表2危害严重程度(S)评分表
故障模式及影响分析

图来确定潜在的故障原因,针对每一个故障模式,应尽可能地列出所想到的故障原因/故障 机理,潜在故障原因/机理应尽可能地描述准确和完整,以便针对相关的原因采取有的放矢 的补救措施。一般来说,确定潜在故障原因应首先从具有最高严重度的故障入手。频度(O) 是指在产品设想的使用寿命内,潜在故障原因/机理出现的可能性。一般从以往类似产品的 资料,如测试报告,顾客满意度报告,顾客退货报告,维修资料等来确定故障发生的频度。
严重度是潜在故障模式发生后,对系统、零件或顾客影响后果的严重程度的评价指标,
它是衡量潜在故障后果的指标。严重度是针对潜在故障后果而言的,减少严重度级别数值,
唯一的方法是修改设计。如果严重度的评价超出了小组的经验或知识范围,应与相关的工程
技术人员进行协商。表 2 给出了一个供参考的严重度分级标准。 表 2 严重度(S)评分表
2 FMEA 的实施步骤
FMEA 技术的分析过程包括识别潜在的故障模式,以及从故障后果的严重度(S)、故
障发生的频度(P)和故障的不可探测度(D)等三个方面评估故障模式。根据这三个方面
的评价得分计算故障的风险顺序数(RPN),风险顺序数高的故障模式即为改进的重点环节,
需分析其发生的原因和机理,拟定改进方案及实施计划。实施改进方案后,应对改进效果进
2
(3)分析潜在故障后果,评价其严重等级 潜在故障后果是指潜在故障模式对系统功能/顾客的影响。要根据顾客(这里所指的顾 客,既包括产品的最终使用者,也包括下一级的设计、制造人员)可能发现或经历的情况来
描述故障后果。要清楚地说明该故障是否会影响到产品的安全性或与政府、行业规定发生不
符。不仅要考虑故障后果对本系统的影响,也要考虑对其他系统、顾客的影响。
装置、统计过程控制、过程评价等过程控制方法。
S评分表
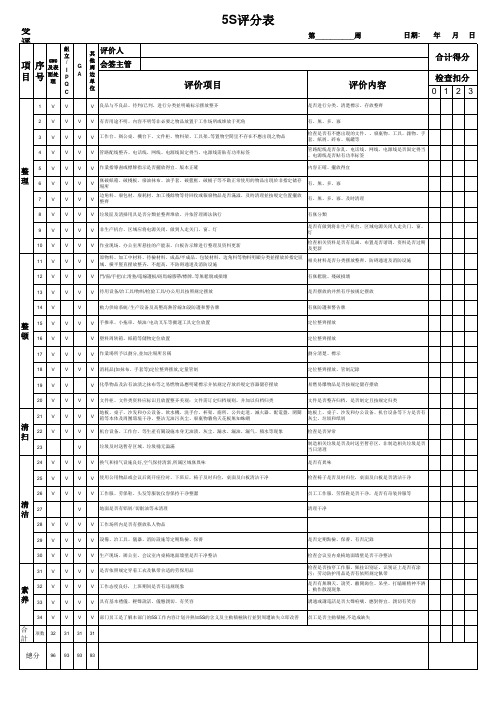
评
组 立
其 评价人
項
序 CNC 及表
目 号 面处 理
/ I P
G A
他 周
会签主管
边
单
Q
位
C
5S评分表
评价项目
1VV
V 良品与不良品、待判/已判、进行分类並明确标示摆放整齐
第__________周
评价内容
是否进行分类、清楚標示、存放整齊
日期: 年 月 日
合计得分 检查扣分 0123
2 V V V V 有否用途不明、內容不明等非必要之物品放置于工作场所或堆放于死角
29 V V V V 設備、治工具、儀器、消防設施等定期點檢、保養
是否定期點檢、保養,有否記錄
30 V V V V 生产现场、辦公室、会议室内桌椅地面墙壁是否干净整洁
31 V V V V 是否依照规定穿着工衣及佩带合适的劳保用品
素 32 V
V
V
V 工作态度良好,上班期间是否有违规现象
养 33 V
V
V
20 V V V V 文件柜、文件类资料应标识且放置整齐美观;文件需订定归档规则,并加以归档归类
文件是否整齐归档,是否制定且按规定归类
地板、桌子、沙发和办公设备、飲水機、洗手台、杯架、廁所、公共走道、滅火器、配電盤、開闢 地板上、桌子、沙发和办公设备、机台设备等下方是否有
