机床运动仿真
SolidWorksMotion虚拟样机运动仿真

注意事项:在建立复杂运动副时,需要注意运动副之间的约束关系是否合理,避免 出现运动学奇异或动力学不稳定的情况。
运动仿真结果分析
运动学分析:对运动过程中各部 件的位置、速度、加速度等参数 进行计算和评估
SolidWorks Motion与 Adams软件无缝 集成,实现运动 仿真与动力学分 析的完美结合。
通过Adams软 件进行更深入 的动力学分析, 包括碰撞检测、 振动分析等。
方便地在 Adams软件中 进行优化设计, 提高产品的性 能和可靠性。
实现从 SolidWorks到 Adams的模型 传递,保持数 据的一致性和 完整性。
结果分析:通过仿真结果分析船舶推进系统的性能表现,如推进效率、稳定性等,为优化 设计和改进提供依据。
PART 07
SolidWorks Motion未来发
展与展望
新功能与技术趋势
人工智能与机器学习在SolidWorks Motion中的应用,提高仿真效率和准确性。 云技术与实时协作功能,实现异地团队共同进行运动仿真与分析。 虚拟现实与增强现实技术,提供更真实的运动仿真体验和可视化效果。
04 S o l i d W o r k s Motion高级功能
06 S o l i d W o r k s Motion应用案例
PART 01 添加章节标题
PART 02
SolidWorks Motion概述
定义与功能
添加标题
定义:SolidWorks Motion是一款基于SolidWorks平台的运动仿真插件,用于对机械系统进行运 动学和动力学仿真。
PART 06
基于EON的数控机床换刀系统运动仿真
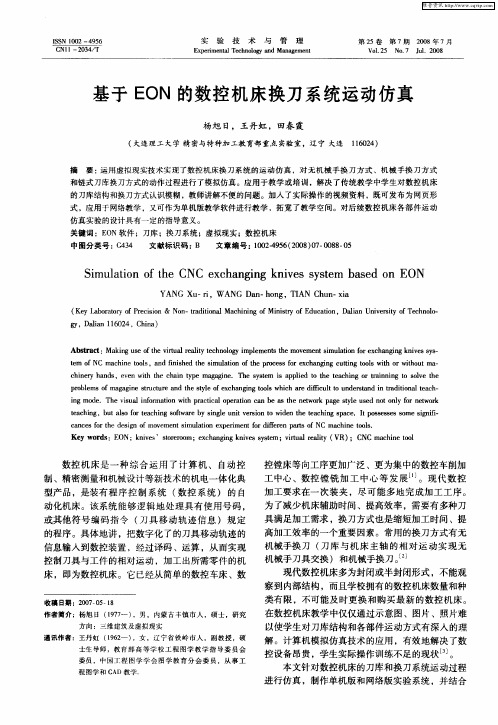
仿真实验的设计具有一定 的指导意义。
关键词 :E N软件 ;刀库 ;换刀系统 ;虚拟现实 ;数控机床 O 中图分类号 : 4 4 G 3 文献标识码 : B 文章编号 : 0 245 (0 8 o — 0 8 0 10 -9 6 2 0 )7 0 8 —5
S muain o h NC e c a gn n v ss se b s d o i lt ft e C x h n ig k ie y tm a e n EON o
和链式刀库换 刀方式 的动作过程进行 了模拟仿真 。应用于教学或 培训 ,解 决了传统教学 中学生对数控机 床
的刀库结构和换 刀方式认识模糊 , 师讲解不便的 问题 。加入 了实际操作的视频资料 ,既可发布为 网页形 教
式 ,应 用于网络教学 。又可作为单机版教学软件进行教学 ,拓宽 了教学 空间。对后 续数控机床各部 件运动
c i e a d ,e e t h h i y e ma a i e T e s se s a p id t e ta h n r t in n o s l e t e h n r h n s v n w h t e c a n tp g g n . h y t m i p l o t e c i g o r n ig t ov h y i e h a
i g mo e h iu n omain w t r ci a o e ain c n b s t en t r a e sye u e o o l rn t r n d .T e v s a if r t h p a t l p r t a e a h e l o i c o wo k p g tl s d n t ny f ewo k o
Ab t a t Ma i gu e o e vr a e i c n lg lme t e mo e n i lt n fre c a gn n v ss s s r c : k n s f h itl r a t t h o o y i e n st v me t mu ai o x h n i gk ie y — t u l ye mp h s o
1.6VERICUT机床加工仿真过程

第1章VERICUT系统简介本章介绍VERICUT 7.2软件的系统需求、安装步骤和功能模块。
通过本章的学习,掌握VERICUT 7.2软件的系统需求、软件安装方法及其基本功能,了解VERICUT软件的工作过程。
1.1 系统要求VERICUT 7.2软件的系统要求如表1-1所示。
