW2000F117PW-10079-22-14Rev 1May 9/08B4902Chip Detector w/Self-ClosingValvePratt & Whitney PW400079-22-14Rev 1May 9/08B4903Chip Detector w/Self-ClosingValvePratt & Whitney PW400079-23-00Initial Feb 28/942Z6468Self-Closing Valve Allison AE2100 79-22-02Rev 2Nov 19/991A6473Chip Detector w/Self-ClosingValvePratt & Whitney PW4000 79-22-03Initial Jul 15/931B6488Chip Detector w/ Self-ClosingValvePratt & Whitney PW400079-22-02Rev 2Nov 19/991A6505Chip Detector w/Self-ClosingValvePratt & Whitney PW4000 79-21-51Rev 2Nov 17/061D6549Debris Monitor Hispano-Suiza CFM56 79-21-52Rev 1Oct 20/001B6550Chip Detector Hispano-Suiza CFM56 79-31-10Rev 2May 9/944J6588Electric Chip Detector GE LM6000 79-22-04Initial Oct 15/921A6618Chip Collector w/Self-ClosingValveGarrett APU79-22-10Initial Dec 15/971A6794Chip Collector w/Self-ClosingValveIAE V250079-23-00Initial Feb 28/941B6820Chip Detector Allison AE2100 79-23-05Initial Jun 1/981F6875Lubriclone Rolls-Royce AE1107C 79-22-07Initial Mar 15/951A6902Chip Collector w/Self-ClosingValvePratt & Whitney JT9D79-22-07Initial Mar 15/951A6925Chip Collector w/Self-ClosingValvePratt & Whitney JT9D79-22-09Rev 2Jan 3/001A6945Chip Collector w/Self-ClosingValvePratt & Whitney JT8D79-22-09Rev 2Jan 3/001A6947Chip Collector w/Self-ClosingValvePratt & Whitney JT8D79-22-09Rev 2Jan 3/001A6948Chip Collector w/Self-ClosingValvePratt & Whitney JT8D79-22-12Initial Sep 15/961A7091Chip Collector w/Self-ClosingValvePratt & Whitney JT9D79-22-16Initial Dec 15/971A7476Chip Collector w/Self-ClosingValveRolls-Royce BR715Manual (ATA Number)CurrentRevisionRevisionDateEaton PartNumberDescription OEM Application77-42-03Initial Jan 03/001J7589Smart Zapper Power Module Westland Seaking77-42-04Initial Jan 03/001Z7628Smart Zapper Maint. Panel Westland Seaking79-22-16Initial Dec 15/971A7802Chip Collector w/Self-ClosingValveRolls-Royce BR71579-22-46Rev 1Jan 29/041B7802Chip Detector Rolls-Royce TRENT 500/900 79-22-47Initial Dec 29/062Z7802DMS Inhibitor Rolls-Royce TRENT 500/900 63-41-20Initial Feb 15/021D7829Debris Monitor Agusta AB13963-41-20Initial Feb 15/021B7830Chip Detector w/Adapter Agusta AB13963-41-20Initial Feb 15/022A7831Oil Filler Agusta AB13963-41-20Initial Feb 15/021B7839Chip Detector w/SCV Agusta AB13963-41-20Initial Feb 15/022A7840-1Oil Filler Agusta AB13963-41-20Initial Feb 15/022B7841Vented Breather Agusta AB13963-41-21Initial Feb 15/021J7895Power Module Agusta AB13979-11-24Initial Apr 14/041F8550DMS Separator Hispano-Suiza GE90-115B63-41-20Initial Feb 15/022F8566E/O Sensor Agusta AB13979-36-13Initial Jun 30/061F8664-4ODM Separator GE GP7200。
WARN 1700 Utility Winch 产品说明书

WARNING signals a hazard that CAUTION signals a hazard thatMOVING PARTS ENTANGLEMENT HAZARDFailure to observe these instructions could lead to severe injury or death.keep hands clear of wire rope, hook loop, hook and fairlead opening during installation, operation and whenFALLING OR CRUSHING HAZARDFailure to observe these instructions could lead to severe injury or death.Safety Precautions - continuedCAUTIONMOVING PARTS ENTANGLEMENT HAZARDFailure to observe these instructions could lead to minor to moderate injury.General Safety:• Always Know Your Winch: Take time to fully read and understand the included Installation and Operations guide, and Basic Guide to Winching Techniques, in order to understand your winch and the winching operation.• Never operate this winch if you are under 16 years of age.• Never operate this winch when under the influence of drugs, alcohol or medication.• Never exceed winch or wire rope rated capacity. Double line using a snatch block to reduce winch load.Installation Safety:• Always choose a mounting location that is sufficiently strong to withstand the maximum pulling capacity of your winch.• Always use factory approved switches, remote controls, accessories and installation components.• Always use grade 5 or better hardware, never weld bolts and never use longer bolts than those supplied from factory.• Always complete winch mounting and attachment of hook to hook loop before wiring winch during installation. • Always position fairlead with WARNING label on top.• Always spool the wire rope onto the drum as indicated by the drum rotation label on the winch.Required for automatic brake to work (if winch is so equipped) and for correct installation orientation.• Always prestretch wire rope and respool under load before use. Tightly wound wire rope reduces chances of "binding", which is wire rope working it's way down into a loosely wound wire rope layer, and catching or damaging itself.Winching Safety:• Always inspect winch installation and wire rope and hook condition before operating winch. Frayed, kinked or damaged wire rope must be replaced immediately. Loose or damaged winch installation must be corrected immediately.• Never hook wire rope back onto itself. This damages the wire rope. Always use a choker chain, wire choker rope or tree trunk protector on the anchor.• Always prior to winching, remove any element that may interfere with safe winch operation.• Always take your time when rigging for a winch pull.• Always be certain the anchor you select will withstand the load, and the strap or chain will not slip.• Never engage or disengage clutch if winch is under load, wire rope is in tension or wire rope drum is moving• Always unspool as much wire rope as possible when rigging. Double line or pick distant anchor point.• Never winch with less than 5 wraps of wire rope around the drum, the wire rope could come loose from the drum. • Always stand clear of wire rope and load during operation.• Never touch wire rope or hook while in tension or under load.• Never touch wire rope or hook while someone else is at the control switch or during winching operation.• Never touch wire rope or hook while remote control is plugged into winch.• Always stand clear of wire rope and load and keep others away while winching.• Always require operator and bystanders to be aware of stability during winching of vehicle and/or load.• Always keep remote control lead clear of the drum, wire rope and rigging. Inspect for cracks, pinches, frayed wires or loose connections. Replace if damaged.Failure to observe these instructions could lead to minor to moderate injury. To avoid injury to hands and fingers:wear heavy leather gloves when handling a wire rope.let wire rope slip through your hands.be aware of possible hot surface at winch motor, drum or wire rope during or after winch use.CAUTIONNeverNeverWinch Failure HazardShock & Fire HazardMoving Parts Entanglement HazardOperating Instructions - continuedSPOOLING IN UNDER LOAD❑The wire rope must always spool onto the bottom of the drum as indicated by decal on the winch.❑Power in the wire rope evenly and tightly on the drum. This prevents the outer wire wraps from drawing into the inner wraps, binding and damaging the wire rope.❑Avoid shock loads when spooling, by using the control switch intermittently to take up wire rope slack. Shock loads can momentarily far exceed the winch and wire rope ratings.❑To prolong the life of the winch, use a snatch block and a double-line rigging technique. This is especially important when pulling heavy loads.SPOOLING IN UNDER NO LOAD❑Assisted: Have your assistant hold the hook with the hook strap putting as much constant tension on the wire rope as possible. While keeping tension, the assistant should walk toward the winchwhile you operate the control switch spooling in the wire rope. Release the switch when the hook isa minimum of 4 ft (1.2m) from the fairlead opening. Spool in the remainder for storage.