水乙二醇和甲醇 - 水和阶段的建模实验的分离效率
乙醇——水不同精馏分离操作过程塔效率的确定

乙醇——水不同精馏分离操作过程塔效率的确定李春鹏金丽军(沈阳化工学院,材料学院高分子材料0406,110142)摘要精馏是分离均相混合液的重要方法之一,化工生产中常用的精馏设备主要有填料塔和板式塔两大类,本文主要研究的是用板式塔中的筛板塔分离乙醇——水二元混合物,根据不同操作条件即精馏塔全回流和部分回流(R=3,R=5)条件下,确定理论塔板数,进而由公式ET =NT/NP*100%确定塔效率。
结论:加热电压为121V的全回流条件下塔效率为82.86%,加热电压为129V的全回流条件下塔效率为97.14%;R=3时,塔效率为98.14%,R=5时,塔效率为95.14%。
关键字:精馏乙醇——水塔效率回流比Ethanol——water distillation tower efficiency of the different operating processLichunpeng JinLijun(shenyang insitiute of chemical technology, polymer material 0406 of school of material science and engineering 110142 )AbstractDistillation is one of the important ways of the separation of the mixture,Chemical production equipment used in the main distillation towers is two kinds . This paper studies the plate tower is the sieve tower ethanol -- water mixtures . Under the distillation of the entire return and return (R = 3, R = 5) conditions .Identified a number of theoretical plates ,by E T=N T/N P*100%to determine the efficiency of tower , Conclusion: when heating voltage is 121 V under the conditions of total reflux, the tower efficiency is 82.86% ,when it is 129 V , the tower efficiency is 97.14%, when R=3 , the tower efficiency is 98.14%,and when R=5 , the tower efficiency is 95.14%Keywords :Distillation Ethanol -- water tower efficiency Reflux Ratio一引言蒸馏是借助液体混合物中各组分的挥发性的不同而进行分离的化工单元操作,若将混合物加热到沸腾(只令其部分汽化),沸点低的组分(易挥发组分或轻组分)在气相中的浓度比在液相中的浓度要高,沸点高的组分(难挥发组分或重组分)在液相中浓度比在汽相中的高。
乙醇——水不同精馏分离操作过程塔效率的确定

乙醇——水不同精馏分离操作过程塔效率的确定李春鹏金丽军(沈阳化工学院,材料学院高分子材料0406,110142)摘要精馏是分离均相混合液的重要方法之一,化工生产中常用的精馏设备主要有填料塔和板式塔两大类,本文主要研究的是用板式塔中的筛板塔分离乙醇——水二元混合物,根据不同操作条件即精馏塔全回流和部分回流(R=3,R=5)条件下,确定理论塔板数,进而由公式ET =NT/NP*100%确定塔效率。
结论:加热电压为121V的全回流条件下塔效率为82.86%,加热电压为129V的全回流条件下塔效率为97.14%;R=3时,塔效率为98.14%,R=5时,塔效率为95.14%。
关键字:精馏乙醇——水塔效率回流比Ethanol——water distillation tower efficiency of the different operating processLichunpeng JinLijun(shenyang insitiute of chemical technology, polymer material 0406 of school of material science and engineering 110142 )AbstractDistillation is one of the important ways of the separation of the mixture,Chemical production equipment used in the main distillation towers is two kinds . This paper studies the plate tower is the sieve tower ethanol -- water mixtures . Under the distillation of the entire return and return (R = 3, R = 5) conditions .Identified a number of theoretical plates ,by E T=N T/N P*100%to determine the efficiency of tower , Conclusion: when heating voltage is 121 V under the conditions of total reflux, the tower efficiency is 82.86% ,when it is 129 V , the tower efficiency is 97.14%, when R=3 , the tower efficiency is 98.14%,and when R=5 , the tower efficiency is 95.14%Keywords :Distillation Ethanol -- water tower efficiency Reflux Ratio一引言蒸馏是借助液体混合物中各组分的挥发性的不同而进行分离的化工单元操作,若将混合物加热到沸腾(只令其部分汽化),沸点低的组分(易挥发组分或轻组分)在气相中的浓度比在液相中的浓度要高,沸点高的组分(难挥发组分或重组分)在液相中浓度比在汽相中的高。
甲醇与水混合液的分离
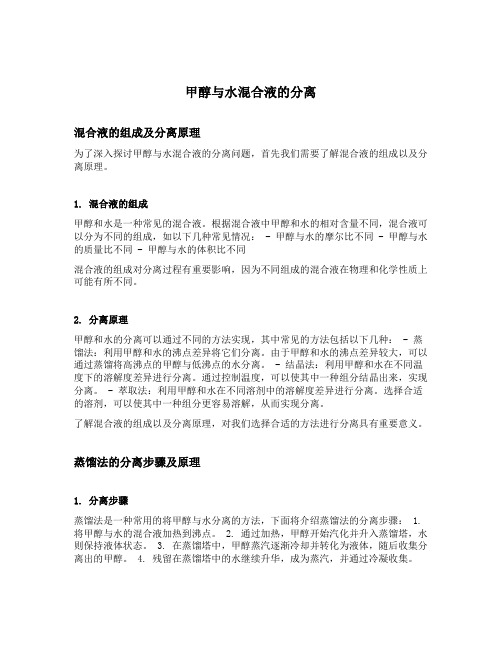
甲醇与水混合液的分离混合液的组成及分离原理为了深入探讨甲醇与水混合液的分离问题,首先我们需要了解混合液的组成以及分离原理。
1. 混合液的组成甲醇和水是一种常见的混合液。
根据混合液中甲醇和水的相对含量不同,混合液可以分为不同的组成,如以下几种常见情况: - 甲醇与水的摩尔比不同 - 甲醇与水的质量比不同 - 甲醇与水的体积比不同混合液的组成对分离过程有重要影响,因为不同组成的混合液在物理和化学性质上可能有所不同。
2. 分离原理甲醇和水的分离可以通过不同的方法实现,其中常见的方法包括以下几种: - 蒸馏法:利用甲醇和水的沸点差异将它们分离。
由于甲醇和水的沸点差异较大,可以通过蒸馏将高沸点的甲醇与低沸点的水分离。
- 结晶法:利用甲醇和水在不同温度下的溶解度差异进行分离。
通过控制温度,可以使其中一种组分结晶出来,实现分离。
- 萃取法:利用甲醇和水在不同溶剂中的溶解度差异进行分离。
选择合适的溶剂,可以使其中一种组分更容易溶解,从而实现分离。
了解混合液的组成以及分离原理,对我们选择合适的方法进行分离具有重要意义。
蒸馏法的分离步骤及原理1. 分离步骤蒸馏法是一种常用的将甲醇与水分离的方法,下面将介绍蒸馏法的分离步骤: 1. 将甲醇与水的混合液加热到沸点。
2. 通过加热,甲醇开始汽化并升入蒸馏塔,水则保持液体状态。
3. 在蒸馏塔中,甲醇蒸汽逐渐冷却并转化为液体,随后收集分离出的甲醇。
4. 残留在蒸馏塔中的水继续升华,成为蒸汽,并通过冷凝收集。
2. 分离原理蒸馏法的分离原理是基于甲醇和水的沸点差异。
甲醇的沸点为64.7摄氏度,而水的沸点为100摄氏度。
在加热过程中,甲醇优先沸腾并蒸发,而水则保持液体状态。
通过冷却和凝结,可以将甲醇重新转化为液体并分离出来,而水则通过升华形成蒸汽,并通过冷凝收集。
结晶法的分离步骤及原理1. 分离步骤结晶法是另一种常用的甲醇与水分离方法,下面将介绍结晶法的分离步骤: 1. 将甲醇与水的混合液加热至溶解状态。
乙二醇和水分离的方法
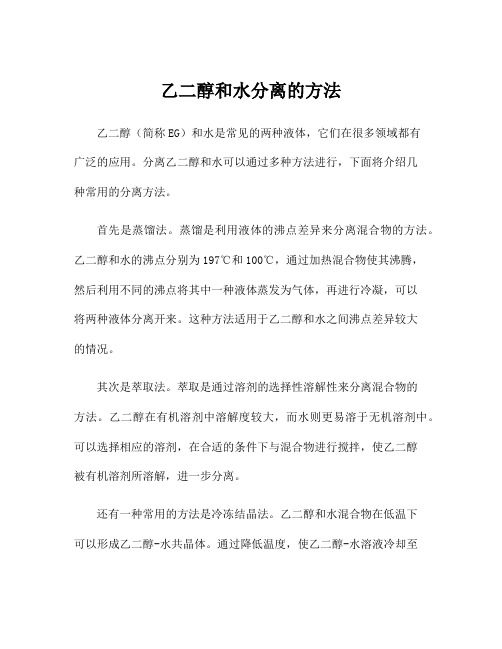
乙二醇和水分离的方法乙二醇(简称EG)和水是常见的两种液体,它们在很多领域都有广泛的应用。
分离乙二醇和水可以通过多种方法进行,下面将介绍几种常用的分离方法。
首先是蒸馏法。
蒸馏是利用液体的沸点差异来分离混合物的方法。
乙二醇和水的沸点分别为197℃和100℃,通过加热混合物使其沸腾,然后利用不同的沸点将其中一种液体蒸发为气体,再进行冷凝,可以将两种液体分离开来。
这种方法适用于乙二醇和水之间沸点差异较大的情况。
其次是萃取法。
萃取是通过溶剂的选择性溶解性来分离混合物的方法。
乙二醇在有机溶剂中溶解度较大,而水则更易溶于无机溶剂中。
可以选择相应的溶剂,在合适的条件下与混合物进行搅拌,使乙二醇被有机溶剂所溶解,进一步分离。
还有一种常用的方法是冷冻结晶法。
乙二醇和水混合物在低温下可以形成乙二醇-水共晶体。
通过降低温度,使乙二醇-水溶液冷却至共晶体形成的温度以下,可以使乙二醇结晶出来。
然后通过过滤等手段将乙二醇晶体和水分离开来。
还可以利用分子筛吸附分离法。
分子筛是一种多孔结构的固体材料,具有选择性吸附功能。
选用合适的分子筛,将乙二醇-水混合物通过吸附塔,使乙二醇在分子筛的孔径内被吸附住,而水则通过筛子流出,从而实现乙二醇和水的分离。
另外,也可以利用膜分离法进行乙二醇和水的分离。
膜分离是利用不同溶质在膜材料上的透过性和选择性来实现分离的过程。
可以选择合适的膜材料,通过渗透压或压力,将乙二醇和水分离开来。
还可以利用离心法进行分离。
通过速度梯度离心机的离心过程,利用乙二醇和水在离心力作用下的不同离心系数,从而将其分离。
综上所述,乙二醇和水的分离方法包括蒸馏法、萃取法、冷冻结晶法、分子筛吸附分离法、膜分离法和离心法等多种方法。
根据具体情况选择合适的方法,可以有效地实现乙二醇和水的分离。
aspen模拟分离乙醇和水采用乙二醇为萃取剂

采用aspen模拟乙醇和水的萃取分离本设计乙醇-水的温度组成图1
所以理论塔板数选24
故选20合适
所以第四块比较好
所以回流比取1.2
8100,考虑到回流中可没能含有水此值应大于8100,
所以可以去
由图纸当萃取剂大于
9000是浓度接近于1
选8块板
故选第四块板作为进料版
所以常压下无法达到99.95%
可见回流比为0.5后基本上不再变化
第一塔塔板,塔径设计
可见塔径1.8m
乙醇出0.225
萃取塔塔顶冷凝器
19*2 换热管长度6m,公称直径700mm,中心拍管束24,518根管子,6管城,正三角形排列,中心距25mm,换热面积182.4
25*2.5 换热长 4.5 900 26 538 6 正三角形32 185.8。
分离甲醇-水混合物化工设计
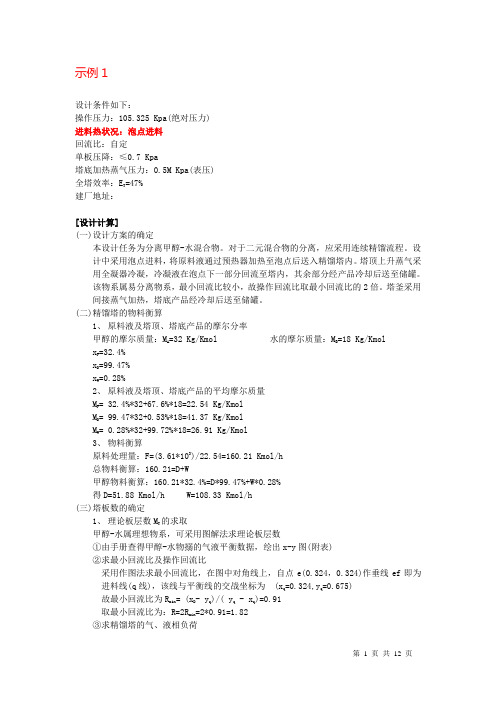
示例1设计条件如下:操作压力:105.325 Kpa(绝对压力)进料热状况:泡点进料回流比:自定单板压降:≤0.7 Kpa塔底加热蒸气压力:0.5M Kpa(表压)全塔效率:E T=47%建厂地址:[设计计算](一)设计方案的确定本设计任务为分离甲醇-水混合物。
对于二元混合物的分离,应采用连续精馏流程。
