论文集散控制
集散控制系统(DCS)
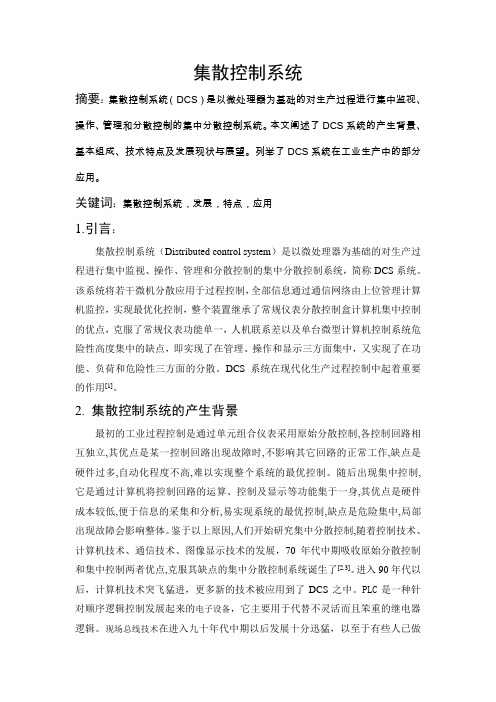
集散控制系统摘要:集散控制系统(DCS)是以微处理器为基础的对生产过程进行集中监视、操作、管理和分散控制的集中分散控制系统。
本文阐述了DCS系统的产生背景、基本组成、技术特点及发展现状与展望。
列举了DCS系统在工业生产中的部分应用。
关键词:集散控制系统,发展,特点,应用1.引言:集散控制系统(Distributed control system)是以微处理器为基础的对生产过程进行集中监视、操作、管理和分散控制的集中分散控制系统,简称DCS系统。
该系统将若干微机分散应用于过程控制,全部信息通过通信网络由上位管理计算机监控,实现最优化控制,整个装置继承了常规仪表分散控制盒计算机集中控制的优点,克服了常规仪表功能单一,人机联系差以及单台微型计算机控制系统危险性高度集中的缺点,即实现了在管理、操作和显示三方面集中,又实现了在功能、负荷和危险性三方面的分散。
DCS系统在现代化生产过程控制中起着重要的作用[1]。
2. 集散控制系统的产生背景最初的工业过程控制是通过单元组合仪表采用原始分散控制,各控制回路相互独立,其优点是某一控制回路出现故障时,不影响其它回路的正常工作,缺点是硬件过多,自动化程度不高,难以实现整个系统的最优控制。
随后出现集中控制,它是通过计算机将控制回路的运算、控制及显示等功能集于一身,其优点是硬件成本较低,便于信息的采集和分析,易实现系统的最优控制,缺点是危险集中,局部出现故障会影响整体。
鉴于以上原因,人们开始研究集中分散控制,随着控制技术、计算机技术、通信技术、图像显示技术的发展,70年代中期吸收原始分散控制和集中控制两者优点,克服其缺点的集中分散控制系统诞生了[2.3]。
进入90年代以后,计算机技术突飞猛进,更多新的技术被应用到了DCS之中。
PLC是一种针对顺序逻辑控制发展起来的电子设备,它主要用于代替不灵活而且笨重的继电器逻辑。
现场总线技术在进入九十年代中期以后发展十分迅猛,以至于有些人已做出预测:基于现场总线的FCS将取代DCS成为控制系统的主角。
集散控制DCS论文

3
a)用少量的过剩空气使黑液中的有机物完全燃烧,这是最关键的。
b)尽量提高炉膛内的燃烧温度,降低燃烧速度。
c)燃烧速度应保持稳定,碱炉操作要求送入炉内的热量稳定。
d)黑液喷嘴产生的黑液液滴的粒度范围是一项重要因素。
e)粒度适中的、活性的、多孔性的黑灰垫层也很关键。
f)黑灰垫层应产生足够的烟雾,避免发生SO2,形成粒性粉尘和酸性腐蚀。
DCS的关键技术在于网络,从上到下是树状拓扑和并行连续的链路结构,中间站联接计算机、现场仪器仪表和控制装置。
2.3MPI网
MPI用于连接多个不同的CPU或设备。MPI符合RS-485标准,具有多点通信的性质,MPI的波特率常设定为187.5kbps,接入到MPI网的设备称为一个节点,不分段的MPI网(无RS-485中继器的MPI网)可以最多有32个网络节点,仅用MPI接口构成的网络,称为MPI分支网(简称MPI网),两个或多个MPI分支网,用网间连接器或路由器连接起来,就能构成较复杂的网络结构,实现更大范围的设备互连,MPI分支网能够连接不同区段的中继器。
蒸发工段送来的浓黑液首先送往浓黑液槽,再经黑液泵进入圆盘蒸发器。在这里,黑液与碱回收炉出来的烟气相接触,使黑液再次浓缩,且可以吸收烟气的碱灰,减少了碱飞失,提高了碱回收率。而后圆盘蒸发器中的黑液自然溢流出来,进入入炉黑液槽,入炉黑液泵再将浓黑液泵往黑液加热器。经黑液加热器的加热后,经黑液喷枪高压喷入高温状态下的碱回收炉。在碱回收炉中,黑液经雾化、干燥后进行燃烧。部分燃烧后的黑液落到碱回收炉的垫层上,在垫层上,黑液中的无机物不断熔融,部分有机物热裂解成气体从垫层排出,部分有机物炭化为元素碳,供燃烧和还原硫酸钠之用,芒硝还原成硫化钠,部分有机物热裂解能更完全燃烧,含硅量高的熔融物能顺利流出。在硫酸盐法木浆碱回收工艺流程中,碱灰溶解槽中的碱灰液被送入芒硝黑液混合器,然后送入燃烧炉。麦草制浆则多采用烧碱法,若黑液碱回收沿用上述这样的流程,会形成大量碱灰液在燃烧炉、碱灰溶解槽及黑液中间槽内循环、沉淀,造成能源损耗,影响工艺流程的畅通。根据麦草浆黑液燃烧特性,让碱回收炉燃烧产生的碱灰直接进入绿液溶解槽。静电除尘器排出的碱灰进入碱灰溶解槽形成碱灰液,然后泵入绿液溶解槽。溶解槽中的绿液送苛化工段进行苛化,从而回收麦草浆中的碱。
集散控制系统的研究

烂烈:垫凰集散控制系统的研究刘卫东(河南未来铝业(集团)有限公司,河南焦作454171)脯羁随着科学技术的飞跃发展,人们为了提高生产效率对自动化程度的要求越来越高。
相应地对控制的要求也越来越复杂。
为了满足这些要求,自控人员经过长期努力终于研制出能够适应恶略环境和复杂控制要求的控制系绫——.集散控制系统。
本文通过对集散控制系统近三十年发展历程的回顾,阐明其卓越的技术特点,并介绍了其未来发展方向。
鹾莲枣j初集散控制系统;产生;特点;组成;方向1引言集敖控制系统(D i st r i but edc ont r ol s ys t em)是以微处理器为基础的对生产过程进行集中监视、操作、管理和分散控制的集中分散控制系统,简称D C S系统。
该系统将若干台微机分散应用于过程控制,全部信息通过通信网络由上位管理计算饥监控,实现最优化控制,整个装置继承了常规仪表分散控制和计算初集中控制的优点,克服了常规仪表功能单一,人一机联系差以及单台微型计算机控制系统危险性高度集中的缺点,既实现了在管理、操作和显示三方面集中,又实现了在功能、负荷和危险性三方面的分散。
因此,D CS系统在现代化生产过程控制中起着越来越重要的作用。
2集散控制系统的产生上世纪30年代40年代,工业自动化装置采用的是分散性控制系统。
所有设备都是独立运行,不联网控制。
随后采用了气动、电动模拟仪表组成过程控制系统,在—定程度上实现了集中监视、操作和分散控制。
最致命的就是老系统之间不便于实现通信,很难分级控制和综合管理。
第三次科技革命开始后,随着计算机技术的发展,人们开始尝试将计算机用于i黜制。
试图利用计算机所具有的功能特点,来克服常规模拟仪表的局5艮忙已但当时采用的办法是用一台计算机控制几十甚至上百个回路,危险性很高,这就是所谓的“危险集中”。
若采用双机双工系统,虽可以提高系统的可靠性,但成本太高,经济性很差,用户难以接受。
直到上世纪70年代开始,随眷十算机技术的日渐成熟,大规模集成电路及微处理器的诞生后,人们开始思考是否能将“危险分散”。
集散控制系统安全性浅析w
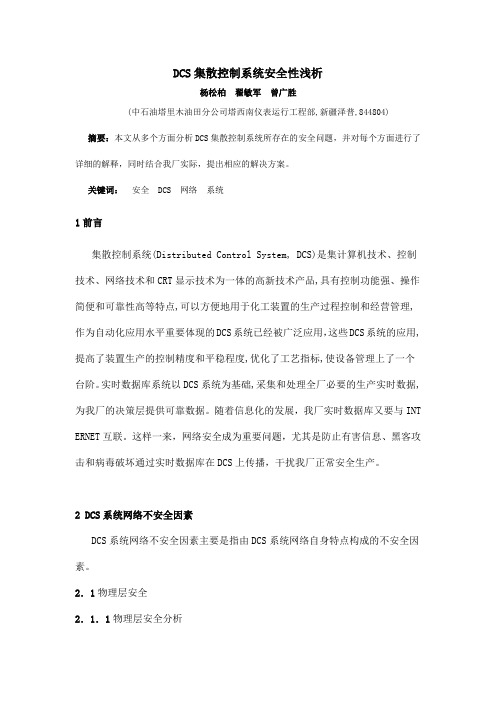
DCS集散控制系统安全性浅析杨松柏翟敏军曾广胜(中石油塔里木油田分公司塔西南仪表运行工程部,新疆泽普,844804) 摘要:本文从多个方面分析DCS集散控制系统所存在的安全问题,并对每个方面进行了详细的解释,同时结合我厂实际,提出相应的解决方案。
关键词:安全DCS 网络系统1前言集散控制系统(Distributed Control System, DCS)是集计算机技术、控制技术、网络技术和CRT显示技术为一体的高新技术产品,具有控制功能强、操作简便和可靠性高等特点,可以方便地用于化工装置的生产过程控制和经营管理,作为自动化应用水平重要体现的DCS系统已经被广泛应用,这些DCS系统的应用,提高了装置生产的控制精度和平稳程度,优化了工艺指标,使设备管理上了一个台阶。
实时数据库系统以DCS系统为基础,采集和处理全厂必要的生产实时数据,为我厂的决策层提供可靠数据。
随着信息化的发展,我厂实时数据库又要与INT ERNET互联。
这样一来,网络安全成为重要问题,尤其是防止有害信息、黑客攻击和病毒破坏通过实时数据库在DCS上传播,干扰我厂正常安全生产。
2 DCS系统网络不安全因素DCS系统网络不安全因素主要是指由DCS系统网络自身特点构成的不安全因素。
2.1物理层安全2.1.1物理层安全分析网络的物理层不安全因素主要指网络周边环境和物理特性引起的网络设备和线路的不可用,而造成网络系统的不可用,它是整个网络系统安全的前提。
即保证网络通信线路的安全,物理设备的安全,防止设备掉线。
2.1.2物理层安全解决方案环境安全:对系统所在环境的安全保护,如区域保护和灾难保护。
DCS的控制室和机柜间的布局、地板样式、墙壁类型、照明方式、地磁电磁干扰、隔断选择、隔音效果、空气洁净度保证、恒温、恒湿及通风设计等,这其中应该着重强调的是空气洁净度保证。
空气洁净度保证是为了避免由于空气中含尘量过高,进入机柜内卡件、电源等设备,导致设备热量不能及时散发从而出现电路故障。
集散控制系统原理及应用
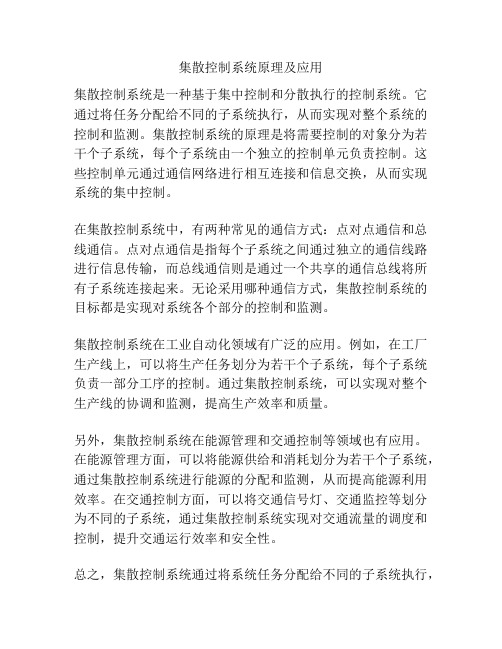
集散控制系统原理及应用
集散控制系统是一种基于集中控制和分散执行的控制系统。
它通过将任务分配给不同的子系统执行,从而实现对整个系统的控制和监测。
集散控制系统的原理是将需要控制的对象分为若干个子系统,每个子系统由一个独立的控制单元负责控制。
这些控制单元通过通信网络进行相互连接和信息交换,从而实现系统的集中控制。
在集散控制系统中,有两种常见的通信方式:点对点通信和总线通信。
点对点通信是指每个子系统之间通过独立的通信线路进行信息传输,而总线通信则是通过一个共享的通信总线将所有子系统连接起来。
无论采用哪种通信方式,集散控制系统的目标都是实现对系统各个部分的控制和监测。