表1-1 VERICUT 7.2软件的系统要求设备配置硬盘空间1GB(完整安装包括:Library(控制系统库)、Sample(样本文件)、Help(帮助)和Java Run-Time)临时硬盘空间除1GB硬盘空间以外,安装VERICUT时需要有1GB的临时硬盘空间Page File 推荐使用两倍的可用物理内存操作系统VERICUT 7.2支持Windows 7 32位/64位、Windows Vista 32位/64位和Windows XP 32位/64位VERICUT 7.2不支持Windows 2000、Windows 98、Windows ME和Windows NT操作系统Java Run Time Environment 1.6.0_07 (included in the VERICUT installation)CATIA V5接口需要Windows Script 5.3或更新的版本物理内存建议最小1GB,首选2GB处理器英特尔奔腾处理器或者100%奔腾兼容的处理器,推荐2GHz或者更快的速度。
特别是在VERICUT中运行其他大的程序时,多处理器可以提高处理性能其他两键或者三键鼠标,建议使用带滚轮的三键鼠标网卡图像设备至少能够显示16位颜色兼容OpenGL图形加速器用于机床仿真视图和零件视图中进行动态的放大、缩小、旋转、平移等操作。
由于显示切削模型需要大量的图形内存,要求显存最低512MB,建议1GB 以上优先主要内容学习目标VERICUT授权许可文件可以支持安装在SUN SPARC/Solaris、Hewlett-Packard PARISC/HP-UX和IBM RS6000/AIX操作系统的服务器上,如表1-2所示。
数控机床仿真分析报告

对仿真结果与实际实验结果之间的误差进行 分析,找出误差来源,提高仿真模型的精度。
04
数控机床仿真分析方法和 结果
仿真分析方法的选择和应用
有限元分析法
通过将机床结构离散化为有限个单元,对每个单元进行力学分析, 从而得出整体结构的应力、应变等参数。广泛应用于复杂结构的 静力学和动力学分析。
运动学仿真
定性和安全性。
运动性能评估
运动学仿真结果显示,机床 的运动轨迹准确、动态响应
良好,能够满足加工要求。
热误差预测
热力学仿真揭示了机床在工 作过程中的温度变化规律, 预测了热误差的产生及其对 加工精度的影响。
仿真分析的局限性和改进方向
01
模型简化与实际差异
02
材料属性与实际不符
03
耦合效应考虑不足
仿真分析基于理想化的模型,可能忽 略了一些实际因素,导致结果与实际 情况存在偏差。未来可考虑引入更精 细的模型和边界条件。
报告背景
随着制造业的快速发展,数控机床作 为现代制造装备的核心,其性能和加 工精度对产品质量和生产效率具有重 要影响。因此,对数控机床进行仿真 分析具有重要意义。
报告范围和限制
报告范围
本报告主要针对数控机床的仿真分析,包括机床结构、运动学、动力学、热力学等方面 的分析。
报告限制
由于时间和资源限制,本报告未能涵盖所有类型的数控机床,仅以某一款典型数控机床 为例进行仿真分析。同时,报告中使用的仿真软件和模型简化也可能存在一定误差和局
仿真结果显示,切削参数的选择对加工效果具有显著影响,合理调整切削参数可以有效提 高加工质量和效率。
冷却系统对加工过程稳定性具有重要作用
分析表明,优化后的冷却系统能够更好地控制加工过程中的温度变化,提高加工过程的稳 定性。
基于UG的车床夹具虚拟设计及运动仿真
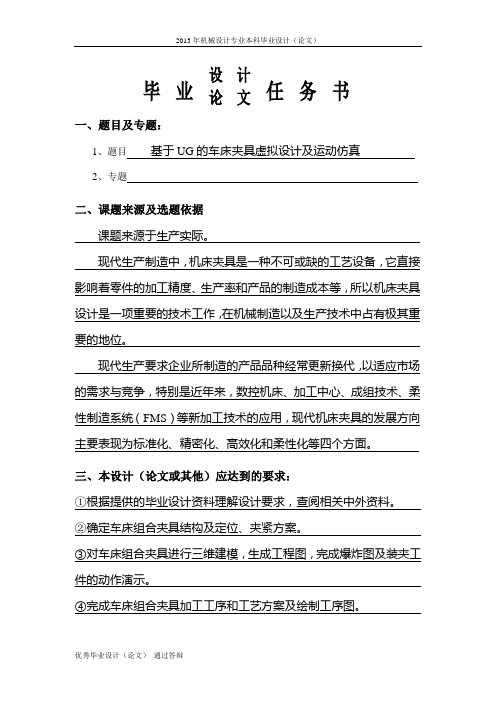
毕业设计论文任务书一、题目及专题:1、题目基于UG的车床夹具虚拟设计及运动仿真2、专题二、课题来源及选题依据课题来源于生产实际。
现代生产制造中,机床夹具是一种不可或缺的工艺设备,它直接影响着零件的加工精度、生产率和产品的制造成本等,所以机床夹具设计是一项重要的技术工作,在机械制造以及生产技术中占有极其重要的地位。
现代生产要求企业所制造的产品品种经常更新换代,以适应市场的需求与竞争,特别是近年来,数控机床、加工中心、成组技术、柔性制造系统(FMS)等新加工技术的应用,现代机床夹具的发展方向主要表现为标准化、精密化、高效化和柔性化等四个方面。
三、本设计(论文或其他)应达到的要求:①根据提供的毕业设计资料理解设计要求,查阅相关中外资料。
②确定车床组合夹具结构及定位、夹紧方案。
③对车床组合夹具进行三维建模,生成工程图,完成爆炸图及装夹工件的动作演示。
④完成车床组合夹具加工工序和工艺方案及绘制工序图。
⑤阅读和翻译英文文献。
⑥撰写毕业设计论文。
四、接受任务学生:五、开始及完成日期:自2012年11月12日至2013年5月25日六、设计(论文)指导(或顾问):指导教师签名签名签名教研室主任〕签名〔学科组组长研究所所长系主任签名2012年11月12日摘要根据任务书的要求,本次任务主要是针对十字头零件的加工设计两套专用的车床夹具,完成相应的加工要求。
主要内容包括:加工零件的分析、分析其结构、各部分相关尺寸、加工工艺过程及工序、零件图的绘制、加工各面、孔等内容。
具体任务是针对车Φ85外圆和挖Φ24槽设计两套专用车床夹具,确定其定位、夹紧方案和误差、切削力的计算。
