影响烧结法生产氧化铝的溶出因素
影响溶出度测定试验结果的因素(标准版)
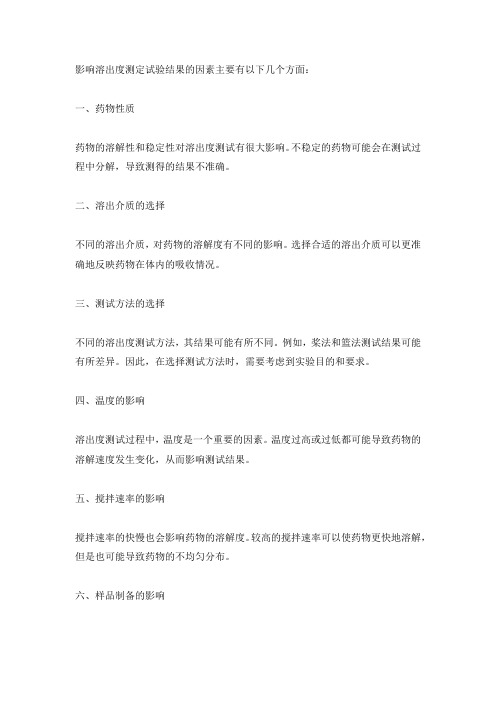
影响溶出度测定试验结果的因素主要有以下几个方面:
一、药物性质
药物的溶解性和稳定性对溶出度测试有很大影响。
不稳定的药物可能会在测试过程中分解,导致测得的结果不准确。
二、溶出介质的选择
不同的溶出介质,对药物的溶解度有不同的影响。
选择合适的溶出介质可以更准确地反映药物在体内的吸收情况。
三、测试方法的选择
不同的溶出度测试方法,其结果可能有所不同。
例如,桨法和篮法测试结果可能有所差异。
因此,在选择测试方法时,需要考虑到实验目的和要求。
四、温度的影响
溶出度测试过程中,温度是一个重要的因素。
温度过高或过低都可能导致药物的溶解速度发生变化,从而影响测试结果。
五、搅拌速率的影响
搅拌速率的快慢也会影响药物的溶解度。
较高的搅拌速率可以使药物更快地溶解,但是也可能导致药物的不均匀分布。
六、样品制备的影响
样品制备的过程中,药物的粉碎程度、颗粒大小等因素都会影响到溶出度测试的结果。
因此,需要严格按照操作规程进行样品制备。
七、测定设备的精度和准确性
测定设备的精度和准确性对测试结果也有很大影响。
如果设备存在误差,那么测试结果就会受到影响。
综上所述,影响溶出度测定试验结果的因素较多,需要在试验中充分考虑这些因素,以确保得到准确可靠的结果。
烧结法生产氧化铝溶出及副反应研究

烧结法生产氧化铝溶出及副反应研究白鹏翔(神华准能资源综合开发有限公司,内蒙古 鄂尔多斯 010300)摘 要:采用烧结法生产氧化铝,熟料中原硅酸钙含量较高,高压溶出时同铝酸钠溶液发生反应,造成Al2O3和Na2O进入白泥导致氧化铝、苛性钠溶出率下降,副反应也无法避免。
本文以中铝中州分公司熟料为实验原料,通过对比试验,对烧结法生产氧化铝熟料溶出时间、溶出温度、溶出液液固比及碳酸钠浓度等因素进行了研究,得出烧结法生产氧化铝最佳溶出条件。
关键词:氧化铝;烧结法;副反应;溶出率;铝酸钠中图分类号:TF821 文献标识码:A 文章编号:1002-5065(2016)23-0029-3Research of dissolution and side reaction in alumina sintering productionBAI Peng-xiang(Shenhua Zhunneng comprehensive resource development limited,Erdos 010300,China)Abstract: Calcium silicate, used for calcining alumina clinker central plains content is higher, high pressure dissolution react with sodium aluminate solution, Al2O3 and Na2O into white clay to alumina, caustic soda dissolution rate decreased, the adverse event is unable to avoid. Based on chalco zhongzhou branch clinker as the experimental material, through the contrast test, for sintering process production alumina clinker dissolution time, temperature and dissolution dissolution liquid liquid solid ratio and the concentration of sodium carbonate was studied, calcining alumina best dissolution conditions are obtained.Keywords: alumina; sintering; side reaction; dissolution rate; sodium aluminate1 烧结法生产氧化铝溶出概述1.1 国内氧化铝生产现状我国是铝土资源大国,且大部分铝土矿为一水硬铝石型铝土矿,占全国总量的99%以上,铝硅比通常在4~7[1],不适合拜耳法生产氧化铝,针对一水硬铝石型铝土矿,国内大部分企业普遍采用烧结法。
溶出的影响因素
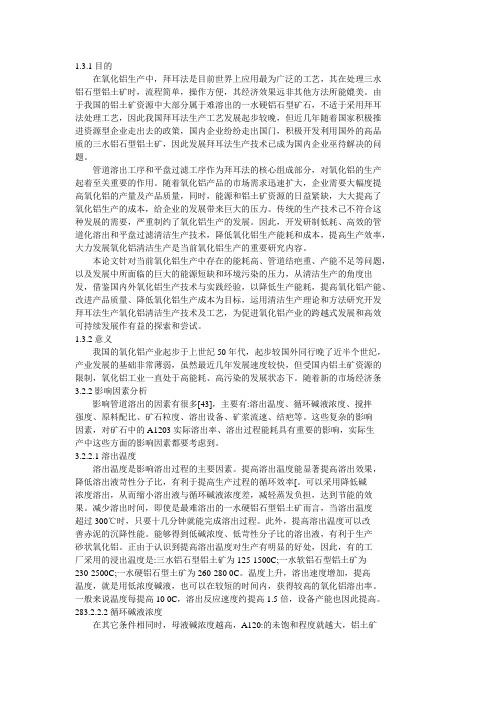
1.3.1目的在氧化铝生产中,拜耳法是目前世界上应用最为广泛的工艺,其在处理三水铝石型铝土矿时,流程简单,操作方便,其经济效果远非其他方法所能媲美。
由于我国的铝土矿资源中大部分属于难溶出的一水硬铝石型矿石,不适于采用拜耳法处理工艺,因此我国拜耳法生产工艺发展起步较晚,但近几年随着国家积极推进资源型企业走出去的政策,国内企业纷纷走出国门,积极开发利用国外的高品质的三水铝石型铝土矿,因此发展拜耳法生产技术已成为国内企业巫待解决的问题。