设计中采用泡点进料,将原料液通过预热器加热至泡点后送入精馏塔内。
塔顶上升蒸气采用全凝器冷凝,冷凝液在泡点下一部分回流至塔内,其余部分经产品冷却后送至储罐。
该物系属易分离物系,最小回流比较小,故操作回流比取最小回流比的2倍。
塔釜采用间接蒸气加热,塔底产品经冷却后送至储罐。
(二)精馏塔的物料衡算1、原料液及塔顶、塔底产品的摩尔分率甲醇的摩尔质量:M A=32 Kg/Kmol 水的摩尔质量:M B=18 Kg/Kmolx F=32.4%x D=99.47%x W=0.28%2、原料液及塔顶、塔底产品的平均摩尔质量M F= 32.4%*32+67.6%*18=22.54 Kg/KmolM D= 99.47*32+0.53%*18=41.37 Kg/KmolM W= 0.28%*32+99.72%*18=26.91 Kg/Kmol3、物料衡算原料处理量:F=(3.61*103)/22.54=160.21 Kmol/h总物料衡算:160.21=D+W甲醇物料衡算:160.21*32.4%=D*99.47%+W*0.28%得D=51.88 Kmol/h W=108.33 Kmol/h(三)塔板数的确定1、理论板层数M T的求取甲醇-水属理想物系,可采用图解法求理论板层数①由手册查得甲醇-水物搦的气液平衡数据,绘出x-y图(附表)②求最小回流比及操作回流比采用作图法求最小回流比,在图中对角线上,自点e(0.324,0.324)作垂线ef即为进料线(q线),该线与平衡线的交战坐标为 (x q=0.324,y q=0.675)故最小回流比为R min= (x D- y q)/( y q - x q)=0.91取最小回流比为:R=2R min=2*0.91=1.82③求精馏塔的气、液相负荷L=RD=1.82*51.88=94.42 Kmol/hV=(R+1)D=2.82*51.88=146.30 Kmol/hL ′=L+F=94.42+160.21=254.63 Kmol/h (非泡点进料要注意q 值) V ′=V=146.30 Kmol/h ④精馏段操作线方程为:y =(L/V)x + (D/V)x D =(99.42/146.30)x+(51.88/146.30)*99.47%=0.6454x+0.3527 提馏段操作线方程为:y ′=(L ′/V ′)x ′ + (W/V ′)x W =(254.63/146.30) x ′-(108.33/146.30)*0.28% =1.7405 x ′-0.0021 ⑤图解法求理论板层数采用图解法求理论板层数(附图),求解结果为: 总理论板层数:N T =13(包括再沸器) 进料板位置: N F =10 2、实际板层数的求取)1()1(A A A A --=y x x y αα%47E 047.1*(345.00= 故= 见后) μαμ=精馏段实际板层数:N 精=9/47%=20 N 提=4/47%=9(四) 精馏塔的工艺条件及有关物性数据的计算以精馏段为例进行计算1、 塔顶操作压力:P D =101.3 Kpa每层塔板压降:△P =0.7 Kpa进料板压力:P F =105.3+0.7*20=119.3 Kpa 精馏段平均压力:(105.3+119.3)/2=112.3 Kpa 2、 操作温度计算依据操作压力,由泡点方程通过试差法计算出泡点温度,其中甲醇、水的饱和蒸气压由安托尼方程计算,计算过程略,计算结果如下:塔顶温度:t D =64.6℃ 进料板温度:t F =76.3℃ 精馏段平均温度:t M =70.45℃ 3、 平均摩尔质量计算塔顶平均摩尔质量计算:由x D =y 1=0.9947,查y-x 曲线(附表),得x 1=0.986M VDm =0.9947*32+(1-0.9947)*18=31.93 M LDm =0.9860*32+(1-0.9860)*18=31.80 进料板平均摩尔质量计算 由图解理论板(附图),得 y f =0.607 x F =0.229M VFm =0.607*32+(1-0.607)*18=26.50 M LFm =0.229*32+(1-0.229)*18=21.21 所以精馏段平均摩尔质量: M Vm =(31.93+26.50)/2=29.22 M Lm = (31.80+21.21)/2=26.51 4、 平均密度计算 ⑴气相密度计算由理想气体状态方程计算,即3/15.1)45.70273(*314.822.29*3.112M Kg RT M P mV m V m m=+==ρ(这里也可以分别计算进料板与塔顶第一板的密度再取平均值) ⑵液相平均密度计算液相平均密度依下式计算,即∑=iiLmραρ1塔顶液相平均密度的计算 由t D =64.6℃ 查手册得,3B 3/K 3.980/K 745m g m g A = ρρ=3/K 7460053.09947.01m g BA LD m=+=ρρρ进料板液相平均密度的计算 由t F =76.3℃ 查手册得,3B 3/K 978/K 735m g m g A = ρρ=进料板液相的质量分量%56.3418*771.032*229.032*229.0=+=A α3/K 7.8776544.03456.01m g BA LF m=+=ρρρ⑶精馏段液相平均密度为:321/K 8122)(m g mL =+=ρρρ5、 液体平均表面张力计算⑴液相平均表面张力依下式计算,即∑=i i L x mσσ(苯、甲苯体系可用此式,醇水体系请用公式4/14/14/1o so w sw m σϕσϕσ+=来计算)塔顶液相平均表面张力的计算 由t D =64.6℃,查手册得mmN m mN m mN B A A m/ 05.190053.09947.0/ 2.65/ 8.18LD B =+===σσσσσ ⑵进料板液相平均表面张力的计算 由t F =76.3℃,查手册得mmN m mN m mN B A A m/ 35.52771.0229.0/ 7.62/ 5.17LF B =+===σσσσσ ⑶精馏段液相平均表面张力为:m mN m m mLF LD L / 7.352)(=+=σσσ6、 平均粘度的计算液相平均粘度依下式计算,即∑=iiL x m μμlg lg⑴塔顶液相平均粘度的计算 由t D =64.6℃ 查手册得,smpa smpa s mpa mmL B A L /34.0lg 0053.0lg 9947.0lg /437.0/34.0D D B A = 解得= =μμμμμμ+=⑵进料板液相平均粘度的计算 由t F =76.3℃ 查手册得smpa smpa s mpa mmL B A L /53.0lg 771.0lg 229.0lg /374.0/28.0F F B A = 解得= =μμμμμμ+=⑶精馏段液相平均表面张力为s mpa /345.0221A =)(=μμμ+(五)精馏塔的塔体工艺尺寸计算1、 塔径的计算精馏段的气、液相体积流率为:021.0)15.1812(08.110*56.8)(L )(L 20C C /10*856812*360051.26*42.94*3600/033.115.1*360022.29*30.146*360021421212.0L 20max343===-=======--V L s s V L h h V V L Lm Lm s Vm Vm s V V C u sm LM L sm VM V ρρρρσρρρρρ)(= 其中由取板间距H T =0.4m ,板上液层高度h L =0.06m ,则H T -h L =0.40-0.06=0.34m 查史密斯关联图得,C 20=0.074sm u / 204.215.115.1812083.0083.0207.35074.020C C max 2.02.0L20=-=== )()(=σ取安全系数为0.7,则空塔气速为sm sm u u / 948.0543.1*1.033*4u 4V D / 543.1204.2*7.0s max ======ππ 按标准塔径圆整后,为D=1.0m 塔截面积为22785.04m D A T ==π实际空塔气速为u=1.033/0.785=1.316s m /2、 精馏塔有效高度的计算(实际高度要注意人孔处、进料板、再沸器、塔顶空间等)精馏段有效高度为Z 精=(N 精-1)H T =(20-1)*0.4=7.6m 提馏段有效高度为Z 提=(N 提-1)H T =(9-1)*0.4=3.2m 在进料板上方开2人孔,其高度为0.8m故精馏塔有效高度为Z =N 精+N 提+0.8*2=12.4m(六)塔板主要工艺尺寸的计算1、 溢流装置计算因塔径D =1.0m ,可选用单溢流弓形降液管,采用凹形受液盘,各项计算如下:⑴塔长l W =0.66D=0.66m⑵溢流堰高度h W 由h W =h L -h OW选用平直堰,堰上液层高度h OW32)(100084.2wh ow l L E h =近似取E =1,则m h ow 93.7)66.03600*10*56.8(*1*100084.2324==-取板上清液层高度h L =60mm故m h w 33310*07.5210*93.710*60---=-=⑶弓形降液管宽度W d 和截面积A f由l w /D=0.66,查图得 A f /A T =0.0722 W d /D=0.124mD W m A A d T f 124.0124.00567.0*0722.02====验算液体在降液管中停留时间 s s L H A hTf 55.263600*10*56.840.0*0567.0*360036004>===-θ 故降液管设计合理⑷降液管底隙高度h 0mm h s m u u l L h w h006.0016.008.0*66.0*36003600*10*56.8/ 08.0*36004000>==''=-则=取故降液管底隙设计合理选用凹形受液盘,深度wh '=50mm 2、 塔板布置⑴塔板的分块因D ≥800mm ,故塔板采用分块式,且分为3块⑵边缘区宽度确定取m W m W W C S S 035.0065.0=='= ⑶开孔面积A a212221222a 532.0)465.0311.0sin 180465.0*311.0465.0311.0(2465.0035.05.02311.0)065.0124.0(5.0)(2sin 180(2A m A mW Dr m W W Dx rx r x r x a c s d =+-==-=-==+-=+-=+-=--ππ故 其中,⑷筛孔计算及其排列本例所处理的物系无腐蚀性,可选用δ=3mm 碳钢板,取筛孔直径d 0=5mm 筛孔按正三角形排列,取孔中心距t 为 t =3d 0=15 mm筛孔数目n 为个2731015.0532.0*155.1155.122===t A n a 开孔率为%1.10)015.0005.0*907.0)907.0220==((=t d ϕ气体通过阀孔的气速为 s m A V u s / 23.19532.0*101.0033.100===(七)筛板的液体力学验算1、 塔板压降⑴干板阻力h c 计算 干板阻力 )()(051.0200LVc C u h ρρ= 由d 0/δ=3/5=1.667, 得C 0=0.772 故液注0448.0)81215.1()772.023.19(051.02==c h ⑵气体通过液层的阻力h l 计算 h l =βh L21210 52.115.1418.1/418.10567.0785.0033.1ms Kgu F sm A A V u v af T s a ====-=-=ρ查图得,β=0.59故液柱m h h h h ow w L l 0354.0)10*93.710*07.52(59.0)(33=+=+==--ββ⑶液体表面张力的阻力σh 计算液体表面张力所产生的阻力σh 由下式计算液柱m gd h L L 00359.0005.0*81.9*81210*7.35*4430===-ρσσ 气体通过每层塔板的液柱高度h P 可按下式计算,即 h P =h c +h l +h σh P =0.0448+0.0354+0.00359=0.084m 液柱 气体通过每层塔板的压降为设计允许值)(7.045.66781.9*812*084.0h P p KPa g L <===∆ρ2、 液面落差对于筛板塔,液面落差很小,且本例的塔径和液流量均不大,故可忽略液面落差的影响。
