GB汽车和挂车-制动器用零部件技术要求及试验方法-编制说明
1-汽车强制性标准内容简介
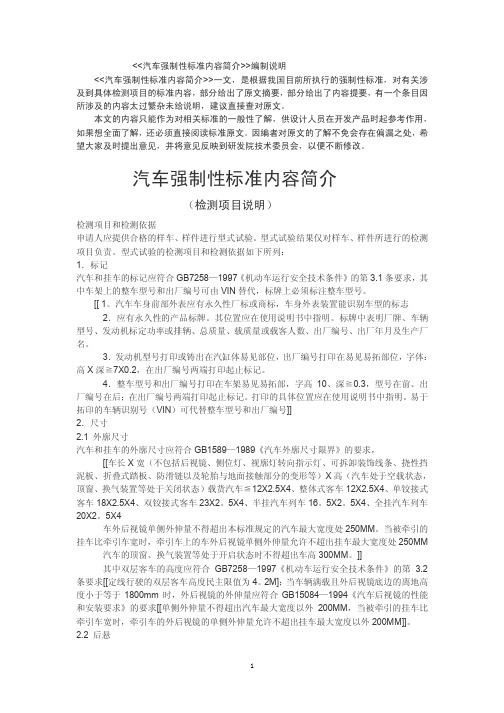
<<汽车强制性标准内容简介>>编制说明<<汽车强制性标准内容简介>>一文,是根据我国目前所执行的强制性标准,对有关涉及到具体检测项目的标准内容,部分给出了原文摘要,部分给出了内容提要,有一个条目因所涉及的内容太过繁杂未给说明,建议直接查对原文。
本文的内容只能作为对相关标准的一般性了解,供设计人员在开发产品时起参考作用,如果想全面了解,还必须直接阅读标准原文。
因编者对原文的了解不免会存在偏漏之处,希望大家及时提出意见,并将意见反映到研发院技术委员会,以便不断修改。
汽车强制性标准内容简介(检测项目说明)检测项目和检测依据申请人应提供合格的样车、样件进行型式试验。
型式试验结果仅对样车、样件所进行的检测项目负责。
型式试验的检测项目和检测依据如下所列:1.标记汽车和挂车的标记应符合GB7258—1997《机动车运行安全技术条件》的第3.1条要求,其中车架上的整车型号和出厂编号可由VIN替代,标牌上必须标注整车型号。
[[ 1。
汽车车身前部外表应有永久性厂标或商标,车身外表装置能识别车型的标志2.应有永久性的产品标牌。
其位置应在使用说明书中指明。
标牌中表明厂牌、车辆型号、发动机标定功率或排辆、总质量、载质量或载客人数、出厂编号、出厂年月及生产厂名。
3.发动机型号打印或铸出在汽缸体易见部位,出厂编号打印在易见易拓部位,字体:高X深≧7X0.2,在出厂编号两端打印起止标记。
4.整车型号和出厂编号打印在车架易见易拓部,字高10、深≧0.3,型号在前、出厂编号在后;在出厂编号两端打印起止标记。
打印的具体位置应在使用说明书中指明。
易于拓印的车辆识别号(VIN)可代替整车型号和出厂编号]]2.尺寸2.1 外廓尺寸汽车和挂车的外廓尺寸应符合GB1589—1989《汽车外廓尺寸限界》的要求,[[车长X宽(不包括后视镜、侧位灯、视廓灯转向指示灯、可拆卸装饰线条、挠性挡泥板、折叠式踏板、防滑链以及轮胎与地面接触部分的变形等)X高(汽车处于空载状态,顶窗、换气装置等处于关闭状态)载货汽车≦12X2.5X4、整体式客车12X2.5X4、单铰接式客车18X2.5X4、双铰接式客车23X2。
-汽车防抱制动系统性能要求和试验方法【国标】
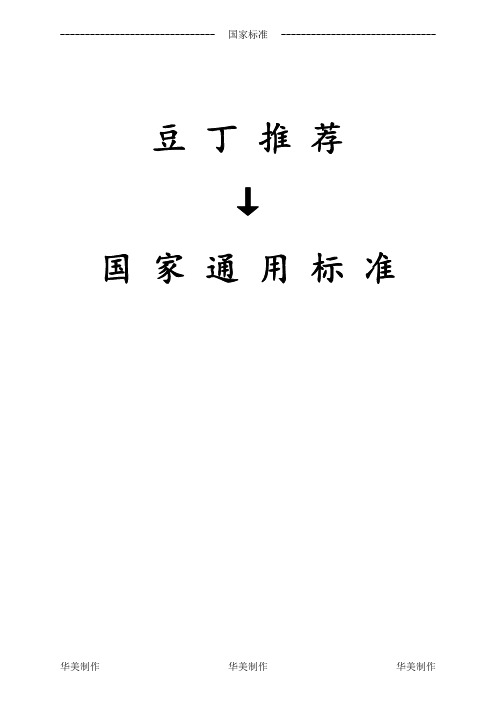
中华人民共和国国家标准
汽车防抱制动系统性能要求和试验方法
Ve hic le sa nt i-lockb rakings ystems performancer equirementsa ndt estp rocedures
GB 13594一 92
本标准参照采用ECE/R13附件 13《带防抱装置的车辆的试验要求》。
c. 测 制 动因数 ZFs和 Z。方法参服 6.5-4.3;
d 按 下 式确定附着系数利用率(E)
对 于 前 轴 :
Zm ·Fm一 0.0 15F m2
E,= ,一 ,
H- , 、
人(Pm ‘十了GFH’`'.1
… … 。.。。.。… … 。二。·。二。… (6)
对于后轴 :
鱼
EZ =
Z- .F。一 0.01 rm)
L— 轴 距 ,m 。 6.5-4.3 确定附着系数利用率(E)试验
8. 装 有 一、二类防抱系统的车辆,确定 K值后,在同一路面上立即做试验确定(E); b 重 新 联接好防抱系统,使各轴制动器正常工作; c. 促 动 管路压力为厂定值上限; d. 车 辆 初速度为 50k m/h,在相应路面上进行制动; e. 测 量 车速从 40k m/h减速到 20k m/h所经历的时间“t"(s); f. 装 防 抱系统车辆的制动因数(Z-)按(3)式确定。 B. 重 复 上述试验三次,求出Z-的算数平均值 乙。
GB18565-2015《道路运输车辆综合性能要求和检验方法》
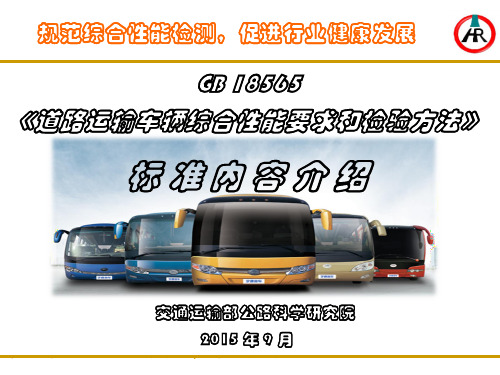
用车型要求、性能、尺寸、位置应符合GB 7258的相关要求, 且完好、无污损。
交通运输部公路科学研究院汽车运输技术研究中心
三、标准变化及要点
交通运输部公路科学研究院汽车运输技术研究中心
三、标准变化及要点
6、行驶系 ▲车架▲车桥▲拉杆和导杆▲车轮及螺栓、螺母▲减振器 ▲悬架
▲轮胎 (1)轮胎的胎冠、胎壁不得有长度超过25mm或深度足以 暴露出帘布层的破裂和割伤以及凸起、异物刺入等影响使用 的缺陷,并装轮胎间应无异物嵌入。 (2)具有磨损标志的轮胎,胎冠的磨损不得触及磨损标 志;无磨损标志或标志不清的轮胎,乘用车和挂车的胎冠花 纹深度应不小于1.6mm;其它车型的转向轮的胎冠花纹深度 应不小于3.2mm,其余轮胎胎纹深度应不小于1.6mm。
交通运输部公路科学研究院汽车运输技术研究中心
三、标准变化及要点
螺栓残缺不全
交通运输部公路科学研究院汽车运输技术研究中心
三、标准变化及要点
交通运输部公路科学研究院汽车运输技术研究中心
三、标准变化及要点
▲ 悬架 (1)弹性元件
悬架的弹性元件,如钢板弹簧、螺旋弹簧、扭杆弹簧、 橡胶减震垫等弹性元件应安装牢固,不应有裂纹、缺片、加 片、断裂、塑性变形和功能失效等现象,空气弹簧不应有泄 漏现象。 (2)部件连接
心处的向心加速度达到0.35g时,车辆不发生侧翻或侧滑,危险 货物运输专用车辆以及罐式车辆应达到0.4g。
交通运输部公路科学研究院汽车运输技术研究中心
商用车辆和挂车制动系统技术要求及试验方法

