KR法与喷吹法在铁水预脱硫中应用的比较
KR法铁水预处理脱硫的生产实践浅析

211管理及其他M anagement and otherKR 法铁水预处理脱硫的生产实践浅析张振杰(南京钢铁股份有限公司板材事业部第一炼钢厂,江苏 南京 210035)摘 要:硫对于大部分钢种危害程度较高的一种元素,并且其通常情况下是以硫化物的形式存在于钢中。
在实际的应用过程中倘若钢内的硫含量过高,将会对钢材的加工以及使用方面造成极大程度的影响,因此对展开铁水预处理脱硫的意义重大。
本文主要针对南钢KR 机械搅拌法改造后铁水预处理脱硫的生产实践进行了有效的分析。
关键词:机械搅拌法;铁水;脱硫;生产中图分类号:TF704.3 文献标识码:A 文章编号:11-5004(2020)22-0211-2 收稿日期:2020-11作者简介:张振杰,男,生于1982年,汉族,河北衡水人,本科,工程师,研究方向:钢铁冶炼及其相关。
近些年来,铁水预处理脱硫技术得到了相对较快的发展,至今已出现了多种不同类型的工艺处理方法,然而在具体的应用过程中经常使用广泛的有喷吹法以及KR 搅拌法。
KR 搅拌法在进行铁水预处理脱硫的生产实践过程中消耗相对喷吹法较小,同时在处理的过程中有所产渣量相对较少,反应速度快和效率高等优势。
1 方案选型现阶段,铁水脱硫的主要手段在具体生产过程中经常采用的有以KR 法未代表的机械搅拌法以及喷吹法。
该两种脱硫方法在具体实践过程中,均有一定的优势与特点,从而使其能够在炼钢业内得到相对较为广的应用。
关于KR 法脱硫工艺与喷吹法脱硫工艺主要特点的比较。
(1)关于KR 脱硫法工艺由于其在脱硫的过程中动力条件相对较为充分因此该工艺具有相对较高的脱硫率,同时其重现性与稳定性相对较高。
然而因为喷吹脱硫工艺在具体的实施过程中其角度方面的制约还有脱硫剂不能下沉等方面因素的影响,在脱硫的过程中存在一定的死角区域,从而一定程度上影响铁水动力学条件,且经常出现回硫的情况以及对于脱硫剂的消耗相对较大等不足之处,由于该因素的存在使得喷吹脱硫工艺在重现性与稳定性方面与KR 脱硫法存在一定的差距。
铁水脱硫比较分析

铁水脱硫工艺分析简况:近5年来铁水脱硫技术在我国发展很快,“铁水脱硫是转炉使用铁水炼钢不可缺少的工序”,这一点在我国得到了认同,先后增加了50多条(含在建)生产线,入炉铁水的脱硫比已经超过30%(有待核定,1998年仅为22%),目前大中型企业都有了不同型式的铁水预处理生产线,国内铁水预处理(脱硫)技术应用情况见表1表1 铁水预处理(脱硫)简况2 机械搅拌法(KR)、喷吹法脱硫比较1)机械搅拌法(KR)是成熟的生产工艺,日本绝大多数企业采用KR法脱硫,武钢已生产20多年,在消化引进技术的基础上有不少创新,生产技术水平和技术经济指标均较原设计有大幅度的提高,除脱硫铁水产量增长86.8%以外,还自行开发了无碳CaO基脱硫剂取代了CaC2,降低了生产成本。
脱硫处理前后铁水温降△t从过去的40-50℃减至28℃,脱硫效率ηs平均达92.5%,脱硫处理后[S]≤0.005%的罐次比率在98%以上,实际上[S]≤0.002%(ω)时的脱硫剂吨(CaO 基)耗量由8.5kg降至5.00kg以下,2001年脱硫剂平均耗量已降至3.78kg,目前兑入转炉经深脱硫的铁水硫含量平均值已达0.0027%,专用脱硫罐罐龄已达400次以上,主要消耗部件搅拌头使用次数平均已达500次,最多曾达631次,吨铁脱硫处理成本小于20元,铁损约为3%(原文是否有误待核定,是否为0.3%),KR法良好的动力学条件、脱硫效果好、粉剂成本低、无喷溅、无污染等优势使济钢、川威、昆钢、上钢一厂等厂相继采用。
2)喷吹法:八十年代初期我院开始研发用喷吹石灰粉法进行铁水脱硫技术并取得成功,石灰粉铁水脱硫技术先后在天钢等十几个厂应用,1998年我院先后又成功为宝钢设计引进了用混铁车进行铁水三脱复合喷吹技术、为本钢设计引进了“镁基”喷吹脱硫复合喷吹技术、2001年又为太钢设计引进了用铁水罐进行三脱复合喷吹技术以及单吹颗粒镁脱硫技术,喷吹法具有以下优点:●程序喷吹(复合、顺序)技术可以最大限度地利用多种粉剂发挥其在铁水预处理(脱硫)中效果。
KR法铁水脱硫工艺的发展、脱硫的原理及其探讨

KR法铁水脱硫工艺的发展、脱硫的原理及其探讨摘要:介绍了KR法铁水脱硫工艺的发展、脱硫的原理、该工艺的优、缺点及影响脱硫效果的因素,对喷吹和KR脱硫工艺进行了比较,为铁水脱硫装置的选择提供借鉴。
关键词:铁水预处理;脱硫;搅拌;喷吹前言铁水预处理已成为现代化的炼钢生产工艺:铁水预处理—复吹转炉—炉外精炼—全连铸和热装热送.当下用户对钢材质量要求越来越苛刻,一般要求钢中的硫含量控制在0.015%以下,有的甚至要求达到“双零”的超低硫水平,而且考虑到减轻转炉的冶炼任务和减少转炉消耗指标,使各冶炼设备的任务更加单一化、专业化,发挥各自的特长,因此近年来国内新建转炉钢厂都配备了铁水脱硫装置,老厂则经过改造配备了脱硫装置.搅拌法作为一种主流脱硫工艺,在国内许多钢厂得到了很好应用.1搅拌脱硫工艺1.1搅拌脱硫工艺在国内的发展KR搅拌法是日本新日铁广烟制铁所于1965年用于工业生产的铁水炉外脱硫技术[1],早在1976年武钢二炼钢就从日本新日铁引进了国内第一台搅拌法脱硫装置,单罐处理能力为70~80t,处理周期约85min,采用CaC2基作为脱硫剂,由于当时该套装置的消耗指标及运行成本均较高,处理周期长,所以并没有在国内得到广泛推广.随着时间的推移,搅拌法脱硫工艺经过近二十年的发展,已形成为一种成熟稳定的脱硫工艺,无论消耗指标、运行成本还是处理周期都大大降低.2000年武钢二炼钢在消化了第一套搅拌法脱硫工艺的基础上,联合原武汉钢铁研究设计总院自主设计和建造了第二套搅拌脱硫装置.2001年宝钢集团一钢公司从日本川崎重工引进两套150t搅拌脱硫装置,2002年原武汉钢铁研究设计总院又在昆钢建造了两套55t的搅拌脱硫装置,2003年原上海冶金设计研究院在宝钢集团上钢三厂建造了两套40t的搅拌脱硫装置.2007年在武钢新二炼钢新建两套200t、马钢四炼钢新建两套300t搅拌脱硫装置.韶钢新一钢工程在建两套130t搅拌脱硫装置,这样在国内已形成了300t、200t、150t、130t、80t、55t、40t的搅拌脱硫大、中、小系列.1. 2 搅拌法脱硫工艺的原理所谓搅拌法脱硫工艺,是将浇铸耐火材料并经过烘烤的十字形搅拌头,插入到有一定量铁水的铁水罐中旋转,使铁水形成漩涡,然后将经过称量好的脱硫剂通过振动给料(或旋转给料器)加入到旋转的铁水中.脱硫剂进入铁水罐后,迅速被漩涡卷入铁水中,在不断的搅拌过程中与铁水中的硫充分反应,从而脱硫的.影响脱硫速度的因素主要有二,一为脱硫剂种类,二为动力学条件.研究证明,动力学条件的影响大于脱硫剂种类的影响,搅拌速度高达 120r/min,铁水充分旋转,获得了良好的冶金动力学条件,投入的脱硫剂能够充分的反应,因此脱硫效率高达 95%以上.目前搅拌法脱硫工艺以石灰作为脱硫剂,再配入少许萤石、铝渣作为助熔剂.