21 V V V V 箱等本体及周圍環境干净、整洁无油污灰尘、廢棄物牆角天花板無知蛛網
有、無、多、寡
3 V V V V 工作台、辦公桌、機台下、文件柜、物料架、工具架..等置物空間里不存在不應出現之物品 4 V V V V 管路配线整齐、电话线、网线、电源线固定得当、电源线需貼有功率标签
创伤严重程度(ISS)评分表
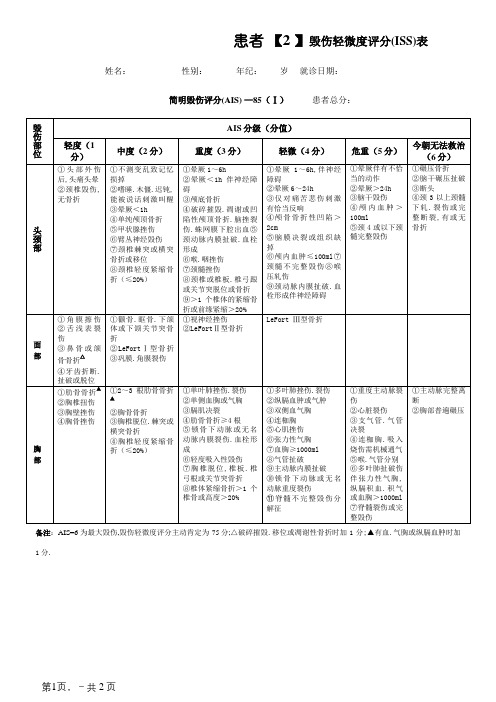
患者【2 】毁伤轻微度评分(ISS)表姓名:_________ 性别:____ 年纪:____岁就诊日期:___________
简明毁伤评分(AIS) —85(Ⅰ)患者总分:___________
备注:AIS=6为最大毁伤,毁伤轻微度评分主动肯定为75分;△破碎摧毁.移位或凋谢性骨折时加1分;▲有血.气胸或纵膈血肿时加1分.
简明毁伤评分(AIS) —85(Ⅱ)
备注:
⏹盘算ISS的一般原则:本法把人体分为6个区域,ISS是身材3个最轻微毁伤区域的最高AIS值的平方和,即
ISS=AIS12+AIS22+AIS32.ISS分值规模1~75分,当患者消失1处或多处AIS=6分毁伤时,直接肯定为ISS最高值75分.
⏹ISS≤16分为轻伤; ISS>16分为重伤; ISS>25分为轻微伤.
⏹ISS>20病逝世率显著增高,ISS>50存活率很低.。
验证和确认的质量风险评估表

验证和确认的范围质量风险评估××××制药有限公司验证和确认范围质量风险评估1.概念:质量风险:指质量危害出现的可能性和严重性的结合。
2.质量风险管理的程序:3、风险矩阵图危害发生的可能性(F)启动风险管理过程4风险评估方法风险识别:可能影响产品质量、产量、工艺操作或数据完整性的风险;风险分析:本案例应用失败模式效果分析,识别潜在的失败模式,对风险发生的频率、严重性和可测量性评分。
风险判定:包括评估先前确认风险的后果,其基础建立在严重程度、可能性及可检测性上;严重程度(S):测定风险的潜在后果,主要针对可能危害产品质量、患者健康及数据完整性的影响。
严重程度分为四个等级:可能性程度(P):测定风险产生的可能性。
根据积累的经验、工艺/操作复杂性知识或小组提供的其他目标数据,可获得可能性的数值。
为建立统一基线,建立以下等级:可检测性(D):在潜在风险造成危害前,检测发现的可能性,定义如下:RPN(风险优先系数)计算:将各不同因素相乘;严重程度、可能性及可检测性,可获得风险系数( RPN = SPD )RPN > 16 或严重程度 = 4高风险水平:此为不可接受风险。
必须尽快采用控制措施,通过提高可检测性及降低风险产生的可能性来降低最终风险水平。
验证应先集中于确认已采用控制措施且持续执行。
严重程度为4时,导致的高风险水平,必须将其降低至RPN最大等于816 ≥ RPN ≥ 8中等风险水平:此风险要求采用控制措施,通过提高可检测性及(或)降低风险产生的可能性来降低最终风险水平。
所采用的措施可以是规程或技术措施,但均应经过验证。
RPN ≤ 7低风险水平:此风险水平为可接受,无需采用额外的控制措施。
质量风险评估表附件2 验证和确认的质量风险评估。
