挤压模具设计说明书资料
6.2正挤压模具设计

实心杆件正挤压 模具
• 同学们判断是否通 用、可调、弹性卸 料、导向、销钉固 定还是台阶固定? • 特点:凸模有护套 机构;拉杆可调、 两层预应力圈
二黑色金属正挤 压杯形件模具
• 同学们判断是否通用、 可调、弹性卸料、导向、 销钉固定还是台阶固定、 凸模内衬活动芯轴? • 凹模与凸模用斜度固定 圈1与5压紧固定;凸模 内衬活动芯轴(气孔); 无定位销 • 注意:每个模具零件都 要考虑装卸!
外圆形状锥形15入模锥度一般采用60126工作带长度d14圆角半径r的大小越大越好根据产品选后间隙b005041工作带长与材料压力顶出力关系凹模能短则短否则增大凸模失稳可能一正挤压模具工作部分零件设计与凸模相互位置不动杯形件要滑动要点
同学们试读出有哪些结构特点?
第三节 正挤压模具结构 一、有色金属管件正挤压 模具没有上卸件装置
图12—20是用于带凸缘铝管 正挤压的导柱通用模架。 不可调整式通用模架的特 点基本上与图12—3的反 挤模相同。它通过凸模27 与凹模7将垫圈样毛坯正 挤成带凸缘的管状零件。 考虑到工件挤压后卡在凹 模内,一副拉杆式顶件机 构,顶出器11将加工好的 工件顶出。模具的导柱安 装在上模,导套则装在下 模,也可以根据需要将导 柱导套反过来安放。
第四节 正挤压模具工作部分设计 一、正挤压凹模
分模原则:见裂就分图a整体图b、c纵向分模图def横
向分模A易裂bc不钻料d钻料难加工ef轴向力大,不钻料
一、正挤压凹模
• 分模原则:见裂就分 • 图a整体图b、c纵向分模图 def横向分模A易裂bc不钻料 d钻料ef轴向力大不钻料
• 要点:外圆形状锥形 1.5°、入模锥度一般采 用60~126° 、工作带 长度d(1-4)、圆角半 径R的大小越大越好根 据产品选, 后间隙 b0.05-0.4
挤压成型模具设计手册

挤压成型模具设计手册一、模具设计基础模具设计是挤压成型工艺中的重要环节,它涉及到产品的形状、尺寸、精度和生产效率等方面。
在进行模具设计时,需要充分了解产品的用途和性能要求,同时考虑到生产条件和制造成本等因素。
二、材料选择与处理模具材料的选择和处理对于模具的寿命和性能至关重要。
常用的模具材料包括钢材、硬质合金、陶瓷等,具体选择应根据产品的要求和生产条件来确定。
材料处理包括热处理、表面处理等,可以提高材料的硬度、耐磨性和耐腐蚀性等性能。
三、模具结构设计模具结构设计是模具设计的核心,它决定了模具的功能和生产能力。
结构设计应充分考虑产品的形状、尺寸、精度和生产效率等因素,同时考虑到材料的流动和排溢等条件。
此外,结构设计还应考虑到维修和保养的方便性。
四、成型工艺优化挤压成型工艺是模具设计的重要环节之一,它涉及到材料的流动、温度和压力的控制等方面。
工艺优化可以提高生产效率、降低能耗和提高产品质量。
在进行工艺优化时,需要考虑多种因素,包括材料的性能、模具的结构和尺寸等。
五、温度控制系统温度是影响挤压成型工艺的重要因素之一,因此温度控制系统的设计也是模具设计的重要环节之一。
温度控制系统应能够精确控制模具的温度,并保持温度的稳定。
此外,温度控制系统的设计还应考虑到加热和冷却的速度和时间等因素。
六、模具强度与刚性模具的强度和刚性是影响模具寿命和产品质量的重要因素。
在进行模具设计时,应充分考虑模具的强度和刚性要求,并采取相应的措施来提高模具的强度和刚性。
例如,可以采用加强筋、增加厚度等方法来提高模具的强度和刚性。
七、润滑与保养润滑和保养是保持模具性能和延长模具寿命的重要措施。
在进行模具设计时,应充分考虑润滑和保养的要求,并采取相应的措施来实现润滑和保养的目的。
例如,可以采用润滑剂、密封圈等来润滑和保养模具。
挤压模具课程设计资料讲解

挤压模具课程设计课题挤压模具课程设计学生姓名孙天宇 1110121103汪浩 1110121104王朝 1110121105王青 1110121106王显 1110121107王业伟 1110121108 院别机械工程学院专业班级11材控(2)班指导教师张红云、张金标、刘建二0一四年十月课程设计任务书机械工程学院11材控班指导教师:张红云,张金标,刘建。
设计课题:挤压模具设计一、设计条件:在19.6MN挤压机的Φ200mm挤压筒上生产出下列条件的合格型材,设计出相应的型材模具。
1.单模孔模具生产如下图型材。
(1,2,3组同学设计)2.双模孔生产ф12mm的圆棒材。
(4,5,6组同学设计)3.三模孔生产ф8mm的圆棒线材。
(7,8,9组同学设计)4.四模孔生产ф6mm的圆棒线材。
(10,11,12组同学设计)5.双模孔生产3*5扁线材。
(13,14,15组同学设计)6.四模孔生产3*5扁线材。
(16,17组同学设计)二、设计内容:1.模孔布置。
2.设计工作带长度。
3.型材模孔尺寸设计。
4.模子强度校核。
5.画出模具图。
三、设计时间:2014年12月27日至10月31日四、设计地点:实验楼C楼501,502五、分组情况:目录第一章概述 ........................................ 错误!未定义书签。
第二章坯料选择 . (6)2.1坯料尺寸计算 (6)2.2挤压比的计算 (6)2.3挤压机的选择 (7)第三章模孔布置 (8)3.1模孔的布置 (8)3.2工作带长度的确定 (9)3.3模孔尺寸的确定 (10)3.4模孔出口尺寸确定 (10)第四章模具外形尺寸设计 (11)4.1模角 (11)4.2模子的外形尺寸 (11)4.3入口圆角半径r (12)4.4挤压模结构形式与模具外形锥度 (12)4.5模具材质的选取 (12)第五章强度校核 (14)第六章绘制模具图 (15)设计小结 (16)参考文献 (22)第一章概述本次设计主要是在给定挤压筒和挤压机的条件下,设计挤压出3 5mm的扁线材所用的双模孔模具。
挤压模具设计书说明书

挤压模具设计书说明书1. 引言本说明书旨在提供挤压模具设计的详细指导。
挤压模具是在挤压工艺中使用的一种关键工具,它对产品的质量和生产效率具有重要影响。