管道溶出工序和平盘过滤工序作为拜耳法的核心组成部分,对氧化铝的生产起着至关重要的作用。
随着氧化铝产品的市场需求迅速扩大,企业需要大幅度提高氧化铝的产量及产品质量,同时,能源和铝土矿资源的日益紧缺,大大提高了氧化铝生产的成本,给企业的发展带来巨大的压力。
传统的生产技术己不符合这种发展的需要,严重制约了氧化铝生产的发展。
因此,开发研制低耗、高效的管道化溶出和平盘过滤清洁生产技术,降低氧化铝生产能耗和成本,提高生产效率,大力发展氧化铝清洁生产是当前氧化铝生产的重要研究内容。
本论文针对当前氧化铝生产中存在的能耗高、管道结疤重、产能不足等问题,以及发展中所面临的巨大的能源短缺和环境污染的压力,从清洁生产的角度出发,借鉴国内外氧化铝生产技术与实践经验,以降低生产能耗,提高氧化铝产能、改进产品质量、降低氧化铝生产成本为目标,运用清洁生产理论和方法研究开发拜耳法生产氧化铝清洁生产技术及工艺,为促进氧化铝产业的跨越式发展和高效可持续发展作有益的探索和尝试。
1.3.2意义我国的氧化铝产业起步于上世纪50年代,起步较国外同行晚了近半个世纪,产业发展的基础非常薄弱,虽然最近几年发展速度较快,但受国内铝土矿资源的限制,氧化铝工业一直处于高能耗、高污染的发展状态下。
随着新的市场经济条3.2.2影响因素分析影响管道溶出的因素有很多[43],主要有:溶出温度、循环碱液浓度、搅拌强度、原料配比、矿石粒度、溶出设备、矿浆流速、结疤等。
氧化铝实验

实验一球磨实验(胡慧萍编)一、实验计划学时12学时二、实验目的与要求1、了解氧化铝生产中物料球磨的重要意义;了解和掌握球磨设施种类和作用机理;2、了解影响球磨效果的主要因素,如:分散介质、球料比、球磨时间和转速。
3、了解用筛分法检验球磨效果。
三、实验原理在拜耳法氧化铝生产工艺中,铝土矿必须经过球磨工序才能进入下一个溶出工序。
铝土矿球磨好或坏直接影响着铝土矿的溶出效果。
在烧结法氧化铝生产工艺中,对铝土矿与配料的球磨好或坏直接影响着物料的烧结效果,以及影响烧结料的溶出效果。
在烧结法氧化铝生产工艺中,熟料溶出就是一个球磨过程,所以,物料球磨的作用就可想而知了。
有关球磨作用的物理模型主要有两类:一类认为在机械能转变为化学能的过程中,热能为中间步骤。
由于无机颗粒在超细球磨过程中其表面化学键断裂而产生不饱和键、自由离子和电子以及晶格缺陷、晶型转变和非晶化等原因,导致晶体内能增高,而且物质内部迅速发展的裂纹使其微接触点温度可达1300K以上,从而诱发机械化学反应在这些“热点”处进行。
另一类认为球磨作用导致晶格松弛与结构裂解,能够激发出的高能电子和离子形成等离子区。
高激发状态诱发的等离子体产生的电子能量可以超过10eV,从而使通常情况下不能进行的反应得以进行。
一般认为,球磨作用能强化矿物的浸出过程,主要归因于在球磨过程中矿物发生了如下的结构变化:(1)晶体的结构畸变;(2)化学反应导致的结构变化;(3)比表面积增大。
从宏观考虑,球磨效果主要体现于矿物颗粒变小,表面积增大。
拜耳法铝土矿球磨要求100号筛残留小于10%;160号筛残留小于20%;烧结法生料球磨要求是细磨,120号筛残留小于14.5%。
四、实验仪器与药品主要仪器:球磨机,筛子主要药品:铝土矿五、实验操作1、铝土矿在空气气氛中球磨球磨罐内衬为聚四氟乙烯,容积250ml,配有大(Φ=20mm)、中(Φ=10mm)、小(Φ=6mm)三种玛瑙球,各若干。
在空气气氛中球磨后,将样品取出,称重,进入筛分操作。
氧化铝生产中熟料溶出二次反应与高浓度粗液制备技术的开题报告

氧化铝生产中熟料溶出二次反应与高浓度粗液制备技术的开题报告一、研究背景氧化铝作为一种广泛应用于制陶、研磨、光学等领域的重要材料,其生产工艺及相关技术研究一直是工业界和学术界关注的热点问题。
其中,熟料溶出二次反应和高浓度粗液制备技术是氧化铝生产过程中的两个重要环节。
在氧化铝生产的过程中,熟料溶出是指通过浸出熟料来获得高浓度氢氧化铝溶液的过程。
在该过程中,熟料的质量和浸出条件等因素会直接影响最终产品的质量和成本。
因此,熟料溶出二次反应的研究至关重要。
另外,高浓度粗液制备技术是指通过浓缩、离心等方法将熟料溶出所得的氢氧化铝溶液处理成含有高浓度氧化铝颗粒的浆料或固体。
高浓度粗液的制备直接关系到氧化铝产品的质量和产量,因此其研究工作也备受重视。
二、研究目的和意义本研究的主要目的在于通过对氧化铝生产中熟料溶出二次反应和高浓度粗液制备技术的研究和优化,提高氧化铝生产过程中产品的质量和效率,同时降低生产成本,实现可持续发展。
具体来说,熟料溶出二次反应研究的意义在于:1. 实现氧化铝产品的精细化生产,提高产品质量和稳定性。
2. 降低生产成本,提高生产效率和经济效益。
3. 推动氧化铝产业技术升级,提高产品附加值和市场竞争力。
高浓度粗液制备技术研究的意义在于:1. 提高产品的产量和质量。
2. 降低产品生产的能耗和环境负荷。
3. 探索新的氧化铝生产技术,促进产业创新和发展。
