制动踏板性能及试验要求
机动车制动踏板力手刹力检测作业指导书

机动车制动踏板力手刹力检测作业指导书(一)、检测目的汽车的制动性能直接关系到行车安全,制动踏板力的大小则是评价制动工作能力的辅助参数之一,它能反映制动管路是否堵塞、泄漏,制动元件是否正常等情况。
(二)、判定标准GB7258-2017《机动车运行安全技术条件》规定:行车制动在产生最大制动效能时的踏板力或手握力应小于等于:乘用车和正三轮摩托车 500N ;摩托车(正三轮摩托车除外) 350N(踏板力)或250N(手握力);其他机动车,700N 。
驻车制动应通过纯机械装置把工作部件锁止,并且驾驶人施加于操纵装置上的力:手操纵时,乘用车应小于等于 400N ,其他机动车应小于等于 600N;脚操纵时,乘用车应小于等于 500N ,其他机动车应小于等于 700N 。
进行制动性能检验时的制动踏板力或制动气压应符合以下要求:a)满载检验时气压制动系:气压表的指示气压≤额定工作气压;液压制动系:踏板力,乘用车≤500N;其他机动车≤700N。
b)空载检验时气压制动系:气压表的指示气压≤750kPa;液压制动系:踏板力,乘用车≤400N;其他机动车≤450N。
摩托车(正三轮摩托车除外)检验时,踏板力应小于等于 350N,手握力应小于等于 250N。
正三轮摩托车检验时,踏板力应小于等于 500N。
三轮汽车和拖拉机运输机组检验时,踏板力应小于等于 600N。
(三)、选用设备机动车制动踏板/手刹力计。
(四)、主要技术参数1.使用环境:温度范围:0~40℃相对湿度:30-85%2.最小刻度:数显,可读到小数点前最后一位3.量程: 0~1000N4.精度: 0.5%5.功耗: 0.4W6.电源: 12V±5%直流7.重量: 2kg(五)、原理1.压力传感器的电源设计成恒流源供电方式,大约1mA左右。
传感器的输出信号经调“0”(由W1完成)送到线性放大器A2。
2. A2对原始信号进行线性放大后,进入峰值检波器储存起电平信号的最大值,即新测过程中的最大值)。
汽车制动性能检测与诊断

⏹汽车制动性能检测与诊断⏹一、制动装置的基本要求行车制动、应急制动、驻车制动功能:强制行驶中的汽车减速,停车,防止停放中的汽车滑移。
GB7258-2012《机动车运行安全技术条件》的规定。
⏹二、制动性能的评价指标1、制动过程分析⏹制动性能的评价指标2、制动效能评价指标1)制动距离:是指机动车在规定的初速度下急踩制动时,从脚接触制动踏板(或手触动制动手柄)时起至机动车停住时止机动车驶过的距离。
2)制动时间(制动协调时间和制动释放时间)。
制动协调时间是指在急踩制动时,从脚接触制动踏板(或手触动制动手柄)时起至机动车减速度(或制动力)达到规定的机动车充分发出的平均减速度(规定的制动力)的75%时所需的时间。
3)制动力。
⏹制动性能的评价指标4)制动减速度:充分发出的平均减速度MFDD:式中:MFDD——充分发出的平均减速度,单位为米每平方秒(m/s2);V0—试验车制动初速度,单位为千米每小时(km/h);Vb—0.8试验车速,单位为千米每小时(km/h);Ve—0.1试验车速,单位为千米每小时(km/h);Sb—试验车速从V0到Vb之间车辆行驶的距离,单位为米(m);Se—试验车速从V0到Ve之间车辆行驶的距离,单位为米(m)。
⏹制动性能的评价指标3、制动稳定性的评价制动稳定性要求:是指制动过程中机动车的任何部位(不计入车宽的部位除外)不允许超出规定宽度的试验通道的边缘线。
制动跑偏、制动侧滑4、制动拖滞制动释放时间无限长。
⏹三、制动性能检验仪器1、制动试验台的分类1)按轴数分:单轴式、双轴式;2)按原理分:反力式、惯性式;3)按试验台支撑形式分:滚筒式、平板式;4)试验台检测参数分:测制动力式、测制动距离式和多功能式。
⏹制动性能检验仪器2、测力式制动试验台1)滚筒式制动试验台⏹制动性能检验仪器(1)滚筒式制动试验台结构电动机:产生动力,带动滚筒及车轮旋转减速器(增扭器):减速增扭;蜗轮蜗杆式滚筒:支撑车轮,制动力的承受装置传感器:测量转换装置(压力式、平衡弹簧式、电位计式、差动变压器式、自整角电机式)举升器:便于汽车驶入或驶出试验台第三滚筒:产生停转信号显示及测量装置。
汽车制动踏板行程及踏板力的评定

工程管理36 2015年60期汽车制动踏板行程及踏板力的评定赫蛟龙身份证:1301301988****0618,河北保定 071000摘要:物质生活水平的日益提高,人们对汽车的舒适性及操纵方便性的要求也越来越高。
作用在汽车制动踏板上的力及其行程,不仅直接影响汽车的制动性能,而且还能说明制动系操纵机构的轻便和舒适程度。
汽车制动踏板力-行程检查仪,简称制动踏板检查仪,用于汽车生产线、总装线或汽车检测站及修理厂检测制动时作用于踏板上的力及其行程。
它亦可用于检测离合器踏板的力和行程,具有体积小、质量轻、使用方便、省力省时和安全可靠等优点。
关键词:汽车制动;制动踏板;模拟方法;评定中图分类号:U463.5 文献标识码:A 文章编号:1671-5810(2015)60-0036-021 导言随着汽车尾气排放及污染日趋严重,并逐渐成为大气环境最突出、最紧迫的问题之一,而且近几年成品油的价格变化成上涨的态势,全球不可再生能源日渐减少,用新能源汽车代替传统汽车是不可否认的事实,其中电动轮汽车有诸多优点,所以本文借助四轮独立驱动电动轮汽车为模型,对制动系统进行系统的研究,提出一些新颖的思想和方法来解决电动汽车制动过程评定性的问题。
2 汽车踏板性能要求和试验方法汽车行业标准QC/T788—2007对汽车踏板的强度要求如下:踏板装置在纵向力作用下,踏板表面的永久变形量≤5mm,且无裂纹或损坏等缺陷。
试验加载方法是按实车状态固定踏板机构总成,将踏板机构输出端与负载机构连接,并将踏板臂在工作行程的中间位置固定.在踏板几何中心点,施加所规定的垂直于踏板表面的纵向力并保持5s,测量加载点的纵向位移(变形)量。
3 结构原理根据设计要求,该设备需设置测力计和行程测量仪方可同时检测制动踏板的力和行程。
根据使用工况,还需设置安装固定装置,即定位板、限位叉等。
要进行力和位移的传递,需设置传递机构,如弹性元件,施力手柄等。
根据使用要求,该设备采用了机械式手动方式,以达到快速、可靠和安全的使用效果。
制动系检测

