半导体制造前道工艺
电子行业:半导体设备系列报告之一-全行业框架梳理

DONGXING SE CURITIE S行业研究电子行业:半导体设备系列报告之一——全行业框架梳理投资摘要:本报告为系列报告之开篇,是半导体设备行业框架性梳理,后续报告我们将分子领域进行详细论述和推荐。
本报告分为四节: 一、芯片制造过程中每种工艺使用不同设备芯片的制造过程可以分为前道工艺和后道工艺。
前道是指晶圆制造厂的加工过程,即在空白的硅片完成电路的加工;后道是指晶圆的切割、封装成品以及最终的测试过程。
前道工艺包括光刻、刻蚀、薄膜生长、离子注入、清洗、CMP 、量测等;后道工艺包括减薄、划片、装片、键合等封装工艺以及终端测试等。
二、半导体设备全球行业格局总述2020年全球半导体设备销售额约711亿美元,其中晶圆制造设备612亿美元,占比86.1%,测试设备60.1亿美元,占比8.5%,封装设备38.5亿美元,占比5.4%。
在晶圆制造设备中,光刻、刻蚀、薄膜生长设备占比最高,合计市场占比超过70%,这三类设备也是集成电路制造的主设备;工艺过程量测设备是质量监测的关键设备,占比可达13%;其他设备占比相对较小。
全球范围内的半导体设备龙头以美国、日本和欧洲公司为主,呈现寡头垄断,CR5市占率超过65%。
三、每一种半导体设备的市场格局各不相同分领域的全球格局来看,光刻机市场基本被阿斯麦公司垄断;刻蚀和薄膜生长市场主要被应用材料、泛林半导体和东京电子三家寡头占据;离子注入由应用材料和亚舍利占据大部分份额;科磊半导体则占据量测设备半壁江山;测试设备则有泰瑞达、爱德万和科休等寡头。
目前,几乎所有领域均有我国企业寻求突破,国产设备的空白正在被逐渐填补,但与国外龙头企业的技术差距仍然较大。
四、国产替代和市场份额提升是我国半导体设备企业的成长主线研发驱动、产业链全球化以及同下游晶圆厂深度绑定是半导体设备形成寡头垄断格局的主要原因。
为打破国外企业的垄断,一方面需要我国设备企业实现高效率和低成本的研发,另一方面需要下游晶圆厂的支持,这两个条件目前已经基本满足,因此我国设备厂商迎来重要的契机。
晶圆制造前道量检测工艺分类、特征、价值分析
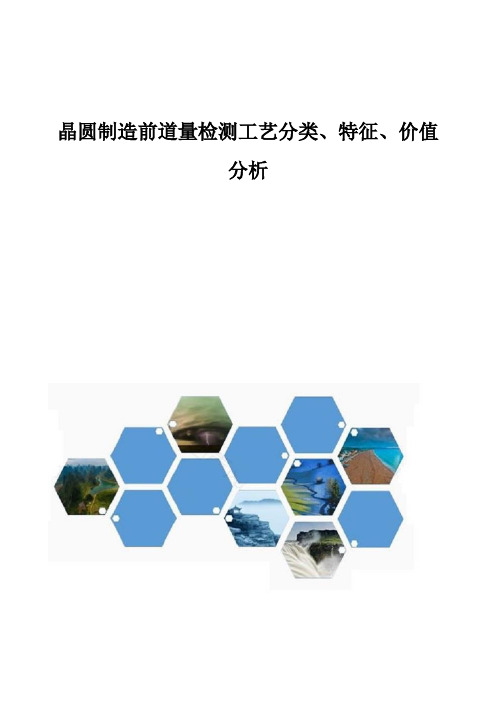
晶圆制造前道量检测工艺分类、特征、价值分析(一)前道量检测贯穿晶圆制造环节始终,是芯片生产线的“监督员”前道量检测使整条前道工艺产线的控制达到最佳化,同时也为追寻芯片生产中发现的问题提供了重要的追寻线索。
半导体芯片制造工艺步骤极多,各步骤之间可能会相互影响,因此很难根据最后出厂产品的检测结果准确分析出影响产品性能与合格率的具体原因。
而且如果不能在生产过程中及时检测到工艺缺陷,则此批次工艺中生产出来的大量不合格产品也会额外增加厂商的生产成本。
因此前道量检测贯穿芯片制造环节始终,对加工制造过程进行实时的监控,确保每一步加工后的产品均符合参数要求。
而且,产品小组可以通过分析前道量检测产生的检测数据及时发现问题根源,使之能够采取最有效的方式进行应对,从而制造出参数均匀、成品率高、可靠性强的芯片。
前道量检测根据测试目的可以细分为量测和检测。
量测主要是对芯片的薄膜厚度、关键尺寸、套准精度等制成尺寸和膜应力、掺杂浓度等材料性质进行测量,以确保其符合参数设计要求;而检测主要用于识别并定位产品表面存在的杂质颗粒沾污、机械划伤、晶圆图案缺陷等问题。
前道量检测分类及主要技术资料来源:公开资料前道量测、检测均会用到光学技术和电子束技术,但是两种技术在量测与检测下各具不同的特点。
光学量测通过分析光的反射、衍射光谱间接进行测量,其优点是速度快、分辨率高、非破坏性,但缺点是需借助其他技术进行辅助成像;电子束量测是根据电子扫描直接放大成像,其优点是可以直接成像进行测量,但缺点是速度慢、分辨率低,而且使用电子束进行成像量测操作时需要切割晶圆,(立鼎产业研究网)因此电子束量测具有破坏性。
光学检测是通过光信号对比发现晶圆上存在的缺陷,其优点是速度快,但缺点是无法呈现出缺陷的具体形貌;而电子束检测可以直接呈现缺陷的具体形貌,但是该方法在精度要求非常高的情况下会耗费大量的时间。
在实际的芯片制造过程中,光学技术与电子束技术常常被结合使用,比如检测环节一般先采用光学检测定位缺陷位置,再使用电子束检测对缺陷进行精确扫描成像,两种技术的结合使用可以提高量检测的效率,并降低对芯片的破坏性。
半导体前道制造工艺流程ppt

薄膜厚度的测量
总结词
薄膜厚度的测量是半导体前道制造工艺中非常重要的环节,对于产品的质量和稳 定性具有重要影响。
详细描述
薄膜厚度的测量一般采用光学测量方法,如椭圆偏振仪、干涉仪等。这些仪器利 用光的干涉原理来测量薄膜厚度,精度可达到纳米级别。在测量过程中,需要注 意薄膜的均匀性和稳定性,以避免对测量结果造成误差。
掺杂浓度的测量
总结词
掺杂浓度的测量是半导体前道制造工艺中的重要环节 ,对于产品的电学性能和质量具有重要影响。
详细描述
掺杂浓度的测量一般采用离子束分析(IBA)或二次离 子质谱(SIMS)等精密仪器。这些仪器通过分析薄膜 中的离子束或二次离子的数量和能量,来确定掺杂浓 度和分布情况。在测量过程中,需要注意仪器的精度 和稳定性,以避免对测量结果造成误差。