当铁水中的硅含量在0. 05!以上时,脱硫反应为: 反应生成的CO 气体对铁水起到搅拌作用,更加快了脱硫反应的进行.因为高炉铁水中的硅含量一般均大于0. 05%,因此脱硫反应均为(1)式.在反应式(1)中生成的Ca 2 SiO 4 层将石灰颗粒包住,此层质地紧密,且熔点高,阻碍了铁水中的硫透过它向深部扩散,使脱硫速度变缓,且生成的致密层包住新加入的石灰,增加了石灰的消耗,因此向脱硫剂中配入萤石等助熔剂,生成低熔点物质,从而使铁水中的硫进一步与石灰反应,能提高脱硫效率约 20%[2].由于降低氧势可以提高脱硫效率,因此部分钢厂向铁水中加入铝渣,通过铝脱氧来降低氧势[3].1. 3 搅拌法脱硫工艺的优缺点1. 3. 1 搅拌法脱硫工艺的优点1) 脱硫效率高而稳定搅拌法脱硫工艺由于其良好的动力学条件及重现性,使脱硫效率高而稳定,且回硫少,国内某厂,采用搅拌法一个班处理了8 炉铁水,7 炉达到0. 001%,一炉为0. 002%,而采用石灰加镁粉的喷吹法则较难达到这个水平,且回硫情况较严重[4].2) 脱硫剂搅拌法采用石灰基脱硫剂,运输与储存无需特殊措施,镁基喷吹法脱硫工艺所用镁粉需钝化处理,且运输和储存需有防护措施.3) 运行成本无论是喷吹工艺还是搅拌工艺,主要运行成本为脱硫剂和耐材.搅拌装置的搅拌头经过多年的改进,寿命已经大大提高,目前通常大于250 炉,在武钢高达500 多炉,而喷吹法喷枪的寿命通常在60 多炉;搅拌装置采用石灰基的脱硫剂,来源广泛,价格低廉,而镁基脱硫剂价格很高,且受市场的波动影响较大,通过对国内某厂生产数据的分析,在铁水终点硫≤0. 005%时,搅拌法比喷吹法运行成本低,而当铁水终点硫> 0. 005%,喷吹法比搅拌法运行成本低.1. 3. 2 搅拌法脱硫工艺的缺点1) 设备较大,占用面积较多.2) 一次性投资较大.3) 铁水的温降较大.4) 铁损较大.5) 处理周期较长.1. 4 影响搅拌法脱硫效率的因素影响搅拌法脱硫效果的主要因素如下.1) 在进行搅拌脱硫之前,铁水液面上的渣子不能太多,否则将会影响脱硫剂的充分反应.因此在搅拌脱硫之前需进行前扒渣,以扒除70%的渣量为宜,或者采用已成熟的捞渣工艺,韶钢KR 脱硫装置中选用了山东烟台的新型捞渣装置.2) 搅拌桨的转速不能太低,否则达不到良好的动力学条件,脱硫效率降低.通常搅拌作业时的正常转速为 100 ~120 r/s,随着搅拌头的损耗,可适当提高搅拌桨的转速,以保证良好的动力学条件.3) 脱硫剂必须是粉剂,以增加反应面积,使铁水中的硫与石灰充分接触.如果脱硫剂颗粒太大,则脱硫剂无法充分反应,且增加了单耗,直接影响脱硫效果.通常要求脱硫剂<3 mm.4)脱硫剂主要成分是石灰,因此石灰的质量对脱硫效果影响非常大,主要是石灰中的 CaO 含量、石灰的活性度及石灰中的硫含量.5) 搅拌桨的插入深度要适当,插入深度过深或过浅都会直接影响到脱硫效果,过浅,搅拌时喷溅严重,且铁水罐内下部铁水搅动效果差;过深,则上部的铁水搅动较差.2 搅拌法与喷吹法比较2. 1 脱硫工艺比较两种脱硫工艺的比较见表 1.2. 2 脱硫运行成本估算比较脱硫运行成本估算的比较见表 2.2. 3 两种脱硫方法的分析评价通过对两种脱硫工艺的脱硫效果和运行成本综合比较,可见搅拌法在深脱硫和总成本方面优势突出.对于大中钢铁企业,从长远考虑并结合生产实际,KR 搅拌法铁水预脱硫应是更具有深远价值的选择.3 结论搅拌法脱硫工艺作为一种高效,低成本的脱硫工艺在国内外已得到广泛推广,在国内已经形成由小到大的系列产品.尽管搅拌脱硫设备的一次性投资较大,但脱硫效果好,运行成本低,收回投资快.因此搅拌法脱硫将成为今后的一种主流脱硫工艺,得到更广泛的推广,并有向三脱处理工艺演化的趋势.。
KR法铁水脱硫数值分析
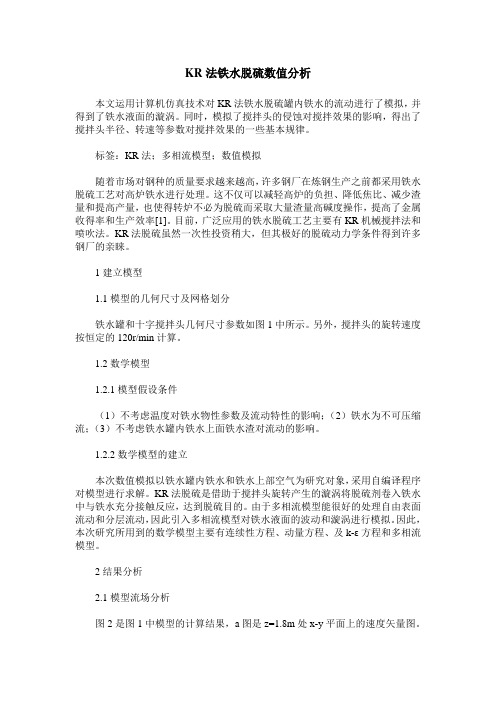
KR法铁水脱硫数值分析本文运用计算机仿真技术对KR法铁水脱硫罐内铁水的流动进行了模拟,并得到了铁水液面的漩涡。
同时,模拟了搅拌头的侵蚀对搅拌效果的影响,得出了搅拌头半径、转速等参数对搅拌效果的一些基本规律。
标签:KR法;多相流模型;数值模拟随着市场对钢种的质量要求越来越高,许多钢厂在炼钢生产之前都采用铁水脱硫工艺对高炉铁水进行处理。
这不仅可以减轻高炉的负担、降低焦比、减少渣量和提高产量,也使得转炉不必为脱硫而采取大量渣量高碱度操作,提高了金属收得率和生产效率[1]。
目前,广泛应用的铁水脱硫工艺主要有KR机械搅拌法和喷吹法。
KR法脱硫虽然一次性投资稍大,但其极好的脱硫动力学条件得到许多钢厂的亲睐。
1建立模型1.1模型的几何尺寸及网格划分铁水罐和十字搅拌头几何尺寸参数如图1中所示。
另外,搅拌头的旋转速度按恒定的120r/min计算。
1.2数学模型1.2.1模型假设条件(1)不考虑温度对铁水物性参数及流动特性的影响;(2)铁水为不可压缩流;(3)不考虑铁水罐内铁水上面铁水渣对流动的影响。
1.2.2数学模型的建立本次数值模拟以铁水罐内铁水和铁水上部空气为研究对象,采用自编译程序对模型进行求解。
KR法脱硫是借助于搅拌头旋转产生的漩涡将脱硫剂卷入铁水中与铁水充分接触反应,达到脱硫目的。
由于多相流模型能很好的处理自由表面流动和分层流动,因此引入多相流模型对铁水液面的波动和漩涡进行模拟。
因此,本次研究所用到的数学模型主要有连续性方程、动量方程、及k-ε方程和多相流模型。
2结果分析2.1模型流场分析图2是图1中模型的计算结果,a图是z=1.8m处x-y平面上的速度矢量图。
从a图中可以看出,十字搅拌头带动罐内铁水按逆时针方向旋转,搅拌头半径范围内速度较大,沿径向速度逐渐减小。
b图是x=0截面上的流速矢量图,由于搅拌头的旋转,铁水沿切向旋转的同时,铁水还往径向流动,遇到铁水罐罐壁处流动受阻,铁水流股分成上、下两个不同方向的流动,并各自形成回流。
对KR法与喷吹法两种铁水脱硫工艺的探讨 阐述武钢二炼钢厂投产应用多年的铁水搅拌式脱硫
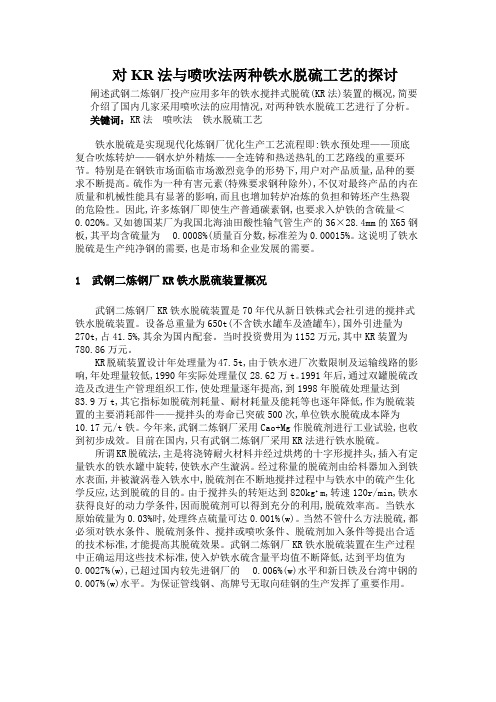
对KR法与喷吹法两种铁水脱硫工艺的探讨阐述武钢二炼钢厂投产应用多年的铁水搅拌式脱硫(KR法)装置的概况,简要介绍了国内几家采用喷吹法的应用情况,对两种铁水脱硫工艺进行了分析。
关键词:KR法喷吹法铁水脱硫工艺铁水脱硫是实现现代化炼钢厂优化生产工艺流程即:铁水预处理——顶底复合吹炼转炉——钢水炉外精炼——全连铸和热送热轧的工艺路线的重要环节。
特别是在钢铁市场面临市场激烈竞争的形势下,用户对产品质量,品种的要求不断提高。
硫作为一种有害元素(特殊要求钢种除外),不仅对最终产品的内在质量和机械性能具有显著的影响,而且也增加转炉冶炼的负担和铸坯产生热裂的危险性。
因此,许多炼钢厂即使生产普通碳素钢,也要求入炉铁的含硫量<0.020%。
又如德国某厂为我国北海油田酸性输气管生产的36×28.4mm的X65钢板,其平均含硫量为0.0008%(质量百分数,标准差为0.00015%。