检维修工作危害分析JHA评价表(含LSR评分说明)

工作危害分析(JHA)评价表
编制:
审核:
日期:二〇二〇年九月二十七日
工作危害分析法(JHA)说明
本方法适用于检维修工作,以作业项目为单元,对作业过程伤害人的工作危害分析,由项目分管部门、项目负责人、检修人员、安全员等完成。
具有工作危害的10大作业均有安全规程,评价分析过程予以执行。
工作危害分析:
事故发生的可能性L;
事故后果的严重性S;
风险等级R,用公式表示:R= L×S
1.发生事故的可能性L判定准则,按表1取值:
表1
2.事故后果严重性S判定准则,按表2取值:
表2
3.
表3
工作危害分析(JHA)评价表。
FMEA SOD 打分表

高
50次每1000个
1次每20辆中
9
20次每1000个
1次每50辆中
8
10次每1000个
1次100辆中
7
一般
2次每1000个
1次每500辆中
6
0.5次每1000个
1次每2000辆中
5
0.1次每1000个
1次每10000辆中
4
低
0.01每1000个
1每100000辆中
3
≤0.001每1000个中
1每1000000
9
可能在有预警下危害操作(机械或装配)
基本功能的损失或降级
基本功能损失(车辆不能操作,但不影响车辆安全操作)
8
大规模中断
100%的产品是废品。流水线停止或停止出货
基本功能损失(车辆可操作,但降低了功能的等级)
7
显著中断
生产运转一定会产生部分废品。背离最初过程包括流水线速度降低或增加
舒适功能的损失或降级
3
在加工前部分须在位置上加工
外观或听见噪音,车辆可操作,不符合项被有辨别能力的顾客注意到(<25%
2
微小中断
过程,操作或操作者的轻微不便利
没有影响
没有可辨别的后果
1
没有后果
没有可辨别的后果
二发生率(O)评分准则
失效可能性
准则:FMEA要因发生率
(事件每项目/车辆)
等级
非常高
≥100次每1000时问题探测
操作者通过直观/目测/排列/耳听法在位置上做失效模式探测或操作者通过使用特性测量(/行/不行、手动转矩检查等)做加工后探测。
7
非常低
加工后问题探测
操作者通过使用变量测量或操作者在位置上通过使用特性测量事后失效模式探测,(行/不行、手动转矩检查等)
创伤严重程度评分表

患者损伤严重度评分(ISS)表
姓名:_________ 性别:____ 年龄:____岁就诊日期:___________
简明损伤评分(AIS)—85(Ⅰ)患者总分:___________
(未完,转背面)
备注:AIS=6为最大损伤,损伤严重度评分自动确定为75分;△粉碎、移位或开放性骨折时加1分;▲有血、气胸或纵膈血肿时加1分.
简明损伤评分(AIS) —85(Ⅱ)
备注:
⏹计算ISS的一般原则:本法把人体分为6个区域,ISS是身体3个最严重损伤区域的最高AIS值的平方和,即
ISS=AIS12+AIS22+AIS32.ISS分值范围1~75分,当患者存在1处或多处AIS=6分损伤时,直接确定为ISS最高值75分。
⏹ISS≤16分为轻伤;ISS>16分为重伤; ISS>25分为严重伤.
