波峰焊焊盘工艺设计规范指引.doc
波峰焊插件焊接流程工艺共30页文档

2020/6/9
7
MIMA手工插件
手工插件(MI)
按照WI规定,将所要插的元件以一定的顺序、一定的步骤, 插在PCB板上的过程。在作业之前,首先要做到静电防护,实 施WI与物料、料号之间的“三一致”确定标准。MI第一工位 必须检查SMT的MARKING标识并按照正确的装置方法将 PCBA安装金手指保护套/托盘。作业员在插本工位元件之前必 须使用手指接触元件的方法检查前一工位所插元件,在作业的 过程中,要特别注意电解电容的方向区分。MI总检依据WMS 与本工位目视WI对PCBA进行100%全检 ,在目检过程中遇到 不良品在力所能及的情况下纠正不良(如:极性反)。如不良品不 能立即重工,把PCBA放到不良品周转架上由线长或组长来解决, 同时将问题反馈给前面相关工位,并做不良记录。
将需要成型的管装IC与塑料管一起装到机器的上料口,将同一型号IC 的空装料管装到机器的出料口,打开运行开关后加工物料。
IC管脚成型机
2020/6/9
6
MIMA元件预加工
注意事项
1、作业时必须采取静电防护。 2、不能混合加工物料,必须加工完一种物料,清理掉落的元件后才可以加
工另一种物料。 3、需加工的元件在加工过程中必须要随机抽取3-5个元件插到PCB板上用引
防静电的,进出车间人员都必须做好静电防护工作。
2020/6/9
3
MIMA元件预加工
主要加工的项目:三极管、晶振、IC、电容器等。
元件(三极管、晶振)加工的方法及注意事项
元件的加工的方法: 1、元件引脚的成型 将料盒里面的未成型的元件(三极管),用手放到成型工装上用力按下, 食指和中指顺势滑下,使元件引脚分开,引脚之间的距离变大后,形成所 需要的形状。
➢ 总的来说:MIMA包括元件预加工、手工插件、 波峰焊接技术、机械组装、ICT测试、FCT测试及 MIMA管理 。
波峰焊作业规范标准
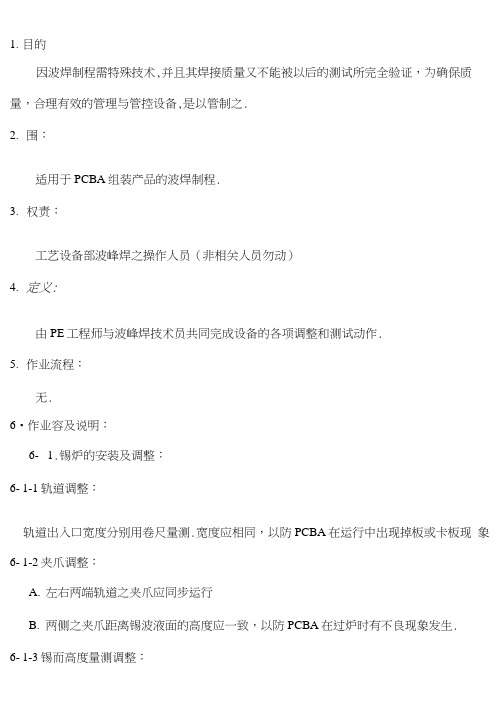
1.目的因波焊制程需特殊技术,并且其焊接质量又不能被以后的测试所完全验证,为确保质量,合理有效的管理与管控设备,是以管制之.2.围:适用于PCBA组装产品的波焊制程.3.权责:工艺设备部波峰焊之操作人员(非相关人员勿动)4.定义:由PE工程师与波峰焊技术员共同完成设备的各项调整和测试动作.5.作业流程:无.6•作业容及说明:6-1.锡炉的安装及调整:6-1-1轨道调整:轨道出入口宽度分别用卷尺量测.宽度应相同,以防PCBA在运行中岀现掉板或卡板现象6-1-2夹爪调整:A.左右两端轨道之夹爪应同步运行B.两侧之夹爪距离锡波液面的高度应一致,以防PCBA在过炉时有不良现象发生.6-1-3锡而高度量测调整:锡而高度量测应在波峰开启的状态下,用钢尺下量至液面,锡面距锡槽边的距离应控制在20±2mm.生产中每两小时量测一次,如高于上述标准.则需添加锡棒拼记录于vv波峰焊日常保养点检表>>•6-1-4锡波高度量测:A.用钢尺垂直于波峰喷口向下量测锡波高度,平视钢尺刻度.高度应在10±3mm以下, 以防波而落差过大造成焊锡大量氧化和吃锡不良.B.PCB吃锡深度控制在其板(或过炉载具)厚的1/2-2/3之间,以防溢锡或漏焊.6-15锡炉传送带测试调整:A.新设备进厂后,在锡炉传送带导轨两端用红色高温胶带标出1000MM长的标示段, 用秒表计算PCBA通过此标示段所耗用的时间,然后用标示段长度除以PCBA通过标示段所耗用的时间,即得到锡炉标准传送带传送速度.B.以A所述的标准传送带速度为参照,校正锡炉自检系统测得的传送带速度,使两者保持一致,即得出正确的锡炉自检速度,一般控制在1700mm±200mm/min之间,生产中每一天读取锡炉自检传送速度一次,并记录于vv波峰焊炉温与链速记录表>>.6-16输送带仰角量测:设备上所安装的角度测量仪所显示的实际输送带仰角,应控制在5° -7°6-1-7.锡炉熔锡温度量测:将温度测试仪电源开关瘤歹至劇上显示数字,然后将温度测试仪之感温头插入锡波而约5mm的位置.待温度测试仪数字显示稳定后,表面所显示数值即为所要测试锡炉熔锡的实际温度.温度应控制在250±10°C,测试完毕,将测试结果(正常生产需每天检测一次)填写在vv波峰焊炉温与链速记录表 >>上.(备注:也可以使用其它温度计进行量测). 6-1-8.锡炉预热温度测试:A.新设备进厂后,在预热区每一个发热段中部各选取一个测试点,设定其预热参数为a,机台自检测得的温度为b,用温度测试仪测试各测试点之温度值为标准预热段温度值c.B.以A所述的标准预热段温度值c为参照,校正锡炉自检系统测得的预热段温度b,使两者保持一致,得到正确的锡炉自检预热段温度值,生产中每两小时读取锡炉自检预热段温度一次,并记录于VV波峰焊预热区记录表».Profile测试所得预热最高温度以产品也指导书为准. 62锡炉Profile测试:6-2-1.测温点的选择参照《Profile制作规》.如客户有特殊需求.依客户要求为准.6-2-1.测试方法及步骤请参照profile炉温测试仪使用说明书.6-2-2profile 测试时机:6-2-2-1.