橡胶的密炼及开炼
橡套软电缆生产工序:开炼和混炼工艺文件

开炼机橡胶塑炼:
本卡片适用于橡皮绝缘电缆的素炼工序。
2工艺技术要点:
2.1塑炼胶应用国标1#,绝缘胶种应采用内芯胶,护套胶种应采用外皮胶。
2.2塑炼用丁苯胶应采用含有25%以上苯乙烯的松香丁苯或充油丁苯。
2.3天然胶塑炼前应用水将外皮冲洗干净,并在30C —60C 的环境中温胶24~36小时。
2.4天然橡胶和丁苯橡胶掺合应均匀,塑炼胶应表面光滑,贴辊面应有亮皱纹。
2.5塑炼过程中的辊温、辊距应符合工艺卡规定。
密炼机橡胶塑炼和密炼:
XXX 公司
橡套软电缆橡胶开炼和混炼工序
工艺卡片
开炼机橡胶混炼:
XXX 公司
橡套软电缆橡胶开炼和混炼工序
工艺卡片
XXX公司橡套软电缆橡胶开炼和混炼工序文件编号| Q/JY.GK03-2020
工艺卡片共3页n—第页。
密炼车间工艺流程图

密炼车间工艺流程图一、引言密炼车间是橡胶制品生产过程中的重要环节,通过将橡胶原料与各种添加剂进行混合,以达到预定的物理和化学性能,为后续工序提供高质量的橡胶混炼料。
本文将详细介绍密炼车间的工艺流程图,包括原料准备、混炼、加工和成品检验等环节。
二、工艺流程图1. 原料准备a. 原料仓库:存放橡胶原料、填充剂、增塑剂等。
b. 称量室:按照配方要求,将所需原料进行称量。
c. 搅拌机:将不同种类的橡胶原料进行混合。
2. 混炼a. 密炼机:将原料与添加剂进行混合。
b. 加热系统:提供适宜的温度和压力,促进原料的混合。
c. 冷却系统:冷却混炼后的橡胶混炼料。
3. 加工a. 开炼机:将混炼后的橡胶料进行破碎和塑化。
b. 切胶机:将橡胶料切成适当大小的块状。
c. 滚筒破碎机:将橡胶块破碎成小颗粒。
4. 成品检验a. 物理性能测试:对成品橡胶料进行硬度、拉伸强度等物理性能测试。
b. 化学性能测试:对成品橡胶料进行硫含量、酸值等化学性能测试。
c. 外观检查:对成品橡胶料的外观进行检查,确保无明显瑕疵。
5. 成品存储a. 成品仓库:存放合格的成品橡胶料。
b. 包装:将成品橡胶料进行包装,以便运输和销售。
三、流程图详细说明1. 原料准备流程a. 橡胶原料、填充剂、增塑剂等从原料仓库取出。
b. 按照配方要求,将所需原料进行称量。
c. 称量后的原料送入搅拌机进行混合。
2. 混炼流程a. 称量后的原料送入密炼机。
b. 密炼机内提供适宜的温度和压力,促进原料的混合。
c. 混炼后的橡胶混炼料经过冷却系统冷却。
3. 加工流程a. 混炼后的橡胶料送入开炼机进行破碎和塑化。
b. 塑化后的橡胶料送入切胶机进行切割。
c. 切割后的橡胶料送入滚筒破碎机进行破碎成小颗粒。
4. 成品检验流程a. 从生产线上取出样品进行物理性能测试。
b. 从生产线上取出样品进行化学性能测试。
c. 对成品橡胶料的外观进行检查,确保无明显瑕疵。
5. 成品存储流程a. 合格的成品橡胶料送入成品仓库进行存储。
橡胶密炼机与混炼工艺.

橡胶密炼机与混炼工艺1.密炼机密闭式炼胶机简称密炼机,主要用于橡胶的塑炼和混炼。
密炼机是一种设有一对特定形状并相对回转的转子、在可调温度和压力的密闭状态下间隙性地对聚合物材料进行塑炼和混炼的机械,主要由密炼室、转子、转子密封装置、加料压料装置、卸料装置、传动装置及机座等部分组成。
密炼机是在开炼机的基础上发展起来的一种高强度间隙性的混炼设备。
自1916年出现真正意义上的Banbury(本伯里型密炼机后,密炼机的威力逐渐被人们所认识,它在橡胶混炼过程中显示出来比开炼机优异的一系列特征,如:混炼容量大、时间短、生产效率高;较好的克服粉尘飞扬,减少配合剂的损失,改善产品质量与工作环境;操作安全便利,减轻劳动强度;有益于实现机械与自动化操作等。
因此,密炼机的出现是橡胶机械的一项重要成果,至今仍然是塑炼和混炼中的典型的重要设备,仍在不断的发展和完善。
密炼机基本知识基本结构密炼机一般由密炼室、两个相对回转的转子、上顶栓、下顶栓、测温系统、加热和冷却系统、排气系统、安全装置、排料装置和记录装置组成。
转子的表面有螺旋状突棱,突棱的数目有二棱、四棱、六棱等,转子的断面几何形状有三角形、圆筒形或椭圆形三种,有切向式和啮合式两类。
测温系统是由热电偶组成,主要用来测定混炼过程中密炼室内温度的变化;加热和冷却系统主要是为了控制转子和混炼室内腔壁表面的温度。
工作原理密炼机工作时,两转子相对回转,将来自加料口的物料夹住带入辊缝受到转子的挤压和剪切,穿过辊缝后碰到下顶拴尖棱被分成两部分,分别沿前后室壁与转子之间缝隙再回到辊隙上方。
在绕转子流动的一周中,物料处处受到剪切和摩擦作用,使胶料的温度急剧上升,粘度降低,增加了橡胶在配合剂表面的湿润性,使橡胶与配合剂表面充分接触。
配合剂团块随胶料一起通过转子与转子间隙、转子与上、下顶拴、密炼室内壁的间隙,受到剪切而破碎,被拉伸变形的橡胶包围,稳定在破碎状态。
同时,转子上的凸棱使胶料沿转子的轴向运动,起到搅拌混合作用,使配合剂在胶料中混合均匀。
二、炼胶工艺

二、炼胶工艺本工艺主要包括有混炼胶的(密)混炼、热炼、加硫、返炼等四个工序的生产工艺。
通过对生胶及其配合剂的混合、分散、热处理等过程,使配合剂完全而均匀地分散到生胶中,并产生结合橡胶,同时消除结构化现象,制备出性能均匀、一致,具有一定工艺可塑性的混炼胶,供注射成型使用。
生产过程所使用的设备必须是经检查完好且正常运转。
1.操作程序1.1(密)混炼工艺按照产品的配方及混炼工艺要求,将各种配合剂(硫化剂除外)通过密炼机均匀分散到生胶(硅橡胶)中。
1.1.1 开机前检查机器、设备、风压及冷却水等是否正常。
