胀形 翻边 缩口(二)
第5章胀形翻边缩口成型及工艺
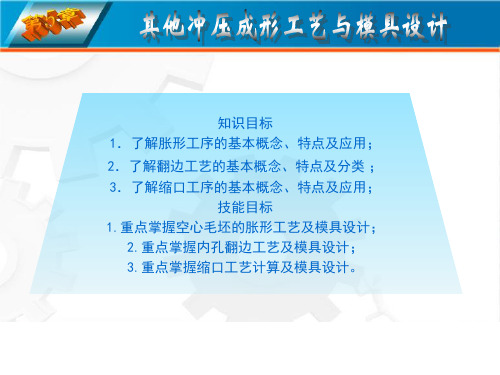
胀形工艺与模具设计
底部起伏 成形计算
侧壁胀形 计算
总胀形力
5.1
5.1.4 胀形模设计实例
胀形工艺与模具设计
1—下模座; 2、11—螺钉; 3—压凹坑凸模; 4—压凹坑凹模; 5—胀形下模; 6—胀形上模; 7—聚氨酯橡胶; 8—拉杆; 9—上固定板; 10—上模; 12—模柄; 13—弹簧; 14—拉杆螺栓; 15—导柱; 16—导套 胀形模模具装配图
不同材料和厚度的平均缩口系数
m0
5.3
缩口成形工艺与模具设计
5.3.1 缩口成形特点与变形程度
不同模具结构的极限缩口系数
mmin
5.3
5.3.2 缩口工艺计算
缩口成形工艺与模具设计
缩口次数的计算公式:
m为缩口系数 m0为平均缩口系数
5.3
5.3.2 缩口工艺计算
缩口成形工艺与模具设计
斜口形式毛坯高度 :
胀形工艺与模具设计
d max k d0
极限胀形系数 Kmax 与工件切向伸长率 A 的关系为:
或
5.1
5.1.3 空心毛坯胀形
胀形工艺与模具设计
2)软模胀形力
1)刚性凸模胀形力
3)胀形毛坯尺寸
毛坯长度 L0:
5.1
5.1.4 胀形模设计实例
胀形工艺与模具设计
胀形零件
5.1
5.1.4 胀形模设计实例
修边余量
拉深的工艺性
基
本
概
念
变薄拉深
变薄拉深主要是在拉深过程中改变拉深件筒壁厚度,而毛坯的直 径变化很小的拉深方法 。
5.1
5.1.1 胀形的变形特点
胀形工艺与模具设计
5.1
5.1.2 平板毛坯的起伏成形
钣金与成型第5章 胀形与翻边
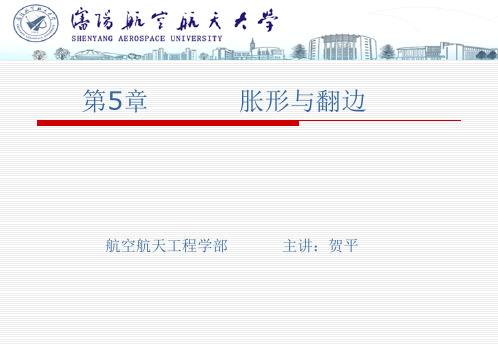
虽然胀形成形极限表示方法不同,但由于胀形区应变
性质相同,且破裂只与变形区应变情况有关,所以影响因 素基本相似。
影响胀形成形极限的材料因素主要是延伸率和应变硬化指
数。一般来讲,延伸率大,破裂前允许的变形程度大,成形极 限也大;应变硬化指数值大,应变硬化能力强,可促使应变分 布趋于均匀化,同时还能提高材料的局部应变能力,故成形极 限也大。
l' l e 2 n l' 0.8
5、 2
翻边
翻边:利用模具将工件的孔边缘翻成竖直
的边。
(图7-1)
一、圆孔翻边 1、圆孔翻边的变形特点(图7-2 ) 变形区应力状态为双向(径向、切向) 受拉的平面应力状态。
变形区的双向应力分布为: 1.155 s
1.155 s (1
极限胀形系数与毛坯切向的许用延 ' 伸率有关,即: dmax d0 p K p 1 d0
(3)张拉成形
特点:曲面变形量很小,破裂不是生产中的主要问题,
零件脱模后的曲面回弹,造成零件出现较大的形 状误差。
措施:工艺上:1)调整压边力;
2)使用拉深筋; 3)增大毛料尺寸等。 选材上:选用屈强比较小的板料成形零件。 张拉成形变形特点及应力应变状态图。
平板张拉成形
……
利用模具把板料上的孔缘或外缘翻成竖边的冲压加工方 法叫翻边。 按工艺特点,翻边分为: 内孔(圆孔或非圆孔)翻边 外缘翻边(内曲翻边、外曲翻边)
变薄翻边
……
按变形性质,翻边分为:
伸长类翻边
压缩类翻边
变薄翻边(属体积成形)
伸长类翻边的特点:
变形区材料切向受拉应力,切向产生伸长变形,导致厚度 减薄,容易发生破裂,如圆孔翻边、外缘的内曲翻边等。 压缩类翻边的特点: 变形区材料切向受压缩应力,切向产生压缩变形,导致厚 度增大,容易起皱,如外缘的外曲翻边。 非圆孔翻边经常是由伸长类翻边、压缩类翻边和弯曲组合 起来的复合成形。
胀形、缩口、翻边教案
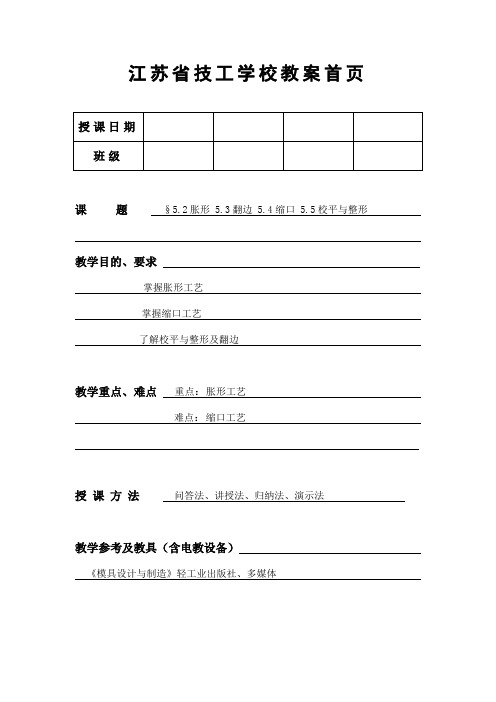
讲授法
5.5校平与整形
板书
10分
利用模具使坯料局部或整体产生不大的塑性变形,
了解
以消除平面度误差,提高制件形状及尺寸精度的冲压
成形方法。
校平和整形工序的工艺特点:
1)允许的变形量很小,坯料的形状与尺寸与制件非常
接近;
2)对模具的成形部分的精度要求比较高;
