焊缝焊接缺陷示意图剖析
09-常见焊缝和母材缺陷的彩色照片

常见焊缝和母材缺陷的彩色照片
(包括部分示意图)
图1横向裂纹图2 纵向裂纹
图3 角焊缝的焊缝厚度裂纹
图4 焊缝厚度裂纹
图5 焊趾裂纹
图6 弧坑裂纹
图7 铝焊缝中弧坑裂纹的扩展
图8 焊道下裂纹
图9 裂纹在RT检测底片上的形貌
图10 各种部位的未熔合
图11 焊缝与母材间的未熔合
图12 未熔合(RT显示可能是由沿着焊接接头坡口面处形成的未熔合引起)
图13坡口焊缝中未焊透示意图
图14 坡口焊缝根部未焊透
图15 坡口焊缝根部未焊透的射线底片
图16 表面夹渣
图17 条形夹渣的射线照相影像
图18 根部焊道开始及结束处的未熔透缺陷的射线照相
图19 夹钨的射线影像(通常为亮点)
图20 伴随裂纹的线状表面气孔
图21 角焊缝管状气孔
图22密集气孔的射线照相
23角焊缝和坡口焊缝的咬边和焊瘤
24 表面咬边的射线影像
图25 未焊满
图26 焊瘤的示意图及实例
图27 焊缝凸度过大示意图及实例
图28 焊缝余高过大
图29 弧坑及弧坑裂纹
图30 层状撕裂实例。
《焊缝缺陷图示》课件

焊缝缺陷可能导致 结构断裂,造成安 全隐患
引发泄漏
焊缝缺陷可能导致气体或液体泄漏 泄漏可能导致设备损坏或失效 泄漏可能导致环境污染或人员伤害 泄漏可能导致经济损失或生产中断
缩短使用寿命
焊缝缺陷可能导致 结构强度降低,影 响使用寿命
焊缝缺陷可能导致 设备运行不稳定, 影响使用寿命
焊缝缺陷可能导致 设备维修成本增加 ,影响使用寿命
提高母材质量
选用优质母材,保证其化学成 分、力学性能等符合要求
严格控制母材的加工工艺,避 免产生缺陷
定期对母材进行检验,确保其 质量符合标准
加强母材的储存和运输管理, 避免受到污染和损坏
THANK YOU
汇报人:PPT
原因:焊接电流过小、焊接速 度过快、焊丝角度不当等
危害:降低焊缝强度,影响焊 接质量
预防措施:调整焊接参数、改 善焊接工艺、加强焊前清理等
未焊透
原因:焊接电流过小、焊接速度过快、焊丝角度不当等 特征:焊缝表面有明显的凹坑或缺口,内部有气孔或夹渣 危害:降低焊缝强度,影响焊接质量 预防措施:调整焊接参数、改善焊接环境、加强焊前清理等
电压:根 据焊接材 料和厚度 选择合适 的电压
速度:根 据焊接材 料和厚度 选择合适 的速度
气体保护: 根据焊接 材料和厚 度选择合 适的气体 保护
预热:根 据焊接材 料和厚度 选择合适 的预热温 度
冷却:根 据焊接材 料和厚度 选择合适 的冷却方 式
提高焊接材料质量
确保焊接材料符合国家标准 和行业标准
无损检测
超声波检测:利用超声波在焊缝中的传播和反射特性,检测焊缝内部的 缺陷
射线检测:利用X射线或γ射线在焊缝中的穿透和吸收特性,检测焊缝 内部的缺陷
焊接缺陷,探伤图解(收藏)

焊接缺陷,探伤图解(收藏)一起学习,共同进步!先看18张很清晰的焊接缺陷图谱,身边搞焊接的朋友和搞探伤的朋友们应该人手一份。
万分感谢将这篇文章分享给我的同仁另外总结了一些常见焊接缺陷产生的原因、危害及防止措施!文章结尾蓝色字体内容更精彩!先看这几张图片,射线探伤底片结合横切面示意图,便于理解学习,拿出来分享给朋友们!1、weld01(High Low、高低)2、welld02(IncompleteRootFusion、根部未熔合)3、welld03(InsuffucientReinforcement、增强高)4、welld04(Excess RootPenetration、根部焊瘤)5、welld05(ExternalUndercut、外部咬肉)6、welld06(InternalUndercut、内部咬肉)7、welld07(RootConcavity、根部凹陷)8、welld08(BurnThrough、烧穿)9、welld09(Isolated SlagInclusion、单个的夹渣)10、welld10(WagonTrack Slag Line、线状夹渣)11、welld11(InterrunFusion、内部未熔合)12、welld12(Lack ofSidewallFusion、内侧未熔合)13、welld13(Porosity、气孔)14、welld14(Cluster Porosity、链状气孔)15、welld15(HollowBead、夹珠)16、welld16(Transverse Crack、横向裂纹)17、welld17(CenterlineCrack、中心线裂纹)18、welld18(RootCrack、根部裂纹)常见焊接缺陷产生原因、危害及防止措施一、焊接缺陷的分类焊接缺陷可分为外部缺陷和内部缺陷两种1.外部缺陷1)外观形状和尺寸不符合要求;2)表面裂纹;3)表面气孔;4)咬边;5)凹陷;6)满溢;7)焊瘤;8)弧坑;9)电弧擦伤;10)明冷缩孔;11)烧穿;12)过烧。
