成型问题概论
紫砂壶机车成型方式探讨

紫砂壶机车成型方式探讨概论:机车成型的紫砂壶由来已久,一直未成为紫砂市场的热点,原因是机车壶制作需要单一产品有较大的生产基数,而一个单一产品如果单次的出货数量过分巨大,经销商会出现销售迟滞,对销售效率的提高不利。
这种因为需求不足造成的机车成型方式的落寞维持了相当长的时间,只是最近的几年,因为移动互联网的兴起,尤其自2014-2015年开始的“微商”,到如今垂直电商与抖音直播等销售方式并存的今天,紫砂,尤其是基础紫砂壶款的销售发生了井喷式的增长,原先的传统全手工或者借助石膏等各种形式的模具成型的半手工模式无法满足销售量的增长,因而机车成型再次兴起,并且迅速成为有争议的成型模式。
一、什么是紫砂机车壶不知从何时起,除了问全手工和半手工这样的老问题,有一句话成了许多紫砂壶友嘴里经常会提的一个问题:“你这个壶是机制的吗”?问这个问题的壶友基本属于非常不了解紫砂壶。
因为“你这个壶是机制的吗”这句话有一个隐含的情境——这个世上存在一种机器,只需在这个机器的一头塞进去一块泥料,或者灌入一坛紫砂泥浆,然后由一个工人在这台“神奇”的机器的“系统”上选择任意一个你需要的壶型,按动按钮,机器启动发出隆隆的声音,随着多余的紫砂(泥浆)废料从一个排污口排出,这个机器的另外一端立马就出现了一把已经基本完工的紫砂壶,整个过程只用时几分钟,随后第二把、第三把、第四把。
反正你只管往“加料口”放入足够的紫砂泥料,另外一端的“出壶口”工人只要把紫砂壶码好入窑,就会有源源不断的成品紫砂壶被制造出来。
必须明确的是以上的这种“神奇”机器以前没存在过。
随着科技的发展将来会不会出现也不好说,不过按照现有紫砂壶通常的制作方式和流程来说,短期内出现这种高科技机器的可能几乎为零。
就算是经常提到的灌浆壶也得有后续大量的“整理”工作,才能让这个灌浆成型的壶以一个还能说得过去的样子呈现在大家面前。
而这些“整理”工作至今也不可能彻底摆脱人工的介入。
到现在为止的这些已经存在的非人工成型的方式,无非还是在成型速度上的“弯道超车”,实实没有到“平地起飞”地彻底突破人工瓶颈的程度。
055091410成型设备概论真题及解答
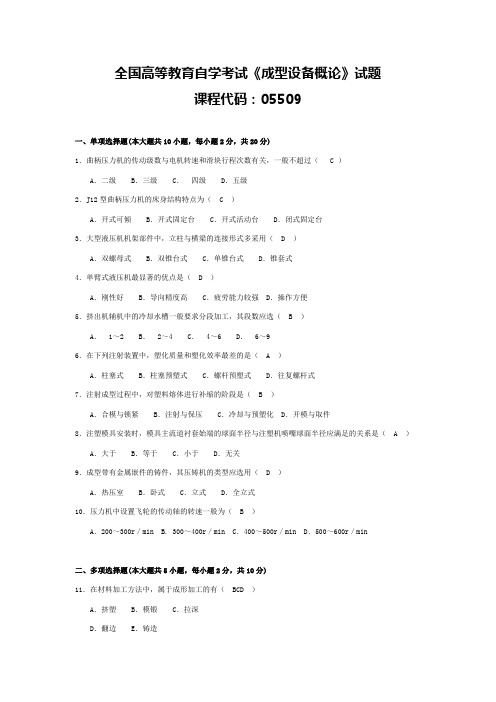
全国高等教育自学考试《成型设备概论》试题课程代码:05509一、单项选择题(本大题共10小题,每小题2分,共20分)1.曲柄压力机的传动级数与电机转速和滑块行程次数有关,一般不超过( C )A.二级 B.三级 C.四级 D.五级2.J12型曲柄压力机的床身结构特点为( C )A.开式可倾 B.开式固定台 C.开式活动台 D.闭式固定台3.大型液压机机架部件中,立柱与横梁的连接形式多采用( D )A.双螺母式 B.双锥台式 C.单锥台式 D.锥套式4.单臂式液压机最显著的优点是( D )A.刚性好 B.导向精度高 C.疲劳能力较强 D.操作方便5.挤出机辅机中的冷却水槽一般要求分段加工,其段数应选( B )A. 1~2 B. 2~4 C. 4~6 D. 6~96.在下列注射装置中,塑化质量和塑化效率最差的是( A )A.柱塞式 B.柱塞预塑式 C.螺杆预塑式 D.往复螺杆式7.注射成型过程中,对塑料熔体进行补缩的阶段是( B )A.合模与锁紧 B.注射与保压 C.冷却与预塑化 D.开模与取件8.注塑模具安装时,模具主流道衬套始端的球面半径与注塑机喷嘴球面半径应满足的关系是( A ) A.大于 B.等于 C.小于 D.无关9.成型带有金属嵌件的铸件,其压铸机的类型应选用( D )A.热压室 B.卧式 C.立式 D.全立式10.压力机中设置飞轮的传动轴的转速一般为( B )A.200~300r/min B. 300~400r/min C.400~500r/min D.500~600r/min二、多项选择题(本大题共5小题,每小题2分,共10分)11.在材料加工方法中,属于成形加工的有( BCD )A.挤塑 B.模锻 C.拉深D.翻边 E.铸造12.在曲柄压力机中,属于能源部分的零件有( AC )A.电动机 B.气垫 C.飞轮D。
滑块 E.工作台13。
曲柄压力机的操纵机构中,转键式离合器的特点有( BCE )A.安全性高 B.结构简单 C.刚性结合D.调模方便 E.维护成本低14.注塑成型机的液压式合模装置的结构形式主要有( ABCD )A.单缸直压式 B.充液式 C.增压式D.稳压式 E.肘杆式15.塑料的三种物理状态分别为( BCD )A.液态 B.玻璃态 C.高弹态D.粘流态 E.固态三、填空题(本大题共lO小题,每空1分,共20分)16.成形生产包括:模具工业和成形设备工业两大主体。
材料成型原理课后答案

材料成型原理课后答案材料成型原理是指通过不同的成型工艺,将原料加工成所需形状和尺寸的零部件或制品的原理。
在工程制造领域中,材料成型是非常重要的一环,它直接影响着制品的质量和性能。
下面就材料成型原理的相关问题进行解答。
1. 什么是材料成型原理?材料成型原理是指将原料加工成所需形状和尺寸的零部件或制品的原理。
它是通过对原料进行加工,使其发生形状、尺寸和性能的改变,从而得到符合要求的制品。
材料成型原理是工程制造中的重要环节,它直接关系到制品的质量和性能。
2. 材料成型的基本过程是什么?材料成型的基本过程包括原料的预处理、成型工艺和制品的后处理。
首先,原料需要进行预处理,包括清洁、除杂、干燥等工序,以保证原料的质量和加工的顺利进行。
然后,根据制品的要求,选择合适的成型工艺,如锻造、压铸、注塑等,对原料进行加工成型。
最后,对成型后的制品进行后处理,包括去除余渣、表面处理、热处理等工序,以提高制品的质量和性能。
3. 材料成型原理的影响因素有哪些?材料成型原理的影响因素包括原料的性能、成型工艺、成型设备和操作技术等。
首先,原料的性能直接影响着成型的难易程度和制品的质量。
