ISO9001-2015可追溯性批次管理规范
批次标识及可追溯管理规定

1. 目的对可追溯性和批次管理方式进行适当策划,确保在需要时以可能最小的追溯范围对产品质量形成的过程进行追溯。
2. 适用范围适用于从原材料到半成品、完成品到包装入库等全过程的质量追溯和控制。
3. 职责3.1 物控部是批次管理的归口部门。
3.2 生产部与品质部要负责生产过程中可追溯管理。
4. 工作流程5. 控制要求5.1原材料,外购件来料标识。
物控部仓库接受检验合格后的原材料入库,按批次标识区分存放,登记《原材料入库记录表》,做到先进先出,按批次发放。
5.2 入库标识原材料入厂后,存放到待检区。
经品管部检验合格的,仓库管理员盘点核对原材料批次号,并记录到《原材料入库记录表》中,进行入库处理。
入库后的原材料挂上“商品卡”,在“商品卡”上写入库时间、数量、入厂批次号。
5.3 原材料领出原材料领出时,仓库管理员按先进先出的原则付料,《原材料领料单》上填写批次号,核对《原材料领料单》信息:物料名称、物料号、规格、任务单号、领料数量等。
生产过程按领料时的批号填写到《生产流程卡》。
5.4 生产过程中标识5.4.1物料员及作业者将所领到的原材料摆放到规定区域,流转中做好区分及标识,领料时材料批次号填写到《生产流程卡》,《生产流程卡》贯穿整个生产过程。
材料批次号、任务号、生产日期、作业者等信息填写在《生产流程卡》,保证产品批次信息可追溯。
542《生产流程卡》包装工序记录完成后,由生产部收集,根据需要统计汇总相应信息, 按《记录控制程序》保存记录。
5.5质量状态标识5.5.1产成品、半成品、原材料按质量状态分为合格品、不合格品。
5.5.2分条车间、镀锡车间完工的产品经作业者检查及品管部检验员检验确认合格,标识“合格品”标签转序;生产过程中发现原材料及产成品不合格,标识“不合格品标签” 存放于“不合格区”,按《不合格品控制程序》处理。
5.5.3包装按任务单贴小包装“产品标签”标识,“产品标签”由生产主管负责确认相应信息打印提供。
产品批次追溯管理制度
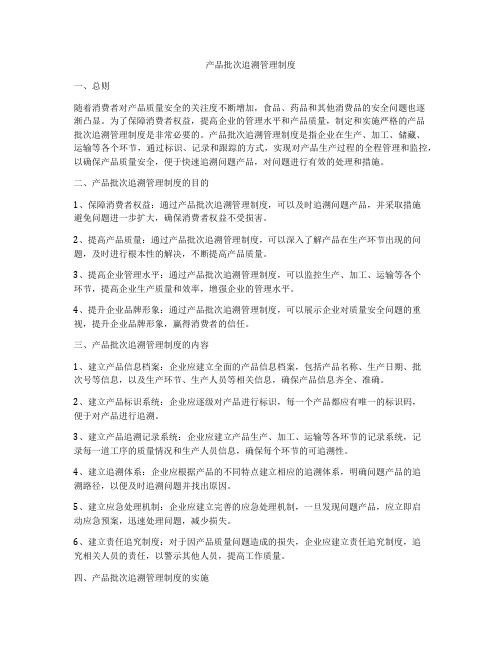
产品批次追溯管理制度一、总则随着消费者对产品质量安全的关注度不断增加,食品、药品和其他消费品的安全问题也逐渐凸显。
为了保障消费者权益,提高企业的管理水平和产品质量,制定和实施严格的产品批次追溯管理制度是非常必要的。
产品批次追溯管理制度是指企业在生产、加工、储藏、运输等各个环节,通过标识、记录和跟踪的方式,实现对产品生产过程的全程管理和监控,以确保产品质量安全,便于快速追溯问题产品,对问题进行有效的处理和措施。
二、产品批次追溯管理制度的目的1、保障消费者权益:通过产品批次追溯管理制度,可以及时追溯问题产品,并采取措施避免问题进一步扩大,确保消费者权益不受损害。
2、提高产品质量:通过产品批次追溯管理制度,可以深入了解产品在生产环节出现的问题,及时进行根本性的解决,不断提高产品质量。
3、提高企业管理水平:通过产品批次追溯管理制度,可以监控生产、加工、运输等各个环节,提高企业生产质量和效率,增强企业的管理水平。
4、提升企业品牌形象:通过产品批次追溯管理制度,可以展示企业对质量安全问题的重视,提升企业品牌形象,赢得消费者的信任。
三、产品批次追溯管理制度的内容1、建立产品信息档案:企业应建立全面的产品信息档案,包括产品名称、生产日期、批次号等信息,以及生产环节、生产人员等相关信息,确保产品信息齐全、准确。
2、建立产品标识系统:企业应逐级对产品进行标识,每一个产品都应有唯一的标识码,便于对产品进行追溯。
3、建立产品追溯记录系统:企业应建立产品生产、加工、运输等各环节的记录系统,记录每一道工序的质量情况和生产人员信息,确保每个环节的可追溯性。
4、建立追溯体系:企业应根据产品的不同特点建立相应的追溯体系,明确问题产品的追溯路径,以便及时追溯问题并找出原因。
5、建立应急处理机制:企业应建立完善的应急处理机制,一旦发现问题产品,应立即启动应急预案,迅速处理问题,减少损失。
6、建立责任追究制度:对于因产品质量问题造成的损失,企业应建立责任追究制度,追究相关人员的责任,以警示其他人员,提高工作质量。
ISO9001-2015产品标识和追溯程序(中英文)

产品标识和追溯程序Product Identification and Trace-ability(ISO9001:2015)1.0目的 Purpose:生产物料、产品施以明确的标记,以识别质量状态,产品种类,并反映某一箱或某一批产品的历史,以对质量问题及原因、责任等进行追溯,需要时追回不合格的产品。
Make clear identification to all incoming materials and product manufactured by DXC to identify their status of quality and specifications, to reflect the history of a certain carton or a certain batch of production so that trace the problem and its cause, responsibility and collect the rejected product if required.2.0范围Scope:所有生产的塑料产品于来料、生产过程、储存、检查和交付的各阶段,如果客户有特别的要求,则按客户的要求进行标识。
