工艺分析方法
新工艺的技术经济分析方法
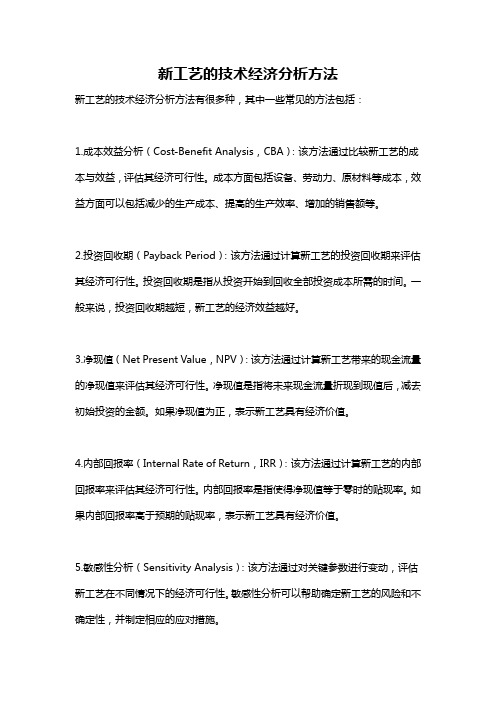
新工艺的技术经济分析方法
新工艺的技术经济分析方法有很多种,其中一些常见的方法包括:
1.成本效益分析(Cost-Benefit Analysis,CBA):该方法通过比较新工艺的成本与效益,评估其经济可行性。
成本方面包括设备、劳动力、原材料等成本,效益方面可以包括减少的生产成本、提高的生产效率、增加的销售额等。
2.投资回收期(Payback Period):该方法通过计算新工艺的投资回收期来评估其经济可行性。
投资回收期是指从投资开始到回收全部投资成本所需的时间。
一般来说,投资回收期越短,新工艺的经济效益越好。
3.净现值(Net Present Value,NPV):该方法通过计算新工艺带来的现金流量的净现值来评估其经济可行性。
净现值是指将未来现金流量折现到现值后,减去初始投资的金额。
如果净现值为正,表示新工艺具有经济价值。
4.内部回报率(Internal Rate of Return,IRR):该方法通过计算新工艺的内部回报率来评估其经济可行性。
内部回报率是指使得净现值等于零时的贴现率。
如果内部回报率高于预期的贴现率,表示新工艺具有经济价值。
5.敏感性分析(Sensitivity Analysis):该方法通过对关键参数进行变动,评估新工艺在不同情况下的经济可行性。
敏感性分析可以帮助确定新工艺的风险和不确定性,并制定相应的应对措施。
以上方法并不是互相独立的,常常会结合使用,以全面评估新工艺的技术经济可行性。
工艺技术方案常用的评价方法

工艺技术方案常用的评价方法工艺技术方案常用的评价方法作为一个职业策划师,我们需要为客户设计工艺技术方案,并对其进行评估,以确保方案的可行性和优越性。
评价方法是这个过程中必不可少的一环。
本文将介绍六种常用的工艺技术方案评价方法。
一、SWOT分析法SWOT分析法是一种常用的评价工具,它通过分析工艺技术方案的优势、劣势、机会和威胁,来评估方案的可行性。
在使用SWOT分析法时,需要考虑到方案的内部和外部环境,以及竞争对手的情况。
通过这种方法,我们可以找到方案的优势和劣势,并为改进方案提供有利的建议。
二、成本效益分析法成本效益分析法是一种以成本和收益为基础的评估方法。
通过分析方案的成本和预计的收益,我们可以评估方案的经济性,并为客户提供可行的建议。
这种方法可以帮助我们发现方案中的不必要的开支,并帮助客户节约成本。
三、权衡分析法权衡分析法是一种考虑多个因素的评估方法。
我们可以将需要考虑的因素列出来,然后对它们进行评分,最终计算出总分。
这种方法可以帮助我们更全面地考虑方案中的各个方面,并为客户提供更好的建议。
四、专家评估法专家评估法是一种通过请专家来评估方案的可行性的评估方法。
专家可以是相关领域的专业人士,也可以是有经验的从业者。
通过专家的评估,我们可以获得更专业的建议,并为客户提供更优秀的工艺技术方案。
五、实验法实验法是一种通过实验来评估方案可行性的评估方法。
我们可以在实验室或现场进行实验,以评估方案的可行性和优越性。
这种方法可以帮助我们更准确地了解方案的效果,并为客户提供更好的建议。
六、比较分析法比较分析法是一种通过比较不同方案来评估方案的可行性的评估方法。
我们可以将不同方案的优劣进行比较,以选择最优的方案。
这种方法可以帮助我们更好地了解方案的差异,并为客户提供更优秀的工艺技术方案。
总结工艺技术方案评价是我们为客户设计方案的重要一环。
在评价过程中,我们需要考虑到方案的不同方面,并选用合适的评价方法。
SWOT分析法、成本效益分析法、权衡分析法、专家评估法、实验法和比较分析法都是常用的评价方法,我们可以根据具体情况选择适合的方法来评价方案。
关键工艺技术分析
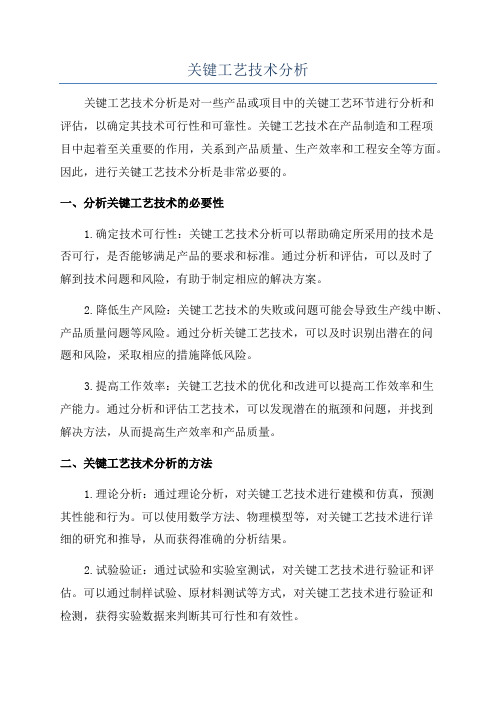
关键工艺技术分析关键工艺技术分析是对一些产品或项目中的关键工艺环节进行分析和评估,以确定其技术可行性和可靠性。
关键工艺技术在产品制造和工程项目中起着至关重要的作用,关系到产品质量、生产效率和工程安全等方面。
因此,进行关键工艺技术分析是非常必要的。
一、分析关键工艺技术的必要性1.确定技术可行性:关键工艺技术分析可以帮助确定所采用的技术是否可行,是否能够满足产品的要求和标准。
通过分析和评估,可以及时了解到技术问题和风险,有助于制定相应的解决方案。
2.降低生产风险:关键工艺技术的失败或问题可能会导致生产线中断、产品质量问题等风险。
通过分析关键工艺技术,可以及时识别出潜在的问题和风险,采取相应的措施降低风险。
3.提高工作效率:关键工艺技术的优化和改进可以提高工作效率和生产能力。
通过分析和评估工艺技术,可以发现潜在的瓶颈和问题,并找到解决方法,从而提高生产效率和产品质量。
二、关键工艺技术分析的方法1.理论分析:通过理论分析,对关键工艺技术进行建模和仿真,预测其性能和行为。
可以使用数学方法、物理模型等,对关键工艺技术进行详细的研究和推导,从而获得准确的分析结果。
2.试验验证:通过试验和实验室测试,对关键工艺技术进行验证和评估。
可以通过制样试验、原材料测试等方式,对关键工艺技术进行验证和检测,获得实验数据来判断其可行性和有效性。
3.现场观察:通过对现场生产过程的观察和调研,对关键工艺技术进行实地分析。
可以观察工艺操作、设备状况等,了解关键工艺技术的实际应用情况,发现问题和潜在风险。
4.经验总结:通过对历史数据和经验总结,对关键工艺技术进行评估和分析。
可以调研类似产品或项目的实施情况,借鉴其他企业或项目的经验教训,从而对关键工艺技术进行分析和判断。
三、关键工艺技术分析的内容1.技术可行性分析:包括对关键工艺技术的原理、优点和不足进行分析和评估,确定其可行性和可靠性。
2.风险评估:对关键工艺技术的潜在风险进行评估,识别出可能导致技术失败或问题的因素和瓶颈。
工艺安全分析方法
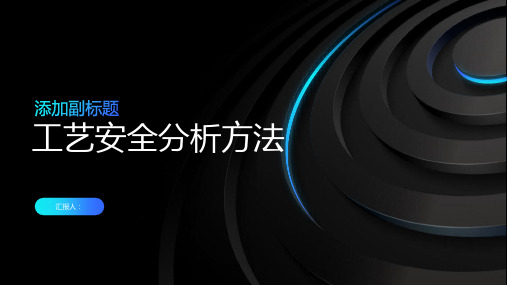
优化操作流程: 根据分析结果, 优化操作流程, 提高工作效率和 生产安全性
培训员工:根据 分析结果,对员 工进行培训,提 高员工的安全意 识和操作技能
故障树分析
定义和目的
故障树分析:是 一种系统安全分 析方法,通过构 建故障树模型, 分析系统故障的