其次,成型工艺的选择和设计对成型效果起着决定性的作用。
成型设备的性能和精度也会影响成型的质量和效率。
操作技术则是保证成型过程顺利进行的重要因素。
4. 材料成型原理的发展趋势是什么?随着科学技术的不断发展,材料成型原理也在不断创新和完善。
未来,材料成型将更加注重节能环保、智能化和数字化。
新材料、新工艺、新设备的不断涌现,将推动材料成型原理朝着高效、精密、绿色的方向发展。
同时,数字化技术的应用将使成型过程更加智能化和可控化,提高生产效率和产品质量。
5. 如何提高材料成型的质量和效率?要提高材料成型的质量和效率,首先需要加强对原料的质量控制,保证原料的质量稳定。
其次,要优化成型工艺和设备,提高成型的精度和效率。
同时,加强操作技术的培训和管理,确保成型过程的稳定和可控。
材料成型概论第六讲板带材生产工艺

材料成型概论第六讲板带材⽣产⼯艺材料成型概论第⼀讲第⼆讲第三讲第四讲第五讲第六讲第七讲第⼋讲第九讲第⼗讲材料成型概述炼钢炼铁⽣产材料塑性成型的基础钢坯型钢⽣产线棒材⽣产板带钢⽣产钢管⽣产挤压拉拔⽣产锻压冲压⽣产材料成型的发展及应⽤第六讲板带材⽣产6.1 6.2 6.3 6.4 6.5 板带材⽣产的⼀般概念板带材的品种及分类热轧中厚板⽣产热轧板带钢⽣产冷轧板带钢⽣产6.1 板带材⽣产的⼀般概念板带材(Finished sheet/plate and strip)是指形状为平板状断⾯基本为矩形宽度远⼤于厚度的⾦属材,B/H可达5000以上,少数达到10000。
⼀般将单张供应的板材和成卷供应的带材总称为板带材。
板材的主要尺⼨是厚度H、宽度B与长度L;带钢或板卷⼀般只标出厚度H与宽度B,再附以卷重G。
6.1 板带材⽣产的⼀般概念6.1 板带材⽣产的⼀般概念在⽣产上,板带钢宽⾼⽐⼤,散热⾯积⼤,温降快且波动明显;对不均匀变形⾮常敏感;变形量⼤,特别是薄规格⽣产,轧制压⼒⼤。
所以⽣产时要特别注意板型,减少轧制压⼒。
尺⼨要求精确:特别是厚度最主要板型要求良好:平坦、⽆浪形和瓢曲。
表⾯要求光洁:不得有⽓泡、结疤、拉裂、刮伤、折叠、裂缝、夹杂和压⼊氧化铁⽪。
性能要求较⾼:⼒学性能、⼯艺性能和某些钢板的特殊物理和化学性能。
6.1 板带材⽣产的⼀般概念为达到上述要求,采⽤了⼤量现代轧制技术,板带钢⽣产技术可以反映轧钢⽣产的技术⽔平。
对⼯业发达国家,⼀般板带钢产量占钢材总产量的50-60%以上。
6.1 板带材⽣产的⼀般概念板带材轧制指采⽤纵轧⽅式在由上下平轧辊构成的辊缝中将扁锭或板坯轧制成板带材的成型⽅法。
轧制板带材的轧机⼤多是四辊轧机,轧制箔材(极薄带)⽤六辊或多辊轧机。
粗轧机也采⽤⼆辊可逆式或万能式轧机。
板带材的轧制⽅法有单⽚轧制、成卷轧制、单机架可逆轧制、连续式轧制、多辊轧制等⼏种。
板带材的轧制⽅法(a)单机架四辊可逆轧制;(b)五机架四辊连续轧制;(c)单机架多辊可逆轧制6.1 板带材⽣产的⼀般概念板带材⽣产的特点:厚度H.长度B.宽度L外形特点:①形状扁平,断⾯简单,宽厚⽐⼤;②单位体积的表⾯积⼤。
成型设备概论试题及答案与评分标准D

成型设备概论复习资料一、单项选择题1.曲柄压力机刚性离合器常见的是__B____。
A.滑销式B.转键式C.滚柱式D.牙嵌式2.压力机中飞轮的转速一般为_____B____。
A.200~300r/min B.300~400r/min C.400~500r/min D.500~600r/min 3.曲柄压力机对闭合高度计算时应注意上下极限位置处留余量为____ C ___。
A.1mm B.2mm C.5mm D.10mm4.液压机传统的结构形式是____ A ___。
A.梁柱组合式B.单臂式C.双柱下拉式D.框架式5.下列液压元件中,属于执行元件的是____B _____。
A.液压泵B.液压缸C.换向阀D.溢流阀6.挤出机冷却水槽一般分___ B ____段。
A.2~3 B.2~4 C.3~4 D.3~57.适用于厚壁制件生产的喷嘴是____ B _____。
A.通用式B.延伸式C.远射程式D.自锁式8.排气式注射机与普通注射机的主要区别在____ B _____。
A.合模装置B.塑化装置C.液压装置D.电气装置9.曲柄压力机滑块的行程是曲柄半径的___ B _____。
A.一倍B.两倍C.三倍D.四倍10.国产注射成型机SZ-40/32,其中数字32代表____A _____。
A.锁模力为320K N B.锁模力为320K gC.锁模力为32K N D.锁模力为32K g二、多项选择题11.在曲柄压力机中,属于传动部分的零件有___ AB ____。
A.带传动B.齿轮传动C.飞轮D.电气传动E.液压传动12.曲柄压力机转键式离合器的特点有____ ACE _____。
A.安全性高B.结构简单C.运行条件简单D.调整方便E.维护成本低13.冲压自动线的优点有___ACDE ______。
A.提高了生产率B.减少了生产工序C.改善了劳动条件D.缩短了生产周期E.降低了生产成本14.液压-曲肘式合模装置的特点有___ ABC ______。
材料成型概论第四章挤压成型ppt课件

(a)正挤压;(b)反挤压;(c)侧向挤压;(d)玻璃润滑挤压; (e)静液挤压;(f)连续挤压
经营者提供商品或者服务有欺诈行为 的,应 当按照 消费者 的要求 增加赔 偿其受 到的损 失,增 加赔偿 的金额 为消费 者购买 商品的 价款或 接受服 务的费 用
4.1.2 挤压成型的基本方法
4.2.2 挤压变形区及应力应变状态
2.变形区内的应力应变状态 ❖ 应力状态:三向压应力,即轴向压应力σl,径向压应
力σr及周向压应力σθ(轴对称σr=σθ) ❖ 应变状态:两向压缩、一向延伸,即轴向延伸变形
εl,径向压缩变形εr及周向压缩变形εθ (轴对称εr=εθ)
