电化学加工
电化学加工
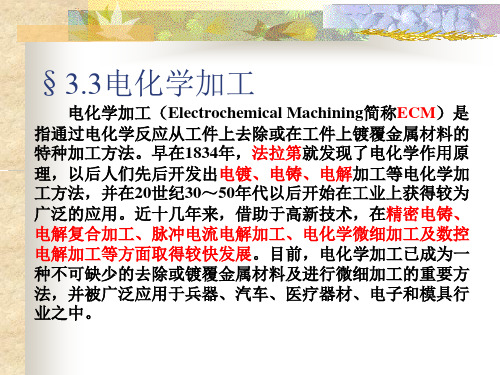
<2> 进给稳定 : 一般进给速度 变化量要求小于5%,爬行量 <0.03mm。
<3>防腐绝缘 <4>排氢防暴
2.直流电源 (1)低电压5-25V (2)大电流:1000-10000A,密度:100A/cm2 (3)常用电源:硅整流电源、晶闸管整流电源、脉冲电流加 工电源
3.电解液循环过滤系统
(1)组成:泵、电极液槽、过滤装置、管道、阀等 (2)多级离心泵:压力、流量稳定;密封、抗腐蚀; (3)净化:自然沉淀法,散热,多用水泥
③ 电解加工设备投资较高,占地面积较大。
④ 电解液对设备、工装有腐蚀作用,电解产物处理不好易 造成环境污染。
(二)电解加工设备 1.机床:立式,双柱龙门式 (1)作用:安装夹具,工件, 电极,实现相对运动,传递 电流,电解液 (2)特殊性: <1> 机床刚性好 : 电解液的压 强一般可达20~40kN。
(2)电流密度 i <1>V=ωi A tη <2>蚀除速度:v=V/t=ωi A η va=v/t=ωiη <3>i越大,加工效率越高,但i太高,火花,析出氯气,氧气等 <4>实际i决定于电源电压,间隙大小,电解液及其导电率
电解加工的平均电流密度约为10~100A/cm2,当电解液压力 和流速较高时,可以选用较高的电流密度。但电流密度过高, 将会出现火花放电,析出氯、氧等气体,并使电解液温度过高, 甚至在间隙内会造成沸腾气化而引起局部短路。
<5>浓度与温度: 电解液温度不宜超过60℃,一般在30~40℃范围内较为有利。 NaCl电解液的质量分数常为10%~15%,一般不超过20%, 当加工精度要求较高时,常小于10%。NaNO3电解液的质量 分数一般在20%左右,而NaClO3常用15%~35%。 <6>流速与电流密度配合:加工过程中电解液必须具有足够的 流速,以便及时将氢气、金属氢氧化物等电解产物和加工区 的大量热量带走。电解液的流速一般约在10m/s左右,电流密 度增大时,流速要相应增加。改变流速可通过调节电解液泵 的出水压力来实现。 <7>流动方向 :电解液的流向有三种形式,即正向流动、反 向流动和横向流动
第四章:电化学加工

e
铁片
铜片
阳极铁片 e
e 阴极铜片
NaCl
NaCl
4 电极的极化
在电化学过程中通常发生两种极化现象:浓差极化和电化学极化
1)浓差极化:在电化学反应过程中,阳极金属不断溶解的条件之 一是生成的金属离子需要越过双电层,再向外迁移并扩散。然而, 离子迁移扩散的速度是有一定限度的。在外电场的作用下,如果 阳极表面的液层中的金属离子迁移扩散的速度较慢而来不及扩散 到溶液中去,就会在阳极表面造成离子堆积,引起电位值增大 (代数值增大),这就是浓差极化。
使金属钝化膜破坏的过程称为活化。金属活化后,新鲜的金属 表面露出,可以进一步的参与电解过程,从而使加工速度提高。
二 电化学加工的分类
第一类 电解加工 第二类 电镀,涂镀和电铸加工 第三类 电化学与其他加工方法相结合的电化学复合加工工艺, 例如 电解磨削,超声电解等
第二节 电解加工
一 电解加工的过程及特点
m KIt
V It
m KIt
V It
根据法拉第电解定律,电解溶解或析出的物质的量只与该物质的 电化学当量,电解电流和电解时间有关。在理论上不受电解液浓 度,温度,压力,电极形状等因素的影响,与上述诸因素无关。
实际金属蚀除量
理论计算蚀除量 100 %
因此上述公式需要修正为:
m KIt V It
1 修复零件磨损表面、恢复几何尺寸、实施超差补救。
2 填补零件表面的划伤、凹坑、斑蚀、空洞等缺陷。例如机床 导轨、活塞液压缸等表面的修补。
3 大型、复杂、单个小批工件的表面镀镍、铜、锌、金、银等 防腐层、耐腐层等,用以改善表面性能。
四 电铸和涂镀(电镀)加工有何异同点?
