涡轮增压器织构化浮环轴承润滑数值模拟-论文
涡轮增压器浮环轴承静特性分析

C h i n a N o r t h E n g i n e R e s e a r c h I n s t i t u t e , D a t o n g S h a n x i 0 3 7 0 3 6 , C h i n a )
Ab s t r a c t : A t h e o r e t i c a l s t u d y c o n c e r n i n g t h e s t a t i c p e r f o r ma n c e o f t u r b o c h a r g e r lo f a t i ng — in r g b e a r i n g wa s p r e s e n t e d. T h e
GU O Ho n l f Zh an g Sh a ol i n Me n Ri x i u Cen Sh a o q i
( 1 . S c h o o l o f Me c h a n i c a l E n g i n e e i r n g , Z h e n g z h o u U n i v e r s i t y , Z h e n g z h o u He n a n 4 5 0 0 0 1 , C h i n a ;
2 0 1 3年 1 1月
润滑与密封
L UBRI C AT I ON ENGI NEERI NG
NO V . 2 01 3
第3 8பைடு நூலகம் 第 1 1 期
增压器浮环轴承转子系统稳定性的研究

21 年 1 01 O月
铁 道 机 车 车 辆
RAI AY 0COM 0TI LW L VE & CAR
Vo . 1 S p l 13 u p 0c . t 2 1 01
文章 编号 :0 8 8 2( 0 1 0 3 7 4 1 O —7 4 2 1 )S ~O 0 ~O
要 因 为其结 构 简单 , 率 高 , 定性 比普 通 轴 承 优 越 的 效 稳
特 点 , 而在 提 高性能 的 同时也 引起 较 严 重 的非线 性 失 然
测试设备 主要包括转速传 感器 、 电涡 流振 动传感器 、 功率 源 、 信号分析仪及 计算机 。测试框 图见 图 1 动态 。
蚓
h 1\ \ J l 1 v 』1 / l J l I l 1 J j 【 【 f I I J l j 1 t 1fl l 『 l 1 l \ 【 1 l I l I 1 J f I \ \ l f 【 I
行 了 浮环 轴 承 转 速 及 运 动 轨 迹 的测 试 研 究 , 成 了 定 性 分 析 ; 而 根 据 评 判 参 数 采 用 有 限元 法 进 行 了 “ 角 域 ” 完 进 四 下 的定 量计 算 , 验 证 了分 析 结 果 。本 研 究 为 转 子 轴 承 系 统 的 优 化 设计 及 可 靠性 分 析 提供 了技 术 支 持 。 并 关键 词 增 压 器 ;浮 环 轴 承 ; 定 性 稳
浮环轴 承工作 时 以一定转 速旋 转 , 相应 地 减小 了与
轴 颈和 轴承 座 孑 之 间 的 相 对 速 度 , 环 速 度 与 轴 颈 速 L 浮
度、 内外 间 隙 、 半径 比及 内外 间隙 的偏 心度 相关 , 颈 速 轴 度一 定 时 , 环速 度 则 由偏 心度 唯 一 确定 , 此反 映 轴 浮 因
涡轮增压器毕业论文[管理资料]
![涡轮增压器毕业论文[管理资料]](https://img.taocdn.com/s3/m/77e6b0fff18583d0486459ba.png)
河南职业技术学院毕业设计(论文)题目涡轮增压器故障原因分析及使用维护系(分院)汽车工程系学生姓名张俊学号07184008专业名称汽车检测与维修指导教师高云2010年4月26日涡轮增压器故障原因分析及使用维护张俊摘要:涡轮增压已经越来越多的被汽车所使用,也越来越多的被人们所知悉,他的好坏决定着现代汽车动力性,本文主要浅析涡轮增压的使用维护及简单故障原因分析关键词:涡轮增压、使用维护、故障分析一、引言:随着国民经济的迅猛发展,汽车产量逐年增加,2006年已达720万辆。
我国汽车保有量越来越多,车型也越来越复杂。
尤其是高科技的飞速发展,一些新技术、新材料在汽车上得到广泛应用,而涡轮增压在汽车上的应用则赋予汽车更强更大的动力性,且涡轮增压发动机的耗油量也并不比不增压的发动机耗油量高多少,在汽车使用中,增压器难免会有问题,而这将直接影响发动机的动力性,分析研究增压器故障,现象,探索和研究增压器的结构原因具有重大的现实意义。
本文重点通过增压器的结构原理及一些日常维护,正确认识增压器故障,更好的使用和维护增压器。
二、涡轮增压的日常应用:涡轮增压的主要作用就是提高发动机进气量,从而提高发动机的功率和扭矩,让车子更有劲。
涡轮增压的英文名字为Turbo,一般来说,如果我们在轿车尾部看到Turbo或者T,即表明该车采用的发动机是涡轮增压发动机了。
相信大家都在路上看过不少这样的车型,,,三、涡轮增压的原理与类型最早的涡轮增压器用于跑车或方程式赛车上的,这样在那些发动机排量受到限制的赛车比赛里面,发动机就能够获得更大的功率。
众所周知发动机是靠燃料在汽缸内燃烧作功来产生功率的,由于输入的燃料量受到吸入汽缸内空气量的限制,因此发动机所产生的功率也会受到限制,如果发动机的运行性能已处于最佳状态,再增加输出功率只能通过压缩更多的空气进入汽缸来增加燃料量,从而提高燃烧作功能力。
因此在目前的技术条件下,涡轮增压器是惟一能使发动机在工作效率不变的情况下增加输出功率的机械装置。
涡轮增压器轴向力稳态数值模拟及优化

涡轮增压器轴向力稳态数值模拟及优化李庆斌;胡辽平;杨迪;曹刚;闫海东【摘要】Turbine and compressor flow field grid models of a turbocharger were established by using Numeca numerical software. At different engine speeds, the axial forces of turbine and compressor in the steady state were computed. It indicates that the axial force that pointed to the compressor from the turbine was larger and that the opposite force was smaller. Besides, the flow field of compressor was analyzed, which was found that the static pressure distribution at the back of impeller correlated with the axial force closely. Further, the influence of tip clearance of blade on axial force was researched, which was found that not only the increasing axial clearance had more positive effect than that of radial clearance to decrease the axial force, but also the efficiency loss was larger. Finally,the turbine efficiency was not reduced when the cross section of volute was modified and the axial force at high speed of engine decreased by 8 N.%采用Numeca数值分析软件建立了某增压器涡轮机及压气机端流场网格模型,并计算出发动机不同转速下涡轮增压器的涡轮端及压气机端的稳态轴向力分布,分析得出由涡轮端指向压气机端方向的轴向力值较大,而由压气机端指向涡轮端方向的轴向力值较小.对压气机叶轮流场进行了分析,发现压气机叶轮背部间隙内的静压分布与轴向力大小紧密相关;研究了叶轮叶顶间隙对轴向力的影响,发现叶轮轴向间隙对轴向力的影响比径向间隙大,但效率损失亦较大.在保证涡轮机效率不降低的原则下,时涡轮箱流道截面进行了改进,轴向力在发动机高转速下降低约8N.【期刊名称】《车用发动机》【年(卷),期】2012(000)004【总页数】5页(P10-14)【关键词】涡轮增压器;轴向力;流场;数值模拟;优化【作者】李庆斌;胡辽平;杨迪;曹刚;闫海东【作者单位】湖南天雁机械有限责任公司,湖南衡阳 421005;湖南天雁机械有限责任公司,湖南衡阳 421005;湖南天雁机械有限责任公司,湖南衡阳 421005;湖南天雁机械有限责任公司,湖南衡阳 421005;湖南天雁机械有限责任公司,湖南衡阳421005【正文语种】中文【中图分类】TK421.8止推轴承设计是涡轮增压器结构设计的重要组成部分,在止推轴承设计前要计算转子的轴向力,它是压气机叶轮和涡轮叶轮两侧气体压力的代数和[1]。
《基于流固耦合的涡轮叶片三维非定常数值模拟》论文摘要编写