原因和影响。
目的:识别和 评估系统潜在 的故障风险, 为改进系统安 全性提供依据。
工艺Hale Waihona Puke 全分析方法汇报人:目录
添加目录标题
01
工艺安全分析方法概 述
02
安全检查表分析
04
危险与可操作性分析
05
工艺危害分析
故障树分析
03
06
添加章节标题
工艺安全分析方 法概述
定义和作用
工艺安全分析方法:用于评估工艺过程中潜在的危险和危害,并提出相应的预防和控制措施。
定义:通过系统地收集和分析工艺过程中的各种信息,识别潜在的危险和危害,并提出相应 的预防和控制措施。
定期进行安全 检查,及时发 现并消除安全
隐患
优化工艺流程, 降低风险
建立应急响应 机制,提高应 对突发事件的
能力
安全检查表分析
安全检查表制定
确定检查项目:根据工艺流程、设备、 操作等确定检查项目
制定检查标准:根据国家标准、行业标 准、企业标准等制定检查标准
制定检查方法:根据检查项目的特点, 选择合适的检查方法
故障树的建立和分析步骤
确定故障树的目的和范围 收集和整理相关数据 建立故障树模型 分析故障树的逻辑关系 计算故障树的概率 提出改进措施和预防措施
故障树分析的应用和限制
应用:用于分析复杂系统的故障原因和影响 限制:无法处理非确定性因素和随机事件 应用:用于评估系统安全性和可靠性 限制:需要专业知识和经验进行建模和评估
工业工程7大手法

工业工程7大手法工业工程是一门综合性的学科,旨在通过系统地设计、改进和优化生产过程,提高生产效率和质量。
在实际操作中,工业工程师们常常使用一些特定的手法来解决问题和改善工作流程。
本文将介绍工业工程中的7大手法,帮助读者更好地了解和应用这些方法。
第一大手法:时间研究法时间研究法是工业工程中常用的一种测量和分析工作时间的方法。
通过对工作过程中的各个环节进行观察和记录,可以准确地了解每个环节所花费的时间和各个环节之间的关系。
借助时间研究法,工业工程师可以找出工作过程中的瓶颈和低效环节,并提出相应的改善措施,以提高工作效率。
第二大手法:价值流分析法价值流分析法是一种通过对生产过程中的价值流进行分析,找出其中的浪费和瓶颈,并提出改善措施的方法。
通过绘制价值流图,工业工程师可以清晰地看到各个环节之间的关系,找出不必要的环节和浪费的资源,从而优化整个生产过程,提高生产效率和质量。
第三大手法:工艺分析法工艺分析法是一种通过对生产工艺进行分析和评估,找出其中的问题和改进空间的方法。
通过对工艺流程的详细分解和分析,工业工程师可以发现工艺中存在的不合理之处,并提出相应的改进措施。
工艺分析法可以帮助企业提高生产效率、降低成本,提高产品质量。
第四大手法:人机工程学人机工程学是一门研究人与机器之间的交互关系,以提高工作效率和人机适应性的学科。
工业工程师可以运用人机工程学的原理和方法,对工作环境、工作设备和工作流程进行优化和改进,以提高工作效率和员工的工作满意度。
第五大手法:设备维护管理设备维护管理是一种通过合理的设备维护和保养,延长设备使用寿命,提高设备可靠性和稳定性的方法。
通过制定合理的设备维护计划、定期检修和维护设备,可以减少设备故障和停机时间,提高生产效率。
第六大手法:质量管理质量管理是一种通过制定和实施质量管理体系,提高产品和服务质量的方法。
通过建立质量控制和质量保证体系,工业工程师可以对生产过程进行全面控制和管理,确保产品和服务的质量符合要求,提高客户满意度。
工艺过程设计的步骤与分析

工艺过程设计的步骤与分析1.收集和分析产品信息:包括产品的特点、要求、用途等。
了解产品的基础信息,为后续工艺过程的确定提供依据。
2.确定产品加工流程:根据产品的特点与需求,确定产品的加工流程。
这包括了原材料的选择、加工方法的确定等。
3.选择加工设备:根据产品的加工流程,选择适合的加工设备。
考虑设备的生产能力、稳定性、维护成本等因素。
4.制定工艺参数:根据产品的特点与要求,制定出合理的工艺参数。
包括温度、压力、速度等。
这些参数对产品的质量和效率有着重要的影响。
5.制定操作规程:根据产品的工艺参数,制定出相应的操作规程。
包括操作的顺序、操作的要点等。
操作规程的正确执行是保证产品质量的重要因素。
6.制定质量检验标准:根据产品的特点与要求,制定质量检验标准。
包括外观检查、尺寸检查等。
对于关键性部位,可以制定更严格的检验标准。
7.制定安全操作规程:根据产品的特点与工艺过程的危险性,制定相应的安全操作规程。
包括操作人员的安全防护措施、设备的安全使用等。
8.进行工艺过程验证:制定出工艺过程后,需要进行工艺过程验证。
通过试验、检验等方法,验证工艺过程的正确性和可行性。
在此过程中,可以发现并纠正工艺过程中存在的问题。
9.确定工艺过程文件:在工艺过程设计完成后,需要进行整理和归档,形成相应的工艺过程文件。
这些文件包括工艺流程图、工艺参数表、操作规程等,用于生产过程中的参考和规范。
1.工艺分析:对产品的工艺进行详细的分析。
包括了原材料的特点和要求、加工流程的合理性等。
工艺分析的目的是找出工艺过程中存在的问题,并制定相应的措施。
2.设备分析:对加工设备进行详细的分析。
包括了设备的性能、技术指标等。
设备分析的目的是选择适合的加工设备,保证产品的质量和效率。
3.人员分析:对操作人员进行分析。
包括了操作人员的技能水平、经验等。
人员分析的目的是保证操作人员能够正确执行操作规程,并提出相应的培训和提升计划。
4.环境分析:对工艺过程所处的环境进行分析。
工艺流程的数据采集与分析方法
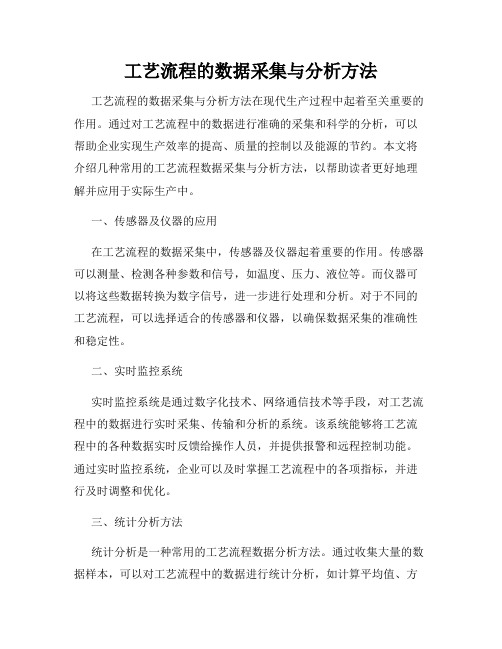
工艺流程的数据采集与分析方法工艺流程的数据采集与分析方法在现代生产过程中起着至关重要的作用。
通过对工艺流程中的数据进行准确的采集和科学的分析,可以帮助企业实现生产效率的提高、质量的控制以及能源的节约。
本文将介绍几种常用的工艺流程数据采集与分析方法,以帮助读者更好地理解并应用于实际生产中。
一、传感器及仪器的应用在工艺流程的数据采集中,传感器及仪器起着重要的作用。
传感器可以测量、检测各种参数和信号,如温度、压力、液位等。
而仪器可以将这些数据转换为数字信号,进一步进行处理和分析。
对于不同的工艺流程,可以选择适合的传感器和仪器,以确保数据采集的准确性和稳定性。
