短行程中立辊二项式控制方式的应用
%a2立辊调宽短行程控制模拟研究与应用
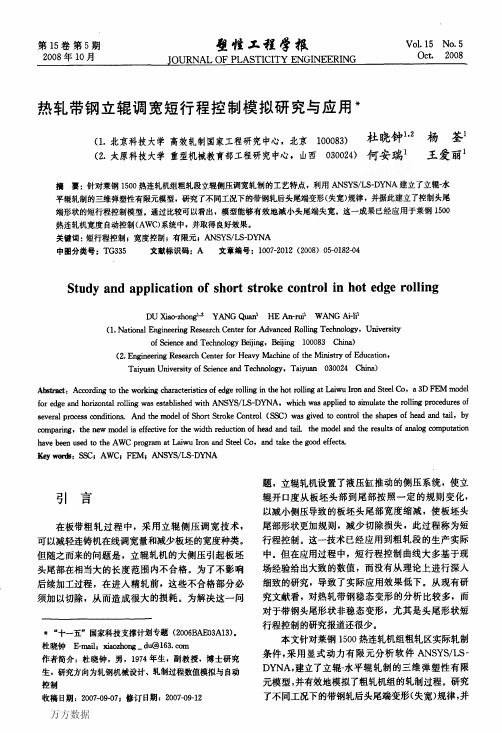
Key words:SSC,AwCI FEM;ANSYS/LS—DYNA
引言
在板带粗轧过程中,采用立辊侧压调宽技术, 可以减轻连铸机在线调宽量和减少板坯的宽度种类。 但随之而来的问题是,立辊轧机的大侧压引起板坯 头尾部在相当大的长度范围内不合格。为了不影响 后续加工过程,在进入精轧前,这些不合格部分必 须加以切除,从而造成很大的损耗。为解决这一问
3D删model
a
for edge and horizontal rolling WaS established with ANSYS/LS—DYNA.which was applied to simulate the rolling procedures of
several process conditions.And the nlodel of Short Stroke Control(SSC)was gived to control the shapes of head and tail,by
、一 一一 ≮
~
头 部
.-一短行程辊缝设定——◆
、 - 一一
一- 一一
尾
端
SS
朔.件长度
SS
图1短行程控制原理示意图 Fig.1 Diagram of SSC principle
2 ANSYS/LS—DYNA有限元模型
模拟采用显式动力弹塑性有限元法,轧件采用 双线性随动强化弹塑性材料模型。轧辊采用刚性材 料模型,用具有·定厚度的辊环建立几何模型;轧 辊与轧件均用六面体实体单元划分网格;轧辊与轧 件间的接触摩擦采用库仑摩擦。为减少计算时间, 利用轧制过程的对称性,取轧件宽度方向的1/2建
表1轧制工艺参数 Tab.1 Rolling process parameters
【VIP专享】辊轮传输工作原理和应用实例
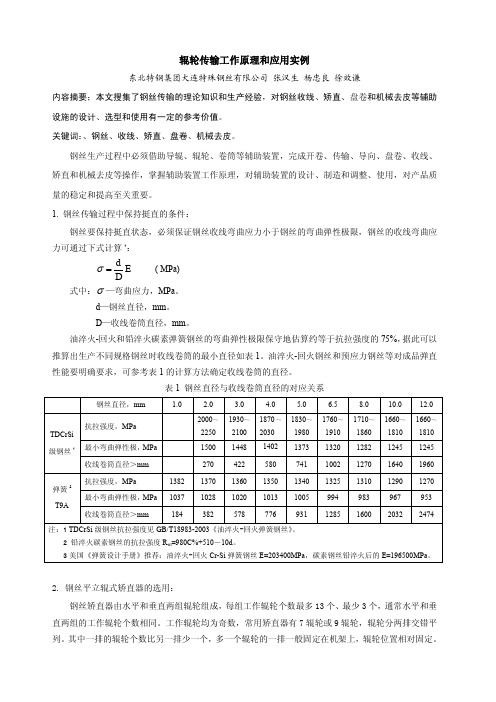
辊轮传输工作原理和应用实例东北特钢集团大连特殊钢丝有限公司 张汉生 杨忠良 徐效谦内容摘要;本文搜集了钢丝传输的理论知识和生产经验,对钢丝收线、矫直、盘卷和机械去皮等辅助设施的设计、选型和使用有一定的参考价值。
关键词:、钢丝、收线、矫直、盘卷、机械去皮。
钢丝生产过程中必须借助导辊、辊轮、卷筒等辅助装置,完成开卷、传输、导向、盘卷、收线、矫直和机械去皮等操作,掌握辅助装置工作原理,对辅助装置的设计、制造和调整、使用,对产品质量的稳定和提高至关重要。
1. 钢丝传输过程中保持挺直的条件:钢丝要保持挺直状态,必须保证钢丝收线弯曲应力小于钢丝的弯曲弹性极限,钢丝的收线弯曲应力可通过下式计算1:E Dd=σ ( MPa)式中:σ—弯曲应力,MPa 。
d —钢丝直径,mm 。
D —收线卷筒直径,mm 。
油淬火-回火和铅淬火碳素弹簧钢丝的弯曲弹性极限保守地估算约等于抗拉强度的75%,据此可以推算出生产不同规格钢丝时收线卷筒的最小直径如表1。
油淬火-回火钢丝和预应力钢丝等对成品弹直性能要明确要求,可参考表1的计算方法确定收线卷筒的直径。
表1 钢丝直径与收线卷筒直径的对应关系2. 钢丝平立辊式矫直器的选用:钢丝矫直器由水平和垂直两组辊轮组成,每组工作辊轮个数最多13个、最少3个,通常水平和垂直两组的工作辊轮个数相同。
工作辊轮均为奇数,常用矫直器有7辊轮或9辊轮,辊轮分两排交错平列。
其中一排的辊轮个数比另一排少一个,多一个辊轮的一排一般固定在机架上,辊轮位置相对固定。
另一排辊轮可通过螺栓和滑块作垂直于钢丝方向的移动,以适应于不同规格钢丝的矫直要求。
矫直器选用的关键是辊轮直径和个数。
辊轮个数越多产生的波浪弯越多,矫直效果越好,所以强度高、弹力大,难矫直的钢丝必须选用多辊矫直器。
钢种与工作辊轮个数的对应关系见表2。
表2 钢种与工作辊轮个数的对应关系工作辊轮的直径取决于钢丝的直径,常用辊轮直径D=20~150mm ,辊轮直径与钢丝直径的对应关系如表3。
板形控制技术及应用
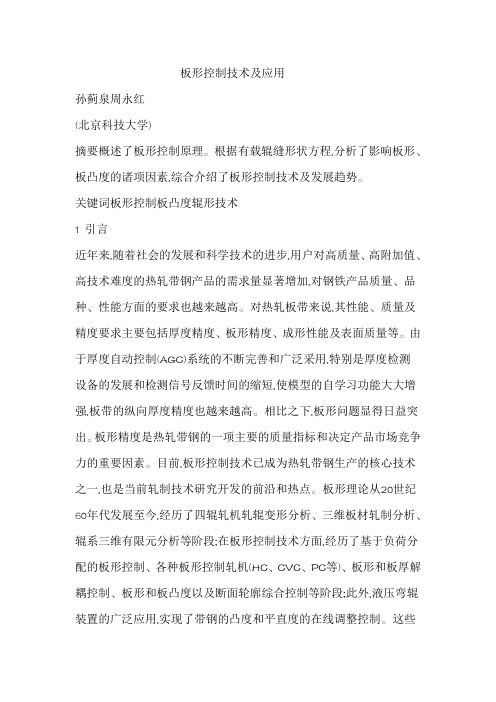
板形控制技术及应用孙蓟泉周永红(北京科技大学)摘要概述了板形控制原理。
根据有载辊缝形状方程,分析了影响板形、板凸度的诸项因素,综合介绍了板形控制技术及发展趋势。
关键词板形控制板凸度辊形技术1 引言近年来,随着社会的发展和科学技术的进步,用户对高质量、高附加值、高技术难度的热轧带钢产品的需求量显著增加,对钢铁产品质量、品种、性能方面的要求也越来越高。
对热轧板带来说,其性能、质量及精度要求主要包括厚度精度、板形精度、成形性能及表面质量等。
由于厚度自动控制(AGC)系统的不断完善和广泛采用,特别是厚度检测设备的发展和检测信号反馈时间的缩短,使模型的自学习功能大大增强,板带的纵向厚度精度也越来越高。