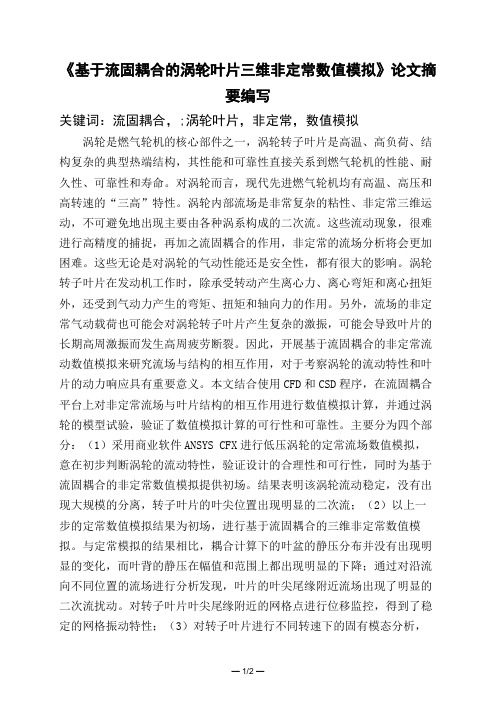
《基于流固耦合的涡轮叶片三维非定常数值模拟》论文摘要编写关键词:流固耦合,;涡轮叶片,非定常,数值模拟涡轮是燃气轮机的核心部件之一,涡轮转子叶片是高温、高负荷、结构复杂的典型热端结构,其性能和可靠性直接关系到燃气轮机的性能、耐久性、可靠性和寿命。
对涡轮而言,现代先进燃气轮机均有高温、高压和高转速的“三高”特性。
涡轮内部流场是非常复杂的粘性、非定常三维运动,不可避免地出现主要由各种涡系构成的二次流。
这些流动现象,很难进行高精度的捕捉,再加之流固耦合的作用,非定常的流场分析将会更加困难。
这些无论是对涡轮的气动性能还是安全性,都有很大的影响。
涡轮转子叶片在发动机工作时,除承受转动产生离心力、离心弯矩和离心扭矩外,还受到气动力产生的弯矩、扭矩和轴向力的作用。
另外,流场的非定常气动载荷也可能会对涡轮转子叶片产生复杂的激振,可能会导致叶片的长期高周激振而发生高周疲劳断裂。
因此,开展基于流固耦合的非定常流动数值模拟来研究流场与结构的相互作用,对于考察涡轮的流动特性和叶片的动力响应具有重要意义。
本文结合使用CFD和CSD程序,在流固耦合平台上对非定常流场与叶片结构的相互作用进行数值模拟计算,并通过涡轮的模型试验,验证了数值模拟计算的可行性和可靠性。
主要分为四个部分:(1)采用商业软件ANSYS CFX进行低压涡轮的定常流场数值模拟,意在初步判断涡轮的流动特性,验证设计的合理性和可行性,同时为基于流固耦合的非定常数值模拟提供初场。
结果表明该涡轮流动稳定,没有出现大规模的分离,转子叶片的叶尖位置出现明显的二次流;(2)以上一步的定常数值模拟结果为初场,进行基于流固耦合的三维非定常数值模拟。
与定常模拟的结果相比,耦合计算下的叶盆的静压分布并没有出现明显的变化,而叶背的静压在幅值和范围上都出现明显的下降;通过对沿流向不同位置的流场进行分析发现,叶片的叶尖尾缘附近流场出现了明显的二次流扰动。
对转子叶片叶尖尾缘附近的网格点进行位移监控,得到了稳定的网格振动特性;(3)对转子叶片进行不同转速下的固有模态分析,— 1/2 —— 1/2 —获得该涡轮的共振转速图,从而确定了该涡轮从起动至设计点工作状态的四个共振转速。
基于Fluent涡轮增压器浮环轴承三维油膜力的仿真

基于Fluent涡轮增压器浮环轴承三维油膜力的仿真作者:郑惠萍彭立强来源:《汽车科技》2016年第01期摘要:浮环轴承具有结构简单、成本低、稳定性好、适应高转速等特点而在航空机械、汽车发动机等领域得到广泛的应用。
本文首先通过Gambit软件建立了浮环轴承的双油膜有限元模型,然后利用fluent软件对轴承的三维油膜力进行模拟分析,研究在相同供油压力下,转速对油膜力分布、承载力的影响。
分析结果表明浮环轴承内外油膜均存在楔形的收敛区和发散区,在这两个区域上分别存在正压值和负压值,其最大值随转速的升高而增大;轴承内外油膜的承载力均随转速的增加而增大。
三维仿真模拟得到的油膜压力分布规律与文献[1]理论计算结论一致,本文给出了一种较准确的油膜力计算方法为后继的研究工作打下了基础。
关键词:浮环轴承;油膜力;有限元模型;油膜承载力中图分类号:TH117 文献标识码:A 文章编号:1005-2550(2016)01-0007-05Abstract: Floating ring bearings have been widely applied in aviation machinery, automobile engine etc for the characteristics of simple structure, low cost, good stability, suitable for high rotation speed etc. This paper first established a double oil films finite element model of floating ring bearing through Gambit software , and then three-dimensional oil film force of the bearing was simulated and analyzed using fluent software and the influence of the rotational speed to the oil film force distribution and bearing capacity was studied in the same oil pressure. Analysis results showed that inside and outside oil film in floating ring bearing have wedge-shaped the region of convergence and divergence zone. The positive pressure and negative pressure exist in these two regions respectively, and the maximum pressure value increases with the rise of rotational speed; inside and outside oil film bearing capacity increases with the rise of rotational speed. 3D simulation results showed that pressure distribution of oil film in floating ring bearings is consistent with documentation [1] theoretical study, this calculation method of oil film force in floating ring bearings is provided as the base of the latter research涡轮增压器是一种空气压缩机,它对提高发动机的功率、减少燃油消耗起到非常重要的作用。
涡轮增压柴油机叶轮疲劳仿真及试验

{ u …
图 1 增 压 器 叶 轮 有 限 元 模 型
( 二) 叶轮 强 度计 算及 分 析 在实际 一 I : 作 中, 叶片牢 【 舌 l 在 底 盘上 , 本 次 分 析 对 叶 片象 。 考虑其 在高速 运转下的载荷情
况, 以C AE 软件 为分 析平 台对 叶轮进 行仿 真分析 , 运用 疲劳 理 论可视程 序化 对疲 劳寿命进行 预测 。 最后 以发 动机考核试验 的 试 验结 果对理论分析进 行了验 证, 发现此 型号叶轮疲 劳寿命 满 足发动机 l T作 需求 , 为叶轮 的设计工作 提供理论 依据 。
涡轮 增压 柴 油机 叶轮 疲 劳仿 真及 试 验
口柳 州铁 道 职 业 技 术 学 院 杨 玲 玲
口北汽黑豹 ( 威海 ) 汽车有限公 司 席德明
【 摘
要】 本 文以增压 器叶轮 为研 究对 象, 以满足涡轮 增压
低 周 疲 劳 寿 命 具 有 重 要 意义 。 二、 有 限 元模 型 仿 真计 算
本 文所 研 究 的 p - 轮 材 料 为 锅 合 金 C3 5 5 T 6 1 ,弹 性 模 量
E = 6 . 9 x 1 0 Mp a , 泊松比0 . 3 1 。I 于叶轮 的外形结 构较 为复杂, 本
【 关键 词 】 柴油机 涡轮增压 器 叶轮 疲 劳 史密斯公式 【 中图分 类号 】 G 【 文献标识码 】 A 【 文章编号 】 0 4 5 ( 1 — 9 8 8 9 ( 2 0 1 7 ) 0 5 C 一 0 1 9 0 — 0 3
其 中,△ s 为局部应变 幅值 ,A c t 为局部应力幅 值, £ 为弹性 模量 ,k 为循环强度 系数 ,, l 为循环应变硬化指 数。 此 理论在前人学 者不 断研究试验 的基础上 , 有众 多方 法理
211003044_涡轮增压器超高速轴承一转子动力学建模及模态参数识别