半导体前道制造工艺流程ppt
xx年xx月xx日
目 录
• 半导体前道制造工艺概述 • 半导体前道制造工艺流程 • 半导体前道制造工艺的设备 • 半导体前道制造工艺的检测与测量 • 半导体前道制造工艺的优化与发展趋势
01
半导体前道制造工艺概述
半导体前道制造工艺的定义
半导体前道制造工艺是指利用半导体材料和制程技术,将半 导体器件制作成集成电路的过程。
随着工艺节点缩小,技术难度和成本急剧 增加。
材料短缺
部分新型材料依赖进口,存在供应风险。
制造成本
工艺复杂度高,制造成本高。
良品率
工艺不稳定导致良品率低。
半导体前道制造工艺的未来发展
新工艺技术
研究和发展新的工艺技术,如新材 料、新结构、新器件等。
跨领域合作
加强与科研机构、高校的合作,推 动产学研一体化。
曝光设备
gouging半导体工艺
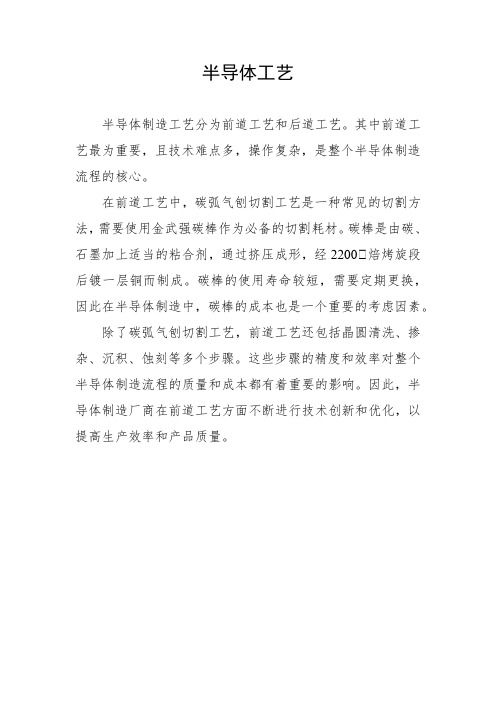
半导体工艺
半导体制造工艺分为前道工艺和后道工艺。
其中前道工艺最为重要,且技术难点多,操作复杂,是整个半导体制造流程的核心。
在前道工艺中,碳弧气刨切割工艺是一种常见的切割方法,需要使用金武强碳棒作为必备的切割耗材。
碳棒是由碳、石墨加上适当的粘合剂,通过挤压成形,经2200℃焙烤旋段后镀一层铜而制成。
碳棒的使用寿命较短,需要定期更换,因此在半导体制造中,碳棒的成本也是一个重要的考虑因素。
除了碳弧气刨切割工艺,前道工艺还包括晶圆清洗、掺杂、沉积、蚀刻等多个步骤。
这些步骤的精度和效率对整个半导体制造流程的质量和成本都有着重要的影响。
因此,半导体制造厂商在前道工艺方面不断进行技术创新和优化,以提高生产效率和产品质量。
半导体封装制程与设备材料知识介绍

24~32
Ceramic Plastic
2.54 mm (100miles)
Surface Mount
SOP Small Outline Package
QFP Quad-Flat
Pack
封裝型式
Shape
Typical Features
Material Lead Pitch No of I/O
Plastic
1.27 mm (50miles) 2 direction
lead
8 ~40
Plastic
1.0, 0.8, 0.65 mm 4 direction
lead
88~200
Surface Mount
FPG
Flat Package of Glass
LCC
Leadless Chip
Carrier
封裝型式
Shape
Tester
Digital
Credence
SC312
Digital
Teradyne
J750
Mix-Signal Credence
Quartet one and one+
Mix-Signal HP
HP93000 P600
Mix-Signal HP
HP93000 C400
Mix-Signal Teradyne
Die Attach (上片)
Deposition (沉积)
WireBonding (焊线)
Wafer Inspection (晶圆检查) 前段結束
Molding (塑封)
Laser mark (激光印字)
Laser Cut & package saw Testing
半导体前工程

P(或N)区 扩散
离子注入
《电子制造技术基础》课程作业-2016级电封班
流程示意
光刻掩膜版制作 电子束将绘制好的图案刻蚀在一系列 镀铬的玻璃板上,用于将电路图转移 到电路板上
晶圆表面Hale Waihona Puke 成一 层二氧化硅薄膜涂光刻胶
送入烘干设 备加热烘干 光刻胶
紫外线照射在光刻胶上成像
《电子制造技术基础》课程作业-2016级电封班
晶圆处理—化学气相沉积
利用化学反应,在反应室内让反应物(通常是气态)反 应生成固态生成沉积在晶体表面的一种薄膜沉积技术。 在电子制物,并造中,用于在晶圆上形成电路中的介电 材料。可以生成氮化硅、多晶硅等材料。
氮化硅薄膜
《电子制造技术基础》课程作业-2016级电封班
晶圆处理—氧化
二氧化硅薄膜
硅
在晶圆表面形成一层二氧化硅,用作器件的 保护层、钝化层、绝缘材料,另外,二氧化 硅对某些杂质能起到掩蔽作用,从而可以实 现选择扩散。 主要有热氧化法、干氧氧化法、水汽氧化法 及湿氧氧化法等。不同方法生成的氧化层厚 度不同,实际生产中根据具体要求选择
《电子制造技术基础》础》机械工业出版社 SILICON RUN 视频
《电子制造技术基础》课程作业-2016级电封班
旋转桶中的熔融 纯硅
生长好的单晶硅
晶圆切割
《电子制造技术基础》课程作业-2016级电封班
前工程主要工艺
晶圆处理
清洗
氧化
前道工序
化学气相沉 积 光刻 、蚀刻 扩散、离 子注入
晶圆针测筛选
《电子制造技术基础》课程作业-2016级电封班
晶圆处理—清洗
制作出的晶圆表面附着大约2um的 Al2O3和甘油混合液保护层,在制作前 必须进行表面清洗。 盐酸、硫酸、过氧化氢、氨水等用 来去除所有的有机物和金属污染物。
半导体全面分析:制造三大工艺,晶圆四大工艺!

