GPET Pump Set up Procedures - from Rexroth
钢瓶抽真空数值操作流程

钢瓶抽真空数值操作流程英文回答:Vacuuming a gas cylinder involves a specific procedure to ensure that all air and gases are removed from the cylinder, creating a vacuum inside. This process is commonly used in various industries, including the manufacturing of electronic components, medical devices, and scientific research.Here is a step-by-step guide on how to vacuum a gas cylinder:1. Prepare the equipment: Gather all the necessary equipment, including a vacuum pump, pressure gauge, vacuum chamber, and vacuum hose. Ensure that all equipment is clean and in good working condition.2. Inspect the gas cylinder: Before starting the vacuuming process, inspect the gas cylinder for any damagesor leaks. If any issues are found, repair or replace the cylinder before proceeding.3. Connect the equipment: Connect the vacuum pump to the gas cylinder using a vacuum hose. Make sure the connection is secure and airtight.4. Start the vacuum pump: Turn on the vacuum pump and allow it to run for a few minutes to remove any remaining gases or air from the system.5. Monitor the pressure: Use a pressure gauge to monitor the pressure inside the gas cylinder. As the vacuum pump operates, the pressure should gradually decrease. Aim to achieve the desired level of vacuum based on thespecific requirements of your application.6. Maintain the vacuum: Once the desired vacuum level is reached, continue running the vacuum pump to maintain the vacuum inside the gas cylinder. Monitor the pressure gauge regularly to ensure the vacuum is sustained.7. Seal the cylinder: Once the vacuuming process is complete, close any valves or openings on the gas cylinderto maintain the vacuum inside. This will prevent any air or gases from entering the cylinder.8. Test the vacuum: After sealing the cylinder, performa vacuum test to ensure the integrity of the vacuum. Youcan use a vacuum gauge or other appropriate testing equipment to verify the vacuum level.9. Document the process: Keep a record of the vacuuming process, including the vacuum level achieved, duration ofthe process, and any other relevant information. This documentation is important for quality control and future reference.中文回答:真空化气瓶需要按照特定的程序进行操作,以确保气瓶内所有的空气和气体被排除,从而在气瓶内形成真空。
Zoll AutoPulse心肺复苏机用户手册
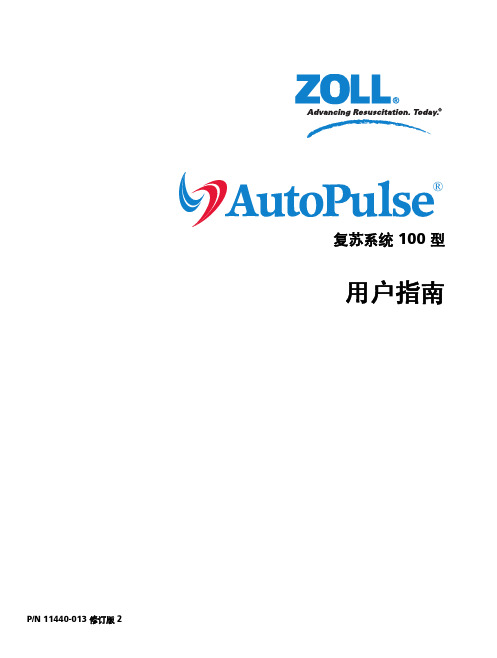
0344
USA ZOLL Circulation 650 Almanor Avenue Sunnyvale, CA 94085 USA 电话:+1.978.421.9655
第2页
P/N 11440-013 修订版 2
用户指南
目录
图 ...............................................................................................................................v
1 AutoPulse® 简介 ................................................................................................1-1 1.1 使用说明 ........................................................................................................................1-1 1.2 系统说明 ........................................................................................................................1-1 1.3 系统组件 ........................................................................................................................1-2
灌装机的现场操作流程

灌装机的现场操作流程英文回答:The on-site operation process of a filling machine typically involves several steps. Here is a general overview of the process:1. Preparation: Before starting the operation, it is important to ensure that the filling machine is clean and in proper working condition. This includes checking the machine for any damages or malfunctions and cleaning it thoroughly.2. Set up: Once the machine is ready, the next step is to set it up according to the specific requirements of the product being filled. This includes adjusting the filling volume, speed, and other parameters as needed.3. Product loading: The next step is to load the product into the machine's hopper or reservoir. This can bedone manually or through an automated system, depending on the capabilities of the machine.4. Machine start-up: After the product is loaded, the operator can start the machine. This may involve pressing a start button or activating a control panel. The machinewill then initiate the filling process.5. Filling process: The filling machine will begin dispensing the product into the containers. This can be done using various mechanisms, such as piston fillers, gravity fillers, or vacuum fillers, depending on the nature of the product and the desired filling method.6. Monitoring: During the filling process, the operator needs to closely monitor the machine's performance to ensure that it is working properly. This includes checking for any leaks, jams, or other issues that may affect the quality of the filled containers.7. Quality control: As the containers are being filled, it is important to periodically check the filled containersfor quality control purposes. This may involve inspecting the fill level, checking for any defects or contaminants, and ensuring that the containers are properly sealed.8. Packaging and labeling: Once the containers are filled and checked for quality, they can be prepared for packaging and labeling. This may involve placing them in boxes, applying labels, and preparing them for shipment or storage.9. Clean-up: After the filling operation is complete, it is essential to properly clean and sanitize the filling machine to prevent any cross-contamination or product residue. This includes disassembling and cleaning the machine components, as well as following any specific cleaning procedures recommended by the manufacturer.中文回答:灌装机的现场操作流程通常包括以下几个步骤:1. 准备工作,在开始操作之前,必须确保灌装机清洁并处于正常工作状态。
ITT Goulds Pumps 泵操作指南说明书
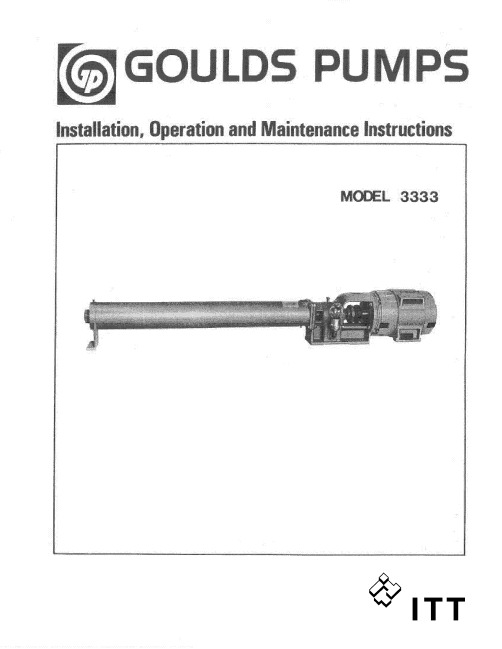
If using a cartridge mechanical seal, the centering clips must be installed and set screws loosened prior to setting impeller clearance. Failure to do so could result in sparks, heat generation, and mechanical seal damage.
General precautions
General precautions
WARNING:
A pump is a pressure vessel with rotating parts that can be hazardous. Hazardous fluids may be contained by the pump including high temperature, flammable, acidic, caustic, explosive, and other risks. Operators and maintenance personnel must realize this and follow safety measures. Personal injuries will result if procedures outlined in this manual are not followed. ITT Goulds Pumps will not accept responsibility for physical injury, damage or delays caused by a failure to observe the instructions in this manual and the IOM provided with your equipment.
T-REX 601A W 43CC 汽油动力滑板车 用户手册说明书

T-REX 601A/W43CC GAS POWERED SCOOTER USER MANUAL BOOKTable of content Important Safety PrecautionsQuick Start GuideBrake Adjustment GuideChain Adjustment Guide Carburetor Adjustment Guide Steering Column Adjustment Trouble ShootingEasy Step InstallationImportant Safety PrecautionsPlease operate your scooter with the following safety instructions. This scooter should only be ridden by persons with excellent vision, balance, coordination, reflex muscle tone, strength, and the good reaction to sudden incident.1. Please read the manual and all safety notice carefully, understand its functions,maintenance and operating procedures completely before using the scooter.2. Minor shall never operate this scooter without adult supervision.3. Never operate your scooter on slick or unstable surfaces such as dampness or lossgravel, etc.4. Never operate your scooter on public road, street, or highway.5. Never operate your scooter without wearing proper safety equipments.6. Never operate your scooter under influence of alcohol, drug or magnet.7. Never attempt wheelies, jumps, or other stunts.8. Never operate your scooter on steep hill or inclines.9. Do not turn at excessive speeds.10. Always inspect your scooter prior to each use to make sure it is in safe condition. Followinspection and maintenance procedures in this manual.11. Fuel is highly flammable. Keep it safe away from any source of fire.12. Engine and muffler will get hot while using, don’t touch with hand.Quick Start Guide:Make sure that all cables are not binding and have good action. Check gas lines so they are not too close to any moving parts. Make sure handlebar hinge is secure.1. Fill fuel tank with premixed two-stroke (cycle) oil in it. We recommend a ratio of 32 to 1.DO NOT use straight gas; engine will seize and can cause injury.2. Prime the carburetor by pressing the bulb located on the bottom of the carburetor untilall air bubbles and fuel flow back to the tank through the clear line.3. Place the choke (the lever located on the side of the air filter) in the "OFF" (up )position (this does not mean the choke is off, it means the engine is off - the choke is on in this position)4. Pull the pull start to get the engine going. If this is your first or second time starting thescooter, it may take 10-20 pulls to start it. This will get much easier after the scooter is broken in. Do not yank on pull starter too hard. Short quick pulls will work fine; yanking too hard will break pull starter.5. Once the scooter is started, let the engine idle for a minute, and then Flip the choke tothe "ON" (lever down)position before the engine dies.6. Give the engine a little throttle right after it starts to get it going. You may also have togive it a little bit of throttle while pulling the pull start, although this often not necessary.Press the kill button to stop the engineAnd now you're good to go! Once your scooter gets broken in, it won't be necessary to turn the choke on to start the scooter, and it won't take so many pulls to get it started. It does help to pump the bulb under the carburetor every time just to get the fuel flowing through it, since it dries up when it sits.BRAKE ADJUSTMENT GUIDEOften the disc brakes on our gas scooters will require adjusting. Do each step below and check and see if the brakes are adjusted correctly after each step. There is no need to complete all the steps if only one or two adjustments fix them. Usually the firstStep One:This usually fixes any problems. First turn the smaller hex bolt circled above using a 2.5mm hex wrench. There are two hex heads on this same screw circled above. The smaller 2.5mm one is hidden deep beneath the larger 5mm one.Step Two:Usually Step One fixes most problems, the next three steps help fine tune the brakes. Loosen the cable holder using a 5mm hex wrench. Then use some pliers to hold the cable, then move the arm towards the engine, and retighten the 5mm hex screw.Step Three:Turn the knob circled by hand as shown in the picture.Step Four:Turn the silver piece circled above by hand, then lock it in place by turning the black piece until it is closest to the hand lever just like in the picture above.Chain Adjustment GuideProper chain adjustment is important for performance and safety. If the chain is adjusted too tightly it will bind and prematurely wear the chain and cause reduced performance. Ifthe chain is too loose it may jump teeth or fall off the sprocket.STEP ONE:Check the chain. See if there is some play in the chain or if it feels too tight. Check the top and bottom lengths and see if either one deflects 1/4 to 1/2 inch with light pressure. When you press on the chain it should deflect about 1/4 to 1/2 of an inch. Check both lengths of the chain. We have found that most of the scooters arrive with the chain too tight.STEP TWO:If adjustment is needed, loosen the bolt and nut securing the band brake to the frame. Just back it off a bit so it isn't too tight.STEP THREE:Loosen the large nuts securing the rear axle. Loosen both sides just a little--maybe one or two turns.STEP FOUR:Use the chain adjusters to move the wheel back to tighten or forward to loosen the chain. To use the adjusters, loosen the outer nut and then turn the inner nut to the desire position then tighten the outer nut back up against the inner nut to lock it in place. STEP FIVE:Tighten everything back up and check the chain again. Don't forget to tighten the axle and band brake connection to the frame.CARBURETORS ADJUSTMENT GUIDESometimes the carburetors aren't quite adjusted correctly from the factory. If your scooter isn't quite going as fast as it should, or it won't idle, then you probably need to adjust your carburetor. It's easy to adjust one. Just follow these steps:The small gold screw on the side of the carburetor is the idle speed screw. This screw controls the idle speed; the tip should extend about a 1/8 of an inch (4 mm). Adjust it so the engine will idle at just fast enough speed to stay running. The black screw located lower on the side of the carburetor next to the choke lever is for the high speed mixture. Step One:Remove the air filter cover. This is the black box located on the left side of the scooter, towards the front of the engine. There is a screw right in the middle to unscrew.Step Two:You should now be able to see the air filter and behind it the carburetor. There are two screws on the carburetor which you can adjust, the air screw and the idle screw (see picture to right for guide).Step Three:Usually the idle screw doesn't need any adjustment. What usually needs adjustment is the air screw. We've found screwing it all the way in, and then out 3 1/2 turns is usually the right setting. Start by turning this screw in (clockwise) until it stops. Don't turn it in tight, just until it stops. Next, turn the screw out two full turns (counter-clockwise). This is the factory setting. You should be able to start and operate the scooter with this setting. Once you have it running, you can fine tune. You should try putting the scooter up on a brick or chair, and then giving it throttle after you adjust it.It's adjusted optimally when the engine is making the highest pitched noise.Step Four:There is also a main jet adjustment screw dead center on the top of the carburetor. This is most always set at 1 full turn out. If this is not adjusted correctly, your scooter may not run, or run very poorly. Once again, turn screw all the way in (clockwise) and then out (counter-clockwise) 360 degrees (1 full turn).Steering Column Adjustment:To tighten:Loosen small set screw on top nut, take big crescent wrench and turn nut clockwise. Be careful not to over tighten. Lift the front of the scooter off the ground. Push the handle bar in one direction or the other. It should swing freely. If it just stops and doesn't swing in one direction then back again it is too tight.To see if it is to lose:Kneel in front of scooter, pick up front end of scooter by the fork with one hand, grab the steering column below the release post with the other hand and rock back and forth. You should not feel any play, if you do tighten as instructed above.Gasoline / Oil Mixture Synthetic oils are the best to use in your scooter, alongwith a standard grade octane pump gas.A word on engine oil: 32: 1 is the recommendedmixture ratio. This ratio is dependant on the quality of2-cycle premix oil used.TIP: If using a high-quality synthetic oil such asMaxima Castor 927 mix at 32:1 ratio for bestperformance.Tire pressure 30 to 35 PSIThe rear tire tube valve is a little tricky to get to. Theeasiest method is to pull the valve over with ascrewdriver and then thread on a valve extension(available at any auto parts store). Adjust air pressureas necessary and then remove valve extension. Spark Plug Gap 024-.028 inches (.60-.70 mm)I'm having trouble starting my gas powered scooter.What is the best way to start it?Please read our starting guide first. If it still won't start, you may need to adjust your carburetor. Please read the section ‘adjust you carburetor” for details.On my scooter when I'm riding it a lot of the time the chain just falls off. How do I fix it?It's usually very easy to fix. There are two reasons it can happen:1.If it happened when you were acceleratingit usually happens because the front andrear sprocket are misaligned. To fix it youneed to remove the engine from the enginemount, then adjust the engine mount (it canslide once you loosen the bolts) to get thesprockets in better alignment. This can bedone by loosening the three bolts on thebottom of the engine. The idea is to get thefront and rear sprockets aligned in astraight line.2.Otherwise you might need to tighten thechain, but usually the problem is #1. See“Chain Adjustment Guide”.What's the purpose of the small plastic tube that says 40ml on it that comes with the gas powered scooter?40ml is how much two-stroke oil you need to mix with 1 liter of gas. Please check your scooter's fuel tank size. This might be how much oil you need for a full tank. It is usually easier to get a gas tank that holds a gallon or two and dedicate that to your two-stroke engine. Then you'll always have gas/oil mixed and ready.How do I mix the gas and oil? How much oil do I put in?Most of our scooters come with a 1 liter tank, which means it's just 40ml (one canister) of 2-stroke oil per tank of gas. Regardless of your tank size, these instructions will work:You fill a gas tank with one or two gallons and leave a little room for oil, then dump in the right amount of oil and slosh it around to mix it. Some oils don't require as much as others for proper lubrication. Follow what the oil bottle directions instruct for mixing. Here is the basic mixing formula for a gallon.Here's how you do the math:There are 128 oz of gas in a gallon. 