商用车辆和挂车制动系统技术要求及试验方法本文介绍了商用车辆和挂车制动系统技术要求及试验方法。
文章从制动系统的基本组成和工作原理入手,详细介绍了制动器、制动阀、制动管路等关键部件的技术要求。
同时,针对商用车辆和挂车在不同工况下的制动性能要求,对制动系统的性能指标进行了详细阐述,包括制动距离、制动力、制动平衡等。
最后,文章还介绍了商用车辆和挂车制动系统的试验方法,包括静态试验、动态试验、紧急制动试验等。
这些试验方法可以有效评估制动系统的安全性能和可靠性,为制造商和用户提供重要的参考依据。
- 1 -。
GB7258-2017宣贯材料
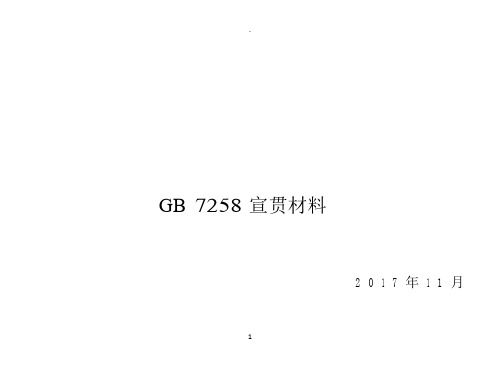
.GB 7258 宣贯材料2017年11月1GB 7258标准的范围进口商检3GB 7258标准修订原因⏹公路客车和旅游客车还存在客货混装等违规情况,安全技术要求仍偏低,公交车的防火安全性和乘员逃生便捷性的要求不足⏹货车的交通事故问题仍比较突出,重中型载货汽车、危险货物运输车辆的安全配置偏低,半挂汽车列车的主挂车制动不匹配⏹新能源汽车、旅居车辆等新兴车辆的安全技术要求缺失⏹与其他国家标准相协调,如:车辆外廓尺寸(GB1589)术语和定义《中华人民共和国道路交通安全法》第五十七条中的“全挂拖斗车”仅指牵引杆挂车列车(全挂汽车列车),不包括中置轴挂车列车。
中置轴挂车列车可以上高速公路行驶。
对于国产货车和挂车,只有车辆名称上能体现危险货物运输的车型(如:运油车),或《公告》、《机动车整车出厂合格证》上注明“适用于危险货物运输”的车型才允许申请“危化品运输”使用性质整车标志、VI N⏹ 4.1条是对机动车整车标志的规定。
与GB7258—2012相比做了如下修改:为了防止在用机动车替换原车商标/厂标而导致群众错误辨识车型明确规定车身前部外表面装置的商标/厂标应与车辆品牌相适应; 对机动车产品标牌,特别是应标示的内容根据车辆产品的实际状况和管理需求适当进行了调整;进一步规范了车辆识别代号的打刻要求,严格了总质量大于等于12000kg的货车、货车底盘改装的专项作业车及所有牵引杆挂车的车辆识别代号打刻位置要求,增加了部分重型货车、挂车还应在其货箱或常压罐体上打刻至少两个车辆识别代号的要求;35整车标志⏹商标和厂标“车身前部”是指“车身长度二分之一以前的部位”,并非指车身正前方;“永久保持”的意思是指“商标或厂标应以焊接等非经破坏性操作不能卸除的方式固定在车辆上”;“商标”是指“车辆制造厂家的商标或车辆产品品牌的商标”;“厂标”则是指“车辆制造厂家的代表标志”改装车—《汽车产品外部标识管理办法》规定“采用外购底盘的专用车应保留原底盘的商品商标、生产企业名称等,同时还应标注专用车生产企业的名称、商品商标、车型名称等信息。
编制说明-商用车制动系统技术要求及试验方法
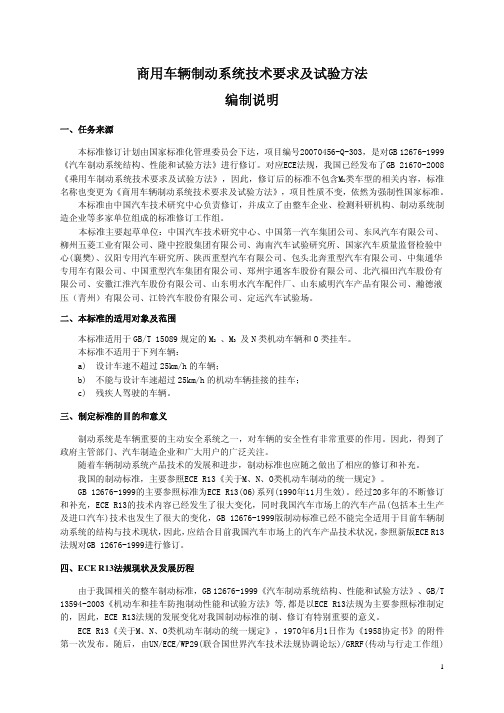
商用车辆制动系统技术要求及试验方法编制说明一、任务来源本标准修订计划由国家标准化管理委员会下达,项目编号20070456-Q-303,是对GB 12676-1999《汽车制动系统结构、性能和试验方法》进行修订。
对应ECE法规,我国已经发布了GB 21670-2008《乘用车制动系统技术要求及试验方法》,因此,修订后的标准不包含M1类车型的相关内容,标准名称也变更为《商用车辆制动系统技术要求及试验方法》,项目性质不变,依然为强制性国家标准。
本标准由中国汽车技术研究中心负责修订,并成立了由整车企业、检测科研机构、制动系统制造企业等多家单位组成的标准修订工作组。
本标准主要起草单位:中国汽车技术研究中心、中国第一汽车集团公司、东风汽车有限公司、柳州五菱工业有限公司、隆中控股集团有限公司、海南汽车试验研究所、国家汽车质量监督检验中心(襄樊)、汉阳专用汽车研究所、陕西重型汽车有限公司、包头北奔重型汽车有限公司、中集通华专用车有限公司、中国重型汽车集团有限公司、郑州宇通客车股份有限公司、北汽福田汽车股份有限公司、安徽江淮汽车股份有限公司、山东明水汽车配件厂、山东威明汽车产品有限公司、瀚德液压(青州)有限公司、江铃汽车股份有限公司、定远汽车试验场。
二、本标准的适用对象及范围本标准适用于GB/T 15089规定的M2 、M3 及N类机动车辆和O类挂车。
本标准不适用于下列车辆:a)设计车速不超过25km/h的车辆;b)不能与设计车速超过25km/h的机动车辆挂接的挂车;c)残疾人驾驶的车辆。
三、制定标准的目的和意义制动系统是车辆重要的主动安全系统之一,对车辆的安全性有非常重要的作用。
因此,得到了政府主管部门、汽车制造企业和广大用户的广泛关注。
随着车辆制动系统产品技术的发展和进步,制动标准也应随之做出了相应的修订和补充。
我国的制动标准,主要参照ECE R13《关于M、N、O类机动车制动的统一规定》。
GB 12676-1999的主要参照标准为ECE R13(06)系列(1990年11月生效)。
货运挂车气压制动系统技术要求和试验方法
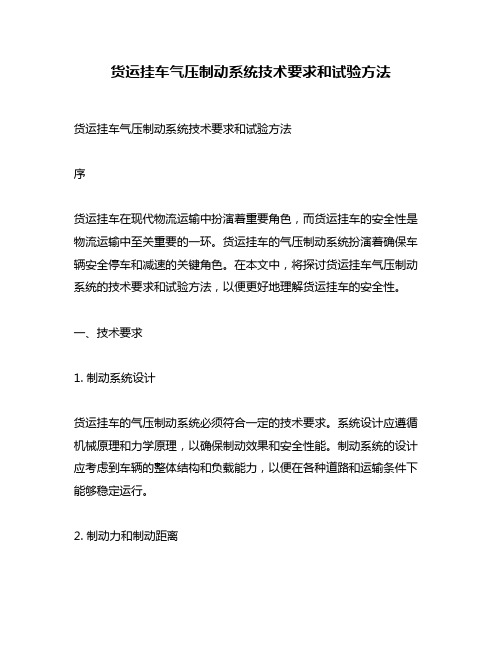
货运挂车气压制动系统技术要求和试验方法货运挂车气压制动系统技术要求和试验方法序货运挂车在现代物流运输中扮演着重要角色,而货运挂车的安全性是物流运输中至关重要的一环。
货运挂车的气压制动系统扮演着确保车辆安全停车和减速的关键角色。
在本文中,将探讨货运挂车气压制动系统的技术要求和试验方法,以便更好地理解货运挂车的安全性。
一、技术要求1. 制动系统设计货运挂车的气压制动系统必须符合一定的技术要求。
系统设计应遵循机械原理和力学原理,以确保制动效果和安全性能。