3)通常在专用的精压机进行校平和整形,若用机械
5.5.2整形
板书
弯曲回弹会使工件的弯曲角度改变;由于凹模圆
了解
角半径的限制,拉深或翻边的工件也不能达到较小的圆
角半径。利用模具使弯曲或拉深后的冲压件局部或整
体产生少量塑性变形以得到较准确的尺寸和形状,称为
整形。整形常在弯曲、拉深、成形工序之后。
四
小结
归纳法
1、冷挤压,胀形
3分
2、缩口
3、校平与整形
江苏省技工学校教案首页
授课日期
班级
课题§5.2胀形 5.3翻边 5.4缩口 5.5校平与整形
教学目的、要求
掌握胀形工艺
掌握缩口工艺
了解校平与整形及翻边
教学重点、难点重点:胀形工艺
难点:缩口工艺
授课方法问答法、讲授法、归纳法、演示法
教学参考及教具(含电教设备)
《模具设计与制造》轻工业出版社、多媒体
授课执行情况及分析
板书设计或授课提纲:
5.2胀形
1、定义
2、起伏成形
胀形主要有起伏成形和空心毛坯胀形两类。
5.3翻边
利用模具,将工件的孔边缘或外缘边缘翻成竖立直边的成形方法。
1、内孔翻边
1)变形特点
2)外缘翻边
2.分类
(1)外凸外缘翻边
29_里仁-胀形与翻边
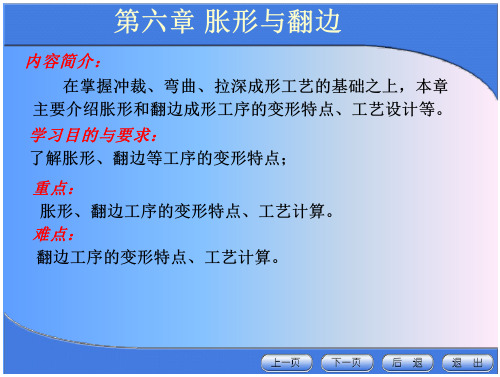
翻边高度:
极限翻边高度:
第六章 胀形与翻边
(2)拉深后再翻边 先拉深后翻边的高度h
翻边的极限高度:
预制孔直径:
拉深高度:
(3)翻边力的计算
用圆柱形平底凸模翻边: 用球形凸模:
第六章 胀形与翻边
三、变薄翻边 变薄翻边属于体积成形。翻边时,
凸凹模之间采用小间隙,凸模下方的 材料变形与圆孔翻边相似,但它们成 形为竖边后,将会在凸凹模的小间隙 之间受到挤压,进一步发生较大的塑 性变形,使厚度显著减薄,从而提高 翻边高度。
第六章 胀形与翻边
内容简介:
在掌握冲裁、弯曲、拉深成形工艺的基础之上,本章 主要介绍胀形和翻边成形工序的变形特点、工艺设计等。
学习目的与要求:
了解胀形、翻边等工序的变形特点;
重点:
胀形、翻边工序的变形特点、工艺计算。
难点:
翻边工序的变形特点、工艺计算。
第六章 胀形与翻边
本章目录
概述 第二节 胀形 第三节 翻边
(2)压凸包 凸包高度受材料限制,还与凸模形状及润滑状态有关。
第六章 胀形与翻边
起伏成形
第六章 胀形与翻边
深度较大的局部胀形法 a) 预成形 b)最后成形
第六章 胀形与翻边
第一节 胀形
(3)圆柱形空心毛坯胀形 圆柱形空心毛坯胀形:将圆柱形空心毛坯(管状或桶状)向
外扩张成曲面空心零件的冲压加工方法 a、胀形方法:刚性模具胀形、软模胀形、液体胀形 b、成形极限
第六章 胀形与翻边
概述
胀形:利用模具迫使板料在处于双向受拉的应力状态下发 生厚度减薄和表面积增大,以获取零件几何形状的冲压方 法。有刚模胀形、橡皮胀形和液压胀形等。
第五章胀形与翻边
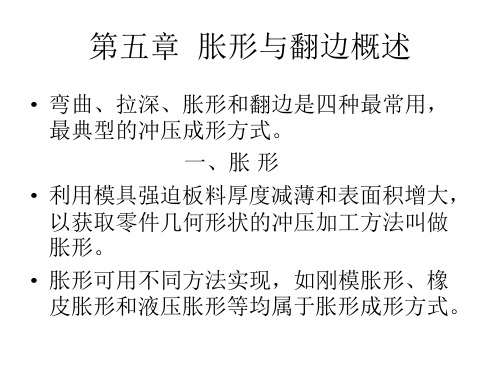
• 在圆孔翻边的中间阶 段,即凸模下面的材 料尚未完全转移到侧 面之前,如果停止变 形,就会得到右图所 示的成形方式,这种 成形方式叫做扩孔, 生产应用也很普遍。
第五章 胀形与翻边概述
• 弯曲、拉深、胀形和翻边是四种最常用, 最典型的冲压成形方式。 一、胀 形 • 利用模具强迫板料厚度减薄和表面积增大, 以获取零件几何形状的冲压加工方法叫做 胀形。 • 胀形可用不同方法实现,如刚模胀形、橡 皮胀形和液压胀形等均属于胀形成形方式。
• 右图是用球头凸模胀形平 板毛坯的示意图,这种胀 形方法可视为纯胀形。纯 胀形时,毛坯被带有拉深 筋的压边圈压死,变形区 限制在拉深筋以内的毛坯 中部,在凸模力作用下, 变形区大部分材料受双向 拉应力作用(忽略板厚方 向的应力),沿切向和径 向产生拉伸应变,使材料 厚度减薄,表面积增大, 并在凹模内形成一个凸包。
二.圆孔翻边
• 利用模具把板料上的孔缘或外缘翻成 竖边的冲压加工方法叫做翻边。 • 右图是圆孔翻边示意图。翻边时带有 圆孔的环形毛坯被压边圈压死,变形 区基本上限制在凹模圆角以内,并在 凸模轮廓的约束下受单向或毛坯中心的圆孔不断胀 大,凸模下面的材料向侧面转移,直 到完全贴靠凹模侧壁,形成直立的竖 边。
