轴承钢管生产工艺
钢管分类大全 钢管生产工艺大全

钢管分类大全钢管生产工艺大全钢管分类大全钢管生产工艺大全钢管分类大全.钢管生产工艺大全钢管按生产方法可以分成两大类:无缝钢管和存有缠钢管。
1.无缝钢管按生产方法可分为:热轧无缝管、冷拔管、精密钢管、热扩管、冷旋压管和挤压管等。
无缝钢管用优质碳素钢或合金钢做成,存有钢材、钢(忽)之分后。
2.焊接钢管因其焊接工艺不同而分为炉焊管、电焊(电阻焊)管和自动电弧焊管,因其焊接形式的不同分为直缝焊管和螺旋焊管两种,因其端部形状又分为圆形焊管和异型(方、扁等)焊管。
冲压钢管就是由卷曲管形的钢板以对缝或螺旋缠冲压而变成,在生产方法上,又分成扰动流体运送用冲压钢管、螺旋缠电焊钢管、轻易卷焊接钢管、电焊管及等。
无缝钢管可以用作各种行业的液体气压管道和气体管道等。
冲压管道可以用作输水管道、煤气管道、暖气管道、电器管道等。
钢管按制管材质(即钢种)可分为:碳素管和合金管、不锈钢管等。
碳素管及又可以分成普通碳素钢管及和优质碳素结构管。
合金管又可分为:低合金管、合金结构管、高合金管、高强度管。
轴承管、耐热耐酸不锈管、精密合金(如可伐合金)管以及高温合金管等。
按相连接方式分类钢管按管端联接方式可分为:光管(管端不带螺纹)和车丝管(管端带有螺纹)。
车丝管又分为:普通车丝管和管端加厚车丝管。
加厚车丝管还可以分成:外加厚(拎外螺纹)、内加厚(拎内螺纹)和内外加厚(拎内外螺纹)等地车丝管。
车丝管若按螺纹型式也可分为:普通圆柱或圆锥螺纹和特殊螺纹等地车丝管。
另外,根据用户需要,车丝管一般均配有管接头交货。
按镀涂特征分类钢管按表面镀涂特征可分为:黑管(不镀涂)和镀涂层管。
镀层管存有镀锌管、镀铝管、镀铬管、滤渣铝管以及其他合金层得钢管。
涂层管有外涂层管、内涂层管、内外涂层管。
通常采用的涂料有塑料、环氧树脂、煤焦油环氧树脂以及各种玻璃型的防腐涂层料。
镀锌管又分为kbg管,jdg管,螺纹管等不锈钢管分类按生产方式分类不锈钢管按生产方式分为无缝管和焊管两大类,无缝钢管又可分为热轧管,冷轧管、冷拔管和挤压管等,冷拔、冷轧是钢管的二次加工;焊管分为直缝焊管和螺旋焊管等。
轴承制造专业术语

气体环境: 一个有限的空间如熔炉里的空气的组成成分。
ATMOSPHERE CONTROLLED FURNACE: Furnace which uses endothermic base atmosphere
which is formed by the partial reaction of a mixture of fuel, gas, and air in an
80% ANNEAL: Tempering operation; process of heating product to remove hydrogen
from railroad product so the product does not crack.
80% 退火:回火操作;加热去氢以达到用于铁路的产品不易碎裂的目的。
the production of high quality alloy steel.
合金钢:指钢中含有铁,碳,以及镍、铬、钼等一种或多种其他的合金元素。Timken 公司是全球领先的高质量合金钢的生产商。
AMERICAN NATIONAL STANDARDS INSTITUTE - ANSI: An agency that develops standards
tempering or stabilizing process. (Also called Shotblasting)
磨料喷砂法:热处理之后磨削之前去除产品表面氧化皮的工序;把工件放进滚筒里,用高速金属磨料喷击表面。这道工序也起到回火或退火处理的作用。(也叫喷丸处理)
ABRASIVE WEARING: Damage to bearing parts caused by fine foreign particles which
GCr15轴承钢管快速球化退火工艺研究

编号 为 K1 K , , 9 , 2 … K 。其 主 要化 学 成分 ( 量百 分 质
含 量 ) 别 为 W( ) 09 % , Mn= . % , S) 分 C = .9 W( ) 03 0 W(i=
0 1 %, ( r 1 4 .9 w C) . %。 =4
间 长 达 l~ 8 。 2 1h
在不 改 变 工艺 流 程 的情 况 下 , 热 轧穿 孔后 的 对
年 快 速球 化退 火工 艺成 为研 究 的热点 。
毛管 进 行取 样 。任 意抽 取 一 根 穿孑 后 雾冷 的毛管 . L 其 规格  ̄4 mmx m 距 毛 管 端 部 2 0 1 4 m, 0 mm 处 , 砂 用
基 金 项 目 : 庆 科 技 学 院 横 向科 研 项 目( 1— 0 )重 庆 科 技 学 院 大 学生 科 技 创 新 项 目 重 19 0 1 ; 作 者 简 介 : 蜀 焱 (9 3 )男 , 川南 部 人 , 士 , 师 , 任 17 一 , 四 硕 讲 研究 方 向 为材 料 加 工 。