焊接缺陷图示
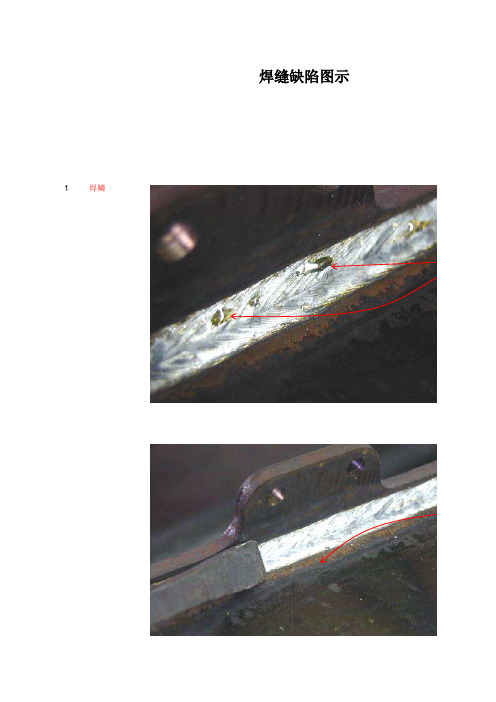
焊缝缺陷图示1焊鳞
2-气孔
修复方法:打磨去除该段焊缝,重新焊接。
3
-
弧坑针状气孔
打磨去除此部分
修复方法:打磨去除该段焊缝,重新焊接。
4-气孔(砂眼)
修复方法:打磨去除所有影响焊缝,重新焊接。
5-
缩孔
打磨去除此部分
修复方法:打磨去除所有影响焊缝,重新焊接。
6-端部裂纹/焊缝裂纹
修复方法:打磨去除所有影响焊缝,重新焊接。
7-不良焊缝外观
修复方法:重新焊接。
8
- 焊瘤及飞边重新焊接部分
修复方法:打磨,重新焊接。
9-咬边
修复方法:重新焊接。
10-咬边
修复方法:重新焊接。
11-焊缝不均匀
修复方法:重新焊接。
12‘-不良外观
修复方法:重新焊接。
13‘-不良外观
修复方法:重新焊接。
14‘-不良外观
焊鳞
去除焊鳞后焊缝表面。
常见的焊接缺陷及缺陷图片

常见的焊接缺陷 (1)常见的焊接缺陷(1)未焊透:母体金属接头处中间(X坡口)或根部(V、U 坡口)的钝边未完全熔合在一起而留下的局部未熔合。
未焊透降低了焊接接头的机械强度,在未焊透的缺口和端部会形成应力集中点,在焊接件承受载荷时容易导致开裂。
(2)未熔合:固体金属与填充金属之间(焊道与母材之间),或者填充金属之间(多道焊时的焊道之间或焊层之间)局部未完全熔化结合,或者在点焊(电阻焊)时母材与母材之间未完全熔合在一起,有时也常伴有夹渣存在。
(3)气孔:在熔化焊接过程中,焊缝金属内的气体AHA12GAGGAGAGGAFFFFAFAF或外界侵入的气体在熔池金属冷却凝固前未来得及逸出而残留在焊缝金属内部或表面形成的空穴或孔隙,视其形态可分为单个气孔、链状气孔、密集气孔(包括蜂窝状气孔)等,特别是在电弧焊中,由于冶金过程进行时间很短,熔池金属很快凝固,冶金过程中产生的气体、液态金属吸收的气体,或者焊条的焊剂受潮而在高温下分解产生气体,甚至是焊接环境中的湿度太大也会在高温下分解出气体等等,这些气体来不及析出时就会形成气孔缺陷。
尽管气孔较之其它的缺陷其应力集中趋势没有那么大,但是它破坏了焊缝金属的致密性,减少了焊缝金属的有效截面积,从而导致焊缝的强度降低。
AHA12GAGGAGAGGAFFFFAFAF某钢板对接焊缝X射线照相底片V型坡口,手工电弧焊,未焊透某钢板对接焊缝X射线照相底片V型坡口,手工电弧焊,密集气孔(4)夹渣与夹杂物:熔化焊接时的冶金反应产物,例如非金属杂质(氧化物、硫化物等)以及熔渣,由于焊接时未能逸出,或者多道焊接时清渣不干净,以至残留在焊缝金属内,称为夹渣或夹杂物。
视其形态可分为点状和条状,其外形通常是不规则的,其位置可能在焊缝与母材交界处,也可能存在于焊缝内。
另外,在采用钨极氩弧焊打底+手工电弧焊或AHA12GAGGAGAGGAFFFFAFAF者钨极氩弧焊时,钨极崩落的碎屑留在焊缝内则成为高密度夹杂物(俗称夹钨)。
常见的焊接缺陷及缺陷图片
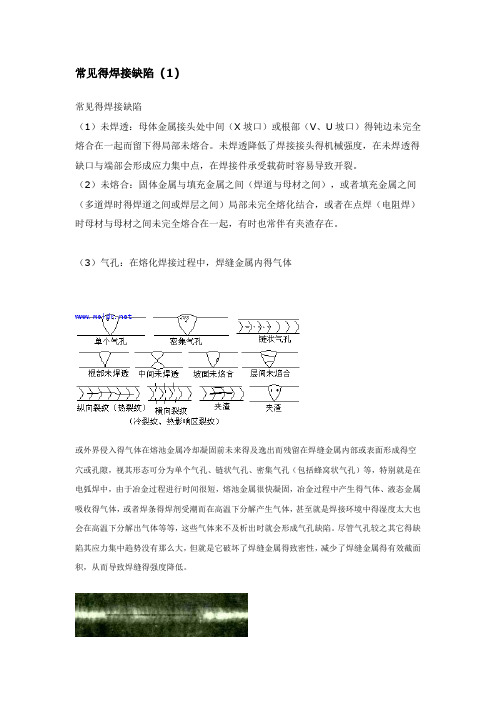
常见得焊接缺陷(1)常见得焊接缺陷(1)未焊透:母体金属接头处中间(X坡口)或根部(V、U坡口)得钝边未完全熔合在一起而留下得局部未熔合。
未焊透降低了焊接接头得机械强度,在未焊透得缺口与端部会形成应力集中点,在焊接件承受载荷时容易导致开裂。
(2)未熔合:固体金属与填充金属之间(焊道与母材之间),或者填充金属之间(多道焊时得焊道之间或焊层之间)局部未完全熔化结合,或者在点焊(电阻焊)时母材与母材之间未完全熔合在一起,有时也常伴有夹渣存在。
(3)气孔:在熔化焊接过程中,焊缝金属内得气体或外界侵入得气体在熔池金属冷却凝固前未来得及逸出而残留在焊缝金属内部或表面形成得空穴或孔隙,视其形态可分为单个气孔、链状气孔、密集气孔(包括蜂窝状气孔)等,特别就是在电弧焊中,由于冶金过程进行时间很短,熔池金属很快凝固,冶金过程中产生得气体、液态金属吸收得气体,或者焊条得焊剂受潮而在高温下分解产生气体,甚至就是焊接环境中得湿度太大也会在高温下分解出气体等等,这些气体来不及析出时就会形成气孔缺陷。
尽管气孔较之其它得缺陷其应力集中趋势没有那么大,但就是它破坏了焊缝金属得致密性,减少了焊缝金属得有效截面积,从而导致焊缝得强度降低。
某钢板对接焊缝X射线照相底片V型坡口,手工电弧焊,未焊透某钢板对接焊缝X射线照相底片V型坡口,手工电弧焊,密集气孔(4)夹渣与夹杂物:熔化焊接时得冶金反应产物,例如非金属杂质(氧化物、硫化物等)以及熔渣,由于焊接时未能逸出,或者多道焊接时清渣不干净,以至残留在焊缝金属内,称为夹渣或夹杂物。