三、研究内容和方法本研究的内容主要包括:1. 熟料溶出二次反应机理和影响因素的研究。
2. 熟料溶液的浓缩、离心等处理工艺的优化。
3. 高浓度粗液的制备方法的研究和优化。
研究方法主要包括文献调研、实验研究和数值模拟等。
通过分析熟料溶出反应过程中各项参数的变化规律和相互关系,建立反应模型并进行计算机模拟和优化,探究最优化条件和操作参数。
同时,将实验室研究成果应用于氧化铝生产实际过程中,通过对实际生产数据的分析和对比,验证模型和方法的可行性和效果。
四、预期结果和创新点本研究预期能够:1. 深入了解氧化铝生产中熟料溶出机制和影响因素,探索最优化条件和操作参数。
溶出工序矿石溶出效果影响因素分析

溶出工序矿石溶出效果影响因素分析作者:韩涛来源:《决策探索·收藏天下(中旬刊)》 2019年第4期摘要:溶出工序是氧化铝生产的核心环节,对赤泥沉降分离、种分分解率、氧化铝的回收率、碱耗等工艺技术经济指标将产生直接影响,决定着氧化铝生产成本。
文章主要对矿石溶出效果的主要影响因素进行分析讨论,同时针对生产系统提出了措施和建议,以期对生产进行最大的优化,获得更好的经济效益。
关键词:拜耳法溶出系统;管道化;压煮器;溶出工序;一水硬铝石一、概述拜耳法生产氧化铝最重要的工序之一就是溶出,而其目的在于将铝土矿中的氧化铝水合物溶解成铝酸钠溶液。
可以知道,溶出效果的好坏会直接影响拜耳法生产氧化铝的技术经济指标。
目前,铝土矿资源紧缺,国内可用铝土矿质量逐渐下降,对溶出的安全生产造成了前所未有的挑战,也导致溶出生产能耗升高。
本文从义翔铝业有限公司生产实践出发,对高压溶出生产过程的影响因素做相关论述。
二、溶出工序现状义翔铝业有限公司目前有10万吨线和40万吨线两套溶出系统。
1 0万吨线采用的是高压蒸汽管道化停留罐溶出技术,是在以前的熔盐管道化的基础上改造而来;40万吨线采用的是单管预热一压煮器溶出技术。
三、生产影响因素分析(一)矿石溶出性能的影响铝土矿的溶出性能指溶出矿石中Al203的难易程度。
氧化铝的溶出过程,从本质上来讲,实际是对矿石品格的破坏过程。
在拜耳法溶出过程中,氧化铝水合物是因OH-离子进入而遭到破坏的。
致密的铝土矿几乎没有空隙和裂缝,比起疏松多孔的铝土矿来说,溶出性能差得多。
目前义翔铝业有限公司使用的矿石为典型的河南一水硬铝石难溶矿石,其中所含的伊利石为其主要含硅矿物,这种矿石结晶致密,在生产上的表现为原料磨工作效率下降,单位时间内的下矿量减少,同时预脱硅槽矿浆细度超标,由于氧化铝矿石与溶液的接触条件越差,致使溶出效果变差。
在实际生产中只有保证较细的矿石粒度、高循环母液苛性碱浓度和较高的溶出温度,才能保证矿石的溶出率。
氧化铝生产溶出技术工艺简介演示
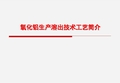
六、 氧化铝生产技术展望
基础理论研究 重点:为进一步简化流程、提高效率、降低能耗、 优化指标提供理论支持和技术支撑 1.氧化铝颗粒形貌、结构的变化规律与其物理性能的关 系研究 2.铝酸钠溶液的结构与化学的研究 3.生产过程热力学、动力学和反应工程学的研究 4.化学添加剂防垢技术与机理的研究 5.氧化铝生产短流程基础理论研究
四、 溶出区域设备介绍
高压溶出区域效果图
四、 溶出区域设备介绍
溶出高压进料隔膜泵
四、 溶出区域设备介绍
四、 溶出区域设备介绍
溶出套管
四、 溶出区域设备介绍
溶出预热加热套管 单套管 三套管
四、 溶出区域设备介绍
闪蒸槽(自蒸发器)
四、 溶出区域设备介绍
闪蒸槽(自蒸发器)
三、影响溶出工艺的主要因素
含铁矿物的危害
生产难以滤除的微小氧化铁水合物颗粒,进入成品氢 氧化铝之后影响质量。 生产大量沉降性能很差的赤泥。 以类质同晶形态进入针铁矿中的Al3+,降低矿石Al2O3 的提取率。
含钛矿物的危害
钛酸钠在铝矿物表面形成一层致密的保护膜,隔绝其 与溶液的接触。 生产钛酸钠造成苛性碱损失,细小钛酸钠会生产胶体, 恶化赤泥沉降。
一水硬铝石型
三水铝石—一水软铝石型 一水软铝石—一水硬铝石型
258~280
170~210 258~280
4.8~6.5
0.7~1.9 4.8~6.5
一、氧化铝生产溶出工艺现状
拜耳法溶出技术 大多采用间接加热强化溶出技术
单管预热—压煮器溶出技术 管道化溶出技术 管道间接加热—停留罐溶出技术 双流法溶出技术
一、氧化铝生产溶出工艺现状
铝土矿的分类 一水硬铝石型矿石 一水软铝石型矿石 三水型铝土矿 混合型铝土矿 我国铝土矿大多为一水硬铝石型铝土矿,具有高铝、 高硅、低铁、高硫等特点,其中一水硬铝石占98.46%
影响氧化铝配料的主要因素及控制措施

精 准 配料 进行 了阐述 。
关键 词 : 氧 化铝 ; 配料 中 图分 类号 : T F 8 2 1 文献 标 识码 : A 文章 编 号 : 1 1 — 5 O O 4 ( 2 0 1 7) 1 1 一 O 0 9 8 — 2
1 前言