相比之下,板形问题显得日益突出。
板形精度是热轧带钢的一项主要的质量指标和决定产品市场竞争力的重要因素。
目前,板形控制技术已成为热轧带钢生产的核心技术之一,也是当前轧制技术研究开发的前沿和热点。
板形理论从20世纪60年代发展至今,经历了四辊轧机轧辊变形分析、三维板材轧制分析、辊系三维有限元分析等阶段;在板形控制技术方面,经历了基于负荷分配的板形控制、各种板形控制轧机(HC、CVC、PC等)、板形和板厚解耦控制、板形和板凸度以及断面轮廓综合控制等阶段;此外,液压弯辊装置的广泛应用,实现了带钢的凸度和平直度的在线调整控制。
这些理论和技术的采用都使板形控制水平得到了很大的提高,板形控制精度也得到了大幅提升。
2 板形控制原理由于轧出带钢的断面形状即是有载辊缝形状,因此板形控制的实质就是控制带钢宽度方向上的有载辊缝,从而获得所需的带材轮廓和平直度。
影响有载辊缝形状的因素较多,主要有工作辊辊形、使辊系产生弯曲变形的轧制力和弯辊力、改变轧辊辊形的热辊形和磨损辊形以及一些可控辊形技术。
2.1 有载辊缝形状有载辊缝形状可用如下方程描述[2]:CR= PKP+ FKF+ECωC+EΣ(ωH+ωW+ωO)+E0Δ式中CR--与带钢凸度有关的有载辊缝形状;P--轧制力;F--弯辊力;KP--辊系在轧制力作用下的弯曲变形,又称为轧机横向刚度;KF--辊系在弯辊力作用下的弯曲变形,又称为弯辊横向刚度;ωC--可控辊形,根据所采用的CVC或PC等技术确定其值;ωH--热辊形;ωW--磨损辊形;ωO--初始辊形,根据板形控制需要,进行辊形设计和磨辊;Δ--入口带钢凸度;E0、EC、EΣ--相关系数。
立辊轧机在梅钢热轧板厂的应用

在偶 道次 时 , 统保 存 由仪 表 测 压头 采 集 的 系
R 2水平 轧机 的总 的轧 制 力 , WC 系统 通 过 测 得 A
端 大 。因此 , 经过 水 平 轧 制 道 次 后 , 来 的 失 宽 原
被 进 一 步扩 大 。
Байду номын сангаас
跟 踪 , 设定 液压 A 预 WC, 在水 印处 加 大侧 压量 , 消
除水 印处 产生 的多 余 的 宽展 量 , 水 平 轧 制后 的 使
板坯 达 到设定 的宽 度值 。
对于带钢尾部 通过 轧辊 时 的非稳 定轧 制情 况 , 可 以作 类 似 解 释 。 另 外 , 钢 中 间 部 分 的 “ 带 狗
轧制侧压 板坯 的两 个立 侧 面 , 以减 小 并保 证 板带 钢的宽度 和精度 ; 可将板坯 对准轧 制 中心线 , 起导
芦
铮
武仁 户 立辊轧机 在 梅钢 热轧 板厂 的应 用
・9 ・
间足 够 长 , 钢 头 部 出 现 塑 性 变 形 区时 , 钢 内 带 带
部才 形 成 回牵 剪 切 应 力 , 迫 轧 件 充 满 辊 缝 。 强
自学习功 能。实践证 明 , 梅钢 热轧板 厂立辊轧机 的应 用是成 功 的, 并在 实际生产 中取 得 了良好
的效 果。
关键 词 : 立辊 轧机 ; 行程 ; 度补偿 ; 短 硬 轧制 力控制
App ia in f Edg r M ili tRol ng Pl nta eg ng lc to o e l n Ho l a tM i a i
向板坯 的作用 ; 制厚度 大 于 10 m 的板坯 时 , 轧 0 m
短流程连铸连轧成套装备的工作原理和技术优势
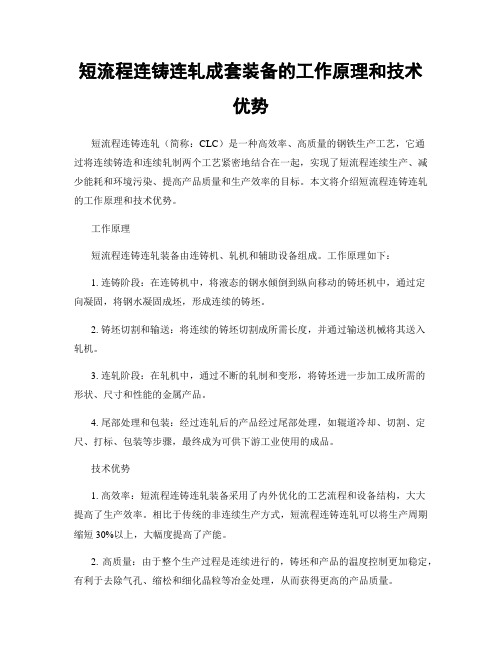
短流程连铸连轧成套装备的工作原理和技术优势短流程连铸连轧(简称:CLC)是一种高效率、高质量的钢铁生产工艺,它通过将连续铸造和连续轧制两个工艺紧密地结合在一起,实现了短流程连续生产、减少能耗和环境污染、提高产品质量和生产效率的目标。
本文将介绍短流程连铸连轧的工作原理和技术优势。
工作原理短流程连铸连轧装备由连铸机、轧机和辅助设备组成。
工作原理如下:1. 连铸阶段:在连铸机中,将液态的钢水倾倒到纵向移动的铸坯机中,通过定向凝固,将钢水凝固成坯,形成连续的铸坯。
2. 铸坯切割和输送:将连续的铸坯切割成所需长度,并通过输送机械将其送入轧机。
3. 连轧阶段:在轧机中,通过不断的轧制和变形,将铸坯进一步加工成所需的形状、尺寸和性能的金属产品。
4. 尾部处理和包装:经过连轧后的产品经过尾部处理,如辊道冷却、切割、定尺、打标、包装等步骤,最终成为可供下游工业使用的成品。
技术优势1. 高效率:短流程连铸连轧装备采用了内外优化的工艺流程和设备结构,大大提高了生产效率。
相比于传统的非连续生产方式,短流程连铸连轧可以将生产周期缩短30%以上,大幅度提高了产能。
2. 高质量:由于整个生产过程是连续进行的,铸坯和产品的温度控制更加稳定,有利于去除气孔、缩松和细化晶粒等冶金处理,从而获得更高的产品质量。
3. 节约能源和环保:短流程连铸连轧装备采用了先进的能量回收和净化设备,有效利用余热和废气等资源,降低了能耗和环境污染。