次试验全部完成,提高试验或检测效率。
4)结构简单、安全方便,不需专门的混凝土基础;日常维护 方便、耗电量低。 5)重复性差、占地面积大、需要助跑车道;
(3)惯性式制动试验台
惯性式滚筒制动试验台用旋转飞轮的转动惯量模拟车辆 道路行驶时的平移动能,测试结果与实际工况更为接近。
制动时,轮胎对滚筒表面产生阻力,由于滚筒传动系统具 有一定的惯性,因而滚筒表面将相对于车轮移过一定距离。因 此,惯性式制动试验台可以模拟道路制动试验工况。
(1)反力式制动试验台
(1)驱动装臵 由电动机、减速器和链传动组成。 (2)滚筒装臵 由四个滚筒组成。 每对滚筒独立设臵,有主动
电动机的转动 通过减速器内的蜗轮 蜗杆和圆柱齿轮传动 传递给主动滚筒 通过链传动
滚筒和从动滚筒之分。
传递给从动滚筒
工作过程
(3)测量装臵
主要由测力杠杆、测力传感器和测力弹簧等组成。 测力杠杆一端与传感器连接,另一端与减速器连接 测力杠杆的位移或力
杠杆前端的测力传感器
反映制动力大小的电信号
工 作 过 程
指示与控制装置
(4)举升装置 为了便于汽车出入试验台,在两滚筒之间设有举升装 置,一般由举升器、举升平板和控制开关等组成。
(5)第三滚筒 测量车轮转速;当被检测车轮制动时,转速下降至接近
抱死时,向控制装置发出信号使驱动电机停止转动,以防止
滚筒剥伤轮胎、保护驱动电机。
现用的路试检测检测设备
1.非接触式多功能速度仪
可检测:制动距离、速度、MFDD、减速度、油耗、制动时间
2.制动踏板力计
3.转向盘转动量扭矩检测仪
美国现代便携式制动性能检测设备
VC3000便携式制动性能检测仪
测量参数:
汽车制动性能道路试验

汽车制动性能道路试验一、试验要求1.制动速度和制动距离行车制动性能是在规定的条件下,通过测试相应的初速度下的制动距离和/或充分发出的平均减速度来确定。
充分发出的平均减速度(MFDD )按下式计算:22(-)25.92(-)ab ae e b v v MFDD s s 制动距离是指驾驶员开始促动制动控制装置时起到车辆停止时止,车辆驶过的距离。
制动初速度是指驾驶员开始促动制动控制装置时车辆的速度,试验中,制动初速度应不低于规定值的98%。
2.试验条件(1)试验路面应为干燥、平整、清洁的混凝土或具有相同附着系数的其他路面,在路面纵向任意50m 的长度上的坡度应小于1%,路拱坡度应小于2%。
(2)风速应小于5m/s ,气温不超过35o C 。
(3)满载试验时,试验车辆处于厂定最大总质量状态,载荷均匀分布。
轴载质量的分配按制造厂的规定。
若装载质量在各桥间的分配有多种方案,车辆最大总质量在各桥间的分配必须保证各桥载质量与其最大允许载质量的比值相同。
(4)空载试验时,汽车燃油加至厂定油箱容积的90%,加满冷却液和润滑油,携带随车工具和备胎,另包括200kg 质量(为驾驶员、一名试验员和仪器质量)。
(5)试验前应调整好制动系统,制动器应磨合好。
轮胎充气至厂定压力值。
二、制动性能要求行车制动性能必须在车轮不抱死、任何部位不偏离出3.7m 通道且无异常制动的情况下获得的,当车速低于15km/h 时,允许车轮抱死。
最大控制力不得超过规定值。
三、实验数据分析1.第一次试验数据(往方向)(1)车速随时间变化图像(2)踏板力随时间的变化曲线(3)时间和制动距离时间-速度曲线中的黄色部分,是系统用于计算MFDD 的区域;时间-踏板力曲线中的褐色部分,是系统用于计算平均踏板力的部分。
本次试验所得结果为:制动初速度:52.5km/h制动时间为:3.22s制动距离为:24.836m平均制动踏板力为:139.691N充分发出的平均减速度(MFDD)为:5.007m/s22.第二次试验数据分析(返方向)(1)车速随时间变化曲线(2)踏板力随时间变化曲线(3)制动距离随时间变化关系时间-速度曲线中的黄色部分,是系统用于计算MFDD 的区域;时间-踏板力曲线中的褐色部分,是系统用于计算平均踏板力的部分。
汽车实验学试验报告
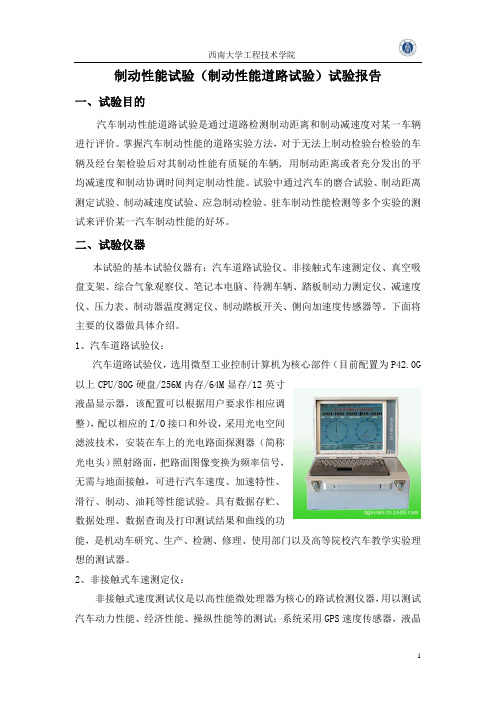
制动性能试验(制动性能道路试验)试验报告一、试验目的汽车制动性能道路试验是通过道路检测制动距离和制动减速度对某一车辆进行评价。
掌握汽车制动性能的道路实验方法,对于无法上制动检验台检验的车辆及经台架检验后对其制动性能有质疑的车辆, 用制动距离或者充分发出的平均减速度和制动协调时间判定制动性能。
试验中通过汽车的磨合试验、制动距离测定试验、制动减速度试验、应急制动检验、驻车制动性能检测等多个实验的测试来评价某一汽车制动性能的好坏。
二、试验仪器本试验的基本试验仪器有:汽车道路试验仪、非接触式车速测定仪、真空吸盘支架、综合气象观察仪、笔记本电脑、待测车辆、踏板制动力测定仪、减速度仪、压力表、制动器温度测定仪、制动踏板开关、侧向加速度传感器等。
下面将主要的仪器做具体介绍。
1、汽车道路试验仪:汽车道路试验仪,选用微型工业控制计算机为核心部件(目前配置为P42.0G 以上CPU/80G硬盘/256M内存/64M显存/12英寸液晶显示器,该配置可以根据用户要求作相应调整),配以相应的I/O接口和外设,采用光电空间滤波技术,安装在车上的光电路面探测器(简称光电头)照射路面,把路面图像变换为频率信号,无需与地面接触,可进行汽车速度、加速特性、滑行、制动、油耗等性能试验。
具有数据存贮、数据处理、数据查询及打印测试结果和曲线的功能,是机动车研究、生产、检测、修理、使用部门以及高等院校汽车教学实验理想的测试器。
2、非接触式车速测定仪:非接触式速度测试仪是以高性能微处理器为核心的路试检测仪器,用以测试汽车动力性能、经济性能、操纵性能等的测试;系统采用GPS速度传感器,液晶显示,实时显示多项测试数据、曲线,清晰直观;测试项目采用菜单式操作,简单易用;传感器系数、测试参数等系统自动存储,掉电不丢失。
整机设计符合人机工程学,便于操控,该仪器是汽车制造、汽车检测、汽车维修、科研部门、道路交通部门以及农机安全监理部门的理想检测设备和高等院校汽车方面的理想教学设备。
汽车制动性实验报告

