标准海管UT工艺
UT通用工艺规程

UT通⽤⼯艺规程1 适⽤范围1.1 本规程适⽤于公司承压设备采⽤A型脉冲反射式超声仪检测⼯件缺陷的超声检测⽅法和质量分级。
1.2 本规程适⽤于⾦属材料制承压设备⽤原材料或零部件和焊接接头的超声检测,也适⽤于⾦属材料制再⽤承压设备的超声检测。
1.3 本规程规定了承压设备厚度的超声测量⽅法。
1.4 与承压设备有关的⽀撑件和结构件的超声检测,也可参照本规程。
2 依据标准TSG R0004-2009 《固定式压⼒容器安全技术监察规程》GB150-2011 《压⼒容器》NB/T47013-2015 《承压设备⽆损检测》3 术语和定义本规程引⽤设术语和定义按照NB/T47013.1中第3条款及NB/T47013.3中第3条款的界定。
4 检测⼈员4.1 超声检测检测的⼈员应满⾜NB/T47013.1的有关规定。
4.2超声检测⼈员应具有⼀定的⾦属材料、设备制造安装、焊接及热处理等⽅⾯的基本知识,应熟悉被捡⼯件的材质、⼏何尺⼨及透声性等,对检测中出现的问题能作出分析、判断和处理。
5 检测设备和器材5.1 推荐使⽤下⾯的超声仪仪器型号产地HS600 武汉中科PXUT-350C 南通友联5.2 检测仪器、探头和组合性能5.2.1检测仪器采⽤A型脉冲反射式超声检测仪,起⼯作频率按-3dB测量应⾄少包括0.5MHz-10MHz频率范围,超声仪器各性能的测试条件和指标要求应满⾜NB/T47013.3附录A的要求并提供证明⽂件,测试⽅法按GB/T27664.1的规定。
圆形晶⽚直径⼀般不应⼤于40mm,⽅形晶⽚任⼀边长⼀般不应⼤于40mm,其性能指标应符合NB/T47013.3附录的要求并提供证明⽂件,测试⽅法按GB/T27664.2的规定。
5.2.3 仪器和探头的组合性能5.2.3.1 仪器和探头的组合性能包括⽔平线性、垂直线性、组合频率、灵敏度余量、盲区(仅限直探头)和远场分辨⼒。
5.2.3.2 新购置的超声检测仪器和探头,或仪器和探头在维修或更换主要部件后及检测⼈员有怀疑时应测定仪器和探头的组合性能。
海底管线铺设焊接工艺与设备研究
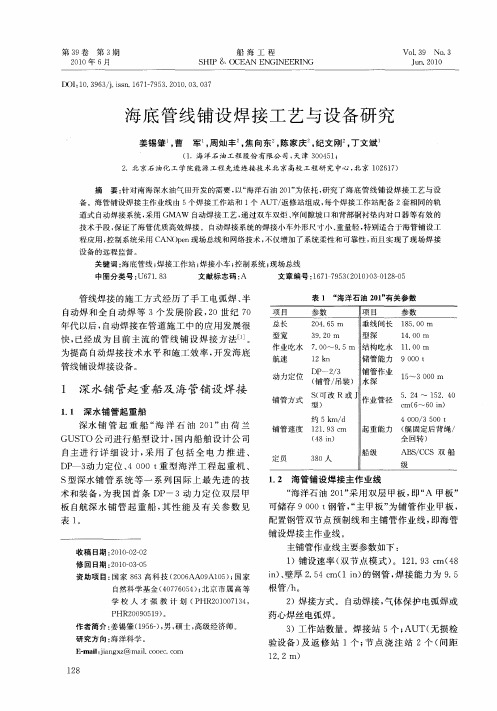
1 2 海 管铺设 焊接 主作业线 . “ 海洋 石 油 2 1 采用 双 层 甲板 , A 甲板 ” 0” 即“ 可储 存 90 0t 0 钢管 , 主 甲板 ” “ 为铺 管 作业 甲板 ,
配 置钢管 双节 点预 制 线 和 主铺 管作 业 线 , 海管 即
铺设 焊接 主作业线 。 主铺管 作业线 主要参 数如 下 : 1 设速 率 ( )铺 双节 点 模 式 ) 2 . 3c 4 。1 1 9 m( 8 i)壁 厚 2 5 m( n 的钢 管 , 接 能力 为 9 5 n、 . 4c 1i) 焊 .
根 管/ 。 h
收 稿 日期 :000—2 2 1—20
修 回 日期 :000—5 2 1—30 资 助 项 目 : 家 8 3高 科 技 ( 0 6 0 A1 5 ; 国 6 2 0 AA 9 O ) 国家 自然科 学 基 金 ( 07 0 4 ; 京 市 属 高 等 4765)北 学 校 人 才 强 教 计 划 ( HR 0 0 7 3 , P 2 1 0 14
参 数 1 50 8 . 0m
1 .0m 4 0
快, 已经成 为 目前 主 流 的 管 线 铺 设 焊 接 方 法 l 。 】 J 为提 高 自动 焊接 技术 水 平 和施 工 效率 , 开发 海底
作业 吃水 航速
7 。 ~ 9 5m 结 构 吃 水 . 0 . 1 n 2k 储管能力
备 。海管铺设焊接主作业线由 5 个焊接工作站和 1 A 个 UT/ 返修站组 成 , 每个焊接工作站配备 2套相同的轨 道式 自动焊接系统 , 采用 GMA 自动焊接工艺 , W 通过双车双炬 、 窄间隙坡 口和背部铜衬垫 内对 口器等 有效的 技术手段 , 保证了海管优质高效焊接 。自动焊接系统 的焊接小车外形尺寸小 、 重量轻 , 特别适合于海管铺设工
对管道问题的最权威解答(4)

对管道问题的最权威解答(4)身为全国锅炉压力容器标准化技术委员会压力管道分技术委员会副秘书长,《压力管道安全技术监察规程一工业管道》和《压力管道规范一工业管道》的主要起草人,ASME相关规范的译者和校对者之一,应道宴大师每天都会接到许多来自全国各地管道从业人员的咨询。
为了能够帮助更多的管道人,为了能让知识更大范围地传播,管道365特开设【管问应答】栏目,搜集和整理应大师的答复,为管道人答疑解惑!问:首次出现撬装系统监督检验,是在TSG21-2016实施意见中提出的,只是说系统需要监督检验,但是没有规定应该监管的管道是按照安装过程还是制作过程来监管,所以监督检验的时候,每一小段耐压试验是否应该作为A类项目进行监督检验,应该注意什么呢?答:大的撬装也可把它当作一个小装置。
其中不同的容器,不同的管道,有不同的设计条件和耍求。
因此,装置中是如何处理的,撬装中也实事求是地同样规则处理。
而不是认为是一个位号,而要执行什么统一的要求。
这就是我理解的实事求是。
压缩机撬装柔性分析请参考有关管道规范。
质检总局特种设备局关于《固定式压力容器安全技术监察规程》(TSG21-2016)的实施意见(质检特函(2016)46号)2016-09-30(六)使用管理。
2.关于撬装式承压设备系统或机械设备系统(以下简称“设备系统”)的使用登记。
