某超薄壁零件应用五轴高速加工方案
薄壁零件的机械加工工艺分析
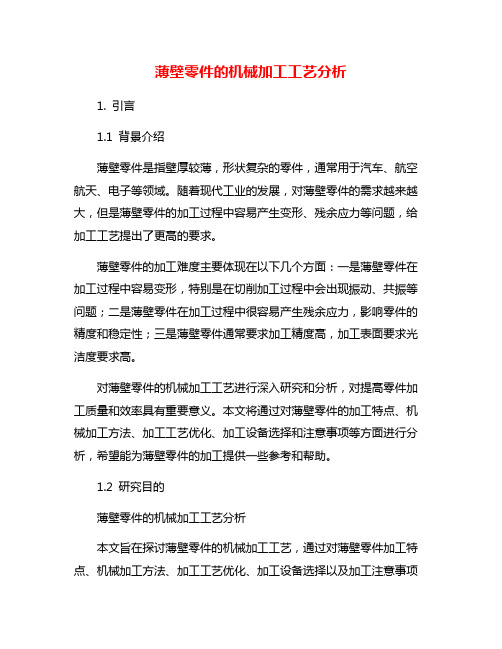
薄壁零件的机械加工工艺分析1. 引言1.1 背景介绍薄壁零件是指壁厚较薄,形状复杂的零件,通常用于汽车、航空航天、电子等领域。
随着现代工业的发展,对薄壁零件的需求越来越大,但是薄壁零件的加工过程中容易产生变形、残余应力等问题,给加工工艺提出了更高的要求。
薄壁零件的加工难度主要体现在以下几个方面:一是薄壁零件在加工过程中容易变形,特别是在切削加工过程中会出现振动、共振等问题;二是薄壁零件在加工过程中很容易产生残余应力,影响零件的精度和稳定性;三是薄壁零件通常要求加工精度高,加工表面要求光洁度要求高。
对薄壁零件的机械加工工艺进行深入研究和分析,对提高零件加工质量和效率具有重要意义。
本文将通过对薄壁零件的加工特点、机械加工方法、加工工艺优化、加工设备选择和注意事项等方面进行分析,希望能为薄壁零件的加工提供一些参考和帮助。
1.2 研究目的薄壁零件的机械加工工艺分析本文旨在探讨薄壁零件的机械加工工艺,通过对薄壁零件加工特点、机械加工方法、加工工艺优化、加工设备选择以及加工注意事项等方面进行深入分析,以期为相关行业提供一定的参考和指导。
薄壁零件因其结构特殊、加工难度大、容易变形等特点,在实际生产中存在一定的挑战。
通过对薄壁零件的机械加工工艺进行研究分析,可以帮助企业更加有效地解决加工过程中所面临的问题,提高生产效率、降低生产成本,提升产品质量和市场竞争力。
研究目的的关键在于深入了解薄壁零件的加工特点和加工工艺,找出存在的问题并提出解决方案,为制造工程技术人员提供可行的指导意见和建议。
通过本文的研究,希望能够为薄壁零件的机械加工工艺提供更加系统和全面的分析,为相关领域的技术人员提供参考和借鉴,推动薄壁零件的机械加工技术不断创新和提升。
1.3 研究意义薄壁零件在机械加工领域中起着重要的作用,其加工工艺的优化对于提高产品质量、降低生产成本具有重要意义。
由于薄壁零件的特殊性,其加工过程中容易出现变形、裂纹等问题,因此需要对其加工进行深入研究和优化。
powermill 2020五轴数控加工编程应用实例

powermill 2020五轴数控加工编程应用实例PowerMill 2020是一款功能强大的五轴数控加工编程软件,可以用于制造复杂的零件和模具。
下面是一个应用实例,演示如何使用PowerMill 2020进行五轴数控加工编程。
1. 打开PowerMill 2020软件,并导入要加工的零件模型。
2. 在软件中创建新的加工操作,选择合适的加工策略,例如五轴联动加工、五轴侧铣等。
3. 设定加工参数,例如刀具、切削参数、冷却方式等。
4. 进行加工模拟,检查加工过程是否正确。
如果有错误,需要进行调整。
5. 将加工代码导出到数控机床中,进行实际加工。
在应用实例中,我们需要注意以下几点:
1. 在选择加工策略时,需要考虑零件的形状、材料和加工要求等因素,以确保加工效率和精度。
2. 在设定加工参数时,需要结合实际情况进行调整,例如切削速度、进给速度和切削深度等。
3. 在进行加工模拟时,需要仔细检查加工过程,特别是刀具路径和切削参数等方面,以确保实际加工中不会出现错误。
4. 在实际加工中,需要确保数控机床的精度和稳定性,同时需要操作人员的技能和经验,以确保加工质量和效率。
总之,PowerMill 2020五轴数控加工编程软件的应用实例需要结合实际情况进行调整和优化,以确保加工质量和效率。
五轴加工中心加工复杂零件案例分析

Research and Exploration |研究与探索.探讨与创新五轴加工中心加工复杂零件案例分析吴卫江(广东省核工业华南高级技工学校,广东韶关512026)摘要:对五轴加工进行概述,分析了其在复杂零件加工中的优势,并以小轿车模型为例,分析了五轴数控加工技术的 实际应用及效果。
关键词:五轴数控加工;小轿车;优势中图分类号:TG547 文献标识码:A文章编号:1671-0711 (2017) 01 (下)-0182-021五轴加工概述当前,随着自动化技术的发展,数控机床已经 成为当代制造业的主要设备,数控技术是提高制造 水平的保障,传统的加工技术正在逐渐被数控技术 替代,数据技术已经成为一个国家先进制造业的保 障。
五轴联动加工中心则是当前数控机床的最高水 平,但是由于制造业的发展水平有限,我国的高端 数控加工设备和先进发达国家相比还有差距。
因此,在多轴联动加工软件平台和数据库开发方面,需要 进一步进行研发。
和传统的三轴加工技术相比,五轴加工技术对 零件进行加工时,采用机床5个坐标轴,分别为X、Y、Z3个坐标轴和任意2个旋转轴。
其中,绕X、Y、Z的旋转轴分别称为A、B、C轴,其余为A、B、C中的任意2个自由度。
五轴数控加工主要应用在 轮船、水电水利、航空航天等高端产品的核心部件 制造,其应用非常广泛,比如制造水利水电设备中 的发电机转子,汽车发动机中的涡轮及模具,这些 核心部件对产品的质量和性能直接产生影响。
当前,西方装备制造业较发达,五轴联动加工中心的应用 已经十分广泛,并且加工精度也越来越高,因此,为了提高我国的制造业加工水平,开展五轴加工技 术的研究十分重要。