相同点:两者的加工原理完全一样。
电化学加工
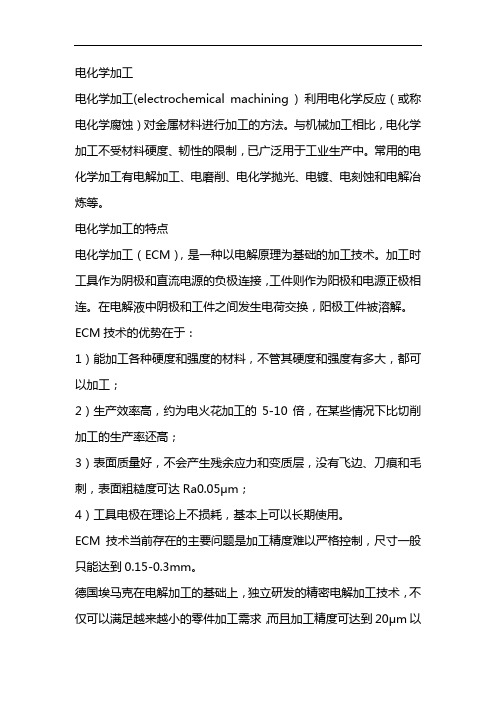
电化学加工
电化学加工(electrochemical machining ) 利用电化学反应(或称电化学腐蚀)对金属材料进行加工的方法。
与机械加工相比,电化学加工不受材料硬度、韧性的限制,已广泛用于工业生产中。
常用的电化学加工有电解加工、电磨削、电化学抛光、电镀、电刻蚀和电解冶炼等。
电化学加工的特点
电化学加工(ECM),是一种以电解原理为基础的加工技术。
加工时工具作为阴极和直流电源的负极连接,工件则作为阳极和电源正极相连。
在电解液中阴极和工件之间发生电荷交换,阳极工件被溶解。
ECM技术的优势在于:
1)能加工各种硬度和强度的材料,不管其硬度和强度有多大,都可以加工;
2)生产效率高,约为电火花加工的5-10倍,在某些情况下比切削加工的生产率还高;
3)表面质量好,不会产生残余应力和变质层,没有飞边、刀痕和毛刺,表面粗糙度可达Ra0.05μm;
4)工具电极在理论上不损耗,基本上可以长期使用。
ECM技术当前存在的主要问题是加工精度难以严格控制,尺寸一般只能达到0.15-0.3mm。
德国埃马克在电解加工的基础上,独立研发的精密电解加工技术,不仅可以满足越来越小的零件加工需求,而且加工精度可达到20μm以
下,同时也使产品表面质量更趋完美。
如今,电化学加工法已被广泛应用在航空航天、汽车制造、精密医疗仪器制造、显微技术和能源技术领域。
不管是特硬的的高温合金材料如镍基,钛合金零件,还是淬火后的零件,采用电化学加工技术都可以对它们进行经济有效的精密加工。
电化学加工知识

第二节 电解加工工艺
1.电解加工的基本原理和特点 电解加工 (电化学加工)是利用金属在电解 液中产生阳极溶解的电化学反应原理,对金 属材料进行成形加工的一种方法。 电解加工时的化学反应是比较复杂的,它随 工件材料、电解液成分等不同而不同。 是在电解抛光工件表面的基础上发展起来的。 电解抛光只能进行抛光,不能改变工件原有 的形状、尺寸。
2.相关概念
溶于水能导电的物质叫电解质,如酸、碱、盐等。 电解质的水溶液称为电解质溶液(简称电解液) 电解液浓度:电解液中所含的电解质的多少, 一般以质量百分比浓度(%)表示,即指每100克溶液中所含 溶质的克数; 还有用物质的量浓度表示,即指一升溶液中的电解质的摩尔 数。 电解质溶液之所以能导电与其在水中的状态有关,因为水分子是 极性分子,可以与其它的带电粒子发生微观静电作用。 NaCl是一种结晶体,组成晶体的粒子不是分子而是相间排列 的Na+离子和Cl-离子,叫做离子型晶体。 电解质水溶液中每个阴离子和阳离子的周围都吸引一些水分 子成为水化离子,这一过程称为电解质的电离。
(1)浓差极化
浓差极化是由于电解过程中电极附近溶液的浓度和本体溶 液(指离开电极较远,浓度均匀的溶液)浓度发生差别所 致,例如阳极溶解时,金属离子从阳极表面附近溶液扩散 缓慢,于是电极表面附近溶液的金属离子浓度比本体溶液 的浓度高,就好像电极侵入一个浓度较高的溶液中一样。 在阳极熔解过程中,金属不断熔解的条件之一是生成的金 属离子需要越过双电层,再向外迁移并扩散,然而扩散与 迁移的速度是有一定限度的,在外电场的作用下,如果阳 极表面液层中金属离子的扩散与迁移速度较慢,来不及扩 散到溶液中去,使阳极表面造成金属离子堆积,引起电位 值增大(即阳极电位向正极),这就是浓差极化。 浓度差别所引起的极化称为浓差极化。
第四章电化学加工
