焊接裂纹产生及预防
焊接裂纹产生原因及防治措施

以下为焊接裂纹产生原因及防治措施,一起来看看吧。
1、焊接裂纹的现象在焊缝或近缝区,由于焊接的影响,材料的原子结合遭到破坏,形成新的界面而产生的缝隙称为焊接裂缝,它具有缺口尖锐和长宽比大的特征。
按产生时的温度和时间的不同,裂纹可分为:热裂纹、冷裂纹、应力腐蚀裂纹和层状撕裂。
在焊接生产中,裂纹产生的部位有很多。
有的裂纹出现在焊缝表面,肉眼就能观察到;有的隐藏在焊缝内部,通过探伤检查才能发现;有的产生在焊缝上;有的则产生在热影响区内。
值得注意的是,裂纹有时在焊接过程中产生,有时在焊件焊后放置或运行一段时间之后才出现,后一种称为延迟裂纹,这种裂纹的危害性更为严重。
2、焊接裂纹的危害焊接裂缝是一种危害大的缺陷,除了降低焊接接头的承载能力,还因裂缝末端的尖锐缺口将引起严重的应力集中,促使裂缝扩展,最终会导致焊接结构的破坏,使产品报废,甚至会引起严重的事故。
通常,在焊接接头中,裂缝是一种不允许存在的缺陷。
一旦发现即应彻底清除,进行返修焊接。
3、焊接裂纹的产生原因及防治措施由于不同裂缝的产生原因和形成机理不同,下面就热裂缝、冷裂缝和再热裂缝三类分别予以讨论。
3.1、热裂纹热裂缝一般是指高温下(从凝固温度范围附近至铁碳平衡图上的A3线以上温度)所产生的裂纹,又称高温裂缝或结晶裂缝。
热裂缝通常在焊缝内产生,有时也可能出现在热影响区。
原因:由于焊接熔池在结晶过程中存在着偏析现象,低熔点共晶和杂质在结晶过程中以液态间层存在形成偏析,凝固以后强度也较低,当焊接应力足够大时,就会将液态间层或刚凝固不久的固态金属拉开形成裂缝。
此外,如果母材的晶界上也存在有低熔点共晶和杂质,则在加热温度超过其熔点的热影响区,这些低熔点化合物将熔化而形成液态间层,当焊接拉应力足够大时,也会被拉开而形成热影响区液化裂缝。
总之,热裂缝的产生是冶金因素和力学因素综合作用的结果。
防治措施:防止产生热裂缝的措施,可以从冶金因素和力学因素两个方面入手。
控制母材及焊材有害元素、杂质含量限制母材及焊接材料(包括焊条、焊丝、焊剂和保护气体)中易偏析元素及有害杂质的含量。
焊接冷裂纹产生原因及防止措施
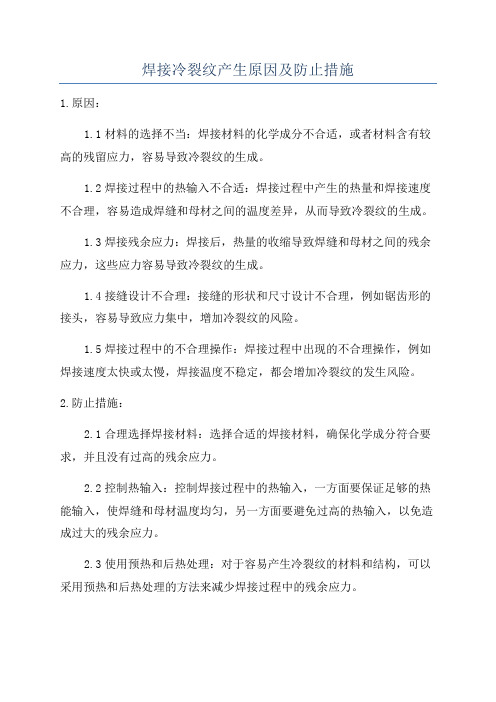
焊接冷裂纹产生原因及防止措施1.原因:1.1材料的选择不当:焊接材料的化学成分不合适,或者材料含有较高的残留应力,容易导致冷裂纹的生成。
1.2焊接过程中的热输入不合适:焊接过程中产生的热量和焊接速度不合理,容易造成焊缝和母材之间的温度差异,从而导致冷裂纹的生成。
1.3焊接残余应力:焊接后,热量的收缩导致焊缝和母材之间的残余应力,这些应力容易导致冷裂纹的生成。
1.4接缝设计不合理:接缝的形状和尺寸设计不合理,例如锯齿形的接头,容易导致应力集中,增加冷裂纹的风险。
1.5焊接过程中的不合理操作:焊接过程中出现的不合理操作,例如焊接速度太快或太慢,焊接温度不稳定,都会增加冷裂纹的发生风险。
2.防止措施:2.1合理选择焊接材料:选择合适的焊接材料,确保化学成分符合要求,并且没有过高的残余应力。
2.2控制热输入:控制焊接过程中的热输入,一方面要保证足够的热能输入,使焊缝和母材温度均匀,另一方面要避免过高的热输入,以免造成过大的残余应力。
2.3使用预热和后热处理:对于容易产生冷裂纹的材料和结构,可以采用预热和后热处理的方法来减少焊接过程中的残余应力。
2.4设计合理的焊缝:在设计焊缝时,应尽量避免锯齿形的接头,可以采用圆弧形或其他形状,以减少应力集中。
2.5严格控制焊接过程参数:焊接过程中应严格控制焊接速度、焊接压力和焊接温度等参数,确保稳定和合理的焊接条件。
2.6检测和治理裂纹:焊接后应对焊缝进行严格的裂纹检测,如超声波检测、磁粉检测等,一旦发现裂纹,应及时采取治理措施,包括打磨、退火或重新焊接等。
2.7人员培训和操作规范:通过人员培训,提高焊接人员的技术水平和操作规范,减少不合理操作的发生,从而减少冷裂纹的产生。
总结起来,焊接冷裂纹的产生主要是由材料的选择不当、焊接过程中的热输入不合适、焊接残余应力、接缝设计不合理和焊接过程中的不合理操作等原因造成的。
为了防止焊接冷裂纹的产生,应选择合适的焊接材料、控制热输入、使用预热和后热处理、设计合理的焊缝、严格控制焊接过程参数、检测和治理裂纹,并加强人员培训和操作规范。
碳钢焊接裂纹产生的原因及预防措施
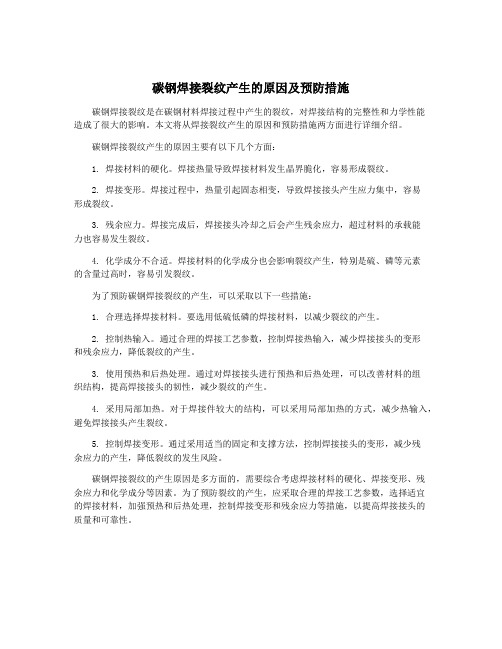
碳钢焊接裂纹产生的原因及预防措施碳钢焊接裂纹是在碳钢材料焊接过程中产生的裂纹,对焊接结构的完整性和力学性能造成了很大的影响。
本文将从焊接裂纹产生的原因和预防措施两方面进行详细介绍。
碳钢焊接裂纹产生的原因主要有以下几个方面:1. 焊接材料的硬化。
焊接热量导致焊接材料发生晶界脆化,容易形成裂纹。
2. 焊接变形。
焊接过程中,热量引起固态相变,导致焊接接头产生应力集中,容易形成裂纹。
3. 残余应力。
焊接完成后,焊接接头冷却之后会产生残余应力,超过材料的承载能力也容易发生裂纹。
4. 化学成分不合适。
焊接材料的化学成分也会影响裂纹产生,特别是硫、磷等元素的含量过高时,容易引发裂纹。
为了预防碳钢焊接裂纹的产生,可以采取以下一些措施:1. 合理选择焊接材料。
要选用低硫低磷的焊接材料,以减少裂纹的产生。
2. 控制热输入。
通过合理的焊接工艺参数,控制焊接热输入,减少焊接接头的变形和残余应力,降低裂纹的产生。
3. 使用预热和后热处理。
通过对焊接接头进行预热和后热处理,可以改善材料的组织结构,提高焊接接头的韧性,减少裂纹的产生。
4. 采用局部加热。
对于焊接件较大的结构,可以采用局部加热的方式,减少热输入,避免焊接接头产生裂纹。
5. 控制焊接变形。
通过采用适当的固定和支撑方法,控制焊接接头的变形,减少残余应力的产生,降低裂纹的发生风险。
碳钢焊接裂纹的产生原因是多方面的,需要综合考虑焊接材料的硬化、焊接变形、残余应力和化学成分等因素。