2五轴加工复杂零件优势在复杂零件加工过程中,五轴加工具有以下优 势:(1)采用五轴加工技术通过一次装夹零件可以 完成零件的大部分加工,缩短了加工时间和零件制 造周期,并且降低了工作人员的工作量。
(2)在复 杂零件加工过程中,利用刀具的旋转实现零件的切 削,由于采用不同的切削原理、刀具与被加工工件 的接触角度不相同,导致工件的加工质量和切削结 果也不相同。
五轴加工工作流程及基本原理

五轴加工工作流程及基本原理摘要:简洁扼要说明五轴加工流程,并对关键节点工作原理展开详细说明。
应用齐次变换法,对五轴CAM刀位数据及后处理机床各轴运动进行数据建模求解,该方法简便易于理解。
关键词:五轴加工;CAM;程序后处理;齐次变换引言目前越来越多领域对其产品的设计要求日益提高,除了传统航天航空、汽车轮船等领域经常用到大曲率的曲线表面,以达到较高的空流体力学性能,日常用品因功能外观要求,也开始使用越来越多的自由形状。
传统3轴加工仅可加工一个单凸曲线特征的表面,对复杂曲线变化的表面(深凹或低切)无能为力,此时需要使用5轴加工。
另外对形状尺寸公差要求严格的产品,也可采用5轴一次装夹进行多面加工,避免多次装夹导致精度损失。
成功的5轴加工取决于4个不同程度互相依赖的因素:●机床(床身结构刚性、主轴稳定性、传动系统精度等)●控制硬件(电机、反馈部件、驱动器等)●控制软件(数控系统运动、插补算法等)●工艺编程软件(刀具轨迹的生成和后处理)综述所述,在5轴加工中,机床、控制系统、刀具夹具等纯技术性能并非影响最终结果的唯一因素,结果的质量在很大程度上取决于支持整个工艺的设计工具(特别是CAM软件)的正确使用。
本文就第4点展开详细说明,对5轴加工工作流程及基本原理进行简介。
1.五轴加工工作流程简介如图1所示,五轴加工工作流程大致如下[1]:1)产品3D设计根据产品的功能及外观要求,利用CAD设计软件进行3D设计,CAD设计软件提供多种自由曲面造型,主要有Coons曲面、Bezier曲面、B样条曲面等,另外3D设计软件一般可与有限元分析软件、CAM软件进行结合对接,为产品设计优化、后续加工制造提供好的支持。
常用的CAD设计软件有:UG、Pro/E、SolidWorks等。
2)刀具位置文件生成输入产品的3D造型文件,利用CAM软件对刀具类型及参数、工艺方案、刀轴控制方式、刀具路径规则等进行设置,并计算生成刀具位置文件(该计算处理称为CAM的主处理)。
高速切削技术在薄壁零件加工中的应用研究

高速切削技术是诞生 于 2 0世纪 3 0年代 的一项 先 进 制造技术 ,其 采用超 硬材料 刀具和模具 ,利用高精
度 、高 自动化和高柔性的制造设备实现 了高效率 、高 柔性和高质量 的切 削加工 ,被称 为是 2 世 纪机械 制 1
造业 的一 场技术革命 ,在工程领 域的应用逐 渐成 熟 。由于高 速切 削技 术具 有 高 主轴 转 速 、高 进 给速 度 、低切削力和高切削速度等特点 ,能有效地缩短加 工时 间并降低加工 成本 ,加 工精 度高且 表面 质量好 , 符合薄壁箱体 生产 的发展趋势 ,因而获得广泛应用 。 作者针 对薄壁箱体零 件的工艺特点及生产实 际要 求 ,对薄壁箱体零件高速切削 的可行性进行 了分析 与
高速切削技术在薄壁零件加工中的应用研究
周 文 ( 南通纺织职业技术学院,江苏南通 260 ) 207
摘要 :从 薄壁箱体的加工效率 、加工精度等 角度出发 ,分析薄壁箱体零 件高速切 削加工 的优 势和可行 性。针对其 工艺 特点及生 产实际要求 ,分析高速加工 中存在 的工 艺问题 ,给出具体 的解决 措施 。实践 表明 :采用 高速切削加 工技术加 工薄 壁 箱体 ,加工效率高 ,工件表面质量好 。 关键词 :高速切削技术 ;加工效率 ;加 工精度 ;薄壁箱体零件
nn , te me s r s w r u o wad t e o v h r c s rb e f ma h nn . T e p a t e h w t a h p l ai n o ih i g h a u e e e p tfr r o r s le t e p o e s p o lms o c i i g h r ci s s o h tt e a p i t fh g — c c o s e d ma h n n e h o o y i c i i g t i — i k e sb x d s a e o k ic sc n g i ih e ce c n o d s ra e q a i . p e c i i g t c n lg n ma hn n n t c n s o e — h p d w r p e e a an h g f in y a d g o u f c u t h h i l y
五轴加工技术在复杂零件加工中应用

五轴加工技术在复杂零件加工中应用摘要:本文结合生产实践经验,从五轴加工的策略、CAM后置处理的构造、机床的高级功能3个方面简要介绍了数控系统为SINUMERIK840Dsl的DMG260-11五轴加工中心在应用方面的方法及技巧。
关键词:五轴加工;复杂零件;加工应用引言现代工业中五轴加工技术正被广泛应用,在航空航天、汽车、船舶等制造行业发挥了越来越重要的作用。