相较于传统工艺,其能源消耗可以减少20%以上,有利于可持续发展。
4. 灵活性:短流程连铸连轧工艺适应性强,可生产多种材料和规格的产品,包括普通碳素钢、合金钢、不锈钢等。
同时,它也可以灵活应对市场需求的变化,快速调整生产线的生产规模和品种组合。
5. 降低投资和运营成本:短流程连铸连轧装备比传统装备的投资成本更低,且占地面积较小,使得钢铁企业能够降低建设成本和运营成本。
总结短流程连铸连轧成套装备的工作原理和技术优势使其成为现代钢铁生产的重要工艺。
1780热连轧辊缝控制与应用
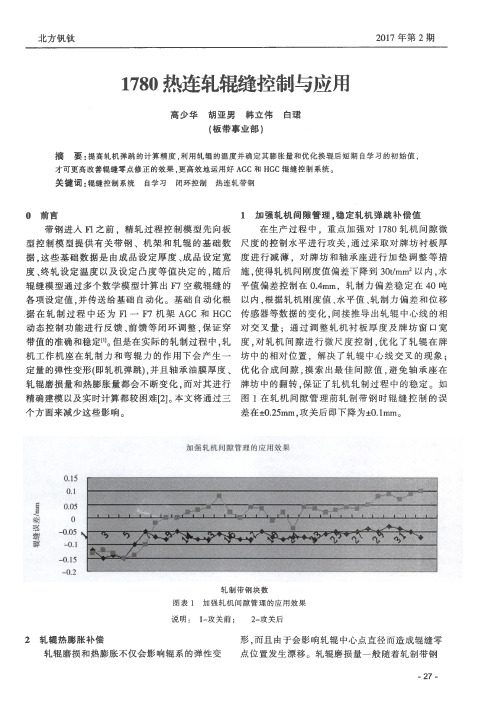
,
机工作机座在轧制 力 和 弯辊力 的作用下会产生
一
解 决 了 乳 辊 中 心 线交 叉 的 现 象
,
;
定 量 的 弹性 变 形 即 轧 机 弹 跳
(
)
,
并 且轴 承 油 膜厚 度
,
、
优 化合成间 隙 摸索 出 最 佳 间 隙值 避免 轴 承 座 在 牌 坊 中 的 翻 转 保 证 了 乳 机 轧 制 过 程 中 的 稳定
25 m m
,
攻 关 后 即 下 降 为 ±0
.
1
mm。
加 强 轧 机 间 隙管 理 的 应 用 效 果
E
0 05
.
^
1 雨 Q ^ —
-
J
L
-l _I _ I _I _
L
;
_ I_ I_ I _ I_
L
r」
 ̄ * ̄
l
? _
.
l_
I_
l_
l
_
i
_
i
l
—
I
_J
一 __1
_
-
0
.
1
5
—
0 2
.
轧 制 带钢 块数
图表
1
加 强乳 机 间 隙 管 理 的 应 用 效 果
-
说明
2
:
1
攻关前
;
2
-
攻关后
轧 辊 热 膨 胀 补 偿 形 而 且 由 于 会 影 响 乳 辊 中 心 点 直 径 而 造 成 辊 缝 零
,
北 方 钒钛20
1
立辊AWC-SSC控制系统简介

立辊AWC-SSC控制系统简介
宽度尺寸精度是热轧带钢产品质量的重要指标,良好的宽度精度不仅可以降低带钢的切边损耗,提高产品的成材率,而且将给热轧用户及后部工序创造更好的生产条件。
宽度偏差每减小 1mm,成材率就可以提高0.1﹪左右。
因此,宽度控制技术的开发与应用对节能降耗,提高经济效益尤为重要。
从目前热轧生产线上的设备配置情况看,热轧带钢产品的宽度控制主要在粗轧区实现,只有准确设定粗轧宽度模型,才能有效控制精轧的出口宽度。
AWC 的任务就是根据机架的刚度系数、板坯实际宽度等,为立辊压下系统计算出侧压设定值,以消除由于温度改变导致轧制力变化,而导致轧机辊缝值发生变化的影响,维持恒定的立辊负载辊缝值,获得恒宽的板坯。
另外为了克服头尾宽度变窄,立辊还要投入短行程控制。
AWC 控制系统由 L2 级模型计算机、L1 级 AWC 控制器、L0 级液压传动装置以及机械设备等部分组成。
控制功能包括:粗轧带钢目标宽度的确定、粗轧立辊开口度的预设定及其轧后修正、宽度控制及其模型自学习、短行程控制(SSC)、轧制力反馈宽度自动控制(RF-AWC)、前馈宽度控制(FF-AWC)、动态补偿(DSU)、带钢缩颈补偿(NEC)
等。
供货范围如下:
全套电控设备的供货;全套设备的出厂调试;全套设备的检验、验收、包装、运输;现场的安装(指导)、系统调试;热负荷试车及售后的技术服务;产品、技术培训等相关技术服务。
该项目适用于所有的新建和欲改造的立辊设备。
同时,通过技术集成和转移,可为轧钢控制技术国产化作出较大贡献。
该系统已经成功稳定的应用在国内多条热连轧生产线并取得了的很好的控制效果。
优化短行程控制提高热轧卷板宽度精度
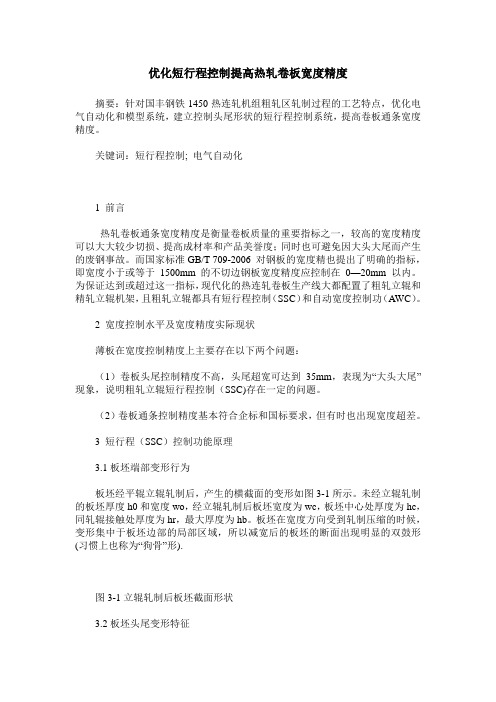
优化短行程控制提高热轧卷板宽度精度摘要:针对国丰钢铁1450热连轧机组粗轧区轧制过程的工艺特点,优化电气自动化和模型系统,建立控制头尾形状的短行程控制系统,提高卷板通条宽度精度。
关键词:短行程控制; 电气自动化1 前言热轧卷板通条宽度精度是衡量卷板质量的重要指标之一,较高的宽度精度可以大大较少切损、提高成材率和产品美誉度;同时也可避免因大头大尾而产生的废钢事故。
而国家标准GB/T 709-2006 对钢板的宽度精也提出了明确的指标,即宽度小于或等于1500mm 的不切边钢板宽度精度应控制在0—20mm 以内。
为保证达到或超过这一指标,现代化的热连轧卷板生产线大都配置了粗轧立辊和精轧立辊机架,且粗轧立辊都具有短行程控制(SSC)和自动宽度控制功(AWC)。
2 宽度控制水平及宽度精度实际现状薄板在宽度控制精度上主要存在以下两个问题:(1)卷板头尾控制精度不高,头尾超宽可达到35mm,表现为“大头大尾”现象,说明粗轧立辊短行程控制(SSC)存在一定的问题。
(2)卷板通条控制精度基本符合企标和国标要求,但有时也出现宽度超差。
3 短行程(SSC)控制功能原理3.1板坯端部变形行为板坯经平辊立辊轧制后,产生的横截面的变形如图3-1所示。