• 胀形成形极限以零件是否发生破裂来判别。 • 一般来讲,胀形破裂总是发生在材料厚度 减薄最大的部位,所以变形区的应变分布 是影响胀形成形极限的重要因素。 • 影响胀形成形极限的材料因素主要是延伸 率和应变硬化指数n。一般来讲,延伸率大, 破裂前允许的变形程度大,成形极限也大; n值大,应变硬化能力强,可促使应变分布 趋于均匀化,同时还能提高材料的局部应 变能力,故成形极限也大。
胀形与翻边
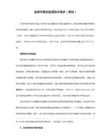
胀形常与其它方式的成形同时发生。
至变形结束 a)弯曲、局部胀形 胀形变形过程
b)胀形扩展
胀形和拉伸的区别:
胀形主要受ห้องสมุดไป่ตู้向拉力的作用,拉伸是压应力与 拉应力共同的结果。
它与拉深的分界点取决于毛坯尺寸,材料性能,模具 几何参数和压边力大小d/D0约在0.38~0.35之间
平板毛坯的起伏变形
起伏成形 : 平板毛坯的胀形又称起伏成形
变形程度:翻边前孔径d与翻边后孔径D的 比值 K=d/D K取决于变形程度,K值越小,变形程度越大
■翻边力的计算 采用平底凸模翻边:F=1.1∏(D-d)tReL 采用球头凸模翻边:
变薄翻边: 翻边时材料竖边变薄,是拉应力作用下材 料的自然变薄,是翻边的自然情况。 从变薄翻边的过程看出,变形程度不进局 定于翻遍系数,还决定与壁部的变薄系数。 用Kb表示: Kb=t后/t前 翻边参数如下图所示:
加强筋,花纹,图形及标记等)、圆柱空心毛坯胀 形及张拉成形(壶嘴,皮带轮,波纹管,各种接头) 等。
胀形的变形特点: 1)毛坯的塑性变形局限于一个固定的变形区范 围内,板料不向变形区外转移,也不从外部进入 变形区。 2)变形区材料受双向拉应力作用,沿径向和切 向产生伸长变形,板厚变薄,属伸长类变形,其 主要破坏形式是胀裂。 3)胀形时变形区材料由于受双向拉应力作用, 不存在压应力,而且拉应力沿厚度方向分布均匀, 因此不易失稳起皱,回弹小,尺寸精度高,表面 质量好。
P可近似计算:
P=1.15Rm2t/dmax Rm—材料抗拉强度 dmax—胀形后零件的最大直径
翻边
定义:利用模具将工序的孔边缘或外边缘 翻成竖直的直边,称为翻边。 翻边的分类:内孔翻边,变薄翻边和外缘 翻边。
冲压工艺学6-胀形与翻边讲解
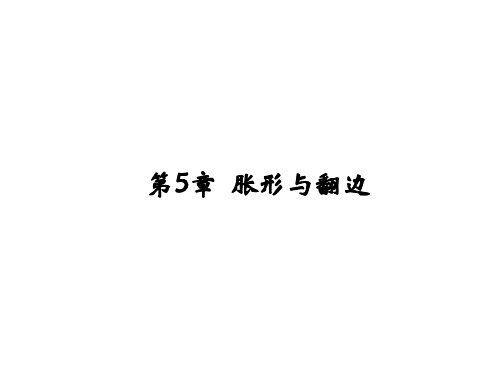
F KAt
2
2)圆柱形空心毛坯胀形力的计算 可按下式 计算。
F p A
胀形单位压力p可按下式计算。
2t p 1.15 z d max
5.2 翻边
利用模具把板料孔缘或外缘翻成竖边,或将 圆柱形空心毛坯口部翻出法兰的冲压工序。 翻边总是与弯曲变形同时发生。如图5-11所示, 根据翻边件形状及变形区应力应变状态的不 同,翻边可分为直线翻边、伸长类翻边、压 缩类翻边和复合翻边四种形式。直线翻边即 弯曲,压缩类翻边的本质与拉深相同。此外, 按翻边材料厚度变化情况,翻边还可分为普 通翻边与变薄翻边两类。
a)径向和厚度方向应变分布 b)切向和径向应变分布 图5-3 胀形件的应变分布和应变状态图
5)胀形变形服从材料的变形规律 当存在多种变形可能性时,实际的变形方式 使得载荷最小。毛坯的外径足够大,内孔较小 时,拉深变形阻力和扩孔、翻边变形阻力大于 胀形变形阻力时,变形性质由胀形决定。
图4-6
毛坯尺寸和工序类型的关系
图5-7 两道工序完成的凸形
(2)圆柱形空心毛坯的胀形 1)胀形方式 a.橡皮(或聚氨酯)凸模 胀形 该胀形方式如图5-8 所示。由于聚氨酯橡胶优 良的物理机械性能,用它 作工作介质的胀形得到愈 来愈广泛的应用。
图5-8 橡皮凸模胀形
b.分块式凸模胀形 如图5-9所示,采用刚性凸模, 凸模必须作成分块式,以便出模时由楔状心块 将其分开。
a)应力状态 b)应变状态 图5-2 变形区应力和应变状态