在拜耳 法氧化铝 生产 中 ,需要准确 调配铝 矿石 、循环 母 液和 石灰 的比例 ,以期获得较 好的溶 出效果和 更高 的产量 ; 由于生产 的复杂性 ,实际生产操作中是以溶出 R p值 ( 溶液中 A1 O 。 与N a , O 的浓 度比 ) 作 为配料的结果 ,以结果反过来指 导配料的调整 , 一般要求控制在 1 . 1 4至 1 . 2 O, 并尽量保持稳定 、 减 少波动 ;但是 ,由于物料成 分波动 、设备可 靠性差和 溶出 条件不同 ,对配料结果都会产生影响 ,需要采取相应的措施 。
2 . 6 磨 机 开 、停 车 的 影 响
磨机开车前需要先确认中间泵、旋流器等流程畅通之后才
下矿 、下灰 ,这造成流程多进了母液 ,容易造成配料偏低 ,可 以先保持低流量母液运行 2 O 至3 0分钟之后再调整至正常流量, 通过矿浆槽和溶出前槽的容量缓冲来消除波动 。
2. 7 磨机 系统泄漏和检修的影 响 由于磨 机进料端 、出料端容 易产生漏 料 ,这一 部分的物
度级未达标时 ,称为细 度 “ 跑粗”。当发生严重细度跑 粗时 , 原 矿浆 中的矿石 粒度较大 ,多数 沉在矿浆 槽底部 ,进入溶 出 系统的料 浆多数是 循环母液 ,此 时进料密 度仪的数 据会 出现
堆场过小和定点布料 、短路 应急拉矿等现象 。 铝矿石 的含水量 也是 影响配料 的原 因 。特 别是 在南方 , 由于雨水 量较大 ,矿 石含水 量的增 加 ,造成磨 机有效 下旷量 偏少 ,进而降低 了溶出 R p值 。 2 . 2 循环 母液Rp 、Nk 浓度 波动 循环母液 Rp值和 NR浓度 ( 溶液中 Na , O 的浓度 ) 对配 料的影响也是比较大的 ,根据经验 ,循环母液 Rp升 高 0 . 0 1 , 则溶 出 R ! o也 随之上 升 0 . O 1 ;循环 母液 Nk浓 度升高 3 g / 1 至 5 g / 1 , 则溶 出 R p下降 0 . O 1 。 所以, 要关注循环 母液浓度的变化 , 及时调整 母液配入量 ;另外 ,蒸发工序要注意补碱的均衡 I 生, 补碱流量波动不可太大 。
氧化铝陶瓷烧结常见问题

氧化铝陶瓷烧结常见问题
氧化铝陶瓷烧结过程中可能会遇到的问题包括:
1. 烧结温度高:由于氧化铝的熔点高达2020℃,因此其烧结难度极大。
降低烧结温度是氧化铝陶瓷行业所关心和必需解决的问题。
2. 晶粒尺寸控制:烧结温度对晶粒生长的影响较大,而烧结时间与烧结压力的影响相对来说就比较小一些。
3. 颜色质量问题:在氧化铝陶瓷烧成后,可能会出现瓷件表面有斑点,如黑点、棕点、红点;瓷件表面产生斑块,如暗斑(阴斑),黑色云斑、亮斑等;瓷件有色差现象,如整体发黄或发灰等问题。
解决这些问题的方法包括采用热压烧结技术,即在烧结的同时施加一定的压力,使得原子的扩散速率增大,从而提高了烧结驱动力,使得烧结过程所需的时间大大减短。
此外,还可以通过获得分散均匀、无团聚,并具有良好烧结活性的超细粉体以降低陶瓷的烧结温度。
工艺流程优化在氧化铝溶出中的应用

工艺流程优化在氧化铝溶出中的应用摘要:氧化铝的制备程序繁琐,涉及工序较多,本文主要针对溶出工序提出了优化措施,阐述了氧化铝是如何制得。
氧化铝溶出方面存在很多待解决问题,所以选择两个方面的流程优化进行叙述,确保溶出高效率运行和成本的降低。
为以后其它方面的优化做了铺垫。
关键词:现状;溶出工序;优化内容氧化铝的制备工序有很多,所以整体会比较复杂。
它的制备方法也有很多种,比如碱法等其他方式,碱法是现在很多企业普遍使用的。
根据它的自身特性,它又被成为拜耳法。
用它生产氧化铝,可以使用铝矿石与碱发生反应,因为铝矿石中含有氧化铝,这样两者反应可制得铝酸钠溶液,剩余不和碱反应或性质稳定的杂质则作为残渣处理。
拜耳法制备氧化铝要经过多道工序,其中最重要的一步就是溶出,它也包括多个步骤。
这一步骤旨在能够把氧化铝转变为铝酸钠。
一、发展现状现在铝行业的发展前景非常的不乐观,因为制作工序所需原材料的价格不断上涨,而且还不见有下降的趋势,所以各个企业的发展都出现了淡季的情况,向前发展是越来越困难。
既然原材料的价格不能改变,那么就要在工序上降低成本,所以如何在工序过程中降低企业的总体成本,并且不改变工作的效果,就成为了企业发展的首要任务。
相关的企业现在已经通过各个方面的努力,终于找到了优化方法。
在预脱硅循环母液流程方面,既能减少了企业的成本,更加缩短了员工的工作时间,同时还能降低各种能耗比;还有在溶出机组压缩器填充方式上的改变,它通过把管道分为两段,同时进行填充,既加快了填充的速度,又加快了溶出速率。
这两种方式的优化,为铝行业的发展提供了充分的条件。
二、溶出工序2.1溶出工序的影响因素对溶出的影响因素有很多。
例如,温度,搅拌强度和循环母液浓度等。
溶出包括高温溶出和低温溶出,当升高一定的温度时,铝矿石中的氧化铝能够与碱更好的反应,加快氧化铝的分解速度,溶液中的分子变得不再稳定,这时再使用浓度比较低的母浓液就可以得到溶出液。
由于母液中含有氧化钠溶液,溶出液和它的浓度有一定的差距,所以大大的提高了碱的使用率,因此温度对溶出的影响是非常大的。
氧化铝生产标准试题(附答案)

一、选择题:1.氧化铝的分子式为 C 。