1/25th of that would be: 1/25*128 = 5.12 oz of oil needed.The disc is straight but the brake assembly is not. The front brake is straight and works. Also the cable pulls the lever and it hits the engine. We tried adjusting the cable with no results. Try using the large adjustment cylinder... it is silver... should fix the problem.I filled gas, pressed the bulb. Then I keep the thing off and pull start and it does not start. What is wrong? Please be sure that the two tubes from gas tank installed to the right nipples under the engine. The right order is that the black one goes on the curved nipple and the clear goes on the straight.If it still does not start, pump the primer bulb 10 times and put the choke in the up position and give it 5-7 quick short pulls. It should start, if not, give little throttle while pulling rope.When pull to start engine, it pulls out but engine does not turn over. Two or three tries and it engage and engine turns over or starts. There is a problem with starter pawl. If your scooter is still under the warranty, contact the distributor for the replacement parts.What kind of maintenances should I perform on my scooter?There is one maintenance check which is very important. Make sure all of the bolts are tightened before you go out riding. These scooters vibrate quite a bit, which causes the bolts to come loose. Specifically, check the front axel bots, the engine mounts (located right beneath the engine), the gas tank screws, the front fender screw (if your scooter has a front fender), and the deck screws. Also make sure the handlebar folding mechanism is good and tight. You should also oil the chain once in a while (not very often). 3-in-1 oil works great for that.What are the two tubes coming from the gas tank to the carburetor?There are two tubes: one from the tank to the carburetor and one going the other way.The clear tube is the fuel return; The black tube is the fuel supply. The black one goes on the curved nipple and the clear goes on the straight one.What kind of gas do I need to put in a gas powered scooter?32 to 1 is the ratio recommended.Doesn't matter what kinds of unleaded gas but make sure you use two-stroke oil?Does the gas powered scooter require any lubrication of the transmission?The 90 weight gear oil in the transmission should not need changing for the life of the gas powered scooter.Thanks for buying one of these great T-REX scooters! There are 10 easy steps to putting your scooter together. Please read the instruction carefully before you start riding scooter.Easy Step Installation1. Unpack the scooter by opening the top ofthe box and remove the loose parts at thetop. Remove the Styrofoam holding thefront wheel by tipping it back toward therear of the scooter while you hold thehandle-bar post. Then remove the rearStyrofoam.2. Find your tools and attach the steeringcolumn to its hinge. Don't make it too tightfor now but later you might want to tightenthis if the column is too loose. 13mm and14mm wrenches required.See “Steering Adjustment Guide”.3.Lock the steering column in placeby rotating the locking bolt up andthen turning the nut clockwise. Itworks just like the one on a typicalbicycle seat post.4. Attach the handlebar ends with thethumb screws. See the photo so you put the right end on the right side. Note: The front axle is pointing backwards as packed.5. Attach seat post and seat. Insert the seat post fully into the sleeve until it hits the bottom, then tighten the strap. Remove the scooter from the box by lifting the seat post and handlebars. Turn handlebars forward and lay the scooter on its right side (side opposite the engine).5mm hex wrench needed .7. Put the kickstand down and bring the scooter upright. Attach the gas tank with the two hex bolts. Slide the hose springs closer to the gas tank and route the hoses so that they aren't in the way of any moving parts (chain, wheel, etc.). Also make sure they are not pinched. 8mm hex wrench needed.8. Adjust the brakes by tightening the adjustments at both ends of the brake cable until the wheel still rolls but the brake works well. See the “Brake Adjustment Guide”9. Adjust chain. See the “Chain Adjustment Guide”10. Adjust Carburetor if needed. See the “ Carburetor Adjustment Guide”SEA BEYOND INT’L INC LOS ANGELES, CALIFORNIA UNITED STATES OF AMERICA。
Christensen Turbine Pump产品简介说明书
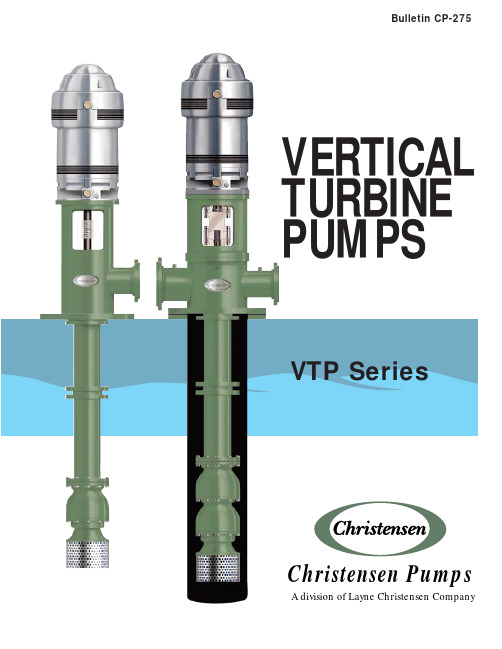
VERTICAL TURBINE PUMPSBulletin CP-275Christensen Pumps A division of Layne Christensen CompanyYou not only get the latest inpump design and technology from Christensen, you get more than 100 years of pump manufacturing know-how that includes most of the major innovations in pump engineering and materials. All ourproducts reflect theengineering design advances for top efficiencyand head generation.Our engineersare specialists using computer assisted design and extensive test research facilities.They develop the specifications thatguide our in-house pattern shop technicians in thedevelopment of precision turbine pattern equipment. The result is consistent casting accuracy, close tolerances, and the quality needed to maintain water passage shape and pump efficiencies.Christensen further controls the quality of its products in its foundries. Here the molding,core work and Vitra-Glass enamel-ing are closely supervised for tight quality standards.Our modern manufacturing facilities assure dimensionally consistent, high quality, fully machined parts, produced on a volume basis to bring down costs.Every impeller is precision balanced on a micro processor balance analyzer. Christensen is one of the largest manufacturers in the turbine industry.From design to pattern shop to foundry to manufacturing to warehousing–Christensen is acompletely integrated producer. Our network of turbine warehouses brings pumps and same days ser-vice to you. We offer full service on new units. Plus rebowling, rebuild-ing and repair on turbine pumps and submersible and centrifugal pumps.We are committed to service. We offer ready availability of complete pumps, repair parts and service.We are continually improving and expanding our turbine products warehouse network with locations in key areas.3123Packing Box Assembly45ColumnAssembly HeadshaftStainless Steel.Bronze Packing GlandCast Iron BoxThrottle BushingExtra length bronze for better shaft support, longer packing life.Water Lubrication1Adjusting NutPermits exact impeller adjustment formaximum performance.2Discharge HeadHeavy duty head provides maximumaccessibility to service packing boxassembly. Two piece head shaft is standard. 3Prelube Connection4Column AdapterAccepts threaded or flanged column.5Adjusting NippleThreads directly into column adapter.Headshaft stickup set exactly by threading head on column as required.6Discharge Bowl BearingBronze.7Discharge BowlClose grained cast iron.8Pump ShaftOversized high strength polished stainless steel.9Intermediate BowlsClose grained cast iron. Waterways glasslined for maximum efficiency.10ImpellersSilicon bronze, designed for maximumefficiency. Precision balanced for smoothoperation.11Intermediate Bowl BearingsBronze or rubber for long pump life under any well conditions.12Lock ColletsSteel construction secures impeller topump shaft.13Sand CollarAccurately located at suction bowl bearingto eliminate possible sand buildup.14Suction Bowl BearingBronze. Grease packed for long trouble-free life.15Tail Pipe or Strainer–OptionalOptional tail pipe cut to desired length forbest suction conditions. Strainer providesprotection from large solids.4Glass Lined BowlsHeavy duty Class 30 cast iron inter-mediate bowls with standard feature of vitra-glass lined waterways formaximum efficiency and wear protection.LINESHAFTSHORT SET TURBINE• Capacities to 9000 GPM (2043 m /h)• Heads to 1400 feet (427 m)Consult factory for higher capacities Design FlexibilityChristensen offers a wide variety of design options to suit most any short set turbine applications.VERTICAL HOLLOW SHAFT OR SOLIDSHAFT MOTORSCAST IRON ORFABRICATEDDISCHARGE HEADDesigned for mounting electric motor.PACKED STUFFING BOX OR MECHANICAL SEALTHREADED OR FLANGED COLUMN ASSEMBLIESWith bronze or cast iron bearing retainers.LINESHAFTPolished high strength stainless steel. Other alloys available.INTERMEDIATE BOWLSWaterways glass lined for maximum efficiency.IMPELLERSTaperlocked or keyed construction. Precision balanced for smooth operation.INTERMEDIATE BOWL BEARINGSBronze, rubber or carbon for long pump life under any conditions.SUCTION BELL BEARINGGrease-packed for longtrouble-free life.6791081314151211ImpellersSEMI -OPEN IMPELLERCLOSED IMPELLER5123Tube Tension Assembly Column Assembly45Headshaft Steel.Tube Tension Nut Heavy Duty Cast Iron.Tension Nut BushingBronze construction. Spiralgroove insures positive lubrication tolineshaft bearings.Heavy Duty Tension PlateFor positive alignment of lineshaftbearings.OIL LUBRICATION1Adjusting NutPermits exact impeller adjustment for maximum performance.2Large Capacity Manual or Solenoid Oiler Assures constant oil supply.3Discharge HeadHeavy duty head provides maximum accessibility to service tube tension assembly. Two piece head shaft is standard.4Lock RingPositively locks adjusting nipple to discharge head.5Adjusting NippleThreads directly into column adapter. Headshaft stickup set exactly by threading head on column as required.6Tube Adapter Bushing Bronze.7Double Bowl Seal–OptionalProvides positive sealing of developed head.8Pump ShaftOversized high strength polished stainless.9Discharge BowlClose grained cast iron. Relief ports insure posi tive bearing lubrication.10Discharge Bowl BearingBronze. Close tolerance fit for minimum leakage.11ImpellersSilicon bronze. Designed for maximum efficiency. Precision balanced for smooth operation.12Intermediate BowlsClose grained cast iron. Waterways glass lined for maximum efficiency.13Intermediate Bowl BearingsBronze or rubber for long pump life under any well conditions.14Lock ColletsSteel construction secures impeller to pump shaft.15Sand CollarAccurately located at suction bowl bearing to eliminate possible sand buildup.16Suction Bowl BearingBronze. Grease packed for long trouble-free life.17Tail Pipe or Strainer–OptionalTail pipe cut to desired length for best suction conditions. Strainer provides protection from large solids.6ImpellersSEMI -OPEN IMPELLERCLOSED IMPELLERGlass Lined BowlsHeavy duty Class 30 cast iron inter-mediate bowls with standard feature of lined waterways for maximum effi-ciency and wear protection.Column AssemblyLineshaftHigh strength steel. Ground and polished for exact bearing fit. Enclosing TubeExtra heavy steel tubing for positive bear-ing alignment.Enclosed Lineshaft Bearings Bronze Construction–High strength bearing bronze, spiral grooved for positive lubrication.Column Pipe and CouplingsParallel thread, accurately machined for easy installation, accurate alignment.Tube Centering SpiderStabilizes enclosing tube for smoother operation.BronzeConstruction6891271011151617141378HEADPERSTG(FT.)FLOW (100 U.S.GPM)2502001501009080706050403025201510987HEADPERSTG(FT.)FLOW (100 U.S. GPM)30025020015010090807060504030250.40.60.8 1.0 1.5 2.03456789101520Type “F”Head Type “U”DischargeLocatedUnderground9Type “T”Suction InletLocated in theHeadType “L”(Can)Suction InletLocated inthe Can101Discharge Head C.I. ASTM A48, CL 30B2HeadShaftWater Lube Stainless–ASTM A582, Type 416Oil LubeSteel–AISI C10453Adjusting Nut Ductile Iron–ASTM A536, Gr. 65-45-124Gib Key Mild Steel–ASTM A108, Gr. 10185Tension NutOil Lube Only Cast Iron–ASTM A48, CL 30B 6Tension Nut Bushing Oil Lube Only Bronze–ASTM B584 C9037Tension Plate Oil Lube Only Cast Iron–ASTM A48, CL 30B 8Oiler Body Oil Lube Only Aluminum SAE 329 or Steel 9Stuffing BoxWater Lube Cast Iron–ASTM A48, CL 30B 10Stuffing Box Bushing Water Lube Bronze–ASTM B584 C90311Stuffing Box Stud Water Lube Stainless–ASTM A276, Type 31612Stuffing Box Stud Nut Water Lube Stainless–ASTM A276, Type 31613Stuffing Box Washer Water Lube Stainless–ASTM A240, Type 30414Stuffing Box Gasket Water Lube Garlock Brand Blue Guard15Stuffing Box Split Gland Water Lube Aluminum Bronze–ASTM B148HT 16Stuffing Box Slinger Water LubeRubber17PackingGraphited Acrylic Yarn 18Column Nipple Pipe–ASTM A5319Lock RingDuctile Iron–ASTM A536, Gr. 65-45-1220Reducer – Bushing Cast Iron–ASTM A48, CL 30B 21Companion FlangeCast Iron–ASTM A48, CL 30B 22Companion Flange Gasket Garlock Brand Blue Guard23Nameplate Stainless–ASTM A240, Type 31624Sole Plate Steel Plate–ASTM A283, Gr. D 25Column Pipe Pipe–ASTM A5326Column Coupling Pipe–ASTM A5327Tube Nipple Pipe–ASTM A12028Enclosing Tube Bronze ConstructionSteel–SCH80, ASTM A120, Gr. B29Oil Tube Coupling 30Lineshaft Bearing Bronze Construction Bronze–ASTM B584 C90331LineshaftW/L–Chrome Spot Steel–AISI C1045W/L–Stainless Stainless–ASTM A582, Type 416Oil Lube Steel–AISI C104532Lineshaft Chrome Spot Water Lube Only Chrome Facing–Rockwell #7633Lineshaft Coupling Water Lube Mild Steel–ASTM A108, Gr. 1018Stainless Stainless–ASTM A582, Type 41634Water Lube Retainer Retainer Silicon Bronze–ASTM B584 C873InsertRubber 35Tube Centering Spider Rubber36Discharge Bowl Cast Iron–ASTM A48, CL 30B 37Discharge Bushing Water Lube Bronze–ASTM B584 C90338Throttle Bushing Oil LubeBronze–ASTM B584 C90339Intermediate Bowl Cast Iron–ASTM A48, CL 30B, Enameled 40Top Inter Bowl Cast Iron–ASTM A48, CL 30B, Enameled 41Inter Bowl Bushing Bronze Bronze–ASTM B584 C903Rubber Rubber42Wear Rings – Optional Inter Bowl Bronze–ASTM B584 C903ImpellerBronze–ASTM B584 C90343Impeller Silicon Bronze–ASTM B584 C87344Taper Lock Mild Steel–ASTM A108, Gr. 101845Suction Bowl Cast Iron–ASTM A48, CL 30B 46Suction Bushing Bronze–ASTM B584 C90347Sand Collar Bronze–ASTM B584 C90348Suction Strainer Hot Galvanized–ASTM A12349Plug Steel–ASTM A108, Gr. 121150Screw Bearing Bronze Construction Bronze–ASTM B584 C90351Bowl Shaft Stainless–ASTM A582, Type 41652Hex Bolt Steel–SAEJ 429, Gr. 853Lock Washer Steel–ASTM A108, Gr. 1018054Suction Adapter Submersible Only Ductile Iron–ASTM A536, Gr. 65-45-12Cast Iron–ASTM A48, CL 40B55Adapter Plate Submersible Only (Optional)Ductile Iron–ASTM A536, Gr. 65-45-1256Motor CouplingSubmersible Only Stainless Steel–ASTM A582, Type 41657Motor Mounting Bolts Submersible Only Stainless–ASTM A276, Type 31658Suction Screen Submersible Only AISI 304 Stainless 59Cable GuardSubmersible Only AISI 304 Stainless60Discharge BearingSubmersible Only Bronze–ASTM B584 C90361Discharge Bearing Plug Submersible Only Mild Steel–ASTM A108, Gr. 101862Upthrust WasherSubmersible OnlyStainless Steel–ASTM A582, Type 416Standard Materials of ConstructionNo.DescriptionMaterial11Products to ServeThe Municipal Industrial and Agricultural markets complete with repair components and parts.Christensen PumpsA division of Layne Christensen CompanyThe LAYNE CHRISTENSEN NetworkThe Layne Christensen CompanyCorporate Headquarters • 1900 Shawnee Mission Parkway • Mission Woods, KS 66205For more information, call or write your nearest Christensen Pumps sales office or representativeOFFICE LOCATIONSLayne Christensen Company Fairbanks, AK 907/455-0242 Beverly, NJ 609/877-2700 Barstow, CA 760/254-3351 Bridgewater, NJ 732/469-8720 Butler, PA 724/283-2262 Chandler, AZ 409/895-9404 Dracut, MA 978/937-2242 Fontana, CA 909/390-2833 Grayson, KY 606/474-6285 Holbrook, NY 631/218-0749 Irvine, CA 949/955-1122 La Habra, CA 562/691-0903 Las Vegas, NV 702/221-9717 Rayne, LA 337/334-3126 Salt Lake City, UT 801/972-3333 Schoharie, NY 518/295-8288 Tacoma, WA 253/536-1161 Woodland, CA 530/662-2825 Quakertown, PA 215/538-6177Christensen Pumps Memphis, TN 901/276-6605International Directional Services Chandler, AZ 480/824-7100 Salt Lake City, UT 801/974-1032 Layne GeoConstruction Boston, MA 508/588-8889 Butler, PA 724/283-2262 Grayson, KY 606/474-6285 Honolulu, HI 808/949-3070 Irvine, CA 949/955-1122 Ruther Glen, VA 804/448-8060Layne-Atlantic Albany, GA 229/438-8164 Bloomingdale, GA 912/748-9244 Lakeland, FL 863/666-2433Layne Arkansas Stuttgart, AR 870/673-1591Layne-Central Baton Rouge, LA 225/744-4899 Jackson, MS 601/922-4312 Memphis, TN 901/274-2324 Pensacola, FL 850/432-5101 West Monroe, LA 318/396-0678Layne GeoSciences, Inc. Bridgewater, NJ 732/469-8720 Dracut, MA 978/937-2242 Milwaukee, WI 262/246-4646 Mission Woods, KS 913/321-5000 Woodland, CA 530/662-2825Layne-Northern Lansing, MI 517/323-4931 Mishawaka, IN 574-259-5234Layne-Northwest Milwaukee, WI 262/246-4646 Wausau, WI 715/359-4211Layne Texas Houston, TX 713/466-5001 Tyler, TX 903/592-6176Layne Western Aurora IL 630/897-6941 Beecher, IL 708/946-2244 Cushing, OK 918/225-1119 Denver, CO 303/755-1281 Des Moines, IA 515/986-3462 Kansas City, KS 913/321-5000 Kearney, NE 308/234-1914 Omaha, NE 402/359-2042 St. Louis, MO 636/343-3700 Wichita, KS 316/264-5365Reynolds, Inc. Baytown, TX 281/838-0441 Birmingham, AL 205/322-5956 Fairburn, GA 770/969-4040 Indianapolis, IN 317/353-0199 Louisville, KY 502/585-1241 Middletown, OH 513/424-7287 Orleans, IN812/865-3232a division of Layne Christensen Company1212 University Street – Memphis, TN 38108 – 901/276-6605*************************************Christensen Pumps。