集散控制系统在工业自动化领域有广泛的应用。
例如,在工厂生产线上,可以将生产任务划分为若干个子系统,每个子系统负责一部分工序的控制。
通过集散控制系统,可以实现对整个生产线的协调和监测,提高生产效率和质量。
另外,集散控制系统在能源管理和交通控制等领域也有应用。
在能源管理方面,可以将能源供给和消耗划分为若干个子系统,通过集散控制系统进行能源的分配和监测,从而提高能源利用效率。
在交通控制方面,可以将交通信号灯、交通监控等划分为不同的子系统,通过集散控制系统实现对交通流量的调度和控制,提升交通运行效率和安全性。
总之,集散控制系统通过将系统任务分配给不同的子系统执行,
实现对整个系统的控制和监测。
它在工业自动化、能源管理和交通控制等领域都具有广泛的应用前景。
集散控制系统综述 (2)
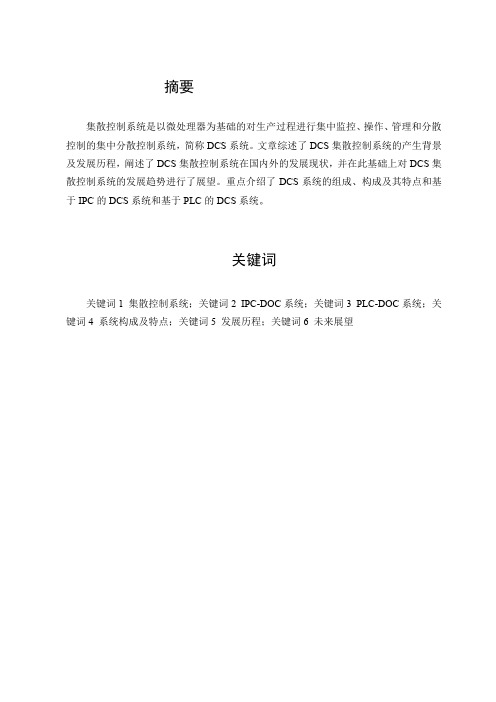
摘要集散控制系统是以微处理器为基础的对生产过程进行集中监控、操作、管理和分散控制的集中分散控制系统,简称DCS系统。
文章综述了DCS集散控制系统的产生背景及发展历程,阐述了DCS集散控制系统在国内外的发展现状,并在此基础上对DCS集散控制系统的发展趋势进行了展望。
重点介绍了DCS系统的组成、构成及其特点和基于IPC的DCS系统和基于PLC的DCS系统。
关键词关键词1集散控制系统;关键词2 IPC-DOC系统;关键词3PLC-DOC系统;关键词4 系统构成及特点;关键词5发展历程;关键词6未来展望前言集散控制系统 (Distributed Control System, 简称DCS)是计算控制系统发展到一定阶段的产物。
它是以微处理机为核心,采用数据通讯技术和图形显示技术的新型计算机控制系统,它是一种利用计算机技术对生产过程进行集中监视、操作、管理和现场前端分散控制相统一的新型控制技术。
该系统能够完成直接数字控制、顺序控制、批量控制、数据采集与处理、多变量解藕控制以及最优控制等功能,在先进的集散型控制系统中,还包含有生产的指挥、调度和管理功能。
1975年,美国Honeywell公司推出了第一套集散控制系统TDC- 2000,它特点就是:集中管理、集中操作,分散控制、分散危险,特别适合大规模生产过程和大型设备的管理、控制和操作,随着计算机性能价格比的不断提高、通用计算机技术、控制理论与技术、显示技术的发展,特别是网络技术的发展,集散控制系统逐渐发展起来。
而促进集散控制系统不断向前发展的主要动力在于应用需求的不断提高,特别是石油化工生产过程中的应。
因此它的发展一方面向现场深入,另一方面向高层发展,特别是近年来开放系统体系结构的发展,各种网络通信规约的标准化,克服了过去各种计算机系统不能互相通信的“孤岛”现象,使得面向过程控制的集散控制系统和面向生产管理与调度的管理信息系统MIS可以互相传递信息, 出现了将DCS与MIS集成在一起的计算机集成制造系统CIMS和计算机集成过程控制CIPS,这种系统使得企业自动化水平大大提高,计算机不仅可以进行单个设备、生产工序的控制,可以将个别的生产单元联系在一起进行协调控制,实现整个生产过程的总体优化,进一步对全厂的生产调度、物料平衡、成本控制、库存控制、质量控制、统计分析等功能实现全面的综合自动化, 形成现代企业的计算机管理控制一体化系统。
集散控制系统-设计论文

第1章绪论本课题主要是利用组态软件模拟PLC的被控对象和控制过程。
主要涉及PLC和组态王软件的运用和集散控制系统的应用。
随着工业自动化水平的迅速提高,计算机在工业领域的广泛应用,人们对工业自动化的要求越来越高,种类繁多的控制设备和过程监控装置在工业领域的应用,使得传统的工业控制软件已无法满足用户的各种需求。
在开发传统的工业控制软件时,当工业被控对象一旦有变动,就必须修改其控制系统的源程序,导致其开发周期长;已开发成功的工控软件又由于每个控制项目的不同而使其重复使用率很低,导致它的价格非常昂贵;在修改工控软件的源程序时,倘若原来的编程人员因工作变动而离去时,则必须同其他人员或新手进行源程序的修改,因而更是相当困难通用工业自动化组态软件的出现为解决上述实际工程问题提供了一种崭新的方法,因为它能够很好地解决传统工业控制软件存在的种种问题,使用户能根据自己的控制对象和控制目的的任意组态,完成最终的自动化控制工程。
自动化已经成为一种趋势,对自动化过程的监控就成为我们不可以回避的课题。
现在组态软件做为通用的工具提醒本课题的重要性。
2000年以来,国内监控组态软件产品、集散控制技术、市场都取得了飞快的发展,应用领域日益拓展,用户和应用工程师数量不断增多。
充分体现了“工业技术民用化”的发展趋势。
监控组态软件是工业应用软件的重要组成部分,其发展受到很多因素的制约,归根结底,是应用的带动对其发展起着最为关键的推动作用。
集散控制系统和组态软件是在信息化社会的大背景下,随着工业 IT 技术的不断发展而诞生、发展起来的。
在整个工业自动化软件大家庭中,监控组态软件属于基础型工具平台。
集散控制系统给工业自动化、信息化、一体化、及社会信息化带来的影响是深远的,这种变化仍在继续发展。
因此集散控制系统作为新生事物尚处于高速发展时期,目前还没有专门的研究机构就它的理论与实践进行研究、总结和探讨,更没有形成独立、专门的理论研究机构。
第2章概述2.1集散控制系统集散控制系统(DCS)即分散控制系统。
集散控制原理及应用
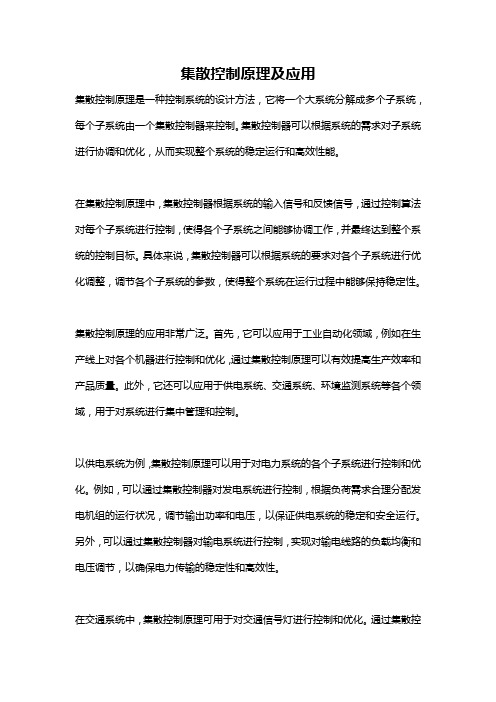
集散控制原理及应用集散控制原理是一种控制系统的设计方法,它将一个大系统分解成多个子系统,每个子系统由一个集散控制器来控制。
集散控制器可以根据系统的需求对子系统进行协调和优化,从而实现整个系统的稳定运行和高效性能。
在集散控制原理中,集散控制器根据系统的输入信号和反馈信号,通过控制算法对每个子系统进行控制,使得各个子系统之间能够协调工作,并最终达到整个系统的控制目标。
具体来说,集散控制器可以根据系统的要求对各个子系统进行优化调整,调节各个子系统的参数,使得整个系统在运行过程中能够保持稳定性。
集散控制原理的应用非常广泛。
首先,它可以应用于工业自动化领域,例如在生产线上对各个机器进行控制和优化,通过集散控制原理可以有效提高生产效率和产品质量。
此外,它还可以应用于供电系统、交通系统、环境监测系统等各个领域,用于对系统进行集中管理和控制。
以供电系统为例,集散控制原理可以用于对电力系统的各个子系统进行控制和优化。
例如,可以通过集散控制器对发电系统进行控制,根据负荷需求合理分配发电机组的运行状况,调节输出功率和电压,以保证供电系统的稳定和安全运行。
另外,可以通过集散控制器对输电系统进行控制,实现对输电线路的负载均衡和电压调节,以确保电力传输的稳定性和高效性。
在交通系统中,集散控制原理可用于对交通信号灯进行控制和优化。
通过集散控制器对各个路口的信号灯进行协调调度,可以根据实时交通情况合理控制红绿灯的时长和节奏,以减少交通拥堵和事故发生,提高交通效率。
在环境监测系统中,集散控制原理可以用于对监测站点的数据采集和处理。
通过集散控制器对各个监测点的数据进行集中管理和控制,可以及时发现和处理异常情况,保障环境监测的准确性和及时性。
总的来说,集散控制原理是一种分布式控制方法,能够对一个大系统进行分解和协调。
它的应用非常广泛,可以应用于各个领域,用于系统的控制和优化,提高系统的稳定性和性能。
随着科技的不断发展和进步,集散控制原理将会在更多的领域得到应用和推广。
浅谈集散控制系统
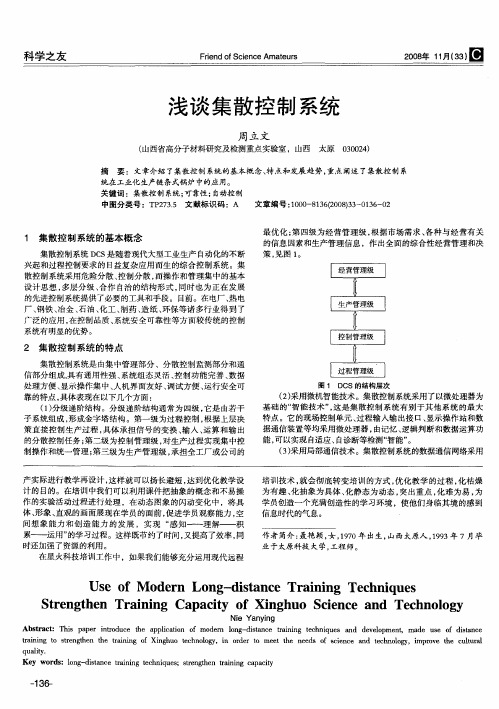
集散控 制系统 DC S是随着现代大型工业生产 自动化的不断 兴起和过程控制要求的 日益复杂应用 而生 的综合控 制系统 。集 散控制系统采用危险分散 、 控制分散 , 而操作和管理集 中的基本 设计思想 , 多层分级 、 合作 自治的结构形 式 , 同时也 为正在发 展 的先进控制 系统提供 了必要的工具 和手段 。 目前 。在电厂、 电 热
( ) 级 递 阶 结 构 。分 级 递 阶 结 构 通 常 为 四级 , 是 由若 干 1分 它 子 系统 组成 , 形成金字塔结构 。第一 级为过程控制 , 根据 上层 决 策 直接控制 生产过程 , 具体 承担信号 的变换 、 输入 、 运算 和输 出 的分散 控制 任务 ; 第二级为控制 管理级 , 生产过程实现集 中控 对 制操作 和统一 管理 ; 第三级 为生产 管理级 , 承担全工厂或公 司的
作 者 简介 : 聂艳颖 , ,9 0年 出生 , 女 17 山西 太原人 。9 3年 7月毕 19 业 于太原科技大学 , 工程师。
在星火科技培训工作 中 ,如果我们 能够 充分运用现代远程
Us f M o e n Lo g d sa c a n n c n q e e o d r n - it n e Tr i i g Te h i u s
S r n t e a n n p ct f Xi g u ce c n c n l g t e g h n Tr i i g Ca a iy o n h o S in e a d Te h o o y
集散控制系统设计论文

课程名称:集散控制系统设计班级:自动化学号: Xb*名:***日期: 2013 年 12 月 17日一、设计要求本课程设计是针对学生学习和运用专业知识的综合考核和检查,使学生接受工程类基本训练的重要环节,是自动化(热工)专业的《集散控制系统》专业课程学习的必修内容之一。