这说明了铁水脱硫是生产纯净钢的需要,也是市场和企业发展的需要。
1 武钢二炼钢厂KR铁水脱硫装置概况武钢二炼钢厂KR铁水脱硫装置是70年代从新日铁株式会社引进的搅拌式铁水脱硫装置。
设备总重量为650t(不含铁水罐车及渣罐车),国外引进量为270t,占41.5%,其余为国内配套。
当时投资费用为1152万元,其中KR装置为780.86万元。
KR脱硫装置设计年处理量为47.5t,由于铁水进厂次数限制及运输线路的影响,年处理量较低,1990年实际处理量仅28.62万t。
1991年后,通过双罐脱硫改造及改进生产管理组织工作,使处理量逐年提高,到1998年脱硫处理量达到83.9万t,其它指标如脱硫剂耗量、耐材耗量及能耗等也逐年降低,作为脱硫装置的主要消耗部件——搅拌头的寿命已突破500次,单位铁水脱硫成本降为10.17元/t铁。
今年来,武钢二炼钢厂采用Cao+Mg作脱硫剂进行工业试验,也收到初步成效。
目前在国内,只有武钢二炼钢厂采用KR法进行铁水脱硫。
铁水预处理脱硫分析
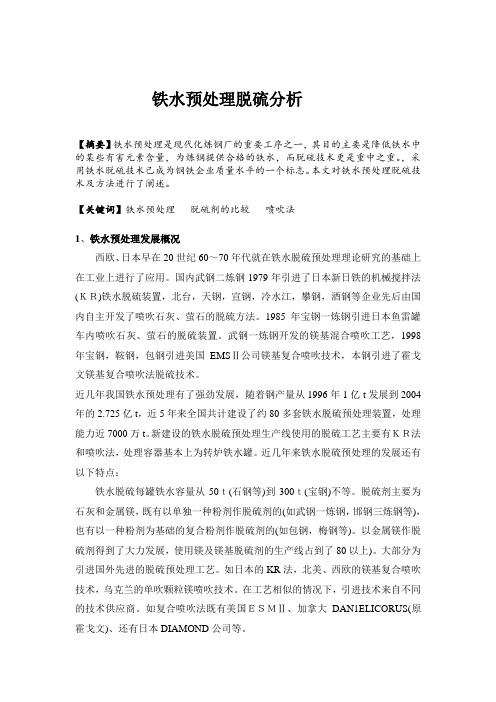
铁水预处理脱硫分析【摘要】铁水预处理是现代化炼钢厂的重要工序之一,其目的主要是降低铁水中的某些有害元素含量,为炼钢提供合格的铁水,而脱硫技术更是重中之重。
,采用铁水脱硫技术已成为钢铁企业质量水平的一个标志。
本文对铁水预处理脱硫技术及方法进行了阐述。
【关键词】铁水预处理脱硫剂的比较喷吹法1、铁水预处理发展概况西欧、日本早在20世纪60~70年代就在铁水脱硫预处理理论研究的基础上在工业上进行了应用。
国内武钢二炼钢1979年引进了日本新日铁的机械搅拌法(KR)铁水脱硫装置,北台,天钢,宣钢,冷水江,攀钢,酒钢等企业先后由国内自主开发了喷吹石灰、萤石的脱硫方法。
1985年宝钢一炼钢引进日本鱼雷罐车内喷吹石灰、萤石的脱硫装置。
武钢一炼钢开发的镁基混合喷吹工艺,1998年宝钢,鞍钢,包钢引进美国EMSⅡ公司镁基复合喷吹技术,本钢引进了霍戈文镁基复合喷吹法脱硫技术。
近几年我国铁水预处理有了强劲发展,随着钢产量从1996年1亿t发展到2004年的2.725亿t,近5年来全国共计建设了约80多套铁水脱硫预处理装置,处理能力近7000万t。
新建设的铁水脱硫预处理生产线使用的脱硫工艺主要有KR法和喷吹法,处理容器基本上为转炉铁水罐。
近几年来铁水脱硫预处理的发展还有以下特点:铁水脱硫每罐铁水容量从50t(石钢等)到300t(宝钢)不等。
脱硫剂主要为石灰和金属镁,既有以单独一种粉剂作脱硫剂的(如武钢一炼钢,邯钢三炼钢等),也有以一种粉剂为基础的复合粉剂作脱硫剂的(如包钢,梅钢等)。
以金属镁作脱硫剂得到了大力发展,使用镁及镁基脱硫剂的生产线占到了80以上)。
大部分为引进国外先进的脱硫预处理工艺。
如日本的KR法,北美、西欧的镁基复合喷吹技术,乌克兰的单吹颗粒镁喷吹技术。
在工艺相似的情况下,引进技术来自不同的技术供应商。
如复合喷吹法既有美国ESMⅡ、加拿大DAN1ELICORUS(原霍戈文)、还有日本DIAMOND公司等。
我国在早期引进国外先进技术的基础上改进的自主知识产权开发技术也在发挥着作用。
喷吹法和KR机械搅拌法在铁水脱硫中的分析

脱硫技术 初创于 二十世纪三十年代 , 发展于二十世纪六十 年代 , 至今 ,
已经 日趋成熟 。 目前 ,铁水脱硫 已经形成 了十几种脱硫 方法 ,这其中 最具有代 表性、应用最广泛 的当属喷 吹法 和 K R法 ( 又称 KR机械 搅
一
的 发展 ,生 成 了混 合和复 合喷 吹法两种 形式 的喷 吹法 。混合 喷 吹法
定 的费用。但 K R机械搅拌 法也有其 自身 的局限性 。由于 K R机械
合 。在 C a O、Mg 和C a C 在 内的脱硫粉 剂充 分混合 后 ,再 使用惰 性 搅拌法对设备机械 的要 求较高 ,特别是对耐火材料 制成 的搅拌器要求 极高 ,搅拌 器的生命往往很短 。而 且 K R机械搅拌法设备 所 占场地也 气体 将其 喷进铁水 中 。在 混合 喷吹法 铁水脱 硫过程 中 ,镁 系和钙 系 脱硫粉 剂通 过混合 ,钙 系脱硫粉 剂会分 散镁 气泡 ,进 而增 加镁 的有 较大 ,投资较 高,适用于 资金 充足、规模较大 的钢铁生产 厂家。 效表面 面积 , 并形 成 Mg S 。 在脱 硫的上升过 程中将 Mg S 脱 离出铁水 ,
的发展 ,提 高铁 水脱 硫、脱硫的效率显得 尤为重要。本文通过分 别分析 了喷吹法和 K R 机械搅拌 法在铁水脱硫 K R机械搅拌法各 自的优 势。 关 键 词 :铁 水 脱 硫 ; 喷 吹 法 ; K R法
O 引 言
随着 二十一世纪以来科学技术的飞速发展 , 能源产业 、 化工产业、
拌法 )。
法中 ,脱硫剂仅仅借助 惰性气体才能与铁水混合 ,造成只 有在 自身的
上升过程之 中才 能吸收铁 水中的硫元素 ,使得大量 的脱硫 剂无法完全
KR法铁水预处理的脱硫效果
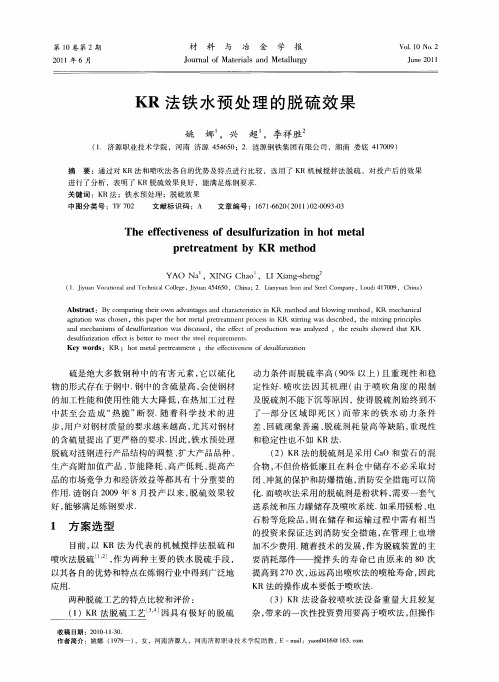
1 方 案选 型
目前 , K 以 R法 为代 表 的机 械 搅 拌 法 脱硫 和 喷 吹法 脱硫 , 为 两种 主要 的铁 水 脱 硫 手 段 , 作 以其各 自的优势 和特 点在 炼钢 行业 中得 到广 泛地
Absr t: By c m pa ngt i t ac o i r herown d ntg sa d c r ce sisi KP m eho n l w i eh a va a e n haa tr tc n . i t d a d b o ngm t od,KR e h n cl m c a ia a iai n wa ho e gtto sc s n,t sp pe he h ea r te t e o e si KR tri g w a e c be hi a rt otm tlp er am ntpr c s n sirn sd sr d,t i i rncpe i hem xng p i ils a e h ni Sofdeul iz to sds u sd, t f c fpr du to a a ay e , t eul ho e ha . nd m c a s s f ai n wa ic se m ur he e e to o ci n w s n lz d he r s t s w d t tKP s d s f iz to e e ti b te o me tt t e e u r m e s eul ur ain f c s e trt e he se lr q ie nt. Ke y wor s: KR ; ho ea eram e ; t fe tv nesofd s f iai n d tm tlprte t nt he e ci e s eul z to ur