Apply to all injection molding plastics product, incoming material, product in process, storage, inspected and delivery stages. Make identification in accordance with customer if customer have special requirement.3.0定义Definitions:3.1DXC: 的简称。
DXC is the short form of DXC3.2MFG: Manufacturing的英文缩写;3.3QE:Quality Engineer品质工程师缩写4.0职责Responsibility4.1QE:将客户对产品和包装箱标识要求传达给生产部。
铸造产品标识及追溯性管理规范
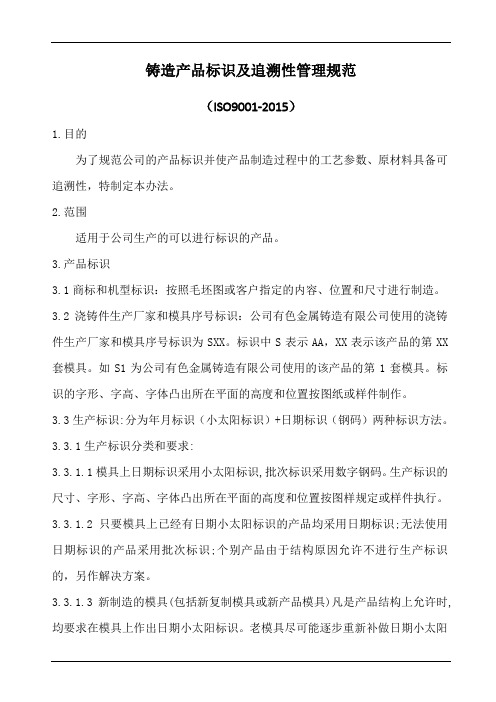
铸造产品标识及追溯性管理规范(ISO9001-2015)1.目的为了规范公司的产品标识并使产品制造过程中的工艺参数、原材料具备可追溯性,特制定本办法。
2.范围适用于公司生产的可以进行标识的产品。
3.产品标识3.1商标和机型标识:按照毛坯图或客户指定的内容、位置和尺寸进行制造。
3.2浇铸件生产厂家和模具序号标识:公司有色金属铸造有限公司使用的浇铸件生产厂家和模具序号标识为SXX。
标识中S表示AA,XX表示该产品的第XX 套模具。
如S1为公司有色金属铸造有限公司使用的该产品的第1套模具。
标识的字形、字高、字体凸出所在平面的高度和位置按图纸或样件制作。
3.3生产标识:分为年月标识(小太阳标识)+日期标识(钢码)两种标识方法。
3.3.1生产标识分类和要求:3.3.1.1模具上日期标识采用小太阳标识,批次标识采用数字钢码。
生产标识的尺寸、字形、字高、字体凸出所在平面的高度和位置按图样规定或样件执行。
3.3.1.2只要模具上已经有日期小太阳标识的产品均采用日期标识;无法使用日期标识的产品采用批次标识;个别产品由于结构原因允许不进行生产标识的,另作解决方案。
3.3.1.3新制造的模具(包括新复制模具或新产品模具)凡是产品结构上允许时,均要求在模具上作出日期小太阳标识。
老模具尽可能逐步重新补做日期小太阳标识。
3.3.1.4产品的日期标识或批次标识位置要求尽可能设置在装机时容易拆装辨认的位置(如产品的合盖面)。
3.3.2浇铸件生产标识的表示方法(见附表:压铸部产品生产标识制作规定) 3.3.2.1日期标识1)年月旬标识年月标识:在模具上直接做出年月标识称小太阳标识(见下图)。
中间小圆内数字表示年份,小圆外的12小格表示月份,从正上方顺时针方向的第一格开始,依次表示为1、2、3……12月份。
旬标识: 生产时在小格内打点,在某月小格内打一点表示该月上旬生产的产品,在某月小格内打两点表示该月中旬生产的产品,在某月小格内打三点表示该月下旬生产的产品。
(ISO9001-2015)标示和可追溯性管理程序

标示和可追溯性管理程序(ISO9001-2015)1﹑目的﹕对产品在生产各阶段和过程进行适当的标识,防止误用,对产品各阶段和过程质量形成追溯, 确保只有检验合格才能交付。
2﹑适用范围﹕适用于本公司所有进料﹑制程中产品以及成品状态标识3﹑权责﹕3.1研发部﹕负责建立材料﹑零组件与产品的料号规格。
3.2生产部﹕负责生产过程中所有产品皆有适当的标识。
3.3品管部﹕负责验证所有产品均有适当的标识。
3.4各相关责任单位负责相关作业的追溯。
4﹑名词定义﹕无5﹑作业内容﹕5.1进料的标识5.1.1进料产品的标示:供货商送货时外箱和内包装上贴物料标签,标示料号、数量、厂商名称、生产日期等。
5.1.2进料状态的标示1)进料检验经品管判定合格的材料由IQC在物料标签上,贴“PASS”标贴,并勾选对应的月份,放于良品区待仓库入库。
2)进料检验经品管判定为不合格的材料,由IQC在外箱贴红色“拒收”标签,并勾选对应的月份,放置于不合格品区待退。
3)进料检验经品管判定为不合格的材料特采时,由IQC在外箱贴“特采”标贴,并勾选对应的月份,放于良品区待仓库入库。
4)进料检验经品管判定因承认书、样品、环保报告缺失时,由IQC在外箱贴“待处理”标贴,放于待检区待验。
5)进料检验经品管判定为不合格的材料但可以经挑选入库的,由IQC在外箱贴“挑选”标贴,放于待检区。
6)IQC验好的材料按标贴放置于良品或不良品区域,准备检验的材料放置于“待验”区域。
5.2进料的追溯5.2.1当发生原材质量异常时,由品管执行追溯。
5.2.2追溯的途经与方法:《收料三联单》→《采购单》→《IQC进料统计报表》或《过账单》→《送货单》的追溯到生产厂商、生产日期、品名规格、料号、数量。