⏹ISS>20病死率明显增高,ISS>50存活率很低。
创伤严重程度(ISS)评分表

有不适当
折
后,头
②嗜睡、木
伴神经障碍
碍
的动作
②脑干碾
痛头晕
僵、迟钝,
③颅底骨折
②昏迷6〜
②昏迷〉
压撕裂③
②颈椎
能被语言刺
24h
24h
断头
损伤,
激唤醒③昏
④粉碎、开放
③仅对疼痛
③脑干损
④颈3以
无骨折
迷V1h
或凹陷性颅
刺激有恰当
伤
上颈髓下
顶骨折、脑挫
④单纯颅顶
裂伤、蛛网膜
反应
④颅内血
轧、裂伤
⑤心肌挫伤
④连枷
(<20%
脉或无名动
胸、吸入
⑥张力性气
烧伤需机
脉内膜裂伤、
胸
械通气
胸
血栓形成
部
⑥轻度吸入
⑦血胸》
⑤喉、气
1000ml
管分离
性损伤
⑧气管撕裂
⑥多叶肺
⑦胸椎脱位,
⑨主动脉内
撕裂伤伴
椎板、椎弓根
膜撕裂
张力性气或关节突骨折来自胸,纵膈⑩锁骨下动
积血、积
⑧椎体压缩
脉或无名动
气或血胸
骨折>1个椎
骨或高度>
关节突脱位
压缩骨折
或骨折
⑨颈动脉内
(<20%
⑨〉1个椎体
膜撕裂、血栓
形成伴神经
的压缩骨折
障碍
或前缘压缩
>20%
①角膜
擦伤②
舌浅表
裂伤
③鼻骨
或颌骨
骨折
④牙齿
折断、
撕裂或
脱位
①颧骨、眶
4.1.3、 FMEA-MSR评分表
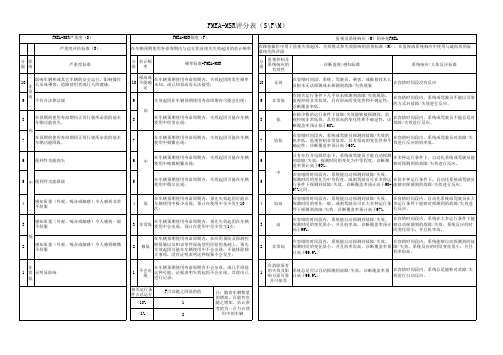
分影 级响
严重度标准
10
非
影响车辆和或其它车辆的安全运行. 影响操作 人员或乘客、道路使用者或行人的健康。
常
高 9 不符合法律法规
8
在预期的使用寿命期间正常行驶所必需的基本 车辆功能丧失。
高
7
在预期的使用寿命期间正常行驶所必需的基本 车辆功能降级。
6 便利性功能丧失
7
较低
在容错时间段内,系统或驾驶员探测到故障/失效的 机率低。监视控制非常低效,具有很高的变化性和不 确定性,诊断覆盖率预计高于60%。
在容错时间段内,系统或驾驶员对故障/失 效进行反应的机率低。
6
在车辆预期使用寿命周期内,失效起因可能在车辆 中 使用中略微频繁出现;
6
5
在车辆预期使用寿命周期内,失效起因可能在车辆 使用中偶尔出现;
分 级
监视控制及 系统响应的
有效性
诊断监视/感知标准
系统响应/人体反应标准
10
无效
在容错时间段,系统、驾驶员、乘客、或维修技术人 员根本无法探测或未探测到故障/失效现象
在容错时间段没有反应
9
非常低
在相关运行条件下几乎从未探测到故障/失效现场。 监视控制非常低效,具有很高的变化性和不确定性, 诊断覆盖率低。
分 估计频 级率
频率标准-FMEA-MSR
10
极高或 不能确
定
在车辆预期使用寿命周期内,失效起因的发生频率 未知,或已知很高而无法接受;
9
失效起因在车辆预期使用寿命周期内可能会出现;
高
8Hale Waihona Puke 在车辆预期使用寿命周期内,失效起因可能在车辆 使用中经常出现;
药物副作用量表
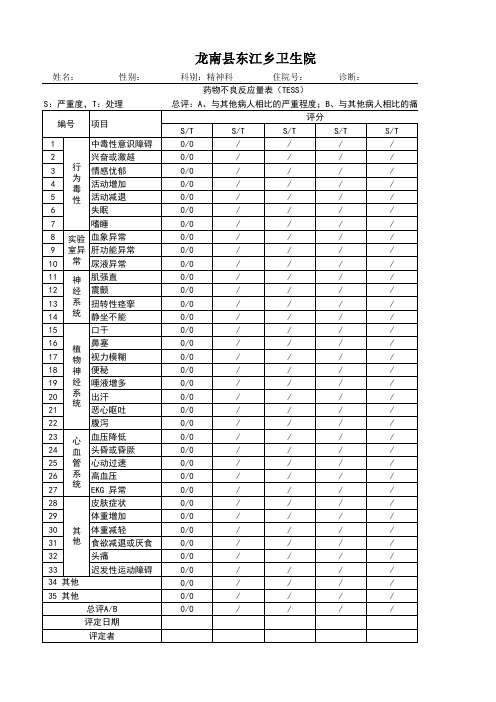
姓名: 性别: 科别:精神科 住院号: 诊断: 药物不良反应量表(TESS) S:严重度,T:处理 编号 1 2 3 4 5 6 7 8 9 10 11 12 13 14 15 16 17 18 19 20 21 22 23 24 25 26 27 28 29 30 31 32 33 34 其他 35 其他 总评A/B 评定日期 评定者 其 他 心 血 管 系 统 植 物 神 经 系 统 行 为 毒 性 项目 中毒性意识障碍 兴奋或激越 情感忧郁 活动增加 活动减退 失眠 嗜睡 实验 血象异常 室异 肝功能异常 常 尿液异常 神 经 系 统 肌强直 震颤 扭转性痉挛 静坐不能 口干 鼻塞 视力模糊 便秘 唾液增多 出汗 恶心呕吐 腹泻 血压降低 头昏或昏厥 心动过速 高血压 EKG 异常 皮肤症状 体重增加 