检查清理(密)混炼室、转子及上顶栓等部件,清理干净余胶或杂物。
一切正常方可开机操作。
1.1.2 通知配料人员将已配好的生胶、配合剂、粉料、白碳黑等材料运到混炼作间,经检查无误后停放待用。
1.1.3 按上表中的程序进行胶料的(密)混炼操作。
1.2 薄通工艺对密炼机排下的胶料进行补充加工,使胶料分散更均匀。
1.2.1 每辊混炼胶按重量均匀分成二份,每份混炼胶称作“一辊胶”(约为20kg)。
1.2.2 清理开炼机辊筒、挡板及盛料盘,应无粉尘、油污或杂物,无上辊胶留下的余胶。
1.2.3 启动开炼机,通冷却水,调节辊距至≤0.5mm,辊温≤50℃,将一辊混炼胶分成适当的小块逐一投入开炼机进行薄通。
1.2.4 每辊胶薄通次数不少于3遍,但不多于10遍,每遍操作时间约为15分钟。
1.2.5 薄通结束后,调大辊距,将胶料压片下料停放,胶料须存放8小时后方可投入下工序使用。
1.3 热炼工艺对未加硫的混炼胶进行热处理,通过热炼时辊筒传递的热量,使混炼胶内有害的低分子物质及水份能够充分挥发,并消除胶料的结构化现象,同时使配合剂在胶料中进一步均匀分散。
1.3.1 清理开炼机辊筒、挡板及盛料盘,应无粉尘、油污或杂物,无上辊胶留下的余胶。
1.3.2 启动开炼机,调节配电柜的控制电流(或温度控制仪器表),将辊筒温度预热至120~135℃。
橡胶密炼工艺
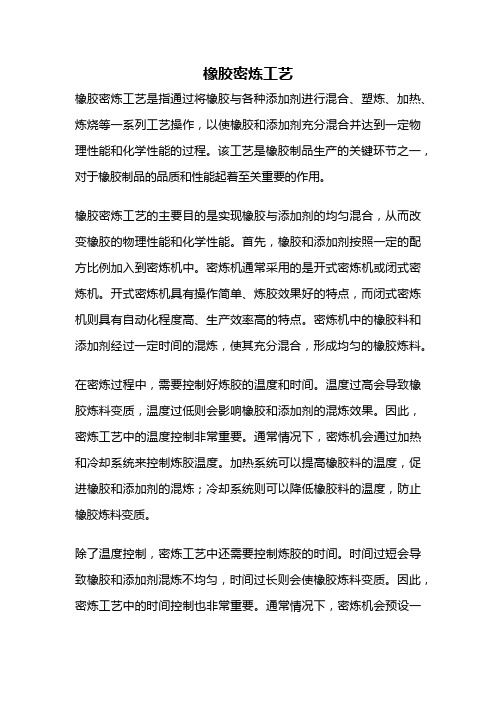
橡胶密炼工艺橡胶密炼工艺是指通过将橡胶与各种添加剂进行混合、塑炼、加热、炼烧等一系列工艺操作,以使橡胶和添加剂充分混合并达到一定物理性能和化学性能的过程。
该工艺是橡胶制品生产的关键环节之一,对于橡胶制品的品质和性能起着至关重要的作用。
橡胶密炼工艺的主要目的是实现橡胶与添加剂的均匀混合,从而改变橡胶的物理性能和化学性能。
首先,橡胶和添加剂按照一定的配方比例加入到密炼机中。
密炼机通常采用的是开式密炼机或闭式密炼机。
开式密炼机具有操作简单、炼胶效果好的特点,而闭式密炼机则具有自动化程度高、生产效率高的特点。
密炼机中的橡胶料和添加剂经过一定时间的混炼,使其充分混合,形成均匀的橡胶炼料。
在密炼过程中,需要控制好炼胶的温度和时间。
温度过高会导致橡胶炼料变质,温度过低则会影响橡胶和添加剂的混炼效果。
因此,密炼工艺中的温度控制非常重要。
通常情况下,密炼机会通过加热和冷却系统来控制炼胶温度。
加热系统可以提高橡胶料的温度,促进橡胶和添加剂的混炼;冷却系统则可以降低橡胶料的温度,防止橡胶炼料变质。
除了温度控制,密炼工艺中还需要控制炼胶的时间。
时间过短会导致橡胶和添加剂混炼不均匀,时间过长则会使橡胶炼料变质。
因此,密炼工艺中的时间控制也非常重要。
通常情况下,密炼机会预设一个炼胶时间,到达预设时间后自动停机,以确保炼胶时间的准确控制。
在橡胶密炼工艺中,还需要添加一些助剂来改善橡胶的加工性能和使用性能。
常用的助剂有硫化剂、促进剂、防老剂等。
硫化剂可以使橡胶在一定温度下发生硫化反应,使橡胶具有较好的耐热性和耐老化性;促进剂可以加快硫化反应速度,提高橡胶硫化的效果;防老剂可以延缓橡胶的老化速度,提高橡胶制品的使用寿命。
这些助剂的添加量和添加顺序也需要严格控制,以保证橡胶炼料的质量。
橡胶密炼工艺是一项复杂而精细的工艺,需要操作人员具备丰富的经验和专业知识。
在密炼过程中,需要不断监测和调整工艺参数,以确保橡胶炼料的质量。
同时,还需要定期维护和保养密炼机设备,以确保设备的正常运行和使用寿命。
开炼机混炼工艺和密炼机混炼工艺
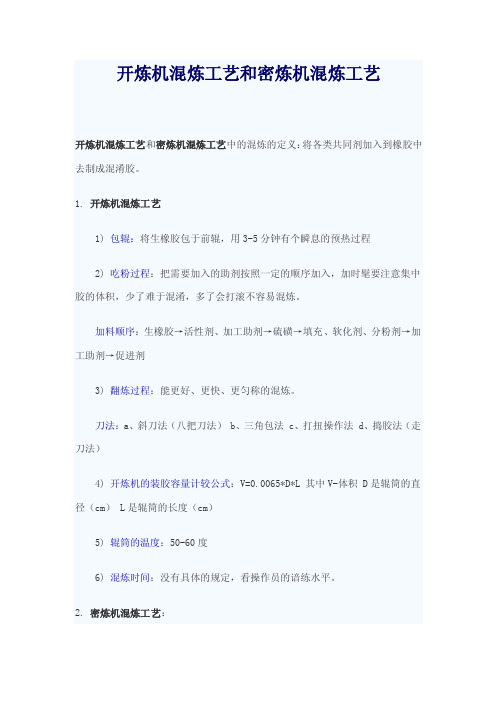
开炼机混炼工艺和密炼机混炼工艺
开炼机混炼工艺和密炼机混炼工艺中的混炼的定义:将各类共同剂加入到橡胶中去制成混淆胶。
1. 开炼机混炼工艺
1) 包辊:将生橡胶包于前辊,用3-5分钟有个瞬息的预热过程
2) 吃粉过程:把需要加入的助剂按照一定的顺序加入,加时髦要注意集中胶的体积,少了难于混淆,多了会打滚不容易混炼。
加料顺序:生橡胶→活性剂、加工助剂→硫磺→填充、软化剂、分粉剂→加工助剂→促进剂
3) 翻炼过程:能更好、更快、更匀称的混炼。
刀法:a、斜刀法(八把刀法) b、三角包法 c、打扭操作法 d、捣胶法(走刀法)
4) 开炼机的装胶容量计较公式:V=0.0065*D*L 其中V-体积 D是辊筒的直径(cm) L是辊筒的长度(cm)
5) 辊筒的温度:50-60度
6) 混炼时间:没有具体的规定,看操作员的谙练水平。
2. 密炼机混炼工艺:
1) 一段混炼:一次混炼好,混炼的程序:生橡胶→小料→补强剂→软化剂→排胶→压片机加硫磺、促进剂→下片→冷却停放。
2) 二段混炼:分两段混炼第橡胶生产工艺一段:生橡胶→小料→补强剂→软化剂→排胶→压片→冷却第二段:母胶→硫磺、促进剂→压片→冷却。
橡胶工艺流程
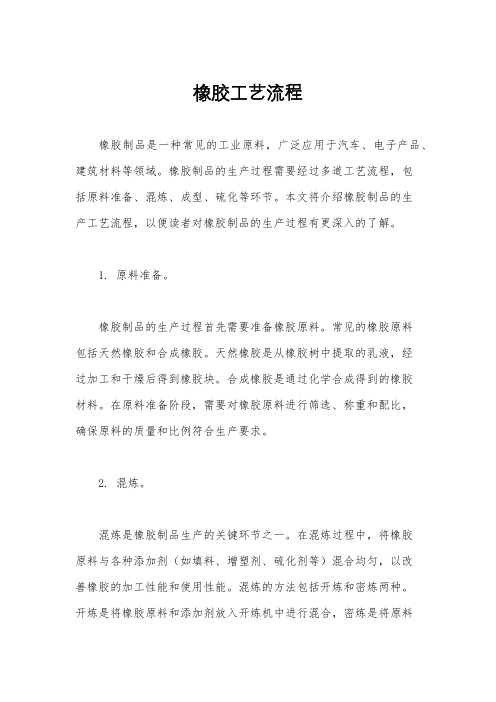
橡胶工艺流程橡胶制品是一种常见的工业原料,广泛应用于汽车、电子产品、建筑材料等领域。
橡胶制品的生产过程需要经过多道工艺流程,包括原料准备、混炼、成型、硫化等环节。
本文将介绍橡胶制品的生产工艺流程,以便读者对橡胶制品的生产过程有更深入的了解。
1. 原料准备。
橡胶制品的生产过程首先需要准备橡胶原料。
常见的橡胶原料包括天然橡胶和合成橡胶。
天然橡胶是从橡胶树中提取的乳液,经过加工和干燥后得到橡胶块。
合成橡胶是通过化学合成得到的橡胶材料。
在原料准备阶段,需要对橡胶原料进行筛选、称重和配比,确保原料的质量和比例符合生产要求。
2. 混炼。
混炼是橡胶制品生产的关键环节之一。