新设备进厂时,由锡炉工程师对锡炉进行Profile测试,以检测设备工作性能及技术指标.相关数据标准及测试点选取由锡炉工程师参照业界标准,结合公司实际情况确定各项参数的设定及测试点选取.6-2-22新机种上线,由锡炉工程师参照客供标准Profile,并结合本公司实际情况测得该机种在本公司生产环境下之标准Profile,如客户有特殊要求,请以客户要求为准.622-3.每周对每台波峰焊用测温仪测试一次Profile并存档,.并确实以Profile反映数据为参照来设定锡炉工作参数,达到合理有效的管控锡炉各项参数、监测锡炉工作状态的目的, 以此来保证良好的焊接质量.6-2-24测试基木参数要求:6-2-2-5如在生产过程中出现品质异常需重新测试Profile.6-2-2-6设备在维修后.为确保其温控系统未受到影响.也需测试Profile.6-3.锡炉助焊剂比重测试: 将所要测试的助焊剂用吸管吸入测试量杯中,然后将比重计轻轻放入测试量杯中,待液面 与比重计皆静止不动时读取比重计所显示的数值,即得到所测试助焊剂的比重.(读取数 据时以液面的凹而为准)•每天开线前对锡炉所使用之助焊剂进行量测并把量测结果填写 在v 波峰焊机每天点检报告>> 上.6-5.锡炉PPM 值管控: 6-5-1.锡炉PPM 值管控由工程单位实施执行,并持续改善.6- 52每日锡炉工程师需对炉后补焊段不良进行统计,分析其不良原因并写出改善说明.7. 生产注意事项:7- 1.生产前注意事项:7- 1-1.查看锡炉锡液温度是否在设定温度.7- 12锡炉液位是否在要求围. 设备型号「 链速(ram/min)-助焊剂济虽 预热卜” 预热二・ 预热三卩 披峰一丿波峰二卩 焊接时间(S )「 NK-350< 1700 (rm/rTdnj< 0.张1 (nun)*3 1300 150t>25l)t<> 250匕 3・5 (S) ~ 注释…首先训节彼堆焊链速为1700 (mm/min ) ± 200(«!n/.in ),当PCBA 经过助焊剂区时流虽喷芻 为0.4ml±0. lml/min,经过第一预热区时其温度 达到13CTC 土5匸,当PCBA 经过笫二预热区时其 温度达到1509土5£,当PCBA 经过第三预热区 时其温度达到17()9 ±59,当经过焊接区时其温 度达到2509土 10t 打波躍焊接时间为3 5(S )土 0.5(S ),焊接完成后经过冷却区羯度逐渐下降到 509以下。
PCBA波峰焊接DIP治具设计技术规范
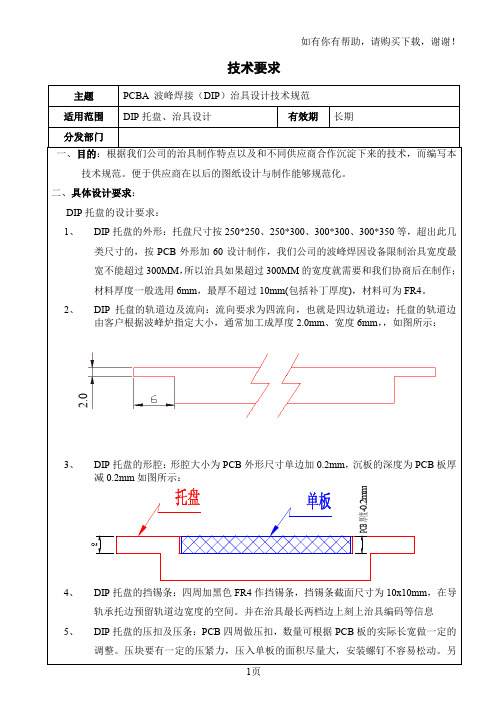
技术要求主题PCBA 波峰焊接(DIP )治具设计技术规范 适用范围DIP 托盘、治具设计 有效期 长期分发部门 一、目的:根据我们公司的治具制作特点以及和不同供应商合作沉淀下来的技术,而编写本技术规范。
便于供应商在以后的图纸设计与制作能够规范化。
二、具体设计要求:DIP 托盘的设计要求:1、 DIP 托盘的外形:托盘尺寸按250*250、250*300、300*300、300*350等,超出此几类尺寸的,按PCB 外形加60设计制作,我们公司的波峰焊因设备限制治具宽度最宽不能超过300MM ,所以治具如果超过300MM 的宽度就需要和我们协商后在制作;材料厚度一般选用6mm ,最厚不超过10mm(包括补丁厚度),材料可为FR4。
2、 DIP 托盘的轨道边及流向:流向要求为四流向,也就是四边轨道边;托盘的轨道边由客户根据波峰炉指定大小,通常加工成厚度2.0mm 、宽度6mm ,,如图所示:3、 DIP 托盘的形腔:形腔大小为PCB 外形尺寸单边加0.2mm ,沉板的深度为PCB 板厚减0.2mm 如图所示:4、 DIP 托盘的挡锡条:四周加黑色FR4作挡锡条,挡锡条截面尺寸为10x10mm ,在导轨承托边预留轨道边宽度的空间。
并在治具最长两档边上刻上治具编码等信息5、 DIP 托盘的压扣及压条:PCB 四周做压扣,数量可根据PCB 板的实际长宽做一定的调整。
压块要有一定的压紧力,压入单板的面积尽量大,安装螺钉不容易松动。
另2.0P C B 厚度-0.2m m外,如果PCB大小超过一定程度,还需要加压条来压紧PCB,以防止PCB中间部位拱起,导置漏锡,压条的数量根据PCB宽度来决定,压条一般需做成防呆或刻上标记,加以区分,有多根压条的尽量做到一致,可互换,使用更方便快捷。
如图所示:6、DIP托盘的上锡开口:托盘开孔处参照Gerber文件和实际样板。
原则上托盘开孔边到焊盘的距离>=3mm,托盘开孔边的壁厚>=1mm,托盘底部最薄处>=1mm,如下图所示:托盘避让贴片元器件的开槽面积尽量小,保证托盘的整体较厚实;由于托盘较厚,开孔处较窄的地方背面斜坡加长,倒角刀的角度分为135°及90°两种。
波峰焊工艺规范