铁 素 体 通 过 碳 的扩 散 向奥 氏体 基 体 生 长 形 成 等 轴 状 晶粒 。 因此 , 现 离 异 共 析 转 变 的 关 键 是 在 基 体 实 中保 持 足 够 的 弥 散 的未 溶 碳 化 物粒 子 作 为后 续 的
8 0C;保 温 1 ~ 0 n后 随 炉 冷 10 i ,冷 却 到 1 ̄ 0 2 mi 2 mn
摘
要 : 据快 速球 化 退 火 原 理 , 生 产现 场切 取 G r5轴 承 钢 管 试 样 , 照 不 同 的 快 速 球化 退 火 方 案 试 验 。 察 其 根 从 Cl 按 观
轴承钢的冶炼
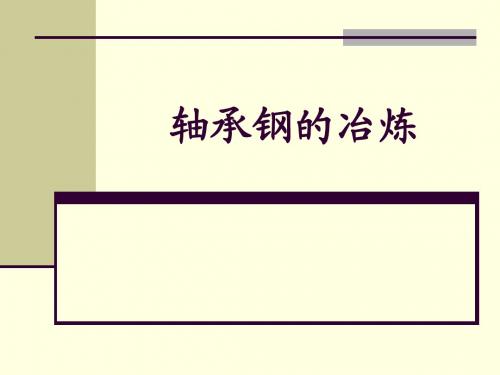
于废钢;
采用铁水预处理,进一步提高铁水的纯净度; 转炉终点碳控制水平高,钢渣反应比电炉更趋
于平衡;
转炉钢气体含量低;
连铸和炉外精炼和工艺水平与电炉相当。
日本和德国采用不同的生产工艺,区别——炼
钢终点碳的控制;
日本——“三脱”预处理,少渣冶炼高碳钢技
大容量初炼炉,保证钢水低磷,成份温度合格,
实现无渣出钢;
具备加热、真空、合金微调的精炼装置,最大限
度脱除氧、氢等气体。保护浇铸防二次氧化;
采用多极组合电磁搅拌和轻压下技术,保证钢坯
的中心质量,减少中心偏析;
轧机均为无扭无张力高速轧机轧制,保证轧材尺
寸精度和表面质量。
国产轴承钢精炼比已经达到 100% ,平均氧含
调整钢液成分、调整精炼渣成分、吹氩搅拌;
快速造碱性渣——脱氧脱硫;
底吹氩控制 —— 过大,钢渣反应过分激烈和钢液
对耐火材料冲刷严重,氧化物和钛化物进入钢液; 过小钢液温度、成分以及钢渣反应都不均匀,不
充分,脱氧产物不能充分上浮;
合适的底吹氩制度:精炼前期以较大的氩气压力
搅拌;后期以较小的氩气压力搅拌 ——使钛含量
/模铸(410mm×560mm),棒线材;
日本新日铁:高炉——转炉——LD转炉——LF
钢包精炼——RH——连铸,生产Ø19-120mm棒 线材;
日本爱知制钢:EAF——钢包精炼——RH——
连铸,生产Ø16-100mm棒线材;
德国克虏伯:110t UHP- EAF——钢包冶金——
连铸(6流260mm×330mm),生产Ø28-80mm
浇注过程中夹杂物的控制
常见汽车级机床用零件机加热处理工艺路线
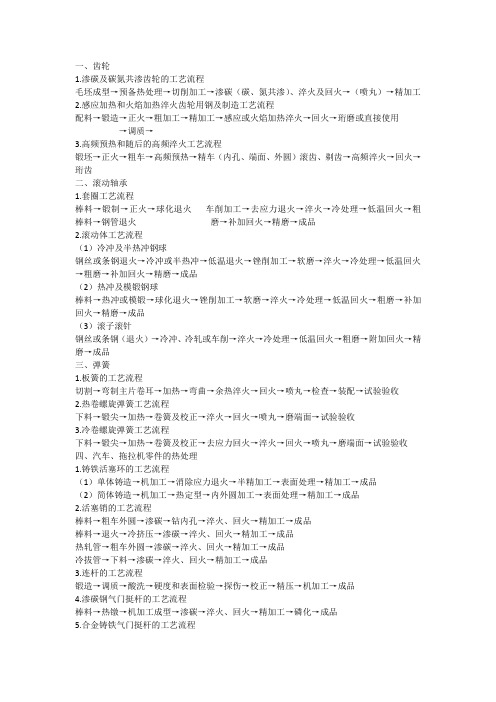
一、齿轮1.渗碳及碳氮共渗齿轮的工艺流程毛坯成型→预备热处理→切削加工→渗碳(碳、氮共渗)、淬火及回火→(喷丸)→精加工2.感应加热和火焰加热淬火齿轮用钢及制造工艺流程配料→锻造→正火→粗加工→精加工→感应或火焰加热淬火→回火→珩磨或直接使用→调质→3.高频预热和随后的高频淬火工艺流程锻坯→正火→粗车→高频预热→精车(内孔、端面、外圆)滚齿、剃齿→高频淬火→回火→珩齿二、滚动轴承1.套圈工艺流程棒料→锻制→正火→球化退火车削加工→去应力退火→淬火→冷处理→低温回火→粗棒料→钢管退火磨→补加回火→精磨→成品2.滚动体工艺流程(1)冷冲及半热冲钢球钢丝或条钢退火→冷冲或半热冲→低温退火→锉削加工→软磨→淬火→冷处理→低温回火→粗磨→补加回火→精磨→成品(2)热冲及模锻钢球棒料→热冲或模锻→球化退火→锉削加工→软磨→淬火→冷处理→低温回火→粗磨→补加回火→精磨→成品(3)滚子滚针钢丝或条钢(退火)→冷冲、冷轧或车削→淬火→冷处理→低温回火→粗磨→附加回火→精磨→成品三、弹簧1.板簧的工艺流程切割→弯制主片卷耳→加热→弯曲→余热淬火→回火→喷丸→检查→装配→试验验收2.热卷螺旋弹簧工艺流程下料→锻尖→加热→卷簧及校正→淬火→回火→喷丸→磨端面→试验验收3.冷卷螺旋弹簧工艺流程下料→锻尖→加热→卷簧及校正→去应力回火→淬火→回火→喷丸→磨端面→试验验收四、汽车、拖拉机零件的热处理1.铸铁活塞环的工艺流程(1)单体铸造→机加工→消除应力退火→半精加工→表面处理→精加工→成品(2)简体铸造→机加工→热定型→内外圆加工→表面处理→精加工→成品2.活塞销的工艺流程棒料→粗车外圆→渗碳→钻内孔→淬火、回火→精加工→成品棒料→退火→冷挤压→渗碳→淬火、回火→精加工→成品热轧管→粗车外圆→渗碳→淬火、回火→精加工→成品冷拔管→下料→渗碳→淬火、回火→精加工→成品3.连杆的工艺流程锻造→调质→酸洗→硬度和表面检验→探伤→校正→精压→机加工→成品4.渗碳钢气门挺杆的工艺流程棒料→热镦→机加工成型→渗碳→淬火、回火→精加工→磷化→成品5.合金铸铁气门挺杆的工艺流程合金铸铁整体铸造(间接端部冷激)→机械加工→淬火、回火→精加工→表面处理→成品合金铸铁整体铸造(端部冷激)→机械加工→消除应力退火→精加工→表面处理→成品钢制杆体→堆焊端部(冷激)→回火→精加工→成品钢制杆体→对焊→热处理→精加工→表面处理→成品6.马氏体型耐热钢排气阀的工艺流程马氏体耐热钢棒料→锻造成型→调质→校直→机加工→尾部淬火→抛光→成品7.半马氏体半奥氏体型耐热钢(Gr13Ni7Si2)排气阀的工艺流程棒料→顶锻→精压→热处理→精加工→成品8.