未经立辊轧制的板坯厚度h0和宽度wo,经立辊轧制后板坯宽度为wc,板坯中心处厚度为hc,同轧辊接触处厚度为hr,最大厚度为hb。
板坯在宽度方向受到轧制压缩的时候,变形集中于板坯边部的局部区域,所以减宽后的板坯的断面出现明显的双鼓形(习惯上也称为“狗骨”形).图3-1立辊轧制后板坯截面形状3.2板坯头尾变形特征板坯立辊轧时板坯与轧辊接触后,余属变形首先沿着轧辊的切向流动,形成宽度的缩窄,直至形成一定的刚端,这种金属向中部流动的情况逐渐受阻而停止。
图3-2所示为立辊轧制时板坯咬入过程十个瞬间板坯变形的情况。
可以清楚的看到,从第四步开始,板坯脱离同轧辊的接触,此时板坯尚未离开辊缝的出口。
厚宽钢带连轧设备的辊形控制技术研究
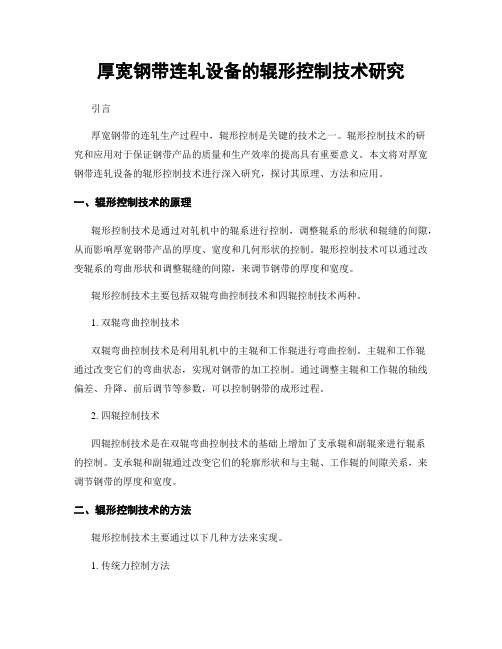
厚宽钢带连轧设备的辊形控制技术研究引言厚宽钢带的连轧生产过程中,辊形控制是关键的技术之一。
辊形控制技术的研究和应用对于保证钢带产品的质量和生产效率的提高具有重要意义。
本文将对厚宽钢带连轧设备的辊形控制技术进行深入研究,探讨其原理、方法和应用。
一、辊形控制技术的原理辊形控制技术是通过对轧机中的辊系进行控制,调整辊系的形状和辊缝的间隙,从而影响厚宽钢带产品的厚度、宽度和几何形状的控制。
辊形控制技术可以通过改变辊系的弯曲形状和调整辊缝的间隙,来调节钢带的厚度和宽度。
辊形控制技术主要包括双辊弯曲控制技术和四辊控制技术两种。
1. 双辊弯曲控制技术双辊弯曲控制技术是利用轧机中的主辊和工作辊进行弯曲控制。
主辊和工作辊通过改变它们的弯曲状态,实现对钢带的加工控制。
通过调整主辊和工作辊的轴线偏差、升降、前后调节等参数,可以控制钢带的成形过程。
2. 四辊控制技术四辊控制技术是在双辊弯曲控制技术的基础上增加了支承辊和副辊来进行辊系的控制。
支承辊和副辊通过改变它们的轮廓形状和与主辊、工作辊的间隙关系,来调节钢带的厚度和宽度。
二、辊形控制技术的方法辊形控制技术主要通过以下几种方法来实现。
1. 传统力控制方法传统力控制方法是通过测量轧机中的辊系受力情况,来实现辊形的控制。
通过在辊系上安装力传感器和位移传感器,测量辊系的受力情况和变形情况,并通过控制系统进行反馈调节,实现钢带的稳定加工。
2. 数学模型控制方法数学模型控制方法是通过建立辊系的数学模型,来预测和控制辊系的形状和辊缝的间隙。
通过建立辊系的力学方程、变形方程和热力耦合方程等数学模型,可以进行辊形的预测和辊缝的控制。
3. 人工智能控制方法人工智能控制方法是将人工智能技术应用于辊形控制中。
通过人工智能算法和模型的优化,可以实现辊形控制的精确调节和优化控制。
借助机器学习和深度学习等技术,可以让系统具备自动学习和智能调节的功能。
4. 仿真模拟控制方法仿真模拟控制方法是通过建立辊形控制的仿真模型,对不同辊形控制策略进行仿真测试和评估。
c2 method 辊炼 -回复
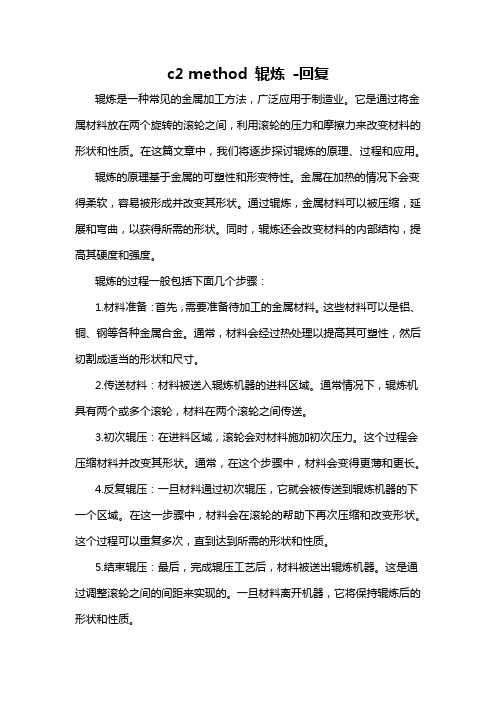
c2 method 辊炼-回复辊炼是一种常见的金属加工方法,广泛应用于制造业。
它是通过将金属材料放在两个旋转的滚轮之间,利用滚轮的压力和摩擦力来改变材料的形状和性质。
在这篇文章中,我们将逐步探讨辊炼的原理、过程和应用。
辊炼的原理基于金属的可塑性和形变特性。
金属在加热的情况下会变得柔软,容易被形成并改变其形状。
通过辊炼,金属材料可以被压缩,延展和弯曲,以获得所需的形状。
同时,辊炼还会改变材料的内部结构,提高其硬度和强度。
辊炼的过程一般包括下面几个步骤:1.材料准备:首先,需要准备待加工的金属材料。
这些材料可以是铝、铜、钢等各种金属合金。
通常,材料会经过热处理以提高其可塑性,然后切割成适当的形状和尺寸。
2.传送材料:材料被送入辊炼机器的进料区域。
通常情况下,辊炼机具有两个或多个滚轮,材料在两个滚轮之间传送。
3.初次辊压:在进料区域,滚轮会对材料施加初次压力。
这个过程会压缩材料并改变其形状。
通常,在这个步骤中,材料会变得更薄和更长。
4.反复辊压:一旦材料通过初次辊压,它就会被传送到辊炼机器的下一个区域。
在这一步骤中,材料会在滚轮的帮助下再次压缩和改变形状。
这个过程可以重复多次,直到达到所需的形状和性质。
5.结束辊压:最后,完成辊压工艺后,材料被送出辊炼机器。
这是通过调整滚轮之间的间距来实现的。
一旦材料离开机器,它将保持辊炼后的形状和性质。
辊炼的应用非常广泛。
它可以用于制造金属板、管和棒材等各种形式的金属产品。
辊炼机器还可以被用于压制和制造金属的零部件和组件。
此外,辊炼还可以用于改变金属材料的硬度和强度,以满足特定的工程要求。
例如,辊炼可以用于提高铝合金的强度,使其更适用于航空航天和汽车制造等应用。
除了金属加工外,辊炼还可以用于塑料和橡胶等其他材料的加工。