5.3制程标示与追溯5.3.1生产部门产品标识生产作业员于外箱或小包装上贴上白色“产品状态单”,标识日期、工单号码、料号、机种、数量、制程段,放置于待检区,交FQC检验.5.3.2生产部门产品状态标识A、作业员制程中的不合格产品贴上“不良品状态单”,填写“工单号、机型、不良代码(原因)、测试员(全检员)、维修员、站别、维修结果”。
ISO9001:2015产品标识可追溯性控制程序

1.目的:建立适当的产品标识系统,明确产品的检验状态,以确保需要时对产品质量的形成过程,可实行追溯。
2.范围:本程序适应于公司所有生产的产品从原物料到成品交付全过程的标识和可追溯。
3.职责:3.1 品控部负责进料、制程、成品检验和试验状态的标识。
3.2 生产部负责生产过程的产品标识及其品质状态的标识。
4.定义:无5.工作程序5.1 产品标识:5.1.1 生产部使用各类配套物料,品质工程部对所有的物料和产品进行编号(目前以客户料号/品名为准)。
5.1.2 供应商提供的物料由供应商在外包装箱上标识,标识必须包含物料名称规格、数量、日期、质量状态。
5.1.3 生产过程中转序之产品标识:用插架周转并贴“产品标识/交接卡”,以<生产加工流程单>、<产品标识/交接单>交接下工序。
5.1.4 生产过程中按以下方法进行标识:各工序加工中产品,用标签或区域标识其型号(名称)/类别等。
5.1.5 当客户对产品的标识有特别要求时,由销售部通知相关部门(附客户要求的背景材料)按客户要求进行标识。
5.1.6 当有新材料或新产品需做特别标识进行追溯时,由相关人员提出明确的标识方法和要求,由作业人员做特别标识。
5.2 检验和试验状态标识:5.2.1 进料检验状态的标识:5.2.1.1 仓库应划出“待检区”、“合格区”、“不良品区”,用区域对不同质量状况的来料进行标识、隔离。
5.2.1.2 来料经检验且判为合格时,在所检物料包装标识上贴上绿色“PASS”标签。
5.2.1.3来料经检验且判为不合格时,于所检物料包装识别上贴“NG”标签。
当不合格来料处理结果为特采时,检验员在来料包装上贴上“特采”标签;当不合格来料处理结果为让步、接受或挑选时,检验人员在来料包装上贴上“特采”,并写出处理方式;当不合格来料处理结果为退货时,检验人员于来料包装上贴红色“NG”标签,并注明原因及处理方式.5.2.2 生产过程检验状态的标识:5.2.2.1 生产部之生产线上的物料及存料,必须保留原检验状态之标识。
ISO9001-2015成批产品批次管理规范
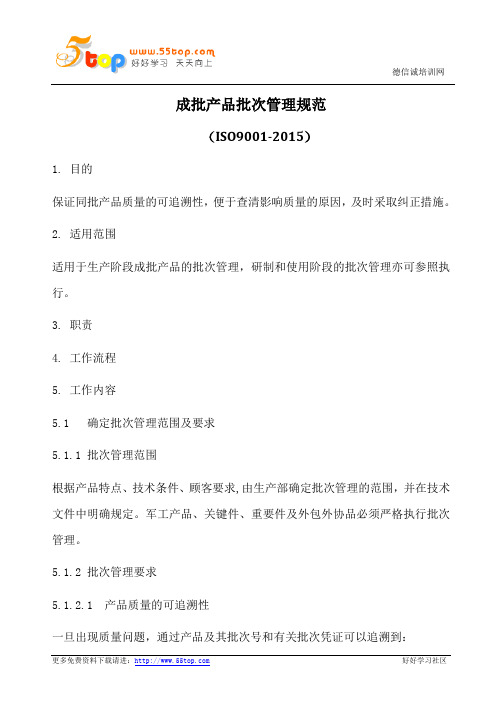
成批产品批次管理规范(ISO9001-2015)1. 目的保证同批产品质量的可追溯性,便于查清影响质量的原因,及时采取纠正措施。
2. 适用范围适用于生产阶段成批产品的批次管理,研制和使用阶段的批次管理亦可参照执行。
3. 职责4. 工作流程5. 工作内容5.1 确定批次管理范围及要求5.1.1 批次管理范围根据产品特点、技术条件、顾客要求,由生产部确定批次管理的范围,并在技术文件中明确规定。
军工产品、关键件、重要件及外包外协品必须严格执行批次管理。
5.1.2 批次管理要求5.1.2.1 产品质量的可追溯性一旦出现质量问题,通过产品及其批次号和有关批次凭证可以追溯到:a)原材料的来源;b)加工过程的历史:产品出厂(或生产)日期、组成该产品的批次号;c)产品交付后的分布和场所。
5.2 分批5.2.1 实行批次管理的成批产品,应做到“五清”、“五分批”。
五清:批次清、数量清、质量状态清、原始记录清、批号清。
五分批:分批投料、分批加工、分批转工、分批入库、分批出厂。
5.2.2 批次要时间顺序连续编号,不应重复。
组批批号的编制以月份为界,方法是年—月—序号-组批数量。
组批数量按100件或100件的倍数,不足100件的按实际数量组批。
顾客有特殊要求的批号编排及组批数量必须按顾客的要求执行。
5.2.3 批次标志必须清晰可辩,牢固持久。
5.2.4 生产部根据当月计划排列批次号。
5.3 分批流转加工5.3.1 批次凭证的建立在以下文件中必须具有批次验收的栏目,并相应记录批号、质量状态、责任者、检验者。
a) 质量记录;b) 材料代用和不合格品审理单;c) 产品出厂的质量证明;d) 产品制造过程中的《工艺流程记录》其它有关文件。
5.3.2 文件凭证的填写a) 字迹和印章要准确、清楚,符合归档要求;b) 内容填写不完整、不明确时,不得转入下道工序;c) 有关批次内容变更时,应严格履行更改手续,并归档备查。
5.3.3 批次凭证的传递《工艺流程记录》等需流动的批次凭证,应随该批产品传递。
ISO 9001:2015版全套体系文件 产品标识与追溯控制程序

(1.0版)
制订:
审批:
2020-1-1发布2020-1-1实施
有限公司
编 号
版本/版次
A / 0
文件类别
程 序 文 件
页 码
1 / 2 页
文件名称
产品标识及追溯程序
生效日期
1 目的
适时地识别产品和服务和来源,以保证在出现不合格或需要的情况下及时追溯.