❑Unassisted: Arrange the wire rope to be spooled so it will not kink or tangle when spooled. Be sure any wire rope on the drum is tightly and evenly layered. Spool enough wire rope to complete thenext full layer on the drum. Tighten and straighten the layer. Repeat process until the hook is aminimum of 4ft (1.2m) from the fairlead. Spool in the remainder for storage.SPOOLING REMAINDER FOR STORAGEKeep hands clear of the wire rope, hook and fairlead opening. Always use the hook strap to hold hook when spooling under no load. Carefully power in the remaining wire rope, jogging the control switch to take up the last of the slack. Secure the hook to a suitable anchor point near the winch. Be careful not to over tighten or damage may occur to the wire rope or anchor point.RIGGING❑Always spool out as much wire rope as possible when preparing rigging. Pick an anchor as far away as is practical; this provides the winch with its greatest pulling power.❑Rigging a double line with a snatch block will reduce the load on the winch to half without significant loss of spooling speed.❑Natural anchors such as trees, stumps and rocks are the handiest when available. Attach the choker chain, wire choker rope or tree trunk protector on the anchor as low as possible to avoid pulling the anchor down. If several possible anchors are available but they are not strong enough individually, it may be practical to attach a wire or chain choker around several anchors to form a strong collective anchor point.。
windows craft 编译代码
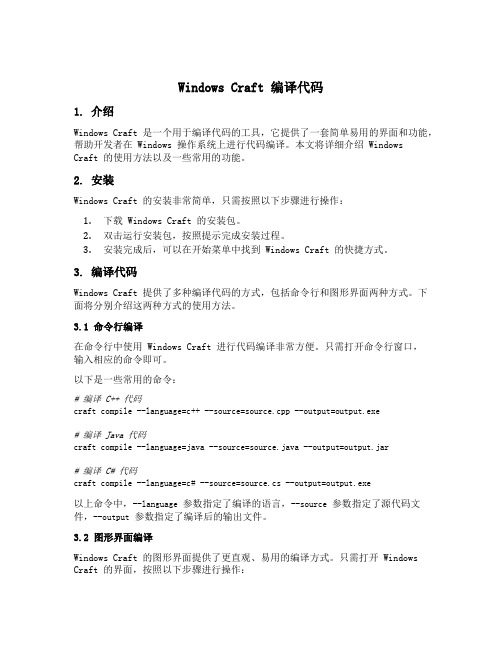
Windows Craft 编译代码1. 介绍Windows Craft 是一个用于编译代码的工具,它提供了一套简单易用的界面和功能,帮助开发者在 Windows 操作系统上进行代码编译。
本文将详细介绍 WindowsCraft 的使用方法以及一些常用的功能。
2. 安装Windows Craft 的安装非常简单,只需按照以下步骤进行操作:1.下载 Windows Craft 的安装包。
2.双击运行安装包,按照提示完成安装过程。
3.安装完成后,可以在开始菜单中找到 Windows Craft 的快捷方式。
3. 编译代码Windows Craft 提供了多种编译代码的方式,包括命令行和图形界面两种方式。
下面将分别介绍这两种方式的使用方法。
3.1 命令行编译在命令行中使用 Windows Craft 进行代码编译非常方便。
只需打开命令行窗口,输入相应的命令即可。
以下是一些常用的命令:# 编译 C++ 代码craft compile --language=c++ --source=source.cpp --output=output.exe# 编译 Java 代码craft compile --language=java --source=source.java --output=output.jar# 编译 C# 代码craft compile --language=c# --source=source.cs --output=output.exe以上命令中,--language参数指定了编译的语言,--source参数指定了源代码文件,--output参数指定了编译后的输出文件。
3.2 图形界面编译Windows Craft 的图形界面提供了更直观、易用的编译方式。
只需打开 Windows Craft 的界面,按照以下步骤进行操作:1.打开 Windows Craft。
2.在界面上选择要编译的代码文件。
MORNSUN B05_XT-2WR3 Series DC DC Converter Datashe

2W isolated DC-DC converterFixed input voltage,unregulated single outputPatent Protection RoHSFEATURES●Continuous short-circuit protection ●No-load input current as low as 8mA●Operating ambient temperature range:-40℃to+105℃●High efficiency up to 86%●Compact SMD package●I/O isolation test voltage 1.5k VDC●Industry standard pin-outB05_XT-2WR3series are designed for use in distributed power supply systems and especially suitable in applications such as pure digital circuits,low frequency analog circuits,relay-driven circuits and data switching circuits.Selection GuideCertificationPart No.Input Voltage (VDC)OutputFull Load Efficiency (%)Min./Typ.Capacitive Load(µF)Max.Nominal (Range)Voltage (VDC)Current(mA)Max./Min.--B0503XT-2WR35(4.5-5.5) 3.3400/4074/782400B0505XT-2WR35400/4080/842400B05X7XT-2WR37286/2980/841000B0509XT-2WR39222/2281/851000B0512XT-2WR312167/1781/85560B0515XT-2WR315133/1382/86560B0524XT-2WR32483/882/86220Input SpecificationsItemOperating ConditionsMin.Typ.Max.UnitInput Current(full load /no-load)5VDC input3.3VDC output--339/8357/--mA5VDC/7VDC output --477/8500/--9VDC/12VDC output --471/8494/--15VDC/24VDC output--466/8488/--Reflected Ripple Current*--15--Surge Voltage (1sec.max.)-0.7--9VDCInput Filter Capacitance filter Hot PlugUnavailableNote:*Reflected ripple current testing method please refer to DC-DC Converter Application Note for specific operation.Output SpecificationsItemOperating ConditionsMin.Typ.Max.UnitVoltage AccuracySee output regulation curve (Fig.1)Linear RegulationInput voltage change:±1%3.3VDC output----±1.5--5VDC/7VDC/9VDC/12V DC/15VDC/24VDC output ----±1.2Load Regulation10%-100%load3.3VDC output --1020%5VDC/7VDC output--9159VDC output--81012VDC/15VDC output --71024VDC output--610Ripple &Noise*20MHz bandwidth --75200mVp-p Temperature Coefficient Full load--±0.02--%/℃Short-circuit ProtectionContinuous,self-recoveryNote:*The“parallel cable”method is used for ripple and noise test,please refer to DC-DC Converter Application Notes for specific information. General SpecificationsItem Operating Conditions Min.Typ.Max.UnitIsolation Input-output electric strength test for1minute with aleakage current of1mA max.1500----VDC Insulation Resistance Input-output resistance at500VDC1000----MΩIsolation Capacitance Input-output capacitance at100kHz/0.1V--20--pFOperating Temperature Derating when operating temperature≥85℃,(seeFig.2)-40--105℃Storage Temperature-55--125Case Temperature Rise Ta=25℃--25--Storage Humidity Non-condensing5--95%RHReflow Soldering Temperature*Peak temp.Tc≤245℃,maximum durationtime≤60s over217℃Vibration10-150Hz,5G,0.75mm.along X,Y and Z Switching Frequency Full load,nominal input voltage--220--kHz MTBF MIL-HDBK-217F@25℃3500----k hours Moisture Sensitivity Level(MSL)IPC/JEDEC J-STD-020D.1Level1Note:*See also IPC/JEDEC J-STD-020D.1.Mechanical SpecificationsCase Material Black plastic;flame-retardant and heat-resistant(UL94V-0)Dimensions13.20x11.40x7.25mmWeight 1.4g(Typ.)Cooling Method Free air convectionElectromagnetic Compatibility(EMC)Emissions CE CISPR32/EN55032CLASS B(see Fig.4for recommended circuit) RE CISPR32/EN55032CLASS B(see Fig.4for recommended circuit)Immunity ESD IEC/EN61000-4-2Air±8kV,Contact±6kV perf.Criteria B Typical Characteristic Curves3.3VDC output5VDC/7VDC/9VDC/12VDC/15VDC/24VDC outputFig.1Design Reference1.Typical applicationInput and/or output ripple can be further reduced,by connecting a filter capacitor from the input and/or output terminals to ground as shown in Fig.3.Choosing suitable filter capacitor values is very important for a smooth operation of the modules,particularly to avoid start-up problems caused by capacitor values that are too high.For recommended input and output capacitor values refer to Table 1.Vin0VDCCinDC CoutFig.3Table 1:Recommended input and output capacitor valuesVin Cin Vo Cout5VDC 4.7µF/16V3.3VDC/5VDC 10µF/16V ----7VDC/9VDC4.7µF/16V ----12VDC 2.2µF/25V ----15VDC 1µF/25V ----24VDC0.47µF/50V2.EMC compliance circuitFig.4EmissionsC1,C24.7µF /16VC3Refer to the Cout in Fig.3CY 270pF/2kV LDM6.8µH3.For additional information,please refer to DC-DC converter application notes on80O u t p u t P o w e r P e r c e n t (%)Ambient Temp.()℃Temperature Derating CurveSafe Operating AreaFig.2Dimensions and Recommended Layout Tape and Reel InfoNotes:1.For additional information on Product Packaging please refer to .Tube Packaging bag number:58210024,RollPackaging bag number:58200054;2.If the product is not operated within the required load range,the product performance cannot be guaranteed to comply with allparameters in the datasheet;3.The maximum capacitive load offered were tested at input voltage range and full load;4.Unless otherwise specified,parameters in this datasheet were measured under the conditions of Ta=25℃,humidity<75%RH with nominalinput voltage and rated output load;5.All index testing methods in this datasheet are based on our company corporate standards;6.We can provide product customization service,please contact our technicians directly for specific information;7.Products are related to laws and regulations:see"Features"and"EMC";8.Our products shall be classified according to ISO14001and related environmental laws and regulations,and shall be handled byqualified units.MORNSUN Guangzhou Science&Technology Co.,Ltd.Address:No.5,Kehui St.1,Kehui Development Center,Science Ave.,Guangzhou Science City,Huangpu District,Guangzhou,P.R.China Tel:86-20-38601850Fax:86-20-38601272E-mail:***************。
WLS15 Pro LED Strip Light with PICK-IQ 说明书
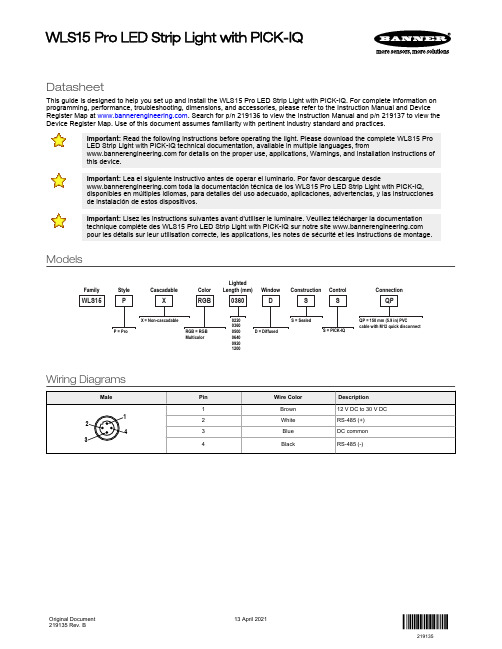