硫是 绝 大多 数 钢 种 中的 有 害元 素 , 以硫 化 它 物 的形式 存在 于钢 中. 中 的含 硫量 高 , 使 钢材 钢 会 的加 工性 能 和使 用 性 能 大 大 降低 , 在热 加 工 过 程 中甚 至 会 造 成 “ 脆 ” 裂. 着 科 学 技 术 的 进 热 断 随 步, 用户 对钢 材质 量 的要求 越来 越高 , 尤其 对 钢材 的含 硫量 提 出 了更 严格 的要 求 . 因此 , 铁水 预处 理
铁水脱硫方法

铁水脱硫是钢铁生产过程中的一项重要技术,旨在降低铁水中的硫含量,以保证钢铁产品的质量。
硫在钢铁中以硫化物的形式存在,会降低钢的纯净度,影响其机械性能,特别是对于海洋平台、汽车板等高品质钢材的生产,要求铁水中的硫含量必须严格控制。
常见的铁水脱硫方法有以下几种:
1. 机械搅拌法(KR法):通过机械搅拌器使铁水旋转,并喷入脱硫剂,如CaO或MgO,通过搅拌使脱硫剂与硫化物反应,实现脱硫。
2. 喷吹法:利用喷枪将粉末状的脱硫剂直接喷入铁水中,脱硫剂与铁水中的硫化物发生反应,从而降低硫含量。
3. 气体搅拌法:将含有硫的气体通入铁水中,通过气体的搅拌作用,使硫化物与气体充分混合并排出。
4. 悬浮法:将含硫化合物的悬浮液通入铁水中,通过悬浮液的吸附作用将硫分从铁水中分离出来。
5. 压入法:将含硫气体或液体通过压力直接压入铁水中,使其与铁水充分接触并达到脱硫效果。
以上方法中,机械搅拌法(KR法)因其效率高、控制参数灵活而被广泛应用。
此外,还有利用摇包、搅拌时间、转速等参数进行优化的方法,以及对脱硫剂的加入速度和量进行控制的技术,以提高脱硫效率和降低成本。
KR脱硫和喷吹脱硫成本明细对比
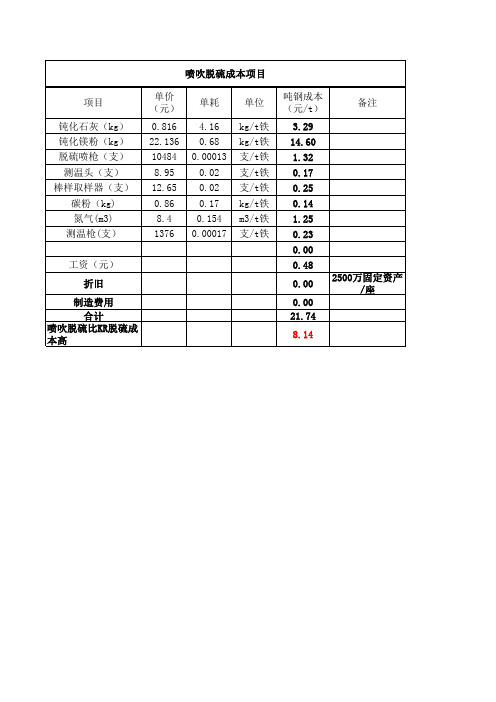
KR脱硫成本项目 项目 混合脱硫粉(kg) 高铝渣粉(kg) 搅拌桨(支) 测温头(支) 棒样取样器(支) 碳粉(kg) 氮气(m3) 测温枪(支) 电耗 折旧 制造费用 单价 (元) 0.67 0.938 49572 8.95 12.65 0.86 8.4 1376 0.42 单耗 12.25 0.7 0.00004 0.015 0.015 0.036 0.25 0.00007 0.5 单位 kg/t铁 kg/t铁 支/t铁 支/t铁 支/t铁 kg/t铁 m3/t铁 支/t铁 度/t铁 吨钢成本 (元/t) 7.96 0.64 1.92 0.13 0.18 0.03 2.04 0.09 0.20 0.40 0.00 0.00 13.60 4000万固定资产/ 座 平均每包搅拌12分钟 无流量计,估计值 备注
喷吹脱硫成本项目 项目 钝化石灰(kg) 钝化镁粉(kg) 脱硫喷枪(支) 测温头(支) 棒样取样器(支) 碳粉(kg) 氮气(m3) 测温枪(支) 工资(元) 折旧 制造费用 合计 喷吹脱硫比KR脱硫成 本高 单价 (元) 0.816 22.136 10484 8.95 12.65 0.86 8.4 1376 单耗 4.16 0.68 0.00013 0.02 0.02 0.17 0.154 0.00017 单位 kg/t铁 kg/t铁 支/t铁 支/t铁 支/t铁 kg/t铁 m3/t铁 支/t铁 吨钢成本 (元/t) 3.29 14.60 1.32 0.17 0.25 0.14 1.25 0.23 0.00 0.48 0.00 0.00 21.74 8.14 2500万固定资产 /座 备注
搅拌12分钟
KR法与喷吹法在铁水预脱硫中应用的比较
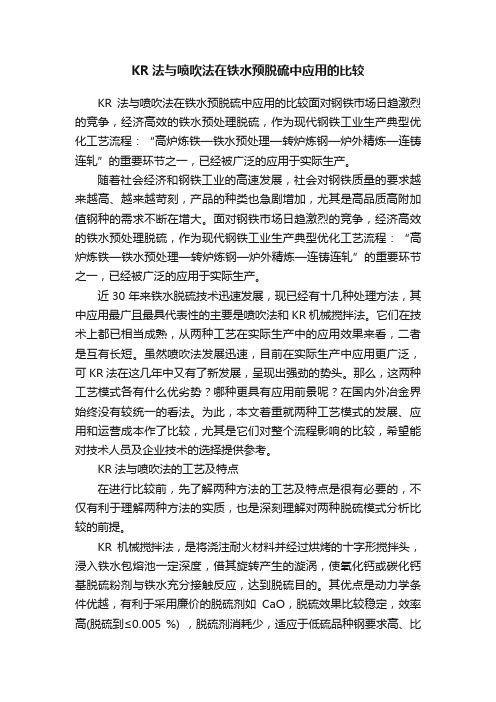
KR法与喷吹法在铁水预脱硫中应用的比较KR法与喷吹法在铁水预脱硫中应用的比较面对钢铁市场日趋激烈的竞争,经济高效的铁水预处理脱硫,作为现代钢铁工业生产典型优化工艺流程:“高炉炼铁—铁水预处理—转炉炼钢—炉外精炼—连铸连轧”的重要环节之一,已经被广泛的应用于实际生产。
随着社会经济和钢铁工业的高速发展,社会对钢铁质量的要求越来越高、越来越苛刻,产品的种类也急剧增加,尤其是高品质高附加值钢种的需求不断在增大。
面对钢铁市场日趋激烈的竞争,经济高效的铁水预处理脱硫,作为现代钢铁工业生产典型优化工艺流程:“高炉炼铁—铁水预处理—转炉炼钢—炉外精炼—连铸连轧”的重要环节之一,已经被广泛的应用于实际生产。
近30年来铁水脱硫技术迅速发展,现已经有十几种处理方法,其中应用最广且最具代表性的主要是喷吹法和KR机械搅拌法。
它们在技术上都已相当成熟,从两种工艺在实际生产中的应用效果来看,二者是互有长短。
虽然喷吹法发展迅速,目前在实际生产中应用更广泛,可KR法在这几年中又有了新发展,呈现出强劲的势头。
那么,这两种工艺模式各有什么优劣势?哪种更具有应用前景呢?在国内外冶金界始终没有较统一的看法。
为此,本文着重就两种工艺模式的发展、应用和运营成本作了比较,尤其是它们对整个流程影响的比较,希望能对技术人员及企业技术的选择提供参考。
KR法与喷吹法的工艺及特点在进行比较前,先了解两种方法的工艺及特点是很有必要的,不仅有利于理解两种方法的实质,也是深刻理解对两种脱硫模式分析比较的前提。
KR机械搅拌法,是将浇注耐火材料并经过烘烤的十字形搅拌头,浸入铁水包熔池一定深度,借其旋转产生的漩涡,使氧化钙或碳化钙基脱硫粉剂与铁水充分接触反应,达到脱硫目的。
其优点是动力学条件优越,有利于采用廉价的脱硫剂如CaO,脱硫效果比较稳定,效率高(脱硫到≤0.005 %) ,脱硫剂消耗少,适应于低硫品种钢要求高、比例大的钢厂采用。
不足是,设备复杂,一次投资较大,脱硫铁水温降较大。
单喷和复喷及KR法脱硫工艺分析
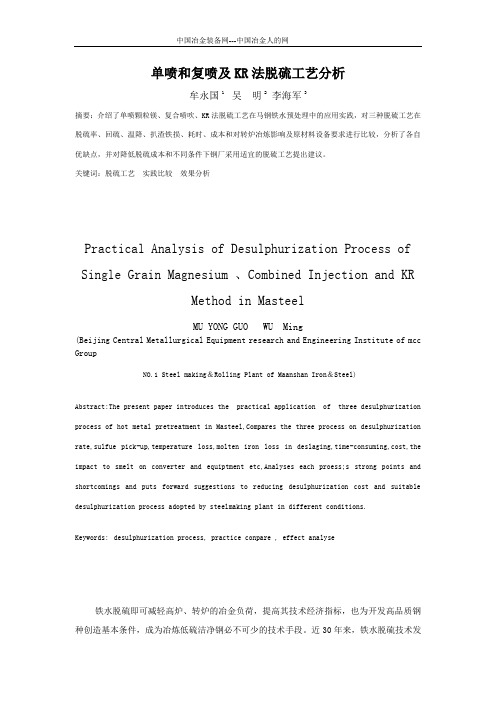
单喷和复喷及KR法脱硫工艺分析牟永国 1 吴明 2 李海军 3摘要:介绍了单喷颗粒镁、复合喷吹、KR法脱硫工艺在马钢铁水预处理中的应用实践,对三种脱硫工艺在脱硫率、回硫、温降、扒渣铁损、耗时、成本和对转炉冶炼影响及原材料设备要求进行比较,分析了各自优缺点,并对降低脱硫成本和不同条件下钢厂采用适宜的脱硫工艺提出建议。