4.1.2标识方法:铭牌、标签、附件、唛头、挂牌、分区放置、单证签名或其他认可的标记均可。
4.2商品的质量状态标识
4.2.1对每批进货商品,品管课进行抽样检验和验证,并作好检验状态标识。
4.2.2检验状态标识方法:检验记录、挂标识牌、划区存放等。
4.3服务识别
服务各阶段主要通过各种审查记录、合同单据等形式区分,各责任单位保存有关证据。
4.4产品、服务的可追溯性
若客户退货或投诉,可通过产品上的标识或客户提供的源头资讯结合产品\服务各阶段的记录,单据历史记载,可达成追溯的目的。
5术语解释
可追溯性:追溯所考虑对象的历史、应用情况或所处场所的能力。
6相关文件
《仓库管理规定》
7 相关记录 无
编 制
审 核
批 准
日 期
日 期
日 期
有限公司
编 号
2 范围
本程序适用经贸产品的标识追溯及服务过程与状态的识别追溯。
3职责
3.1业务课(或供应商)负责产品的标识。
3.2业务课、营业课负责服务的识别。
3.3品管课负责商品检验状态的标识。
4工作程序
4.1产品标识
4.1.1每批进货及发货商品,业务课都要检查产品的标识是否符合合同或法规要求;如供应商所作标识不全或损坏,要及时查明并补充。对标识的变更和移植要予以记录。
ISO9001-2015产品鉴别与追溯作业程序A0
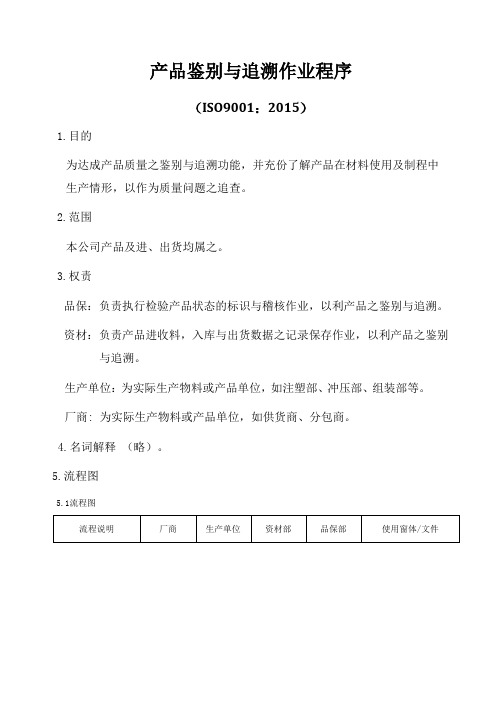
产品鉴别与追溯作业程序
(ISO9001:2015)
1.目的
为达成产品质量之鉴别与追溯功能,并充份了解产品在材料使用及制程中生产情形,以作为质量问题之追查。
2.范围
本公司产品及进、出货均属之。
3.权责
品保:负责执行检验产品状态的标识与稽核作业,以利产品之鉴别与追溯。
资材:负责产品进收料,入库与出货数据之记录保存作业,以利产品之鉴别与追溯。
生产单位:为实际生产物料或产品单位,如注塑部、冲压部、组装部等。
厂商: 为实际生产物料或产品单位,如供货商、分包商。
4.名词解释(略)。
5.流程图
5.1流程图
6.作业内容
6.1 产品之鉴别
ISO9001-2015内审员升级培训(100元) ISO9001-2015内审员培训(200元) :。
(IATF16949ISO9001-2015)产品批次管理规范(10P)
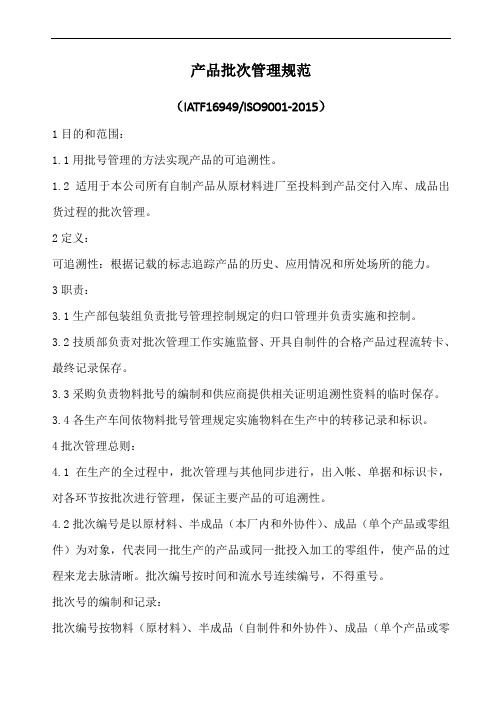
产品批次管理规范(IATF16949/ISO9001-2015)1目的和范围:1.1用批号管理的方法实现产品的可追溯性。
1.2适用于本公司所有自制产品从原材料进厂至投料到产品交付入库、成品出货过程的批次管理。
2定义:可追溯性:根据记载的标志追踪产品的历史、应用情况和所处场所的能力。
3职责:3.1生产部包装组负责批号管理控制规定的归口管理并负责实施和控制。
3.2技质部负责对批次管理工作实施监督、开具自制件的合格产品过程流转卡、最终记录保存。
3.3采购负责物料批号的编制和供应商提供相关证明追溯性资料的临时保存。
3.4各生产车间依物料批号管理规定实施物料在生产中的转移记录和标识。
4批次管理总则:4.1在生产的全过程中,批次管理与其他同步进行,出入帐、单据和标识卡,对各环节按批次进行管理,保证主要产品的可追溯性。
4.2批次编号是以原材料、半成品(本厂内和外协件)、成品(单个产品或零组件)为对象,代表同一批生产的产品或同一批投入加工的零组件,使产品的过程来龙去脉清晰。
批次编号按时间和流水号连续编号,不得重号。
批次号的编制和记录:批次编号按物料(原材料)、半成品(自制件和外协件)、成品(单个产品或零组件)的不同分别编号。
1.采购部:板材、压线框、螺丝、冷轧材等外购物料均用我司采购部下达采购订单时与供应商确认统一的物料批次号,并建立物料采购批次管理台账,同时要求供应商按照我司要求在物料的最小包装物(塑料颗粒同样)上注明批次号和“货品编码”,原材料则要求供应商在原材料卷/板上面注明批次号;我司编制物料批次号由四组组成:XX(大类)+X(供应商代码)+XXXX(收货年月)+ XXXX(流水号)针对客户(如HN)的指定原材料的批次号则把RM更改为HN:即:HN+ X(供应商代码)+XXXX(收货年月)+ XXXX(流水号);2半成品仓管:①收料入库时在“采购收货单”的“备注”栏写上批次号;②在仓库物料卡上标明“批次号”,不同批次物料不要混料;③生产领料/仓管发料在“领料单”/“生产发料单”上注明“批次号”,领/发料遵循先进先出原则;④退料时半成品仓管在“出库单存根”的“备注”栏填写“批次号”,手工建立批次管理台账。
批次的可追溯性管理制度

产品批次管理实施操作细则