(1)安装在“设备系统”上的压力容器和压力管道,应当由具有相应资质的单位设计、制造,并依据相应安全技术规范要求经过制造监督检验。
(2)包含压力容器或压力管道的“设备系统”,其制造单位应当持有相应级别的压力容器制造许可证、压力管道元件制造许可证或压力管道安装许可证,系统经过制造监督检验(其中安全技术规范中未规定制造监督检验的压力管道元件可参照安装监督检验的要求进行)。
(3)“设备系统”中的压力管道可作为压力容器附属装置一并按照压力容器办理使用登记;只有压力管道的,按照压力管道办理使用登记。
(4)“设备系统”由使用单位直接申请办理使用登记(简单压力容器和本规程14范围内的压力容器除外),不需要办理压力容器或压力管道安装告知和安装监检。
海洋平台海底管道立管环空区域封堵灌浆防腐施工工艺
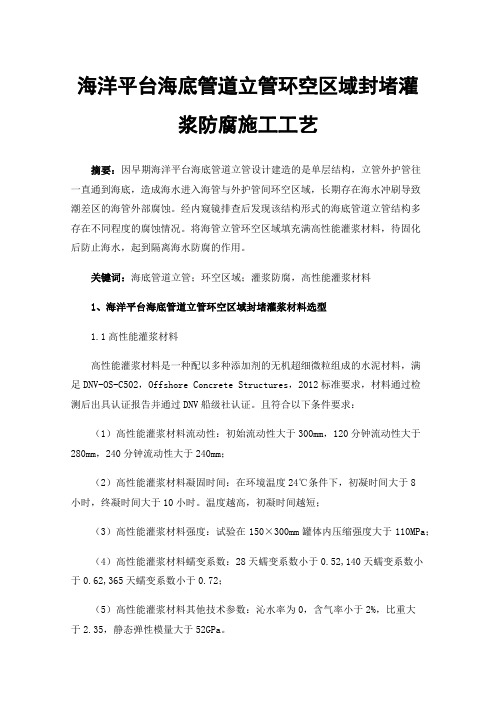
海洋平台海底管道立管环空区域封堵灌浆防腐施工工艺摘要:因早期海洋平台海底管道立管设计建造的是单层结构,立管外护管往一直通到海底,造成海水进入海管与外护管间环空区域,长期存在海水冲刷导致潮差区的海管外部腐蚀。
经内窥镜排查后发现该结构形式的海底管道立管结构多存在不同程度的腐蚀情况。
将海管立管环空区域填充满高性能灌浆材料,待固化后防止海水,起到隔离海水防腐的作用。
关键词:海底管道立管;环空区域;灌浆防腐,高性能灌浆材料1、海洋平台海底管道立管环空区域封堵灌浆材料选型1.1高性能灌浆材料高性能灌浆材料是一种配以多种添加剂的无机超细微粒组成的水泥材料,满足DNV-OS-C502,Offshore Concrete Structures,2012标准要求,材料通过检测后出具认证报告并通过DNV船级社认证。
且符合以下条件要求:(1)高性能灌浆材料流动性:初始流动性大于300mm,120分钟流动性大于280mm,240分钟流动性大于240mm;(2)高性能灌浆材料凝固时间:在环境温度24℃条件下,初凝时间大于8小时,终凝时间大于10小时。
温度越高,初凝时间越短;(3)高性能灌浆材料强度:试验在150×300mm罐体内压缩强度大于110MPa;(4)高性能灌浆材料蠕变系数:28天蠕变系数小于0.52,140天蠕变系数小于0.62,365天蠕变系数小于0.72;(5)高性能灌浆材料其他技术参数:沁水率为0,含气率小于2%,比重大于2.35,静态弹性模量大于52GPa。
1.2 封堵设备及密封工具材料(1)环空封隔器:采用套筒模式使用机械机关驱动的锚固装置,其设计最大承载重量超过3吨,套筒向外伸长的张力抓,抓住护管的内壁且不能伤及内管壁,在海管环空区域的水下至少1米处完成锚固安装。
环空封隔器的设计直径应满足直径间隔4寸宽度,再减去内外管两个管壁的尺寸宽度,以便能卡在内外管环空空隙区域空间内;(2)两端封口板:材质为316不锈钢的环形圈板,用于海管立管环空段下上端封口,下端封口板防止高性能灌注材料漏入海里,上端封口板防止灌浆材料漫出环空区域内;(3)水下堵漏球:一种快干灌浆材料容量包,常温下5分钟之内固化,可实现水下固化封堵,球体直径大于10cm ,渗水率1GPM以下;(4)环氧粘接层UW:主要材质为聚乙烯,具有良好的柔韧性适用于海水以及潮湿的工况,自流平设计,零VOC, 耐化学腐蚀,耐磨,完全固化时间不得多于24小时。
UT焊缝工艺

压力容器焊缝超声波检测工艺规程1 适用范围1.1 本工艺规程适用于母材厚度8~120mm锅炉、钢制压力容器、压力管道及特种设备对接缝的超声检测。
1.2 本工艺不适用于弯头与直管、带颈法兰与直管、回弯头与直管以接焊缝的超声波探伤与评级。
2 引用标准2.1 GB 150 《钢制压力容器》2.2 JB 4730-94 《压力容器无损检测》2.3 JB4126 《超声波检验用钢制试块的制造和控制》2.4 ZBJ04 001《A型脉冲反射式超声探伤仪通用技术条件》2.5 ZBY230 《A型脉冲反射式超声探伤仪通用技术条件》2.6 ZBY231 《超声探伤用探头性能测试方法》3 人员要求3.1 从事超声波探伤的检测人员应严格按《特种设备无损检测人员考核与监督管理规则》的要求,经培训考核取得特种设备安全监察机构颁发的有效资格证,从事与考核项目及级别相应的无损检测工作。
3.2 应具有丰富的超声波检测经验,掌握一定的材料、焊接基础知识。
3.3 超声波检测人员的视力应每年检查一次,校正视力不低于1.0。
3.4报告编制、审核人资格不低于UTⅡ级,初级人员从事超声波检测辅助工作。
4检测仪器、试块、耦合剂4.1 检测仪器应采用A型脉冲反射式超声波探伤仪,其工作频率范围为2.5~5mHz。
仪器至少在荧光屏满刻度的80%范围内呈线性显示。
衰减器具有80dB 以上连续可调,步进级每档不大于2dB,其精度为任意相邻12dB误差在±1dB 以内,最大累计误差不超过1dB。
水平线性误差不大于1%。
垂直线性误差不大于5%,在使用过程中,每隔三个月仪器水平线性和垂直线性进行一次测定。
测定方法按ZBY 230规定进行。
4.2 探头4.2.1 斜探头声束轴线水平偏离角不应大于2°,主声束垂直方向不应有明显的双峰。
4.2.2 斜探头每个工作日应在标准试块上校准试块上校准前沿距离、K值和主声速偏离。
4.3 仪器和探头的系统性能在达到所探工件的最大检测声程时,其有效灵敏度余量应大于或等于10dB。