关键词:脱硫工艺实践比较效果分析Practical Analysis of Desulphurization Process of Single Grain Magnesium 、Combined Injection and KRMethod in MasteelMU YONG GUO WU Ming(Beijing Central Metallurgical Equipment research and Engineering Institute of mcc GroupNO.1 Steel making&Rolling Plant of Maanshan Iron&Steel)Abstract:The present paper introduces the practical application of three desulphurizationprocess of hot metal pretreatment in Masteel,Compares the three process on desulphurization rate,sulfue pick-up,temperature loss,molten iron loss in deslaging,time-consuming,cost,the impact to smelt on converter and equiptment etc,Analyses each proess;s strong points and shortcomings and puts forward suggestions to reducing desulphurization cost and suitable desulphurization process adopted by steelmaking plant in different conditions.Keywords:desulphurization process, practice conpare , effect analyse铁水脱硫即可减轻高炉、转炉的冶金负荷,提高其技术经济指标,也为开发高品质钢种创造基本条件,成为冶炼低硫洁净钢必不可少的技术手段。
KR法与喷吹法两种铁水脱硫工艺的比较

KR法与喷吹法两种铁水脱硫工艺的比较赵炜①(南京钢铁股份有限公司,江苏南京210035)摘要:对单喷颗粒镁、复合喷吹、KR法三种脱硫工艺在脱硫率、回硫、温降、扒渣铁损、耗时、成本和对转炉冶炼影响及原材料设备要求进行比较,分析了各自优缺点,并对降低脱硫成本和不同条件下钢厂采用适宜的脱硫工艺提出建议。
关键词:脱硫工艺;技术设备;脱硫效果;温降;铁损;成本1 前言现代化炼钢厂的生产工艺流程是:高炉炼铁铁水———铁水预处理———顶底复合吹炼转炉—钢水炉外精炼———全连铸和热送热轧,而铁水脱硫是整个工艺路线中的重要环节。
铁水脱硫也是生产纯净钢和市场、企业发展的需要。
目前铁水脱硫工艺较为成熟的主要有KR法(机械搅拌法)和喷吹法两种,从两种工艺在实际生产中的应用效果来看,二者是互有长短。
为此,本文着重就两种工艺模式的发展、应用和运营成本作了比较。
2 KR法和喷吹法的工艺及特点所谓KR脱硫法,主是将浇铸耐火材料并经过烘烤的十字形搅拌头,插入有定量铁水的铁水罐中旋转使铁水产生漩涡。
脱硫剂在不断地搅拌过程中与铁水中的硫产生化学反应,达到脱硫的目的。
KR法优点是动力学条件优越,脱硫效果比较稳定,脱硫剂消耗较少,适应于低硫品种钢比例大、要求高的钢厂采用。
不足是,设备复杂,一次投资较大,脱硫铁水温降较大。
喷吹法,是利用惰性气体(N2或Ar)作载体将脱硫粉剂(如CaO,CaC2和Mg)由喷枪喷入铁水中,使喷吹气体、脱硫剂和铁水三者之间充分混合进行脱硫。
目前,以喷吹镁系脱硫剂为主要发展趋势,其优点是设备费用低,操作灵活,喷吹时间短,铁水温降小。
3 KR 法与喷吹法两种工艺的比较从铁水脱硫工艺倍受人们的重视以来,KR法与喷吹法技术一直处于发展之中,目前虽仍需完善,可也日趋于成熟,本文主要从以下几个方面对两种脱硫方法进行具体比对。
3.1 技术与设备喷吹法因其设备用量少、基建投入低、高效经济等诸多优势而处于脱硫技术的主要发展趋势之一,可在相当长的时间中国都是引进国外的技术和设备。
KR法铁水脱硫工艺的发展、脱硫的原理及其探讨

书山有路勤为径,学海无涯苦作舟
KR 法铁水脱硫工艺的发展、脱硫的原理及其探讨
广泛,价格低廉,而镁基脱硫剂价格很高,且受市场的波动影响较大,通过对国内某厂生产数据的分析,在铁水终点硫≤0. 005%时,搅拌法比喷吹法运行成本低,而当铁水终点硫0. 005%,喷吹法比搅拌法运行成本低.
1. 3. 2 搅拌法脱硫工艺的缺点
1) 设备较大,占用面积较多.
2) 一次性投资较大.
3) 铁水的温降较大.
4) 铁损较大.
5) 处理周期较长.
1. 4 影响搅拌法脱硫效率的因素
影响搅拌法脱硫效果的主要因素如下.
1) 在进行搅拌脱硫之前,铁水液面上的渣子不能太多,否则将会影响脱硫剂的充分反应. 因此在搅拌脱硫之前需进行前扒渣,以扒除70%的渣量为宜,或者采用已成熟的捞渣工艺,韶钢KR 脱硫装置中选用了山东烟台的新型捞渣装置.
2) 搅拌桨的转速不能太低,否则达不到良好的动力学条件,脱硫效率降低. 通常搅拌作业时的正常转速为100 ~120 r/s,随着搅拌头的损耗,可适当提高搅拌桨的转速,以保证良好的动力学条件.
3) 脱硫剂必须是粉剂,以增加反应面积,使铁水中的硫与石灰充分接触. 如果脱硫剂颗粒太大,则脱硫剂无法充分反应,且增加了单耗,直接影响脱硫效果. 通常要求脱硫剂小于3 mm.
4)脱硫剂主要成分是石灰,因此石灰的质量对脱硫效果影响非常大,主要是。
铁水炉外预处理脱硫技术

铁水炉外预处理脱硫技术机械搅拌法与吹气搅拌法的经济效益分析1.建设投资机械搅拌法简称KR法,由于设备体积庞大,数量多且复杂,因此基本建设投资是吹气搅拌法的一倍。
如果安装一套吹气搅拌法脱硫设备用500万元,而KR法就要1000万元。
2.占地面积KR法由于要保证搅拌头既能上下升降,又能围绕圆心旋转,还要把特制的石灰粉用专门设备加入铁水罐中。
因此,KR法本体设备占地面积大。
不像吹气搅拌法设备比较灵巧,占地空间小。
吹气搅拌法尤其适合老厂改造采用。
3.脱硫剂KR法使用的脱硫剂是石灰粉。
此法对石灰粉粒度的要求是十分严格的,必须经过专用设备加工而成。
石灰粉不易保存,非常易水化,尤其是在夏季CaO更容易受潮,变成Ca(OH)2。
氢氧化钙易结块,其化学性质与氧化钙有根本的变化,严重影响铁水脱硫效果。
因此,使用KR法脱硫,必须建一座专用的石灰粉供应基地。
包括石灰焙烧窑、破碎机、球磨机、储料仓等。
石灰粉供应基地的建设大约也要900-1000万元。
另外,石灰粉对环境污染也比较厉害。
因此,采用KR法脱硫除尘设备的投入也是相当可观的。
另外,石灰粉的用量大约是钝化镁的10倍。
用钝化颗粒镁脱硫,一般耗量0.4千克/吨铁。
用石灰粉耗量为4千克/吨铁。
如果对50吨铁水进行脱硫处理。
用钝化颗粒镁只需20千克。
而用石灰粉至少需要200千克。
而吹气搅拌法使用的钝化颗粒镁就没有上面提到的,石灰粉易水化而改性的问题。
因为颗粒镁表面被一层钝化膜包覆。
钝化颗粒镁有专业生产厂商供应,十分方便,随用随要,而且易于保存。
4.铁水处理时间KR法铁水脱硫处理时间比较长,是吹气搅拌法铁水脱硫处理时间的3-4倍。
吹气搅拌铁水脱硫反应时间,一般只需5-8分钟。
那么KR法就要20-32分钟。
为什么KR法脱硫反应时间长?主要原因是石灰粉只能加在铁水的表面,由于石灰粉比重轻,很难完全与铁水接触,所以反应速度慢。
脱硫时间长。
另外,脱硫反应是一个吸热反应,铁水温度若偏低,反应速度更慢,脱硫时间会更长。
武钢二炼钢KR铁水脱硫生产实践