汽车制动性实验报告汽车制动性能试验报告一、试验目的1)学习制动性能道路实验的基本方法,以及实验常用设备;2)通过道路实验数据分析真实车辆的制动性能;3)通过实验数据计算实验车辆的制动协调时间、充分发出的制动减速度和制动距离。
二、试验对象试验对象:金龙6601E2客车;试验设备:1)实验车速测量装置:常用的有ONO SOKKI机械五轮仪、ONO SOKKI 光学五轮仪和RT3000惯性测量系统。
实验中实际使用的是基于GPS的RT3000惯性测量系统。
2)数据采集、记录系统:ACME便携工控机3)GEMS液压传感器,测量制动过程中制动压力的变化情况。
.三、试验内容1)学习机械五轮仪的工作原理、安装方法及安装注意事项;了解实验车上的实验设备及安装方法;由于制动实验中,实验车辆上的所有人和物都处于制动减速度的环境中,因此需要对所有物品进行固定,以防止实验过程中对设备的损伤以及对实验人员的损伤。
另外,由于实验过程是在室外进行,要求实验系统能够承受各种环境的影响,因此需要针对实验内容选择实验设备及防范措施。
2)学习车载开发实验软件的使用,了解制动性能分析中比较重要的实验数据的内容和测量方法。
3)制动协调时间的测量在常规制动试验中,采集制动信号、动压力信号、车轮轮速信号和五轮仪车速信号。
将五轮仪的车速方波信号转化为可直接观察的车速信号和制动减速度信号。
在同一个曲线图表中绘制制动踏板信号、制动压力信号和制动减速度信号,观察制动压力和制动减速度在踩计算当前制下制动踏板后随时间变化的情况,动情况下的制动协调时间。
充分发出的制动减速度和制动距离的计算4)22u?u充分发出的制动减速度:eb?MFDD)25.92(s?s制动距离2τ1u?τ0a2??u?s0a a25.923.62bmax5)根据实验设be??备设计制动实验的实验方法,要求的实验车速范围应包括30Km/h~50Km/h;6)车速、轮速的计算方法分析;7)按照实验方法在可能的条件下进行制动实验。
制动踏板总成技术条件

共 5 页第 1 页旧底图总号底 图 总 号编 制校 对签 字标准化会 签 QC/T797-2008 汽车塑料件、橡胶件和热塑性弹性体件的材料标识和标记JT-D0101-3504-1 QC/T788-2007 汽车踏板装置性能要求及台架试验方法QC/T484-1999 汽车油漆涂层3.1 一般要求制动踏板总成技术条件设计文件名称GB/T10125-2012 人造气氛腐蚀试验 盐雾试验3.2.1纵向位移:GB 8410-2006 汽车内饰材料的燃烧特性1 范围本技术条件规定了XX车型SUV多用途乘用车用制动踏板总成性能要求和台架试验方法。
本技术条件适用于XX车型SUV机械铰链式金属制动踏板总成。
2 引用标准XX车型SUV多用途乘用车产品型号名称3 技术要求将制动踏板按照实车状态安装固定,按图1加载方式,加载50N±2N的正反方向的纵向力作用下,踏板的纵向位移应小于或等于2.0mm。
图1 纵向力加载与纵向位移测量3.1.2制动踏板总成在整个工作行程中应动作灵活,无异常响声。
3.1.4工作环境温度:-40℃~80℃。
3.1.3外观:零件表面光洁,无裂纹、毛刺、划痕等缺陷;焊接部位不得有漏焊、气孔、烧穿、咬肉等缺陷。
3.2 基本要求3.1.1产品应符合本技术条件要求,并按规定程序批准的图样与技术文件制造。
旧底图总号底 图 总 号签 字3.2.3.1纵向刚度性能:将制动踏板按照实车状态安装固定,在踏板面上按图1加载方式,加载500N±10N的纵向力作用下,踏板的纵向位移应小于或等于5.0mm。
3.2.3.1侧向刚度性能:将制动踏板按照实车状态安装固定,按图2加载方式,加载100N±5N的正反方向的纵向力作用下,踏板的纵向位移应小于或等于2.5mm。
3.2.3刚度性能3.3.1高温工作性能:在70℃±2℃的环境中试验时,制动踏板总成在全行程运动过程中,不得有卡滞、卡阻现象和异常响声。
中华人民共和国机动车制动检验规范(试行)