半导体全⾯分析:制造三⼤⼯艺,晶圆四⼤⼯艺!技术:设计流程 100 亿个晶体管在指甲盖⼤⼩的地⽅组成电路,想想就头⽪发⿇!⼀个路⼝红绿灯设置不合理,就可能导致⼤⽚堵车,电⼦在芯⽚上跑来跑去,稍微有个 PN 结出问题,电⼦同样会堵车,所以芯⽚的设计异常重要 芯⽚制造的过程就如同⽤乐⾼盖房⼦⼀样,先有晶圆作为地基,再层层往上叠的芯⽚制造流程后,就可产出必要的芯⽚(后⾯会介绍),然⽽,没有设计图,拥有再强制造能⼒都没有⽤1. 规格制定在 IC 设计中,最重要的步骤就是规格制定,这个步骤就像是在设计建筑前,先决定要⼏间房间、浴室,有什么建筑法规需要遵守,在确定好所有的功能之后在进⾏设计,这样才不⽤再花额外的时间进⾏后续修改第⼀步:确定 IC 的⽬的、效能为何,对⼤⽅向做设定第⼆步:察看需要何种协议,否则芯⽚将⽆法和市⾯上的产品相容第三步:确⽴ IC 的实作⽅法,将不同功能分配成不同的单元,并确⽴不同单元间连结的⽅法,如此便完成规格的制定 2. 设计芯⽚细节这个步骤就像初步记下建筑的规画,将整体轮廓描绘出来,⽅便后续制图。
在 IC 芯⽚中,便是使⽤硬体描述语⾔(HDL)将电路描写出来。
常使⽤的 HDL 有Verilog、VHDL等,藉由程式码便可轻易地将⼀颗 IC 功能表达出来。
接着就是检查程式功能的正确性并持续修改,直到它满⾜期望的功能为⽌ 3. 设计蓝图在 IC 设计中,逻辑合成这个步骤便是将确定⽆误的 HDL code,放⼊电⼦设计⾃动化⼯具(EDA tool),让电脑将 HDL code 转换成逻辑电路,产⽣如下的电路图,之后,反复的确定此逻辑闸设计图是否符合规格并修改,直到功能正确为⽌ 4. 电路布局与绕线将合成完的程式码再放⼊另⼀套EDA tool,进⾏电路布局与绕线(Place And Route)。
在经过不断的检测后,便会形成如下的电路图。
图中可以看到蓝、红、绿、黄等不同颜⾊,每种不同的颜⾊就代表着⼀张光罩 ▲常⽤的演算芯⽚- FFT 芯⽚,完成电路布局与绕线的结果 5.光罩⼀颗IC 会产⽣多张的光罩,这些光罩有上下层的分别,每层有各⾃的任务。
半导体前道制造工艺流程

P+ N-epi P+ N-epi P+
N+-BL
N+-BL
P-SUB
涂胶—烘烤---掩膜(曝光)---显影---坚膜—蚀刻—清洗 —去膜--清洗—P+扩散(B)
第三次光刻—P型基区扩散孔
决定NPN管的基区扩散位置范围 SiO2
P
P
P+
P+ N-epi P+
N+-BL
N+-BL
P-SUB
去SiO2—氧化--涂胶—烘烤---掩膜(曝光)---显影---坚膜 —蚀刻—清洗—去膜—清洗—基区扩散(B)
• 5。光III---N管场区光刻,N管场区注入, 以提高场开启,减少闩锁效应及改善阱 的接触。
B+
光刻胶
P-
N-Si
CMOS集成电路工艺 --以P阱硅栅CMOS为例
• 6。光III---N管场区光刻,刻出N管场区 注入孔; N管场区注入。
P-
N-Si
CMOS集成电路工艺 --以P阱硅栅CMOS为例
第四次光刻—N+发射区扩散孔
• 集电极和N型电阻的接触孔,以及外延层的反偏孔。 • Al—N-Si 欧姆接触:ND≥1019cm-3,
P P+
N+-BL
N+
P+ NP-epi
P+
N+-BL
P-SUB
SiO2
去SiO2—氧化--涂胶—烘烤---掩膜(曝光)---显影---坚膜 —蚀刻—清洗—去膜—清洗—扩散
二、晶圆针测制程
• 经过Wafer Fab之制程後,晶圆上即形成 一格格的小格 ,我们称之为晶方或是晶粒 (Die),在一般情形下,同一片晶圆上 皆制作相同的晶片,但是也有可能在同一 片晶圆 上制作不同规格的产品;这些晶圆 必须通过晶片允收测试,晶粒将会一一经 过针测(Probe)仪器以测试其电气特性, 而不合格的的晶粒将会被标上记号(Ink Dot),此程序即 称之为晶圆针测制程 (Wafer Probe)。然後晶圆将依晶粒 为单位分割成一粒粒独立的晶粒
半导体前道设备行业研究

半导体前道设备行业研究1.半导体设备行业介绍1.1半导体生产过程中有哪些工艺步骤,需要用到哪些设备?集成电路系采用一定的工艺,把一个电路中所需的晶体管、电阻、电容和电感等元件及它们之间的连接导线全部制作在一小块半导体晶片如硅片或介质基片上,然后焊接封装在一个管壳内,成为具有所需电路功能的电子器件。
半导体设备在芯片制造中发挥着重要作用。
半导体设备是半导体制造的基石,是半导体行业的基础和核心。
半导体工艺流程主要包括硅片制造、IC设计、芯片制造和芯片封测,从产业链来看,半导体设备在硅片制造以及芯片制造的前道/后道工艺中均发挥着重要作用。