手术室恒速泵操作流程

手术室恒速泵操作流程英文回答:The operating room constant speed pump is an essential device used during surgeries to deliver fluids and medications to patients at a predetermined rate. As an operating room nurse, I am responsible for operating the constant speed pump and ensuring its proper use. Here is a step-by-step guide to the operation process:1. Preparation: Before using the constant speed pump, I make sure to gather all the necessary equipment and supplies, including the pump itself, IV bags or syringes with the required fluids or medications, tubing, and any additional accessories such as filters or extension sets. I check the expiration dates and integrity of all items to ensure patient safety.2. Priming the pump: I start by priming the pump, which involves removing any air bubbles from the tubing andensuring a continuous flow of fluid. I connect the tubing to the pump and fill the tubing with the fluid or medication, making sure to remove any air pockets. This step is crucial to prevent air embolisms and ensure accurate delivery.3. Setting the flow rate: Once the pump is primed, I set the desired flow rate based on the physician's orders. This can be done by entering the rate directly into the pump's control panel or by adjusting the manual flowcontrol knob. I double-check the settings to ensure accuracy and prevent any potential errors.4. Connecting to the patient: After setting the flow rate, I connect the tubing to the patient's IV catheter or other access device. I make sure the connection is secure and free from any leaks. I also check the compatibility of the fluids or medications being delivered to ensure patient safety.5. Monitoring and adjustment: Once the constant speed pump is running, I closely monitor the flow rate and thepatient's response. I regularly check the pump's display to ensure the flow rate remains stable and within the prescribed range. If any changes are needed, such as adjusting the flow rate or stopping the pump, I take prompt action and document the interventions.6. Troubleshooting: In case of any malfunction or alarm from the constant speed pump, I follow the manufacturer's instructions and troubleshooting guidelines. I take appropriate actions to resolve the issue or seek assistance from the biomedical engineering department if needed.7. Documentation: Throughout the entire process, I document all the relevant information, including the start and stop times of the pump, the flow rate settings, any adjustments made, and the patient's response. Accurate documentation is crucial for maintaining a comprehensive record of the patient's care and for legal and quality assurance purposes.中文回答:手术室恒速泵是手术过程中不可或缺的设备,用于以预定速率向患者输送液体和药物。
潜水池和温泉泳池泵所有者指南说明书

OWNER’S MANUAL Swimming Pool and Spa PumpREAD THIS MANUAL CAREFULLYBEFORE USING THE SPECK PUMPSECTION 1 IMPORTANT SAFETY INSTRUCTIONSWhen installing and using this electrical equipment,basic safety precautions should always be followed:READ AND FOLLOW ALL INSTRUCTIONS.WARNING -To reduce the risk of injury, do not permit children to use this equipment.(For cord - and plug - connected units)WARNING - Risk of Electric Shock. Connect onlyto a grounding type receptacle protected by a ground-fault circuit-interrupter (GFCI). Contact a qualified electrician if you cannot verify that the receptacle is protected by a GFCI.(For cord - and plug - connected units)WARNING - Do not bury cord. Locate cord to minimize abuse from lawn mowers, hedge trimmers,and other equipment.(For cord - and plug - connected units)WARNING - To reduce the risk of electric shock,replace damaged cord immediately.(For cord - and plug - connected units)WARNING - To reduce the risk of electric shock, do not use extension cord to connect unit to electric supply;provide a properly located outlet.(For swimming pool pumps with a minimum 25-foot(7.6-m) cord)NOTE: All wiring should be done by a qualified electrician in accordance with the National Electrical Code and all Local Codes.NOTE: Before installation, inspect all equipment, plumbing and wiring for damage that may have occurred during shipment.The shipping container has been specifically designed to prevent damage, however, any indications of damage should be carefully noted on the delivery ticket and a claim needs to be filed with the carrier.All pumps are water tested on a test stand to ensure that they meet specification.CAUTION - This pump is for use with storable pools only. Do not use with permanently installed pools. A storable pool is constructed so that it may be readily disassembled for storage and reassembled to its original integrity. A permanently installed pool is constructed in or on the ground or in a building such that it cannot be readily disassembled for storage.(For swimming pool pumps with or without a maximum 3 foot (0.91 -m) cord)CAUTION - This pump is for use with permanently installed pools and may also be used with hot tubs and spas if so marked. Do not use with storable pools. A permanently installed pool is constructed in or on the ground or in a building such that it cannot be readily disassembled for storage. A storable pool is constructed so that it may be readily disassembled for storage and reassembled to its original integrity.TO REDUCE RISK OF ELECTRICAL SHOCK,connect ground wires to grounding screw located in the motor. Use no smaller than a #1 2 AWG (3.3mm2) wire.TO REDUCE RISK OF ELECTRICAL SHOCK,a bonding connector is provided for bonding to metal water pipes, metal rails, or other metal within 5 feet of the swimming pool. All local points should be bonded with a #8 AWG (8.4mm2) wire.NOTE:To installer and/or operator of the Speck Swimming Pool Pump; the manufacturer’s warranty will be void if the pump is improperly installed and/or operated.READ INSTRUCTIONS CAREFULLY .SAVE THESE INSTRUCTIONS!1.2.3.4.5.6.7.8.9.10.SECTION 2 WINTERIZINGIn areas subject to freezing winter temperatures, protect by removing drain plugs. Do not replace plug.Store plug in strainer basket for winter.An alternative is to remove the pump and motor from plumbing and store indoors in a warm and dry location.Locate pump as close to the pool as practical.Consult local codes for minimum distance between pool and pump.The piping should be as direct and free from turns orbends as possible, as elbows and other fittings greatly increase friction losses.Place pump on a solid foundation which provides arigid and vibration-free support so that it is readily accessible for service and maintenance.Protect the pump against flooding and excessmoisture, and prevent foreign objects from clogging air circulation around motor.DO NOT store or use gasoline or other flammablevapors or liquids in the vicinity of this pump. DO NOT store pool chemicals near the pump.DO NOT remove any safety alert labels such asDANGER,WARNING,or CAUTION.Keep safety labels in good condition and replace missing or damaged labels.When connecting pipework to pump it is recommendedto use multi-purpose PVC glue to attach slip fittings to adaptors. If threaded connections are used it is recommended that thread seal tape be used. If the suction pipe is not sealed correctly, the pump will not prime properly and will pump small volumes of water or none at all. NOTE: The adaptors on the pump housing are factory mounted and should never be removed. Removal of these adaptors will void warranty.When installing the pump, care should be taken to seethat the suction line is below water level to a point immediately beneath the pump to ensure quick priming via a flooded suction line. The height between the pump and the water level should not be more that 4 feet. (Does not apply to Model 2180/..G for flooded suction.)SECTION 3EQUIPMENT OPERATION ANDMAINTENANCESECTION 4 MAINTENANCE2/1 LOCATION2/2 INSTALLATION1.2.3.4.5.6.1.2. 3.4.5.6.The pump requires little or no service other than reasonable care and periodic cleaning of the strainer basket. The seal on the pump is a mechanical seal.The seal may come loose during the course of time,depending on the running time and water quality. If water continually leaks out, a new mechanical seal should be fitted.To replace a mechanical seal, remove the eight bolts holding the casing to the seal-housing. Slide the motor part including the seal-housing out. Remove impellernut by turning it counter-clockwise when facing it,while holding motor shaft with a 1/2” wrench at rear end of motor. Pull pump impeller from shaft and slide seal from impeller shaft. To re-assemble,reverse the process. (Use a drop of loctite to secure the impeller nut.) Note: Make sure both parts of the mechanical seal (ceramic and spring portion) are clean. Gently wipe polished faces with soft and dry cotton cloth.Surfaces can easily be damaged by dirt and scratching.Only water should be used as lubricant to mount both parts of the mechanical seal.REV. 071503 - Model 21 - 802999999926Suction and discharge line should be independentlysupported at a point near the pump to avoid strains being placed on the pump.It is advisable to install a gate valve and union in boththe suction and discharge line in the event that the pump must be removed for servicing.Model GSBefore starting the pump for the first time, remove the filler plug. Fill pump body with water until level with suction inlet. Replace plug, hand tight, making sure the O-ring is not damaged. (Does not apply to Model 2180/..G for flooded suction.)Model BSBefore starting the pump for the first time, remove the see-through lid. (Unscrew each of the four lid-knobs a little at a time, and continue this process until the whole lid comes off evenly, not tilted .) Fill strainer tank with water until level with suction inlet. Replace lid, making sure the O-ring is not damaged. Screw the four lid-knobs down evenly, hand tight.When installing and using the motor, basic safetyprecautions should always be followed. The wiring of motor should be done by a licensed electrician in accordance with local codes. Be certain that the motor frame is grounded. Motor name plate has voltage, phase, ampere draw and other motor information as well as wiring connection instructions.BONDING:As required by National Electrical Code Article 690-22, the pump motor must be electrically bonded to the pool structure (reinforced bars, etc.) by a solid copper conductor not smaller than #8 AWG via the external copper bonding lug on the pump motor.GROUNDING:Permanently ground the pump motor using a conductor of appropriate size. Connect to the #10 green headed ground screw provided inside the motor terminal box.NOTE:Do not connect to electric power supply until unit is permanently grounded.Make sure see-through lid and o-ring are clean and properly positioned. Tighten see-through lid (hand tight). Tighten all pipes and fittings on suction side of pump.Be sure water in pool is high enough to flow through skimmer.Make sure strainer tank is full of water.Open all valves in system. Clean skimmer and strainer tank. Open pump and check for clogging of impeller.Check voltage at motor. If low, pump will not come up to speed.Check that all power switches are on. Be sure fuse or circuit breaker is properly set.Time set properly? Check motor wiring at terminals.With power off, turn shaft. It should spin freely. If not, disassemble and repair.Back wash filter when filter pressure is high, or clean cartridges.Clean skimmer and pump strainer baskets.See problem 1.See problem 1.Noise when shaft is turned up by hand.Motor is hot in bearing area when running.Replace bearings.Increase size of electrical wire. Be sure motor is operating on correct voltage.Shield motor from sun’s rays.Do not tighten cover or enclose motor.a. Suction air leak.b. No water in pump.c. Closed valves or blocked lines.d. Low voltage to motor.a. No power to motor.b. Pump jammed.a. Dirty filter.b. Dirty skimmer basket.c. Suction air leak.d. Closed valves or blocked lines.a. Bad bearings.a. Low voltage.b. Installed in direct sun.c. Poor ventilation.1. Pump will not prime.2. Motor does not turn.3. Low flow.4. Noisy operation of motor.5. Motor runs hot.SECTION 6 TROUBLESHOOTING GUIDEPROBLEMPOSSIBLE CAUSESSOLUTIONThese motors will run hot to the touch, however, this is normal. They are designed that way. Thermal overload protector will function to turn them off if there is an overload or high temperature problem. Excessive heat can be caused by:SECTION 5 SERVICING INFORMATIONWhen calling the manufacturer regarding a question or problem with your pump, please have the serial number available. The serial number is located on the Speck Pump model label on the motor or pump flange.Replacement parts may be available from your installer.Call, fax, or write:Speck Pumps - Pool Products, Inc. • 8125 Bayberry Road • Jacksonville, FL 32256Phone(904)739-2626•Fax(904)737-5261•email:************************Repair leak. Check suction pipe, see-through lid in place? O-ring clean?Remove blockage or increase suction pipe size. Make sure strainer tank is clean. Are all suction valves fully open?Disassemble pump and remove foreign matter from impeller.Improve suction conditions. (Reduce suction lift, reduce number of fittings,increase pipe size.) Increase discharge pressure and reduce flow by throttling discharge valve.Check wiring diagram on motor.Check with volt meter. Increase size of supply wire. Report low supply voltage to power company. Voltage at motor must be within 10% of motor nameplate voltage.Heaters should be one size larger than full load amps shown on motor nameplate.Indicated by high amperage readings on motor, binding shaft. Disassemble unit and correct.a. Air leak in suction line. Bubblesin water returning to pool at inlet.b. Restricted suction line due to blockage or undersize pipe.Indicated by high vacuum reading at pump suction.c. Foreign matter (gravel, metal,etc.) in pump impeller.d. Cavitation.a. Motor is not connected properly.b. Low voltage due to undersize wire or low incoming voltage.c. Wrong size heaters in protective device.d. Overload due to binding in pump or wrong size impeller.PROBLEM POSSIBLE CAUSESSOLUTION6. Noisy operation of pump.7. Motor overload protection “kicks out.”SAVE THESE INSTRUCTIONS!LIMITED WARRANTYThe pump and motor are warranted to be free from defects in materialand workmanship for a period of twenty-four (24) months from the date that the pump is originally installed.Notwithstanding any provision herein to the contrary, the warranties and obligations hereunder shall not in any event extend for more than 3 years beyond the date of shipment of the motor and the pump from the factory in Jacksonville, Florida.Warranty is void in the following cases: damages which result in wholeor in part from: (a) careless or improper installation of the pump or the motor; b) Improper or negligent use and maintenance of the pump or the motor; (c) tampering with the pump or the motor by unauthorized repair personnel.The manufacturer’s sole obligation hereunder shall be to replace orrepair any defective pump or motor. The manufacturer reserves the absolute right to determine whether any defective pump or motor should be replaced or repaired.Any customer who wishes to make a claim under this Limited Warranty shall notify the manufacturer of such claim by telephone or by mail. After the customer has been authorized to return a defective pump or motor, the customer must return the pump or motor to the manufacturer at 8125 Bayberry Road, Jacksonville,Florida 32256. Any goods returned to the manufacturer without prior authorization will be returned to the shipper unopened. Themanufacturer shall not bear any costs or risks incurred In shipping a defective pump or motor to the manufacturer or in shipping a repaired or replaced pump or motor to a customer.The manufacturer will charge customers for all nonwarranty workwhich it may perform. Warranty work will not be performed until the customer has accepted the price quoted.EXCEPT AS SPECIFICALLY SET FORTH ABOVE, NO OTHERWARRANTIES, WHETHER EXPRESSED OR IMPLIED, INCLUDING,WITHOUT LIMITATION, THE IMPLIED WARRANTIES OF MERCHANTABILITY AND FITNESS FOR A PARTICULAR PURPOSE, ARE MADE BY THE MANUFACTURER. IN NO EVENT WILL THE MANUFACTURER BE LIABLE FOR ANY LOSS, INCLUDING TIME, MONEY , GOODWILL, LOST PROFITS AND CONSEQUENTIAL DAMAGES BASED ON CONTRACT, TORT OR OTHER LEGAL THEORY , WHICH MAY ARISE HEREUNDER OR FROM THE USE, OPERATION OR MODIFICATION OF THE PUMP ,MOTOR OR ASSOCIATED PARTS, THE MAXIMUM LIABILITY OF THE MANUFACTURER HEREUNDER SHALL NOT EXCEED THE AMOUNT ACTUALLY PAID BY THE CUSTOMER FOR THE PUMP ,MOTOR, AND ASSOCIATED PARTS.Some states do not permit limitations on the terms of impliedwarranties or on the recovery of incidental or consequential damages. Accordingly, the limitations contained in paragraph 7 may not apply to certain customers.This warranty gives customers specific legal rights. Customers mayhave other rights which vary from state to state.1.2.3.4.5. 6.7.8.9.Date of Installation____________________Installed By__________________________For Service Call________________________________The manufacturer supplies a limited warranty to the original consumer purchaser of the pump and the motor on the following terms and conditions:REV. 071503 - Model 21 - 802999999926。
