数控系统信息采集
FANUC数控系统的机床数据采集

FANUC数控系统的机床数据采集(2012-05-24 14:13:55)▼分类:机床数据采集及监控标签:发那科fanuc数据采集0i16i18i同西门子数控系统一样,日本发那科(FANUC)生产的数控系统是全球数控机床上装备的主要的系统之一。
从上世纪70年代以来,其生产的系统种类较多,较常用的如早期的FANUC 0/6/15/18系统等,后随着数字驱动技术和网络技术等技术的发展,又推出了i系列的系统,如FANUC 0i/15i/16i/18i/21i/31i等数控系统。
早期的FANUC系统开放性差,通常使用宏程序和硬件连接方式进行数据采集,但采集的数据比较少,而且实时性差,对加工和操作带来影响。
但这类系统目前已逐渐淘汰,使用量比较小。
在i系列数控系统中,由于配置的不同,则可使用不同的方法进行数据采集。
在配有网卡的数控系统中可利用FANUC系统的数据服务功能实现数据采集。
在FANUC的许多系统中网卡都是选件,而在最新的系统上,网卡逐渐变成了标准配置,如FANUC 0i-D等。
制造数据管理系统MDC对于具有以太网的FANUC数控系统,可采集的数据量也非常多。
典型的数据包括:–操作方式数据:手动JOG、MDA、自动、编辑等–程序运行状态:运行,停止,暂停等–主轴数据:主轴转速、主轴倍率,主轴负载,主轴运转状态–进给数据:进给速度、进给倍率–轴数据:轴坐标,轴负载–加工数据:当前执行的程序号;当前使用的刀具–报警数据:报警代码、报警和信息容所有数据均实时后台采集,不用任何人工干预。
制造数据管理系统M对于不具有以太网的FANUC i系列的数控系统,也可采集大量的数据。
典型的数据包括:–操作方式数据:手动JOG、MDA、自动、编辑等–程序运行状态:运行,停止,暂停等–主轴数据:主轴转速、主轴倍率,主轴负载,主轴运转状态–进给数据:进给速度、进给倍率–加工数据:执行的程序号;使用的刀具号–报警数据:NC报警和PLC报警状态所有数据均实时后台采集,不用任何人工干预,也无需修改NC程序。
数控机床数据采集
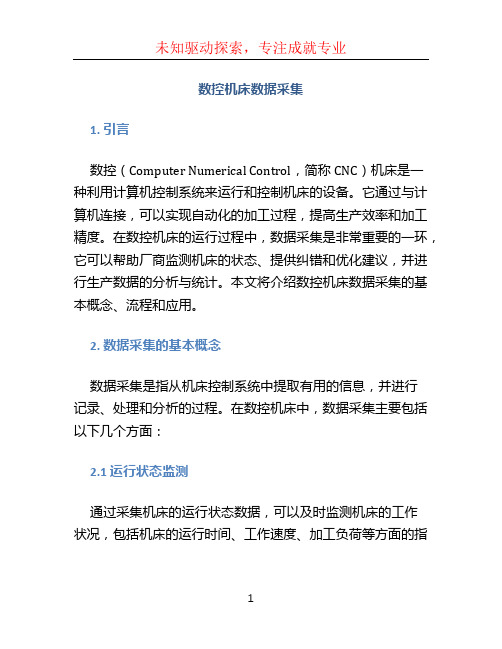
数控机床数据采集1. 引言数控(Computer Numerical Control,简称CNC)机床是一种利用计算机控制系统来运行和控制机床的设备。
它通过与计算机连接,可以实现自动化的加工过程,提高生产效率和加工精度。
在数控机床的运行过程中,数据采集是非常重要的一环,它可以帮助厂商监测机床的状态、提供纠错和优化建议,并进行生产数据的分析与统计。
本文将介绍数控机床数据采集的基本概念、流程和应用。
2. 数据采集的基本概念数据采集是指从机床控制系统中提取有用的信息,并进行记录、处理和分析的过程。
在数控机床中,数据采集主要包括以下几个方面:2.1 运行状态监测通过采集机床的运行状态数据,可以及时监测机床的工作状况,包括机床的运行时间、工作速度、加工负荷等方面的指标。
这些数据可以用来判断机床的性能是否正常,是否需要进行维护和保养。
2.2 故障诊断与纠错数据采集还可以用于故障诊断与纠错。
通过采集机床运行过程中的异常数据和错误信息,可以判断出可能存在的问题,并进行相应的调整和修复。
这可以提高机床的稳定性和可靠性,减少故障停机时间。
2.3 生产数据分析与统计对机床生产过程中的数据进行分析和统计,可以得到生产过程的特征和规律。
这有助于优化生产过程,提高生产效率和产品质量。
同时,也可以根据数据分析的结果进行生产计划的调整和优化,以满足不同的订单需求。
3. 数据采集的流程数控机床数据采集的流程主要包括数据获取、数据传输、数据处理和数据存储等多个环节。
下面将对每个环节进行详细介绍。
3.1 数据获取数据获取是指从数控机床中提取数据的过程。
数控机床的控制系统通常会提供各种接口和协议,用于与外部设备进行数据交换。
可以通过这些接口将数据传输到数据采集设备上。
数据获取的方式可以是实时采集,也可以是定期采集,根据实际需求进行选择。
3.2 数据传输数据传输是指将采集到的数据传输到数据处理设备的过程。
数据传输可以通过有线或无线方式进行,常见的有以太网、USB和Wi-Fi等。
MDC机床监控与数据采集解决方案