检测内柔外刚的海底管线要内外兼修

海底输送管线多数埋在海底土中一定深度,其检测不同于陆上管线,陆上管线可以用飞机巡线或人工步行巡线,而深海管道只能用间接地经过潜艇等带仪器随着线路扫描,收集数据,通过计算机判断管线是否处于安全范围,或处于可接受的边缘。
没有人直接检查来得直接、准确可靠、权威。
深海管道的检测需要一套特殊的船只与潜艇,因此检测费用是很高的。
浅海海底管线可以依靠潜水员下水检测,但某些处于潮差波浪破碎带的管段,受风浪、潮流、冰凌等影响很大,潜水员检测有困难。
海底管线剩余壁厚和管体裂纹的检测只能内检测,不能进行外检测。
因此,海底管道的检测与陆上管道根本不同。
检测要选择合理季节,避开台风,捕渔季节。
1内检测01剩余壁厚和裂纹检测海底管线腐蚀剩余壁厚和管线裂纹适宜用清管器型内检测装置(smart pig)进行全线检测。
漏磁检测清管器(MFL)适用于油、气管线检测,只允许检测壁厚12mm以内的管道,检测精度不高,不能检测裂纹,可以检测到外壁腐蚀区段。
超声波内检测清管器(UT)既不适用于海底厚壁管的检测,海底海管大多是厚壁管,也不适用于气管线检测,但其精度较高,通过改进可以探测纵向裂纹。
不同类型的清管器漏磁检测器检测漏磁检测器是目前管道检测中应用历史较长,技术较成熟的设备,主要用在管道穿孔之前确定腐蚀剩余壁厚和行走距离。
漏磁检测器由电池模块、传感器模块一起通过联轴器连接成一体。
漏磁检测的原理是:漏磁式检测器的磁铁将磁通引入管壁,当检测器在管内行走时,如果管壁无缺陷,则磁力线囿于管壁之内;如果管道内外表面有缺陷,则有一部分磁力线会穿到管壁之外,并发生扭曲。
这些穿出管壁且被扭曲的磁力线可被漏磁式检测器的线圈或磁铁两极之间的传感器检测出来并形成电信号。
中国、美国、英国、德国都可以生产先进的漏磁检测器。
美国公司系缆式海底集油、集气管线漏磁检测器能检测管线的腐蚀状况和准确确定泄漏点位置,最大检测长度为3.2km。
我国中石化具有完全知识产权的三轴高清漏磁检测器、惯性导航测量系统和基于弱磁技术的管道应力检测系统,可以检测出最小长度5毫米、最小深度0.5毫米的腐蚀和机械划伤等缺陷,并能对缺陷位置进行高精度定位,还能检测出海底管道应力异常情况和管道漂移情况。
基于DNV-RP-F101规范的腐蚀海底管道强度评估研究

基于DNV-RP-F101规范的腐蚀海底管道强度评估研究王猛;赵冬岩【摘要】近年来海底管道由于腐蚀缺陷造成失效的事件有增多的趋势。
为了评估在管道发生腐蚀后失效的风险性,对DNV-RP-F101的腐蚀管道强度评估方法进行研究,通过算例对影响强度评估的关键因素进行了敏感性分析,并对DNV-RP-F101和DNV-OS-F101的关系进行了探讨。
结果表明,影响强度评估结果的三个主要因素中,缺陷检测数据误差对评估结果影响最大。
当满足一定条件时,屈强比对评估结果的影响可忽略。
【期刊名称】《海洋工程装备与技术》【年(卷),期】2017(004)005【总页数】5页(P276-280)【关键词】海底管道腐蚀缺陷强度评估【作者】王猛;赵冬岩【作者单位】海洋石油工程股份有限公司,天津300451;海洋石油工程股份有限公司,天津300451【正文语种】中文【中图分类】TE973随着国内海洋工程的发展,我国在役海底管道总长度已超过6000km。
但由于运营维护技术和管理上的原因,多数管道自从投产以来未进行任何清管、通球等基本的维护活动。
20%的海底管道无法进行内检,管道的腐蚀和强度现状对管道安全运行存在重大影响。
腐蚀导致管道壁厚减薄,使管道承压能力降低且引起应力集中。
当腐蚀缺陷的深度和数量达到一定程度时,为维护管道而进行的修复、停工将造成经济损失。
更为严重的是管道发生破裂,引发事故。
因此,国内对缺陷检测和评估的需求日益迫切。
对管道缺陷的检测和评估技术已经发展了40年,并形成了成熟的规范。
美国Battlle研究所根据断裂力学理论和爆裂试验结果提出了半理论半经验公式NG-18[1];美国机械工程师协会(ASME)在此基础上建立了腐蚀管道评估规范ASMEB31G[2];Kiefner等[3]在NG-18的基础上对其进行了修正,将短腐蚀近似为抛物线形腐蚀,而将长腐蚀近似为矩形腐蚀,称之为改进的B31G方法;Fu等[4]釆用非线性有限元模拟分析腐蚀管道承压状态,证明基于应力失效准则的非线性有限元分析方法能较为准确地预测腐蚀管道的极限内压;挪威船级社(DNV)对腐蚀海底管道进行一系列数值模拟和试验研究,并结合英国天然气公司的研究成果,形成了DNV-RP-F101腐蚀管道剩余强度评估推荐规范[5]。
ut工艺规程和操作指导书(1)

UT检测工艺一、检测工艺文件检测工艺文件包括工艺规程和操作指导书。
二、超声检测工艺规程→超声检测工艺规程应根据相关法规、安全技术规范、产品标准、有关的技术文件和NB/T 3-2015等相关检测标准要求,并针对检测机构的特点和检测能力而编制的技术文件。
→超声检测工艺规程应涵盖本单位(制造、安装或检验检测单位)产品(或检测对象)的检测范围。
→超声检测通用工艺规程一般以文字说明为主,检测对象一般为某类工件,它应具有一定的覆盖性和通用性。