视其形态可分为点状与条状,其外形通常就是不规则得,其位置可能在焊缝与母材交界处,也可能存在于焊缝内。
另外,在采用钨极氩弧焊打底+手工电弧焊或者钨极氩弧焊时,钨极崩落得碎屑留在焊缝内则成为高密度夹杂物(俗称夹钨)。
W18Cr4V(高速工具钢)-45钢棒对接电阻焊缝中得夹渣断口照片钢板对接焊缝X射线照相底片V型坡口,手工电弧焊,局部夹渣钢板对接焊缝X射线照相底片V型坡口,手工电弧焊,两侧线状夹渣钢板对接焊缝X射线照相底片V型坡口,钨极氩弧焊打底+手工电弧焊,夹钨(5)裂纹:焊缝裂纹就是焊接过程中或焊接完成后在焊接区域中出现得金属局部破裂得表现。
常见的焊接缺陷及缺陷图片
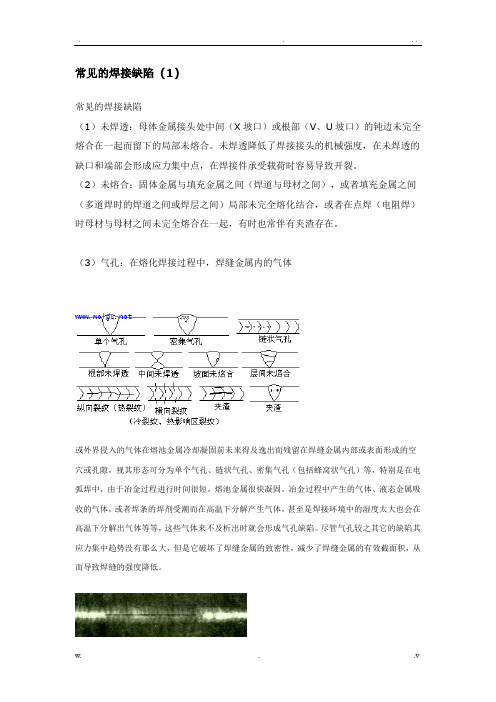
常见的焊接缺陷(1)常见的焊接缺陷(1)未焊透:母体金属接头处中间(X坡口)或根部(V、U坡口)的钝边未完全熔合在一起而留下的局部未熔合。
未焊透降低了焊接接头的机械强度,在未焊透的缺口和端部会形成应力集中点,在焊接件承受载荷时容易导致开裂。
(2)未熔合:固体金属与填充金属之间(焊道与母材之间),或者填充金属之间(多道焊时的焊道之间或焊层之间)局部未完全熔化结合,或者在点焊(电阻焊)时母材与母材之间未完全熔合在一起,有时也常伴有夹渣存在。
(3)气孔:在熔化焊接过程中,焊缝金属内的气体或外界侵入的气体在熔池金属冷却凝固前未来得及逸出而残留在焊缝金属内部或表面形成的空穴或孔隙,视其形态可分为单个气孔、链状气孔、密集气孔(包括蜂窝状气孔)等,特别是在电弧焊中,由于冶金过程进行时间很短,熔池金属很快凝固,冶金过程中产生的气体、液态金属吸收的气体,或者焊条的焊剂受潮而在高温下分解产生气体,甚至是焊接环境中的湿度太大也会在高温下分解出气体等等,这些气体来不及析出时就会形成气孔缺陷。
尽管气孔较之其它的缺陷其应力集中趋势没有那么大,但是它破坏了焊缝金属的致密性,减少了焊缝金属的有效截面积,从而导致焊缝的强度降低。
某钢板对接焊缝X射线照相底片V型坡口,手工电弧焊,未焊透某钢板对接焊缝X射线照相底片V型坡口,手工电弧焊,密集气孔(4)夹渣与夹杂物:熔化焊接时的冶金反应产物,例如非金属杂质(氧化物、硫化物等)以及熔渣,由于焊接时未能逸出,或者多道焊接时清渣不干净,以至残留在焊缝金属内,称为夹渣或夹杂物。
视其形态可分为点状和条状,其外形通常是不规则的,其位置可能在焊缝与母材交界处,也可能存在于焊缝内。
另外,在采用钨极氩弧焊打底+手工电弧焊或者钨极氩弧焊时,钨极崩落的碎屑留在焊缝内则成为高密度夹杂物(俗称夹钨)。
W18Cr4V(高速工具钢)-45钢棒对接电阻焊缝中的夹渣断口照片钢板对接焊缝X射线照相底片V型坡口,手工电弧焊,局部夹渣钢板对接焊缝X射线照相底片V型坡口,手工电弧焊,两侧线状夹渣钢板对接焊缝X射线照相底片V型坡口,钨极氩弧焊打底+手工电弧焊,夹钨(5)裂纹:焊缝裂纹是焊接过程中或焊接完成后在焊接区域中出现的金属局部破裂的表现。
焊接缺陷图例

焊缝术语图列一、未融合的各种位置
二、接头未融合
四、未焊满
六、各种类型的裂纹
1、火口开裂
2、表面裂纹
3、热影响区裂纹
4、层状撕裂
5、纵向裂纹
6、根部裂纹
7、根部表面裂纹
8、角裂纹
9、趾裂纹
10、横向裂纹
11、焊道下裂纹
12、焊缝融合线裂纹
13、焊道金属裂纹
七、横向裂纹纵向裂纹
八、趾裂纹
九、焊道下裂纹
10、焊道余高
12、凸形角焊缝
13、下凹焊道
14、各种焊缝裂纹图列
1、火口开裂
2、表面裂纹
3、热影响区裂纹
4、层状撕裂
5、纵向裂纹
6、根部裂纹
7、根部表面裂纹
8、角裂纹
9、趾裂纹
10、横向裂纹
11、焊道下裂纹
12、焊缝融合线裂纹
13、焊道金属裂纹
(此文档部分内容来源于网络,如有侵权请告知删除,文档可自行编辑修改内容,供参考,
感谢您的配合和支持)。
常见的焊接缺陷及缺陷图片
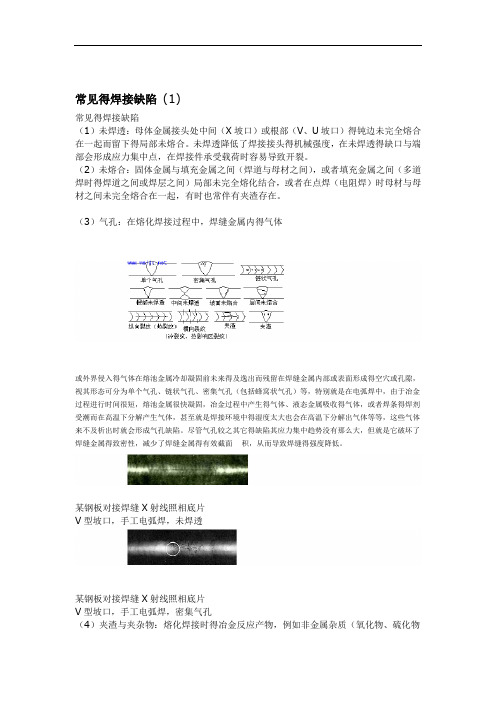
常见得焊接缺陷(1)常见得焊接缺陷(1)未焊透:母体金属接头处中间(X坡口)或根部(V、U坡口)得钝边未完全熔合在一起而留下得局部未熔合。
未焊透降低了焊接接头得机械强度,在未焊透得缺口与端部会形成应力集中点,在焊接件承受载荷时容易导致开裂。
(2)未熔合:固体金属与填充金属之间(焊道与母材之间),或者填充金属之间(多道焊时得焊道之间或焊层之间)局部未完全熔化结合,或者在点焊(电阻焊)时母材与母材之间未完全熔合在一起,有时也常伴有夹渣存在。
(3)气孔:在熔化焊接过程中,焊缝金属内得气体或外界侵入得气体在熔池金属冷却凝固前未来得及逸出而残留在焊缝金属内部或表面形成得空穴或孔隙,视其形态可分为单个气孔、链状气孔、密集气孔(包括蜂窝状气孔)等,特别就是在电弧焊中,由于冶金过程进行时间很短,熔池金属很快凝固,冶金过程中产生得气体、液态金属吸收得气体,或者焊条得焊剂受潮而在高温下分解产生气体,甚至就是焊接环境中得湿度太大也会在高温下分解出气体等等,这些气体来不及析出时就会形成气孔缺陷。