轮廓加工精度是评价零件加工质量的重要指标,也是五轴数控加工工艺的研究重点。
如何控制加工轮廓设误差,涉及到加工工艺系统、CAD/CAM等诸多因素,如机床伺服运动控制、机床几何误差测量补偿、刀位轨迹规划、数控编程、插补方法、切削工艺参数等。
国内外学者在该领域内做了大量的理论和实践工作,取得不少成绩,但仍然存在很多问题需要解决或改善。
1加工策略的选择1.1五轴定向加工针对一些加工区域敞开性好、倾斜面上的孔、面加工等内容较多的零件,五轴联动加工数控编程烦琐、加工效率及刚性也有待提高。
采用五轴定向加工方式可实现这类零件的高效和高质量加工。
五轴定向加工是指利用五轴机床加工时,根据所需要加工区域位置把两个旋转轴转到一定角度后,锁定两个旋转轴,进行3个直线轴联动加工。
当一个区域的加工完成后,再调整两个旋转轴的角度继续加工。
由于减少两个旋转轴的运动,五轴定轴加工方式增强了加工时的整体刚性,可以选择加工效率较高的粗加工切削策略。
SINUMERIK840Dsl数控系统中的,CYCLE800是五轴定向加工辅助循环,在手工编程时经常应用。
1.2五轴联动加工五轴联动加工常用以解决三轴无法加工的制造问题,如曲面法向拉线类零件,设计加工路线时要求刀具沿法向切削,三轴联动通常不能满足其要求。
加工叶轮、叶片等带有空间扭曲曲面的零件时,只有采用五轴联动加工方式,使刀具随时旋转摆动角度才能避免干涉情况。
对于有些回转零件,加工时虽不存在干涉问题,但采用3种联动加工方式需要多次转位衔接加工面,直接影响零件表面质量和加工精度,五轴联动加工方式能有效解决该加工问题。
五轴组合零件数控加工工艺及工装设计
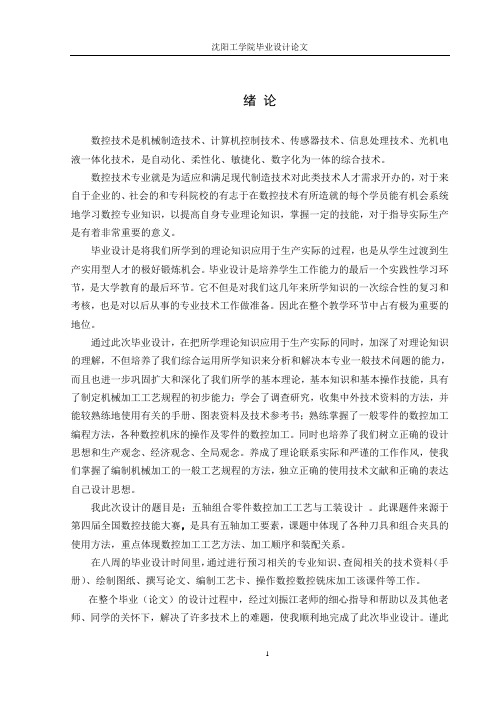
绪论数控技术是机械制造技术、计算机控制技术、传感器技术、信息处理技术、光机电液一体化技术,是自动化、柔性化、敏捷化、数字化为一体的综合技术。
数控技术专业就是为适应和满足现代制造技术对此类技术人才需求开办的,对于来自于企业的、社会的和专科院校的有志于在数控技术有所造就的每个学员能有机会系统地学习数控专业知识,以提高自身专业理论知识,掌握一定的技能,对于指导实际生产是有着非常重要的意义。
毕业设计是将我们所学到的理论知识应用于生产实际的过程,也是从学生过渡到生产实用型人才的极好锻炼机会。
毕业设计是培养学生工作能力的最后一个实践性学习环节,是大学教育的最后环节。
它不但是对我们这几年来所学知识的一次综合性的复习和考核,也是对以后从事的专业技术工作做准备。
因此在整个教学环节中占有极为重要的地位。
通过此次毕业设计,在把所学理论知识应用于生产实际的同时,加深了对理论知识的理解,不但培养了我们综合运用所学知识来分析和解决本专业一般技术问题的能力,而且也进一步巩固扩大和深化了我们所学的基本理论,基本知识和基本操作技能,具有了制定机械加工工艺规程的初步能力;学会了调查研究,收集中外技术资料的方法,并能较熟练地使用有关的手册、图表资料及技术参考书;熟练掌握了一般零件的数控加工编程方法,各种数控机床的操作及零件的数控加工。
同时也培养了我们树立正确的设计思想和生产观念、经济观念、全局观念。
养成了理论联系实际和严谨的工作作风,使我们掌握了编制机械加工的一般工艺规程的方法,独立正确的使用技术文献和正确的表达自己设计思想。
我此次设计的题目是:五轴组合零件数控加工工艺与工装设计。
此课题件来源于第四届全国数控技能大赛,是具有五轴加工要素,课题中体现了各种刀具和组合夹具的使用方法,重点体现数控加工工艺方法、加工顺序和装配关系。
在八周的毕业设计时间里,通过进行预习相关的专业知识、查阅相关的技术资料(手册)、绘制图纸、撰写论文、编制工艺卡、操作数控数控铣床加工该课件等工作。
五轴联动加工实例

第二节 球面刻字加工实例
一、球面刻字加工工艺分析 首先分析完成这个加工任务需要哪几个步骤。
图9-64 第一次粗加工后效果
第67页/共130页
第二节 球面刻字加工实例
图9-65 第二次粗加工后效果
第68页/共130页
第二节 球面刻字加工实例
图9-66 球面精加工后效果
第69页/共130页
第二节 球面刻字加工实例
图9-84 精加工参数
5.创建加工操作并产生加工刀具路径
第88页/共130页
第二节 球面刻字加工实例
(1)球面粗加工 选择“mill—contour”类型的子类型“CAVI T Y — M I L L ” , 创 建 一 个 层 铣 操 作 , 命 名 为 “ C AV I T Y — M I L L 1”。
第一节 多面体加工实例
图9-28 “进给和速度”对话框
第30页/共130页
第一节 多面体加工实例
图9-29 切削参数——策略
第31页/共130页
第一节 多面体加工实例
图9-30 切削参数——余量
第32页/共130页
第一节 多面体加工实例
图9-31 切削参数——连接
第33页/共130页
第一节 多面体加工实例
第一节 多面体加工实例
图9-24 “自动进刀/退刀”对话框
第26页/共130页
第一节 多面体加工实例
图9-25 “避让几何”对话框
第27页/共130页
第一节 多面体加工实例