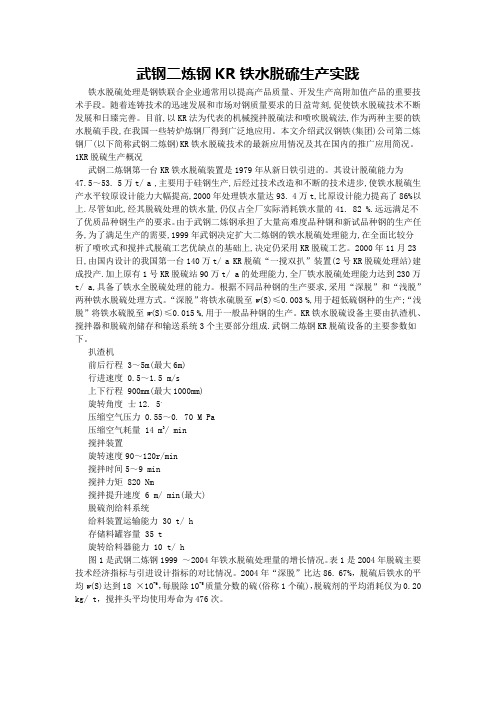
武钢二炼钢KR铁水脱硫生产实践铁水脱硫处理是钢铁联合企业通常用以提高产品质量、开发生产高附加值产品的重要技术手段。
随着连铸技术的迅速发展和市场对钢质量要求的日益苛刻,促使铁水脱硫技术不断发展和日臻完善。
目前,以KR法为代表的机械搅拌脱硫法和喷吹脱硫法,作为两种主要的铁水脱硫手段,在我国一些转炉炼钢厂得到广泛地应用。
本文介绍武汉钢铁(集团)公司第二炼钢厂(以下简称武钢二炼钢)KR铁水脱硫技术的最新应用情况及其在国内的推广应用简况。
1KR脱硫生产概况武钢二炼钢第一台KR铁水脱硫装置是1979年从新日铁引进的。
其设计脱硫能力为47.5~53. 5万t/ a ,主要用于硅钢生产,后经过技术改造和不断的技术进步,使铁水脱硫生产水平较原设计能力大幅提高,2000年处理铁水量达93. 4万t,比原设计能力提高了86%以上.尽管如此,经其脱硫处理的铁水量,仍仅占全厂实际消耗铁水量的41. 82 %.远远满足不了优质品种钢生产的要求。
由于武钢二炼钢承担了大量高难度品种钢和新试品种钢的生产任务,为了满足生产的需要,1999年武钢决定扩大二炼钢的铁水脱硫处理能力,在全面比较分析了喷吹式和搅拌式脱硫工艺优缺点的基础上,决定仍采用KR脱硫工艺。
2000年11月23日,由国内设计的我国第一台140万t/ a KR脱硫“一搅双扒”装置(2号KR脱硫处理站)建成投产.加上原有1号KR脱硫站90万t/ a的处理能力,全厂铁水脱硫处理能力达到230万t/ a,具备了铁水全脱硫处理的能力。
根据不同品种钢的生产要求,采用“深脱”和“浅脱”两种铁水脱硫处理方式。
“深脱”将铁水硫脱至w(S)≤0.003 %,用于超低硫钢种的生产;“浅脱”将铁水硫脱至w(S)≤0.015 %,用于一般品种钢的生产。
KR铁水脱硫设备主要由扒渣机、搅拌器和脱硫剂储存和输送系统3个主要部分组成.武钢二炼钢KR脱硫设备的主要参数如下。
扒渣机前后行程 3~5m(最大6m)行进速度 0.5~1.5 m/s上下行程 900mm(最大1000mm)旋转角度士12. 5。
青钢KR法脱硫流场和颗粒分布影响的数值模拟

内进行 旋转 , 旋 转产 生 的漩 涡带 动脱 硫剂 与铁 水接
触 发 生 反应 , 从 而 达 到脱 硫 的 目的。 为 了提 高 K R 法 的脱硫 效率 , 奚超 超…通过数 值模 拟对 K R搅拌脱 硫 铁水 罐 内的 流场 进 行 了优 化 研究 。S h a o P i n ; 通 过 水模 型 和模拟 对 比验证 数值 模 拟 的准确 性 , 并研 究 了插 入深 度 和搅拌 转 速对 涡漩 深度 、 湍 动 能和混 匀 时 间的影 响 。程新 德 等D 通过加 入少 量颗 粒研 究 颗粒 在流 场 中的运动 轨迹 。李 志杰等 在青 钢新厂 区 投 产前 对 K R搅拌 脱 硫 进 行 了初 步 的数 值 模 拟 , 研究了 1 0 0 t 铁 水罐 标 准搅 拌 头 脱硫 时搅 拌 转 速对 铁 水 速度场 、 死 区大小 、 湍 动 能 和 涡 漩 深 度 的影 响 。2 0 1 6 年底 青 钢 新 厂 区投 产 , 本 研 究 在 文献 [ 4 ] 研 究 的基 础 上 , 通过 建 立青 钢现 场 实 际 尺寸 模 型 , 采用 F l u e n t C F D软 件 分析 不 同搅 拌 头插 入 深度 ( 搅 拌头 顶部 到 铁水 原始 液 面 的距 离 ) 和搅 拌 头直 径对
( 1北京科技大学 冶金与生态工程学院 , 北京 1 0 0 0 8 3 ; 2青岛特殊钢铁有限公司 炼钢厂 , 山东 青岛 2 6 0 0 4 3 )
摘
要: 使用 F l u e n t 软件对 青钢 K R搅拌脱硫进行 数值模拟 , 分 析搅 拌头插入深度 和直径对铁水 罐内流场和颗粒 分布的影
言
m l T l , 底 部直径 2 7 0 0 m m, 高度 3 4 0 0 m m。K R脱硫 站 使用倒 十 字型搅 拌 头 ( 4 桨 叶) , 顶 部 比底部 略大 , 尺
kr法脱硫工艺介绍[材料浅析]
![kr法脱硫工艺介绍[材料浅析]](https://img.taocdn.com/s3/m/1e25acab941ea76e59fa042a.png)
脱硫剂消耗与指标
脱硫剂配比与成分要求
脱硫剂的组成配比:石灰90%,萤石10%, 其中石灰和萤石的质量标准如下表。
其中粒度在0.5-1.0mm之间的比例大于80%,粒 度小于0.3mm和大于1.2mm的比例要求 ≤10%。
重点资料
15
脱硫剂消耗与指标
脱硫剂的加入量及搅拌时间
脱硫剂加入量(Kg) 脱硫剂个硫单耗(Kg /[S].t)铁水重量(t) (铁水初始%S-铁水目标%S)
重点资料
29
铁水脱硫处理在钢铁厂的作用
1、实现全量铁水预处理脱硫时,解放了高炉的 生产能力。 2、减轻或消除了吹氧转炉在炼钢时的脱硫负 担。 3、铁水脱硫已成为现代钢铁工业优化工艺流 程的重要手段,是连接高炉和转炉之间的桥梁, 是提高钢质量、扩大品种的主要措施。
重点资料
30
重点资料
31
搅拌系统画面
重点资料
10
KR搅拌脱硫示意图
备料加料系统画面
重点资料
11
拌脱硫示意图
液压系统画面
重点资料
12
KR法脱硫与喷吹法脱硫工艺特点对比
脱硫工艺特点对比
KR机械搅拌法,是将浇注耐火材料并经过烘烤的十字形搅拌头,浸入铁 水包熔池一定深度,借其旋转产生的漩涡,经过称量的脱硫剂由给料器 加入到铁水表面,并被旋涡卷入铁水中使氧化钙基脱硫粉剂与铁水充分 接触反应,达到脱硫目的。其优点是动力学条件优越,
铁水kr机械搅拌法脱硫概述脱硫站工艺布置及流程图铁水条件及脱硫规模kr脱硫主体设备及分布kr脱硫示意图kr法脱硫与喷吹法脱硫工艺特点对比脱硫剂消耗与指标kr脱硫法搅拌与加料操作kr搅拌头的结构与应用铁水脱硫后扒渣的重要性环境保护铁水预处理脱硫在钢铁厂的作用目录1重点资料所谓kr法脱硫是将浇注耐火材料并经过烘烤的十字形搅拌头浸入铁水包熔池一定深度借其旋转产生的漩涡经过称量的脱硫剂由给料器加入到铁水表面并被旋涡卷入铁水中使氧化钙基脱硫粉剂与铁水充分接触反应达到脱硫目的
不同脱硫剂与铁水脱硫工艺的分析和比较
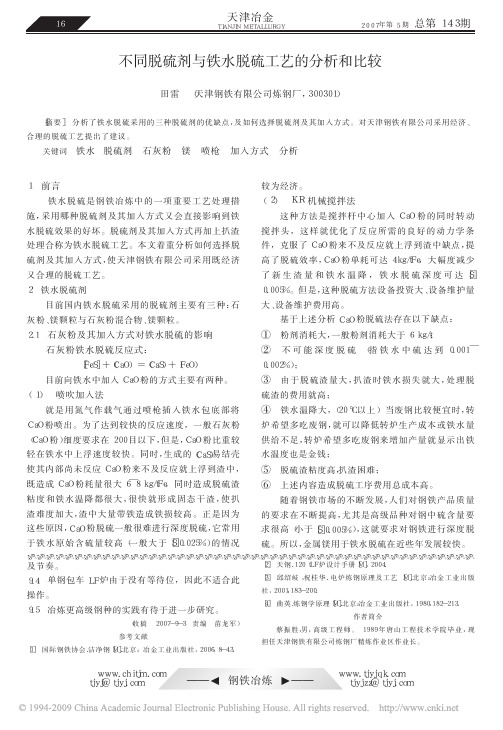
处理合称为铁水脱硫工艺。本文着重分析如何选择脱 件, 克服了 CaO 粉来不及反应就上浮到渣中缺点, 提
硫剂及其加入方式, 使天津钢铁有限公司采用既经济 高了脱硫效率, CaO 粉单耗可达 4kg/tFe, 大幅度减少
又合理的脱硫工艺。
了 新 生 渣 量 和 铁 水 温 降 , 铁 水 脱 硫 深 度 可 达 [S]
炼 铸 造 工 艺 生 产 坯 料 , 再 经 热 轧 、冷 轧 的 工 艺 流 程 进 2 钢种成分
行生产。表面带有深振痕、皮下夹杂等缺陷的铸坯, 如
表 1 是 304 型不锈钢典型钢种成分。