本说明书将涵盖挤压模具设计的基本概念、设计要点和步骤等内容,旨在帮助设计人员更好地理解和应用挤压模具设计相关知识。
2. 挤压模具设计概述挤压是一种通过挤压机将熔融的原料挤出成型的工艺。
挤压模具是挤压过程中起到塑料流动、形成和冷却等作用的工具。
挤压模具设计需要考虑多个因素,如材料选择、模具结构、模具加工工艺等。
3. 挤压模具设计步骤3.1. 产品分析在进行挤压模具设计之前,首先需要对待生产产品进行详细分析。
这包括产品的材料、形状、尺寸、表面要求等方面的分析。
通过产品分析,可以为模具设计提供基本的设计要求和指导。
3.2. 模具结构设计模具结构设计是挤压模具设计的核心部分。
在模具结构设计过程中,需要考虑到产品的形状和尺寸要求,确定模具的结构形式、模腔布置、模具开合方式等。
合理的模具结构设计能够有效提高产品的一致性和精度。
3.3. 材料选择挤压模具的材料选择对于模具寿命和产品质量具有重要影响。
常见的挤压模具材料包括合金钢、硬质合金等。
在选择材料时,需要综合考虑材料的硬度、强度、热导率等因素。
3.4. 模具加工工艺模具加工工艺是指模具从原料到成品的全过程。
挤压模具加工工艺包括切割、车削、铣削、磨削等。
在进行模具加工时,需要根据模具的具体要求选择合适的加工工艺,保证模具的加工精度和质量。
4. 挤压模具设计要点4.1. 模具结构要点•模具结构应满足产品的外观要求,确保产品的形状和尺寸精度。
•模具结构应具备良好的冷却系统,以提高模具的散热效果,避免产品变形和模具损坏。
•模具结构应具备合理的模腔设计,以确保塑料流动的均匀性和稳定性。
4.2. 模具材料要点•模具材料应具有高硬度和耐磨性,以提高模具的使用寿命。
•模具材料应具有良好的热导率,以实现有效的模具冷却效果。
4.3. 模具加工工艺要点•模具加工工艺应具有高加工精度和稳定性,以确保模具的质量和精度。
挤压模具说明书

1. 绪论1. 1 挤压的定义及分类1. 1. 1 挤压的定义挤压是将挤压模具装在压力机上,将金属坯料放入模腔内,利用压力机的往返运动,在强大的压力和一定的速度之下,迫使金属在挤压模的型腔内发生塑性变形,从模腔中挤出,从而获得所需形状、尺寸以及具有一定力学性能的挤压件。
挤压是在很强的三向应力状态下的成型的过程,因而允许很大的变形量,更适于低塑性材料的成型。
显然,挤压加工是靠模具来控制金属流动,靠金属体积的大量转移来成型零件的;在整个变形过程中,其材料的体积是保持不变的[1]。
挤压成型速度范围很广,它既可在专用挤压机上进行,也可在一般的机械压力机、液压机、摩擦压力机以及高速空气锤上进行。
挤压成型温度范围也很广,它既可在常温、中温下进行,也可在高温中进行。
根据制品形状的要求,有各种与之相配的模具。
挤压模具是挤压生产中最重要的工具,它的结构形式、各部分尺寸、模具材料、模具的装配形式等,对挤压力、金属流动的均匀性、制品尺寸的稳定性、制品表面质量以及模具自身的使用寿命等都产生极大的影响[2]。
1. 1. 2 挤压的分类(1)按毛坯加热温度的不同分类1)冷挤压在室温中对毛坯进行挤压。
冷挤压的特点及应用范围;采用冷挤压法加工可以降低原材料消耗,材料的利用率高达70%~90%[4]。
在冷挤压中,金属材料处于三向不等的压应力作用下,挤压后金属材料的晶粒组织更加细小而密实;金属流线不被切断,而是沿着挤压件轮廓连续分布;同时,由于冷挤压利用了金属材料经冷加工而产生的加工硬化的特性,使冷挤压件的强度大为提高,从而提供了用低强度钢代替高强度钢的可能性[3]。
此外,冷挤压靠强大的压力来熨平毛坯表面,因此可以获得较高尺寸精度和较低表面粗糙度的冷挤压件。
冷挤压模具与一般冷冲模相比,工作时所受的压力大得多,因而在强度、刚度和耐磨性等方面的要求都较高。
冷挤模不同于冷冲模的地方主要有:●凹模一般为组合式(凸模也常常用组合式)结构;●上﹑下模板更厚,材料选择得更好,满足模具的强度要求;●导柱直径尺寸较大,满足模具的刚度要求;●工作零件尾部位置均加有淬硬的垫板;●模具易损件的更换、拆卸更方便[5]。
冷挤压工艺和模具设计说明书模板

冷挤压工艺及模具设计
5.1.4 冷挤压变形程度
在冷挤压过程中,变形程度是决定使用设备压力大小及 影响模具寿命的主要因素之一,若要提高生产率,就必须增 大每次挤压的变形程度,以减少挤压次数。但变形程度越大, 其变形抗力也越大,就会降低模具的寿命,甚至引起凸模折 断或凹模开裂。因此对各种挤压材料,都应选择合适的变形 程度。
冷挤压工艺及模具设计
表5-1 碳素钢及低合金钢的许用变形程度
材料牌号 10 15 35 45 15Cr
34CrMo
反挤压εF 75~80 70~73 50 40 42~50 40~45
表5-2 有色金属冷挤压的许用变形程度
金属材料 铝
截面收缩率εF(%)
正挤压
95~99
防锈铝
反挤压
90~99
紫铜、黄铜、硬铝
单位挤压应力 /MPa
250~300 1500~2000
300~500 2000~2500
500~700 2500~3000
700~800 3000~3500
800~900 3500~4000
表5-4 冷挤压专用液压机主要技术规格
公称挤 活塞直 压力/kN 径/mm
10000
360
20000
500
30000
冷挤压工艺及模具设计
(4) 提高零件的精度,降低表面粗糙度
由于金属表面在高压、高温(挤压过程中产生的热量) 下受到模具光滑表面的熨平,因此,制件表面很光,表面强 度也大为提高。冷挤压零件的精度可达1T8~1T9级,有色金
属冷挤压零件的表面粗糙度可达Ra=1.6~0.4μm。有的冷挤
压件无需切削加工。
冷挤压工艺及模具设计
对于有些材料,为了确保冷挤压过程中的润滑层不被过 大的单位接触压力所破坏,毛坯要经过表面化学处理。例如 碳钢的磷酸盐处理(磷化)、奥氏体不锈钢的草酸盐处理、 铝合金的氧化、磷化或氟硅化处理、黄铜的钝化处理等。经 化学处理后的毛坯表面,覆盖一层很薄的多孔状结晶膜,它 能随毛坯一起变形而不剥离脱落,经润滑处理后在孔内吸附 的润滑剂可以保持挤压过程中润滑的连续性和有效的润滑效 果。
挤压模设计4.