在此之前,首先要拟定一套高效的加工方案,进行工序及工步的确定,进而根据所选定的方案完善相应的计算和加工工艺卡片,再由所需要求,设计出夹具的尺寸,根据查找的资料,实现理论的设计。
在得到理论设计的尺寸和方案之后,利用UG进行三维建模,并对所画的各部件做装配、爆炸及运动仿真等工作,最后,将所有零部件及装配图生产工程图。
数控车床仿真操作方法

数控车床仿真操作方法数控车床(Computer Numerical Control Lathe)是一种通过预先编程的方式实现自动加工的机床。
该机床主要通过计算机软件控制其操作,具有高效、精确和灵活的特点。
在进行数控车床的仿真操作时,需要考虑以下几个步骤:1. 准备工作在进行数控车床的仿真操作之前,首先需要进行一些准备工作。
这包括选择合适的数控车床设备和编程软件,并安装好相应的驱动程序。
同时,还需要准备好待加工的工件和刀具。
2. 编程数控车床的操作是通过预先编程实现的。
在进行仿真操作之前,需要使用编程软件进行程序编写。
编程的过程主要包括确定加工轨迹、选择刀具和切削参数,并设置相应的加工指令。
3. 载入工件和刀具数据完成编程后,需要将工件和刀具的数据导入到仿真软件中。
这些数据包括工件的尺寸、形状和材料特性,以及刀具的参数和切削条件等。
通过导入这些数据,可以在仿真软件中模拟出真实的加工环境。
4. 进行仿真操作在进行仿真操作时,首先需要选择合适的仿真模式,如运动仿真、切削仿真或加工过程仿真等。
通过选择不同的仿真模式,可以观察到不同的加工效果和过程。
在仿真操作中,可以通过改变工件和刀具的数据来模拟不同的加工条件。
例如,改变工件的形状和尺寸,可以观察到不同的切削效果;改变刀具的参数和切削条件,可以观察到不同的切削力和切削温度等。
同时,还可以通过改变加工指令来模拟不同的加工过程。
例如,改变进给速度和主轴转速等,可以观察到不同的切削速度和加工效率。
通过这些操作,可以对加工过程进行优化和调整,以达到更好的加工效果和加工质量。
5. 分析和评估在进行仿真操作的同时,还可以对加工过程进行分析和评估。
通过仿真软件提供的数据和结果,可以进行加工力分析、刀具磨损分析和工件表面质量评估等。
通过这些分析和评估,可以得出加工过程的优缺点,并为进一步的改进提供参考。
总。
基于ADAMS的PRS—XY型混联机床机构运动学仿真分析
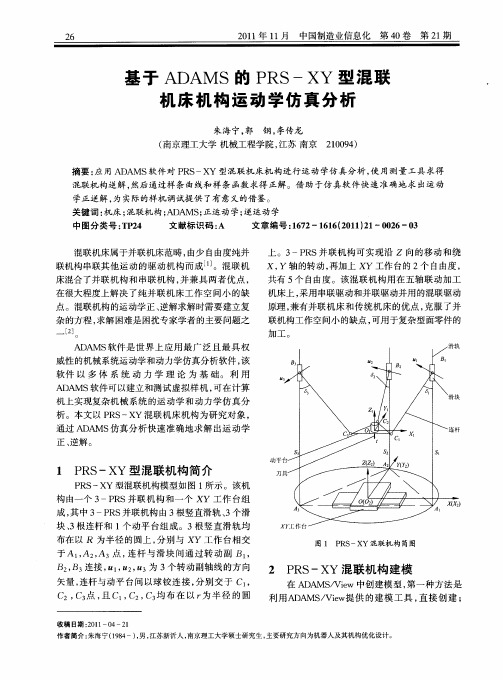
动
1 P S Y 型 混 联 机构 简 介 R —X
P S—X 型混联 机构 模 型如 图 1 R Y 所示 。该 机 构 由一 个 3 RS并 联 机 构 和 一 个 XY 工 作 台组 一P 成, 中3 R 其 一P S并联 机 构 由 3 竖直 滑轨 、 根 3个滑 块 、 连杆 和 1个 动 平 台组 成 。3根 竖 直 滑 轨均 3根
—
方 向与 三 相 同。
3 P S—X 混 联 机 构 运 动 学 分 析 R Y
3 1 逆 解分析 .
逆解就是 已知刀尖的位置和刀轴的姿态 , 求滑
块在 滑轨 上 的位 置 等 。在 刀 尖 处 添 加 多 自由度 驱
5t l 1 00 , 5O
图 4 滑块 速 度 一时 间 图
设 置 仿 真 时 间 参 数 为 2s 仿 真 步 数 为 50 0, 0
步 , 行 仿 真后 进 行 测 试 , 试 步 骤 是 :u d 运 测 b i— l
mesr-pitopit nw, 弹 出 的对 话 框 中 aue- on o - e 在 t n 选好 需 要测 试 的 Makr 以及 参 考 坐标 系 , 后 re 点 先 获得滑 块 和动平 台 的 位移 一时 间 图 以及速 度 一时 间 图。图形 生 成好 之 后 进 入 A A D MS的后 处 理 模 块 , 出 图 2和 图 5所示 滑块位 移 一时 间图和 工作 得 台 的位 移 一时 问 图 , 以及 滑块速 度 一时 间图和 工作 台的速度 一时 间 图。 图 2和 图 4中的 3条 不 同线 型分别 对应 3个 滑块 , 3和 图 5中的 2条 不 同线 图 型分别 对应 工作 台 的 x, 向滑 台 。 y
NX Motion运动仿真在专用螺纹加工机床设计中的应用
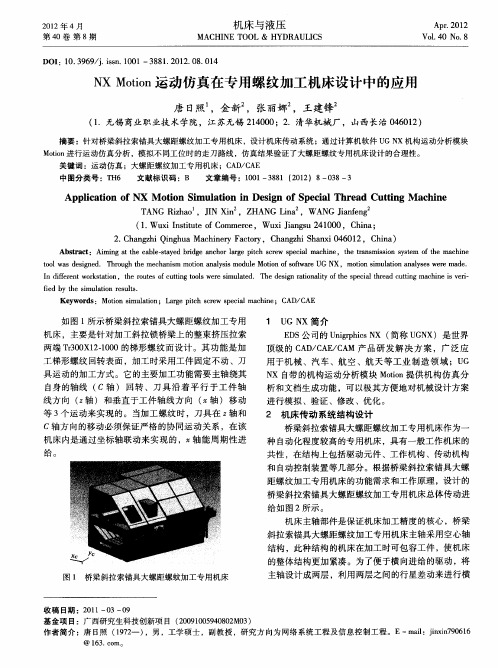
如图1 所示 桥梁斜拉索锚具大螺距螺纹加工专用
1 U X简介 GN E S公司的 U ip i X ( D n r cN ghs 简称 U N )是世界 G X
机床 ,主要是针对加工斜拉锁 桥梁上 的整束挤压拉索 两端 T30 1— 0 r X 21 0的梯形螺纹而设 计 。其功能 是加 0 0
@ 1 .C B 。 63 O
第 8期
唐 日照 等 :N t n运动仿真在专用螺纹加工机床设计 中的应用 X Moi o
・ 9・ 3