波峰焊工艺规范自动化测试与控制研究所1.范围1.1主题内容波峰焊是将熔融的液态焊料,借助与泵的作用,在焊料槽液面形成特定形状的焊料波,插装了元器件的PCB置与传送链上,经过某一特定的角度以及一定的浸入深度穿过焊料波峰而实现焊点焊接的过程;波峰面的表面均被一层氧化皮覆盖,它在沿焊料波的整个长度方向上几乎都保持静态,在波峰焊接过程中,PCB接触到锡波的前沿表面,氧化皮破裂,PCB前面的锡波无皲褶地被推向前进,这说明整个氧化皮与PCB以同样的速度移动波峰焊机焊点成型:当PCB进入波峰面前端时,基板与引脚被加热,并在未离开波峰面之前,整个PCB浸在焊料中,即被焊料所桥联,但在离开波峰尾端的瞬间,少量的焊料由于润湿力的作用,粘附在焊盘上,并由于表面张力的原因,会出现以引线为中心收缩至最小状态,此时焊料与焊盘之间的润湿力大于两焊盘之间的焊料的内聚力;因此会形成饱满,圆整的焊点,离开波峰尾部的多余焊料,由于重力的原因,回落到锡锅中 ;1.2适用范围本指导性技术文件适用于波峰焊技术;2.引用文件JB/T 7488-1994波峰焊工艺规范3.波峰焊质量控制要求3.1严格工艺制度填写操作记录,每2小时记录一次温度等焊接参数;定时或对每块印制板进行焊后质量检查,发现焊接质量问题,及时调整参数,采取措施;3.2定期检查根据波峰焊机的开机工作时间,定期检测焊料锅内焊料的铅锡比例和杂质含量如果锡的含量低于极限时,可添加一些纯锡,如杂质含量超标,应进行换锡处理;3.3经常清理波峰喷嘴和焊料锅表面的氧化物等残渣;4.波峰焊操作步骤4.1焊接前准备检查待焊PCB该PCB已经过涂敷贴片胶、SMC/SMD贴片、胶固化并完成THC插装工序后附元器件插孔的焊接面以及金手指等部位是否涂好阻焊剂或用耐高温粘带贴住,以防波峰后插孔被焊料堵塞;如有较大尺寸的槽和孔也应用耐高温粘带贴住,以防波峰焊时焊锡流到 PCB 的上表面;将助焊剂接到喷雾器的软管上;4.2开炉a.打开波峰焊机和排风机电源;b.根据 PCB 宽度调整波峰焊机传送带或夹具的宽度;4.3设置焊接参数助焊剂流量:根据助焊剂接触PCB底面的情况确定;使助焊剂均匀地涂覆到PCB的底面;还可以从PCB上的通孔处观察,应有少量的助焊剂从通孔中向上渗透到通孔顶面的焊盘上,但不要渗透到组件体上;预热温度:根据波峰焊机预热区的实际情况设定PCB 上表面温度一般在 90-130℃,大板、厚板、以及贴片元器件较多的组装板取上限传送带速度:根据不同的波峰焊机和待焊接PCB的情况设定一般为 0.8-1.92m/min焊锡温度:必须是打上来的实际波峰温度为 250±5℃时的表头显示温度;由于温度传感器在锡锅内,因此表头或液晶显示的温度比波峰的实际温度高5-10℃左右测波峰高度:调到超过 PCB 底面,在 PCB 厚度的 2/3处;4.4首件焊接并检验待所有焊接参数达到设定值后进行a.把 PCB 轻轻地放在传送带或夹具上,机器自动进行喷涂助焊剂、干燥、预热、波峰焊、冷却;b.在波峰焊出口处接住 PCB;c.按出厂检验标准;4.5根据首件焊接结果调整焊接参数4.6连续焊接生产a.方法同首件焊接;b.在波峰焊出口处接住 PCB,检查后将 PCB 装入防静电周转箱送修板后附工序;c.连续焊接过程中每块印制板都应检查质量,有严重焊接缺陷的印制板,应立即重复焊接一遍;如重复焊接后还存在问题,应检查原因、对工艺参数作相应调整后才能继续焊接;4.7检验标准按照出厂检验标准5.波峰焊工艺参数控制要点5.1焊剂涂覆量要求在印制板底面有薄薄的一层焊剂,要均匀,不能太厚,对于免清洗工艺特别要注意不能过量;焊剂涂覆方法是采用定量喷射方式,焊剂是密闭在容器内的,不会挥发、不会吸收空气中水分、不会被污染,因此焊剂成分能保持不变;关键要求喷头能够控制喷雾量,应经常清理喷头,喷射孔不能堵塞;5.2印制板预热温度和时间预热的作用:a.将焊剂中的溶剂挥发掉,这样可以减少焊接时产生气体;b.焊剂中松香和活性剂开始分解和活性化,可以去除印制板焊盘、元器件端头和引脚表面的氧化膜以及其它污染物,同时起到保护金属表面防止发生再氧化的作用;c.使印制板和元器件充分预热,避免焊接时急剧升温产生热应力损坏印制板和元器件;印制板预热温度和时间要根据印制板的大小、厚度、元器件的大小和多少、以及贴装元器件的多少来确定;预热温度在 90-130℃PCB 表面温度,多层板以及有较多贴装元器件时预热温度取上限,不同PCB 类型和组装形式的预热温度参考表 1;参考时一定要结合组装板的具体情况,做工艺试验或试焊后进行设置;预热时间由传送带速度来控制;如预热温度偏低或和预热时间过短,焊剂中的溶剂挥发不充分,焊接时产生气体引起气孔、锡球等焊接缺陷;如预热温度偏高或预热时间过长,焊剂被提前分解,使焊剂失去活性,同样会引起毛刺、桥接等焊接缺陷;因此要恰当控制预热温度和时间,最佳的预热温度是在波峰焊前涂覆在PCB底面的焊剂带有粘性;5.3焊接温度和时间焊接过程是焊接金属表面、熔融焊料和空气等之间相互作用的复杂过程,必须控制好焊接温度和时间,如焊接温度偏低;液体焊料的黏度大,不能很好地在金属表面润湿和扩散,容易产生拉尖和桥连、焊点表面粗糙等缺陷;如焊接温度过高,容易损坏元器件,还会由于焊剂被炭化失去活性、焊点氧化速度加快,产生焊点发乌、焊点不饱满等问题;波峰温度一般为 