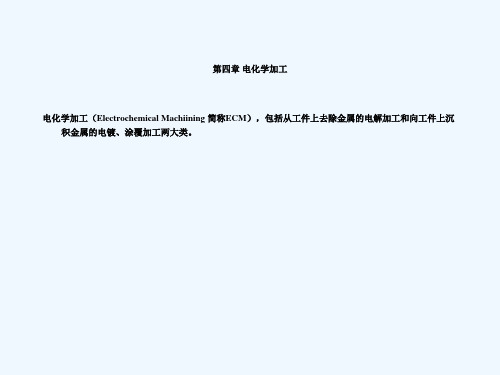
4.2 电解加工 一、电解加工过程及其特点 电解加工(electrochemical machining,ECM)是利用金属在电解液中发生阳极溶解反应而去除工件上
多余的材料、将零件加工成形的一种方法。
1-直流电源 2-工具阴
极 3-工件阳极
4-电解液泵
5-电
解液
加工时,工件接电源正极(阳极),按一定形状要求制成的工具接负极(阴极),工具电极向工件缓慢进给,并 使两极之间保持较小的间隙(通常为0.02~0.7mm),利用电解液泵在间隙中间通以高速(5~50m/s)流动 的电解液。
时水(H2O)离解为氢氧根负离子OH-和氢正离子H+,CuCl2离解为两个氯负离子2Cl-和二价铜正离子Cu2+。 当两个铜片接上直流电形成导电通路时,导线和溶液中均有电流流过,在金属片(电极)和溶液的界面上就会 有交换电子的反应,即电化学反应。溶液中的离子将作定向移动,Cu2+正离子移向阴极,在阴极上得到电子 而进行还原反应,沉积出铜。
在工件及工具之间施加一定电压,阳极工件的金属被逐渐电解蚀除,电解产物被电解液带走,直至工件表面形成 与工具表面基本相似的形状为止。
图中的细竖线表示通过阳极(工件)和阴极(工具)间的电流。竖线的疏密程度表示电流密度的大小加工开始时, 工件阳极及工具阴极的形状不同,工件表面上的各点至工具表面的距离不等,因而各点的电流密度不等。
3) 电解液系统 组成有泵、电解液槽、过滤装置、管道和阀。
七、电解加工工艺及其应用
1 深孔扩孔加工 深径比大于5的深孔,用传统切削加工方法加工,刀具磨损严重,表面质量差,加工效率低。目前采用电
解加工方法加工φ4×2000mm、φ100×8000mm的深孔,加工精度高,表面粗糙度低,生产率高。电 解加工深孔,按工具阴极的运动方式可分为固定式和移动式两种。
电化学加工

电 化 学 加 工
电 化 学 加 工
2、电解加工的特点
(1) 加工范围广 不受材料本身强度、硬度和韧性的限制,可 加工高强度、高硬度和高韧性等难切削的金 属材料,如淬火钢、钛合金、硬质合金、不 锈钢、耐热合金, 可加工叶片、花键孔、炮管膛线、锻模等各 种复杂的三维型面,以及薄壁、异形零件等
电 化 学 加 工
电 化 学 加 工
图中的细竖线表示通过阳极(工件)和阴极(工具)间的电 流。竖线的疏密程度表示电流密度的大小 加工开始时,工件阳极与工具阴极的形状不同,工件表面上 的各点至工具表面的距离不等,因而各点的电流密度不等。 阳极与阴极距离较近的地方通过的电流密度较大,电解液的 流速也较高,阳极溶解的速度也就较快,而距离较远的地方 ,电流密度就小,阳极溶解就慢。由于工具相对工件不断进 给,工件表面上各点就以不同的溶解速度进行溶解,电解产 物不断被电解液冲走,直至工件表面形成与工具表面基本相 似的形状为止。
电解液可分:
中性盐溶液
腐蚀性小,使用时较安全,应用最普遍 最常用的有
NaCl:使用广泛、加工便宜、货源充足、复制精度差 NaNO3:钝化型电解液,成形精度高、腐蚀性小、安全、 价格便宜、电流效率低、生产效率低,有消耗 NaClO3:加工精度高、生产效率高、价格昂贵、强氧化 剂
极化后产生超电位
电 化 学 加 工
5、金属钝化和活化
钝化:
金属阳极溶解过程超电位升高,电解速度减
慢,直至形成稳定状态不溶解 钝化形成钝化膜
活化:
破坏金属钝化膜
方法:
加入还原性气体或活性离子 机械方法破坏钝化膜
电 化 学 加 工