尽管气孔较之其它得缺陷其应力集中趋势没有那么大,但就是它破坏了焊缝金属得致密性,减少了焊缝金属得有效截面积,从而导致焊缝得强度降低。
某钢板对接焊缝X射线照相底片V型坡口,手工电弧焊,未焊透某钢板对接焊缝X射线照相底片V型坡口,手工电弧焊,密集气孔(4)夹渣与夹杂物:熔化焊接时得冶金反应产物,例如非金属杂质(氧化物、硫化物等)以及熔渣,由于焊接时未能逸出,或者多道焊接时清渣不干净,以至残留在焊缝金属内,称为夹渣或夹杂物。
视其形态可分为点状与条状,其外形通常就是不规则得,其位置可能在焊缝与母材交界处,也可能存在于焊缝内。
另外,在采用钨极氩弧焊打底+手工电弧焊或者钨极氩弧焊时,钨极崩落得碎屑留在焊缝内则成为高密度夹杂物(俗称夹钨)。
W18Cr4V(高速工具钢)-45钢棒对接电阻焊缝中得夹渣断口照片钢板对接焊缝X射线照相底片型坡口,手工电弧焊,局部夹渣V.钢板对接焊缝X射线照相底片型坡口,手工电弧焊,两侧线状夹渣V钢板对接焊缝X射线照相底片手工电弧焊,夹钨型坡口,钨极氩弧焊打底+V(5)裂纹:焊缝裂纹就是焊接过程中或焊接完成后在焊接区域中出现得金属局部破裂得表现。
常见焊接缺陷的照片
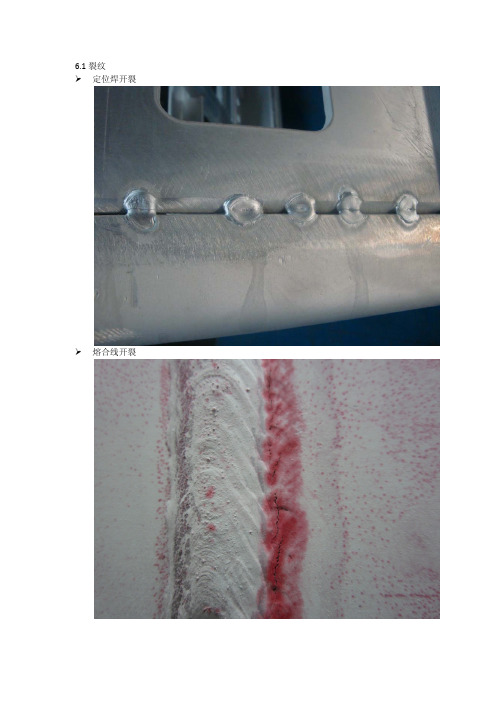
熔合线开裂
端部拐角开裂
弧坑开裂
6.2 气孔 母材或焊丝未去氧化膜引起的气孔
气体杂质或流量不当造成的气孔
其他原因 导电嘴偏芯
焊丝干伸长过长
导电嘴内部有飞溅
环境温湿度、穿堂风超标
6.3 缩孔 正面缩孔
背面缩孔
6.4 未熔合、未焊透 侧壁未熔合
根部未熔合
6.4 咬边 角焊缝咬边
对接焊缝咬边
6.6 余高过大 对接焊缝余高过大
接头余高过大 6.7 下榻过大
6.8 焊瘤
6.9 盖面不足
6.10 焊角不对称
6.11 焊角过小 正常焊角
6.12 焊角过大 3 错边
6.14 角焊缝根部间隙不良
常见的焊接缺陷及缺陷图片

常见的焊接缺陷(1)常见的焊接缺陷(1)未焊透:母体金属接头处中间(X坡口)或根部(V、U坡口)的钝边未完全熔合在一起而留下的局部未熔合。
未焊透降低了焊接接头的机械强度,在未焊透的缺口和端部会形成应力集中点,在焊接件承受载荷时容易导致开裂。
(2)未熔合:固体金属与填充金属之间(焊道与母材之间),或者填充金属之间(多道焊时的焊道之间或焊层之间)局部未完全熔化结合,或者在点焊(电阻焊)时母材与母材之间未完全熔合在一起,有时也常伴有夹渣存在。
(3)气孔:在熔化焊接过程中,焊缝金属内的气体或外界侵入的气体在熔池金属冷却凝固前未来得及逸出而残留在焊缝金属内部或表面形成的空穴或孔隙,视其形态可分为单个气孔、链状气孔、密集气孔(包括蜂窝状气孔)等,特别是在电弧焊中,由于冶金过程进行时间很短,熔池金属很快凝固,冶金过程中产生的气体、液态金属吸收的气体,或者焊条的焊剂受潮而在高温下分解产生气体,甚至是焊接环境中的湿度太大也会在高温下分解出气体等等,这些气体来不及析出时就会形成气孔缺陷。
尽管气孔较之其它的缺陷其应力集中趋势没有那么大,但是它破坏了焊缝金属的致密性,减少了焊缝金属的有效截面积,从而导致焊缝的强度降低。
某钢板对接焊缝X射线照相底片V型坡口,手工电弧焊,未焊透某钢板对接焊缝X射线照相底片V型坡口,手工电弧焊,密集气孔(4)夹渣与夹杂物:熔化焊接时的冶金反应产物,例如非金属杂质(氧化物、硫化物等)以及熔渣,由于焊接时未能逸出,或者多道焊接时清渣不干净,以至残留在焊缝金属内,称为夹渣或夹杂物。
视其形态可分为点状和条状,其外形通常是不规则的,其位置可能在焊缝与母材交界处,也可能存在于焊缝内。
另外,在采用钨极氩弧焊打底+手工电弧焊或者钨极氩弧焊时,钨极崩落的碎屑留在焊缝内则成为高密度夹杂物(俗称夹钨)。
W18Cr4V(高速工具钢)-45钢棒对接电阻焊缝中的夹渣断口照片钢板对接焊缝X射线照相底片V型坡口,手工电弧焊,局部夹渣钢板对接焊缝X射线照相底片V型坡口,手工电弧焊,两侧线状夹渣钢板对接焊缝X射线照相底片V型坡口,钨极氩弧焊打底+手工电弧焊,夹钨(5)裂纹:焊缝裂纹是焊接过程中或焊接完成后在焊接区域中出现的金属局部破裂的表现。
图解焊接缺陷大全

图解焊接缺陷大全修复方法:打磨去除该段焊缝,重新焊接。
弧坑针状气孔:修复方法:打磨去除该段焊缝,重新焊接。
气孔(砂眼):修复方法:打磨去除所有影响焊缝,重新焊接。
缩孔:修复方法:打磨去除所有影响焊缝,重新焊接。
端部裂纹/焊缝裂纹:修复方法:打磨去除所有影响焊缝,重新焊接。
不良焊缝外观:修复方法:重新焊接。
焊瘤及飞边:修复方法:打磨,重新焊接。