为了实施ISO/TS16949:2002标准,搞好企业批次的可追溯性管理,特制定本制度。
一、企业在推行ISO/TS16949:2002标准时,把批次的追溯性管理,作为质量管理体系建设的
重要内容来抓,有计划、有步骤地予以实施。
二、制定《批次的可追溯性记录流转卡》(简称流转卡)。
从原材料进厂、温(冷)锻造、车削加工、
热处理、磨削加工、成品入库、发货用户,确定专人,分段记录,填写《流转卡》。
三、严格执行《流转卡》,要求各段标识固定、清楚、批次准确、记录完整、卡片清洁、流转及
时。
若下段发现上段不符合要求,下段记录人员有权要求上段有关人员重新填写。
四、质量部门是批次的可追溯性管理的职能部门,要随时到各段检查、指导、协调,发现问题
及时纠正。
要制定考核办法,要与经济效益及个人收入挂勾。
五、从原材料进厂至产品出库发货用户,各段要按批次,遵循“先进厂、先加工、先发货”的
原则,不得混批。
六、《流转卡》及有关资料,由质量部门统计员负责每月底到成品库核对台帐,并负责收集,分
类存档,要保存10年以上,以备追溯查询。
批次管理的质量追溯要求

批次管理的质量追溯要求1. 引言在现代生产和制造业中,批次管理和质量追溯是至关重要的。
批次管理是指对产品进行分类和组织,使其具备可追溯性和可管理性的能力。
质量追溯则是指能够追溯产品的质量信息、生产环境和生产过程,以便及时发现和解决质量问题,保证产品的质量和安全。
本文将探讨批次管理的质量追溯要求,包括要求的基本原则和标准、数据采集和记录、信息管理和追溯技术等内容。
2. 质量追溯要求的基本原则和标准每一批产品和原材料都应该有唯一的标识号或批号,以便进行追溯。
生产过程中的每一步都应该进行记录,包括原材料的来源、生产人员、生产设备等信息。
所有的质量检测和测试结果都应该进行记录,并与对应的批次相关联。
批次的产品应该可以追溯到原材料的来源和生产过程的每一步,以便发现和解决质量问题。
3. 数据采集和记录3.1. 数据采集方式手动记录生产人员可以手动将数据记录在纸质或电子表格上。
这种方式简单易行,但可能存在人为错误和数据丢失的风险。
自动采集利用传感器和数据采集设备自动采集数据,并传输到数据系统中进行记录。
这种方式能够减少人为错误,并且能够更快速和准确地采集数据。
3.2. 数据记录内容产品信息包括产品的批次号、生产日期、生产人员等信息。
原材料信息包括原材料的批次号、来源、供应商等信息。
生产过程信息包括生产环境、生产设备、操作人员等信息。
质量检测信息包括检测结果、检测时间、检测人员等信息。
4. 信息管理和追溯技术4.1. 数据库管理系统使用数据库管理系统可以对采集的数据进行存储、管理和查询。
通过建立数据模型和关联关系,可以实现对产品和原材料的追溯。
4.2. 条码和二维码对产品和原材料进行条码或二维码标识,可以方便地记录和追溯信息。
扫描条码或二维码可以获取相应的产品和原材料信息。
4.3. 物联网技术利用物联网技术,可以实现对生产设备和传感器的联网和监控。
通过实时采集和传输数据,可以实现对生产过程的实时监控和追溯。
5. 总结批次管理的质量追溯要求是现代生产和制造业中的重要环节。
ISO9001-2015标识和可追溯性控制程序A0
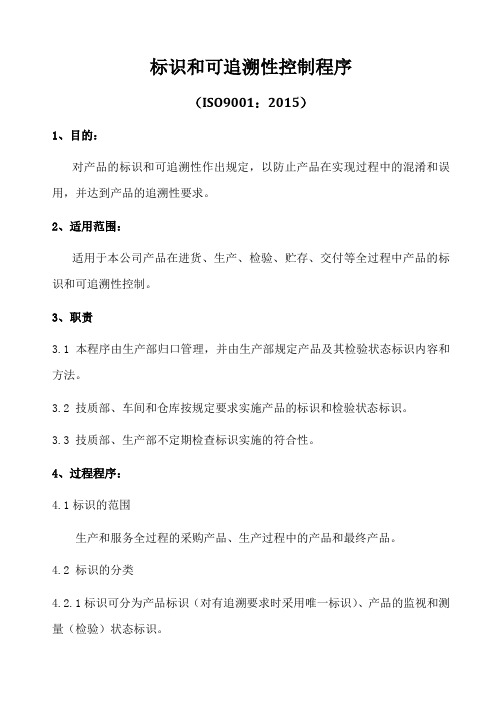
标识和可追溯性控制程序(ISO9001:2015)1、目的:对产品的标识和可追溯性作出规定,以防止产品在实现过程中的混淆和误用,并达到产品的追溯性要求。
2、适用范围:适用于本公司产品在进货、生产、检验、贮存、交付等全过程中产品的标识和可追溯性控制。
3、职责3.1本程序由生产部归口管理,并由生产部规定产品及其检验状态标识内容和方法。
3.2 技质部、车间和仓库按规定要求实施产品的标识和检验状态标识。
3.3 技质部、生产部不定期检查标识实施的符合性。
4、过程程序:4.1标识的范围生产和服务全过程的采购产品、生产过程中的产品和最终产品。
4.2 标识的分类4.2.1标识可分为产品标识(对有追溯要求时采用唯一标识)、产品的监视和测量(检验)状态标识。
4.2.2监视和测量状态标识分为“待检”、“合格”、“不合格”、“待判定”四种。
其中不合格品处置的分类按《不合格品控制程序》执行。
4.3产品标识4.3.1产品标识的方式a)原材料库、成品库的库存产品采用货卡、标识卡标识。
b)在周转过程中的产品采用生产任务计划书、标识卡或工艺文件、标签等作产品标识。
c)最终成品采用生产任务计划书、标识卡或产品检验合格单或检测报告标识。
4.3.2产品标识的内容a)原材料标识的内容包括:编号、名称、规格、材料牌号、产地、进公司日期等。