二、实时监控系统实时监控系统是通过数字化技术、网络通信技术等手段,对工艺流程中的数据进行实时采集、传输和分析的系统。
该系统能够将工艺流程中的各种数据实时反馈给操作人员,并提供报警和远程控制功能。
通过实时监控系统,企业可以及时掌握工艺流程中的各项指标,并进行及时调整和优化。
三、统计分析方法统计分析是一种常用的工艺流程数据分析方法。
通过收集大量的数据样本,可以对工艺流程中的数据进行统计分析,如计算平均值、方差、相关系数等。
统计分析可以帮助发现数据中的规律和趋势,以及确定异常值和异常原因。
同时,还可以应用统计模型进行预测和优化,提高工艺流程的稳定性和可控性。
四、数据挖掘技术数据挖掘技术是对大量数据进行深入挖掘和分析的一种方法。
通过数据挖掘,可以从工艺流程的数据中发现隐藏的模式、关联规则和异常信息。
数据挖掘可以帮助企业发现潜在的问题和机遇,以及进行精细化管理和优化。
常用的数据挖掘技术包括分类、聚类、关联规则等。
五、人工智能与机器学习人工智能与机器学习技术在工艺流程数据采集与分析中有着广泛的应用。
通过训练机器学习模型,可以对工艺流程的数据进行智能化分析和决策支持。
人工智能技术可以帮助识别工艺流程中的异常情况,并提供预测和优化建议。
同时,还可以利用机器学习算法进行模式识别和模型预测,以实现工艺流程的智能化控制。
产品工艺分析主要分析工艺难度作业时间和作业方法作业手段及分析

产品工艺分析主要分析工艺难度作业时间和作业方法作业手段及分析工业产品造型设计风格的形成,有诸多因素,它既与材料、结构有关,又与加工工艺密切相关,美观的造型设计,必须通过各种工艺手段将其制成物质产品,如果没有先进、合理、可行的工艺手段,再先进的结构和美观的造型,也只是纸上谈兵,而实现不了。
此外,即使是同一种款式的造型设计,采用相同的材料,由于工艺方法与水平的差异,也会产生相差十分悬殊的质量效果。
因此,在产品设计分析中,工艺分析是十分重要的内容。
制造工艺对产品的造型效果和质量影响很大,主要从以下几个方面反映出来。
一、工艺方法相同的材料和结构方式,采用不同的工艺方法,所获得的外观效果差异较大。
采用先进的工艺方法就能获得好的造型效果。
反之,即使很好的设计,如果粗制滥造或工艺落后,最终的产品也会一塌糊涂。
例如,同样的零件需要铸造成型,采用翻砂铸造所得零件表面粗糙,尺寸精度很低;如改用腊模型的精密铸造,其表面质量就可提高很多。
所以,较小的精密零件都采用精密铸。
对于金属切削机床,过去是由天轴皮带传动。
机床造型庞大,布局零乱,敞露,操作极不安全,而且由于转速低,工件表面精度不高。
采用齿轮传动方式后,机床造型就变得紧凑,并且是封闭的,操作安全多了。
随着工艺方法的不断更新,新近出现的数控机床、电脑控制的全自动机床,比过去的老机床经济、实用、美观。
加工出的零件质最高,速度快,工人劳动强度低。
在科学不断进步,工艺不断更新的今天,许多过去由手工操作的工作现在都由机器代替了,从而产品的质量有了大幅度提高。
工业容器的椭圆封头,现在已有统一标准。
由专门厂家按特定工艺生产。
比用手工弯板的单件生产质量有了很大提高、现在统一生产的椭圆封头外形圆滑,尺寸精确,生产效率高。
用它组装的锅炉、储罐、反应塔等容器质量也相应提高了。
再如,钢板的成型加工,采用手工方法卷板成型,其外观很难达到平滑整齐,且效率低,劳动强度大。
而采用机器弯板,冷冲工艺,成型准确,产品质量优良,外形美观,棱线分明、平直,生产效率高。
工艺分析范例(仅供参考,他写的并不好)
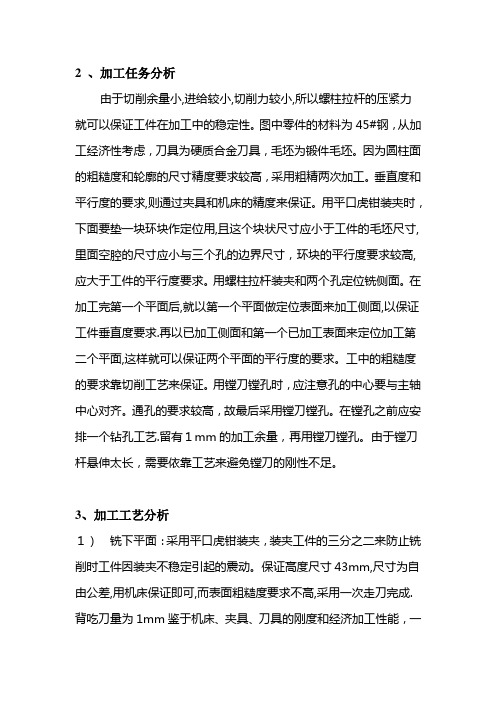
2 、加工任务分析由于切削余量小,进给较小,切削力较小,所以螺柱拉杆的压紧力就可以保证工件在加工中的稳定性。
图中零件的材料为45#钢,从加工经济性考虑,刀具为硬质合金刀具,毛坯为锻件毛坯。
因为圆柱面的粗糙度和轮廓的尺寸精度要求较高,采用粗精两次加工。
垂直度和平行度的要求,则通过夹具和机床的精度来保证。
用平口虎钳装夹时,下面要垫一块环块作定位用,且这个块状尺寸应小于工件的毛坯尺寸,里面空腔的尺寸应小与三个孔的边界尺寸,环块的平行度要求较高,应大于工件的平行度要求。
用螺柱拉杆装夹和两个孔定位铣侧面。
在加工完第一个平面后,就以第一个平面做定位表面来加工侧面,以保证工件垂直度要求.再以已加工侧面和第一个已加工表面来定位加工第二个平面,这样就可以保证两个平面的平行度的要求。
工中的粗糙度的要求靠切削工艺来保证。
用镗刀镗孔时,应注意孔的中心要与主轴中心对齐。
通孔的要求较高,故最后采用镗刀镗孔。
在镗孔之前应安排一个钻孔工艺.留有1mm的加工余量,再用镗刀镗孔。
由于镗刀杆悬伸太长,需要依靠工艺来避免镗刀的刚性不足。
3、加工工艺分析1)铣下平面:采用平口虎钳装夹,装夹工件的三分之二来防止铣削时工件因装夹不稳定引起的震动。
保证高度尺寸43mm,尺寸为自由公差,用机床保证即可,而表面粗糙度要求不高,采用一次走刀完成.背吃刀量为1mm鉴于机床、夹具、刀具的刚度和经济加工性能,一次铣削量不大,故采用Ø80硬质合金铣刀水平面切入的进给路线.根据切削用量手册查表得Vc=120m/min,由公式Vc=πdn/1000,求得转速n=Vc×1000/πd.即n=477.7≈480r/min.f取0.5mm/min,则进给速度为Vf=n×f=0.5×480=240,则Vf取240mm/min2)钻孔、镗孔:采用平口虎钳装夹,由于有精度要求,采用粗精两次加工.镗孔的背吃刀量为0.5mm。
粗加工时:用Ø15.5麻花钻.Vc=10m/min,由公式Vc=πdn/1000,求得转速n=Vc×1000/πd.即n=200r/min. f取0.1, 则进给速度为Vf=n×f=0.1×200=20, 则Vf取20mm/min.精加工时:用Ø16镗刀,Vc=80m/min,由公式Vc=πdn/1000,求得转速n=Vc×1000/πd.即n=1600r/min.由于镗杆悬伸量较长,镗刀的钢度不是很好,为了保证加工精度,所以f取0.075, 则进给速度为Vf=n×f=0.075×1600=120, 则Vf取120mm/min3)铣侧面:为了防止铣削时因螺母松动引起的震动。
制造工艺分析
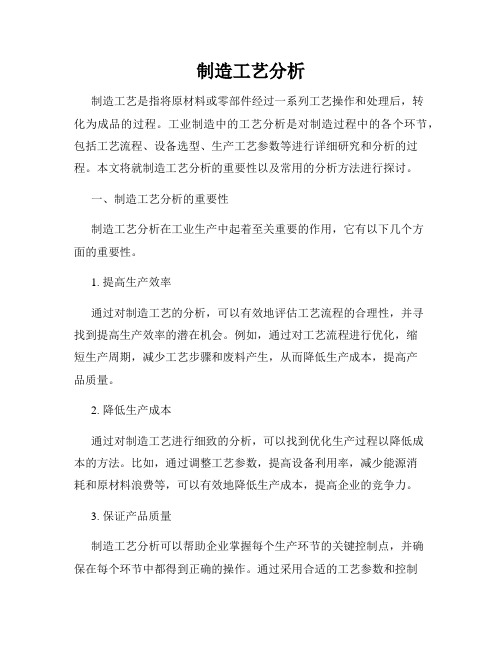
