10-1.物与情报流程图 ★
精益生产-物与情报流程图

上記以外物品的置場表示。沒有順序, 上記以外物品的置場表示。沒有順序,單純 品的置場表示
為了自各生產Line的引取, 為了自各生產Line的引取,以怎樣的狀態加 各生 的引取 表示。 表示。 KANBAN順序碼關係 Lot形成 例如:排除KANBAN順序碼關係,是以Lot 例如:排除KANBAN順序碼關係,是以Lot形成 每次1 個體…etc etc。 每次1個個體 etc。 在各個線邊為了仕掛而設立的道具。 仕掛而設立的道具 在各個線邊為了仕掛而設立的道具。 內容附記) (內容附記)
引
仕
引
對象工程 前後的連結全部描繪 前後的連結全部描繪
前工程
物與情報在工 情報在工 向有流動嗎? 向有流動嗎? 的掌握。 的掌握。
生產計劃
(週/次)
生產計劃
(週 週/次)
交貨計劃
材採購看板
沖壓生產看板
熔接生產看板
素 材 店 面
物
沖壓線
料 店 面
熔接線
成 品
外包採購看板
店 面
理貨區
進料區 (本廠)
進料區 (海龍)
工作能力. 工作能力.行動
<STEP 1>
現物的事實描繪看得見的。 地現物的事實描繪看得見的。(稀少的情況
象工程的前後工程包含全部的連結捕捉。 象工程的前後工程包含全部的連結捕捉。
是前工程→對象工程→後工程進行 是前工程→對象工程→後工程進行 像這樣一直在流動
仕掛的大小工程L/T理貨場目的地方向物流…) 仕掛的大小工程L/T理貨場目的地方向物流 ) 的大小
線
熔接線
邊 店
KZ
意見=問題點 意見=問題點 找
有的姿 現有的姿態 有的
<STEP 4>
精益生产管理专有名词说明

9
精益生产
10
OEE
11
JIT
准时化(JIT-Just in time)生产。即以市场为龙头在合适的时间、生产合适的数量和高质量的产品,JIT需要以拉动生产 为基础,以平准化(Leveling System)为条件。所谓拉动生产是以看板管理为手段,采用“取料制”即后道工序根据“市 场”需要进行生产,对本工序在制品短缺的量从前道工序取相同的在制品量,从而形成全过程的拉动控制系统,绝不多生 产一件产品。 自働化是指自律地控制不正常的情况和具有人的判断力的自动化, 也就是发现异常或缺陷的装置和出现这些异常或缺陷时能够使生产线或者设备停下来的装置。 它包含了发现不合格零部件就不让该零件通过生产线的机构,因此能够达到以下效果: 因为有了自働化就无须人员去监控异常情况这样一来可以削减作业人员,从而达到降低成本的目的。 由于有生产完所需要的零部件设备就能停下来,而且生产的零部件又都是合格品,因此可以减少库存量,从而可以实现生 产同步化。 该自働化要求对设备及环境持续改善,刺激了员工的能动性,因而增强了对人格的尊重。 看板管理:又成为视板管理、看板方式、看板法等,是20世纪50年代由日本丰田汽车公司创立的一种先进的生产现场管理 方法或生产控制技术,是目视管理的重要工具。 平准化是指工件的被拉动到生产系统之前要进行人为的按照加工时间、数量、品种进行合理的搭配和排序,使拉动到生产 系统中的工件流具有加工工时上的平稳性,保证均衡生产,同时在品种和数量上实现混流加式运动,起到对市场多品种、 小批量需要的快速反应和满足功能。
15
标准作业
16 17
时间观测 工程别能力表
18
标准作业组合票
19 20 21
标准作业票 山积表 标准手持数
22
{企业管理流程图}物与情报流程图应用讲义

▲
▲▲ ▲▲
完成品放置处的在库(安全值=工程能力不足的份量)? ・・・可动率、不良、看板变动、稼动时间差等
(2) 关于生产工序的运行
*定义:用时间表示所有物与信息
⑤加工等待
④Lot形成等待 ③回收等待
②完成品在库
①加工的LT
⑧对应班差的在库 ⑦非常用在库
⑥信息变动对应在库
生产LT=①+②+③+④+⑤+⑥ + ⑦ + ⑧
(1) 通过品番表来看在哪里生产 (2) 按品番,分别用线连接各工序
〈焊接〉
工程1
〈加工〉
工程A
工程2
工程B
组装
找出决定前后工序取货量的因素 ・・・量、设备制约、品质制约(配合度差?)