通过理论分析和设计室学生掌握一般工业工程的集散控制系统特点、原理和应用方法。
了解发电厂集散控制系统的硬件选型、设计和软件组态基本构成。
本课程设计的特点是,内容所涉及的知识面较一般习题广,有较强的系统性和综合性,在运算、绘图、编写设计文本方面有较高的要求。
本课程实际应针对交通运算组织学课程涉及的相关理论与方法,结合具体实践背景,解决实际问题。
要求:(1)能从数字控制系统功能要求出发,制订或分析设计方案,合理地选择控制系统硬件设备,确定软件需求。
(2)能按工艺的控制要求,选择相关模块,设计组态图。
(3)能考虑控制系统安装与调整、使用与维护、经济和安全等问题,对集散控制系统的安装技术要求进行设计。
(4)图面符合国家有关标准及行规,技术要求完整合理。
硬件设计:确定集散控制对象,根据对象确定控制器基本参数、模拟量类型、控制点数和基本参数、开关类型、点数和基本参数、网络组成、类型和基本参数,绘制硬件原理图和工程设计图纸。
软件设计:根据确定控制对象,绘制操作员站软件框图、组态软件框图。
二、课程设计应完成的任务任选一个下述被控对象,根据其控制要求,选用浙大中DCS系统JX-300制定控600MW机组主蒸汽温度控制系统,要求将锅炉出每个学生应完成:总体方案图1张、接线图1张,组态图3张,SAMA图1张;设计说明书一份,说明书应包括:确定总体方案,选定I/O点,控制系统的组态图等内容。
三、工作计划本次课程设计安排时间为4周,2013年12月7日~2013年12月28日,具体工作计划如下:1、2013年12月7日~8日,选择硬件模件和软件模件, 设计满足热工过程控制要求的集散控制系统总体方案;2、2013年12月9日~12日,画出系统实现图;3、2013年12月14日~16日,组态与仿真, 画出系统实现的有关组态图4、2013年12月28日,书写说明, 撰写设计说明书上交评分。
集散控制系统在化工过程控制中的应用研究

集散控制系统在化工过程控制中的应用研究摘要:集散控制系统是微处理器的集中分散系统,20世纪70年代中期引入第一个集散控制系统以来,其发展迅速,是具有巨大发展空间的化工和工业过程的主要管理系统。
化工企业集散控制系统安全可靠,方便简单使用。
它测量和控制化学生产中的各种生产数据。
在化工过程应用中起着重要作用,并在此基础上分析了集散控制在化工企业中的应用。
关键词:集散控制系统;化工企业;应用集中和分散管理是集散控制重要特征,在计算机和网络技术的飞速发展,集散控制系统不仅用于分散控制,而且用于集成管理。
通过开放性集散控制系统,不仅可以连接来自不同供应商的多个管理系统产品,还可以交换数据以确保更好的兼容性。
由于这些优点,集散控制系统可以应用于各种行业,例如在冶金、炼油厂、建筑、纺织品、化学和制药行业。
一、系统硬件组成1.系统结构。
操作站,包括工程师和操作员站。
工程师站配备了用于工程设计、系统扩展或服务变更的配置软件,操作员站在实时监控程序运行,即操作员控制台的操作平台,并通过流程监控任务监控整个运行。
进程控制实验室为每组受控对象配备两台计算机,一台用于工作站和1个用于工作站操作员站,有限责任公司的SCKEY配置软件安装在工作站上,DCS控制程序用于编写和修改。
如advan trol软件安装在操作方,两个操作平台相互独立运行。
一个平台的退出不会影响另一个平台的正常运行。
控制站,现场IP地址定义执行相应的实时控制流程,控制现场生产过程。
现场控制站的主控卡是系统硬件和软件的核心,它协调控制中心的所有软件和硬件通信,并执行各种控制任务,包括I/o处理、控制、上行和下行网络通信以及诊断。
数据卡是主数据卡和后续I/o卡之间的连接,I/o卡用于各种现场输入和输出,JX-300XP系统的网络分为内部监控、过程控制和控制站网络。
监视网络使用TCP/IP协议将高级监视程序连接到技术站和操作站。
该技术控制器网络用于网络互联引擎、操作员站、控制站和通信处理SCNET II通信处理单元。
浅谈集散控制系统及其应用

弯管流量计实际上是一个90度标准弯头,没有比它结构更简单的流量传感器了。
随着机械加工工业的发展和行业标准化及规范化管理的不断完善,用作弯管传感器的标准机制弯头性价比越来越高。
它的特点是:①结构简单,价格低廉。
②弯管流量计传感器耐磨损,对微量磨损不敏感。
③安装简单,可采用直接焊接法进行安装,使现场跑冒滴漏的麻烦得到彻底的解决。
④适应性强,量程范围宽,直管段要求不严。
只要是可以用孔板、涡街、均速管流量计来测量的管道内流体流量都可以用弯管流量计进行测量,而且在耐高温、耐高压、耐冲击、耐振动、耐潮湿、耐粉尘等方面,弯管流量计远优于其它流量计。
⑤弯管流量计的量程比可达1:10,对于蒸汽,它的适用范围为0~70m/s,可以较好地满足蒸汽流量测量的要求。
⑥弯管流量计由于其特殊的测量原理,使其在实际应用时对直管段的要求不严格,一般只要求前5D、后2D即可,远远低于其他流量测量装置的要求。
⑦弯管流量计精度高,重现性好,测量精度可达1.14%,重现性精度可达0.2%,一次安装后,不再需要重复拆装,因此,其安装精度也能得到最佳保证。
⑧弯管流量计的最突出特点是无任何附加节流件或插入件,可大大降低流体在管道内输送的动力消耗,节约能源,尤其对那些大系统、大管径、低压头的测量对象好处更加明显。
综上所述,蒸汽流量仪表的选用是非常重要的,准确测量蒸汽流量是生产部门都需要和普遍关心的问题。
因此,应针对生产实际情况,我们应作一些技术分析工作,走出一条蒸汽流量测量的正确之路。
浅谈集散控制系统及其应用动力系李忠良【内容提要】集散控制系统是以微处理为基础的集中分散控制系统,它的主要特征是集中管理和分散控制,从模拟电动仪表的操作习惯出发,开发人—机间良好的操作界面,用于操作人员的监视操作。
【关键词】集散控制系统集中管理分散控制应用!!!!!!!!!!!!!!!!!!!!!!!!!!!!!!!!!!!!!!!!!!!!一、集散控制系统的基本概念集散控制系统是以微处理为基础的集中分散控制系统,它的主要特征是集中管理和分散控制。
集散控制系统设计论文

课程名称:集散控制系统设计班级:自动化学号: Xb103******名:***日期: 2013 年 12 月 17日一、设计要求本课程设计是针对学生学习和运用专业知识的综合考核和检查,使学生接受工程类基本训练的重要环节,是自动化(热工)专业的《集散控制系统》专业课程学习的必修内容之一。
通过理论分析和设计室学生掌握一般工业工程的集散控制系统特点、原理和应用方法。
了解发电厂集散控制系统的硬件选型、设计和软件组态基本构成。
本课程设计的特点是,内容所涉及的知识面较一般习题广,有较强的系统性和综合性,在运算、绘图、编写设计文本方面有较高的要求。
本课程实际应针对交通运算组织学课程涉及的相关理论与方法,结合具体实践背景,解决实际问题。
要求:(1)能从数字控制系统功能要求出发,制订或分析设计方案,合理地选择控制系统硬件设备,确定软件需求。
(2)能按工艺的控制要求,选择相关模块,设计组态图。
(3)能考虑控制系统安装与调整、使用与维护、经济和安全等问题,对集散控制系统的安装技术要求进行设计。
(4)图面符合国家有关标准及行规,技术要求完整合理。
硬件设计:确定集散控制对象,根据对象确定控制器基本参数、模拟量类型、控制点数和基本参数、开关类型、点数和基本参数、网络组成、类型和基本参数,绘制硬件原理图和工程设计图纸。
软件设计:根据确定控制对象,绘制操作员站软件框图、组态软件框图。
二、课程设计应完成的任务任选一个下述被控对象,根据其控制要求,选用浙大中D C S系统J X-300制定控600MW机组主蒸汽温度控制系统,要求将锅炉出每个学生应完成:总体方案图1张、接线图1张,组态图3张,SAMA图1张;设计说明书一份,说明书应包括:确定总体方案,选定I/O点,控制系统的组态图等内容。
集散控制系统论文

摘要本文介绍了集散控制系统(DCS)的发展。
并以日本横河公司的第三代中型集散控制系统为例介绍了集散控制系统的结构。
本文还介绍了当前流行的一些集散控制系统的结构,组成,特点与应用。
最后文章还阐述了集散控制系统的发展前景关键词:集散控制系统;发展;应用图1一般测控系统1 绪论集散控制系统(TotalDistributedControlSystem)是以处理器为基础的集中分散型的控制系统。
第一套集散控制系统在70年代中期问世以来,集散控制系统已在工业控制领域中得到了广泛的应用与发展,越来越多的仪表和控制工程师已经认识到集散控制系统必将成为过程控制的主流,在计算机集成制造系统(ComputerIntegratedManufacturingSystem)或计算机集成作业系统(ComputerIntegratedProductionSystem)中,集散控制系统将成为主角,发挥它们的优势。
集散控制系统的主要特性是它的集中管理和分散控制。
而且,随着计算机技术的发展,网络技术已经使集散控制系统共不仅主要用于分散控制,而且向着集成管理的方向发展,系统地开放不仅使不同制造厂商的集散控制系统产品可以互相连接,而且使得他们可以方便的进行数据交换,系统地开放也是第三方的软件可以方便的在现有的集散控制系统上应用。
因此,集散控制系统早已在原有的概念上有了新的含义。
我国已引进的不同型号的集散控制系统的数量多达几百套,应用的工业控制领域也已遍及石油化工,冶金,炼油,建材,纺织,制药等行业。