甲醇与水混合液的分离
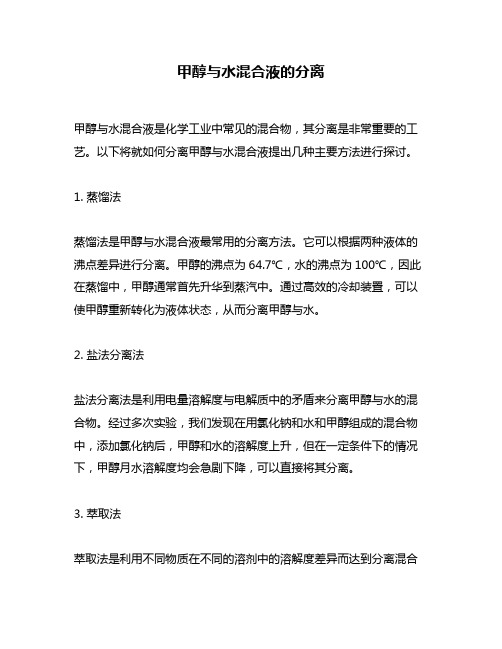
甲醇与水混合液的分离
甲醇与水混合液是化学工业中常见的混合物,其分离是非常重要的工艺。
以下将就如何分离甲醇与水混合液提出几种主要方法进行探讨。
1. 蒸馏法
蒸馏法是甲醇与水混合液最常用的分离方法。
它可以根据两种液体的沸点差异进行分离。
甲醇的沸点为64.7℃,水的沸点为100℃,因此在蒸馏中,甲醇通常首先升华到蒸汽中。
通过高效的冷却装置,可以使甲醇重新转化为液体状态,从而分离甲醇与水。
2. 盐法分离法
盐法分离法是利用电量溶解度与电解质中的矛盾来分离甲醇与水的混合物。
经过多次实验,我们发现在用氯化钠和水和甲醇组成的混合物中,添加氯化钠后,甲醇和水的溶解度上升,但在一定条件下的情况下,甲醇月水溶解度均会急剧下降,可以直接将其分离。
3. 萃取法
萃取法是利用不同物质在不同的溶剂中的溶解度差异而达到分离混合
物的目的,该方法可使用多种溶剂,比如苯、四氯化碳、正己烷等溶剂。
将混合物与所选用的溶剂进行混合,经过多次的搅拌和分离,甲
醇与水会分别部分溶解于不同的溶剂中,从而实现对甲醇与水的分离。
4. 晶体分离
晶体法是一种高效可靠,且可以大规模操作的分离方法。
这种方法是
先将甲醇与水混合物溶解,然后撞击或加热,或者根据溶液中物质的
不同挥发性,会在不同的条件下形成晶体,从而进行混合物的快速分离。
总的来说,以上提到的方法都可以用来分离甲醇与水混合液,每种方
法都有其局限性和技术难度,只有在实际应用时运用适合的真空,温度,壁厚等等工艺技术才能实现较高的分离效果。
分离甲醇—水混合液的筛板精馏塔化工原理课程设计大学论文
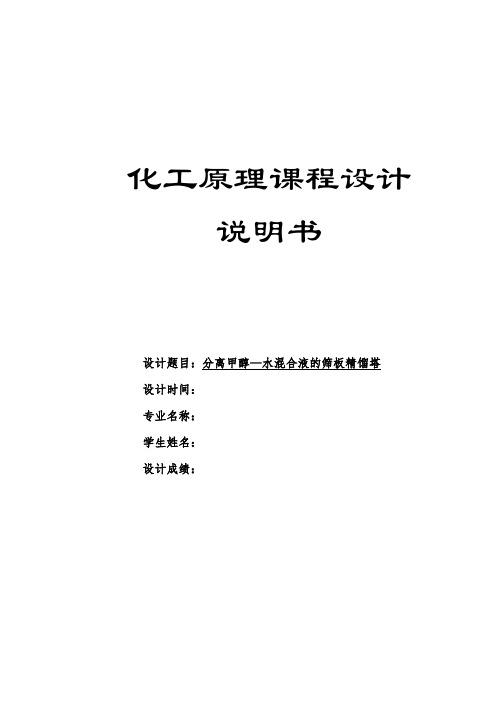
化工原理课程设计说明书设计题目:分离甲醇—水混合液的筛板精馏塔设计时间:专业名称:学生姓名:设计成绩:化工原理课程设计任务书一、设计题目分离甲醇——水混合液的筛板精馏塔二、设计数据及条件生产能力:年处理甲醇——水混合液 8.3 万吨(年开工300天)原料:轻组分含量为 40% (质量百分率,下同)的常温液体分离要求:塔顶轻组分含量不低于 93%塔底轻组分含量不高于 24%建厂地区:沈阳市三、设计要求:1、编制一份精馏塔设计说明书,主要内容要求:<1>.前言<2>.流程确定和说明<3>.生产条件确定和说明<4>.精馏塔的设计计算<5>.主要附属设备及附件的选型计算<6>.设计结果列表<7>.设计结果的自我总结评价与说明<8>.注明参考和使用的设计资料2、编制一份精馏塔工艺条件单,绘制一份带控制点的工艺流程图。
前言精馏是利用液体混合物中各组分挥发性的差异对其进行加热,然后进行多次混合蒸气的部分冷凝和混合液的部分加热汽化以达到分离目的的一种化工单元操作。
精馏操作应在塔设备中完成,塔设备提供气液两相充分接触的场所,有效地实现气液两相间的传热、传质,以达到理想的分离效果,在化工、炼油、石油化工等工业中得到广泛应用。
精馏是分离液体混合物最常用的一种单元操作,精馏过程中气液两相多次直接接触和分离,利用液相混合物个各组分的挥发度不同,使易挥发组分由液相向气相转移,实现原料液中各组分的分离。
本设计的题目是甲醇-水二元物系板式精馏塔的设计。
采用板式塔分离甲醇-水的液相混合物。
板式塔与填料塔相比用于精馏装置有诸多优势。
板式塔是逐级接触,混合物浓度呈阶跃式变化。
板式塔主要功能:在每块踏板上气液两相若保持充分接触,可为传质过程提供足够大且不断更新的相际接触面,减小传质阻力;在塔内使气液两相呈逆流流动,以提供最大的传质阻力。
板式塔可方便地住塔板安装冷却盘管。
甲醇和水分离课程设计
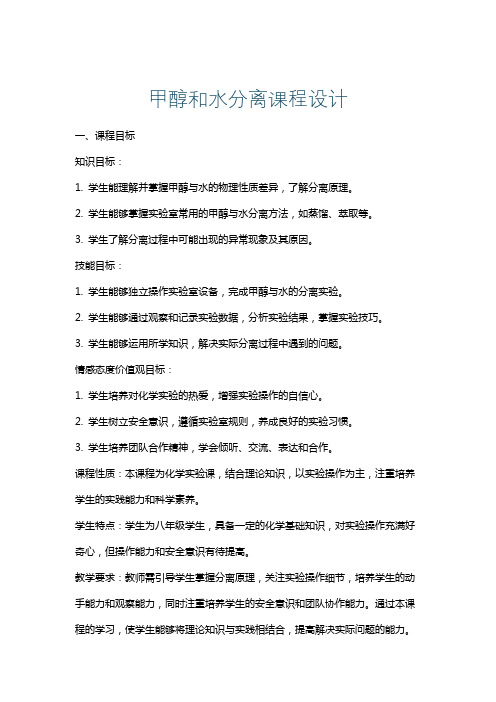
甲醇和水分离课程设计一、课程目标知识目标:1. 学生能理解并掌握甲醇与水的物理性质差异,了解分离原理。
2. 学生能够掌握实验室常用的甲醇与水分离方法,如蒸馏、萃取等。
3. 学生了解分离过程中可能出现的异常现象及其原因。
技能目标:1. 学生能够独立操作实验室设备,完成甲醇与水的分离实验。
2. 学生能够通过观察和记录实验数据,分析实验结果,掌握实验技巧。
3. 学生能够运用所学知识,解决实际分离过程中遇到的问题。
情感态度价值观目标:1. 学生培养对化学实验的热爱,增强实验操作的自信心。
2. 学生树立安全意识,遵循实验室规则,养成良好的实验习惯。
3. 学生培养团队合作精神,学会倾听、交流、表达和合作。
课程性质:本课程为化学实验课,结合理论知识,以实验操作为主,注重培养学生的实践能力和科学素养。
学生特点:学生为八年级学生,具备一定的化学基础知识,对实验操作充满好奇心,但操作能力和安全意识有待提高。
教学要求:教师需引导学生掌握分离原理,关注实验操作细节,培养学生的动手能力和观察能力,同时注重培养学生的安全意识和团队协作能力。
通过本课程的学习,使学生能够将理论知识与实践相结合,提高解决实际问题的能力。
二、教学内容本节课程依据课程目标,结合教材第十章“溶液的分离与提纯”相关内容,组织以下教学大纲:1. 理论知识:- 介绍甲醇与水的物理性质差异,如沸点、溶解度等。
- 讲解蒸馏、萃取等分离方法的原理和适用范围。
2. 实践操作:- 演示甲醇与水分离的实验操作流程,包括设备准备、操作步骤及注意事项。
- 学生分组进行实验操作,完成甲醇与水的分离。
3. 教学内容安排与进度:- 第一课时:讲解理论知识,使学生了解分离原理和方法。
- 第二课时:演示实验操作,学生观察并学习操作技巧。
- 第三课时:学生分组实验,实践分离操作,教师巡回指导。
4. 教材章节及内容列举:- 第十章“溶液的分离与提纯”:- 10.1 溶液的分离方法简介- 10.2 蒸馏与萃取- 10.3 甲醇与水的分离实验教学内容注重科学性和系统性,结合理论知识与实践操作,使学生在掌握分离原理的基础上,提高实验操作能力。
共沸精馏分离生物醇-水混合物的模拟与优化

共沸精馏分离生物醇-水混合物的模拟与优化共沸精馏(water-ethanol azeotropic distillation)是一种分离生物醇(bioalcohols)和水混合物的有效方法。
它涉及到将生物醇—水混合物分离成水和生物醇的两个组分,这两个组分具有不同的沸点和极性,因此可以通过精馏的方式分离它们。
精馏过程的仿真是可以提供详细的过程数据和最优设计参数的重要工具。
目前,使用计算机仿真技术来设计和优化共沸精馏分离生物醇—水混合物的过程受到业界的广泛关注。
在这种仿真环境下,编写精确的数学模型是很重要的,它可以有效地预测过程参数,并确定最优设计参数。
为了优化共沸精馏分离生物醇—水混合物的过程,也需要考虑过程所需的能量消耗和材料消耗,特别是在可持续发展理论的指导下,这对于制定减少能耗和材料消耗的技术方案非常重要。
因此,我们需要降低过程中多余的材料和能量消耗,在精细计算中选择最优参数,最大程度地提高最终产品的质量。
除了运用计算技术和数学模型,为了进一步推动共沸精馏分离生物醇—水混合物的优化,一些实验研究也活跃在这一领域。
实验研究主要目的是通过测试和评估不同温度、压力、循环次数和蒸馏塔的参数等条件,以优化这一过程。
此外,研究者还通过开发新型蒸馏塔,并使用新型专用塔内结构,以进一步降低能耗和材料消耗,并针对现有过程进行改进。
总之,共沸精馏分离生物醇—水混合物是一种成熟的技术,其理论和模型在不断发展与完善。
它既可以用计算技术和数学模型模拟和优化,也可以通过实验研究来进一步优化,从而最大限度地减少过程中的能耗和材料消耗,从而提高最终产品的质量。
甲醇和水混合液的分离方法

甲醇和水混合液的分离方法甲醇和水的混合液是一种常见的有机物与无机物混合体系。
在实际应用中,我们常常需要将甲醇和水进行分离,以便进一步利用它们或满足特定的需求。
对于这一问题,目前已经提出了多种有效的分离方法。
本文将对甲醇和水混合液的分离方法进行深入探讨,并提供个人的观点和理解。
1. 蒸馏法蒸馏法是一种常见且经济高效的分离方法,适用于甲醇和水之间的混合液。
这种方法利用了甲醇和水的不同沸点,通过升温使其中一种成分先沸腾,再通过冷凝散热使其转化为液体,从而实现分离。
由于甲醇和水的沸点相差较大,因此蒸馏法可以较为高效地将它们分离。
2. 萃取法萃取法是另一种常用的分离方法,适用于甲醇和水之间的混合液。
该方法利用了甲醇和水之间的亲疏性差异,通过添加特定的溶剂来实现分离。
常用的溶剂有石油醚、正己烷等。
这些溶剂能够选择性地溶解其中一种成分,从而实现分离。
3. 结晶法结晶法适用于甲醇和水之间的溶液中含有固态物质的情况。
该方法通过降温或添加适当的剂量来使其中一种成分结晶,从而实现分离。
在结晶过程中,甲醇和水的溶解度也会发生变化,利用这一特性可以将两者分离。
4. 膜分离法膜分离法是一种利用特殊透析膜的分离方法,适用于分子量较小、溶液浓度较低的甲醇和水混合液。
这种方法通过利用膜的选择性,使得其中一种成分能够通过膜而另一种成分无法通过,从而实现分离。
以上所提到的分离方法在实际应用中都有各自的优缺点。
蒸馏法是一种经济高效、广泛适用的分离方法,适合于甲醇和水之间的大量分离;萃取法则适用于对成品纯度要求较高的分离过程;结晶法适用于固态物质的去除;膜分离法适用于小分子量、低浓度的分离。
在分离甲醇和水混合液的过程中,还有一些其他的因素需要考虑,例如温度、压力和操作条件等。
这些因素会对分离效果产生影响,需要根据具体情况进行调整和优化。
对于甲醇和水混合液的分离,我们可以根据不同的需求选择适当的分离方法。
在实际应用中,需要综合考虑各种因素,选择最合适的方法以实现高效、经济的分离效果。
[优秀毕业设计精品] 分离甲醇—水混合液的连续筛板精馏塔设计
![[优秀毕业设计精品] 分离甲醇—水混合液的连续筛板精馏塔设计](https://img.taocdn.com/s3/m/7d808efa9b89680203d82532.png)
《化工原理课程设计》说明书设计题目:分离甲醇—水混合液的连续筛板精馏塔设计学院:化工与药学院专业:化学工程与工艺年级班别:09级化工工艺2班学号:学生姓名:时间:2011 年12月31日前言化工生产常需进行液体混合物的分离以达到提纯或回收有用组分的目的,精馏是利用液体混合物中各组分挥发度的不同并借助于多次部分汽化和部分冷凝达到轻重组分分离的方法。
精馏操作在化工、石油化工、轻工等工业生产中中占有重要的地位。
为此,掌握气液相平衡关系,熟悉各种塔型的操作特性,对选择、设计和分析分离过程中的各种参数是非常重要的。
塔设备是化工、炼油生产中最重要的设备类型之一。
本次设计的筛板塔是化工生产中主要的气液传质设备。
此设计苯-甲苯物系的精馏问题进行分析、选取、计算、核算、绘图等,是较完整的精馏设计过程,该设计方法被工程技术人员广泛的采用。
塔设备的设计和研究,已经受到化工行业的极大重视。
在化工生产中,塔设备的性能对于整个装置的产品产量、质量、生产能力和消耗定额,以及三废处理和环境保护等各个方面,都有非常重大的影响。
精馏过程的实质是利用混合物中各组分具有不同的挥发度。
即在同一温度下,各组分的饱和蒸汽压不同这一性质,使液相中的轻组分转移到汽相中,汽相中的重组分转移到液相中,从而达到分离的目的。
因此精馏塔操作弹性的好坏直接关系到石油化工企业的经济效益。
精馏设计包括设计方案的选取,主要设备的工艺设计计算——物料衡算、热量衡算、工艺参数的选定、设备的结构设计和工艺尺寸的设计计算,辅助设备的选型,工艺流程图,主要设备的工艺条件图等内容。
通过对精馏塔的运算,可以得出精馏塔的各种设计如塔的工艺流程、生产操作条件及物性参数是合理的,换热器和泵及各种接管尺寸是合理的,以保证精馏过程的顺利进行并使效率尽可能的提高。