3)变形力—行程曲线 与拉深不同,胀形时变 形区是在不断扩大的。由于加工硬化,胀形变 形力-行程曲线是单调增曲线,产生破裂时胀 形力达到最大值。
4)应变和板厚的分 布 图5-3是平板毛 坯局部胀形时的应 变分布图。由图中 可见,变形区内径 向应变εr和切向应 变εθ全部大于零, 而厚度方向的应变 小于零,坯料变薄。
变形工序2汇总.
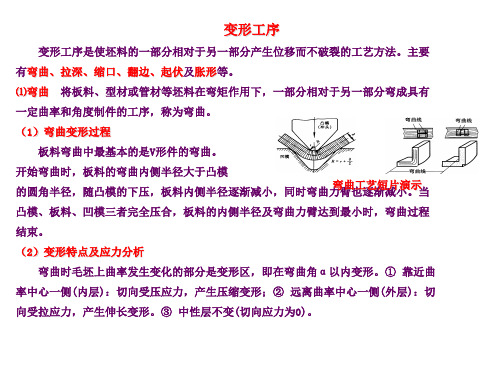
凸模、板料、凹模三者完全压合,板料的内侧半径及弯曲力臂达到最小时,弯曲过程
结束。 (2)变形特点及应力分析 弯曲时毛坯上曲率发生变化的部分是变形区,即在弯曲角α 以内变形。① 靠近曲 率中心一侧(内层):切向受压应力,产生压缩变形;② 远离曲率中心一侧(外层):切 向受拉应力,产生伸长变形。③ 中性层不变(切向应力为0)。
⑶缩口
将空心件或管件口部直径缩小的成形方法。 缩口工艺短片演示
⑷翻边 方法。
在板料或半成品上,使材料沿其内孔或外缘的一定曲线翻成竖立边缘的成形
翻边工艺短片制品表面上通过局部变薄,获得各种形状的凸起与凹陷
的方法。局部变形后的部位,因形状变化和加工硬化等原因,其强度和刚度提高。
(3)弯曲时容易出现的问题 ① 裂纹: σ 拉>σ b时产生。故变形程度不能过大,最小弯曲半径Rmin=(0.25~1)t t——材料板厚 纤维性: 弯曲线与材料的纤维线垂直时,允许的γ 行(重合)时,则易开裂。 ② 回弹(弹复): 当外力去除后,毛坯的塑性变形保留下来,而弹性变形完全消失,使其形状和尺寸 都 发生与加载时变形方向相反的变化,这种现象称为回弹。回弹与材料力学性能、r/δ 和制件弯曲角度α 有关,为消除回弹影响,弯曲模的角度应比被弯曲角度小一个回弹 角。 回弹大小与弯曲半径R、料厚t、材料等因素有关。回弹角一般都在0~10℃。 克服: 反变形法,模具角度设计应比所需制件角度小一点。
(4)拉深模具的特点 拉深模具与冲裁模具相比有如下特点: ①模具间隙较大;
②模具无刃口,呈圆角; (5)旋转体拉深件毛坯尺寸的计算
旋转体拉深件计算毛坯尺寸时,通常认为拉深件与其毛坯的重量不变、体积不 变,对于厚度不变的拉深件,则其面积不变。旋转体拉深件毛坯直径的计算可以用重 量法、体积法和面积法计算。当拉深件厚度不变时,通常采用面积法进行计算,具体 计算方法如下
第五章-缩口和胀形

❖ 硬质合金冲模 ❖ 多工位级进模
§5 - 1 缩口和胀形
缩口和胀形是属于二次加工的两个成形工序, 其毛料大多是管件或拉深件。缩口是把冲压件或 管件的口部缩小,而胀形则是将毛料的某部分胀 大。有时这两个工序也在同一零件中出现。
一、缩口
1.概念 缩口是使在空心件或管子的开口处加压缩小的一种冲压工
图5-16 液压胀形 (a)倾注液体法(b)充液橡胶囊法
书图5-9 胀形零件的尺寸
[5]
(2)缩口主要是防止工件失稳起皱,而胀形则主要是防止 毛料受拉而胀裂;
(3)缩口和胀形变形程度都采用变形前后工件的直径比来 表示,即 变形程度=变形后直径 / 变形前直径 其区别在于:胀形变形程度k>1 缩口变形程度m<1
5.胀形模结构
胀形零件图【8】3-202胀形模
杯形工序件压凸腰部
图【8】3-202胀形模
应变状态: 厚度方向εt和 经向εφ为正; 纬向εθ为负。
书图5-2 缩口工序变形特点
3.缩口系数m
缩口的变形程度用缩口系数m表示
在缩口变形过程中,材料 主要受切向压应力,使直径 减小,壁厚增加。由于切向 压应力的作用,缩口时毛料 便容易失稳起皱。同时,在 非变形区的筒壁,由于承受 全部缩口压力,也易失稳产 生变形。
缩口系数与模具的结构形式关系极大,还与材料的厚 度、种类及表面质量有关。 表5-2是不同材料、不同支承方式的允许缩口系数参考数值。
从二个表数值可看出:材料塑性愈好,厚度愈大,或模 具结构中对筒壁有支承作用的,许可缩口系数便较小。
4.缩口模具的支承形式
缩口模具的支承形式有三种:
(1)无支承缩口模 (2)外支承缩口模 (3)内外支承形式