制造工艺分析制造工艺是指将原材料或零部件经过一系列工艺操作和处理后,转化为成品的过程。
工业制造中的工艺分析是对制造过程中的各个环节,包括工艺流程、设备选型、生产工艺参数等进行详细研究和分析的过程。
本文将就制造工艺分析的重要性以及常用的分析方法进行探讨。
一、制造工艺分析的重要性制造工艺分析在工业生产中起着至关重要的作用,它有以下几个方面的重要性。
1. 提高生产效率通过对制造工艺的分析,可以有效地评估工艺流程的合理性,并寻找到提高生产效率的潜在机会。
例如,通过对工艺流程进行优化,缩短生产周期,减少工艺步骤和废料产生,从而降低生产成本,提高产品质量。
2. 降低生产成本通过对制造工艺进行细致的分析,可以找到优化生产过程以降低成本的方法。
比如,通过调整工艺参数,提高设备利用率,减少能源消耗和原材料浪费等,可以有效地降低生产成本,提高企业的竞争力。
3. 保证产品质量制造工艺分析可以帮助企业掌握每个生产环节的关键控制点,并确保在每个环节中都得到正确的操作。
通过采用合适的工艺参数和控制技术,可以提高产品的稳定性和一致性,保证产品质量的稳定性和可靠性。
4. 促进技术创新通过对制造工艺的分析,可以及时发现新的工艺技术和设备,从而促进技术创新和产业升级。
定期进行工艺分析,了解最新的生产技术和市场需求,有助于企业保持竞争力,并根据市场需求调整和改进产品的制造工艺。
二、制造工艺分析的常用方法下面介绍几种常用的制造工艺分析方法。
1. 流程分析法流程分析法是指对整个制造流程进行细致的分析,包括原材料采购、生产过程、产品装配和成品检验等环节。
通过逐步分解和审查每个环节中的工艺步骤和参数,可以发现潜在的问题和改进的空间,并寻找到提高生产效率和品质的方法。
2. 时间研究法时间研究法是通过对每个工序的工时和运动进行观察和记录,来评估制造工艺的效率和性能。
通过时间研究,可以找出生产中的瓶颈和浪费,并提出改进建议,以提高生产效率和降低成本。
工艺流程的可靠性分析与改进
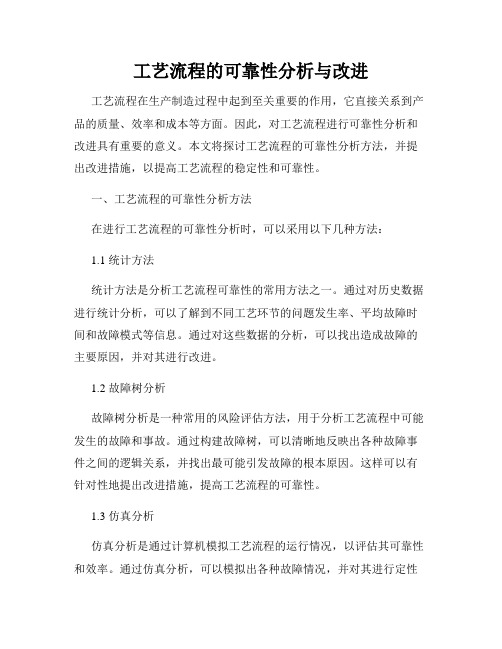
工艺流程的可靠性分析与改进工艺流程在生产制造过程中起到至关重要的作用,它直接关系到产品的质量、效率和成本等方面。
因此,对工艺流程进行可靠性分析和改进具有重要的意义。
本文将探讨工艺流程的可靠性分析方法,并提出改进措施,以提高工艺流程的稳定性和可靠性。
一、工艺流程的可靠性分析方法在进行工艺流程的可靠性分析时,可以采用以下几种方法:1.1 统计方法统计方法是分析工艺流程可靠性的常用方法之一。
通过对历史数据进行统计分析,可以了解到不同工艺环节的问题发生率、平均故障时间和故障模式等信息。
通过对这些数据的分析,可以找出造成故障的主要原因,并对其进行改进。
1.2 故障树分析故障树分析是一种常用的风险评估方法,用于分析工艺流程中可能发生的故障和事故。
通过构建故障树,可以清晰地反映出各种故障事件之间的逻辑关系,并找出最可能引发故障的根本原因。
这样可以有针对性地提出改进措施,提高工艺流程的可靠性。
1.3 仿真分析仿真分析是通过计算机模拟工艺流程的运行情况,以评估其可靠性和效率。
通过仿真分析,可以模拟出各种故障情况,并对其进行定性和定量分析。
通过对仿真结果的分析,可以找出工艺流程中的瓶颈和问题,并提出相应的改进策略,以提高工艺流程的可靠性。
二、工艺流程的改进措施在进行工艺流程的改进时,可以采取以下几种措施:2.1 优化工艺参数通过对工艺参数的优化,可以提高工艺流程的稳定性和可靠性。
可以通过设计实验,探索最佳的工艺参数组合,以提高产品的质量和生产效率。
此外,还可以借助数据分析工具,对工艺参数和产品质量之间的关系进行建模和分析,以找出参数变化对产品质量的影响,并提出相应的改进措施。
2.2 引入智能化技术随着智能化技术的发展,可以将其应用于工艺流程改进中。
例如,可以使用传感器和物联网技术对工艺过程进行实时监测和控制,以及自动化设备对工艺流程进行精细调控。
这些智能化技术的应用,可以提高工艺流程的稳定性和反应速度,减少人为因素对工艺流程的干扰,从而提高其可靠性。
工艺流程分析

工艺流程分析工艺流程分析是指对某项工艺进行详细的流程分析,了解每个环节的操作步骤、原料的加工方式和相关设备的使用等内容。
通过对工艺流程的分析,可以找出存在的问题和不合理之处,以便进行优化和改进,提高生产效率和产品质量。
下面是对某种工艺流程的分析,以供参考。
某种工艺流程主要包括原料加工、成型、加工、组装和包装等环节。
1. 原料加工环节:原料加工是工艺流程的第一步,也是非常关键的一步。
原料的质量和加工方式对产品的品质有着直接的影响。
在原料加工的环节中,可以采用物理或化学的方法对原料进行处理,以达到所需的性能。
此外,还需要考虑原料的储存条件和防潮、防尘等措施。
2. 成型环节:成型是将加工好的原料按照设计要求进行模具成型的过程。
在成型环节中,需要选择合适的模具,并进行模具的调试和加工参数的设置。
成型过程需要保证模具温度、压力和速度的稳定性,以保证产品的质量和外观。
同时,对于有特殊要求的产品,还需要进行后续的热处理等工序。
3. 加工环节:加工环节是对成型好的产品进行进一步的加工和加工。
加工过程包括表面处理、精度加工、孔加工等环节。
在加工环节中,需要选择合适的工装和工装夹具,并进行加工参数的优化和调试。
同时,还需要对加工过程进行监控和控制,以保证产品的质量和精度。
4. 组装环节:组装环节是将加工好的零部件按照设计要求进行组装,形成成品。
在组装环节中,需要保证每个零部件的准确性和精度,同时还需要进行装配顺序的合理安排和配件的正确选配。
对于大型和复杂的产品,还需要进行企业级和个人级的装配质量检查,以确保产品的安全性和可靠性。
5. 包装环节:包装环节是将装配好的成品进行包装和运输的环节。
在包装环节中,需要根据产品的大小、重量和特点,选择合适的包装材料和包装方式。
同时还需要进行运输包装和储存包装的区别,以确保产品在运输和储存过程中的安全和完整。
以上是对某种工艺流程的分析,通过对每个环节的详细分析,可以找出存在的问题和不合理之处,并进行改进和优化,从而提高生产效率和产品质量。
工艺工程师的分析手法

工艺工程师的分析手法工艺工程师的分析手法是指工艺工程师在解决生产过程中的问题或优化生产效率时所采用的一系列方法和技巧。