A、Al (OH)3B、Na2OC、Al2O3D、Na2O〃Al2O32.氧化铝是 C 。
A、酸性氧化物B、碱性氧化物C、两性氧化物D、盐类化合物3.氧化铝的同素异构体中常见的是 A C 。
A、α—Al2O3B、β—Al2O3C、γ—Al2O3D、δ—Al2O34. A 是Al (OH)3在较高温度下焙烧的产物, C 是Al (OH)3在较低温度下焙烧的产物。
A、α—Al2O3B、β—Al2O3C、γ—Al2O3D、δ—Al2O35.三水铝石的分子式为 A B 。
A、Al (OH)3B、Al2O3〃3H2OC、γ—AlOOHD、γ—Al2O3〃H2O6.一水软铝石的分子式为 A B 。
A、γ—AlOOHB、γ—Al2O3〃H2OC、α—AlOOHD、α—Al2O3〃H2O7.一水硬铝石的分子式为 C D 。
A、γ—AlOOHB、γ—Al2O3〃H2OC、α—AlOOHD、α—Al2O3〃H2O8.氧化铝水合物在无机酸和碱性溶液中,溶解性最好的是 A ,溶解性最差的是 C 。
A、三水铝石 B、一水软铝石 C、一水硬铝石 D、刚玉9. D 是氧化铝生产最主要的矿石资源。
A、刚玉B、明矾石C、霞石D、铝土矿10.铝土矿的类型有 A B C D 。
A、三水铝石型B、一水软铝石型C、一水硬铝石型D、混合型11.铝土矿质量的好坏可依据哪项进行评价 A B C 。
A、氧化铝含量B、A/SC、矿石的类型D、硬度12.对我国铝土矿质量特点的描述,哪项是正确的 A B C D 。
A、铝硅比较低B、高硅C、低铁D、一水硬铝石型13.铝属于 D 。
A、重金属B、贵金属C、稀有金属D、轻金属14.烧结法和拜耳法都属于 B 。
A、酸法B、碱法C、酸碱联合法D、热法15.目前,工业上几乎全部是采用 B 法生产AO。
A、酸法B、碱法C、酸碱联合法D、热法16.目前世界上95%以上的Al2O3均是用 A 法生产的。
碳酸钠浓度对熟料氧化铝净溶出率的影响及控制

Na2O
18117 2112 2143 2134
K2O 3145
Na2Os 1107
ηA
91199 88182 86173 86130
ηN
9617 94149 93153 94142
表 2 溶液成分
成
项目
Na2O T 分
溶出液 ,g/ l 100117
碳分母液 ,g/ l 16717
赤泥洗液 ,g/ l 42163
务年限 。 缺点 :电铲工作线较短
收稿日期 :2000 - 05 - 09
经过几年的摸索和实践 ,由纵向开采改为横向 开采 ,不仅创造了较好的经济效益 ,而且也创造了可 观的社会效益 ,做到了矿产资源的合理开发 ,对人类 的生存和发展有着深远的现实意义 。
参考文献 :
〔1〕宜阳石灰石矿地质勘探报告〔R〕. 1976. 〔2〕焦玉书. 金属矿山露天开采〔M〕. 北京 :冶金工业出版社 ,1989. 〔3〕采矿设计手册〔Z〕. 北京 :中国建筑工业出版社 ,1987.
43 %、33 %和 20 %。说明大量的 Al2O3 是成为水化
石榴石损失的〔1〕。
从表 1 中 Al2O3 和 Na2O 的 净 溶 出 率 分 析 , Al2O3 的净溶出率比入磨熟料标溶降低 5169 个百 分点 ,而 Na2O 的净溶出率比起入磨熟料ηN标 仅降 低 2128 个百分点 。而且赤泥在洗涤过程中 , Na2O 的溶出率不但没有降低 ,反而增加了 0189 个百分 点 。进一步证明了 C2S 主要是以水化石榴石形态进 入赤泥 ,含水铝硅酸钠形态进入赤泥的量比较少 。
钙形式占的比例较大 ,一般为 40 %左右 ,原硅酸钙
在溶出过程中比较活跃 ,它是造成 Al2O3 损失的主
烧结法熟料溶出工艺研究

doi:10.3969/j.issn.1007-7545.2013.01.008烧结法熟料溶出工艺研究程来星(黄石职业技术学院,湖北黄石43500)摘要:通过正交试验与单因素试验考察了溶出时间、液固比、溶出温度及调整液中碳酸钠浓度等因素对烧结法熟料溶出过程的影响,并确定了影响因素的主次关系。
结果表明,影响因素主次关系依次是温度、时间、液固比、碳酸钠浓度,在下述条件下,氧化铝溶出率达到91.26%:碳酸钠浓度20 g/L、液固比5∶1、溶出时间30 min、溶出温度80 ℃。
关键词:氧化铝;烧结法;熟料溶出;正交试验中图分类号:TF821 文献标识码:A 文章编号:1007-7545(2013)01-0000-00Study on Sintering Clinker Digestion ProcessCHENG Lai-xing(Huangshi Polytechnic College, Huangshi 435000, Hubei, China)Abstract:The effects of temperature, time, ratio of liquid to solid(L/S), and concentration of sodium carbonate in correction liquor in