向进给 。主运动是 由伺服 电机 M 2通过 同步齿 形带 驱
动主轴 I ;轴 向进 给运动 由伺服 电机 M 3带动 滚珠 丝 杆 副拖 动主轴箱完成 ;横 向进给运动 的传动链是 :伺
M t n进行运动仿真分析 ,模拟不同工位 时的走 刀路线 ,仿真结果验证 了大螺距螺纹专用机 床设计 的合理性 。 oi o 关键词 :运 动仿 真 ;大螺距螺纹加工专用机床 ;C D C E A / A 中图分类号 :T 6 H 文献标识码 :B 文章编号 :10 3 8 2 1 )8— 3 3 0 1— 8 1(0 2 0 8—
具运动 的加工方式 。它 的主要 加工功能需要 主轴绕其 自身 的轴线 ( c轴 ) 回转 、刀具沿 着 平行 于工 件 轴 线方 向 ( 轴 )和垂 直于工 件轴线 方 向 ( ) 移动 z 轴 等 3 运动来实现的。当加工 螺纹时 ,刀具在 z 个 轴和 c轴方 向的移动必须保证严格的协 同运动关系 ,在该 机床 内是通过坐标轴联动来实 现的 , 轴能周期 性进
法兰盘上 ,伺服 电机 M1 2与 主轴箱一起运动 。 、M
z‘
上 - : -
图 4 螺 纹 切 削 循 环 过 程
数控机床仿真实训 (1)
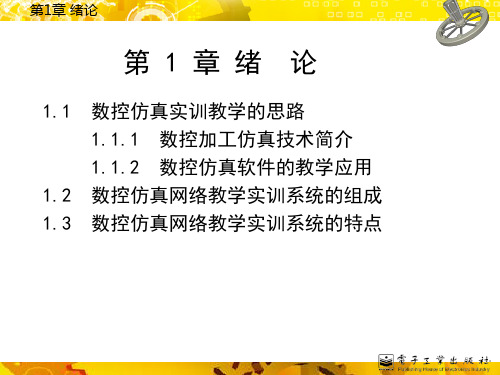
真系统”和德国“MTS数控编程仿真系统”。这类软件可以用来学习 数控机床的编程与操作,具有“以软代硬”来熟悉编程与操作、减少 废品和撞机等优点,是一种现代化教学和实训的好方法。
第1章 绪论 • 1.上海宇龙“数控加工仿真系统” • 整个系统分成四个模块,每一个模块中包含不同功能,每个模块功能都
将铣、车、钻、镗等加工方法的加工路线描绘出来,并能提供错误信
息的反馈,使工程技术人员能预先看到制造过程,及时发现生产过程
中的不足,有效预测数控加工过程和切削过程的可靠性及高效性,此
外,还可以对一些意外情况进行控制。数控加工仿真代替了试切等传
统的走刀轨迹的检验方法,大大提高了数控机床的有效工时和使用寿
第1章 绪论
第1章绪 论
1.1 数控仿真实训教学的思路 1.1.1 数控加工仿真技术简介 1.1.2 数控仿真软件的教学应用
1.2 数控仿真网络教学实训系统的组成 1.3 数控仿真网络教学实训系统的特点
第1章 绪论
• 1.1.1 数控加工仿真技术简介
•
在数控加工过程中,为检查数控程序的正确性,传统上采用试切
第1章 绪论 • (2)程序编辑模块。用于数控程序的输入、修改及显示编辑。NC程序的
读取如同生产实际一样,采用面板手工输入和程序文件读入两种方式。 • (3)程序处理模块。通过对NC代码的理解、检查代码语法语意的正确性,
经过译码、刀补计算、进给速度处理,得到刀具中心轨迹和其他所需数据, 用于模拟加工。 • (4)模拟加工模块。具有自动加工和手动加工等功能,系统通过对处理 后NC程序的离散和插补,直接驱动数控系统显示屏或三维动画仿真。在模 拟加工过程中,数控系统显示屏按实际加工状态,可工作在图形模拟或数 字状态两种方式下。
普通车床变速箱的三维虚拟设计及运动仿真
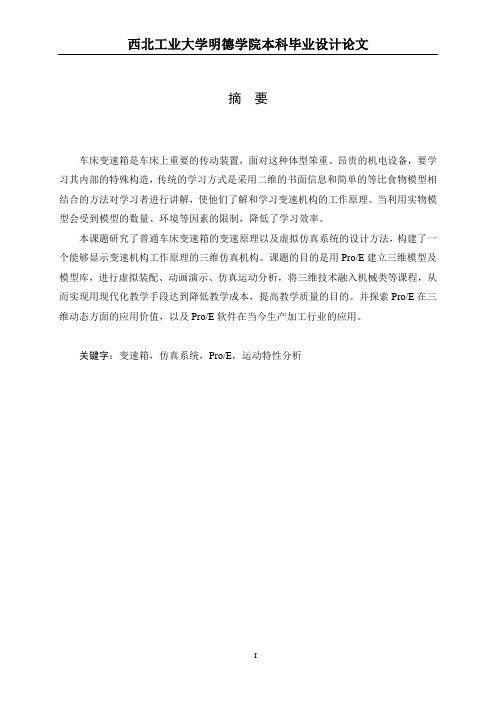
摘要车床变速箱是车床上重要的传动装置,面对这种体型笨重、昂贵的机电设备,要学习其内部的特殊构造,传统的学习方式是采用二维的书面信息和简单的等比食物模型相结合的方法对学习者进行讲解,使他们了解和学习变速机构的工作原理。
当利用实物模型会受到模型的数量、环境等因素的限制,降低了学习效率。
本课题研究了普通车床变速箱的变速原理以及虚拟仿真系统的设计方法,构建了一个能够显示变速机构工作原理的三维仿真机构。
课题的目的是用Pro/E建立三维模型及模型库,进行虚拟装配、动画演示、仿真运动分析,将三维技术融入机械类等课程,从而实现用现代化教学手段达到降低教学成本,提高教学质量的目的。
并探索Pro/E在三维动态方面的应用价值,以及Pro/E软件在当今生产加工行业的应用。
关键字:变速箱,仿真系统,Pro/E,运动特性分析ABSTRACTLathe gearbox is important gear on a lathe, in the face of this kind of bodily form bulky and expensive mechanical and electrical equipment, to study its internal structure, the special traditional way of learning is to use 2 d written information and simple geometric model method of combining the food to interpretation of