DatasheetThis guide is designed to help you set up and install the WLS15 Pro LED Strip Light with PICK-IQ. For complete information on programming, performance, troubleshooting, dimensions, and accessories, please refer to the Instruction Manual and Device Register Map at . Search for p/n 219136 to view the Instruction Manual and p/n 219137 to view the Device Register Map. Use of this document assumes familiarity with pertinent industry standard and practices.Important: Read the following instructions before operating the light. Please download the complete WLS15 Pro LED Strip Light with PICK-IQ technical documentation, available in multiple languages, from for details on the proper use, applications, Warnings, and installation instructions of this device.Important: Lea el siguiente instructivo antes de operar el luminario. Por favor descargue desde toda la documentación técnica de los WLS15 Pro LED Strip Light with PICK-IQ,disponibles en múltiples idiomas, para detalles del uso adecuado, aplicaciones, advertencias, y las instrucciones de instalación de estos dispositivos.Important: Lisez les instructions suivantes avant d'utiliser le luminaire. Veuillez télécharger la documentation technique complète des WLS15 Pro LED Strip Light with PICK-IQ sur notre site pour les détails sur leur utilisation correcte, les applications, les notes de sécurité et les instructions de montage.ModelsWLS15XRGB 0360D QPConnectionWindowLighted Length (mm)ColorCascadableFamilyX = Non-cascadableRGB = RGB Multicolor022003600500064009201200QP = 150 mm (5.9 in) PVCcable with M12 quick disconnectS = SealedSConstructionS = PICK-IQS ControlStyleP P = ProD = DiffusedWiring DiagramsWLS15 Pro LED Strip Light with PICK-IQOriginal Document 219135 Rev. B13 April 2021219135SpecificationsSupply Voltage12 V DC to 30 V DCUse only with suitable Class 2 power supply (UL) or a SELV power supply (CE)See electrical characteristics on product labelSupply Protection CircuitryProtected against reverse polarity and transient voltagesNote: Do not spray cable with high-pressure sprayer, or cable damage will result.ConstructionClear anodized aluminum housing Polycarbonate outer housing Polyamide end capsConnections150 mm (6 in) PVC cable with a 4-pin M12 male quick disconnect Models with a quick disconnect require a mating cordsetMountingIntegral mounting slots for M4 (#8) screws, tighten to 0.56 N·m (5 in·lbf) max torqueMultiple bracket options availableSecure cables within 150 mm (5.9 in) of the lightNote: It is recommended to use the provided mounting bushings when mounting using the endcaps. Center the mounting bushings in each slot to allow for expansion and contraction.Install using a M4 (#8) screw in each bushing torqued to a maximum of 0.45 N-m (4 in-lbf). For 920 mm and 1200 mm models in environments that vary more than 10 °C (18 °F), it is recommended to use one of the mounting bracket options instead of the end cap slots. If using the LMBWLS15 clip bracket and additional attachment is desired, only one end may be fastened using one of the spacers provided in the LMBWLS15 hardware packet to allow the opposite end to expand and contract. See mounting options in the instruction manual for bracket and tape options that allow expansion and contraction over temperature variations.Environmental RatingRated IEC IP66 and IEC IP67Suitable for wet locations per UL 2108Vibration and Mechanical ShockVibration: 10 Hz to 55 Hz, 1.0 mm peak-to-peak amplitude per IEC 60068-2-6Shock: 15G 11 ms duration, half sine wave per IEC 60068-2-27Operating Temperature–40 °C to +50 °C (–40 °F to +122 °F)Storage Temperature: –40 °C to +70 °C (–40 °F to +158 °F)CertificationsE476617Dimensions - Tel: + 1 888 373 6767P/N 219135 Rev. BBanner Engineering Corp. Limited WarrantyBanner Engineering Corp. warrants its products to be free from defects in material and workmanship for one year following the date of shipment. Banner Engineering Corp. will repair or replace, free of charge, any product of its manufacture which, at the time it is returned to the factory, is found to have been defective during the warranty period. This warranty does not cover damage or liability for misuse, abuse, or the improper application or installation of the Banner product.THIS LIMITED WARRANTY IS EXCLUSIVE AND IN LIEU OF ALL OTHER WARRANTIES WHETHER EXPRESS OR IMPLIED (INCLUDING, WITHOUT LIMITATION, ANY WARRANTY OF MERCHANTABILITY OR FITNESS FOR A PARTICULAR PURPOSE), AND WHETHER ARISING UNDER COURSE OF PERFORMANCE, COURSE OF DEALING OR TRADE USAGE.This Warranty is exclusive and limited to repair or, at the discretion of Banner Engineering Corp., replacement. IN NO EVENT SHALL BANNER ENGINEERING CORP. BE LIABLE TO BUYER OR ANY OTHER PERSON OR ENTITY FOR ANY EXTRA COSTS, EXPENSES, LOSSES, LOSS OF PROFITS, OR ANY INCIDENTAL, CONSEQUENTIAL OR SPECIAL DAMAGES RESULTING FROM ANY PRODUCT DEFECT OR FROM THE USE OR INABILITY TO USE THE PRODUCT, WHETHER ARISING IN CONTRACT OR WARRANTY, STATUTE, TORT, STRICT LIABILITY, NEGLIGENCE, OR OTHERWISE.Banner Engineering Corp. reserves the right to change, modify or improve the design of the product without assuming any obligations or liabilities relating to any product previously manufactured by Banner Engineering Corp. Any misuse, abuse, or improper application or installation of this product or use of the product for personal protection applications when the product is identified as not intended for such purposes will void the product warranty. Any modifications to this product without prior express approval by Banner Engineering Corp will void the product warranties. All specifications published in this document are subject to change; Banner reserves the right to modify product specifications or update documentation at any time. Specifications and product information in English supersede that which is provided in any other language. For the most recent version of any documentation, refer to:.For patent information, see /patents.FCC Part 15 and CAN ICES-3 (B)/NMB-3(B)This device complies with part 15 of the FCC Rules and CAN ICES-3 (B)/NMB-3(B). Operation is subject to the following two conditions:1.This device may not cause harmful interference, and2.This device must accept any interference received, including interference that may cause undesired operation.This equipment has been tested and found to comply with the limits for a Class B digital device, pursuant to part 15 of the FCC Rules and CAN ICES-3 (B)/NMB-3(B). These limits are designed to provide reasonable protection against harmful interference in a residential installation. This equipment generates, uses and can radiate radio frequency energy and, if not installed and used in accordance with the instructions, may cause harmful interference to radio communications. However, there is no guarantee that interference will not occur in a particular installation. If this equipment does cause harmful interference to radio or television reception, which can be determined by turning the equipment off and on, the user is encouraged to try to correct the interference by one or more of the following measures:•Reorient or relocate the receiving antenna.•Increase the separation between the equipment and receiver.•Connect the equipment into an outlet on a circuit different from that to which the receiver is connected.•Consult the manufacturer.Mexican ImporterBanner Engineering de Mèxico, S. de R.L. de C.V.David Alfaro Siqueiros 103 Piso 2 Valle orienteSan Pedro Garza Garcia Nuevo Leòn, C. P. 6626981 8363.2714© Banner Engineering Corp. All rights reserved。
AS 1544.2-2003 Methods For Impact Tests On Metals - Charpy V-notch