不 能 在 热 轧 氧 化 、酸 洗 失 重 等 过 程 完 全 消 除 掉 , 则 铸
表 1 304 系不锈钢典型钢种成分
品表面质量精美等因素, 被广泛应用于制品、家电、装 铸 坯 振 痕 深 度 状 况 , 分 析 了 振 痕 深 度 影 响 因 素 , 并 提
饰、水利、化工等行业, 是应用最广泛的不锈钢钢种。
出工艺控制措施, 降低振痕深度到 0.33 μm 以下, 达到
18- 8 型不锈钢产品规模化生产 一 般 采 用 连 续 冶 铸坯无修磨轧制要求。
2 铁水脱硫剂
0.005%。但是, 这种脱硫方法设备投资大、设备维护量
目前国内铁水脱硫采用的脱硫剂主要有三种: 石 大、设备维护费用高。
灰粉、镁颗粒与石灰粉混合物、镁颗粒。
基于上述分析 CaO 粉脱硫法存在以下缺点:
2.1 石灰粉及其加入方式对铁水脱硫的影响
① 粉剂消耗大, 一般粉剂消耗大于 6 kg/t;
就 是 用 氮 气 作 载 气 通 过 喷 枪 插 入 铁 水 包 底 部 将 ④ 铁水温降大, ( 20 ℃以上) 当废钢比较便宜时, 转
铁水预处理脱硫的优点
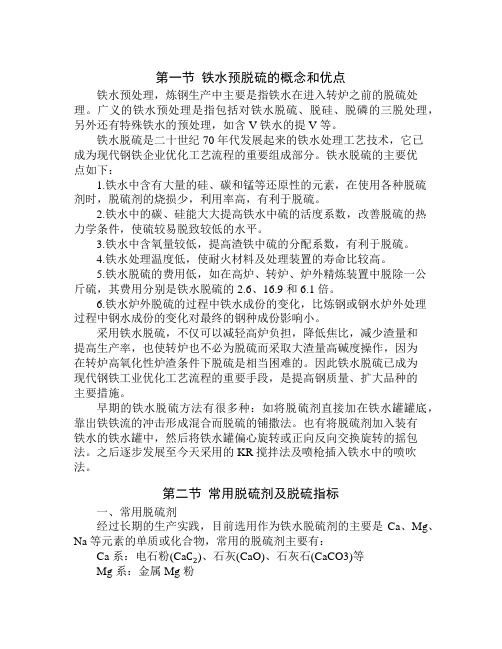
第一节铁水预脱硫的概念和优点铁水预处理,炼钢生产中主要是指铁水在进入转炉之前的脱硫处理。
广义的铁水预处理是指包括对铁水脱硫、脱硅、脱磷的三脱处理,另外还有特殊铁水的预处理,如含V铁水的提V等。
铁水脱硫是二十世纪70年代发展起来的铁水处理工艺技术,它已成为现代钢铁企业优化工艺流程的重要组成部分。
铁水脱硫的主要优点如下:1.铁水中含有大量的硅、碳和锰等还原性的元素,在使用各种脱硫剂时,脱硫剂的烧损少,利用率高,有利于脱硫。
2.铁水中的碳、硅能大大提高铁水中硫的活度系数,改善脱硫的热力学条件,使硫较易脱致较低的水平。
3.铁水中含氧量较低,提高渣铁中硫的分配系数,有利于脱硫。
4.铁水处理温度低,使耐火材料及处理装置的寿命比较高。
5.铁水脱硫的费用低,如在高炉、转炉、炉外精炼装置中脱除一公斤硫,其费用分别是铁水脱硫的2.6、16.9和6.1倍。
6.铁水炉外脱硫的过程中铁水成份的变化,比炼钢或钢水炉外处理过程中钢水成份的变化对最终的钢种成份影响小。
采用铁水脱硫,不仅可以减轻高炉负担,降低焦比,减少渣量和提高生产率,也使转炉也不必为脱硫而采取大渣量高碱度操作,因为在转炉高氧化性炉渣条件下脱硫是相当困难的。
因此铁水脱硫已成为现代钢铁工业优化工艺流程的重要手段,是提高钢质量、扩大品种的主要措施。
早期的铁水脱硫方法有很多种:如将脱硫剂直接加在铁水罐罐底,靠出铁铁流的冲击形成混合而脱硫的铺撒法。
也有将脱硫剂加入装有铁水的铁水罐中,然后将铁水罐偏心旋转或正向反向交换旋转的摇包法。
之后逐步发展至今天采用的KR搅拌法及喷枪插入铁水中的喷吹法。
第二节常用脱硫剂及脱硫指标一、常用脱硫剂经过长期的生产实践,目前选用作为铁水脱硫剂的主要是Ca、Mg、Na等元素的单质或化合物,常用的脱硫剂主要有:Ca系:电石粉(Ca C2)、石灰(CaO)、石灰石(CaCO3)等Mg系:金属Mg粉Na系:苏打(Na2CO3)二、常用脱硫剂反应特点1.电石粉碳化钙脱硫反应为用Ca C2脱硫有如下特点:1)在高碳系铁水中,Ca C2分解出的Ca离子与铁水中的硫有极强的亲和力。
- 1、下载文档前请自行甄别文档内容的完整性,平台不提供额外的编辑、内容补充、找答案等附加服务。
- 2、"仅部分预览"的文档,不可在线预览部分如存在完整性等问题,可反馈申请退款(可完整预览的文档不适用该条件!)。
- 3、如文档侵犯您的权益,请联系客服反馈,我们会尽快为您处理(人工客服工作时间:9:00-18:30)。
KR法与喷吹法在铁水预脱硫中应用的比较面对钢铁市场日趋激烈的竞争,经济高效的铁水预处理脱硫,作为现代钢铁工业生产典型优化工艺流程:“高炉炼铁—铁水预处理—转炉炼钢—炉外精炼—连铸连轧”的重要环节之一,已经被广泛的应用于实际生产。
随着社会经济和钢铁工业的高速发展,社会对钢铁质量的要求越来越高、越来越苛刻,产品的种类也急剧增加,尤其是高品质高附加值钢种的需求不断在增大。
面对钢铁市场日趋激烈的竞争,经济高效的铁水预处理脱硫,作为现代钢铁工业生产典型优化工艺流程:“高炉炼铁—铁水预处理—转炉炼钢—炉外精炼—连铸连轧”的重要环节之一,已经被广泛的应用于实际生产。
近30年来铁水脱硫技术迅速发展,现已经有十几种处理方法,其中应用最广且最具代表性的主要是喷吹法和KR机械搅拌法。
它们在技术上都已相当成熟,从两种工艺在实际生产中的应用效果来看,二者是互有长短。
虽然喷吹法发展迅速,目前在实际生产中应用更广泛,可KR法在这几年中又有了新发展,呈现出强劲的势头。
那么,这两种工艺模式各有什么优劣势?哪种更具有应用前景呢?在国内外冶金界始终没有较统一的看法。
为此,本文着重就两种工艺模式的发展、应用和运营成本作了比较,尤其是它们对整个流程影响的比较,希望能对技术人员及企业技术的选择提供参考。
KR法与喷吹法的工艺及特点在进行比较前,先了解两种方法的工艺及特点是很有必要的,不仅有利于理解两种方法的实质,也是深刻理解对两种脱硫模式分析比较的前提。
KR机械搅拌法,是将浇注耐火材料并经过烘烤的十字形搅拌头,浸入铁水包熔池一定深度,借其旋转产生的漩涡,使氧化钙或碳化钙基脱硫粉剂与铁水充分接触反应,达到脱硫目的。
其优点是动力学条件优越,有利于采用廉价的脱硫剂如CaO,脱硫效果比较稳定,效率高(脱硫到≤0.005 %) ,脱硫剂消耗少,适应于低硫品种钢要求高、比例大的钢厂采用。
不足是,设备复杂,一次投资较大,脱硫铁水温降较大。
喷吹法,是利用惰性气体(N2或Ar)作载体将脱硫粉剂(如CaO,CaC2和Mg)由喷枪喷入铁水中,载气同时起到搅拌铁水的作用,使喷吹气体、脱硫剂和铁水三者之间充分混合进行脱硫。
目前,以喷吹镁系脱硫剂为主要发展趋势,其优点是设备费用低,操作灵活,喷吹时间短,铁水温降小。
相比KR法而言,一次投资少,适合中小型企业的低成本技术改造。
喷吹法最大的缺点是,动力学条件差,有研究表明,在都使用CaO基脱硫剂的情况下,KR法的脱硫率是喷吹法的四倍。
KR法与喷吹法的发展及现状从前面分析二者的方法和特点可以知道,它们互有长短、各具特色,这也决定了它们的发展历程和现状必然是不同的。
进一步了解它们的发展和现状,将更有利于理解各自技术的特点。
从时间上来看,喷吹法的研发及应用要早于机械搅拌法。
喷吹法主要有原西德Thyssen的ATH(斜插喷枪)法、新日铁的TDS(顶吹法)和英国谢菲尔德的ISID法,早在1951年,美国钢厂就已成功地运用浸没喷粉工艺喷吹CaC2粉进行铁水脱硫。
直至今日,尽管两种脱硫工艺方法在技术上都已相当成熟,全世界绝大多数钢铁厂广泛采用仍是铁水喷粉脱硫工艺。
机械搅拌法有原西德DO (Demag-Ostberg) 法、RS (Rheinstahl) 法和赫歇法, 日本新日铁的KR (Kambara Reactor) 法和千叶的NP 法,其中,以KR法工艺技术最成熟、应用最多。