半导体生产过程中有哪些工艺步骤,需要用到哪些设备?前道晶圆制造工艺复杂,分别为氧化/扩散、光刻、刻蚀、离子注入、薄膜生长、抛光、金属化,清洗和检测是贯穿半导体制造的重要环节,简化来看,按照工艺次序可分为:氧化:在硅片表面形成二氧化硅层,由于二氧化硅硬度高且致密,可以保护晶圆表面不被划伤并且阻挡污染物。
涂胶:通过涂胶机在晶圆表面均匀涂覆光刻胶。
光刻:通过光刻曝光将设计好的电路图从掩膜版转移到晶圆表面。
显影:在显影机中利用显影剂去除被曝光的光刻胶,在光刻胶膜上显示出电路图形。
刻蚀:在刻蚀机中通过离子撞击去除多余的氧化层或其他薄膜层,将电路图形从光刻胶膜永久转移到晶圆表面。
离子注入:将掺杂剂材料射入晶圆表面(也可通过热扩散工艺实现)。
该步骤的主要目的是形成PN结,PN结是晶体管工作的基本结构。
(即利用PN结的导通和截止分别代表1和0)去胶:光刻胶仅作为转移电路图形的中介,最终并不在电路中发挥实际作用,因此需要通过去胶机去除。
薄膜沉积:前述操按照预定的电路图在相应位置形成了核心器件PN结,但这些结构是分立的,需要添加导电层实现互连(相当于电路中的导线),薄膜沉积操作可将金属层等结构添加在晶圆表面。
薄膜沉积也可以在晶圆表面添加绝缘介质或其他半导体,沉积好的薄膜将作为电路的功能材料层(类比3D打印)。
半导体制程简介

半导体制程简介半导体制程是指制造半导体器件所需的一系列工艺步骤和设备。
它是将材料转换为具有特定功能的半导体器件的过程,多数情况下是芯片制造的关键部分。
半导体制程通常分为六个主要步骤:前道工艺、IC 设计、曝光与衬底处理、薄膜沉积、刻蚀与清洗、以及后道工艺。
前道工艺是半导体制程的起始阶段。
在这个阶段,制造商会选择适合的衬底材料(通常是硅),并使用一系列的物理和化学方法准备它,以便于后续的加工。
IC 设计是将半导体器件的功能、结构和电路设计成电子文件的过程。
这些文件将被用于后续的曝光与衬底处理。
曝光与衬底处理是半导体制程的关键步骤之一。
在这个步骤中,使用光刻机将设计好的电子文件投射到光敏材料上,形成模式。
然后,通过化学方法去除暴露的材料,从而得到衬底上的所需结构。
这些步骤会多次重复,以逐渐形成多层结构。
在薄膜沉积阶段,使用化学蒸气沉积(CVD)或物理蒸镀(PVD)等方法将薄膜材料沉积到衬底上。
这些膜层将用于实现器件的不同功能,如导电层、绝缘层和隔离层等。
刻蚀与清洗是将多余的材料从衬底上去除的过程。
使用化学或物理方法,将不需要的材料刻蚀掉,并进行清洗和检查,确保器件的质量和一致性。
后道工艺是半导体制程的最后阶段。
在这个阶段中,制造商会进行结构和线路的连接,以及器件的测试和封装等。
这些步骤将半导体器件转换为实际可用的芯片。
半导体制程是一个复杂而精细的过程。
通过精确的控制和不断的优化,制造商可以获得高质量、高性能的半导体器件。
这些器件在现代技术中发挥着重要的作用,包括计算机、通信设备、消费电子产品等。
因此,半导体制程在推动科技进步和社会发展中扮演着重要的角色。
半导体制程在现代科技领域扮演着极为重要的角色。
随着信息技术的发展和人们对高性能电子设备的需求不断增长,半导体制程成为了现代社会的基石之一。
在这方面,特别值得一提的是摩尔定律。
摩尔定律是一种经验规律,它指出在相同面积上可以容纳的晶体管数量每隔大约18-24个月将翻一番,同时造价也会下降50%。
半导体封装生产线工艺流程分析
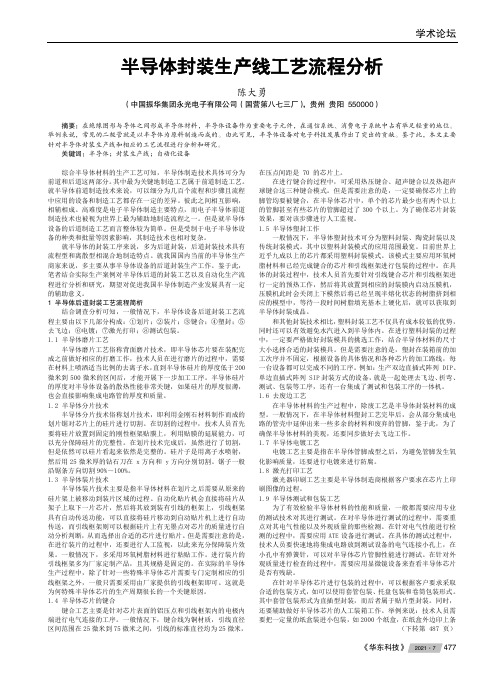
半导体封装生产线工艺流程分析陈大勇(中国振华集团永光电子有限公司(国营第八七三厂),贵州 贵阳 550000) 摘要:在绝缘图形与导体之间形成半导体材料,半导体设备作为重要电子元件,在通信系统、消费电子系统中占有举足轻重的地位。
举例来说,常见的二极管就是以半导体为原料制造而成的。
由此可见,半导体设备对电子科技发展作出了突出的贡献。
鉴于此,本文主要针对半导体封装生产线和相应的工艺流程进行分析和研究。
关键词:半导体;封装生产线;自动化设备综合半导体材料的生产工艺可知,半导体制造技术具体可分为前道和后道这两部分。
其中最为关键地制造工艺属于前道制造工艺。
就半导体前道制造技术来说,可以细分为几百个流程和步骤且流程中应用的设备和制造工艺都存在一定的差异。
彼此之间相互影响,相辅相成。
高难度是电子半导体制造主要特点,而电子半导体前道制造技术也被视为世界上最为辅助地制造流程之一。
但是就半导体设备的后道制造工艺而言整体较为简单。
但是受制于电子半导体设备的种类和批量等因素影响,其制造技术也相对复杂。
就半导体的封装工序来说,多为后道封装,后道封装技术具有流程型和离散型相混合地制造特点。