关键词:甲醇水精馏段提馏段目录一、甲醇-水连续精馏塔设计条件 (1)二、设计方案的确定 (4)三、精馏塔的物料衡算 (5)四、塔板数的确定 (5)⑴理论塔板层数N t的求取 (5)⑵塔板效率和实际塔板数: (7)五、物性数据的计算 (7)⑴平均摩尔质量计算 (7)⑵操作温度计算 (8)⑶平均密度计算 (9)六、平均黏度的计算 (10)七、表面张力 (12)八、塔和塔板工艺尺寸计算 (13)九、塔板主要工艺尺寸的计算 (16)⑴溢流装置 (16)⑵塔板布置 (18)十、筛板的流体力学验算 (20)⑴塔板压降 (20)⑵液面落差 (22)⑶液沫夹带 (23)⑷漏液 (23)十一、塔板负荷性能图 (25)十三、辅助设备的计算及选型 (34)⑴原料贮罐 (34)⑵产品贮罐 (34)⑶塔顶全凝器 (36)⑷塔底再沸器 (37)⑸精馏塔 (38)⑹管径的设计 (38)⑺泵的计算及选型 (40)十三、设计评述 (41)十四、参考文献 (42)十五、设计附图 (42)一、甲醇-水连续精馏塔设计条件(1)生产能力:25000吨/年,年开工300天(2)进料组成:甲醇含量45%(质量分数)(3)采用间接蒸汽加热并且加热蒸汽压力:5 kgf/cm2(4)进料温度:采用泡点进料(5)塔顶馏出液甲醇含量99%(质量分数)(6)塔釜轻组分的浓度≤2%(本设计取0.01)(7)塔顶压强常压(8)单板压降≤0.7Kpa(9)冷却水进口温度25℃二、设计方案的确定本设计任务为甲醇-水的精馏。
分离甲醇--水混合液的筛板精馏塔的设计计算

化工原理课程设计分离甲醇-水混合液的筛板精馏塔设计潍坊学院小组成员:吴鑫李春阳袁旭目录第一章设计题目 (6)第二章工艺计算 (7)2.1精馏塔的物料衡算 (7)2.2塔板数的确定 (8)N的求取 (9)2.2.1理论板数T2.3工艺条件及有关物性数据计算 (10)2.3.1 图解法求理论塔板数 (10)2.3.2操作压力计算 (11)2.3.3 操作温度计算 (11)2.3.4相对挥发度的计算 (12)2.3.5平均摩尔质量计算 (12)2.3.6平均密度的计算 (13)2.3.7体平均表面张力计算 (15)2.3.8液体平均黏度计算 (16)2.3.9实际塔板数的计算 (17)2.4塔的主要工艺尺寸计算 (18)2.5塔板主要工艺尺寸的计算 (20)2.5.1溢流装置计算 (20)2.5.2塔板板面布置 (21)2.5.3筛孔计算及排列 (21)2.6筛板的流体力学验算 (22)2.6.1液面落差 (23)2.6.2液沫夹带 (23)2.6.3漏液 (23)2.7负荷性能图 (24)2.7.1漏液线(气相负荷下限线) (24)2.7.2 液体流量下限线 (24)2.7.3液体流量上限线 (25)2.7.4 过量液沫夹带线 (25)2.7.5 液泛线 (25)2.7.6塔板工作线 (28)第三章设计总结 (29)第四章附属设备的选型与设计 (31)4.1冷凝器的选择 (31)4.2再沸器的选择 (32)第五章塔附件的设计 (33)5.1接管的计算与选择 (33)5.1.1进料管 (33)5.1.2回流管 (33)5.1.3塔底出料管 (33)5.1.4塔顶蒸汽出料管 (34)5.1.5塔底进气管 (34)5.2 筒体 (34)5.3 封头 (34)5.4法兰的选取 (34)5.5裙座 (35)5.6人孔 (35)第六章塔总高度设计 (36)6.1塔顶部空间高度 (36)6.2塔总体高度计算 (36)第七章设计心得 (37)参考文献 (38)前言精馏是利用液体混合物中各组分挥发性的差异对其进行加热,然后进行多次混合蒸气的部分冷凝和混合液的部分加热汽化以达到分离目的的一种化工单元操作。
分离甲醇-水混合液(混合气)的填料精馏塔课程设计教材
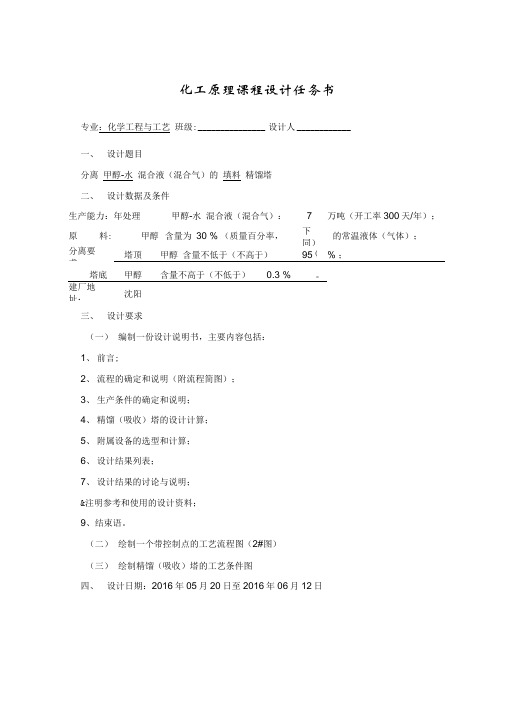
化工原理课程设计任务书专业:化学工程与工艺班级: _______________ 设计人____________一、设计题目分离甲醇-水混合液(混合气)的填料精馏塔二、设计数据及条件生产能力:年处理甲醇-水混合液(混合气):7万吨(开工率300天/年);原料: 甲醇含量为30 % (质量百分率,下同)的常温液体(气体);分离要求:塔顶甲醇含量不低于(不高于)95 (% ;塔底甲醇含量不高于(不低于)0.3 %。
建厂地址:沈阳三、设计要求(一)编制一份设计说明书,主要内容包括:1、前言;2、流程的确定和说明(附流程简图);3、生产条件的确定和说明;4、精馏(吸收)塔的设计计算;5、附属设备的选型和计算;6、设计结果列表;7、设计结果的讨论与说明;&注明参考和使用的设计资料;9、结束语。
(二)绘制一个带控制点的工艺流程图(2#图)(三)绘制精馏(吸收)塔的工艺条件图四、设计日期:2016年05月20日至2016年06月12日化工原理课程设计任务书 (1)目录 (2)前言 (4)第一章流程确定和说明 (4)1.1加料方式的确定 (5)1.2进料状况的确定 (5)1.3冷凝方式的确定 (5)1.4回流方式的确定 (5)1.5加热方式的确定 (6)1.6加热器的确定 (6)第二章精馏塔设计计算 (6)2.1操作条件与基础数据 (6)2.1.1操作压力 (6)2.1.2气液平衡关系与平衡数据 (7)2.2精馏塔工艺计算 (7)2.2.1物料衡算 (7)2.2.2热量衡算 (11)2.2.3理论塔板数计算 (14)2.3精馏塔主要尺寸的设计计算 (15)2.3.1精馏塔设计主要依据和条件 (15)2.3.2塔径设计计算 (22)2.3.3填料层高度的设计计算 (24)第三章附属设备及主要附件的选型计算 (26)3.1冷凝器 (26)3.2加热器 (27)3.3塔内其他构件 (28)3.3.1接管管径的选择 (28)3.3.2除沫器 (30)3.3.3液体分布器 (31)3.3.4液体再分布器 (33)3.3.5填料及支撑板的选择 (33)3.3.6塔釜设计 (33)3.3.7塔的顶部空间高度 (34)3.4精馏塔高度计算 (34)第四章设计结果自我总结和评价 (35)4.1精馏塔主要工艺尺寸与主要设计参数汇总 (35)4.2自我评价和总结 (35)4.21满足工艺和操作的要求 (36)4.2.2满足经济上的要求 (36)4.2.3保证生产安全 (36)4.3总结 (36)附录 (38)一、................................................................................................................... 符号说明38二、................................................................................................................... 参考文献39、八、■刖言在化学工业和石油工业中广泛应用的诸如吸收、解吸、精馏、萃取等单元操作中,气液传质设备必不可少。
精馏和共沸相结合分离乙二醇单甲醚、甲醇和水的方法
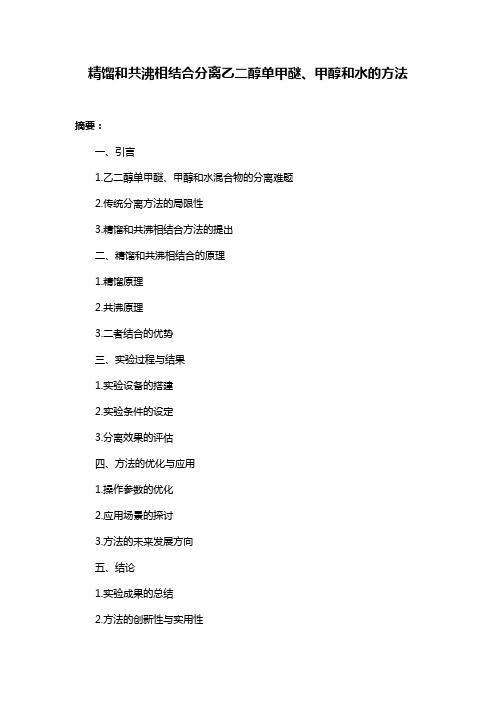
精馏和共沸相结合分离乙二醇单甲醚、甲醇和水的方法摘要:一、引言1.乙二醇单甲醚、甲醇和水混合物的分离难题2.传统分离方法的局限性3.精馏和共沸相结合方法的提出二、精馏和共沸相结合的原理1.精馏原理2.共沸原理3.二者结合的优势三、实验过程与结果1.实验设备的搭建2.实验条件的设定3.分离效果的评估四、方法的优化与应用1.操作参数的优化2.应用场景的探讨3.方法的未来发展方向五、结论1.实验成果的总结2.方法的创新性与实用性3.对相关领域的启示与借鉴意义正文:一、引言乙二醇单甲醚、甲醇和水是一种常见的混合物,它们的分离一直是化工领域的一个难题。
传统的分离方法,如蒸馏、萃取等,存在分离效率低、能耗高、操作复杂等问题。
因此,研究一种高效、节能、操作简便的分离方法具有重要的实际意义。
本文提出了一种精馏和共沸相结合的方法,对乙二醇单甲醚、甲醇和水的混合物进行分离,取得了良好的效果。
二、精馏和共沸相结合的原理1.精馏原理:精馏是利用混合物中各组分挥发度的差异进行分离的方法。
在精馏过程中,混合物加热至沸腾,挥发性较高的组分首先蒸发,然后通过冷却器冷却成为液体,从而实现分离。
2.共沸原理:共沸是指两种或多种液体在一定条件下可以共沸混合,形成共沸混合物。
通过共沸混合物,可以实现混合物中某些组分的分离。
3.二者结合的优势:精馏和共沸相结合的方法充分利用了两种方法的优点,既可以实现高挥发性组分的分离,又可以降低能耗,提高分离效率。
三、实验过程与结果1.实验设备的搭建:根据实验需求,搭建了一套精馏和共沸相结合的实验设备,包括加热装置、蒸馏装置、冷却装置等。
2.实验条件的设定:根据乙二醇单甲醚、甲醇和水的物性数据,设定了一系列实验条件,如加热温度、冷却温度等。
3.分离效果的评估:通过实验观察到了乙二醇单甲醚、甲醇和水的分离过程,并对分离效果进行了评估。
实验结果表明,精馏和共沸相结合的方法可以实现乙二醇单甲醚、甲醇和水的有效分离。
化工甲醇合成工艺的化学质量平衡建模与控制
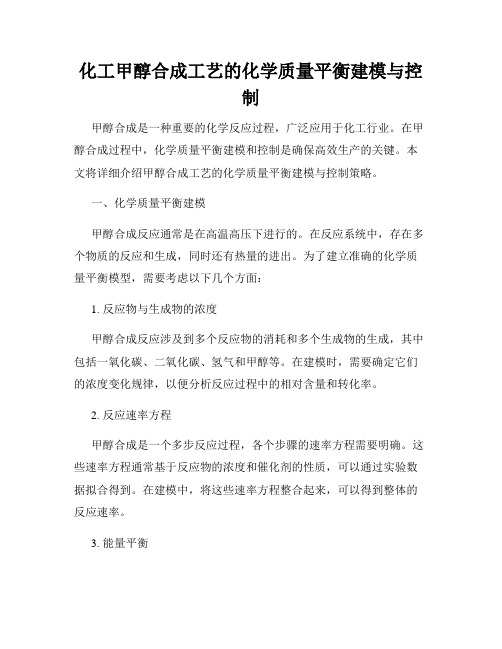
化工甲醇合成工艺的化学质量平衡建模与控制甲醇合成是一种重要的化学反应过程,广泛应用于化工行业。
在甲醇合成过程中,化学质量平衡建模和控制是确保高效生产的关键。
本文将详细介绍甲醇合成工艺的化学质量平衡建模与控制策略。
一、化学质量平衡建模甲醇合成反应通常是在高温高压下进行的。
在反应系统中,存在多个物质的反应和生成,同时还有热量的进出。
为了建立准确的化学质量平衡模型,需要考虑以下几个方面:1. 反应物与生成物的浓度甲醇合成反应涉及到多个反应物的消耗和多个生成物的生成,其中包括一氧化碳、二氧化碳、氢气和甲醇等。
在建模时,需要确定它们的浓度变化规律,以便分析反应过程中的相对含量和转化率。
2. 反应速率方程甲醇合成是一个多步反应过程,各个步骤的速率方程需要明确。
这些速率方程通常基于反应物的浓度和催化剂的性质,可以通过实验数据拟合得到。
在建模中,将这些速率方程整合起来,可以得到整体的反应速率。
3. 能量平衡甲醇合成反应是一个放热反应,需要考虑到能量的进出。
在建模过程中,需要确定热量的转移方式,以及反应系统中的温度变化规律。
通过能量平衡的建模,可以更好地控制反应过程的温度以及相关的热量收支。
二、化学质量平衡控制甲醇合成工艺的化学质量平衡控制旨在确保反应的高效进行和产物的高纯度。
以下是几个常用的控制策略:1. 副反应的抑制甲醇合成反应中存在一定副反应的产生,如醇醚和甲醇水合物的生成。
这些副反应会降低反应的选择性和产物的纯度。
通过改变反应条件和催化剂的选择,可以有效抑制副反应的发生。
2. 适当的催化剂添加催化剂在甲醇合成反应中起到重要的作用。
通过调整催化剂的成分和添加量,可以提高反应速率和产物的选择性。
此外,催化剂的再生和使用寿命也需要注意,及时更换和修复催化剂可以保证反应系统的稳定运行。
3. 温度和压力控制甲醇合成反应对温度和压力的控制较为敏感。
在建模时,可以根据反应热力学性质和实际需求确定合适的温度和压力范围。
通过控制温度和压力的变化率,可以实现对反应的调控和优化。
化工模拟实训作业(甲醇-水精馏分离过程模拟计算 )
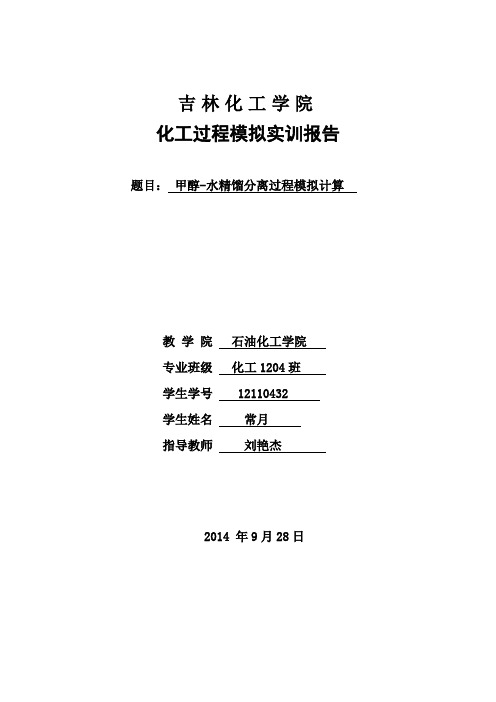
吉林化工学院化工过程模拟实训报告题目:甲醇-水精馏分离过程模拟计算教学院石油化工学院专业班级化工1204班学生学号 12110432学生姓名常月指导教师刘艳杰2014 年9月28日1、软件功能简介Aspen Plus是一个生产装置设计、稳态模拟和优化的大型通用流程模拟系统。
AspenPlus是大型通用流程模拟系统,源于美国能源部七十年代后期在麻省理工学院(MIT)组织的会战,开发新型第三代流程模拟软件。
该项目称为“过程工程的先进系统”,并于1981年底完成。
1982年为了将其商品化,成立了AspenTech公司,并称之为Aspen Plus。