AS 1544.2—2003Australian Standard ™Method for impact tests on metals Part 2: Charpy V-notchAS 1544.2 L i c e n s e d t o C o l i n M . L o r r i m a r M T S M e t o n 22 M a y 2007. 1 u s e r p e r s o n a l u s e r l i c e n c e o n l y . S t o r a g e , d i s t r i b u t i o n o r u s e o n n e t w o r k p r o h i b i t e d .This Australian Standard was prepared by Committee MT-006, Mechanical Testing of Meta ls. It wa s a pproved on beha lf of the Council of Sta nda rds Austra lia on15 August 2003 and published on 19 September 2003.The following are represented on Committee MT-006:Australasian Railway AssociationAustralasian Aluminium CouncilAustralian Industry GroupBureau of Steel Manufacturers of AustraliaCSIRO Measurement LaboratoryCSIRO Telecommunications and Industry PhysicsInstitute of Materials Engineering AustralasiaKeeping Standards up-to-dateSta nda rds a re living documents which reflect progress in science, technology a ndsystems. To ma inta in their currency, a ll Sta nda rds a re periodica lly reviewed, andnew editions re published. Between editions, mendments m y be issued. Sta nda rds ma y a lso be withdra wn. It is importa nt tha t rea ders a ssure themselves they a re using a current Sta nda rd, which should include a ny a mendments whichmay have been published since the Standard was purchased. Deta iled information a bout Sta nda rds ca n be found by visiting the Sta nda rds Austra lia web site a t www.sta nda .a u a nd looking up the releva nt Sta nda rdin the on-line catalogue. Alternatively, the printed Catalogue provides information current at 1 January each year, and the monthly magazine, The Global Standard , has a full listing of revisionsand amendments published each month. We a lso welcome suggestions for improvement in our Sta nda rds, a nd especiallyencoura ge rea ders to notify us immedia tely of a ny a ppa rent ina ccura cies or a mbiguities. Conta ct us via ema il a t ma il@sta nda .a u, or write to the ChiefExecutive, Sta nda rds Austra lia Interna tiona l Ltd, GPO Box 5420, Sydney, NSW 2001. This Standard was issued in draft form for comment as DR 03087.L i c e n s e d t o C o l i n M . L o r r i m a r M T S M e t o n 22 M a y 2007. 1 u s e r p e r s o n a l u s e r l i c e n c e o n l y . S t o r a g e , d i s t r i b u t i o n o r u s e o n n e t w o r k p r o h i b i t e d .巴巴客标准 免费下载AS 1544.2—2003Australian Standard ™Method for impact tests on metalsPart 2: Charpy V-notchOriginated as AS B188.2—1962.Previous edition AS 1544.2—1989.Third edition 2003.COPYRIGHT© Standards Australia InternationalAll rights are reserved. No part of this work may be reproduced or copied in any form or by anymeans, electronic or mechanical, including photocopying, without the written permission of thepublisher.Published by Standards Australia International LtdGPO Box 5420, Sydney, NSW 2001, AustraliaISBN 0 7337 5042 7 L i c e n s e d t o C o l i n M . L o r r i m a r M T S M e t o n 22 M a y 2007. 1 u s e r p e r s o n a l u s e r l i c e n c e o n l y . S t o r a g e , d i s t r i b u t i o n o r u s e o n n e t w o r k p r o h i b i t e d .AS 1544.2—2003 2PREFACEThis Standard was prepared by the Standards Australia Committee MT-006, MechanicalTesting of Metals, to supersede AS 1544.2―1989, Methods for impact tests on metals, Part2: Charpy V-notch.The objective of this Standard is to specify a method for testing toughness in metals byimpact testing.This Standard is Method 2 of a series of Standards on the methods for impact testing ofmetals. The series comprises the following methods:AS1544 Method for impact tests on metals1544.1 Part 1: Izod1544.2 Part 2: Charpy V-notch1544.3 Part 3: Charpy U-notch and keyhole notch1544.4 Part 4: Calibration of the test machine1544.5 Part 5: Assessment of fracture surfaces appearance of steelResearch indicates that significant differences in absorbed energy are obtained usingmachines fitted with 2 mm radius strikers and 8 mm radius strikers at absorbed energyvalues exceeding 100 joules.The term ‘normative’ has been used in this Standard to define the application of theappendix to which it applies. A ‘normative’ appendix is an integral part of a Standard.L i c e n s e d t o C o l i n M . L o r r i m a r M T S M e t o n 22 M a y 2007. 1 u s e r p e r s o n a l u s e r l i c e n c e o n l y . S t o r a g e , d i s t r i b u t i o n o r u s e o n n e t w o r k p r o h i b i t e d .巴巴客标准 免费下载3 AS 1544.2—2003CONTENTSPageFOREWORD (4)1 SCOPE (5)2 REFERENCED DOCUMENTS (5)3 DEFINITIONS (5)4 TESTING MACHINE (6)5 TEST PIECE (9)6 PROCEDURE (11)7 REPORT...................................................................................................................13 APPENDICES A INSTALLATION, CALIBRATION AND MAINTENANCE OF THE TESTING MACHINE ...............................................................................................14 B RECORD OF TEST RESULTS (17)L i c e n s e d t o C o l i n M . L o r r i m a r M T S M e t o n 22 M a y 2007. 1 u s e r p e r s o n a l u s e r l i c e n c e o n l y . S t o r a g e , d i s t r i b u t i o n o r u s e o n n e t w o r k p r o h i b i t e d .AS 1544.2—2003 4FOREWORDThe Charpy V-notch Impact Test is a pendulum-type single-blow impact test in which thetest piece, V-notched in the middle and supported at both ends as a simple beam, is brokenby a falling pendulum which strikes the test piece opposite the notch. The energy absorbedis determined from the subsequent rise of the pendulum.The satisfactory operation of a pendulum impact testing machine is dependent on factorswhich include the design, the foundation, the accuracy of construction of machinecomponents, the degree of wear, and the friction-free movement of the pendulum.During a test, all the absorbed energy indicated by the machine is attributed to thefracturing of the test piece. However, it is known that there are other mechanisms by whichsmall amounts of energy may be absorbed. It is suspected that items such as test piecesupports, the machine foundation and frame work, the pendulum and striker, ejection anddrag of the broken test piece cause some degree of energy absorption. This energy is notdetermined, as suitable methods and apparatus have not yet been developed for measuringenergy absorption by these individual items.L i c e n s e d t o C o l i n M . L o r r i m a r M T S M e t o n 22 M a y 2007. 1 u s e r p e r s o n a l u s e r l i c e n c e o n l y . S t o r a g e , d i s t r i b u t i o n o r u s e o n n e t w o r k p r o h i b i t e d .巴巴客标准 免费下载5 AS 1544.2—2003.au Standards Australia STANDARDS AUSTRALIAAustralian StandardMethod for impact tests on metalsPart 2: Charpy V-notch 1 SCOPEThis Standard specifies the conditions for performing the Charpy V-notch impact test onmetals. It also includes requirements for the installation of the testing machine, its initialand periodic calibration, and recommendations for its maintenance by the user.2 REFERENCED DOCUMENTS The following documents below are referred to in this Standard: AS 1544 Method for impact tests on metals 1544.4 Part 4: Calibration of the testing machine 1544.5 Part 5: Assessment of fracture surface appearance of steel ISO 148 Steel—Charpy impact test (V-notch) ASTM E23 Methods for notched bar impact testing of metallic materials 3 DEFINITIONS For the purpose of this Standard, the definitions below apply. 3.1 Centre of percussion That point in a pendulum at which a blow, delivered in a tangential direction, will cause no reaction at the centre of rotation. 3.2 Initial potential energy The energy theoretically available in a pendulum-type impact testing machine when the pendulum is returned from its striking position to its initial release position. 3.3 Length of pendulum The distance from the axis of rotation of the pendulum to the impact point of the pendulum, on a standard test piece. 3.4 Point of impact The midpoint of the line of contact between the striking edge and the test piece. 