就我国国内当前的半导体生产商家来说,多主要从事半导体设备的后道封装生产工作。
鉴于此,笔者结合实际生产案例对半导体后道的封装工艺以及自动化生产流程进行分析和研究,期望对促进我国半导体制造产业发展具有一定的辅助意义。
1 半导体后道封装工艺流程简析结合调查分析可知,一般情况下,半导体设备后道封装工艺流程主要由以下几部分构成:①划片;②装片;③键合;④塑封;⑤去飞边;⑥电镀;⑦激光打印;⑧测试包装。
1.1 半导体磨片工艺半导体磨片工艺俗称背面磨片技术,即半导体芯片要在装配完成之前做好相应的打磨工作,技术人员在进行磨片的过程中,需要在材料上喷洒适当比例的去离子水,直到半导体硅片的厚度低于200微米到500微米的区间后,才能开展下一步加工工序。
半导体硅片的厚度对半导体设备的散热性能非常关键,如果硅片的厚度很薄,也会直接影响集成电路管的厚度和质量。
Wafer制程及IC封装制程

晶圆研磨
• 晶片从背面磨至适当厚度以配合产品结构和封装的需 求。
• 晶圆正面贴上UV tape,再以机械的方式对晶圆研背 面进行研磨,至所需之晶圆厚度,再以紫外线曝照胶 带,使其由晶圆正面剥离取出。
晶圆切割
晶圆安装
切割
晶Байду номын сангаас检查
上片准备
目的:将前段制程加工完成的晶圆上一颗颗晶粒切割
由于晶粒与晶粒之間距很小,而且晶粒又相当脆弱, 因此晶片切割机精度要求相当高,切割的过程中会产生很 多的小粉屑,因此在切割過程中必須不断地用纯水冲洗残 屑,以避免污染到晶粒。
化学气相沉积(CVD)
较为常见的的CVD薄膜有:二氧化硅、氮化硅、多晶硅耐火金属与这类 金属的硅化物
物理气相沉积(PVD)
电化学气相沉积
微影制程
• 原理:在晶片表面上覆上一层感光材料,透过光罩的图形,使晶片表 面的感光材料进行选择性的感光。
• 光学微影技术是一个图案化的制程,用紫外线把光罩设计好的图案转 印在涂布晶圆表面的光阻上。
Wafer制程
2、晶圆制造基本过程 垫底准备并涂上保护层 涂布光阻
光罩 光刻 去光阻
由於 IC 的電路是分多層製作在晶片上,故上述之流程會重複數次
磊晶
(1)晶圆清洗
移除粒子,有机物质,金属,及原生氧化层 避免晶片内电路形成短路或断路的现象
(2)磊晶
在晶圆经过适当的清洗后,送到热炉管内,在含氧的 环境中,以加热氧化的方式在晶圆表面形成一层SiO2层, 增强半导体晶片的工作效能。
总检
目的:在完成封裝动作后,尽管IC之前已通过前段晶圆针測,但为 了确保IC不因前述个封裝流程影响其原有功能,所以必须进行百分 之百的电性功能检验以避免客户拿到不良品。 最终测试(FT)主要是针对封装完成的半导体晶片,再次进行电性 功能测试及各类动作。
先进半导体器件前中后工艺流程

先进半导体器件前中后工艺流程
先进半导体器件的前、中、后工艺流程如下:
前工序(前道工艺):
1. 成膜淀积工艺:在晶圆上形成各种薄膜材料,包括导体、半导体和介质材料等。
这些薄膜材料由不同的元素和化合物组成,形成器件的关键结构。
2. 光刻工艺:在薄膜上形成图案并刻蚀,加工成确定形状。
光刻是半导体制造中的关键环节,通过光刻技术将设计好的电路图案转移到光敏材料上,然后进行刻蚀和剥离,形成电路图样。
3. 掺杂工艺:在半导体中掺入微量导电性杂质,以控制器件的电学性能,如导电类型、载流子浓度等。
掺杂工艺是实现半导体器件导电性能的关键步骤之一。
中工序(中道工艺):
1. 刻蚀工艺:将经过光刻和掺杂后的晶圆表面进行刻蚀,以形成各种半导体器件的结构和电路。
刻蚀工艺是实现器件微观结构的关键步骤之一。
2. 镀膜工艺:在器件表面镀上一层薄膜,以保护器件免受环境影响,提高器件的稳定性和可靠性。
镀膜工艺对于提高器件性能和延长使用寿命具有重要意义。
后工序(后道工艺):
1. 封装工艺:将制作好的芯片进行封装,以实现芯片与外部电路的连接和保护。
封装工艺是半导体制造中的重要环节,对于保证芯片的性能和可靠性具有重要意义。
2. 测试与可靠性验证:对封装好的芯片进行测试和可靠性验证,以确保其性能符合要求。
测试环节是保证芯片性能和可靠性的关键步骤之一。
以上是先进半导体器件的前、中、后工艺流程的简要介绍,每个环节都有其特定的作用和要求,只有严格控制每个环节的质量和工艺参数,才能制造出高性能、高可靠性的半导体器件。
半导体封装的基本定义和内涵 电子封装的工程的六个阶段

(Finish Goods)入库所组成。
半导体器件制作工艺分为前道和后道工序,晶圆制造和测试被称为前道(Front End)工序,而芯片的封装、测试及成品入库则被称为后道(Back End)工序,前道和后道一般在不同的工厂分开处理。