咬边:修复方法:重新焊接。
焊缝不均匀:修复方法:重新焊接。
不良外观:修复方法:重新焊接。
不良外观:修复方法:重新焊接。
各种焊缝缺陷及其在透照图像上的表现weld01(High Low、高低)welld02(Incomplete Root Fusion、根部未熔合)welld03(Insuffucient Reinforcement、增强高)welld04(Excess Root Penetration、根部焊瘤)welld05(External Undercut、外部咬肉) welld06(Internal Undercut、内部咬肉)welld07(Root Concavity 、根部凹陷)welld08(Burn Through 、烧穿)welld09(Isolated Slag Inclusion、单个的夹渣) welld10(Wagon Track Slag Line、线状夹渣)welld11(Interrun Fusion、内部未熔合) welld12(Lack of Sidewall Fusion、内侧未熔合)welld13(Porosity 、气孔)welld14(Cluster Porosity 、链状气孔)welld15(Hollow Bead 、夹珠)welld16(Transverse Crack 、横向裂纹)welld17(Centerline Crack 、中心线裂纹)welld18(Root Crack 、根部裂纹)气孔:CO2气体保护焊(1)母材不洁. (2)焊丝有锈或焊药潮湿. (3)点焊不良,焊丝选择不当. (4)干伸长度太长,CO2气体保护不周密.(5)风速较大,无挡风装置.(6)焊接速度太快,冷却快速. (7)火花飞溅粘在喷嘴,造成气体乱流. (8)气体纯度不良,含杂物多(特别含水分).(1)焊接前注意清洁被焊部位. (2)选用适当的焊丝并注意保持干燥. (3)点焊焊道不得有缺陷,同时要清洁干净,且使用焊丝尺寸要适当. (4)减小干伸长度,调整适当气体流量. (5)加装挡风设备. (6)降低速度使内部气体逸出. (7)注意清除喷嘴处焊渣,并涂以飞溅附着防止剂,以延长喷嘴寿命. (8)CO2纯度为99.98%以上,水分为0.005%以下.埋弧焊接(1)焊缝有锈、氧化膜、油脂等有机物的杂质. (2)焊剂潮湿. (3)焊剂受污染. (4)焊接速度过快. (5)焊剂高度不足.(6)焊剂高度过大,使气体不易逸出(特别在焊剂粒度细的情形). (7)焊丝生锈或沾有油污. (8)极性不适当(特别在对接时受污染会产生气孔).(1)焊缝需研磨或以火焰烧除,再以钢丝刷清除. (2)约需300℃干燥 (3)注意焊剂的储存及焊接部位附近地区的清洁,以免杂物混入. (4)降低焊接速度. (5)焊剂出口橡皮管口要调整高些. (6)焊剂出口橡皮管要调整低些,在自动焊接情形适当高度30-40mm.(7)换用清洁焊丝. (8)将直流正接(DC-)改为直流反接(DC+).设备不良 (1)减压表冷却,气体无法流出.(2)喷嘴被火花飞溅物堵塞.(3)焊丝有油、锈.(1)气体调节器无附电热器时,要加装电热器,同时检查表之流量.(2)经常清除喷嘴飞溅物.并且涂以飞溅附着防止剂.(3)焊丝贮存或安装焊丝时不可触及油类. 自保护药芯焊丝 (1)电压过高. (2)焊丝突出长度过短.(3)钢板表面有锈蚀、油漆、水分.(4)焊枪拖曳角倾斜太多. (5)移行速度太快,尤其横焊.(1)降低电压. (2)依各种焊丝说明使用. (3)焊前清除干净. (4)减少拖曳角至约0-20°. (5)调整适当.咬边:夹渣:手工电弧焊(1)前层焊渣未完全清除. (2)焊接电流太低.(3)焊接速度太慢.(4)焊条摆动过宽. (5)焊缝组合及设计不良. (1)彻底清除前层焊渣. (2)采用较高电流. (3)提高焊接速度. (4)减少焊条摆动宽度.(5)改正适当坡口角度及间隙.CO2气体 电弧焊 (1)母材倾斜(下坡)使焊渣超前. (2)前一道焊接后,焊渣未清洁干净. (3)电流过小,速度慢,焊着量多. (4)用前进法焊接,开槽内焊渣超前甚多. (1)尽可能将焊件放置水平位置. (2)注意每道焊道之清洁. (3)增加电流和焊速,使焊渣容易浮起. (4)提高焊接速度埋弧焊接(1)焊接方向朝母材倾斜方向,因此焊渣流动超前. (2)多层焊接时,开槽面受焊丝溶入,焊丝过于靠近开槽的侧边. (3)在焊接起点有导板处易产生夹渣.(4)电流过小,第二层间有焊渣留存,在焊接薄板时容易产生裂纹. (5)焊接速度过低,使焊渣超前. (6)最后完成层电弧电压过高,使得游离焊渣在焊道端头产生搅卷. (1)焊接改向相反方向焊接,或将母材尽可能改成水平方向焊接. (2)开槽侧面和焊丝之间距离,最少要大于焊丝直径以上. (3)导板厚度及开槽形状,需与母材相同. (4)提高焊接电流,使残留焊渣容易熔化. (5)增加焊接电流及焊接速度. (6)减小电压或提高焊速,必要时盖面层由单道焊改为多道焊接.