奥氏体耐热钢排气阀的工艺流程棒料→顶锻→精压→阀面和尾部堆焊耐热合金→热处理→杆部滚压或软氮化→精加工→成品9.半轴调质的工艺流程合金结构钢棒料→锻造成形→正火或退火→机械加工→调质→校直→精加工→成品10.半轴的表面淬火的工艺流程棒料→锻造成形→预先热处理→校直→机械加工→表面淬火→校直→精加工→成品11.柱塞副和喷油嘴偶件的工艺流程热扎退火棒料→自动机加工成型→热处理→精加工→时效→成品12.拖拉机履带板(1)40SiMn2履带板的热处理热轧成形→下料→机加工→热处理→成品(2)ZGMn13履带板的热处理铸造成型→热处理→成品五、金属切削机床零件的热处理1.机床导轨(1)MM7125平面磨床立柱镶钢导轨锻造→正火→机加工→消除应力退火→机加工→淬火→回火→磨(2)M9025工具曲线磨床镶钢导轨锻造→退火→机加工→淬火→回火→磨(3)S788轴承磨床镶钢导轨机加工→消除应力退火→机加工→渗碳→淬火→回火→磨→时效(4)MZ208轴承磨床镶钢导轨锻造→退火→机加工→消除应力退火→机加工→淬火→冰冷处理→回火→磨→时效2.机床主轴(1)CA6104车窗主轴(45钢)下料→粗加工→正火→机加工→高频淬火→回火→磨(2)T68、T611镗床的镗杆及MGB132磨床的主轴(35CrMoAlA钢)下料→粗车→调质→精车→消除应力处理→粗磨→渗氮→粗磨(3)SGC630精密丝杠车床主轴(12CrNi3A)锻造→正火→机加工→渗碳→正火→校直→消除应力→机加工→头部淬火→颈部淬火→回火→磨→时效(4)X62W万能升降台铣床主轴(球墨铸铁QT60-2)铸造→机加工→淬火→回火(5)M1040无心磨床主轴(球墨铸铁QT60-2)铸造→机加工→正火→机加工3.丝杠(1)7级或7级精度一下的一般丝杠(45钢)下料→正火或调质→校直→消除应力处理→机加工(2)6级或6级以上精密不淬硬丝杠(T10或T12钢)球化退火→机加工→消除应力处理→机加工→时效→精加工(3)中大型精密淬硬丝杠(CrWMn)锻造→球化退火→机加工→消除应力→机加工→消除应力→机加工→淬火、回火→冰冷处理→回火→探伤→机加工→时效→精加工→时效→精加工(4)中小型精密淬硬丝杠(9Mn2V)锻造→球化退火→机加工→消除应力→机加工→淬硬淬火→回火→冰冷处理→回火、探伤→机加工→时效→精加工→时效→精加工(5)滚珠丝杠(GCr15,GCr15SiMn)4.弹簧卡头(1)卧式多轴自动车床夹料卡头(9SiCr)锻造→退火→机加工→淬火→回火→机加工→磨开口→胀大定型(2)卧式多轴自动车床送料卡头(T8A钢)锻造→退火→机加工→淬火→回火→磨(3)仪表机床小型专用卡头(60Si2)退火→机加工→淬火→回火→磨(4)磨阀辨机床专用卡头(65Mn)锻造→正火→高温→回火→机加工→淬火→回火→机加工5.摩擦片(1)X62W万能升降台铣床摩擦片(A3)机加工→渗碳→淬火→回火→机加工→回火(2)DLMO电磁离合器摩擦片(65Mn)冲片→淬火→回火→磨(3)电磁离合器摩擦片(6SiMnV)锻造→退火→切片→淬火→回火→磨6.FW250万能分度头主轴(45)锻造→正火→机加工→淬火→回火→机加工7.万能分度头蜗杆(20Cr)正火→机加工→渗碳→机加工→淬火→回火→机加工8.三爪卡盘卡爪(45)正火→机加工→淬火→回火→高频淬火→回火→法蓝→磨加工9.三爪卡盘丝(45)锻造→正火→机加工→淬火→回火→法蓝→磨六、活塞1.20CrMnMo钢制活塞的热处理锻造→正火→检验→机加工→渗碳→检验→正火→淬火→清洗→回火→检验→喷砂→磨削2.钒钢活塞的热处理下料→锻造→检验→预先淬火→球化退火→检验→机加工→淬火→回火→检验→磨削七、凿岩机钎尾锻造→退火→检验→渗碳→检验→淬火→回火→清洗→检验→磨削。
轴类零件加工工艺
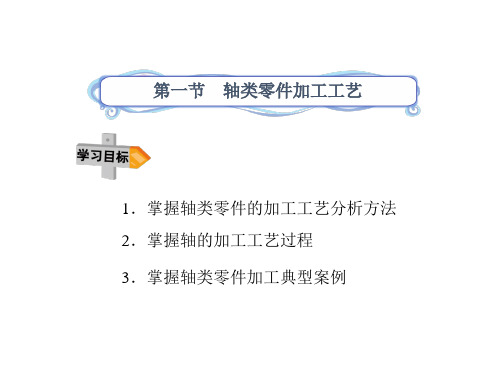
• 一、箱体零件的功用、结构及技术要求
1.功用、结构
功用:将机器中有关部件的轴、套、齿轮等相关零件连接成 一个整体,使这些零件保持正确的相对位置,并按一定的传动关 系协调地工作。
结构:形状复杂,壁薄且不均匀,内部呈腔形,既有精度要求 较高的孔系和平面,也有许多精度要求较低的紧固孔。
a)
b)
a)齿轮油泵箱体 b)齿轮减速箱箱体
Hale Waihona Puke 2.防止套类零件变形的工艺措施套类零件一般都存在壁较薄、径向刚度较差、容易变形等缺点。
套类零件变形的原因及工艺措施
导致变形的因素
工艺措施
夹紧力
(1)使夹紧力均匀分布,如图a所示 (2)变径向夹紧为轴向夹紧,如图b所示 (3)增加套筒毛坯的刚度,如图c所示
外力
切削力
重力 离心力
(1)增大刀具的主偏角 (2)内、外表面同时加工,如图c所示 (3)粗、精加工分开进行 增加辅助支承 配重
套类零件的毛坯类型与所用材料、结构形状和尺寸大小有关, 常采用型材、锻件或铸件。
毛坯内孔直径小于φ20mm时大多选用棒料,孔径较大、长度 较长的零件常用无缝钢管或带孔的铸、锻件。