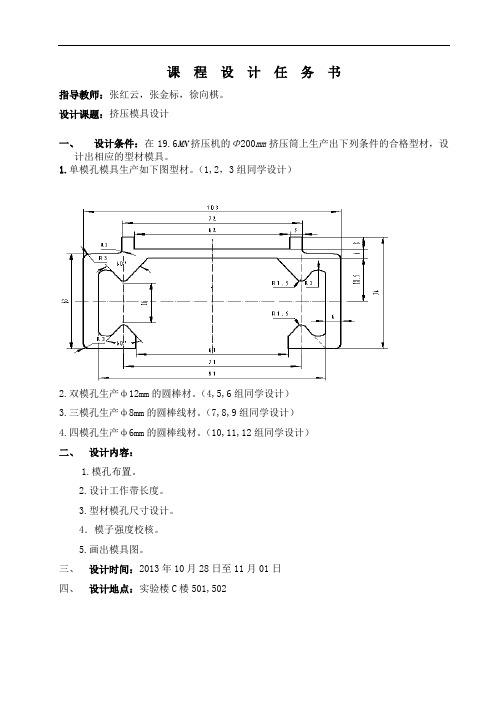
课程设计任务书指导教师:张红云,张金标,徐向棋。
设计课题:挤压模具设计一、设计条件:在19.6MN挤压机的Φ200mm挤压筒上生产出下列条件的合格型材,设计出相应的型材模具。
1.单模孔模具生产如下图型材。
(1,2,3组同学设计)2.双模孔生产ф12mm的圆棒材。
(4,5,6组同学设计)3.三模孔生产ф8mm的圆棒线材。
(7,8,9组同学设计)4.四模孔生产ф6mm的圆棒线材。
(10,11,12组同学设计)二、设计内容:1.模孔布置。
2.设计工作带长度。
3.型材模孔尺寸设计。
4.模子强度校核。
5.画出模具图。
三、设计时间:2013年10月28日至11月01日四、设计地点:实验楼C楼501,502五、分组情况:目录第一章绪论 (1)1.1 挤压技术简介 (1)1.2 热挤压模具在有色金属生产中的应用 (1)1.3 关于镁及镁合金 (1)1.4 关于挤压模具设计 (1)第二章坯料选择 (2)2.1 锭坯尺寸选择 (2)2.2 挤压比计算 (2)2.3 锭坯材料选择 (3)第三章模孔布置 (4)3.1 模孔布置 (4)3.2 模孔尺寸的确定 (5)3.3 模孔工作带长度的确定 (5)3.4 导流模设计 (5)第四章模具外形尺寸设计 (7)4.1模具外径D的设计 (7)4.2 模具厚度H (7)4.3 挤压模结构形式与模具外形锥度 (7)4.4 模具入口处圆角半径的确定 (7)4.5 模具出口部位结构及尺寸 (8)4.6 模具材料的确定 (9)第五章棒材模强度校核 (11)第六章绘制模具图 (12)设计小结 (14)参考文献 (15)致谢 (16)第一章绪论1.1 挤压技术简介挤压是将金属毛坯放入模具模腔内,在强大压力和一定速度的作用下,迫使金属从模腔中挤出,从而获得所需形状、尺寸以及具有一定力学性能的制品。
因此,挤压加工是利用模具来控制金属流动,使金属体积大量转移来形成零件。
挤压模具是挤压生产中最重要的工具,它的结构形式、各部分尺寸、模具材料、模具的装配形式等,对挤压力、金属流动的均匀性、制品尺寸的稳定性、制品表面质量以及模具自身的使用寿命等都产生极大的影响。
冷挤压工艺和模具设计说明书模板

冷挤压工艺及模具设计
5.2 冷挤压模具设计
5.2.1 冷挤压模的特点
由于冷挤压时,单位挤压力较大,因此冷挤压模具的强 度、刚度及耐用度等方面其要求都比一般冲模高,它与一般 普通冲模相比,主要有以下特点: 1.模具的工作部分与上、下底板之间一般都设有足够 的支承面与足够厚度的淬硬垫板,以承受很大的压力,减少 上、下底板上的单位压力。
冷挤压时,一次挤压加工所容许的变形程度,称为许用 变形程度。不同材料有不同的许用变形程度。在工艺上,每 道冷挤压工序的变形程度应尽量小于许用值,使模具承受的 单位挤压力不超过模具材料许用应力(目前一般模具材料的 许用应力为2500~3000N/mm2),确定许用变形程度数值是 冷挤压工艺计算的一个重要依据,因为冷挤压许用变形程度 的大小决定了制件所需的挤压次数。若计算出的冷挤压变形 程度超过许用值、则必须用多次挤压完成,以延长模具寿命, 避免损坏模具。
冷挤压工艺及模具设计
3.复合挤如图5-3所示,挤压时,金属流动方向相对于 凸模运动方向,一部分相同,另一部分相反,适用于各种复 杂形状制件的挤压;改变凹模孔口或凸、凹模之间缝隙的轮 廓形状,就可以挤出形状和尺寸不同的各种空心件和实心件。
图5-1 正挤压图
5-2 反挤压图
5-3 复合挤
冷挤压工艺及模具设计
程度。
冷挤压工艺及模具设计
4.1.4.1 变形程度的表示方法 变形程度是表示挤压时金属塑性变形量大小的指标,其 最常用的表示方法有两种:截面收缩率和挤压面积比。 (1) 截面收缩率 式中
挤压模具设计说明书

由于B0=1.4㎜.本设计△=0.1
故Tk=1.4+0.1=1.5㎜
7.模孔工作带长度hg的确定
由于本型材制品的对称性较好,外形相对较小,一般可取2~6㎜,生产实践中对铝合金常用6~15㎜
本设计取hg=6mm
8.模芯的设计
一般伸出下模工作带3-5mm,本设计取4mm,模腔外形按空心型材的空心部分确定。
序号
(mm)
(mm)
单重wd
填充系数K
填充后长度Le
压余厚hy
(mm)
切压余后的有效长度Ld
挤压比
λ
制品长
L制
(m)
成品数
nx6
(m)
成品重
W制(kg)
成材率
W制/Wd
(%)
1
Φ95
Φ90
270
4.64
1.114
242
20
222
54.65
13.512×6m3.89 Nhomakorabea83.84%
2
Φ95
Φ90
320
5.50
因为本设计采用孔道式分流组合模
故:取H上=48H下=40模垫厚10㎜
5.组合模相关参数的确定:
1).分流孔的个数取4个,形状为扇形
2).扇形面积的确定:
因为分流孔面积与制品断面积的比值∑F分/F型=K,K即为分流比,,一般K对于空心型材时,取K=10~30。本设计取K=10
分流孔的面积∑F分=K. F型=10×241=2410 mm2
图7
依据经验a一般取2~5㎜,有的取8㎜.本设计取8㎜
图8
关于α的计算,由上图知
h=H/2+8=38.1/2+8=27.05㎜
铝型材挤压模具设计书

铝型材挤压模具设计书一、前言铝型材挤压模具是铝型材生产的核心设备之一,其设计质量直接影响到产品的质量和生产效率。
铝型材挤压模具的设计书是非常重要的,它不仅包含了模具的结构、尺寸、工艺等方面的信息,还需要考虑到生产实际情况和经济效益等因素。
本文将从以下几个方面介绍铝型材挤压模具设计书。
二、设计书内容1. 模具结构模具结构是指模头、挤出孔、定位销、导向柱等部件的组合方式。
在设计时需要考虑到产品形状、尺寸和特殊要求等因素,以确定最合适的结构方案。
2. 尺寸参数尺寸参数是指模具各部件的尺寸大小,包括了长度、宽度、高度等方面。
在设计时需要根据产品要求和加工工艺等因素进行计算,以确保各部件尺寸精确合理。
3. 工艺流程工艺流程是指产品从原材料到成品的加工过程,在设计时需要考虑到每个环节所需的设备和工序,并根据实际情况进行调整和优化。
4. 材料选用材料选用是指模具各部件所使用的材料,需要根据模具的使用环境、产品要求和经济效益等因素进行选择。
5. 加工精度加工精度是指模具各部件的加工精度要求,包括了尺寸精度、表面光洁度等方面。
在设计时需要考虑到加工设备和技术水平等因素,以确保模具的质量和生产效率。
6. 维护保养维护保养是指模具在使用过程中需要进行的维护保养工作,包括了清洗、润滑、更换零部件等方面。
在设计时需要考虑到维护保养的便捷性以及对生产效率的影响。
三、设计书编写步骤1. 确定产品要求和加工工艺在编写设计书之前,需要明确产品形状、尺寸和特殊要求等方面的信息,并确定加工工艺流程。
2. 设计模具结构根据产品要求和加工工艺流程,确定最合适的模具结构方案,并进行初步设计。
3. 计算尺寸参数根据初步设计确定各部件尺寸大小,并进行计算和校验。
4. 选择材料根据模具使用环境、产品要求和经济效益等因素,选择合适的材料。
5. 确定加工精度要求根据产品要求和加工工艺流程,确定模具各部件的加工精度要求。
6. 考虑维护保养在设计时需要考虑到模具的维护保养便捷性,以及对生产效率的影响。
毕业设计(论文)-冷挤压模具设计说明书

毕业设计(论文)-冷挤压模具设计说明书摘要阶梯形零件是多种复杂形状的组合,其成形工艺较难,在工艺设计和变形方案的制定上,有其独自的特点。
这类零件一般可采用板料多道拉深来成形。
但是对于本设计中的阶梯方铝罩零件来说,其内外都呈现阶梯状且形状不一致辞,并且由于中间过渡部分形状不规则,因此不可能用板材成形工艺成形,而只能采用挤压等其他方法成形。
对于复杂的阶梯形零件,一次挤压不容易达到预期成形效果。
因此,一般采用有预成形的多道次挤压工艺。