Dynamic Modeling and Modal Parameter Identification ofUltra-high Speed Bearing-Rotor of Turbocharger *Ping Gong 1Zhen-hui Hu 2Qing-shan Zhang 2Ri-xiu Men 3Shi-yuan Pei 2,*(1.China Aviation Development Harbin Bearing Limited Company;2.Key Laboratory of Education Ministry for Modern Design and Rotor-Bearing System,Xi’an Jiaotong University;3.National key Laboratory of High Turbocharging Technologyfor Diesel Engine,North China Engine Research Institute)Abstract:Aiming at the problems of traditional turbocharger ultra-high speed bearing-rotor system,such as low accuracy of dynamic modeling,difficult identification of modal parameters and so on,the dynamic model and differential equation of motion of turbocharger are established based on Timoshenko beam theory.The modal parameters of turbocharger under different excitation positions and with or without pre-tightening force are identified by hammering test.And the theoretical and experimental results are compared and verified.The results show that when the excitation turbocharger is in different positions,the excitation modes of the system are different.The pretightening force has an important influence on the dynamic analysis results of the rotor,and increasing the pretightening force can significantly improve the rotor stiffness.The established dynamic model and modal identification method have certain accuracy and applicability,which can provide theoretical and experimental basis for subsequent turbocharger structure optimization design and modal parameter identification.Keywords:Timoshenko Beam Finite Element Theory;Dynamic Modeling;Turbocharger;Modal Test;Frequency Response Function摘要:针对传统涡轮增压器超高速轴承-转子系统动力学建模精度不高、模态参数不易识别等问题,基于Timoshenko 梁理论建立了涡轮增压器动力学模型及运动微分方程,利用锤击法试验对增压器不同激励位置、有无预紧力等工况下的模态参数进行了识别,并将理论与试验分析结果进行了对比验证。
涡轮增压器轴承体耦合传热的数值仿真

涡轮增压器轴承体耦合传热的数值仿真作者:龚金科田应华贾国海章滔来源:《湖南大学学报·自然科学版》2015年第04期摘要:基于涡轮增压器轴承体冷却机理,采用专业CFD软件和FEM软件分别建立了轴承体流体区域和固体区域网格仿真模型.运用流固耦合的仿真计算方法对涡轮增压器轴承体进行耦合传热分析,得到轴承体流体区域的流场、换热系数及温度场,并分析轴承体固体区域的温度场.仿真结果表明:机油和水同时冷却方式下,轴承体温度分布较均匀,其冷却性能较好.与实验对比,仿真模型的温度符合实际轴承体温度分布,证明了此方法的可行性,为轴承体冷却性能的设计优化提供依据.关键词:涡轮增压器;温度场;冷却轴承体;流固耦合摘要:基于涡轮增压器轴承体冷却机理,采用专业CFD软件和FEM软件分别建立了轴承体流体区域和固体区域网格仿真模型.运用流固耦合的仿真计算方法对涡轮增压器轴承体进行耦合传热分析,得到轴承体流体区域的流场、换热系数及温度场,并分析轴承体固体区域的温度场.仿真结果表明:机油和水同时冷却方式下,轴承体温度分布较均匀,其冷却性能较好.与实验对比,仿真模型的温度符合实际轴承体温度分布,证明了此方法的可行性,为轴承体冷却性能的设计优化提供依据.关键词:涡轮增压器;温度场;冷却轴承体;流固耦合涡轮增压器安装在发动机的进排气歧管上,在高温、高压和高速运转的恶劣环境下工作\[1\],其各部件的温度分布不均匀,对于轴承体,存在较大温差,承受着很大的热应力.轴承体作为增压器结构中的重要组成部分,起到支撑密封环和浮动轴承的作用,而密封环和浮动轴承又是涡轮增压器可靠性中的薄弱环节,轴承体的热负荷程度直接影响到密封环和轴承的使用寿命和工作可靠性\[2-5\].国内外为了降低涡轮增压器全浮动轴承和密封环附近温度,目前普遍采取用机油、水同时冷却的方式,并对其腔体进行优化设计\[6-7\].但对于两种液体同时冷却的方式缺乏系统的传热分析和流场的研究.本文基于轴承体冷却机理,利用专业CFD软件和FEM软件对某发动机涡轮增压器轴承体进行耦合传热数值仿真研究,即同时采用机油和水对轴承体进行冷却.通过计算得到轴承体流体区域的流场、换热系数和温度场分布,以及其固体区域的温度场,并将仿真计算值与实验值进行对比验证.1 涡轮增压器轴承体传热原理采用有限单元法对流体的流动与传热进行数值仿真,首先需要建立反映工程本质的数学模型.涡轮增压器轴承体传热的数学模型包括冷却水和机油的流动与传热模型、轴承体固体导热模型和冷却介质与轴承体交界面的耦合传热模型.在冷却水和机油的流动与传热计算中,其流动和传热过程都遵从质量守恒、动量守恒和能量守恒定律.对于涡轮增压器轴承体内腔冷却液与轴承体之间的换热问题,只在内部壁面边界上存在热量交换,由于流体温度与固体壁面温度之间是相互制约的关系,边界条件无法预先确定.其边界上的温度、换热系数,都应看成是计算结果的一部分,而不是已知条件\[9\].由边界面的热平衡可知,在轴承体内部导向边界的热流密度等于从边界面传给周围流体的热流密度,即在涡轮增压器轴承体流固耦合传热边界上,固体传出的热量等于冷却液吸收的热量,由傅里叶定律和牛顿冷却公式可得\[8\]:-λ(Tn)w=h(Tw-Tf).(3)式中:λ为导热系数,W/(m·K);h为换热系数,W/(m2·K);Tw为壁面温度,K;Tf为流体温度,K.本文所使用的FEM软件提供了流固耦合传热交界面模型,即流体域和固体域几何位置重合的面,如图1所示.在进行流固耦合传热仿真计算时,固体域和流体域之间可通过此交界面进行数据传递.当CFD软件仿真计算出流体区域的壁面温度和换热系数,将数据映射到图1所示的耦合传热交界面上,成为FEM软件计算的第3类热边界条件.经过FEM软件仿真计算后,得到轴承体固体区域的温度场,再通过耦合传热交接面将固体区域内部壁面温度映射到流体区域,成为流体CFD软件计算的边界条件.如此反复计算,直到轴承体节点上的温度不再变化为止.其过程如图2所示.2 涡轮增压器轴承体仿真模型2.1 涡轮增压器轴承体网格仿真模型涡轮增压器轴承体在实际工作中,存在着机油、冷却水、涡轮轴、涡轮箱、压气机之间的传热情况,在进行数值仿真计算前,为了简化分析影响轴承体冷却性能的主要因素,对轴承体外表面倒角和细小结构进行简化,可避免计算出错并使计算收敛更快.在三维建模软件中按照轴承体实际尺寸建立几何模型,导出x_t格式文件,利用网格软件分别抽取轴承体冷却油腔和冷却水腔,并将其导入CFD软件进行网格划分,如图3和图4所示.对于固体区域,为保证内部细小尺寸结构不失真,设置了最小网格尺寸,同时为了控制轴承体网格的数量,也设置了网格的最大尺寸,其网格如图5所示.2.2 物理模型材料准确的材料物性参数是仿真分析获得准确结果的重要前提.在该FEM软件中,对于固体域通常需要提供固体材料的热传导率、比热容、密度等参数.涡轮增压器轴承体的材料选用灰铸铁(HT)250,密度为7 280 kg/m3,比热容为510 J/(kg·K),泊松比为0.156,热传导率为45 W/(m·K),线膨胀系数为9×10-6 K,杨氏模量为138 000.对于流体区域的冷却液则需要定义其密度、比热容、动力粘度及导热系数等.当冷却液压力一定时,其物性参数只与温度有关,即温度的单值函数.2.3 边界条件在本文研究的流固耦合计算模型中,固体壁面的边界条件主要是指轴承体涡轮端和压气机端传热边界条件,不考虑辐射的影响.控制涡轮增压器转速为80 000 r/min,涡轮进气温度800 ℃,在该工况下通过传热边界测试获取轴承体涡轮端、压气机端的初始温度.在计算过程中,认为冷却液的流动是三维不可压缩的粘性湍流流动,湍流模型采用kε湍流模型.机油的入口采用压力边界条件,压力入口为0.3 MPa,温度为100 ℃,冷却水进口采用流速边界条件,流速为1.5 m/s,温度为80 ℃,机油和冷却水的出口都采用压力边界条件,分别为0.15 MPa和0.2 MPa.轴承体表面采用无滑移壁面边界条件.由于轴承体通过其外壁面散热,设环境温度为25 ℃,热传递系数为50 W/(m2·K).3 仿真计算结果通过仿真计算得到增压器轴承体流体区域的流场、换热系数和温度场分布以及固体区域的温度场.3.1 流场分析图6给出了冷却油腔内机油速度流线图,机油入口末端管径变小,机油速率迅速增加,并分为三股流分别流向油腔顶部、中部和底部,使得机油充满整个腔体.