3.5 Sample A portion of material or a group of items selected from a batch or consignment by a sampling procedure. 3.6 Secondary standard test pieces Charpy test pieces having an assigned impact value obtained from tests performed upon a verified testing machine.L i c e n s e d t o C o l i n M . L o r r i m a r M T S M e t o n 22 M a y 2007. 1 u s e r p e r s o n a l u s e r l i c e n c e o n l y . S t o r a g e , d i s t r i b u t i o n o r u s e o n n e t w o r k p r o h i b i t e d .AS 1544.2—2003 6Standards Australia.au 3.7 Standardized test piecesCharpy test pieces from a nationally recognized source which have certified impact valuesfor testing machine verification purposes.3.8 Striking energyThe kinetic energy of the pendulum of the testing machine at the instant of impact.3.9 Striking velocityThe linear velocity of the striking edge at the instant of impact.3.10 Test pieceA prepared piece for testing, made from a test specimen by some mechanical operation.3.11 Test specimenA portion of material, or a single item taken from the sample, for the purpose of applying a particular test. 3.12 Verification Proving of calibration procedures by testing of standardized test pieces. 4 TESTING MACHINE 4.1 General The testing machine shall be of the pendulum type, and shall be so constructed that the loss of energy (such as from translation, rotation or vibration) in the machine framework and pendulum during a test, is negligible (see ISO 148). Under certain circumstances, charpy machines meeting the requirements of ASTM E23 shall be deemed to comply with this Standard. Machines that have been calibrated to ASTM E23 may be used for testing with this Standard provided that the minimum specified energy is equal to or less than 100 joules. NOTE: Machines complying with this Standard and that have been calibrated to AS 1544.4 do not meet the requirements of ASTM E23. 4.2 Installation, calibration and maintenance The machine shall be installed and calibrated in accordance with Paragraphs A1 and A2 of Appendix A. It shall be recalibrated periodically, and when otherwise necessary, in accordance with Paragraph A2 of Appendix A. The machine should be maintained in satisfactory working order and condition in the intervals between successive recalibrations, in accordance with Paragraph A3 of Appendix A. 4.3 Test piece supports The test piece supports consist of two mutually perpendicular surfaces extending on each side of, and normal to, the plane of swing of the pendulum. Essentially, one of these divided surfaces supports the weight of the test piece and the other takes the reaction from the impact blow on the test piece. The corresponding parts of the divided surfaces are coplanar. The level of the supports shall be such that the longitudinal axis of a supported test piece is parallel within 2:1000 to the reference surface of the machine. The supports shall be of hardened steel. They shall be attached rigidly to the frame of the machine and shall satisfy the following conditions (see Figure 1): (a)Distance between supports ................................................................40 +0.5,−0 mm. (b) Radius of curvature......................................................................1.0 mm to 1.5 mm.L i c e n s e d t o C o l i n M . L o r r i m a r M T S M e t o n 22 M a y 2007. 1 u s e r p e r s o n a l u s e r l i c e n c e o n l y . S t o r a g e , d i s t r i b u t i o n o r u s e o n n e t w o r k p r o h i b i t e d .巴巴客标准 免费下载7 AS 1544.2—2003.au Standards Australia (c)Taper of supports (see Note 1)..................................................................1 ±0.1 in 5. (d) Angle of supports (see Note 2).........................................................90 ±0.1 degrees.NOTES:1 Ma chines ma nufa ctured with supports ha ving a n included a ngle of 78 degrees to80 degrees are acceptable.2 A relieving recess is provided at the junction of the two support surfaces.4.4 StrikerThe striker and its components shall comply with the following requirements:(a) The striker shall be of hardened steel.(b) The striker shall be attached rigidly to the pendulum and shall satisfy the followingconditions (see Figure 1):(i)Included angle of striker.............................................................30 ±1 degrees. (ii) Radius of curvature of striking edge.....................................2.0 mm to 2.5 mm. (iii) Maximum width of striker.....................................................................18 mm. NOTE: The ma ximum width requirement a pplies to a ny pa rt of the pendulum which pa sses between the supports for a dista nce of 7.5 mm from the centre of a supported sta ndard test piece in a direction pa ra llel to the striking edge. For rea sons outlined in Clause 4.5, widths less than 18 mm are desirable to ensure that adequate clearance can be maintained. (c) The striking edge shall be rounded with a smooth profile blending with the faces of the striker. (d) The plane of swing of the striking edge shall be within 0.5 mm of the centre of the gap between the supports. It shall also be vertical and normal to the supports. (e) When the striking edge is 10 mm away from the plane of the reaction surface of the supports, it shall be parallel within 0.03 mm in 10 mm to this plane. (f) When the striking edge makes contact with the test piece, the line of contact shall be perpendicular within 2 degrees to the longitudinal axis of the test piece. In addition, the striker shall be symmetrical about the plane of the swing of the striking edge. 4.5 Test piece clearance The requirements for the geometry of the test piece, test piece supports and striker at the instant of impact are such as to ensure clearance between the striker, the broken halves of the test piece and the supports, during the test. However, this clearance can be lost as a result of asymmetry of the striker or a change in alignment of the pendulum. The clearance between the supports and striker, or any adjacent part of the pendulum which passes between the supports, shall be not less than 10.5 mm. The broken test piece should be free to leave the machine with the minimum of interference, and should not rebound into the pendulum. Any end stop used for locating the test piece in the supports shall be retracted in order that it does not impede the movement of the test piece during the test. NOTE: Clea ra nce of 13 mm should be used to ensure the specimen does not interfere with the striker. 4.6 Centre of percussion The distance of the centre of percussion from the axis of rotation shall be equal to the length of the pendulum, ±1 percent.L i c e n s e d t o C o l i n M . L o r r i m a r M T S M e t o n 22 M a y 2007. 1 u s e r p e r s o n a l u s e r l i c e n c e o n l y . S t o r a g e , d i s t r i b u t i o n o r u s e o n n e t w o r k p r o h i b i t e d .AS 1544.2—2003 8Standards Australia .au4.7 Striking velocityThe striking velocity shall be 4.5 to 7.0 m/s. In the case of a dispute 5 to 5.5 m/s shall beused.4.8 Indicating equipmentFor scales graduated in joules, the scale intervals shall not exceed 1 J for machines having astriking energy of 160 J or less, or 2 J for machines having a striking energy greater than160 J.DIMENSIONS IN MILLIMETRES FIGURE 1 ARRANGEMENT OF SUPPORTS, TEST PIECE AND STRIKER For scales graduated in other units, the scale intervals shall not exceed 1 percent of the maximum scale value. The thickness of the scale marks and the width of the tip of the pointer shall not exceed one fifth of the minimum scale spacing. The pointer should permit a reading free from parallax error. The length of the smallest scale mark should not be less than 2.5 mm. 4.9 Zero reading When the machine is operated normally but without a test piece in position, the reading indicated by the pointer is the zero reading. This reading shall not exceed ±0.5 percent of the nominal initial potential energy (see Paragraph A3.4 of Appendix A). 