• 三、套类零件的加工工艺分析
1.保证相互位置精度的工艺措施
轴承套毛坯采用“4件合一”的方 式加工:指棒料按四个轴承套零件尺 寸下料,四件同时加工
传动轴是轴类零件中使 用最多、结构最为典型的一 种阶梯轴,所示。该轴为小 批量生产,材料选择45钢, 淬火硬度40~45HRC。试分 析其加工工艺过程。
1.结构分析
主要结构要素有内外圆柱面、螺纹、键槽等,该轴为典型的 阶梯轴结构,有两个支承轴颈。
2.技术要求
两端轴颈的尺寸精度为IT7,表面粗糙度Ra值为0.8μm; 用于安装齿轮的轴颈的尺寸精度主IT7,表面粗糙度Ra值为 1.6μm; 右端轴颈外圆上规定了圆柱度为0.02mm; 左端轴颈外圆上规定了圆柱度为0.02mm; 轴上各配合面对两端轴颈的公共轴线的径向跳动为0.02mm, 可保证齿轮平稳传动。
钢管加工工艺
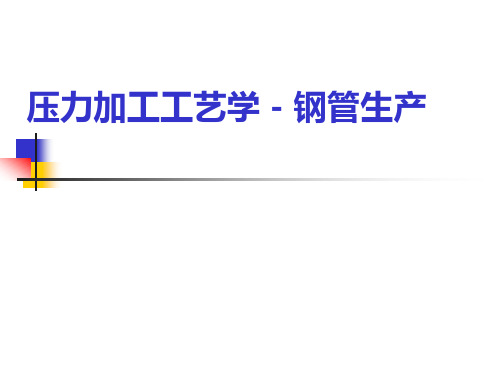
热轧无缝管:实心管坯→穿孔→延伸 →定(减)径→冷却→精整。
焊管:板带坯料→成型(管筒状) →焊 接成管→精整。
1.3 钢管的技术要求与发展趋势
⑴ 对多种腐蚀介质的高抗蚀性、对高温强度 和低温韧性的要求越来越高,使得管材产品的 化学成分不断变化,冶炼、加工工艺不断改进;
⑵ 管材产品尺寸(壁厚精度)、形状精度的要 求促使在线检测、自动控制技术不断进步;
(2)做结构件:在同样重量下,钢管相 对于其他钢材具有更大的截面模数,也 就是说它具有更大的抗弯、抗扭能力, 属于经济断面钢材、高效钢材。
二、钢管的分类
1 按生产方式分类
(1)热加工管(无缝钢管):热轧穿孔、 挤压、P.P.M(压力穿孔)、冲压法;
(2)焊管(有缝钢管):包括直缝钢管 与螺旋焊管;
压力加工工艺学-钢管生产
1 概述
1.1 钢管的特性与分类: 一、钢管的概念与用途 钢管的概念:凡是两端开口并具有中空封 闭型断面,且长度与断面周长成较大比例 的钢材,统称为钢管。而比值较小的钢材 称为管段或管件。
钢管的用途:
(1)输送流体:具有封闭的中空几何形 状,可以作为液、气体及固体的输送管 道;
(4)加热温度考虑工艺条件
a)GCr15 1%C(高碳钢),1.5%Cr(硬、耐磨),在 允许温度范围内取下限,防止脱碳;
b)硅钢希望脱碳,加热温度可提高;
(1)连铸圆坯:是目前国际上应用较多的坯料,也是衡量一 个国家钢管生产技术水平的标志之一。其具有成本低、 能耗少、组织性能稳定等特点,是管坯发展的主流,也 是钢管实现连轧的首要条件。
(2)轧坯:一般为圆坯,生产中也经常使用。 (3)铸(锭)坯:主要有方(锭)坯,用于P.P.M轧制方式(或压
力穿孔)。 (4)锻坯:用于穿孔性能较差的合金钢与高合金钢管的生产。
钢管生产流程

钢管生产流程
钢管是一种常见的金属制品,广泛应用于建筑、机械、化工等
领域。
它的生产流程经过多道工序,需要经过严格的控制和监测,
以确保产品质量和性能。
下面将介绍钢管的生产流程。
首先,钢管的生产通常以原材料的准备开始。
原材料主要包括
钢板、钢坯等。
这些原材料需要经过切割、热处理等工艺,以满足
后续生产的要求。
接下来是钢管的成型工艺。
成型工艺通常分为冷拔和热轧两种
方式。
冷拔是将钢坯通过模具冷变形成型,适用于生产精密钢管;
热轧则是将钢坯加热至一定温度后通过轧制机械成型,适用于生产
一般钢管。
随后是焊接工艺。
对于一些需要焊接的钢管,会经过焊接工艺。
焊接工艺主要包括高频焊、埋弧焊等方式,通过将钢板或钢带经过
卷板、成型、焊接等工序,最终形成焊接钢管。
然后是钢管的表面处理。
表面处理是为了提高钢管的耐腐蚀性
能和美观度。
通常包括酸洗、磷化、镀锌等工艺,以确保钢管在使
用过程中不易生锈、耐腐蚀。
最后是检测和包装。
在生产完成后,钢管需要经过一系列的检测,包括外径、壁厚、长度、化学成分、力学性能等指标的检测。
合格后,钢管会进行包装,通常采用塑料薄膜包装或捆扎包装,以
确保产品的安全运输和存储。
总的来说,钢管的生产流程经过原材料准备、成型、焊接、表
面处理、检测和包装等多个环节。
每个环节都需要严格控制和监测,以确保最终产品的质量和性能。
同时,生产过程中也需要注重节能
减排和安全生产,促进钢管产业的可持续发展。
GCRgcr轴承钢
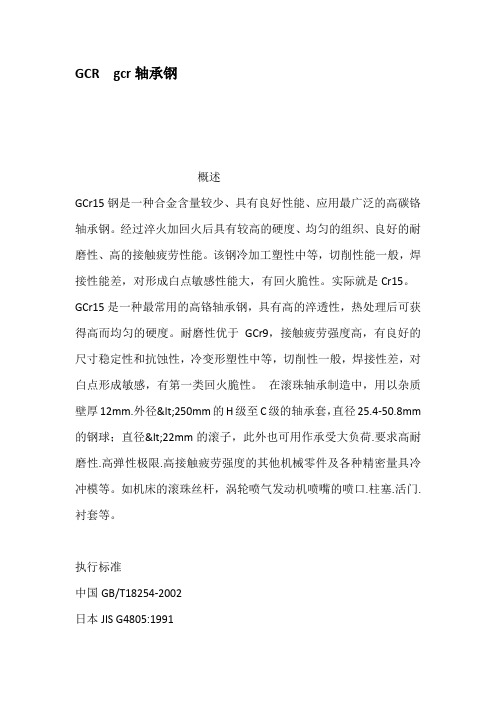
GCR gcr轴承钢概述GCr15钢是一种合金含量较少、具有良好性能、应用最广泛的高碳铬轴承钢。
经过淬火加回火后具有较高的硬度、均匀的组织、良好的耐磨性、高的接触疲劳性能。
该钢冷加工塑性中等,切削性能一般,焊接性能差,对形成白点敏感性能大,有回火脆性。
实际就是Cr15。
GCr15是一种最常用的高铬轴承钢,具有高的淬透性,热处理后可获得高而均匀的硬度。
耐磨性优于GCr9,接触疲劳强度高,有良好的尺寸稳定性和抗蚀性,冷变形塑性中等,切削性一般,焊接性差,对白点形成敏感,有第一类回火脆性。