中华⼈民共和国机动车制动检验规范(试⾏)⽬录第⼀章总则第⼆章制动装置第三章⽤制动距离检验车辆制动性能第四章⽤制动⼒检验汽车制动性能第五章检验仪器、设备与试验场地第六章附则第⼀章总则第⼀条为保障⾏车安全,提⾼运输效率,适应交通运输现代化的需要,特制订本规范。
第⼆条本规范适⽤于汽车(包括于汽车带挂车和半挂车)、⽆轨电车、特种汽车、⼆、三轮摩托车和⽅向盘式拖拉机带挂车等机动车辆,对⼿扶式拖拉机的制动装置也提出了适当要求。
第三条机动车的制动装置及制动性能,必须符合本规范的有关要求。
对于汽车、⽆轨电车和牵引车带半挂车的制动性能要求,根据其总重量按⼩、中、⼤三种车型分别规定(详见表⼀和表⼆)。
第四条本规范由交通监理部门和公安交通管理部门负责监督、贯彻执⾏。
第⼆章制动装置第五条通⾏城镇街道和公路的机动车以及出⼚的新车,必须装有⾏车和停车制动装置。
挂车和半挂车(包括新出⼚的)必须装有⾏车制动装置。
两轴挂车⾄少在后轴两轮上装有⾏车制动装置。
⼿扶拖拉机拖带的挂车也必须装有可靠的制动装置。
制动装置应保持技术状况良好,操纵轻便,完整可靠。
第六条停车制动装置的安装位置要适当,其⼿柄⾏程必须有⼀定的贮备。
停车制动杆卡锁必须有效。
施加于停车制动杆上的⼒,不⼤于35公⽄。
第七条制动管路要有⾜够的耐压强度并安装牢固,不得与运动件摩擦相碰,不得有漏油、漏⽓现象。
第⼋条⽓压制动系统必须装有限压装置,确保不超过贮⽓筒允许的最⼤⽓压。
贮⽓筒应装有放⽔阀。
第九条采⽤⽓压制动系统的车辆,应在发动机最⼤转速下,四分种(带挂车的为六分钟)内,⽓压表的指⽰⽓压不低于起步⽓压。
贮⽓筒的容量,应在不继续充⽓的情况下,连续五次紧急制动后,⽓压不低于起步⽓压。
第⼗条采⽤液压制动系统或机械制动系统的车辆,要求在踏板全⾏程的五分之四以内,达到最⼤制动效能。
第⼗⼀条在车轮跳动和转向时,不应有⾃⾏制动现象。
当挂车与牵引车意外脱离后,挂车应能⾃⾏制动,牵引车的制动仍然有效。
汽车制动性能试验

汽车制动性能试验一、实验目的1、测定汽车的制动性能2、掌握影响制动性能的主要因素二、实验使用仪器非接触车速仪、风速计各一套,打印纸若干,试验车一辆等三、实验原理1、制动距离与制动减速度(定义、影响因素)2、制动效能的恒定性(定义、影响因素)3、制动时汽车的方向稳定性(定义、影响因素)本次实验,主要利用非接触车速仪来测量汽车在不同的车速下制动时车辆的制动距离和制动时间,进而计算出制动减速度,并对其结果进行评判,对该车的制动性能作出评价。
四、实验方法及步骤试验前将光电头安装于车上,把车速仪各连线接好,接上电源,特别注意电源正负极不要接错。
将制动踏板开关装在踏板上,另一端接在仪器后面板的“制动”插座上。
1、选择工况:开机或按复位键,显示Good字样,在按制动键,奏输入音乐。
2、预置数据:检查修改传感器系数。
按B键,最高位LED显示b,然后按两位数字键,表示制动初速,最低两位LED显示制动初速值(单位:10公里/小时),如果键入数字出错,可重新按B键,再键入正确的数字。
例如:欲从30公里/小时制动,则先按B键,再按数字0和数字3两个键。
按C键最高位LED显示C,然后按二位数字键,表示采样速度间隔,由最低二位LED 显示采样速度间隔值(单位:10公里/小时)。
如果键入数字出错,可重新按C键,再键入正确的数字,例如希望速度每变化10公里/小时得到一组相应的距离值和时间值,则可先按C键,再按数字0和数字1两个数字键。
3、准备试验:按开始键,奏输入完成音乐,LED显示汽车速度。
当汽车实测速度等于预置初速时,仪器发出有节奏的蜂鸣声,表示测试条件已具备。
可待汽车实际速度略大于预置初速后,做制动准备。
4、试验过程:按开始键,表示制动准备就绪。
当司机监视车速等于预置车速时迅速踩动踏板,测试过程自动开始,显示器仍然显示即时速度值,最低位LED 显示U。
入狱监视其它参数的变化情况,可用键盘改变显示内容。
按B键,显示距离值;按C键,显示时间值;按D键,显示减速度值;按A键,重新显示速度值。
GB 12676—1999汽车制动系统结构、性能和试验方法