经营者提供商品或者服务有欺诈行为 的,应 当按照 消费者 的要求 增加赔 偿其受 到的损 失,增 加赔偿 的金额 为消费 者购买 商品的 价款或 接受服 务的费 用
缺点 7.金属损失大,成材率低,且工具消耗大,生产成本高; 8.金属与工模具间摩擦系数大,金属在变形区内流动
不均匀,产品组织性能沿长度和断面上不均匀; 9.与轧制成型相比生产率低。
经营者提供商品或者服务有欺诈行为 的,应 当按照 消费者 的要求 增加赔 偿其受 到的损 失,增 加赔偿 的金额 为消费 者购买 商品的 价款或 接受服 务的费 用
4.2.1 挤压成型过程
❖ 基本挤压阶段 开始挤压阶段完成后,锭坯在挤压轴的压力作用下, 由模孔流出形成制品,直至筒内锭坯长度接近变形 区压缩锥高度,这一阶段为基本挤压阶段,又称平 流挤压阶段。 挤压过程中,锭坯任一横截面上的金属质点皆以相 同速度或一定的速度差流入变形区压缩锥。
经营者提供商品或者服务有欺诈行为 的,应 当按照 消费者 的要求 增加赔 偿其受 到的损 失,增 加赔偿 的金额 为消费 者购买 商品的 价款或 接受服 务的费 用
玻璃成型及其模具-4概论

液态成型的优点
液态成型 缺点
工艺过程比较复杂,一些工艺 过程还难以控制
液态成形零件内部组织的均匀性、 致密性一般较差
液态成形零件易出现缩孔、缩松、 气孔、砂眼、夹渣、夹砂、裂纹等 缺陷,产品 质量不够稳定
由于铸件内部晶粒粗大,组织不均 匀,且常伴 有缺陷,其力学性能 比同类材料的塑性成形低
(7) 皱纹 皱纹有各种形状,有的是折痕,有的是成片的很细的皱纹。皱纹
产生的原因主要是由于料滴过冷,料滴过长,料滴未落在初形模中间 而粘连在模腔壁上而产生的。
(8) 表面缺点 瓶罐的表面发毛、不平,主要是由于模腔表不光滑而造成的。模
型的润滑油不清洁或涂油的刷子过脏,也会使瓶罐表面质量下降。
(9) 气泡 在成形过程中产生的气泡往往是几个大气泡或集中在一起的若干
模具涂层:现在常在玻璃模具的棱角和冲头与玻璃接触的部分采用热喷涂层,喷焊一 层镍铬合金粉末,以提高接触表面的高温耐磨性、耐高温、抗氧化。用灰铸铁制作的 玻璃模具,热喷涂镍基自熔合金,可使模具寿命提高5倍以上,主要问题是需要重新加 工以及模具成本较高。
铸造工艺及缺陷控制
金属的成形方法可分为铸造、塑性成形(或称压力加 工)、切削加工、焊接和粉末冶金五大类。
液态合金的工艺性能
液态成型过程的工艺性能表征为液态合金的 铸造性能
通常是指合金的流动性、收缩性 吸气性及偏析等性能
合金铸造性能是选择铸造金属材料,确定铸件的 铸造工艺方案及进行铸件结构设计的依据
二、 铸造工艺基础
定义:铸造是指将熔融态的金属(或合金)浇注于
特定型腔的铸型中凝固成形的金属材料成形方法。
适于做复杂外形特别是复杂内腔的毛坯对材料的适应性广铸件的大小几乎不受限制成本低原材料来源广泛价格低廉一般不需要昂贵的设备是某些塑性很差的材料如铸铁等制造其毛坯或零件的唯一成型工艺液态成型工艺过程比较复杂一些工艺过程还难以控制液态成形零件内部组织的均匀性致密性一般较差液态成形零件易出现缩孔缩松气孔砂眼夹渣夹砂裂纹等缺陷产品质量不够稳定由于铸件内部晶粒粗大组织不均有缺陷其力学性能比同类材料的塑性成形低液态成型液态成型过程的工艺性能表征为液态合金的铸造性能通常是指合金的流动性收缩性吸气性及偏析等性能合金铸造性能是选择铸造金属材料确定铸件的铸造工艺方案及进行铸件结构设计的依据定义
塑料成型的方法概论PPT学习教案
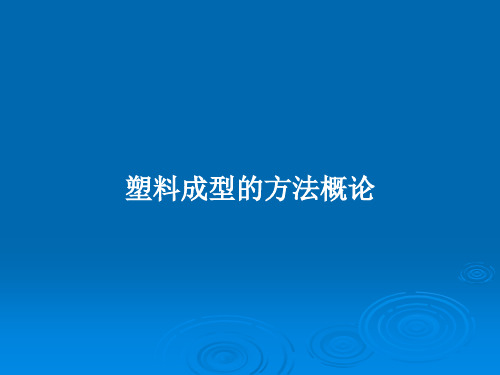
一、塑料的成型特性
1、塑料的类型
⑴ 热固性塑料: 在初次受热时变软,可以制成一定 形状, 但加热 到一定 时间或 加入固 化剂后 ,就硬 化定型 ,再加 热不熔 融也不 溶解, 形成体 型(网 状)结 构物质 的塑料 。
这种类型在成形过程中发生了化学变化,分子 结构产生了变化。
常见的热固性塑料有:酚醛塑料、 氨基塑 料、环 氧树脂 等。
(1)排气式注射成型。排气式注射成型应用的排气式注射机, 在料筒中部设有排气口,亦与真空系统相连接,当塑料化时, 真空泵可将塑料中合有的水汽、单体、挥发性物质及空气经排 气口抽走;原料不必预干燥,从而提高生产效率,提高产品质 量。特别适用于聚碳酸酯、尼龙、有机玻璃、纤维素等易吸湿 的材料成型。
(2) 流动注射成型。流动注射成型可用普通移动螺杆式注射机。 即塑料经不断塑化并挤入有一定温度的模具型腔内,塑料充满型 腔后,螺杆停止转动,借螺杆的推力使模内物料在压力下保持适 当时间,然后冷却定型。流动注射成型克服了生产大型制品的设 备限制,制件质量可超过注射机的最大注射量。其特点是塑化的 物件不是贮存在料筒内,而是不断挤入模具中,因此它是挤出和 注射相结合的一种方法。
(3) 共注射成型。共注射成型是采用具有两个或两个以上注射单 元的注射机,将不同品种或不同色泽的塑料,同时或先后注入模 具内的方法。用这种方法能生产多种色彩和(或)多种塑料的复合 制品,有代表性的共注射成型是双色注射和多色注射。
第12页/共73页
(4) 无流道注射成型。模具中不设置分流道,而由注射机的延 伸式喷嘴直接将熔融料分注到各个模腔中的成型方法。在注射 过程中,流道内的塑料保持熔融流动状态,在脱模时不与制品 一同脱出,因此制件没有流道残留物。这种成型方法不仅节省 原料,降低成本,而且减少工序,可以达到全自动生产
射出成型概论

螺桿轉速
每分鐘最快轉速RPM RPM=每分鐘泵浦吐出量(L)/油壓馬達過油量(c.c) 泵浦吐出量=油泵吐出量(c.c)*120*f / 馬達級數 設定方法: 螺桿轉速盡可能低,這樣不會過熱,溫度也均勻,為避 免發生空當時間(計量時間大過冷卻時間),提高轉速,調整 背壓,尋求最佳值
位置
在射出成型循環中, 行程控制用得最多, 而行程的精 確度對於射出成型品質穩定的控制也是最重要. 因此, 如 何控制行程的精確度是射出成型關鍵性的技術.