为了预防裂纹的产生,应采取合理的焊接工艺参数,选择适宜的焊接材料,加强预热和后热处理,控制焊接变形和残余应力等措施,以提高焊接接头的质量和可靠性。
焊接热裂纹的产生原因及防止方法

一、热裂纹产生的原因分析1、焊缝中杂质和拉应力的存在因为焊缝中的杂质在焊缝结晶过程中会形成低熔点结晶。
原因是低熔点共晶物的存在.结晶时被推挤到晶界上,形成液态薄膜,凝固收缩时焊缝金属在拉应力作用下,液态薄膜承受不了拉应力而形成裂纹。
热裂纹就轻易在焊缝金属中产生.所以要控制焊缝金属杂质的含量,减少低熔点共晶物的天生。
同时由此可见结晶裂纹的产生是低熔点共晶体和焊接拉应力共同作用的结果,二者缺一不可。
低熔点共晶体是产生结晶裂纹的内因,焊接拉应力是产生结晶裂纹的外因。
2、焊缝终端部位温度的变化埋弧焊焊接时,当焊接热源靠近纵焊缝的终端部位时,焊缝端部正常的温度场将发生变化,越靠近终端其变化越大.由于引弧板的尺寸远比筒体小,其热容量也小得多,而熄弧板与筒体之间只靠定位焊连接,故可视为大部门不连续.所以终端焊缝部位的传热前提是很差的,致使该部位局部温度升高,熔池外形发生变化,熔深也将随之变大,同时熔池在高温下停留的时间也变长,熔池凝固的速度变慢,尤其当熄弧板尺寸过小、熄弧板与筒体之间的定位焊缝过短、过薄时更为明显. 焊缝外形对结晶裂纹的形成有显著的影响。
熔宽与熔深比小易形成裂纹,熔宽与熔深比大抗结晶裂纹性较高。
3、焊接线能量的影响因为埋弧焊所采用的焊接热输入量往往比其他焊接方法要大得多,焊接线能量的大小直接影响到焊缝的成形,而焊缝的成形外形又直接决定着焊缝凝固后的晶粒分布和低熔点共晶体的存在位置及受力情况,因而对结晶裂纹产生与否影响较大。
另外,焊缝的横向收缩量远比间隙的张开量要小,使终端部位的横向拉伸力比其他焊接方法要大.这对开坡口的中厚板和不开坡口的较薄板尤为明显.4、其他情况如存在强制装配,装配质量不符合要求.二、焊缝裂纹的性质及特点终端裂纹形成的部位有时为终端,有时为距终端四周地区150mm范围内,有时为表面裂纹,有时为内部裂纹,而大多数情况是发生在终端四周的内部裂纹.裂纹与焊缝的波纹线相垂直,露在焊缝表面的有显著的锯齿外形。
碳钢焊接裂纹产生的原因及预防措施

碳钢焊接裂纹产生的原因及预防措施碳钢焊接是工程行业常见的一种焊接方式,但在实际操作中,碳钢焊接裂纹的产生是一个比较常见的问题。
裂纹不仅会影响焊接件的整体质量,还会导致安全隐患,因此我们有必要对碳钢焊接裂纹的产生原因进行深入了解,并采取相应的预防措施,以最大程度地避免碳钢焊接裂纹的产生。
碳钢焊接裂纹产生的原因:1. 焊接残余应力:在焊接过程中,焊接区域产生了残余应力,这些残余应力会使焊缝区域发生形变,从而导致裂纹的产生。
2. 焊接材料内部结构缺陷:碳钢焊接材料本身存在内部结构缺陷,比如夹杂物、气孔等,这些缺陷会成为裂纹的起始点,导致裂纹进一步扩展。
3. 焊接温度过高或过低:焊接温度过高会导致焊接材料过热,从而引发晶界腐蚀和变形;而焊接温度过低则会使焊接材料发生脆化,增加了裂纹的产生风险。
4. 焊接残余氢元素:在焊接过程中,如果残余氢元素过多,会导致焊接区域发生氢脆,进而引发裂纹的产生。
5. 焊接速度不均匀:焊接速度不均匀会导致焊接区域产生温度梯度,从而引发焊接残余应力,增加了裂纹的产生风险。
碳钢焊接裂纹的预防措施:1. 合理控制焊接残余应力:采用合适的焊接工艺参数,减小焊接残余应力,比如采用低氢电极焊接,采用后继焊接对残余应力进行消除等。
2. 做好焊接材料预处理工作:在焊接前,对焊接材料进行预处理,包括除去氧化膜、清除油污等,以减少内部结构缺陷的存在。
3. 控制焊接温度:采用适当的焊接温度,避免焊接温度过高或过低,减少焊接材料的脆化风险。
4. 降低残余氢含量:采用低氢电极、预热焊接材料、热后处理等措施,降低焊接区域的残余氢含量。
5. 均匀控制焊接速度:控制焊接速度的均匀性,减小温度梯度,避免焊接残余应力的产生。
碳钢焊接裂纹的产生原因主要包括焊接残余应力、焊接材料内部结构缺陷、焊接温度过高或过低、焊接残余氢元素和焊接速度不均匀等因素。
为了预防碳钢焊接裂纹的产生,我们应该采取合理控制焊接残余应力、做好焊接材料预处理、控制焊接温度、降低残余氢含量和均匀控制焊接速度等措施。
焊接产生裂纹的原因

焊接产生裂纹的原因焊接是一种常见的金属连接方法,它通常用于制造和维修工业部件。
然而,焊接过程中经常会出现裂纹,对焊接接头的强度和可靠性产生负面影响。
本文将探讨焊接产生裂纹的原因,并提供一些预防措施和解决方法。
1. 温度梯度引起的热应力焊接过程中,焊接区域会受到局部加热和快速冷却的影响,导致温度梯度的存在。
这种温度梯度会引起金属的热应力,使焊接接头产生裂纹。
解决方法:•控制焊接过程中的局部预热和退火,使温度梯度减小。
•使用预热设备在焊接区域加热,使温度分布更均匀。
•合理选择焊接电流和速度,避免出现过大的温度梯度。
2. 结构应力引起的裂纹焊接接头通常会承受结构应力,如拉伸、挤压或弯曲力。
由于焊接引起的组织和性能变化,焊接接头在受到结构应力时容易产生裂纹。
解决方法:•选择合适的焊接方法和焊接接头结构,减少结构应力对焊接接头的影响。
•优化焊接参数,使焊接接头的强度与结构应力相匹配。
•进行后焊热处理,提高焊接接头的强度和韧性。
3. 金属材料的选择和准备焊接材料的选择和准备对焊接接头的质量有重要影响。
不同材料的熔点、热膨胀系数和焊接性能不同,可能导致焊接接头产生裂纹。
解决方法:•选择合适的焊接材料,使其熔点和热膨胀系数与基材相匹配。
•对焊接材料进行预处理,去除氧化物和杂质,提高焊接接头的强度和韧性。
•使用合适的焊接方法和技术,确保焊接材料在焊接过程中融合良好。
4. 不适当的焊接参数和工艺焊接参数和工艺的选择对焊接接头的质量和裂纹的形成有重要影响。
过高或过低的焊接电流、电压、焊接速度和功率都可能导致焊接接头产生裂纹。