图9-26 “安全平面”对话框
第28页/共130页
第一节 多面体加工实例
图9-27 “平面构造器”对话框
第29页/共130页
第一节 多面体加工实例
零件的五轴加工
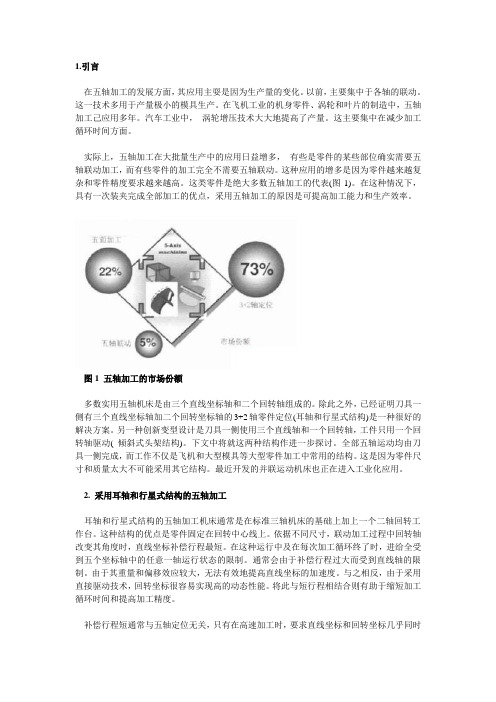
1.引言在五轴加工的发展方面,其应用主耍是因为生产量的变化。
以前,主要集中于各轴的联动。
这一技术多用于产量极小的模具生产。
在飞机工业的机身零件、涡轮和叶片的制造中,五轴加工己应用多年。
汽车工业中,涡轮增压技术大大地提高了产量。
这主要集中在减少加工循环时间方面。
实际上,五轴加工在大批量生产中的应用日益增多,有些是零件的某些部位确实需要五轴联动加工,而有些零件的加工完全不需要五轴联动。
这种应用的增多是因为零件越来越复杂和零件精度要求越来越高。
这类零件是绝大多数五轴加工的代表(图1)。
在这种情况下,具有一次装夹完成全部加工的优点,采用五轴加工的原因是可提高加工能力和生产效率。
图1 五轴加工的市场份额多数实用五轴机床是由三个直线坐标轴和二个回转轴组成的。
除此之外,已经证明刀具一侧有三个直线坐标轴加二个回转坐标轴的3+2轴零件定位(耳轴和行星式结构)是一种很好的解决方案。
另一种创新变型设计是刀具一侧使用三个直线轴和一个回转轴,工件只用一个回转轴驱动( 倾斜式头架结构)。
下文中将就这两种结构作进一步探讨。
全部五轴运动均由刀具一侧完成,而工作不仅是飞机和大型模具等大型零件加工中常用的结构。
这是因为零件尺寸和质量太大不可能采用其它结构。
最近开发的并联运动机床也正在进入工业化应用。
2. 采用耳轴和行星式结构的五轴加工耳轴和行星式结构的五轴加工机床通常是在标准三轴机床的基础上加上一个二轴回转工作台。
这种结构的优点是零件固定在回转中心线上。
依据不同尺寸,联动加工过程中回转轴改变其角度时,直线坐标补偿行程最短。
在这种运行中及在每次加工循环终了时,进给全受到五个坐标轴中的任意一轴运行状态的限制。
通常会由于补偿行程过大而受到直线轴的限制。
由于其重量和偏移效应较大,无法有效地提高直线坐标的加速度。
与之相反,由于采用直接驱动技术,回转坐标很容易实现高的动态性能。
将此与短行程相结合则有助于缩短加工循环时间和提高加工精度。
补偿行程短通常与五轴定位无关,只有在高速加工时,要求直线坐标和回转坐标几乎同时到达目标位置才会有问题。
复杂曲面零件的五轴数控加工技术研究

复杂曲面零件的五轴数控加工技术研究
张映故
【期刊名称】《现代制造技术与装备》
【年(卷),期】2024(60)3
【摘要】随着科技水平的不断提升,精密复杂曲面零件的应用越来越广泛。
曲面驱动是复杂曲面零件加工的重要方法,驱动刀轨的规划直接关系到曲面物理特性的调控,应用五轴数控加工技术能够提升复杂曲面零件的加工质量。
文章主要研究复杂曲面零件的五轴数控加工技术,以佛像这个复杂曲面零件为例,分析了曲面驱动刀轨规划、工装方案设计、加工策略以及试制加工过程。
在实际加工过程中,技术人员应充分理解驱动刀轨规划思路与原理,在粗加工、精加工中完善刀轨设计,并进行试制加工。
【总页数】3页(P63-65)
【作者】张映故
【作者单位】柳州职业技术学院
【正文语种】中文
【中图分类】TP3
【相关文献】
1.基于UG的复杂曲面叶轮三维造型及五轴数控加工技术研究
2.复杂曲面五轴数控加工关键技术研究
3.复杂曲面零件数控加工的关键问题r——解读《复杂曲面零件
五轴数控加工理论与技术》4.五轴数控机床高效加工多曲面零件工艺5.基于五轴数控加工工艺的复杂曲面零件加工轨迹分析
因版权原因,仅展示原文概要,查看原文内容请购买。
复杂薄壁_薄板类零件高速加工技术初探_陈战士

· 47 ·
复杂薄壁、 薄板类零件高速加工技术初探
*+ ,@AB CDB *+ ,13 *+:13 :,6, :,:6 H:>6 :,:6 HG6 M NO :,6, H:76 :,6, H:G6 IJ0;01201KL JL34 IJ0;01201KL JL34 IJL12L;L IKL34 IJL12L;L IKL34 ./012034 ./012034 ./0120;0<= 76, >?, 766E7FG >F>E7:G 7?>E7FG 77?E6 : 7?,E6>, 89 57 89 56 89 >6 89 7, 89 5, 89 5, a ! "#$ %&’() 56, 56, 56, 56, 56, 56, 56, 56,
图 2 圆弧进刀
图 3 等高层切法
图 4 插铣法
②半精加工
半精加工要避免急剧的铣切运动 。
为避免过切, 不可采用螺旋或斜坡进刀。 半精加工和精
加工的切削用量, 一般应在保证加工质量的前提下, 兼 顾切削效率、 经济性和加工成本, 高速加工中其径向进 刀量应小于 6% ~8% 的刀具直径,且满足等量切削条 件。 ③精加工 精加工要避免急剧变化的刀具运动,
Study on High-speed Machining Technology of Complicated Thin-walled and Thin-veneer Parts
CHEN Zhan-shi, SI Xiao-mei, LIU Dong-xiao, et al.