2 集散控制系统的发展历史初始阶段:1975年美国霍尼韦尔公司第1套TDC2000集散控制系统问世不久。
世界各国仪表制造商就相继推出了自己的集散控制系统。
即第1代集散控制系统,比较著名的有:霍尼韦尔公司的TDC2000;FOXBORO 公司的SPECTRUM;FISHER公司的PROV0X;横河公司的CENTUM;西门子公司的TELEPERM等。
集散控制的原理及应用

集散控制的原理及应用什么是集散控制集散控制(Decentralized Control)是一种在分布式系统中使用的控制方法。
它是一种分散决策的方式,通过在系统中各个节点上进行局部决策,实现整体的协调与控制。
集散控制的目标是通过最小的中央控制器来实现复杂的系统控制,在分布式系统中具有很高的可扩展性和可靠性。
集散控制的原理集散控制的原理基于分布式系统的思想,它将系统分为多个自治节点,并通过在各个节点之间进行通信以实现协调与控制。
每个节点都具有一定的决策能力,并通过与其他节点的交互来达成共识。
集散控制通过将系统的控制任务分散到各个节点,避免了单点故障,提高了系统可靠性和可扩展性。
集散控制的原理可以简化为以下几个步骤: 1. 系统分解:将系统分解为多个自治节点。
每个节点负责执行特定的任务。
2. 节点决策:每个节点根据自身的输入和状态进行决策,并执行相应的操作。
3. 信息交互:节点之间通过通信方式传递信息,共享各自的状态和决策结果。
4. 协调与控制:节点根据接收到的信息进行协调和控制,实现整体的目标。
集散控制的应用集散控制广泛应用于各个领域的分布式系统中。
下面列举了一些典型的应用场景:工业控制系统在工业控制系统中,集散控制可以实现对生产线的协调和控制。
每个机器或设备都可以作为一个节点,通过集散控制实现整个生产线的优化和调度。
例如,通过集散控制可以将订单和生产计划分发到各个节点,使得生产线始终保持高效运转。
智能交通系统在智能交通系统中,集散控制可以实现对交通信号灯的协调和控制,以及实时交通流量监测和调整。
每个交通信号灯可以作为一个节点,通过集散控制算法实现交通流量的最优调度,提高道路的通行效率。
能源管理系统在能源管理系统中,集散控制可以实现对能源生产和消费的协调和控制。
每个能源设备(例如风力发电机、太阳能电池板等)可以作为一个节点,通过集散控制算法实现能源的优化分配和利用,提高能源的利用效率。
分布式计算系统在分布式计算系统中,集散控制可以实现对计算资源的协调和控制。
浅谈对集散控制系统系统的认识及应用
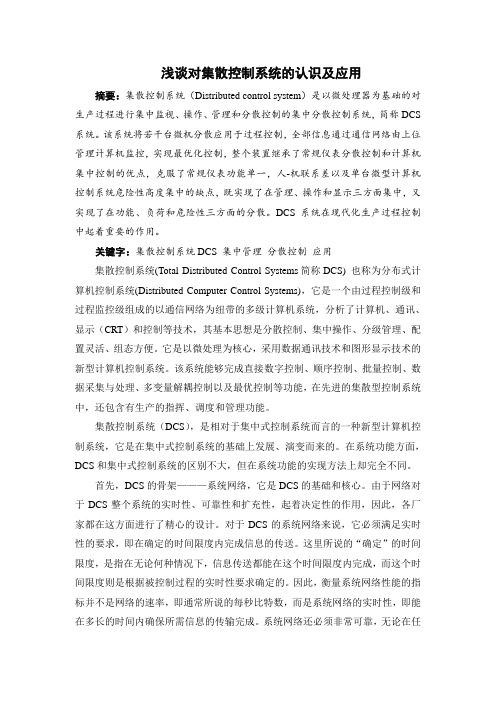
浅谈对集散控制系统的认识及应用摘要:集散控制系统(Distributed control system)是以微处理器为基础的对生产过程进行集中监视、操作、管理和分散控制的集中分散控制系统,简称DCS 系统。
该系统将若干台微机分散应用于过程控制,全部信息通过通信网络由上位管理计算机监控,实现最优化控制,整个装置继承了常规仪表分散控制和计算机集中控制的优点,克服了常规仪表功能单一,人-机联系差以及单台微型计算机控制系统危险性高度集中的缺点,既实现了在管理、操作和显示三方面集中,又实现了在功能、负荷和危险性三方面的分散。
DCS系统在现代化生产过程控制中起着重要的作用。
关键字:集散控制系统DCS 集中管理分散控制应用集散控制系统(Total Distributed Control Systems简称DCS) 也称为分布式计算机控制系统(Distributed Computer Control Systems),它是一个由过程控制级和过程监控级组成的以通信网络为纽带的多级计算机系统,分析了计算机、通讯、显示(CRT)和控制等技术,其基本思想是分散控制、集中操作、分级管理、配置灵活、组态方便。
它是以微处理为核心,采用数据通讯技术和图形显示技术的新型计算机控制系统。
该系统能够完成直接数字控制、顺序控制、批量控制、数据采集与处理、多变量解耦控制以及最优控制等功能,在先进的集散型控制系统中,还包含有生产的指挥、调度和管理功能。
集散控制系统(DCS),是相对于集中式控制系统而言的一种新型计算机控制系统,它是在集中式控制系统的基础上发展、演变而来的。
在系统功能方面,DCS和集中式控制系统的区别不大,但在系统功能的实现方法上却完全不同。
首先,DCS的骨架———系统网络,它是DCS的基础和核心。
由于网络对于DCS整个系统的实时性、可靠性和扩充性,起着决定性的作用,因此,各厂家都在这方面进行了精心的设计。
对于DCS的系统网络来说,它必须满足实时性的要求,即在确定的时间限度内完成信息的传送。
集散控制系统论文
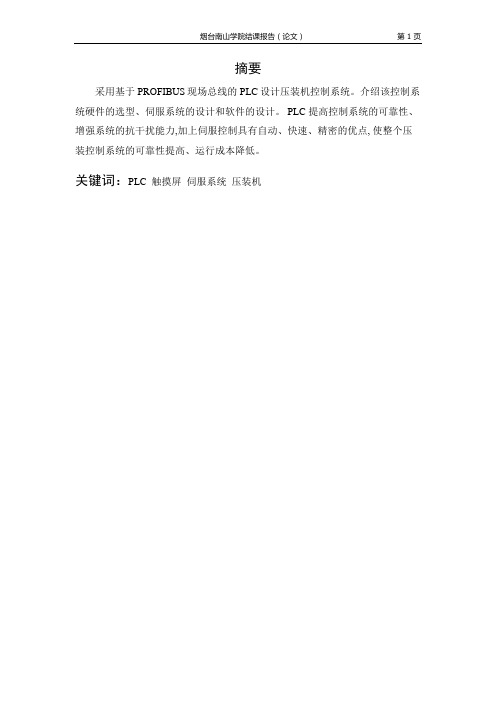
摘要采用基于 PROFIBUS现场总线的PLC设计压装机控制系统。
介绍该控制系统硬件的选型、伺服系统的设计和软件的设计。
PLC 提高控制系统的可靠性、增强系统的抗干扰能力,加上伺服控制具有自动、快速、精密的优点, 使整个压装控制系统的可靠性提高、运行成本降低。
关键词:PLC 触摸屏伺服系统压装机1.绪论可编程控制器PLC提高了控制系统的可靠性、增强了系统的抗干扰能力,触摸屏则为整个控制系统提供了良好的人机操作界面,加上伺服控制所具有的控制精度使它们越来越广泛地应用于工业生产的各个领域。
作者所要阐述的就是基于 PLC和触摸屏的伺服控制技术在汽车传动装置的压装生产上的应用。
为保证压装控制系统的运行并提高其可靠性, 采用SIE-MENS的触摸屏、SIEMENS公司的S7-300系列PLC和611U伺服驱动器对压装机的控制系统进行设计。
2.压装机工作原理2.1压装机工序压装机的压装轴工序主要包括归零、摆放工件、压装轴旋转到压装位、上下油缸压装、压装轴旋转到卸件位、下件气缸压下、推件气缸推进翻转缸、翻转气缸翻转将工件送到传送轨道;压装机的换压头轴工序主要包括归零、换头轴旋转、上油缸动作、夹紧油缸松开 (夹紧 ) 卸下 (装上 ) 压头。
为了保证压装机工作的可靠性, 控制系统必须满足以下要求:(1)需检测压装机的工件摆放位置、压头选择、胎具胎垫选择, 保证压装质量和安全;(2)每个工步均可在手动和自动状态下工作(3)考虑到压装轴和换头轴同时转动存在安全隐患, 要求两个轴的动作实现互锁;(4)实现系统压装和卸件动作同时进行的控制要求, 但是在压装完最后一个工件要实现单独卸件,压装动作停止;( 5) 考虑到翻转动作过快有安全隐患, 要求翻转速度能得到控制。
2.2系统组成系统主要由触摸屏、可编程控制器、伺服驱动器、伺服电机、液压站等构成,该控制系统主要通过 PLC 程序来控制伺服电机、油缸的压力以及油缸的运动位移以达到控制压件质量; 同时根据要求实现更换压头以达到压装要求。
集散控制系统的通信技术论文.doc
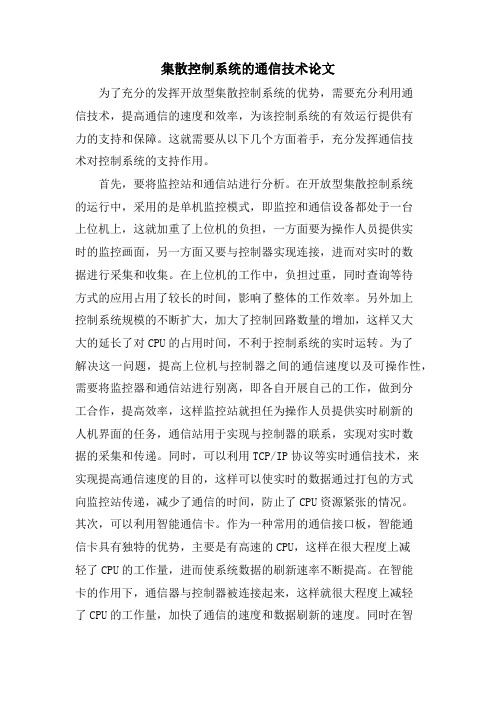
集散控制系统的通信技术论文为了充分的发挥开放型集散控制系统的优势,需要充分利用通信技术,提高通信的速度和效率,为该控制系统的有效运行提供有力的支持和保障。
这就需要从以下几个方面着手,充分发挥通信技术对控制系统的支持作用。
首先,要将监控站和通信站进行分析。
在开放型集散控制系统的运行中,采用的是单机监控模式,即监控和通信设备都处于一台上位机上,这就加重了上位机的负担,一方面要为操作人员提供实时的监控画面,另一方面又要与控制器实现连接,进而对实时的数据进行采集和收集。
在上位机的工作中,负担过重,同时查询等待方式的应用占用了较长的时间,影响了整体的工作效率。
另外加上控制系统规模的不断扩大,加大了控制回路数量的增加,这样又大大的延长了对CPU的占用时间,不利于控制系统的实时运转。
为了解决这一问题,提高上位机与控制器之间的通信速度以及可操作性,需要将监控器和通信站进行别离,即各自开展自己的工作,做到分工合作,提高效率,这样监控站就担任为操作人员提供实时刷新的人机界面的任务,通信站用于实现与控制器的联系,实现对实时数据的采集和传递。
同时,可以利用TCP/IP协议等实时通信技术,来实现提高通信速度的目的,这样可以使实时的数据通过打包的方式向监控站传递,减少了通信的时间,防止了CPU资源紧张的情况。
其次,可以利用智能通信卡。
作为一种常用的通信接口板,智能通信卡具有独特的优势,主要是有高速的CPU,这样在很大程度上减轻了CPU的工作量,进而使系统数据的刷新速率不断提高。
在智能卡的作用下,通信器与控制器被连接起来,这样就很大程度上减轻了CPU的工作量,加快了通信的速度和数据刷新的速度。
同时在智能通信卡的作用下,可以对传送和接收的数据进行保护,防止数据的丧失,大大的提高了系统运行的平安性和稳定性。
计算机技术的不断进步和开展,可以将运行过程进行分解,进而提高系统的运行速度,多串口技术就是通信技术的一个典范,通过在硬件上使用多端口的通信卡和软件上采用多线程技术,可以将程序分解和简化,大大的提高了工作的效率。
- 1、下载文档前请自行甄别文档内容的完整性,平台不提供额外的编辑、内容补充、找答案等附加服务。
- 2、"仅部分预览"的文档,不可在线预览部分如存在完整性等问题,可反馈申请退款(可完整预览的文档不适用该条件!)。
- 3、如文档侵犯您的权益,请联系客服反馈,我们会尽快为您处理(人工客服工作时间:9:00-18:30)。