learners, to make them understand and study the working principle of variable speed mechanism. By using physical model will be affected by the number of models, environmental factors such as limit, reduce the learning efficiency.This topic research the engine lathe gearbox transmission principle and design method of virtual simulation system, builds a able to display the 3 d simulation of shift gear working principle. Subject is the purpose of using Pro/E 3 d model is set up and model library, virtual assembly, animation, motion characteristics.Key words: Transmission, the simulation system, Pro/E, movement characteristics analysis目录第一章绪论 (1)1.1P RO/E的应用及车床的发展 (1)1.1.1 Pro/E在工业中的应用 (1)1.1.2 国内外机床发展状况 (2)1.2P RO/ENGINEER软件的简介 (2)1.2.1 Pro/ENGINEER的发展历程 (2)1.2.3 Pro/ENGINEER主要模块及应用领域 (4)1.3本课题主要研究内容 (6)第二章车床变速箱的概况 (8)2.1变速箱组成及特点 (8)2.2变速箱的主要传动系统构成 (8)2.3主轴箱的主要参数 (9)2.4传动系统及传动方案的确定 (9)2.5轴在箱体的定位 (12)第三章变速箱的三维实体建模 (13)3.1齿轮参数化建立 (13)3.2齿轮的建模过程 (35)3.3轴的建模过程 (38)3.4变速箱的装配过程 (43)3.4.1 轴的装配过程 (43)3.4.2 轴之间的定位装配过程 (44)3.4.3 传动系统的装配 (48)第四章仿真运动 (50)4.1仿真运动的参数设置 (50)4.2模拟仿真运动效果 (53)第五章全文总结 (57)致谢 (58)参考文献 (59)毕业设计小结 (60)第一章绪论1.1 Pro/E的应用及车床的发展1.1.1 Pro/E在工业中的应用CAD技术是先进制造技术的重要组成部分,是计算机技术在工程设计、机械制造等领域中最有影响的一项高新应用技术。
FANUC0I数控加工仿真操作步骤

FANUC0I数控加工仿真操作步骤1.确定工件和夹具:在进行数控加工仿真之前,首先需要确定要加工的工件和夹具。
工件是指需要进行加工的产品,夹具是用于夹持工件并保持其位置的装置。
2.创建数控程序:使用数控编程软件,根据工件的设计要求,编写数控程序。
数控程序是一系列指令,用于控制数控机床的运动轨迹和操作参数。
3.导入数控程序:将编写好的数控程序导入到数控仿真软件中。
数控仿真软件可以模拟数控机床的运动,并显示加工过程中的各种信息,如刀具路径、加工深度等。
4.设置刀具:根据工件的设计要求,选择合适的刀具,并进行设置。
刀具的选择决定了加工过程中的切削速度、进给速度等参数。
5.设置工艺参数:根据工件的材料和加工要求,设置相应的工艺参数。
工艺参数包括切削速度、进给速度、切削深度等。
6.进行仿真:通过数控仿真软件,开始进行数控加工仿真。
在仿真过程中,可以观察刀具的运动轨迹,检测加工过程中的错误和问题。
7.优化加工过程:根据仿真结果,对加工过程进行优化。
可以根据仿真结果调整切削速度、进给速度等参数,以提高加工效率和质量。
8.生成加工报告:完成数控加工仿真后,生成加工报告。
加工报告记录了加工过程中的各种信息,如切削速度、进给速度、加工时间等,以供后续参考和分析。
9.调整数控程序:根据仿真结果和加工报告,对数控程序进行调整。
可以通过调整数控程序中的运动轨迹和操作参数,进一步优化加工过程。
10.导出数控程序:完成数控程序的调整后,将最终的数控程序导出到实际的数控机床中进行加工。
总结:FANUC0i数控加工仿真操作步骤包括确定工件和夹具、创建数控程序、导入数控程序、设置刀具和工艺参数、进行仿真、优化加工过程、生成加工报告、调整数控程序和导出数控程序。
这些步骤可以帮助操作人员在加工之前进行全面的模拟和优化,以提高加工效率和质量。
数控机床的数学模型与仿真技术