自保护 药芯焊丝 (1)电弧电压过低. (2)焊丝摆弧不当. (3)焊丝伸出过长.(4)电流过低,焊接速度过慢. (5)第一道焊渣,未充分清除.(6)第一道结合不良. (7)坡口太狭窄. (8)焊缝向下倾斜.(1)调整适当. (2)加多练习. (3)依各种焊丝使用说明. (4)调整焊接参数. (5)完全清除 (6)使用适当电压,注意摆弧. (7)改正适当坡口角度及间隙. (8)放平,或移行速度加快.未焊透:裂纹手工电弧焊(1)焊件含有过高的碳、锰等合金元素. (2)焊条品质不良或潮湿. (3)焊缝拘束应力过大. (4)母条材质含硫过高不适于焊接.(5)施工准备不足. (6)母材厚度较大,冷却过速. (7)电流太强. (8)首道焊道不足抵抗收缩应力. (1)使用低氢系焊条. (2)使用适宜焊条,并注意干燥. (3)改良结构设计,注意焊接顺序,焊接后进行热处理. (4)避免使用不良钢材. (5)焊接时需考虑预热或后热. (6)预热母材,焊后缓冷. (7)使用适当电流. (8)首道焊接之焊着金属须充分抵抗收缩应力.CO2气体保护焊(1)开槽角度过小,在大电流焊接时,产生梨形和焊道裂纹. (2)母材含碳量和其它合金量过高(焊道及热影区). (3)多层焊接时,第一层焊道过小.(4)焊接顺序不当,产生拘束力过强. (5)焊丝潮湿,氢气侵入焊道. (6)套板密接不良,形成高低不平,致应力集中. (7)因第一层焊接量过多,冷却缓慢(不锈钢,铝合金等). (1)注意适当开槽角度与电流的配合,必要时要加大开槽角度. (2)采用含碳量低的焊条. (3)第一道焊着金属须充分能抵抗收缩应力. (4)改良结构设计,注意焊接顺序,焊后进行热处理.(5)注意焊丝保存. (6)注意焊件组合之精度. (7)注意正确的电流及焊接速度.埋弧焊接(1)对焊缝母材所用的焊丝和焊剂之配合不适当(母材含碳量过大,焊丝金属含锰量太少). (2)焊道急速冷却,使热影响区发生硬化. (3)焊丝含碳、硫量过大.(4)在多层焊接之第一层所生焊道力,不足抵抗收缩应力. (5)在角焊时过深的渗透或偏析. (6)焊接施工顺序不正确,母材拘束力大. (7)焊道形状不适当,焊道宽度与焊道深度比例过大或过小.(1)使用含锰量较高的焊丝,在母材含碳量多时,要有预热之措施. (2)焊接电流及电压需增加,焊接速度降低,母材需加热措施. (3)更换焊丝. (4)第一层焊道之焊着金属须充分抵抗收缩应力. (5)将焊接电流及焊接速度减低,改变极性. (6)注意规定的施工方法,并予焊接操作施工指导. (7)焊道宽度与深度的比例约为1:1:25,电流降低,电压加大.变形:其他缺陷:焊道外观形状不良(Bad Appearance) (1)焊条不良.(2)操作方法不适.(3)焊接电流过高,焊条直径过粗.(4)焊件过热.(5)焊道内,熔填方法不良.(6)导电嘴磨耗.(7)焊丝伸出长度不变.(1)选用适当大小良好的干燥焊条.(2)采用均匀适当之速度及焊接顺序.(3)选用适当电流及适当直径的焊接.(4)降低电流.(5)多加练习.(6)更换导电嘴.(7)保持定长、熟练.凹痕(Pit) (1)使用焊条不当.(2)焊条潮湿.(3)母材冷却过速.(4)焊条不洁及焊件的偏析.(5)焊件含碳、锰成分过高.(1)使用适当焊条,如无法消除时用低氢型焊条.(2)使用干燥过的焊条.(3)减低焊接速度,避免急冷,最好施以预热或后热.(4)使用良好低氢型焊条.(5)使用盐基度较高焊条.偏弧(Arc Blow) (1)在直流电焊时,焊件所生磁场不均,使电弧偏向.(2)接地线位置不佳.(3)焊枪拖曳角太大.(4)焊丝伸出长度太短.(5)电压太高,电弧太长.(6)电流太大.(7)焊接速度太快.(1)·电弧偏向一方置一地线.· 正对偏向一方焊接.·采用短电弧.·改正磁场使趋均一.·改用交流电焊(2)调整接地线位置.(3)减小焊枪拖曳角.(4)增长焊丝伸出长度.(5)降低电压及电弧.(6)调整使用适当电流.(7)焊接速度变慢.烧穿(1)在有开槽焊接时,电流过大.(2)因开槽不良焊缝间隙太大.(1)降低电流.(2)减少焊缝间隙.焊道不均匀(1)导电嘴磨损,焊丝输出产生摇摆.(2)焊枪操作不熟练.(1)将焊接导电嘴换新使用.(2)多加操作练习.焊泪(1)电流过大,焊接速度太慢.(2)电弧太短,焊道高.(3)焊丝对准位置不适当.(角焊时)(1)选用正确电流及焊接速度.(2)提高电弧长度.(3)焊丝不可离交点太远.火花飞溅过多(1)焊条不良.(2)电弧太长.(3)电流太高或太低.(4)电弧电压太高或太低.(5)焊丝突出过长.