250±5℃必须测打上来的实际波峰温度;由于热量是温度和时间的函数,在一定温度下焊点和组件受热的热量随时间的增加而增加;波峰焊的焊接时间通过调整传送带的速度来控制,传送带的速度要根据不同型号波峰焊机的长度、预热温度、焊接温度统筹考虑进行调整,以每个焊点接触波峰的时间来表示焊接时间,一般焊接时间为 3-4s;5.4印制板爬坡角度和波峰高度印制板爬坡角度为 3-7℃;是通过调整波峰焊机传输装置的倾斜角度来实现的;适当的爬坡角度有利于排除残留在焊点和组件周围由焊剂产生的气体,当THC与SMD混装时,由于通孔比较少,应适当加大印制板爬坡角度;通过调节倾斜角度还可以调整 PCB 与波峰的接触时间, 倾斜角度越大,每个焊点接触波峰的时间越短,焊接时间就短;倾斜角度越小,每个焊点接触波峰的时间越长,焊接时间就长;适当加大印制板爬坡角度还有利于焊点与焊料波的剥离;当焊点离开波峰时,如果焊点与焊料波的剥离速度太慢,容易造成桥接;适当的波峰高度使焊料波对焊点增加压力和流速有利于焊料润湿金属表面、流入小孔,波峰高度一般控制在印制板厚度的 2/3 处;5.5工艺参数的综合调整工艺参数的综合调整对提高波峰焊质量是非常重要的;焊接温度和时间是形成良好焊点的首要条件;焊接温度和时间与预热温度、焊料波的温度、倾斜角度、传输速度都有关系;综合调整工艺参数时首先要保证焊接温度和时间;双波峰焊的第一个波峰一般在 235-240℃/1s 左右,第二个波峰一般在 240-260℃/3s 左右;焊接时间=焊点与波峰的接触长度/传输速度焊点与波峰的接触长度可以用一块带有刻度的耐高温玻璃测试板走一次波峰进行测量;传输速度是影响产量的因素;在保证质量的前提下,通过合理的综合调整各工艺参数,可以实现尽可能的提高产量的目的;。
波峰焊焊接工艺

PPT文档演模板
波峰焊焊接工艺
A v v
B1 B2
焊料
沿深板
• PCB离开焊料波时﹐分离点位于 B1和B2之间的某个地方﹐分离后 形成焊点
PPT文档演模板
波峰焊焊接工艺
6: 防止桥联的发生
6.1 使用可焊性好的元器件/PCB 6.2 提高助焊剂的活性 6.3 提高PCB的预热温度﹐增加焊盘的
湿润性能 6.4 提高焊料的温度 6.5 去除有害杂质﹐减低焊料的内聚力﹐
PPT文档演模板
波峰焊焊接工艺
6-3. 锡槽温度不足沾锡时间太短,可用提高锡
槽温度加长焊锡时间,使多余的锡再回流到 锡槽来改善. 6-4.
出波峰后之冷却风流角度不对,不可朝锡 槽方向吹,会造成锡点急速,多余焊锡无法 受重力与内聚力拉回锡槽. 6-5.
手焊时产生锡尖,通常为烙铁温度太低, 致焊锡温度不足无法立即因内聚力回缩形 成焊点,改用较大瓦特数烙铁,加长烙铁在 被焊对象的预热时间.
PPT文档演模板
波峰焊焊接工艺
• 在通过波峰焊接之前预热,有以下几个理由:
3.1. 提升了焊接表面的温度,因此从波峰上要求较少的温 带能量,这 样有助于助焊剂表面的反应和更快速的焊接。
3.2. 预热也减少波峰对元器件的热冲击,当元器件暴露在突然的温度梯 度下时可能被削弱或变成不能运行。
3.3. 预热加快挥发性物质从PCB上的蒸发速度。这些挥发性物质主要来自 于助焊剂,但也有可能来自较早的操作、储存条件和处理。挥发物在 波峰上的出现可能引起焊锡飞溅和PCB上的锡球。
三:波峰焊接缺陷分析
1.沾锡不良
这种情况是不可接受的缺点,在焊点上只有 部分沾锡.分析其原因及改善方式如下:
1-1.
波峰焊托盘设计规范
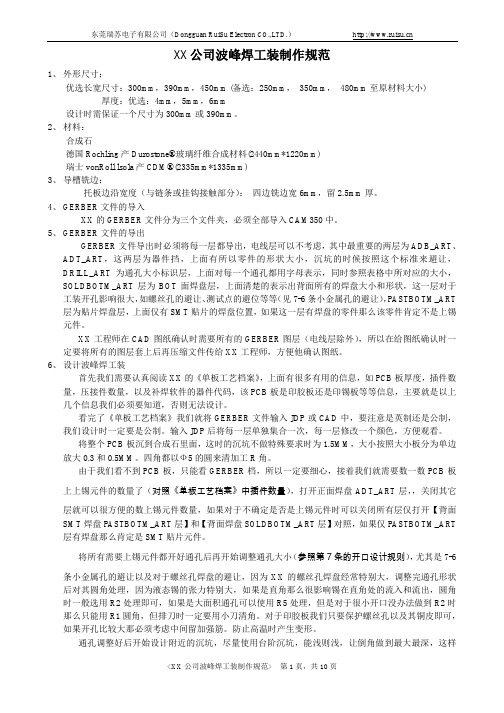
210
右 图 所 示 , 以 PCB板 外 形 单 边 放 大 70,
工 装 外 形 为 300*300。 而 此 时 PCB板 与
工装的间距较大,可以轻松放置压块
及刻字。
GZ2102EA
RS
采用
定工装外形大小示意图
压块的设计:压块我们选用 10*20 中心孔压块,压入 PCB 板中的距离为 2.7MM,两个压块的间距为 100MM,如果 PCB 板小于 100MM,那么单边尽量使用两个,距离可以稍微大一点,但要居中对称放 置。如果有零件和 PCB 板缺口干扰我们才可以挪动压块位置。锁压块的孔使用Ф2.5 攻 M3 的牙,由 下至上锁 M3*27 平头螺丝安装压块,注意加平垫和弹垫。
看完了《单板工艺档案》我们就将 GERBER 文件输入 JDP 或 CAD 中,要注意是英制还是公制, 我们设计时一定要是公制。输入 JDP 后将每一层单独集合一次,每一层修改一个颜色,方便观看。
将整个 PCB 板沉到合成石里面,这时的沉坑不做特殊要求时为 1.5MM,大小按照大小板分为单边 放大 0.3 和 0.5MM。四角都以Ф5 的圆来清加工 R 角。
将所有需要上锡元件都开好通孔后再开始调整通孔大小(参照第 7 条的开口设计规则),尤其是 7-6
条小金属孔的避让以及对于螺丝孔焊盘的避让,因为 XX 的螺丝孔焊盘经常特别大,调整完通孔形状 后对其圆角处理,因为液态锡的张力特别大,如果是直角那么很影响锡在直角处的流入和流出,圆角 时一般选用 R2 处理即可,如果是大面积通孔可以使用 R5 处理,但是对于很小开口没办法做到 R2 时 那么只能用 R1 圆角,但排刀时一定要用小刀清角。对于印胶板我们只要保护螺丝孔以及其铜皮即可, 如果开孔比较大那必须考虑中间留加强筋。防止高温时产生变形。