腔体内速度流线分布均匀,机油流动顺畅,有利于机油对轴承体的冷却.3.2 流体域壁面换热系数如图8所示,机油腔体壁面换热系数从涡轮端至压气端,先减小,后增大,形成明显的换热系数梯度.最大换热系数分布在细小油道靠近涡轮端侧,当涡轮轴高速旋转时,机油与轴承体进行剧烈换热,较高的换热系数主要分布在机油腔体进口管道、细小油道以及腔体底部和顶部,大约在800~2 000 W/(m2·K)之间.在机油出口端,换热系数有所下降,大概在400~800 W/(m2·K)之间.这是由于换热系数与温差、机油流速等有关.当机油经过轴承冷却后,其温度上升,与轴承体的温差减小,且腔体的出口管道截面积比进口大,机油流速下降,故此区域换热系数变小.图中所示深蓝色区域,换热系数最小,主要由于机油流速在此区域较小,与轴承体换热较差.3.3 流体区域壁面温度场分析图9为机油腔体壁面温度场分布云图,温度从腔体顶部至底部依次降低,由于机油腔体上部分靠近涡轮端,热量来自发动机气缸中排出的废气,通过涡轮箱而传递到轴承体的顶部,热量从轴承体的涡轮端至压气端依次传递,为了充分冷却轴承体,热量传递至机油腔体时,流过腔体的机油带走一部分热量,越靠近涡轮端,带走的热量越多,相反,靠近压气端带走的热量较少,故油腔呈现明显的温度梯度.从图9中可知,机油腔体壁面温度最高为536.69 ℃,最低温度分布在靠近压气端一侧,为101.45 ℃.图10为水冷腔体壁面温度场分布云图,其温度分布与机油腔体壁面相似,温度从涡轮端至压气端都是依次递减.最高温度为553.57 ℃,最低温度为158.53 ℃.对比图9可知,水冷腔壁面最高温度略高于油腔壁面最高温度.3.4 轴承体温度场分析如图11所示,轴承体整体温度从涡轮端至压气端依次递减,最高温度分布在与涡轮废气直接接触的区域,约为550~600 ℃.经过水和机油的冷却,轴承体靠近压气端一侧温度下降至95.17 ℃.图12为轴承体切片温度云图,其内部温度从高至低过渡自然,温度梯度变化缓慢.在正常工况下,发动机尾气的热量通过涡轮箱传递给轴承体,一部分被冷却介质带走,另一部分传导至压气机,与此同时,涡轮轴高速旋转所产生的一部分热量通过机油传递至轴承体.水和机油同时冷却方式下,轴承体冷却效果最佳,不易产生局部高温和热应力,轴承体工作较稳定,保证了涡轮增压器的可靠性与耐久性.4 实验验证对涡轮增压器轴承体的温度分布进行数值模拟时,仿真结果的精确程度与传热边界条件的确定直接相关.为测得准确的实际轴承体局部温度值,需在涡轮增压器轴承体的不同位置布置测温点[9].热电偶是温度测量仪表中一种常用的测温原件,通过将热能转换成电能,再使用电气仪表读取被测介质的温度.其使用寿命长、装配简单,具有测量范围大、测量精度高等优点,能够在高温环境中工作.在涡轮增压器轴承体的传热试验中,采用WRTK112工业铠装热电偶分别对轴承体外表面和内腔进行温度测量并验证模拟仿真的准确性,其测点位置如图13所示.本实验为了模拟发动机排气,利用经过燃烧室加热的气体驱动涡轮增压器转动,控制增压器转速为80 000 r/min,涡轮进气温度为800 ℃,待增压器稳定运行后,测取验证条件.如图14所示,仿真计算结果和实测结果基本吻合,其最大误差仅为4.6%,图15为涡轮增压器轴承体温度测量实验装置.上述结果表明仿真模型的温度分布符合实际轴承体温度分布,采用计算流体力学软件和有限元软件相结合进行流固耦合仿真的方法对涡轮增压器轴承体传热和冷却性能的研究是可行的.5 结论本文采用流固耦合的方法对某发动机涡轮增压器轴承体进行耦合传热分析,结果如下:1)机油的流场表明:机油在腔体内流动顺畅,总体速度分布较均匀.2)机油腔体壁面换热系数从涡轮端至压气端,换热系数先减小,后增大,形成明显的换热系数梯度,其入口端换热系数大于出口端.3)流体区域壁面温度从腔体顶部至底部依次降低,但水冷腔体壁面最高温度略高于机油腔体壁面的最高温度.4)轴承体固体温度从涡轮端至压气端依次递减,温度梯度变化缓慢,其内部温度分布较均匀,不易产生局部高温和热应力.5)通过计算结果与实验结果的比较,模型仿真的整体温度场分布基本符合实际轴承体的温度分布,证明了此仿真方法的可行性.参考文献[1] 胡友安,李晓东,陈图钧,等. 涡壳温度场和热应力的有限元分析 [J]. 机械强度,2007, 29(1): 130-134.HU Youan, LI Xiaodong, CHEN Tujun, et al. Analysis on temperature field and thermal stress of turbocharger housing by finite element method [J]. Mechanical Strength, 2007, 29(1): 130-134. (In Chinese)[2] 胡群,韩同群,张云鹏. 车用涡轮增压汽油机冷却系统设计与匹配 [J]. 湖北汽车工业学院学报, 2008(4):18-22 .HU Qun, HAN Tongqun, ZHANG Yunpeng. The design and matching of cooling system for turbocharged gasoline engine on vehicles [J]. Journal of Hubei Automotive Industries Institute, 2008 (4): 18-22. (In Chinese)[3] 朱大鑫. 涡轮增压与涡轮增压器 [M]. 北京:机械工业版社, 1992.ZHU Daxin. Turbocharged technology and the turbocharger [M]. Beijing: Mechanical Industry Press, 1992. (In Chinese)[4] 黄智昊. 涡轮增压器发展前景分析 [J]. 商用汽车, 2004(12): 88-89.HUANG Zhihao. The prospects analysis of turbocharger development [J]. Commercial Vehicle, 2004(12): 88-89. (In Chinese)[5] 胡友安,李晓东. 涡轮增压器蜗壳热裂纹的试验研究 [J]. 河海大学学报, 2008, 36(6): 846-849.HU Youan, LI Xiaodong. Experimental study on heat cracks of turbine housing on turbochargers [J]. Journal of Hehai University, 2008, 36(6): 846-849. (In Chinese)[6] 徐行军. 柴油机冷却系统结构优化及缸盖热应力分析 [D]. 天津:天津工业大学,2010:14-15.XU Hangjun. Structural optimization for diesel engine cooling systems and thermal stress analysis for its cylinder head [D]. Tianjin: Tianjin Polytechnic University, 2010: 14-15. (In Chinese)[7] 傅松,胡玉平,李新才,等. 柴油机缸盖水腔流动与沸腾传热的流固耦合数值模拟 [J]. 农业机械学报, 2010, 41(4): 26-30.FU Song, HU Yuping, LI Xincai, et al. Numerical simulation of water flow and boiling heat transfer for cooling chamber of cylinder head on diesel engine by fluidsolid coupling method [J]. Journal of Agricultural Machinery, 2010, 41 (4): 26-30. (In Chinese)[8] 贾力,方肇洪. 高等传热学 [M]. 北京:高等教育出版社, 2008.JIA Li, FANG Zhaohong. Advanced heat transfer [M]. Beijing: Higher Education Press,2008. (In Chinese)[9] 徐思友,吴新涛,闫瑞乾,等. 增压器轴承和密封环温度试验研究 [J]. 车用发动机,2010(2): 35-37.XU Siyou, WU Xintao, YAN Ruiqian, et al. Experimental study of temperature for bearings and seal rings on turbocharger [J]. Vehicle Engine, 2010(2): 35-37. (In Chinese)。
涡轮风扇结构于数值模拟优化设计