其中的关键是如何合理分配材料变形程度,控制材料流动,减少过度变形,从而得到合格的零件。
本文探讨了阶梯方铝罩挤压的可行性,通过对产品零件图的分析,制定了几种工艺方案并进行分析比较,在选择最优方案的同时也制定了工艺流程。
在此基础上详细地介绍了阶梯方铝罩挤压模具的设计过程。
采用冷挤压工艺加工后,提高了零件的精度和表面质量,改善了强度和韧性,减少了切削加工量,节约了原材料,提高了生产效率,也改善了零件的组织性能。
关键词:阶梯方铝罩,成形工艺,冷挤压,模具设计IABSTRACTMulti-step part is a combination, which is composed with various complicated shapes. Its forming craft is more difficult. So it has its own characteristic in the technological design and the distortion plan formulation. Generally, this kind of components can be formed with the technology of multi-drawing the sheet. However, the product in this paper is not so regular. Its shape has steps both in exterior andinterior and the shape is irregular. At the same time, the middle transition part is so complex that it is impossible to adopt the drawing technology to form. Therefore, we need to consider the cold extrusionand other way to get the shape. It is no easy to achieve the anticipated formed effect with only one extrusion, because the step-shape is so complex. It should use multi-extrusion craft with pre-form forging. So the key is how to distribute rationally the distortion degree, control material flow, reduce the excessive deformation and obtain the qualified components. The feasibility of extrusion forming of multi-step part was discussed in this article. With the analysis of several technological programs, the optimal plan was made and selected, the technological process was determined. Based on the pre-discussion, the extrusion die was design and the design process is presented detailedly. By using the cold extrusion craft process, the precision and the surface quality of the product is improved, the intensity and toughness is got better, the cutting process is reduced, the raw material is saved. Not only does it enhanced the production efficiency, but also improve the organization of component.Keywords: multi-step part,forming technique,cold extrusion,die designII目录第1章冷挤压技术的介绍 .............................................11.1冷挤压工艺的实质 .................................................11.2冷挤压工艺的优点 .................................................11.3冷挤压工艺的缺点 .................................................21.4冷挤压工艺的应用范围 .............................................31.5冷挤压工艺的的发展方向 ...........................................3 第2章工艺分析及制定 ...............................................42.1产品零件的分析 ...................................................42.2工艺方案的分析 ...................................................5 第3章毛坯制备及处理 ..............................................113.1冷挤压件毛坯的制备 ..............................................113.2冷挤压件材料的软化热处理 ........................................133.3冷挤压件的表面处理与润滑 ........................................14 第4章冷挤压力 .....................................................164.1影响冷挤压压力的主要因素 ........................................164.2变形程度 ........................................................164.3冷挤压力的计算 ..................................................17 第5章冷挤压设备的选择 ............................................185.1冷挤压设备的基本要求 ............................................185.2冷挤压设备的选择 ................................................18 第6章冷挤压模具设计 ..............................................206.1冷挤压模具特点 ..................................................206.2冷挤压模架设计 ..................................................206.3凸、凹模设计 ....................................................216.3.1反挤压凸模的设计 (21)6.3.2反挤压凹模的设计 (23)6.3.3反挤压凸、凹模制造公差 (25)第7章模具结构部件设计 (26)7.1上模具部分结构设计 ..............................................267.2卸件装置设计 ....................................................27III7.3下模具部分结构设计 ..............................................297.4模具结构和工作原理 ..............................................307.5成形模具三维图 ................................ 错误~未定义书签。