真空加压饱和装置操作流程

真空加压饱和装置操作流程The operation process of the vacuum pressurization saturation device is crucial for achieving the desired results in various industries, particularly in the field of food processing and packaging. 真空加压饱和装置的操作流程对于在食品加工和包装等领域取得理想的结果至关重要。
From the initial setup to the final product, every step in the operation process requires precision and attention to detail. 从初始设置到最终产品,操作流程中的每一步都需要精确和对细节的关注。
It involves carefully preparing the materials, setting up the equipment, monitoring the process, and maintaining safety protocols. 这涉及到仔细准备材料、设置设备、监控过程以及遵守安全规程。
The first step in the operation process of the vacuum pressurization saturation device is to prepare the materials to be processed. 真空加压饱和装置操作流程的第一步是准备待加工的材料。
This may involve cleaning, cutting, and portioning the ingredients according to the specific requirements of the product. 这可能涉及按照产品的具体要求清洁、切割和分配原料。
离心泵封闭试验英语

离心泵封闭试验英语The centrifugal pump, a marvel of engineering, is an essential component in various industrial applications. Its performance is critical, and thus, it undergoes rigorous testing to ensure reliability.During the sealing test of a centrifugal pump, the focus is on the integrity of the pump casing and impeller. Any leakage could compromise the system's efficiency and safety.The process involves pressurizing the pump with a controlled amount of air or liquid to simulate operational conditions. Sensors and gauges are meticulously monitored to detect even the slightest signs of leakage.A successful test confirms that the pump is sealed properly, with no air or liquid escaping from the intended flow path. This is vital for maintaining the pump's performance and preventing potential environmental hazards.In case of a failed test, the pump is disassembled to identify the source of the leak. It could be due to faulty gaskets, damaged seals, or improper assembly, all of which require immediate attention.Once the issue is resolved, the pump is reassembled and tested again. The cycle continues until the pump meets the stringent standards set for its operation.The sealing test is not just a one-time procedure; it is a continuous process that ensures the centrifugal pump remains in optimal condition throughout its service life.In conclusion, the sealing test of a centrifugal pump is a crucial step in the pump's lifecycle. It ensures that the pump operates efficiently and safely, protecting both the system and the environment.。
ETP Series - 自主吸取泵说明书
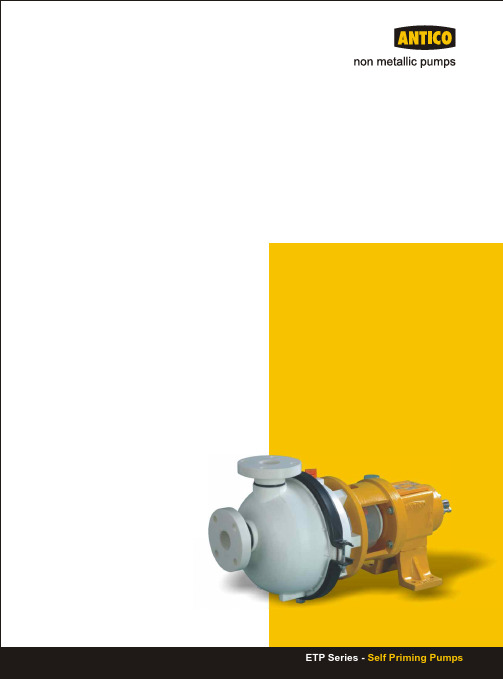
ETP Series - Self Priming PumpsETP SERIESDecades of experience in development &manufacturing of injection MouldedPolypropylene Corrosion Resistant Pumps.ETP 5078Large Priming ChamberInjection moulded corrosionresistant polypropyleneself-priming chamber retains liquid for priming and enables pump to lift up to 3 mts.Check ValvePrevents back - flow siphoning and allows for faster restart.Ball BearingsInboard bearing is pressed on shaft and free to float axially in frame - carries radial load only.Outboard double row ball bearing is shouldered and locked on shaft with lock-nut and washer, and in bearing housing to carry radial and any unbalanced thrust load. All bearing fits are precision bored.Bearing FrameHeavy Cast Iron construction, precision machined for no shaft deflection of more than 0.05mm contains large oil reservoir.Gland packing pumps come with pure PTFE or PTFE Impregnated Blue Asbestos against specific customer requirements.Internal Mechanical Seal developed by Antico, has rotary unit fitted on the impeller and stationary unithoused in a rubber bellow. Polypropylene bellow holder ensures proper seal face loading. Used extensively in metal finishing industries.3Q (m /hr)H (m )100203040510152050 Hz n = 2900Performance Range ChartSealing OptionsMetallic seal is a multi spring outside mounted balanced seal with 'O' Ring as secondary seal. Excellent for crystalline media since clogging of rotary unit does not occur as is the case in PTFE bellows seal. Wide range of seal face materials available for various applications.G l a n d P a c k i n g I n t e r n a l M e c h a n i c a l S e a l M e t a l l i c S e a l P T F E B e l l o w sG l a n d P a c k i n g I n t e r n a l M e c h a n i c a l S e a l M e t a l l i c S e a l P T F E B e l l o w sETP - 50PTFE bellows provide universal chemical resistance for a wide range of services & non-wetted metal parts eliminate the need for expensive metallurgies. TB/TBR seal is inherently hydraulically balanced to ensure proper face loading. Installs easily on outside of stuffing box; eliminates the use of elastomers.Anticorrosive Equipment Pvt Ltd15, Hind Service Industries, 2nd Floor,Off V. S. Road, Shivaji Park, Mumbai - 400 028, India Phone : +91 22 2446 6496, 2446 8340, 2445 3501Fax : +91 22 2444 9271info@anticopumps.co.in www.anticopumps.co.inPump Dimensions & ConnectionsH 2B A EH 1CDM1M2S1Ø D(F )PC D GS2(I ) NO OF HOLE(H) HOLEDIADISCHARGE(F )PC D G(I ) NO OF HOLE(H) HOLEDIASUCTIONH 3NOTE :1) ALL DIMENSIONS IN mm2) DIMENSIONS SUBJECT TO CHANGE WITHOUT NOTICE 3) FLANGES AS PER ANSI B 16.5 # 150 FFETP - 50 MODELAH1H2M1M2S1S2Ø DBCDEF GH I F GI H SUCTION FLANGEDISCHARGE FLANGE12653165184204659518023012.525560H3178120501804120501804。
诺德克斯堡迪拜医疗设备有限公司的气泡伸展泵产品说明说明书
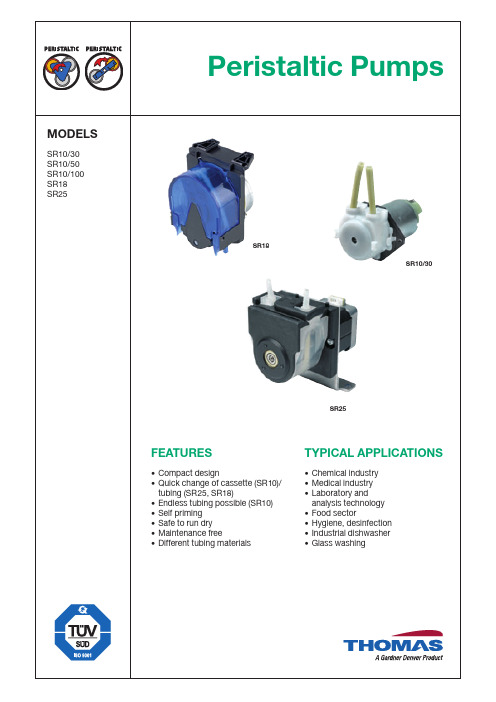
●●●●●●●●●●●●●●●1)●●●●●●●●5 – 7891112 – 17Stand-by pumpOperation mode DrivePage12/24 V D C12/24 V D C L C m o t o r230 V A C100 V /50-60 H zS t e p p e r m o t o rS h o r t t i m e o p e r a t i o nI P 54I P 54, a d j u s t a b l eC o n t i n u o u s o p e r a t i o n115 V A CFlow (ml/min)SR10/30SR10/50SR10/100SR18SR25MotorBracketLidTubingRollers Pump bodyMotor with gear boxroller carrier with spring Tubing with connectorsRolling bandClampr a w i n g 2018K A 01-05-0•Speed reduction through frictional connection from the motor shaft to the rollers.•Very simple construction with the use of few parts only.•Easy change of the cassette.•Generally 3 rollers.•For short time operation only.•If the pump is stored longer than three months, we recommend to take the cassette off the motor shaft and store it separately.•Different motors available(DC, low cost DC, AC and stepper motor).•Peristaltic pump with QuiXchange system •Tube exchange without tooling within seconds •Spring loaded roller carrier with two rollers for extre-mely long durability •Optional …sequencer“ for flow adjustment •AC-motorSeries SR18•Protection of the tubing due to spring loaded rollers and guiding side rollers.•Quick and easy change of the tubing.•Roller carrier with two rollers.•Also suitable for continuous operation, depending on the drive.•If stored longer than three months, we recommend to remove the tubing.•Different gear motors available (DC, AC and stepper motor).Series SR25Pump body1) We recommend to roughen the shaft in axial direction when changing the cassette(sand paper grit size 150).Norprene ®, PharMed BPT ®Norton Co. Reg. TM’sSR10SR18SR25Flow16 – 55 ml/min2) Note:The indicated values are average measured with water.The actual values depend on different parameters like quality and age of tubing, pressure of tubing beds, pressure ratios, viscosity, etc. (max deviation ± 30%)Please see page 4 for recommended running times andSR10/30 DC angled fixing(straight without drawing)Interference suppression according to EN 55011B (CE-conform)SR10/30 ACI n c h e s a r e s h o w n i n ( )W e i g h t 0,11 k gWeight 0,39 kgFixingInner tubingØFlow 230/50 Hz mm ml/minstraight 1,0 20300561angledCurrent consumption depending on the tubing diameter, at free flow and nominal voltage 12 V DC: 180 – 300 mA24V DC: 90 – 150 mA 230 V/50 Hz: 190 mA2030...Stock programme230 V/50 Hz, 12/24 V low cost DC For short time operation only D r a w i n g 11236I n c h e s a r e s h o w n i n ( )2) Note:The indicated values are average measured with water.The actual values depend on different parameters like quality and age of tubing, pressure of tubing beds, pressure ratios, viscosity, etc. (max deviation ± 30%)Please see page 4 for recommended running times and SR10/30 DC Angled flangeSR10/30 DC Straight flangew i n g 2030K A 04-04-00Weight 0,16 kgWeight 0,16 kgFixingInner tubing ØFlow 2)mm ml/minstraight 1,0 20angled straight 1,537angled straight 2.055angled straight 2,580angledCurrent consumption depending on the tubing diameter, at free flow and nominal voltage 12 V DC: 160 – 260 mA24 V DC: 80 – 130 mAFlow20 – 80 ml/min12/24 V Direct current motor For short time operation only 1) other tubing materials on request2) Note:The indicated values are average measured with water.The actual values depend on different parameters like quality and age of tubing, pressure of tubing beds, pressure ratios, viscosity, etc. (max deviation ± 30%)Please see page 4 for recommended running times and D r a w i n g 2030K A 02-04-00I n c h e s a r e s h o w n i n ( )Weight 0,08 kg1) Option: 14-pole connecting cable with plug,rocker switch for clockwise and lefthanded runningPotentiometer and speed-push-button, part number 29000702Flow0,5 – 20 ml/min24 V DC with stepper motor For short time operation only Circuit board recommended for test purposes4 possible operating methods • internal speed selection via jumper –option with wiring set 1)• external speed selection • analog input via pc• digital input (clocked pulse)Features• speed pre-selection• clockwise-, counter clockwise operation • instant priming• selective operating method80 (3,15)50 (2)42 (1,65)72 (2,8)ɂ3,6(0,14)* Delay fuse to be used.1) Note:The indicated values are average measured with water.The actual values depend on different parameters like quality and age of tubing, pressure of tubing beds, pressure ratios, viscosity, etc. (max deviation ± 30%)Please see page 4 for recommended running times and Flow 52 – 220 ml/minSR10/50 ACSR10/50 DCCurrent consumption depending on the tubing diameter, at free flow and nominal voltage 12 V DC: 0,4 – 0,54 A24 V DC: 0,2 – 0,27 A 230 V/50 Hz: 0,35 AOption:Straight flange for flush mounting part number 20501 ...Recommended inference suppression according to EN 55011 B (CE-conform)12/24 V DC – with additional circuit board (on request)2050...Stock programme2) Note:The indicated values are average measured with water.The actual values depend on different parameters like quality and age of tubing, pressure of tubing beds, pressure ratios, viscosity, etc. (max deviation ± 30%)Please see page 4 for recommended running times and Flow 1300 – 3000 ml/minSR10/100 DC With bracketCurrent consumption at free flow and nominal voltage12 V DC: 3,0 A 24 V DC: 1,5 A 230 V/50 Hz: 0,4 AOption:Recommended inference suppression according to EN 55011 B (CE-conform)12/24 V DC – with additional circuit board (on request)1) other tubing material on requestSR10/100 ACPeristaltic Pumps Series SR101) Note:The indicated values are average measured with water.The actual values depend on different parameters like quality and age of tubing, pressure of tubing beds, pressure ratios, viscosity, etc. (max deviation ± 10%)Please see page 4 for recommended running times and general data.Flow5 – 50 ml/min230 V/50 Hz 2), synchronous gear motor Suitable for continuous running Peristaltic Pumps SR18 with QuiXchange SystemFeaturesSequencer to adjust on/off-time (0% –100%)Nominal speedQuiXchange ml/minTubing only 9201855192018551920185529201855292018553920185539201855492018554ml/minTubing only 92018502920185022018...Stock programmeOptions: mounting clip Art. Nr. 29027360threaded tubing connector Art. Nr. 29027298Tubing QuiXchange2) Note:The indicated values are average measured with water.The actual values depend on different parameters like quality and age of tubing, pressure of tubing beds, pressure ratios, viscosity, etc. (max deviation ± 10%)Please see page 4 for recommended running times and Flow2 – 287 ml/min12/24 V, Direct current motor D r a w i n g 2025K A 04-04-00I n c h e s a r e s h o w n i n ( )D r a w i n g 2025K A 05-04-00I n c h e s a r e s h o w n i n ( )Bore pattern to fit in a housing see page 14.SR25, 10 to 80 rpm Direct current motorSR25–170 rpm 1)Direct current motorMaterial of tubing connectors:Tubing Silicon: for all Ø PVCTubing Novoprene:Ø 1,6/3,2 mm – PVCØ 4,1/4,8 mm – PPOption:Recommended inference suppression according to EN 55011 B (CE-conform)2025...Stock programme1) Pump with counter bearing2) Note:The indicated values are average measured with water.The actual values depend on different parameters like quality and age of tubing, pressure of tubing beds, pressure ratios, viscosity, etc. (max deviation ± 10%)Please see page 4 for recommended running times and Flow6 – 746 ml/minFor short time operation onlyMaterial of tubing connectors:Tubing Silicon: for all Ø PVCTubing Novoprene:Ø 1,6/3,2 mm – PVC2025...Stock programmeD r a w i n g 2025K A 03-04-00I n c h e s a r e s h o w n i n ( )D r a w i n g 2025K A 02-04-00I n c h e s a r e s h o w n i n ( )Bore pattern to fit in a housing see page 14.SR25–500 rpm shaded pole motor 1)SR25, 30 to 170 rpm shaded pole motor1) Pump with counter bearing 3) Fan2) Note:The indicated values are average measured with water.The actual values depend on different parameters like quality and age of tubing, pressure of tubing beds, pressure ratios, viscosity, etc. (max deviation ± 10%)Please see page 4 for recommended running times andBore pattern to fit in a housing(not illustrated)SR25, 1to 10 rpm Synchronous motorElectrical wiring:Option:Flow0,2 – 14 ml/minSuitable for continuous operation Material of tubing connectors:Tubing Novoprene:Ø 1,6/3,2 mm – PVCØ 4,1/4,8 mm – PP2025...Stock programme2) Note:The indicated values are average measured with water.The actual values depend on different parameters like quality and age of tubing, pressure of tubing beds, pressure ratios, viscosity, etc. (max deviation ± 10%)Please see page 4 for recommended running times and I n c h e s a r e s h o w n i n ( )1) Option: 200 mm 14-pole connecting cable with plug,rocker switch for clockwise and lefthanded runningPotentiometer and speed-push-button, part number 29000702Flow0,1 – 430 ml/min24 V DC with stepper motorCircuit board recommended for test purposes II III IV1,6 – 40 rpm 6 – 150 rpm12 – 300 rpmMax. flow 2) ml/min 0,3 – 7 1 – 262 – 5520252200202521001 – 30 4 – 1109 – 21020252201202521012 – 609 – 21520 – 430Peristaltic Pumps SR25-S3004 possible operating methods • internal speed selection via jumper –option with wiring set 1)• external speed selection • analog input via pc• digital input (clocked pulse)Features• speed pre-selection• clockwise-, counter clockwise operation • instant priming• selective operating method1600384pin assignment X3X1+/--/+X2J1J2X380 (3,15)50 (2)42(1,65)72 (2,8)ɂ3,6(0,14)1) Note:The indicated values are average measured with water.The actual values depend on different parameters like quality and age of tubing, pressure of tubing beds, pressure ratios, viscosity, etc. (max deviation ± 10%)Please see page 4 for recommended running times and general data.Synchronous motor SR25 – adjustable plastic housingwith synchronous motor (for wall fastening)Synchronous motor Voltage:230 V/50 Hz Power consumption:7,5 WTubing:Novoprene Pressure height:max. 10 m H 2O Suction height:max. 8 m H 2OEMC guide lineInterference resistance according to EN 50082-1Emitted interference according to EN 55011 BFlow0,2 – 21 ml/minPeristaltic Pumps SR25 - AdjustableD r a w i n g 16894I n c h es a r e s h o w n i n ( )Test-set with all tubings 92025857500 rpm 920258011)–––Rolling bandPart number29008965ClampPart number29020480SiliconNovoprenePharMed BPT ®Peristaltic Pumps SR251) Clockwise directionTubing PropertiesN = Novoprene Nor = Norprene ®Ph = PharMed BPT ®S = SiliconV = Viton ®The material resistance is influenced by temperature and concentration of the medium.The data have to be seen as indications and do not guarantee the material properties.A =small or no effectB =minor or moderate effectC =severe effectD =no reliable data, please test before use -=no available dataNorprene ®, PharMed BPT ®, Viton ® Du Pont, Norton Co. Reg. TM’s,。