该软件经过20多年来不断地改进、扩充和提高,已先后推出了十多个版本,成为举世公认的标准大型流程模拟软件,应用案例数以百万计。
Aspen Plus是AspenTech工程套装软件(AES)的一个成员,它是一套非常完整产品,特别对整个工厂、企业工程流程工程实践和优化和自动化有着非常重要的促进作用。
自动的把流程模型与工程知识数据库、投资分析,产品优化和其它许多商业流程结合。
Aspen Plus包括数据,物性,单元操作模型,内置缺省值,报告及为满足其它特殊工业应用所开发的功能。
比如像电解质模拟,Aspen Plus主要的功能如下:(1)Windows交互性界面(2)图形向导(3)EO模型(4)ActiveX (OLE Automation)控件全面的单元操作:包括气/液,气/液/液,固体系统和用户模型。
(1)ACM Model Export选项(2)热力学物性(3)收敛分析(4)Calculator models 计算模式(5)灵敏度分析(6)案例研究(7)Design Specification 功能:(8)数据拟合(9)优化功能(10)开放的环境2、已知基础数据及分离任务(1)已知基础数据F1:35℃,101kPa,1000 kg/hr的甲醇(62%w)-水(38%w)。
分离甲醇-水双组分均相混合物常压连续精馏筛板塔 课程设计

希腊字母
δ θ υ ρ σ φ α ----筛板的厚度 m ----液体在降液管内停留的时间 s ----粘度 mPa.s ----密度 kg/m3 ----表面张力 N/m ----开孔率 无因次 ----质量分率 无因次
目
录
一、 概述................................................................................................................................... 5 1. 精馏操作对塔设备的要求和类型 ................................................................................... 5 2.精馏塔的设计步骤 ............................................................................................................. 7 二、 精馏塔的热量衡算 ........................................................................................................... 7 1. 全凝器的热量衡算: ....................................................................................................... 7 2. 再沸器的热负荷............................................................................................................... 8 三、 精馏塔的物料衡算 .............................................................................. 8 1. 原料液及其塔顶、塔底产品的摩尔分率 ....................................................................... 8
甲醇 水 分离精度
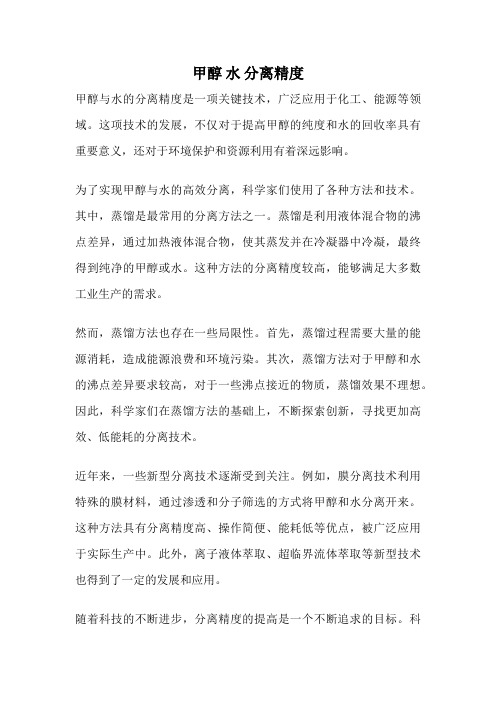
甲醇水分离精度甲醇与水的分离精度是一项关键技术,广泛应用于化工、能源等领域。
这项技术的发展,不仅对于提高甲醇的纯度和水的回收率具有重要意义,还对于环境保护和资源利用有着深远影响。
为了实现甲醇与水的高效分离,科学家们使用了各种方法和技术。
其中,蒸馏是最常用的分离方法之一。
蒸馏是利用液体混合物的沸点差异,通过加热液体混合物,使其蒸发并在冷凝器中冷凝,最终得到纯净的甲醇或水。
这种方法的分离精度较高,能够满足大多数工业生产的需求。
然而,蒸馏方法也存在一些局限性。
首先,蒸馏过程需要大量的能源消耗,造成能源浪费和环境污染。
其次,蒸馏方法对于甲醇和水的沸点差异要求较高,对于一些沸点接近的物质,蒸馏效果不理想。
因此,科学家们在蒸馏方法的基础上,不断探索创新,寻找更加高效、低能耗的分离技术。
近年来,一些新型分离技术逐渐受到关注。
例如,膜分离技术利用特殊的膜材料,通过渗透和分子筛选的方式将甲醇和水分离开来。
这种方法具有分离精度高、操作简便、能耗低等优点,被广泛应用于实际生产中。
此外,离子液体萃取、超临界流体萃取等新型技术也得到了一定的发展和应用。
随着科技的不断进步,分离精度的提高是一个不断追求的目标。
科学家们正在不断探索新的材料和技术,以提高甲醇与水分离的效率和精度。
他们希望通过改进现有的分离方法,或者发展新的分离技术,实现甲醇与水的高效分离,为产业发展和环境保护做出更大的贡献。
甲醇与水的分离精度是一个关键技术,对于化工、能源等行业具有重要意义。
科学家们通过不断创新和探索,致力于提高分离技术的效率和精度,以满足不同领域的需求。
他们的努力将促进产业发展,推动可持续发展的进程。
我们期待着这个技术在未来的应用中取得更大的突破和进展。
- 1、下载文档前请自行甄别文档内容的完整性,平台不提供额外的编辑、内容补充、找答案等附加服务。
- 2、"仅部分预览"的文档,不可在线预览部分如存在完整性等问题,可反馈申请退款(可完整预览的文档不适用该条件!)。
- 3、如文档侵犯您的权益,请联系客服反馈,我们会尽快为您处理(人工客服工作时间:9:00-18:30)。
Available online at Chemical Engineering and Processing47(2008)209–214Separation efficiency of thin-film evaporators:Experiments withwater–ethylene glycol and methanol–water and stage-based modelingFrank Schaal,Klemens Schilling,Hans Hasse∗Institute of Thermodynamics and Thermal Process Engineering,Universit¨a t Stuttgart,D-70550Stuttgart,GermanyReceived23November2006;received in revised form22February2007;accepted26February2007Available online3March2007AbstractThin-film evaporators are often used for separations.Despite the long-standing research in this area,there is still a lack of reliable data on measurements on test systems that could be used for model development and validation.In this research,therefore,the partial evaporation of the binary mixtures of ethylene glycol and water as well as water and methanol is studied in a laboratory-scale thin-film evaporator operated in counter-current mode.Two types of equilibrium stage models of the separation process are tested,in which the process is described as open and closed evaporation,respectively.The results show that,especially at low vapor streams,a considerable rectification effect occurs in the thin-film evaporator that can only be modeled using the closed evaporation approach.The equilibrium stage approach is sufficient for describing the data from the present work.©2007Elsevier B.V.All rights reserved.Keywords:Thin-film evaporator;Separation;Modeling;Ethylene glycol;Water;Methanol1.IntroductionThis research focuses on the use of thin-film evaporators for separations.The general advantages of thin-film evapora-tors are short residence times and small temperature differences required for heating[1].Billet[2,3]and Skoczylas and Dziak[4] have studied the separation efficiency of thin-film evaporators using the binary systems methanol–ethanol,methanol–water, water–ethylene glycol,and acetone–n-butanol.However,the data basis provided in that research is not wide,and most of the results are only presented in graphical form.The present work aims at extending the available data by providing experimental data for the systems water–ethylene glycol and methanol–water. These non-reactive test systems were chosen to complement studies on reacting solutions containing formaldehyde,water, and methanol[5–7].Abbreviations:GC,gas chromatograph;GOX,glycerine oxethylate;HP, Hewlett-Packard;PTFE,polytetrafluoroethylene/teflon;TEG,tri-ethylene gly-col;TCD,thermal conductivity detector∗Corresponding author.Tel.:+4971168566105;fax:+4971168566140.E-mail