体重减轻 食欲减退或厌食 头痛 迟发性运动障碍 总评:A、与其他病人相比的严重程度;B、与其他病人相比的痛苦程度 评分 S/T 0/0 0/0 0/0 0/0 0/0 0/0 0/0 0/0 0/0 0/0 0/0 0/0 0/0 0/0 0/0 0/0 0/0 0/0 0/0 0/0 0/0 0/0 0/0 0/0 0/0 0/0 0/0 0/0 0/0 0/0 0/0 0/0 0/0 0/0 0/0 0/0 S/T / / / / / / / / / / / / / / / / / / / / / / / / / / / / / / / / / / / / S/T / / / / / / / / / / / / / / / / / / / / / / / / / / / / / / / / / / / / S/T / / / / / / / / / / / / / / / / / / / / / / / / / / / / / / / / / / / / S/T / / / / / / / / / / / / / / / / / / / / / / / / / / / / //T / / / / / / / / / / / / / / / / / / / / / / / / / / / / / / / / / / / /
常用患者病情评估评分表

非特异性疾病病情程度评价和预后预测系统
APACHEⅡ(软件) 是目前临床上重症监护病房应用最广泛、最具权威的危重病病情评价系统。也可用于混合病种。临床应用:非特异性疾病病情程度评价和预后预测方法。适用于ICU、急诊。 数据采集应为病人入ICU或抢救开始后24小时内最差值.;评估前,需要检查生命体征,血常规,电解质,血气分析,肾功检查。如果暂时缺如,也可以以正常值替代,以得出分值,先行评估。事后修正。 APACHE Ⅱ、 Ⅲ评分,分3部分:急性生理学评分,年龄评分,慢性健康状况评分
RAPS分值 REMS分值 病死危险率 ≤7 ≤11 10% 8 16-17 50% ≥14 ≥24 100%
RAPS和REMS(RAPS - 评价院前或住院病人转运风险;REMS - 预测急诊病人的病死危险性) 评分注意事项: 参数取同一时间点 动态评分24小时最差值是指总分的最差值 血压最好由同一人反复测量,测量部位固定 测量外周血氧饱和的部位应固定
RAPS和REMS评分与病死危险性对应表
临床意义
分值越高,提示病情越重,死亡率越高。 动态分值反应病情演变和治疗效果 预测死亡率准确性:APACHE Ⅲ >Ⅱ>Ⅰ 局 限 性:急诊获取相关参数比较困难 注明:PaO2、FiO2(mmHg)填入时以小数为准,比如PaO2为75%,填0.75;FiO2为40%,则填0.40。
FMEA在抛光设备维修管理中的应用

FMEA在抛光设备维修管理中的应用摘要:FMEA(Failure Mode and Effect Analysis,失效模式和影响分析)是一种用来确定潜在失效模式及其原因的分析方法[1]。
本文结合了对NACHI不二越SPM23抛光设备在近几年的维修和管理,以实际事例说明了失效模式和影响分析对抛光设备进行风险评估的流程,较为详尽的阐述了FMEA的概念及FMEA在设备管理中的具体应用。
关键词:设备管理;失效模式; 影响分析;抛光设备硅片是重要的半导体制造材料。
半导体硅片制备工艺复杂,流程繁多,抛光工序是生产硅片时最后一道加工工序,也是最重要的一道工序,抛光设备的可靠性和稳定性将直接影响硅片表面几何参数,对硅片产量和良率起关键性作用。
FMEA作为一种用来确定潜在失效模式及其原因的分析方法,可以帮助设备管理人员从设备故障的因果关系出发,找出潜在的故障原因,提前分析故障主因以及可能对设备、对产品、对生产人员造成的影响,保障设备长期安全稳定的运行。