胀形 翻边 缩口(二)
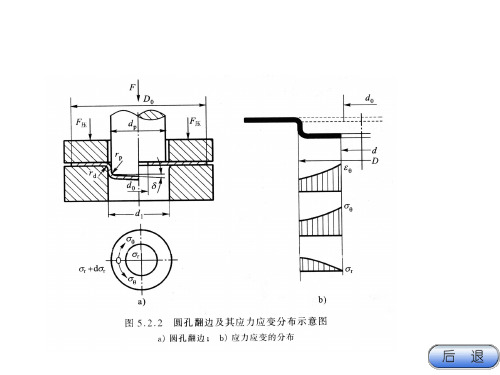
5.3.2缩口变形程度 缩口变形程度
缩口变形程度用缩口系数K来表示,其表达式: 缩口变形程度用缩口系数 来表示,其表达式: 来表示
d K= D
式中:d—缩口后的直径 式中: 缩口后的直径 D—为缩口前的直径 为缩口前的直径
5.3.3缩口模具结构设计举例 缩口模具结构设计举例
刚制气瓶缩口模,成形材料为1 刚制气瓶缩口模,成形材料为1mm的08钢(如 的08钢 图5.3.3) 33
2.冲压设备规格的选择 冲压设备规格的选择 1)公称压力 1)公称压力 一般情况下, 一般情况下,设备的公称压力应大于或等于成 形总工艺力的1.3倍。 形总工艺力的1.3倍 1.3 2)滑块行程 2)滑块行程 在拉深、弯曲工序中工件的高度较大时, 在拉深、弯曲工序中工件的高度较大时,为便 于取件,滑块行程应大于或等于工件高度的2.5 2.5倍 于取件,滑块行程应大于或等于工件高度的2.5倍。 3)闭合高度 闭合高度 模具的闭合高度必须适合于压力机闭合高度范围 的要求,它们之间的关系一般为: 的要求,它们之间的关系一般为:
D = d p + 4dH − 3.44d × r = 542 + 23.8×16− 3.44× 23.8× 2.25mm≈ 65mm
2
2) 计算拉深次数 因为 ; t / D = 2.3%
d ' 凸 54 = = 0.83 D 65
m总 =
d 23.8 = = 0.366 D 65
初定 r1 ≈ ( 4 ~ 5)t 《冲压手册》中查表可得极限拉深 从 冲压手册》 系数 [m1 ] = 0.44, [m2 ] = 0.75 又由 所以
特点:生产率高,操作比较安全,用于大批量的, 特点:生产率高,操作比较安全,用于大批量的,采用其他工序 加工困难的精度要求不太高的小型工件的生产。 加工困难的精度要求不太高的小型工件的生产。
第五章、翻边与胀形

②软模胀形
利用橡胶,聚氨酯,PVC塑料等作 利用橡胶,聚氨酯,PVC塑料等作 13聚氨酯强度、弹性、 聚氨酯强度 凸模 图5-13聚氨酯强度、弹性、耐 油性方面优于橡胶 得到广泛运用。 橡胶, 油性方面优于橡胶,得到广泛运用。
③液压胀形 P75, P75,
图5-14
图册P68, 图册P68, P68
h1=h-r-to =h-
(1h=1/2Dm(1-K )+ 0.43r+0.75to (1hmax=1/2Dm(1-KL)+0.43r+0.75to
当h>hmax 不能一次成形
(2)可采用拉深后再翻边 (2)可采用拉深后再翻边
或采取预胀形 或拉深后翻边
先确定翻边 h1、 后定 do、 h2 d0有错 196页 有错 页 Dm − do to ∏ to h1 = − (r + ) + (r + ) 2 2 2 2 Dm ≈ (1 − k ) + 0.57 r 2 d o = Dm + 1.14r
δ p = K p −1 θ
得出K 由 δ θp得出Kp 表5-3
5.张拉成形 5.张拉成形
有些大型零件,底部曲率半径很大,曲面部分变 有些大型零件,底部曲率半径很大,曲面部分变 大型零件 形量小,回弹大。 形量小,回弹大。 需胀形的方式增大塑性变形量。 需胀形的方式增大塑性变形量。 增大塑性变形量 两种方法: 两种方法: 采用增大进料阻力工艺措施( 一是采用增大进料阻力工艺措施 调整压边力, 一是采用增大进料阻力工艺措施(调整压边力, 使用拉深筋,增大毛坯尺寸)提高毛坯变形程度。 使用拉深筋,增大毛坯尺寸)提高毛坯变形程度。 可采用δ 较小的板料成形。 可采用δs/δb较小的板料成形。
冲压课后题
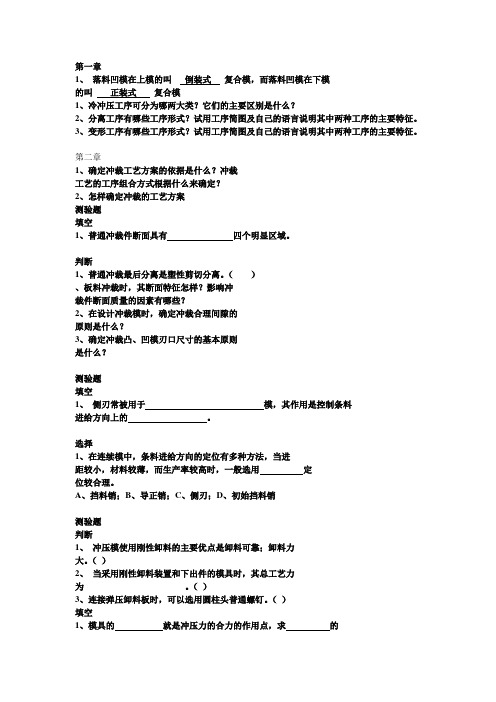
第一章1、落料凹模在上模的叫倒装式复合模,而落料凹模在下模的叫正装式复合模1、冷冲压工序可分为哪两大类?它们的主要区别是什么?2、分离工序有哪些工序形式?试用工序简图及自己的语言说明其中两种工序的主要特征。