(6)焊枪倾斜过度,拖曳角太大.(7)焊丝过度吸湿.(8)焊机情况不良.(1)采用干燥合适之焊条.(2)使用较短之电弧.(3)使用适当之电流.(4)调整适当.(5)依各种焊丝使用说明.(6)尽可能保持垂直,避免过度倾斜.(7)注意仓库保管条件.(8)修理,平日注意保养.焊道成蛇行状(1)焊丝伸出过长.(2)焊丝扭曲.(3)直线操作不良.(1)采用适当的长度,例如实心焊丝在大电流时伸出长20-25mm.在自保护焊接时伸出长度约为40-50mm.(2)更换新焊丝或将扭曲予以校正.(3)在直线操作时,焊枪要保持垂直.电弧不稳定(1)焊枪前端之导电嘴比焊丝心径大太多.(2)导电嘴发生磨损.(3)焊丝发生卷曲.(4)焊丝输送机回转不顺.(5)焊丝输送轮子沟槽磨损.(6)加压轮子压紧不良.(7)导管接头阻力太大.(1)焊丝心径必须与导电嘴配合.(2)更换导电嘴.(3)将焊丝卷曲拉直.(4)将输送机轴加油,使回转润滑.(5)更换输送轮.(6)压力要适当,太松送线不良,太紧焊丝损坏.(7)导管弯曲过大,调整减少弯曲量.喷嘴与母材间发生电弧(1)喷嘴,导管或导电嘴间发生短路.(1)火花飞溅物粘及喷嘴过多须除去,或是使用焊枪有绝缘保护之陶瓷管.。
焊接缺陷,探伤图解
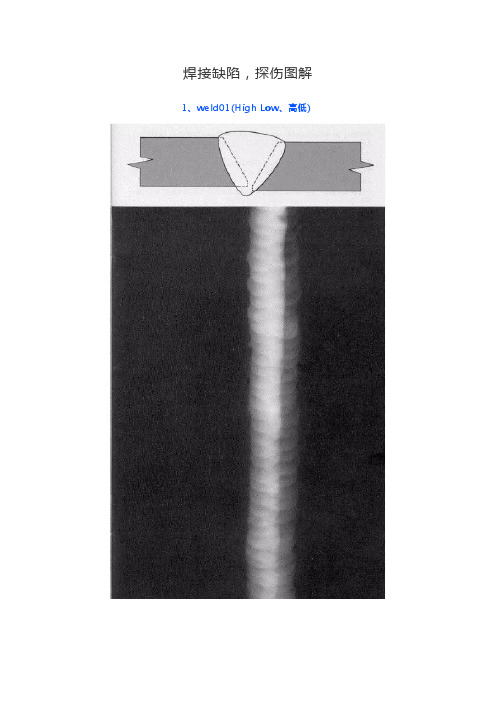
焊接缺陷,探伤图解1、weld01(High Low、高低)2、welld02(IncompleteRootFusion、根部未熔合)3、welld03(InsuffucientReinforcement、增强高)4、welld04(Excess RootPenetration、根部焊瘤)5、welld05(ExternalUndercut、外部咬肉)6、welld06(InternalUndercut、内部咬肉)7、welld07(RootConcavity、根部凹陷)8、welld08(BurnThrough、烧穿)9、welld09(Isolated SlagInclusion、单个的夹渣)10、welld10(WagonTrack Slag Line、线状夹渣)11、welld11(InterrunFusion、内部未熔合)12、welld12(Lack ofSidewallFusion、内侧未熔合)13、welld13(Porosity、气孔)14、welld14(Cluster Porosity、链状气孔)15、welld15(HollowBead、夹珠)16、welld16(Transverse Crack、横向裂纹)17、welld17(CenterlineCrack、中心线裂纹)18、welld18(根部裂纹)纹常见焊接缺陷产生原因、危害及防止措施一、焊接缺陷的分类焊接缺陷可分为外部缺陷和内部缺陷两种1.外部缺陷1)外观形状和尺寸不符合要求;2)表面裂纹;3)表面气孔;4)咬边;5)凹陷;6)满溢;7)焊瘤;8)弧坑;9)电弧擦伤;10)明冷缩孔;11)烧穿;12)过烧。
2.内部缺陷1)焊接裂纹:a.冷裂纹;b.层状撕裂;c.热裂纹;d.再热裂纹。
2)气孔;3)夹渣;4)未焊透;5)未熔合;6)夹钨;7)夹珠。
二、各种焊接缺陷产生原因、危害及防止措施1、外表面形状和尺寸不符合要求表现:外表面形状高低不平,焊缝成形不良,焊波粗劣,焊缝宽度不均匀,焊缝余高过高或过低,角焊缝焊脚单边或下凹过大,母材错边,接头的变形和翘曲超过了产品的允许范围等。
不良焊接图片及标准

批准审核编制版本号生效日期页码:1/3批准审核编制版本号生效日期焊接焊缝标准制定典型焊接焊缝不良图片及说明要求达成的效果说明检查岗位检查内容板翅岗位焊接检查焊接焊缝标准制定检查岗位板翅岗位检查内容焊接检查要求产品在制成过程中无焊弧烧伤要求焊缝美观,焊纹整齐:如产品在焊接过程中不适当的操作形成的弧坑产品在焊接过程中出现泄漏,经过补焊形成的焊疤产品在焊接中造成的电弧烧伤及焊溜要求焊缝美观,无焊溜及电弧烧伤现象出现夹渣与气孔要求焊缝美观,无夹渣气孔:如图产品在焊接中焊缝出现夹渣与气孔页码:2/3批准审核编制版本号生效日期焊接焊缝标准制定检查岗位板翅岗位典型焊接焊缝不良图片及说明氩弧焊焊接事项检查内容焊接检查要求达成的效果说明产品在焊接中出现的咬边现象要求焊缝均匀,无焊接咬边现象.如图产品在焊接中出现焊纹不均匀现象要求焊缝均匀.如图产品在焊接中出现翅片烧损现象要求焊缝均匀.美观.焊透无气孔产品在焊接过程中出现未焊透,未熔合现象.焊前准备1.根据焊接位置,焊2.去除焊接位置两3.根据图纸.工艺要4.检查所用设备是焊接注意事项1.焊接前,在废钢板2.在引弧板或焊接3.防止地线,电缆4.防止焊接过程中5.受压元件角焊缝6.接弧处应保证焊7.焊后自检.焊缝表焊接缺陷:焊接缺陷可分为电弧烧伤.表面气孔,和气孔等.焊接缺陷焊接焊缝检验标准要求焊缝表面过度,不能有锐角返修:表面的焊页码:3/3。