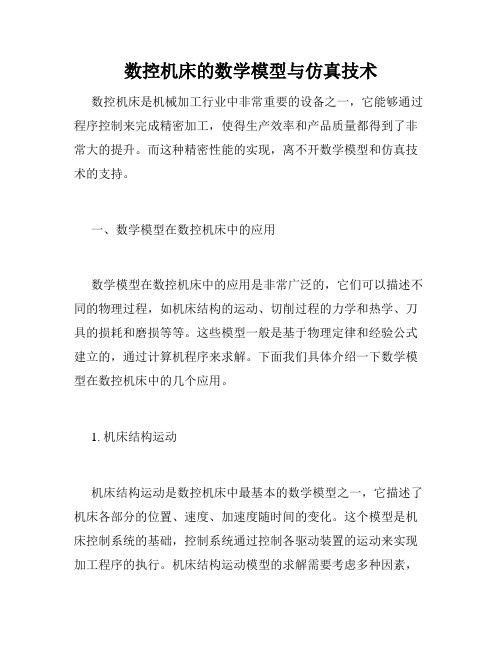
数控机床的数学模型与仿真技术数控机床是机械加工行业中非常重要的设备之一,它能够通过程序控制来完成精密加工,使得生产效率和产品质量都得到了非常大的提升。
而这种精密性能的实现,离不开数学模型和仿真技术的支持。
一、数学模型在数控机床中的应用数学模型在数控机床中的应用是非常广泛的,它们可以描述不同的物理过程,如机床结构的运动、切削过程的力学和热学、刀具的损耗和磨损等等。
这些模型一般是基于物理定律和经验公式建立的,通过计算机程序来求解。
下面我们具体介绍一下数学模型在数控机床中的几个应用。
1. 机床结构运动机床结构运动是数控机床中最基本的数学模型之一,它描述了机床各部分的位置、速度、加速度随时间的变化。
这个模型是机床控制系统的基础,控制系统通过控制各驱动装置的运动来实现加工程序的执行。
机床结构运动模型的求解需要考虑多种因素,如机床的结构、驱动装置的特性、工件的形状等等,通常使用有限元分析或者正逆动力学模型来求解。
2. 切削过程力学模型切削过程力学模型是研究刀具与工件之间力学相互作用的数学模型,它可以描述刀具的进给、切削和退出过程中的切削力和其他作用力。
这个模型可以帮助设计和选择刀具,优化切削参数,以及预测刀具寿命和工件表面形貌等,它是数控加工中非常重要的数学模型之一。
普遍用的刀具力模型包括切削力系数法、影响系数法、弹性回复切削力模型等。
3. 切削过程热学模型切削过程热学模型是描述切削过程中的热处理过程的数学模型,它可以预测切削面温度和刀具温度等。
这个模型可以帮助优化切削参数,提高切削速率、降低刀具磨损、减少工件变形和提高表面质量等。
切削过程热学模型主要包括经验模型和物理模型。
经验模型通常基于实验数据,通过适当的修正,可以很好地预测切削温度和刀具温度。
物理模型则基于热传导、热应力等物理理论,需要更大的计算开销,但是可以准确地反映热传导和热应力的特性。
二、数控机床仿真技术数控机床仿真技术是基于数学模型的的数字仿真技术,它可以模拟机床的运动、加工过程和性能。
ug仿真-机床运动仿真
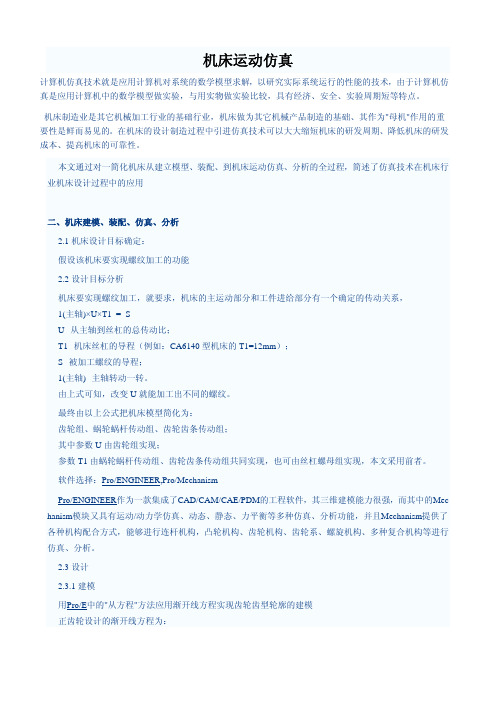
二、机床建模、装配、仿真、分析 2.1 机床设计目标确定: 假设该机床要实现螺纹加工的功能 2.2 设计目标分析 机床要实现螺纹加工,就要求,机床的主运动部分和工件进给部分有一个确定的传动关系, 1(主轴)×U×T1 = S U--从主轴到丝杠的总传动比; T1--机床丝杠的导程(例如:CA6140 型机床的 T1=12mm); S--被加工螺纹的导程; 1(主轴)--主轴转动一转。 由上式可知,改变 U 就能加工出不同的螺纹。 最终由以上公式把机床模型简化为: 齿轮组、蜗轮蜗杆传动组、齿轮齿条传动组; 其中参数 U 由齿轮组实现; 参数 T1 由蜗轮蜗杆传动组、齿轮齿条传动组共同实现,也可由丝杠螺母组实现,本文采用前者。 软件选择:Pro/ENGINEER,Pro/Mechanism Pro/ENGINEER作为一款集成了CAD/CAM/CAE/PDM的工程软件,其三维建模能力很强,而其中的Mec hanism模块又具有运动/动力学仿真、动态、静态、力平衡等多种仿真、分析功能,并且Mechanism提供了 各种机构配合方式,能够进行连杆机构,凸轮机构、齿轮机构、齿轮系、螺旋机构、多种复合机构等进行 仿真、分析。 2.3 设计 2.3.1 建模 用Pro/E中的"从方程"方法应用渐开线方程实现齿轮齿型轮廓的建模 正齿轮设计的渐开线方程为:
在 Pro/Mechanism 中可进行的分析测量的量有:位置、速度、加速度、连接反作用、净负荷、冲力。 在 Pro/Mechanism 中测量对模型各种运动参数进行测量,假如不符合要求,则重新建立模型,再次进行 仿真、分析,直至模型达到设计要求为止
由仿真、分析结果进行改进再仿真,直至达到设计要求,接着进行各部分功能细化,机床样机最终定型。 三、结论
本文借助Pro/E实现了对简化机床从建立模型、装配到仿真分析的全过程,最终实现了对机床样机的设 计。借助像Pro/E这样的三维CAD软件和仿真技术,大大缩短了新产品设计的周期;而且通过对数字化模型 的分析可以提早发现产品的缺陷并加以修改,达到了优化设计的目的;直接在数字化模型上进行各种运动 及材料特性的仿真分析而不用投入大量的人力、财力进行产品试制,有效节约了生产成本。应用仿真技术 对机床行业,及各个机械行业都是大有裨益的
数控车床的三维建模与运动仿真

Omn i — d i r e c t on i l a mu l t i p l e p e r s p e c t i v e sW e e l i n g s a n d u n d e r s t nd a i n g .