在混炼过程中,将橡胶原料与各种添加剂(如填料、增塑剂、硫化剂等)混合均匀,以改善橡胶的加工性能和使用性能。
混炼的方法包括开炼和密炼两种。
开炼是将橡胶原料和添加剂放入开炼机中进行混合,密炼是将原料放入密炼机中进行混合。
混炼过程需要控制时间、温度和压力,确保橡胶混合均匀。
3. 成型。
成型是将混炼后的橡胶料加工成所需形状的过程。
常见的成型方法包括挤出、压延和模压。
挤出是将橡胶料挤出成型,压延是将橡胶料通过压延机加工成片状,模压是将橡胶料放入模具中进行成型。
成型过程需要根据产品要求选择合适的成型方法,并控制温度、压力和速度,确保成型品质量符合要求。
4. 硫化。
硫化是橡胶制品生产的最后一个环节。
在硫化过程中,将成型后的橡胶制品放入硫化炉中进行硫化处理,使橡胶分子间发生交联,提高橡胶的强度和弹性。
硫化过程需要控制温度、压力和硫化时间,确保橡胶制品硫化均匀,达到设计要求的性能指标。
总结。
橡胶制品的生产工艺流程包括原料准备、混炼、成型和硫化四个主要环节。
每个环节都需要严格控制生产参数,确保橡胶制品的质量和性能符合要求。
同时,随着科技的进步,橡胶制品的生产工艺也在不断创新和改进,以满足不同领域对橡胶制品的需求。
希望本文能为读者对橡胶制品的生产工艺有所了解,并对橡胶制品的应用和发展有所启发。
橡胶炼胶车间:开炼机和密炼机

橡胶炼胶车间:开炼机和密炼机炼胶的三个阶段:主要包括三个阶段:①生胶加热。
即将已塑炼的生胶在机上再次重炼,加热软化,并加入其他聚合物共混。
②加配合剂。
一般先加软化剂、硬脂酸等,然后加入粉料和炭黑等(炭黑也可预先和部分生胶先单独混为母炼胶)。
硫磺一般在混炼的最后,或在胶料经停放后,于第二次重炼时再加入。
③混炼均匀和下片。
当所有配合剂添加完毕后,应再继续翻炼,使混合均匀,然后卸下胶片。
橡胶开炼机(开放式炼胶机),靠手动动操作,其炼胶原理是橡胶在旋转辊筒的间隙中,在较高温度下,反复受到剪切作用。
密闭式炼胶机混炼过程:密闭式炼胶机的转子表面和混炼室壁面之间的间隙大小,随转子转动有很大范围的变化,对胶料产生强烈的剪切作用。
混炼效果比开放式炼胶机大得多,各种粉料配合剂在混炼室内和胶料混合而不飞扬在外,而且自动仪表控制混炼过程。
开炼机与密炼机有哪些区别?1、开炼机是双辊机,利用不同转速相对运动的两个辊产生剪切力来塑炼。
操作是要不断的进行打三角包的操作。
密炼机是利用内部的设计好的桨叶相对运动时产生空间的规律性收缩来产生剪切力。
2、开炼机(开放式炼胶机)靠人工打胶,每个批次每个炼胶工有不同,炼出来的胶不稳定;开炼机结构简单成本低,但是劳动强度大,污染大,对工人身体伤害大。
密炼机(密闭式炼胶机)机器混炼机,稳定,效率快,产能高。
3、开炼机结构简单,易清洗;密炼机结构复杂,不易清洗4、开炼机不安全,裸露在外面;密炼机安全性高,密闭式。
5、开炼机散热快,不易死料;密炼机不易散热6、开炼机可以出片,密炼机不能出片7、开炼机价格便宜,密炼机较贵,但是可以加热,可抽真空,还有加压密炼机可以用来处理难塑化的材料。
劳动强度低适应性强。
开炼机与密炼机工艺的区别开炼机与密炼机工艺的不同,在炼胶时选择开炼机或密炼还是依据胶料的特性来选择的。
开炼机炼胶与密炼机炼胶是有很多不同的,并不单单是什么降低劳动强度、操作条件好等方面,如果密炼工艺没有设计好的话,工人是宁愿开炼机炼胶的,因为容易操作,已经很熟练了,炼出来的胶基本上是没有问题;而密炼出来的胶,虽然一次炼的料是开炼机的数倍,但是工艺没设计好,胶料出现焦烧或者分散不均报废,实际的劳动已经支出了,而且还浪费了原材料,还不得不重新混炼,因此如何设计好密炼机的工艺、严格控制温度是密炼机炼胶的一个主要问题,只有合理利用才能事半功倍。
橡胶的密炼及开炼.
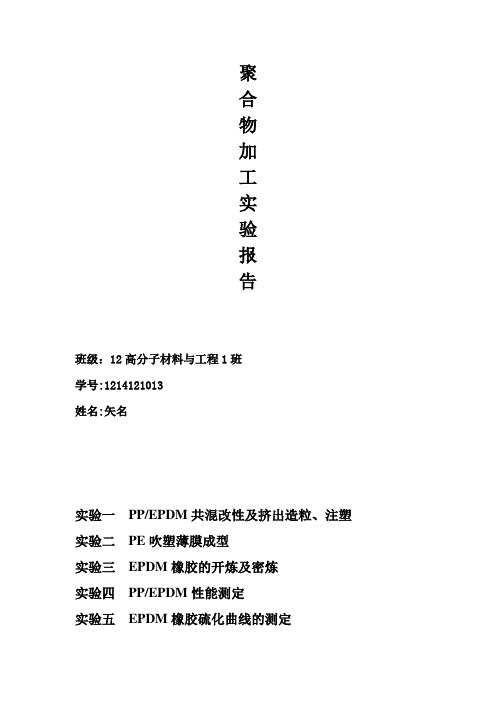
4. 吃粉过程中每加人一种配合剂后都要捣胶两次。在加入填充剂和补强剂时要让粉料自然地进入胶料中,使之与橡胶均约接触混合,而不必急于捣胶;同时还需逐步调宽辊距,使堆积胶保持在适当则范围内。待粉料全部吃进后,从中央处割刀分往两端,进行捣胶操作促使混炼均匀。
电控系统由电控箱、操作台和各种电器仪表组成,是整个机台的操作中心。
(2)台秤、游标卡尺,炼胶刀
图27-3
实验原料
天然橡胶
四.实验步骤:(图27-4)
图27-4
1. 开车前必须检查混炼室转子间有无杂物,上、下顶栓,仪表、信号装置等的完好,方可准备开车。
2. 开启主机、减速器和主电机等冷却系统的进水阀和排水阀。
本实验选用密炼机对天然橡胶进行机械法塑炼。生胶置于密炼机中,两转子相对回转,将来自加料口的物料夹住带入辊缝受到转子的挤压和剪切,穿过辊缝后碰到下顶拴尖棱被分成两部分,分别沿前后室壁与转子之间缝隙再回到辊隙上方。在常温(小于50℃)下反复受到机械力的作用,使分子链断裂,与此同时断裂后的大分子自由基在空气中氧化作用下,发生了一系列力学与化学反应,最终达到降解,生胶从原先高韧高弹性变为柔软可塑性,满足混炼的要求。此外,塑炼的时间、塑炼工艺操作方法及是否加入塑解剂也影响塑炼的效果。在绕转子流动的一周中,物料处处受到剪切和摩擦作用,使胶料的温度急剧上升,粘度降低。由于密炼机混炼时胶料受到的剪切作用比开炼机大得多,炼胶温度高,使得密炼机炼胶的效率大大高于开炼机。
压料装置部分由上顶栓及气缸等组成。安装在混炼室上面。
卸料装置部分由安装在混炼室下面的下顶栓和下顶栓锁紧机构组成。
传动装置部分由电机、弹性联轴节、减速器和齿形联轴节等组成。
密炼机的工作原理
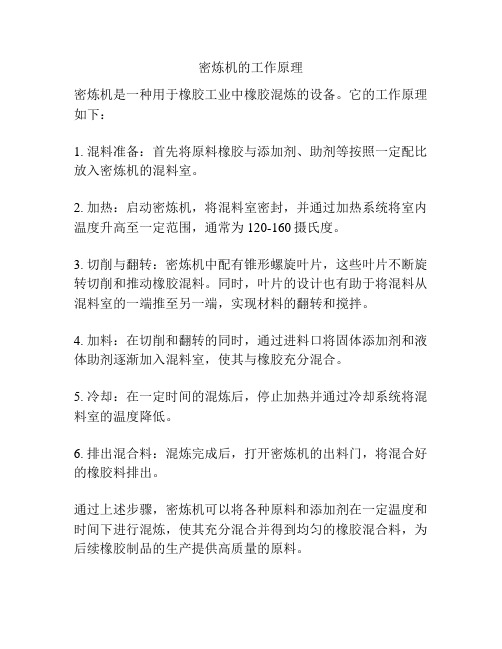