GB 12676—1999前言本标准是根据联合国欧洲经济委员会(ECE)第13号法规《关于M、N、O类机动车制动的统一规定》和ISO 7634—1995《被牵引车辆气制动系试验方法》、ISO 7635—1991《道路车辆气压、气液制动性试验方法》和ISO 6597—1991《道路车辆液压制动系性能试验方法》等国际标准和法规对GB/T 12676—90《汽车制动性能道路试验方法》进行修订的。
修订后本标准做为强制性标准实施。
本标准中有关汽车制动系统结构、性能方面的内容在技术上是等效采用ECE第13号法规;有关汽车制动系统性能试验方法方面的内容在技术上是等效采用ISO 6597—1991、ISO 7634—1995和ISO 7635—1991标准。
该三项国际标准是按照ECE 第13号法规的要求制定的。
本标准是对GB/T 12676—90的修订,技术内容上较原标准增加很多,增加了对汽车制动系统结构功能和性能指标的要求,试验方法也进行了很大修改。
1 本标准实施之日起,下列条款12个月后实施:①第4.1.5条有关接续挂车的气动接头必须是双管路或多管路的要求。
②第5.1.4条有关制动性能必须在车轮不抱死的条件下的要求。
2 本标准实施之日起,下列条款24个月后实施。
①第4.1.4.3条中有关挂车气制动系和牵引车驻车制动系同时作用的要求。
②第4.2.5.1条有关传能装置中零部件失效时,必须保证继续向不受失效影响的其他部分供应能量的要求。
③第4.2.12.1条有关液面报警装置的要求。
④第4.2.12.2条有关液压制动系必须安装失效报警装置。
⑤第4.2.12.3条有关制动液类型的标志的要求。
⑥第4.2.13条有关储能装置中安装报警装置。
⑦第4.4条有关弹簧制动系的要求。
⑧第5.1.5条有关车辆状况应符合附录A的要求。
⑨第5.2.1.2条有关发动机接合的0型试验性能要求。
⑩第5.2.4条和第5.2.5条有关行车制动系Ⅱ型和ⅡA型试验的要求。
制动性能

要求
前轴(左右轮制动力差的最大值/左右轮最大制动力中的大值)
≤20%
后轴及其他轴(轴制动力≥轴荷*60%时,左右轮制动力差的最大值/左右轮最大制动力中的大值)
≤24%
后轴及其他轴(轴制动力<轴荷*60%时,左右轮制动力差的最大值/该轴轴荷)
≤8%
(3)制动协调时间合格标准
机动车制动形式
协调合格时间
3、每半年或一年对整机精度进行一次标定检查。
4、每季度应对压力传感器等进行一次彻底清扫。
5、每半年应打开仪表箱及强电控制箱,检查各种接插件、接线端是否松动,并清扫灰尘。
6、定期检查各部分连接电缆。
7、每周视情况清除滚筒表面污物。
B:平板制动
引车员以10km/h的速度驶上平板制动试验台、当汽车车轮胎在行驶到平板制动试验台的二分之一时实施制动、然后重新起步让机动车以10km/h左右的速度驶过,前板制动试验台的二分之一时实施驻车制动。检测过程中,设备区域内禁止站人。
五、日常维护
1、定期检查扭力箱油量。
2、每季度清洗一次套筒磙子链及链轮,清洗的加注机油。
三轮汽车、正三轮摩托车和拖拉机运输机组检验时,踏板力不应大于600 N根据以上规定制定本细则。
二、检测用设备
ZCS-130B轴(轮)重试验台
FZ-130G制动力试验台(大车线)
HPZS-10【C】平板制动试验台(小车线)
三、主要技术参数
ZCS-130B轴(轮)重试验台
1、最大允许轴荷:13000 kg
(a)满载检验时
①气压制动系:气压表的指示气压≤额定工作气压
②液压制动系:踏板力,乘用车≤500N
其它机动车≤700N
(b)空载检验时
①气压制动系:气压表的指示气压≤600kPa
4.2._汽车制动性能检测项目检测方法及有关标准

汽车制动性能检测方法与评价指标一、台试检验制动性能1 制动性能台试检验的主要检测项目:(1)制动力;(2)制动力平衡要求;(3)车轮阻滞力;(4)制动协调时间。
2 制动性能检测方法(1)用反力式滚筒试验台检验制动试验台滚筒表面应干燥,没有松散物质即油污。
驾驶员将车辆驶上滚筒,位置摆正,变速器置于空档,启动滚筒,使用制动,测取各轮制动力、每轴左右轮在制动力增长全过程中的制动力差、制动协调时间、车轮阻滞力和驻车制动力等参数值,并记录车轮是否抱死。
在测量制动时,为了获得足够的附着力以避免车轮抱死,允许在车辆上增加足够的附加质量和施加相当于附加质量的作用力(附加质量和作用力不计入轴荷;也可采取防止车轮移动的措施(例如加三角垫块或采取牵引等方法)。
(2)用平板制动试验台检验制动试验台平板表面应干燥,没有松散物质或油污。
驾驶员以5km/h~10km/h的速度将车辆对正平板台并驶上平板,置变速器于空档,急踩制动,使车辆停住,测得的各轮制动力、每轴左右轮在制动力增长全过程的制动力差、制动协调时间、车轮阻滞力和驻车制动力等参数值。
3 制动性能台试检验的技术要求(1)(1) 制动性能台试检验车轴制动力的要求见表4-1。
表4-1车辆类型制动力总和整车质量的百分比%前轴制动力于轴荷的百分比%空载满载 汽车、汽车列车605060*注:空、满载状况下测试应满足此要求。
(2)制动力平衡要求在制动力增长全过程中,左、右轮制动力差与该左、右轮中制动力大者比较对前轴不得大于20%,对于后轴不得大于24%。
(3)车轮阻滞力汽车和无轨电车车轮阻滞力均不得大于该轴轴荷5%。
(4)驻车制动性能检验当采用制动试验台检验车辆驻车制动的制动力时,车辆空载,乘坐一名驾驶员,使用驻车制动装置,驻车制动了的总和应不小于该车在测试状态下整车重量的20%。
对总质量为整备质量1.2倍以下的车辆此值为15%。
(5)机动车制动完全释放时间限制机动车制动完全释放时间(从松开制动踏板到制动消除所需要的时间)对单车不得大于0.8s 。
实验四 汽车制动性能试验