Goulds Pumps Pump Selection System (PSS) User's Gu
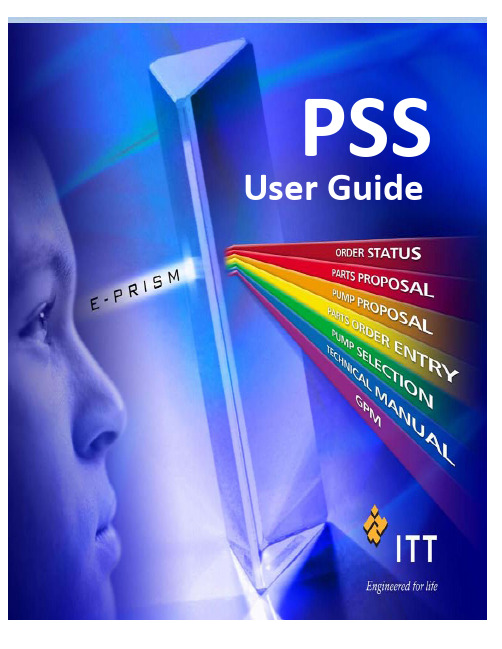
ContentsWhat’s on the Pump Selection System (PSS) screens? (4)The Criteria screen (4)The Selection screen (4)The Curves screen (4)The Preferences screen (5)Conducting a Basic Pump Criteria Search (5)Criteria screen, Basic tab (5)To perform a basic criteria pump search (5)To correct for viscosity (6)Optional selection criteria (6)Adding More Advanced Attributes for a Pump Search (7)Criteria screen, Advanced tab (7)Enter more advanced information relative to your requirements 7Entering Information Needed for Quotations (8)Proposal Header section (8)To obtain a Priced Pump Quotation (8)Viewing Pump Search Results (9)Results screen (9)To view pumps for analysis, printing or side-by-side comparison (9)To sort the selection list (9)To change the width of columns in the selection list . 9To change the contents or order of the columns in the selection list. (9)To remove pumps (10)To manually add (select) pumps (10)File management (10)To save your pump selections (10)To create new pump selections (10)To retrieve your pump selections (11)Viewing and Printing Pump Performance Curves (11)Curves screen (11)To display the CDS and equivalent water performance curves 12Additional Design Points (12)System Resistance Curves (12)To display viscosity corrections (13)To adjust pump speed, flow, head and impeller diameter 13 To evaluate multiple pump operation (13)To evaluate multiple pump speeds (13)To print performance curves (14)Setting Preferences (15)Preferences screen (15)Use Browser to view PDF file (15)To change the default units of measure (15)To change the default cycles (16)To change the contents and display order of items in the Selection List (16)To save your preferences (16)What’s on the Pump Selection System (PSS) screens?When you start PSS, the Criteria screen’s Basic tab appears.The Criteria screenThe Criteria screen is used to perform criteria searches. The Criteria screen has two tabs:▪Basic – This tab allows you to enter your operating criteria in order to begin your search for a pump. You can also correct for viscosity and limit your search tospecific pump models and/or speeds.▪Advanced – This tab allows you to enter more advanced information relative to your requirements▪Slurry Correction – This tab allows you to enter your Slurry information relative to your requirements▪Spec Questions – This tab allows you to enter Specification information relative to your requirements and helps narrow your search.▪Liquid Properties – This tab allows you to enter Liquid Properties that will be displayed on the Customer Datasheet.The Selection screenThe Selection screen displays the list of selected pumps based upon the requirements you entered on the Criteria screen. You can also use this screen to manually pick (add) or delete pumps by model, size, speed and/or curve number.Information is listed in tabular format to simplify pump comparisons. Pumps arehighlighted with an explanation of any warning messages that were generated based on your specified limits.The Curves screenThe Curves screen allows you to preview and print your selected performance curve(s).You can graph pumps individually, in series or in parallel and perform side-by-side comparisons. The Curves screen has two tabs:▪CDS – Shows the Water equivalent ISO performance curve. By default, pump performance is based on Water (s.g. 1.0, cp. 1.0) at 70o F.▪Line -- Shows the single-line and actual viscous performance curves. You can evaluate multiple pump operation and make pump adjustments to speed, impellerdiameter, flow and head.The Preferences screenThe Preferences screen allows you to customize the Pump Selection System (PSS). This screen can be accessed using the Settings – Preferences menu option. You can change units-of-measure and customize the contents and layout of the Selection screen.Conducting a Basic Pump Criteria SearchCriteria screen, Basic tabTo perform a basic criteria pump search1.Enter values for Flow, Total Dynamic Head, Cycles and (optionally) NPSHa.2.In the Models and Speeds boxes, select the models and speeds you want to search.You must choose at least one model and speed to perform a criteria search.Tip For faster searches; limit the number of chosen models & speeds.3.Click Search. The list of matching pumps will be shown on the Results screen.To correct for viscosityBy default, pump performance is based on Water at 70o F.1.In Liquid Properties, enter values for Temperature, Specific Gravity and Viscosity.2.Click Search. To view the viscous curve, go to Curves and click Line.Optional selection criteria▪% Headrise to Shut-Off – highlight pumps with a % Headrise to Shut-Off less than min, and/or more than to max.▪Suction Specific Speed Less than - highlight pumps that exceed this NSS value.▪Operating Point to be % BEP - highlight pumps with %BEP less than min, and/or more than to max.▪Allow near miss. Check this box to include in the search results pumps that slightly miss the required rated conditions▪Impeller diameter. Select any of the available options in order to limit the search results accordingly▪End of Curve to be greater or equal % - Allows you to enter the end of curve to be greater or Equal as a % of BEP Flow or % of Rated flow▪Min. dNPSH (NPSHa –NPSHr) – Allows you to enter the dNPSH at @ rated flow or @ 120% of rated flow.▪Minimum Flow to be less or Equal % - Allows you to enter the Minimum flow to be less or equal as % of BEP Flow or % of Rated Flow.The optional selection criteria are checked against each pump on the selection list and display a warning message if any of the specified conditions are violated. Completing this section does not limit your search or prevent you from selecting a pump with the exception of the impeller diameter field.Adding More Advanced Attributes for a Pump SearchCriteria screen, Advanced tabEnter more advanced information relative to your requirements1.Apply NPSH margin criteria for life cycle costCalculates the recommended NPSH margin (per Hydraulic Institute method) based on pump application, geometry and inlet conditions. Please ensure you have enteredthe NPSHa and added the “Min HI/ANSI NPSHa” and “Suction Energy” columns to theresults TAB, see Setting Preferences2.Based on your particular application or service, complete the Solids, Pulp & Paper,and/or Vertical Services sections.3.Notes entered will be printed only in the single line view datasheets.4.Click SearchEntering Information Needed for QuotationsProposal Header sectionEnter the information that is appropriate for your application. Click on Selection to go back to the criteria screenTo obtain a Priced Pump QuotationContact your nearest Goulds Pumps sales office or representative. To request a priced quotation by e-mail, go to , click Contact Goulds Pumps, and fill in the request formViewing Pump Search ResultsResults screenTip It takes about five seconds to load each curve (five curves would take 25 seconds).To view pumps for analysis, printing or side-by-side comparison1.To select a pump on the selection list, click the check box to the left of the pump.Click again to clear your selection. Repeat for multiple pumps or click Select All to select all pumps on the list. Click Select None to clear.2.Click View Selected. The Curves screen, CDS tab will appear and display eachselected curve.3.You can simply view one curve by double clicking on the selected curveTo sort the selection list▪Click the column heading that you want to sort by. To reverse the sort order, click again.To change the width of columns in the selection list▪Drag the boundary on the right side of the column heading until the column is the width you want.To change the contents or order of the columns in the selection list.▪You can temporarily change the order of the columns by dragging and dropping the column to the appropriate location. To permanently change the column sequence,see Setting Preferences.To remove pumps▪On the Selection screen, click Remove Unselected to remove all pumps that are not selected. Click Remove Selected to remove all selected pumps. Alternatively you can right click anywhere in the results table and use the filter options to reduce thenumber of selections.To manually add (select) pumps1.On the Results screen, click Add… and in the Add Pump dialog box…2.To Add by Model -- Click on a model in the Model list. Use the Cycles list box tochoose 60Hz or 50Hz speeds. Select the desired size/speed from the list, then click Add.3.To Add by Curve No. -- Enter the curve number in the Curve No box, then click Add.4.Click Done when finished. Manually added pumps appear at the bottom of theselection list.File managementPSS allows you save your selections either as individual services, each one under its own project/proposal name, or, in case of a project containing many services, all services can be saved under the same project/proposal nameTo save your pump selections1.You can either click on the save icon in the main tool bar or use the File - Savemenu option. The selection will be saved under the current proposal file name.One proposal may contain multiple pump selections.To create new pump selections1.You can create a New pump selection, within the same proposal, by pressing theNew icon or using the File - New Item menu option. One proposal maycontain multiple pump selections.2.To create a New pump proposals select the File – New Proposal menu option or clickon “New Proposal for PSS Item menu optionTo retrieve your pump selections1.Select the File - Open Proposal option from the main menu. Alternatively you canclick on the “Open Proposal for PSS items” menu optionViewing and Printing Pump Performance CurvesCurves screenThe Curves screen allows you to analyze, compare and print the selected performance curve(s). The Curves screen has four tabs:CDS – Displays the primary and water equivalent performance curves.▪Line – Displays the single-line and viscous performance curves. Use the Line tab to adjust pump speed and impeller diameters and to graph pumps individually, inseries or in parallel.▪View – Controls which curve elements (System Curves, etc.) are displayed. The View Add. Tab is activated in case the first stage size is different than the additional stage one and allows the user to view both curves.To display the CDS and equivalent water performance curves1.Click the CDS tab.2.Click the pump curve thumbnail to display the performance curve in the mainwindow.3.To change the information plotted on the curve, use the check boxes in the Viewtab.Additional Design Points1.Click on the Line Tab2.Click the pump curve thumbnail to select the curve you wish to evaluate.3.Click on “System curves/ Des.points”4.Click on Add in the Additional Design Points section of the screen.5.Double-click Flow Value, enter a flow value and press [Enter].6.Double-click Head Value, enter a head value and press [Enter].7.To edit or rename a Design Point, double-click on the value in the label field youwish to edit, type the new value, and press [Enter]. To remove a Design Point, select the Design Point, and click Remove.Tip Check the box “I want variable speed curves to go thru above point to have the program generate a set of variables speed curves that will go throughthe additional design point defined.System Resistance Curves1.Below the System Resistance Curves list, click Add.2.To edit or rename an existing System Resistance Curve, double-click the curveslabel, type the new value, and press [Enter].3.Below the Flow / Head list, click Add. Double-click on Flow Value, enter a flow valueand press [Enter]. Double-click on Head Value, enter a head value and press [Enter].Tip At least two (2) Head / Flow points are required to define a System Resistance Curve. Entering just two points will generate a parabolic curve.4.To remove an entire System Resistance Curve – In the System Resistance Curves list,select the curve and click Remove.To remove a Head/Flow point – In the Flow / Head list, select the set of points and click Remove.To display viscosity corrections1.Click the Line tab.2.Click the pump curve thumbnail to display the actual viscous fluid performancecurve in the main window. The viscosity correction factors are shown in the curves title block section. To calculate the water equivalent, divide the viscous value by its viscosity correction factor.3.To change what is displayed on the curve, use the check boxes in the View tab.To adjust pump speed, flow, head and impeller diameter1.Click the Line tab.2.Select the curve of the pump you wish to adjust by clicking its curve thumbnail.3.Click the Speed, Diameter, Flow or Head fields and type the new value. Press [Tab] tosee how pump performance is affected. You can also use the arrow buttons toincrease/decrease the pump speed and/or impeller diameter to the next increment. Tip When using the arrow buttons, you don’t need to press [Tab] after each change but you should wait for PSS to update the curve before makinganother change.To evaluate multiple pump operation1.Click the Line tab.2.Click the pump curve thumbnail to select the curve you wish to evaluate.3.Click Multi, click Pumps and select Parallel or Series.4.Enter the number of pumps in the Quantity field.5.Click Update to view the resulting performance curve.To evaluate multiple pump speeds1.Click the Line tab.2.Click the pump curve thumbnail to select the curve you wish to evaluate3.Click View variable speed curves. A set of 3 speeds will be added by default in 300RPM steps4.To add a new speed, click Add, double-click the Speed field, type a new speed value,and press [Enter]. Repeat to add additional speeds or edit existing speeds.5.When finished, click Draw to view the multi-speed curve.6.To delete a speed, select the speed and click Remove.To print performance curves1.Click the pump curve thumbnail to select the curve you wish to print2.Click on Create PDF button and select one or more forms from the available printforms.3.Once the Pump performance curve(s) are shown in Acrobat Reader you can you usethe Print feature to create a hard copy of the curve(s).Setting PreferencesPreferences screenThe Preferences screen allows you to customize the Pump Selection System (PSS). You can change units-of-measure and customize the contents and layout of the selection list.Use Browser to view PDF file1.This box should be checked only if the operating system is not MS Windows2.Acrobat Reader Path. The Adobe Acrobat Reader is required in order to create aprintable version of the pump performance curve.To change the default units of measure1.To change the units of measure for all fields, click the System Units: box and choosethe desired unit-of-measure (US Customery, Metric).2.To change the unit of measure for an individual field, click the Units box to thefield’s right (Capacity).To change the default cycles1.This setting control the default setting for cycles when a new selection is createdTo change the contents and display order of items in the Selection List1.Click on the Results Table drop down2.Select the columns you would like to see.3.Change to order the columns are shown using the up / down arrowsTo save your preferences1.Click Save Preferences to save your preference settings. Saved settings areautomatically loaded each time you run PSS.2.Click ok to temporarily (just for the current session) accept the changes made.Pump Selection ChartFigure 1. Pump Selection ChartPlease check our website () for the latest copy of the Pump Selection Chart.。
德斯米自主泵型NSA型产品说明书