工艺规程的编制要点(1)涵盖本单位的检测范围,是通用性技术要求、原则性指导文件;(2)根据检测单位的特点和能力编写,是对现行标准规范的补充;(3)内容不能照搬照抄外单位的文件,必须有本单位的特色;|(4)跟具体的工程项目没有必要的关联,是检测单位自身检测能力的体现;(5)由检测单位Ⅲ级专业人员编制,检测责任师审核,单位技术负责人批准;(6)规程中某一项技术要求需要展开说明的,可采用附录形式编入;(7)不得将管理制度、操作规程等与工艺规程无关的内容写入正文;(8)工艺规程要完整,一些关键的数据和指标应明确写入规程中,以供检测人员使用;(9)工艺规程的编制应按NB/~的规定明确其相关因素的具体范围或要求,如相关因素的变化超出规定时,应重新编制或修订。
(10)相应检测标准变更、采用新的检测工艺时,应对工艺规程进行修订,重新审批发布。
(如果来不及修订工艺规程时,所编制的操作指导书应由检测单位技术负责人批准)。
工艺规程的编制原则(1)遵照国家现行标准和法规的要求,在检测工艺上可以比现行标准、法规更细,更具体,要求更高;(2)应根据本单位无损检测人员技术水平、检测能力,做到简明扼要,提出切实可行的工艺措施;(3)应采用本单位一些行之有效的做法,应有自己的特色;`(4)工艺规程中每一步骤都要写清楚做什么、由谁去做、采用什么设备和辅助器材、什么时机做、按什么标准做;(5)采用非标准检测工艺(如非标准温度范围内的渗透检测、探头移动区不符合要求的超声波检测、焦距不符合要求的射线检测等)时,应对该检测工艺进行验证;(6)明确对操作人员和责任人员的职责和要求;(7)要融入其它施工质量验收规范中有关无损检测方面的内容(如SH/T3543-2007 石油化工建设工程项目施工过程技术文件规定条的要求:无损检测单位应按SH/T3503的规定提交无损检测报告。
UT探伤工艺

无损检测工艺坡口焊缝的超声波检测上海振华港口机械(集团)股份有限公司常州基地质检部探伤室坡口焊缝的超声波检测工艺1.主题内容与适用范围本标准适用于ZPMC制造起重机械如集装箱岸桥和场桥、卸船机、散货机等起重机械钢结构焊缝的超声检测。
1.1每种无损探伤方法均有优点和局限性,各种方法对缺陷的检测几率也不会相同,超声探伤(UT)方法主要用于检测被检物的内部缺陷。
1.2本工艺与标准适用于指导厚度在8mm和200mm之间、包括这两个厚度在内的坡口焊缝和热影响区进行的超声检测。
这些工艺和标准不适用于管材与管材的T、Y或K形连接焊缝的检测。
1.3母材这些工艺不打算用于母材采购的检测。
不过,与焊接有关的、在邻近(焊缝的)母材中出现的、按本规范条款为不合格的不连续(开裂,层状撕裂,分层等),必须报告工程师处理。
2.引用标准ANST/AWSD1.1-2002美国国家标准-钢结构焊接规范JB4730-1994中国机械行业标准压力容器无损检测3.超声探伤人员资质审定3.1只有取得专业认证机构颁发NDTUT-II级及II级以上资格的人员才可以独立进行超声检测、签发报告。
3.2资质审定按GB9445进行,由书面考试和用以证明操作能力的操作考试组成,操作考试应使用生产中检验焊缝所用的专用设备和规程。
这一考试必须要求超声操作人员证明其具有应用本规范规定准确探测和处理检测结果的能力。
4.超声设备4.1设备要求超声仪器必须为脉冲反射式探伤仪,配用振荡频率为1~6MHz的换能器。
显示必须为整流的视频扫描的A型显示。
4.2水平线性检测仪器的水平必须按“AWSD1.1:2002版钢结构焊接规范”6.30.1在检测所用的全声程距离内进行鉴定。
4.3检测仪器要求检测仪器必须带有内部稳压装置,使得温升后当额定供电电压变化15%、或在使用电池情况下整个充电使用寿命时间内,响应变化不大于±1dB。
必须装一警报器或仪表,以便在电池耗尽而仪器切断之前,发出电池电压下降信号。
TKY管节点UT检测专家系统研究
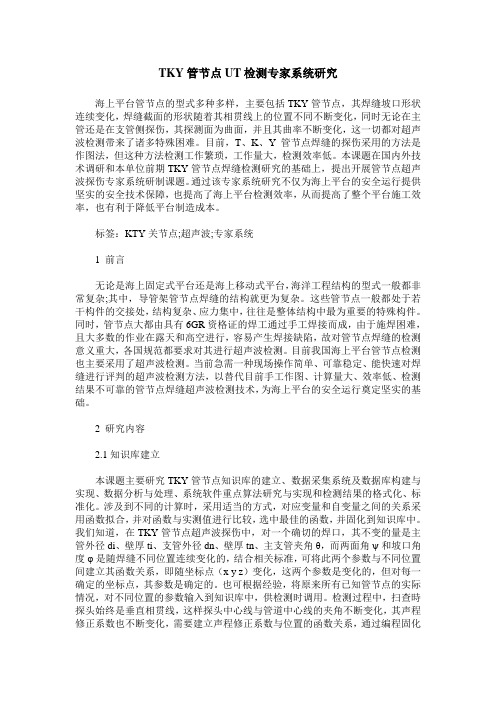
TKY管节点UT检测专家系统研究海上平台管节点的型式多种多样,主要包括TKY管节点,其焊缝坡口形状连续变化,焊缝截面的形状随着其相贯线上的位置不同不断变化,同时无论在主管还是在支管侧探伤,其探测面为曲面,并且其曲率不断变化,这一切都对超声波检测带来了诸多特殊困难。
目前,T、K、Y管节点焊缝的探伤采用的方法是作图法,但这种方法检测工作繁琐,工作量大,检测效率低。
本课题在国内外技术调研和本单位前期TKY管节点焊缝检测研究的基础上,提出开展管节点超声波探伤专家系统研制课题。
通过该专家系统研究不仅为海上平台的安全运行提供坚实的安全技术保障,也提高了海上平台检测效率,从而提高了整个平台施工效率,也有利于降低平台制造成本。
标签:KTY关节点;超声波;专家系统1 前言无论是海上固定式平台还是海上移动式平台,海洋工程结构的型式一般都非常复杂;其中,导管架管节点焊缝的结构就更为复杂。
这些管节点一般都处于若干构件的交接处,结构复杂、应力集中,往往是整体结构中最为重要的特殊构件。
同时,管节点大都由具有6GR资格证的焊工通过手工焊接而成,由于施焊困难,且大多数的作业在露天和高空进行,容易产生焊接缺陷,故对管节点焊缝的检测意义重大,各国规范都要求对其进行超声波检测。
目前我国海上平台管节点检测也主要采用了超声波检测。
当前急需一种现场操作简单、可靠稳定、能快速对焊缝进行评判的超声波检测方法,以替代目前手工作图、计算量大、效率低、检测结果不可靠的管节点焊缝超声波检测技术,为海上平台的安全运行奠定坚实的基础。
2 研究内容2.1知识库建立本课题主要研究TKY管节点知识库的建立、数据采集系统及数据库构建与实现、数据分析与处理、系统软件重点算法研究与实现和检测结果的格式化、标准化。