浸焊切脚波峰焊作业工艺规范

8、经常检验加热处导线,避免老化漏电。
9、注意检查锡液面,应不低于缸体顶部20mm。
六、工作态度
1、不接收不良品、不制造不良品。
2、安全生产,做好保护措施。
3、检查好上一工位的作业内容。
4、5秒后基本凝固时,放入流水线流入下一道工序。
5、切脚机开始进行切脚操作,观察线路板是否有翘起或变形。
6、切脚高度为1-1.6mm,合格后流入自动波峰焊机
7、操作设备使用完毕,关闭电源。
四、工艺要求
1、助焊剂在线路板焊盘上要喷均匀。
2、上锡时线路板的铜板面刚好与锡面接触0.5mm即可,不得有锡尘粘附在线路板上。
3、助焊剂、稀在空气中。
4、若长期不使用,应回收助焊剂,密闭。发泡管应浸在盛有助焊剂的密闭容器中。
5、焊接作业中应保证通风,防止空气污染,作业人员应穿好工作服,戴好口罩。
6、链爪清洁储液箱体应经常添加与定期更换,液面高度为槽高的1/2—2/3处,注意调整毛刷与链爪间隙。
3、不得时间过长、温度过高引起铜铂起泡现象,锡炉温度为255-265度(冬高夏低),上锡时间2-3秒。
4、焊点必须圆滑光亮,线路板必须全部焊盘上锡。
5、保证工作台面清洁,对设备定时进行记录。
五、注意事项
1、焊接不良的线路必须重焊,二次重焊须在冷却后进行。
2、操作过程中,不要触碰锡炉,不要让水或油渍物掉入锡炉中,防止烫伤。
3、将切脚机的高度、宽度调节到相应位置,输送带的宽度及平整度与线路板相符,切脚高度为1-1.6mm,将切脚机输送带和切刀电源开关置于ON位置。
4、检查待加工材料批号及相关技术要求,发现问题提前上报组长进行处理。
5、按波峰焊操作规程对整机进行熔锡、预热、清洗、传送调节速度与线路板相应宽度,直到启动灯亮为止。
pcb焊盘设计规范

注:以下设计标准参照了IPC-SM-782A标准和一些日本着名设计制造厂家的设计以及在制造经验中积累的一些较好的设计方案。
以供大家参考和使用(焊盘设计总体思想:CHIP件当中尺寸标准的,按照尺寸规格给出一个焊盘设计标准;尺寸不标准的,按照其物料编号给出一个焊盘设计标准。
IC、连接器元件按照物料编号或规格归类给出一个设计标准。
),以减少设计问题给实际生产带来的诸多困扰。
1、焊盘规范尺寸:不得用于商业用途不得用于商业用途不得用于商业用途不得用于商业用途不得用于商业用途不得用于商业用途不得用于商业用途2、SMT焊盘命名规则建议(英制英寸:用IN表示;公制毫米用MM表示,数据中间的小数点用d表示,以下数据均为元件的一些尺寸参数,这些参数能决定焊盘的尺寸和形状。
不同参数之间用“X”隔开)一、普通电阻(R)、电容(C)、电感(L)、磁珠(FB)类元件(元件形状矩形):元件类型+尺寸制式+外型尺寸规格命名。
如:FBIN1206、LIN0805、CIN0603、RIN0402、CIN0201;二、排阻(RN)、排容(CN):元件类型+尺寸制式+外型尺寸规格+P+引脚数目命名。
如:RNIN1206P8。
代表排阻,外型规格尺寸为1206,总共有8只引脚;三、钽质电容(TAN):元件类型+尺寸制式+外型尺寸规格命名。
如:TANIN1206。
代表钽质电容,其外型尺寸为1206;四、铝电解电容(AL):元件类型+尺寸制式+外型尺寸(上面部分的直径X元件高度)规格命名。
如:ALMM 5X5d4。
代表铝电解电容,其上面部分的直径为5mm,元件高度为5.4mm;五、二极管(DI):这里主要指两个电极的二极管分两类:1、平面型二极管(DIF):元件类型+尺寸制式+与PCB接触部分引脚尺寸规格(长X宽)+X+引脚跨距尺寸命名。
如:DIFMM1d2X1d4X2d8。
表示平面型二极管,引脚的长1.2mm,宽度1.4mm,引脚之间跨距为2.8mm;2、圆柱型二极管(DIR):元件类型+尺寸制式+外型尺寸规格命名。
波峰焊托盘设计规范
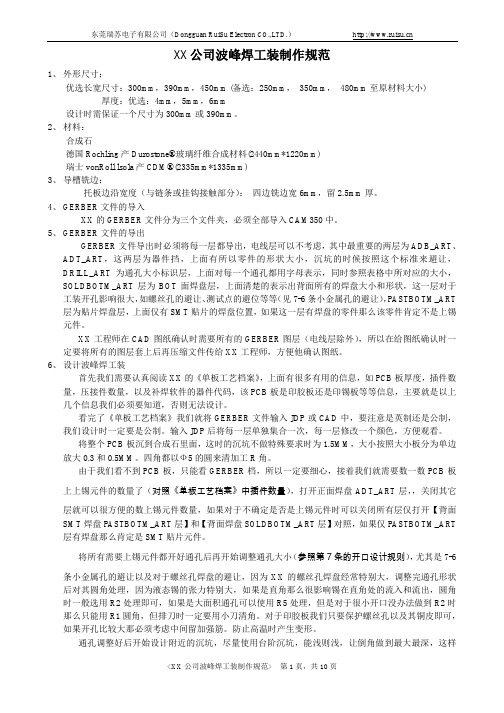
由于大板受热后会膨胀得比较大,所以要放大 0.5MM 间隙。
(大小板定义标准:≥250mm*250mm 的为大板;<250mm*250mm 的为小板。)
大PCB板时两边各加0.5MM 工装
PCB大板
小PCB板时两边各加0.3MM 工装
PCB小板
大板沉坑示意图
小板沉坑示意图
(3)开口与托盘沉坑边最小距离:大板:0.8mm,小板:0.5mm。以保证 PCB 板在任何位置时都可以 完全盖出通孔,这样可以保证不会发生溢锡现象。
210
45
210
GZ2102EA
45
RS
不采用
350 AD820E VER.A
0202A02REV.A
左 图 所 示 , 当 PCB板 为 210*210时 , 以
PCB板 外 形 单 边 放 大 45, 工 装 外 形 为
300*300。 而 此 时 PCB板 与 工 装 的 间 距
小,放置压块及刻字后,布局很紧张。 70
<XX 公司波峰焊工装制作规范> 第 5 页,共 10 页
东莞瑞苏电子有限公司(Dongguan RuiSu Electron CO.,LTD.)