mentionedFirst of all, the skeleton of DCS system network, it is the basis of the DCS and the core. Due to network for DCS, reliability and real-time performance of the whole system scalable, plays a decisive role, therefore all the manufacturers in this aspect has carried on the elaborate design. For DCS system network, it must meet the requirements of real-time, namely the complete transmission of information within a certain time limit. Here \"ok\" the time limit, is to point to in no matter what circumstances, information can be found within the time limit, and the time limit is according to the real-time requirement of the control process. Measure system, therefore, the rate of network performance index is not the networkDCSDCS, known as the number of bits per second (BPS), but the system real-time performance of the network, can be in a much longer time to ensure the transmission of the information needed to complete. System network must also is very reliable, in any case, the network communication cannot interrupt, so most of DCS adopts double bus, ring, or double star network topology. In order to meet the requirements of system expansion, the system can access the maximum number of nodes on the network should be several times greater than the actual use of the number of nodes. So, on the one hand, can add a new node at any time, on the other hand can also make the system run in a lighter network communication load condition, in order to ensure the real-time and reliability of the system. In the process of system operation, the Internet and various nodes in the net is possible at any time, especially the operator station, in this way, network reconfiguration often, and this kind of operation is absolutely should not affect the normal operation of the system, therefore, system network should have a strong online refactorings. Second, it is a completely to the I/O processing and realization of direct digital control (DDC) function of the network nodes. Usually to set the scene in a set of DCS I/O control station, to share the I/O and control function of the whole system. This can avoid the failure of the whole system due to a site failure, improve system reliability, also can make the site to share the data acquisition and control functions, to improve the performance of the whole system. DCS operator station is to handle all related to the operation of Human Machine Interface (HMI - Human Machine Interface or operator Interface) function of the network nodes.Engineer station is offline on DCS configuration, configuration and online system of supervision, control, maintenance of network nodes, its main function is to provide the DCS configuration, configuration software tools (that is, the configuration software), and DCS run online real-time monitoring the DCS operation of each node on the network,make the system engineer can engineer timely adjust system configuration and some parameters setting, make the DCS under the best working status at any time. Unlike the centralized control system, all the DCS requires system configuration function, can say, no system configuration function of the system can't call it the DCS.DCS since 1975, has experienced the developing course of more than 30 years. In this more than 30 years, although DCS happens on the system architecture of major changes, but after continuous development and improvement of its function and performance have been great improved. In general, the DCS is toward a more open, more standardized, more the direction of the transition.As a computer control system in the field of production process automation, the traditional DCS is only a narrow concept. If thought DCS was production process automation system, it will lead to the wrong conclusion, because now the meaning of computer control system has been greatly expanded, it includes not only the past DCS contained in the various content, also down deep into the field of each measurement devices, actuators, up to the production management, all aspects of enterprise management. In the traditional sense