解决方法:•根据焊接材料的特性和焊接要求,选择合适的焊接参数。
•进行焊接试验和质量控制,确保焊接接头达到预期的质量要求。
•遵循正确的焊接工艺和操作规程,保证焊接接头的质量和强度。
5. 应力集中和裂纹敏感区域焊接接头通常存在着应力集中和裂纹敏感区域,这些区域容易产生裂纹。
焊接过程中的热收缩和组织变化可能导致焊接接头的应力集中和裂纹敏感性增加。
碳钢焊接裂纹产生的原因及预防措施

碳钢焊接裂纹产生的原因及预防措施【摘要】碳钢焊接裂纹产生的原因主要包括残余应力过大、焊接工艺不当和材料选择不当。
为了预防碳钢焊接裂纹的产生,可以采取控制残余应力、优化焊接工艺和选择合适的材料等措施。
综合考虑并采取相应的预防措施,才能有效避免裂纹的产生。
碳钢焊接裂纹的产生是由多种因素共同作用引起的,只有综合考虑并采取相应的预防措施,才能有效避免裂纹的产生。
【关键词】碳钢焊接、裂纹产生原因、预防措施、残余应力、焊接工艺、材料选择、控制、优化、合适材料、综合考虑、预防措施效果、避免裂纹。
1. 引言1.1 碳钢焊接裂纹产生的原因及预防措施碳钢焊接裂纹是在焊接过程中常见的缺陷之一,其产生原因复杂多样。
主要包括残余应力过大、焊接工艺不当、材料选择不当等因素。
在焊接完成后,焊接区域内会有残余应力存在,如果这些应力超过了材料的承受范围,就容易导致裂纹的产生。
焊接工艺的选择和执行对于裂纹的产生也有很大的影响。
如焊接电流过大或过小、焊接速度不恰当等都会导致焊接区域受到过大的应力而产生裂纹。
选择不当的材料也会导致碳钢焊接裂纹的产生,例如材料强度不匹配或者选用了易焊接但容易开裂的材料。
为了预防碳钢焊接裂纹的产生,我们可以采取一些措施。
首先是控制残余应力,可以通过热后处理等方法来降低焊接区域的残余应力。
其次是优化焊接工艺,确保焊接参数的选择合理,以及焊接过程中的操作规范。
最后是选择合适的材料,确保材料的强度和焊接性能符合要求,避免出现材料选择不当导致的裂纹问题。
碳钢焊接裂纹的产生是由多种因素共同作用引起的。
只有综合考虑并采取相应的预防措施,才能有效避免裂纹的产生。
有效的预防措施可以保障碳钢焊接的质量和安全。
2. 正文2.1 碳钢焊接裂纹产生的原因碳钢焊接裂纹产生的原因主要包括残余应力过大、焊接工艺不当和材料选择不当。
残余应力过大是碳钢焊接裂纹产生的主要原因之一。
在焊接过程中,因为固相变化和组织结构发生变化而产生的残余应力会导致材料的微观结构发生变化,从而使焊缝区出现应力集中,最终导致裂纹的产生。
碳钢焊接裂纹产生的原因及预防措施
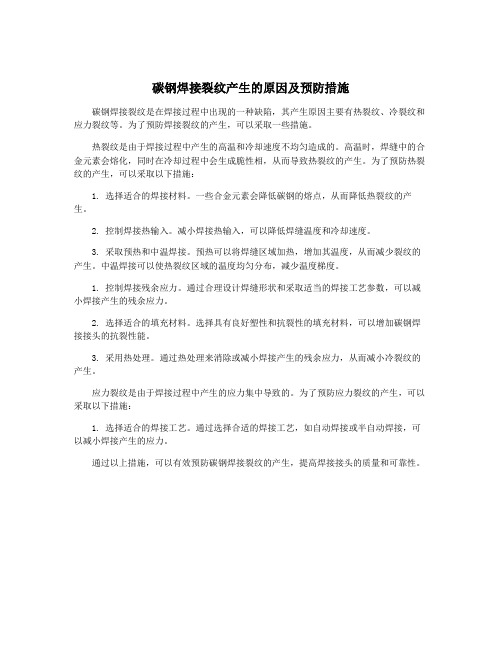
碳钢焊接裂纹产生的原因及预防措施
碳钢焊接裂纹是在焊接过程中出现的一种缺陷,其产生原因主要有热裂纹、冷裂纹和应力裂纹等。
为了预防焊接裂纹的产生,可以采取一些措施。
热裂纹是由于焊接过程中产生的高温和冷却速度不均匀造成的。
高温时,焊缝中的合金元素会熔化,同时在冷却过程中会生成脆性相,从而导致热裂纹的产生。
为了预防热裂纹的产生,可以采取以下措施:
1. 选择适合的焊接材料。
一些合金元素会降低碳钢的熔点,从而降低热裂纹的产生。
2. 控制焊接热输入。
减小焊接热输入,可以降低焊缝温度和冷却速度。
3. 采取预热和中温焊接。
预热可以将焊缝区域加热,增加其温度,从而减少裂纹的产生。
中温焊接可以使热裂纹区域的温度均匀分布,减少温度梯度。
1. 控制焊接残余应力。
通过合理设计焊缝形状和采取适当的焊接工艺参数,可以减小焊接产生的残余应力。
2. 选择适合的填充材料。
选择具有良好塑性和抗裂性的填充材料,可以增加碳钢焊接接头的抗裂性能。
3. 采用热处理。
通过热处理来消除或减小焊接产生的残余应力,从而减小冷裂纹的产生。
应力裂纹是由于焊接过程中产生的应力集中导致的。
为了预防应力裂纹的产生,可以采取以下措施:
1. 选择适合的焊接工艺。
通过选择合适的焊接工艺,如自动焊接或半自动焊接,可以减小焊接产生的应力。
通过以上措施,可以有效预防碳钢焊接裂纹的产生,提高焊接接头的质量和可靠性。
焊接裂纹成因分析及其防治措施

焊接裂纹成因分析及其防治措施1、焊接裂纹的现象在焊缝或近缝区,由于焊接的影响,材料的原子结合遭到破坏,形成新的界面而产生的缝隙称为焊接裂缝,它具有缺口尖锐和长宽比大的特征。
按产生时的温度和时间的不同,裂纹可分为:热裂纹、冷裂纹、应力腐蚀裂纹和层状撕裂。
在焊接生产中,裂纹产生的部位有很多。
有的裂纹出现在焊缝表面,肉眼就能观察到;有的隐藏在焊缝内部,通过探伤检查才能发现;有的产生在焊缝上;有的则产生在热影响区内。
值得注意的是,裂纹有时在焊接过程中产生,有时在焊件焊后放置或运行一段时间之后才出现,后一种称为延迟裂纹,这种裂纹的危害性更为严重。
常见裂纹的发生部位与型态如下图所示。
常见裂纹的发生部位与型态2、焊接裂纹的危害焊接裂缝是一种危害最大的缺陷,除了降低焊接接头的承载能力,还因裂缝末端的尖锐缺口将引起严重的应力集中,促使裂缝扩展,最终会导致焊接结构的破坏,使产品报废,甚至会引起严重的事故。
通常,在焊接接头中,裂缝是一种不允许存在的缺陷。
一旦发现即应彻底清除,进行返修焊接。
3、焊接裂纹的产生原因及防治措施由于不同裂缝的产生原因和形成机理不同,下面就热裂缝、冷裂缝和再热裂缝三类分别予以讨论3.1、热裂纹热裂缝一般是指高温下(从凝固温度范围附近至铁碳平衡图上的A3线以上温度)如下图所示所产生的裂纹,又称高温裂缝或结晶裂缝。
热裂缝通常在焊缝内产生,有时也可能出现在热影响区,如图所示。
原因:由于焊接熔池在结晶过程中存在着偏析现象,低熔点共晶和杂质在结晶过程中以液态间层存在形成偏析,凝固以后强度也较低,当焊接应力足够大时,就会将液态间层或刚凝固不久的固态金属拉开形成裂缝。
此外,如果母材的晶界上也存在有低熔点共晶和杂质,则在加热温度超过其熔点的热影响区,这些低熔点化合物将熔化而形成液态间层,当焊接拉应力足够大时,也会被拉开而形成热影响区液化裂缝。