同时,FMEA能帮助设备管理人员建立出一套日常巡检、日常维修和定期保养的规则。
1FMEA在抛光设备维修管理中的应用介绍1.1 FMEA在设备维修管理中的作用在设备维修管理中,为了减少设备维修和消除设备故障,通常需要对设备各过程步骤和过程工作元素中人、机、料、环的功能和过程特性进行分析,找出设备潜在的故障风险点,评估设备每种故障的发生率(O)、失效后果(FE)、严重程度(S)和失效模式(FM),并找到失效原因(FC),针对失效原因做出预防控制,评估探测度(D),提高设备的可靠性和稳定性。
2使用失效模式和影响分析(FMEA)的具体步骤2.1抛光设备故障模式的统计根据抛光设备维修、保养的记录统计出各故障类型、发生率(O)和严重程度(S)。
设备维修应保存叫修记录、维修记录、审核记录等。
以此数据统计设备完好率,重复性故障和重大故障的宕机时长,对失效模式导致的影响有迹可循。
发生率(O)评估失效潜在故障要因的发生可能性,用数字1~10表示,数值越大代表发生率越高。
故障模式及影响分析

数是对潜在故障风险性的度量。风险顺序数越大,表明该故障模式对公司的影响越大,必须
采取纠正措施或预防措施,以努力减小 RPN 的值。 团队成员对各种故障模式的严重度(S)、频度(O)和不可探测度(D)的评定应一致。
意见不一致时,应通过讨论、调查、再研究,以获得一致。即使是对个别的 S、O、D 进行
修改也应取得基本一致意见。上述有关严重度(S)、频度(O)和不可探测度(D)的等级 划分并没有唯一的标准,可以根据企业自身的经验和产品的特点而定,但在同一企业内相类
测度定为 10。表 4 提供了不可探测度的参考评价标准。
表-4 不可探测度(D)评价等级表
探测性
评定准则
不可探测度
现行控制方法无法找出潜在原因,或根本没有现行的控 几乎不可能
10
制方法
很微小 现行控制方法只有极低的概率可以探测出潜在原因
9
微小
现行控制方法只有非常小的概率可以探测出潜在原因
8
很小
现行控制方法只有很少的机会可以探测出潜在原因
故障模式及影响分析
1 FMEA 简介
FMEA(故障模式及影响分析)是英文“Failure Mode and Effects Analysis”的缩写,也 译为失效模式与影响分析,是用于分析当前产品设计/过程设计可能导致的故障及后果的一 种技术方法,其充分利用员工的知识和创造能力,以规范化和文件化的 FMEA 分析表格来 辨认和评价可能发生的故障,并通过设计变更等措施防止这些故障的出现,或至少减少故障 的数量。20 世纪 50 年代中期,美国 Grumman 公司在生产一种新型飞机时,因为工程重大, 工程人员采用了一种故障分析的方法,来降低设计、生产的风险性,这就是今天 FMEA 的 雏形。随着 FMEA 在航空航天工业的成功运用,其他行业纷纷效仿,将 FMEA 移植到各自 的领域中,FMEA 技术得到了进一步的发展和完善。70 年代中期,美国发布了 FMEA 的军 用标准 MIL-STD-1629。80 年代,美国汽车业的三大巨头 FORD、GM、CRYSLER 将 FMEA 纳入 QS-9000 的行业标准中,并要求其供货商将使用 FMEA 作为质量管理的一部分。今天, FMEA 已经在全球得到了广泛应用。
危害因素(危险源)清单填制说明

危害因素(危险源)清单填制说明1 危险源辨识范围1.1 常规或非常规的活动:常规活动:供水、供电、供暖、幼儿托管、饮食加工、房屋租赁、房产管理、工程管理、医疗服务、离退休管理、保安、保洁、绿化、维修、防洪防汛、防雷防电等。
非常规活动:农药喷洒、紧急动火、动土、临时用电等。
1.2 所有进入作业场所的人员的活动:办公、生活、健身、娱乐、交通、其他。
1.3 作业场所的设施、设备:办公设施、生活设施、消防设施、供电设施、车辆。