在滚珠轴承制造中,用以杂质壁厚12mm.外径<250mm的H级至C级的轴承套,直径25.4-50.8mm 的钢球;直径<22mm的滚子,此外也可用作承受大负荷.要求高耐磨性.高弹性极限.高接触疲劳强度的其他机械零件及各种精密量具冷冲模等。
如机床的滚珠丝杆,涡轮喷气发动机喷嘴的喷口.柱塞.活门.衬套等。
执行标准中国GB/T18254-2002日本JIS G4805:1991美国ASTM A295:1998统一数字代号:B00150化学成分C:0.95-1.05Mn:0.20-0.40Si:0.15-0.35S:≤0.020P:≤0.027Cr:1.30-1.65Mo:≤0.10Ni:≤0.30Cu:≤0.25Ni+Cu≤0.50热处理其热处理制度为:钢棒退火,钢丝退火或830-840度油淬。
热处理工艺参数:1.普通退火:790-810度加热,炉冷至650度后,空冷——HB170-2072.等温退火:790-810度加热,710-720度等温,空冷——HB207-2293.正火:900-920度加热,空冷——HB270-3904.高温回火:650-700度加热,空冷——HB229-2855.淬火:860度加热,油淬——HRC62-666.低温回火:150-170度回火,空冷——HRC61-667.碳氮共渗:820-830度共渗1.5-3小时,油淬,-60度至-70度深冷处理+150度至+160回火,空冷——HRC≈67生产制造方法对轴承钢的冶炼质量要求很高,需要严格控制硫、磷和非金属夹杂物的含量和分布,因为非金属夹杂物的含量和分布对轴承钢的寿命影响很大。
钢管的铸造和锻造工艺
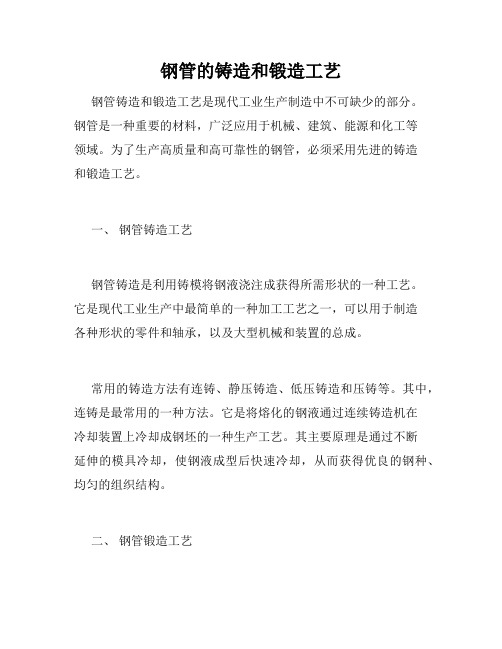
钢管的铸造和锻造工艺钢管铸造和锻造工艺是现代工业生产制造中不可缺少的部分。
钢管是一种重要的材料,广泛应用于机械、建筑、能源和化工等领域。
为了生产高质量和高可靠性的钢管,必须采用先进的铸造和锻造工艺。
一、钢管铸造工艺钢管铸造是利用铸模将钢液浇注成获得所需形状的一种工艺。
它是现代工业生产中最简单的一种加工工艺之一,可以用于制造各种形状的零件和轴承,以及大型机械和装置的总成。
常用的铸造方法有连铸、静压铸造、低压铸造和压铸等。
其中,连铸是最常用的一种方法。
它是将熔化的钢液通过连续铸造机在冷却装置上冷却成钢坯的一种生产工艺。
其主要原理是通过不断延伸的模具冷却,使钢液成型后快速冷却,从而获得优良的钢种、均匀的组织结构。
二、钢管锻造工艺钢管锻造是通过应用压力、力和温度等制造所需的形状的一种工艺。
这种工艺可以改变钢的物理和化学性质,从而提高其机械性能和耐磨性。
常用的锻造方法有自由锻、轧制锻造、环轧锻造、坯锻造和模锻等。
其中,自由锻造是最古老的锻造方法之一,也是最常用的一种方法。
它是将钢坯放在锻造装置上,并利用偏置、锤头等力量将钢坯加工成所需的形状。
三、钢管铸造与锻造工艺的比较钢管铸造和锻造工艺各自都有其优点和不足。
铸造工艺可以生产大量的产品,并能够制造复杂的零件和轴承。
而锻造工艺可以提高钢的机械性能,并能够生产更加精确的产品。
铸造工艺的缺点是其所生产的产品易受缺陷和杂质等因素的影响。
而锻造工艺的缺点则是其所生产的产品往往较小和比较难制造。
综上所述,钢管铸造和锻造工艺在现代工业生产中都扮演着重要的角色。
它们各自具有其独特的优点和不足,可以根据生产需要进行选择和应用。
无论是铸造还是锻造,都需要采用先进的工艺和设备,以确保生产出质量稳定,性能优良的钢管产品。
轴类零件加工工艺介绍
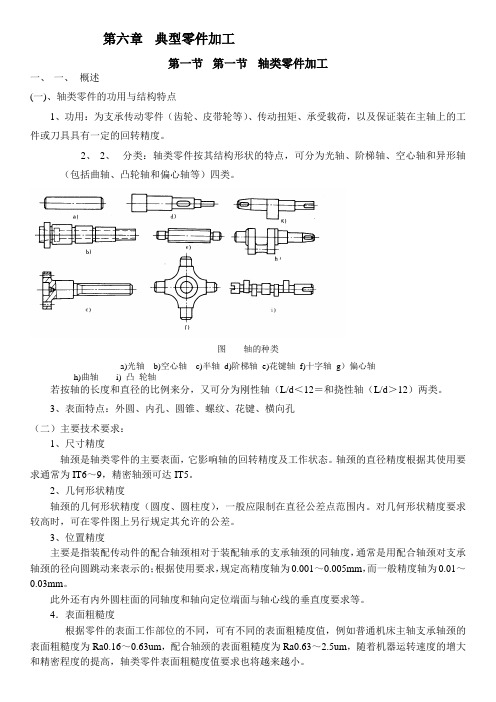
第六章典型零件加工第一节第一节轴类零件加工一、一、概述(一)、轴类零件的功用与结构特点1、功用:为支承传动零件(齿轮、皮带轮等)、传动扭矩、承受载荷,以及保证装在主轴上的工件或刀具具有一定的回转精度。
2、2、分类:轴类零件按其结构形状的特点,可分为光轴、阶梯轴、空心轴和异形轴(包括曲轴、凸轮轴和偏心轴等)四类。
图轴的种类a)光轴b)空心轴c)半轴d)阶梯轴e)花键轴f)十字轴g)偏心轴h)曲轴i) 凸轮轴若按轴的长度和直径的比例来分,又可分为刚性轴(L/d<12=和挠性轴(L/d>12)两类。
3、表面特点:外圆、内孔、圆锥、螺纹、花键、横向孔(二)主要技术要求:1、尺寸精度轴颈是轴类零件的主要表面,它影响轴的回转精度及工作状态。
轴颈的直径精度根据其使用要求通常为IT6~9,精密轴颈可达IT5。
2、几何形状精度轴颈的几何形状精度(圆度、圆柱度),一般应限制在直径公差点范围内。
对几何形状精度要求较高时,可在零件图上另行规定其允许的公差。
3、位置精度主要是指装配传动件的配合轴颈相对于装配轴承的支承轴颈的同轴度,通常是用配合轴颈对支承轴颈的径向圆跳动来表示的;根据使用要求,规定高精度轴为0.001~0.005mm,而一般精度轴为0.01~0.03mm。
此外还有内外圆柱面的同轴度和轴向定位端面与轴心线的垂直度要求等。
4.表面粗糙度根据零件的表面工作部位的不同,可有不同的表面粗糙度值,例如普通机床主轴支承轴颈的表面粗糙度为Ra0.16~0.63um,配合轴颈的表面粗糙度为Ra0.63~2.5um,随着机器运转速度的增大和精密程度的提高,轴类零件表面粗糙度值要求也将越来越小。