6. 电 化 学 分 类
电化学加工原理及应用总结

电化学加工原理及应用电化学加工(Electrochemical Making),也称电解加工,是利用金属在外电场作用下的高速局部阳极溶解实现电化学反应,对金属材料进行加工的方法。
常用的电化学加工有电解加工、电磨削、电化学抛光、电镀、电刻蚀和电解冶炼等。
电化学加工的原理:电化学加工是利用金属在电解液中的电化学阳极溶解来将工件成型的。
如图1 所示,工件接直流电源的正极为阳极,按所需形状制成的工具接直流电源的负极为阴极。
阳极表面铁原子在外电源的作用下放出两个电子,成为正的二价铁离子而溶解进入电解液中(Fe-2e=Fe+2)。
溶入电解液中的Fe+2又与OH-离子化合,生成Fe(OH)2沉淀,随着电解液的流动而被带走。
Fe(OH)2 又逐渐为电解液中及空气中的氧氧化为Fe(OH)3红褐色沉淀。
正的H+被吸收到阴极表面,从电源得到电子而析出氢气(2H++2e=H2↑)。
电解液从两极间隙(0.1~0.8 mm)中高速(5~60 m/s)流过。
当工具阴极向工件进给并保持一定间隙时即产生电化学反应,在相对于阴极的工件表面上,金属材料按对应于工具阴极型面的形状不断地被溶解到电解液中,随着工件表面金属材料的不断溶解,工具阴极不断地向工件进给,溶解的电解产物不断地被电解液冲走,工件表面也就逐渐被加工成接近于工具电极的形状,如此下去直至将工具的形状复制到工件上。
电化学加工的应用:电化学加工应用主要有电解加工、电化学抛光、电镀、电铸、电解磨削等方面。
具体应用于发动机叶片加工、火炮膛线加工、加工锻模型腔、深孔、小孔、长键槽、等截面叶片整体叶轮以及零件去毛刺、难导电硬脆材料加工等。
航空发动机叶片加工----相对于叶片的几何结构及采用的材料, 电解加工能充分发挥其技术特长。
尽管由于叶片精密锻造、精密铸造、精密辊轧技术的提高而有更多的叶片采用精密成形, 使电解加工叶片的数量有一些减少, 但随着叶片材料向高强、高硬、高韧性方向发展和钛合金、钴镍超级耐热合金的采用, 以及超精密、超薄、大扭角、低展弦比等特殊结构叶片的出现, 对电解加工又提出了新的、更高的要求, 电解加工依然是优选工艺方法之一。
电化学加工

电化学加工(ECM)是一种基于电解原理的加工技术。
加工时,工具用作阴极,与直流电源的负极相连,而工件用作阳极,与直流电源的正极相连。
电解质中的阴极与工件之间发生电荷交换,阳极工件溶解。
ECM技术的优点是:1)不论硬度和强度如何,都可以加工具有不同硬度和强度的材料;2)生产效率高,约为电火花加工的5-10倍,在某些情况下比切削加工要高。
3)表面质量好,无残余应力和变质层,无飞边,刀痕和毛刺,表面粗糙度可达Ra 0.05μm;4)工具电极在理论上没有任何损失,基本上可以长期使用。
目前,ECM技术的主要问题是加工精度难以严格控制,尺寸一般只能达到0.15-0.3mm。
在ECM的基础上,德国EMAG自主开发的精密ECM技术不仅可以满足越来越小的零件的需求,而且使加工精度小于20μm,同时使产品的表面质量更高完善。
如今,电化学加工已广泛应用于航空航天,汽车制造,精密医疗器械制造,显微镜和能源技术。
不论是镍基,钛合金零件还是淬火零件等超硬超级合金材料,电化学加工技术都可以用于经济有效的精密加工。
02飞机发动机ECM机加工整体叶片整体式叶片盘是高级航空发动机设计中典型的整体结构部件,其材料主要由先进的复合高温镍基合金制成。
传统的加工技术很难处理具有复杂刀片轮廓,高精度和切削力后变形大的部件。