保壓壓力
定義:在射出動作的後段, 要控制熔融原料在模穴 中充填適當, 所使用的壓力. 說明: 在射出動作中是用高壓快速的方法來充填模穴, 但是 為了避免太多的壓力存於產品中, 因此在射出動作的後段, 一般用低壓的方式來使成品品質更好, 這就是維持壓力.
背压
在螺桿轉動進料動作中, 油壓缸所呈現阻止螺桿後退的壓力. 在進料的動作中, 螺桿一轉動就會往後退, 為了確保原料 熔融混合均勻, 就要使原料多承受螺桿混鍊一些時間, 因 此不能讓螺桿後退太快. 所以要在油壓缸內加大壓力迫使 螺桿後退較慢,而原料得以有很均勻的混鍊. 作用: 使原料在螺桿中更加致密 稳定計量以及脫氣(减少银丝现象) 设定方法: 在储料终止前降低背壓和螺桿轉速,如此才能使每一 模的射出料量得以準確,料量準確才能減少每一模的差異
压缩段
1.对塑料起挤压和剪切作用,同时使物料继续受热, 由固体变为熔融体,赶走原料中的空气及其他挥发成 份,增大密度,成为完全塑化的粘流状态(但不一定均 勻),一般通用型螺桿壓縮段長為全螺旋槽的25% 2.此段在原料熔解過程為擠壓,熔解及排氣之功能
计量段(均化)
1.原料至此,大部份呈液體狀態, 但由於原料的熔 解有先後,溫度不均勻,混合也未盡完善,再者壓縮 段所造成的擾流,在此段进一步搅料塑化均匀,并定 量定压地通过机头成型
材料成型概论 第三章 轧制成型2
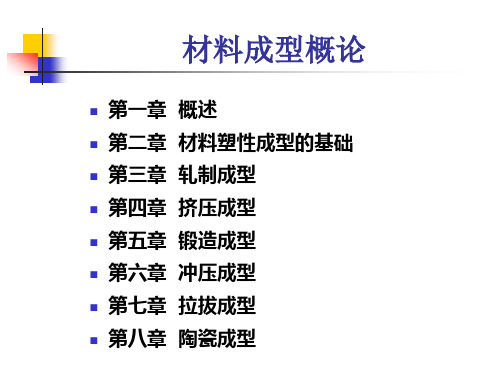
轧机按轧辊装配形式分类
按轧辊的数目、放置、大小来区分轧机的基本型式 为:表3-2
3.4.1 轧钢生产系统
轧钢生产工艺过程: 由钢锭或钢坯轧成具有一定规格和性能的钢材的一 系列加工工序的组合。
❖ 在提高质量和产量的同时,力求降低成本是制定轧 钢生产工艺过程的总任务和总依据。
❖ 碳素钢和合金钢的基本典型生产工艺过程如下图所 示。
3.4.1 轧钢生产系统
轧钢生产工艺过程总包括六大工序: 热轧工艺系统—— 坯料准备→加热→轧制→冷却→精整→验收入库 冷轧工艺系统—— 坯料准备→酸洗→轧制→退火→精整→验收入库
材料也比较稀贵,产量不大而产品种类繁多。 ❖ 常属中型或小型的型钢生产系统或混合生产系统。
❖ 各种轧钢生产系统组成见下表。
3.4.1 轧钢生产系统
轧材生产系统的发展: ❖ 向大型化、连续化、自动化方向发展。 ❖ 工艺流程经历了“长流程”到“短流程”的发展过
程。 ❖ 目前“长流程”和“短流程”共存。 ❖ 长流程主要吃铁水,短流程主要吃废钢。
❖ 采用连铸板坯作为轧制板带钢的原料是今后发展的 必然趋势。
3.4.1 轧钢生产系统
型钢生产系统 热轧线材、热轧棒材、热轧H型钢、热轧型钢
❖ 型钢生产系统的规模往往不很大,就规模而言可分 为大型、中型和小型三种生产系统。
❖ 年产100万t以上的称大型生产系统;年产30~ 100万t称中型生产系统;年产30万t以下的称小型 生产系统。
NB塑胶成型概论

NB塑膠成型概論章節一:成型概論章節二:原料介紹章節三:機台與模具保養原則及使用規範章節四:射出參數設定章節五:不良對策章節一:成型概論成形品因模溫所形成的應力殘留程度大致有如圖之關系,依不同材質其流動粘度對溫度的依存性及熱傳率各自不同,所以成形工程的適當模溫範圍也各自不同。
內應力可分為流動應力(流動所造成的)及熱應力(模具溫具與塑料溫度差愈多,熱應力愈大):模溫 :殘留應力% :適當模溫範圍較高模溫之結果:1增加結晶度及較均勻的結構。
2使成形收縮充分,日後的後收縮減少。
3增加成品的強度及耐熱性。
4減少內應力的殘留,分子配向及變形。
5減少充填時的流動抵抗。
6使成形品外觀具光澤。
7造成冷卻時間加長。
8成品易有毛邊。
9近澆點處厚肉部易縮水。
10遠澆點處改善縮水現象。
11使結合線不明顯而呈霧狀。
一般而言:料管設定溫度每段料管溫度差10~15度,例如以PC+ABS材質來說有HEAT RUNNER則五段溫為260 255 245 230 220若無熱澆道系統,則五段溫為250 260 245 230 220,(紅色部是為防止脫模產生拉絲現象而使末段溫比前段溫低)一.模穴內壓的形成和密度變化1 充填FILLING:塑膠熔膠在射出階段只因流路阻抗而微受壓縮,內壓緩慢上昇,密度也微上昇,而充填速度快慢會對成形品外觀及分子配向和結晶度有重要影響。
Q(充填速度)=V(流動速度)*A(熔膠流動先端所含蓋的截面積)當熔膠通過狹窄的流路時,流動速度會劇增,使成形品容易產生噴痕、流痕等不良,同時高速流動的熔膠會產生極大剪應力(附註3),造成與模壁之摩擦過大,導致摩擦生熱所產生之熱量釋放至成品,因過熱而劣化,劣化部份會浮現於表面上,造成流痕。
若熔膠通過寬厚之流路,則流動速度變慢,易使成形品出現波紋無光澤。
2 壓縮PACKING:模穴被充滿熔膠時,仍處於高溫低密度的狀態,在充填後必立即繼續加壓以提高模穴內熔膠的密度。
熔膠被縮壓其密度及內壓都會急劇上昇,故壓縮程度決定成形品的外形輪郭及是否發生溢料FLASH之因素。
材料成型过程控制概论

2020/7/10
2
自动控制
自动控制是采用自动检测、信号调节(包括 数字调节器、计算机)、电动执行等自动化装置, 组成的闭环控制系统,它使各种被控变量(如流 量、温度、张力、轧机辊缝和轧机转速等)保持 在所要求的给定值上。过程自动化是指在生产过 程中,由多个自动控制系统组合的复杂过程控制 系统。