b)周转产品标识的内容包括:产品型号规格、名称和流转途径等,具体按标识卡设定内容实施。
c)成品标识的内容包括:产品名称、规格型号、及生产日期等。
4.4监视和测量状态标识4.4.1监视和测量状态标识的方式监视和测量状态标识可以用标牌及分区堆放等方式进行。
具体规定如下:a) 待检品:凡未经检验的产品均应放在“待检区”或挂“待检”标牌进行标识。
b) 合格品:经检验合格的产品应放在“合格区”或挂“合格”标签进行标识。
c)不合格品:经检验判为不合格的产品应放置在“不合格区”或挂“不合格”标牌。
按《不合格品控制程序》评审处置后,进行标识。
ISO9001-2015可追溯性批次管理规范

可追溯性批次管理规范(ISO9001:2015)1.批次管理目的:为了确保产品生产质量、配件以及原材料采购质量的可追溯性和确实实施先进先出,特制定本管理办法。
2.批次管理范围:本办法实用于公司产品用的原材料采购、外协、外购件、零部件、在制品、半成品的入库、制造、保管、包装、运输等各环节的可追溯性管理。
3.批次管理职责:3.1 品质部:负责所有批次的归口管理;负责监督车间生产的产品批次的填写;质检人员对自己填写批次的准确性负全责。
3.2 采购部门:负责推动供应商进行批次管理,送货时需在送货单,包装箱标签相应栏中填写批次,登记备查;3.3营业部:负责发出产品批次内外包装一致性的最终确认、发货和批次的准确记载;对退回产品批次的确认和协助品质部对质量的追溯;3.4各生产部门:各部门主管是推动批次管理的第一责任者。
冲压、注塑、组装、资材负责本部门产品的批次管理。
作业人员对自己填写批次的准确性负责。
3.5 资材人员:负责检查购入材料、入库和发出产品批次是否完整:无批次、批次不对应、批次不清楚、内外包装批次不符,库管员拒绝入库;对库存材料、产品批次的管理,做到:货架、托盘上的材料、产品分批次摆放,分批次挂牌,批次标识醒目,先进先出,不混放、错发。
无批次入库、无批次出库由责任库管员负全责。
3.6 财务部:负责ERP系统加入批次内容,并对各车间编制生产流转卡,材料入库单、领料单,成品入库单、出库单的收集、整理、核算、存档管理负责。
4.产品批次编制规则:4.1冲压部、注塑部、组装部装配产品批次编制规则:操作人员按“年2位 + 月2位 + 日2位 + 生产班次1位 + 生产线(机台编号)2位”共9位数进行编号:其中,班次中“1”代表早班,“2”代表晚班;如:A、年+ 月+ 日+ 生产班次+ 生产机台号13 07 14 1 01为2013年7月14日早班1号机台生产的产品。
B、当班没用完的材料退回库房,退料批次与领出时批次一致。
ISO9001:2015标识和可追溯性管理程序
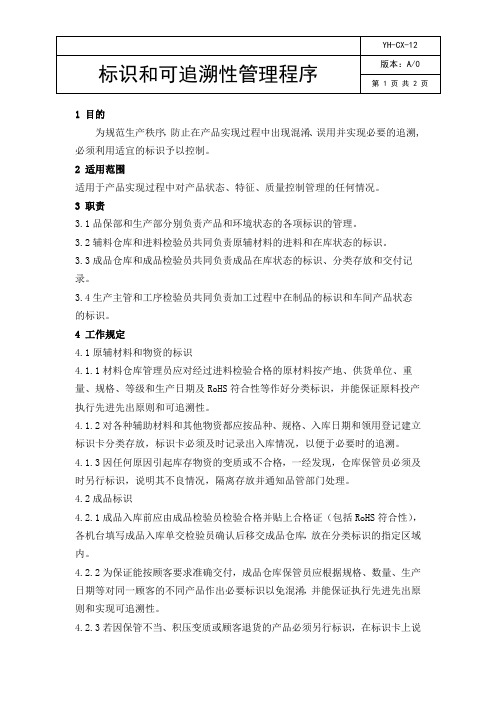
1 目的为规范生产秩序,防止在产品实现过程中出现混淆、误用并实现必要的追溯,必须利用适宜的标识予以控制。
2 适用范围适用于产品实现过程中对产品状态、特征、质量控制管理的任何情况。
3 职责3.1品保部和生产部分别负责产品和环境状态的各项标识的管理。
3.2辅料仓库和进料检验员共同负责原辅材料的进料和在库状态的标识。
3.3成品仓库和成品检验员共同负责成品在库状态的标识、分类存放和交付记录。
3.4生产主管和工序检验员共同负责加工过程中在制品的标识和车间产品状态的标识。
4 工作规定4.1原辅材料和物资的标识4.1.1材料仓库管理员应对经过进料检验合格的原材料按产地、供货单位、重量、规格、等级和生产日期及RoHS符合性等作好分类标识,并能保证原料投产执行先进先出原则和可追溯性。
4.1.2对各种辅助材料和其他物资都应按品种、规格、入库日期和领用登记建立标识卡分类存放,标识卡必须及时记录出入库情况,以便于必要时的追溯。
4.1.3因任何原因引起库存物资的变质或不合格,一经发现,仓库保管员必须及时另行标识,说明其不良情况,隔离存放并通知品管部门处理。
4.2成品标识4.2.1成品入库前应由成品检验员检验合格并贴上合格证(包括RoHS符合性),各机台填写成品入库单交检验员确认后移交成品仓库,放在分类标识的指定区域内。
4.2.2为保证能按顾客要求准确交付,成品仓库保管员应根据规格、数量、生产日期等对同一顾客的不同产品作出必要标识以免混淆,并能保证执行先进先出原则和实现可追溯性。
4.2.3若因保管不当、积压变质或顾客退货的产品必须另行标识,在标识卡上说明不良原因,隔离存放到待处理区,及时报告质量、业务和生产等部门评审处理。
4.3在制品标识4.3.1在生产现场各工序的在制品,根据生产流程卡及流转单上的编号、顾客、型号或规格等内容,以在制品加工流转卡的方式,由各工序领班负责实施标识管理。