⑤ 加工(生产指示)的方法
⑦ 搬运 方法
⑤ 加工 方法
④ 完成品 材料的 放置方式
焊接
组装
⑥ 工程内加工品
与周期
③ 集货 方法
⑦-3 使用工具
・叉车 or 牽引车 or 台车 or 链条
取
焊接
毎10分钟
组装
(1) 工程间搬运(部品调配)
*物流LT (用语集中无定义)
(1) 工厂内部部品的调配・・・看板周期 (2) 物流中,所有物与信息的时间表示形式
组装工厂
供应商
① 看板的 周期
(1‐4‐4)
工程
供应商
取取取货取取
②纳入时间 的变动
⑤加工等待 ④Lot形成等待 ③回收等待
LT缩短的方法
②完成品在库 ①加工的LT
⑧直班日差对 应在库
⑦非常用在库 ⑥信息变动 对应在库
① 减少标准手持量 ②取货多次化 ③ 回收的多次化
回收看板的废除 ④ 生产Lot少量化 (段取改善)・・ ⑤ 同样 ⑥ 减少取货变动 ⑦ 工程可信度向上信 ⑧ 生产能力向上
物与情报流程图

理貨 出貨場
顧客 (交貨地點)
引
1-4-4
FAX
1回/日
11
②交貨物流
③
⑤
④ 理貨的
生産指示 完成品及 做法
的方法 材料的放
置方式
顧客 ① (交貨地點)
販賣的 情報
溶接
組付
和前置時間 工程内半成品
⑥
做法 搬運的
②
①
工程3
保有庫存(店面)的方法
②
①
③ 工程2-1
工程1
工程3
工程2-2
18
④-3 有沒有在必要場所設置完成品店面?
*後工程所要的東西是否可依需要的時間領取?
(2)從前後生產線的実力差來看
④ 工程能力不足的工程
高不良率需有安心量・・・內容也要調查)
⑦
出貨場 理貨場
交貨物流
②
12
②交貨物流
②-1 理貨場、出貨場是怎麼樣的相互関係呢?
・理貨場:對受訂物品備齊1便分貨物之場所(到什麼時候?) ・出貨場:將一便已備齊之物品上貨車之場所(何時出貨?) ・理貨場和出貨場是同一個或各別的?
同樣:是否有各別建構奇数便・偶数便置場(有超過以上的情況?) 各別:有別的出貨作業指示嗎?
⑥
做法 搬運的
⑦
⑤
生産指示 的方法
④ 完成品及 材料的放 置方式
③
理貨的 做法
顧客 ① (交貨地點)
販賣的 情報
溶接
組付
出貨場 理貨場
交貨物流
②
14
③理貨的做法
③-1 是否有從生產線領取的方法
TPS物与情报流程图应用培训资料
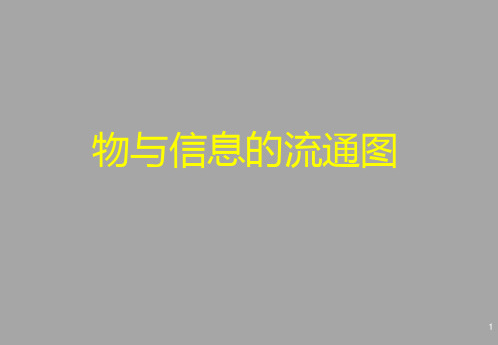
④ 工程能力较差的工程 (因不良率高,会有一些安全在库・・・也需调查 其内容) ⑤ 段取实力较差的地方 ⑤ ④ (批次生产・・・时间、次数) ⑥ 有班差的地方 工程1 工程2 (是否有在库+计划?)
⑥
工程1 <1班生产>
1班用 2班用
工程3
工程2
<2班生产>
生产形态相反的情况下也一样
28
*重要的是・・・减少看板(物与信息的停滞) 发现浪费,改善→成本低减 *生产的LT 生产线生产时,看板流转总张数所需时间 加工看板
*完成品放置处(安全值) 量产工程的LT
表示“在通常的量产状态下” 生产工程的实力值, 工程收到加工指示开始, 到完成品(一箱)完成为止的时间 对应班差的在库 看板
客户 (纳入处)
② 纳入物流
7
① 销售(发注)信息
⑦ 搬运 方法 焊接
⑤ 加工 方法 组装 ⑥ 工程内加工品 与周期
④ 完成品 材料的 放置方式
③ 集货 方法
集 货 处 出 货 处
① 销售 信息
客户 (纳入处)
② 纳入物流
8
① 销售信息
①-1 信息如何传达?