以下是几种常见的工艺工程师分析手法。
1. 流程分析:工艺工程师通过对生产过程中各个环节的详细分析,了解每个环节的工艺流程、设备使用和材料流动等情况,找出存在的问题并提出改进措施。
流程分析可以帮助工艺工程师识别生产中的瓶颈,并找出提升生产效率的方法。
2. 数据分析:工艺工程师通过收集和分析生产过程中的数据,以了解生产过程中存在的问题或可能造成问题的因素。
数据分析可以帮助工艺工程师了解生产过程中的实际状况,并帮助他们制定相应的改进计划。
3. 故障分析:当生产过程中出现故障时,工艺工程师会运用故障分析手法,对故障进行深入分析,找出故障发生的原因,并采取相应的措施进行修复。
故障分析可以帮助工艺工程师提高生产设备的可靠性,减少生产中的故障次数和停机时间。
4. 性能评估:在生产过程中,工艺工程师通过对产品的性能进行评估,以了解产品是否符合要求,并找出可能影响产品性能的因素。
性能评估可以帮助工艺工程师确定产品的质量状况,并提出相应的改进意见。
5. 成本分析:工艺工程师通过对生产过程中的成本进行分析,了解生产过程中的各项成本,并找出可以降低成本的方法。
成本分析可以帮助工艺工程师优化生产过程,降低生产成本,提高企业的竞争力。
6. 缺陷分析:当产品在生产过程中出现缺陷时,工艺工程师可以运用缺陷分析手法,对缺陷进行分析,找出导致缺陷的原因,并提出相应的改进意见。
缺陷分析可以帮助工艺工程师提高产品的质量水平,减少产品的不良率。
7. 设计优化:工艺工程师通过对产品和生产过程进行优化设计,以提高产品的质量和生产效率。
设计优化可以帮助工艺工程师降低生产成本,提高产品的竞争力。
这些分析手法通常是工艺工程师在实际工作中采用的一些常用方法和技巧。
通过应用这些分析手法,工艺工程师可以深入了解生产过程的各个环节,找出问题根源,并提出改进措施,从而提升生产效率,降低成本,提高产品质量,促进企业的可持续发展。
分析工艺流程的方法
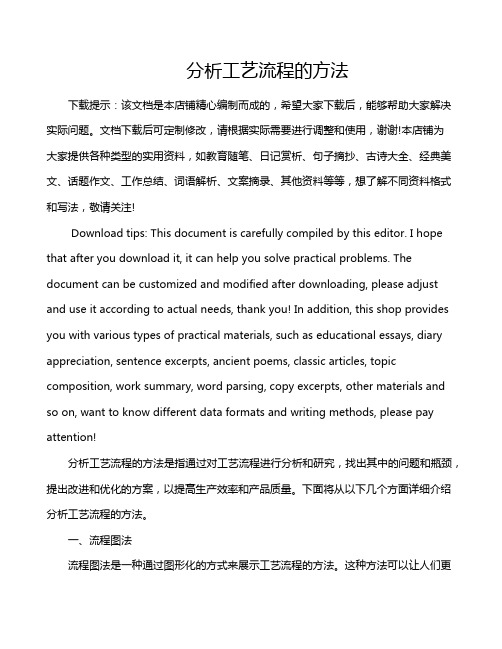
分析工艺流程的方法下载提示:该文档是本店铺精心编制而成的,希望大家下载后,能够帮助大家解决实际问题。
文档下载后可定制修改,请根据实际需要进行调整和使用,谢谢!本店铺为大家提供各种类型的实用资料,如教育随笔、日记赏析、句子摘抄、古诗大全、经典美文、话题作文、工作总结、词语解析、文案摘录、其他资料等等,想了解不同资料格式和写法,敬请关注!Download tips: This document is carefully compiled by this editor. I hope that after you download it, it can help you solve practical problems. The document can be customized and modified after downloading, please adjust and use it according to actual needs, thank you! In addition, this shop provides you with various types of practical materials, such as educational essays, diary appreciation, sentence excerpts, ancient poems, classic articles, topic composition, work summary, word parsing, copy excerpts, other materials and so on, want to know different data formats and writing methods, please pay attention!分析工艺流程的方法是指通过对工艺流程进行分析和研究,找出其中的问题和瓶颈,提出改进和优化的方案,以提高生产效率和产品质量。
工艺化需求分析方法概述
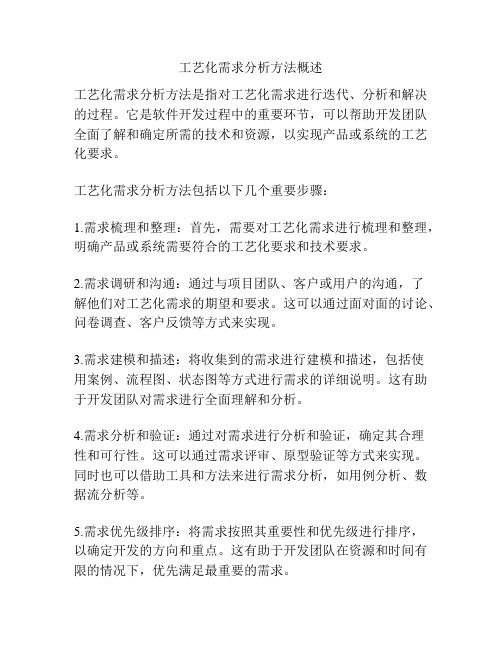
工艺化需求分析方法概述工艺化需求分析方法是指对工艺化需求进行迭代、分析和解决的过程。
它是软件开发过程中的重要环节,可以帮助开发团队全面了解和确定所需的技术和资源,以实现产品或系统的工艺化要求。
工艺化需求分析方法包括以下几个重要步骤:1.需求梳理和整理:首先,需要对工艺化需求进行梳理和整理,明确产品或系统需要符合的工艺化要求和技术要求。
2.需求调研和沟通:通过与项目团队、客户或用户的沟通,了解他们对工艺化需求的期望和要求。
这可以通过面对面的讨论、问卷调查、客户反馈等方式来实现。
3.需求建模和描述:将收集到的需求进行建模和描述,包括使用案例、流程图、状态图等方式进行需求的详细说明。
这有助于开发团队对需求进行全面理解和分析。
4.需求分析和验证:通过对需求进行分析和验证,确定其合理性和可行性。
这可以通过需求评审、原型验证等方式来实现。
同时也可以借助工具和方法来进行需求分析,如用例分析、数据流分析等。
5.需求优先级排序:将需求按照其重要性和优先级进行排序,以确定开发的方向和重点。
这有助于开发团队在资源和时间有限的情况下,优先满足最重要的需求。
6.变更管理和控制:需求是一个动态的过程,在开发过程中可能会有需求变更。
因此,需要建立一套变更管理和控制的机制,确保变更得到及时处理和沟通。
通过以上的工艺化需求分析方法,开发团队可以更好地理解和满足工艺化需求,确保产品或系统的工艺化要求被合理地满足。
这些方法提供了对需求进行全面分析和验证的途径,有助于减少开发过程中的错误和风险。
同时,它们也为产品或系统的工艺化要求的后续开发和优化提供了一个基础。
工艺化需求分析方法是软件开发过程中非常重要的一环,它帮助开发团队全面了解和确定所需的技术和资源,以实现产品或系统的工艺化要求。
下面将详细介绍一些常用的工艺化需求分析方法。
1. 需求梳理和整理:需求梳理是将模糊的需求想法和要求转化为可执行的计划,将模糊的想法和需求进行整理、梳理和明确。
工艺作品四步分析法
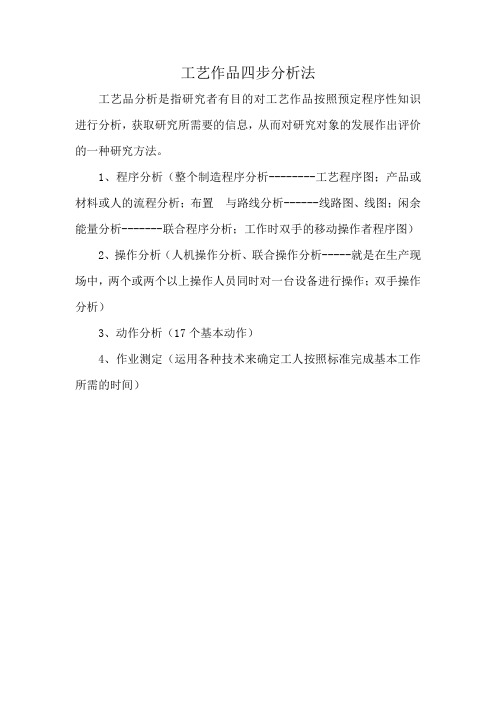
工艺作品四步分析法