address:hasse@itt.uni-stuttgart.de(H.Hasse).The second target of this investigation is to analyze how accurately stage-based models can describe the separation in thin-film evaporators.Rate-based modeling is not addressed in this short contribution.However,the experimental data are pre-sented in a way so that they can be used for comparisons with such more sophisticated models at any time.Two different stage-based modeling approaches are discussed:the open and closed evaporation.In open evaporation,it is assumed that the vapor is separated from the liquid immediately after the evaporation. Hence,there is no difference between counter-and co-current and no rectification effects can occur.In closed evaporation,the vapor remains in contact with the liquid so that counter-and co-current can be distinguished and rectification effects can be modeled.It turns out that the latter model allows a descrip-tion of the data from the present work.The question of the appropriate choice of the number of stages used in the model is addressed.2.ExperimentsAll experiments were carried out using a laboratory-scale thin-film evaporator,cf.Fig.1.The evaporator(QVF Engineer-ing GmbH,Mainz)consists of a vertical glass tube with a heating jacket,which is thermostated by a liquid.The heatingfluids0255-2701/$–see front matter©2007Elsevier B.V.All rights reserved. doi:10.1016/j.cep.2007.02.018210F .Schaal et al./Chemical Engineering and Processing 47(2008)209–214Fig.1.Flow sheet of the thin-film evaporator.were chosen as follows:for evaporation temperatures below 100◦C distilled water,for temperatures between 100and 150◦C tri-ethylene glycol (TEG),for higher temperatures glycerine oxethylate (GOX).The total length of the evaporator is 732mm,the inner diameter is 50mm,the wiped length is 300mm.The stirrer inside consists of three PTFE rotor blades,a so-called Smith rotor.The blades have slanted teeth to enhance mixing and transport of the film.The liquid is distributed to the inner wall by centrifugal force using a turning ring device.There are temperature-measuring points on the product side in the gas phase in the bottom and the head of the evaporator.Temperature data were taken in the experiments but are believed to be inaccurate,due to low vapor flow rates and probably addi-tional problems with the processing unit.On the heating side only the temperature of the thermostat bath is known.There-fore,the present study does not supply useful information on heat transfer,and consequently no temperature data is reported at all.Temperatures can be estimated from the model presented below.The feed is continuously pumped into the evaporator (diaphragm metering pump by ProMinent,Heidelberg,model gamma-RS),the head product (after condensation)and the bot-tom product are pumped out level controlled (diaphragm pumps by Telab,Moers,model BF414).The flow rates of feed,head product and bottom product are measured by means of balances,with which the mass changes in feed and product containers are monitored.The ‘evaporation rate’(ER)is defined as the quotient of the head and the feed mass flow.The compositions of the inlet and outlet streams are investi-gated by gas chromatography.The gas chromatograph used is a Hewlett-Packard HP 6890with a HP-INNOWax Polyethylene Glycol HP 19091N-213capillary and a thermal conductivity detector (TCD).The samples of the head and bottom productswere taken in stationary state,which was attained in 15–20min in most cases.All experiments that are presented in the following were conducted at constant pressure (20and 40kPa,respectively for methanol–water,10kPa for ethylene glycol–water),which was controlled and measured by a unit from MKS Instru-ments,Munich.The rotation speed of the stirrer was adjusted to 300min −1.In test runs the rotation speed was varied between 200and 1500min −1without any significant influence on the results.The feed flow rate varied between 0.5and 1.1kg h −1,again without significant influence on the results.For each of the two studied systems,three feed compositions were stud-ied.For each composition,the evaporation rate ER was varied over the entire accessible range by changing the heating fluid temperature.For controlling the heating fluid temperature,a thermostat (type MV4of Julabo,Seelbach)was used.Only the bath temperature is known,but not reported here.The results are fully documented in Table 1(water–ethylene glycol)and Table 2(methanol–water).The overall mass balance was fulfilled with a relative accuracy of typically 1%.For the component mass balances that number is 1.5%.The estimated accuracies are 1%(relative)for the mass flows,1%(relative)for the pressure,and 0.3%(absolute)for the mass fractions.3.ModelingThe modeling of the thin-film evaporation is based on the simple concept of equilibrium stages in the present work.Two different approaches,open and closed evaporation,are used.They are introduced in Fig.2.In multi-stage open evaporation,it is assumed that the gas phase does not have any contact with the liquid phase in other stages—this would correspond to a fast gas flow in the center of the thin-film evaporator basically withoutF .Schaal et al./Chemical Engineering and Processing 47(2008)209–214211Table 1Experimental results for water–ethylene glycol (p =10kPa)x F W(g g −1)˙m H (kg h −1)˙m B (kg h −1)x H W (g g −1)y B W(g g −1)0.150.0670.4230.8810.0280.0770.4150.8820.0140.0940.5110.8800.0160.0970.5270.8970.0140.0990.5620.8780.0210.1070.9360.9540.0610.1230.9450.9390.0410.1390.8530.8880.0320.1410.8620.9050.0260.1580.8480.8520.0150.1610.8700.8940.0180.1760.7940.7780.0070.2110.7700.6860.0050.2590.4170.3820.0030.500.0960.9660.9940.4420.2240.8540.9920.3640.3180.7550.9900.2920.3670.6080.9840.1990.3960.5500.9740.1600.4180.5450.9750.1210.4380.5070.9670.0970.4540.4820.9580.0720.4630.5090.9350.1060.5200.5080.9300.0540.5400.4820.9010.0490.800.2980.6770.9970.7080.4250.4830.9960.6270.4330.4780.9960.6200.4500.5290.9970.6200.4790.5790.9970.6280.6340.3790.9950.4670.6460.3900.9950.4570.6940.3170.9950.3640.7160.2700.9750.2950.7500.2720.9930.2610.7550.2210.9820.1650.7590.2470.9720.2350.7700.2070.9690.1510.7780.2490.9820.2310.7940.2850.9880.2480.8160.2290.9750.171Fig.2.Flow sheet of four-stage open evaporation (left)and four-stage closed evaporation in counter-current (right).any interaction with the liquid film at the wall.In contrast,in multi-stage closed evaporation a contact between the upward flow of the gas and the downward flow of the liquid enhances the separation efficiency.Each stage is heated.Both the number of stages as well as the heat supplied to each stage or alternatively the evaporation rate in each stage need to be specified.The number of equilibrium stages was varied here to study its influence,since no infor-mation on the appropriate choice of that number is available in advance.The heat supplied to each stage was assumed to be the same for all stages for simplicity.After specifying these parameters together with the feed flow rate and composition,the only remaining parameter is the evaporation rate ER,for which the experimental value was used.The most important result from the simulation is the composition of the head and bottom product of the evaporator.Since the feed is supplied at the upper end of the wiped range,it is also supplied to the top stage of the model.Condensation in the top of the evaporator above the feed point may enhance the separation,especially if vapor streams are small.Some con-densation was observed in the experiments in the evaporator top,but the effect of that condensation on the separation in the experiments is believed to be small.It is not described by the model.The physical properties of the pure fluids and the binary mix-tures were obtained from the ASPEN database.The Wilson method was used for the description of the binary interac-tions.The vapor-liquid equilibria of the studied systems are well described by that resulting model,at given temperature and liq-uid phase composition,the mean deviation of the vapor phase composition does not exceed 0.01mol/parison of experiments and simulation 4.1.Water–ethylene glycolIn Figs.3–6,the head and bottom concentration of the low boiling substance,water,are shown as a function of the evap-oration rate.Fig.3is a magnified view of the most interesting part of Fig.5.Experimental results are represented bysym-Fig.3.Model vs.experimental results for water–ethylene glycol,enlarged.x F W=0.5g g −1,p =10kPa.212F .Schaal et al./Chemical Engineering and Processing 47(2008)209–214Table 2Experimental results for methanol–water p (kPa)x F M(g g −1)˙m H (kg h −1)˙m B (kg h −1)y H M (g g −1)x B M(g g −1)200.1880.1680.6860.5950.0910.1980.6660.5670.0670.2480.6060.5290.0440.3210.5310.4710.0190.3530.4970.4420.0120.4160.4230.3780.0040.4970.3480.3170.0010.5960.2480.2600.0000.6800.1850.2340.001400.2700.2000.5550.7020.1200.2810.4910.5830.0740.3440.4160.5670.0310.4910.2600.4350.002400.7060.2610.4920.8990.6040.3630.3960.8880.5320.4310.3180.8840.4610.5140.2420.8690.3390.5670.1790.8470.2530.6240.1230.8050.162bols,model predictions by lines.The wider the gap between head and bottom concentrations at a constant evaporation rate is,the better is the corresponding separation efficiency.The observed results are strongly influenced by the feedcomposi-Fig. 4.Model vs.experimental results for water–ethylene glycol,x F W=0.8g g −1,p =10kPa.Fig. 5.Model vs.experimental results for water–ethylene glycol,x F W=0.5g g −1,p =10kPa.tion,as can be understood by considering the mass balance.For evaporation rates in the range of the mass concentration of the low boiling substance in the feed,large changes are observed.The simulation results show the expected trends:the cal-culated separation efficiency increases with the number of equilibrium stages.In Fig.3,results for 1–30stages are ing more than eight stages leads only to little further change.Of course,there is no difference between open and closed evaporation for one stage.For the multi-stage process,the separation efficiency of the closed evaporation is better than for the open paring the results from the simu-lations with those from the experiments,it can be seen that,as expected,the experimental separation efficiency is better than that of a single equilibrium stage.These trends were observed for all experiments.For the further discussion only modeling results for an eight-stage open evaporation and an eight-stage closed evaporation are used,see Figs.4–6.The choice of that particular number should not be interpreted physically.It ismoreFig. 