・看板或指示
取
送信
客户 (纳入处)
取
①-2 传达的频率?
5
何时(timing) 谁
单位
方法
2.现状把握方法
6
【2】 物与信息流程图的画法
用自己的眼睛现地现物地把握事实 (同时调查现状是如何形成的)
从后工序向前工序追溯
⑦ 搬运 方法 焊接
⑤ 加工 方法 组装 ⑥ 工程内加工品 与周期 ④ 完成品 材料的 放置方式
③ 集货 方法
物与情报流程图
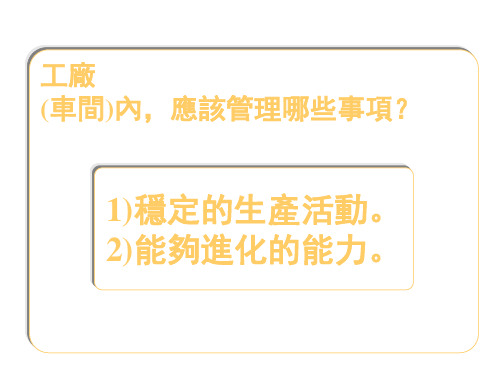
1 2 3 4
生產型號 生產數量 生產線體 產能 (工程能力表)
5
產能 (換模能力)
以公司內當下需生產的型號 各型號當下所需的數量 各工段實體線數 1)每日投入生產時間*90%=a 2)瓶頸工時的把握 3)人+機器的作業時間 1)每日投入生產時間*10%=b 2)b/換模次數=換模目標
一、應有線數、應有班次、應有產能(型號、數量)
多回運搬 2日 0H/日平均
1回/2日 2日
115.4個/人.H 182.9個/人.H 52.6個/人.H 86.3%
問題指摘+對策實施
符號認識練 習
符號認識練 習
實務操作
一、物與情報流程圖繪製 二、問題指摘 三、對策提出 四、發表
感謝聆聽
流程重組(Business Process Reengineering)
物與情報流程圖使用時機 當對客戶提供產品時,那裡就會有價值流程,此時 正是觀察並將從原料到客戶之間的整個價值流程最 佳化的時候。
透過物與情報流程圖掌握〝流動速度〞
進料
進料 倉庫
生產製造過程
製造週期時間(MCT)
成品 倉庫
出貨
多代 9品目 15288個
熱處理
洗淨 36品目 62356個 490分/1直
裝配 10品目 15360個 490分/1直 4分/回
出荷
17品目
29896個 490分/1直
2~1~1 3日
3回/1日 9日 2.3H/日平均 36.4個/人.H 72.8%
1回/3日 3日
1回/1日 3日 0/日平均
多回運搬 4H 0H/日平均
No. 調查項目 6 生產節拍(T/TIME) 7 標準工時 (ΣCT) 8 每線應配置人力 9 標準作業
Lean 02 物与情报流图

SMT發料單 Ass’y發料單
出貨 通知單
1回/日(0.5H)
Packing list & Invoice 1回/日(10`)
30日
供应商
前置时间 30日 / Lot
7日
2日
2日
IQC
处理时间 3日/ Lot
发 料
2日
35K / Lot
SMT
组 装
包 装
物流 出货 频度1回/日
1H
客戶
频率3回/周 处理时间1.5H/回
滞 査 运 工
•工程等待 •收容数等待 •批量等待 •搬运的等待 •与标准比较,正常或异常 •改变物的位置 •变形,变质,装配,分解 増加成本
增加附加价值
5
工程分析基本符号
分析记号 基 本 记 号 名 加工 量的检查 质的检查 搬运 贮藏.停滞
辅 助 记 号
称 数.量的确认 品质的确认
内
容
变质.变形.装配.分解.准备作业
引取 加工
二.物的流程调查与整理
產品類別 類別 品名 下 料 粗 磨 退 火 滾 粉 皮 膜 精粗 鍛鍛 抽 擠 T4
1 A01 A02 A03 B01 B02 C01 C02 C03 C05
1
2
1 1 1 1 1 1 1 1 1 1 1 1 1 1
3
4
2 2 3 3 2 3 3 3 3 2 3 2/4 3 3 3 2 2 2 2 2 2 2
18
物与情报流程图作成要领
一 .符号及内容完全了解 二 .情报.物的流程调查与整理 三 .流程内容调查 四 .问题点显在化;针对问题点实施改善
19
一.物与情报流程图介绍
1、目的:
系统性紧张感建立-威力0312
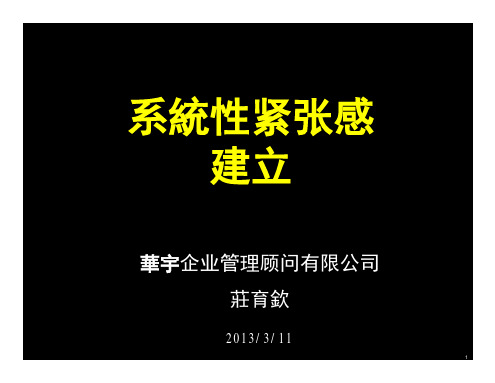