2 危险源的辨识2.1作业活动信息的收集包括:a)场站、设备的设计信息,设备、设施之间的安全距离;b)设备、设施的运行情况;c)物料的物理形态、化学特性、物料要用手移动的距离和高度;d)生活配套设施和应急设施;e)生产过程中使用和产生的高温、高压、易燃、易爆、噪音、粉尘、有毒气体等,以及有害气体与主风向的关系;f)员工的不良习惯、心态、健康状况及违章操作等;g)自然条件中的气象及地质现象,如雷击、暴雨、洪水、地震等;h)机动车在道路行使可能遇到的人员、路况、车况、气候影响等。
2.2危险源辨识的时态和状态:过去、现在和将来三种时态及正常、异常和紧急三种状态。
2.3 危险源辨识的方法风险识别以事故预防,控制和减少事故及污染发生为指导思想,采用下列多种方法相结合的方式,对涉及到的全部危险源进行辨识。
a)现场观察:对作业活动、设备运转或系统活动进行现场观测,分析人员、工艺、设备运转存在的危险源;b)查阅资料:通过查阅事件、事故、职业病记录和台帐,可从中发现其存在的危险源;c)安全检查表:剖析系统,确定检查项目,按顺序编制表格,以提问或现场观察等方式确定检查项目的状况,确定危险源。
d)座谈:召集安全管理人员、专业技术人员、操作人员,集思广益、讨论分析作业活动或设备运转过程中存在的危险源。
2.4 危害因素识别的步骤a) 安全环保科负责组织各单位进行危害因素识别工作;b)各单位应召集具有现场安全管理经验、熟悉业务和工艺流程的人员组成辩识组,采用适当的方法对本部门本单位范围内的生产和服务过程进行危害因素识别,进行风险评价,填写《危害因素清单》和《重大风险清单》;c)各单位将《危害因素清单》和《重大风险清单》经本单位主管领导审批后报安全环保科一份备案,本单位留存一份。
FMEA评分表

8
≥1%,<2%
7
中等:一般与以前时有失效发生,但不占主要比例的过程相类似的工艺有关
≥0.2%,<1%
6
≥0.05%,<0.2%
5
≥0.01%,<0.05%
4
低:很少几次与相似过程有关的失效
≥0.001%,<0.01%
3
很低:很少几次与几乎完全相同的过程有关的失效
≥0.0001,<0.001 %
几乎肯定
1
9
后加工问题探测
在处理(加工)后由操作员通过目测、触觉和听觉方法对失效模式进行探测
微小
8
在来源处探测问题
由操作员通过目测,触觉和听觉方法站内失效模式探测或在处理(加工)后利用计数型工具(止/通规,数显工具)
很低
7
在加工后探测问题
在处理(加工)后由操作员利用计量型工具对失效模式进行探测或通过站内操作员利用计数型工具(止/通规,数显工具)
上等偏高
4
在源头探测问题
于站内通过自动控制模式进行失效模式探测,并自动锁定有差异部分于站内的预防进一步处理
高
3
错误探测和/或问题预防
于站内通过自动控制进行错误(原因)探测,探测到错误部分并防止有缺陷零件生产
非常高
2
探测方法不运用错误预防
透过工装夹具设计,机器设计或零件设计,进行错误(原因)预防;通过过程/产品设计防错,有缺陷零件不可能产生
≥0.001%,<0.01%
3
几乎一样的设计中,无可观察到的失效
≥0.0001,<0.001 %
2
非常低
通过预防措施消减失效的可能性
≤0.0001
1
3.DFMEA探测度评分表(D):
检维修工作危害分析JHA评价表(含LSR评分说明)

工作危害分析(JHA)评价表
编制:
审核:
日期:二〇二〇年九月二十七日
工作危害分析法(JHA)说明
本方法适用于检维修工作,以作业项目为单元,对作业过程伤害人的工作危害分析,由项目分管部门、项目负责人、检修人员、安全员等完成。
具有工作危害的10大作业均有安全规程,评价分析过程予以执行。
工作危害分析:
事故发生的可能性L;
事故后果的严重性S;
风险等级R,用公式表示:R= L×S
1.发生事故的可能性L判定准则,按表1取值:
表1
2.事故后果严重性S判定准则,按表2取值:
表2
3.