网卡 网卡 网卡 网卡 网卡/串口
西门子 PLC
网卡/串口
欧姆龙 PLC
网卡/串口
采集协议及授权情 况 FOCAS 专用
EZSocket
OPCUA 或专用协 议
DDE 或 OPCDA
OPCUA 或直接采 集
直接采集
备注 全系列免授权 M70/M80/C70 系列免授 权 专用协议免授权 含 PCU 为 windows XP、NT 系统 免授权 免授权
,[IDnum] ,[MachineSN] ,[MachineType] ,[MachineIP] ,[MachineMode] ,[MachineStatus] ,[PowerOnTime] ,[RunningTime] ,[CuttingTime] ,[ProcessingPart] ,[CurrentProgramName] ,[ProcessingCount] ,[ProcessedCount] ,[SpindleLoad] ,[SpindleSpeed] ,[FeedSpeed] ,[SpindleOverride] ,[FeedOverride]
术服务为主导、立足于离散制造业科技领域,专业致力于工业设备数据采集的科技企业。 本着“质量争优、诚信为本”的朴素经营理念,严格按照现代企业模式进行管理运营,致力 成为中国智能制造工业软件和工业互联网的一支劲旅。
乐芯科技是专注于 DNC、MDC 和工业设备智能网关的和软硬件服务。公司主要面向 离散制造企业提供专业技术咨询、智能制造整体解决方案,主要客户包括航空、航天、装 备、汽车、石油等制造业客户,为客户提供包括数控机床联网 DNC、数控机床数据采集 MDC、制造数据管理 NCM 和工业设备智能网关的产品和服务,帮助传统企业转型升级, 支持并促进实现互联网工业和智能制造。
《基于Flink的机床状态实时采集与监控系统的设计与实现》

《基于Flink的机床状态实时采集与监控系统的设计与实现》一、引言随着工业 4.0时代的到来,智能制造成为了工业发展的新趋势。
机床作为制造业的核心设备,其实时状态采集与监控对于提高生产效率、降低故障率具有重要意义。
本文将介绍一种基于Flink的机床状态实时采集与监控系统的设计与实现,以实现对机床状态的实时监测和数据分析。
二、系统需求分析本系统的主要目标是实现对机床状态的实时采集、监控和分析。
为此,我们需要分析系统所需的功能模块、性能需求和安全性需求。
功能模块包括:1. 数据采集模块:负责从机床传感器中实时采集数据。
2. 数据传输模块:负责将采集的数据传输至数据中心。
3. 数据处理模块:负责对数据进行实时处理和分析。
4. 监控展示模块:负责将处理后的数据以图表等形式展示给用户。
性能需求包括:1. 实时性:系统应能在短时间内对机床状态进行实时监测。
2. 准确性:系统应能准确采集和传输机床状态数据。
3. 可扩展性:系统应具有良好的可扩展性,以适应不同类型和规模的机床。
安全性需求包括:1. 数据加密:确保数据在传输过程中的安全性。
2. 权限控制:确保只有授权用户才能访问系统。
三、系统设计本系统采用Flink作为核心处理引擎,实现机床状态的实时采集、传输、处理和监控。
系统架构主要包括数据采集层、数据传输层、数据处理层和监控展示层。
数据采集层通过传感器实时采集机床状态数据,并将其传输至数据传输层。
数据传输层采用可靠的数据传输协议,将数据传输至数据中心。
数据处理层利用Flink对数据进行实时处理和分析,包括数据清洗、统计分析等。
监控展示层将处理后的数据以图表等形式展示给用户。
四、关键技术实现1. 数据采集:采用传感器技术,实时采集机床状态数据。
为保证数据的准确性和实时性,需选择合适的传感器和采样频率。
2. 数据传输:采用可靠的数据传输协议,如MQTT或Kafka 等,将数据从机床传输至数据中心。
为保证数据的安全性,需对数据进行加密处理。
基于Web的数控机床信息采集技术研究

CX A A公 司 的 “ 能 终 端 ” 品作 为 异 步 串 口服 务 智 产 器 , 用数 控系 统 串 口打 印语 句 , 行 数控 加工 信 利 进 息 采集 技术 研究 。
3 信 息采 集的数 据库 结构
匹配 的通 信 软件则 是 根据 不 同 的应 用 需要 和数 控 系
统 的不 同 自行 研究 开 发或 定 制 , 日本 F N C公 司 以 A U 的 O 系统 为 例 ( 同 ) 要 实 现 P i 下 , C机 与 F N C 的 A U
。
信 息采集原理实 际是基 于 网络 化制 造技 术平 台 , 调用 C C系统 变量 , N 通过 变 量读 和写 C C的各 种 内 N
l 2
在 现 有 的 技 术 条 件 下 , 信 服 务 器 、 络 交 换 通 网 机、 无线 网 卡及 各 类 数 控 机 床 均 有 非 常 成熟 的 产 品 及 附带通 讯 接 口可供 选 择 。异 步 串 口服务 器 及 与 之
发是 整个 远程监 控技 术平 台 的核 心技 术 。本 论 文 以
示, 所有 被管理 数据 均置 于服务 器数据库 中。 ( ) 2 交
图 1 信 息 采 集 的 网 络 化 制 造 技 术 平 台
换 机 : 通信 服 务 器端 和无 线 路 由器端 需 要 传 输 的 将 信 息打包传 输 。 ( ) 线 路 由器 : 3无 利用 不 同的 I P地
设备 是异 步 串 口服务器 。
收稿 日期 :0 0— 6— 1 2 1 0 2
作者简介 : 范彩霞(9 6 , , 17 一)女 河南 _ ̄峡人 , -- -j 黄河科技学 院工学院机械系讲师 , 工学硕士, 主要从事数字化制造研究。 路素青 (94一) 男 , 17 , 河南安阳人 , 黄河科技学院讲师 , 硕士 , 研究 方向 : 工程管理 。
“数控系统装调与维护”教学情境设计——应用六步教学法