实验四汽车制动性能试验一、实验目的及要求1.实验目的了解汽车制动性能实验的要求;掌握汽车制动性能的道路实验方法;学习实验记录处理和分析实验结果;评价实验车辆制动性能的优劣。
培养学生理论联系实践的学习精神,增强学生动手能力。
2.实验要求(1)车辆条件对新车或大修后的车辆进行试验,试验前需进行一定行程的走合,新车一般按照制造厂的规定进行走合(行程一般为1000km~1500km)。
试验前还应注意各总成的技术状况和调整状况,应使之处于良好状态,如点火系、供油系、制动蹄鼓间隙、车轮轴承紧度、车轮定位、轮胎气压与标准值相差不超过±10kPa等。
对于车辆载荷,我国规定动力性试验时汽车为满载,货车内可以按规定载质量均匀放置沙袋;轿车、客车以及货车驾驶室的乘员可以重物替代,每位乘员的质量相当于65kg。
试验前汽车应通过运行而充分预热。
新车通常进行满载制动检验;在用车进行空载检验。
(2)道路条件动力性试验的大多数项目应在混凝土或沥青路面的直线段上进行。
要求路面平整、干燥、清洁、纵向坡度不大于0.1%,路长2-3km,宽不小于8m,测试路段长度200米。
(3)气候条件试验应避免在雨雾天进行,气压在99.3kPa~120kPa;气温在0℃~40℃;风速小于3m/s;相对湿度小于95%。
二、实验预习及准备(一)实验原理汽车的制动性能是汽车的主要性能,汽车的制动性试验主要是通过道路试验来评定。
通常从制动效能、制动效能恒定性和制动时的方向稳定性三方面评价。
一般要测定冷制动及高温下(热态)汽车的制动距离、制动减速度、制动时间等参数。
另外还要测定在转弯与变更车道时汽车制动的方向稳定性。
装有防抱制动系统的车辆,还要进行防抱制动性能试验。
1.磨合试验(1)磨合前的检查试验。
首先检查仪表及汽车的技术状况。
制动初速度为30km/h,保持制动减速度为3m/s2或保持相应的踏板力、管路压力值,直至车辆完全停止。
制动间隔为1.6km,制动次数不超过10次,记录管路压力和踏板力、减速度、制动初温。
汽车制动离合踏板总成技术要求

F507项目制动、离合踏板总成技术要求东风小康汽车有限公司产品技术中心F507项目制动、离合踏板总成除满足JT-FA-DP-2013-068_东风小康F505风光车型踏板及支架总成检查技术条件的要求外;还应满足下列要求..1.1 基本要求1.1.1 工作灵活性:踏板总成在整个工作行程上应轻便灵活;无异常噪声和干燥摩擦..当撤去踏板上的作用力之后;各踏板在回位弹簧的作用下;应能快速自行复位..1.1.2 外观:零件表面光洁、无氧化、裂纹、气泡、毛刺、严重划痕等缺陷;焊点正确牢固;不得有虚焊、夹渣、裂纹或未焊透等现象;无突起和其它缺陷及踏板支架各安装孔不得错位..1.1.3 踏板材料、厚度、踏板臂旋转角度、转动部位所涂润滑脂型号、各关重尺寸、制动与离合踏板之间间距及弹簧回位力等关键参数必须与会签的产品二维图规定的参数一致..1.2 性能要求踏板性能要求按QC/T788汽车踏板装置性能要求及台架试验方法验收1.2.1 纵向位移:在表1规定的法向力作用下;踏板或踏板总成应无裂纹或永久变形;并满足表1的规定..1.2.2 横向位移:在50N的横向力作用下;踏板或踏板总成应满足表2的规定..1.2.3 护套接合力:在±15N·m的倾斜力矩作用下;踏板护套应无脱落、断裂和其它异常如护套和踏板总成一起总成供货..1.2.4 噪音:踏板在整车装配后;工作过程中的噪音应不大于65dB;在全部试验过程中应无异常噪音..表1 踏板或踏板总成允许的纵向位移表2踏板或踏板总成允许的横向位移1.3 强度1.3.1 强度:在规定的法向推力作用下;踏板应无裂纹或破坏等缺陷;并满足规定的技术要求;详见表3所示..1.3.2 破坏试验:踏板或踏板总成发生功能或结构损坏时的载荷应满足表4的规定..表3 踏板或踏板总成强度要求表4 踏板或踏板总成发生功能或结构损坏时的载荷要求1.4 温度适应性1.4.1 高温工作性:在80±2℃的环境温度中工作时;不得有干涉拉挂现象和异常响声..1.4.2 低温工作性:在-40±2℃的环境温度中工作时;不得有干涉拉挂现象和异常响声..1.4.3 护套冷冲击:踏板护套在进行冷冲击试验后;应无裂纹或其它异常..1.5 耐久性1.5.1 在耐久性试验过程中应无裂纹、噪声、明显的永久变形和其它异常..1.5.2 耐久性试验后;踏板装置在50N±1N正反两方向纵向力作用下的纵向位移不应大于4mm;在50N±1N正反两方向侧向力作用下的侧向位移不应大于6mm..1.6 抗扭性能:在制动踏板上施加15N·m±1 N·m正反两方向的旋转力矩;制动踏板和焊缝应无裂纹或损坏等缺陷..1.7 表面涂层耐腐蚀性:经中性盐雾试验48h后;无基体腐蚀;不得有直径大于2.0mm的腐蚀点;不得产生膨胀、剥落及涂膜软化;允许有微小和分散的腐蚀点;焊缝和螺纹处的腐蚀可不考虑..1.8 踏板开关基本要求:开关示意图:表5固定开关;并按图A所示施加轴向和径向力1.9踏板开关试验要求:表6试验模式测试电压:DC14V±0.5V 无负载测试周期:300个周期。
汽车刹车踏板 标准

汽车刹车踏板标准
汽车刹车踏板(Brake Pedal)是用于控制汽车制动系统的重要组件。
虽然没有统一的国际标准规定汽车刹车踏板的具体尺寸和形状,但通常遵循一些基本原则和设计考虑,以确保安全和舒适性。
一般来说,汽车刹车踏板的设计应当符合以下标准和原则:
1.尺寸和形状:刹车踏板应当具有足够的宽度和长度,以方便驾驶员在不同驾驶条件
下轻松操作。
通常情况下,踏板宽度应适中,足够驾驶员在穿着不同鞋类时都能够轻松操作。
2.防滑设计:踏板表面通常设计成防滑纹理或具有抗滑性能,以确保驾驶员即使在潮
湿或多雨的环境下,也能够牢固地踩踏并控制制动。
3.力度和灵敏度:踏板需要具备适当的力度和灵敏度,这意味着它不应过于僵硬或过
于松弛,确保驾驶员能够准确感知和控制刹车的力度。
4.安全考虑:刹车踏板的设计应当符合安全标准,确保在紧急制动情况下,驾驶员能
够迅速做出反应并施加适当的力度。
5.可靠性和耐久性:刹车踏板必须具有足够的耐久性和可靠性,能够在长期使用中保
持稳定性和性能。
需要指出的是,不同车型和制造商可能会在刹车踏板的设计上有所差异,但一般都会遵循类似的基本原则和安全考虑。
在实际驾驶中,刹车踏板的设计应该满足驾驶员的操作习惯和舒适性需求,以确保安全和可靠的驾驶体验。
制动性能检测的基础知识