涉及到不同的计算时,采用适当的方式,对应变量和自变量之间的关系采用函数拟合,并对函数与实测值进行比较,选中最佳的函数,并固化到知识库中。
我们知道,在TKY管节点超声波探伤中,对一个确切的焊口,其不变的量是主管外径di、壁厚ti、支管外径dn、壁厚tn、主支管夹角θ,而两面角ψ和坡口角度φ是随焊缝不同位置连续变化的,结合相关标准,可将此两个参数与不同位置间建立其函数关系,即随坐标点(x y z)变化,这两个参数是变化的,但对每一确定的坐标点,其参数是确定的。
PAUT和AUT检测技术在海管检测中的对比分析
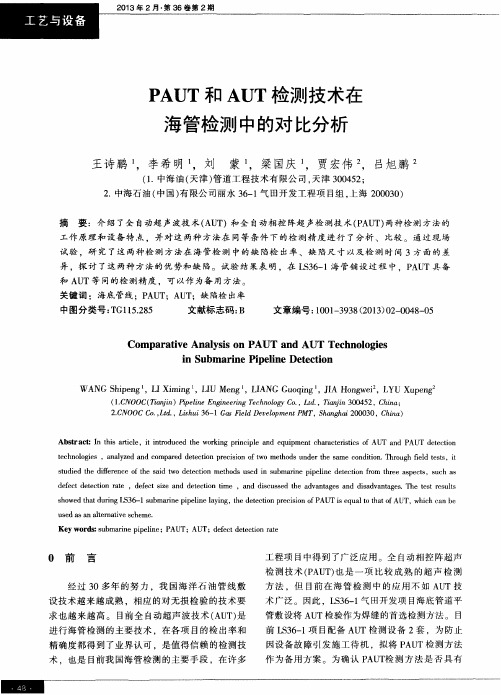
王诗 鹏 ,李 希 明 ,刘 蒙 ,梁 国庆 ,贾宏 伟 , 吕旭 鹏
( 1 . 中海油 ( 天津 ) 管道 工程 技术有 限公 司 , 天津 3 0 0 4 5 2 ;
2 . 中海石 油 ( 中国 ) 有 限公 司丽水 3 6 — 1 气 田开发 工程项 目组 , 上海 2 0 0 0 3 0 )
Ke y wo r ds : s ub mar in e pi p e l i ne;P AUT;AUT;de f e c t de t e c t i o n r a t e
2 . C NOOC C o . , L t d . ,L i s h u i 3 6 — 1 Ga s F i e l d De v e l o p me n t P MT ,S h a n g h a i 2 0 0 0 3 0,C h i n a)
Ab s t r a c t :I n t h i s a r t i c l e ,i t i n t r o d u c e d t h e wo r k i n g p i r n c i p l e a n d e q u i p me n t c h a r a c t e i r s t i c s o f AUT a n d P AU T d e t e c t i o n t e c h n o l o g i e s ,a n a l y z e d a n d c o mp a r e d d e t e c t i o n p r e c i s i o n o f t w o me t h o d s u n d e r t h e s a me c o n d i t i o n . T h r o u g h i f e l d t e s t s ,i t
UT探伤工艺

无损检测工艺坡口焊缝的超声波检测上海振华港口机械(集团)股份有限公司常州基地质检部探伤室坡口焊缝的超声波检测工艺1. 主题内容与适用范围本标准适用于ZPMC制造起重机械如集装箱岸桥和场桥、卸船机、散货机等起重机械钢结构焊缝的超声检测。
每种无损探伤方法均有优点和局限性,各种方法对缺陷的检测几率也不会相同,超声探伤(UT)方法主要用于检测被检物的内部缺陷。
本工艺与标准适用于指导厚度在 8mm和200mm之间、包括这两个厚度在内的坡口焊缝和热影响区进行的超声检测。
这些工艺和标准不适用于管材与管材的T、Y或K形连接焊缝的检测。
母材这些工艺不打算用于母材采购的检测。
不过,与焊接有关的、在邻近(焊缝的)母材中出现的、按本规范条款为不合格的不连续(开裂,层状撕裂,分层等),必须报告工程师处理。
2. 引用标准ANST/AWS 美国国家标准-钢结构焊接规范JB 4730-1994 中国机械行业标准压力容器无损检测3. 超声探伤人员资质审定只有取得专业认证机构颁发NDT UT-II级及II级以上资格的人员才可以独立进行超声检测、签发报告。
资质审定按GB9445进行,由书面考试和用以证明操作能力的操作考试组成,操作考试应使用生产中检验焊缝所用的专用设备和规程。
这一考试必须要求超声操作人员证明其具有应用本规范规定准确探测和处理检测结果的能力。
4. 超声设备设备要求超声仪器必须为脉冲反射式探伤仪,配用振荡频率为1~6MHz的换能器。
显示必须为整流的视频扫描的A型显示。
水平线性检测仪器的水平必须按“AWS :2002版钢结构焊接规范”6.30.1在检测所用的全声程距离内进行鉴定。
检测仪器要求检测仪器必须带有内部稳压装置,使得温升后当额定供电电压变化15%、或在使用电池情况下整个充电使用寿命时间内,响应变化不大于±1dB。
必须装一警报器或仪表,以便在电池耗尽而仪器切断之前,发出电池电压下降信号。
检测仪器的校准检测仪器必须有校准用增益(衰减)控制器,它应至少在60dB的整个范围内每档1dB或2dB间断可调。
T K Y 型管接点焊缝UT检验工艺

1.5.3 T K Y型管状焊缝缺陷定位基准点数量确定的基本原则
T型焊缝可定4个基准点,也可定两个基准点,因为 T型焊缝可按支管直径四等分,而Y(K)型焊缝不可等 分,因此,把基准点a和C两个点均定在主管的工艺线 上,操作性强且准确。用这种方法定基准点也为使用 微机辅助做焊逢缺陷定位分析打下了基础。只设两个 基准点测量X值时,由于其距离大可能遇到困难,但是 ,在两个基准点附近的缺陷,测量X值时只要按示意图 所示方向用“+”“-”X值就很方便。
①取样操作:
海洋石油工程股份有限公司
地址:天津市塘沽区河口街 2-37 邮编:300452
OFFSHORE OIL ENGINEERING CO., LTD.