KR法搅拌脱硫是日本新日铁广钿制铁所于1963年开始研究,1965年才实际应用于工业生产,之后迅猛的发展趋势表明,它具有投入生产使用较早的喷吹法无可比拟的某种优势。
在冶金工业中喷吹这种形式应用非常广泛,比如在转炉及精炼工艺中的各种顶吹、底吹和复吹技术等。
当铁水预处理时,使用喷吹法把脱硫剂加入铁水中进行脱硫,这显然是可行的且易于人们接受。
最早脱硫剂是以氧化钙基为主,辅助添加CaC2,而且喷吹过程也很难获得较好的动力学条件,这时主要面临两个问题:一是,如何保证CaC2的安全存贮运输和脱硫剂的脱硫效果;二是,怎样解决因动力学不足导致的脱硫效率低下,不能实现深脱硫的问题。
第一个问题侧重于开发使用更具有脱硫效率且安全的脱硫剂,于是出现了镁基复合喷吹法,脱硫效果有所改善却成效不大,而且镁粉在运输、储存、使用中同样存在很多的安全隐患,给生产带来诸多不便。
然而,新型脱硫剂——钝化颗粒镁的开发成功,使纯镁喷吹脱硫技术得以实现,达到了真正高效安全的工艺目标,目前,镁系脱硫剂已经成为世界铁水预处理中的主导脱硫材料。
针对第二个问题,如何才能获得更好的动力学条件呢?从工艺模式着手,技术人员研发出了具有实际应用价值的机械搅拌脱硫法,其中以KR法为典型,在根本上改善了脱硫过程中的动力学条件,并可以在脱硫剂中不加CaC2而主要采用CaO,避免了生产中使用CaC2而带来的不便和危险。
然而,在工业应用时却又出现许多技术难题,比较突出的如,搅拌头的使用寿命较短;单工位操作设备导致更换搅拌头的同时无法进行铁水脱硫等。
可最终这些难点还是被陆续攻破,解决了搅拌头的寿命问题,使其从原来的几十炉提高到现在的几百炉,而且摸索出了氧化钙基脱硫剂应该有一个最佳的指标要求,可以达到最理想的脱硫效果。
目前,KR 法已经完全可以达到深脱硫的要求,即把铁水中的硫脱至小于0.005%-0.001%。
同时,双工位布置形式的出现克服了单工位的不足,使生产的连续化程度得以提高。
很长时间,KR法成本问题(尤其是前期投资)加上其过程时间较长,以及不适应于大型铁水罐,故发展缓慢;直至二十世纪后期,其投资降低后,加上运行费用低廉,所以又受到了重视。
KR法与喷吹法的比较从铁水脱硫工艺倍受人们的重视以来,KR法与喷吹法技术一直处于发展之中,目前虽仍需完善可也已趋近于成熟,这样两者之间才更具备可比性,本文主要从以下几文面进行具体比较。
1 技术与设备在喷吹法中,单吹颗粒镁铁水脱硫工艺因其设备用量少、基建投入低、脱硫高效经济等诸多优势而处于脱硫技术的主要发展趋势之一,可在相当长的时间我国都是引进国外的技术和设备。
到2002年10月国内才首次开发出铁水罐顶喷单一钝化颗粒金属镁脱硫成套技术设备,整套装置中,除重要电器元器件采用进口或合资的外,其余机电产品100%实现了国产化,包括若干最关键的技术设备。
喷吹技术和设备的国产化直接降低了建设投资和运行操作的成本,从前期的一次性投资来看,要比KR法略有优势。
虽然搅拌法的技术专利也是国外拥有,可从其设备和技术本身而言并没有难点,机械构成是常规的机械传动和机械厂提升;加料也采用的是常规大气压下的气体粉料输送系统,可以说在系统的机、电、仪、液等方面的技术应用都是十分成熟。
尽管如此,KR 法设备仍然是重量大且较复杂,可它的优势是运营操作费用低廉,由此所产生的经济效益完全可弥补前期的一次性高额投资。
根据有关推算,一般3~5年即可收回所增加的投资。
2000年武汉钢铁设计研究院针对武钢二炼钢厂的情况,对KR 法和喷吹法两种方案的投资进行了估算,KR 法的投资估算比喷吹法投资估算多200万元。
2 脱硫效果实际生产过程中的铁水脱硫效果,不仅与设备有关,而且受脱硫剂、操作工艺水平、时间及温度等诸多因素影响,本文主要考虑的是纯镁喷吹法和CaO 基KR法。
一般对铁水预处理的终点硫含量要求是不高于50ppm,工厂生产和实验研究结果表明,喷吹法因其脱硫剂Mg的较强脱硫能力,KR法由于其表现出色的动力学条件,在可以接受的时间内(一般≤15min),它们都能达到预处理要求的目标值。
国内各大钢厂的具体脱硫数据可见表1。
在喷吹法中,复合脱硫剂使用CaO比例越高,脱硫效果越差,使用纯镁时脱硫率最高;KR法使用CaO脱硫剂,脱硫率只是略低于喷吹纯镁。
3 温降铁水温降的消极影响是降低了铁水带入转炉的物理热,主要体现在转炉吃废钢的能力下降,导致转炉冶炼的能耗和物料消耗升高,直接影响了冶炼的经济成本。
KR法因动力学条件好,铁水搅拌强烈,而且CaO的加入量较大,导致温降也大,目前国内KR法工艺应用较成熟的武钢可以使温降控制在28℃左右。
相比之下,镁基的脱硫温降都比较小(参照表1),主要原因有以下三点:喷吹法动力学条件差,铁水整体搅拌强度不大,热量散失少;金属镁的脱硫反应过程是个放热反应;镁的利用率高,脱硫粉剂加入量少。
4 铁损铁水预处理脱硫过程的铁损主要来自于两部分:脱硫渣中含的铁和扒渣过程中带出的铁水。
由于两种工艺模式的不同,实际渣中含铁和扒渣带出铁量都有较大的差别,目前没有公开发表的详细对比数据。
一方面,较少的脱硫剂产生的脱硫渣少,则渣中含铁量也低,由此颗粒镁喷吹脱硫的铁损要少一些;另外,颗粒镁喷吹脱硫的渣量少,扒净率相对低,而KR法的脱硫渣扒净率相对高。
就扒渣的铁损而言,由于还取决于高炉渣残留量及扒渣过程,综合考虑看KR法与喷吹法区别不大。
究竟哪个是主要因素,与各钢厂的实际操作有很大的关系,通过换算,得出具体数据可见表2。
可见,喷吹法时,采用脱硫剂的CaO含量越高,则扒渣铁损越大;而KR法使用CaO作为主要脱硫剂成分,其铁损只是略高于喷吹镁脱硫铁损。
5 脱硫剂铁水预处理过程中,脱硫剂是决定脱硫效率和脱硫成本的主要因素之一。
根据日本新日铁曾做的计算,脱硫剂的费用约为脱硫成本的80%以上,所以,脱硫剂种类的选择是降低成本的关键。
然而,选择时必须得结合考虑不同工艺方法的特点。
基于动力学条件和脱硫效率,目前喷吹法主要采用的是镁基脱硫剂,KR 法采用的是石灰脱硫剂。
根据理论计算,在1350℃,镁脱硫反应的平衡常数可达3.17×103,平衡时的铁水含硫量可达1.6×10-5%,大大高于CaO的脱硫能力。
然而,上文已经把两种脱硫剂在各自工艺中的脱硫效果进行了对比,表明,结合实际生产工艺后它们都能达到用户对脱硫的最高要求。
在脱硫方式选择时还要考虑脱硫剂的一个因素,就是脱硫剂的来源问题。
一般而言,大部分钢铁生产企业都要使用石灰石,要么有自己的石灰厂,要么有稳定的协作供货渠道,来源稳定,成本稳定,而且供货及时,不用考虑仓储问题。
虽然我国的金属镁资源丰富,可是相对钢铁企业来说,获得搅拌法所需的CaO基脱硫剂更为容易,钝化颗粒镁就不具备这些有利因素。
℃左右。
相比之下,镁基的脱硫温降都比较小(参照表1),主要原因有以下三点:喷吹法动力学条件差,铁水整体搅拌强度不大,热量散失少;金属镁的脱硫反应过程是个放热反应;镁的利用率高,脱硫粉剂加入量少。