这些材料在热条件下同样具备可塑性,可以通过辊炼来改变其形状和性质。
总之,辊炼是一种常见而重要的金属加工方法。
它通过利用滚轮的压力和摩擦力来改变金属材料的形状和性质。
扁钢热连轧机立辊导卫装置的控制原理及应用
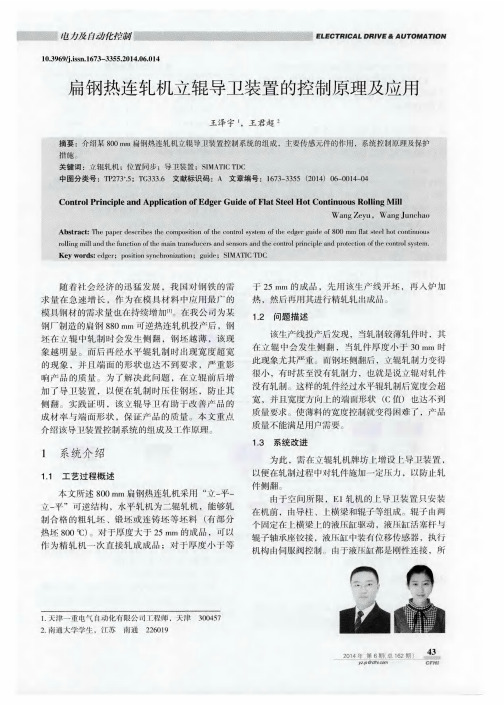
② 奇道次 ( 首道次 除外) 的厚度等于上道次 E 1 的出口厚度 ( 来 自于二级计算机 的计算 ) 。
斜 坡 发生 器 位 鼹调 节器
图2 E 1 导 卫 位 置 控 制 原 理 图
2 0 1 年 第6 期( 总1 6 2 期)
y z j . s @c f h i . c o m CF HI
由于 E l 与E 2 导 卫装 置 的结构 并不 相 同 ,并 且 该 热连 轧 机 的结 构 ( 立一 平一 立一 平 )非 对 称 ,所 以 两 个立 辊导 卫装 置 的工艺 动作 顺序 也不 同。
3 . 1 E1 上 导 卫控 制
( 1 ) 逻 辑控 制
②E 1 机前热检器检得钢坯 。
EL EcT RI c AL oR l v E & A uToM A TI o N
( 3 ) 热金 属 检 测 器
热金 属 检测 器 ( 以下 简称 热检 ) 的原理 是 :由
③偶道次的厚度等于每道次中 F 1 的出口厚度 ( 来 自于二级计算机的计算) 。
此 处控 制 逻 辑 的关 键是 确定 E 1 上 导 卫装 置 从 预摆 状 态切换 到工 作状 态 时的触 发事件 ,由于轧 机
偶 道 次轧 制时 ,当上 述两 个信 号 中的任 意一个
产 生后 ,E1 上导 卫切 换 到工作状 态 。
( 2 )控 制 算 法
因两个液压缸都采用刚性连接 ,所以同步控制 精 度要 求很 高 。在此 位置控 制 系统 中 ,设 置 了两个
比例 一 积分 调 节器 ,其 中 ,位置 调节 器 负 责 两个 缸 平 均位 置 的控制 ,同步调节 器 负责两个 缸位 置 同步
轧机立辊宽度自动控制(AWC)系统在钢厂的应用
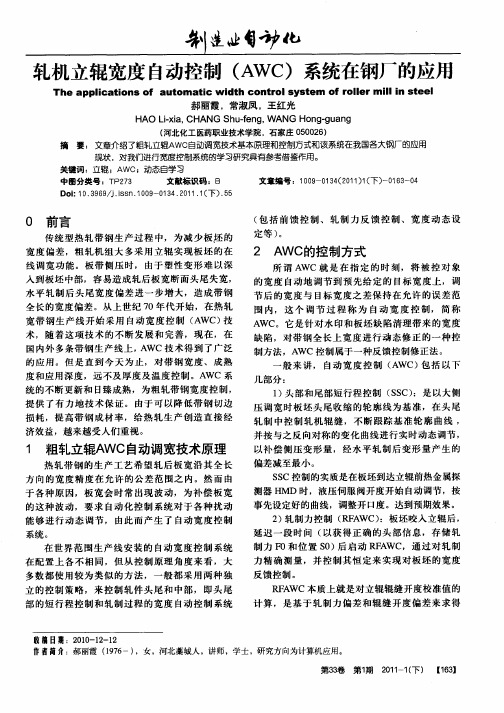
轧机立辊宽度 自动控制 ( WC A )系统在钢厂的应用
The app¨c i at ons o aut f om a i i h cont oIs t t c w dt r ys em oler m ili eeI of r l l n st
在 世 界 范 围生 产 线 安 装 的 自动 宽 度 控 制 系统 在配 置 上 各 不相 同 ,但从 控 制 原 理 角 度来 看 ,大 多数 都 使 用较 为 类 似 的方 法 , 一般 都 采 用 两 种独
力精 确 测 量 ,并 控 制其 恒 定 来 实现 对 板 坯 的 宽度
反 馈控制 。
第3 卷 3 第1 期 2 1 - ( ) [6 ] 0 1 1 下 1 3
偏 差减 至最小 。 S C控制 的实质是 在板坯到 达立辊前 热金属探 S 测器 H MD 时 ,液压 伺服 阀开度 开始 自动调 节 ,按
损 耗 ,提 高带 钢 成 材 率 ,给 热 轧 生 产创 造 直 接 经 济效 益 ,越来 越受人 们重视 。
1 粗轧立辊A wC自动调宽技术原理
度 和应 用深 度 ,远不 及厚 度 及温 度控 制 。A WC系
的 宽度 自动地 调 节到 预 先 给 定 的 目标 宽 度上 ,调
节 后 的宽 度 与 目标 宽 度之 差保 持 在 允许 的误 差范
围 内 ,这 个 调 节 过 程 称 为 自动 宽 度 控 制 , 简 称 A WC。它是 针 对 水 印和板 坯 缺 陷清 理 带来 的 宽度 缺 陷 ,对带 钢 全 长 上 宽度 进 行 动 态修 正 的 一种 控
立 的控 制 策 略 ,来 控制 轧 件 头 尾 和 中部 ,即 头 尾
部 的短 行程 控 制 和 轧 制过 程 的 宽 度 自动 控 制 系统
简述二辊周期式冷轧管机的应用与发展

简述二辊周期式冷轧管机的应用与发展1 二辊周期式冷轧管机的应用特点周期式冷轧管机是有色金属管材生产中广泛应用的一种基本生产方法,管材按一定频率送进由芯棒和周期往复运动的孔型所组成的轧槽内,内壁在芯棒的支撑下,靠逐渐收缩的变断面孔型碾压管坯,实现减径减壁功能,如图1所示。
轧制中金属受三向压应力作用,具有良好的塑性变形条件,而往复运动的孔型将周期送进的金属的塑变分散到整个有效轧程中去,最大限度地利用金属的塑性,达到用较小的轧制力实现较大加工率的目的,具有显著的“微观变形,宏观积累”的效果,因而是充分发挥材料塑性的最有效的冷加工工艺方法。
具有以下六个方面的显著特点:(1)道次加工率可以达到70%~90%,延伸系数3~10,一次冷轧相当于4~5次拉伸,具有较高的劳动效率。
特别是对于塑性低、难变形合金,是目前最为有效的铜合金管拉伸前的开坯手段。