of the DCS now only refers to this part of the automation control of the production process, and the concept of industrial automation system, should be the location of a comprehensive solution to enterprises, the total solution. Only from this point of view put forward problems and solve problems, to make the computer automation really play its proper role.DCSDCSDCS has the following features:1. High reliability. Due to dispersion in the function of DCS control system implemented on the computer, the system structure of fault tolerance design, so the failure will not result in system of a computer is the loss of their other functions. In addition, due to the system based on the task of each computer is single, can according to need to realizethe function of use with a specific structure and special computer software, so that every computer in the system reliability is also improved.2. Open. DCS with open, standardized, modular and seriation design, computer using LAN communication of the system, and realize the information transmission, when need to change or expand the system function, new computer can be easily connected to the system communication network or unloaded from the network, almost does not affect other the work of a computer system.Form ofIs the abbreviation of Distributed Control System DCS (Distributed Control System), in the domestic industry is called Distributed Control System.It is a composed of process Control and process monitoring by the Computer system of multilevel Communication network as the link, a combination of Computer (Computer), Communication (Communication), display (CRT) and Control (Control) and so on 4 c technology, its basic idea is decentralized Control, centralized operation and decentralized management, flexible configuration, easy configuration.The development historyThe first stageFrom 1975 to 1980, the technical features of DCS control system in this period is characterized by:DCSDCS1) controlled by microprocessor based unit, realize the decentralized control, there are all kinds of algorithms, through configuration loop control independently, has the self-diagnosis function2) used for CRT monitors the operation of the station and unit separation process, realize the centralized monitoring, centralized operation3) USES the advanced redundant communication systemThe second stage1980-1985. During this period and distributing control system of the technical features are:1) the figures of the microprocessor to improve, improve the resolution of the CRT display2) strengthen the modular system3) to strengthen the information management system, and strengthen the function of communicationThe third stageAfter 1985, into the third generation of distribution system, its technical features are:1) using open systems management2) using 32-bit microprocessor operation station3) adopting multi-user real-time multitasking operating systemSince the ninety s, the computer technology by leaps and bounds, more new technology has been applied into DCS. PLC is a kind of developed electronic devices to control the sequence logic, it is mainly used to replace is not flexible and heavy relay logic. Field bus technology in the mid - ninety - s after developing very rapidly, so much so that some people have made a prediction: based on field bus control system of FCS will replace DCS as protagonist.Features introducedDCS is a Distributed Control System (Distributed Control System), the domestic general practice known as Distributed Control System. It is a composed of process Control and process monitoring by the Computer system of multilevel Communication network as the link, a combination of Computer (Computer), Communication (Communication), display (CRT) and Control (Control) and so on 4 c technology, its basic idea is decentralized Control, centralized operation and decentralized management, flexible configuration, the configuration is convenient, DCS characteristics are as follows.High reliabilityDue to dispersion in