工艺品分析是指研究者有目的对工艺作品按照预定程序性知识进行分析,获取研究所需要的信息,从而对研究对象的发展作出评价的一种研究方法。
1、程序分析(整个制造程序分析--------工艺程序图;产品或材料或人的流程分析;布置与路线分析------线路图、线图;闲余能量分析-------联合程序分析;工作时双手的移动操作者程序图)
2、操作分析(人机操作分析、联合操作分析-----就是在生产现场中,两个或两个以上操作人员同时对一台设备进行操作;双手操作分析)
3、动作分析(17个基本动作)
4、作业测定(运用各种技术来确定工人按照标准完成基本工作所需的时间)。
工艺方案分析
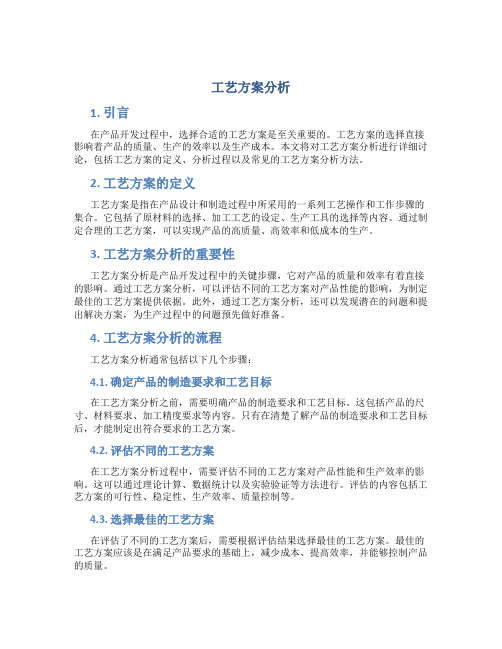
工艺方案分析1. 引言在产品开发过程中,选择合适的工艺方案是至关重要的。
工艺方案的选择直接影响着产品的质量、生产的效率以及生产成本。
本文将对工艺方案分析进行详细讨论,包括工艺方案的定义、分析过程以及常见的工艺方案分析方法。
2. 工艺方案的定义工艺方案是指在产品设计和制造过程中所采用的一系列工艺操作和工作步骤的集合。
它包括了原材料的选择、加工工艺的设定、生产工具的选择等内容。
通过制定合理的工艺方案,可以实现产品的高质量、高效率和低成本的生产。
3. 工艺方案分析的重要性工艺方案分析是产品开发过程中的关键步骤,它对产品的质量和效率有着直接的影响。
通过工艺方案分析,可以评估不同的工艺方案对产品性能的影响,为制定最佳的工艺方案提供依据。
此外,通过工艺方案分析,还可以发现潜在的问题和提出解决方案,为生产过程中的问题预先做好准备。
4. 工艺方案分析的流程工艺方案分析通常包括以下几个步骤:4.1. 确定产品的制造要求和工艺目标在工艺方案分析之前,需要明确产品的制造要求和工艺目标。
这包括产品的尺寸、材料要求、加工精度要求等内容。
只有在清楚了解产品的制造要求和工艺目标后,才能制定出符合要求的工艺方案。
4.2. 评估不同的工艺方案在工艺方案分析过程中,需要评估不同的工艺方案对产品性能和生产效率的影响。
这可以通过理论计算、数据统计以及实验验证等方法进行。
评估的内容包括工艺方案的可行性、稳定性、生产效率、质量控制等。
4.3. 选择最佳的工艺方案在评估了不同的工艺方案后,需要根据评估结果选择最佳的工艺方案。
最佳的工艺方案应该是在满足产品要求的基础上,减少成本、提高效率,并能够控制产品的质量。
4.4. 优化和改进工艺方案工艺方案的选择并不是一次性的过程,随着产品要求的改变或者新的技术的出现,工艺方案也需要不断进行优化和改进。
在实际生产中,可以通过持续改进的方法,不断提高工艺方案的性能和效果。
5. 常见的工艺方案分析方法工艺方案分析可以采用多种方法来进行。
工艺方案分析
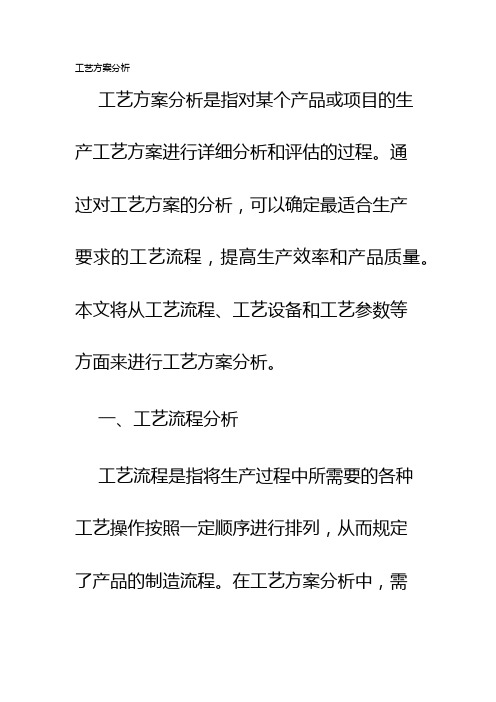
工艺方案分析工艺方案分析是指对某个产品或项目的生产工艺方案进行详细分析和评估的过程。
通过对工艺方案的分析,可以确定最适合生产要求的工艺流程,提高生产效率和产品质量。
本文将从工艺流程、工艺设备和工艺参数等方面来进行工艺方案分析。
一、工艺流程分析工艺流程是指将生产过程中所需要的各种工艺操作按照一定顺序进行排列,从而规定了产品的制造流程。
在工艺方案分析中,需要对工艺流程进行详细分析,确定各个工序的先后关系和操作要求。
对于不同的产品,其工艺流程也会有所不同。
在分析工艺流程时,需要考虑以下几个因素:1. 生产要求:根据产品的质量要求和产量要求确定工艺流程。
如果产品质量要求较高,可能需要增加一些质量控制的工序,如检测和测试工序;如果产量要求较高,可能需要采用一些自动化设备来提高生产效率。
2. 原材料特性:不同的原材料可能需要不同的处理工序。
在分析工艺流程时,需要考虑原材料的特性,以便确定合适的工艺操作。
3. 设备和工人的技术水平:工艺流程中所需要使用的设备和技术水平对工艺方案也有影响。
如果设备的性能不够稳定,可能需要增加一些工艺控制措施;如果工人的技术水平不高,可能需要改进操作方法或者提供培训。
二、工艺设备分析工艺设备是指在生产过程中所使用的各种设备,如机床、设备、工具等。
在工艺方案分析中,需要对工艺设备进行分析,以确定其适应性和可行性。
在分析工艺设备时,需要考虑以下几个因素:1. 设备的性能:设备的性能直接影响工艺的实施效果。
在分析工艺设备时,需要考虑设备的精度、可靠性、生产能力等因素,以便评估其对工艺方案的适应性。
2. 设备的成本:设备的成本也是考虑的因素之一。
在分析工艺设备时,需要综合考虑设备的购买成本、运行成本以及维护成本等因素,以确定其经济性。
3. 设备的适应性:不同的产品可能需要不同的设备。
在分析工艺设备时,需要考虑设备的适应性,以确定其是否满足工艺方案的要求。
三、工艺参数分析工艺参数是指在生产过程中需要控制和调节的各种参数,如温度、压力、转速等。
工艺技术方案分析四个方面

工艺技术方案分析四个方面工艺技术方案分析是一种对特定工艺技术方案进行评估和分析的方法。
它可以帮助工程师和决策者确定最合适的工艺技术方案,并为其后续实施提供指导。
在进行工艺技术方案分析时,可以从以下四个方面来进行评估和分析。
首先是工艺实施性分析。
在这方面,需要对工艺技术方案的实施可行性进行综合评估。
主要考虑工艺工程能力、材料供应情况、设备技术状况等方面的问题。
例如,某工艺技术方案需要用到大量的某种特殊材料,但市场上该材料的供应有限,那么这种方案在实施上可能会面临困难。
通过对这些实施性因素进行评估和分析,可以帮助决策者确定最合适的工艺技术方案。
其次是工艺技术性能评估。
在这方面,需要对工艺技术方案的性能进行评估。
主要考虑工艺工程的效率、产品质量、环境影响等方面的因素。
例如,某工艺技术方案可以提高产品的生产效率,但同时也会增加环境污染,那么在评估和分析时需要综合考虑这两个方面的因素。
通过对工艺技术的性能进行评估,可以为决策者提供决策依据,并确保选择的工艺技术方案能真正满足生产需求。
第三是工艺技术经济性评估。
在这方面,需要对工艺技术方案的经济效益进行评估。
主要考虑工艺工程的投资、生产成本、市场前景等方面的因素。
例如,某工艺技术方案需要巨大的资金投入,但根据市场预测,该产品的市场需求前景不明朗,那么在评估和分析时需要综合考虑投资和市场前景的因素。