(1. Luoyang Institute of Electro-Optical Equipment, AVIC, Luoyang 471009; 2. Wuhan University of Technology Huaxia College, Wuhan, 430223 ) The processing methods, processing parameters and fixture of complicated thin-walled and thin-veneer parts were pre- [Abstract] sented. The problem of thin-walled and thin-veneer parts machining was solved. The machining technology will be used future. [Keywords] NC processing technology; high-speed machining; processing parameters; fixture
五轴数控编程加工案例

五轴数控编程加工案例介绍和分析前言当前模具制造行业中,三轴数控加工技术已经普遍应用并且相对成熟,但随着五轴数控技术的发展与推进,先进的五轴数控加工技术在市场上体现出了明显的优越性,故而引进五轴数控加工技术,建立一个高效率、高质量、短周期、低成本的产品生产框架来适应市场的发展,以求在市场竞争中立于不败之地已经成为我们必须面对的问题。
近段时间,珠海某大型电器模具厂采购我司的五轴数控编程软件PowerMILL,本人接受公司的任务,为该客户进行五轴技术的培训辅导,并结合实际加工进行模具的试切,实例指导客户应用五轴加工技术,让客户看到了客观具体的三轴加工与五轴加工两者的效率和质量对比数据。
本文即以此次培训五轴工件试切为例,禅述在电器注塑模具加工当中,五轴数控加工技术相对于传统的三轴数控加工技术的若干优越性。
一、五轴数控加工技术简述1、五轴刀轴和五轴刀轴控制五轴是由3个线性轴(Linear axis) 加上2个旋转轴(Rotary axis)组成。
五轴刀轴控制是CAM系统五轴技术的核心。
五轴CAM系统计算出每个切削点刀具的刀位点(X,Y,Z)和刀轴矢量(I,J,K),五轴后处理器将刀轴矢量(I,J,K)转化为不同机床的旋转轴所需要转动的角度(A,B,C)其中的两个角度;然后计算出考虑了刀轴旋转之后线性移动的各轴位移(X,Y,Z)。
2、五轴机床类型按两旋转轴的运动位置结构来划分,可分为Table-Table、Head-Head、Table-Head三种类型。
1)Table-Table:此类型机床主轴方向不动,两个旋转轴均分布在工作平台上;工件加工时旋转轴随工作台旋转,加工时必须考虑装夹承重,可加工的工件尺寸比较小。
2)Head-Head:此类机床工作台不动,两个旋转轴均在主轴上。
机床可加工的工件尺寸比较大。
3)Table-Head:此类机床的两个旋转轴分别处于主轴和工作台上,工作台可以旋转,可装夹尺寸较大的工件;主轴可摆动,改变刀轴方向灵活。
复杂曲面零件数控加工的关键问题——解读《复杂曲面零件五轴数控加工理论与技术》

1五轴数控加工简介复杂曲面零件作为数字化制造的主要研究对象之一,在航空、航天、能源和国防等领域中有着广泛的应用,其制造水平代表着一个国家制造业的核心竞争力。
复杂曲面零件往往具有形状和结构复杂、质量要求高等难点,是五轴数控加工的典型研究对象。
当前,复杂曲面零件主要包括轮盘类零件、航空结构件以及火箭贮箱壁板等,如图1所示。
轮盘类零件是发动机完成对气体的压缩和膨胀的关键部件,主要包括整体叶盘类零件和叶片类零件。
整体叶盘类零件的叶展长、叶片薄且扭曲度大,叶片间的通道深且窄,开敞性差,零件材料多为钛合金、高温合金等难加工材料,因此零件加工制造困难。
叶片是一种特殊的零件,数量多、形状复杂、要求高、加工难度大且故障多发,一图1复杂曲面零件直以来都是各发动机厂生产的关键。
航空整体结构件由整块大型毛坯直接加工而成,在刚度、抗疲劳强度以及各种失稳临界值等方面均比铆接结构胜出一筹,但由于其具有尺寸大、材料去除率大、结构复杂、刚性差等缺点,因此加工后会产生弯扭组合等加工变形。
随着新一代大型运载火箭设计要求的提高,为保证火箭的可靠性,并减轻结构质量,提高有效载荷,对火箭贮箱壁板网格壁厚精度和根部圆弧过渡尺寸都提出了更严格的要求。
五轴数控铣削加工具有高可达性、高效率和高精度等优势,是加工大型与异型复杂零件的重要手段。
五轴数控机床在3个平动轴的基础上增加了2个转动轴,不但可以使刀具相对于工件的位置任意可控,而且刀具轴线相对于工件的方向也在一定的范围内任意可控。
五轴数控加工的主要优势包括:①提高刀具可达性。
通过改变刀具方向可以提高刀具可达性,实现叶轮、叶片和螺旋桨等复杂曲面零件的数控加工。
②缩短刀具悬伸长度。
通过选择合理刀具方向可以在避开干涉的同时使用更短的刀具,提高铣削系统的刚度,改善数控加工中的动态特性,提高加工效率和加工质量。
③可用高效加工刀具。
通过调整刀轴方向能够更好地匹配刀具与工件曲面,增加有效切宽,实现零件的高效加工。
大直径薄壁框类零件的五轴联动加工工艺优化
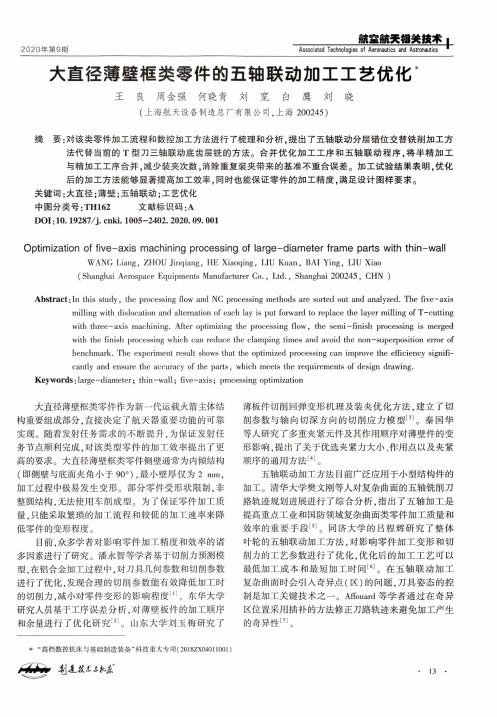
2020年第9期___________航空航天栩关技术Associated Technologies o f Aeronautics and Astronautics大直径薄壁框类零件的五轴联动加工工艺优化*王良周金强何晓青刘宽白鹰刘晓(上海航天设备制造总厂有限公司,上海200245)摘要:对该类零件加工流程和数控加工方法进行了梳理和分析,提出了五轴联动分层错位交替铣削加工方 法代替当前的T型刀三轴联动底齿层铣的方法。
合并优化加工工序和五轴联动程序,将半精加工 与精加工工序合并,减少装夹次数,消除重复装夹带来的基准不重合误差。
加工试验结果表明,优化 后的加工方法能够显著提高加工效率,同时也能保证零件的加工精度,满足设计图样要求。