(5)开口大小的确认:5mm。正常情况下开口大小只要单边放大 5MM 即可,因为过大开口 PCB 板 受热很大,很可能影响到正面的 SMT 元件。特殊情况例外。
工装大小的设计:整体基板设计好了我们再开始设计工装的大小以及其它附件,选用尺寸时一般 是在 PCB 整体型腔的大小上放大 45-70MM,然后再看按照客户给的尺寸取最接近的值,如果 PCB 板 比较小,那么我们要将其连板后再用同样的方法设计外型大小。
300
AD820E VER.A
国家标准-》无铅波峰焊接通用工艺规范

国家标准-》无铅波峰焊接通用工艺规范ICS 31(180L 30 备案号:23055--2008 J国中华人民共和国机械行业标准JB,T 7488—20087488—1 994 代替JB,T无铅波峰焊接通用工艺规范for lead-free General technological specification wavesoldering 2008(07(0 1实施 2008(02(0 1发布员会发布中华人民共禾口国国家发展和改革委JB,r 7488-一2008目次前言( ( ( ( (( ( ((( (( ( ( ( (( ( ( ( (( ( (( ( ( IIl1 范[1| ( ( (( ( ( ( ( (( ( (((12规范性引用文件 ( ( ((1 3术语和定义 ( ((1 4无铅波峰焊接工艺要求?? 3 4(1无铅波峰焊对无铅焊料、印制电路板等关键原材料的要求 3 4(2无铅工艺对波峰焊设备的要求一5 5无铅波峰焊接的工艺流程和工艺控制 (5 5(1无铅波峰焊接的一般工艺流程 ( ( ( 5 5(2无铅波峰焊接的工艺控制 6 6无铅波峰焊接电子组装件产品的质量检验 7 6(1 无铅波峰焊接电子组装件的焊接质量要求 7 6(2无铅波峰焊接焊点的质量要求 7 附录A(资料性附录)无铅波峰焊接常见的主要缺陷11 与对策1A(1焊料球 ( (I1A(2桥连 ( ( (( ( ( ( (1A(3漏焊(不润湿) ( ( ( 12 A(4拉尖 ( ( ( ( ( ( ( 12A(5焊缝起翘与焊盘起翘 ( ( ( ( 13 A(6表面粗糙与裂纹, 14 图1无铅波峰焊接温度曲线示意图 7 图2无铅焊点的润湿角示意图 8图4满足可接受条件的金属化孔图3满足目标条件的金属化孔填充 8填充 ((8 图5 iL壁表面的焊锡润湿不良 ( (9 图6满足目标条件一1,2,( (9 图7满足可接受条件一1,3级2,3级 10网8满足1级要求,2,3级为缺陷一10I 图A(1元件上的焊料球 (1 图A(2器件引脚间的焊料球 I】图A(3元件端头问的桥连 12 图A 4器件引脚之问的桥连 ((125 图A E?制电路板焊盘无焊料 12 图A(6元件端头无焊料 12 图A(7元件端头焊料拉尖 13 图A(8印制电路板焊盘焊料拉尖 13 图A(9焊料与焊盘问局部翘起13 图A(10 焊料与焊盘问翘起 ( 13(IB厂r 7488--20081 图A(1 焊盘与印制电路板之间分离 (13 图A(12无铅焊点表面上的粗糙与裂纹 (14 表1在电子产品生产中推荐使用下列的无铅焊料合金 3 表2无铅印制电路板焊盘表面镀(涂)( 一4 表3无铅元器件焊端表面镀层层4表4带引脚的金属化孔一焊接最低可接受条件 9 表5检查用的放大倍数(焊盘宽度) 10117488--2008 JB,T舀刚本标准代替JB,T 7488一1994《波峰焊工艺规范》。
波峰焊PCB焊盘工艺设计规范指引

波峰焊PCB焊盘工艺设计规范指引
摘要:焊盘工艺设计规范是对焊盘尺寸、形状、位置等进行统一设计,以确保焊接质量和产品质量的一项重要规范。
本文结合实际,从焊盘基本
参数、焊盘板化设计、焊盘形状、焊点位置及其尺寸等详细阐述了波峰焊PCB焊盘工艺设计规范指引,以期为PCB焊盘工艺设计提供参考。
关键词:波峰焊;PCB;焊盘工艺设计;规范指引
Keywords: Reflow soldering; PCB; Welding pad process design; Specification guide
一、焊盘基本参数
1.1焊盘材料
铜板或其他金属材料制成的焊盘,需采用环氧树脂(FR-4)。
1.2焊盘尺寸
PCB焊盘的尺寸大小要求可根据具体物理原件而定;其尺寸规格大小
一般为0.3mm×0.3mm至50.0mm×50.0mm。
1.3焊盘位置
PCB焊盘的位置应在指定的焊盘板和组件位置,需尽可能与焊接头和PCB连接,以免受到任何机械伤害。
二、焊盘板化设计
2.1特殊焊盘形状
为了获得更好的焊接效果和拓展设计空间,PCB焊盘可以设计为圆形、方形、菱形、椭圆等形状。
2.2绝缘层
为了防止电流漏出给到其他组件,焊盘应加上绝缘层,以保护组件,
绝缘材料一般为环氧树脂、玻璃纤维布等。
波峰焊工艺流程说明
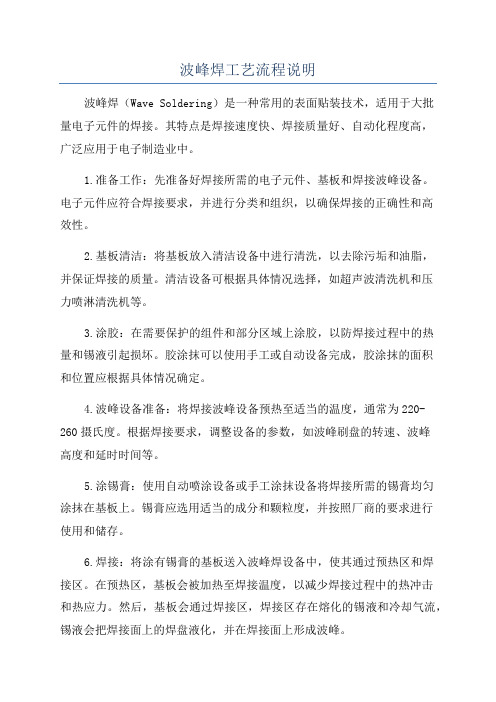
波峰焊工艺流程说明波峰焊(Wave Soldering)是一种常用的表面贴装技术,适用于大批量电子元件的焊接。