表3
工作危害分析(JHA)评价表
工作危害分析(JHA)评价表
工作危害分析(JHA)评价表
工作危害分析(JHA)评价表
工作危害分析(JHA)评价表
工作危害分析(JHA)评价表
工作危害分析(JHA)评价表
工作危害分析(JHA)评价表
工作危害分析(JHA)评价表。
- 1、下载文档前请自行甄别文档内容的完整性,平台不提供额外的编辑、内容补充、找答案等附加服务。
- 2、"仅部分预览"的文档,不可在线预览部分如存在完整性等问题,可反馈申请退款(可完整预览的文档不适用该条件!)。
- 3、如文档侵犯您的权益,请联系客服反馈,我们会尽快为您处理(人工客服工作时间:9:00-18:30)。
1.影响范围限于设备附近2.非毒性物质外泄,不需其他单位协助3.服务效率降低
1.部分或全部仪器设备停工1日以下2.财务损失在50万元以下
病人访客
仅需评估无须额外医疗处置
10
员工
可能导致暂时性失能(伤害)
1.工作中可能造成感官上的明显不舒服(原员工曾反映或抱怨)2.有害物接触2-4小时(含)3.处于噪音区80-84dB/8h
1.长期工作可能造成必要的医疗,但可能在医疗后恢复机能2.有害物接触4-6小时(含)3.处于噪音区85-89dB/8h
1.范围扩及院内其他工作区(如该工作楼面以外)单位外2.有毒性物质外泄,但未发生中毒事件3.火警需外部支援4.主要之服务作业停止,如手术、门诊停止
1.部分或全部仪器设备停工3日至1周2.财务损失在150万元
表2危害严重程度(S)评分表
评分
人员安全(HS)
人员健康(HH)
影响范围(ER)
停工损失(TL)
1
员工
无明显危害
1.不会造成感官的不适或职业病2.有害物接触1小时(含)内
1.无明显危害2.服务未受到影响
1.不会造成生产停工2.财务损失20万以下
病人访客
不需任何评估或处置
5
员工
可能导致医疗的需求(或曾经发生惊吓情况)
病人访客
1.访客或病人死亡2.3名以上病人或访客住院
备注:严重度(S)=人员安全(HS)+人员健康(HH)+影响范围(ER)+停工损失(TL)
病人访客
2名病人或访客住院
20
员工
1.因意外导致员工死亡
2.员工自杀3.3名以上员工住院
1.长期工作可能造成永久性职业病2.有害物接触6-8小时(含)3.处于噪音区90dB/8h
1.范围扩及院外2.有毒性物质外泄,导致中毒事件3.火警需撤离
4.服务作业完全终止
1.部分或全部仪器设备停工1周以上2.财务损失超过200万以上
1.影响范围限于工作区附近(例如工作楼面)或于单位内2.非毒性物质外泄,需其他单位协助3.灾害初期即已控制4.部分服务不完全
1.部分或全部仪器设备停工1-3日2.财务损失在100万元以下
病人访客
2名访客或病人需额外医疗处置,但不需住院
15
员工
1.因意外导致员工永久性伤害2.2名员工住院3.3名以上员工因病需停止工作