密炼机的工作原理
密炼机是一种用于橡胶工业中橡胶混炼的设备。
它的工作原理如下:
1. 混料准备:首先将原料橡胶与添加剂、助剂等按照一定配比放入密炼机的混料室。
2. 加热:启动密炼机,将混料室密封,并通过加热系统将室内温度升高至一定范围,通常为120-160摄氏度。
3. 切削与翻转:密炼机中配有锥形螺旋叶片,这些叶片不断旋转切削和推动橡胶混料。
同时,叶片的设计也有助于将混料从混料室的一端推至另一端,实现材料的翻转和搅拌。
4. 加料:在切削和翻转的同时,通过进料口将固体添加剂和液体助剂逐渐加入混料室,使其与橡胶充分混合。
5. 冷却:在一定时间的混炼后,停止加热并通过冷却系统将混料室的温度降低。
6. 排出混合料:混炼完成后,打开密炼机的出料门,将混合好的橡胶料排出。
通过上述步骤,密炼机可以将各种原料和添加剂在一定温度和时间下进行混炼,使其充分混合并得到均匀的橡胶混合料,为后续橡胶制品的生产提供高质量的原料。
橡胶产品生产工艺规程

橡胶产品生产工艺规程JW---- 橡胶产品生产工艺规程制订:审核:批准:批准日期:目录一、生胶的塑炼程序 (1)1、生胶塑炼前的准备工作 (1)2、开炼机的塑炼 (1)3、密炼机的塑炼 (1)4、塑炼胶的检验、冷却、停放 (1)二、混炼工序 (2)1、配合剂的加工 (2)2、配合剂的称量 (3)3、密炼机的混炼、开炼机的混炼 (4)4、无硫及和制备 (5)5、无硫胶的冷却、停放 (5)三、压片工序 (5)1、混炼胶的热炼和无硫胶的加硫 (4)2、压延机的压片、冷却 (4)3、胶片的裁断、质检 (5)4、半成品支座的冷压成型 (1)5、半成品胶片的验收、贮存………………………………….四、挤出工序 (7)1、混炼胶的热炼、下片 (7)2、挤出机工艺条件 (7)3、挤出操作 (8)4、挤出半成品的冷却、质检、包装…………………………….五、硫化工序 (9)1、止水带的硫化……………………………………………..2、支座的硫化………………………………………………..六、产品的质检、包装、储存……………………………………. 附录:橡胶止水带和板式橡胶支座的生产工艺流程图…………..一、生胶塑炼工序1、生胶塑炼前的准备工作(1)烘胶天然橡胶和氯丁橡胶在冬季温度低时变硬,为利于加工必须进行烘胶。
a、设备:半环形烘胶房b、烘胶条件:相对湿度:60~70%温度:天然胶50~60℃氯丁胶30~40℃时间:天然胶24~36小时氯丁胶4~6小时c、操作要点:把合格的生胶送入烘胶房摆放整齐,胶间适当留有距离30~40cm,这样有利于烘热,按先入先出的原则到规定时间必须取出。
(2)切胶将胶块清理干净,去掉包装物和杂质,在切胶机上切成6±2kg的三角块,进行塑炼。
2、开炼机塑炼为提高生胶可塑度,利于加工,对可塑性低的胶种进行塑炼,辊筒温度应控制在55℃以下。
调节冷却水,进行塑炼。
开炼机塑炼操作方法(XK-400、450开炼机);a、天然橡胶装胶量控制在40±5kg。
橡胶生产工艺流程

橡胶生产工艺流程橡胶生产工艺流程主要包括原料准备、混炼、模压、硫化等环节。
以下是一个大致的橡胶生产工艺流程。
首先是原料准备环节。
橡胶的主要原料有天然橡胶和合成橡胶,此外还需要添加剂如促进剂、防老化剂、增塑剂等。
原料需要按照一定的配方比例加入到生产设备中。
接下来是混炼环节。
混炼是指将原料进行机械拌和工艺,使其在一定温度条件下充分混合,同时提高橡胶的弹性和可塑性。
混炼一般分为开炼和密炼两个阶段。
开炼时将橡胶原料与一些添加剂加入到混炼机中,通过转动的刀叶将原料进行充分切割、破碎,使之达到均匀分散的目的。
密炼则是在开炼的基础上,进一步加入剂料进行混炼,使橡胶获得更好的塑胶性态。
然后是模压环节。
模压是将混炼好的橡胶放入到模具中,经过加热和压力作用,使橡胶在模具中变形成所需的形状。
模压通常采用加热板式压力机,通过加热板的加热和模具的压力,使橡胶在短时间内完成硫化反应,达到所需的硬度和强度。
最后是硫化环节。
硫化是指将已经成型的橡胶制品加热到一定温度,在一定时间内与硫化剂发生化学反应,使橡胶分子中的交联结构增加,从而提高橡胶的强度和耐磨性。
硫化过程一般分为热硫化和冷硫化两种形式。
热硫化是将橡胶制品放入加热箱中进行硫化,冷硫化则是在室温下进行硫化。
硫化时间和温度需要根据橡胶的种类和产品的要求进行调整。
整个橡胶生产工艺流程需要严格控制各个环节的参数和工艺要求,以确保橡胶制品的质量和性能。
同时,还需要注意生产中的环境保护和能源消耗,采取相应的措施减少污染和资源浪费。
总结起来,橡胶生产工艺流程主要包括原料准备、混炼、模压和硫化。
在这个流程中,需要控制好每个环节的参数和工艺要求,以确保橡胶制品的质量和性能。
橡胶密炼机工作原理
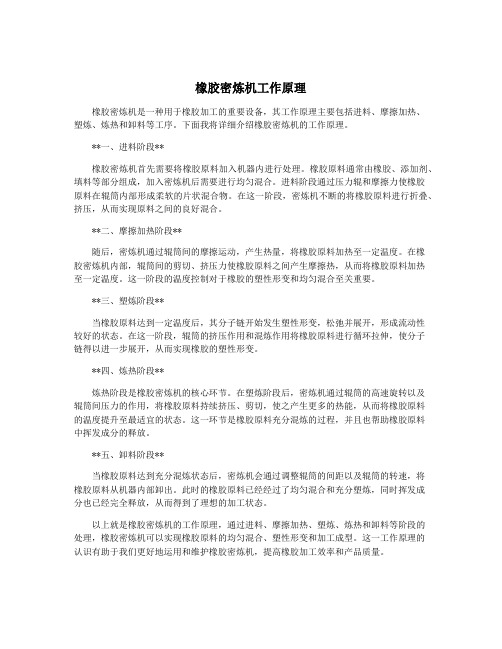
橡胶密炼机工作原理橡胶密炼机是一种用于橡胶加工的重要设备,其工作原理主要包括进料、摩擦加热、塑炼、炼热和卸料等工序。
下面我将详细介绍橡胶密炼机的工作原理。
**一、进料阶段**橡胶密炼机首先需要将橡胶原料加入机器内进行处理。
橡胶原料通常由橡胶、添加剂、填料等部分组成,加入密炼机后需要进行均匀混合。
进料阶段通过压力辊和摩擦力使橡胶原料在辊筒内部形成柔软的片状混合物。
在这一阶段,密炼机不断的将橡胶原料进行折叠、挤压,从而实现原料之间的良好混合。
**二、摩擦加热阶段**随后,密炼机通过辊筒间的摩擦运动,产生热量,将橡胶原料加热至一定温度。
在橡胶密炼机内部,辊筒间的剪切、挤压力使橡胶原料之间产生摩擦热,从而将橡胶原料加热至一定温度。