其特点是焊接速度快、焊接质量好、自动化程度高,广泛应用于电子制造业中。
1.准备工作:先准备好焊接所需的电子元件、基板和焊接波峰设备。
电子元件应符合焊接要求,并进行分类和组织,以确保焊接的正确性和高效性。
2.基板清洁:将基板放入清洁设备中进行清洗,以去除污垢和油脂,并保证焊接的质量。
清洁设备可根据具体情况选择,如超声波清洗机和压力喷淋清洗机等。
3.涂胶:在需要保护的组件和部分区域上涂胶,以防焊接过程中的热量和锡液引起损坏。
胶涂抹可以使用手工或自动设备完成,胶涂抹的面积和位置应根据具体情况确定。
4.波峰设备准备:将焊接波峰设备预热至适当的温度,通常为220-260摄氏度。
根据焊接要求,调整设备的参数,如波峰刷盘的转速、波峰高度和延时时间等。
5.涂锡膏:使用自动喷涂设备或手工涂抹设备将焊接所需的锡膏均匀涂抹在基板上。
锡膏应选用适当的成分和颗粒度,并按照厂商的要求进行使用和储存。
6.焊接:将涂有锡膏的基板送入波峰焊设备中,使其通过预热区和焊接区。
在预热区,基板会被加热至焊接温度,以减少焊接过程中的热冲击和热应力。
然后,基板会通过焊接区,焊接区存在熔化的锡液和冷却气流,锡液会把焊接面上的焊盘液化,并在焊接面上形成波峰。
7.冷却:基板离开焊接区后,通过冷却区进行冷却。
冷却区通常通过冷却风扇或冷却装置来实现,以使焊接后的电子元件迅速冷却,并保持其焊接质量。
8.检测:对焊接后的基板进行外观检测和功能测试,以确保焊接的质量和可靠性。
外观检测可以通过目视检查或辅助工具进行,功能测试需要使用相应的测试设备。
9.清理:清除焊接过程中产生的残留物,如焊渣和焊接剩余物。
清理可以通过手工或自动设备进行,以保持焊接面和基板的干净。
以上是波峰焊工艺的一般流程,具体的工艺参数和设备配置可以根据不同的焊接要求和生产情况进行调整和优化。
波峰焊工艺 PCB_焊盘工艺设计规范

波峰焊工艺PCB 焊盘与孔设计规范1. 目的规范产品的PCB焊盘设计工艺,规定PCB焊盘设计工艺的相关参数,使得PCB 的设计满足可生产性。
2. 适用范围本规范适用于本公司电子产品的PCB 工艺设计,运用于但不限于PCB 的设计、PCB 批产工艺审查、单板工艺审查等活动。
本规范之前的相关标准、规范的内容如与本规范的规定相抵触的,以本规范为准3.引用/参考标准或资料TS—S0902010001 <<信息技术设备PCB 安规设计规范>>IPC-SM-782<<表面贴装设计与焊盘结构标准>>IPC-2221<< PCB设计通用标准>>IEC60194 <<印制板设计、制造与组装术语与定义>> (Printed Circuit Board designmanufacture and assembly-terms and definitions)IPC—A—600F <<印制板的验收条件>> (Acceptably of printed board)IEC609504.规范内容4.1焊盘的定义通孔焊盘的外层形状通常为圆形、方形或椭圆形。
具体尺寸定义详述如下,名词定义如图所示。
1)孔径尺寸:若实物管脚为圆形:孔径尺寸(直径)=实际管脚直径+0.20∽0.30mm(8.0∽12.0MIL)左右;若实物管脚为方形或矩形:孔径尺寸(直径)=实际管脚对角线的尺寸+0.10∽0.20mm(4.0∽8.0MIL)左右。
2)焊盘尺寸:常规焊盘尺寸=孔径尺寸(直径)+0.50mm(20.0 MIL)左右。
4.2 焊盘相关规范4.2.1所有焊盘单边最小不小于0.25mm,整个焊盘直径最大不大于元件孔径的3倍。
一般情况下,通孔元件采用圆型焊盘,焊盘直径大小为插孔孔径的1.8倍以上;单面板焊盘直径不小于2mm;双面板焊盘尺寸与通孔直径最佳比为2.5,对于能用于自动插件机的元件,其双面板的焊盘为其标准孔径+0.5---0.6mm4.2.2 应尽量保证两个焊盘边缘的距离大于0.8mm,与过波峰方向垂直的一排焊盘应保证两个焊盘边缘的距离大于1.0mm(此时这排焊盘可类似看成线组或者插座,两者之间距离太近容易桥连)在布线较密的情况下,推荐采用椭圆形与长圆形连接盘。
波峰焊接工艺介绍
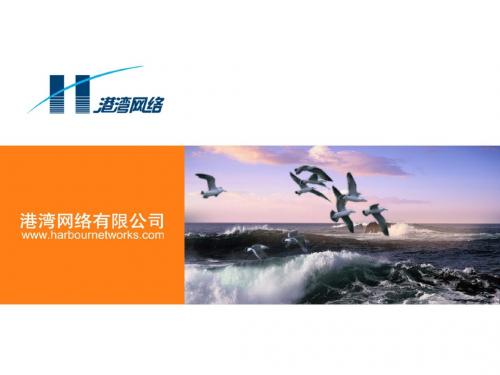
波峰焊工艺--助焊剂涂布方法1 波峰焊工艺--助焊剂涂布方法 --助焊剂涂布方法
发泡式:目前众多的生产企业使用的波峰焊机装有发泡式涂敷助焊剂装置。 ① 发泡式:目前众多的生产企业使用的波峰焊机装有发泡式涂敷助焊剂装置。这 些设备只要清洗干净,对发泡装置不加改造或稍加改造即可用于免清洗工艺, 些设备只要清洗干净,对发泡装置不加改造或稍加改造即可用于免清洗工艺,投 资少。采用发泡工艺的缺点是助焊剂的用量不易控制,涂敷不均匀, 资少。采用发泡工艺的缺点是助焊剂的用量不易控制,涂敷不均匀,在PCB板上 板上 有残留助焊剂,给免清洗工艺带来明显的影响。更换孔径细密的发注管使发泡细密, 有残留助焊剂,给免清洗工艺带来明显的影响。更换孔径细密的发注管使发泡细密, 调节发泡高度为不超过PCB板厚度的 ,使泡沫正好沾着 板厚度的1/3,使泡沫正好沾着PCB板底部,不翻上 板底部, 调节发泡高度为不超过 板厚度的 板底部 不翻上PCB 板顶部,涂敷均匀,则能使焊剂残留减至最少,又能获得较好的焊接效果。另外, 板顶部,涂敷均匀,则能使焊剂残留减至最少,又能获得较好的焊接效果。另外, 发泡装置是开启式的,助焊剂中溶剂极易挥发,需定定时测量助焊剂的密度, 发泡装置是开启式的,助焊剂中溶剂极易挥发,需定定时测量助焊剂的密度,添加 稀释剂来调正其密度,以保证达到最佳焊接效果。 稀释剂来调正其密度,以保证达到最佳焊接效果。同时因吸收空气中水分和落入灰 尘等杂质极易使助焊剂变质,使用一段时间后需要更换助焊剂,造成一定的浪费。 尘等杂质极易使助焊剂变质,使用一段时间后需要更换助焊剂,造成一定的浪费。