总之,热裂缝的产生是冶金因素和力学因素综合作用的结果。
防治措施:防止产生热裂缝的措施,可以从冶金因素和力学因素两个方面入手。
焊接裂纹的产生及防止措施
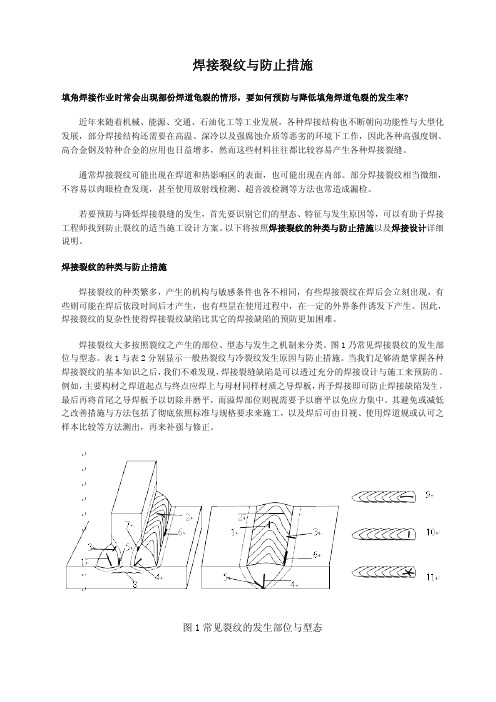
焊接裂纹与防止措施填角焊接作业时常会出现部份焊道龟裂的情形,要如何预防与降低填角焊道龟裂的发生率?近年来随着机械、能源、交通、石油化工等工业发展,各种焊接结构也不断朝向功能性与大型化发展,部分焊接结构还需要在高温、深冷以及强腐蚀介质等恶劣的环境下工作,因此各种高强度钢、高合金钢及特种合金的应用也日益增多,然而这些材料往往都比较容易产生各种焊接裂缝。
通常焊接裂纹可能出现在焊道和热影响区的表面,也可能出现在内部。
部分焊接裂纹相当微细,不容易以肉眼检查发现,甚至使用放射线检测、超音波检测等方法也常造成漏检。
若要预防与降低焊接裂缝的发生,首先要识别它们的型态、特征与发生原因等,可以有助于焊接工程师找到防止裂纹的适当施工设计方案。
以下将按照焊接裂纹的种类与防止措施以及焊接设计详细说明。
焊接裂纹的种类与防止措施焊接裂纹的种类繁多,产生的机构与敏感条件也各不相同,有些焊接裂纹在焊后会立刻出现,有些则可能在焊后依段时间后才产生,也有些昰在使用过程中,在一定的外界条件诱发下产生。
因此,焊接裂纹的复杂性使得焊接裂纹缺陷比其它的焊接缺陷的预防更加困难。
焊接裂纹大多按照裂纹之产生的部位、型态与发生之机制来分类。
图1乃常见焊接裂纹的发生部位与型态。
表1与表2分别显示一般热裂纹与冷裂纹发生原因与防止措施。
当我们足够清楚掌握各种焊接裂纹的基本知识之后,我们不难发现,焊接裂缝缺陷是可以透过充分的焊接设计与施工来预防的。
例如,主要构材之焊道起点与终点应焊上与母材同样材质之导焊板,再予焊接即可防止焊接缺陷发生,最后再将首尾之导焊板予以切除并磨平,而溢焊部位则视需要予以磨平以免应力集中。
其避免或减低之改善措施与方法包括了彻底依照标准与规格要求来施工,以及焊后可由目视、使用焊道规或认可之样本比较等方法测出,再来补强与修正。
图1常见裂纹的发生部位与型态表1常见热裂纹发生原因与防止措施表2常见热裂纹发生原因与防止措施适当之焊接设计焊接设计应考虑母材之可焊性、焊材与母材之匹配、焊接效率、焊接方式、焊道尺寸、焊接变形及接合板挫屈等因素。
焊接裂纹的形成机理与预防措施

焊接裂纹的形成机理与预防措施1、产生焊接冷裂纹的原因焊接冷裂纹在焊后较低的温度下形成。
由于这种裂纹形成与氢有关,且有延迟开裂的特点,因此又称之为焊接氢致裂纹或者延迟裂纹。
产生焊接冷裂纹的三个必要条件:〔1〕氢。
氢的主要来源是焊材中的水分和焊接区域中的油污、铁锈、水以及大气中的水汽等。
这些水、铁锈或者有机物经焊接电弧的高温热作用分解成氢原子而进入焊接熔池中。
在焊接过程中氢除向大气中扩散外,余下的在焊缝中呈过饱和状态,即在焊缝中存在着扩散氢。
根据氢脆理论,这种扩散氢将向应变集中区〔如微裂纹或者缺口尖端附近〕扩散,当该区的氢浓度到达某一临界值时,裂纹便继续扩展。
〔2〕应力。
依据目前国及国际的施工水平,在球罐的组装过程中总会存在或者多或者少的强力组对,所以在组装完成后便存在着应力,这种应力在焊后整体热处理完成后也不可能彻底消除。
再加之球罐焊接是一个局部加热过程,在焊接过程中产生应力与应变的循环,因此球罐焊接后必然存在剩余应力。
〔3〕组织。
焊接热影响区组织中过硬的马氏体含量越多越容易产生冷裂纹。
3、防止产生焊接冷裂纹的措施〔1〕尽量选用对冷裂纹不敏感的材料选用在质量好的母材。
即选用碳当量低的优质钢材,特别是防止母材大型夹渣。
所以在球壳板创造前必须对板材进展严格的超声波检查,对有严重夹层等缺陷的钢材不得使用。
〔2〕尽量减少氢的来源。
第一,球罐的焊接选用低氢型焊条,必要时要采用超低氢型的焊条;第二,焊条使用前一定要按产品使用说明发展烘干,并贮存在100~150℃的恒温箱中,在使用时放入保温筒并随用随取,在保温筒存放时间不得超过4h,否那末要按原烘干温度重新烘干,重复烘干不得超过两次;第三,要彻底去除焊接坡口外表及坡口两侧20mm围的油污、水分,、铁锈及其他杂物;第四,不在雨雪天及空气相对湿度大于90%时施焊;第五,采取有效的防风措施,以防止吹弧,使焊接熔池得到有效的隔离保护。
〔3〕选用适当的焊前预热温度和预热围。
焊接裂纹产生原因及防治措施

焊接裂纹产生原因及防治措施焊接裂纹是指在焊接过程中,焊缝或焊接接头出现的裂纹现象。
焊接裂纹的产生原因有很多,主要包括材料选择不当、焊接工艺参数不合理、应力集中、焊接变形等因素。
为了防止焊接裂纹的产生,需采取相应的防治措施。
一、材料选择不当是造成焊接裂纹的主要原因之一。
不同材料的热膨胀系数、熔点和强度等性质差异较大,若选择不当,会导致焊接时产生较大的残余应力,从而引发焊接裂纹。
因此,在焊接前应对材料进行仔细选择,确保焊接材料的相容性和相似性。
二、焊接工艺参数不合理也是引起焊接裂纹的重要原因。
焊接过程中,焊接电流、电压、速度等参数的选择不当,容易造成焊接热输入过大或过小,从而导致焊接裂纹的产生。
因此,需要根据焊接材料的厚度、形状和焊接位置等因素,合理调整焊接工艺参数,以减少焊接残余应力的产生。
三、应力集中也是焊接裂纹的重要原因之一。
焊接过程中,由于材料的热膨胀和收缩不均匀,会导致焊接接头处应力集中,从而造成焊接裂纹的产生。
为了减少应力集中,可以采取适当的预热和后热处理措施,使焊接接头的温度均匀分布,减少残余应力的产生。
四、焊接变形也是引起焊接裂纹的常见原因。
焊接过程中,由于热膨胀和收缩的影响,焊接接头会发生一定的变形,如果变形过大,就会产生焊接裂纹。
为了控制焊接变形,可以采用适当的夹具和焊接顺序,使焊接接头得到良好的约束,减少变形的发生。
为了预防焊接裂纹的产生,可以采取以下防治措施:1.合理选择焊接材料,确保材料具有相似的熔点和热膨胀系数,减少焊接时的残余应力。