通过对工艺技术的经济性进行评估,可以帮助企业决策者确定最合适的工艺技术方案,并最大程度地提高企业的经济效益。
最后是工艺技术安全性评估。
在这方面,需要对工艺技术方案的安全性进行评估。
主要考虑工艺工程的安全隐患、作业环境、人员培训等方面的因素。
例如,某工艺技术方案存在较大的安全隐患,需要采取特殊的防护措施,并对人员进行专门的培训,那么在评估和分析时需要综合考虑这些安全因素。
通过对工艺技术的安全性进行评估,可以帮助企业决策者确定最合适的工艺技术方案,并保障工作环境和员工的安全。
工艺PIE和PE有什么区别

工艺PIE和PE有什么区别工艺PIE和PE是两种常见的工艺分析方法,它们在工业生产中都扮演着重要的角色。
虽然它们都是用来帮助企业提高生产效率和质量,但在具体应用和方法上存在一些明显的区别。
工艺PIE的特点和应用工艺PIE是指工艺过程的瓶颈,即Process Impr-ovement Engine的缩写。
它通过分析生产过程中的瓶颈点和改进空间,帮助企业找到最大化生产效率和降低成本的方法。
工艺PIE的分析过程通常包括数据收集、制程模型构建、动态模拟和优化决策等步骤。
工艺PIE的应用范围非常广泛,可以用于生产线的优化、工艺参数的调整、设备的改进等方面。
通过工艺PIE分析,企业可以准确把握生产过程中的瓶颈,有针对性地进行优化和改进,从而提高生产效率和降低成本。
PE的特点和应用PE是Product Engineering的缩写,是一种通过对产品进行工程设计和分析的方法。
PE的目标是在产品开发阶段尽早发现和修复缺陷,以确保产品质量和性能达到预期要求。
PE通常涵盖了产品设计、原型制作、测试验证等环节。
PE的应用领域主要是产品开发和设计,涉及到原型制作、工程设计、性能测试等方面。
通过PE分析,企业可以及早发现产品存在的问题和缺陷,降低产品开发过程中的风险,提高产品的质量和市场竞争力。
工艺PIE和PE的区别虽然工艺PIE和PE都是用来帮助企业提高生产效率和产品质量的方法,但它们在具体应用和方法上存在一些明显的区别。
•应用领域不同:工艺PIE主要应用于生产过程中的优化和改进,而PE主要应用于产品设计和开发。
•分析对象不同:工艺PIE关注的是工艺过程中的瓶颈和改进空间,而PE关注的是产品的设计和性能。
•方法和工具不同:工艺PIE通常采用数据模型和优化算法进行分析,而PE通常使用CAD软件、原型制作等工具。
综上所述,工艺PIE和PE是两种不同的工艺分析方法,各自在生产优化和产品设计中发挥着重要作用。
企业根据实际需求可以选择合适的方法来提高生产效率和产品质量。
- 1、下载文档前请自行甄别文档内容的完整性,平台不提供额外的编辑、内容补充、找答案等附加服务。
- 2、"仅部分预览"的文档,不可在线预览部分如存在完整性等问题,可反馈申请退款(可完整预览的文档不适用该条件!)。
- 3、如文档侵犯您的权益,请联系客服反馈,我们会尽快为您处理(人工客服工作时间:9:00-18:30)。
数控加工工艺过程
数控加工工艺过程是利用切削刀具 在数控机床上直接改变加工对象的形状、 尺寸、表面位置、表面状态等,使其成 为成品或半成品的过程。
• 数控加工工艺的内容: • (1) 选择并确定进行数控加工的零件及内容; • (2) 对零件图纸进行数控加工的工艺分析; • (3) 数控加工的工艺设计; • (4) 对零件图纸的数学处理; • (5) 编写加工程序单; • (6) 按程序单制作控制介质; • (7) 程序的校验与修改; • (8) 首件试加工与现场问题处理; • (9) 数控加工工艺文件的定型与归档。
• 数控加工工艺守则
• 数控加工应遵守普通加工通用工艺守则的有关规 定遵守下表“数控加工工艺守则”的规定
项目
要求内容
加工前 的准 备
(1) 操作者必须根据机床使用说明书熟悉机床的性能、加工范围和精度, 并要熟练地掌握机床及其数控装置或计算机各部分的作用及操作方法。
(2) 检查各开关、旋钮和手柄是否在正确位置。 (3) 启动控制电气部分,按规定进行预热。 (4) 开动机床使其空运转,并检查各开关、按钮、旋钮和手柄的灵敏性及
数控加工工艺
自适应性较差,加工过程中可能遇到的所有问题必须事先精心考 虑,否则导致严重的后果。
3、制定数控加工工艺要进行零件图形的数学 处理和编程尺寸设定值的计算
编程尺寸并不是零件图上设计的尺寸的简 单再现,在对零件图进行数学处理和计算时,编 程尺寸设定值要根据零件尺寸公差要求和零件的 形状几何关系重新调整计算,才能确定合理的编 程尺寸。
数控加工的原理
通过把数字化了的刀具移动轨迹信息 (通常指CNC加工程序),传入数控机床 的数控装置,经过译码、运算,指挥执行 机构(伺服电机带动的主轴和工作台)控 制刀具与工件相对运动,从而加工出符合 编程设计要求的零件。
机床零
数控加工工艺是采用数控机床加工零件 时所运用各种方法和技术手段的总和, 应用于整个数控加工工艺过程。
•
实 例 : 如 右 图 :
• 可以先在普通机床上把底面和四个轮廓面加工好 (“基面先行”),其余的顶面、孔及沟槽安排在立 式加工中心上完成(工序集中原则),加工中心工 序按“先粗后精”、“先主后次”、“先面后孔” 等原则可以划分为如下15个工步:
• 1、粗铣顶面。
• 2、钻φ32、φ12等孔的中心孔(预钻凹坑)。
• 3.数控加工的工艺路线设计
• 数控加工的工艺路线设计与普通机床加工的常规工 艺路线拟定的区别主要在于它仅是几道数控加工工 艺过程的概括,而不是指从毛坯到成品的整个工艺 过程,而且要兼顾常规工序的安排,使之与整个工 艺过程协调吻合。
• (1) 工序的划分
• 划分方法 :
• ①按安装次数划分工序
• ②按所用刀具划分工序
• 3、钻φ32、φ12孔至φ11.5。
• 4、扩φ32孔至φ30。
• 5、钻3×φ6的孔至尺寸。
• 6、粗铣φ60沉孔及沟槽。 • 7、钻4×M8底孔至φ6.8。 • 8、镗φ32孔至φ31.7。 • 9、精铣顶面。 • 10、铰φ12孔至尺寸。 • 11、精镗φ32孔至尺寸。 • 12、精铣φ60沉孔及沟槽至尺寸。 • 13、φ12孔口倒角。 • 14、3×φ6、4×M8孔口倒角。 • 15、攻4×M8螺纹完成。
• ③按粗、精加工划分工序
• ④按加工部位划分工序