4.3.2处在流动状态中的在制品标识是最容易造成脱落、丢失或遭到破坏的,为保证准确标识,不致因标识不清而造成失误或差错,工序检验员有责任进行严格、细致的监督和检查,并负责及时恢复相应标识。
标识和可追溯性控制程序—2015版三体系程序文件ISO9001

标识和可追溯性控制程序1、目的本程序规定了公司对原辅材料、半成品及成品电缆进行标识、追溯的方法、内容及要求。
2、适用范围适用于对采购产品、中间产品和最终产品的产品标识及产品的检验状态标识。
3、职责3.1采购部负责各种原辅材料的产品标识及标识的维护,原始资料的收集和传递。
3.2生产部负责入库成品电缆的分类标识、管理及标识的维护,原始资料的收集。
3.3生产部负责生产现场的原辅材料、半成品、成品状态的标识及标识的维护,及生产、自检原始记录的收集。
3.4质量部负责各类检验状态标识及检验状态标识规定的制订,及对原辅材料、半成品及成品电缆的检验状态的标识。
3.5质量部负责制定《产品标识规定》。
4、工作程序4.1产品的标识公司对产品标识采用:《产品制造卡》、《产品制造流程卡》、《产品合格证》、产品盘号、检验印章、标识牌等各种质量记录及其它各种适用的形式实现标识与可追溯性管理。
4.1.1原辅材料标识4.1.1.1每种原辅材料在库房内均应定置摆(堆)放,并有产品标识及检验状态标识。
4.1.1.2原辅材料进厂后,综合管理部负责组织人员把材料卸到指定待检区。
质量部根据检验标准对待检材料进行检验。
4.1.1.3采购部根据检验结果,将材料按指定位置入库摆放并做好标识。
4.1.1.4采购部按《产品防护控制程序》对库存原辅材料及标识进行维护。
因防护不当或存放较久(超过质保期),对原辅材料状态难以确认时,应及时通知质量部对其进行重新检验,如不合格转移至不合格品区隔离放置。
4.1.2半成品标识4.1.2.1生产设备部使用《产品制造卡》或《产品制造流程卡》对半成品进行标识,并在半成品交检前对产品自检状态用文字标识在“产品制造卡”或“产品制造流程卡”上。
4.1.2.2质量部用红色检验员章:a.“合格检XX”和b.“不合格检XX”章在半成品标识卡上对其进行检验状态标识。
4.1.2.3标识卡由各当班操作人员负责填写、悬挂,每盘半成品均应悬挂标识卡,悬挂应规范、牢靠。
ISO9001-2015物料标识和可追溯性管理程序
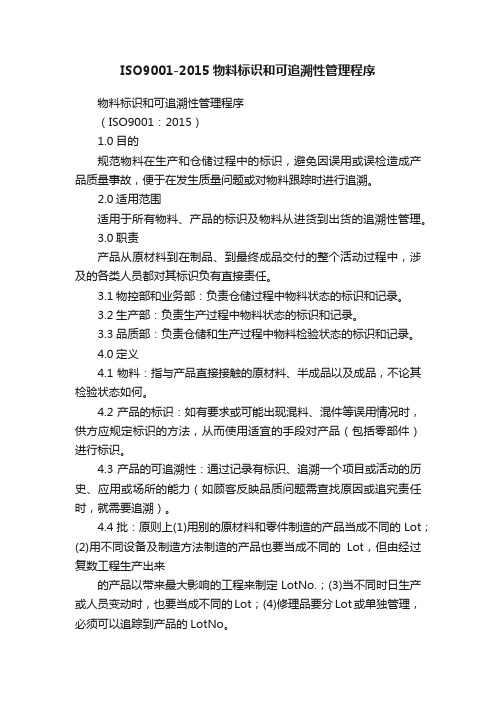
ISO9001-2015物料标识和可追溯性管理程序物料标识和可追溯性管理程序(ISO9001:2015)1.0目的规范物料在生产和仓储过程中的标识,避免因误用或误检造成产品质量事故,便于在发生质量问题或对物料跟踪时进行追溯。
2.0适用范围适用于所有物料、产品的标识及物料从进货到出货的追溯性管理。
3.0职责产品从原材料到在制品、到最终成品交付的整个活动过程中,涉及的各类人员都对其标识负有直接责任。
3.1物控部和业务部:负责仓储过程中物料状态的标识和记录。
3.2生产部:负责生产过程中物料状态的标识和记录。
3.3品质部:负责仓储和生产过程中物料检验状态的标识和记录。
4.0定义4.1物料:指与产品直接接触的原材料、半成品以及成品,不论其检验状态如何。
4.2产品的标识:如有要求或可能出现混料、混件等误用情况时,供方应规定标识的方法,从而使用适宜的手段对产品(包括零部件)进行标识。
4.3产品的可追溯性:通过记录有标识、追溯一个项目或活动的历史、应用或场所的能力(如顾客反映品质问题需查找原因或追究责任时,就需要追溯)。
4.4批:原则上(1)用别的原材料和零件制造的产品当成不同的Lot;(2)用不同设备及制造方法制造的产品也要当成不同的Lot,但由经过复数工程生产出来的产品以带来最大影响的工程来制定LotNo.;(3)当不同时日生产或人员变动时,也要当成不同的Lot;(4)修理品要分Lot或单独管理,必须可以追踪到产品的LotNo。
5.0工作程序5.1物料的标识5.1.1物料进厂后,由仓管员在包装箱外或物料表面贴“待检”标识,放在“待检区”。
5.1.2仓管员应对每批次物料赋予一个材料批号LotNo(唯一性编号)并记录,以保证该记录能够识别供应商、原材料名称、规格、纳入日期。
5.1.3QC检验时,应将物料的LotNo记录在《进料检验报告单》上。
经检验合格的物料,在材料仓中应使用“材料卡”进行标识。
5.1.4对于存放时间过长的材料,应在“材料卡”上标识“半年、一年、二年”,以便责任者及时对材料进行防损处理。
产品可追溯性管理规定