(三)、轴类零件的材料和毛坯合理选用材料和规定热处理的技术要求,对提高轴类零件的强度和使用寿命有重要意义,同时,对轴的加工过程有极大的影响。
1、轴类零件的材料一般轴类零件常用45钢,根据不同的工作条件采用不同的热处理规范(如正火、调质、淬火等),以获得一定的强度、韧性和耐磨性。
技术探讨我国轴承钢管的发展现状及生产工艺

技术探讨我国轴承钢管的发展现状及⽣产⼯艺冯志坚8⽉初,海关总署发布数据显⽰,6⽉份,我国出⼝轴承44708万套,出⼝⾦额达到195064万元,同⽐分别增长5.0%和4.2%;上半年累计出⼝255963万套,出⼝⾦额达到110.6亿元,同⽐分别增长0.9%和2.0%。
其中,轴承钢管作为轴承套圈的原材料,在我国轴承⼯业发展过程中起到了重要作⽤。
⽬前,中国已是装备制造⼤国,但实现“强”还有⼀定距离,其原因之⼀,是装备的轴承性能影响了整机的关键性能。
轴承钢是⽤于设备轴承制造的⼀种重要基础钢种,在众多品种的钢铁产品中被称为“钢中之王”,⼴泛应⽤于运输机械(汽车、⾼速列车等)、⼯程机械、冶⾦、⽯油化⼯、发电、航空航天、军⼯、风电和海洋⼯程等领域。
轴承钢的质量优劣,直接决定了重⼤装备和精密装备轴承的好坏。
轴承钢应具有长寿命、⾼精度、⾼刚度和⾼耐磨性等性能。
同时,轴承钢也是检验项⽬多、质量要求严、⽣产难度⼤的钢种之⼀。
作为“钢中之王”家族成员,轴承钢管是轴承钢⼆⽕成材产品。
作为轴承套圈⽤钢,其⽣产有其特殊性和严格要求。
由于我国整体冶炼⽔平限制和⽣产企业⾃⾝存在的问题,以及轴承套圈加⼯技术的发展现状,我国轴承钢管在质量、⽣产成本、材料利⽤率等⽅⾯的优势并不明显,其发展空间受到挤压。
⽬前,我国轴承钢管⽣产存在哪些问题?我国轴承钢管的⽣产⼯艺现状如何?轴承钢管今后的发展思路是什么?这些都是需要探讨的问题。
轴承钢管整体现状有待改变⽬前,我国国内轴承钢管产量仅占轴承钢总产量的8%,与发达国家占⽐20%~30%相⽐,仍有很⼤差距。
在轴承钢管品质⽅⾯,国内产品也存在品质稳定性差、疲劳寿命短、洁净度低等问题。
我国轴承钢管的应⽤,⼀般局限于普通轴承的轴承套圈⽤料,⾼端轴承套圈仍依赖进⼝。
1品种结构不合理,坯料供给⽭盾突出我国很多钢铁企业均存在钢材品种“全⽽不专”的⽣产现状。
⼀些企业的产品品种覆盖板、管、型、材和特殊钢材,普通钢材同质化问题严重,低端竞争呈现⽩热化。
轴承制造工艺流程

轴承制造工艺流程
轴承是机械传动中常用的元件,而轴承制造工艺流程是非常重要的。
下面我们将介绍一下轴承制造的工艺流程。
第一步:原材料准备
轴承制造的第一步是原材料准备。
主要原材料包括钢管、钢板、
钢带等。
这些原材料需要经过严格的筛选和测试,以保证材料的质量
和使用效果。
第二步:精密钢管制备
将不同品种的钢线经过喷丸、送丝、预卷、纵割、初轧、精轧、
洗油、探伤等工序来制备不同种类、精度等级的钢管。
第三步:轴承环加工
将钢管通过车削、滚削、磨削等加工方法加工成不同直径、厚度、精度等级的轴承环。
在加工过程中需要注意质量控制,保证加工的轴
承环质量符合要求。
第四步:小球制备
小球也是轴承中的重要组成部分之一。
小球制备使用的原料主要
是钢线。
通过自动化生产线加工,以及真空炉球化等技术,将钢线制
成不同直径、精度等级的小球。
第五步:组装与检测
将制好的轴承环和小球组装在一起,同时进行适当的加工和修整,以保证轴承的精度等级。
在轴承组装完成后,进行检测和测试,以保
证轴承的质量达到标准,达到使用要求。
总的来说,轴承制造的工艺流程包括原材料准备、精密钢管制备、轴承环加工、小球制备、组装与检测等几个关键步骤。
这些步骤非常
重要,直接影响了轴承品质的优劣。
通过严格的生产和制造,可以保
证轴承质量的稳定和使用效果的优良。
轴承钢管的热加工生产工艺
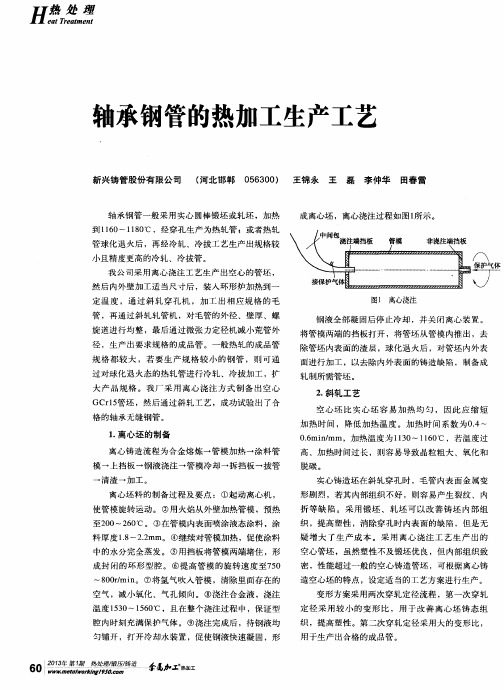
然 后 内外壁 加 工 适 当尺 寸 后 ,装 入 环 形炉 加 热 到一
定 温 度 ,通 过 斜 轧 穿 孔 机 ,加 工 出相 应 规 格 的 毛
图1 离心浇注
管 ,再通过斜轧轧管机 ,对毛管的外径、壁厚 、螺
旋 道 进 行 均 整 ,最 后通 过 微 张 力定 径 机减 小 荒 管 外
大 产 品 规 格 。 我 厂 采 用 离 心 浇 注 方 式 制 备 出 空 心 GC r l 5 管 坯 ,然 后通 过 斜 轧 工 艺 ,成 功试 验 出 了合 格 的轴 承 无缝 钢 管 。
2 . 斜轧工艺
空 心 坯 比 实 心 坯 容 易 加 热 均 匀 , 因此 应 缩 短 加 热 时 间 ,降 低 加 热 温 度 。加 热 时 间 系 数 为 0 . 4 ~ 0 . 6 mi n / mm,加 热温 度 为 1 1 3 0 ~1 1 6 0 ℃ ,若 温 度过 高 、加 热 时 间过长 ,则 容 易导 致 晶 粒粗 大 、氧 化和