制动系统的设计应考虑到车辆的整体结构和负载能力,以便在各种道路和运输条件下能够稳定运行。
2. 制动力和制动距离货运挂车的气压制动系统需要提供足够的制动力和合理的制动距离,以确保车辆在紧急情况下能够安全停车。
制动力主要取决于制动系统的设计和制动器的性能,而制动距离则取决于车辆的速度和路面情况。
3. 制动系统灵敏度货运挂车的气压制动系统应具有良好的灵敏度,以便驾驶员可以根据需要调整制动力。
制动系统的灵敏度取决于气压制动阀门和制动器的设计,同时还需要考虑到驾驶员的体力和反应能力。
4. 制动系统的可靠性和耐久性货运挂车的气压制动系统需要具备良好的可靠性和耐久性,以确保长时间、高频次的使用。
制动系统的各个部件和连接件应具备高强度和耐用性,以防止系统在使用过程中出现故障和损坏。
二、试验方法1. 制动性能试验为了评估货运挂车的气压制动系统的制动性能,可以进行制动力和制动距离的试验。
试验时,可以选取不同速度的车辆,在条件相同的情况下进行制动,并记录制动力和制动距离的数据。
通过对试验数据的分析,可以评估制动系统的性能是否符合技术要求。
2. 制动系统灵敏度试验为了评估货运挂车的气压制动系统的灵敏度,可以进行制动力的调整试验。
试验时,可以通过操纵气压制动阀门的方式,调整制动力的大小,并记录不同制动力下的制动距离和驾驶员的操控感受。
通过对试验结果的分析,可以评估制动系统的灵敏度是否符合技术要求。
《强制性产品认证实施规则 汽车用制动器衬片》(CNCA-C11-20_2020)

编号:CNCA-C11-20:2020强制性产品认证实施规则汽车用制动器衬片2020-05-29发布 2020-06-01 实施国家认证认可监督管理委员会发布目录0 引言 (1)1适用范围 (1)2认证依据标准 (1)3 认证模式 (1)4 认证单元划分 (2)5 认证委托 (2)5.1认证委托的提出与受理 (2)5.2申请资料 (3)5.3实施安排 (3)6 认证实施 (3)6.1型式试验 (3)6.1.1型式试验方案 (3)6.1.2型式试验样品要求 (3)6.1.3型式试验项目 (4)6.1.4型式试验的实施 (4)6.1.5型式试验报告 (4)6.2 初始工厂检查 (4)6.2.1基本原则 (4)6.2.2生产一致性控制计划审查 (5)6.2.3生产一致性工厂现场检查 (5)6.3 认证评价与决定 (5)7 获证后监督 (6)7.1获证后的跟踪检查 (6)7.1.1获证后的跟踪检查原则 (6)7.1.2获证后的跟踪检查内容 (6)7.2生产现场抽取样品检测或者检查 (6)7.2.1生产现场抽取样品检测或者检查原则 (6)7.2.2生产现场抽取样品检测或者检查内容 (6)7.3市场抽样检测或者检查 (7)7.3.1市场抽样检测或者检查原则 (7)7.3.2市场抽样检测或者检查内容 (7)7.4获证后监督的频次和时间 (7)7.5获证后监督的记录 (7)7.6获证后监督结果的评价 (7)8 认证证书 (8)8.1认证证书的保持 (8)8.2认证证书的内容 (8)8.3认证证书的变更 (8)8.4认证证书的注销、暂停和撤销 (8)8.5认证证书的使用 (9)9认证标志 (9)10 收费 (9)12 认证实施细则 (9)附件1:汽车用制动器衬片产品描述 (11)附件2:生产一致性要求 (12)0 引言根据《国务院关于调整工业产品生产许可证管理目录加强事中事后监管的决定》(国发〔2019〕19号)相关要求,汽车用制动器衬片产品由生产许可证管理转为强制性产品认证管理。
GB 11567.2-2001汽车和挂车后下部防护要求

GB11567.2-2001(2001-08-22发布,2002-05-01实施)前言本标准全部技术内容为强制性要求。
本标准仅对GB11567-1994《汽车和挂车侧面及后下部防护装置要求》中有关后下部防护装置的内容进行了修订。
本标准参照采用了联合国欧洲经济委员会(ECE)1983年7月11日发布的ECE R58《关于1:批准后下部防护装置2:批准安装有已批准的后下部防护装置的车辆3:批准就具有后下部防护的车辆的统一规定》的全部技术内容。
本标准修订的内容与ECE R58的主要差异在于增加了具有吸能性能的后下部防护装置的技术要求和移动壁障追尾碰撞试验条件与程序。
本标准的附录A、附录B、附录C为标准的附录。
本标准与GB11567-1994的主要差异有:①分别对后下部防护装置、安装了符合本标准第Ⅰ部分要求的后下部防护装置的N2、N3、O3和O4类车辆、具有后下部防护的车辆进行了规定。
②本标准仅仅保留了GB11567-1994中关于后下部防护装置外形的要求(GB11567-1994中的3.2.5),对GB11567-1994中其他关于后下部防护装置的要求全部进行了修改。
③本标准以附录的形式规定了后下部防护装置的静态加载试验条件与程序、移动壁障追尾碰撞试验条件与程序和测量仪器。
本标准自实施之日起,替代GB11567-1994中有关后下部防护装置的内容。
关于标准实施日期的建议:l)对于新定型的车辆:自本标准实施之日起开始实施。
2)对于新生产的车辆:自2002年7月1日起开始实施。
本标准由国家机械工业局提出。
本标准由全国汽车标准化技术委员会归口。
本标准起草单位:中国汽车技术研究中心、长春汽车研究所。
本标准主要起草人:朱彤、朱西产、崔光滨。
本标准委托全国汽车标准化技术委员会负责解释。
本标准首次发布于1989年,1994年第一次修订,本次为第二次修订。