2.合理调整焊接工艺参数,根据焊接材料的特性和焊接位置,确定合适的焊接电流、电压和速度等参数,以减少焊接热输入和残余应力。
3.采取适当的预热和后热处理措施,使焊接接头的温度均匀分布,减少应力集中和残余应力的产生。
4.采用适当的夹具和焊接顺序,控制焊接变形,减少焊接裂纹的发生。
5.进行焊接前的材料表面处理,确保焊接接头的清洁度和表面质量,减少焊接缺陷的产生。
薄板焊接裂纹产生原因及防治措施
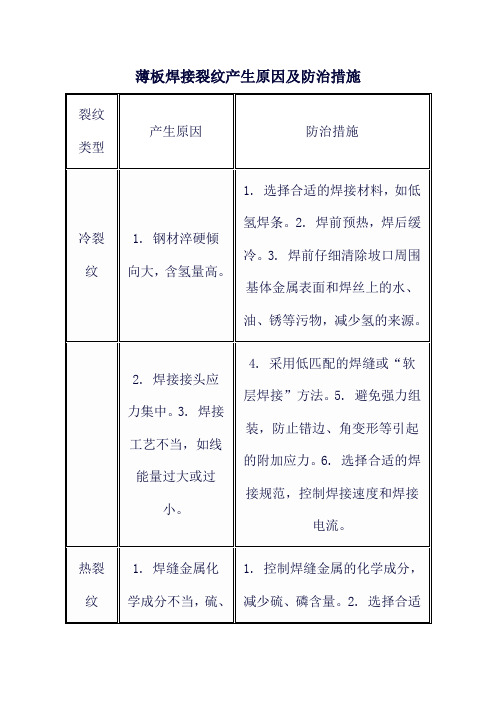
4. 选择合理的焊接次序和方向,减少焊接应力。5. 采用碱性焊条,提高焊缝的韧性。
再热裂纹
1. 钢材含有沉淀强化元素,如Cr、Mo、V等。2. 焊接后热处理过程中析出沉淀硬化相。
1. 控制基体金属的化学成分,减少沉淀强化元素的含量。2. 改善粗晶区的组织,减少马氏体组织。3. 减少焊接接头的应力集中,降低残余应力。
薄板焊接裂纹产生原因及防治措施
裂纹类型
产生原因
防治
1. 选择合适的焊接材料,如低氢焊条。2. 焊前预热,焊后缓冷。3. 焊前仔细清除坡口周围基体金属表面和焊丝上的水、油、锈等污物,减少氢的来源。
2. 焊接接头应力集中。3. 焊接工艺不当,如线能量过大或过小。
层状撕裂
1. 金属材料中含有较多的非金属夹杂物。2. 厚板角焊时产生较大的Z向拉伸应力。
1. 选用具有抗层状撕裂能力的钢材。2. 在接头设计和焊接施工中采取措施降低Z向应力和应力集中。3. 改进焊接工艺,如采用多层多道焊等。
4. 采用低匹配的焊缝或“软层焊接”方法。5. 避免强力组装,防止错边、角变形等引起的附加应力。6. 选择合适的焊接规范,控制焊接速度和焊接电流。
热裂纹
1. 焊缝金属化学成分不当,硫、磷等杂质含量高。2. 焊接线能量大,导致晶粒粗大。
1. 控制焊缝金属的化学成分,减少硫、磷含量。2. 选择合适的焊接线能量,避免晶粒粗大。3. 对于刚性大的焊件,采用焊前预热和焊后缓冷的方法。
焊接裂纹产生原因及防治措施

焊接裂纹就其本质来分,可分为热裂纹、再热裂纹、冷裂纹、层状撕裂等。
下面仅就各种裂纹的成因、特点和防治办法进行具体的阐述。
1.热裂纹在焊接时高温下产生的,故称热裂纹,它的特征是沿原奥氏体晶界开裂。
根据所焊金属的材料不同(低合金高强钢、不锈钢、铸铁、铝合金和某些特种金属等),产生热裂纹的形态、温度区间和主要原因也各不相同。
目前,把热裂纹分为结晶裂纹、液化裂纹和多边裂纹等三大类。
1)结晶裂纹主要产生在含杂质较多的碳钢、低合金钢焊缝中(含S,P,C,Si 缝偏高)和单相奥氏体钢、镍基合金以及某些铝合金焊缝中。
这种裂纹是在焊缝结晶过程中,在固相线附近,由于凝固金属的收缩,残余液体金属不足,不能及时添充,在应力作用下发生沿晶开裂。
防治措施:在冶金因素方面,适当调整焊缝金属成分,缩短脆性温度区的范围控制焊缝中硫、磷、碳等有害杂质的含量;细化焊缝金属一次晶粒,即适当加入Mo、V、Ti、Nb等元素;在工艺方面,可以通过焊前预热、控制线能量、减小接头拘束度等方面来防治。
2)近缝区液化裂纹是一种沿奥氏体晶界开裂的微裂纹,它的尺寸很小,发生于HAZ近缝区或层间。
它的成因一般是由于焊接时近缝区金属或焊缝层间金属,在高温下使这些区域的奥氏体晶界上的低熔共晶组成物被重新熔化,在拉应力的作用下沿奥氏体晶间开裂而形成液化裂纹。
这一种裂纹的防治措施与结晶裂纹基本上是一致的。
特别是在冶金方面,尽可能降低硫、磷、硅、硼等低熔共晶组成元素的含量是十分有效的;在工艺方面,可以减小线能量,减小熔池熔合线的凹度。
3)多边化裂纹是在形成多边化的过程中,由于高温时的塑性很低造成的。
这种裂纹并不常见,其防治措施可以向焊缝中加入提高多边化激化能的元素如Mo、W、Ti等。
2、再热裂纹通常发生于某些含有沉淀强化元素的钢种和高温合金(包括低合金高强钢、珠光体耐热钢、沉淀强化高温合金,以及某些奥氏体不锈钢),他们焊后并未发现裂纹,而是在热处理过程中产生了裂纹。
焊接裂纹及防治措施

1 焊接裂纹及防治措施焊接裂纹是焊接构件施工过程中最为严重的缺陷,轻则返修,重则构件报废。
焊接裂纹有焊缝或熔合线或热影响区裂纹,有表面或内部贯穿裂纹,有弧坑或焊址或焊缝根部裂纹,有层状撕裂等。
以焊缝冷却结晶时出现的时间阶段分,有热裂纹和冷裂纹或延迟裂纹。
(1)热裂纹的成因影响热裂纹形成的因素有:焊缝在冷却结晶过程中,由于快速冷却凝固收缩,晶粒截面间的液态金属补充不足,致使液态薄层开裂;母材热影响区和多层焊的根部焊缝易产生低熔点共晶物的熔解(即硫偏析),产生裂纹。
(2)冷裂纹的成因影响冷裂纹形成的因素有:焊接接头中金相组织的硬度、脆性较高;焊接接头中焊缝扩散氢的含量较高;焊接接头的拘束应力较大。
(3)焊接裂纹的防止措施1)控制焊材的化学成分由于钢材化学成分已经选定,因此焊材选配时应选硫、磷含量低、锰含量高的焊材。
使焊缝金属中的硫磷偏析减少,改善部分晶体形状,提高抗热裂性能。
2)控制焊接工艺参数、条件控制焊接电流与速度,使每一焊道的焊缝成形系数达到1、1~1、2,减少在焊缝中心形成硫磷偏析,提高抗裂性能。
避免采用小角度、窄间隙的焊缝坡口,致使焊缝成形系数过小。
加强焊前预热,降低焊缝在冷却结晶过程中的冷却速度。
采用合理的焊接顺序,使大多数焊缝在较小的拘束度下焊接,减少焊缝收缩拉力。
3)提高根部焊缝质量焊缝根部焊接是厚板焊接的起始点;是保证焊缝质量的根基;亦是产生裂纹的敏感区,因此焊缝根部的焊接措施必须慎之由慎。
加强焊缝坡口的清洁工作,清除一切有害物质;加强焊前预热温度的控制;焊前对坡口根部进行烘烤,去除一切水分、潮气,降低焊缝中氢含量。
使用小直径手工焊条打底,确保根部焊透;控制焊层厚度,适当提高焊道成形系数;控制焊接速度,适当增加焊接热输入量。
控制熔合比:在确保焊透的前提下,控制母材熔化金属在焊缝金属中的比例,减少母材中有害物质对焊缝性能的影响。