華宇企业管理顾问有限公司 莊育欽
2013/3/11
1
課程大綱
1、什么是系统性紧张感 2、如何建立紧张感? 3、緊張感的迷思 4、成功的经营模式-小批量
‧精益的本质 ‧如何推动LEAN
5、造物前先造人
‧管理、监督者的职责 ‧管理、监督者的业务
6、结论
2
系统性紧张感建立
1、什么是系统性紧张感
24
缺乏应变能力
根源于5S被误解,造成随意性与应急文化
人
问题 及异常 没有 显在化
事.物
定容、 定量、 定位、 没有做好
情报
生产 没有节奏 没有情报
改善的基础:5S的推动
25
应对变动的能力:
稳定化 物与情报的掌握 拉动化 柔性化
26
建立具有柔性能力的运营系统
n设备柔性
• 可移动 • 小设备 • 快速切换
不成長,也能獲利
在流程中,塑造穩定化系統 快 速 化 反 應 能 力
短 交 期
減 少 變 動
系 統 性 緊 張 感
柔 性 化 能 力
少 量 多 樣
少 人 化
20
精益的本质
面对多样化与多变的环境:即空的世界 无常与多变是常态:重新洗牌 应该把适应变化当成必备能力 l LEAN就是在培养这种能力 在顺应这种改变 l 这就是经营的本质:
l l
工作的基本:管理、监督者是经过部属取得成果的。 教导方法的基本:如果被教导者没有学会、即是教导 者没有教好。
*管理、监督者应了解这些基本、除努力提升个人的 潜力外、并吸取以下知识:TWI(工作教导方法) OJT (在职培训)、TPS、TPM 。
39
系统性紧张感建立
物与情报流程图(价值流)日译版

目录
• 物与情报流程图概述 • 价值流分析基础 • 物与情报流程图绘制技巧 • 价值流改进策略实施 • 物与情报流程图在供应链管理中应用 • 总结与展望
01 物与情报流程图概述
定义与目的
定义
物与情报流程图(Material and Information Flow Diagram)是一种可视化 工具,用于描述产品从原材料到最终顾客手中的整个过程中物质和信息的流动 情况。
流程图在价值流中作用
可视化生产过程
流程图将复杂的生产过程以图形化的 方式呈现出来,使得管理者能够直观 地了解生产流程。
识别浪费与瓶颈
通过流程图分析,企业可以识别出生 产过程中的浪费环节和瓶颈工序,进 而采取针对性措施进行改进。
优化生产布局
流程图有助于企业发现生产布局中的 不合理之处,通过调整布局来减少物 料搬运距离、提高生产效率。
供应链中价值流概念延伸
1 2
价值流定义
在供应链中,价值流指的是从原材料采购到最终 产品交付给客户的整个过程中所涉及的物流、信 息流和资金流。
价值流分析
通过对供应链中价值流的分析,可以识别出增值 和非增值活动,优化资源配置,提高供应链效率。
3
价值流图
价值流图是一种可视化工具,用于描述供应链中 的价值流,帮助管理者更好地理解供应链运作流 程。
评估实施效果
对优化方案进行实施并评估效果,持续改进。
标准化和固化
将优化后的流程进行标准化和固化,确保持 续改进效果。
案例分享:成功企业实践
企业A
通过绘制物与情报流程图,成功优化了生产流程,提高 了生产效率。
企业C
通过对比不同部门的流程图,实现了资源共享和协同作 业,降低了运营成本。
物与情报流程图说明
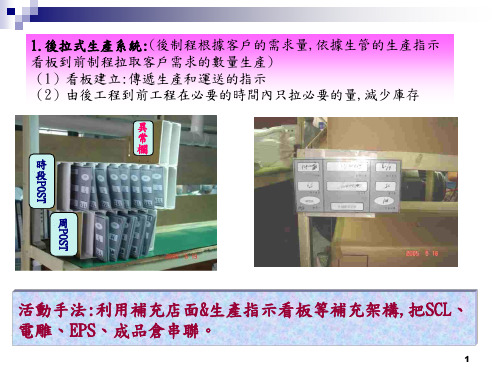
POST
1.後拉式生產:改善前之物與情報流程圖: 1.後拉式生產:改善前之物與情報流程圖: 後拉式生產 (3)了解生產環節(分歧合流點)的物流是否順暢,情報連接是否緊湊從 (3) 而分析與改善物流與情報
納入計劃
生管
業務
a
b
待 派 修 區 整
待 電 派 焊 區
待 派磨 區面
待 派電 區雕
待 E 派 P 區 S
6