clinker digestion process were investigated with orthogonal experiment and single factor experiment, and the four factors were determined based on influence momentum. The results show that the four factors in sequence from high to low are temperature, time, L/S, concentration of sodium carbonate. The leaching rate of alumina is 91.26% under the conditions including digestion temperature of 80 ℃, dissolving time of 30 min, L/S of 5∶1, and concentration of sodium carbonate of 20 g/L.Key words:alumina; sintering process; digestion of clinker; orthogonal experiment烧结法生产氧化铝工艺中由于熟料溶出时发生二次反应[1-2],不仅使氧化铝溶出率降低,还会影响其他工艺过程的正常运行,从而直接影响氧化铝生产技术经济指标[3]。
碳酸钠在烧结法熟料溶出过程中作用与浓度控制

通过以上论述我们可知 ,溶出液中控制 1 ,试验共分四组 ,其结果见表 1 。
表 1 不同碳碱浓度下的氧化铝溶出率η( %)
试验
调整液成分液
第一组
序号 NT
Al2O3 Na2OC ηA
ηN
第二组
ηA
ηN
第三组
ηA
ηN
第四组
ηA
ηN
1
59. 10 55. 92 13. 60 93. 29 96. 50 91. 89 94. 24 92. 93 96. 78 94. 78 97. 47
我们不考虑调整液中 Al2O3 浓度的变化 对溶出率的影响 ,只考虑 Na2CO3 浓度的不
·34 ·
矿产保护与利用 2000 年
同对对溶出率的影响 ,我们取每组最大的三 项 Al2O3 溶出率 , 按出现的机率统计如下 : (1) 碳酸钠浓度为 35. 20g/ l 的出现机率为 100 % ; (2) 碳酸钠浓度为 32. 80g/ l 的出现机 率为 75 % ; (3) 碳酸钠浓度为 20. 15g/ l 的出 现机率为 50 % ; (4) 碳酸钠浓度为 23. 20g/ l , 29. 45g/ l ,37. 80g/ l 的出现机率分别为 20 %。 从统计的结果上看 ,调整液中的碳酸钠浓度 控制在 30~35g/ l 间 ,氧化铝的溶出率较高 , 且出现的机率较高 。
2. 2 生产跟踪试验
表 2 碳碱全部入磨和部分入磨 Al2O3 溶出率η对比( %)
日期ηA标
全部入磨 (1 # ηN标 ηA初
磨) ηN初
部分入磨 (2 # 磨) ηA标 ηN标 ηA初 ηN初
1 94. 56 97. 64 93. 49 94. 47 94. 97 97. 52 91. 46 95. 03
优化烧结法生产氧化铝脱硅过程的措施
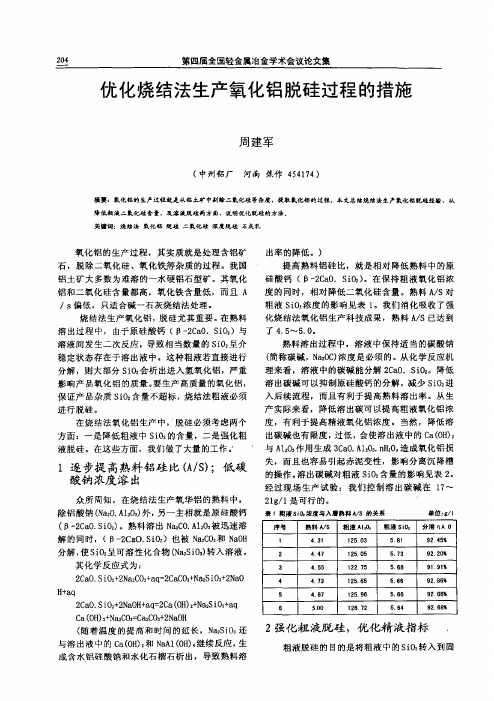
第四届全国轻金属冶金学术会议论文集
优化烧结法生产氧化铝脱硅过程的措施
周建军
(中州铝厂河南焦作454174)
摘要:氧化铝的生产过程就是从拓土矿中驯赊二氯化硅等杂质.提取氧化拓的过程.本丈总结烧蛄法生产氧化招脱硅经验,从 降低粗液二氧化硅含量,置溶液脱硅两方面,说明优化脱硅的方法. 关键词:烧蛄法氧化拓脱硅二氧化硅深度脱硅石灰乳
氧化铝的生产过程,其实质就是处理含铝矿 石,脱除二氧化硅、氧化铁筹杂质的过程。我国 铝土矿大多数为难溶的一水硬铝石型矿。其氧化 铝和二氧化硅含量都高,氧化铁含量低,而且A /S偏低,只适合碱一石灰烧结法处理。
烧结法生产氧化铝,脱硅尤其重要。在熟料 溶出过程中,由于原硅酸钙(B一2CaO.SiOz)与 溶液问发生二次反应,导致相当数量的SiO。呈介 稳定状态存在于溶出液中。这种粗液若直接进行 分解,则大部分siO。会析出进入氢氧化铝,严重 影响产品氧化铝的质量。要生产高质量的氧化铝, 保证产品杂质SiO。含量不超标,烧结法粗液必须 进行脱硅。
失,而且也容易引起赤泥变性,影响分离沉降槽
的操作。溶出碳碱对粗液SiOz含量的影响见表2。
经过现场生产试验:我们控制溶出碳碱在17~
219/1是可行的。
衰f相液si ol浓度与^磨熟料^/s的关系
单位:∥
序号
热料k/s 辊液hI舢 粗液Si0, 分溶nA 0
1
4 3l
125 03
5 81
92 45X
III,0
Fe,O,
Nk
渣体成分g,l
^j,o’
Nc
Si of
l含量(x)
52 7
1B 2
1 7e
0 32
0 t2
108 5
氧化铝溶出