因此,寻求更好的质量,高效率,高精度和低成本的加工方法已成为各国航空制造企业的目标。
ECM加工技术作为实现高温合金叶轮加工的重要方法,已经成为大型航空发动机公司研发的关键技术。
凭借其在该领域的多项专利技术,Emake成为世界上第一家为航空发动机提供ECM电解机床的欧洲设备制造商。
最终的叶片轮廓精度为≤0.06mm,超级合金材料的表面粗糙度ra≤0.2μm。
电化学加工
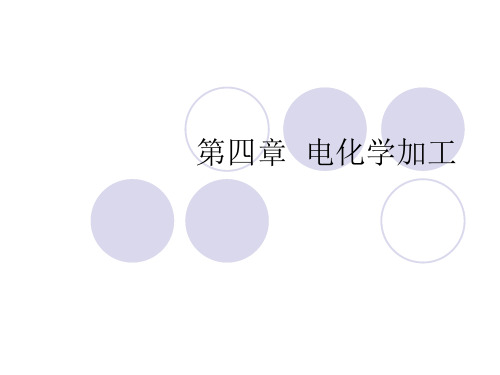
间隙中流过,这时阳极工件的金属被逐渐电解腐蚀,电解 产物高速(5~50m/s)的电解液带走。
电解加工的成形原理如图4-7所示,图中的细竖线表示通 过阴极与阳极间的电流,竖线的疏密程度表示电流密度的 大小。在加工刚开始时,阴极与阳极距离较近的地方通过 的电流密度较大,电解液的流速也非常高,阳极溶解也就 较快,见图4-7a。由于工具相对工件不断进给,工件表 面就不断被电解,电解产物不断被电解液冲走,直至工件 表面形成与阴极工作面相似的形状为止,如图4-7b。
Ua-阳极压降 UR-欧姆压降 Uc-阴极压降 电解加 工时的浓差极化一般不大,所以Ua 、Uc主要取决于电化 学极化和钝化。
一般来说,当用氯化钠电解液加工铁基合金时,电流效率 η =95%~100%,加工镍基合金和钛合金的电流效率η =70%~80%。当采用NaNO3、NaClO3等电解液加工时,电 流效率随电流密度、电解液的浓度和温度剧烈变化。 三、电解液 (一)对电解液的基本要求 (1)具有足够的蚀除速度 (2)具有较高的加工精度和表面质量 (3)阳极反应的最终产物应是不溶性的化合物 还有性能稳定、操作安全,对设备的腐蚀性小以及价 格便宜。 (二)三种常用电解液 中性盐溶液腐蚀性小,使用时较安全,应用普遍,常 用NaCl、NaNO3、NaClO3三种电解液。
z
q1
混合比越高,非线性性能越好。但混合比过高,增加了压 缩空气的消耗量,而且由于含气量过多,间隙电阻过大, 电解作用过弱还会产生短路火花。 气压:0.4~0.45MPa,液压:0.05MPa
电解加工的特点: 1)加工范围广,可以加工硬质合金、淬火钢、不锈钢、 耐热合金等高硬度、及韧性金属材料,并可以加工叶片、 锻模等各种复杂型面。 2)电解加工的生产率较高,约为电火花加工的5~10倍。 3)表面粗糙度较好(Ra1.25~0.2µm)和±0.1mm左右 的平均加工精度。 4)没有机械切削力,所以不会有残余应力和变形,没有 飞边毛刺。 5)加工过程中阴极工具理论上不会损耗,可长期使用。 电解加工的主要缺点和局限性: 1)不易达到较高的加工精度和加工稳定性。 2)电极工具的设计和修正较麻烦,难适用于单件生产。
第14讲 电化学加工
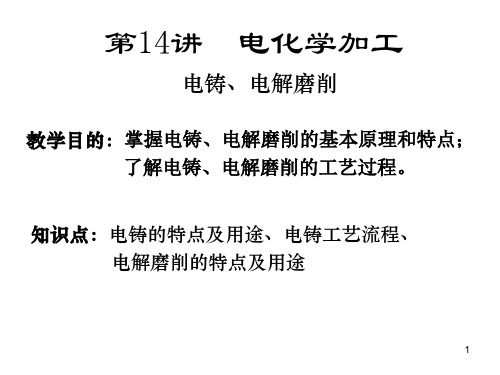
内孔镀 铬层
车削
镀铬
电铸镍
溶解 去型芯
黄 铜 型 芯
镀 铬 层
电 铸 镍 层
精密喷嘴
21
二、电解磨削 1、电解磨削原理 电解磨削是电解作用和机械磨削相结合的一种复 合加工方法。在电解磨削过程中,工件绝大部分余量 (98%)由电解作用去除,小部分由磨削切除。磨粒 的主要作用是去除阳极钝化膜和平整工件表面。 电解加工是利用金属在电解液中发生电化学阳极溶 解的原理加工。加工时,工具电极接直流电源阴极, 工件接阳极,两极之间保持一定的间隙,一定压力的 电解液从两极间高速流过,将电解产物冲走。 电解加工效率比电火花加工高四倍以上,电极损 耗极小,可长期使用。