1.後拉式生產系統: 1.後拉式生產系統:(後制程根據客戶的需求量,依據生管的生產指示 後拉式生產系統 看板到前制程拉取客戶需求的數量生產) (1)看板建立:傳遞生產和運送的指示 (2)由後工程到前工程在必要的時間內只拉必要的量,減少庫存
時 段 POST
活動手法:利用補充店面&生產指示看板等補充架構, SCL、 活動手法:利用補充店面&生產指示看板等補充架構,把SCL、 店面 看板等補充架構 電雕、EPS、成品倉串聯。 電雕、EPS、成品倉串聯。
成 品 倉
客 戶
4
1.後拉式生產: 1.後拉式生產: 後拉式生產 (6)改善後
納入計劃
返回
生管
業務
a
b
受 入 場
c
S C L 線電 雕E P S成 品 倉客 戶
5
1.後拉式生產: 1.後拉式生產: 後拉式生產 (6)改善後
納入計劃
返回
生管
業務
a
b
受 入 場
c
S C L 線
E P S
成 品 倉
客 戶
c
理 貨 出 貨 場
2
客 戶
1.後拉式生產: 1.後拉式生產: 後拉式生產 (4)改善中
納入計劃
2.TPS分析改善手法 - 物与情报流程图

TPS分析改善手法 - 物与情报流程图课程大纲价值流图概述•精益生产目标•价值流图源起•价值流图要素精益生产的目标•强调以小批量生产取代大批量生产,意味着以细而急的水柱取代寛而缓的流动。
•起到库存减量(减少不必要成本)与周转时间降低(快速对市场进行应变)的效果。
VSM 起源•价值流图为1998年6月由美国麻省理工学院精益企业研究所的二位研究人员所开发,在丰田系统被称为材料及信息流图析,是一种发现问题的手段。
VSM要素•物流•讯息流其它:资金流…•长江(古称江、大江,外国人多称杨子江),全长6,380公里,发源于中国青海省唐古拉山各拉丹东雪山的姜根迪如冰川中,是中国、亚洲第一和世界第三长河流(次于亚马孙河及尼罗河),其长度超过地球半径。
长江年径流量为9513亿立方米,占全中国河流年径流量的三分之一。
•从源头青海各拉丹东到湖北宜昌是为长江的上游流域;从宜昌到江西湖口则是长江的中游流域;湖口到上海的长江入海口,是为长江之下游流域。
•长江水系流域面积180万平方公里,占中国陆地面积的18.8%。
支流流域面积1万平方公里以上的支流有49条,主要有嘉陵江、汉水,岷江、雅砻江、湘江、沅江、乌江、赣江、资水和沱江;•主要湖泊有洞庭湖、鄱阳湖、太湖、梁子湖、巢湖和洪湖等长江三峡位于重庆市和湖北省境内的长江干流上,西起重庆市奉节县的白帝城,东至湖北省宜昌市的南津关,全长193公里,由瞿塘峡、巫峡、西陵峡组成。
「两岸猿声啼不住,轻舟已过万重山」 四川省都江堰市城西,岷江上游340千米处。
江堰是由战国时秦国蜀郡太守李冰及其子于约前256年至前251年主持始建的。
经过历代整修,两千年多来都江堰一直在发挥巨大的作用。
兼有防洪排沙、水运、城市供水等综合效用。
它所灌溉的成都平原是闻名天下的「天府之国」。
北部为高原浅谷区,高原面高程在4500-5000米。
原面上河谷在近期仍有强烈活动。
沿江大的活动断裂带常有地震发生。
荆江指湖北省枝江到湖南省洞庭湖口城陵矶一段长江的别称。
发现可疑物品应急预案及处置流程图

发现可疑物品应急预案及处置流程图
小区发现可疑物品时
一、发现者不准触摸或搬动,应立即向值班领导及项目部领导报告,并留守现场,指导业主或行人远离该处,禁止吸烟或动明火,阻止他人接触或靠近可疑物。
二、值班领导和护卫队速到现场了解情况,如观察可疑物品可能为危险品或爆炸品时,要立即打110报警,按照火警紧急疏散路线疏散附近区域的人员,设置临时警戒线,阻止人员入内,并向公司领导报告。
三、护卫队领导立即通知中控室加强对小区的观察,队员阻止任何人员进入,所有电梯暂停使用,对附近区域进行全面搜寻,寻找可疑人员和其他可疑情况。
四、警方人员到现场后,护卫队要主动配合消除爆炸危险隐患,并积极协助进行调查,同时做好认真的记录。