(2)可显著缩短管材加工工艺流程,减少拉伸所造成的几何废料及辅助生产时间,生产效率和成品率提高15%~20%,特别是近年来以长行程、高频率、双回转双送进为代表的新型轧制设备的发展,为超长铜合金管材连续化生产奠定了技术基础。
(3)在变形区内金属周向、径向压缩应力作用明显,而轴向作用力相对较小,因而可以起到显著的纠偏作用,一般轧制后管材的偏心率会比挤压偏心率下降50%以上,这是靠拉伸不可能实现的,因而可以显著提高产品的壁厚公差精度,是目前高精度薄壁铜合金管材生产的关键工艺环节。
(4)轧制回程对处于轧槽中的管材具有均整碾压作用,一段金属从送进孔型到脱离孔型,处于不断变形、不断均整的过程,因而轧制管材既具有塑性变性对组织的强化作用,又具有显著提高管材表面质量及尺寸精度的作用,为高精管材抛光拉伸奠定了基础。
(5)冷轧管机结构复杂、设备投资高、维护调整困难、工具制造成本高,生产效率受设备结构及调整、维护、更换工具、装料等辅助因素影响较大。
(6)二辊周期式冷轧管机受轧辊孔型及运动特点的限制,轧制产品椭圆度及表面光洁度不如拉伸制品,因而二辊周期轧制一般应用于拉伸前的开坯工序。
铝热轧立辊的应用
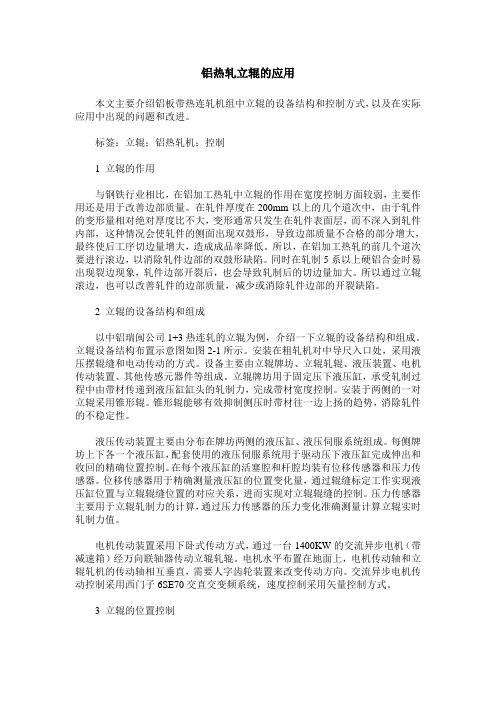
铝热轧立辊的应用本文主要介绍铝板带热连轧机组中立辊的设备结构和控制方式,以及在实际应用中出现的问题和改进。
标签:立辊;铝热轧机;控制1 立辊的作用与钢铁行业相比,在铝加工热轧中立辊的作用在宽度控制方面较弱,主要作用还是用于改善边部质量。
在轧件厚度在200mm以上的几个道次中,由于轧件的变形量相对绝对厚度比不大,变形通常只发生在轧件表面层,而不深入到轧件内部,这种情况会使轧件的侧面出现双鼓形,导致边部质量不合格的部分增大,最终使后工序切边量增大,造成成品率降低。
所以,在铝加工热轧的前几个道次要进行滚边,以消除轧件边部的双鼓形缺陷。
同时在轧制5系以上硬铝合金时易出现裂边现象,轧件边部开裂后,也会导致轧制后的切边量加大。
所以通过立辊滚边,也可以改善轧件的边部质量,减少或消除轧件边部的开裂缺陷。
2 立辊的设备结构和组成以中铝瑞闽公司1+3热连轧的立辊为例,介绍一下立辊的设备结构和组成。
立辊设备结构布置示意图如图2-1所示。
安装在粗轧机对中导尺入口处,采用液压摆辊缝和电动传动的方式。
设备主要由立辊牌坊、立辊轧辊、液压装置、电机传动装置、其他传感元器件等组成。
立辊牌坊用于固定压下液压缸,承受轧制过程中由带材传递到液压缸缸头的轧制力,完成带材宽度控制。
安装于两侧的一对立辊采用锥形辊。
锥形辊能够有效抑制侧压时带材往一边上扬的趋势,消除轧件的不稳定性。
液压传动装置主要由分布在牌坊两侧的液压缸、液压伺服系统组成。
每侧牌坊上下各一个液压缸,配套使用的液压伺服系统用于驱动压下液压缸完成伸出和收回的精确位置控制。
在每个液压缸的活塞腔和杆腔均装有位移传感器和压力传感器。
位移传感器用于精确测量液压缸的位置变化量,通过辊缝标定工作实现液压缸位置与立辊辊缝位置的对应关系,进而实现对立辊辊缝的控制。
压力传感器主要用于立辊轧制力的计算,通过压力传感器的压力变化准确测量计算立辊实时轧制力值。
电机传动装置采用下卧式传动方式,通过一台1400KW的交流异步电机(带减速箱)经万向联轴器传动立辊轧辊。
二项式法计算负荷例题切削机床
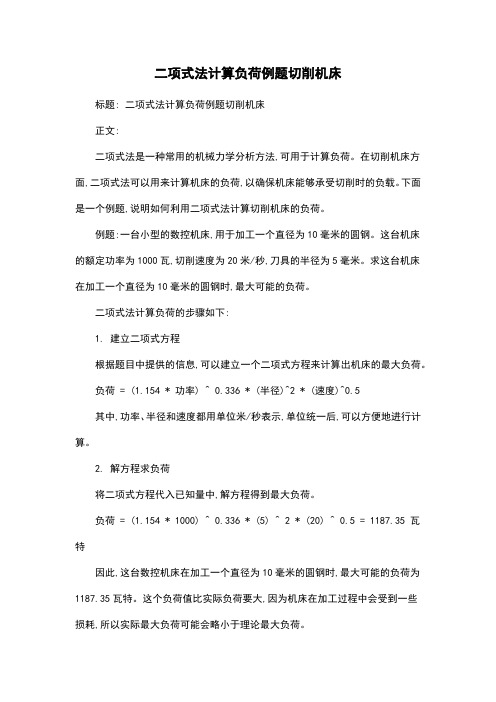
二项式法计算负荷例题切削机床标题: 二项式法计算负荷例题切削机床正文:二项式法是一种常用的机械力学分析方法,可用于计算负荷。
在切削机床方面,二项式法可以用来计算机床的负荷,以确保机床能够承受切削时的负载。
下面是一个例题,说明如何利用二项式法计算切削机床的负荷。
例题:一台小型的数控机床,用于加工一个直径为10毫米的圆钢。
这台机床的额定功率为1000瓦,切削速度为20米/秒,刀具的半径为5毫米。
求这台机床在加工一个直径为10毫米的圆钢时,最大可能的负荷。
二项式法计算负荷的步骤如下:1. 建立二项式方程根据题目中提供的信息,可以建立一个二项式方程来计算出机床的最大负荷。
负荷 = (1.154 * 功率) ^ 0.336 * (半径)^2 * (速度)^0.5其中,功率、半径和速度都用单位米/秒表示,单位统一后,可以方便地进行计算。
2. 解方程求负荷将二项式方程代入已知量中,解方程得到最大负荷。
负荷 = (1.154 * 1000) ^ 0.336 * (5) ^ 2 * (20) ^ 0.5 = 1187.35 瓦特因此,这台数控机床在加工一个直径为10毫米的圆钢时,最大可能的负荷为1187.35瓦特。
这个负荷值比实际负荷要大,因为机床在加工过程中会受到一些损耗,所以实际最大负荷可能会略小于理论最大负荷。
拓展:二项式法在机械力学分析中应用范围广泛,可以用来计算各种机械的负荷。
在切削机床方面,二项式法可以用来计算机床的负载,以确保机床能够承受切削时的负载。