翻板 invert
胶涂布 Adhesive printing
Wave solder 波峰焊
Insert THD 手插件
invert 翻板
波峰焊工艺技术介绍
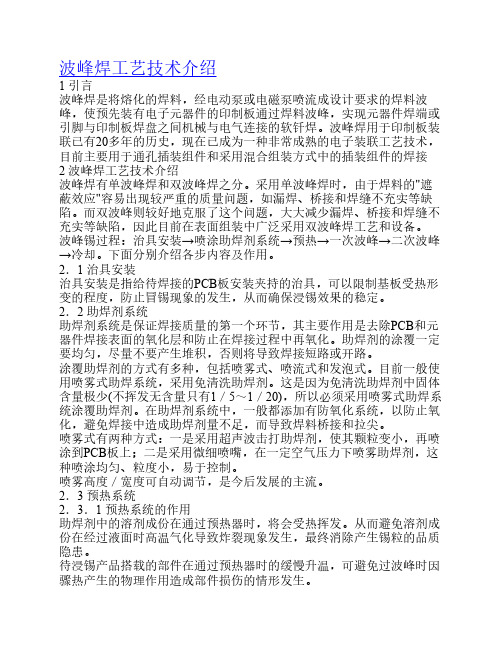
波峰焊工艺技术介绍1 引言波峰焊是将熔化的焊料,经电动泵或电磁泵喷流成设计要求的焊料波峰,使预先装有电子元器件的印制板通过焊料波峰,实现元器件焊端或引脚与印制板焊盘之间机械与电气连接的软钎焊。
波峰焊用于印制板装联已有20多年的历史,现在已成为一种非常成熟的电子装联工艺技术,目前主要用于通孔插装组件和采用混合组装方式中的插装组件的焊接2 波峰焊工艺技术介绍波峰焊有单波峰焊和双波峰焊之分。
采用单波峰焊时,由于焊料的"遮蔽效应"容易出现较严重的质量问题,如漏焊、桥接和焊缝不充实等缺陷。
而双波峰则较好地克服了这个问题,大大减少漏焊、桥接和焊缝不充实等缺陷,因此目前在表面组装中广泛采用双波峰焊工艺和设备。
波峰锡过程:治具安装→喷涂助焊剂系统→预热→一次波峰→二次波峰→冷却。
下面分别介绍各步内容及作用。
2.1 治具安装治具安装是指给待焊接的PCB板安装夹持的治具,可以限制基板受热形变的程度,防止冒锡现象的发生,从而确保浸锡效果的稳定。
2.2 助焊剂系统助焊剂系统是保证焊接质量的第一个环节,其主要作用是去除PCB和元器件焊接表面的氧化层和防止在焊接过程中再氧化。
助焊剂的涂覆一定要均匀,尽量不要产生堆积,否则将导致焊接短路或开路。
涂覆助焊剂的方式有多种,包括喷雾式、喷流式和发泡式。
目前一般使用喷雾式助焊系统,采用免清洗助焊剂。
这是因为免清洗助焊剂中固体含量极少(不挥发无含量只有1/5~1/20),所以必须采用喷雾式助焊系统涂覆助焊剂。
在助焊剂系统中,一般都添加有防氧化系统,以防止氧化,避免焊接中造成助焊剂量不足,而导致焊料桥接和拉尖。
喷雾式有两种方式:一是采用超声波击打助焊剂,使其颗粒变小,再喷涂到PCB板上;二是采用微细喷嘴,在一定空气压力下喷雾助焊剂,这种喷涂均匀、粒度小,易于控制。
喷雾高度/宽度可自动调节,是今后发展的主流。
2.3 预热系统2.3.1 预热系统的作用助焊剂中的溶剂成份在通过预热器时,将会受热挥发。
- 1、下载文档前请自行甄别文档内容的完整性,平台不提供额外的编辑、内容补充、找答案等附加服务。
- 2、"仅部分预览"的文档,不可在线预览部分如存在完整性等问题,可反馈申请退款(可完整预览的文档不适用该条件!)。
- 3、如文档侵犯您的权益,请联系客服反馈,我们会尽快为您处理(人工客服工作时间:9:00-18:30)。
波峰焊PCB焊盘工艺设计规范指引7
未做特别要求时,手插零件插引脚的通孔规格如下:
针对引脚间距≤2.0mm的手插PIN、电容等,插引脚的通孔的规格为:0.8~0.9mm 未做特别要求时,自插元件的通孔规格如下:
多个引脚在同一直线上的器件,象连接器、DIP 封装器件、T220 封装器件,布局时应使其轴线和波峰焊方向平行
波峰焊方向
较轻的器件如二级管和1/4W 电阻等,布局时应使其轴线和波峰焊方向垂直
贴片元件过波峰焊时,对板上有插元件(如散热片、变压器等)的周围和本体下方其板上不可开散热孔
锡珠
贴片元件过波峰焊时,底面(焊接面)零件本体必须高度5mm≤5.0mm
需要过锡炉后才焊的元件,焊盘要开走锡位,方向与过锡方向相反,宽度视孔的大小为焊盘与较大面积的导电区如地、电源等平面相连时,应通过一长度较细的导电线路进
过波峰焊之下板裸露铜箔为0.5MM宽、0.5MM间距的条纹形裸铜;大面积裸露铜箔内如有元件脚,其焊盘要与其他裸铜箔隔开;相邻元件脚的焊盘要独立开,不可有裸铜连过波峰焊的插
件元件焊盘边缘间距应大于1.0mm,(包括元件本身引脚的焊盘边缘间
Min 1.0mm
绿油
覆盖
PT下方有贴片元件时,贴片元件DIP后方须加窃锡焊盘,窃锡焊盘宽为4MM,长度A同尺
B
波
A
需波峰焊的贴片IC要设计为纵向过锡炉;各脚焊盘之间要加阻焊漆;在最后一脚要设计窃锡焊盘,如受PCB LAYOUT限制无法设计窃锡焊盘,应将DIP后方与焊盘邻近或相连的线路绿漆开放为裸铜,作为窃锡焊盘用。
针对多层板双面均有锡膏工艺,需过波峰焊时,底面(焊接面)贴片元件的焊盘或本体边缘与插件零件焊盘边缘距离≥4mm,双列或多列组件下板脚内部不可有贴片零件。
>4mm。