制动性能检测的基础知识汽车制动性能好坏,是安全行车最重要的因素之一,因此也是汽车检测诊断的重点。
汽车具有良好的制动性能,遇到紧急情况,可以化险为夷;在正常行驶时,可以提高平均行驶速度,从而提高运输生产效率。
一、对制动系的技术要求汽车制动系应具有行车制动、应急制动和驻车制动三大基本功能。
①行车制动系必须使驾驶员能控制车辆行驶,使其安全、有效地减速和停车。
行车制动装置的作用应能在各轴之间合理分配,以充分利用各轴的垂直载荷。
应急制动必须在行车制动系有一处失效的情况下,在规定的距离内将车辆停住。
应急制动可以是行车制动系统具有应急特性或是同行车制动分开的独立系统(注意应急制动不是行车制动中的急速踩下制动踏板)。
驻车制动应能使车辆即使在没有驾驶员的情况下,也能停放在上、下坡道上。
②制动时汽车的方向稳定性,即制动时不发生跑偏、侧滑及失去转向的能力。
③制动平稳。
制动时制动力应迅速平稳地增加;在放松制动踏板时,制动应迅速消失,不拖滞。
④操纵轻便。
施加于制动踏板和停车杠杆上的力不应过大,以免造成驾驶员疲劳。
⑤在车辆运行过程中,不应有自行制动现象。
⑥抗热衰退能力。
汽车在高速或下长坡连续制动时,由于制动器温度过高导致摩擦系数降低的现象称为热衰退。
要求制动系的热稳定性好,不易衰退,衰退后能较快地恢复。
⑦水湿恢复能力。
汽车涉水,制动器被水浸湿后,应能迅速恢复制动的能力。
TOP二、制动系常见故障1、制动失效。
即制动系出现了故障,完全丧失了制动能力。
2、制动距离延长,超出了允许的限度。
3、制动跑偏。
是指汽车直线行驶制动时,转向车轮发生自行转动,使汽车产生偏驶的现象。
由于汽车制动时,偏离了原来的运行轨迹,因而常常是造成撞车、掉沟,甚至翻车等事故的根源,所以必须予以重视。
引起跑偏的因素,就制动系而言,一是左右轮制动力不等;二是左右轮制动力增长速度不一致。
其中特别是转向轮,因此要对制动力增长全过程的左右轮制动力差作出规定,且对前后轴车轮的要求不同。
- 1、下载文档前请自行甄别文档内容的完整性,平台不提供额外的编辑、内容补充、找答案等附加服务。
- 2、"仅部分预览"的文档,不可在线预览部分如存在完整性等问题,可反馈申请退款(可完整预览的文档不适用该条件!)。
- 3、如文档侵犯您的权益,请联系客服反馈,我们会尽快为您处理(人工客服工作时间:9:00-18:30)。
制动踏板性能及试验要求
发布实施
发布
目录
前言 (1)
1范围 (2)
2规范性引用文件 (2)
3术语和定义 (2)
4性能要求 (3)
5试验相关要求 (4)
6试验方法 (4)
前言
本标准按照GB/T1.1—2020给出的规则起草。
本标准为首次发布。
制动踏板性能及试验要求
1范围
本标准规定了制动踏板的技术要求、试验方法。
2规范性引用文件
下列文件对于本文件的应用是必不可少的。
凡是注日期的引用文件,仅注日期的版本适用于本文件。
凡是不注日期的引用文件,其最新版本(包括所有的修改单)适用于本文件。
GB/T5620道路车辆汽车和挂车制动名词术语及其定义
GB/T10125—2012人造气氛腐蚀试验盐雾试验
QC/T788汽车踏板装置性能要求及台架试验方法
3术语和定义
下列术语和定义适用本文件。
3.1纵向位移
在垂直于踏板表面、过踏板几何中心点正反两方向纵向力P1作用下,踏板产生的垂直位移量。
参考图1。
图1纵向位移示意
3.2侧向位移
在平行于踏板表面、过踏板几何中心点正反两方向侧向力T作用下,踏板产生的水平位移量。
参考图2。
图2侧向位移示意图
3.3刚度
在垂直于踏板表面、过踏板几何中心点纵向力P2作用下.踏板产生的垂直变形量。
参见图3。
4性能要求
4.1一般要求
4.1.1工作灵活性:踏板装置在整个工作行程中应动作灵活,无异常响声。
4.1.2外观:零件表面光洁,无裂纹、毛刺、划痕等缺陷;焊接部位不得有漏焊、气孔、烧穿、咬肉等缺陷。
4.2基本要求
4.2.1纵向位移:在(50±2)N正反两方向的纵向力作用下,踏板的纵向位移应小于或等于2.0mm。
4.2.2侧向位移:在(50±2)N正反两方向的侧向力作用下,踏板的侧向位移应小于或等于4.0mm。
4.2.3踏板刚度:在表1规定的纵向力P作用下,踏板的纵向位移应小于或等于
5.0mm。
表1刚度试验施加在踏板上的纵向力
踏板种类制动踏板(乘用车)制动踏板(其他汽车)
施加在踏板几何
中心点十的纵向力P(500土10)N(700土15)N
4.3温度适应性
4.3.1髙温工作性:在(80±2)℃的环境温度中试验时,踏板装置不得有干涉、卡阻现象和异常响声。
4.3.2低温工作性:在(-40±2)℃的环境温度中试验时,踏板装置不得有干涉、卡阻现象和异常响声。
4.4抗扭性能
在踏板上施加(15±l)N・m正反两方向的旋转力矩,踏板和焊缝应无裂纹或损坏等缺陷。
4.5强度
踏板装宜在表2规定的纵向力P作用下,踏板表面永久变形量小于或等于5.0mm,并且无裂纹或损坏等缺陷。
表2强度试验施加在踏板上的纵向力
图3刚度变形量示
踏板种类制动踏板
施加在踏板几何中心点上的纵向
(2000±500)N
力P
4.6工作耐久性
4.6.1在工作耐久性试验过程中,踏板装置不应发生影响功能的变形,不应出现裂纹或其他异常情况。
4.6.2工作耐久性试验后,踏板装置的纵向位移测量值不应大于4.0mm,侧向位移测量值不应大于6.0mm。