the function of DCS control system implemented on the computer, the system structure of fault tolerance design, so the failure will not result in system of a computer is the loss of their other functions. In addition, due to the system based on the task of each computer is single, can according to need to realize the function of use with a specific structure and special computer software, so that every computer in the system reliability is also improved.openDCS with open, standardization, modularization and serialization design, computer using LAN communication of the system, and realize the information transmission, when need to change or expand the system function, new computer can be easily connected to the system communication network or unloaded from the network, almost does not affect other the work of a computer system.flexibilityBy configuration software application process according to different objects of software and hardware configuration, the measurement and control signal and connection relationship between each other, from the control algorithms library to choose suitable control law, and from the basic graphics graphics library calls for a variety of monitoring and alarm screen, and conveniently constitute the necessary control system.Easy to maintainSpecial function of a single small or micro computer, has the characteristics of maintenance is simple, convenient, when a local or a computer failure, can be in online without affecting the operation of the whole system change, rapid troubleshooting. coordinationSend a variety of data through the communication network between each workstation, the system information sharing, coordination, to complete the overall function and the optimization of control system.To control the function is all readyControl algorithm is rich, continuous control, sequence control and batch control into an organic whole, can realize cascade, feedforward decoupling, adaptive and predictive control, and other advanced control, and can easily add the special control algorithm is required. DCS structure mode is very flexible and can be managed by a dedicated computer, operator station and engineer station, record stand, field control station and data acquisition station, etc, can also be used by the general servers, industrial control computer and programmable controller. At the bottom of the process control level by general decentralized field control station, data acquisition station on-site data acquisition and control, and production level monitoring computer via data communication network. Production monitoring level focus on data from the process control level for operation management, such as all kinds of optimization, statistics, fault diagnosis and display alarm, etc. With the development of computer technology, the DCS can be in accordance with the needs and higher performance of computer equipment connection through the network to realize centralized management of the more advanced features, such as planning and scheduling, inventory management, energy management, etc.structureStructurally, divided into DCS including process level, operation level and management level. Process level is mainly composed of process control station, the I/O unit and field instrument, is the main implement part of the system control function. Operation level including: operator station and engineer station, to complete the operation of the system and configuration. Management level mainly refers to the plant management information system (MIS), as an application of DCS higher level at present domestic paper industry application to this layer of the system is less.DCS control program: DCS control decision making is done by process control station, so the control program is performed by the process control station.The composition of the process control station:DCS process control station is a complete computer system, mainly by the power, the CPU (central processing unit), the network interface and I/OI/O: control