根部焊材可选用低配:根据根部焊缝的施焊条件与要求,在保证焊缝力学性能的条件下,根部焊缝的焊材可选用韧性好,强度稍低的焊材施焊,以增加其抗裂性。
焊接裂纹形成的原因及防止措施
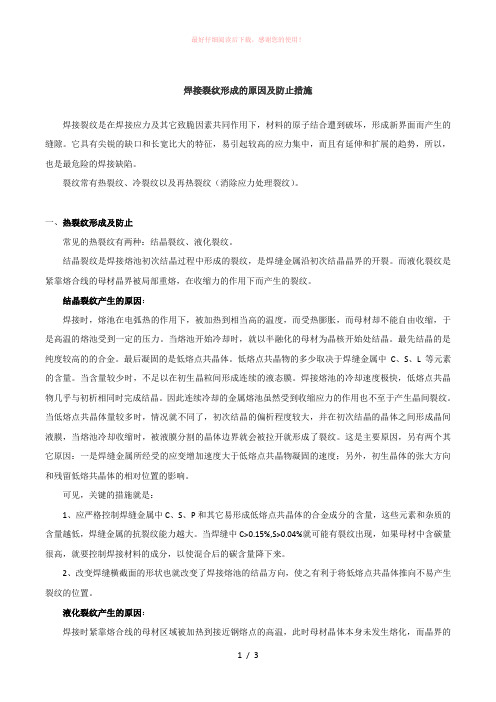
焊接裂纹形成的原因及防止措施焊接裂纹是在焊接应力及其它致脆因素共同作用下,材料的原子结合遭到破坏,形成新界面而产生的缝隙。
它具有尖锐的缺口和长宽比大的特征,易引起较高的应力集中,而且有延伸和扩展的趋势,所以,也是最危险的焊接缺陷。
裂纹常有热裂纹、冷裂纹以及再热裂纹(消除应力处理裂纹)。
一、热裂纹形成及防止常见的热裂纹有两种:结晶裂纹、液化裂纹。
结晶裂纹是焊接熔池初次结晶过程中形成的裂纹,是焊缝金属沿初次结晶晶界的开裂。
而液化裂纹是紧靠熔合线的母材晶界被局部重熔,在收缩力的作用下而产生的裂纹。
结晶裂纹产生的原因:焊接时,熔池在电弧热的作用下,被加热到相当高的温度,而受热膨胀,而母材却不能自由收缩,于是高温的熔池受到一定的压力。
当熔池开始冷却时,就以半融化的母材为晶核开始处结晶。
最先结晶的是纯度较高的的合金。
最后凝固的是低熔点共晶体。
低熔点共晶物的多少取决于焊缝金属中C、S、L等元素的含量。
当含量较少时,不足以在初生晶粒间形成连续的液态膜。
焊接熔池的冷却速度极快,低熔点共晶物几乎与初析相同时完成结晶。
因此连续冷却的金属熔池虽然受到收缩应力的作用也不至于产生晶间裂纹。
当低熔点共晶体量较多时,情况就不同了,初次结晶的偏析程度较大,并在初次结晶的晶体之间形成晶间液膜,当熔池冷却收缩时,被液膜分割的晶体边界就会被拉开就形成了裂纹。
这是主要原因,另有两个其它原因:一是焊缝金属所经受的应变增加速度大于低熔点共晶物凝固的速度;另外,初生晶体的张大方向和残留低熔共晶体的相对位置的影响。
可见,关键的措施就是:1、应严格控制焊缝金属中C、S、P和其它易形成低熔点共晶体的合金成分的含量,这些元素和杂质的含量越低,焊缝金属的抗裂纹能力越大。
当焊缝中C>0.15%,S>0.04%就可能有裂纹出现,如果母材中含碳量很高,就要控制焊接材料的成分,以使混合后的碳含量降下来。
2、改变焊缝横截面的形状也就改变了焊接熔池的结晶方向,使之有利于将低熔点共晶体推向不易产生裂纹的位置。
钢结构焊接裂纹的原因及防治措施

钢结构焊接裂纹的原因及防治措施钢结构是现代建筑中常见的结构形式之一,它具有重量轻、强度高、施工速度快等优点,因此被广泛应用于各类建筑工程中。
然而,在钢结构的制造和施工过程中,焊接裂纹往往成为一个常见的质量问题。
本文将探讨钢结构焊接裂纹的形成原因,并提出相应的防治措施。
一、焊接裂纹的形成原因1.1 材料问题钢材的组织结构和化学成分不合理是导致焊接裂纹的主要原因之一。
当钢材中含有含碳、硫、磷等含量超过规定标准的元素时,焊接时易产生高硬度和脆性物质,从而引发裂纹的形成。
1.2 焊接参数不当焊接过程中,焊接电流、焊接速度、焊接温度等焊接参数的选择不当,都可能导致焊接裂纹的生成。
例如,焊接电流过大会导致材料过热,从而在焊接接头中产生裂纹。
1.3 体积收缩差异钢材在焊接过程中会受到热量的影响而发生热胀冷缩,而焊接接头中的同时发生焊接金属的热收缩和焊接基体的冷缩,而两者之间的体积收缩差异可能引起焊接裂纹的形成。
1.4 焊接应力焊接过程中,焊接热量引入工件,产生应力集中,而大的应力集中可能导致焊接裂纹的生成。
特别是当焊接接头应力集中点的应力超过材料的承载极限时,裂纹便会发生。
二、焊接裂纹的防治措施2.1 材料严格控制在钢结构的制造和施工过程中,应严格控制材料的质量。
选用质量合格、符合要求的钢材,特别是控制其中的碳含量、硫含量、磷含量等关键成分的含量。
2.2 合理选择焊接参数在焊接过程中,应根据具体的钢材和焊接需求,合理选择焊接参数。
通过调整焊接电流、焊接速度、焊接温度等参数,确保焊接接头的均匀加热,避免产生过度应力。
2.3 预热和后续热处理对于较大尺寸、厚度较大的焊接接头,应进行预热处理。
通过预热可以减少焊接接头的冷缩和应力积聚,从而减少焊接裂纹的产生。
同时,在焊接完成后,可采取适当的后续热处理,通过热处理来消除残余应力。
2.4 控制焊接应力在焊接过程中,应合理控制焊接应力。
可以通过选用合适的焊接顺序、采用适当的焊接顺序交替焊接等方法,来减少焊接接头中的应力集中,降低焊接裂纹的风险。
焊接裂纹产生原因及防治

焊接裂纹产生原因及防治焊接裂纹是在焊接过程中或焊接完成后在焊缝或母材中产生的开裂缺陷。
焊接裂纹的产生原因多种多样,主要包括以下几个方面:1.焊接过程中的温度应力:焊接时,因为焊接区域发生了局部加热和冷却,导致焊接接头中的温度差异,从而造成了焊接区域的应力。
如果这种应力超过了焊接材料的强度极限,就会产生裂纹。
2.冶金因素:焊接过程中,由于温度升高,焊接材料和母材之间发生相互作用,形成了互溶区。
如果溶液比较富含低熔点的物质,就会导致物质从高温区流向低温区,从而增大了焊接接头的收缩量,引起裂纹。
3.废气、含氧量过高:当焊接环境中的氧气含量过高时,焊接时会发生氧化反应,在焊接接头中产生大量的氧化物,增大了焊接接头的收缩量,从而导致了裂纹的产生。
4.焊接过程中的振动:焊接过程中的振动会使焊接接头中的晶粒发生变化,从而影响了焊接材料的性能,使其发生了裂纹。
针对焊接裂纹的防治措施主要包括以下几个方面:1.提高焊接工艺:合理选择焊接工艺参数,如焊接电流、焊接电压和焊接速度等,以控制焊接过程中的温度和应力。
2.控制焊接过程中的温度升降速度:控制焊接过程中的升温速度和冷却速度,以避免焊接接头产生过大的应力。
3.控制焊接环境:减少焊接环境中的含氧量,避免产生氧化反应和氧化物。
4.优化焊接材料:合理选择焊接材料,根据焊接接头的要求选择合适的材料,以提高焊接接头的性能。
5.加强材料的前处理:在焊接前进行必要的预处理工作,如去污、除锈、磷化等,以提高焊接接头的质量。
综上所述,焊接裂纹的产生原因多种多样,需要综合考虑多个方面的因素来进行防治。