此外,还可以根据机床的特性,选择适当的刀具半径和速度,以达到最佳的加工效果。
二项式法是一种简单而有效的方法,可以帮助我们计算出机床的负荷,从而保证机床的安全和稳定运行。
粗轧E2立辊短行程异常动作的研究及应用分析

粗轧E2立辊短行程异常动作的研究及应用分析发布时间:2023-02-17T00:46:53.269Z 来源:《科技新时代》2022年19期作者:朱国铭[导读]朱国铭宝钢湛江钢铁有限公司/热轧厂摘要:本文对1780热轧R2轧机的基本轧制原理做了详细的介绍,同时对1780热轧E2短行程异常动作的原因做了深入的研究对比分析,然后明确指出改进措施的方式及其改进后的实际效果,为消除E2立辊短行程异常,过程需要保证电气及机械设备稳定、步骤衔接紧密、设备动作响应迅速及时,本文主要通过系列优化技术,从单体设备的跟踪动作速度及衔接紧密性上,消除E2立辊短行程异常目的。
最终让读者对1780热轧E2立辊短行程异常动作原因分析及改进措施能有一个清晰的了解和认识。
关键字:R2轧机;E2立辊;短行程;Author'sname:ZhuGuoming(Author'sunit:BaosteelZhanjiangIronandSteelCo.,Ltd./HotRollingMill)Abstract:Thispaperintroducesthebasicrollingprincipleof1780hotrollingR2millindetail,andmakesanin-depthstudyandcomparativeanalysisofthereasonsfortheabnormalshortstrokeactionof1780hotrollingE2,andthenclearlypointsoutthewayofimprovementmeasuresandtheactualeff Keywords:R2rollingmill;E2verticalroll;Shortstroke;前言R2轧机位于R1轧机之后,有两个立辊和四个水平辊。
两个立辊(E2)位于R2入口辊道之后,具有自动定宽控制功能(AWC)。
通过立辊可以把板坯宽度轧减到目标宽度。
钢波纹板辊压成形技术及应用

钢波纹板辊压成形技术及应用1、波纹板的辊压成形技术波纹管由波纹板分片弯曲连接成形,波纹板制造一般采用板料卷辊压成形,辊压孔型系统有连续成形系统和专用孔型系统。
目前生产波纹板应用最广泛的是连续成形系统,即首先弯中心波,然后弯相邻波,最后弯边波。
该孔型系统的优点为辊耗最低,其缺点为工件易出现横向弯曲和扭曲。
专用孔型系统主要用于生产波纹板,在开始阶段先预弯出弧形波,再将其镦压成形,该方法保证各弯角处金属减薄最轻。
其缺点为辊耗高,对成形设备和材料要求高。
项目组根据多年的研究和产品开发经验,将上述两种孔型系统进行了整合,充分吸取了两种成形方法的优点,克服了成形过程中经常出现的横向弯曲、扭曲和边波等缺陷。
经试验验证,该成形系统能很好地实现宽幅板类产品辊压成形。
项目组近年来对宽幅板类辊压工艺进行了较系统的研究,与长春轨道客车合作建立了常用辊压板材性能数据库,该数据库包含SUS301L-ST、SUS301L-HT、SUS301L-DLT、太钢00Cr12Ni、05CuPCrNi、09CuPCrNi、08F、Q235、Q345、Q610等材料各项力学性能,该数据库的建立,为辊压工艺的开发和有限元数值模拟研究奠定了基础。
在辊弯过程中常常遇到一些问题,如袋形波、边波、划痕、翘曲、裂纹、回弹、断面形状畸变等。
针对上述缺陷的产生,项目组结合长春轨道客车不锈钢车体波纹顶板和波纹地板开发项目,利用有限元模拟研究了波纹板类产品辊压变形过程,计算了角部节点辊压应变分布,分析了缺陷产生的原因和解决办法。
板材横向,即宽度方向,在弯曲角部位附近,应变变化大,并有明显的峰值,而在底部部位应力均匀分布,因此应变主要集中在弯曲角附近的变形区域。
板材的纵向变形主要集中在变形区和变形过渡区,反映在弯曲部位,变形量较大,但处于弹性变形范围,即板材在纵向上存在弹性拉伸变形,该应变的存在,将引起型材纵向弯曲和断面形状畸变。
总的来说,横向应变要大于纵向应变,说明变形主要发生在横向即板材的宽度方向,在冷弯成形中,摩擦是重要的影响因素,利用有限元模拟了摩擦系数对冷弯成形的影响。
- 1、下载文档前请自行甄别文档内容的完整性,平台不提供额外的编辑、内容补充、找答案等附加服务。
- 2、"仅部分预览"的文档,不可在线预览部分如存在完整性等问题,可反馈申请退款(可完整预览的文档不适用该条件!)。
- 3、如文档侵犯您的权益,请联系客服反馈,我们会尽快为您处理(人工客服工作时间:9:00-18:30)。
第3期(总第172期)
2012年6月机械工程与自动化
MECHANICAL ENGINEERING & AUTOMATIONNo.3
Jun.