2020/7/10
材料成形过程控制
1. 概论
余万华 北京科技大学材料学院
2020/7/10
1
材料成形过程控制
这门课是在学习完《自动控制原理》的基础 上开设的,目的是:
(1)学习现代控制理论的一些基本知识; (2)从系统角度讲解自动控制原理的应用; (3)工业过程控制系统; (4)了解材料加工生产过程中的一些实际
控制系统的组成和工作原理。
3
自动控制目的
生产过程实现自动化的目的是:提高工序质量, 用有限资源,制造持久耐用的精美产品;在人 力不能胜任的复杂快速工作场合中实现自动操 作;把人从繁重枯燥的体力劳动中解放出来; 不轻易受人的情绪和技术水平的影响,稳定工 序质量。实现自动化大批量生产,提供质量好、 性能稳定、价格具有竞争力的产品,为企业生 存发展提供更大的空间。
2020/7/10钢生产日益连续化。
轧制速度的不断提高。
生产过程计算机控制。
产品质量和精度高标准交货。
操作者具有高度水平。
由于连轧机生产效率高,质量易于控制,轧制过程连续,易于实现自动化和机械化, 而且这种轧机产量大,生产效率高,质量易于控制,经济效益非常显著。所以各种先进 的科学成果都竞相应用于连轧过程,大大促进了连轧过程自动化的发展,其中以热带连 轧自动化的发展最为迅速和成熟。
2020/7/10
材料成型原理与工艺(01)-液态金属成形概论
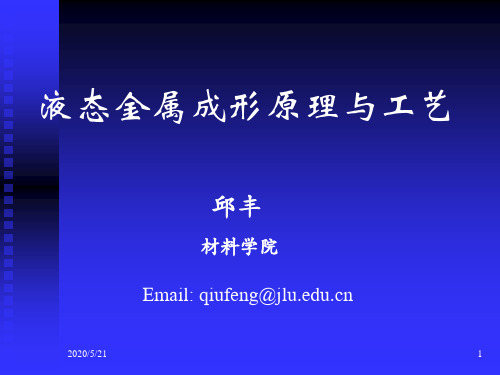
夹杂物的排除: 夹杂物的排除:
金属液静止处理、真空浇注,加熔剂, 金属液静止处理、真空浇注,加熔剂,过滤法
2012-1-8
凝固区域
固相区、凝固区、液相区
凝固方式
逐层凝固方式 体积凝固(糊状凝固方式) 体积凝固(糊状凝固方式) 中间凝固方式
2012-1-8 22
如果合金的结晶温度范围很宽,且铸件的温度分布较 为平坦,则在凝固的某段时间内,铸件表面并不存在 固体层,而液、固并存的凝固区贯穿整个断面。由于 这种凝固方式与水泥类似,即先呈糊状而后固化,故 称为糊状凝固。球墨铸铁、高碳钢、锡青铜和某些黄 铜等都是糊状凝固的合金。 中间凝固方式 大多数合金的凝固介于逐层凝固和糊状 凝固之间,称为中间凝固方式。中碳钢、高锰钢、白口 铸铁等具有中间凝固方式
气压保温浇包
15
采用德国KW公司技术的新二线主机,发动机缸体造型生产线。
罗兰门第制芯中心
2012-1-8 16
二、液态金属在铸型中的流动
1、 液态金属充型能力的基本概念 、
液态金属充满铸型型腔,获得形状完整、轮廓清晰的铸件的能力, 叫做液态金属充填铸型的能力,简称液态金属的充型能力。 液态金属充填铸型一般是在纯液态下充满型腔的,也有边充型边结晶的 情况,在充型过程中当液态金属中形成晶粒堵塞充型通道时,流动则停 止,造成铸件“浇不足”缺陷。 液态金属的充型能力(实验-螺旋形试样):
2012-1-8
18
思考题 1 1. 液态金属成形的概念是什么?液态金属 液态金属成形的概念是什么? 成形具有哪些优点? 成形具有哪些优点? 2. 液态金属成形生产过程。 液态金属成形生产过程。
材料成型概论-第四讲-钢坯型钢生产工艺

轧制缺陷
形状特征 产生原因
轧辊调整不当、孔型不当等 初轧机辊面粗糙或轧制方法不当 辊面粗糙、磨损或氧化皮剥落 导卫装置不适、磨损、粘结等 孔型过充满、辅助设施安装不当
沿轧制方向出现的重叠缺陷 沿轧制方向出现的皱纹缺陷 制品表面粗糙呈凸凹不平状 表面划有沟状痕迹 沿轧制方向出现的连续凸筋
辊 印
……
表面缺陷呈周期性出现
其横截面主要是圆形,也可以是方形、矩形 或多边形。
4.1.2 钢坯的表面和内部缺陷
4.1.2 钢坯的表面和内部缺陷
表面缺陷: 钢锭带来的缺陷
种 类 形状特征 产生原因
钢锭纵裂纹或热应力
钢锭横裂纹、加热不均等 钢锭表面或表层有气泡 钢锭凝固时的收缩孔等 钢锭内部或表面有杂质混入 钢锭的二次结疤或低温轧制
4.1 钢坯生产
4.1.1 钢坯的种类、形状和用途
按断面形状和特性不同可分为五类:
方坯、矩形坯、板坯、异型坯、管坯
方坯(blooms and billets)
其断面为方形,横截面沿长度方向不变。 边长大于 150mm 方坯称为大方坯 (Square blooms)。 边长40~150 mm方坯称为小方坯(billets)或方 坯(Square billets)。
钢材品种规格:轧制钢材的断面形状和尺寸总称。
4.2.1 型钢定义
全长具有一定断面形状和尺寸的实心钢材称为型 钢。(Hot/Cold-Rolled bars/sections)
简单断面型钢:圆钢、方钢、扁钢、角钢、六角 钢、多边形钢等; 复杂断面型钢:槽钢、工字钢、H型钢、钢轨等。
4.2 型钢生产的一般概念
断面各分支部分接触轧辊和变形的非同时性;
断面各处温度不均匀,而产生轧后冷却收缩不均匀,造成 轧件弯曲和扭转; 工具磨损也不均匀,轧件尺寸难以精确计算; 轧机调整、导卫装置设计、安装复杂。
等静压成型概论
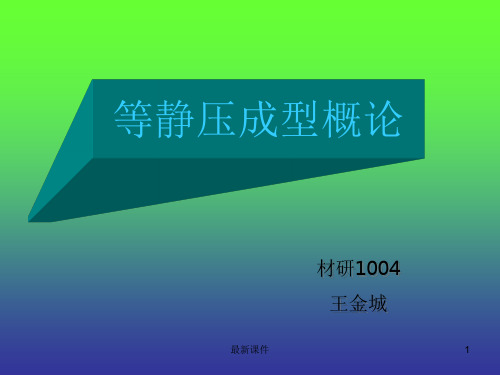
湿袋式装料机构
1-料桶,2-粉料, 3-模袋,4-振动
台