通过合理选择焊接工艺参数、控制焊接过程中的温度和应力、控制焊接环境、优化焊接材料以及加强材料的前处理等措施,可以有效预防和防治焊接裂纹的产生,提高焊接接头的质量。
焊缝裂纹产生的原因和解决方法

焊缝裂纹产生的原因和解决方法焊缝裂纹是焊接过程中常见的一种质量问题,主要是由于焊接应力和热应力引起的。
本文将从焊缝裂纹的原因和解决方法两个方面进行详细介绍。
焊缝裂纹产生的原因主要有以下几点:1. 焊接应力:焊接过程中,由于金属受热膨胀和冷却收缩,会产生应力。
如果焊接接头的应力超过了材料的强度极限,就会导致焊缝裂纹的产生。
2. 焊接材料的选择:焊接材料的选择直接影响着焊缝的质量。
如果选择的材料与基材的化学成分和物理性能不匹配,就会导致焊缝裂纹的产生。
3. 焊接工艺不当:焊接工艺参数的选择不合理,如焊接电流、电压、焊接速度等控制不当,都会导致焊缝裂纹的产生。
4. 焊接过程中的杂质:焊接过程中,如果焊缝中存在杂质、氧化物等,会导致焊缝的质量下降,从而容易产生裂纹。
针对焊缝裂纹产生的原因,可以采取以下解决方法:1. 控制焊接应力:通过合理的焊接工艺参数和焊接顺序,减小焊接接头的应力集中。
可以采用预热、中间退火等措施,使应力得到释放,从而减少焊缝裂纹的产生。
2. 选择合适的焊接材料:在焊接材料的选择上,应根据基材的化学成分和物理性能要求,选择与之相匹配的焊接材料。
同时,还要注意焊接材料的纯净度和含杂质的情况,以避免焊缝裂纹的产生。
3. 控制焊接工艺参数:合理选择焊接电流、电压、焊接速度等参数,保证焊接过程中的热输入和冷却速度合理。
同时,还应注意焊接过程中的保护气体和焊接速度的控制,以避免焊缝裂纹的产生。
4. 清除焊接过程中的杂质:焊接过程中要注意清除焊缝中的杂质、氧化物等,保证焊缝的质量。
可以采用机械清理、化学清洗等方法,使焊接接头表面清洁,减少焊缝裂纹的产生。
焊缝裂纹的产生主要是由于焊接应力和热应力引起的。
为了解决焊缝裂纹问题,需要从控制焊接应力、选择合适的焊接材料、控制焊接工艺参数和清除焊接过程中的杂质等方面入手。
只有采取有效的措施,才能有效预防和解决焊缝裂纹问题,提高焊接质量。
- 1、下载文档前请自行甄别文档内容的完整性,平台不提供额外的编辑、内容补充、找答案等附加服务。
- 2、"仅部分预览"的文档,不可在线预览部分如存在完整性等问题,可反馈申请退款(可完整预览的文档不适用该条件!)。
- 3、如文档侵犯您的权益,请联系客服反馈,我们会尽快为您处理(人工客服工作时间:9:00-18:30)。
力和敏感材料 • Solutions解决方法 – Control hydrogen 控制氢含量
Hydrogen氢
Stress应力
Sensitive Material
敏感材料
Underbead Cracking 焊道下裂纹
• Cause : 原因
Excessive hydrogen and stress and a sensitive base material (HAZ)太高的氢含量,应力和敏感材料
• Solutions解决方法
– Use proper joint detail使用正确的接头 – Control penetration (current density)控制 熔深(电流密度)
Surface Profile Cracking 表面成形裂纹 • Cause 3: – Concave surface cracks during solidification内凹的焊道表面在凝固 时开裂
Hydrogen氢
Stress应力
Sensitive Material
敏感材料
Underbead Cracking 焊道下裂纹
• Cause : 原因
Excessive hydrogen and stress and a sensitive base material (HAZ)太高的氢含量,应
No Cracking
40
30
Mn/S > 20:1
Cracking
20
10
0.06
0.08
0.10
0.12
0.14
0.16
0.18
Carbon, wt %
Segregation Cracking 偏析裂纹 • Cause 1: 原因
low melting point constituents segregate to the centerline during solidification在凝固
1/4”
FCAW-g
1/4”
FCAW-g
Segregation Cracking 偏析裂纹
Solutions:解决方法 • Minimize alloy pickup减少合金拾取
– Minimize admixture减少熔和比 – Minimize penetration (minimize current density {d= I/A})减少熔深(减少电流密度) – May require joint detail change或许需要改 变坡口形式
Segregation Cracking 偏析裂纹
Solutions:解决方法 • Minimize alloy pickup减少合金拾取
– Minimize admixture 减少熔和比 – Minimize penetration (minimize current density {d= I/A}) 减少熔深(减少电流密度)
Transverse Crack横向裂纹
Throat Crack焊喉处裂纹
Toe Crack 焊趾裂纹
Crater Cracks in Aluminum Weld铝焊接中的弧坑裂纹
Underbead Cracks焊道 下裂纹
Centerline Cracking 焊缝中心裂纹
Underbead Cracking焊道下裂纹
AWS D1.1 Figure 3.2
Groove Preparation
Root OpБайду номын сангаасning R = 1/4