文章编号:1672-6413(2012)03-0171-0
2短行程中立辊二项式控制方式的应用
褚 希
(安徽工业大学电气信息学院,安徽 马鞍山 243000
)摘要:介绍了二项式控制方式的原理与应用。
在热轧粗轧短行程过程中,二项式控制方式的应用可以大幅度减少轧件端部的“鱼尾”状形变,优化控制曲线,减少端部剪切量,增加经济效益。
关键词:短行程控制;折线式控制方式;二项式控制方式中图分类号:TG335.11 文献标识码:B
收稿日期:2012-01-11;修回日期:2012-02-1
5作者简介:褚希(1984-)
,男,安徽马鞍山人,在读硕士研究生,主要研究方向:热轧粗轧短行程控制理论。
0 引言
热轧粗轧轧制过程中,板坯需要经过立辊和水平辊的轧制,
由于存在立辊侧压的影响,按照刚性理论研究,轧件会形成一个“鱼尾”或者“舌形”的头尾部。
这是因为轧件金属更加容易按轧制方向流动,却比较难产生预期宽展和增厚,
导致端部变形明显,经过水平轧制后,
端部的变形不但不会变小,反而会加长,造成变宽或者失宽现象,如果宽度偏差大于允许范围值,则需要切除不合格端部,导致成形率下降。
为提高轧件轧制的收益率,短行程控制应运而生,下面介绍其在热轧粗轧中的应用。
1 短行程控制简介
普通轧钢模式立辊一般不动,但是由于头、尾金属经过水平辊道次后,就像擀面杖擀面条一样,钢件中间压缩的金属会向头部和尾部流动,形成“鱼尾”状端部,如图1所示。
图1 普通轧件轧制示意图(未采用短行程控制)
为提高轧件轧制的收益率,短行程控制应运而生,这是因为侧压调宽后轧件端部曲线会压缩,立辊的辊缝会相对正常轧制增大,
其目的是补偿水平辊轧制后的宽度,这样就会减少头、尾部失宽度。
短行程轧制示意图如图2所示。
由图2可以看出立辊控制轨迹,侧压量增大,头尾部宽度改变明显。
当然,
立辊侧压量增大多少,采用什么方式进行调节可以使失宽度减小,
这是短行程控制的难题。
图2 短行程轧制示意图
2 短行程控制方式
2.1 双折线短行程控制方式
在实际控制过程中,某钢厂某生产线粗轧热轧立辊的短行程控制采用的是双折线短行程控制方式,控制曲线采用直线近似代替。
其具体控制方法为:轧制板坯头部时,
开口最大,轧制进行时,逐步减小辊缝直至静态轧制标准。
尾部方式相反,由静态辊缝逐渐增大,到达尾端时,开口度最大。
采用此辊缝变化的控制方式,经水平轧制后,带钢头、尾部形状得到很大的改善,提高了成形率。
2.2 二项式方程在短行程控制中的应用
折线控制大大改善了带钢的头、尾部形变,给钢厂
带来了较大的收益,
如何优化短行程控制,带来更大的经济效益,是众学者、专家研究的课题。
下面以轧件端部形状为模型,介绍二项式方程在短行程控制中的应用。
短行程控制模型如图3所示。
其中,SH1为短行程尾部宽度,SH2为短行程中部宽度,LH1为短行程控制全长,LH2为短行程控制中部长度,S0为轧件期望宽度。
折线控制需要3个点,分别为图3中的点1、点2和点3,由这3点亦可拟合出二项式方程:
y=a0+a1(l-x)+a2(
l-x)2。
其中:x为短行程控制点到端部的距离;l为头部短行程控制长度,l=LH1;y为立辊的开度修正量;a0、a1、a2
为多项式系数,采用3点法确定:
a0=S0,
a1
=(SH2-S0)LH2LH1-LH2-(SH1-S0)(LH1-LH2)LH1LH2,a2=
(SH1-S0)LH1LH2-(SH2-S0)LH2(LH1-LH2)。
图3 短行程控制模型
根据某一钢种的现场数据,比较折线控制方式与二项式控制方式。
图4为两种控制方式下头部开度的变化曲线。
图5为不同的控制方式下带钢头部宽度的变化曲线,从图5中可以看出二项式控制方式比折线方式有着明显的改善。
3 结束语
采用多项式曲线代替传统的折线控制方式,不但
可以减少折线控制产生的误差,
而且能更好地控制轧件头、尾部形状的变化,减少了头尾部的剪切量,增加了轧钢的成形率。
图4
两种控制方式下头部开度的变化曲线
图5 不同控制方式下带钢头部宽度的变化曲线
参考文献:
[1] Ginzburg
V B.高精度板带材轧制理论与实践[M].姜明东,译.北京:冶金工业出版社,2000.
[2] 孙一康.
带钢热连轧的模型与控制[M].北京:冶金工业出版社,2007.
[3] 汪祥能,
丁修坤.现代带钢连轧机控制[M].沈阳:东北大学出版社,1996.
App
lication of Binomial Control of Roller in Short StrokeCHU
Xi(College of Information Engineering,Anhui University
of Technology,Ma’anshan 243000,China)Abstract:The application of binomial control will reduce the fishtail shape deformation in both ends of the slab in hot rolling course,which can not only optimize the control curve,but also decrease the slab head cut to increase the financial benefit.This paperintroduced the principle and application of binomial control in hot rolling.Key
words:short stroke control;creased control;櫆櫆櫆櫆櫆櫆櫆櫆櫆櫆櫆櫆櫆櫆櫆櫆櫆櫆櫆櫆櫆櫆櫆櫆櫆櫆櫆櫆櫆櫆櫆櫆櫆櫆櫆櫆櫆櫆櫆櫆櫆櫆櫆櫆櫆櫆櫆櫆櫆櫆櫆
binomial control(上接第170页)
参考文献:
[1] 汪贵平.
汽车发动机电控汽油喷射系统故障诊断与排除[M].北京:人民交通出版社,2005.
[2] 肖永清.
新型轿车电控系统的原理与故障检修[M].北京:人民邮电出版社,2006.[3] 冯健璋.
汽车发动机原理与汽车理论[M].北京:机械工业出版社,2005.
[4] 张建俊.
汽车检测与故障诊断技术[M].北京:机械工业出版社,1999.
Standardized Process of Modern Automobile Detection and
MaintenanceLIU Cun-
shan(Dongguan Institute of Technology,Dongg
uan 523808,China)Abstract:The modern automobile is a kind of comprehensive sysetm integrating mechanical,electrical,fluid technology,we shouldanalyze the phenomenon of failure to determine the fault position and then repair it.This paper takes the automobile startup failure asexample,elaborates the standardization process of modern automobile detection and repair,so that the car can better and fasterrecover its
function.Key
words:auto repair;standardization process;fault analysis·
271·机械工程与自动化 2012年第3期 。