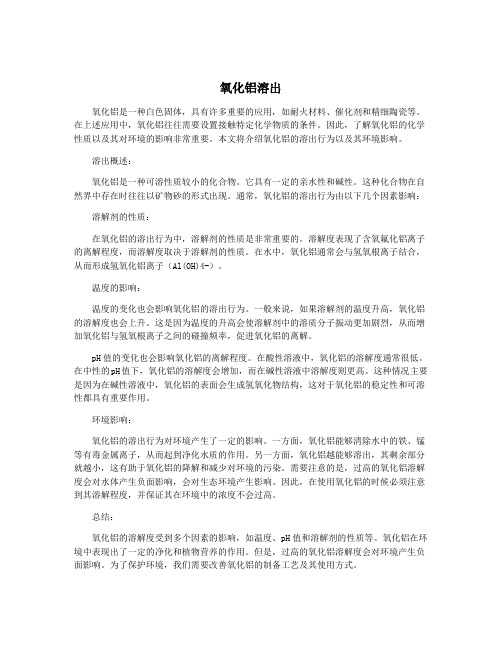
氧化铝溶出氧化铝是一种白色固体,具有许多重要的应用,如耐火材料、催化剂和精细陶瓷等。
在上述应用中,氧化铝往往需要设置接触特定化学物质的条件。
因此,了解氧化铝的化学性质以及其对环境的影响非常重要。
本文将介绍氧化铝的溶出行为以及其环境影响。
溶出概述:氧化铝是一种可溶性质较小的化合物。
它具有一定的亲水性和碱性。
这种化合物在自然界中存在时往往以矿物砂的形式出现。
通常,氧化铝的溶出行为由以下几个因素影响:溶解剂的性质:在氧化铝的溶出行为中,溶解剂的性质是非常重要的。
溶解度表现了含氧氟化铝离子的离解程度,而溶解度取决于溶解剂的性质。
在水中,氧化铝通常会与氢氧根离子结合,从而形成氢氧化铝离子(Al(OH)4-)。
温度的影响:温度的变化也会影响氧化铝的溶出行为。
一般来说,如果溶解剂的温度升高,氧化铝的溶解度也会上升。
这是因为温度的升高会使溶解剂中的溶质分子振动更加剧烈,从而增加氧化铝与氢氧根离子之间的碰撞频率,促进氧化铝的离解。
pH值的变化也会影响氧化铝的离解程度。
在酸性溶液中,氧化铝的溶解度通常很低。
在中性的pH值下,氧化铝的溶解度会增加,而在碱性溶液中溶解度则更高。
这种情况主要是因为在碱性溶液中,氧化铝的表面会生成氢氧化物结构,这对于氧化铝的稳定性和可溶性都具有重要作用。
环境影响:氧化铝的溶出行为对环境产生了一定的影响。
一方面,氧化铝能够清除水中的铁、锰等有毒金属离子,从而起到净化水质的作用。
另一方面,氧化铝越能够溶出,其剩余部分就越小,这有助于氧化铝的降解和减少对环境的污染。
需要注意的是,过高的氧化铝溶解度会对水体产生负面影响,会对生态环境产生影响。
因此,在使用氧化铝的时候必须注意到其溶解程度,并保证其在环境中的浓度不会过高。
总结:氧化铝的溶解度受到多个因素的影响,如温度、pH值和溶解剂的性质等。
氧化铝在环境中表现出了一定的净化和植物营养的作用。
但是,过高的氧化铝溶解度会对环境产生负面影响。
为了保护环境,我们需要改善氧化铝的制备工艺及其使用方式。
氧化铝生产过程高压溶出部分

氧化铝生产过程具有流程长、工序多、连续性强的特点,这些特点使氧化铝生产过程的控制水平落后其它行业的控制水平,我国的铝矿石98%以上是一水硬铝石,这种矿石的硬度大,在生产过程中对设备的磨损严重、结疤严重,这些因素增加了生产过程控制的难度,使得我国的氧化铝生产过程控制水平落后于世界其它国家。
生产过程控制是企业技术进步和文明生产的重要组成部分。
目前氧化铝生产过程控制水平还不高,有许多难题亟待解决,对氧化铝生产过程控制进行研究是非常必要的,通过对氧化铝生产过程控制的研究,改变氧化铝生产条件,优化氧化铝生产的技术经济指标,降低氧化铝生产成本,提高我国氧化铝在国际市场上的竞争能力。
氧化铝生产方法大致可分为碱法、酸法、酸碱联合法和热法。
但在工业上得到应用的只有碱法。
碱法生产氧化铝,是用碱(NaOH或Na2CO3)来处理铝矿石,使矿石中的氧化铝转变成铝酸钠溶液。
矿石中铁、钛等杂质和绝大部分的硅则成为不溶解的化合物,将不溶解的残渣(赤泥)于溶液分离,经洗涤后弃去或可行综合利用。
从净化后纯净的铝酸钠溶液(精液)分解析出氢氧化铝,分解母液经蒸发后用于溶出下批铝土矿。
碱法生产氧化铝又分拜尔法、烧结法和拜尔——烧结联合法等多种流程,而全世界生产的氧化铝和氢氧化铝,90%以上是用拜尔法生产的,氧化铝的基本工艺流程如图所示。
从拜尔法生产的基本工艺流程,我们可以把整个生产过程大致分为如下主要的生产工序:原矿浆制备、高压溶出、溶出矿浆的稀释及赤泥的分离和洗涤,晶种分解,氢氧化铝分级与洗涤,氢氧化铝焙烧、母液蒸发及苏打苛化等,本课题只对其中四大关键工序原矿浆制备(即配料)、高压溶出、精种分解、母液蒸发生产过程的控制进行研究。
一、对国外研究现状分析随着计算机和自动化技术的飞速发展,在各个生产过程中已越过广泛地应用计算机实现自动化。
在氧化铝生产过程中,应用先进的计算机技术,实现全过程的自动检测,自动控制和优化调度管理,已是发展的趋势。
- 1、下载文档前请自行甄别文档内容的完整性,平台不提供额外的编辑、内容补充、找答案等附加服务。
- 2、"仅部分预览"的文档,不可在线预览部分如存在完整性等问题,可反馈申请退款(可完整预览的文档不适用该条件!)。
- 3、如文档侵犯您的权益,请联系客服反馈,我们会尽快为您处理(人工客服工作时间:9:00-18:30)。
影响烧结法生产氧化铝的溶出因素
作者:丁亚茹
来源:《中国新技术新产品》2011年第14期
摘要:我国铝土矿的质量比较差。
其中加工困难、耗能大的一水硬铝石型矿石占全国总储量的98%以上。
其中铝硅比大于7的只占总矿藏的21.8%,而铝硅比小于7的矿石则适宜用烧结法进行生产。
我国生产氧化铝主要是采用拜耳-烧结混联法。
此种方法主要是采用拜耳法的赤泥作为烧结法的原料进行烧结生产。
近年,内蒙古地区粉煤灰中还有大量的氧化铝,经证实可以大量的生产氧化铝。
提取粉煤灰中的氧化铝的主要方法便是烧结法。