中华人民共和国国家标准汽车和挂车后下部防护要求GB11567.2-2001Motor vehicles andtrailers-代替GB 11567-1994部分内容Rear underrun protection requirements 1范围本标准规定了汽车和挂车后下部防护装置的技术要求和试验方法。
04.484-2008 ABS性能要求与试验方法

下列文件中的条款通过本标准的引用而成为本标准的条款。凡是注日期的引用文件,其随后所有的修改单(不包括勘误的内容)或修订版均不适用于本标准,然而,鼓励根据本标准达成协议的各方研究人员使用这些文件的最新版本。凡是不注日期的引用文件,其最新版本适用于本标准。
GB4094 汽车操纵件、指示器及信号装置的标志
偏移率:S平台±7º/s以内,A平台±5º/s以内,B平台±3º/s以内。
3.系统的所有功能必须正确实现,不能有影响批量生产的缺陷存在。
1注:该项性能要求目标值仅针对前驱动车。
冰面-〉沥青路面
50
1.制动性能:经过对接点后整车减速度恢复到70%高附减速度时间的中值≤1.2s。
2.操纵安全性
偏移率:S平台±7º/s以内,A平台±5º/s以内,B平台±3º/s以内。
2)ABS打开功能时制动距离≤ ABS关闭增加20%以内,同时附着系数利用率ε≥0.90(根据制动距离的数值确定是否进行ε检测)。
4.操纵安全性
1)保持行使路线;
2)偏移率:±3º/s以内。
5.行使路线偏移:Sy≤±0.5m。
6.系统的所有功能必须正确实现,不能有影响批量生产的缺陷存在。
50
环形(R100)或其他(顺时针及逆时针)
3.第一周期:车辆减速度下降<0.15g。车辆减速度增加响应时间<400ms(响应时间:从减速度最低值恢复到最大值的时间)。
4.制动性能:ABS制动距离小于带EBD下的BE(Best effort)制动距离的95%,带EBD的 BE制动距离比不带EBD的BE制动距离小8%(同步附着系数利用率≤0.6,悬架状态稳定,试行)。同时附着系数利用率ε≥0.90(根据制动距离的数值确定是否进行ε检测)。或者100km/h制动的制动距离≤44m。
机动车安全技术检验机构常规检验

机动车安全技术检验机构常规检验资格许可技术条件为规范机动车安全技术检验(以下简称“安检”)机构的常规检验资格许可,保障安检机构有序运行和规范安检机构工作,根据《中华人民共和国道路交通安全法》及其实施条例、《中华人民共和国行政许可法》、《中华人民共和国产品质量法》、《中华人民共和国计量法》及其实施细则、《机动车安全技术检验机构管理规定》(国家质量监督检验检疫总局令第87号,以下简称“管理规定”)等有关法律、法规和行政规章,制定本技术条件。
安检机构获得常规检验资格许可,必须满足本技术条件的要求。
1. 法人资格安检机构应当依法设立,具有法人资格,并承担相应的法律责任。
2. 依法经营安检机构应当遵守国家的法律法规,依法经营。
其企业的经营范围、事业法人和社团法人的业务范围应涵盖机动车安检。
3. 计量认证安检机构,必须经省级以上质量技术监督部门对其计量认证合格,获得计量认证合格证书。
在计量认证有效期内和认证合格范围内从事安检活动。
4. 人员安检机构应当具有与其从事检验、设备维护检查活动相适应的专业技术人员和管理人员。
4.1安检机构应设有机构负责人、技术负责人、质量负责人、报告授权签字人(或称“主任检验员”、“总检”),同时还应设有引车员、外观检验员、底盘检验员、登录员等检验人员和设备维护人员。
从事安检工作的专业技术人员必须经省级以上质量技术监督部门考核合格,持证上岗。
汽车常规检验安检机构,专业技术人员应不少于12人,摩托车常规检验安检机构应不少于6人。
4.2 安检机构上述岗位人员要求。
4.2.1机构负责人,应当熟悉机动车检验业务,了解与安检相关的法律法规和标准。
4.2.2 技术负责人、质量负责人、报告授权签字人,应当具备以下要求:⑴熟悉安检业务、相关的法律、法规和标准;⑵具有机动车相关专业的大专以上学历,或者中级以上工程技术职称;⑶熟悉机动车的理论与构造,熟悉各检验工位业务、流程及相关专业知识;⑷有3年以上的机动车检验的工作经历;⑸熟悉安检机构资格许可技术条件。
仅与车桥制动设计应用有关的国标要求介绍-20200313

GB 12676-2014
I型试验(衰退试验) 1,重复制动试验 2,连续制动试验 3,热态性能试验 4,正常行驶试验
GB 12676-2014
• 重复制动试验
GB 12676-2014
GB 12676-2014
• 连续制动试验
GB 12676-2014
• 热态性能试验
同时需要查看标准QC/T239和GB/T12780
GB 12676-2014
M和N类车辆 制动系统的性 能要求: 行车制动系统
GB 12676-2014
• 应急制动装置是指在车辆的常规制动系统出现故障的情况下,用来保证车辆仍然具有一定程 度的制动性能的一组装置或一个系统。也就是说在正常情况下,应急制动装置是不起作用的 (或者不认为其产生的制动效果属于应急制动)。
GB 7258-2017
GB 7258-2017
7.10.3 驻车制动性能 在GB 12676-2014的5.2.3.1和5.2.3.2中对满载时驻车也有要求。
GB 7258-2017
第7.11节 台试检验制动性能 (台架实验)
GB 7258-2017
7.11.1 行车制动性能 7.11.1.1 制动百分比要求 台试检验制动力要求
仅与车桥制动设计应用有关的 国标要求内容介绍
-20200313
GB 12676-2014 商用车辆和挂车制动 系统技术要求及试验方法
GB7258-2004-机动车运行安全技术条件