钢液全部凝固后停止冷却 ,并关 闭离心装置。 将管模两端的挡板打开 ,将管坯从管模 内推出 ,去
除 管坯 内表 面 的渣 层 ,球 化 退 火 后 ,对 管 坯 内 外表 面 进 行加 工 ,以去 除 内外表 面 的 铸造 缺 陷 ,制 备成 轧 制 所需 管坯 。
径 ,生产出要求规格的成 品管。一般热轧的成品管 规 格都较 大 ,若要 生产规格较 小 的钢 管 ,则可 通 过对球化退火态的热轧管进行冷轧 、冷拔加工 ,扩
脱碳 。
1 . 离心坯的制备
离心 铸 造 流程 为 合 金 熔炼 一管 模 加 热 一涂 料 管 模 一 上 挡板 一钢液 浇 注 一 管模 冷 却 一拆 挡 板 一拔 管
控制轧制、控制冷却工艺

控制轧制、控制冷却⼯艺控制轧制、控制冷却⼯艺技术1.1 控制轧制⼯艺控制轧制⼯艺包括把钢坯加热到适宜的温度,在轧制时控制变形量和变形温度以及轧后按⼯艺要求来冷却钢材。
通常将控制轧制⼯艺分为三个阶段,如图 1.1所⽰[2]:(1>变形和奥⽒体再结晶同时进⾏阶段,即钢坯加热后粗⼤化了的γ呈现加⼯硬化状态,这种加⼯硬化了得奥⽒体具有促使铁素体相变形变形核作⽤,使相变后的α晶粒细⼩;(2> (γ+α>两相区变形阶段,当轧制温度继续降低到Ar3温度以下时,不但γ晶粒,部分相变后的α晶粒也要被轧制变形,从⽽在α晶粒内形成亚晶,促使α晶粒的进⼀步细化。
图1.1控制轧制的三个阶段(1>—变形和奥⽒体再结晶同时进⾏阶段;(2>—低温奥⽒体变形不发⽣再结晶阶段;(3>—<γ+α)两相区变形阶段。
1.2 控制轧制⼯艺的优点和缺点控制轧制的优点如下:1.可以在提⾼钢材强度的同时提⾼钢材的低温韧性。
采⽤普通热轧⽣产⼯艺轧制16Mn钢中板,以18mm厚中板为例,其屈服强度σs≤330MPa,-40℃的冲击韧性A k≤431J,断⼝为95%纤维状断⼝。
当钢中加⼊微量铌后,仍然采⽤普通热轧⼯艺⽣产时,当采⽤控制轧制⼯艺⽣产时,-40℃的A k值会降低到78J以下,然⽽采⽤控制轧制⼯艺⽣产时。
然⽽采⽤控制轧制⼯艺⽣产时-40℃的A k值可以达到728J以上。
在通常热轧⼯艺下⽣产的低碳钢α晶粒只达到7~8级,经过控制轧制⼯艺⽣产的低碳钢α晶粒可以达到12级以上<按ASTM标准),通过细化晶粒同时达到提⾼强度和低温韧性是控轧⼯艺的最⼤优点。
2.可以充分发挥铌、钒、钛等微量元素的作⽤。
在普通热轧⽣产中,钢中加⼊铌或钒后主要起沉淀强化作⽤,其结果使热轧钢材强度提⾼、韧性变差,因此不少钢材不得不进⾏正⽕处理后交货。
当采⽤控制轧制⼯艺⽣产时,铌将产⽣显著的晶粒细化和⼀定程度的沉淀强化,使轧后的钢材的强度和韧性都得到了很⼤提⾼,铌含量⾄万分之⼏就很有效,钢中加⼊的钒,因为具有⼀定程度的沉淀强化的同时还具有较弱的晶粒细化作⽤,因此在提⾼钢材强度的同时没有降低韧性的现象。
套筒零件加工工艺分析
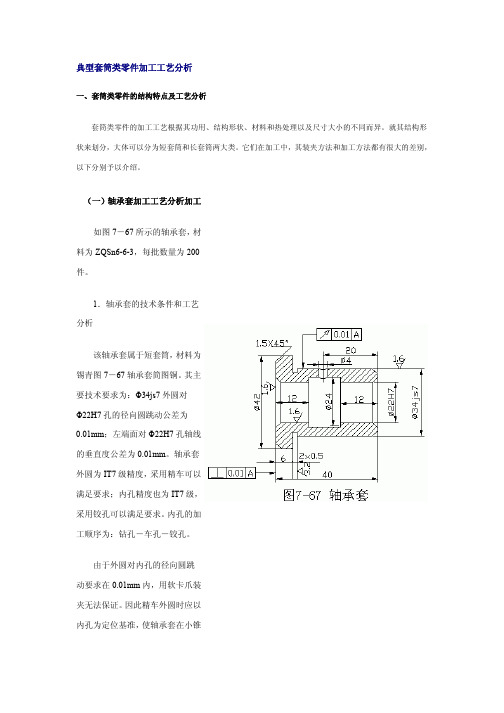
3
粗车 空刀槽 2×0.5mm,取总长 40.5mm,车分割槽 Ф20×3mm, 中心孔
两端倒角 1.5×45°,5 件同加工,尺寸均相同
钻孔 Ф22H7 至 Ф22mm 成单件
4
钻
软爪夹 Ф42mm 外圆
• 车端面,取总长 40mm 至尺寸
5 车、铰
• 车内孔 Ф22H7 为 Ф22 mm • 车内槽 Ф24×16mm 至尺寸 • 铰孔 Ф22H7 至尺寸 • 孔两端倒角
由于外圆对内孔的径向圆跳 动要求在 0.01mm 内,用软卡爪装 夹无法保证。因此精车外圆时应以 内孔为定位基准,使轴承套在小锥
度心轴上定位,用两顶尖装夹。这 样可使加工基准和测量基准一致, 容易达到图纸要求。
车铰内孔时,应与端面在一次 装夹中加工出,以保证端面与内孔 轴线的垂直度在 0.01mm 以内。
3.精铰(浮动镗刀镗孔)到 Ф70±0.02mm,
表面粗糙度值 Ra 为 2.5µm
4
滚压孔 用滚压头滚压孔至 Ф70
mm,表面粗糙 一端用螺纹固定在夹具中, 另一
度值 Ra 为 0.32µm
端搭中心架
1.车去工艺螺纹,车 Ф82h6 到尺寸,割 R7 槽
软爪夹一端,以孔定位顶另一端
2.镗内锥孔 1°30′及车端面
5
车
软爪夹一端,中心架托另一端(百 分表找正孔)
3.调头,车 Ф82h6 到尺寸,割 R7 槽
软爪夹一端,顶另一端
4.镗内锥孔 1°30′及车端面
软爪夹一端,顶另一端
二、套筒类零件加工中的主要工艺问题
一般套筒类零件在机械加工中的主要工艺问题是保证内外圆的相互位置精度(即保证内、外圆表面的 同轴度以及轴线与端面的垂直度要求)和防止变形。
gcr15轴承钢管尺寸规格

gcr15轴承钢管尺寸规格摘要:I.轴承钢管简介- 轴承钢管的定义与作用- GCr15 轴承钢管的特点II.GCr15 轴承钢管尺寸规格- 轴承钢管的内径规格- 轴承钢管的外径规格- 轴承钢管的厚度规格III.GCr15 轴承钢管生产工艺- GCr15 轴承钢管的制造流程- GCr15 轴承钢管的加工方法IV.GCr15 轴承钢管的应用领域- GCr15 轴承钢管在轴承制造中的应用- GCr15 轴承钢管在汽车工业中的应用- GCr15 轴承钢管在航空航天领域中的应用正文:轴承钢管是一种用于制造轴承的专用钢材,具有良好的耐磨性、高的接触疲劳性能以及高的硬度。