前道工序是从整块硅圆片入手经多次重复的制膜、氧化、扩散,包括照相制版和光刻等工序,制成三极管、集成电路等半导体元件及电极等,开发材料的电子功能,以实现所要求的元器件特性。
后道工序是从由硅圆片分切好的一个一个的芯片入手,进行装片、固定、键合联接、塑料灌封、引出接线端子、按印检查等工序,完成作为器件、部件的封装体,以确保元器件的可靠性,并便于与外电路联接。
1.半导体制造工艺和流程1.1晶圆制造晶圆制造主要是在晶圆上制作电路与镶嵌电子元件(如电晶体、电容、逻辑闸等),是所需技术最复杂且资金投入最多的过程。
以微处理器为例,其所需处理步骤可达数百道,而且所需加工机器先进且昂贵。
虽然详细的处理程序是随着产品种类和使用技术的变化而不断变化,但其基本处理步骤通常是晶圆先经过适当的清洗之后,接着进行氧化及沉积处理,最后进行微影、蚀刻及离子植入等反复步骤,最终完成晶圆上电路的加工与制作。
1.2 晶圆测试晶圆经过划片工艺后,表面上会形成一道一道小格,每个小格就是一个晶片或晶粒(Die),即一个独立的集成电路。
在一般情况下,一个晶圆上制作的晶片具有相同的规格,但是也有可能在同一个晶圆上制作规格等级不同的晶片。
晶圆测试要完成两个工作:一是对每一个晶片进行验收测试,通过针测仪器(Probe)检测每个晶片是否合格,不合格的晶片会被标上记号,以便在切割晶圆的时候将不合格晶片筛选出来;二是对每个晶片进行电气特性(如功率等)检测和分组,并作相应的区分标记。
1.3 芯片封装首先,将切割好的晶片用胶水贴装到框架衬垫(Substrate)上;其次,利用超细的金属导线或者导电性树脂将晶片的接合焊盘连接到框架衬垫的引脚,使晶片与外部电路相连,构成特定规格的集成电路芯片(Bin);最后对独立的芯片用塑料外壳加以封装保护,以保护芯片元件免受外力损坏。
半导体前道制造工艺流程

半导体前道制造工艺流程概述半导体前道制造工艺是半导体芯片制造的关键环节之一。
前道制造工艺主要包括晶圆制备、晶圆清洗、胶水涂覆、光刻、蚀刻、清洗等环节,其中光刻、蚀刻和清洗是半导体制造中最重要的三个环节。
本文将对半导体前道制造工艺流程进行详细介绍。
晶圆制备晶圆制备是半导体前道制造的第一步,主要是透过纯化的多晶硅棒,通过切片技术来制成直径300mm左右、厚度1mm左右的硅晶圆片。
硅晶圆必须满足超低的纯度和超高的均匀度要求,任何一点的杂质都可能导致晶体内部成分松散或者晶体内部的电性能变差,因此该环节质量一定。
此外,基于成本和工艺效率的考虑,一个硅晶圆可以同时切成数百个芯片,因此晶圆的一切制作、用途决策等均要在这基础上进行。
晶圆清洗晶圆清洗主要目的是除去制造晶圆时留下的切割油、抛光膏等均会导致晶圆表面污染、氧化等现象。
标准的晶圆清洗采用的是反离子注入喷鸟装置(RIE)来清洗。
在晶圆上喷洒液体,然后用空气来冲洗表面。
在RIE里,使用了一种叫作“离子捕捉粒子”的技术,这种技术能够把尺寸更小的粒子与晶圆分离。
这样,就能够让晶圆更加干净,从而确保制造出来的芯片更加的稳定可靠。
胶水及光刻晶圆上的各种半导体器件主要是通过在晶圆上形成不同形状的光刻胶图案来实现的。
制作光刻胶图案的过程中,需要先将涂在晶圆表面的光刻胶附着在晶圆表面上,然后使用一个称作突出光的元件,将晶圆暴露在紫外线下,从而形成所需要的光刻胶图案。
使用的光刻胶方案、光刻设备等都需要在实践中大量的经验积累。
蚀刻和清洗半导体芯片中的不同部件通过在晶圆片上形成结构来完成,比如,制作芯片的隧道势垒二极管的过程就包括光刻、蚀刻、清洗三个环节。
通常来说,蚀刻工艺会使用一个称作刻蚀液的溶液来进行。
这种溶液通常由几十种不同化学药物的混合物组成,以精细控制相应的腐蚀反应。
如果蚀刻时间过长,晶圆上的光刻胶可能被烧掉或者被溶解掉,导致芯片在制造过程中失效。
而蚀刻时间过短,则可能会导致芯片结构精度的损失。
半导体工艺流程
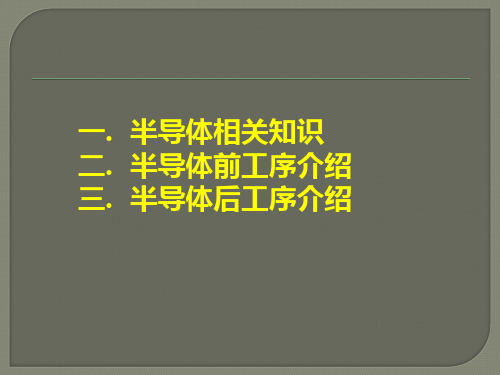
20世纪50年代: 晶体管技术 20世纪60年代: 工艺技术 20世纪70年代: 竞争 20世纪80年代: 自动化 20世纪90年代: 批量生产
21世纪: 器件进入规模时代和智能时代
前道工序(Front End)制程 晶圆处理制程(Wafer Fabrication;
简称 Wafer Fab) 管芯中测(Wafer Probe);
2000
50mm 100mm 125mm 150mm 200mm
300mm
2′ 4′
5′ 6′
8′
12′
在国内也不是很普及。
不同尺寸的硅片—从开始生产 —到生产高峰 — 再到逐步淘汰的生命周期
100mm 1975年
150mm 19831年4年