烧结法中的氧化铝的提取一定程度上取决于溶出过程。
溶出过程中,二次反应损失是造成溶出率降低的主要因素,这篇文章主要是研究如何减少二次反应的发生,提高溶出率。
关键词:拜耳法;烧结法;溶出率;二次反应损失;铝硅比;钙比;碱比;苛性碱
中图分类号:TQ424.27文献标识码:A
氧化铝生产的方法包括:酸法、碱法、酸碱联合法,碱法又可以分为拜耳法、烧结法、拜耳-烧结联合法。
通常采用何种方法要根据矿藏的特点而定。
我国铝土矿的质量比较差。
其中加工困难、耗能大的一水硬铝石型矿石占全国总储量的98%以上。
其中铝硅比大于7的只占总矿藏的21.8%,而铝硅比小于7的矿石则适宜用烧结法进行生产。
我国生产氧化铝主要是采用拜耳-烧结混联法。
此种方法主要是采用拜耳法的赤泥作为烧结法的原料进行烧结生产。
近年,内蒙古地区粉煤灰中还有大量的氧化铝,经证实可以大量的生产氧化铝。
提取粉煤灰中的氧化铝的主要方法便是烧结法。
烧结法中的氧化铝的提取一定程度上取决于溶出过程。
烧结法的主要原理:
由碱、石灰和铝土矿组成的炉料经过烧结,使炉料中的氧化铝转变为易溶的铝酸钠,氧化铁转变为易水解的铁酸钠,氧化硅转变为不溶的原硅酸钙。
由这三种化合物组成的熟料在用稀碱溶液溶出时,固相铝酸钠溶于溶液,铁酸钠水解为氧化铁水合物沉淀除去,原硅酸钙不与水反应全部进入赤泥。
在溶出过程中的影响溶出率的因素主要是因为发生二次反应损失。
二次反应如下:[1]
2CaO·Si02+2NaOH+aq=Na2SiO3+2Ca(OH)2+aq
3Ca(OH)2+2NaAI(OH)4+aq=3CaO·Al2O3·6H2O(↓)+2NaOH+aq
3CaO·A12O3·6H2O+xNa2SiO3+aq=3CaO·A12O3·xSiO2·(6-2x)H2O+2xNaOH+aq 在生产过程中,二次反应受配方和反应条件的影响。
1 配方的影响[2]
配方的影响主要取决于:铝硅比、碱比、钙比、生料加煤。
1.1 铝硅比
如果熟料铝硅比低,那么熟料中原硅酸钙含量高,因而在溶出时与苛性碱的二次反应也比较强烈,使二次反应损失增大,氧化铝和氧化钠的净溶出率降低。
1.2 碱比和
高碱配方的熟料,氧化钠溶出率低,并且还会引起溶出液苛性比值升高,增加二次反应损失。
低碱配方的熟料,使生料中的氧化钠不足以使全部氧化铝和氧化铁变成铝酸钠和铁酸钠。
1.3 钙比
高钙配方的熟料,生成铝酸钙的可能性大,造成氧化铝损失也大;同时苛化反应增加,会使溶出液的苛性比值升高,增加二次反应损失;熟料中游离氧化钙多,会使赤泥溶剂化,造成沉降性能恶化,造成熟料溶出率降低。
低钙配方,生料中氧化钙也不足以使全部二氧化硅变为原硅酸钙,造成氧化铝、氧化钠的一次化学损失增加,标准溶出率降低。
1.4 生料加煤
生料加煤除能改善窑内的热工制度,提高窑的产能以及脱硫等许多优点之外,,还能使熟料孔隙度较大,质量较好,可以改善赤泥沉降性,抑制二次反应,提高溶出率。
2 溶出条件的影响
2.1温度
温度高时,主副化学反应的速度都会加快。
温度越高,二次反应越多,净溶出率越低。
但温度如果过低,溶出不完全,溶液黏度增加使赤泥沉降性能会变坏,反而延长了赤泥与溶液的接触时间,同样造成氧化铝和氧化钠的损失。
2.2 Na2Ok浓度
溶出液Na2Ok浓度越高,二次反应就会越多,二次反应损失越大。
但Na2Ok浓度取决于氧化铝浓度和苛性比值,当氧化铝浓度给定的情况下,苛性比值越小,则Na2Ok浓度越低。
但Na20k浓度如果过低,溶液就会发生分解。
2.3碳酸钠浓度
(1)碳酸钠会分解原硅酸钙生成铝硅酸钠造成氧化铝和氧化钠的损失。
(2)碳酸钠又会与石
灰乳反应生成CaCO3,从而抑制二次反应,并且还能分解二次反应产物铝硅酸钙,降低氧化
铝的损失。
(3)碳酸钠能够起到抑制赤泥膨胀的作用。
2.4 溶出液固比与赤泥含量
入磨液固比越小,赤泥含量就会越高,固体数量越多,固体表面积越大,二次反应损失也就越大,从而降低了氧化铝和氧化钠的溶出率。
2.5 溶出时间溶出时间
是指从熟料开始入磨直至溶液与赤泥分离所需要的时间,即溶液与赤泥接触的时间。
溶出时间越长,二次反应损失越大。
所以生产上要尽可能缩短溶出时间。
2.6熟料的磨细度
溶出反应与二次反应都是液相与固相之间的反应,固相的表面状态对溶出过程影响很大。
综上所述,在氧化铝溶出过程中,引起溶出率降低的主要因为二次方应损失引起。
那么降低二次反应即可提高溶出率。
那么降低二次反应的主要方法有:
(1)采用低苛性比值溶出,苛性比值控制在1.25左右,减少溶液中游离的苛性碱浓度;(2)控制一定量的Na2CO3质量浓度,Na20c质量浓度控制在22~27g/L;(3)采用二段磨溶出流程;(4)在不显著影响赤泥沉降速度的前提下,采用偏低的溶出温度,控制温度不超过95℃;(5)快速分离赤泥,减少溶液与赤泥的接触时间和面积。
参考文献
[1]杨重愚主编.氧化铝生产工艺学.冶金工业出版社.1993年10月第二版.230-232.
[2]王捷编.氧化铝生产工艺.冶金工业出版社.2006年6月第一版.109-113.。