这一阶段的温度控制对于橡胶的塑性形变和均匀混合至关重要。
**三、塑炼阶段**当橡胶原料达到一定温度后,其分子链开始发生塑性形变,松弛并展开,形成流动性较好的状态。
在这一阶段,辊筒的挤压作用和混炼作用将橡胶原料进行循环拉伸,使分子链得以进一步展开,从而实现橡胶的塑性形变。
**四、炼热阶段**炼热阶段是橡胶密炼机的核心环节。
在塑炼阶段后,密炼机通过辊筒的高速旋转以及辊筒间压力的作用,将橡胶原料持续挤压、剪切,使之产生更多的热能,从而将橡胶原料的温度提升至最适宜的状态。
这一环节是橡胶原料充分混炼的过程,并且也帮助橡胶原料中挥发成分的释放。
**五、卸料阶段**当橡胶原料达到充分混炼状态后,密炼机会通过调整辊筒的间距以及辊筒的转速,将橡胶原料从机器内部卸出。
此时的橡胶原料已经经过了均匀混合和充分塑炼,同时挥发成分也已经完全释放,从而得到了理想的加工状态。
以上就是橡胶密炼机的工作原理,通过进料、摩擦加热、塑炼、炼热和卸料等阶段的处理,橡胶密炼机可以实现橡胶原料的均匀混合、塑性形变和加工成型。
这一工作原理的认识有助于我们更好地运用和维护橡胶密炼机,提高橡胶加工效率和产品质量。
橡胶的工艺流程
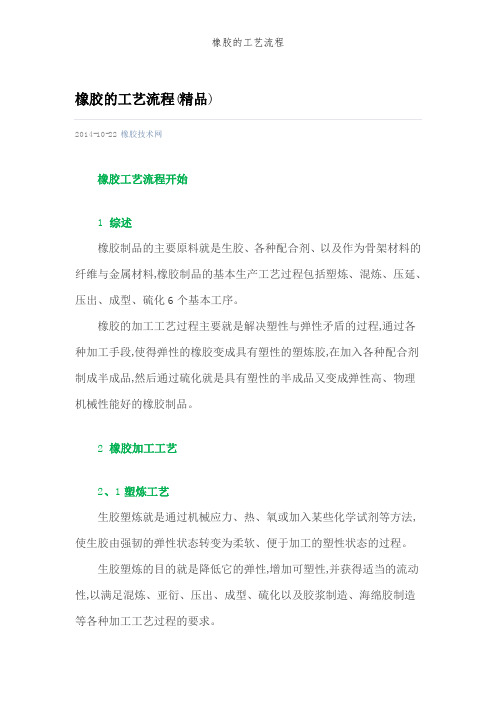
橡胶的工艺流程(精品)2014-10-22橡胶技术网橡胶工艺流程开始1 综述橡胶制品的主要原料就是生胶、各种配合剂、以及作为骨架材料的纤维与金属材料,橡胶制品的基本生产工艺过程包括塑炼、混炼、压延、压出、成型、硫化6个基本工序。
橡胶的加工工艺过程主要就是解决塑性与弹性矛盾的过程,通过各种加工手段,使得弹性的橡胶变成具有塑性的塑炼胶,在加入各种配合剂制成半成品,然后通过硫化就是具有塑性的半成品又变成弹性高、物理机械性能好的橡胶制品。
2 橡胶加工工艺2、1塑炼工艺生胶塑炼就是通过机械应力、热、氧或加入某些化学试剂等方法,使生胶由强韧的弹性状态转变为柔软、便于加工的塑性状态的过程。
生胶塑炼的目的就是降低它的弹性,增加可塑性,并获得适当的流动性,以满足混炼、亚衍、压出、成型、硫化以及胶浆制造、海绵胶制造等各种加工工艺过程的要求。
掌握好适当的塑炼可塑度,对橡胶制品的加工与成品质量就是至关重要的。
在满足加工工艺要求的前提下应尽可能降低可塑度。
随着恒粘度橡胶、低粘度橡胶的出现,有的橡胶已经不需要塑炼而直接进行混炼。
在橡胶工业中,最常用的塑炼方法有机械塑炼法与化学塑炼法。
机械塑炼法所用的主要设备就是开放式炼胶机、密闭式炼胶机与螺杆塑炼机。
化学塑炼法就是在机械塑炼过程中加入化学药品来提高塑炼效果的方法。
开炼机塑炼时温度一般在80℃以下,属于低温机械混炼方法。
密炼机与螺杆混炼机的排胶温度在120℃以上,甚至高达160-180℃,属于高温机械混炼。
生胶在混炼之前需要预先经过烘胶、切胶、选胶与破胶等处理才能塑炼。
几种胶的塑炼特性:天然橡胶用开炼机塑炼时,辊筒温度为30-40℃,时间约为15-20min;采用密炼机塑炼当温度达到120℃以上时,时间约为3-5min。
丁苯橡胶的门尼粘度多在35-60之间,因此,丁苯橡胶也可不用塑炼,但就是经过塑炼后可以提高配合机的分散性顺丁橡胶具有冷流性,缺乏塑炼效果。
顺丁胶的门尼粘度较低,可不用塑炼。
密炼机作业指导书
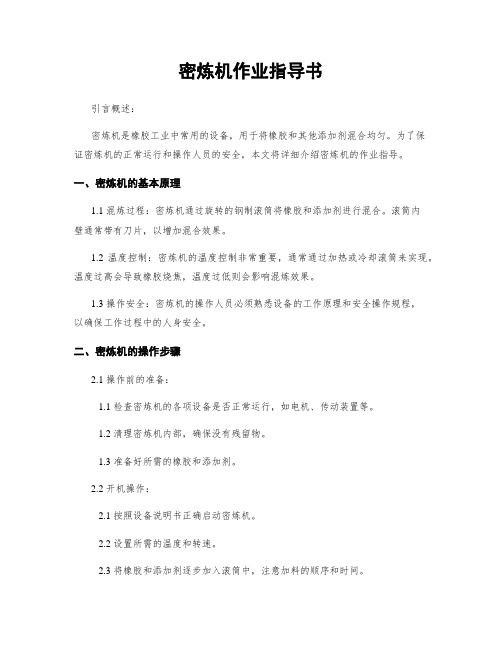
密炼机作业指导书引言概述:密炼机是橡胶工业中常用的设备,用于将橡胶和其他添加剂混合均匀。
为了保证密炼机的正常运行和操作人员的安全,本文将详细介绍密炼机的作业指导。
一、密炼机的基本原理1.1 混炼过程:密炼机通过旋转的钢制滚筒将橡胶和添加剂进行混合。
滚筒内壁通常带有刀片,以增加混合效果。
1.2 温度控制:密炼机的温度控制非常重要,通常通过加热或冷却滚筒来实现。
温度过高会导致橡胶烧焦,温度过低则会影响混炼效果。
1.3 操作安全:密炼机的操作人员必须熟悉设备的工作原理和安全操作规程,以确保工作过程中的人身安全。
二、密炼机的操作步骤2.1 操作前的准备:1.1 检查密炼机的各项设备是否正常运行,如电机、传动装置等。
1.2 清理密炼机内部,确保没有残留物。
1.3 准备好所需的橡胶和添加剂。
2.2 开机操作:2.1 按照设备说明书正确启动密炼机。
2.2 设置所需的温度和转速。
2.3 将橡胶和添加剂逐步加入滚筒中,注意加料的顺序和时间。
2.3 运行过程中的注意事项:3.1 密炼机运行过程中应保持稳定,避免突然停机或转速变化过大。
3.2 定期检查滚筒内的温度和混合效果,必要时进行调整。
3.3 不得将手或其他物体伸入滚筒内,以免发生危险。
三、密炼机的维护保养3.1 清洁保养:1.1 每次使用后,应清理密炼机内部的残留物。
1.2 定期检查密炼机的各个部件是否正常,如皮带、链条等,必要时进行更换或维修。
1.3 保持密炼机的外部清洁,避免灰尘和杂物进入设备内部。
3.2 润滑维护:2.1 密炼机的各个传动部件应定期加注润滑油,确保正常运转。
2.2 滚筒内的刀片应保持锋利,定期检查并更换。
3.3 定期检修:3.1 密炼机的关键部件,如电机、减速器等,应定期进行检修和维护。
3.2 密炼机的电气系统应定期检查,确保安全可靠。
四、常见故障及处理方法4.1 密炼机无法启动:1.1 检查电源是否正常。
1.2 检查电机是否故障。
1.3 检查控制系统是否正常。
轮胎厂密炼工艺流程

轮胎厂密炼工艺流程
1. 原料称重
根据配方要求,按比例称取各种原材料,包括天然橡胶、合成橡胶、炭黑、石蜡油、硫化剂等。
2. 开炼
将称重好的原料投入密炼机,在高温高剪切力条件下进行均匀混合,使各组分熔化、分散,制备出均匀的胶料。