8
在Y型焊缝上缺陷波反射最高处用万能取形规取样 见图-2
1
2
3
1、Y形管焊缝 2、3用万能取形规在Y形管焊缝上缺陷最高 波 处量取管焊缝外形 4、万能取形规量取管焊缝外形之情形效果
T K Y 型管接点焊缝
超声波检验 工 艺
(适用API RP-2X-[A\C 级]、AWS D1.1标准)
邢树宏
二 ○ ○ 六 、七
海洋石油工程股份有限公司检验公司
地址:天津市塘沽区河口街 2-37 邮编:
OFFSHORE OIL ENGINEERING CO., LTD
.2
自我介绍
邢树宏 服务单位 海洋石油工程股份有限公司检验公司 检验资格ABS UT二级/NDT检验技师
取样;
(四) 补图操作时一定按原取样位置重新量取主、支管曲率; (五)摸拟定位操作时所采用相关尺寸数据应是实际测量数据 。
海洋石油工程股份有限公司
地址:天津市塘沽区河口街 2-37 邮编:300452
大口径海底管道工程焊接工艺

文章编号:1002—025X(2013)08—0025—04大口径海底管道工程焊接工艺李国兴1,牛益民1,王营2(1.中国石油管道学院,河北廊坊065000;2.石油天然气工程质量监督总站,河北廊坊065000)摘要:海底管道作为最重要的海洋石油天然气的运输方式,发展速度逐年加快,本文着重介绍了我国海底管道焊接技术的发展现状和大口径海底管道焊接工艺,并以一条大口径海底管道为例,重点介绍在海底管道工程中采用的先进焊接技术、焊接工艺以及海底管道焊后强制冷却工艺。
关键词:海底管道;焊接工艺;喷淋;力学性能中图分类号:TG457.6文献标志码:B0海底管道施工状况世界海底油气管道的总量已超过10万km,最大作业水深已达3000i n。
我国已建成海底管道近数百万米,最大作业水深300m,中海油在渤海海域的海底管线累计超过了200km。
在南海海域约2000 km,其作业水深也可达300m。
其中,有一条海底输气管线长达800km左右,是我国目前最长的一条海底管道。
中石化海洋管道建设的步伐也在不断加快。
围绕位于渤海之滨的胜利油田,中石化就先后建成了170条总计超过360km的海底油气管线和注水管线。
目前,我国建成的海底管道一般直径在711m m 以下。
作为我国最大的油气生产企业,中石油公司近年来加大了海上石油工程研究和开发,海洋管道建设发展很快.目前已研究开发建成了直径为914 m m的大口径海底输气管道。
已正式投运送气。
这条输气管线是我国目前直径最大的一条海底管线,为我国海底管道建设技术发展作出了贡献。
中石油和中石化均有可铺设3001T I以下水深的海底管道铺设工程船。
中海油公司近年来已经建造了可铺设3000 m水深的海洋管道铺设工程船.大大提高了我国海洋管道施工的水平和能力。
收稿日期:2013-04—091海洋管道焊接技术海洋工程是施工风险很大、技术要求很高的施工,特别在海上采用工程船进行海底管道铺设要求更高.海底管道铺设采用工程船施工的工序框图如图1昕示.图l海辰管逼铺设施工工序【皇l焊接施工是海底管道施工过程中的重要环节,制约着后续的检测、防腐、下管等工序。
国内海底管道后挖沟施工技术

机选型提出建议。
关键词:海管;后挖沟;犁式挖沟;喷射式后挖沟
中图分类号:TE 54
文献标志码:粤
文章编号:员园园圆原圆猿猿猿(圆园21)07原园071原园3
Pipeline Post Trenching Technology in China
LIU Yu, HUANG Haibin, QU Youjie, CHEN Junyou, LI Jing
法多用于较浅水域,例如过河管线、海管登陆段部分等, 1.2 国外挖沟机现状
对于特殊海床,例如地貌凹凸不平、岩石质海底等部位也
国外在海管挖沟技术和设备方面均比较成熟,制造
常采用预挖沟法。预挖沟挖沟土方量大、开沟宽度大,对 了多种形式的水下挖沟机,包括喷射式、机械切割式、犁
管线不存在损伤风险。2)边铺管边挖沟。在管道铺设过程 式、ROV式等多种形式,基本覆盖了所有的土壤情况,表1
60 80 kPa
式挖沟机工作流程[4-5]。
5.0(25 kPa),
非接触式挖沟机 上海打捞局 — 3.0(40 kPa), 300 0~55 kPa土壤,适合砂质
碧海骄子铁军锻造——UT788CD-1建造管理经验

企业巡礼UT788CD-1 (海洋石油681船)是名副其实的“碧海骄子”。
它是由国际知名的ROLLS-ROYCE Marin设计公司按照英劳LRs规范设计,满足CCS规范,由CCS 审图、检验并入CCS船级,同时满足DNV规范的有关COFM-C(3)V(3)、NAUT-OSV(A)入级符号的要求。
作为国家和中国海油石油总公司深水发展战略中的重要一环,UT788CD-1 (海洋石油681船)是为3000米深水钻井平台“海洋石油981”建造的主要配套船舶,能提供海上平台拖带、深海起抛锚、供应淡水、燃油、散料和平台守护等服务,具有对外消防、浮油回收功能及ROV水下机器人功能。
它是我国新一代集深海抛锚、拖拽、定位及平台供应功能于一体的最高端船舶,是世界顶级深水三用工作船。
请看UT788CD-1(海洋石油681船)的主要技术参数:总 长: 93.40 m垂线间长: 81.80 m型 宽: 22.00 m型深(至1st甲板): 9.50 m设计吃水(3.0米干舷): 6.50 m最大吃水(1.8米干舷): 7.72 mUT788CD-1“海洋石油681”船主要性能如下:航 速: 18.28 Kn系柱拉力: 342 T航 区: 无限航区续 航 力: 10000 n mile自 持 力: 60 天总 吨 位: 6300 TUT788CD-1 (海洋石油681船)的技术实力和作业能力在国际同类船舶中处于领先地位,代表了国际海洋工程装备制造的最高水平。
它以矫健有力的身姿,正在为中国海洋石油深水发展战略贡献着自己坚实的力量。
UT788CD项目部的全体员工们是一支铁军。
这支来自于不同车间的优秀员工队伍团结一心,体现出高昂的工作激情,钢铁般的斗志和凝聚一心的团队精神。
UT788CD-1 (海洋石油681船)从设计伊始就受到集团公司和武船集团领导的高度重视,建造期间每周召开协■ 徐俊碧海骄子铁军锻造——UT788CD—1建造管理经验Copyright©博看网 . All Rights Reserved.中国军转民 37企业巡礼调会,针对该船生产资源配置、进度、技术等重难点逐条落实责任人和完成时间,各方面都给予了最大程度的优待和配合。
07.3UT法规标准工艺
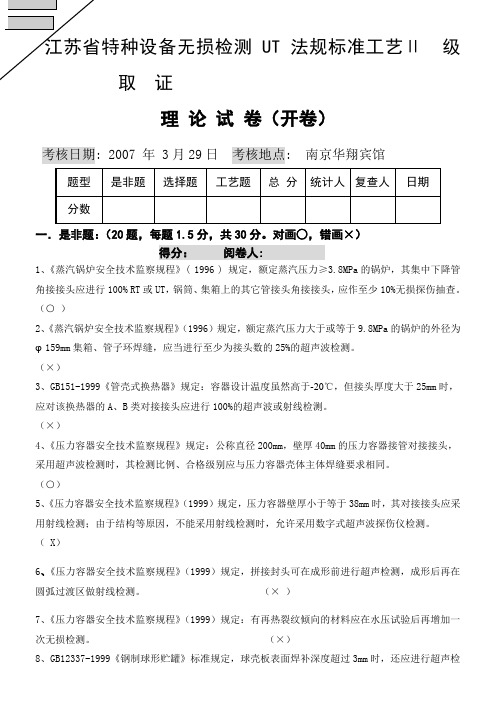
UT 法规标准工艺Ⅱ 级证理 论 试 卷(开卷)考核日期: 2007 年 3月29日 考核地点: 南京华翔宾馆一.是非题:(20题,每题1.5分,共30分。
对画○,错画×)得分: 阅卷人: 1、《蒸汽锅炉安全技术监察规程》( 1996 ) 规定,额定蒸汽压力≥3.8MPa 的锅炉,其集中下降管角接接头应进行100% RT 或UT ,锅筒、集箱上的其它管接头角接接头,应作至少10%无损探伤抽查。
(○ )2、《蒸汽锅炉安全技术监察规程》(1996)规定,额定蒸汽压力大于或等于9.8MPa 的锅炉的外径为φ159mm 集箱、管子环焊缝,应当进行至少为接头数的25%的超声波检测。
(×)3、GB151-1999《管壳式换热器》规定:容器设计温度虽然高于-20℃,但接头厚度大于25mm 时,应对该换热器的A 、B 类对接接头应进行100%的超声波或射线检测。
(×)4、《压力容器安全技术监察规程》规定:公称直径200mm ,壁厚40mm 的压力容器接管对接接头,采用超声波检测时,其检测比例、合格级别应与压力容器壳体主体焊缝要求相同。
(○)5、《压力容器安全技术监察规程》(1999)规定,压力容器壁厚小于等于38mm 时,其对接接头应采用射线检测;由于结构等原因,不能采用射线检测时,允许采用数字式超声波探伤仪检测。
( X )6、《压力容器安全技术监察规程》(1999)规定,拼接封头可在成形前进行超声检测,成形后再在圆弧过渡区做射线检测。
(× )7、《压力容器安全技术监察规程》(1999)规定:有再热裂纹倾向的材料应在水压试验后再增加一次无损检测。
(×)8、GB12337-1999《钢制球形贮罐》标准规定,球壳板表面焊补深度超过3mm 时,还应进行超声检测。
(○)9、根据GB150-1998《钢制压力容器》规定,壳体壁厚为36mm的16MnR钢板,应逐张进行超声检测。
- 1、下载文档前请自行甄别文档内容的完整性,平台不提供额外的编辑、内容补充、找答案等附加服务。
- 2、"仅部分预览"的文档,不可在线预览部分如存在完整性等问题,可反馈申请退款(可完整预览的文档不适用该条件!)。
- 3、如文档侵犯您的权益,请联系客服反馈,我们会尽快为您处理(人工客服工作时间:9:00-18:30)。
ULTRASONIC TESTING PROCEDURE (PIPELINE)ULTRASONIC EQUIPMENTUltrasonic Test Instrumenta) The ultrasonic test instrument shall be the pulse-echo type suitable for use withtransducers oscillating at frequencies between 2 and 6 MHz.b) The instrument’s display shall be an “A” scan rectified video trace. The dynamic range ofthe display shall be such that a difference of 1dB of amplitude can be easily detected on the display.c) The horizontal linearity of the test instrument shall be qualified within 1% over the fullsound path distance to be used in testing.d) The instrument shall also provide a amplifier linearity within 5% of full screen height.e) The instrument shall have a calibrated gain (Attenuation) electrically accurate to withinplus or minus 2dB over a range of not less than 60 dB.f) Each instrument-transducer combination shall be capable of producing a minimum 3/4CRT vertical scale deflection from an echo received from the 4 in. radius curved surface of the IIW calibration block with