6.Model vs.experimentalresults for water–ethylene glycol,x F W=0.15g g −1,p =10kPa.F .Schaal et al./Chemical Engineering and Processing 47(2008)209–214213Fig.7.Model vs.experimental results for methanol–water,x F M=0.706g g −1,p =40kPa.a question of discretization,and the number 8was simply consid-ered here to be sufficiently large.Note that all stages are heated and the influence of the stage number on the separation is much smaller than in distillation.Figs.4–6show that the experimental separation efficiency depends on the evaporation rate.For very high or low evapora-tion rates (close to 1or 0,respectively),the process is determined by mass balances.The most interesting effects occur at evapo-ration rates close to the feed concentration of the low boiling substance.A comparison of experiments and simulations in that region shows that for high evaporation rates (0.8,cf.Fig.4),the separation is reasonably described by an open evaporation,whereas for low evaporation rates (0.15,cf.Fig.6)the closed evaporation model is more appropriate.This finding is not unex-pected as small evaporation rates correspond to small gas flow rates and,hence,to a longer contact between gas and liquid,resulting in a better separation.This effect has already been described by Ref.[3].4.2.Methanol–waterCompared to the water–ethylene glycol system,the sep-aration of methanol and water is more difficult.Hence,the difference between the open and closed evaporation is by far larger.As for the water–ethylene glycol system,onlymodelingFig.8.Model vs.experimental results for methanol–water,x F M=0.27g g −1,p =40kPa.Fig.9.Model vs.experimental results for methanol–water,x F M=0.188g g −1,p =20kPa.results for an eight-stage open evaporation and an eight-stage closed evaporation are shown,see Figs.7–9.As already seen for the water–ethylene glycol system,also for the methanol–water system the separation efficiency decreases with increasing evaporation rates.At high evaporation rates (0.706,cf.Fig.7),the experimental results are well described by the open evaporation model,at low evaporation rates (0.188,cf.Fig.9),the closed evaporation is the better model.Especially for practical purposes it is interesting to note that within the experimental accuracy,all results lie between the lines resulting from these two modeling concepts so that they can be used for defining the range in which experimental results are expected.It should also be noted that in contrast to the conclusions of Ref.[4,8,9],our results for the methanol–water system show a considerable rectification effect.5.ConclusionsExperimental results from the partial evaporation of the binary mixtures of ethylene glycol and water as well as water and methanol in a thin-film evaporator are reported.The results can be described using the simple equilibrium stage model.Modeling results only vary for evaporation rates close to the feed concentration of the low boiler.At low evaporation rates (0.1–0.2)a considerable rectification effect occurs that can only be modeled using the closed evaporation approach whereas at high evaporation rates (0.7–0.8)the open evaporation model is more appropriate.AcknowledgementThanks are due to Alexei Gortychov,Universit¨a t Stuttgart,for his contributions to the experimental part of this work.Appendix A.Nomenclature ER evaporation rate (g g −1)˙m mass flow (kg h −1)p pressure (Pa)x imass fraction of the component i in the liquid phase (g g −1)214F.Schaal et al./Chemical Engineering and Processing47(2008)209–214y i mass fraction of the component i in the gas phase(g g−1)SuperscriptsB bottomF feedH headSubscriptsi component iM methanolW waterReferences[1]B.Kaiser,M.Kranz,D¨u nnschichtverdampfer in der thermischen Trenntech-nik,Vakuum in Forschung und Praxis2(1999)71–77.[2]R.Billet,D¨u nnschichtdestillation in der Verfahrens-und Umwelttechnik,Chemie-Technik19(1990)50–55.[3]R.Billet,Trennleistung von D¨u nnschichtverdampfern,Chem.Ing.Tech.72(2000)565–570.[4]A.Skoczylas,J.Dziak,Separation efficiency of thin-layer evaporators,Com-put.Chem.Eng.14(1990)1001–1007.[5]K.Schilling,M.Sohn, E.Str¨o fer,H.Hasse,Reaktive Verdampfungformaldehydhaltiger Mischungen und Process Monitoring mit Online NMR-Spektroskopie,Chem.Ing.Tech.75(2003)240–244.[6]M.Maiwald,T.Gr¨u tzner,E.Str¨o fer,H.Hasse,Quantitative NMR spec-troscopy of complex technical mixtures using a virtual reference:chemical equilibria and reaction kinetics of formaldehyde–water–1,3,5-trioxane, Anal.Bioanal.Chem.385(2006)910–917.[7]T.Gr¨u tzner,H.Hasse,Solubility of formaldehyde and trioxane in aqueoussolutions,J.Chem.Eng.Data49(2004)642–646.[8]R.Billet,Trennung von Fl¨u ssigkeitsgemischen durch teilweise Destillation,Chem.Ing.Tech.29(1957)733–742.[9]K.Dieter,Leistungsverhalten von D¨u nnschichtverdampfern II(Stof-faustauschzahlen beim Destillieren),Chemiker-Zeitung94(1970)445–451.。