涡轮风扇结构于数值模拟优化设计摘要摘要:采用有限元方法分析出涡轮风扇支板个数为10时发生断裂的原因是高周疲劳破坏,并且叶片发生疲劳的主要原因是支板个数设置不合理.通过Campbell图分析出了两种优化方案,即支摘要:采用有限元方法分析出涡轮风扇支板个数为10时发生断裂的原因是高周疲劳破坏,并且叶片发生疲劳的主要原因是支板个数设置不合理.通过Campbell图分析出了两种优化方案,即支板个数为3和19.从共振点个数、应力水平及理论寿命来看,支板个数为19均优于3.分别对支板个数为10和3的叶片进行疲劳寿命模拟计算,结果表明,两者的疲劳寿命均较短,不符合工程实际要求,最终确定支板个数19为优化方案.关键词:涡轮风扇叶片;支板;振动;疲劳;优化设计0引言风扇在航空涡轮增压器[1]中的主要作用是为压气机散热,其包括风扇导流环、支板、风扇叶轮、风扇罩等.在工作过程中,风扇与涡轮同轴连接,随着涡轮轴的转动而转动,涡轮风扇工作时具有转速高、转速变化范围较宽、形体单薄、气动载荷较大及热载荷大等特点[2],因此涡轮风扇叶片出现故障的次数较多,其工作状态和使用年限直接影响涡轮增压器的故障发生.目前,对于叶片与轮盘振动破坏及疲劳分析时,徐可宁等[3]利用三维叶轮机械气动弹性分析软件AEAS,对某压气机转子错频叶盘结构进行了振动响应分析,吴承伟等[4]采用疲劳分析方法对离心式叶轮叶片进行了寿命计算并提供了一种计算方式,得出影响离心压缩机叶片寿命的因素包括稳态平均应力及交变应力.金鑫[5]等采用通用动态尾流理论进行风力机气动力学计算,对叶片进行加载分析,得出风力机系统振动耦合分析.关振群等[6]对闭式叶轮的振动特性及叶轮的疲劳寿命提出了运用有限元的方法对其进行计算.总之,国内大多数研究人员对叶片进行振动破坏及疲劳寿命分析时,主要是利用单一的求解方法,很少能够全部采用有限元数值方法对叶片进行振动特性分析及疲劳寿命计算,进而优化结构.基于上述原因,本文在动强度及疲劳分析理论基础上,运用ABAQUS对涡轮风扇叶片进行分析,并采用Campbell图得出了两种优化方案,通过进行激振力模态分析及疲劳寿命计算,最终确定出较合理的优化方案.1涡轮风扇动强度分析1.1风扇有限元模型建立涡轮风扇由叶轮和导流罩两部分组成,导流罩外壁与内壁之间通过10个支板连接.其中叶轮由17个叶片组成,考虑到整体模型划分网格时工作量大的问题,依据整体模型具有循环对称性的优势,取整体模型沿着周向的1/17扇形(单只叶片)作为基本模型,这样能有效降低计算时间,提高分析效率.模型建立过程中,由于所提供的IGS格式几何文件中的模型为壳体,需将几何模型导入UG中,选择合适的公差将涡轮风扇缝合为实体,建立成单只叶片的模型.之后采用通用CAE前处理软件Hypermesh建立风扇的有限元模型,即将取出的单只叶片导入Hypermesh中进行单只叶片有限元网格划分,共计14162个单元,17880个节点.具体模型见图1.1.2材料属性和边界条件(1)材料属性风扇选用材料为钛合金,由于计算过程中不考虑热应力的作用,忽略材料随温度的变化,取钛合金(TC4)在常温下的材料属性,钛合金参数见表1.(2)边界条件涡轮作为动力,通过轴的传动带动风扇转动,在施加边界条件时需要将轴孔处的所有节点x、y和z方向位移固定,即:U1、U2和U3同时为0,同时选定转轴Z轴,沿着Z 轴方向创建2个基准点,作为旋转方位,施加周期性边界条件,叶片数为17,并且施加循环对称约束边界条件,如图2所示.1.3载荷与动强度分析1.3.1载荷计算动强度时需要在ABAQUS中给定转速10、25000、45000、50000、52000、60000rpm;叶片设置了10个支板,空气经过导流罩入口,经过支板流向风扇叶轮,由于支板的存在导致流过叶片的空气不均匀,风扇叶片每旋转一周,这种不均匀性的气体作用一次,从而产生了周期性的气流激振力,设气流激振力的频率[7]为式中n为风扇叶片的转速,单位r/s;i为支板个数,取10;T为气流激振力的周期,单位s;w为激振力的圆频率,单位rad/s.气流激振力的计算结果,通过NUMECA可以得出,取为800Pa.1.3.2动强度分析将给定转速与气流激振力加载到叶片模型上之后进行模态分析,具体结果见表2.为了进一步研究叶片的共振特性,得出共振点转速与共振频率,确定低阶次频率之后,还要考虑与支板个数相等的动频、与风扇叶片数相等的动频阶次以及风扇叶片个数与支板个数之差相等的动频阶次.根据表2绘制了Campbell图,见图3.图3中主要关注17倍频(K=17,17为风扇叶片个数),10倍频(K=10,10为支板个数),7倍频(K=7,7为风扇叶片个数与支板个数之差),1倍频和2倍频.同时垂直横轴设有一条实线和两条虚线,实线代表涡轮风扇叶片的工作转速范围内的最大值52000rpm.两条虚线表示安全裕度,左侧虚线代表工作转速范围内最小值25000rpm的85%,即21250rpm,右侧虚线代表超过工作转速范围内的最大值52000rpm的10%,即5200rpm.判断单只风扇叶片共振分析时,只要倍频线与基频线的交点出现在转速波动范围内,即产生共振,该交点就是共振点,通过共振点可确定发生共振时的频率与转速.表3就是通过图3确定的共振转速.从图3的Campbell图和表3可以看出,在工作转速范围内,共有六个共振转速.由支板个数(10)带来的激励源,使叶轮存在三个共振转速:与二阶模态对应的转速为24006rpm,与三阶模态对应的转速为32706rpm,与四阶模态对应的转数为53234rpm;由风扇叶片数(17)与支板(10)的差数7带来的激励源,其共振转数有两个:二阶模态时相应转速34850rpm,三阶模态时相应转速48975rpm;而由风扇叶片数(17)带来的激励源,其共振转数有一个:与四阶模态对应的转数为30489rpm.六个共振转速中,模态为弯曲振型最危险,即转速32706rpm和转速48975rpm是最危险的共振转速.在最危险共振转速工况下对叶片进行静强度分析,结果见图4.在共振转速48975rpm下的应力大于共振转速32706rpm产生的应力值,对照S-N 曲线可知,应力S越大,疲劳寿命N越短,高周疲劳(应力疲劳)破坏产生,因此共振转速48975rpm是更加危险的工况.从上述分析过程中不难看出,风扇叶片个数、支板个数及两者差别均会带来激振源,其所产生的共振更会造成风扇叶片累计损伤.所以在调整风扇叶片个数较困难的情况下,由支板个数不合理导致风扇叶片在其工作转速范围内存在共振点的个数过多,即使当风扇工作在共振转速附近时可以通过人为控制,但由于共振点个数过多,也很难实现,由此证明支板个数为10是不合理的.2风扇结构优化设计2.1确定优化方案针对支板个数为10的风扇叶片分析中出现的问题,确定支板个数为奇数时更能满足17只叶片的工作要求,同时从图3中可以看出,考虑避开风扇共振区域,只能在共振区域两端进行选择,所以最终将支板个数调整为3个和19个,并分别对其进行对比分析,确定最优方案.2.2优化模型动强度分析在计算优化模型过程中,分析步的设置与原模型只需将加载气流激振力调整为18000Pa和25000Pa即可.2.2.1支板个数分别为3和19时,涡轮风扇动强度分析由于只考虑单只风扇叶片是否会发生共振,所以根据计算结果直接绘制Campbell 图.图5中,支板个数为3的存在5个共振点,而支板个数为19的存在4个共振点,每个共振点下计算出的共振转速与共振频率见表4、5.利用表4得出支板个数为3时,存在五个共振点:危险转速一(32750rpm)是由支板个数3导致的;危险转速二与危险转速五则是由叶片个数17与支板个数3导致的,即与14倍频线有两个交点;危险转速三(37325rpm)与危险转速四(33583rpm)是由叶片个数17导致的.其中,一阶弯曲在五个共振点中是最危险的,最终确定了最危险共振转速37250rpm.通过表5分析可得,虽然支板个数为19时,仍然会出现4个共振点,但是在这4个共振点发生的振型中并没有出现弯曲振型,因此相比其他支板个数有明显优势,但仍需要进行强度分析.弯扭复合与二阶扭转相比,对风扇叶片产生的疲劳损伤更为严重,因此在以上4个共振点中我们确定危险转速二是最危险的情况,此时共振转速为30489rpm.在最危险共振转速工况下对叶片进行静强度分析,结果见图6.从图6和表6中可以看出,支板个数为19与支板个数为3时均存在共振的情况,但支板个数为19的共振转速和共振时产生应力值均小于支板个数为3的情况,同时对照S-N 曲线可知,应力S越大,疲劳寿命N越短,支板个数为19的寿命均高于支板个数为3的寿命.3疲劳寿命计算3.1疲劳寿命计算模型选择的计算模型与前面动强度计算相同,而且由于整个运算过程相同,通过共振分析确定支板个数为19的寿命均高于支板个数为3的寿命.为了避免重复,只对支板个数为10和3的叶片进行疲劳寿命分析,运用fe-safe与ABAQUS联合计算,选出合理的优化结构.3.2高周疲劳载荷谱确定涡轮风扇叶片高周疲劳载荷谱由应力均值σL和高周应力幅值σa两部分组成,其中应力均值σL是由涡轮风扇叶片在离心力载荷与稳态气流力载荷作用确定的应力值,而高周应力幅值σa是气流激振力产生的扰动应力.但同一个风扇叶片上,应力均值σL和高周应力幅值σa并不是出现在同一位置,为了安全考虑,以最危险工况为准,将其视为发生于同一点,于是确定风扇叶片的高周疲劳载荷谱.图7是一个循环周次下高周疲劳载荷谱.3.3疲劳计算结果分析(1)支板个数为10时疲劳寿命图8显示,风扇运转过程中疲劳寿命最短处发生在叶身处,通过线性化得出支板个数为10的涡轮风扇叶片在经过1.47×109周次的循环后,风扇叶片的根部即发生了疲劳断裂,最先发生断裂的位置是在第7419单元1号节点位置,该位置也是叶片叶身最大应力处,发生断裂时共振的频率是1487Hz,折算后约为85h,也就是支板个数为10时,在发生共振情况下,涡轮风扇叶片在运转85h后出现了疲劳断裂.