4.7振动耐久性
4.7.1耐振动性试验后,踏板装置不应发生影响功能的变形,不应出现裂纹或其他异常情况。
4.7.2耐振动性试验后,踏板装置的纵向位移和侧向位移测量值应分别满足4.2.1和4.2.2的要求。
4.7.3对带制动灯开关的踏板装置,在耐振动性试验过程中,制动灯开关不应触发。
4.8耐腐蚀性
经72h盐雾试验后,基体无红锈,涂层无气泡、开裂、脱落现象,允许有微小和分散的腐蚀点,焊接和螺纹处的腐蚀可不考虑,划痕处单边扩蚀≤2mm。
5试验相关要求
5.1试验设备
5.1.1试验所用仪器仪表、设备应满足相关项冃试验条件的要求,不应对试验样品功能产生不利的影响。
5.1.2性能测试用测量装置的精度等级不应低于0.5级,寿命试验用测量装置的精度等级不应低于1.5级。
5.2试验条件
5.2.1测试前应对样品预动作5次。
5.2.2除另有规定外,试验环境温度为(8〜38)℃。
5.3试验样品
每项试验的样品数量不宜少于3件。
除工作耐久性、振动耐久性、耐腐蚀性试验外。
其余样品试验前需卸除回位弹簧。
6试验方法
6.1基本性能
6.1.1纵向位移
6.1.1.1将被试样品按实车状态固定在试验装置上,踏板臂在踏板设计全行程的中间行程位置刚性固定。
6.1.1.2在垂直于踏板表面、过踏板几何中心点处施加(50±2)N的纵向力,保持5s,并将此位置确
定为踏板纵向位移测量零点,然后解除纵向力;再反向施加(50±2)N 的纵向力,保持5s 后,测量相对于测量零点踏板的纵向位移量。
6.1.2侧向位移
6.1.2.1样品安装状态同6.1.1.1,侧向位移测量示意图见图5。
6.1.2.2在踏板一侧与水平面平行且过踏板几何中心点施加(50±2)N 的侧向力,保持5s。
并将此位置确定为踏板侧向位移测量零点,然后解除侧向力;再反向施加(50±2)N 的侧向力,保持5s 后,测量相对于测量零点踏板的水平位移量。
图5侧向位移测量示意图
6.1.3刚度
6.1.3.1样品安装和固定方式同6.1.1.1。
6.1.3.2在垂直踏板表面、过踏板几何中心点处预先施加(10〜20)N 纵向力,并将此位置确定为踏板纵向位移的零点。
6.1.3.3对踏板装置施加表1规定的纵向力,保持5s 后解除纵向力,共进行5次。
测量并记录第5次施加纵向力时,踏板的纵向位移量。
6.2温度适应性
6.2.1
高温适应性
1一位移传憊器;2—踏板臂位置固定装暹;3—加载装置;4拉压力传感器;5—夹紧装置
图4纵向位移测量示意图
1一气缸;2—压力传感器;3—夹紧装置;4-位移传感器
6.2.1.1将被试样品在(80±2)℃的环境温度中放置4h,然后在此环境温度下使踏板装置在全行程下动作5次,观察踏板在运动过程中是否有干涉、卡阻现象和异常响声。
6.2.1.2将被试样品冷却至室温后按6.1.1和6.1.2进行纵向位移和侧向位移测量。
6.2.2低温适应
除环境温度为(-40±2)℃外,其余同6.2.1。
6.3抗扭性能
按实车状态将被试样品安装在试验装置上,然后按图6所示,以踏板与踏板杠杆的主焊缝中心线为轴线,在踏板上施加相当于(l52±l)N・m的正反两方向旋转力矩。
然后检査焊缝和踏板装置有无裂纹或损坏等异常现象。
图6抗扭性能测量示意图
6.4强度
6.4.1样品安装和固定方式同6.1.1.1。
6.4.2在垂直于踏板表面、过踏板几何中心点处预先施加(10〜20)N的纵向力。
将此位置确定为踏板位移测量零点。
6.4.3按表2规定对踏板装置施加纵向力,保持5s后解除纵向力,共进行5次。
然后测量相对于测量零点踏板的永久变形量,检査样品有无裂纹或损坏等缺陷。
6.5工作耐久性
6.5.1制动踏板耐久性
6.5.1.1将被试制动踏板装置按实车状态安装在试验装置上,将踏板输岀端与实车配套产品相连接。
6.5.1.2制动踏板工作耐久性试验见表3,先按图7所示的P1加载方向和加载位置进行50万次工作耐久性试验,然后按P2加载方向和加载位置进行50万次工作耐久性试验。
表3制动踏板工作耐久性试验条件
纵向力/N
试验频率/Hz踏板行程
乘用车商用车
500±20700±200.3〜1.0设计行程的80%±5%
6.5.1.3试验过程中,注意观察样品足否发生阻滞和卡死等异常悄况,各连接件有无松动,各零件有无危及功能的变形和损坏。
6.5.1.4试验结束后,按6.1.1和6.1.2进行纵向位移和侧向位移测量。
图7踏板耐久性加力位置示意图
6.5.2振动耐久性
6.5.2.1将被试样品按实车安装状态安装在振动试验台上.然后以44m/s2的振动加速度和33.3Hz的振动频率进行107次垂直方向的振动试验。
6.5.2.2试验结束后,按6.1.1和6.1.2进行纵向位移和侧向位移测量。
6.5.2.3检査并记录各连接件有无松动及各零部件变形和损坏情况。
6.6耐腐蚀性
将被试样品按实车安装状态放置在盐雾试验箱内,然后按GBAT10125—2012规定的中性盐雾试验要求进行72h的连续喷雾试验。
试验结束后,将样品从盐雾试验箱内取出,用不高于40℃的清洁流水轻轻清洗,除去样品表面盐沉积物,然后在2min内用空气吹干,检査并记录样品表面的腐蚀情况。
基体无红锈,涂层无气泡、开裂、脱落现象,允许有微小和分散的腐蚀点,焊接和螺纹处的腐蚀可不考虑,划痕处单边扩蚀≤2mm。