挤压模说明书

课程设计
牌号XC111(L型)
制品的截面积F制=185.7mm2
.孔形在模子端面位置的确定
(由于本型材为等壁厚的型材,故型材的几何重心位于置模子的中心)几何中心的计算
如右图建立工件得坐标系:
2.选坯核选设备
焊合室的形状和大小对焊缝的质量有很大的影响。
有利于消除焊合室边缘与模孔平面之间的结合死区,在恰当的地方加倒圆角,可以采用大圆角R=5-
,上模舌芯工作带尺寸
模孔工作带长度g h 的确定
组合模的工作带应比一般结构的模子工作带长,并在入口方带有锥度,以改善焊缝质量。
由于本型材制品的对称性较好,外形相对较小,一㎜,本设计取mm h g 4=。
挤压模具设计说明书资料

二.总设计过程概论1.挤压工艺流程:铸锭加热→挤压→切压余→淬火→冷却→切头尾→切定尺→时效→表面处理→包装→出厂2.挤压工艺条件1)铸锭的加热温度6063铝的最高允许加热温度为550℃,下限温度为320℃,为了保证制品的组织,性能,挤压时锭坯的加热温度不宜过高,应尽量降低挤压温度2)挤压筒的加热温度模具的成分多为合金钢,由于导热性差,为避免产生热应力,挤压前挤压筒要预热,为保证挤压制品的质量,并且具有良好的挤压效应,挤压筒温度可取400℃~450℃。
3)挤压温度热挤压时,加热温度一般是合金熔点绝对温度的0.75~0.95倍,本设计挤压温度为450℃~500℃,挤压过程中温度控制在450℃左右4)挤压速度考虑金属与合金的可挤压性,制品质量要求及设备的能力限制,本设计的挤压速度取0.7~0.8m/s5)工模具的润滑因本设计采用热挤压,故不采用润滑6)模具模具应具有足够的耐高温疲劳强度和硬度,较高的耐回火性及耐热性,足够的韧性,低的膨胀系数和良好的导热性,可加工性,及经济性,本设计采用4Cr5MoSiV1作为模具的材料,热处理的硬度为HRC45~507)切压余根据所选的设备:500T,切压余厚为20mm;800T,切压余厚为25mm8)淬火本工艺过程中,制品挤出后可通过设置风扇对制品进行吹风来达到风淬的目的9)冷却直接露置在空气中冷却,达到自然时效的目的10)切头尾本工艺过程统一去头尾各300mm三.实心型材模设计1.所要设计的实心型材制品本制品的形状和尺寸如下图1牌号XC111(L 型)制品的截面积F 制=116.42mm模孔外接圆直径D 外=46.28mm 现有设备(如下表):设备吨位500T800T 1630T 挤压筒直径0D Φ95 Φ125 Φ187 挤压截面积0F 70851226627451锭坯尺寸ddD L Φ90x270/320Φ120X400/450Φ178X540/600/660冷床长26m 32m 44m 填充系数 1.114 1.085 1.104 压余厚20 25 30 最大挤压比97.4 8273.6加工范围最大外接圆直径Φ65 Φ95 Φ147挤一根最小制品断面积F 制min72 150 3722.选坯和选设备根据加工范围要求(F 制≥F 制min,及D 外≤D 外max )只有500T 的可用,按成才率最高的原则,进一步优化,计算列表序号0D d D (mm ) dL (mm ) 单重wd 填充系数K 填充后长度Le 压余厚hy (mm) 切压余后的有效长度Ld挤压比λ制品长L 制(m) 成品数nx6 (m) 成品重W 制(kg)成材率W 制/Wd (%)1 Φ95 Φ90 270 4.64 1.114 242 20 222 54.65 13.51 2×6m 3.8983.84%2 Φ95 Φ90 320 5.50 1.114 287 20 267 54.65 16.25 2×6m 3.8970.73%最后选择成才率最高的83.84%对应的方案 1 即:500T 的挤压机设备锭坯尺寸为:dd D L =Φ90X270mm λ=54.653.挤压力的计算根据经验系数公式:211.7750.8bD PDd, D 为挤压筒内径,d 为制品等面积直径,b为某温度下坯料的抗拉强度,450℃下6063的b≈12MPa带入数据求得:29511.7750.89512253.812.2PTF <额定吨位500T ,设备选择符合要求,即理论技术可行4.实心型材模具体结构设计模组的结构如下图图21.模子2.模垫3.前环4.后环5.保护垫板6.前机架7.模座8.模套9.剪刀 10.挤压筒模组的结构:对于不同吨位的挤压机,下图中的主要结构尺寸都是配套设置的,可以从有关资料中查得。
挤压模具设计(1)
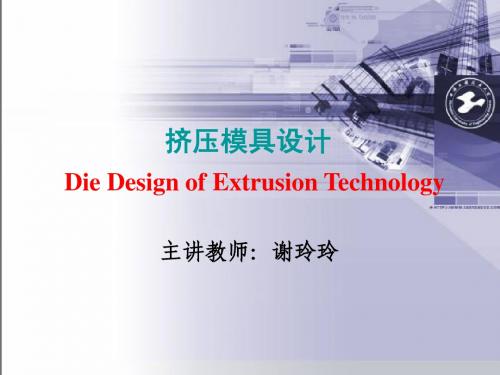
1.1铝合金型材分类
型材的分类编号,除了各个企业自行开发的 产品外,一般用“XC”代表型材。“XC”后面的 数字,按顺序分别代表类、目、组和序号。
如XC111-1,即为第1类、第1目、第1组中的 第1号型材。
1.1.1 型材“类”的划分
• XC711 XC722 XC731 XC747
边框型材 骨架型材
插角型材
联结型材
• XC754 XC7610
XC776 XC703
附件型材
散热型材
整体型材 空心型材
1.1.3 型材“组”的划分
在同一“目”中,按型材形状又分为组, 一个图形即为一组,依自然顺序排列。 如XC541、XC542、XC543等。
图1-4(1) 逐渐变断面型材品种举例
图1-4(2) 逐渐变断面型材品种举例
1.1铝合金型材分类
铝合金带筋整体壁板已成为一种专用型 材,主要用于航空航天、船舶、汽车、交通 运输、建筑等工业部门作为比强度高的结构 材料,可分为实心断面和空心断面两大类。
按形状壁板型材又可分为对称的、不对称的 壁板型材和直角形的、梯形的、丁字形的、 十字形的和异形的,参见图1—5。
第一小组的品种相当多,目前大约包括800个典 型规格。 第二小组型材的品种很少,目前不超过 50个典 型规格。
1.1铝合金型材分类
阶段变断面型材根据型材部分 ( 薄端 ) 的外形 可分为 T 字形的、工字形的、槽形的、带弯边槽 形的、 z 字形的和任意截面的型材,而大头部分 (厚端)的外形可能是各种各样的。 该种型材的特点是:大头端是一个整体,其横断 面积超过其型材部分横断面积的3—10倍, 大头部分长度通常为100—600mm。
铝型材挤压模具设计书
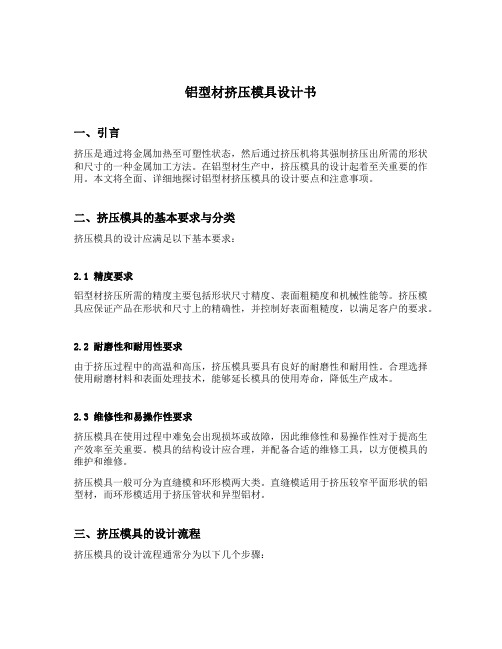
铝型材挤压模具设计书一、引言挤压是通过将金属加热至可塑性状态,然后通过挤压机将其强制挤压出所需的形状和尺寸的一种金属加工方法。
在铝型材生产中,挤压模具的设计起着至关重要的作用。
本文将全面、详细地探讨铝型材挤压模具的设计要点和注意事项。
二、挤压模具的基本要求与分类挤压模具的设计应满足以下基本要求:2.1 精度要求铝型材挤压所需的精度主要包括形状尺寸精度、表面粗糙度和机械性能等。