模袋一般用橡胶塞塞紧袋口,再用金属丝扎紧密封,以 防止液体渗入粉料。压制密度高的压坯时,通常要先排除粉 料的中空气,可采用注射器针最插新课入件橡皮塞内用真空泵抽出。 25
➢冷等静压制(CIP)
⑷压制和脱模
密封(抽空)装料模袋 要套上多孔金属管
前者常用水或油作压力介 的。弹性模具在受到液体介
质,故有液静压、水静压或 质压力时产生的变形传递到
油水静压之称;
模具中的粉料,粉料与模具
后者常用气体(如氩气) 壁的摩擦力小,坯体受力均
作压力介质,故有气体热等 匀,密度分布均匀,产品性
静压之称。
能有很大提高。
最新课件
4
➢等静压制的基本原理
等静压成型的过程
拉杆式压力容器结构
1-螺母2-上横板3-介质输入管4-盖
板5、6-密封塞7-拉杆8-压力容器9-
外箍10-下横最板新课件
11
➢冷等静压制(CIP)
螺纹式容器在纵向受压时不均匀 的螺纹负荷是造成压力容器破坏
的主要因素
螺纹式结构 压力容器装卸料口是靠压紧螺母压 紧密封塞和密封垫圈来密封紧固的。 工作室经受的轴向压力由压紧螺母 和筒体通过螺纹联接来承受,工作室 经受的径向压力由筒体承受。
多角形或不规则形的粉末容易压得强度较高的压块。 粉末料的适当湿度有助于压块有较高的密度;但湿度过大 (超过4%)又使压制过程中难以从模袋内排除空气,容易 造成压块分层和在烧结时开裂。
最新课件
24
➢冷等静压制(CIP)
⑶装料和密封抽气
湿袋式装料过程示于右图。
模袋应放置在电磁振动台上装料,通过振动器
聚合物成型加工基础概论(PDF)

高分子材料加工工程过去、现在、未来四川大学高分子科学与工程学院1838年,A.Parker制备出了第一种人造塑料——硝酸纤维素,并在1862年伦敦的国际展览会上展出。
当时,人们希望该材料能替代象牙一类的天然材料,被称为Parkesine。
1840年,Goodyear和Hancock针对天然橡胶开发了“硫化”工序,达到消除粘性增加弹性的目的。
通过加入硫磺粉末在橡胶本体中产生了额外的化学键,从而使得天然橡胶性能发生改变。
1851年,硬质橡胶实现商品化。
1870年,纽约的J.Hyatt在高温高压下制备了低硝酸含量的硝酸纤维素,俗称赛璐珞,并申请了专利。
它是第一种具有商业价值的聚合物,也是在1907年Bakeland开发出酚醛塑料前唯一的商品塑料。
而由苯酚和甲醛反应制得酚醛塑料则是最古老的真正意义上的合成聚合物。
高分子的过去、现在和未来在Staudinger的理论出现之前,科学界对橡胶和其他分子量很高的材料的本质认识一直是不清楚的。
对19世纪的大多数研究学者来说,分子量超过10,000g/mol的物质似乎是难以置信的,他们把这类物质同由小分子稳定悬浮液构成的胶体系统混为一谈。
Staudinger否定了这些物质是有机胶体的观点。
他假定那些高分子量的物质,即聚合物,是由共价键形成的真实大分子,并在其大分子理论中阐明了聚合物由长链构成,链中单体(或结构单元)通过共价键彼此连接。
较高的分子量和大分子长链特征决定了聚合物独特的性能。
尽管一开始他的假设并不为大多数科学家所认可,但最终这种解释得到了合理的实验证实,为工业化学家们的工作提供了有力的指导,从而使得聚合物的种类迅猛地增长。
1953年,Staudinger被授予诺贝尔奖。
现在人们都已非常清楚:塑料以及橡胶、纤维素、DNA等很多物质都是大分子。
是钢的体积产量的2~3倍法国西德乐公司的DLC高效成型机正在成型的塑料瓶日精ASB公司的DLC高效成型机塑料管材的智能铺设精确厚度控制多层复合膜吹塑成型高分子材料工程未来发展热点高效化高速化精密化WP 公司的远程控制WP 公司的远程控制36吨/小时产量的设备36吨/小时产量的设备可注射万分之一克的精密注射机可注射万分之一克的精密注射机聚合物加工的概念聚合物加工(Polymer Processing)是将聚合物物料转变为实用制品的各种工艺和工程。
发泡成型原理概论
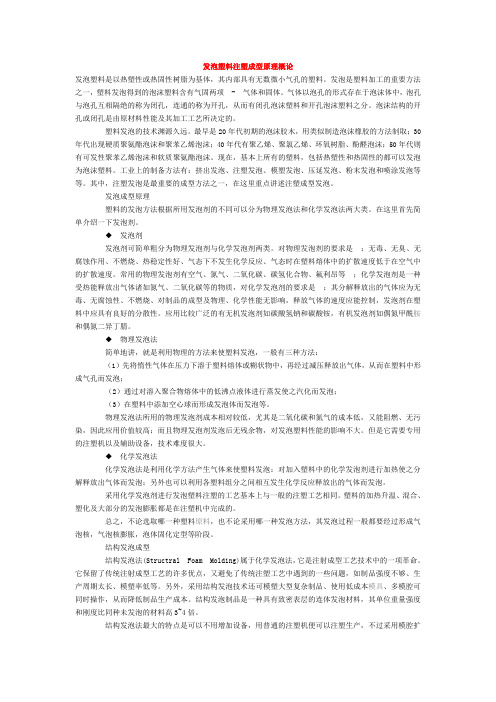
发泡塑料注塑成型原理概论发泡塑料是以热塑性或热固性树脂为基体,其内部具有无数微小气孔的塑料。
发泡是塑料加工的重要方法之一,塑料发泡得到的泡沫塑料含有气固两项- 气体和固体。
气体以泡孔的形式存在于泡沫体中,泡孔与泡孔互相隔绝的称为闭孔,连通的称为开孔,从而有闭孔泡沫塑料和开孔泡沫塑料之分。
泡沫结构的开孔或闭孔是由原材料性能及其加工工艺所决定的。
塑料发泡的技术渊源久远。
最早是20年代初期的泡沫胶木,用类似制造泡沫橡胶的方法制取;30年代出现硬质聚氨酯泡沫和聚苯乙烯泡沫;40年代有聚乙烯、聚氯乙烯、环氧树脂、酚醛泡沫;50年代则有可发性聚苯乙烯泡沫和软质聚氨酯泡沫。
现在,基本上所有的塑料,包括热塑性和热固性的都可以发泡为泡沫塑料。
工业上的制备方法有:挤出发泡、注塑发泡、模塑发泡、压延发泡、粉末发泡和喷涂发泡等等。
其中,注塑发泡是最重要的成型方法之一,在这里重点讲述注塑成型发泡。
发泡成型原理塑料的发泡方法根据所用发泡剂的不同可以分为物理发泡法和化学发泡法两大类。
在这里首先简单介绍一下发泡剂。
◆发泡剂发泡剂可简单粗分为物理发泡剂与化学发泡剂两类。
对物理发泡剂的要求是:无毒、无臭、无腐蚀作用、不燃烧、热稳定性好、气态下不发生化学反应、气态时在塑料熔体中的扩散速度低于在空气中的扩散速度。