4.10 Friction losses Energy is absorbed by friction, including air resistance, bearing friction and friction of the pointer. The total losses by friction for one swing shall not exceed 0.5 percent of the initial potential energy (see Paragraph A3.5 of Appendix A).L i c e n s e d t o C o l i n M . L o r r i m a r M T S M e t o n 22 M a y 2007. 1 u s e r p e r s o n a l u s e r l i c e n c e o n l y . S t o r a g e , d i s t r i b u t i o n o r u s e o n n e t w o r k p r o h i b i t e d .巴巴客标准 免费下载9 AS 1544.2—20034.11 Initial potential energyThe initial potential energy shall not differ from the nominal value by more than ±1 percent. (See AS 1544.4 for the method of determining initial potential energy.) 4.12 Indicated absorbed energyThe error in indicated absorbed energy shall not exceed 3 percent of the energy corresponding to the indicated value, or 1 percent of the energy corresponding to the full scale, whichever is the greater. (See AS 1544.4 for the method for calibration of scales.) 5 TEST PIECE5.1 Sampling and preparationSamples for testing shall be selected in accordance with the requirements of the relevant product specification or code of practice, as applicable. Any significant metallurgical damage shall be removed by machining.All samples, specimens and test pieces shall be adequately identified as to their origin and location.5.2 Form of test piece 5.2.1 GeneralThe test piece, which shall be machined all over, shall be 55 mm long, and in the centre of the length of one face there shall be a V-notch of 45 degrees included angle, 2 mm depth and 0.25 mm root radius. The plane of symmetry of the notch shall be perpendicular to the longitudinal axis of the test piece (see Figures 2 and 3). 5.2.2 Standard test pieceThe standard test piece shall be of square cross-section, nominally 10 mm × 10 mm. 5.2.3 Subsidiary test piecesWhere a standard test piece cannot be obtained from the material, one of the subsidiary test pieces of rectangular cross-section and having the notch cut in one of the narrower faces, shall be used.NOTE: No general correlation has been established between results obtained from test pieces of different sizes, and results should be compared only on test pieces of identical dimensions.5.2.4 Dimension and tolerances of test piecesThe standard test piece and subsidiary test pieces shall have dimensions and tolerances in accordance with Table 1.L i c e n s e d t o C o l i n M . L o r r i m a r M T S M e t o n 22 M a y 2007. 1 u s e r p e r s o n a l u s e r l i c e n c e o n l y . S t o r a g e , d i s t r i b u t i o n o r u s e o n n e t w o r k p r o h i b i t e d .AS 1544.2—2003 10Standards Australia.auTABLE 1DIMENSIONS AND TOLERANCES OFTEST PIECESCharacteristic Nominal dimension MachiningtoleranceLength 55 mm±0.60 mmThicknessStandard test pieceSubsidiary test piece Subsidiary test piece Subsidiary test piece Subsidiary test piece10 mm 7.5 mm 6.7 mm 5 mm 2.5 mm±0.11 mm ±0.11 mm ±0.06 mm ±0.06 mm ±0.06 mm Width10 mm ±0.06 mm Root radius of notch 0.25 mm±0.025 mm Depth below notch8 mm ±0.06 mm Distance of centre of notch from one end of test piece 27.5 mm±0.42 mmAngle between plane of symmetry of notch and longitudinal axis of test piece 90° ±2° Angle of notch45° ±2° Angle between adjacent longitudinal faces of test piece90°±20°NOTE: Some product Standards may require a full material thickness test pieceDIMENSIONS IN MILLIMETRESFIGURE 2 STANDARD AND SUBSIDIARY TEST PIECES5.3 Notch preparationUnless a particular method is specified in the relevant product specification or code of practice, the notch may be cut by any machining method providing a smooth profile, as specified, is produced (see Figure 3).L i c e n s e d t o C o l i n M . L o r r i m a r M T S M e t o n 22 M a y 2007. 1 u s e r p e r s o n a l u s e r l i c e n c e o n l y . S t o r a g e , d i s t r i b u t i o n o r u s e o n n e t w o r k p r o h i b i t e d .11 AS 1544.2—2003NOTE: The impact properties of some materials may be affected by the notch preparation methodemployed; for exa mple, to a void the effect of stra in a geing in the notch region of low ca rbon steel, it is advisable to notch the test pieces the same day as they are tested and to form the notch using light cuts with a finishing cut of 0.03 mm to 0.05 mm.FIGURE 3 ENLARGED VIEW OF NOTCHIN TEST PIECE6 PROCEDURE6.1 Conditioning of test piece 6.1.1 GeneralThose portions of any appliance that make contact with the test piece during transfer to the machine shall be at the same temperature as the test piece. This requirement also applies to any device which uses the notch for centring.NOTE: The mechanism e.g. tongs, which are used to handle the specimens in the bath should be pla ced in the ba th for a minimum of 5 minutes before testing a nd returned to the ba th between tests.6.1.2 Tests at ambient temperatureThe ambient test temperature shall be recorded immediately before testing. In the event of dispute, the test temperature shall be 20 ±2°C.6.1.3 Tests at subzero temperatures or temperatures up to 200°CWhere the impact properties are to be determined at subzero temperatures, or at temperatures above ambient up to 200°C, the test piece shall be brought to the specified test temperature by immersion in a continuously agitated liquid bath or gaseous medium. The period of immersion of the test piece and appliance in a bath at the test appliance in a bath at the test temperature shall not be less than 5 minutes, and in the case of a gaseous medium, not less than 30 minutes.NOTE: The test pieces should be suspended a minimum of 25 mm from the bottom of the immersion tank.The test piece shall be broken within 5 s from the time of removal from the conditioning medium.NOTE: For tests a t tempera tures a bove 20°C, a n oil ba th is preferred to a wa ter ba th for conditioning.6.1.4 Tests at temperatures above 200°CFor tests at temperatures above 200°C, the test piece shall be heated in a suitable oven or furnace at the specified test temperature for 30 min, or in a suitable liquid bath for a sufficient time to permit the test piece to reach the test temperature.L i c e n s e d t o C o l i n M . L o r r i m a r M T S M e t o n 22 M a y 2007. 1 u s e r p e r s o n a l u s e r l i c e n c e o n l y . S t o r a g e , d i s t r i b u t i o n o r u s e o n n e t w o r k p r o h i b i t e d .AS 1544.2—2003 12Standards Australia .auThe test piece shall be broken within 5 s from the time of removal from the oven, furnace or bath.NOTE: The use of a salt bath furnace may be found to be unsatisfactory, as encrustations of salt may prevent proper seating of the test piece.6.1.5 Accuracy of conditioning temperatureUnless otherwise specified in the product specification or code of practice, the temperature of the conditioning medium shall conform to Table 2.TABLE 2TEMPERATURE OF CONDITIONING MEDIUMSpecified test temperatureTolerance on temperature ofconditioning medium°C°C Below −60−60 to 100 Above 100 to 200±2 ±1 ±26.2 Location of test pieceThe test piece shall lie with the notched face squarely against the reaction supports so that it will be struck on the face opposite the notch (see Figure 1).The plane of symmetry of the notch shall be within 0.5 mm of the plane of swing of the striking edge. If an end stop is used to position the test piece, the form of the stop shall be such that it does not impede the movement of the test piece.The use of an end stop shall make it necessary to machine the test piece length to tolerances closer than those given in the Table 1. 