挤压模具应保证产品在形状和尺寸上的精确性,并控制好表面粗糙度,以满足客户的要求。
2.2 耐磨性和耐用性要求由于挤压过程中的高温和高压,挤压模具要具有良好的耐磨性和耐用性。
合理选择使用耐磨材料和表面处理技术,能够延长模具的使用寿命,降低生产成本。
2.3 维修性和易操作性要求挤压模具在使用过程中难免会出现损坏或故障,因此维修性和易操作性对于提高生产效率至关重要。
模具的结构设计应合理,并配备合适的维修工具,以方便模具的维护和维修。
挤压模具一般可分为直缝模和环形模两大类。
直缝模适用于挤压较窄平面形状的铝型材,而环形模适用于挤压管状和异型铝材。
三、挤压模具的设计流程挤压模具的设计流程通常分为以下几个步骤:3.1 铝型材挤压工艺分析在开始设计挤压模具之前,需要进行铝型材挤压工艺的分析。
包括材料的选择、预热温度的确定、挤压压力和速度的设定等。
3.2 模具结构设计模具结构设计是挤压模具设计的关键。
需要考虑挤压过程中的应力分布、热传导和冷却等因素,并确定模具的主要结构尺寸。
3.3 模具材料选择挤压模具的材料应具有良好的耐热性、耐磨性和冲击韧性。
常用的模具材料包括高速工具钢、合金工具钢和硬质合金等。
3.4 模具加热与冷却设计为了保证挤压过程的顺利进行,模具需要进行加热和冷却。
合理的加热和冷却设计能够提高铝型材的形状精度和表面质量。
四、挤压模具的制造和调试挤压模具的制造和调试过程中需要注意以下事项:4.1 制造工艺的选择根据不同模具的要求,选择合适的制造工艺,包括数控加工、热处理和表面处理等。
(数控模具设计)挤压模具设计书说明书
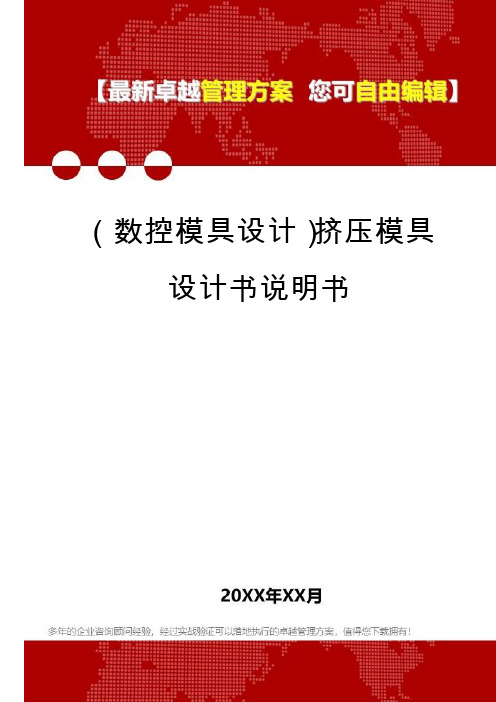
(数控模具设计)挤压模具设计书说明书铜合金压气缸的热挤压工艺及模具设计摘要铜合金压气缸的生产方法常见的有管料的切削加工,离心铸造后切削加工,热挤压法。
热挤压法生产材料利用率最高,生产效率最高,产品质量最高。
本文分析热挤压工艺及模具设计。
热挤压工艺分析综述:铜合金的热挤压温度根据经验可以定为730℃。
压气缸的毛坯件属于杯形件的一种,因此采用的是反挤压。
若采用一次挤压成形则所需挤压力和变形程度太大。
因此采用两次反挤压,第一次将棒料挤压成为杯形件,切削加工成空心圆柱形。
再经过第二次反挤压将内孔扩大,外径不变。
经过两次反挤压得到挤压件成形毛坯。
模具设计分析综述:两序挤压则需要两套挤压模具。
两套模具采用通用凹模,结构简单。
第一套模具凸模采用一般的反挤压凸模结构。
第二套模具需要有模芯结构,模芯可以是固定式的也可以是活动式的。
本次设计将模芯设计为固定式的即凸模和模芯一体式的。
设计成整体式的好处是结构简单,生产效率高。
与此同时,顶件器只需设计成中空的即可,当凸模压下时,模芯正好进入顶件器的内腔中。
关键词:反挤压,压气缸,模具设计,模芯C oppe r A ll o y C y li nde r P r e ss u r e o f H o t E x t r u s i onT e c hno l og y and D i e D e s i gnABSTRACTC oppe r a ll o y p r e ss u r e cy li nde r p r odu c t i on m e t hod s c o mm on p i pem a t e r i a l c u tt i ng p r o c e ss i ng,m a c h i n i ng a ft e r c en t r i f uga l c a s t i ng,ho t e x t r u s i on m e t hod.H o t e x t r u s i on m e t hod i s t he h i ghe s tu t ili z a t i on r a t e o f m a t e r i a l s,t he h i ghe s t p r odu c t i one ff i c i en cy,and t he h i ghe s t qua li t y o f p r odu c t.I n t h i s pape r,ho t e x t r u s i on t e c hno l og y and d i e de s i gn i s ana l ys ed.H o t e x t r u s i on t e c hno l og y ana l ys i s w e r e r e v i e w ed:C oppe r a ll o yc an be c l a ss i f i ed a s 730℃ho te x t r u s i on t e m pe r a t u r e a cc o r d i ng t ot he e x pe r i en c e.P r e ss u r e cy li nde r o f a b l an k pa r t s be l ong t o t he c up, s o t he ba ck w a r d e x t r u s i on i s u s ed.If u s i ng an e x t r u s i onf o r m i ng,t he needed e x t r u s i on and de f o r m a t i on deg r ee i s t oo l a r ge. s o t he ba ck w a r d e x t r u s i on s houd be u s ed t w i c e.T he f i r s t e x t r u s i onw ill m a k e t he ba r be c o m e t he c up,and t hen,m a k e t he c up be c o m et he ho ll o w cy li nd r i c a l b y m a c h i n i ng.A ft e r s e c ond ba ck w a r de x t r u s i on w ill en l a r ge t he i nne r ho l e,and t he ou t s i de d i a m e t e ri s c on s t an t.A ft e r t w i c e ba ck w a r d e x t r u s i on,w e c an ge t t he b l oo m.M o l d de s i gn ana l ys i s w e r e r e v i e w ed:T he t w o o r de r s quee z i ngr equ i r e s t w o s e t s o f e x t r u s i on d i e s T w o s e t s o f m ou l d adop tgene r a l c on c a v e d i e.T he f i r s t s e t o f m ou l d pun c h adop t s gene r a lba ck w a r d e x t r u s i on pun c h d i e s t r u c t u r e.A s e c ond s e t o f m ou l d need a m o l d c o r e s t r u c t u r e,m o l d c o r e c an be s t a t i ona r y o ra c t i v i t i e s.T h i s de s i gn w ill de s i gn f o r f i x ed t he pun c h m o l d c o r e and m o l d c o r e one-p i e c e.D