常用的物理发泡剂有空气、氮气、二氧化碳、碳氢化合物、氟利昂等;化学发泡剂是一种受热能释放出气体诸如氮气、二氧化碳等的物质,对化学发泡剂的要求是:其分解释放出的气体应为无毒、无腐蚀性、不燃烧、对制品的成型及物理、化学性能无影响,释放气体的速度应能控制,发泡剂在塑料中应具有良好的分散性。
应用比较广泛的有无机发泡剂如碳酸氢钠和碳酸铵,有机发泡剂如偶氮甲酰胺和偶氮二异丁腈。
◆物理发泡法简单地讲,就是利用物理的方法来使塑料发泡,一般有三种方法:(1)先将惰性气体在压力下溶于塑料熔体或糊状物中,再经过减压释放出气体,从而在塑料中形成气孔而发泡;(2)通过对溶入聚合物熔体中的低沸点液体进行蒸发使之汽化而发泡;(3)在塑料中添加空心球而形成发泡体而发泡等。
工程材料与成形技术基础-概论试讲
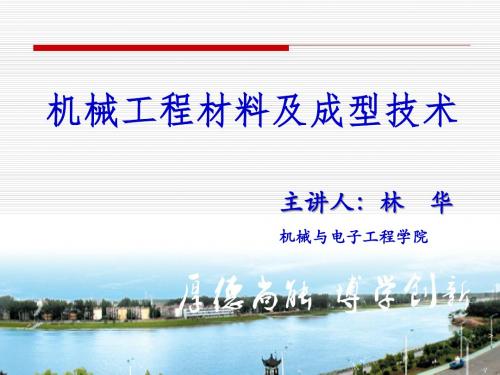
概“论9.11”事件与材料
纽约世贸大厦
1973年竣工,110层、411m 主体钢架结构(用钢7.8万 吨) 墙面由铝板和玻璃砖 组成
2001年9月11日,美国纽约 世界贸易中心遭到恐怖分 子以民航客机撞击被摧毁 。世贸大厦的钢结构具有 不合理的搭接式结构,材 料又不是耐热钢。在高温 下就能软化,甚至熔化导 致世贸大厦倒塌。
在它上面。
概论
概论
几种可反复读写的移动存储器的比较
种类
使用的 主要材料
存储 容量
软盘 氧化铁磁性材料 1.44 Mb
多元合金和以ZnS等 CD-RW 为主的陶瓷材料 650 Mb
特点
容量小,主要是文本文件 的存储。 驱动器兼容CD光盘,光盘 价低,用量高速增长。
MO (磁光盘)
VD-RW
TbFeCo合金磁光材 650Mb
船体采用了高强 度复合材料,使 船的重量减至 5220公斤,航速 高达44.5公里/ 时 (选自Popular Science 中文版 1998年6月,p.4)
概论
高分子材料具有 突出的隔热、绝 缘和柔韧性能
概论
比尔.盖茨与光盘
比尔.盖茨在西雅图 Microsoft公司外的 树林里,手持一张 CD光盘,坐在高55 英尺(16.5米),计 330,000 页的资料上。 照片不仅说明一张 小小CD光盘可以存 储比尔.盖茨身下厚 达55英尺的一张张 资料,而且,节约 了森林资源,于环 保有利,因为纸张 是造纸原料。
世界由“蒸汽时代” 进入“电气时代”
莫尔斯电报 机发报
概第论三次工业革命(20世纪40年代起)
以核能、电子计算机、空间技术和生物工程的发明和 使用为主要标志,涉及信息技术、新能源技术、新材料技 术、生物技术、空间技术和海洋技术等诸多领域的一场信 息控制技术革命。
材料成型原理-4.1 4.2 晶体形核
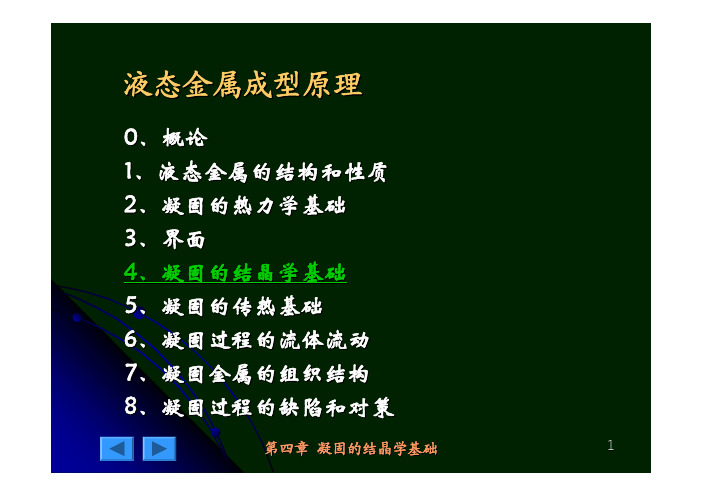
4、凝固的结晶学基础5、凝固的传热基础6、凝固过程的流体流动7、凝固金属的组织结构8、凝固过程的缺陷和对策第四章(1)由液体向晶态固体(2)由液体向非晶态固体常用工业合金或金属的凝固过程一般只涉及前者,本章主要讨论液态金属、合金的凝固过程。
第四章第五节液-第六节共晶合金的凝固第七节包晶合金的凝固第四章毕。
第四章6第四章()V G L T S T Δ=−−⋅Δ=−过冷:液体金属开始结晶的温度必须低于平衡熔点Tm ,此现象称之为过冷。
过冷度ΔT=Tm-T 。
过冷度ΔT 越大,凝固相变驱动力ΔG V 越大。
过冷度ΔT 越大,凝固相变驱动力ΔG V越大。
第五节液-固界面形貌的稳定性第六节共晶合金的凝固第七节包晶合金的凝固第四章发生形核的过程,也称z非自发形核(heterogeneous nucleation外来质点或型壁界面提供的衬底进行生核过程,亦称“异质形核”或“非均质形核工业金属凝固大都是异质生核。
第四章第四章系统自由能变化= 体积自由能的变化SLV A G V G σ+Δ⋅=ΔΔG -系统自由能变化V,A -分别为晶胚的体积和表面积σSL -晶胚的界面能ΔG V -单位体积液态金属凝固时自由能的变化10第四章凝固的结晶学基础SL V r G r G σππ23434+Δ−=ΔLS m r r T T L G σππ23434+⋅Δ−=ΔLS m r T T L r σππ23434+Δ⋅−=对于半径为r 的球形晶胚(均质生核),0=∂Δ∂r G T L T G r m LS V LS Δ=Δ−=σσ22*令,则有求得临界晶核半径:V LS G r Δ=σ2*mV T TL G Δ−=Δ因1、临界形核半径第四章TL T G r mLS V LS Δ=Δ−=σσ22*r <r*时,r ↑→ΔG ↑r = r*处时,ΔG 达到最大值r >r*时,r ↑→ΔG ↓实际上金属结晶的过冷度一般为几分之一到几十摄氏度。
- 1、下载文档前请自行甄别文档内容的完整性,平台不提供额外的编辑、内容补充、找答案等附加服务。
- 2、"仅部分预览"的文档,不可在线预览部分如存在完整性等问题,可反馈申请退款(可完整预览的文档不适用该条件!)。
- 3、如文档侵犯您的权益,请联系客服反馈,我们会尽快为您处理(人工客服工作时间:9:00-18:30)。
合理假設 可能是原料問題
基本原則 BASIC ROULES Some Basic Rules to Follow in Effectively Solving Molding Problems...