3. 排渣
将密炼好的胶料经过挤出头排出,同时去除其中的空气和杂质。
4. 下料
将挤出的胶料切割成适当大小,以备后续使用。
5. 再生胶制备
将废旧轮胎、边角料等回收的橡胶废料投入再生胶生产线,经过机械剪切、加热等工艺,制成再生胶用于掺入新胶中。
6. 混炼
将下料后的新胶和适量再生胶按比例投入混炼机,进行均匀混合。
7. 出胶
密炼好的胶料从出胶口排出成型,制成胶馍或胶皮状,待后续成型或挤出加工。
8. 检测
定期抽取样品,检测密炼胶的物理化学性能指标,确保符合质量要求。
9. 包装入库
合格的密炼胶进行包装,贴上标签后入库保存,待后续加工使用。
开炼机的工作原理
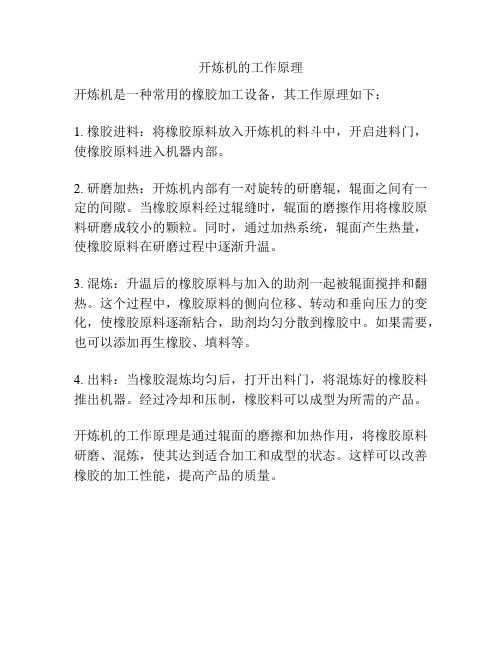
开炼机的工作原理
开炼机是一种常用的橡胶加工设备,其工作原理如下:
1. 橡胶进料:将橡胶原料放入开炼机的料斗中,开启进料门,使橡胶原料进入机器内部。
2. 研磨加热:开炼机内部有一对旋转的研磨辊,辊面之间有一定的间隙。
当橡胶原料经过辊缝时,辊面的磨擦作用将橡胶原料研磨成较小的颗粒。
同时,通过加热系统,辊面产生热量,使橡胶原料在研磨过程中逐渐升温。
3. 混炼:升温后的橡胶原料与加入的助剂一起被辊面搅拌和翻热。
这个过程中,橡胶原料的侧向位移、转动和垂向压力的变化,使橡胶原料逐渐粘合,助剂均匀分散到橡胶中。
如果需要,也可以添加再生橡胶、填料等。
4. 出料:当橡胶混炼均匀后,打开出料门,将混炼好的橡胶料推出机器。
经过冷却和压制,橡胶料可以成型为所需的产品。
开炼机的工作原理是通过辊面的磨擦和加热作用,将橡胶原料研磨、混炼,使其达到适合加工和成型的状态。
这样可以改善橡胶的加工性能,提高产品的质量。
密炼工艺流程

密炼工艺流程密炼是橡胶工业中的一项重要工艺,通过密炼可以将多种橡胶材料和添加剂均匀混合,从而制得具有所需性能的橡胶混炼胶料。
本文将介绍密炼的工艺流程。
密炼的工艺流程主要包括投料、预热、补料、炼炉、冷却和卸料等环节。
首先,在进行密炼之前,需要准备好橡胶材料和各种添加剂。
橡胶材料包括天然橡胶和合成橡胶,添加剂包括硫化剂、助剂和填充剂等。
在投料环节,将预先称好的橡胶材料和添加剂按照一定比例投放到密炼机的料斗中。
接下来是预热环节,预热的目的是提高橡胶材料的流动性,加快反应速度。
通过控制密炼机的温度和转速,将橡胶材料加热至一定温度,通常为100-130摄氏度。
当橡胶材料预热至一定温度后,开始进行补料。
补料是为了加入一些在预热过程中易挥发的添加剂,例如活性助剂和硫化剂。
这些添加剂的补料量通常是根据产品的需求和配方进行调整的。
然后是炼炉环节,炼炉主要是将橡胶材料进行剪切、拉伸和摩擦,使其得到混合和分散。
密炼机的炼炉内部有多种剪切叶片和搅拌装置,通过不同的叶片和搅拌方式,可以实现不同程度的橡胶混炼。
在炼炉的过程中,还需要添加一些非挥发性的添加剂。
这些添加剂包括填充剂、防老剂和防焦剂等。
此外,也可以根据需要加入一些颜料和润滑剂。
炼炉结束后,需要进行冷却环节。
冷却的目的是降低胶料的温度,防止后续加工过程中过度热化。
通常采用冷却水循环方式进行冷却,同时需注意冷却速度的控制,以免过快导致结块或质量损失。
最后是卸料环节,卸料是指将密炼机中的胶料取出。
根据密炼机的类型和工艺要求,卸料方式可分为手工取料和自动取料两种。
在卸料过程中,需要保证胶料的密封性,以免受到外界污染。
综上所述,密炼的工艺流程包括投料、预热、补料、炼炉、冷却和卸料等环节。
通过合理控制每个环节的工艺参数和操作条件,可以得到符合要求的橡胶混炼胶料,为橡胶制品的后续加工提供良好的原料基础。
密炼车间工艺流程图
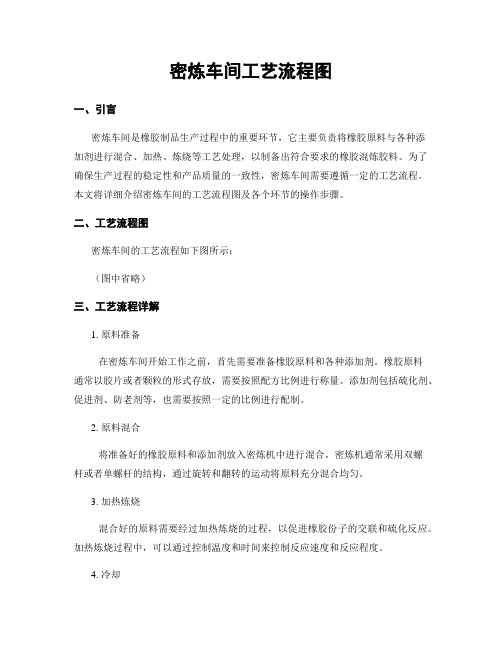
密炼车间工艺流程图一、引言密炼车间是橡胶制品生产过程中的重要环节,它主要负责将橡胶原料与各种添加剂进行混合、加热、炼烧等工艺处理,以制备出符合要求的橡胶混炼胶料。
为了确保生产过程的稳定性和产品质量的一致性,密炼车间需要遵循一定的工艺流程。
本文将详细介绍密炼车间的工艺流程图及各个环节的操作步骤。
二、工艺流程图密炼车间的工艺流程如下图所示:(图中省略)三、工艺流程详解1. 原料准备在密炼车间开始工作之前,首先需要准备橡胶原料和各种添加剂。
橡胶原料通常以胶片或者颗粒的形式存放,需要按照配方比例进行称量。
添加剂包括硫化剂、促进剂、防老剂等,也需要按照一定的比例进行配制。
2. 原料混合将准备好的橡胶原料和添加剂放入密炼机中进行混合。
密炼机通常采用双螺杆或者单螺杆的结构,通过旋转和翻转的运动将原料充分混合均匀。
3. 加热炼烧混合好的原料需要经过加热炼烧的过程,以促进橡胶份子的交联和硫化反应。
加热炼烧过程中,可以通过控制温度和时间来控制反应速度和反应程度。
4. 冷却经过加热炼烧后的橡胶混炼胶料需要进行冷却处理,以降低温度并使其固化。
冷却可以通过自然冷却或者利用冷却设备进行。
5. 粉碎冷却后的橡胶混炼胶料需要进行粉碎处理,以便后续的加工和使用。
粉碎可以采用切割、研磨或者挤压等方式进行。
6. 包装和存储粉碎后的橡胶混炼胶料需要进行包装和存储。
通常采用密封包装,以防止橡胶混炼胶料受潮或者污染。
存储时需要注意避免阳光直射和高温环境。
四、操作步骤1. 原料准备a. 根据配方比例准备橡胶原料和添加剂。
b. 使用天平进行准确的称量。
c. 将称量好的原料放入密炼机的料斗中。
2. 原料混合a. 打开密炼机的开关,启动机器。
b. 调整密炼机的转速和温度,使其达到适宜的混合条件。
c. 将料斗中的原料缓慢加入密炼机中。