e s i gn i n t o i n t eg r a l ad v an t age i s s i m p l e s t r u c t u r e,h i gh p r odu c t i on e ff i c i en cy a t t he s a m e t i m e,t opp i e c e s s i m p l y de s i gned t o be ho ll o w,w hen t he c on v e x m o l d,m o l dc o r e r i gh t i n t o t he l u m en o f t op p i e c e s.KEY W O RD S:ba ck w a r d e x t r u s i on, cy li nde r p r e ss u r e,m o l d de s i gn, m o l d c o r e目录前言 (1)第一章热挤压技术的介绍 (2)§1.1热挤压工艺的实质 (2)§1.2热挤压工艺的特点 (2)§1.3热挤压工艺的主要过程: (3)第二章工艺分析及制定 (4)§2.1产品零件分析 (4)§2.2挤压件图制定 (4)§2.3工艺方案分析 (5)§2.4毛坯形状及尺寸选择 (6)第三章坯料的处理 (8)§3.1坯料加热方法 (8)§3.2加热温度 (8)§3.3坯料润滑 (9)第四章变形量和挤压力 (11)§4.1影响挤压力主要因素 (11)§4.2变形程度 (12)§4.3挤压力 (12)§4.4热挤压设备选用原则 (13)§4.5热挤压设备选用 (14)第五章模具结构设计 (15)§5.1挤压模具设计的基本要求 (15)§5.2反挤压凸模的设计 (16)§5.3热反挤压凹模的设计 (17)§5.4热挤压凸模固定板的设计 (19)§5.5顶出装置的设计 (20)§5.6模具结构原理 (21)§5.7模具材料的选择 (22)结论 (25)参考文献 (26)致谢 (28)前言压气缸户外断路器中的关键零件,要求“三高”即高的导电率、高的硬度和高的强度,以降低能耗和提高产品的可靠性。
挤压模具设计
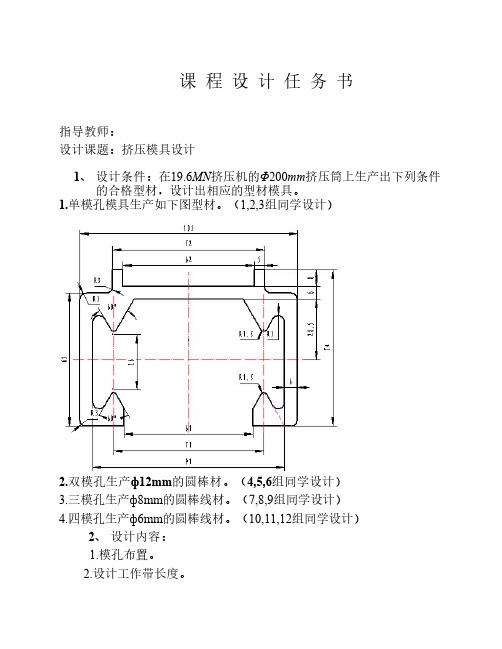
课程设计任务书指导教师:设计课题:挤压模具设计1、设计条件:在19.6MN挤压机的Φ200mm挤压筒上生产出下列条件的合格型材,设计出相应的型材模具。
1.单模孔模具生产如下图型材。
(1,2,3组同学设计)2.双模孔生产ф12mm的圆棒材。
(4,5,6组同学设计)3.三模孔生产ф8mm的圆棒线材。
(7,8,9组同学设计)4.四模孔生产ф6mm的圆棒线材。
(10,11,12组同学设计)2、设计内容:1.模孔布置。
2.设计工作带长度。
3.型材模孔尺寸设计。
4.模子强度校核。
5.画出模具图。
3、设计时间:2012年12月10日至12月14日4、设计地点:实验楼C楼501,5025、分组情况:组号学生安排情况型材金属种类10910121001----0910121012,0810121039,0810121114铜及其合金20910121013----0910121023,0810121027铝及其合金30910121026----0910121036镁及其合金40910121037----0910121048铜及其合金50910121049----0910121060铝及其合金60910121061----0910121072镁及其合金70910121073----0910121084铜及其合金80910121085----0910121096铝及其合金90910121097----0910121108镁及其合金100910121109----0910121120铜及其合金110910121121----0910121132铝及其合金120910121133----0910121140,0906131060,0906121043镁及其合金目录第一章概述 11.1 性能特点 11.2 应用领域 11.3 铝加工行业分布 11.4 铝合金挤压加工的现状与发展 11.5 铝合金未来挑战 2第二章挤压工艺设计 32.1挤压工艺流程: 32.2挤压工艺条件 32.3坯料尺寸计算 32.3.1锭坯直径计算 32.3.2锭坯长度的确定 42.3.3挤压比的计算 4第三章棒材热挤压模具设计 63.1所要设计的棒材制品 63.2棒材模模孔布置 63.3棒材模模孔尺寸的确定 83.4模具入口处圆角半径r 83.5棒材模模孔工作带长度的确定 83.6棒材模外形尺寸的确定 93.6.1模具外形D 93.6.2模具厚度H 93.6.3 模具的外形锥度 93.6.4 模具的出口带直径 103.7棒材模的强度校核 103.8双孔棒材模的主要数据 103.9 模具图 10总结 12参考文献 13第一章概述1.1 性能特点铝及铝合金具有一系列特性,在金属材料的应用中仅次于钢材而居第二位。
挤压模具设计课程设计
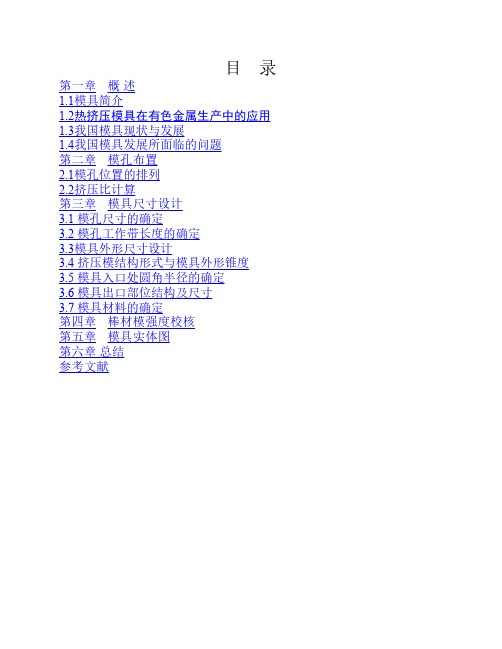
目录第一章概述1.1模具简介1.2热挤压模具在有色金属生产中的应用1.3我国模具现状与发展1.4我国模具发展所面临的问题第二章模孔布置2.1模孔位置的排列2.2挤压比计算第三章模具尺寸设计3.1 模孔尺寸的确定3.2 模孔工作带长度的确定3.3模具外形尺寸设计3.4 挤压模结构形式与模具外形锥度3.5 模具入口处圆角半径的确定3.6 模具出口部位结构及尺寸3.7 模具材料的确定第四章棒材模强度校核第五章模具实体图第六章总结参考文献第1章概述1.1模具简介模具,工业生产上用以注塑、吹塑、挤出、压铸或锻压成型、冶炼、冲压、拉伸等方法得到所需产品的各种模子和工具。
简而言之,模具是用来成型物品的工具,这种工具由各种零件构成,不同的模具由不同的零件构成。
他主要通过成型材料物理状态的改变来实现物品外形的加工。
模具是制造业的重要基础工艺装备,工业产品大批量生产和新产品开发都离不开模具,用模具生产制件所达到的(四高二低)高精度,高复杂程度,高一致性,高生产率和低耗能、低耗材,使模具工业在制造业中的地位越来越重要。
在中国人们已经越来越认识到模具技术水平的高低,已经成为衡量一个国家制造业的水平高低的重要标志,并在很大程度上决定着产品质量,效益和新产品的开发能力。
模具品种繁多,共有10大类,包括冲压、塑料、橡胶、铸造、锻压等,用于制造业中几乎所有产品的生产,可见模具的服务范围已包括国民经济的许多方面,现在模具技术已成为衡量一个国家产品制造水平的重要标志之一,没有高水平的模具就没有高水平的产品已成为共识。
随着产品更新换代越来越快,新产品不断涌现。
新技术日新月异,模具的使用范围已越来越广,对模具的要求也越来越高了。
1.2热挤压模具在有色金属生产中的应用在当代工业制品和生活制品中,有相当部分金属构件的成品或半成品是经过压力加工方法生产而得的。
采用模具加工成形金属构件,具有生产效率高,质量好,节省材料,成本低,以及规格灵活多变等特点,近几年来,在国民经济建设的各个领域中,得到了广泛的应用。
- 1、下载文档前请自行甄别文档内容的完整性,平台不提供额外的编辑、内容补充、找答案等附加服务。
- 2、"仅部分预览"的文档,不可在线预览部分如存在完整性等问题,可反馈申请退款(可完整预览的文档不适用该条件!)。
- 3、如文档侵犯您的权益,请联系客服反馈,我们会尽快为您处理(人工客服工作时间:9:00-18:30)。
5)工作带长度的确定
铝合金工作带一般最短可取2.5~3.0mm,最长可取8~10mm
由于是等壁厚型材,故工作带长度h定各处相等,本次设计取
h=4㎜,如下图:
6)阻碍角
由于h定≤10~15㎜,故不采用阻碍角
7)模子强度的校核
本设计为L型薄壁型材,故模子的强度校核可以忽略
8)画图,如下图:
四.空心型材模设计
表7
序号
D0
(F0)
Dd
(mm)
Ld
(mm)
单重wd
填充系数K
填充后长度Le
压余厚hy
(mm)
切压余后的有效长度Ld
挤压比
λ
制品长
L制
(m)
成品数
nx6
(m)
成品重
W制(kg)
成材率
W制/Wd
(%)
1
Φ125
120
400
12.20
1.085
369
25
344
50.9
17.5
2X6
7.84
64.2
2
Φ125
分流桥弯曲应力校核
Hmin=L√p/2*√[σb]
式中: Hmin=分流桥的最小高度
L分流桥宽度,经计算L=20.6
P挤压机的最大的比压
[σb]模具材料在温度下的许用应力.在450~500℃下,对于3Cr2W8V取[σb]=1000Pa
代入数据得
Hmin≈7.0
由于上模厚度H上=48>7.0
故符合要求
则 =2+0.2+0.1=2.3mm
型材的圆角及圆弧没有偏差要求,故可按名义尺寸设计
由于这种角材在挤压的过程中由并口现象,角度取91°
制造偏差为 mm,主要尺寸如下图
4)孔形在模子端面位置的确定
(由于本型材为等壁厚的型材,故型材的几何重心在置模子的中心)
压力中心的计算
(以左下端点为坐标原点)算得
x=8.47
1.所要设计的制品
本设计制品的的牌号为I513回型管
具体参数为
B=50.8 H=38.1 T=1.4重量:0.653Kg/m
具体如下图
图6
2.选坯核选设备
制品的截面积:F制=241mm2
模孔外接圆直径D外=63.5㎜
根据加工范围要求(F制≥F制min,及D外≤D外max)由表3知
只有800T的可用
按成才率最高的原则,在进一步计算优化,计算列表如下
9.上模凸台长取21mm.用于装配定位
10.定位销,螺钉按GB标准选取标准件
定位销的直径取Φ8,螺钉采用M10,具体说明见装配图
11.模子强度校核:
这种模子在工作时承受载荷最不利的情况是分流孔道和焊合室尚未进入金属和金属充满焊合室以后流出模孔之际,故强度的校核主要是争对模子的分流桥,模桥的弯曲应力和抗剪强度:
模组尺寸如下表
设备吨位
500T
800T
1630T
Φ1×Φ2×H
Φ160×Φ180×190
Φ210×Φ250×240
Φ310×Φ350×340
H1
20
30
30
H2
80~90
90~100
110~150
H3
50~60
50~60
60~80
挤压模具的尺寸如下表
设备吨位
500T
800T
1630T
Φd1/d2×h2
模子外形尺寸的确定(如下图)
依据表6的数据可以确定
d1=135㎜d2=145㎜h1=12㎜h2=25㎜
3)模子内形尺寸的确定
挤压比λ=54.65<λMAX,故不需要多孔挤压
确定模孔尺寸:由公式
外形尺寸 C为裕量系数△为尺寸公差
则A=30(1+0.0085)+0.6=30.855mm
壁后尺寸
=0.05-0.15薄壁取上限,后壁取下限,本设计取0.1
按经验公式:Φ95~130㎜h=10~15㎜
本设计取h=14,形状为碟形如图:
图11
6.模子内形尺寸的确定
工件及模具如图所示
图12
模具图如下
图13
按经验公式A=A0+K A0
A--制品外形的模孔尺寸
A0-制品外形的公称直径
K-经验系数,由于本设计争对6063合金,取K=0.012
得HK=38.1+0.5=38.6, BK=50.8+0.6=51.4
120
450
13.73
1.085
415
25
390
50.9
19.8
3X6
11.75
85.6
最后选择成才率最高的85.6%对应的方案2
即800T的挤压设备
锭坯尺寸为:Dd X Ld=Φ120X450mm
λ=50.90
3.挤压力的计算
根据经验系数公式
P=α*Kf(㏑λ+4υL/D)
F=A*P
α表征挤压难易程度的经验系数,对于空心型材取α=1.1~1.5,
F=164.6×∏×1252 /4=2.02MN
换算成吨位:约202T
F<额定吨位800T,设备选择符合要求,即所选设备理论可行
4.模组及模子外形尺寸确定:
模组尺寸结构简图如前图3所示
根据前面计算,从表6选取
H1=30 H2=100 H3=50
模子外形尺寸简图如前图4依据表6的数据可以确定
d1=165㎜d2=175㎜h1=12㎜h2=88㎜
制品型材壁厚可由经验公式B=B0+△确定
由于B0=1.4㎜.本设计△=0.1
故Tk=1.4+0.1=1.5㎜
7.模孔工作带长度hg的确定
由于本型材制品的对称性较好,外形相对较小,一般可取2~6㎜,生产实践中对铝合金常用6~15㎜
本设计取hg=6mm
8.模芯的设计
一般伸出下模工作带3-5mm,本设计取4mm,模腔外形按空心型材的空心部分确定。
考虑金属与合金的可挤压性,制品质量要求及设备的能力限制,本设计的挤压速度取0.7~0.8m/s
5)工模具的润滑
因本设计采用热挤压,故不采用润滑
6)模具
模具应具有足够的耐高温疲劳强度和硬度,较高的耐回火性及耐热性,足够的韧性,低的膨胀系数和良好的导热性,可加工性,及经济性,本设计采用4Cr5MoSiV1作为模具的材料,热处理的硬度为HRC45~50
1.114
287
20
267
54.65
16.25
2×6m
3.89
70.73%
最后选择成才率最高的83.84%对应的方案1
即:500T的挤压机设备
锭坯尺寸为: =Φ90X270mm
λ=54.653.挤Βιβλιοθήκη 力的计算根据经验系数公式:
,D为挤压筒内径,d为制品等面积直径, 为某温度下坯料的抗拉强度,450℃下6063的 ≈12MPa
Φ135/Φ145×20~25
Φ165/Φ175×25~30
Φ250/Φ260×30~40
h1
12
12~13
12~13
5.实心模尺寸数据设计
1).选坯和选择设备
根据前面的计算
挤压筒内直径 =95㎜锭坯尺寸: =Φ90×270
挤压比λ=54.65
2).模组及模子尺寸外形的计算
根据前面计算,从表5选取
H1=20H2=90H3=60
图1
牌号XC111(L型)
制品的截面积F制=116.4
模孔外接圆直径D外=46.28mm
现有设备(如下表):
设备吨位
500T
800T
1630T
挤压筒直径
Φ95
Φ125
Φ187
挤压截面积
7085
12266
27451
锭坯尺寸
Φ90x270/320
Φ120X400/450
Φ178X540/600/660
冷床长
带入数据求得:
F<额定吨位500T,设备选择符合要求,即理论技术可行
4.实心型材模具体结构设计
模组的结构如下图
图2
1.模子2.模垫3.前环4.后环5.保护垫板6.前机架7.模座
8.模套9.剪刀10.挤压筒
模组的结构:
对于不同吨位的挤压机,下图中的主要结构尺寸都是配套设置的,可以从有关资料中查得。模组的主要结构尺寸如图3
26m
32m
44m
填充系数
1.114
1.085
1.104
压余厚
20
25
30
最大挤压比
97.4
82
73.6
加工范围
最大外接圆直径
Φ65
Φ95
Φ147
挤一根最小制品断面积
F制min
72
150
372
2.选坯和选设备
根据加工范围要求(F制≥F制min,及D外≤D外max)只有500T的可用,按成才率最高的原则,进一步优化,计算列表
本设计取α=1.3
P――为单位挤压力,MPa
F――为最大挤压力, N
A――挤压筒内孔的面积,mm2
λ――挤压系数
Kf-――材料在挤压温度下的变形抗力(查表),MPa
υ――摩擦系数
L――铸锭敦粗后额长度,mm
Kf查表取16
υ取0.30
故P=1.3×16(㏑50.90+4×0.30×415/125)
=164.6MPa
7)切压余
根据所选的设备:500T,切压余厚为20mm;800T,切压余厚为25mm
8)淬火
本工艺过程中,制品挤出后可通过设置风扇对制品进行吹风来达到风淬的目的
9)冷却
直接露置在空气中冷却,达到自然时效的目的