2 演 示制 定项 目进程表 。 )
第教学背景
教学 目标 : 过本课的学 习使学 生掌握数 通 控通 道、伺服通道与 F S S B的参数设置方法 , 理 解数控通道 、伺服通道 与 F S S B的参数设 置功 能及应用 方法 。 本课完成 时 间为 6学时 , 学生 人数 为 4 0 人, 1 组, 分 0 每组 完成数控通道 、伺服通道 与 Fs S B的参数设置操 作。 学生已经掌握的知识 : 数控机 床的结构和 控制原理 ; 数控系统的组成和硬件连接 ; 数控机 床的 控制面板 操作 。 运 用 的设 备及 辅 助工具 : 功 能数 控车 全 床 、加 工中心实切系统( f 系统 :ANUC 0) F i 工具 : 字万 用 表 、螺 丝 刀 。 数 准 备 的文 件 : 目任 务 书 、 实 训 指 导 项 书 、FAN UC 0 ~M D 参数 说 明书 B一 i 6 3 0 M一 1 4 1 C 0 、评分标 准、F ANUC i 0 地 址 表 、实 训 报 告 册 (包 括 实 训 操 作 步 骤 记 录 、 评 分 表 、 实 训 分析 和 总 结)。
教 育教 学研 究
“ 控系统装调 与维护 "教 学情境 设计 数
应用六步教学法
陈志平 杨金鹏 ( 四川信息职业技术学院 四川广 元 6 8 1) 20 7 【 要】传 统教 学过 程 中以教 师讲授 为主 , 摘 学生 只能被 动 的接 受 。在实 训课 中传 统的表 学方法 已不能 充分激发 的学 - 鬻趣 。 学生 V 无法 使 学生 更好 的提 高操 作技能 , 使实训课逐渐 变得枯 燥无味 。本文 参照 《 国家职业标 准 : 数控机床装 调维修 工》和数控设备 应.-’ 护专 q ̄ I l l 业人 才培 养计 划 , 主要 研 究 “ 步教 学法 ” 在 “ 六 数控 机床 蓑调 与堆护 ”课 程 中的应 用方 法和教 学情境 设 计 。 【 关键 词l六 步教 学法 参数设 置 教 学情境 设计 【 中图分类 号】G4 1 2 4. 【 献标 识码 】A 文 【 文章编号】1 7 —8 ( 0 0 -0 5 -0 292 1)7 20 2 63 0 0
数控机床的数据采集与分析方法

数控机床的数据采集与分析方法数控机床是一种高精度、高效率的机械设备,广泛应用于制造业的各个领域。
为了实现对数控机床的监控和优化,数据采集与分析方法是至关重要的。
本文将探讨数控机床的数据采集方式以及如何利用这些数据进行分析。
一、数据采集方式1. 传感器数据采集:通过安装传感器在数控机床的各个部位,如进给轴、主轴、刀库等位置,采集到机床运行时的各种物理量,如温度、振动、电流等。
利用这些传感器采集的数据,可以获取到机床在运行过程中的状态信息。
2. PLC数据采集:数控机床通常配备了可编程逻辑控制器(PLC),它可以通过读取和记录机床的输入输出信号,来实现对机床运行状态的监控。
通过提取PLC的数据,可以了解机床的运行时间、工件加工质量以及故障诊断等信息。
3. 数据采集系统:数控机床可以配备专门的数据采集系统。
该系统通过与机床控制系统的数据接口通信,实时获取机床的运行状态数据。
这样的系统可以提供更加详细和全面的数据采集,包括工件的加工参数、刀具状态以及轴向位置等。
二、数据分析方法1. 统计分析:通过对采集到的数据进行统计分析,可以得到机床运行过程中的常规参数统计,如平均值、方差和标准差等。
这些统计数据可以用来评估机床的稳定性和性能,比如工件尺寸的精度和表面质量的均一性等。
2. 趋势分析:将采集到的数据进行时间序列分析,可以得到机床的运行趋势。
通过观察趋势的变化,可以发现机床运行过程中的异常情况,如加工误差的积累、刀具磨损的增加等。
这样的分析可以帮助制定合理的维护计划,提高机床的稳定性和可靠性。
3. 故障诊断:通过对采集到的数据进行故障诊断分析,可以实现对机床故障的及时发现和处理。
通过比较机床的实际运行数据与预设的参数,可以检测机床是否存在异常现象,如传感器故障、电机电流超载等。
利用故障诊断分析,可以提前预警并避免机床故障的发生。
4. 数据挖掘:利用数据挖掘算法,可以从大规模的机床数据中发现潜在的规律和关联。
数控机床技术中的加工过程监控与数据分析

数控机床技术中的加工过程监控与数据分析在现代制造业中,数控机床已经成为关键设备之一。
数控机床技术的发展,不仅大幅提高了加工效率和质量,还使得机械加工与信息技术相结合,为制造业的智能化发展打下了坚实基础。
而在数控机床技术中,加工过程的监控与数据分析则起到了至关重要的作用。
加工过程的监控是通过对数控机床及其设备进行实时监测和数据采集,以实现对加工过程参数的控制和优化。
通过监控加工过程中的各项指标数据,我们可以及时发现问题、调整参数,并保证加工质量的稳定性和可靠性。
同时,监控还可以有效降低机床的故障率,延长设备的使用寿命。
另外,加工过程的监控还可以实现对加工效率的提高,进而降低生产成本,提高企业的竞争力。
在加工过程的监控中,数据分析起到了至关重要的作用。
通过对大量采集到的数据进行处理和分析,我们可以获得有关加工过程中各项参数的趋势和变化情况,从而进行合理的调整和优化。
数据分析可以帮助我们找出加工过程中的潜在问题,预测设备的故障和维护需求,及时采取措施,避免生产中断和设备损坏。
此外,通过数据分析,我们还可以挖掘加工过程中的隐藏信息和规律,优化工艺参数,提高加工效率和质量。
要实现加工过程的监控与数据分析,首先需要选择合适的监控装置和传感器。
这些装置和传感器能够测量和采集机床运行状态、材料特性、工具磨损程度等关键参数的数据,以便后续的分析和处理。
同时,为了能够实时监控和分析数据,还需要建立相应的数据采集和传输系统,确保数据的可靠性和及时性。
在数据分析方面,需要借助一些先进的技术和工具。
其中,机器学习和人工智能技术是十分有效的工具。
通过对大量数据的学习和训练,机器学习系统可以在日常生产中自动识别和归纳出一些重要的特征和规律。
人工智能技术则可以模拟人类的思维过程,进行智能判断和决策。
这些技术的应用可以在很大程度上提高加工过程的监控和数据分析的效率和准确性。
最后,值得注意的是,加工过程的监控与数据分析并不是一次性任务,而是一个持续不断的过程。
DNC数据采集