OPERATION AND MAINTENANCE INSTRUCTIONSDESMI self-priming centrifugal pumpTYPE NSATable of contents:1. PRODUCT DESCRIPTION (3)1.1DELIVERY (3)2. TECHNICAL DATA (3)2.1EXPLANATION OF THE TYPE NUMBER (3)2.2TECHNICAL DESCRIPTION (4)3 . INSTALLATION (5)3.1MOUNTING/FASTENING (5)3.2WIRING (5)4. TRANSPORT/ STORAGE (6)5. INSPECTING THE PUMP (7)5.1INSPECTION (7)5.2FITTING SHAFT (7)5.3FITTING SHAFT SEAL (7)5.4ALIGNING COUPLING (7)6. FROST PROTECTION (8)7. DISMANTLING (8)8. START-UP (9)8.1STARTING (9)9. SYSTEM BALANCING (9)10. INSPECTION AND MAINTENANCE (11)10.1DRAINING THE PUMP (12)10.2BEARINGS (12)11. REPAIRS - ORDERING SPARE PARTS (12)12. OPERATING DATA (12)13. EU DECLARATION OF CONFORMITY (13)14. INFORMATION RELEVANT FOR DISASSEMBLY OR DISPOSAL AT END-OF-LIFE (14)15. ASSEMBLY DRAWINGS AND SPARE PARTS LISTS (15)15.1 ASSEMBLY DRAWING NSA50-200/zz-M12 (15)15.2 ASSEMBLY DRAWING NSA80-250/zz-M12 (16)15.3 ASSEMBLY DRAWING NSA80-250/zz-M09 (17)1.PRODUCT DESCRIPTIONThese operation and maintenance instructions apply to the DESMI NSA-pump series. The pumps are available in the sizes DN50 and DN80 discharge.DESMI NSA is a single-stage self-priming centrifugal pump with stainless steel shaft, and mechanical shaft seal. The NSA-pump is further equipped with a semi-open impeller, which does not choke aseasily as a closed impeller.The pump is suited for clean and polluted liquids with temperatures between 0 and 80︒C. With special shaft seal up to 140︒C.The suction branch of the pump is mounted well above impeller inlet. This is an advantage as the pump will not - in case of a clack flap leakage - loose all the priming water and consequently the priming ability.As the pump is self-priming, contrary to ordinary centrifugal pumps it will resume pumping if, for a short moment, the liquid has been lowered to a level below the suction pipe.The pump is particularly suitable for the pumping of water in connection with e.g. cooling of diesel engines, as bilge pump, ballast pump, irrigation, washing plants, air conditioning, cooling systems, and sanitary systems, etc. Furthermore, in the majority of cases where the transport of liquid is required within industry.1.1DELIVERY- Check on receipt that the delivery is complete and undamaged.- Defects and damages, if any, to be reported to the carrier and the supplier immediatelyin order that a claim can be advanced.2.TECHNICAL DATAThe pumps are manufactured in various material combinations which appear from the type number on the name plate. See below.2.1EXPLANATION OF THE TYPE NUMBERAll the NSA-pumps are provided with a name plate. The type number indicated on the name plate is built up as follows:NSAXXX-YYYB/ZZ-MR/OXXX : Discharge flange diameter.YYY : Standard impeller diameter.B : If mounted with special impeller for 2-pole motorZZ : Height of the impeller blades.M : The material combination of the pump.R : The assembly combination of the pump.O : Actual impeller diameter.M may be the following:A : Standard. casing: GG20. Impeller/wear plate: RG5.B : Standard. casing: GG20. Impeller/wear plate: Stainless steel.C : All cast iron.D : Casing: RG5. Impeller/wear plate: RG5.E : Special bronze casing and/or impellerThe pumps are available in other material combinations at request.R may be the following:07 : Mounted on base frame with petrol or diesel engine, or withhydraulic or electric motor.09 : With bare shaft end.12 : Flange-mounted with electric motor.Before putting a pump into operation, the suitability of the material combination of the pump must always be taken into consideration. In case of doubt, contact the supplier.Pumps in material combinations A and C are primarily used for freshwater.Pumps in material combination D are primarily used for seawater.If the pumps are designed for special purposes the following is to be indicated:Pump No. :Pump type :Application :Comment :2.2TECHNICAL DESCRIPTIONThe noise level from the pump depends on the motor type supplied, as the noise from the pump can be calculated as the noise level of the motor + 2dB(A).The noise level of the motor appears from the instruction manual for the motor.The pump capacity appears on the nameplate of the pump. If the pump has been delivered without motor, the pump capacity is to be indicated on the plate when mounting the motor. The permissible loads on the flanges are indicated in the following table:Fv : The max. permissible sum of the vertical forces on the two flanges. Fh : The max. permissible sum of the horizontal forces on the two flanges. ∑F : The vectorial sum of the two forces Fv and Fh.∑Mt : The max. permissible sum of the torches on the two flanges.In connection with the permissible loads on the flanges the following is to be observed:where index "calc" is the values calculated by the user.3 . INSTALLATION3.1 MOUNTING/FASTENINGThe pump should be mounted and fastened on a solid base plate with a flat and horizontal surface to avoid distortion. Check that the centre line of the shaft is horizontal.The max. permissible loads on the flanges stated in paragraph 2.2. are to be observed.The suction line to the pump is to be mounted carefully, so that it is absolutely tight, as even minor leakages may impede the priming. When pumping polluted liquids a strainer is necessary. The strainer must be equipped with a sieve, the passage area of which is to be 3 x the area of the suction pipe. The mesh size is to be 1-3 mm smaller than the height of the impeller blades of the pump in question.The pipes are to be arranged in such a way that stresses resulting from fluctuations in temperature will not have any effect on the pump. Because of the priming of the pump the pressure pipe is to be arranged so that water locks in the pipe are avoided. If the pump is to be driven by a motor through a flexible coupling, motor and coupling are to be placed on a common base plate. In this connection the following must be observed:- Avoid distortion of the base plate. - Avoid distortion of the piping system.- Check carefully that pump and motor are accurately aligned.At installations pumping hot or very cold liquids, the operator must be aware that it is dangerous to touch the pump surface, and, consequently, he must take the necessary safety measures. When connecting the pump and a prime mover the power transmission is to be equipped with a guard in accordance with the provisions of the COUNCIL DIRECTIVE OF June 14, 1989, on the safety of machines.3.2 WIRINGWiring to be carried out by authorised skilled workmen according to the rules and regulations in force.222 ⎪⎪⎭⎫ ⎝⎛+⎪⎪⎭⎫ ⎝⎛∑∑∑∑t calc calc M M F F4.TRANSPORT/STORAGEThe weights of the pumps without motor are stated in the following table:Lift the pump by placing the rope around it and see to it that the pump is balanced. The rope must not bear against sharp edges and corners.Lifting eyes might be mounted in the pump and used instead. The pump weights appear from the above table.Before shipment the pump is to be fastened securely on a pallet or the like.The pump is to be stored in a dry area.5.INSPECTING THE PUMP5.1INSPECTIONWhen the pump has been dismantled, check the following parts for wear and damage:- Wear plate/impeller : Max. clearance 0.4 - 0.5 mm.- Shaft seal/rear cover : Check seat for flatness and cracks.Check rubber parts for elasticity.- Bearings : Replace in case of wear and noise.5.2FITTING SHAFTWhen the pump has been assembled, check that the shaft rotates freely. In case the shaft has been dismantled in the 12-combination, adjust the shaft to the original, axial position on the electric motor to obtain a 0,2-0,5 mm gap between impeller and wear plate. Fasten the pointed screws (if three screws first the middle screw) according to the below table – screws to be secured with Loctite 243 or Omnifit 40M or similar. Check that the wobble, measured as close to the shaft end as possible, is within the limits indicated in the table.5.3FITTING SHAFT SEALBefore fitting the seat, clean the recess in the shaft seal cover. When fitting the seat, remove the protective coating without scratching the lapped surface. Dip the outer rubber ring of the seat into soapy water. Now press the seat into place with the fingers and check that all parts are correctly imbedded.If it is necessary to use tools for assembling, protect the sliding surface of the seat to prevent it from being scratched or cut. Lubricate the inner surface of the slide ring rubber bellows with soapy water and push it over the shaft. The use of a conical fitting bush as shown on the assembly drawing is recommended to avoid that the rubber bellows is cut.Push the slide ring over the shaft with the hand. If the rubber bellows is tight, use a fitting tool and take care that the slide ring is not damaged. If the carbon ring is not fixed, it is important to check that it is fitted correctly, i.e. the chamfered/lapped side is to face the seat. The carbon ring can be held by a little grease.When using soapy water on the shaft, the bellows will settle and seat in about 15 minutes, and until then tightness should not be expected. After start, check by viewing the leak hole that there are no leaks.5.4ALIGNING COUPLINGIn order to avoid break-downs of a pump coupled to a motor on the same base plate through a flexible coupling, the following should be observed:1. Avoid distortion of the base plate.2. Avoid distortion in the piping system.3. Check on the coupling that pump and motor are aligned accurately.Below please find 2 proposals for alignment. The deviations mentioned cover a complete revolution of the coupling. The distance between the coupling halves is to be between 2 and 4 mm. * : Steel ruler. **6. FROST PROTECTIONPumps, which are not in operation during frost periods, are to be drained to avoid frost damage. Remove the plug at the bottom to empty the pump. Alternatively, it is possible to use anti-freeze liquids in normal constructions.7. DISMANTLINGBefore dismantling the pump make sure that it has stopped. Empty the pump of liquid before it is dismantled from the piping system. If the pump has been pumping dangerous liquids you are to be aware of this and take the necessary safety measures.If the pump has been pumping hot liquids, take great care that it is drained before it is removed from the piping system.8.START-UPA self-priming centrifugal pump will not function until the pump casinghas been filled with liquid. Remove the plug at the top ofthe pump casing and fill the pump with cold liquid. Fit theplug and the pump is ready for service.The liquid alsoserves as coolant for the shaft seal. Consequently, thepump must in no circumstances be started before it hasbeen primed with liquid. Furthermore, the pump mustnever run dry.For safety reasons the pump is only allowed to operate against closed discharge valve for a short time (max. 5 minutes and at a max. temperature of 80°C for standard pumps). Otherwise there is a risk of damage to the pump and, at worst, of a steam explosion. If the pump is not monitored, the installation of a safety device is recommended.The pump is equipped with a relief valve, which opens at a pre-set pressure. Be careful: If the valve opens, the escaping liquid will most likely be hot. The relief valve must in NO circumstances be removed or re-adjusted !As regards maintenance of the relief valve - see paragraph 10.8.1STARTINGBefore starting the pump check that- the shaft rotates freely without jarring sounds.- the pump casing is filled with liquid.Start the pump for a moment to check the direction of rotation. If the direction is correct (i.e. in the direction of the arrow), the pump may be started.9.SYSTEM BALANCINGIt is often difficult to calculate a manometric delivery head in advance. It is, however, decisively important to the quantity of liquid delivered.A considerably smaller delivery head than expected will increase the quantity of liquid delivered, causing increased power consumption and perhaps cavitation in pump and piping. In the pump the impeller may show signs of heavy erosion caused by cavitation (corrosion) which may at times render an impeller unfit for use in a very short time. Not unusually do similar erosions occur in pipe bends and valves elsewhere in the piping system. Therefore, after start-up, it is necessary to check either the quantity of liquid delivered or the power consumption of the pump e.g. by measuring the current intensity of the connected motor. Together with a reading of the differential pressure the quantity of water delivered can be determined against the characteristics of the pump.Should the pump not function as intended, please proceed according to the fault-finding list. Bear in mind, though, that the pump was carefully checked and tested at the factory and that the majority of faults stem from the piping system.10.INSPECTION AND MAINTENANCE- Before any inspection of the pump, check that the unit cannot be started unintentionally.- The system is to be without pressure and drained of liquid.- The repairman must be familiar with the type of liquid, which has been pumped as well as with the safety measures he is to take when handling the liquid.- Inspect the shaft seal for leaks at regular intervals.- Activate the relief valve at regular intervals in order to check the function. If the valve is choked, replace or clean it, if possible.10.1DRAINING THE PUMPWhen the piping system has been drained, note that there is still some liquid left in the pump. Remove the remaining liquid by dismantling the pipe plug at the bottom of the pump.10.2BEARINGSThe pump (09 design only) is equipped with ball bearings, which were lubricated for life before leaving the factory. Therefore, they require no attention but are to be replaced in case of noise or bearing wear. Place a bead of grease on the sides of cleaned or newly mounted bearings. As far as semi-closed bearings are concerned, place grease on the open side of the bearing only.A recommended grease quality on a lithium-basis is used:ESSO ................................................. B eacon 2BP ...................................................... E nergrease EP grease 2Shell ................................................... A lvania grease 2Mobil .................................................. M obil lux grease EP 2 or Mobil plex 47Castrol ................................................ S pherol AP2Texaco ............................................... M ultifak EP 2Q8 ...................................................... R embrandt EP 2 and RubensStatoil ................................................. S tatoil Uniway U211.REPAIRS-ORDERING SPARE PARTSWhen ordering spare parts please always state pump type and pump No. (appears on the name plate of the pump). See also spare parts drawing with item Nos.12.OPERATING DATAThe following working pressures are allowed:The above-mentioned max. working pressure is NOT valid for pumps approved by a classification society. Pumps approved by classification societies have been pressure tested according to the requirements of these societies, i.e. a test pressure of 1.5 x the permissible working pressure. The test pressure is stated in the test certificate and stamped into the discharge flange of the pump.The following max. numbers of revolutions are allowed for NSA-pumps with full impeller diameter:The capacities of the pumps appear from the nameplates.13.EU DECLARATION OF CONFORMITYDESMI PUMPING TECHNOLOGY A/S, hereby declare that our pumps of the type NSA are manufactured in conformity with the following essential safety and health requirements in the COUNCIL DIRECTIVE 2006/42/EC on machines, Annex 1.The following harmonized standards have been used:Pumps delivered by us connected with prime movers are CE-marked and comply with the above requirements.Pumps delivered by us without prime movers (as partly completed machinery) must only be used when the prime mover and the connection between prime mover and pump comply with the above requirements.Nørresundby, March 05 2019Henrik Mørkholt SørensenManaging DirectorDESMI Pumping Technology A/STagholm 19400 NørresundbyRMATION RELEVANT FOR DISASSEMBLY OR DISPOSAL AT END-OF-LIFENo damage materials are used in DESMI pumps – please refer to DESMI Green Passport (can be sent on request – contact a DESMI sales office) – i.e. common recycling companies can handle the disposal at end-of-life. Alternatively the pump and motor can be returned toDESMI at end-of-life for safe recycling.15.ASSEMBLY DRAWINGS AND SPARE PARTS LISTS15.1 ASSEMBLY DRAWING NSA50-200/zz-M121 Nut2 Stud3 Sealing washer5 Impeller6 O-ring8 Washer9 Nut10 Wear plate11 Pump casing12 Stud13 Plug/sealingwasher14 Relief valve17 Shaft/Pointedscrew19 Motor bracket20 Name plate21 Screw fornameplate22 Nut29 Key30 Stud31 Screw/washer33 Plug/sealingwasher37 Shaft seal38 Check valve15.2 ASSEMBLY DRAWING NSA80-250/zz-M121 Pumpcasing2 Motor bracket4 Rear cover6 Pointed screw7 Impeller8 Wear plate9 Set screw10 Washer15 Shaft16 Key17 Intermediate flange*18 Spring washer19 Stud20 Stud21 Stud22 Stud24 Pointed screw25 Nut26 Nut27 Washer28 Pipe plug29 Pipe plug30 Inlet flange31 Screw/washer32 Allen screw**37 Shaft seal38 Check valve41 O-ring44 Sealing washer46 Sealing washer75 Pipe plug76 Relief valve*) Only for size 132motor**) If B5 motor15.3 ASSEMBLY DRAWING NSA80-250/zz-M0917 Key 29 Pipe plug。
气压封口机操作流程

气压封口机操作流程Operating a pneumatic sealing machine can be a relatively straightforward process, although it requires attention to detail and adherence to safety protocols. The first step in the process is to ensure that the machine is properly set up and ready for operation. This includes checking the air pressure, adjusting the temperature settings, and making sure that the sealing material is loaded correctly.气压封口机的操作流程可能相对直截了当,尽管它需要注意细节和遵守安全规程。
流程的第一步是确保机器已经正确设置并准备好运行。
这包括检查气压、调整温度设置,以及确保封口材料被正确加载。
Once the machine is ready, the next step is to begin the sealing process. This involves placing the items to be sealed into the machine, ensuring that they are positioned correctly and evenly. It is important to pay close attention to the placement of the items to ensure a proper seal and to prevent damage to the machine.一旦机器准备好,下一步是开始封口过程。
Booster Pump Operation Procedure

a. Slowly close the discharge valve. b. Power off the motor. c. Fully closed the suction valve.