200mm 1987年
300mm 20年 1995年
10年 1984年 9年 20年
是为了制作电路的保护层,避免电路受到机械 性划伤或高温破坏。也有不做封装就使用的。
从环境、用途、成本考虑。 用户市场的需求
MOS型
双极型
PMOS型 NMOS型 CMOS型
饱和型
非饱和型
BiCMOS TTL IIL ECL/CML
一 双极型工艺: A 在每个器件间要做隔离区(PN结隔离、全介质隔
离及PN结、介质混合隔离) ECL (非饱和型) (不掺金) 、TTL/DTL (饱和 型) 、STTL (饱和型) B 在元器件间自然隔离 IIL(饱和型)
超净间:洁净等级主要由 灰尘颗粒数/m3
0.1µm 1级 35 10 级 350 100级 NA 1000级 NA
0.2µm 0.3µm 7.5 3 75 30 750 300 NA NA
半导体制造前道工艺

文档仅供参考,如有不当之处,请联系改正。
文档仅供参考,如有不当之处,请联系改正。
文档仅供参考,如有不当之处,请联系改正。
蚀刻
• 一般所指蚀刻也称光化学蚀刻,指经过曝 光制版、显影后,将要蚀刻区域旳保护膜 清除,在蚀刻时接触化学溶液,到达溶解 腐蚀旳作用,形成凹凸或者镂空成型旳效 果。(选择性刻蚀转移光刻胶上旳IC设计 图形到晶圆表面)
• 硅片清洗烘干(用于降低污染物,降低缺陷,使光刻 胶更轻易粘附。)
• 涂底 • 旋转涂胶*(利用离心力) • 软烘(清除圆片表面旳潮气,增长粘附性) • 边沿光刻胶旳清除 • 对准* • 曝光*(接触、接近、投影、步进) • 后烘(平衡驻波效应,提升辨别率。) • 显影* • 硬烘(提升刻蚀和注入旳抵抗力,提升粘附性)
• 氧化:使硅片表面形成氧化膜。主 要措施有热氧化法及气相成长法。 (绝缘、保护等作用)
• 化学气相沉积:反应物质在气态条 件下发生化学反应,生成固态物质 沉积在加热旳固态基体表面,进而 制得固体材料旳工艺技术。
文档仅供参考,如有不当之处,请联系改正。
光刻加工
• 光刻是一种利用类似于照片洗印旳原 理经过曝光和选择性化学腐蚀将掩膜 版上旳集成电路印制到硅片上旳精密 表面加工技术。
文档仅供参考,如有不当之处,请联系改正。
晶圆处理工序
• 本工序主要是经过清洗、氧化、 化学气相沉积、涂膜、曝光、显 影、蚀刻、离子植入、金属溅镀 等反复环节在晶圆上制作电路及 电子元件,最终在晶圆上完毕数 层电路及元件加工与制作。
文档仅供参考,如有不当之处,请联系改正。
• 清洗:用特殊旳清洗机和不同旳清 洗剂进行多道清洗。用于降低污染 物。
文档仅供参考,如有不当之处,请联系改正。
半导体前道制造工艺流程
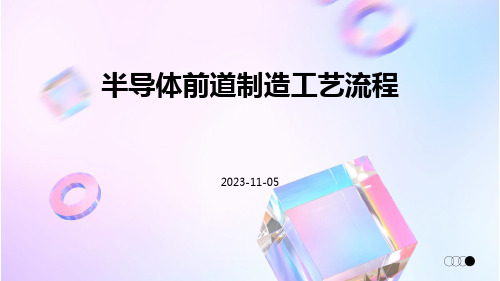
详细描述:半导体前道制造工艺流程中,各种原材料的 质量和稳定性对产品性能有着重要影响。材料问题可能 导致产品性能下降、良品率降低等问题。
1. 严格把控原材料质量:建立严格的原材料质量标准 和检验程序,确保进厂原材料符合要求。
3. 与可靠的供应商合作:选择具有良好信誉和稳定质 量的供应商,确保原材料的稳定供应和质量保障。
02
半导体前道制造主要工艺 流程
氧化过程
设备
氧化炉、尾气处理装置等。
方法
干法氧化、湿法氧化。
目的
提高硅片表面的氧化层,增加薄膜的附着 力和稳定性,同时减少杂质离子影响。
影响因素
温度、湿度、氧气流量等。
光刻过程
设备
光刻机、涂胶/显影机等。
方法
涂胶、曝光、显影。
目的
将设计好的电路图案转移到硅片表 面,以实现电路结构的精确刻画。
03
解决方法:为解决工艺偏差问题,可以采取以下措施
工艺偏差及解决方法
1. 强化工艺控制
通过实时监控关键工艺参数,确保工艺过程的一致性和稳定性。
2. 引入自动化和智能化设备
利用先进的设备和技术,提高工艺控制精度和效率。
3. 定期进行工艺验证和审计
通过验证和审计,发现并纠正工艺偏差,确保工艺过程的可靠性 。
设备故障及解决方法
总结词:设备故障
详细描述:半导体前道制造工艺流程中,各种高精度的设备在长时间运行过程中可能会出现故障,如机械部件磨损、电路故障 等。这些故障可能导致生产停滞、影响产品质量等问题。
设备故障及解决方法
解决方法
为解决设备故障问题,可以采取以下措施
2. 安装监控系统
通过安装传感器和监控系统,实时监测设 备的运行状态,及时发现并处理故障。
半导体制造主要设备及工艺流程

半导体制造主要设备及⼯艺流程半导体产品的加⼯过程主要包括晶圆制造(前道,Front-End)和封装(后道,Back-End)测试,随着先进封装技术的渗透,出现介于晶圆制造和封装之间的加⼯环节,称为中道(Middle-End)。