第4页
DNC系统-功能简介
DNC系统作为车间层控制系统的一个功能单元。 DNC系统功能: ①NC程序及数据的传递,以某种通信协议(如Philip532等)实现通信 功能; ②机床状态采集和上报; ③根据工序计划,自动分配NC程序及数据到相应机床; ④刀具数据的分配与传递。 DNC系统软件的功能模型: ①NC数据管理的主要功能是对数控数据进行管理,主要有数控数据 的显示、插入、修改、删除、更新、锁定(不允许更改)和打印等操 作; ②NC数据执行的主要功能有:数控数据在计算机和机床之间的传送 、删除机床上的数控数据、启动机床上的数控程序、随时从机床设 备获得工作状态信息并存入数据库,作为运行数据采集模块评价加 工过程的根据; ③DNC通讯接口通过DNC协议和数据链路协议建立单元控制系统和 CNC的连接。
第 10 页
DNC数据采集-实现amp;A
第5页
DNC数据采集-实现方式
功能 名 称 说明
宏功能数据采集 状态汇报特殊程序 工况数据采集器
利用内置的宏程序处理模块采集正在执行的NC 程序名(零件名称)、加工开始时间、结束时间 向 DNC 主机传送含有当前状态信息的程序 利用工况数据采集器采集生产现场数据
第6页
DNC数据采集-宏功能
DNC具有多种数据采集方法,全面解决车间环境中的数控与非数控 加工设备、检测、装配设备的工况数据采集。 (1)宏功能自动采集 利用NC 程序宏功能后置处理技术将数控程序处理成能够实现 工况数据采集的程序,能解决量大面广的FANUC 系列数控设备的 数据采集。 实现下列数据的采集: ������ 当前程序名(零件名称) ������ 加工开始时间/加工结束时间、 ������ 主轴转速/进给速度、 ������ 当前刀具号…
基于C#.NET的数控机床实时数据采集系统设计与编程

(Wuxi Institute of Technology,Wuxi 214121,CHN)
Abstract: In order to realize network monitoring and centralized management of FANUC CNC machine tools in the workshop.one method is proposed.C}}multi—thread programming based ()n FOCAS calling is adopted in dot NET platform ,and operation mode,running state and other data can be acquired and saved.At the sam e time user interface is updated too.The applicaton shows that data acquisition and display for muhi— pie m achines can be achieved.The acquiring system has good expansion perform ance and can be easy to install and debug on site,SO it is the basis of inform ation system integration ira the workshop.
2017年 度 汀 苏 省 第 五 期 “333丁 程 ”科 研 资 助 立项 项 目(苏 人 才办 [2017]l9号 );“数 控 机 床 刀 具 智 能 化 管 芙键 技 术研 究 ”(BRA2017480)
2018 各系统CNC 数据采集方法

(VNC, HCN, FJB- WinXP
D4
II)
Matrix Nexus (QTN-II, MTN, STN)
WinXP
D4
Matrix (INTEi150)
WinXP
C9
Matrix (INTEi200)
WinXP
D1
Matrix (INTE-J)
WinXP
D2
–
Matrix II (eSeries)
基本信息
NC 数据
加工数据
刀具信息
开 关 报 报 报 报 设 程 加 产 进 进 主 主 主 各 当 刀具
机 机 警 警号 警 警 备 序 工 量 给 给 轴 轴 轴 轴 前 寿命
时时状
信时状号时
F倍转倍 负负刀
间间态
息长态
间
率速率 载载具
S
号
调试测试软件
4、国产数控系统
国产数控系统采集 广州数控 980TDI/988 等网卡系列机床、华中数控 8 系 列、凯恩帝 KND 最新网卡系列机床都支持数据采集,并且数据采集都很全 面。
5. MAZAK 采集方式/大畏 OKUMA (O-API) MAZAK 官方方式必须开通 MTConnect,购买机床请要求开通,否则后期
费用较高。
大畏 OKUMA OSP200/300 开通(O-API)采集数据量很多。
Mazak
系统包括
CNC Model
CNC O/S
CNC Main s/w ver
二次开发。
–
–
Win7
n/a
8/20/10 v1.1
1/5/10
v1.1
VTC
11/5/10 v1.1
《基于Modbus的数控系统监控功能设计与实现》

《基于Modbus的数控系统监控功能设计与实现》一、引言随着工业自动化技术的不断发展,数控系统在制造业中的应用越来越广泛。
为了提高数控系统的可靠性和效率,监控功能的设计与实现显得尤为重要。
Modbus作为一种常用的工业通信协议,具有广泛的兼容性和可靠性,因此在数控系统监控功能的设计与实现中得到了广泛应用。
本文将介绍基于Modbus的数控系统监控功能的设计与实现,为相关领域的研究和应用提供参考。
二、系统概述本系统基于Modbus通信协议,实现对数控系统的实时监控。
系统主要由上位机监控软件、Modbus通信模块、数控系统三部分组成。
上位机监控软件负责数据的采集、处理和显示,Modbus通信模块负责与数控系统进行数据交换,数控系统则负责执行监控指令。
三、功能设计1. 数据采集:通过Modbus通信模块实时采集数控系统的各种数据,包括机床状态、电机运行数据、加工参数等。
2. 数据处理:上位机监控软件对采集到的数据进行处理,包括数据格式转换、数据存储、数据分析等。
3. 实时显示:将处理后的数据以图表、曲线等形式实时显示在监控界面上,方便操作人员查看。
4. 报警功能:当数控系统出现异常时,系统应能及时发出报警,提醒操作人员进行处理。
5. 远程控制:通过上位机监控软件实现远程控制功能,包括远程启动、停止、急停等操作。
6. 数据存储与查询:将历史数据存储在数据库中,方便后期查询和分析。
四、实现方法1. 硬件设计:硬件部分主要包括Modbus通信模块和数控系统。
Modbus通信模块应具备高速、稳定的数据传输能力,以保证数据的实时性和准确性。
数控系统应支持Modbus通信协议,以便与上位机监控软件进行数据交换。
2. 软件设计:软件部分主要包括上位机监控软件和Modbus 通信协议的实现。
上位机监控软件应具备友好的界面和丰富的功能,方便操作人员使用。
Modbus通信协议的实现应遵循标准规范,以保证数据的可靠传输。
3. 数据处理与显示:上位机监控软件通过Modbus通信模块实时采集数据,对数据进行处理后以图表、曲线等形式显示在界面上。
数控机床的数据采集与分析方法