• (2) 加工顺序的安排 • ①尽量使工件的装夹次数、工作台转动次数、刀具更
换次数及所有空行程时间减至最少,提高加工精度和 生产率。 • ②先内后外原则 • ③精度要求较高的主要表面的粗加工应安排在次要表 面粗加工之前;大表面加工时,一般也需先加工大表 面。 • ④在同—次安装中进行的多个工步,应先安排对工件 刚性破坏较小的工步。 • ⑤在保证加工质量的前提下,可将粗加工和半精加工 合为一道工序。 • ⑥加工中容易损伤的表面(如螺纹等),应放在加工路 线的后面。
4、考虑进给速度对零件形状精度的影响
制定数控加工工艺时,选择切削用量要考虑 进给速度对加工零件形状精度的影响。
在数控加工中,刀具的移动轨迹是由插补运算 完成的。根据差补原理分析,在数控系统已定 的条件下,进给速度越快,则插补精度越低, 导致工件的轮廓形状精度越差。尤其在高精度 加工时这种影响非常明显。
数控加工工艺
所有工艺问题必须事先设计和安排好,并编入加工程序中。数控工艺不 仅包括详细的切削加工步骤,还包括工夹具型号、规格、切削用量和其 它特殊要求的内容,以及标有数控加工坐标位置的工序图等。在自动编 程中更需要确定详细的各种工艺参数。
2、数控加工工艺要求更严密、精确
普通加工工艺
加工时可以根据加工过程中出现的问题比较自由地进行人为调整。
• 1.数控加工内容的选择
• ①、选择原则及内容:
• (1) 普通机床无法加工的内容应作为优先选 择内容。
• (2) 普通机床难加工,质量也难以保证的内 容应作为重点选择内容。
• (3) 普通机床加工效率低,工人手工操作劳 动强度大的内容,可在数控机床尚有加工能 力的基础上进行选择。
• ②、不宜选择数控加工的内容: • (1) 需要用较长时间占机调整的加工内容。 • (2) 加工余量极不稳定,且数控机床上又无法自
7、数控加工程序的编写、校验与修改是数控 加工工艺的一项特殊内容
普通工艺中,划分工序、选择设备等重要内容对数控 加工工艺来说属于已基本确定的内容,所以制定数控 加工工艺的着重点在整个数控加工过程的分析,关键 在确定进给路线及生成刀具运动轨迹。
复杂表面的刀具运动轨迹生成需借助自动编程软件, 既是编程问题,当然也是数控加工工艺问题。这也是 数控加工工艺与普通加工工艺最大的不同之处。
•
• 图2 刀具选择图 • T0101——外轮廓粗加工:刀尖圆弧半径0.8mm,切深2mm,主轴转
速800r/min,进给速度150mm/min。 T0202——外轮廓精加工:刀尖圆弧半径0.8mm,切深0.5mm,主轴转 速1500r/min,进给速度80mm/min。 T0303——切槽:刀宽4mm,主轴转速450r/min,进给速度20mm/min。 T0404——加工螺纹:刀尖角60°,主轴转速400r/min,进给速度 2mm/r(螺距)。 T0505——钻孔:钻头直径16mm,主轴转速450r/min。 T0606——内轮廓粗加工:刀尖圆弧半径0.8mm,切深1mm,主轴转 速500r/min,进给速度100mm/min。 T0707——内轮廓精加工:刀尖圆弧半径0.8mm,切深0.4mm,主轴转 速800r/min,进给速度60mm/min。 3、数值计算 未知点坐标计算:P1(40.7,-33.52),P2(42.95,-53.36) 螺纹尺寸计算:螺纹外圆=32-0.2=31.8 4、编程 设经对刀后刀尖点位于(120,200),加工前各把刀已经完成对刀。 装夹ф50外圆,探出65mm,手动平端面。
·装夹ф50外圆,平端面,对刀,设置第1个工件原点。此 端面做精加工面,以后不再加工。
·调头装夹ф48外圆,平端面,测量总长度,设置第2个工 件原点(设在精加工端面上)
(3)换刀点:(120,200) (4)公差处理:尺寸公差取中值。
• 2、工艺处理 (1)工步和走刀路线的确定,按加工过程确定走刀路线如下: ·装夹ф50外圆表面,探出65mm,粗加工零件左侧外轮廓: 2×45°倒角,ф48外圆,R20,R16,R10圆弧。 ·精加工上述轮廓。 ·手工钻孔,孔深至尺寸要求。 ·粗加工孔内轮廓。 ·精加工孔内轮廓。 ·调头装夹ф48外圆,粗加工零件右侧外轮廓:2×45°倒角, 螺纹外圆,ф36端面,锥面,ф48外圆到圆弧面。 ·精加工上述轮廓。 ·切槽。 ·螺纹加工。 (2)刀具的选择和切削用量的确定,根据加工内容确定所用 刀具如图2所示:
数控加工工艺与普通加工工艺 的区别及特点
由于数控加工采用了计算机控制系统和数 控机床,使得数控加工具有加工自动化程度高、 精度高、质量稳定、生成效率高、周期短、设 备使用费用高等特点。在数控加工工艺上也与 普通加工工艺具有一定的差异。
1、数控加工工艺内容要求更加具体、详细
普通加工工艺
许多具体工艺问题,如工步的划分与安排、刀具的几何形状与尺寸、走 刀路线、加工余量、切削用量等,在很大程度上由操作人员根据实际经 验和习惯自行考虑和决定,一般无须工艺人员在设计工艺规程时进行过 多的规定,零件的尺寸精度也可由试切保证。
• (2) 零件的结构工艺性分析 • ①零件的内腔与外形应尽量采用统一的几何类
型和尺寸 • ②内槽圆角的大小决定着刀具直径的大小,所
以内槽圆角半径不应太小 • ③零件铣槽底平面时,槽底圆角半径r不要过
大。 • ④应尽可能在一次装夹中完成所有能加工表面
的加工,为此要选择便于各个表面都能加工的 定位方式;若需要二次装夹,应采用统一的基 准定位。
5、强调刀具选择的重要性
复杂形面的加工编程通常采用自动编程方 式,自动编程中必须先选定刀具再生成刀具中心 运动轨迹,因此对于不具有刀具补偿功能的数控 机床来说,若刀具预先选择不当,所编程序只能 推倒重来。
6、数控加工工艺的特殊要求
由于数控机床比普通机床的刚度高,所配的刀具也较好,因此 在同等情况下,数控机床切削用量比普通机床大,加工效率也 较高。
数控机床的功能复合化程度越来越高,因此现代数控加工工艺 的明显特点是工序相对集中,表现为工序数目少,工序内容多, 并且由于在数控机床上尽可能安排较复杂的工序,所以数控加 工的工序内容比普通机床加工的工序内容复杂。
由于数控机床加工的零件比较复杂,因此在确定装夹方式和夹 具设计时,要特别注意刀具与夹具、工件的干涉问题。
• 2.数控加工零件的工艺性分析
• 包括内容:产品的零件图样分析和结构工艺性 分析两部分。