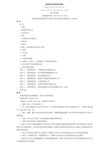
机动车运行安全技术条件Safety specifications formotor vehicles operating on roads(征求意见稿)本稿完成日期:2003年12月28日(请将你们发现的有关专利的内容和支持性文件随意见一并返回)目次前言1 范围2 规范性引用文件3 术语和定义4 整车5 发动机和动力蓄电池6 转向系7 制动系8 照明、信号装置和其他电气设备9 行驶系10 传动系11 车身12 安全防护装置13 消防车、救护车、工程救险车、警车的附加要求14 机动车排气污染物排放控制15 机动车噪声控制附录 A (规范性附录)车速表指示误差检验方法附录 B (规范性附录)转向轮横向侧滑量检验方法附录 C (规范性附录)制动性能检验方法附录 D (规范性附录)前照灯光束照射位置检验方法附录 E (规范性附录)气密性检验方法附录 F (规范性附录)驾驶员耳旁噪声检验方法附录 G (资料性附录)四种类型机动车技术条件要求对应一览表参考文献前言本标准的附录为推荐性的,其余均为强制性的。
本标准代替 GB7258-1997。
本标准与 GB7258-1997 相比,主要修订内容如下:1、增加了第 3 章"术语和定义"。
2、将"三轮农用运输车"更名为三轮汽车,将"四轮农用运输车"更名为低速载货汽车,明确"农用运输车"实质上是汽车的一类。
3、细化、调整、增加了机动车整车标志的要求,根据需要适当增加了部分机动车在图形和文字标志方面的要求。
4、增加了汽车及汽车列车、挂车的轴荷和质量参数的要求。
5、调整了机动车乘坐人数核定的要求。
6、增加了三轮汽车和低速载货汽车应在设计结构上确保在实际使用过程中机动车行驶速度不会超过其最高设计车速的要求,并要求具有皮带传动装置的上述机动车需在车架易见部位打刻能永久保持的标明皮带轮直径的标记。
汽车防滑链性能要求和试验方法编制说明

汽车防滑链性能要求和试验方法编制说明一、工作简况(一)任务来源随着全球气候变化异常,冬季严寒极端气候越发频繁,冬季安装汽车防滑链是车辆在冬季严寒等极端气候条件下行车安全的重要保障。
同时防滑链行业标准也是对国标GB7063-2011护轮板标准的有效补充,2011年车身分标委提出《汽车轮胎防滑链》立项申请,并通过工信部立项评审。
2012年3月工信部下发工信厅科【2012】68号文【关于印发2012年第一批行业标准制修订计划的通知】,编号为2012-0114T-QC,项目名称《汽车轮胎防滑链》。
(二)起草单位本标准主要起草单位:东风汽车公司技术中心、国家汽车质量监督检验中心(襄阳)、黑河红河谷汽车测试中心有限公司、浙江省浦江伯虎链条有限公司、西安联谊橡胶制品有限公司、米其林(中国)投资有限公司。
(三)主要工作过程本标准的制订是以标准工作组的形式开展的。
东风汽车公司技术中心、国家汽车质量监督检验中心(襄阳)作为主要起草单位,组织部分汽车防滑链生产企业、研究机构参与标准的起草工作。
本标准在综合分析国内外同类先进的技术标准基础上,根据我国的实际情况自行制定。
主要工作过程如下: 2010年10月—2012年3月,工作组开始收集国内外有关汽车防滑链标准如日本JIS D 4241、美国SAE J683,并进行了翻译和整理,2012年1月向工信部提交标准立项资料,3月工信部批准标准立项。
标准工作组通过网络和电话对目前市场上的防滑链产品种类、价格和主要生产企业共计十几家进行了初步了解。
2012年4月工作小组走访了部分汽车防滑链厂家,实地考察了各企业生产防滑链的情况及生产防滑链的生产工艺过程,并征求他们对即将起草的行业标准的意见。
最终邀请三家规模较大、技术较强的生产企业作为标准起草组成员,分别是以生产金属防滑链为主的浙江省浦江伯虎链条有限公司和以生产橡胶防滑链为主的西安联谊橡胶制品有限公司、海外以生产新型防滑链为主的米其林(中国)投资有限公司。
GB汽车和挂车-制动器用零部件技术要求及试验方法-编制说明
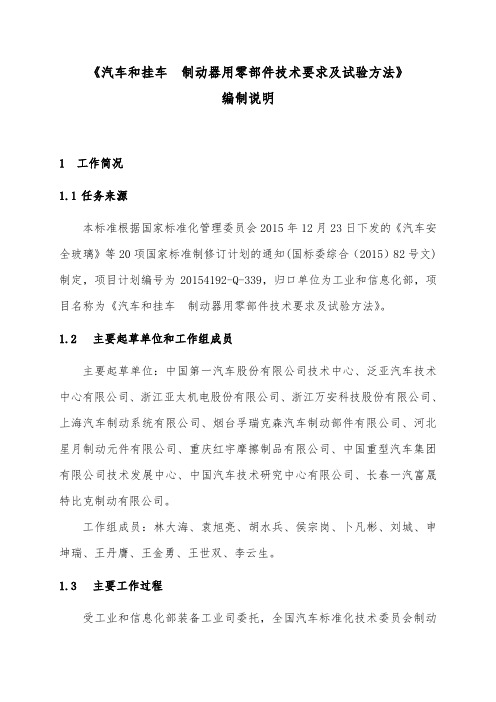
《汽车和挂车制动器用零部件技术要求及试验方法》编制说明1工作简况1.1任务来源本标准根据国家标准化管理委员会2015年12月23日下发的《汽车安全玻璃》等20项国家标准制修订计划的通知(国标委综合(2015)82号文)制定,项目计划编号为20154192-Q-339,归口单位为工业和信息化部,项目名称为《汽车和挂车制动器用零部件技术要求及试验方法》。
1.2主要起草单位和工作组成员主要起草单位:中国第一汽车股份有限公司技术中心、泛亚汽车技术中心有限公司、浙江亚太机电股份有限公司、浙江万安科技股份有限公司、上海汽车制动系统有限公司、烟台孚瑞克森汽车制动部件有限公司、河北星月制动元件有限公司、重庆红宇摩擦制品有限公司、中国重型汽车集团有限公司技术发展中心、中国汽车技术研究中心有限公司、长春一汽富晟特比克制动有限公司。
工作组成员:林大海、袁旭亮、胡水兵、侯宗岗、卜凡彬、刘城、申坤瑞、王丹膺、王金勇、王世双、李云生。
1.3主要工作过程受工业和信息化部装备工业司委托,全国汽车标准化技术委员会制动分技术委员会面向行业组建标准起草工作组,由中国第一汽车股份有限公司技术中心(以下简称“一汽技术中心”)作为牵头单位,负责该标准的前期准备工作,于2014年5月在行业内启动了标准起草工作组筹备工作,向行业内征集参与标准起草工作组的成员单位,并于2014年6月初根据回函情况和参与企业的情况,同时考虑到成员单位涉及的业务分布情况,确定了标准起草工作组成员。