数控机床的数据采集与分析方法随着信息技术的发展,数据采集和分析在数控机床的制造和维护中起着至关重要的作用。
数据采集可以帮助生产厂家实时监测机床的运行状态、性能指标和生产情况,而数据分析则可以帮助厂家优化生产过程、提高机床的使用效率和预测故障。
一、数据采集方法1. 传感器采集:数控机床普遍配备了各种类型的传感器,如温度传感器、压力传感器、振动传感器等,用于采集机床不同部件的运行情况。
通过传感器采集到的数据可以及时反馈到系统中,帮助监测机床的工作状态。
2. 数字控制系统采集:数控机床的数字控制系统可以采集到各种运行参数和状态信息,如主轴转速、进给速度、切削力、功率消耗等。
这些数据可以通过数字接口传输到外部计算机系统,以供进一步分析和利用。
3. 人工采集:除了传感器和数字控制系统采集的数据,操作人员也可以通过观察和记录的方式采集一些关键数据,如故障发生时间、生产数量、停机时间等。
二、数据分析方法1. 统计分析:通过对采集到的数据进行统计分析,可以发现机床的运行模式和规律,如设备的平均运行时间、故障发生的频率和位置等。
这些统计结果可以帮助厂家对设备的使用情况进行评估,制定更合理的生产计划。
2. 故障诊断:利用机床采集到的数据,结合故障数据库和专家经验,可以对机床的故障进行诊断。
通过分析故障发生时的数据特征,可以快速定位故障原因,减少停机时间和维修成本。
3. 运行参数优化:利用数据分析的方法,可以分析机床在不同参数设置下的性能表现,如主轴转速、进给速度等。
通过对数据的分析,可以找到最佳的参数组合,实现机床的最佳运行状态,提高生产效率和产品质量。
4. 预测维护:利用历史数据和机器学习算法,可以建立机床的故障预测模型。
通过对机床运行数据的分析,可以提前预警设备可能发生的故障,并采取相应措施,避免设备停机和生产中断。
5. 能耗分析:通过采集机床的能耗数据,可以对机床的能源利用情况进行分析。
通过找到能耗高的设备和环节,可以进行合理的优化和节能措施,降低生产成本和环境污染。
数控机床状态数据实时采集与监视系统的研究开发