2.3 Swap the pump
2.4 Open another booster pump suction valve
b. Check offloading tank inlet/outlet valve open .(normally open).
第9页
2019/8/13
2. Booster pump operation
2.1 Start the booster pump
c. Open the pump two suction valves.
第3页
2019/8/13
1. Basic booster pump data
1.1 Booster pump operational data
Pumping medium
Crude oil
Density (kg/m3)
Q (m3/h)
925
H (m)
P (kW)
Motor P(KW)
Imbalance between pump and motor
Parts of impeller missing
Troubleshooting and solutions Exchange offloading tank to a high level tank
Stop the pump and check the impeller Check the process and fix the leakage point Stop pump and bleed off the gas. Let the liquid full fill the pump Check the process and fix the leakage point Check the process
Grundfos pump
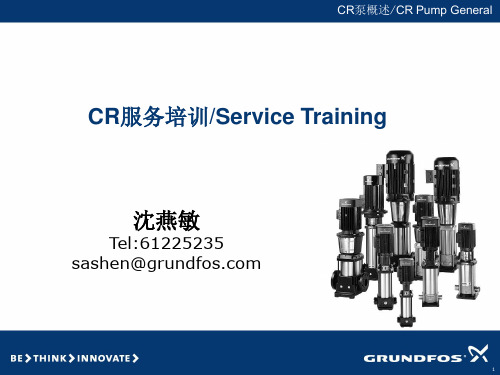
CR服务培训/Service Training
沈燕敏
Tel:61225235 sashen@
1
2
CR 泵性能曲线/CR Pump Performance Curve
3
铭 牌 说 明 — 电 机/Nameplate-Motor
电机的八位编码/P/NO.
产地/producing area
机封/Shaft seal type
水泵的八位编码/P/No. 生产日期/date
6
CR 泵 的 结 构/ Structure
CR10,15,20
CR32/45/64/90
CR1,3,5
7
CR120&CR150
8
CR 主要结构
电机: Grundfos MG & MGE 集装式轴封: 格兰富研制 连轴器
• • • • • • • 严格按照说明书安装/When installing the pump,the I/O must be follow strictly. 水泵的搬运、起吊和运输要按照产品的要求进行,以防意外 Pump’s carrying,lifting and transport should in accordance with the require. 注意水泵进出水的方向/Notice the direction of flow of liquid. 管路连接 /Connection 在与水泵连接前,管路内部和管端要清理干净/Before connection,pipework should be cleaned. 连接的密封面与螺纹不应损坏/The sealed surface of connection and screw thread should be intact. 管路连接时不允许有应力/Ensure the pump is not stressed by pipework. 3. 水泵就位 /Pump location
GPRO 燃油转移泵说明书

PRO35-115 & PRO35-115RD115/230 VoltPRO35-115AD Automatic Diesel Nozzle PRO35-115MD Manual Diesel Nozzle922108-01D11/14To the owner...Congratulations on receiving your GPRO™ Fuel Transfer Pump. We are pleased to provide you with a system designed to give you maximum reliability and efficiency.Your fuel pump is designed, tested, and approved for use with gasoline, kerosene, and diesel fuel. Please take all due pre-cautions when handling these flammable liquids. Your safety is important to us.Also, to assure the longest possible service life, it is important that you follow the operation and maintenance procedures outlined in this manual. We are proud to provide you with a quality product and dedicated support. Together with your conscientious use, we are sure that you will obtain years of safe, dependable service.Victor Lukic, President Great Plains Industries, Inc.TABLE OF CONTENTSGeneral Information ....................................................2Safety Instructions ......................................................2Installation ..................................................................2Operation ....................................................................4Troubleshooting ..........................................................5Illustrated Parts Drawing ............................................6Specifications .............................................................7Parts and Service .......................................................7Warranty .......................................................See InsertSAVE THESE INSTRUCTIONSOWNER'S MANUALYour pump is designed for use only with thin viscosity petroleum fuels such as gasoline (up to 15% alcohol blends such as E15), diesel fuel (up to 20% biodiesel blends such as B20) and kerosene. Do not use this pump for dispensing any fluids other than those for which it was designed. Using the pump with other fuels can damage components and void the warranty. Use of alcohol blends above 10% (E10) and biodiesel blends above 5% (B5) have not been reviewed by UL.Model ComponentsPRO35-115AD: Includes pump, hose and automatic diesel nozzle.PRO35-115MD: Includes pump, hose and manual diesel nozzle.PRO35-115PO: Includes pump only.PRO35-115RD: Includes dedicated pump only for remote dispensing systems.PRO35-115PO/XTS: Includes pump only and compo-nents to assemble to unit before use.NOTE: Suffixes MD, AD, PO and PO/XTS are for order-ing purposes only. Constructions described above are covered as alternate constructions under the Part No.PRO35 UL Listing.How to Use This ManualThe purpose of this manual is to assist you in installing, operating and maintaining your GPRO™ pump. If you need additional assistance, contact your GPRO dealer or the Great Plains Industries Customer Service Department.The following safety alert symbols are used inthis manual. Obey all safety messages that followthis symbol to avoid possible injury or death.DANGER indicates animminently hazardoussituation which, if not avoid-ed, will result in death orserious injury.WA R N I N G i n d i c a t e sa potentially hazardoussituation which, if not avoid-ed, could result in death orserious injury.C A U T I O N i n d i c a t e sa potentially hazardoussituation which, if not avoid-ed, may result in minor ormoderate injury.CAUTION CAUTION used withoutthe safety alert symbolindicates a potentiallyhazardous situation which,if not avoided, may result inproperty damage.There are inherent dangers wherever flammable fuel andAC electrical sources are in close proximity.Static electricity as a source of sparking is always aconcern and requires extreme care in the installation andoperation of your entire fuel transfer system.Additional components such as meters, automatic nozzlesand filters must be listed for use with fuel transfer systems.The flow of fuel through a hose and nozzle can generatestatic electrical charges and dangerous sparking canresult in fire or explosion. Hoses and nozzles must beelectrically conductive and bonded to ground.It is your responsibility to:• Know and follow applicable national, state and localsafety codes pertaining to installing and operatingelectrical equipment for use with flammable liquids.• Know and follow all safety precautions when handlingpetroleum fuels.•Ensure that all equipment operators have access toadequate instructions concerning safe operating andmaintenance procedures.INSTALLATIONMechanical ConnectionsCoverplates protect the operator from moving parts. Neveroperate the pump without coverplates in place. Never applyelectric power to the pump without coverplates in place.Always disconnect power before repairing or servicing.WARNINGAll threaded fuel connections must be sealed with threadtape or a pipe thread sealing compound approved foruse with petroleum fuels.Your pump must be mounted on a vented tank. If thetank is not vented, contact your GPRO distributor forthe correct vent cap.This pump has a built-in check valve to keep the pumpprimed. No additional check valve is required on suctionpipes shorter than 15 ft. (4.6 m). Make sure any checkvalves or foot valves used are equipped with properpressure relief valves.Your pump is designed to mount directly to a standard2 in. female tank fitting. For the suction pipe, a 1¼ in.galvanized steel pipe cut to length and threaded on oneend may be used. Suction pipe should extend to within3 inches of tank bottom. Apply thread tape to the suc-tion pipe thread and securely tighten the suction pipe tothe tank adapter. Once suction pipe is attached to tankadapter, insert suction pipe into tank and tighten tankadapter to tank fitting.2922108-01D PRO35-115 / PRO35-115RDInstall Nozzle Hanger(Not applicable to pumps with -RD suffix) Attention: The nozzle hanger for your pump was removedbefore shipping to protect against damage.To reinstall the nozzle hanger follow the steps below. 1. Remove the two ¼"-20 x ½" bolts and the two flatwashers from the switch coverplate.2. Place the two bolts through the nozzle cover and thenplace the two flat washers on the bolts. The washers are used as spacers to set the nozzle hanger away from the switch coverplate.3. Align the bolts with the two threaded holes on theswitch coverplate; thread the bolts into the holes.Torque bolts to 45-60 in/lb (Figure 1).Switch Locking LeverAttention: The PRO35-115RD remote dispenser pump incorporates an external switch locking lever that locks the pump switch in the “ON” position. The pump is typically shut off using the remote dispensing device “ON-OFF” mechanism.Electrical ConnectionsElectrical wiring and connections must be made only by a licensed electrician in accordance with national, state and local electrical codes regarding Class I, Division 1, Group D locations. Other codes may apply.Thread for the conduit connection at the pump electrical box is ½ in. FNPT.A standard 15-amp breaker is recommended.This pump is equipped with an auxiliary AC accessorylead. The third wire (red) is to be used to energize a control circuit that operates a device such as a signal light or a solenoid operated valve. Maximum amp draw on the control circuit is 1 amp. If you do not need this feature, ensure that the wire is insulated and enclosed within the electrical cavity of the pump.Wiring Details1. Remove electrical coverplate (Figure 2). Install con-duit and cable from switchbox to pump electrical box.Wiring must be in accordance with Class I, Division 1 requirements in the applicable national electrical code.2. Attach ground wire using the green ground screw lo-cated inside the electrical box (Figure 3). Connect the power cable to the pump wiring per the wiring diagram located inside the electrical coverplate. Secure with wire nuts.3. Position wires inside the electrical box. Replaceelectrical coverplate with all seven screws and tighten securely.3922108-01D PRO35-115 / PRO35-115RDTo dispense fuel (for pumps with nozzlehanger):1. Remove the nozzle from the holder. Turn the pumpon by pulling the switch lever down.2. Insert the nozzle into the receiving tank and squeezethe handle to dispense fuel.3. After dispensing fuel, push the switch lever up to turnthe pump off and return the nozzle to the holder. Thenozzle may be locked in place to prevent unauthorizeduse.The pump contains an automatic bypass valve to preventpressure buildup when the pump is on but the nozzleis closed. Do not leave the pump on for more than 10minutes with the nozzle closed.Never leave the pump running without fluid. Dry runningcan damage the pump components.The pump has a duty cycle of 30 minutes ON and 30minutes OFF. Do not overheat. Allow the motor to coolthe same length of time it was in operation.The fuel strainer and check valve assembly should becleaned on a regular basis or if low flowrate is noticed.If the pump becomes too hot, an internal temperature-limiting device will automatically shut the motor off andprevent operation until it cools.4922108-01D PRO35-115 / PRO35-115RDSYMPTOM PROBABLE CAUSE CORRECTIVE ACTIONA. MOTOR DOESNOT RUN 1. No electrical power to pump Check breaker, switchbox and wiring.2. Auxiliary temperature-limitingdevice trippedAllow motor to cool. Auxiliary temperature-limiting device will automati-cally reset.3. Rotor or vanes jammed Remove coverplate and check for damage or obstruction.B. MOTOR RUNSBUT DOES NOTPUMP FLUID 1. Tank level low Add fuel to tank.2. Clogged filter assembly Remove and clean filter assembly.3. Clogged or broken suction pipe Remove pump and clear suction pipe, replace as needed.4. Broken shaft key Replace shaft key. Check rotor or vanes for obstructionC. PUMP FAILS TOPRIME 1. Air leak in system Check for air leaks at all joints2. Bypass valve stuck open Remove bypass valve and clean or replace as needed.3. Check valve stuck open Remove check valve and clean or replace as needed.4. Rotor or vanes worn Check rotor and vanes for excessive wear.D. LOW FLOWRATE 1. Low voltage Check incoming line voltage.2. Clogged filter assembly Clean filter assembly.3. Air leak in system Check for air leaks at all joints.4. Bypass valve stuck open Remove bypass valve and clean or replace as needed.5. Rotor or vanes worn Check rotor and vanes for excessive wear.6. Outlet is blocked Check all accessories for blockage.7. Clogged or broken suction pipe Remove pump and clear suction pipe, replace as needed.D. MOTOR STALLSWHEN NOZZLE ISCLOSED 1. Bypass valve stuck closed Remove bypass valve and clean or replace as needed.2. Rotor or vanes worn Check rotor and vanes for excessive wear.3. Low voltage Check incoming line voltage.B. FUEL LEAKAGE 1. Threaded joint loose Check and reseal threaded joint.2. Insufficient bolt torque Retighten bolts.3. Lost or damaged O-rings Check O-rings for damage. Replace as needed.4. Shaft seal worn or damaged Fuel leaking from drain hole indicates shaft seal needs to be replaced.D. MOTOROVERHEATS 1. Pumping high viscosity fluids Pump only low viscosity fluids2. Clogged filter assembly Clean filter assembly.3. Clogged or broken suction pipe Remove pump and clear suction pipe, replace as needed.5922108-01D PRO35-115 / PRO35-115RD6922108-01D PRO35-115 / PRO35-115RDKits and Accessories133502-1 Vane Kit – O-Ring, 2 in. vanes, shaft key 133503-1Shaft Seal Kit – Retaining ring, shaft seal, spacer washer133503-05 Shaft Seal Kit, Extreme Temperature Series 133504-1Seal Kit121013-503Check Valve Assembly Kit504500-04 Spares, Base Assembly, 2" Inlet 504500-02 Kit, Switch, PRO35-115 / PRO95-230504500-03 Vacuum Breaker Kit150100-502 Fuel Hose, Extreme Temperature Series, 1" NPTx 1" x 18'906009-505 Automatic Diesel Nozzle, Extreme TemperatureSeries, 1" NPT, UL7922108-01D PRO35-115 / PRO35-115RDThe PRO35 series fuel pump is designed to safely trans-fer low viscosity petroleum fuels such as gasoline (up to 15% alcohol blends such as E15), diesel fuel (up to 20% biodiesel blends such as B20) and kerosene. The pump is designed for permanent mounting on vented storage tanks, either in-ground or above-ground. RAINPROOF for outdoor use. Use of alcohol blends above 10% (E10) and biodiesel blends above 5% (B5) have not been reviewed by UL.Performance Pump Rate: Up to 35 GPM (132 LPM) Duty Cycle: 30 minutes ON, 30 minutes OFF Dry Prime:15 ft. (4.6 m) maximumDischarge Lift: 10 ft. (3 m) maximum Operating Temperature-20° F to +125° F (-29° C to +52° C)XTS Operating Temperature Extreme T emperature Series pumps are capableof operation down to -40° F. A ny pump operation below -20° F has not been evaluated by UL.Bypass Pressure25 PSI ElectricalInput: Factory set at 115 VAC, 60 Hz. Optional to set at 230 VAC, 60 Hz.Conduit:½ in. FNPTCurrent Draw: 9.8 amps at full load (at 115 VAC, 60Hz)Motor:¾ HP, 1725 RPM induction type provided with an internal auxiliary temperature-limiting device Mechanical Connections Bung: 2 in. MNPT Inlet: 1 ¼ in. FNPT Outlet: 1 in. FNPTAccessories Hose: 1 in. NPT x 1 in. x 18 ft. (5.5m) Buna-N electrically conductiveNozzle: 1 in. NPT manual or 1 in. NPT auto-matic dieselSecurity: Nozzle can be padlocked Ship WeightPRO35-115PO 67.0 lbs (30.4 kg) PRO35-115MD 78.0 lbs (35.4 kg) PRO35-115AD 80.2 lbs (36.4 kg) PRO35-115RD65.1 lbs (29.5 kg)SAVE THESE INSTRUCTIONSIn order to preserve the UL Listing for pump safety, return the entire pump to the factory for repair or replacement. For products serviced outside the factory, the UL name-plates must be defaced to indicate that the equipment may no longer meet the requirements for UL Listing. This does not apply to products serviced outside the factory under the UL program for Rebuilt Motors for Use in Hazardous Locations.For warranty consideration, parts, or other service infor-mation, please contact your local distributor. If you need further assistance, contact the Great Plains Industries Customer Service Department in Wichita, Kansas, during normal business hours.800-835-0113 or 316-686-7361To obtain prompt, efficient service, always be prepared with the following information:1. The model number of your pump.2. The manufacturing date code of your pump.For the PRO35 series, the date code is located on the motor nameplate.For warranty work, always be prepared with your original sales slip or other evidence of purchase date.Please contact Great Plains Industries before returning any pump. It may be possible to diagnose the trouble and find a solution with a telephone call. Great Plains Industries can also inform you of any special requirements you will need to follow for shipping.POWER OPERATED PUMP FOR PETROLEUMPRODUCTSMOTOR FORHAZARDOUS LOCATIONSCertified Motor© 2014 Great Plains Industries, Inc. All Rights Reserved. Made in U.S.A. and GPRO TM are trademarks,and the electric gear pump design is a registered trademark of Great Plains Industries, Inc.11/14922108-01D。