五、如果可疑物品已经造成人员伤害(如爆炸、毒气扩散等),护卫队要立即打120,并调护卫队员到现场协助抢救,转运伤员,并注意自身的防护;管家(物业)部要安置疏散人员,稳定人员情绪,并协助保护现场。
三十一、公共突发事件(发现可疑物品)处置流程图。
城市突发事件应急处置流程图

城市突发事件应急处置流程图概述该流程图旨在指导城市突发事件的应急处置过程,确保及时、有效地处理各类紧急情况。
流程图包括了事件发生、应急响应、资源调配、协同合作等环节。
流程图graph LRA{事件发生} -- 确认事件类型 --> B[紧急级别评估]B -- 高级别 --> C[启动应急响应]C -- 高级别 --> D[组织应急小组]D -- 低级别 --> E[调配资源]D -- 高级别 --> F[成立指挥部]E --> FF -- 高级别 --> G[情报搜集与分析]G --> H[制定应急处置方案]H --> I[资源调配]I --> J[任务执行]J --> K[定期汇报进展]K --> L[评估与总结]L --> M{完成}流程解析1. 事件发生后,需确认事件类型,以便后续的处置工作。
2. 确认事件的紧急级别,包括高、中、低级别,以便分配相应的资源和采取相应的处置措施。
3. 高级别紧急事件需要启动应急响应,包括组织应急小组和成立指挥部。
4. 组织应急小组是为了协调和管理各方面的应急工作,确保资源调配和任务执行的顺利进行。
5. 低级别紧急事件不需要成立指挥部,但仍需进行资源调配。
6. 情报搜集与分析是为了更好地了解事件的背景和情况,为后续的应急处置方案制定提供依据。
7. 制定应急处置方案是为了明确每个环节的具体步骤和责任,并确保任务的高效执行。
8. 资源调配涉及将所需的人力、物力、财力等资源调配到相应的地点,以支持应急处置工作。
9. 任务执行是根据应急处置方案,按照各自的职责积极参与应急工作。
10. 定期汇报进展是为了及时了解处置工作的进展和问题,以便进行调整和协调。
11. 评估与总结是在事件处理完成后进行的,目的是为了总结经验教训,提升应急处置能力。
12. 完成所有的应急处置工作后,流程结束。
结论该流程图为城市突发事件的应急处置提供了一套清晰的指导流程,有助于各部门在突发事件发生时快速、有序地开展应急工作,提高应对突发事件的效率和能力。
精益价值流—价值

价值流改进重点在于物流和信息流。精益生产中,信息流被视为与物流一样重要。考虑怎样流 动信息才能使一个工序仅仅生产出为下一道工序所需要的物料,而且是在需要的时候进行生产。
价值流程图概念
价值流程图(Value Stream Mapping):通过用特 定的图标将整个价值流的过程绘制出来,使价值 流目视化的工具,包括物流、信息流和过程流。
C、绘制发货与收货信息。在客户图标下画出卡车图标, 填上发货的频率,箭线指向客户。在供应商图标的下 方画一个卡车图标,填上送货的频率,箭线指向价值 流最上游。
C、绘制发货与收货信息。在客户图标下画出卡 车图标,填上发货的频率,箭线指向客户。在 供应商图标的下方画一个卡车图标,填上送货 的频率,箭线指向价值流最上游。
是一种系统改善信息流程、实物流程的方法。
供应商
工序C
信息控制
工序B
客户
工序A
理解流程…看到价值…憧憬未来状态
价值流程图的发展
起源于1980s的TOYOTA, “物与情报流程图”
大野耐一(Taiichi Ohno )
新乡重夫(Shigeo Shingo)
随着1998年美国Mike Rother & John Shook的著作《学习如何看:价值流程 图创造价值和消除浪费》而风靡全球。
“Whenever there is a product for a customer, there is a value stream. The challenge lies in seeing it.”