南京航空航天大学硕士学位论文数控机床状态数据实时采集与监视系统的研究开发姓名:肖士利申请学位级别:硕士专业:机械电子工程指导教师:叶文华20080501南京航空航天大学硕士学位论文 摘 要 生产现场信息的实时采集、传输、处理和分析是现代制造企业进行快速决策与响应的基础。
随着制造自动化和企业信息化的发展,企业对自动采集制造信息的需求越来越强烈,但常常因数控机床的多样性、异构性以及数控系统不开放,使得企业难以实时采集数控机床的现场数据。
因此,研究数控机床状态数据的采集具有重要的现实意义。
论文首先从信息采集的角度分析了数控机床的机床本体、PLC和CNC之间关系,研究了基于数控机床标准通信接口、基于机床PLC、基于机床电气电路三种数据采集方法的实现技术与优缺点。
然后,详细研究了一种基于机床电气电路进行机床数据采集的实现技术——基于外接PLC的采集方法,分析了该方法的实现过程,研究了可从不同OPC服务器读取数据的通用OPC客户端。
在此基础上,设计了具有基于数控机床串口和基于外接PLC两种采集功能的机床数据采集与监视系统(NC-SCADA)总体结构,研究了系统实现的若干关键技术,开发与实现了NC-SCADA系统,并在马钢车轮公司的数控生产线上得到成功应用。
该系统具有通用、可扩展和可重用的特点。
最后,对全文进行总结,并对进一步工作进行了展望。
关键词:数控机床,数据实时采集,OPC,电气电路,宏指令,可编程逻辑控制器数控机床状态数据实时采集与监视系统的研究开发 ABSTRACTThe real-time acquisition, transmission, processing a nd analysis of shopfloor field data are the foundation of rapid decision-making and response in modern manufacturing enterprises. With the development of manufacture automation and enterprise information, the requirement of automatically collecting production information becomes more and more intense for enterprises. However, the variety, heterogeneity and the closed CNC system of NC machine tools make it difficult for enterprises to automatically collect information at manufacturing spots. Therefore, it will be very meaningful to study the data acquisition of NC machine tool.In this paper, the relations between main body, PLC and CNC of NC machine tool in the perspective of i n formation collecting are analyzed, and the realization technology and the advantages and disadvantages of the three collecting methods are researched, which are basing on standard communication interface、PLC、electrical circuit of NC machine tools. Then one realization technology, the method based on external PLC, which is based on the electrical circuit of NC machine tools is studied in detail, the process realizing data real-time acquisition of processing states of NC machine tools by this technique is analyzed, and general OPC client reading data from different OPC server is researched.Basing on this research, the general structure of Data Real-Time Acquisition and Supervision System of NC Machine Tool(NC-SCADA) is designed in this paper, which has two collecting function including the methods based on RS232 serial and external PLC. Several key techniques in realizing the s ystem are studied, and the NC-SCADA system is developed, which was applied successfully on the production line in Wheel and Tyre Plant of Maanshan Iron & Steel Co. Ltd. This system has characteristics of universality, expansibility and reusability.Finally, the whole paper is summed up and further work is looked forwared as well.Key Words:NC machine tool, Data Real-Time Acquisition, OPC, Electrical Circuit, Macroinstruction, PLC南京航空航天大学硕士学位论文 图 清 单图1.1 集中采集集中控制方式 (3)图1.2 分布采集集中控制方式 (3)图2.1 数控系统的组成 (9)图2.2 PLC、CNC和数控机床本体间的信号关系 (12)图2.3 PLC输入信号图示 (16)图2.4 PLC输出信号图示 (16)图2.5 直流输入信号典型电路 (18)图2.6 直流输出信号接口 (18)图2.7 负载为指示灯的信号输出电路 (19)图2.8 负载为继电器线圈的信号输出电路 (19)图2.9 NC-SCADA系统的总体设计 (22)图3.1 主轴正转控制梯形图 (28)图3.2 中间电路 (29)图3.3 主轴电机 (29)图3.4 润滑系统电气控制原理图 (30)图3.5 润滑系统的的PLC控制梯形图 (31)图3.6 OPC接口访问方式 (33)图3.7 服务器、组、对象三者之间的关系 (34)图3.8 OPC连接图 (35)图3.9 SQL Server 2000和Oracle数据库写入数据性能比较 (37)图3.10 三种方法的性能特性比较 (39)图4.1 基于外接PLC的数据采集方法的总体结构图 (45)图4.2 PLC的现场组态 (46)图4.3 DI16数字输入模块地址 (46)图4.4 数控机床继电器接线原理图 (47)图4.5 OPC服务器内部结构图 (48)图4.6 OPC服务器Item对象与数据源的关联 (49)图4.7 本地PC机和远程PC机之间的客户端和服务器基于COM的连接 (51)图4.8 客户端程序工作流程 (52)数控机床状态数据实时采集与监视系统的研究开发 图5.1 NC-SCADA系统的软件功能模型图 (56)图5.2 串口采集流程图 (58)图5.3 OPC服务器列表 (59)图5.4 通过连接点连一个接收器过程 (60)图5.5 订阅式采集流程 (61)图5.6 数据实时采集与监视系统的线程框架图 (64)图5.7 机床的日生产运作情况 (65)图5.8 OEE查询 (65)图5.9 机床电气柜的继电器线路图 (67)图5.10 设备引脚配置 (68)图5.11 系统的运行图 (69)南京航空航天大学硕士学位论文 表 清 单 表2.1 三种采集方法的优缺点 (21)表3.1 三菱系统地址变量 (25)表3.2 各信号组合对应的设备状态 (41)表3.3 六大损失的简单说明及其与OEE的关系 (43)表5.1 机床信号-继电器-PLC DI16地址三者之间的对应关系 (67)数控机床状态数据实时采集与监视系统的研究开发 注 释 表 1.缩写词 SCADA Supervisory Control And Data Acquisition监视控制和数据采集系统DNC Direct Numerical Control or Distributed Numerical Control直接数控或分布式数控NC Numerical Control 数字控制CNC Computer Numerical Control 计算机数字控制MES Manufacturing Executing System 制造执行系统OPC OLE for Process Control 过程控制对象链接和嵌入MRP Material Requirement Planning 物料需求计划MRPII Manufacturing Resource Planning 制造资源计划MAP Manufacturing Automation Protocol 制造自动化协议CAN Controller Area Network 控制器局域网LAN Local Area Network 局域网TCP/IP Transmission Control Protocol/Internet Protocol传输控制协议/互联网协议OSI Open System Interconnect 开放互连系统ISO International Organization for Standardization国际标准化组织PLC Programmable Logic Controller 可编程逻辑控制器PMC Programmable Machine Controller 可编程机床控制器API Application Programming Interface 应用程序编程接口ODBC Open Database Connectivity 开放数据库互连MDI Manual Data Input 人工数据输入RV Receiver 信号接收器DV Driver 信号驱动器DSP Digital Signal Processing 数字信号处理BCD Binary Coded Decimal 二进码十进数HMI Human Machine Interface 人机接口承诺书本人郑重声明:所呈交的学位论文,是本人在导师指导下,独立进行研究工作所取得的成果。
CNC机床加工中的数据采集与分析技术

CNC机床加工中的数据采集与分析技术随着工业自动化的快速发展,计算机数控(CNC)机床在现代制造业中扮演着重要的角色。
CNC机床通过精确控制和操作工件的切削工具,实现高效、精密的加工任务。
在CNC机床加工过程中,数据的采集与分析技术的应用变得越来越重要。
本文将探讨CNC机床加工中的数据采集与分析技术的意义、方法和应用。
一、数据采集的意义数据采集是指通过传感器、监测装置等手段,收集CNC机床加工过程中所产生的各类数据。
这些数据包括切削力、温度、振动、工件位置等。
数据采集的意义在于:1. 提高加工质量和效率:通过及时采集和分析数据,可以对CNC 机床加工过程中的异常情况进行监测和预警,及时调整参数和控制策略,从而提高加工质量和效率。
2. 实现智能化管理:数据采集为CNC机床加工提供了大量的实时信息,通过对这些信息的分析和挖掘,可以实现智能化管理和优化,提高生产效益。
3. 提高设备可靠性和维护效率:通过对CNC机床加工数据的采集和分析,可以了解设备的工作状态和磨损程度,及时排除故障和进行维护,延长设备的使用寿命。
二、数据采集的方法数据采集可以通过多种方式实现,常用的方法包括:1. 传感器采集:通过安装感应器,如应力传感器、温度传感器等,在CNC机床的关键部位进行数据采集。
传感器将实时监测的信号转换为电信号,再通过数据采集系统进行数字化处理,并传输到数据存储设备中。
2. 数据总线采集:采用数据总线技术,将CNC机床的各个部分连接到同一个网络中,实现数据的实时传输和共享。
通过总线接口,可以从机床的各个组成部分,如电机、控制器、传感器等,采集各种数据。
3. 人工采集:除了自动化的数据采集方式外,人工采集也是一种常用的方法。
在CNC机床加工过程中,操作人员可以手动记录关键数据,如刀具磨损情况、加工参数等。
三、数据分析的技术数据采集只是第一步,对采集到的数据进行分析是实现加工优化和设备管理的关键。
下面介绍几种常用的数据分析技术:1. 统计分析:通过统计方法对采集到的数据进行处理,获得加工过程中的平均值、标准差、极差等参数,帮助判断加工的稳定性和可靠性。
《智能化数控系统体系结构及关键技术研究与实现》