a minimum of 40 dB amplification in reserve .ProbeProbes as a straight beam probes 0 degree and angle beam probes of 45, 60 and70 degree. The selection of probe shall be in accordance with client specificationand actual WPS ( thickness, welding bevel, etc.)straight beam probea) Straight beam probes shall be round in shape and shall have an active area of not lessthan 12.5 mm in diameter nor more than 25 mm in diameter maximum.b) The frequency shall be between 2 to 5 MHz.c) Probes of other sizes and frequencies may be used provided they are qualified asdescribed in API RP 2X code and approved by client.Angle beam probea) The oscillating element shall be approximately square / or round in shape withdimensions which result in an included beam angle of approximately 15 degrees at 6 dB less than the centerline maximum.b) A probe with a transducer element in size from 8 to 13 mm in width and 9 to 13 mm inheight operating at 2 to 5 MHz shall be mostly used in accordance with the code’s recommendations.c) The probe shall produce a sound beam in the material being tested within 2 degrees ofone of the following proper angles: 45, 60 and 70 degrees.The actual angle shall be checked or verified during calibration for testing and reported on the applicable test report.d) Each probe shall be clearly marked to indicate the frequency of the transducer, nominalangle of reflection and index point. Probes of other sizes and frequencies may be used provided they are qualified as described in API RP 2X and approved by client.e) The resolution of the angle probe shall be evaluated with the instrument controls set atnormal test settings and with indications from the holes brought to midscreen height.Resolution shall be sufficient to distinguish at least the peaks of indications from the three holes.Periodic CalibrationThe instrument shall be periodically checked in accordance with the “Calibration Procedure of Ultrasonic Flaw Detector”.All ultrasonic flaw detectors shall be calibrated by a recognized test authority. CALIBRATION AND REFERENCE BLOCKSIIW and IOW standard blocks shall be used for the calibration of UT instrument.The reference blocks according to XXXXXXCALIBRATION FOR TESTINGa) Manual ultrasonic weld testing shall be performed at a scanning sensitivity of DACreference sensitivity plus 6 dB minimum. All indications that exceed 50% of DAC screen height shall be evaluated.Figure 1. Reference Block for Manual UTb) With the transducer in Position A, maximize ( peak up ) the echo from theinside notch and adjust amplitude to at least 80% of full screen height. Measure the surface distance from the inside notch to the transducer exit point. Surface distance divided by measured wall thickness equals refracted angle tangent.Position the transducer in line with the outside notch at double the distance used to peak upthe inside notch (Position B). Verify that the outside notch echo peak is at or near zero depth reading. This will establish that refracted angle and velocity settings are sufficiently accurate.Figure 2. Establishing Distance, Refracted Angle, and Velocityc) Using two transducers of equal angle and frequency, one transmitting and the otherreceiving, maximize (peak up) the echo received. Measure the surface distance between the transducer exit points. Half the surface distance divided by measured wall thickness equals the refracted angle tangent. Without changing instrument settings, repeat this process on pipe with unknown velocity, refracted angle, and attenuation to determine any differences.Figure 3 Transfer Procedured) The reference level shall be adjusted to compensate for the differences in surfacecharacter and attenuation between the reference block and the material being tested, by means of the double probe technique.A transfer correction shall be performed and recorded once for each welded joint to betested using part of the test surface exhibiting the roughest condition, except for repetitive testing of the same materials, size and configuration, in which case a transfer correction shall be performed at the beginning of every shift by the ultrasonic operator. Calibration surfaces shall closely match that of the test surface to minimize corrections required. PRODUCTION TESTING PROCEDURESurface PreparationThe surfaces of welds and base metal shall be prepared as follows:a) Contact surfaces shall be free of weld spatter and any condition that might interfere withfree movement of the search unit or impair coupling of ultrasonic vibrations to and from the material examined. When the correction factor has been determined and used see par. 6.3.b) Finished weld surfaces shall be adequate to prevent interference with interpretation ofthe examination.c) Surfaces of the calibration reference