•擬定計畫 Have your plan ready •一次改變一個參數 Make Only One Change at a Time •耐心找出影響 Be Patient, Let Them Take Effect •保持機器運轉狀態 Keep Machine on Cycle •記錄改變結果 Keep Records of Changes
減少縮水的方法 Ways to Minimize Sink Marks 確認部品設計 增加保壓時間
Check the Part Design 確認入料速率 Increase Injection Hold Time 確認熔融溫度 Check Melt Temperature 增加背壓 Increase Back Pressure 維持有效排氣 Maintain Sufficient Venting 增加流道/澆口直徑 Increase Runner/Gate Dimensions
• 確認阻逆閥與料管是否過度磨損或損壞 Check Non-Return Valve and Barrel for Excessive Wear or Damage
剝離 Delamination
層剝離發生的原因在於 混入不相同的聚合物. The Separation by Layer Caused by Contamination of a Dissimilar Polymer.
射出成型問題 Injection molding problems
Voids
Fingerprinting
Streaking
Warpage
Splay Burning
Gloss
Overpackingsh
製程中問題發生時,第一件要想到的事情 製程中問題發生時 第一件要想到的事情 What is the first thing you do to your process when a problem occurs?
氣体燃燒 Gas Burn
•不適當的合模 Tonnage •排氣阻塞 •缺乏適當的排氣 Venting •射出速度過快 •射出壓力過高 High •料溫過高 High •模溫過高 High Improper Clamp Clogged Air Vents Lack of Adequate Injection Speed Too High Injection Pressure Too Melt Temperature Too Mold Temperature Too
空穴 Voids
確認產品設計
減少空穴的方法 Ways to Minimize Voids
確認熔融溫度 Check Melt Temperature 增加背壓 Increase Back Pressure 維持有效排氣 Maintain Sufficient Venting 增加流道/膠口直徑 Increase Runner/Gate Dimensions 增加射出壓力 Increase Injection Pressure
毛邊 Flash
當射出壓力超過合模力 或遮斷閥損壞時,毛邊就 產生. Flash Will Occur When Injection Pressure Exceeds Clamp Force or Shut-Off is Damaged.
毛邊 Flash
•合模力不足 •射出壓力過大 •射出高壓時間過長 •射出速度過快 •料溫過高 •不適當的入料速率 •模具損壞或過熱 Loose Clamp Injection Pressure Too High Injection High Pressure on Too Long Injection Speed Too Fast Melt Temperature Too High Improper Feed Rate Damaged or Overheated Mold
結合線 Weld Lines
來自不同澆口或同一澆口的分 流,當多股熔料前端融合在一起 時,結合線由此產生. Weld lines Occur When Two or More Melt Fronts Merge. Typically, These Will Be Melt Fronts from Different Gates, or a Single Melt Front Forced to Split Around an Obstruction Such as a Core pin.
Surface Burning of 部品表面燒焦 Parts 減少表面燒焦的方法
Ways to Minimize Surface Burning
• 降低儲料溫度 • Decrease the Stock Temperature • 降低射出速度 • Decrease Injection Speed • 確認模具排氣 • Check Venting of the Mold • 加大澆口 • Enlarge Gates • 確認澆道與空射狀況 • Check Sprue for Burning and/or Purge Shot • 確認合模力 • Check Clamp Pressure • 確認排氣 • Check Venting • 降低射出速度 • Decrease Injection Speed • 降低射出壓力 • Decrease Injection Pressure • 確認儲料與模 • Check Stock and Mold Temperatures
Check the Part Design 確認入料速率 Check Feed Rate 增加保壓時間 Increase Injection Hold Time 增加射出速度 Increase Injection Speed 增加模溫 Increase Mold Temperature
彎曲 Warpin g
縮水 Sinks
產品肉厚部,因內應力 影響,致使聚合物分子 量不足的結果. Caused by Internal Stresses within Thicker Sections of the Part as a Result of Insufficient Polymer Molecules.
縮水 Sinks
部品表面燒焦 Surface Burning of Parts
部品表面燒焦發生可能原因由於 過高儲料溫度,過高剪切熱,過高背 壓.確認排氣適當.為克服流動限制, 採高速射出時,摩擦燒焦亦會發生. Surface Burning of Parts Can Be Caused by Too High a Stock Temperature. Excessive Shear Heating Caused by Too High a Back Pressure is Also a Possible Cause. Check to Make Sure that the Venting of the Mold is Adequate. When a High Injection Speed is Used to Overcome Flow Restrictions, Frictional Burning Can Result.
彎曲是因部品的兩側承受 不平均的配向與應力 Warping is Caused by Non-Uniform Orientation and Uneven Stress Levels on Different Sides of the Part.
彎曲 Warping
•確認片狀部品的設計 •確認入料速率 •降低射出壓力 •降低射出速度 •降低模溫 •增加保壓時間 •確認熔融溫度 •確認冷卻過程 Check the Piece Part Design Check Feed Rate Decrease Injection Pressure Decrease Injection Speed Decrease Mold Temperature Increase Injection Hold Time Check Melt Temperature Check Cooling Passages
成型工程塑膠 10項法則 項法則 Ten Do for Molding Engineering Resins
• 熟識成型的原料 Know Your Material • 適當的乾燥 Dry Properly • 按照推薦的成型條件 Use Recommended Processing Conditions • 選用合適的設備 Use Properly Sized Equipment • 適當設計模具 Use Properly Designed Tooling • 流道適當 Use Adequate Runners • 排氣要充分 Use Proper Venting • 選用合適的噴嘴 Use Nozzles with Proper Heat Controls • 採用合適的螺桿設計 Use Proper Screw Design • 一年一次或兩次的設備保養計畫 Schedule Annual or Bi-Annual Equipment Maintenance
氣体燒焦 Gas Burn
氣体燒焦是部品劣解的一 種,發生原因在於空氣或瓦 斯氣於模具內受到絕熱壓縮 燃燒. Gas Burn is a Degradation of the Part Caused by the Compression and Ignition of Trapped Air or Gasses in the Mold.
Check Feed Rate 增加射出速度 Increase Injection Speed 增加射出壓力 Increase Injection Pressure 增加模溫 Increase Mold Temperature