由于半导体产品的加⼯⼯序多,所以在制造过程中需要⼤量的半导体设备和材料。
⼀、晶圆制造在这⾥,我们以最为复杂的晶圆制造(前道)和传统封装(后道)⼯艺为例,说明制造过程的所需要的设备和材料。
晶圆⽣产线可以分成7个独⽴的⽣产区域:扩散(Thermal Process)、光刻(Photo- lithography)、刻蚀(Etch)、离⼦注⼊(Ion Implant)、薄膜⽣长(Dielectric Deposition)、抛光(CMP)、⾦属化(Metalization)。
这7个主要的⽣产区和相关步骤以及测量等都是晶圆洁净⼚房进⾏的。
在这⼏个⽣产区都放置有若⼲种半导体设备,满⾜不同的需要。
例如在光刻区,除了光刻机之外,还会有配套的涂胶/显影和测量设备。
传统封装(后道)测试⼯艺可以⼤致分为背⾯减薄、晶圆切割、贴⽚、引线键合、模塑、电镀、切筋/成型和终测等8个主要步骤。
与IC晶圆制造(前道)相⽐,后道封装相对简单,技术难度较低,对⼯艺环境、设备和材料的要求远低于晶圆制造。
三、半导体⼯艺解析半导体制造⼯艺是集成电路实现的⼿段,也是集成电路设计的基础。
⾃从1948年晶体管发明以来,半导体器件⼯艺技术的发展经历了三个主要阶段:1950年采⽤合⾦法⼯艺,第⼀次⽣产出了实⽤化的合⾦结三极管;1955年扩散技术的采⽤是半导体器件制造技术的重⼤发展,为制造⾼频器件开辟了新途径;1960年平⾯⼯艺和外延技术的出现是半导体制造技术的重⼤变⾰,不但⼤幅度地提⾼了器件的频率、功率特性,改善了器件的稳定性和可靠性,⽽且也使半导体集成电路的⼯业化批量⽣产得以成为现实。
⽬前平⾯⼯艺仍然是半导体器件和集成电路⽣产的主流⼯艺。
- 1、下载文档前请自行甄别文档内容的完整性,平台不提供额外的编辑、内容补充、找答案等附加服务。
- 2、"仅部分预览"的文档,不可在线预览部分如存在完整性等问题,可反馈申请退款(可完整预览的文档不适用该条件!)。
- 3、如文档侵犯您的权益,请联系客服反馈,我们会尽快为您处理(人工客服工作时间:9:00-18:30)。
离子注入
• 用离子束去撞击固态物体。固态物 体会对离子束的运动产生阻碍,使 其最终留在固体中,这一现象就是 离子注入。(掺杂、真空、低温、加 速)
晶元针测
• 经过上道工序后,晶圆上就形成了 一个个的晶粒,然后用针测仪对每 个晶粒检测其性能,将不合格的晶 粒标上记号。之后再把将晶圆切开, 分割成一颗颗单独的晶粒,再按其 电气特性分类,保留合格的晶粒, 舍弃不合格的晶粒。
清洗
预烘和底膜涂覆
蚀刻
• 通常所指蚀刻也称光化学蚀刻,指通过曝 光制版、显影后,将要蚀刻区域的保护膜 去除,在蚀刻时接触化学溶液,达到溶解 腐蚀的作用,形成凹凸或者镂空成型的效 果。(选择性刻蚀转移光刻胶上的IC设计 图形到晶圆表面) • 干法蚀刻 • 湿法蚀刻( HNO3-HF-H2O(HAC) )
光刻加工
• 光刻是一种利用类似于照片洗印的原 理通过曝光和选择性化学腐蚀将掩膜 版上的集成电路印制到硅片上的精密 表面加工技术。
• • • • • • • • • • 硅片清洗烘干(用于减少污染物,减少缺陷,使光刻 胶更容易粘附。) 涂底 旋转涂胶*(利用离心力) 软烘(去除圆片表面的潮气,增加粘附性) 边缘光刻胶的去除应,提高分辨率。) 显影* 硬烘(提高刻蚀和注入的抵抗力,提高粘附性)
半导体制造前道工艺
谢梓建
Attention
• 在参考资料的时候,有的步骤 或是工艺在不同资料里面的说 法有点出入,所以本PPT可能 有很多不对的地方,希望大家 多多指正。
晶圆处理
清洗 氧化
前道工序
化学气相沉 积 晶圆针测 制作 光刻
蚀刻
晶圆
晶圆是指硅半导体集成电路制作所 用的硅晶片,由于其形状为圆形, 故称为晶圆;在硅晶片上可加工制 作成各种电路元件结构,而成为有 特定电性功能之IC产品。晶圆的原 始材料是硅,而地壳表面有用之不 竭的二氧化硅。二氧化硅矿石经由 电弧炉提炼,盐酸氯化,并经蒸馏 后,制成了高纯度的多晶硅,其纯 度高达99.999999999%。
晶圆处理工序
• 本工序主要是通过清洗、氧化、 化学气相沉积、涂膜、曝光、显 影、蚀刻、离子植入、金属溅镀 等反复步骤在晶圆上制作电路及 电子元件,最终在晶圆上完成数 层电路及元件加工与制作。
• 清洗:用特殊的清洗机和不同的清 洗剂进行多道清洗。用于减少污染 物。 • 氧化:使硅片表面形成氧化膜。主 要方法有热氧化法及气相成长法。 (绝缘、保护等作用) • 化学气相沉积:反应物质在气态条 件下发生化学反应,生成固态物质 沉积在加热的固态基体表面,进而 制得固体材料的工艺技术。