systems need to build a signal input and output channels, this is I/O. DCS I/O in general is modular, an I/O module has one or more I/O channel, used to connect the sensors and actuators (regulator).I/O unit: usually, a process control station is a few frame, each frame can put a certain number of modules. CPU's frame is called CPU units, the same process in only one CPU units, other only used to put the I/O module rack is I/O unit.Application at home and abroadDistributed control systemInstrumentation in 1975, the largest U.S. companies Honeyw ell was first introduced to the world its comprehensive TDC - 2000 Distributed Control system (Toal Distributed Control - 2000), the system of the published, immediately cause the industrial Control industry highly, is called \"the most inspiring events\". Companies around the world have also follow suit, launched one after another and distributing system, process control into the distribution system in the new period.During this period have yokogawa's CEN TUM, MO SË Taylor instrument companies in the United States; DCÉ, bobby fischer company; N - 90-400, pele company, foxboro company Cpect Telepermm rum and Germany's Siemens.With the rapid development of computer, especially the micro computer and network technology, combined with the manufacturer's fierce competition, the DCS soon from the first generation of development in the 70 s to 70 s at the beginning of the third generation of DCS. Although before the distribution system of technical level is very high, but there was one of the major ills is: companies launched dozens of different types of systems, almost all the company's patented product, each company in order to protect their own interests, is the patent network are used, this is for the factory, the whole enterprise management problems.With the development of computer and network development makes the control manufacturers more commercial computer technology, in the late 80 s many companies to launch a new generation of distribution system, its main characteristic is the new system of local network with MA P agreement; Reference intelligent transmitter and field bus structure; In the control software of PLC is introduced in sequence control and batch control, make DCS also has the function of PLC.Countries well-known to the early 90 s of the DCS are: 3000, Bailey IN F I - 90, Ro semoun RS - 3 t, W est Hoo se WDPF, L eeds & Non th rup's MAX - 1000, Foxbo Ro IöA S, yokogawa CEN TUM. Mentioned here are large of DCS, the manufacturers in order to meet the needs of the market also has developed A lot of small and medium-sized DCS system such as S - 9000, MAX - 2, LXL, A 2 PACS, and so on.Process industry CIMSProcess industry CIMS is a complex integrated automation system, the processing of object is the enterprise of all production activities, DCS, as a kind of effective tool and means of implementation, do important basis in the process industry CIMS production data acquisition, control and real-time dynamic monitoring, and other functions. Compared with the management computer, DCS can provide more reliable production process data, optimization decisions are made by the CIMS system is more reliable. Look from the function, production automation of process industry CIMS system, dynamic monitor system and on-line quality control can be implemented by DCS. Look from the hierarchical structure of the process industrial CIMS, DCS main task for process control and process optimization, some production scheduling and management also can be finished in DCS.The main manufacturersDCS main manufacturers in China are: Shanghai xinhua, nanjing automation group co., LTD., hangzhou optimal stability and control of zhejiang, hollysys, via, zhejiang province, since the instrument co, luneng control, guodian wisdom deep, Shanghai Chinese, Shanghai focus, since in chint, etc.Abroad: Westinghouse, Emerson, FOXBORO, ABB, Siemens, honeywell, yokogawa, rockwell, yamatake honeywell, FISHER - ROSEMOUNT company, etc.。