R = 3/8 R = 1/2
Groove Angle
a = 45o a = 30o a = 20o
Proper root geometry正确的打底焊道
a
R
Improper root geometry:不正确的焊道
Buttering Layer预堆边
Segregation Cracking 偏析裂纹
Solutions:解决方法 • For steels with high sulfur, increase the manganese content of the electrode.对于含 高硫的母材,增加焊丝的锰含量
UCS = 230C + 190S + 75P + 45Nb – 12.3 Si - 5.4 Mn – 1
Cracking Contributors裂纹支持元素
TWI Hot Cracking Susceptibility:
UCS = 230C + 190S + 75P + 45Nb – 12.3 Si - 5.4 Mn – 1
Segregation Cracking 偏析裂纹 Solutions:解决方法 • Minimize alloy pickup减少合金拾取
– Minimize admixture减少融合比 – Minimize penetration (minimize current density {d= I/A})减少熔深(减少电流密度) – May require joint detail change或许需要改变坡 口形式 – Use of “buttering” techniques 采用“预堆边”
a
R
a is small, but R is increased.夹角小 了,但间隙增加了
“Popsicle” Cracking 凝固裂纹 • Cause 2: 原因
Improper width-to-depth ratio leads to solidification problems不正确的宽深比
Improper width-to-depth ratio leads to solidification problems不当的焊缝宽深比
• Solutions解决方法
– Use proper joint detail使用正确的接头
1.4
W/D > 1.2 1.0
D
W
AWS D1.1 Figure 3.2
– Low in low melting point constituents减少 低熔点的元素
TWI Hot Cracking Susceptibility: TWI热裂纹敏感指数
UCS = 230C + 190S + 75P + 45Nb – 12.3 Si - 5.4 Mn – 1
UCS < 10 “High Resistance to Cracking不易开裂”
a
R = too small太小
Proper root geometry正确的焊道
a
R= small, but a is increased 小 但夹角增加了
Improper root geometry:不正确的焊道
a
R
R and a are both too small 夹角和间 隙都太小
Proper root geometry正确的焊道
Surface Profile Cracking表面成形裂纹
Surface Profile Cracking 表面成形裂纹
Surface Profile Cracking 表面成形裂纹
• Cause 3: – Concave surface cracks during solidification内凹表面在凝固时开裂 • Solution:解决方法 – Make convex surfaces焊成凸的焊缝
Transverse Cracking横向裂纹
Centerline Cracking焊道中心裂纹
Centerline Cracking 焊道中心裂纹
(even though not in center of joint)即使不在中间
Centerline Cracking 焊道中心裂纹
Cause 1: Segregation Cracking 原因1:偏析裂纹 • Low melting point constituents segregate to the centerline during solidification在凝固时低 熔点的元素聚集到中间
Cracking Resistors
裂纹阻止元素
Segregation Cracking 偏析裂纹
Solutions:解决方法 • Use “good” steel使用 “好”的钢 材
– Low in low melting point constituents减少 低熔点的元素 – Avoid “free machining” steels for welded applications 避免使用“不需机加工”的钢材
Why Do Welds Crack?
焊缝为什么会开裂?
David Wang
王秀伟
When did the crack occur?
何时出现裂纹?
During fabrication?
生产中?
In service?
运行中?
Where is the crack?
裂纹出现在哪里?
Longitudinal Crack纵向裂纹
“HOT CRACKING热裂纹 ”
Underbead Cracking焊道下裂 纹
Transverse Cracking横向裂纹
“COLD CRACKING冷裂纹 ”
Underbead Cracking焊道下裂纹
Underbead Cracking 焊道下裂纹 • Cause : 原因
Excessive hydrogen and stress and a sensitive base material (HAZ)太高的氢含量, 应力和敏感材料