blocks shall be of a similar finish to the part underexamination.Couplanta) A couplant material shall be used between the search unit and the test material. Thecouplant shall be either glycerin on cellulose gum and water mixture of a suitable consistently. A wetting agent may be added if needed. Light machine oil may be used for couplant on calibration blocks.b) Components may be tested using the same or different couplant as that used forsensitivity calibration.Scanning ProcedureStraight Beam Technique and Scanninga) At the time of test and prior to angle beam scanning of the weld, the entire base metalthrough which sound will pass during angle beam testing (determined by maximum surface distance required from the weld for the required skip distance) shall be scanned for laminar reflectors or inclusions which might interfere with the examination. If any area of base metal exhibits total loss of back reflection, or if an indication equal to or greater than the original back reflection height is located in a position that will interfere with the normal weld scanning procedure, its size, location, and depth from the face shall be determined and reported separately to Company.b) Where conditions are found to interfere with angle beam testing, other NDT methodsshall be employed.Angle Beam Technique and ScanningA) Generala) The technician shall be given the following information before weld testing iscommenced, and choice of angle(s) of refraction for scanning weld body sidewalk and reinforcement shall depend on the following factors:∙Type of ferritic steel.∙Groove type used.∙Characteristics and orientation of defects likely to occur i.e., the welding process (WPS) ∙Type of weld joint configuration to be tested i.e., the applicable range of diameter, thickness and local dihedral angle.b) A ccurate profiles shall be taken with wire type profile gauges or, if joint angle is acute, asuitably pliable material able to maintain its shape under normal conditions.B) Scanning Techniquea) Scanning may be in any pattern which results in full coverage of the root of the weld, thebody of the weld, and both side fusion lines and base metal heat affected zones.b) Scanning shall generally be performed at a gain setting 6dB above the ReferenceSensitivity Level for the maximum sound path. Evaluation of indications shall be done with the gain control at the Reference Level.C) Selection of Probesa) The nominal frequency shall be 2 to 5 MHz, unless variables, such as fabrication materialgrain structure require the use of other frequencies to assure adequate penetration or better resolution.b) Indications found in the root areas of groove welds in butt joints and along the fusion faceof all welds shall be further evaluated with either 70, 60, or 45 deg. angles, whichever is nearest to being perpendicular to the expected fusion face.D) Scanning PatternsFor girth welds, scanning for volumetric examination shall be carried out from both sides of the weld on the same surface.Indication InvestigationThe indications shall be investigated by maximising the echoes by rotating the probes and by using different angle probes with DAC curves. All indications exceeding 20% of the reference curve shall be investigated with and all indications exceeding 50% shall be reported. Investigation shall be performed to the extent that the operator can determine the shape and location o f the indication. For dimensional evaluation, either the “6 dB-drop”method or time of flight or maximum amplitude method shall be used.DISCONTINUITY EVALUATIONGenerala) Once a reflector has been found by scanning, it shall be carefully evaluated to determinethe following characteristics, as required for application of the Acceptance Criteria and for Reporting:∙Location from an established reference point.∙Location within the weld cross section.∙Sizes - i.e., length along the weld axis and width (height dimension) as seen in the weld cross section, or amplitude relative to reference level.∙Type and Orientation - i.e., classify as linear, planar or spherical reflectors. If planar, the orientation of the plane relative to the brace or chord side fusion boundaries.b) Discontinuities shall be evaluated by use of a combination of Beam Boundary andAmplitude Techniques.Defect Size DeterminationThe following technique shall apply to determine the defect size.a) The length of the discontinuity shall be obtained by recording the location along thelength of weld as determined by 50% of Reference Level (6dB drop) for each end of the reflector.b) The width (height) of the discontinuity shall be determined by 20dB drop (10%intentensity of the maximum echo) technique.Acceptance StandardAcceptance criteria are as Client’s Specification and xx code (根据实际要求)。