《智能化数控系统体系结构及关键技术研究与实现》一、引言随着科技的飞速发展,智能化数控系统已成为现代制造业的核心技术之一。
该系统以数字化技术为基础,通过集成计算机、网络、传感器、自动化控制等先进技术,实现了对制造过程的精确控制与智能化管理。
本文将详细探讨智能化数控系统的体系结构,关键技术研究及其实现方法。
二、智能化数控系统体系结构智能化数控系统的体系结构主要包括硬件层、软件层和应用层。
1. 硬件层:包括中央处理器、输入输出设备、传感器、执行器等。
这些硬件设备负责接收、处理和执行指令,实现制造过程的自动化控制。
2. 软件层:包括操作系统、数控编程软件、数据库管理系统等。
软件层是智能化数控系统的核心,负责实现系统功能的逻辑控制与数据处理。
3. 应用层:根据具体应用需求,将硬件层和软件层进行集成与优化,实现特定制造过程的智能化控制与管理。
三、关键技术研究1. 数字化技术:数字化技术是实现智能化数控系统的关键技术之一。
通过将制造过程进行数字化建模,实现制造过程的精确控制与优化。
2. 传感器技术:传感器技术是实现智能化数控系统的重要手段之一。
通过安装各种传感器,实时监测制造过程中的各种参数,为系统提供实时数据支持。
3. 自动化控制技术:自动化控制技术是实现制造过程自动化的关键技术。
通过计算机对制造过程的控制与优化,实现制造过程的精确、高效和自动化。
4. 网络化技术:网络化技术是实现智能化数控系统的重要手段之一。
通过网络将各个设备进行连接,实现信息的实时传输与共享,提高系统的整体性能。
四、关键技术研究与实现1. 数字化技术研究与实现:通过对制造过程进行数字化建模,实现制造过程的精确控制与优化。
具体实现方法包括建立数字化模型、数据采集与处理、数据分析与优化等。
2. 传感器技术研究与实现:通过安装各种传感器,实时监测制造过程中的各种参数。
具体实现方法包括传感器选型、安装位置选择、信号处理与分析等。
3. 自动化控制技术研究与实现:通过计算机对制造过程的控制与优化,实现制造过程的精确、高效和自动化。
数字化制造SCADA 系统(数据采集与监控系统)简介

西门子与非西门子PLC
检测设备/计算机类型
统一定义标准化数据接口区域 便于管理与可扩展
PLC类型
根据数据采集的要求 定制开发
PC类型
18
数据采集——标准化
标准化
工业网络参考规范
联网方式 联网要求 选型要求 选型参考 施工要求
标准化
集成方式 数据交互方式
数据定义 接口映射
设备接口与控制参考规范
19
介绍内容
数据库 Web服务器
数控中心 (刀具与程序管理)
中心交换机 现场交换机
缸体加工 缸盖加工
总装线 缸盖线 连杆线 曲轴线
分装线1
分装线N
热试
完成线
曲轴加工
10
系统结构说明
系统结构说明:
➢系统底层配置独立的S7 300PLC负责采集现场模拟量和 个数字量信息。也可以采集其他厂家的PLC设备。 ➢现场传感器信号就近接入到分布式IO上,分布式IO通过 工业以太网与主控PLC通讯。 ➢为了均衡负载,配置若干台WinCC数据采集服务器采 集现场的模拟量和数字量信号。 ➢WinCC通过OPC接口向MES层提供数据。 ➢整个网络通过西门子工业以太网Profinet连接。
30
业务层设计方案—在线质量检测
生产线
Siemens PLC 人员与质检数据接口
3 数据采集
扫描登陆/手动入录 1
2 质检数据与产量信息
MES系统
(1)现场扫描或者手动输入人员信息,PLC采集人员信息传送给MES; (2)PLC采集现场质检数据并且记录产量信息,传送给MES。 (3)人员与产品的条码,工艺,质量,物料等采集信息关联。
改进
7
系统典型结构(环网)
如何使用伺服系统进行数据采集

如何使用伺服系统进行数据采集伺服系统是一种常用的控制系统,广泛应用于自动化领域中。
它可以通过收集和处理数据来实现对设备的控制和监测。
在本文中,我们将探讨如何使用伺服系统进行数据采集。
一、介绍伺服系统伺服系统是一种基于反馈控制的系统,主要由伺服电机、编码器、控制器和驱动器组成。
它能够精确控制电机的转动,并实现对设备的精准控制。
伺服系统广泛应用于工业自动化、机器人、数控加工等领域。
二、选择合适的伺服系统在进行数据采集之前,我们需要选择适合的伺服系统。
根据具体应用的需求,我们可以考虑以下几个方面:1. 额定功率:根据设备的负载情况选择合适的伺服系统额定功率,以确保系统能够正常工作并完成所需任务。
2. 控制精度:根据所需的控制精度选择适当的编码器分辨率和控制器,以实现对设备的精确控制。
3. 通信接口:选择支持常用通信接口(如RS485、EtherCAT等)的伺服系统,以便与其他设备进行数据交互和通信。
三、配置伺服系统配置伺服系统是数据采集的关键步骤。
以下是一些通用的配置步骤:1. 安装伺服电机:将伺服电机安装在设备上,并确保与负载的连接牢固可靠。
2. 连接编码器:将编码器与伺服电机连接,确保信号传输可靠,并设置编码器参数。
3. 连接控制器和驱动器:将控制器和驱动器连接起来,并进行必要的设置,确保伺服系统工作正常。
4. 配置控制器参数:根据设备要求,设置控制器参数,如最大转速、加速度、初始位置等。
四、进行数据采集一旦伺服系统配置完成,我们就可以开始进行数据采集。
以下是一些常见的数据采集方法:1. 位置数据采集:通过编码器获取伺服电机的位置信息,并将其记录下来。
这对于位置控制和运动分析非常重要。
2. 功率数据采集:使用额定功率和负载情况,计算伺服系统的功率消耗。
这有助于节能和负载分析。
3. 故障诊断数据采集:通过监测伺服系统的工作状态和报警信息,及时发现并解决潜在故障。
4. 运行时间数据采集:记录设备的运行时间,以评估设备的使用寿命和维护计划。
DNC与MDC数据采集解决方案