3、变形工序有哪些工序形式?试用工序简图及自己的语言说明其中两种工序的主要特征。
第二章1、确定冲裁工艺方案的依据是什么?冲裁工艺的工序组合方式根据什么来确定?2、怎样确定冲裁的工艺方案测验题填空1、普通冲裁件断面具有四个明显区域。
判断1、普通冲裁最后分离是塑性剪切分离。
()、板料冲裁时,其断面特征怎样?影响冲裁件断面质量的因素有哪些?2、在设计冲裁模时,确定冲裁合理间隙的原则是什么?3、确定冲裁凸、凹模刃口尺寸的基本原则是什么?测验题填空1、侧刃常被用于模,其作用是控制条料进给方向上的。
选择1、在连续模中,条料进给方向的定位有多种方法,当进距较小,材料较薄,而生产率较高时,一般选用定位较合理。
A、挡料销;B、导正销;C、侧刃;D、初始挡料销测验题判断1、冲压模使用刚性卸料的主要优点是卸料可靠;卸料力大。
()2、当采用刚性卸料装置和下出件的模具时,其总工艺力为。
()3、连接弹压卸料板时,可以选用圆柱头普通螺钉。
()填空1、模具的就是冲压力的合力的作用点,求的方法就是求空间平行力系的合力的作用点。
2、要使冷冲压模具正常而平稳地工作,必须使与模柄的轴心线(或偏移不大)。
3、弹性卸料装置除了起卸料作用外,还兼起作用。
它一般用于材料厚度相对材料的卸料。
测验题计算如图所示,零件材料为Q235,料厚为2㎜。
计算冲压力,确定压力机公称压力1、什么是模具的压力中心?2、怎样确定模具的压力中心1、冲裁凸模的基本固定方式有哪几种?2、怎么提高凸模的强度和刚度?测验题判断1、标准件就是从标准件厂购买来直接装配在模具上的不需进行任何加工的零件。
()填空1、普通模架在“国家标准”中,按照导柱导套的数量和位置不同可分为:四种模架。
- 1、下载文档前请自行甄别文档内容的完整性,平台不提供额外的编辑、内容补充、找答案等附加服务。
- 2、"仅部分预览"的文档,不可在线预览部分如存在完整性等问题,可反馈申请退款(可完整预览的文档不适用该条件!)。
- 3、如文档侵犯您的权益,请联系客服反馈,我们会尽快为您处理(人工客服工作时间:9:00-18:30)。
3、冲压加工的工序数量确定 工序数量既可指同一性质工序重复进行的次数, 工序数量既可指同一性质工序重复进行的次数,又 可指在整个冲压加工过程所需的总的工序数目。 可指在整个冲压加工过程所需的总的工序数目。 确定工序数量的基本原则是: 确定工序数量的基本原则是:在保证工件质量的前提 考虑生产率和经济性的要求, 下,考虑生产率和经济性的要求,工序数量应尽可能少 些。 顺序确定 4、工序顺序确定 工序顺序 工序顺序是指冲压加工过程中各道工序进行的先后 次序,主要决定于冲压变形规律和零件的质量要求。 次序,主要决定于冲压变形规律和零件的质量要求。
5、确定工序的组合方式 、 冲压工序的组合, 冲压工序的组合,是将两个或两个以上的工序合并在 一道工序内完成。 一道工序内完成。 复合冲压工序:在压力机的一次行程中, 复合冲压工序:在压力机的一次行程中,毛坯或半成 品在模具的同一位置只经过一次定位, 品在模具的同一位置只经过一次定位,便可完成两个或两 个以上的工序。 个以上的工序。
6.冲压设计过程 6.冲压设计过程
1、搜集冲压设计必需的原始资料; 搜集冲压设计必需的原始资料; 2、对冲压件进行工艺分析; 对冲压件进行工艺分析; 进行必要的工艺计算,分析比较并确定最佳工艺方案; 3、进行必要的工艺计算,分析比较并确定最佳工艺方案; 确定模具的结构形式; 4、确定模具的结构形式; 合理选择冲压设备; 5、合理选择冲压设备; 编写工艺过程卡; 6、编写工艺过程卡; 重新审查产品零件图和冲压工艺过程卡; 7、重新审查产品零件图和冲压工艺过程卡; 绘制模具总装图和零件图; 8、绘制模具总装图和零件图; 校核模具图纸; 9、校核模具图纸; 10、编写冲压设计计算说明书。 10、编写冲压设计计算说明书。
6. 5选择冲压设备 选择冲压设备