价值流程图的作用
识别浪费的工具,发现浪费的根源。
改善沟通的工具。用价值流图可反映各项作业怎样与生产控制中 心沟通信息;各项作业之间怎样沟通信息。
- 1、下载文档前请自行甄别文档内容的完整性,平台不提供额外的编辑、内容补充、找答案等附加服务。
- 2、"仅部分预览"的文档,不可在线预览部分如存在完整性等问题,可反馈申请退款(可完整预览的文档不适用该条件!)。
- 3、如文档侵犯您的权益,请联系客服反馈,我们会尽快为您处理(人工客服工作时间:9:00-18:30)。
Y 社 1-2-2
周期7H
輔助
B前工程
1夜班
B社 1-8-4
2夜班
指示書
指示 書
1.8日
C社 1-2-4 1 1夜班
1.5 日 組装線 1夜 班 0.7日
0.4日
D社 1-4-2
生產指示 平準化 水平低
Z 社 1便
C前工程
週期 12H 2夜班 3.0日 4次/D 定時運搬
生產指示沒有一元化 (看板一指示)
內容 工程間看板 H ö Ô Å Â 附記拿取時間
L s ³ m Ô
參考
¼ Ì
內容
「物與情報流程圖」記號
¼ Ì
名稱 看板(e)
名稱 看板(d)
其他道具
Å Â i S j
Å Â i T j
¼ Ì à e
名稱 名牌
週期12H 2夜班
指示 書
1.5日
3.0日
1次/H 定時運搬
1夜班
0.7日
庫存量
1. 填寫生產線,客戶,供應商 2. 填寫物的放置地點(店面,臨時放置場等) 3. 填寫物的流程
4. 填寫搬運的方法,時間 5. 填寫生產指示,情報的流程 6. 填寫在庫量,前置時間,生產形態等
物與情報流程圖
工 供貨點 程 名
物與情報流程圖
生產管理部 生產調查
所謂物與情報流程圖
.透視由供貨點到交貨點物與情報的流程之實態示意圖
記載內容
物品流動 搬運方法 庫存量 生產指示 前置時間
Y社 1-2-2
圖例
工 程 名
物與情報流程圖
供貨點 前工程
批量形成 POST
組裝
物的流程 情報流程 資物備齊
加工 看板
平準化 POST
交貨點
看板受領 POST
X社
1-1-2
A前工程
1班 信號 看板 1.5日
領取 看板
A社
1-12-5
組裝生產線
1班 店面 0.4日 B社 出 貨 區
1-8-4
B前工程
2班 1.8日
組裝 生產線
讓生產線本身 發現不了的 浪費顯現
指示書
指示書
輔 助
1班 1.5日 組裝 生產線 1班
0.4日
C社
1-2-4
Z社 1便
C前工程
2班 3.0日 1次/H 定時搬運
始作 看板 摘取 看板 0.5日 1次/H
理貨
交貨點
仔細調查 發現的問題點
生產線沒有 整流化
批量形成收容器
搬運次數多
平均化 収容架
1次/H 16分割 領取
看板 到達収容架
A社 1-12-5
X 社 1-1-2
周期 6H 1夜班 信号 看板
A前工程
不了解 各線上 的進度
組裝生產線
周期 3H 倉庫 0.4日
X社 1-1-2
前工程
批量形成收容架
組裝
始作 看板 摘出 看板 0.5日 1次/H
貨物備齊 交貨點
平準化 收容架 1次/H16分割 領取 看板 到達收容架 A社 1-12-5 B社 1-8-4 C社 1-2-4 0.4日 D社 1-4-2
A前工程
週期6H 1直
組裝生產線
週期3H 1夜班
組裝線 輔 助
¼ Ì
名稱 出貨區 Ý _ ¼ Ì
¼ Ì名稱 看板(a) Å Â i 1 j à e
內容 領取看板 E o Å Â 附記看板循環週期
看板(b) ¼ Ì 名稱 Å Â i 2 j
名稱 看板(c) 內容 信號看板 附記批量與基準數
à e
內容 上述以外之 post L ã q È O û e 附記使用目的、 Ë I g p Ú I A g p 使用方法
û @
tth1128@
Y社 1-2-2
B前工程
週期7H
2夜班
信号 看板
. 理 貨 的 起 伏
倉庫 0.4日
1.8日
1夜班
組裝線
著 眼 於 平 準 化 理 貨
. 交 貨 時 間 表
Z社 1便
指示 書
C前工程
週期12H 2夜班
指示 書
1.5日
3.0日
1次/H 定時運搬
1夜班
0.7日
著眼於工程的流程
・流程交錯進行 ・進出其他工場
內容
Á v