d. 观察原料的混合情况,确保混合均匀。
3. 加热炼烧a. 调整密炼机的温度和时间参数。
b. 启动加热装置,使密炼机内的温度逐渐升高。
- 1、下载文档前请自行甄别文档内容的完整性,平台不提供额外的编辑、内容补充、找答案等附加服务。
- 2、"仅部分预览"的文档,不可在线预览部分如存在完整性等问题,可反馈申请退款(可完整预览的文档不适用该条件!)。
- 3、如文档侵犯您的权益,请联系客服反馈,我们会尽快为您处理(人工客服工作时间:9:00-18:30)。
聚合物加工实验报告班级:12高分子材料与工程1班学号:1214121013姓名:矢名实验一PP/EPDM共混改性及挤出造粒、注塑实验二PE吹塑薄膜成型实验三EPDM橡胶的开炼及密炼实验四PP/EPDM性能测定实验五EPDM橡胶硫化曲线的测定实验三EPDM橡胶的开炼及密炼天然橡胶密炼机塑炼一、实验目的(1) 掌握橡胶制品配方设计的基本知识,熟悉密炼机进行橡胶塑炼的工艺;(2)了解橡胶塑炼的主要机械设备:密炼机基本结构及操作方法;二、实验原理橡胶制品的基本工艺过程包括配合、生胶塑炼、胶料混炼、成型、硫化五个基本过程,如图27—1所示。
图27-1 橡胶制品工艺过程生胶是线型的高分子化合物,在常温下大多数处于高弹态。
然而生胶的高弹性却给成型加工带来极大的困难,一方面各种配合剂无法在生胶中分散均匀,另一方面,由于可塑性小,不能获得所需的各种形状。
为满足加工工艺的要求,使生胶由强韧的弹性状态变成柔软而具有可塑性状态的工艺过程称作塑炼。
塑炼的目的在于:使生胶由弹性状态转变为可塑性状态,使其可塑性增大,可塑性提高的实质就是橡胶的长链分子断裂,变成分子量较小的,链长较短的分子结构,以利混炼时配合剂的混入和均匀分散;改善胶料的流动性,便于压延、压出操作,使胶胚形状和尺寸稳定;增大胶料的粘着性,方便成型操作;提高胶料在溶剂中的溶解性,便于制造胶浆,并降低胶浆粘度,使之易于深入纤维孔眼,增加附着力;改善胶料的冲模性,使模型制品的花纹饱满清晰。
生胶经塑炼以增加其可塑性。
其实质是生胶分子链断裂,相对分子质量降低,从而使生胶的弹性下降。
在生胶塑炼时,主要受到机械力、氧、热、电和某些化学增塑剂等因素的作用。
工艺上用以降低生胶相对分子质量获得可塑性的塑炼方法可分为机械塑炼法和化学塑炼法两大类。
其中机械塑炼法应用最为广泛。
橡胶机械塑炼的实质是力化学反应过程,即以机械力作用及在氧或其他白由基受体存在下进行的,在机械塑炼过程中,机械力使大分子链断裂,氧对橡胶分子起化学降解作用。
这两个作用同时存在。
本实验选用密炼机对天然橡胶进行机械法塑炼。
生胶置于密炼机中,两转子相对回转,将来自加料口的物料夹住带入辊缝受到转子的挤压和剪切,穿过辊缝后碰到下顶拴尖棱被分成两部分,分别沿前后室壁与转子之间缝隙再回到辊隙上方。
在常温(小于50℃)下反复受到机械力的作用,使分子链断裂,与此同时断裂后的大分子自由基在空气中氧化作用下,发生了一系列力学与化学反应,最终达到降解,生胶从原先高韧高弹性变为柔软可塑性,满足混炼的要求。
此外,塑炼的时间、塑炼工艺操作方法及是否加入塑解剂也影响塑炼的效果。
在绕转子流动的一周中,物料处处受到剪切和摩擦作用,使胶料的温度急剧上升,粘度降低。
由于密炼机混炼时胶料受到的剪切作用比开炼机大得多,炼胶温度高,使得密炼机炼胶的效率大大高于开炼机。
密炼机的炼胶过程是比较复杂的,我们可以从下面的图简单地表示炼胶过程。
从下图可以看到:密炼机对胶料的混炼可分为:细分、混入、分散、均匀等几个阶段。
(图27-2)图27-2密炼机塑炼的优点主要有以下几个方面:(1)密炼机转速高,生产能力大;(2)转子转速的断面结构复杂,转子表面各点与轴心距离不等,因此产生不同的线速度,使两转子间的速比变化很大,促使生胶受到强烈的摩擦、撕裂和搅拌作用。
此外,胶料不仅在两转子的间隙中受到剪切作用,而且还在转子与密炼室壁之间以及转子与上下顶栓的间隙之间都受到剪切作用,因此可以得到较高的塑炼效果;(3)转子的短突棱具有一定导角,能使胶料做轴向移动和转动,起到开炼机手工捣胶的作用,使生胶塑炼均匀;(4)密炼室的温度较高,因此能使生胶受到剧烈的氧化裂解作用,使胶料能在短时间内获得较大的可塑性。
三、仪器设备和原料仪器设备:(1)密炼机(图27-3)密炼机的结构,一般是由密炼室转子部分、压料装置部分、卸料装置部分、传动装置部分、加热冷却及气压、电控系统等部分组成。
混炼室转子部分主要由混炼室、转子等组成。
混炼室带有夹套,可通入冷却水进行冷却。
外部包裹加热片用以加热。
转子两端用双列圆锥滚子轴承安装在混炼室下体机中,两转子通过安装在其颈部的速比齿轮带动,在密炼室内做不同转速的相对回转。
压料装置部分由上顶栓及气缸等组成。
安装在混炼室上面。
卸料装置部分由安装在混炼室下面的下顶栓和下顶栓锁紧机构组成。
传动装置部分由电机、弹性联轴节、减速器和齿形联轴节等组成。
加热冷却系统主要由管道和分配器等组成,以便将冷却水通入混炼室、转子等腔内循环流动,以控制胶料的温度。
气压系统主要由气缸、活塞、气阀,管道和压缩空气控制站等组成。
用于控制上顶栓以及防尘盖的升降。
电控系统由电控箱、操作台和各种电器仪表组成,是整个机台的操作中心。
(2)台秤、游标卡尺,炼胶刀图27-3实验原料天然橡胶四.实验步骤:(图27-4) 气缸 电控箱防尘盖(内部:上顶栓)速比齿轮电动机密炼室 (内部:转子) 减速器图27-41. 开车前必须检查混炼室转子间有无杂物,上、下顶栓,仪表、信号装置等的完好,方可准备开车。
2. 开启主机、减速器和主电机等冷却系统的进水阀和排水阀。