1.3.1 工作组成立会议2014年8月6日在云南省昆明市召开了标准工作组成立会议,来自10家工作组单位的13名专家参加了成立会议。
会议就成立标准工作组的重要性和意义、当前制动器换装零部件市场的情况进行了简要说明,对标准工作组今后的工作提出了要求。
标准工作组负责人就工作组筹备情况、重要工作任务及工作计划向与会代表进行简要汇报。
随后,各位代表从当前制动器换装零部件产品质量、维修市场情况、以及标准采标、工作组主要工作、后续工作等进行了充分交流和沟通。
交通部关于发布货运挂车气压制动技术要求和试验方法等三项交通行业标准的通知-

交通部关于发布货运挂车气压制动技术要求和试验方法等三项交通行业标
准的通知
正文:
---------------------------------------------------------------------------------------------------------------------------------------------------- 交通部关于发布货运挂车气压制动技术
要求和试验方法等三项交通行业标准的通知
各有关单位:
《货运挂车气压制动技术要求和试验方法》等三项交通行业标准业经审查通过,现予发布,自2003年9月1日起实施。
三项标准的编号和名称是:
l、JT/T487—2003《货运挂车气压制动技术要求和试验方法》
2、JT/T488—2003《轿车运输挂车性能试验方法》
3、JT/T490—2003《道路旅客运输服务人员职业服装款式和标志》
以上三项交通行业标准为推荐性标准,由人民交通出版社出版,并在《交通标准化》刊物上公告。
中华人民共和国交通部(章)
二00三年五月十五日
——结束——。
GB11567.1-2001汽车和挂车侧面防护要求

GB 11567.1-2001汽车和挂车侧面防护要求代替GB 11567-1994 部分内容前言本标准全部技术内容为强制性要求。
本标准仅对GB 11567-1994《汽车和挂车侧面及后下部防护装置要求》中有关侧面防护装置的内容进行了修订。
本标准等同采用了联合国欧洲经济委员会(ECE)1988年2月29日发布的ECER73《关于就侧面防护装置方面批准载货车、挂车和半挂车的统一规定》的全部技术内容。
本标准与GB 11567-1994的主要差异有:① 对侧面防护装置的形状和侧面防护装置在车辆横向位置的要求比GBll567-1994更为具体、详细。
② 对侧面防护装置前端的结构和位置要求重新进行了规定。
③ 对侧面防护装置后端的位置限值进行了调整。
④ 对侧面防护装置距车辆上部的距离要求进行了调整和完善。
⑤ 对侧面防护装置的构成,增加了不允许侧面防护装置作为制动元件、气体或液体管路的要求。
⑥ 增加了对特种车辆的补充规定。
本标准自实施之日起,替代GB ll567-1994中有关侧面防护装置的内容。
本标准由国家机械工业局提出。
本标准由全国汽车标准化技术委员会归口。
本标准起草单位:中国汽车技术研究中心、长春汽车研究所。
本标准主要起草人:朱彤、朱西产、崔光滨。
本标准委托全国汽车标准化技术委员会负责解释。
本标准首次发布于1989年,1994年第一次修订,本次为第二次修订。
汽车和挂车侧面防护要求Motor vehicles and trailers-Lateral protection requirements1 范围本标准规定了对汽车和挂车侧面防护的技术要求,以有效地保护无防御行人,以免其跌于车侧而被卷入车轮下面。
本标准适用于N2、N3、O3和O4类车辆,但本标准不适用于:--半挂牵引车;--为搬运无法分段的长货物而专门设计和制造的特殊用途车,如运输木材、钢材棒料等货物的车辆;--为了专门目的设计和制造的、由于客观原因而无法安装侧面防护装置的车辆。
试验方法 (征求意见稿)标准编制说明

汽车用液力变矩器台架试验方法(征求意见稿)标准编制说明一、任务来源2008年,装备工业司下达了《关于开展装备工业行业标准化工作的通知》(工信装函[2008]26号文),要求全国汽车标准化技术委员会等相关单位做好2009年各行业国家标准及行业标准项目计划的申报和编制工作。
全标委通过各专业分技术委员会并同时面向汽车行业征集汽车国家标准和行业标准的计划项目。
在这一背景下,起草单位提交了行业标准《汽车用液力变矩器台架试验方法》的任务书,并获准进行该标准的修订工作。
二、编制过程2.1 成立标准起草小组全国汽车标准化技术委员会于2008年11月发布了汽标秘字(2008)55号文《关于征集汽车行业国家标准及行业标准计划项目的函》。
在汽车变速器分技术委员会秘书处的组织下,2009年12月成立了行业标准《汽车用液力变矩器台架试验方法》的起草小组,标准起草小组按计划开展标准起草工作。
2.2 第一阶段工作本标准的起草制定过程共分为四个阶段,第一个阶段从2009年2月到4月,主要工作为收集分析国内外相关资料。
标准起草小组根据标准制订的需要,收集了国内外相关的政策、资料和标准,国内的标准主要为液力变矩器试验、抽样检验、包装和标牌相关的国家标准和行业标准以及一些相关论文,国外的标准主要是美国SAE、日本JSAE以及前苏联的一些与液力传动相关的标准。
并结合起草单位多年的试验以及国内外整车厂先进的企业标准进行分析。
2.3 第二阶段工作本标准起草小组在经过大量的收集整理调研工作的基础上,提出标准提纲,确定了该标准需要进行标识的内容和要求。
标准起草小组成员单位内部进行讨论、论证,形成标准初步文本;标准起草小组成员单位间通过多种形式不断交流、补充、完善标准文本。