冲压设备类型的选择: 冲压设备类型的选择 主要根据所要完成的冲压的工序性质、 主要根据所要完成的冲压的工序性质、生产批量的大 小、冲压件的几何尺寸和精度要求等来选择冲压设备的 类型: 类型: 1)对于中小型冲裁件、弯曲件或浅拉深件的冲压,常 对于中小型冲裁件、弯曲件或浅拉深件的冲压, 对于中小型冲裁件 采用开式曲柄压力机 2)对于大中型和精度要求高的冲压件,多采用闭式曲 对于大中型和精度要求高的冲压件, 对于大中型和精度要求高的冲压件 柄压力机
冲模压力中心即冲压力合力的作用点。它必须与压力机滑块中心相重 冲模压力中心即冲压力合力的作用点。 合或近似重合。 合或近似重合。
2)凸凹模间隙及其圆角半径的计算,凸凹模工作部 凸凹模间隙及其圆角半径的计算, 分的尺寸计算。 分的尺寸计算。 弹性元件的有关计算。 3)弹性元件的有关计算。如橡皮或弹簧的自由高度 和预压缩量的确定等。 和预压缩量的确定等。 模具有关零件的强度校核。 4)模具有关零件的强度校核。
冲压工序性质的确定主要取决于冲压件的形状、尺寸和精度要求, 冲压工序性质的确定主要取决于冲压件的形状、尺寸和精度要求, 同时还应考虑冲压变形规律及某些具体条件的限制。 同时还应考虑冲压变形规律及某些具体条件的限制。
1)在一般情况下,可从零件图上直观的确定出工序性质。 在一般情况下,可从零件图上直观的确定出工序性质。 2)在某些情况下,需对零件图通过计算、分析比较后, 在某些情况下,需对零件图通过计算、分析比较后, 才能准确地确定出工序性质。 才能准确地确定出工序性质。 3)有时为了改善冲压变形条件或方便工序定位,往往需 有时为了改善冲压变形条件或方便工序定位, 要增加某些附加工序,这些附加工序, 要增加某些附加工序,这些附加工序,则使工序性质的选用 及工艺过程的安排也相应发生了变化。 及工艺过程的安排也相应发生了变化。
3) 对于大型或较复杂的拉深件,常采用上传动的 对于大型或较复杂的拉深件, 闭式双动拉深压力机。 闭式双动拉深压力机。 4)对于大批量生产的或者形状复杂、批量很大的 对于大批量生产的或者形状复杂、 对于大批量生产的或者形状复杂 中小型冲压件, 中小型冲压件,应优先选用自动高速压力机或者多 工位自动压力机 5)对于小批量生产的工件,尤其是大型厚板冲压 对于小批量生产的工件, 对于小批量生产的工件 件,常采用液压机 6) 对于精冲零件,最好选择专用的三动精冲压力 对于精冲零件, 机
6.3确定冲压件工艺方案 确定冲压件工艺方案
1、首先根据图纸进行必要的工艺计算 1)计算毛坯的展开尺寸; 计算毛坯的展开尺寸; 2)工序间的半成品尺寸; 工序间的半成品尺寸; 3)冲压力; 冲压力; 4)排样方式及材料利用率的计算。 排样方式及材料利用率的计算。
如图8.1.1 8.1.1) 2、确定冲压加工的各工序性质 (如图8.1.1) 在冲压加工中,工序性质是指冲压件所需的工序种类。 在冲压加工中,工序性质是指冲压件所需的工序种类。
2.冲压设备规格的选择 冲压设备规格的选择 1)公称压力 1)公称压力 一般情况下, 一般情况下,设备的公称压力应大于或等于成 形总工艺力的1.3倍。 形总工艺力的1.3倍 1.3 2)滑块行程 2)滑块行程 在拉深、弯曲工序中工件的高度较大时, 在拉深、弯曲工序中工件的高度较大时,为便 于取件,滑块行程应大于或等于工件高度的2.5 2.5倍 于取件,滑块行程应大于或等于工件高度的2.5倍。 3)闭合高度 闭合高度 模具的闭合高度必须适合于压力机闭合高度范围 的要求,它们之间的关系一般为: 的要求,它们之间的关系一般为:
6.2冲压件的工艺性分析 冲压件的工艺性分析
冲压件的工艺性是零件对冲压工艺的适应性即冲压加 工的难易程度。 工的难易程度。 工艺分析主要包括技术和经济两方面。 工艺分析主要包括技术和经济两方面。 技术方面:冲压件的结构形状、尺寸大小、精度要求 技术方面:冲压件的结构形状、尺寸大小、 和材料性能等是否符合冲压加工的要求。 和材料性能等是否符合冲压加工的要求。 经济方面:根据生产批量,分析产品成本。 经济方面:根据生产批量,分析产品成本。 冲压件的工艺分析主要是讨论在满足零件使用要求的 前提下,能否以最简单最经济的方法冲压出来。 前提下,能否以最简单最经济的方法冲压出来。