POSTURE PRO Posture Pump 产品说明书

Copyright 2015POSTURE PRO, Inc. • 16421 Gothard St., Ste. D, Huntington Beach, CA 92647 • U.S. Patent Numbers 5,713,841 • 5,906,586. • D508,566S • 7,060,085,B2• 8,029,453,B2 • 8,734,372 • 8,764,693Other patents pending.Consult your health care professional before beginning.Prices and colors subject to change without notice. Posture Pump ®products are not designed to diagnose or cure disease.Posture Pump ® is a serious spinal health product recommended by doctors to thousands of patients throughout the USA and othercountries. It is not a massage device or an “occasional use” product! Keep Posture Pump ® on your bed, night stand or a place where you can USE IT OFTEN. Take it with you on trips. Just minutes on the Posture Pump ® will reinforce your neck and back’s NATURAL CURVED SHAPE, LUBRICATE THE JOINTS and PROMOTE PROPER POSTURE.During the first week, as the natural shape of your neck and back is strengthened, you may experience normal discomfort and soreness. As with any new exercise, THIS IS NORMAL. Skip a few days if you must, but STICK WITH IT! DON’T QUIT! Think of Posture Pump ® as you would your tooth-brush. Just as your toothbrush protects your teeth, let Posture Pump ® strengthen and lubricate your neck and back. Like working oil into a rusty hinge,use Posture Pump ® after long periods of holding your head, neck and back in uncomfortable positions. Many use it just before bedtime to relieve head,neck and back discomfort, stiffness, stress and to fall asleep easier.Posture Pump ®Disc Hydrator ®InstructionsStop! Read This First!”Telephone Neck”Be Flexible! . . . Stand Taller! . . . Look & Feel Younger!Pick Your Posture6 months manufacturer warranty with proof of purchase.Nothing works like Posture Pump ®. Nothing!Arrow from ear canal should line up with center of shoulder.Check yours!Help Prevent the Hump with Posture Pump ® and Avoid Stooped Posture as you age.Use Posture Pump ® regularly as directed and carefully follow directions and cautions .1Revisions 12-22-14Call Posture Pro, Inc, 1-800-632-5776 (USA) or (714) 847-8607 for questions *********************“Computer Neck”Forward Head Carriage: The most common cause of neck and upper back fatigue and tension.Driving Stress:Low back, middle back and neck tension and stiffness.Forward-Flexed Neck Positions: Force the natural curve out of the neck and promote poor posture.Side-Flexed Neck Positions:Cause stiffness and spasm.Shoulder andUpper Back Tension1.After warm-up routine, place deflated unit on a com-fortable, firm surface.Deflate air cell(s) by pushing the button on the pump and squeezing air cell(s).With Comfort Visor TM forehead restraintuntangled at back of unit, slide and center unit under the back of your neck, snugly against your shoulders and upper back.*WARM-UP ROUTINEBegin by slowly turning the head side-to-side 5 times; then tilting the head forward and backward 5 times; then leaning the neck from side-to-side 5 times.2.Center your neckon neck cradle measuring with your index fingers. (see illustration)*4.Hold back of unit down with tips of index fingers or thumbs and further tighten Comfort Vi-sor TM if necessary. (see illustration above)5.Press ends of Comfort Visor TM straps across the Velcro ®forehead section. Comfort Visor TM should be as snug as possible without lifting up the back of the unit and may be tightened further after the first repetition. (Back of frame may lift slightly during application on some surfaces,THIS IS NORMAL .)Instructions for Posture Pump ®Disc Hydrator ®Models 1100-S, 1100-SX and 1400-D Dual Disc Hydrator ®Posture Pump ®Models 1100-S, 1100-SX and 1400-D Dual Disc Hydrator ®WARRANTY: 6 MONTH WARRANTY FROM DATE OF PURCHASE PROVIDED BY MANUFACTURERTo contact Posture Pro, Inc, call 1-800-632-5776 (USA) or (714) 847-8607 Fax (714) 375-4183 •*********************Q:My muscles were sore a day or two after my PosturePump ®session. Is this normal?A:Just like performing any new exercise, an aggressive workoutwith Posture Pump ®can temporarily make you sore. To reduce this occurrence, inflate the unit at lower levels and keep your ses-sions under 10-minutes for the first 2 weeks. This will allow your body to gradually adapt to more aggressive sessions.INSTRUCTIONSAir Cell Positional AdjustmentsUpper Air Cell:Air cell should be centered to expand straight up un-less otherwise recommended by your healthcare professional.To adjust unoccupied air cell: Fully inflate air cell, forcefully CENTER or tilt completely in the desired direction, HOLD and deflate fully. Air cell is now repositioned. Apply as directed.Model 1400-D Lower Air Cell:This air cell can be adjusted by your healthcare professional forward and up with a Rotating-Wedge-Com-ponent as well as unilaterally forward on right or left side to perform spe-cial functions. (Consult your healthcare professional)Rotating-Wedge-Component:This component is not necessary for standard operation but if so equipped, should be in the neutral position (wide side of wedge down ), and should only be adjusted to a horizon-tal position by your Healthcare Professional.Copyright 2015 POSTURE PRO, Inc. • 16421 Gothard St., Ste. D, Huntington Beach, CA 92647 • U.S. Patent Numbers 5,713,841 • 5,906,586. • D508,566S • 7,060,085,B2• 8,029,453,B2 • 8,734,372 • 8,764,693Other patents pending.Consult your health care professional before beginning.Prices and colors subject to change without notice. Posture Pump ®products are not designed to diagnose or cure disease.CAUTIONS – Apply to all Posture Pump ®Products3.Apply Comfort Visor TM by centering it across your forehead.While holding it there with fingers, lightly tighten one side at a time until snug and centered. Allow it to slide back toward hairline as you pull all slack out of Comfort Visor TM ends equally while holding frame down with fingers. Comfort Visor TM will mold to the shape of your forehead as it slides back.Reposition until it feels secure and comfortable. (see illustrations) Note: For smaller heads and shorter necks locate Comfort Visor TM in forward slots. For larger size locate Comfort Visor TM in back slots.8.Next, inflate unit to a comfortable level (never to the point of pain) and relax on inflated unit for 1 to 5 minutes on first session . Gradually work up to a maximum goal of 15 minutes by adding a few minutes to each session or as directed by your healthcare professional. Inflate unit at lower levels the first week, thus reducing soreness commonly caused by aggressive usage.pletely deflate unit, release Velcro ®straps from forehead and remove Comfort Visor TM . Roll off unit to your right or left side slowly and carefully without turning your head. When you are free from the unit and standing or sitting in an upright position,gently and slowly repeat warm-up routine to acclimate your neck muscles to the weight of your head.10.Keep unit near bed or night stand and repeat the above treatment as recommended by your healthcare provider. Keep unit out of the reach of children at all times.*If you are not snug, comfortable and centered on the inflated bladder, or if it seems to inflate unevenly, release the air, then the restraint, center yourself on unit and reapply restraint.6.Slowly pump unit up to your own comfort level; never to the point of pain.Model 1100-S usually 1 to 7 complete pumps; Model 1100-SX between 1 –9complete pumps; Model 1400-D Dual Disc Hy-drator ®usually 2 to 12 complete pumps. Pump less times during first week of use. (Pump is equipped with automatic air release valve, limit-ing inflation.) Never cover up or block off open ends of hand pump.7.Wait approximately 10 seconds; then release all air by pushing the manual air release button on the pump. Repeat approximately 10to15times.IMPORTANT:Posture Pump ®is proven in MRI and x-ray studies to provide high level disc expansion and spinal shaping. We recommendthat it be used with the guidance of a healthcare professional. If the user tolerates the selected unit then user is to carefully follow cautions and instructions below.1.Read instructions completely before using and follow all cautions.2.Do not use this unit without first consulting your doctor. Specific joint, nerve, disc, vascular and other disorders or weaknesses can be aggravated and worsened.3.Do not use if you have implanted spinal hardware.4.Do not use if you are pregnant.5.Do not use if you are injured.6.Never inflate unit to the point of pain.7.Never cover up or block off open ends of hand pump (Safety Release Valve).8.Never reposition your body when neck unit is inflated! When using neck unit and back unit together, always apply the back unit first . When all movement with back unit is complete,apply neck unit. Completely deflate neck unit and release head restraint before moving back unit.9.If Comfort Visor TM restraint is slipping off forehead, lightly moisten inside padded area to help it adhere & mold to the shape of your head.10.If pain results during treatment, discontinue use immediately and consult your doctor.11.If your back is sensitive or extremely stiff, first use the unit on your bed/mattress.As your flexibility increases, you may wish to graduate to a flat, firm surface.12. An aggressive workout with the Posture Pump ®may temporarily cause soreness.If so, reduce the intensity and duration of your treatment.13.Keep unit out of the reach of children at all times.2。
- 1、下载文档前请自行甄别文档内容的完整性,平台不提供额外的编辑、内容补充、找答案等附加服务。
- 2、"仅部分预览"的文档,不可在线预览部分如存在完整性等问题,可反馈申请退款(可完整预览的文档不适用该条件!)。
- 3、如文档侵犯您的权益,请联系客服反馈,我们会尽快为您处理(人工客服工作时间:9:00-18:30)。
5.1
A- SYSTEM & EXTRUDER PUMPS – FE1 ~ Master No. 1 Step #4 –System Pressure Input Command
Prior to completing any of the next steps please ensure that the following system checks have been completed:
• Pumps are NOT in Unload mode.
Please assure a minimum of 15 bar is available to the pump at all times to maintain proper lubrication to the rotary group components
Number: BFB-A04-135 Issue: Dec 2003 –RV1 Replaces: New
A- SYSTEM & EXTRUDER PUMPS – FE1 ~ Master No. 1 Step #4 – Setting Maximum System Pressure
a) Verify the flow command signal measured at test point PIN 3. 3PQ = Extruder pump of - 2.0V 5PQ = System pump of -10V Note: the voltage polarity should be negative.
a) Verify pressure command at test point PIN 1 on Master System Pump Card. (see chart below)
Note: All voltage polarities should be positive.
MTM LTM
New Standard
locked.
Page 2 of 6
Field Bulletin
G-Line PET Machines Rexroth Pump Set-up Procedures
Number: BFB-A04-135 Issue: Dec 2003 –RV1 Replaces: New
A- SYSTEM & EXTRUDER PUMPS – FE1 ~ Master No. 1 Step #3 – Maximum Swash plate Angle Calibration with E-motor OFF
Voltage
(Volts) (-0.1v)
+8.0 +7.4 +10.0 +7.4 +7.2
(Bar)
182 185 250 185 180
Pressure
(PSI)
2640 2683 3626 2683 2611
Page 3 of 6
Field Bulletin
G-Line PET Machines Rexroth Pump Set-up Procedures
**This procedure applies to Extruder pumps only for these models**
A- SYSTEM & EXTRUDER PUMPS – FE1 ~ Master No. 1 Step #1 – Confirm All Jumper Settings
(See reference 5.1 chart specific to machine model.)
PIN 1
=
PIN 2
Reference Ground
Reference Ground
(PIN 7 &8)
(PIN 7 &8)
(*± 0.1V tolerance measurement between Pins 1&2* )
Bosch Rexroth Canada Corp.
Field Bulletin
Number: Issue: Replaces:
BFB-A04-135 Dec 2003 – RV1 New
Husky G-Line PET Machines Rexroth Pump Set-up Procedures
1b) Proceed to adjust R9 to 9.9 V (+/-0.1V) at PIN 4 with a
flow command input value from HMI of -10V measured at PIN 3 Note: Please assure pumps are out of oil warming
A- SYSTEM & EXTRUDER PUMPS – FE1 ~ Master No. 1 Step #2 – Setting System Pump Pressure with E-motor OFF
This calibration must be performed on both the System & Extruder master VT Cards.
4.2
For A4VFE1 PUMPS:
a) Visually verify swash plate angle position as shown on top dial indicator. If the swash plate angle appears to be
15° then measure 8 to 10 Volts at test point PIN4.
b) Using a pressure gauge (0-3000psi) on the system / extruder pump pressure port, adjust R2 until the specified pressure is obtained.
System GPS2 = 2610 (+/-25)psi (180 bar) Extruder GPE2= 2660 (+/-25)psi (183 bar)
ON ON ON OFF OFF OFF
2
Amplification Setting Oil Volume
A4V
With Dampeners Without Dampeners
J1 J2 J11 J3 J4 J5 OFF OFF ON ON ON ON
OFF OFF ON OFF OFF OFF
Note: Jumper J9 – remains ON, Jumper J10- remains OFF Jumper J6,J7 & J8 remains OFF (0-10V input)
system side 58-87psi (4-6 bar).
Note: Do not exceed 100psi (6.9 bar) as to avoid extruder circuit relief from cracking open and
causing an overheating condition
d) Please verify system pressure again and adjust R2 if
required.
e) MTM machine w/o pulsation dampener on pump outlet:
Please offset extruder pressure set point higher than
5.2
Note; adjust clockwise to decrease set pressure
c) Adjust R6 to match the pressure feedback value
measured (at PIN 2) to the set input value (at PIN 1).
VT5041 Series 25 Amplifier Card:
Verify that all pumps have the following jumper settings:
A10V
J1 J2 J11 J3 J4 J5
With Dampeners ON ON ON ON ON ON
Without Dampeners
A- SYSTEM & EXTRUDER PUMPS – FE1 ~ Master No. 1 Step #5 – Setting Minimum Swash plate Angle
Note: This step must be completed within 10 (ten) minutes for
• E-motor running • Out of “oil warming” mode. • All dump valves are closed. • No actuators are moving (drifting). • Relief valves are energized [MTM: Y4DP]
( Reference ground at PIN7&8 )
b) Adjust R9 to +9.9V +/- 0.1 V set value
1a) If less than 15° then start the E-motor with pumps unloaded via the removal of the associated electrical connector. Y1DP = Extruder Y4DP = System
*Note: FE1D Electronic flow & Mechanical pressure control without pressure transducer is used on earlier G line machines *