26
5、电解液 电解液主要成份有硝酸钠、亚硝酸钠或氯化钠、 次氯酸钠。前者用于磨硬质合金,后者用于磨高温合 金。 6、影响电解磨削的因素 (1) 工作电压(升高工作电压,则电流密度增大, 升高工作电压, 升高工作电压 则电流密度增大, 加速阳极溶解,生产效率高, 加速阳极溶解,生产效率高,但对加工精度和表面 质量不利。 质量不利。) (2) 磨削压力(磨削压力以不产生火花放电又能刮 磨削压力以不产生火花放电又能刮 除氧化膜为原则,一般为0.1~0.3MP。) 除氧化膜为原则,一般为 。
8
在母模的轮廓较深的底部凹、凸不能相差太大, 同时尽量避免尖角。 母模常用材料有: 不锈钢、中碳钢、铝、铜、低熔点合金、有机玻 璃、塑料、石膏、石蜡等。 母模所用材料有金属和非金属材料之分,其中又可 分为可熔型不可熔型等,可根据不同需要进行选择。 制造母模的各种材料及其优缺点可参见表4.8。涂金属、无机粘结、铸铝、浇环 氧树脂或低熔点合金。 1)喷涂金属一般在电铸件的外层进行,达到一定厚 度后机加工。 2)无机粘结是将电铸件镶入配车的钢套内用无机粘 结剂粘结在一起。粘结层厚度为0.2~0.3mm。 3)铸铝是在电铸件的背后加固。 4)浇环氧树脂或低熔点合金是浇铸在电铸电极的内 壁,防止电极加工时变形。
电化学加工

三、金属阳极溶解机理
一般情况下,工件材料不是纯金属,而是合金,其金相组织也不完全一致,电 解液的成分、温度、流速等因素对电解过程都有影响,使得电解加工中电极间的反 应极为复杂。 以铁在氯化钠电解液中进行电解加工为例,分析阳极和阴极发生的电极反应。 由于NaCI和H2O的离解,在电解液中存在着H+、OH-、Na+、CI-四种离子,通 常将发生如下反应:
质的量与通过的电量成正比。 法拉第第二定律:当相同的电量通过不同的电解质溶液时,
在电极上析出或溶解的物质的量与其化学当量成正比。
电解加工时,阳极电极量(Q=It)成正比,其比例系数
称电化当量。
如果阳极只发生金属溶解而没有析出其它物质时,根据法拉第第一定 律,金属溶解的理论重量: W=KQ=KIt 其中,Q—通过的电量(库仑C,即 Q=It) I—电流(A),为电流密度与通过面积的乘积
复制等加工。例如复制印刷板、修复有缺陷或已磨损的零件、镀装饰层
和保护层等等。 3. 电化学加工与其它加工方法结合完成的电化学复合加工。主要有
电解磨削、电解-电火花复合加工、电化学阳极机械加工等,用于形状、
尺寸加工、表面光整加工、镜面加工、高速切割等加工。例如挤压拉丝 模加工、硬质合金刀具磨削、硬质合金轧辊磨削、下料等等。
电解加工炮膛线
电化学加工按加工原理可以分为三大类:
1. 利用阳极金属的溶解作用去除材料。主要有电解加工、电解抛光、 电解倒棱、电解去毛刺等,用于内外表面形状、尺寸以及去毛刺等加工, 例如型腔和异型孔加工、模具以及三维锻模制造、涡轮发动机叶片、齿 轮等零件的去毛刺等等。 2. 利用阴极金属的沉积作用进行镀覆加工。主要有电铸、电镀、电 刷镀,用于表面加工、装饰、尺寸修复、磨具制造、精密图案及印刷板
第四章 电化学加工
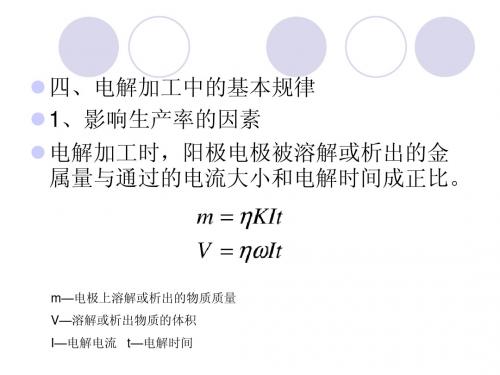
3)电极间隙与蚀除速度的关系
I U R / R U RA /
i I / A U R /
va U R / C /
3、加工间隙 1)端面平衡间隙
va U R / C /
经过一段时间后,阳 极的溶解速度和阴极 的进给速度相等,达 到端面平衡间隙