(2)支板个数为3时疲劳寿命图9中,风扇叶片最短疲劳寿命发生的位置与支板个数为10时相同,疲劳寿命分布状况基本一致,而支板个数为3时疲劳寿命有了较大提高,经测得风扇叶片叶身处的最短寿命为2.73×109周次,转化后约为153h.从以上数据中可以看出,支板个数为3时疲劳寿命虽有高于支板个数为10的情况,但两者均较短.因而对于涡轮风扇而言,风扇叶片是其核心部件,设计时采用的是无限寿命设计方法,要求其寿命较长,但是通过上述两种情况的对比分析,不难发现,支板个数为3的优化方案仍然不能满足要求,结合S-N曲线分析,最终确定采取支板个数为19的优化方案.4结论(1)对支板个数为10的风扇叶片进行动强度分析,结果表明,风扇叶片个数、支板个数及两者差别均会带来激振源,其所产生的共振更会造成风扇叶片累计损伤,进而使叶片产生高周疲劳破坏,且共振点个数较多,即支板个数为10是不合理的.(2)分别对支板个数为3和支板个数为19的涡轮风扇进行动强度分析,结果显示,支板个数为19时,单只风扇叶片出现的共振点是4个,与支板个数为3时相比共振点的个数减少,应力水平较低,寿命较高,不会出现高周疲劳破坏,支板个数为19的方案较优.(3)对支板个数为10和3的叶片进行疲劳寿命模拟计算,结果得出,支板个数为3时疲劳寿命虽高于支板个数为10的情况,但两者均较短,不符合实际工作要求,优化结构选择支板个数为19的方案.参考文献:[1]宋凯,刘堂先,李来平,等.航空发动机涡轮叶片裂纹的阵列涡流检测仿真[J].航空学报,2014,35(8):2355-2363.[2]苏清友.航空涡喷、涡扇发动机主要零部件定寿指南[M].北京:航空工业出版社,2004:181-195.[3]徐可宁,王延荣.压气机转子错频叶盘结构振动响应分析[J].燃气涡轮试验与研究,2013,26(3):6-11.[4]吴承伟,关振群,郭杏林.大型离心压缩机叶轮叶片疲劳可靠性分析[J].装备制造技术,2008,8(1):1-3.[5]金鑫,何玉林,杜静.风机结构耦合振动分析[J].中国机械工程,2008,19(1):9-13.[6]关振群,王鄢,杨树华.大型离心压缩机闭式叶轮动力特性分析[J].大连理工大学学报,2012,52(3):320-326.[7]曲震,柳恺骋.基于周期对称的大小叶片叶盘振动特性分析[J].滨州学院学报,2015,31(2):32-37.。
浮环轴承润滑过程的二维数值分析

维普资讯
望 ! = ! 圣
C 『 1一l 4 /I 4 1 8 ,H -
B n 0 6, . 1 e g 2 0 No 1
轴承 2 0 0 6年 l 期 l
l一4、 5 2
. 产品 设计 与应 用- . I . .
浮环轴承润滑过程的二维数值分析
张 勇, 叶子波
( 华南理工大学 汽车学院, 广东 广州 50 4 ) 16 0
摘要: 以流体滑动轴承的润滑理论 为基础 , 分析研究浮环轴承 的工作机理和结构 参数与性能 的关 系。对 浮环
轴 承建立力平衡 、 力矩及摩擦 功率 损失的方程式 , 得出轴承内外膜承载能力 与相应 转速 比、 间隙 比、 心率等 偏 参数之 间的关 系。绘制 出浮环轴承压力 、 转速 比随间隙比等参数变化 的曲线图 , 为浮 环轴承的设计 提供 理论
主要 符 号说 明
c一 内外 间隙代数和 . C——轴颈 一 。 浮环的间隙( 内间隙)
C——浮环 一 轴瓦的间隙( 外间隙) e _ 偏 心距 - - F—— 内膜 的摩擦力 F——外膜 的摩擦力 。 ^ —— 油膜 厚度
日 一 无量 纲膜 厚 , C - l
风——轴瓦半径 R——轴颈半径 R——浮环内半径 R——浮环外半径 。 S i 内膜的 Sm e e 数 —— o m rl fd
表面织构对浮环轴承环速比影响的实验研究

MAULAN Abduvaki1 PEI Shiyuan1 XU Hua1,2 ZHANG Shenglun1 GUO Yanan1
(1������ Key Laboratory of Education Ministry for Modern Design and Rotor⁃Bearing System,Xi’ an Jiaotong University, Xi’an Shaanxi 710049,China;2������ School of Mechanical Engineering,Xinjiang University,Urumqi Xinjiang 830046,China)
动轴承[1] 。 滚动轴承在低转速下可以 有 效 地 减 少 摩 擦, 但在高速运转工况下, 相对于油膜轴承, 滚动轴 承不能得到良好的润滑, 导致摩擦力增加, 因而不能 很好地满足工作要求。 此外, 滚动轴承的制造成本高 以及寿命有限, 这在很大程度上也限制了其在高速下 的广泛应用。 在浮环轴承中, 全浮环轴承 ( FRB) 相 比半浮环轴承 ( SFRB) , 在高速下具有更低的温升和 摩擦功耗[2] 。 因此, 在高速运转条件下, 全浮环轴承 ( FRB) 以其摩擦功耗低、 可靠性高和成本低等优点 被广泛应用在汽车内燃机上。
上述研究对了解浮环轴承的工作机制和浮环轴承
的优化设计具有较大的参考价值。 但是在浮环轴承的 设计和使用过程中, 目前依然存在很多问题, 比如高 速下 浮 环 转 速 突 降 或 卡 死、 油 膜 涡 动[8] 、 振 动 过 大[9] , 甚至灾难性停机故障[10] 等。 最 近 的 一 项 研 究 报道指出, 润滑油里的微小杂质和磨损碎片会导致汽 车涡轮增压器浮环轴承的故障和持续的噪声[11] 。 此 外, 为追求更高的压缩比和提高输出功率, 涡轮增压 器必须在很高的速度下工作, 一般转速达到 1 × 105 ~ 4×105 r / min, 这时润滑油温升非常高。 SAN ANDRES 等[12] 发现在转速 2������ 4×105 r / min 下运行时, 半浮环轴 承内膜温度可超过 200 ℃ 。 当润滑油温度超过一定值 后, 润 滑 效 果 就 下 降, 甚 至 润 滑 油 会 燃 烧 ( SAE 5W30 润滑油的燃点约为 210 ℃ [1] ) , 从而导致涡轮 增压器的灾难性故障。 这说明浮环轴承的设计理论和 试验研究还远未至完善。
润滑供油压力对涡轮增压器转子稳定性影响

润滑供油压力对涡轮增压器转子稳定性影响
辛易达
(大连民族大学 机电学院,辽宁 大连 116600)
摘 要:利用 FLUENT 求解浮环轴承的润滑油膜的有限元仿真模型,分析供油压力对浮环轴 承 润 滑 特 性 的 影 响 ,进 而 分 析 了 浮 环 轴 承 对 涡 轮 增 压 器 转 子 稳 定 性 的 影 响 。 结 果 表 明 ,浮 环 轴 承 内 外 油 膜 均 有 明 显 的 发 散 区 和 收 敛 区 ,提 高 润 滑 压 力 能 够 有 效 改 善 内 外 油 膜 的 润 滑 性 能 ,转 子的固有频率取决于系统的参数和转子的转速。 关 键 词 :涡 轮 增 压 器 ;转 子 稳 定 性 ;润 滑 系 统 ;FLUENT 中 图 分 类 号 :TP212.14 文 献 标 志 码 :A 文 章 编 号 :16741374(2018)03026106
0 引 言
涡轮增压器 的 应 用 越 来 越 广 泛,但 其 高 故 障 率已成为人们关注的焦点。有数据显 示[13],润 滑 与冷却故障引起的转子失稳在涡轮失效故障中占 比约为 70%,这 也 引 起 了 相 关 学 者 的 重 视 和 研
究。文献[4]用 CFD 方法对浮环轴承三维油膜力 进行了仿真分析,但 并 没 有 考 虑 到 内 外 膜 油 孔 对 油膜压力分布的 影 响;文 献[5]使 用 CFD 方 法 研 究了油孔旋转时浮环轴承载荷的变化和浮环油孔 流 量 的 变 化 ;文 献 [6]基 于 短 轴 承 理 论 对 涡 轮 研 究 了 浮
Abstract:Thefiniteelement modeloflubricating oilfilm offloatingring bearingis built with FLUENTtoanalyzetheinfluenceoftheoilsupplypressureonthelubricationcharacteristicsofthe floatingringbearing,andaccordinglytheeffectofthefloatingringbearingonthestabilityofthe turbochargerrotor.Theresultsindicatethatthereareobviousdivergingandconvergentzonesatboth theinnerandouteroilfilmsofthefloatingringbearing.lubricationpressurecaneffectivelyimprove thelubricationperformanceofinternalandexternaloilfilm,andthenaturalfrequencyoftherotor dependsontheparametersofthesystemandtherotationalspeedoftherotor. Keywords:turbocharger;stabilityoftheturbochargerrotor;lubricationsystem;FLUENT.