关键词:大直径;薄壁;五轴联动;工艺优化中图分类号:T H162 文献标识码:AD O I:10.19287/j.c n k i. 1005-2402. 2020. 09.001Optimization of five-axis machining processing of large-diameter frame parts with thin-wall W A N G L i a n g,Z H O U J i n q i a n g,H E X i a o q i n g,L IU K u a n,B A I Y i n g,L IU X ia o(S h a n g h a i A e r o s p a c e E q u ip m e n ts M a n u f a c tu r e r C o.,L t d.,S h a n g h a i 200245, C H N )A b s t r a c t:In th i s s t u d y,th e p r o c e s s in g flo w a n d N C p r o c e s s in g m e t h o d s a r e s o r te d o u t a n d a n a l y z e d.T h e f i v e-a x i sm illin g w ith d is lo c a t io n a n d a lt e r n a t io n o f e a c h la y is p u t f o r w a r d to r e p l a c e th e l a y e r m i ll in g o f T-c u t t i n gw ith t h r e e-a x i s m a c h i n i n g.A f te r o p tim iz in g th e p r o c e s s i n g f l o w,t h e s e m i-f i n i s h p r o c e s s i n g is m e r g e dw ith th e f i n is h p r o c e s s in g w h ic h c a n r e d u c e th e c l a m p i n g ti m e s a n d a v o id th e n o n-s u p e r p o s i t i o n e r r o r o fb e nc h m a r k.T h e e x p e r i m e n t r e s u lt s h o w s th a t th e o p tim iz ed p r o ce s s i n g c a n im p r o v e t h e ef f ic i e n c y s ig n if ic a n tl y a nde n s u r e th e a c c u r a c y of th e p a r t s,w h ic h m e e t s t h e r e q u i r e m e n t s o f d e s ig n d r a w in g.K e y w o r d s:l a r g e-d i a m e t e r;t h i n-w a l l;f i v e-a x i s;p r o c e s s in g o p ti m i z a ti o n大直径薄壁框类零件作为新一代运载火箭主体结 构重要组成部分,直接决定了航天器重要功能的可靠 实现。
薄壁曲面零件五轴侧铣加工过程几何-力学仿真及变形误差刀路补偿
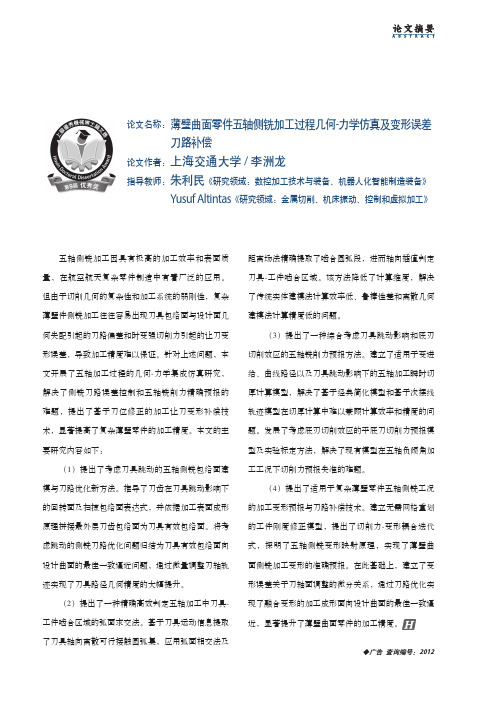
论文名称:薄壁曲面零件五轴侧铣加工过程几何-力学仿真及变形误差 刀路补偿
论文作者:上海交通大学 / 李洲龙 指导教师:朱利民《研究领域:数控加工技术与装备、机器人化智能制造装备》
(2)提出了一种精确高效判定五轴加工中刀具工件啮合区域的弧面求交法。基于刀具运动信息提取 了刀具轴向离散可行接触圆弧集,应用弧面相交法及
距离场法精确提取了啮合圆弧段,进而轴向插值判定 刀具-工件啮合区域。该方法降低了计算何 建模法计算精度低的问题。
(3)提出了一种综合考虑刀具跳动影响和底刃 切削效应的五轴铣削力预报方法。建立了适用于变进 给、曲线路径以及刀具跳动影响下的五轴加工瞬时切 厚计算模型,解决了基于经典简化模型和基于次摆线 轨迹模型在切厚计算中难以兼顾计算效率和精度的问 题。发展了考虑底刃切削效应的平底刀切削力预报模 型及实验标定方法,解决了现有模型在五轴负倾角加 工工况下切削力预报失准的难题。
◆广告 查询编号:2012
(1)提出了考虑刀具跳动的五轴侧铣包络面建 模与刀路优化新方法。推导了刀齿在刀具跳动影响下 的回转面及扫掠包络面表达式,并依据加工表面成形 原理拼接最外层刀齿包络面为刀具有效包络面。将考 虑跳动的侧铣刀路优化问题归结为刀具有效包络面向 设计曲面的最佳一致逼近问题,通过微量调整刀轴轨 迹实现了刀具路径几何精度的大幅提升。
(4)提出了适用于复杂薄壁零件五轴侧铣工况 的加工变形预报与刀路补偿技术。建立无需网格重划 的工件刚度修正模型,提出了切削力-变形耦合迭代 式,探明了五轴侧铣变形映射原理,实现了薄壁曲 面侧铣加工变形的准确预报。在此基础上,建立了变 形误差关于刀轴面调整的微分关系,通过刀路优化实 现了融合变形的加工成形面向设计曲面的最佳一致逼 近,显著提升了薄壁曲面零件的加工精度。
五轴加工解决方案
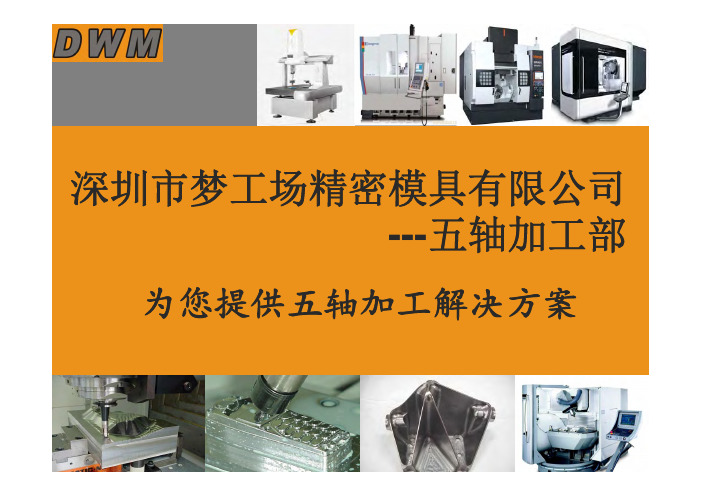
现有设备
DMG (德玛吉车铣复合加工 中心) CTX gamma 2000 双主轴 九轴五联动车 铣复加工中心 最大车削直径; Ф700mm 最大车削长度 ; 2050mm 主轴转速 12000转/分 刀塔的刀具容量 12 刀库容量 60 数控系统 siemens840D
现有设备
GMS-2600ST
(程泰车铣复合加工中心)
双主轴 九轴五联动车铣 复加工中心
最大车削直径
第一刀塔 Ф550mm
第二刀塔 Ф340mm
最大车削长度 1074 mm
主轴转速 12000转/分
刀塔的刀具容量 12