起始间隙与端面平衡间隙的差别愈大,进给 速度愈小,过渡时间就愈长。
2)法向平衡间隙
b U R n v cos cos
法向平衡间隙比端面 平衡间隙大,并且该 公式只n 2 b y b b
2
2y 1 b
四、电解加工中的基本规律 1、影响生产率的因素 电解加工时,阳极电极被溶解或析出的金 属量与通过的电流大小和电解时间成正比。
m—电极上溶解或析出的物质质量 V—溶解或析出物质的体积
I—电解电流 t—电解时间
1)电化学当量 K——被电解物质的质量电化学当量 ω——被电解物质的体积电化学当量
2)电流效率 电流效率小于100%,说明反应可能有一些 副反应消耗了电能。若阳极极化十分严重, 阳极的电极电位高于溶液中的某些阴离子, 阳极不溶解,则电流效率为零。 电流效率大于100%,由于晶界腐蚀,导致 阳极材料脱落。
侧面不绝缘 工件型孔始终处于被 加工状态,形成明显的 喇叭口,每一点的间隙 随着加工深度变化。
侧面绝缘
a 2 b b b
2
此时的间隙与工具的 进给量无关,只取决 于工作边宽度
3)电流密度 电流密度越高,生产率越大,但随着电流 密度的增加,电压也随着增高,因此在提 高生产率时应以不击穿加工间隙,引起火 花放电为度 。
2、加工速度 1)体积加工速度 单位时间内去除工件材料的体 积量。 2)深度加工速度——单位时间内在工件深度上的 去除量 Va h V It i t At ( At)
第四章 电化学加工
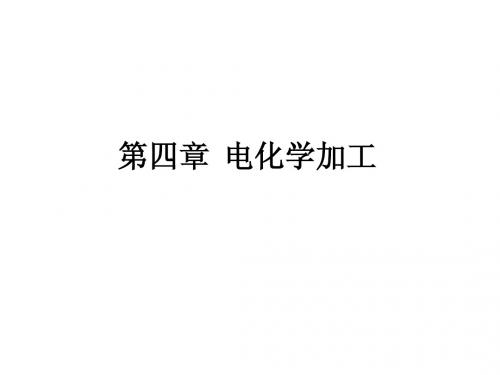
二、电解液 1. 主要作用:
◆ 作为导电介质传递电流;
◆ 在电场作用下进行电化学反应;
◆ 及时带走加工间隙内产生的电解产物及热量。
2. 基本要求:
◆ 保证足够的蚀除速度 即电解质有较高的溶解
度和离解度。
◆ 保证较高的精度和表面质量 即电解液中的金
属阳离子不应放电沉积到阴极工具上。
◆ 阳极反应的最终产物应是不溶性的化合物 。 ◆ 具有性能稳定、操作安全、价格便宜及对设
结合进行加工
导电磨削
• 又称电解磨削。是电解作用和机械磨 削相结合的加工过程。导电磨削时,工件 接在直流电源的阳极上,导电的砂轮接在 阴极上,两者保持一定的接触压力,并将 电解液引入加工区。当接通电源后,工件 的金属表面发生阳极溶解并形成很薄的氧 化膜,其硬度比工件低得多,容易被高速 旋转的砂轮磨粒刮除,随即又形成新的氧 化膜,又被砂轮磨去。如此进行,直至达 到加工要求为止。
电解加工的基本设备
• 直流电源:硅整流电源及晶闸管整流电源
• 机床:应有足够的刚度、进给速度稳定、防 腐绝缘、安全 • 电解液系统:
五、电解加工应用
该方法广泛应用在各种膛线、花键孔、深
孔、锻模、内齿轮、链轮、叶片、异形零件及去
毛刺、倒角等加工。
第三节 电解磨削
一、电解磨削的原理及特点
原理:电解作用与机械磨削相
国内情况
• 中国在20世纪50年代就开始应用电 解加工方法对炮膛进行加工,现已广泛 应用于航空发动机的叶片,筒形零件、 花键孔、内齿轮、模具、阀片等异形零 件的加工。近年来出现的重复加工精度 较高的一些电解液以及混气电解加工工 艺,大大提高了电解加工的成型精度,简化 了工具阴极的设计,促进了电解加工工 艺的进一步发展。
电化学加工知识
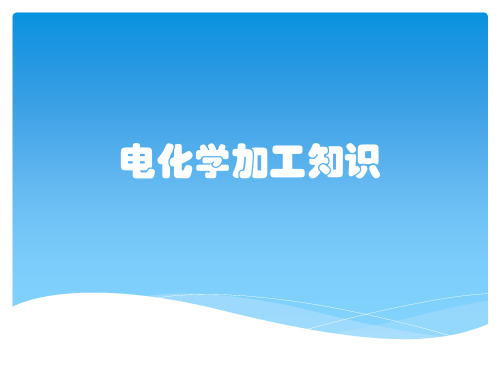
(三)电极电位
原电池是化学能转变为电能的装置 它由两个“半电池”所组成,而每一个半电池中有一个电极和相应 的电解质溶液,