涡轮泵用动静压型机械密封性能数值分析

涡轮泵用动静压型机械密封性能数值分析目录一、内容综述 (2)1.1 研究背景与意义 (3)1.2 国内外研究现状 (4)二、涡轮泵用动静压型机械密封基本理论 (5)2.1 涡轮泵工作原理 (6)2.2 动静压型机械密封结构特点 (7)2.3 机械密封材料选择 (8)三、动静压型机械密封性能影响因素分析 (9)3.1 密封面宽度对性能的影响 (10)3.2 转速对性能的影响 (11)3.3 工作介质对性能的影响 (12)3.4 温度对性能的影响 (13)四、动静压型机械密封性能数值分析方法 (14)4.1 数值模拟方法选择 (16)4.2 控制方程与边界条件设定 (17)4.3 有限元模型建立 (18)4.4 性能参数提取与分析 (19)五、数值模拟结果与分析 (21)5.1 不同密封面宽度下的性能变化 (23)5.2 不同转速下的性能变化 (24)5.3 不同工作介质下的性能变化 (25)5.4 不同温度下的性能变化 (26)六、优化设计建议 (28)6.1 密封面宽度优化 (29)6.2 转速优化 (30)6.3 工作介质选择 (31)6.4 温度控制策略 (32)七、结论与展望 (34)7.1 研究成果总结 (35)7.2 存在问题与不足 (36)7.3 未来发展方向 (37)一、内容综述随着科技的不断发展,涡轮泵作为工业生产中的重要设备,其性能参数的优化和提高已经成为研究的热点。
动静压型机械密封作为一种常用的涡轮泵密封形式,其性能对涡轮泵的整体性能具有重要影响。
本文通过对涡轮泵用动静压型机械密封性能数值分析的研究,旨在为涡轮泵的设计、制造和使用提供理论依据和技术支持。
本文首先介绍了涡轮泵的基本结构和工作原理,以及动静压型机械密封的分类和特点。
在此基础上,分析了动静压型机械密封在不同工况下的性能表现,包括静密封性能、动密封性能、泄漏量和使用寿命等方面。
针对现有研究中存在的问题和不足,提出了改进措施和方法,以提高动静压型机械密封的性能。
211114950_织构设计对润滑脂密封副密封特性影响的数值模拟

第52卷第4期表面技术2023年4月SURFACE TECHNOLOGY·155·织构设计对润滑脂密封副密封特性影响的数值模拟武怀彪1,潘家保1,2,汪奥1(1.安徽工程大学 机械工程学院,安徽 芜湖 241000;2.南京航空航天大学 直升机传动技术国家重点实验室,南京 210016)摘要:目的探究织构设计对润滑脂密封副密封性能的影响规律,得到织构化设计的最佳结构参数和工况条件。
方法基于润滑脂Herschel-Bulkley流变模型和非接触机械密封原理,选择直线型沟槽织构建立端面密封模型。
采用数值模拟方法分析不同倾斜角和转速下密封间隙的流场规律,进一步对密封副泄漏量的影响因素进行系统探究。
结果倾斜角不同,泄漏量随转速的变化规律不同。
倾斜角为30°时,泄漏量随转速的提升而增大;倾斜角为35°时,泄漏量较小,且随转速变化不大;倾斜角为40°,且转速大于2 000 r/min时,泄漏量几乎为0;倾斜角大于等于45°,且转速大于1 000 r/min时,流体反向泵送,无泄漏。
密封间隙和介质初始温度是影响泄漏的主要因素,泄漏量随密封间隙和介质温度的增大而增大。
一定范围内,增加沟槽数量和长度也可减少泄漏。
最佳织构参数和工况条件为倾斜角40°,槽数14,槽长8 mm,槽宽1.5 mm,密封间隙0.03 mm,槽深0.07 mm,温度小于320 K,转速大于2 000 r/min。
结论织构设计能有效抑制流体端面泄漏,润滑脂非牛顿特性对密封副间隙流场有显著影响,后续润滑脂密封副设计中应考虑流体的非牛顿特性。
关键词:润滑脂;密封副;织构化设计;泄漏控制;密封机理;非牛顿流体中图分类号:TH117.2 文献标识码:A 文章编号:1001-3660(2023)04-0155-09DOI:10.16490/ki.issn.1001-3660.2023.04.012Numerical Simulation of Effect of Texture Design on SealingCharacteristics of Grease Sealing PairWU Huai-biao1, PAN Jia-bao1,2, WANG Ao1(1. School of Mechanical Engineering, Anhui Polytechnic University, Anhui Wuhu 241000, China;2. National Key Laboratory of Science and Technology on Helicopter Transmission,Nanjing University of Aeronautics & Astronautics, Nanjing 210016, China)收稿日期:2022–04–06;修订日期:2022–08–12Received:2022-04-06;Revised:2022-08-12基金项目:国家自然科学基金(52005004);清华大学摩擦学国家重点实验室开放基金(SKLTKF21B02);南京航空航天大学直升机传动技术重点实验室开放课题(HTL-O-20G09)Fund:The National Natural Science Foundation of China (52005004); The Tribology Science Fund of State Key Laboratory of Tribology (SKLTKF21B02); Open Fund of the National Key Laboratory of Science and Technology on Helicopter Transmission (HTL-O-20G09)作者简介:武怀彪(1997—),男,硕士研究生,主要研究方向为机械密封。
- 1、下载文档前请自行甄别文档内容的完整性,平台不提供额外的编辑、内容补充、找答案等附加服务。
- 2、"仅部分预览"的文档,不可在线预览部分如存在完整性等问题,可反馈申请退款(可完整预览的文档不适用该条件!)。
- 3、如文档侵犯您的权益,请联系客服反馈,我们会尽快为您处理(人工客服工作时间:9:00-18:30)。
环轴承采取一些限定, 从而将模型进行简化。 浮环
轴承 的供 油形式有轴 向进油和径 向进油两种 , 现 选
择轴 向进 油方式 。 浮环轴 承按照浮环 是否可 以旋 转
分为全 浮动轴承和 半浮动轴承 两类 , 后者 由于限制 浮环 的旋转 运动 而避 免 高离 心力作 用 引起 油膜 中
轴
=
胰
U r R 。 I R 批。
( a )正 视 剖 面 图
B】 欧大
浮环稳 定旋转 时, 平 衡条件 为 内外载荷和力矩
分别大 小相等 ,方 向相反 ,可表述 为
=
W2 和 = Mo 。
( 1 2 )
一
8 l …
+]一
羽 一 广 ~
一1 …
1 . 2 几何模 型 为 了便于模拟织 构对润滑性 能的影 响, 现对 浮
。
W = f f p d x d y 。
( 5 )
润滑 膜 作用 在 固体 表面 的摩 擦 力可 以积 分整
ቤተ መጻሕፍቲ ባይዱ
个润滑膜范围内表面流体层中的剪应力求得,即
,
角所对应 得到 的h ,  ̄ F l h 。 为浮环相应 的 内外 间隙 。
—
.