6.3 Operation of the testing machineThe machine shall be operated in accordance with the manufacturer's instructions. Attention shall be given to the following:(a) Safety, i.e. observing the correct sequence of operations, and taking precautionsagainst possible accident (see Warning). (b) Correct location of the test piece. (c) Setting the pointer.(d) Releasing the pendulum without imparting vibration to it. (e) Reading the scale, avoiding parallax errors (see Note).(f)Clearance. If there is any evidence of jamming, i.e. interference between the broken halves of the test piece and the pendulum, tests shall be discontinued until the cause has been ascertained and the fault rectified (see Paragraph A3.2 of Appendix A).NOTE: If the sca le rea ding is ta ken a fter the pendulum ha s been reset a t its initia l relea se position, ca re should be ta ken to ensure tha t the a ction of a rresting a nd resetting the pendulum does not cause the scale reading to change.L i c e n s e d t o C o l i n M . L o r r i m a r M T S M e t o n 22 M a y 2007. 1 u s e r p e r s o n a l u s e r l i c e n c e o n l y . S t o r a g e , d i s t r i b u t i o n o r u s e o n n e t w o r k p r o h i b i t e d .13 AS 1544.2—2003WARNING: IT IS RECOMMENDED THAT A SAFETY SCREEN BEPROVIDED TO ARREST ANY BROKEN TEST PIECE HALVES EJECTED DURING THE TEST.6.4 Record of test resultsA record of test results shall be made and shall include the information required in Appendix B. 7 REPORTWhere a report of the test is required, it shall include the following: (a)The type of test, i.e. Charpy V-notch. If a subsidiary test piece is used, the thickness shall be stated.(b) Reference to this Australian Standard, i.e. AS 1544.2, and to a relevant productspecification or code of practice, where applicable.(c) The nominal striking energy of the machine, in joules. (d) The identification of the test piece.(e)The indicated absorbed energy, in joules, and if the number is higher than 80 percent of the machine capacity.NOTE: If the test piece a bsorbs the full energy of the ma chine without pa ssing through the supports, the absorbed energy shall be reported as above 80% of the machine capacity.(f) The test temperature, in degrees Celsius (see Clause 6.1). (g) The fracture surface appearance, if required (see AS 1544.5). (h) Date of report.(i)Compliance or otherwise with specified requirements, if applicable.NOTE: When the sta nda rd test piece is used, it is permissible to use symbols in the presentation of test results. Example:C 300 V: χJ at y °C whereC ...................................................................................indicates the type of test (Charpy) 300............................................indicates the striking energy of the machine used in joules V..............................................................................................indicates the type of notch χ....................................................................is the value of the indicated absorbed energy y.....................................................................................................is the test temperature.L i c e n s e d t o C o l i n M . L o r r i m a r M T S M e t o n 22 M a y 2007. 1 u s e r p e r s o n a l u s e r l i c e n c e o n l y . S t o r a g e , d i s t r i b u t i o n o r u s e o n n e t w o r k p r o h i b i t e d .。
nVent PYROTENAX 1850 Fire-Rated Three-Way Splice 2

PYROTENAXFire-Rated Three-Way Splice Instructions for Making a Fire-Rated Three-Way Splice2 |DESCRIPTIONThis kit is used to make a three-way fire-rated field splice for nVent PYROTENAX 1850 Mineral Insulated cables. The process includes splicing the cables together inside the heat insulated enclosure and adding the collars for additional heat protection.For compliance with NEC (NFPA 70, 2014 edition) article 728.5F, this kit must be installed using System 1850 cables if the intent is to create a 1-hour fire-rated circuit.The Components supplied with this splice kit must be used to complete the splice. Substituting other materials or components will void the 1-hour fire rating and approvals.For technical support contact your nVent representative or call (800) 545-6258 for assistance.TOOLS REQUIRED• Open ended torque wrench for cable compression fitting (See Table 1 for size chart)• Wrench for cable compression fitting (See Table 1 for size chart)• Multimeter or continuity tester • 500 Vdc megohmmeter • Safety goggles and gloves • Caulking gun • Flat head screwdriver• 3/16 in diameter masonry drill bit (for 1/4 in concrete screws)• Drill• Hex driver (for drill) to install masonry screws• Wrench for inner box bonding wire: 7/16 in • Loctite ® 567™ instant thread sealantThis component is an electrical device that must be installed correctly to ensure proper operation and to prevent shock or fire. Read these important warnings carefully and follow all installation instructions.• S tore all splice kit components indoors in a clean, dry area.HEALTH HAZARD. Consult your nVentrepresentative or call (800) 545-6258 for MSDS safety information regarding the calcium silicatebox insulation and collars.APPROVALSULC Listed, 1-hour fire-resistant cable, tested to ULC-S139UL Classified, 1-hour fire-resistive cable, tested to UL 2196Completed Splice:• Splice is part of the Electrical Circuit Integrity System (FHIT) System No. 1850 in the UL Fire Resistance Directory when used with UL Classified System No. 1850 Cable (tested with hose stream)• Splice is part of the Electrical Circuit Integrity System Certified for Canada (FHIT7) System No. 1850 in the ULC Fire Resistance Directory when usedwith ULC Classified System No. 1850 Cable (tested with hose stream)Terminations for System 1850 Cables:and branch cable. Next, refer to installation instruction H60459 (Fire-Rated Three-Way Splice End Enclosure Sealing kit) to plug, insulate and seal the third entry into the enclosure since the final enclosure in the series only has 2 cable entries used.KIT CONTENTS: ALL TYPESItem Qty DescriptionA 1 EnclosureB 4 Concrete screws for enclosure mountingC 1 3M™ fire barrier sealantD 1 Collar for branch lineE 2 Collars for main power lineF 6 Hose clampsG 3 Shields for collarsKIT CONTENTS: PRE-TERMINATED CABLES(OR FIELD TERMINATED CABLES*)Item Qty DescriptionA 1 Pre-terminated main power line cable(assumes first line is already installedB 1 Pre-terminated branch line cable* See Fire-Rated Three-Way Splice Field Termination Instructions H60235 for details.AB | 34 | Bonding wire Removable hinge pinRemovable hinge pinRemovablehinge pinF2T2GNDF1T3T190°Pot1/4 in(6 mm)NPT cableentry(Cable shown in frontof the cabinet forillustrative purposes)• Open the outer enclosure and ensure the bonding wireis not attached to the door. Remove if necessary using a7/16 in wrench.• With the outer enclosure door half opened as shown onthe illustration, remove the door by pulling the removablehinge pins. Rotate the pin to lock it in open position.Important: Handle door with care, making sure notto drop it as the calcium silicate insulation may crack orbreak.• Locate enclosure position near the terminated end ofthe existing cable such that this cable has enough slackto enter the enclosure. There should be enough cablelength for the back of the pot to sit approximately 1/4 in(6 mm) past the inner enclosure threaded entry.Note: If it is the initial enclosure, locate its positionso as to extend the cable from the enclosure into thefireproof room.Note: Do not insert the cable /termination inside thebox yet as the box has to be secured first. The illustrationis a reference only to show how the installed cable shouldbe sitting inside the box. | 56 | | 78 | WARNING: For continued protection against risk of equipment damage and fire and to maintain fire-rated certification, replaceonly with fuse of the specified type, current and voltage rating as listed below:ATMR1/80.125 A 14 AWG ATMR2/100.2 A 14 AWG ATMR1/40.25 A 14 AWG ATMR3/100.3 A 14 AWG ATMR1/20.5 A 14 AWG ATMR3/40.75 A 14 AWG ATMR1 1.0 A 14 AWG ATMR1-1/4 1.25 A 14 AWG ATMR1-1/2 1.5 A 14 AWG ATMR2 2.0 A 14 AWG ATMR2-1/2 2.5 A 14 AWG ATMR3 3.0 A14 AWG | 910 | | 1112 | Gloved hand11a22a3411a 22a 345 Apply 1/4 in (6 mm) bead of 3M fire barriersealant around the first collar half shoulder.11a 22a 345Insert collar into the entry until it sits flush with the box (squeezing the fire barrier sealant).1a 22a 345 Repeat for the second collar half. 1a 22a 3451a 22a 345 Apply a 1/4 in (6 mm) bead of fire barrier seal -ant around the collar entry where the collarmeets the box.1a 22a 345Using gloves, ensure there is sealant all around by running your finger around the circumfer -ence. | 1314 | 16 | | 1718 | | 19NORTH AMERICA Tel: +1.800.545.6258 Fax: +1.800.527.5703 Tel: +1.650.216.1526 Fax: +1.650.474.7711 **********************。