7
Value (价值体现)
DNC-分布式数控
DNC主要实现功能
NC程序的远 程双向通讯, 避免设备由于 使用U盘或CF 卡传输时导致 的热插拔及病 毒问题。
NC程序的远 程双向通讯, 避免设备由于 使用U盘或CF 卡传输时导致 的程序丢失问 题。
3
MDC-机床设备数据采集
现场设备采集展示
4
MDC-机床设备数据采集
现场设备采集展示
5
DNC-分布式数控
传统数控程序管理的不足
程序传输须一人在机床前操作,另一人在计算机前操作,工作效率低。
机床程序的传输和管理不到位,也存在被非法复制或意外修改或删除的 隐患。
程序没有集中管理,无法做到数控加工程序共享,降低了工作效率。
程序无严格的流程签署,职责不明晰,出了问题之后无法进行追溯。
6
DNC-分布式数控
DNC主要实现功能
通过机床联网,可对CNC机床的程序上传与下载,实现远程通讯。
对于部分型号的CNC机床,可以远程进行参数的修改,并备份机床参数。 多重目录列表功能,DNC系统在机床控制面板上就可以查询DNC服务器上 的程序列表,并可直接进行远程调用。
可以方便查询所有机床的监控数据,运行历史甘特图,机床运行状态分布图,运行走势图。
2
MDC-机床设备数据采集
现场设备采集列表
序号
设备名称生产厂家1 Nhomakorabea加工中心1
哈挺
2
加工中心2
哈挺
3
加工中心3
哈挺
4
加工中心4
哈挺
控制系统 发那科 发那科 发那科 发那科
2018 各系统CNC 数据采集方法

Win7
n/a
Matrix II (VCN
Win7
n/a
5X)
1/1/12
v1.1
HyperQuadrex
1/1/12
v1.1
Matrix II (QTN II
Win7
n/a
LBB)
1/1/12
v1.1
Matrix II (iSeries)
Win7
n/a
1/1/12
v1.1
Integrex iseries
Matrix (Versatech)
WinXP
D4
1/7/11
v1.1
Versatech
Matrix
WinXP
C3
(CTT,HQR,MP-II)
8/20/10 v1.1
Matrix (VRX, VRX-IIVRXT,SVC)
WinXP
D3
Matrix (VTC)
WinXP
D3
Matrix Nexus
Fusion 640M/M-
Win95
CGG/ACG 6/9/10
v1.0
M/C
5X
Fusion 640M/M-
Win2000 AAG/A9G 6/9/10
v1.1
M/C
5X
Fusion 640MTPro
Win2000 ABD
–
–
–
Fusion 640MPro Win95
–
–
–
–
Fusion 640MPro Win2000 –
5. MAZAK 采集方式/大畏 OKUMA (O-API) MAZAK 官方方式必须开通 MTConnect,购买机床请要求开通,否则后期
- 1、下载文档前请自行甄别文档内容的完整性,平台不提供额外的编辑、内容补充、找答案等附加服务。
- 2、"仅部分预览"的文档,不可在线预览部分如存在完整性等问题,可反馈申请退款(可完整预览的文档不适用该条件!)。
- 3、如文档侵犯您的权益,请联系客服反馈,我们会尽快为您处理(人工客服工作时间:9:00-18:30)。
2
数控系统加工信息采集及处理
数控系统分析: PC嵌入NC
采用与通用PC 机体系结构兼容的总线式、模块化、开放型结构作为开发平台。 代表性系统:西门子公司SINUMERIK 840D/840Di系列;FANUC 160i/180i/210i 系列、FANUC300i/310i/320i 系列;海德汉 iTNC530系列。
r
e
w
K2
u
b
x
x
y
c
A
K1
7
数控系统加工信息采集及处理
问题提出:
不适应网络 化生产 最终用户需 求不专一 数据采集 及处理 现有机床改 造升级
DNC概念: 通常是指计算机直接数控或分布式数控,即用一 台或多台计算机对若干台数控机床进行综合数字 控制,完成制造数据传输、机床状态监控等功能 的一种方法。 1
数控系统加工信息采集及处理
系统特点
系统具有一定的开放性,可供厂家用户进行二次开发。 数控系统有丰富的接口支持:RS232,网络接口,USB等 有较为丰富的开发资源
3
数控系统加工信息采集及处理
数据采集方式
西门子840D系 统
• 通过PLC 读取NC变量 • 商业化的数据采集解决方 案 • 标准化的OPC 接口开发
FANUC 16i/31i 数控系统
• 配备PC 特有的图形用户接 口GUI • 对中国存在一定的技术封 锁 • C 语言或BASIC 语言调用 的FOCAS1 驱动器和函数 库
海德汉iTNC530 数控系统
• 基于PC平台 • Remo Tools SDK开发工具 包
4
数控系统加工信息采集及处理
数控系统分析:
经济型数控系统
数据采集方式
不具有网络接口 系统信息开放少
数据采集卡
• 系统不提供机床信息 • 在机床电气线路上布置信 号采集点
串口数据采集
• 宏指令采集(信息量根据 数控系统确定) • 特殊程序上报采集(需人 员操作)
PLC数据采集
• 机床封闭性,不提供接口, 需改造机床 • 缺乏运行状态参数
5
数控系统加工信息采集及处理
6