刀库容量
24
数控系统 FANUC 31i MODEL A5
现有设备
DMG (德玛吉车铣复合机) CTX 310 四轴车铣复加工中心 最大车削直径; Ф400mm 最大车削长度;450 mm 主轴转速 6000转/分 刀塔的刀具容量 12 数控系统 siemens 840D
设备介绍现有设备hardingexr6005ax哈挺五轴加工中心技术参数axis885mmaxis800mmaxis500mmaxis30120axis360360工作台面600600主轴转速25000rpm数控系统heidenhainitnc530主轴规格hsk63a刀库容量48带刀具自动激光检测系统数量现有设备dmgdmu100p德玛吉五轴加工中心技术参数axis1000mmaxis1000mmaxis1000mm数控摆动铣头baxis30180数控回转工作台360工作台面1100主轴转速8000rpm数控系统siemens840d最大承重1400kg主轴规格sk50主轴最大功率44kw刀库容量40带刀具自动激光检测系统现有设备dmgdmu100monoblock德玛吉五轴加工中心技术参数axis1150mmaxis710mmaxis710mm数控摆动铣头baxis12030数控回转工作台360工作台面1100主轴转速18000rpm数控系统heidenhain最大承重1400kg主轴规格sk50主轴最大功率44kw刀库容量40带刀具自动激光检测系统现有设备dmgdmu80fddoublock德玛吉五轴车削加工中心技术参数axis800mmaxis800mmaxis800mm数控摆动铣头baxis30180数控回转工作台360工作台面800主轴转速18000rpm数控系统siemens840d最大承重1400kg主轴规格sk50主轴最大功率44kw刀库容量40带刀具自动激光检测系统现有设备dmgdmu60monoblock德玛吉五轴加工中心技术参数axis800mmaxis600mmaxis600mm数控摆动铣头baxis12030数控回转工作台360工作台面600主轴转速18000rpm数控系统heidenhain最大承重1400kg主轴规格sk50主轴最大功率44kw刀库容量40带刀具自动激光检测系统数量10台dmg德玛吉车铣复合加工中心ctxgamma2000双主轴九轴五联动车铣复加工中心最大车削直径
五轴加工技术

五轴加工技术简介
机械与动力工程学院
3.五轴加工中的核心技术
RTCP
Definition
RTCP,即旋转 Rotational Tool Center Point Fidia 刀具中心编程 功能,通过在 海德汉 Tool Centre Point Management NC代码中指定 Real-time Tool Center Point rotation PA 刀具中心点位 置和刀轴矢量, 数控系统可以 根据期望的刀 轴矢量,实现 对刀具中心点 的控制。
五轴加工技术简介
机械与动力工程学院
2.五轴加工技术的基本步骤
CAM Computer Aided Manufacture 解读CAD数据 设定编程坐标系 设定选择刀具 确定加工策略 刀具干涉检查与避让 加工过程仿真 输出刀位信息
五轴加工技术简介 机械与动力工程学院
2.五轴加工技术的基本步骤
双转台结构
摆头转台结构
机械与动力工程学院
1.五轴加工技术的基本概念
机床的机械零点
机械零点指机床机 械结构上的零点, 有机床本身的结构 所决定,设定后不 可更改。
五轴加工技术简介
机械与动力工程学院
1.五轴加工技术的基本概念
五轴机床的回转中心 在机床中表示方向的坐标系原点,一般是旋转 轴之间或者旋转轴与主轴的交点
Lookahead G2 blend Wihout Lookahead
1000 500
0
五轴加工技术简介 x 10
5
0
200
400
600 T:0.004s
800
1000
Lookahead 机械与动力工程学院
- 1、下载文档前请自行甄别文档内容的完整性,平台不提供额外的编辑、内容补充、找答案等附加服务。
- 2、"仅部分预览"的文档,不可在线预览部分如存在完整性等问题,可反馈申请退款(可完整预览的文档不适用该条件!)。
- 3、如文档侵犯您的权益,请联系客服反馈,我们会尽快为您处理(人工客服工作时间:9:00-18:30)。
夹紧点 。工件腹板很薄 、 面积大 , 整体刚性差 和支撑强度低 , 为 此, 设计 了两套真空夹具 , 能很好地保证腹板 面与夹具面完全 贴合 , 在加工过程 中, 腹板始终保持刚性状态 。 能很好地减小工
据上述零件结构和技术要求介绍 , 分析可知 , 加工难点如
下几 方 面 :
( 零件腹板 薄, 1) 缘条和筋 条细 , 光面无加强筋及两端开
20 O 8年 l 2月
广 西 轻 工 业
GI AN GⅪ J 瓜 N AL o1 oF LI GHT us TRY
第 1 2期 ( 总第 l 1 ) 2 期
机 械 与 电 气
某超薄壁零件应用五轴高速加工方案
王震 宇
( 广东技术 师范学 院天河学 院 , 东 广 州 5 5 O 广 1 4) 0
口, 长径 比较大。因而 , 加工工艺刚性差 , 不具备一般 的切削支 撑强度。 精加工时 , 腹板易变形 、 易鼓动, 缘条和筋条细 , 易弹性 变形让刀 。
件变形 。 一套用于粗、 精加工格子面 , 如图 3 所示 , 另一套于粗 、
精加工光面 , 如图 4 所示。
( 内、 2) 外缘面为空间双曲面, 缘条侧 面和腹板 之间夹角
高速 加工 为佳 。
些多轴高速加工经验 , 革新了一些工艺技术方法, 较大地提高了
产品质量 和生产效率 。 由于现代飞机高性能的要求 , 零件结构具 有整体化 、 轻量化 、 薄壁化和复杂化等特点 , 为此, 广泛使用轻合 金材料制成 的薄壁结构件 , 而且, 要求生产周期越来越短。在我 厂民机转包生产中, 负责承担开发了—个项 目, 它是某型号 民用 飞机 , 垂直尾翼部件上 的零 件, 属于薄壁结构件 , 材料切除率高 达 9 %左右, 5 传统的低速加工方法变形大, 产品质量不稳定和生
6 3
43 机床 设 备 选 型 .