随后在2009年5月参加了“全国汽车标准化技术委员会汽车变速器分技术委员会2009年度会议”,广泛听取了业内同行的意见,进一步对原有的草案进行了修正和补充,并形成了当前的征求意见稿。
- 1、下载文档前请自行甄别文档内容的完整性,平台不提供额外的编辑、内容补充、找答案等附加服务。
- 2、"仅部分预览"的文档,不可在线预览部分如存在完整性等问题,可反馈申请退款(可完整预览的文档不适用该条件!)。
- 3、如文档侵犯您的权益,请联系客服反馈,我们会尽快为您处理(人工客服工作时间:9:00-18:30)。
《汽车和挂车制动器用零部件技术要求及试验方法》编制说明1工作简况1.1任务来源本标准根据国家标准化管理委员会2015年12月23日下发的《汽车安全玻璃》等20项国家标准制修订计划的通知(国标委综合(2015)82号文)制定,项目计划编号为20154192-Q-339,归口单位为工业和信息化部,项目名称为《汽车和挂车制动器用零部件技术要求及试验方法》。
1.2主要起草单位和工作组成员主要起草单位:中国第一汽车股份有限公司技术中心、泛亚汽车技术中心有限公司、浙江亚太机电股份有限公司、浙江万安科技股份有限公司、上海汽车制动系统有限公司、烟台孚瑞克森汽车制动部件有限公司、河北星月制动元件有限公司、重庆红宇摩擦制品有限公司、中国重型汽车集团有限公司技术发展中心、中国汽车技术研究中心有限公司、长春一汽富晟特比克制动有限公司。
工作组成员:林大海、袁旭亮、胡水兵、侯宗岗、卜凡彬、刘城、申坤瑞、王丹膺、王金勇、王世双、李云生。
1.3主要工作过程受工业和信息化部装备工业司委托,全国汽车标准化技术委员会制动分技术委员会面向行业组建标准起草工作组,由中国第一汽车股份有限公司技术中心(以下简称“一汽技术中心”)作为牵头单位,负责该标准的前期准备工作,于2014年5月在行业内启动了标准起草工作组筹备工作,向行业内征集参与标准起草工作组的成员单位,并于2014年6月初根据回函情况和参与企业的情况,同时考虑到成员单位涉及的业务分布情况,确定了标准起草工作组成员。
1.3.1 工作组成立会议2014年8月6日在云南省昆明市召开了标准工作组成立会议,来自10家工作组单位的13名专家参加了成立会议。
会议就成立标准工作组的重要性和意义、当前制动器换装零部件市场的情况进行了简要说明,对标准工作组今后的工作提出了要求。
标准工作组负责人就工作组筹备情况、重要工作任务及工作计划向与会代表进行简要汇报。
随后,各位代表从当前制动器换装零部件产品质量、维修市场情况、以及标准采标、工作组主要工作、后续工作等进行了充分交流和沟通。
与会代表一致认为成立制动器零部件标准工作组非常必要,该标准的制定将对规范制动器相关零部件的产品质量、售后维修市场、保护正规生产企业、引导制动器产品发展起到积极作用。
最后会议达成如下结论:1)原则上,该标准主要技术内容参照UN R90;2)会后各单位按分工要求对UN R90法规进行翻译,并按时将译文汇总到标准工作组。
1.3.2 工作组第二次会议根据标准工作组成立大会确定的任务,各参与单位按要求对UN R90法规原文进行了翻译,并按要求提交给标准工作组,工作组根据各单位译文,按要求对UN R90译文进行了汇总,并发送给标准工作组各成员。
按照标准工作组工作计划,于2014年11月12日在山东省德州市召开了标准工作组第二次工作会议,10家标准组成员单位的13位代表出席会议。
会议对前期工作进行了总结,通过对UN R90法规译文进行研讨,确定了我国标准的采标原则,同时对今后工作进行了讨论,最后与会代表达成以下意向:1)标准制定原则:标准主要技术内容与UN R90一致,删除与我国认证政策矛盾的章节;台架试验的惯性质量计算方法按我国汽车行业标准;引用标准以我国相关标准为主,摩擦材料生产一致性检查采用GB 5763;在GB/T 5620、GB 12676、GB 21670等引用标准中已定义的术语,本标准中原则上不再重复定义。
2)各单位根据自身产品情况,自行确定产品验证试验,并将验证试验情况于2015年2月底前提交至标准工作组。
3)由标准牵头单位在2015年3月底完成标准立项相关文件,其它各单位成员按要求提供预研报告中的相关资料。
1.3.3 标准项目立项根据工作组第二次会议安排,于2015年3月初完成了标准立项所需的相关文件(标准草案、国家标准项目预研报告、标准项目基本情况以及标准项目建议书),并按要求提交给全国汽车标准化技术委员会制动分技术委员会秘书处,由制动分技术委员会秘书处正式提交立项申请。
2015年12月23日国家标准化管理委员会正式下达了标准制修订计划。
1.3.4 工作组第三次会议项目计划编号正式下达后,根据国标委、工业和信息化部要求,标准工作组编制了标准制定工作计划,并于2016年3月底完成了标准讨论稿编制。
根据标准工作计划,于2016年4月14日在吉林省长春市召开了工作组第三次会议,来自11家单位的16位代表出席了本次会议。
会议介绍了标准立项情况和前期工作,并向代表详细介绍了标准工作计划安排、标准制修订原则。
然后与会代表对标准工作计划、标准工作组讨论稿进行了认真讨论,最后达成如下意见:1)原则上同意标准主体内容,根据前期验证试验情况,N3和M3类车辆的制动鼓/盘的热疲劳试验不采用UN R90的方法,改用恒速拖磨方式;2)制动盘和制动鼓强度试验,UN R90的磨合试验过于复杂,改为与我国相关行业标准一致的磨合试验方法,但制动初温适当提高;3)各成员单位根据自身产品情况,自行确定产品验证试验,验证试验方法和条件按修改后的标准初稿。