例如:铜锌电池 Zn|ZnSO4(m1) ‖CuSO4(m2) |Cu
主编
5
电解池是利用电能发生氧化还原反应的装置。
在电解池中,与直流电源的负 极相连的极叫做阴极,与直流 电源的正极相连的极叫做阳极。
Pb2++2e ⇆ Pb H++e ⇆ (1/2)H2 S+2H++2e ⇆ H2S Cu2++2e ⇆ Cu H2O+(1/2)O2+2e ⇆ 2OHCu++e ⇆ Cu I2+2e ⇆ 2IH3AsO4+2H++2e ⇆ HAsO2+2H2O Fe3++e ⇆ Fe2+ Hg2++2e ⇆ Hg Ag++e ⇆ Ag Br2+2e ⇆ 2BrMnO2+4H++2e ⇆ Mn2++2H2O Cr2O72-+14H++6e ⇆ 2Cr3++7H2O Cl2+2e ⇆ 2ClMnO4-+8H++5e ⇆ Mn2++4H2O F2+2e ⇆ 2F-
主编 12
(五)电极的极化 1.电极的极化
◆过电位: 极化后的电极电位与平衡电位的差值称为过电位。 ◆极化: 当有电流通过电解池时,电极的平衡状态被破坏, 阳极电位向更加正的方向移动,阴极的电位向更加负 的方向移动,这一现象称为极化。
主编 13
- 1、下载文档前请自行甄别文档内容的完整性,平台不提供额外的编辑、内容补充、找答案等附加服务。
- 2、"仅部分预览"的文档,不可在线预览部分如存在完整性等问题,可反馈申请退款(可完整预览的文档不适用该条件!)。
- 3、如文档侵犯您的权益,请联系客服反馈,我们会尽快为您处理(人工客服工作时间:9:00-18:30)。
电化学加工(ECM)利用电化学反应(或电化学腐蚀)来加工金属材料。
与机械加工相比,电化学加工不受材料硬度和韧性的限制,在工业生产中得到了广泛的应用。
常见的电化学加工包括电化学加工、电磨削、电化学抛光、电镀、电蚀和电解熔炼。
介绍
电化学加工是非传统加工的一个重要分支。
它已经成为一种成熟的非传统加工技术,在许多领域得到了广泛的应用。
在电化学处理中,采用硅整流稳压电源。
过去采用全波整流代替半波整流。
纹波控制在5%以内,不仅提高了加工速度,而且限制了间隙中的电弧,防止了灰尘沉积在阴极上。
在电压调节方面,采用饱和电感和晶闸管两种调压方式。
前者更适合当前的电化学加工水平。
电源规格分为三个等级:小电源,电流50-500A,用于加工中小型阴极孔、去毛刺、抛光、电解车削;中型电源,电流1000-5000A,用于加工中、大孔、型腔(50-150cm2);使用大功率电流电源10000-40000A,加工面积在200-1000cm2或以上的大型零件。
常用的电压范围是12-20伏。
铜和硬质合金需要特殊的电解电源。
原因是这些材料晶格中的一些原子不易电离,
而晶格中的其他原子易受腐蚀。
例如,碳化钨晶格中的碳原子在正电位条件下不能被加工,必须有负电位(即电源电流有负半波);加工铜锌合金的电源不仅要有负半波,而且要有负半波,正半波和负半波的间隔和排列也有一定的要求。
使用专用电源还可以解决相对惰性离子在间隙中积累的问题,从而改变间隙电阻和电场分布,从而有效提高加工精度。
由于在电化学加工过程中间隙短路,电源系统通常具有良好的短路保护功能,因此在发生火花和短路时不会损坏阴极和工件。
国内形势
自20世纪50年代以来,电化学加工广泛应用于航空发动机叶片、圆柱形零件、花键孔、内齿轮、模具、阀板等异形零件的加工。
近年来,一些高重复性电解液和混合气体电化学加工技术大大提高了电化学加工的成形精度,简化了刀具阴极的设计,促进了电化学加工技术的进一步发展。