GCr15 轴承钢管是轴承钢管中的一种,由于其合金含量较少,应用广泛,具有良好的性能。
GCr15 轴承钢管的内径规格一般为10-1000mm,根据不同的轴承类型和大小,内径的选择也有所不同。
轴承钢管的外径规格一般为30-400mm,外径的尺寸决定了轴承的负载能力和运转稳定性。
轴承钢管的厚度规格一般为2-20mm,根据轴承的使用环境和负载能力,可以选择不同的厚度。
GCr15 轴承钢管的生产工艺主要包括热轧、冷轧、热处理等步骤。
在热轧过程中,通过轧制使钢材的形状和尺寸符合要求。
在冷轧过程中,通过冷轧使钢材的表面光洁度和尺寸精度得到提高。
热处理是GCr15 轴承钢管生产中的重要步骤,通过热处理可以提高钢材的硬度和韧性。
GCr15 轴承钢管广泛应用于轴承制造、汽车工业和航空航天等领域。
在轴承制造领域,GCr15 轴承钢管用于制造各种轴承,如球轴承、滚子轴承等。
在汽车工业领域,GCr15 轴承钢管用于制造汽车轴承、齿轮等零部件。
在航空航天领域,GCr15 轴承钢管用于制造航空发动机、导弹等高精度零部件。
GCr15 钢管生产工艺要点与理论分析

(上接第315页)摘要:滚动轴承应用于国民经济的各个领域,是工农业不可缺少的零部件。
轴承厂用无缝钢管生产滚动轴承的轴承套圈,我国是在20世纪50年后期开始,逐步的掌握了轴承套圈的生产工艺并投入生产。
本文概要分析生产要点、关键参数及热处理工艺制度。
关键词:GCr15滚动轴承工艺要点关键参数热处理1概述无缝钢管为原料生产轴承套圈是上世纪50年代后期,1953年鞍钢三大工程之一,鞍钢无缝厂-Φ140自动轧管机组(苏联援建)投产,当时在我国是先进、唯一的无缝钢管厂家。
由于建国后大规模经济建设,钢管需求量极大,远远满足不了市场需求。
作为当时急需的航空机构管、石油用管、枪炮军用及一般结构管都是这套Φ140机组来生产。
由于轴承钢工艺要求特殊,热处理复杂,受设备所限,在1955年后,轴承钢管生产量较少,主要用于军工等要害部门。
鉴于轴承钢管产量低、周期长、工艺复杂、热处理设备要求高等特点,至今鞍钢已经不再生产轴承钢管。
1956年后,成都钢管厂建成Φ216、Φ318周期轧管机,包钢Φ400,到1958年全国建成40余套Φ76小型无缝机组,80年衡阳建成Φ108三辊穿轧机组,随后大冶(黄石)、天津Φ250等大型国有企业相继建成投产,为我国无缝钢管蓬勃发展打下基础。
2GCr15钢的特点及冶炼要求滚铬15钢(GCr15)至今为国内外公认的标准牌号轴承钢,为什么常用不衰呢?我们可从它的牌号和化学成份中得到答案,见下表1表1GCr15钢的化学成份(质量分数)%从表1看出:它含碳量在1%左右,含Cr 量在1.5%左右,含P.S 量≤0.025(属于优质钢),所以GCr15钢准确说叫高碳低合金优质铬钢。
其特点:①用高碳(1%)增加硬度和耐磨性;②用铬(1.5%)增加强度和耐腐蚀性;③加热时要防止脱碳:钢管内、外表面每边总脱碳层深度应符合高碳铬轴承钢标准(GB/18254-2002)见表2。
④非金属夹杂物和碳化物不均性等要求应符合GB/T18254-2002的规定。
- 1、下载文档前请自行甄别文档内容的完整性,平台不提供额外的编辑、内容补充、找答案等附加服务。
- 2、"仅部分预览"的文档,不可在线预览部分如存在完整性等问题,可反馈申请退款(可完整预览的文档不适用该条件!)。
- 3、如文档侵犯您的权益,请联系客服反馈,我们会尽快为您处理(人工客服工作时间:9:00-18:30)。
轴承钢管生产工艺
轴承钢管生产工艺是指轴承钢管的生产过程和工艺流程。
下面将介绍轴承钢管的生产工艺流程和主要步骤。
首先,轴承钢管的生产需要选择高质量的轴承钢作为原料。
轴承钢具有高强度、高硬度和良好的纯净性能,能够满足轴承钢管对材质的要求。
其次,将选好的轴承钢加热到适当温度,进行热处理。
热处理过程包括淬火和回火两个步骤,淬火可以提高轴承钢的硬度和强度,回火则能够降低轴承钢的脆性,提高其韧性和冲击韧性。
接下来,对经过热处理的轴承钢进行锻造。
锻造是指将轴承钢加热到一定温度后,通过锻造机械的冲击力使其变形,加工成希望得到的形状和尺寸。
锻造可以提高轴承钢的整体强度和塑性。
然后,对锻造好的轴承钢进行精加工。
精加工是指将轴承钢通过车、铣、磨等加工工艺,加工成轴承钢管的标准尺寸和形状。
精加工过程需要严格控制加工精度,以确保轴承钢管的质量和性能。
最后,对精加工好的轴承钢管进行检验和测试。
检验和测试包括外观检查、尺寸测量、力学性能试验和检验等。
只有通过了检验和测试的轴承钢管才能出厂销售和应用。
轴承钢管生产工艺需要掌握高精度的加工技术和严格的质量控
制。
只有在合理的工艺流程和严格的质量控制下,才能生产出高质量的轴承钢管,满足工业领域对于轴承钢管的要求。