Ke y Wo r d s : ORAC CNC Be n c h La t h e ; Pr o / E; 3 D Mo d e l ; Ki n e ma t i c s S i mu l a t i o n
f r e e d o m c o n s t r a i n t s t o ch a i e v e t h e k i n e m ti a c s s i m u l t a i o n fs o p i n d l e , X, Y d i r e c t i o n , a n d i n t r o d u c e s p e c f i w o p e r a t i o n m e t h o d , nd a t h e m o v e en m t p r i n c i p l e ft o h e C N C l t a h e s h s a b e e n r e p r o d u c e d r e a l i s t c i a l l y . A s p a r t o ft h e s h e l l nd a 6
( S c h o o l o f Ma c h i n e r y a n d A u t o mo b i l e E n g i n e e r i n g , H e f e i U n i v e r s i t y o f T e c h n o l o g y , A n h u i H e f e i 2 3 0 0 0 9 , C h i n a )
机械设计中的动态仿真与分析
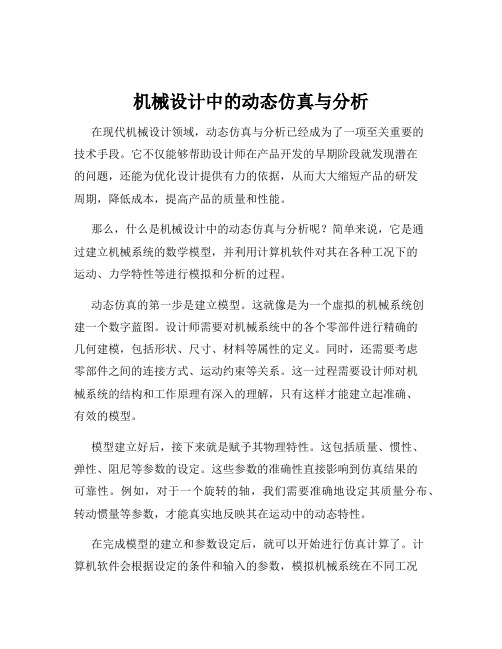
机械设计中的动态仿真与分析在现代机械设计领域,动态仿真与分析已经成为了一项至关重要的技术手段。
它不仅能够帮助设计师在产品开发的早期阶段就发现潜在的问题,还能为优化设计提供有力的依据,从而大大缩短产品的研发周期,降低成本,提高产品的质量和性能。
那么,什么是机械设计中的动态仿真与分析呢?简单来说,它是通过建立机械系统的数学模型,并利用计算机软件对其在各种工况下的运动、力学特性等进行模拟和分析的过程。
动态仿真的第一步是建立模型。
这就像是为一个虚拟的机械系统创建一个数字蓝图。
设计师需要对机械系统中的各个零部件进行精确的几何建模,包括形状、尺寸、材料等属性的定义。
同时,还需要考虑零部件之间的连接方式、运动约束等关系。
这一过程需要设计师对机械系统的结构和工作原理有深入的理解,只有这样才能建立起准确、有效的模型。
模型建立好后,接下来就是赋予其物理特性。
这包括质量、惯性、弹性、阻尼等参数的设定。
这些参数的准确性直接影响到仿真结果的可靠性。
例如,对于一个旋转的轴,我们需要准确地设定其质量分布、转动惯量等参数,才能真实地反映其在运动中的动态特性。
在完成模型的建立和参数设定后,就可以开始进行仿真计算了。
计算机软件会根据设定的条件和输入的参数,模拟机械系统在不同工况下的运动和力学行为。
通过仿真,我们可以得到诸如零部件的位移、速度、加速度、受力等详细信息。
这些信息可以以图表、曲线或者动画的形式呈现出来,让设计师能够直观地了解机械系统的工作状态。
动态仿真与分析在机械设计中的应用非常广泛。
例如,在汽车设计中,通过对发动机的曲柄连杆机构进行动态仿真,可以分析其在不同转速下的受力情况,从而优化零部件的结构设计,提高发动机的可靠性和耐久性;在航空航天领域,对飞行器的起落架进行动态仿真,可以评估其在着陆过程中的冲击载荷,为设计提供改进的方向;在工业机器人的设计中,通过对机器人的运动轨迹进行仿真,可以确保其能够准确、高效地完成预定的任务,同时避免与周围环境发生碰撞。
基于UG的五轴数控虚拟机床仿真技术

基于UG的五轴数控虚拟机床仿真技术王清,机械工程,2111302073摘要:多数五轴数控机床仿真系统,一般只提供二维的动画仿真,而且仿真系统的几何造型功能十分有限,零件和机床模型需要在其他CAD软件中进行建模,然后导入数控仿真系统。
由于文件格式的转化,零件的CAD模型将会产生误差,降低了仿真精度。
该文利用UG CAD/CAM软件造型功能建立五轴数控机床和零件模型,读取数控代码对机床各部件进行三维运动仿真,并对加工过程中机床运动部件之间的干涉及工件过切进行检查,为刀具轨迹的修改提供依据,同时免除了文件格式的转化产生的误差。
关键词:五轴;数控加工;机床仿真;UG NX;ISVTechnology of 5-axis Machining Simulation Based on UG Wang Qing, Mechanical Engineering, 2111302073Abstract: Most machine simulation systems virtually only provide 2D image today. And the modeling ability of those simulation systems of CAD softwareis also limited. So the workpiece should be modeled in other CAD software, then input the date to machine simulation systems. The accuracy will be reduced during the date exchange. In this paper, the machine tool and workpiece models are constructed by UG CAD/CAM software, while the NC programis used as input the date to perform the machine motion. During the simulation, overcut and collisions between the moving machine components can be checked. And the error of data exchange can be avoided.Keywords: 5-axis; NC machining; machining simulation; UG NX; ISV1 引言几十年来,人们普遍认为五轴数控加工技术是加工连续、平滑、复杂曲面的唯一手段。
基于ADAMS的线切割机床双走丝机构的运动仿真
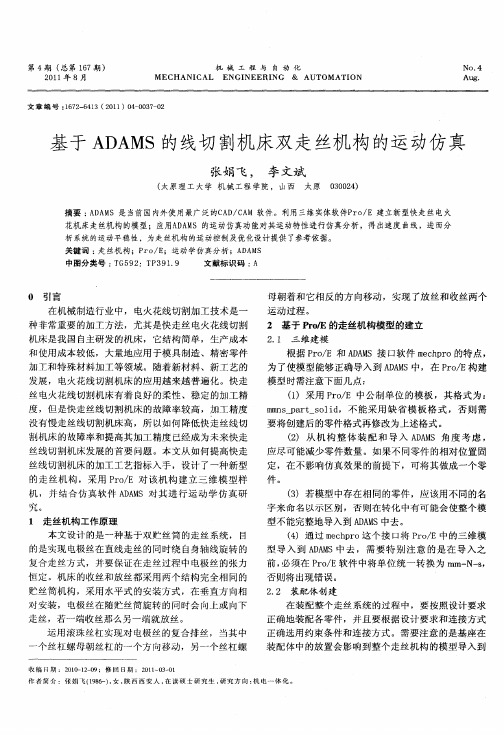
理模 块可 以计 算运 动 副关联 的 两个 构件 的相 对运 动 。
走 丝 ,若一 端收丝那 么另一端 就放 丝 。
运用滚 珠丝杠 实现对 电极丝 的复合排 丝 ,当其 中
一
个丝杠 螺母朝丝 杠 的一个 方 向移 动 ,另一个 丝杠螺
装 配 体中 的放 置会 影响 到整 个走丝 机构 的模 型导入 到
收 稿 日期 :2 1- 2 0 0 0 1— 9;修 回 日期 :2 1- 3 O 0l 0一 l
第 4期 ( 第 1 7期 ) 总 6
2 1 年 8月 01
机 械 工 程 与 自 动 化
M ECH ANI CAL ENGI NEERI NG & AUT0M AT1 0N
No. 4
Aug.