常见的焊接缺陷及缺陷图片
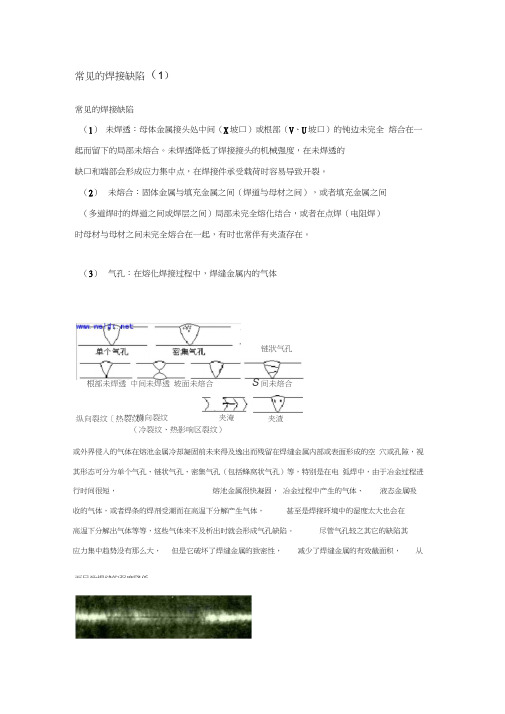
常见的焊接缺陷(1)常见的焊接缺陷(1) 未焊透:母体金属接头处中间(X 坡口)或根部(V 、U 坡口)的钝边未完全 熔合在一起而留下的局部未熔合。
未焊透降低了焊接接头的机械强度,在未焊透的缺口和端部会形成应力集中点,在焊接件承受载荷时容易导致开裂。
(2) 未熔合:固体金属与填充金属之间(焊道与母材之间),或者填充金属之间(多道焊时的焊道之间或焊层之间)局部未完全熔化结合,或者在点焊(电阻焊)时母材与母材之间未完全熔合在一起,有时也常伴有夹渣存在。
(3) 气孔:在熔化焊接过程中,焊缝金属内的气体或外界侵入的气体在熔池金属冷却凝固前未来得及逸岀而残留在焊缝金属内部或表面形成的空 穴或孔隙,视其形态可分为单个气孔、链状气孔、密集气孔(包括蜂窝状气孔)等,特别是在电 弧焊中,由于冶金过程进行时间很短, 熔池金属很快凝固, 冶金过程中产生的气体、 液态金属吸 收的气体,或者焊条的焊剂受潮而在高温下分解产生气体, 甚至是焊接环境中的湿度太大也会在高温下分解出气体等等,这些气体来不及析出时就会形成气孔缺陷。
尽管气孔较之其它的缺陷其应力集中趋势没有那么大, 但是它破坏了焊缝金属的致密性, 减少了焊缝金属的有效截面积,从""'横向裂纹 夹淹 (冷裂纹、热影响区裂纹) 纵向裂纹〔热裂纹)根部未焊透 中间未焊透 坡面未焙合 链狀气孔S 间未焙合夹渣而导致焊缝的强度降低。
某钢板对接焊缝X射线照相底片V型坡口,手工电弧焊,未焊透某钢板对接焊缝X射线照相底片V型坡口,手工电弧焊,密集气孔(4 )夹渣与夹杂物:熔化焊接时的冶金反应产物,例如非金属杂质(氧化物、硫化物等)以及熔渣,由于焊接时未能逸出,或者多道焊接时清渣不干净,以至残留在焊缝金属内,称为夹渣或夹杂物。
视其形态可分为点状和条状,其外形通常是不规则的,其位置可能在焊缝与母材交界处,也可能存在于焊缝内。
另外,在采用钨极氩弧焊打底+手工电弧焊或者钨极氩弧焊时,钨极崩落的碎屑留在焊缝内则成为高密度夹杂物(俗称夹钨)。
焊缝检验参考图集
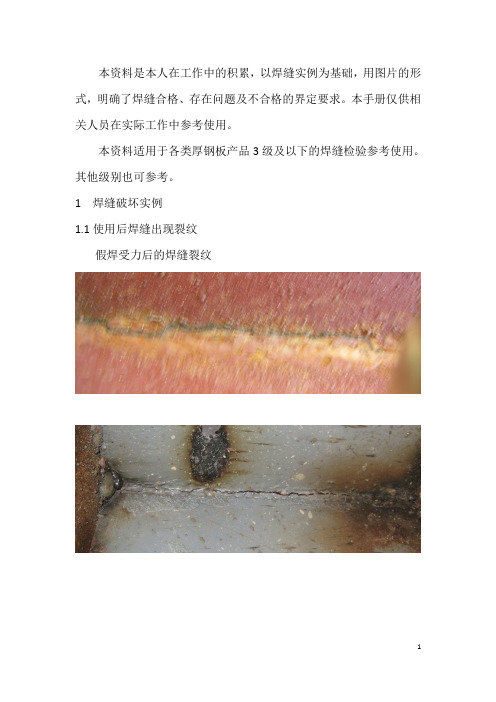
本资料是本人在工作中的积累,以焊缝实例为基础,用图片的形式,明确了焊缝合格、存在问题及不合格的界定要求。
本手册仅供相关人员在实际工作中参考使用。
本资料适用于各类厚钢板产品3级及以下的焊缝检验参考使用。
其他级别也可参考。
1 焊缝破坏实例
1.1使用后焊缝出现裂纹
假焊受力后的焊缝裂纹
1.2 假焊焊缝使用后焊缝撕裂
1.4焊接质量不合格导致使用时焊缝撕裂
1.3 焊缝缺陷导致使用时出现焊缝裂纹
1.5 焊缝高度不合格
1.6焊缝不合格导致破坏
1.7焊缝不合格导致秤体在使用时出现焊缝裂纹
1.8假焊受力后形成的裂纹
1.9假焊形成的裂纹
1.10焊接缺陷,气孔、裂纹等
1.11焊缝夹渣,受力后从夹渣处开始破坏
1.12 焊接电流过大,材料退火导致应力集中使结构破坏
2焊缝实例
下图中的焊缝太薄,实际是假焊,该处母材未融化,只是在母材外表面涂了一层焊液。
材料没有融合在一起,该结构起不了受力作用。
反面过烧,材料性能破坏,不合格。
易造成面板变形,影响产品质量,缩短产品寿命
未焊到位、断焊,焊瘤,不合格
表面链状气孔,不合格
焊缝不合格,欠焊
焊缝外观不合格
穿透性气孔
3 合格焊缝图集3.1 平焊焊缝
3.2立焊
3.2.1 从下往上焊
3.2.2从上往下焊
21。
- 1、下载文档前请自行甄别文档内容的完整性,平台不提供额外的编辑、内容补充、找答案等附加服务。
- 2、"仅部分预览"的文档,不可在线预览部分如存在完整性等问题,可反馈申请退款(可完整预览的文档不适用该条件!)。
- 3、如文档侵犯您的权益,请联系客服反馈,我们会尽快为您处理(人工客服工作时间:9:00-18:30)。
焊缝缺陷图示
1焊鳞
焊鳞
去除焊鳞
后焊缝表面2-气孔
修复方法:打磨去除该段焊缝,重新焊接。
3- 弧坑针状气孔
修复方法:打磨去除该段焊缝,重新焊接。
4-气孔(砂眼)
修复方法:打磨去除所有影响焊缝,重新焊接。
5-缩孔
修复方法:打磨去除所有影响焊缝,重新焊接。
6-端部裂纹/焊缝裂纹
修复方法:打磨去除所有影响焊缝,重新焊接。
7-不良焊缝外观
修复方法:重新焊接。
8-焊瘤及飞边
修复方法:打磨,重新焊接。
9-咬边
修复方法:重新焊接。
10-咬边
修复方法:重新焊接。
11-焊缝不均匀
修复方法:重新焊接。
12‘-不良外观
修复方法:重新焊接。
13‘-不良外观
修复方法:重新焊接。
14‘-不良外观。