验证试验结果应在2016年12月底前提交给标准牵头单位。
根据会议安排,对标准工作组讨论稿进行了修改完善,并于2016年5月初将修改修改完善的标准初稿发给标准起草小组各成员。
1.3.5 标准行业研讨会为了保证标准技术内容更加符合我国制动器行业现状,同时使各企业相关人员及时了解标准主要内容,提前做好产品质量提升工作,经与全国汽车标准化技术委员会制动分技术委员会协商,由全国汽车标准化委员会制动分技术委员会秘书处组织,2017年3月23日,在江西省南昌市召开了标准行业研讨会,来自全国汽车和摩擦材料行业相关单位及标准起草小组成员单位的共计31位代表出席了会议。
会议首先由标准牵头单位一汽技术中心向与会代表介绍了标准立项情况、标准工作组前期工作,对标准草案主要内容进行了详细解读。
然后与会代表与标准起草小组成员就标准主要内容、相关条款以及主要技术指标进行了充分讨论,并提出了许多建设性的意见。
会后,标准起草小组根据本次研讨会提出的意见,进行了认真讨论,并根据起草小组讨论结果,对标准草案进行了修改完善,于2017年5月初发给与会代表和起草小组全体成员,同时要求起草小组各单位按照新修改的标准草案进行进一步的验证试验,并将验证结果在2017年底反馈给起草小组。
根据标准起草小组各成员单位验证试验结果,于2018年2月初对标准初稿再次进行了修改完善,完成标准征求意见稿初稿编制,并发给标准起草小组各成员单位,在标准起草小组内征求意见,同时要求大家在2018年3月10日将反馈意见提交给起草小组。
根据起草小组各成员单位反馈的最后意见,对标准征求意见初稿进行了进一步的修改完善,于2018年5月10日完成标准征求意见稿,并上报制动分技术委员会秘书处。
2编制原则和确定强制性国家标准技术主要内容的论据2.1标准编制原则本标准编制遵循如下原则:1)标准主要技术内容与UN R90一致,删除与我国认证政策矛盾的章节(第3章、第4章、第9章~第12章以及附件1和附件7);2)U N R90的附件10作为本标准的资料性附录给予保留;3)台架试验的惯性质量计算方法按我国汽车行业标准;4)引用标准以我国相关标准为主,摩擦材料生产一致性检查采用GB 5763;5)在GB/T 5620、GB 12676、GB 21670等引用标准中已定义的术语,本标准中原则上不再重复定义;6)标准编制规则按GB/T 1.1-2009及相关标准的规定。
2.2标准主要内容本标准主要包含术语和定义、试验相关要求、技术要求和试验方法、包装和标志、产品一致性等。
本标准与UN R90的主要结构变化对比见表1。
表1 本标准与UN R90主要技术要素对比2.2.1范围由于我国机动车辆在进行整车制动性能认证试验时,通常只对其中一家配套的制动器零部件(制动蹄片总成/制动衬片/衬块总成和制动鼓/制动盘)进行认证试验,其余配套厂家的零部件主要由整车厂自行进行相关验证试验,而对车辆使用过程中从维修市场购置的制动蹄片总成/制动衬片/衬块总成和制动鼓/制动盘等零部件,无相应的整车或台架总成认证要求,从而造成维修市场上的制动器零部件质量莨伪不齐。
由于上述原因,因此,本标准适用范围主要针对没有按整车制动标准GB 12676和GB 21670进行整车制动性能认证的制动器用零部件,具体适用对象如下:a)用于已按GB 12676-2014或GB 21670-2008完成型式认证的M、N和O类车辆的制动系统构成零件的摩擦式制动器的换装制动蹄片总成和换装衬块总成;b)设计为铆接到制动蹄铁上后再装配和使用、已按GB 12676-2014完成型式认证的M3、N2、N3、O3或O4类车辆的换装制动衬片;c)用于单独使用的驻车制动系统的换装制动蹄片总成和衬块总成;d)用于已按GB 12676-2014或GB 21670-2008完成型式认证的M、N和O类车辆的制动系统构成零件的摩擦式制动器的换装制动鼓和换装制动盘。
2.2.2规范性引用文件根据我国标准化相关文件规定,本标准除采用我国对应的规范性引用文件替代UN R90的规范性引用文件外,还增加了5项规范性引用标准,本标准涉及的规范性引用标准与UN R90规范性引用文件对应情况见表2。
表2 本标准规范性引用文件与UN R90对应关系一览表2.2.3术语和定义本标准定义了与换装零部件相关的21项术语。
在引用标准GB/T 526、GB 12676和GB 21670等标准中已有的术语,在本标准中未重复定义。
同时删除了由于本标准技术内容变化不再涉及的术语。
具体情况如下:1)本标准保留的术语有:换装零件、原装零件、制动衬片型号、制动蹄片总成型号、衬块总成型号、原装制动衬片、原装制动蹄片总成、原装衬块总成、换装制动衬片、换装制动蹄片总成、换装衬块总成、驻车制动蹄片(衬块)总成、原装制动盘/制动鼓、换装制动鼓/制动盘、等同制动盘、等同制动鼓、等效制动盘、等效制动鼓、可互换制动盘、可互换制动鼓、特殊制动盘或制动鼓、最小厚度、最大内径等。
2)本标准删除的UN R90术语有:制造商、制动系统、摩擦式制动器、制动衬片总成、制动蹄片总成、制动蹄、衬块总成、背板、制动衬片、鼓式制动衬片、摩擦材料、识别代码、功能尺寸、制动盘/制动鼓型号、试验组、变量、材料组、材料子组。
2.2.4试验相关要求为便于使用和简化标准编制,本标准将涉及试验样品、试验设备以及台架试验转动惯量计算等要求统一放在“试验相关要求”一章。
具体情况如下:1)试验样品要求为了保证试验结果一致性和不同检测机构评价结果的一致性,本标准对不同样品分别给出了最低的试验样品要求,并对不同性质的换装制动盘/制动鼓样品给出了不同的样品要求及每件样品对应的试验或检测项目。