b :O
_ ± 盯 d x d y ,
( P ADA) ; 江 苏 大 学第 l 1批 大 学 生科 研 立 项 资 助 项 目 ( 1 1 A 4 4 6 )
作者简 介:钱晏强 ( 1 9 8 8 一 ) ,男,江苏苏州人,硕士研究生 ,主要研究方 向为 内燃机摩擦学: 通信作者:尹必峰 ( 1 9 7 5 一 ) ,男,江 苏泰 兴人 ,博士 ,副教授 ,主要研 究方 向为内燃机摩擦学及 排放控制 ,E ma i l :y b f @u j s .e d u . c n 。
研究了外问隙对浮环轴承动特性的影响 。 叶子波
等 以流 体滑 动轴 承 的润滑 理 论为 基础 对浮 环轴 承
进行 了润滑 数值分析 ,得 出浮环 内外半径 比增大 ,
其摩擦损失的研究 目 前尚不多见。 自2 0 0 1 年E t s i o n
等 将 表 面 织 构 思想 应 用 到 发 动 机 缸套 一 活 塞 环 系 统 ,并研究证 实其确实具有 润滑减摩功 效 隅 起, 表
偏心 率减 小 ,承载 能力增大 ;间隙过大或过 小 ,难 以形成润 滑油膜 ,影响承载 能力 ;索 氏数越大 ,则 轴承 的承 载能力也越 大 的结论 。王成焘等 指出一
般浮环 轴承外 间隙为 内间隙的两倍 , 内间隙与轴颈
收稿 日期:2 0 1 3 — 0 8 — 3 1
面织构在机械领域的应用研究日益广泛, 有的通过
Al s a e e d为研 究提升高速 涡轮 增压器稳 定性 的 方法 ,分析 了浮环 轴承的静力 学和动力 学特 性 Ⅲ 。
T i a n等建立起 了较 为完整 的浮环轴承动 力学方程 ,
明了其 工作机理 , 并就整体结构对 承载能 力和 转速 对摩擦 力矩 的影 响进行 了分 析 。 然而利用 内外表面 的微 小结 构来 实现 提升 浮环 轴承 承载 能 力和 降低
文献标识码 :A
D Ol :1 O . 3 9 6 9 0 . i s s n . 1 0 0 7 - 7 9 1 X. 2 0 1 3 . 0 6 . 0 0 8
0 引言
为 了应对 能源 危机和环 境 问题 ,目前绝 大部分 的大 功率柴油机 、 半数 以上 的车用 柴油机 以及相 当 比例 的高性 能汽 油机均采用 了涡轮增压技 术 … 。轴 承 是制约增压器 使用寿命 的关键部件 , 在相 继使用 了滚 动轴承和滑 动轴承之 后 , 浮环轴承 以其 具有功 耗低 和稳定性好 的特点而在 增压器 中普遍 使用 , 它 使增 压器 的转速得 以成倍提 高 , 从而使其外 形尺寸 明显缩 小 ,重量减轻 ,使车用发 动机对于废 气涡轮 增压器 的基本要求 最终得 到满足 。
之 比约 为 0 . 0 0 2 - 0 . 0 0 3 ,外 间 隙 与 轴 颈 之 比 约 0 . 0 0 4 - 0 . 0 0 6 。赵 新军等 采 用 电涡流 传感 器进 行 了浮环 轴承转速 及运动轨迹 的测试研究 , 发现浮环 速度 与轴颈速度 、内外 间隙、半径 比及 内外 间隙 的 偏心度 相关 ,轴颈速度 一定时 , 浮 环速度 由偏心度
求解 雷诺方程研 究润滑性 能, 寻找最优织 构参数方 案 [ 9 - 1 0 1 也有 的利 用基于 N— S方程 的 C F D 方法 , 模 拟 并总 结织 构类 型及 几何 参数 对润 滑 性 能的影
基金项 目:国家重大科技成果转化专项资金项 目 ( 2 0 6 0 4 0 3 ) ;江 苏高校优势学科建设工程 资助项 目
( 6 )
,
由午坝祜性 定律 口 J 知
X
} O r
oj
叩 = ( 2 z 一 ) + ( 一 ) 鲁 , ( 7 )
浮环内表面z = = 和外表面z = = 0 ,其摩擦力为
=
翥
图 1 浮环 轴承 示意 图
F i g .1 S c h e ma t i c o f l f o a t i n g - r i n g b e a r
鲁 = 0 , 叩 : c 。 n s t , p = c o n s t , R e y n 。 l d s 方 程 可 简 化 为
)
油膜 厚度 可表 示为
- 6 + ,
( 3 )
h y ( R , 一 R j ) ( 1 + e c o s  ̄ 0 ) , h o = ( R 6 一 r ) ( 1 + 岛 c o s  ̄ 0 。 ) ,
改善增压器浮环轴承苛刻工况条件下的润滑性能
不乏探 索意义 。 本文基 于 C F D 方 法 ,模拟 浮环和轴颈 同轴 时 刻浮环 处于稳定状 态时 , 原始 未织构方案及 两种表 面 凹腔织构 方案 时润 滑油 的流 动状况 , 获取润 滑油 流 动速度 及油膜压 力分布等 信息 , 从而论述 织构在 改善浮环轴 承承载 能力 时所 发挥 的功效 , 进 而为浮 环轴承表 面织构化 设计提供 理论依据 。
凹腔 所 在 附近 区域及 凹腔 所在 以外 区域 的网格 尺
第 3 7卷 第 6 期 2 0 1 3年 1 1月
燕 山大 学 学报
J o ur na l o fYa n s ha n Uni v e r s i t y
VO1 .37 N O.6 NO V. 2 01 3
文章编号:1 0 0 7 - 7 9 1 X( 2 0 1 3 )0 6 - 0 5 2 2 - 0 6
=
[ 豫十 ( U b 引 , ( 8 )
『 - 豫 别 。 ( 9 )
若满足 8项基本 假设 ,由 N— S方程 和连续性
需要说 明的是 ,式 ( 8 ) 、( 9 ) 中的h 、P、 和 并未区分 ,但表示 内外不 同油膜 的对应参数 。
对 廊 的 内 外 膜 力矩 可 表 示 为
表 1 V T 5 0半浮动轴承尺寸
T a b .1 S i z e o f VT5 0 s e mi f l o a t i n g — r i n g b e a r mm
1 - 3 网格 划分 及边 界 条件 设 定 油膜模 型的最小特 征尺寸 凹腔深度 为 2 0 g m, 是最 大特 征尺寸 油膜轴 向长度 2 1 . 5 mm的 1 / 1 0 7 5 , 尺寸跨 度大 , 增 加 了网格划 分 的难度 。为 了更 好地 分析 润滑油流经 凹腔特征 时的流场 , 在H y p e r me s h 软件 中对织 构区域进 行 网格 加密处理 ,凹腔 区域 、
方程可以直接推导出 R e y n o l d s 方程 “ 。对于轴颈
与轴承 同时转动 的滑动轴承 , 润滑介质在 轴承 内外
间隙空间 中的流 动服从 R e y n o l d s方程 ,写成如下
形式
5 2 4
燕 山大 学 学 报
=
r 一 鲁 啬+ ( — u r ) k , ( 1 o
唯一确定 。De l i g a n t 等利用 C F D 方法 分析浮环
轴承特 性 , 揭示轴 承的冷却主要 是轴承及 外部 间隙 的热传 导 ,摩擦 力 矩与 转速 问存 在非 线 性 函数 关
系, 以及摩擦力矩随转速的变化 曲线随着润滑油温 度的降低而变缓的规律 。
上述 围绕 浮环 轴 承展 开 的研 究一 定程 度上 探
1 理论基础及模型处理
1 . 1 基 本 润滑 方程 浮环轴 承是 一种被 浮环 隔开 的双 膜润滑 轴承 , 由于浮环 以一定转 速旋转 , 相应 地减小 了其与轴颈
( 4 )
式 中,s = e / c 。 称 为相 对偏 心率 或偏 心率 ,其 中e 为 偏心距 离 ,c 。 为轴颈 、浮 环和 轴承 孔之 间两两 均 不存在偏 心时 的内外 间隙 。 将轴承及 内外油膜展 开成平 面, 原周 向定义为 瑚 方 向,轴 向定义 为y 车 由 方 向,膜 厚方 向定义为z 轴 方 向。承载量 为整个润 滑膜范 围 内的压 力积分 ,
第 6期
钱 晏强 等 涡轮增压器织构化浮环轴承润滑数值模拟
5 2 3
响规律 [ 1 1 - 1 2 ] o可见, 摩擦副表面织构化是未来低摩
擦技术 的重要手段 之一 , 尝试 引入表面 织构理念来
( ] 鲁) ( + ) 2 叩 0 h , ( 1 )
定 常工 况 下运 转 ,载 荷 转速 等 均 不 随 时 间变 化 ,
涡轮增压器织构化浮环轴承润滑数值模拟