状态 。
选 用从意大利进 口的 FD A K l 五轴联动高速加工 中 I I 2 1 心, 机床参 数为 : 1 I 2 F D Ac 0控制 系统( c摆 轴 ) Hs A、 和 K刀 具系统 , x方 向行程 2 0 mm, 其 7o Y方向行程 1 0 mm, 0 1 z方向 行程 1 o mm, O0 A轴转 角行程 一 0 ~ 4 。 , 转角行程 1 。 + O C轴 1
42 定 位 分析 和 夹具 设计 -
一
图 1 子 面 格
一
图 2光 面采用一面
两孔定位 , 即选用腹板面和两端头大通孔 中心设一小尺寸工艺
3 零件结构 工艺性分析 和加工方案选 定
31 零 件 结 构 工艺 性 分 析 .
孔 作 为 定 位基 准 , 时 又为 夹 紧 点 , 间 大 通孔 中 心 也设 定 为 同 中
32 加 工方 案选 定 -
零件材料牌号和毛坯状态为 7 5 一 7 5 铝合金预拉伸 O 0 T 3 1 板, 材料去除量达 9 %左右。 5 若采用常规低速切削 , 那么切削加 工时间 , 占整个零件生产总时间的比例就 大 , 再加上零件加工 工艺刚性差 , 切削支撑强度低 , 加工变形大 , 那么产品质量和生 产效率很难保证 , 故尽量减少径 向切 削力 、 应力释放和热量等 因素引起变形是关键。 高速加工不但可以提高单位时间材料去 除量 , 而且随着切削速度的提高, 切削力和工件吸收 的热量也 随之降低 , 同时刀具切削的激励频率远离薄 壁结构工艺系统的 固有频率 , 因而高速机床工作平稳 、 振动少 , 能加工 出极光洁 、 精密 、 刚性差, 且因切削力 、 应力释放和热量 等因素易变形 的工 件。 基于内、 外缘面为空间双 曲面 , 缘条和腹板之间夹角不断变 化, 故五轴变角加工可 以完成此结构成形。 综合考虑 , 采用五轴
不断变化 , 筋条垂直于腹板 , 需变角加工 。 ( 材料切削去除量大 , 3) 零件精度和表面质量要求高。
图 3格子 面加 工 夹具 图 4光 面加 工 夹具
【 作者简 介 】 王震宇( 7一 , , 永州 助 1 9 )男 湖南 人, 理工 9 程师, 方向:A / A 研究 c D c M应用 。
4 数 控工艺分析
41 数 控 加 工工 艺路 线 安排 .
双 曲面 , 理论外形精度要求高 , 零件腹板 、 筋条、 缘条厚度 分别 为 1 mm、.mm、. 1 2 1 mm, 5 并且几何尺寸与形位公差 精度 , 以及 表面质量要求高 , 两端头开 口无加强筋连结。
数控工艺路线安排是 : 光面粗 、 精加工一 翻面一格子面粗 、 精加工。 利用高速加工的特点优势 , 以把粗 、 可 精加工工序一次 装夹完成 , 省去 了中间常规校正 、 时效 、 半精加工工序 , 并减少 钳工工作量等 , 这样一来, 大大缩短了零件生产周期。
【 关键词 】 五 轴高 加工; 壁零件; 速 超薄 加工变 优化程 形; 序 【 中图分类号 】T 3 G8 【 文献标识码 】 A 【 文章编号 】 10—63 o81 — 3 0 o327( o) 6 — 3 2 2
1 引言
笔者曾在某飞机制造厂从事数控技术工作多年 ,积累了一
【 摘 要 】 分析了 超薄壁零 技术 和结构工艺 制定了 件的 要求 性, 合理的五 速 轴高 数控加工工艺, 时 同 规划了 有高 具 速加工
特点的数控程序加工策略 , 解决 了超薄壁工件加 工易变形和提高生产效率的难题。 实际生产应用中, 在 五轴高速加工方案得到顺利
地 实施 , 品质 量 和效 率 方 面 已取得 了 良好 效 益 。 产
产周期长 , 努力控制加工变形和提高效率成为难题。
2 零件 结构和技 术要求
此零 件 是 飞机 垂直 尾 翼 部 件上 的重要 受 力 结 构件 , 特点 其
是细长形 , 最大外形轮廓尺寸为 :3 0× 0 ×4 。正面为有加 10 3 0 O
强 筋 的格 子 面 , 图 1 如 所示 , 面为 无 加强 筋 的光 面 , 图 2 背 如 所 示 。零 件 的大通 孔 较多 , 有 两 个小 尺 寸 通 孔 ; 、 缘 为 空 间 还 内 外