[m1 ][m2 ] = 0.44 × ቤተ መጻሕፍቲ ባይዱ.75 = 0.33
m总 〉[m1 ][m2 ]
需要两次拉深, 需要两次拉深,取n=2
3.工序的组合和顺序确定(如图所示 .工序的组合和顺序确定 如图所示 如图所示) 对于象外壳这样工序较多的冲压件, 对于象外壳这样工序较多的冲压件,可以先确定出 零件的基本工序, 零件的基本工序,再考虑对所有的基本工序进行可能 的组合排序, 的组合排序,将由此得到的各种工艺方案进行分析比 从中确定出适合于生产实际的最佳方案. 较,从中确定出适合于生产实际的最佳方案.
特点:生产率高,操作比较安全,用于大批量的, 特点:生产率高,操作比较安全,用于大批量的,采用其他工序 加工困难的精度要求不太高的小型工件的生产。 加工困难的精度要求不太高的小型工件的生产。
6.4 冲压模具的总体设计
1、模具总体结构的设计 2、主要零部件的设计 有关的工艺计算 模具压力中心的计算。 1)模具压力中心的计算。
H max − 5 ≥ H 模 ≥ H min + 10
6. 6冲压工艺文件的编写 冲压工艺文件的编写
冲压工艺文件包括冲压工艺卡片和冲压设计计算说明书。 冲压工艺文件包括冲压工艺卡片和冲压设计计算说明书。 冲压工艺卡片和冲压设计计算说明书 冲压设计计算说明书主要包括: 冲压设计计算说明书主要包括: 1)设计题目 ) 2)冲压件的工艺性分析 ) 3)冲压件的工艺方案制定 ) 4)工艺计算 ) 5)模具的结构合理性分析 ) 6)模具主要零件的结构形式、材料选择、公差配合、 )模具主要零件的结构形式、材料选择、公差配合、 技术要求的说明等。 技术要求的说明等。 7)其他需要说明的问题 ) 8)主要参考资料 )
2.工艺方案的确定 工艺方案的确定 1)计算毛坯尺寸 如图 计算毛坯尺寸(如图 计算毛坯尺寸 如图8.2.1) 根据翻边工艺计算公式,翻边系数K为 根据翻边工艺计算公式,翻边系数 为
2 K = 1− ( 5 − 0 . 43 × 1 − 0 . 72 × 1 . 5 ) = 0 . 61 18
翻边前的拉深件形状与尺寸(如图 翻边前的拉深件形状与尺寸 如图8.2.4) 如图 毛坯直径D按以下公式计算 按以下公式计算: 毛坯直径 按以下公式计算:
6.1 工艺设计的原始材料
1、冲压件的产品图纸及技术条件; 冲压件的产品图纸及技术条件; 2、原材料的尺寸规格、机械性能与工艺性能及供应情 原材料的尺寸规格、 况; 3、产品的生产批量及定型程度; 产品的生产批量及定型程度; 4、供选用的冲压设备的型号、规格、主要技术参数及 供选用的冲压设备的型号、规格、 使用说明书 ; 5、模具制造条件及技术水平; 模具制造条件及技术水平; 6、其他技术资料。 其他技术资料。
5.3 缩口
缩口是将预先成形好的圆筒件或管件坯料,通过模具 缩口是将预先成形好的圆筒件或管件坯料 通过模具 将其口部缩小的一种成形工序(如图 如图5.3.1) 将其口部缩小的一种成形工序 如图
5.3.1 缩口成形的特点
1、常见的缩口形式有(如图 1、常见的缩口形式有(如图5.3.2) 如图5.3.2) 2、缩口时,变形区的金属受切向和轴向压应力,使壁 、缩口时,变形区的金属受切向和轴向压应力, 厚和高度增加; 厚和高度增加;属于压缩类成形工序 3、变形区由于受到较大切向压应力的作用易产生切向 、 失稳而起皱, 失稳而起皱,起传力作用的筒壁区由于受到轴向压应 力的作用易产生轴向失稳而起皱,所以失稳起皱是缩 力的作用易产生轴向失稳而起皱, 口工序的主要障碍。 口工序的主要障碍。
D = d p + 4dH − 3.44d × r = 542 + 23.8×16− 3.44× 23.8× 2.25mm≈ 65mm
2
2) 计算拉深次数 因为 ; t / D = 2.3%
d ' 凸 54 = = 0.83 D 65
m总 =
d 23.8 = = 0.366 D 65