¼ Ì à e
名稱 指示 w ¦
內容 指示領取和始作 w ¦ Ì æ a n ì 使用情報(表單) g p î ñ i \ P j w ¦ I Ô L i p ¦ A Ô A Ê j 時指示的時間 附記(頻率、時間、量)
¼ Ì 內容 記入物的流程 ¨ i ¬ ö à e
附記搬運方法、 L ü ¨ I ¬ ö 頻率、時間
¼ Ì 內容 î ñ ¬ ö 從領取或產生加工 à e
情報的場所到使用 A Ú ¸ Ì æ ½ ¬ o n ì 的場所之連接 î ñ I ê g p î ñ
內容 平準化POST ½ Ï » û e Ë à e 附記交貨時間表、理貨、 L ð Ý Ô \ A Ý ¨ Wã Ú E 出貨相關 Ý Ô I Ö A
Ò L Y Á
名稱 看板POST(c) Å Â û e Ë ( R j 內容 批量形成 post á Ê ` ¬ û e Ë 附記批量大小及其他 à e L á Ê Ú ¡ y ´ ¼
前工程
批量形成收容架
組裝
始作 看板 摘出 看板 0.5日 1次/H
交貨點 供貨點
A前工程
週期6H 1直
生產線
生產指示 情報流程
組裝生產線
週期3H 1夜班
組裝線 輔 助
Y社 1-2-2
B前工程
週期7H
2夜班
信号 看板
倉庫 0.4日
1.8日
1夜班
組裝線
物的流動
搬運方法 前置時間
Z社 1便
指示 書
C前工程
¼ Ì
內容
名稱
其他
´ ¼
¼ Ì
名稱 看板POST(a)
Å Â û e Ë ( P)
名稱 看板POST(b) 內容 pattern 加工 post 附記 pattern 的週期、 順序及限制條件
領取加工之上述以外的情報 Ì æ ¤ n ì ã q È O I î ñ à e (電話的CRT表示等) i d I b q s \ ¦ j 情報的時間 î ñ I Ô 附記(頻率、時間、量) L i p ¦ A Ô A Ê j
名稱 店面
¼ O à e
內容
q É 生產線成品放置場所 記入品番數、最大庫存量、 ¶ Y ü ¬ i ú u ê 領取時間等 L ü i Ô A Å å É Ê A Ì æ Ô
名稱 ¼ Ì
內容
臨時放置
Õ u ú i 1 j
à e
店面不同、確保先入先出 、並依照順序排放貨物 ^ q É s ¯ A mÛ æ ü 的放置場 æ o AÆ
Í ú Ý ¨ I u ê
名稱 臨時放置(b) Õ ú u i 2 j 內容 顯示物品積存顯示 ° ¦ ¨ i Ï ¶ 庫存量、品番數、 à e ° ¦ Ý ¶ Ê A i Ô A 領取時間 Ì æ Ô
¼ Ì 內容 記入工程名、 ¶ Y ü à e
前置時間、稼動時間
L À ^ è i A p ¦ A Ô
L ü H ö ¼ A ü ú A L ø H ì Ô
名稱 內容
工場 客戶名稱、 記入看板循環週期
à e
內容
顯示出貨區場所附記 °¦ Ý _ I ê 理貨時間、出貨時間、 L Ý ¨ Wã Ú Ô A Ý 交貨車便時間表相關 Ô A ð Ý Ô \ I Ö A
à e
L Å Â z Â
著眼於物品積存
・庫存量、工程間的積存 ・有無臨時放置
著眼於搬運
・搬運次數 ・搬運規則
著眼於生產形態
・有無班數差異 ・稼動時間差(加班多少)
著眼於製造
・批量大小,可動率,不良率 ・生產週期
著眼於情報的流程
・生產指示方法 ・平準化水準
例
工 供貨點 程 名
從圖中了解 的問題點
物與情報流程圖
前工程 組裝
組裝、前工程 有班次差異
D社 0.7日
1-4-2
問題點 流程複雜 【例】
生產線
生產線 生產線
生產線
流程的整流化
生產線 生產線
生產線 生產線 生產線
搬運的浪費
生產線
生產線 生產線
同期化
生產線
生產線
生產線 生產線 生產線 生產線
遠
生產線
近、效率好
物與情報流程圖
工 供貨點 程 名
X社 1-1-2
記載內容
貨物備齊 交貨點
平準化 收容架 1次/H16分割 領取 看板 到達收容架 A社 1-12-5 B社 1-8-4 C社 1-2-4 0.4日 D社 1-4-2
¼ Ì
名稱 POST ¼ Ì 看板 Å Â û(d) e Ë (4) 內容 看板滑架 à e Å Â ¹