产品可追溯性管理规定
产品可追溯性文件
本文件旨在建立一条产品追溯通道,以便在已交货至客户之产品发生品质异常时,能够迅速追溯异常品之制造日期、数量及对应的原材料,并采取有效的应对措施。
适用范围包括本公司内购入的原材料、外协外购件进料和生产的产品。
产品批号应按照以下填写规范进行管理:
1.钢印号+生产班次+材料批号
2.生产日期+生产班次+材料批号
3.来料日期
4.材料批号
5.18/04()A。
1810.001-999
职责权限方面,质量中心负责产品追溯号的确定和监督过程中的批号正确性验证,制造部负责按照制定的批号实施生产
并对相关记录标签的正确性负责,质量中心负责按照供应商制定的批号填写相关记录并对过程中的批号正确性进行监督。
批号的定义是在生产中,每一批投料生产出来的产品,在质量和性能上还是有差异的。
为了便于事后追踪产品当时状态,避免混杂不清,故对每一批产品或者材料制定批号编制和追溯原则。
按照填写规范,批号应包含材质、材料、厂家、炉号、产品名称、客户厂家、日期和数量。
工作流程包括批号登录原则,对应的记录和填写方式/内
容来源如下:
1.原材料入库单:材料批号(来源:质保书、材料标示卡)
2.外协件产品出库单:批号(来源:产品入库单、产品标
示卡)
3.过程生产件:批号(来源:产品入库单、产品标示卡)
以上是本公司对产品追溯的管理规范,以确保产品质量和客户满意度。
- 1、下载文档前请自行甄别文档内容的完整性,平台不提供额外的编辑、内容补充、找答案等附加服务。
- 2、"仅部分预览"的文档,不可在线预览部分如存在完整性等问题,可反馈申请退款(可完整预览的文档不适用该条件!)。
- 3、如文档侵犯您的权益,请联系客服反馈,我们会尽快为您处理(人工客服工作时间:9:00-18:30)。
可追溯性批次管理规范
(ISO9001:2015)
1.批次管理目的:
为了确保产品生产质量、配件以及原材料采购质量的可追溯性和确实实施先进先出,特制定本管理办法。
2.批次管理范围:
本办法实用于公司产品用的原材料采购、外协、外购件、零部件、在制品、半成品的入库、制造、保管、包装、运输等各环节的可追溯性管理。
3.批次管理职责:
3.1 品质部:负责所有批次的归口管理;负责监督车间生产的产品批次的填写;质检人员对自己填写批次的准确性负全责。
3.2 采购部门:负责推动供应商进行批次管理,送货时需在送货单,包装箱标签相应栏中填写批次,登记备查;
3.3营业部:负责发出产品批次内外包装一致性的最终确认、发货和批次的准确记载;对退回产品批次的确认和协助品质部对质量的追溯;
3.4各生产部门:各部门主管是推动批次管理的第一责任者。
冲压、注塑、组装、资材负责本部门产品的批次管理。
作业人员对自己填写批次的准确性负责。
3.5 资材人员:负责检查购入材料、入库和发出产品批次是否完整:无批次、批次不对应、批次不清楚、内外包装批次不符,库管员拒绝入库;对库存材料、产品批次的管理,做到:货架、托盘上的材料、产品分批次摆放,分批次挂牌,批次标识醒目,先进先出,不混放、错发。
无批次入库、无批次出库由责任库管员负全责。
德信诚培训网
ISO9001-2015内审员升级培训(100元) ISO9001-2015内审员培训(200元) : 3.6 财务部:负责ERP 系统加入批次内容,并对各车间编制生产流转卡,材料入库单、领料单,成品入库单、出库单的收集、整理、核算、存档管理负责。
4.产品批次编制规则:
4.1冲压部、注塑部、组装部装配产品批次编制规则:操作人员按“年2位 + 月 2位 + 日2位 + 生产班次1位 + 生产线(机台编号)2位” 共9位数进行编号:其中,班次中“1”代表早班,“2”代表晚班;
如:A 、 年 + 月 + 日 + 生产班次 + 生产机台号
13 07 14 1 01
为2013年7月14日早班1号机台生产的产品。
B 、当班没用完的材料退回库房,退料批次与领出时批次一致。
C 、注塑部当班没用完的材料经过加工或烘热,材料质量、性能已经改
变,退料时在原批次后面加上“R ” 后缀符号作为新批次加以区别。
D 、注塑部车间粉碎的回料:入库时,由车间根据批次编写规范“A ”
为原则,重新编一个批次,并在新批次后面加上:“K ” 后缀符号作
为新批次加以区别。
4.2料房粉碎批次编制规则:人员按“年2位 + 月 2位 + 日2位 + 生产班次
1位 + 机台号2位” 共9位数进行编号:其中,班次中“1”代表
早班,“2”代表晚班;
如:A 、 年 + 月 + 日 + 生产班次 + 机台号
13 07 15 1 01
为2013年7月15日早班1#机台粉碎的粉碎料。