- 1、下载文档前请自行甄别文档内容的完整性,平台不提供额外的编辑、内容补充、找答案等附加服务。
- 2、"仅部分预览"的文档,不可在线预览部分如存在完整性等问题,可反馈申请退款(可完整预览的文档不适用该条件!)。
- 3、如文档侵犯您的权益,请联系客服反馈,我们会尽快为您处理(人工客服工作时间:9:00-18:30)。
Workshop 15厚板的单次滚压成型分析模拟Introduction(简介)滚压成型(Rolling)是一种基本的生产技术, 常用来将已经预成型的半成品再制成适合于下一个制程的外型. 滚动制程(Rolling process)基本上是一种准静态的问题因为滚动(Rolling)通常是运作在相对较低的速度下(基本上是 1 m/s), 所以其惯性效应就显得不是那么重要了.典型的滚动(Rolling)几何一般来说需要 3D 的模型, 这会导致模型变得很大, 而且还要包括非线性材料行为以及非线性边界效果(接触跟摩擦). 因为如此, 所以显式(explicit)的动态解法中如果质量排列(mass scaling)有使用的话, 通常是比隐式(implicit)的准静态解法更快速也较可靠.本练习中包含了使用ABAQUS/Explicit 来求解一块板子的一次准静态滚压成型问题. 此一滚压成型制程会减少此板子的厚度42%. 质量排列(Mass scaling)会被使用以减少此分析的计算时间. 为了要比较的关系, 本分析也会使ABAQUS/Standard 中的内隐式解法解一次.本练习基本上是根据ABAQUS Example Problems 手册中的第1.3.6 节“Rolling of thick plates,”而做的.Geometry and model(几何与模型)一个半对称平面应变模型将被使用于一块长度0.092 m 半厚 0.02 m 的板子上. 一个90 部分(四分之一圆)的滚子(roller)建构成一个可分析型的刚体曲面(analytical rigid surface).1.从../IntroClass/workshops/ rolling目录打开一个新的ABAQUS/CAE 程序.在 ABAQUS/CAE中预设会自动产生一个模型叫(Model-1). 然而, since theexplicit dynamics model will later form the basis of the implicit analysis model,你应该将这个模型改一个比较能代表他的名字.2.在模型树中的Model-1上单击鼠标右键并从其弹出来的菜单列中选取Rename功能选项. 将之改名为Explicit.3.在模型树中的Parts上双击以制作一个新的零件. 将此零件取名为plate,选择2D Planar的模型空间(modeling space), 然后设定草图区域的大小为0.5. 查看一下其它的默认值, 然后单击Continue按钮.4.使用Create Lines: Rectangle工具, 画一个矩形0.092 m 长0.020 m 高,如图 Figure W15–1 所示.Figure W15–1 Plate geometry.5.在模型树中的Parts上双击再新建一个零件. 将此零件取名为roller. 也是选择2D Planar的模型空间(modeling space) 然后选用Analytical rigid做为零件类型. 设定草图区域的大小为2.0, 然后单击Continue按钮.6.使用Create Arc工具, 画一个任意半径的90︒的圆弧。
用尺寸工具将半径改成0.170 m,如图 W15–2所示.Figure W15–2 Roller geometry.7.从上方的下拉菜单中选取Tools→Reference Point功能选项, 然后选取此圆弧的圆心点在上面建一个此零件的参考点.Materials and section(材料与剖面性质)此钢板我们假设它是弹塑性材料. 虽然在滚压成型的分析模拟中, 通常是将之考虑成(rate-dependent)(材质特性与受压缩率相关)的塑性行为, 不过此处我们并不做此考虑.1.在模型树中的Materials上双击. 建一个新的材料叫做Steel其特性如下:∙弹性模量(Modulus of elasticity): 1.5E11 Pa∙泊松比(Poisson's ratio): 0.3∙密度(Density): 7850 kg/m3∙初始屈服应力是 168.72 MPa 一直上升到 448.45 MPa 期间应变为100%. 至于塑性特性数据如表 W15–1:Table W15–1 Yield stress-plastic strain data.2.在模型树中的Sections上双击制作一份均质的实体的剖面特性叫做plateSection使用其预设厚度1.0.3.在模型树中, 将Parts项之下的plate展开并在其所弹出来的菜单中的Section Assignments功能选项上双击. 将plateSection这个剖面特性指定到零件中.Assembly(组装)接着我们要将这些零件加到组装中并调整其在组装中的相对位置.1.在模型树中,将Assembly项展开在其中的Instances上双击.2.在弹出的Create Instance对话框中, 将该两个零件都选取起来并单击OK按钮.要调整板子跟滚轮的相对位置, 需要先了解滚轮跟板子先接触的地方是在哪里. 然后才能用一个基准几何来辅助定位. 在本例中板子的右上角将先跟滚轮接触, 滚轮的接触点则是在沿着其边缘大约20% 的地方(相对于滚轮的最底下点).3.从上方的下拉菜单中选取Tools→Datum功能选项, 然后使用其中的Enterparameter方法来制作一个基准点. 将这个点做在滚轮的边上, 同时给予一个正交化的边缘参数(normalized edge parameter)0.2.4.从上方的下拉菜单中选取Instance Translate功能选项, 来修改板子的位置.使用如图W15–3 中所示的起始点跟终止点来定义此移动的向量.注意:你模型中两个部件间的初时相对位置与图中显示的不同.end point start pointFigure W15–3 Part positioning.Sets and surfaces(组别设定与曲面)要让负载跟接触等较容易设定的话, 我们应该要制作几何组别跟曲面.1.在模型树中的Assembly项之下的Sets上双击. 按照图W15–4 中所示的区域来制作这几组几何组别(set):left:板子的左侧边缘bottom:板子的底侧边缘plate:整个板子refPt:滚轮的参考点refPtleft bottom plateFigure W15–4 Geometry sets.2.在模型树中的Assembly项之下的Surfaces上双击. 按照图W15–5 中所示的区域来制作这几个曲面:roller:滚轮面对板子的那一侧topPlate:板子的上侧与右侧topPlaterollerFigure W15–5 Surfaces.Analysis step and output requests(分析步与输出项设定)这个滚压成型的分析模拟将会使用单一个显式动态分析步来求解之.1.在模型树中的Steps上双击来产生一个分析时间为0.1秒的Dynamic,Explicit显式动态分析步取名叫做Single Pass Rolling. 其余的时间增量与其它参数都使用默认值就好.因为在滚压成型问题中通常是会考虑压缩率影响的, 可以用来加速分析效率的唯一方法只有质量排列(mass scaling).2.开启在Edit Step对话框中的Mass Scaling 标签页. 在此页中, 选用Usescaling definitions below选项然后单击Create按钮.3.在Edit mass scaling对话框中, 选择Set作为应用的区域; 并从拉下来的菜单中选取plate零件. 输入Scale by factor的值为1600. 分别按下在Edit mass scaling对话框及Edit Step对话框中的OK按钮.4.接受其预设的场变量输出设定. 在模型树中的History Output Requests上双击来产生一个滚轮参考点处的反作用力矩的历时数据输出项. 在EditHistory Output Request对话框中:A 选取Domain字段处的Set 选项然后从列出来的组别中选取refPt这一组.B 设定在此分析中每100个相等时间间隔才储存输出历程数据.C 从列出来的可用输出变数中, 单击在Forces/Reactions旁边的箭头将之展开还有还有它之下的RF, Reaction forces and moments也展开, 以列出其中的可选取变数. 将其中的 RM3选项打开.D 单击OK按钮.在这个分析中我们预期会有很大的变形发生. 使用ABAQUS/Explicit 中的自适化(adaptive)网格重建功能来减少网格的扭曲变形量, 并在整个分析过程中维持高网格质量.5.从上方的下拉菜单中选取Other→Adaptive Mesh Domain→Manager 功能选项.a.在ALE Adaptive Mesh Domain Manager中单击Edit按钮.b.在Edit ALE Adaptive Mesh Domain对话框中, 将Use the ALEadaptive mesh domain below选项开启.c.在对话框中单击Edit按钮选择区域.d.在提示区中点击Sets选项,在Region Selection对话中来选取plate,单击Continue.e.在其中的频率(frequency)字段输入10以及remeshing sweeps perincrement 字段输入3.W15.7f.将Adaptive mesh controls选项开启, 并单击对话框右侧的Create按钮.其自适化网格重建的参数全都使用其默认值就好.Contact(接触)面跟面的接触将会被设定在plate的顶面跟滚轮的外侧面之间. 其库伦(Coulomb)摩擦系数为0.4.1.在模型树中的Interaction Properties上双击来产生一个Contact特性其名字就使用其预设的IntProp-1.2.在Edit Contact Property对话框中, 选取Mechanical TangentialBehavior选项, 选用其 Penalty 摩擦公式(friction formulation).3.输入摩擦系数0.4. 单击OK.4.在模型树中的Interactions上双击.5.在Create Interaction对话框中, 选取Single Pass Rolling作为此互动相互影响时的分析步并选用Surface-to-surface contact (Explicit)作为其互动类型. 然后单击Continue按钮.6.接下来在提示区会提示你选取在此接触中所使用到的曲面(surfaces), 先按一下提示区中的Surfaces按钮来开启Region Selection对话框. 然后从其中选取roller作为第一个接触面以及topPlate作为第二个接触面(surface).7.接着在Edit Interaction对话框中, 查看一下互动(interaction) 的预设设定然后单击OK按钮.Boundary conditions(边界条件)滚轮以总体坐标的Z-轴做为旋转轴, 转速 6.2832 radians/sec. 至于被滚压的板子则会以1.01587m/sec 的速度沿着总体坐标的X-轴向移动, 这个速度跟滚轮的接触点处的X-轴向速度分量一样. 这样可以将初始的瞬时扰动减到最小因为在接触点的X-轴向上的初始加速度是零.1.在模型树中的BCs 项上单击鼠标右键, 从所弹出来的菜单中选取Manager功能选项.2.制作如表W15–2 中所列的边界条件:a.在Boundary Condition Manager对话框中, 单击Create.b.在Create Boundary Condition对话框中, 为此边界条件取名并选用其适用的分析步. 要设定位移的边界条件时选取Displacement/Rotation类型. 要设定角速度的边界条件时选取Velocity/Angular velocity类型. 然后按下Continue按钮.c.接着选取边界条件所要施加上去的区域.d.然后在Edit Boundary Condition对话框中设定此边界条件的约束条件.Table W15–2 Boundary conditions.Initial conditions(初始状态)如同较早前所提过的, 该板子会被给予一个1.01587 m/sec 的初始速度沿着总体坐标的X-轴向运动.1.在模型树中的Predefined Fields上双击.2.在Create Predefined Fields对话框中, 选取Initial分析步, Mechanical类别, 以及Velocity类型. 将此场(field)取名为initVel然后单击Continue按钮.3.接着选取plate组别作为此初始速度场的有效区域.4.在Edit Predefined Fields对话框中的V1字段中输入值1.01587 m/sec 作为其速度分量.Mesh(网格划分)这块板子上将被划分成150个线性, 平面应变的简积分单元(CPE4R).1.在模型树中将Parts项之下的plate展开并在其中的Mesh上双击.2.从上方的下拉菜单中选取Mesh→Element Type功能选项. 检查在Element type对话框中可用的各种不同选项, 将单元库切换成Explicit项并选用其中的Plane Strain单元, 接受其预设的CPE4R 单元类型3.从上方的下拉菜单中选取Seed→Part功能选项设定单元尺寸大小为0.002.4.从上方的下拉菜单中选取Mesh→Part功能选项然后单击提示区中的Yes按钮将此零件的网格划出. 建好的网格如图 W15–6.Figure W15–6 Plate mesh.Analysis(分析)1.在模型树中的Jobs上双击制作一个分析作业叫做roll-xpl. 其中的各项参数都使用默认值.2.从上方的菜单中选取File→Save As功能选项, 将此模型数据存盘roll.cae.3.在模型树中的roll-xpl上单击鼠标右键, 从其弹出来的菜单中选取Submit功能选项来将这个分析作业送进去进行分析运算.4.在roll-xpl上单击鼠标右键从其弹出来的菜单中选取Monitor功能选项来监看这个分析作业的分析过程.Visualization(可视化呈现解出来的结果)1.等这个分析成功的运算完毕,在模型树中的roll-xpl分析作业上单击鼠标右键从其弹出来的菜单中选取Results功能选项.2.画出模型的未变形与已变形形状.3.从上方的下拉菜单中选取View→ODB Display Options功能选项.4.在ODB Display Options对话框中, 选择Extra Fine的曲线精细度(curverefinement level). 单击Sweep and Extrude卷标页将显示的拉伸深度设为0.01. 单击OK 按钮.5.画出其MISES应力与塑性应变PEEQ. 其MISES应力的等值分布上彩图如图 W15–7 a 中所示.Figure W15–7a Mises stress contours.6.注意plate上表面的分析刚性面的obscures,采用下面的步骤来建rollertranslucent.A 在工具栏,单击Create Display Group工具按钮B 在Create Display Group对话框,选择Part instancesC 选择Plate-1,单击对话框底部的Save Selection As,将显示的group命名为plateD 选择Roller-1,单击对话框底部的Save Selection As,将显示的group命名为roller。