3. 开启空压机,保证压力表读数≥0.4Mpa.4.启动设备电源,将控制箱上红色的“电源开关”顺时针旋开。
5.按下加热开关,并设定塑炼所需温度,开始加热。
6.待温度达到设定温度后,将橡胶加入密炼室中。
用量约为1-1.5kg.7. 压料装置的上顶栓降落对物料加压:将压盖控制按钮向右旋至“压盖降”8. 按下转子转速控制面板上的“RUN“键,并旋转右侧旋钮至所需设定的转子转速。
转速显示在面板显示屏上。
9.待塑炼完全,均匀后,将压盖控制按钮向左旋至“压盖升“,提起上顶栓。
10.将转子转速控制面板右侧旋钮旋至零,并按下“STOP”键,使转子停止转动。
11. 按下“密炼室翻转”键,使密炼室翻转90度,用以排料。
12. 生产结束后,清除密炼室,转子断面密封装置上的粘附物后,按下“密炼室回复”键。
五.注意事项1.顶栓(压盖)处于降落状态时,禁止按“密炼室翻转”键。
2. 当密炼机在混炼工程中因故临时停车时,在故障排除后,必须将密炼室内胶料排出后方可启动主电机。
3. 实验结束后,要及时清理密炼室、转子断面密封装置,压盖上的粘附物,清扫工作场地。
天然橡胶开炼机混炼一.实验目的(1)掌握橡胶制品配方设计的基本知识,熟悉开炼机进行橡胶混炼工艺;(2)了解开炼机基本结构及操作方法;(3)掌握橡胶物理机械性能测试试样制备工艺及性能测试方法。
二.实验原理1.胶料的混炼混炼就是将各种配合剂与塑炼胶在机械作用下混合均匀,制成混炼胶的过程。
混炼过程的关键是使各种配合剂能完全均匀地分散在橡胶中,保证胶料的组成和各种性能均匀一。
对混炼胶的质量要求主要有两个方面:一是胶料能保证制品具有良好的物理机械性能;二是胶料本身要具有良好的工艺加工性能。
为了获得配合剂在生胶中的均勿混合分散,必须借助炼胶机的强烈机械作用进行混炼。
混炼胶的质量控制对保持橡胶半成品和成品性能有着重要意义。
混炼胶组分比较复杂,不同性质的组分对混炼过程、分散程度以及混炼胶的结构响很大的影响。
本实验混炼是在开炼机上进行的。
当胶料加到辊筒上时,由于两个辊筒以不同的线速度相对回转,胶料在被辊筒挤压的同时,在摩擦力和粘附力的作用下,被拉入辊隙中。
形成楔形断面的胶条。
在辊隙中由于速度梯度和辊筒温度的作用致使胶料受到强烈的碾压、撕裂,同时伴随着橡胶分子链的氧化断裂作用。
从辊隙中排出的胶片,由于两个辊筒表面速度和温度的差异而包覆在一个辊筒上,又重新返回两滚筒间,这样多次反复,完成炼胶作业。
为了取得具有一定的可塑度且性能均匀的混炼胶,除了控制辊距的大小、适宜的辊温小于90℃之外,必须按一定的加料混合程序操作。
一般的原则是:量少难分散的配合剂首先加到塑炼胶中,让其有较长的时间分散;量多易分散的配合剂后加;硫化剂应最后加入,因为一旦加入硫化剂,便可能发生硫化反应,过长的混炼时间会使胶料焦烧,不利于气候的成型和硫化程序。
开炼机混炼过程可分为包辊、吃粉和翻炼三个阶段。
包辊是开炼机混炼的前提;橡胶包辊后,为使配合剂尽快混入橡胶中,在辊缝上端应保留有一定的堆积胶。
当加入配合剂时,由于堆积胶的不断翻转和更替,便把配合剂带进堆积胶的皱纹沟中,并进而带入辊缝中,配合剂混入胶料的这个过程称为吃粉阶段。
混炼的第三个阶段为翻炼。
2.橡胶配合剂常包括硫化剂、硫化促进剂、助促进剂、防老剂、填充剂、石蜡和机油等。
橡胶必须经过交联(硫化)才能改善其物理机械性能和化学性能,使橡胶制品只有实用价值。
硫磺是橡胶硫化的最常用的交联剂,本实验配方中的硫磺用量在5phr之内,交联度不很大,所得制品柔软。
选用两种促进剂对天然橡胶的硫化都有促进作用;不同的促进剂同时使用,是因为它们的活性强弱及活性温度有所不同,在硫化时促使进交联作用更加协调、充分显示促进效果。
三、仪器设备和原料1.仪器设备(1) XK-230A型双辊筒开放式炼胶机开放式炼胶基的基本结构如题27-3、4所示,用于生胶塑炼和胶料混炼。
(2)台秤、游标卡尺,27-4 XK-230A型双辊筒开放式炼胶机1 前辊 2后辊 3 挡板 4 大齿轮传动5、8、12、17 机架;6刻度盘;7 控制螺旋杆 9 传动轴齿轮;10加强杆;11 基础板;13安装孔;11传动齿轮 15传动轴;16摩擦齿轮 18 加油装置 19 安全开关箱 20 紧急停车装置2.原料配方下列是指导性实验配方,学生可自行设计配方。
天然橡胶 100硫磺 2.5促进剂TT 1.5促进剂DM 0.5轻质碳酸钙 20~60四、实验准备(1)开车前必须穿戴好劳保用品。
(2)检查各机台紧固件有无松动,损坏。
(3)检查刹车装置是否完好、有效、灵敏;(4)应检查两轴辊筒无异物,各部分是否正常,经检查后方能通电启动。
(5)在老师指导下,按机器的操作规程开动开放式炼胶机,观察机器是否运转正常。
(6)拟定实验配方及各项成型工艺条件。
五、实验步骤1. 开启开炼机:首先开启控制箱左面总电源开关拉闸,然后按下控制面板上的绿色启动按钮。
2. 包辊:在两组相对回转辊筒投料时,引胶并塑炼胶置于辊缝间靠大齿轮一段投入,调整辊距以手顺时针旋转为减距,反之为增距,使塑炼胶即使辊义能在辊缝上部有适当的堆积胶。
经2—3min的辊压、翻炼后,使之均匀连续地包裹在前辊上,形成光滑无隙的包辊胶层。
取下胶层,放宽相距至1.5mm左右。
再把胶层投入辊缝使其包于后辊,然后加入配合剂。
3. 吃粉:不同配合剂要按如下顺序分别加入:固体软化剂→促进剂、防老剂和硬酯酸→氧化锌→补强剂和填充剂→液体软化剂→硫磺。
4. 吃粉过程中每加人一种配合剂后都要捣胶两次。
在加入填充剂和补强剂时要让粉料自然地进入胶料中,使之与橡胶均约接触混合,而不必急于捣胶;同时还需逐步调宽辊距,使堆积胶保持在适当则范围内。