文 章 编 号 :6 2 6 1 2 1 )0 — 0 7 0 1 7— 4 3( 0 1 4 0 3 — 2
究。
()若模 型 中存 在相 同的零件 ,应该 用不 同的名 3
字来 命 名 以示 区别 ,否 则在转 化 中有 可 能会使 整个模
1 走丝机 构工作原 理 本文设计 的是一 种基 于双贮 丝筒 的走丝 系统 , 目
型 不能完整地 导入 到 A A S中去 。 DM
() 通过 m c p o这个 接 口将 P o E中 的三 维模 4 eh r r/
型 导 入 到 A A S中去 ,需 要 特 别 注 意 的 是在 导 入 之 DM 前, 必须 在 P o E软 件 中将单 位统 一 转换 为 m N s r/ m— — ,
否则 将 出现错 误 。
22 装配体创 建 . 在装 配整个 走丝 系统 的过程 中,要按 照设计 要求
正确 地装配 各零件 ,并 且要根 据 设计 要求和 连接 方式 正确选 用约束 条件 和连 接方 式 。需要注 意 的是基座 在
数控加工仿真软件的操作流程是什么

数控加工仿真软件操作流程解析数控加工仿真软件是实现数控机床加工仿真的关键工具,它可以模拟数控机床上的加工过程,帮助用户优化加工方案、减少加工错误。
本文将介绍数控加工仿真软件的操作流程,帮助读者更好地了解如何使用这种工具。
步骤一:打开软件首先,打开数控加工仿真软件,通常软件会显示一个欢迎界面或者加载界面。
等待软件完全加载后,用户可以开始进行后续操作。
步骤二:导入工件模型在软件界面中,用户需要导入待加工的工件模型。
通常可以通过“导入”功能选择本地存储的CAD模型文件,也可以手动建立工件模型。
步骤三:设置加工参数在导入工件模型后,用户需要设置加工参数,包括刀具类型、刀具直径、切削速度、进给速度等。
这些参数将决定仿真过程中刀具的运动轨迹和加工效果。
步骤四:选择加工路径根据实际加工需求,用户可以选择数控加工仿真软件提供的不同加工路径,包括轮廓加工、孔加工、曲面加工等。
每种加工路径都有特定的设置选项,用户需要根据实际情况进行选择。
步骤五:生成加工代码完成加工路径选择后,用户可以生成数控加工代码。
软件会根据用户设置的加工参数和加工路径自动生成对应的加工代码,这些代码将用于控制数控机床进行实际加工操作。
步骤六:进行仿真在生成加工代码后,用户可以进行仿真操作,软件会模拟数控机床上的加工过程,包括刀具的运动轨迹、加工效果等。
用户可以通过仿真结果评估加工方案的合理性,优化加工过程。
步骤七:分析结果最后,用户可以查看仿真结果并分析加工效果。
根据仿真结果,用户可以评估加工方案的优劣,调整加工参数,优化加工路径,以提高加工效率和质量。
通过以上操作流程,用户可以充分利用数控加工仿真软件,实现对数控加工过程的有效控制和优化,提高加工效率,降低加工成本。
感谢阅读本文,希望对数控加工仿真软件的操作流程有所帮助!。
基于ADAMS的并联钻尖刃磨机床运动学仿真研究
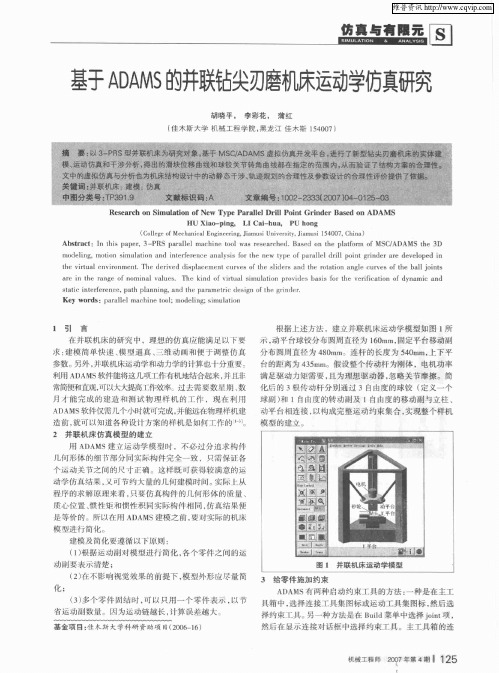
Absr c :I h sp p r t a t n t i a e ,3一 PRS p i Ie c i e umtwa e e h d a' l lma h n s r s a c e Ba e 】 h lto m fMS / a r s d‘ te p af r o C ADAMS t e 3 n h D
mo e i .moi n s mu a in a d i t r rnc nay i f rt e H w t p fp r le rl p i r n ra e d v lp d i dl ng to i l t n n e f e e a lss o h e y e o a a l ld il ontg ide r e eo e n o o t e v ru le v r l n T e‘e ie s lc me ule ft ld r n h o ai n a g e CI e ft e h l on s h it a n ioq me t h ]rr d dip a e nt p s o hes i e sa d t e r tto n l L So h a I{ it c  ̄  ̄ I a i h a g fn ri a a i s Th i d o i t i u a l n p o i e a i o h e l c to y a c a d r n t e r n e o o n 1 l e a J e k n fvr m1 sr l to r v d s b ss f rt e v rl a i n o d n mi n l e i f sa i i t re e c . a h p a n n , n i h p r me rcde i n o h rn e t t 。 n e f r n e p t l n i g a t t a a ti sg f e g i d r c t
基于HTC的机床虚拟装配运动仿真研究

基于HTC的机床虚拟装配运动仿真研究引言:机床是现代工业的重要设备,其精确的运动控制是确保工件质量和生产效率的关键因素之一、然而,传统的机床装配过程需要消耗大量的时间和资源,同时也存在着装配精度难以保证的问题。
虚拟装配技术可以通过计算模拟和仿真分析,大大缩短机床装配周期,提高装配精度和效率。
本文基于HTC的机床虚拟装配运动仿真研究,旨在通过HTC技术实现机床装配过程的虚拟模拟和运动仿真,以提高机床装配效率和精度。
一、HTC技术概述HTC(Head-Mounted Display),即头戴式显示器,是一种虚拟现实设备。
它由一个戴在头上的显示器和一部追踪头部运动的传感器组成,可以实时渲染计算机图形并将其投影到用户的眼前,从而使用户可以体验到身临其境的虚拟世界。
HTC技术在许多领域都有广泛的应用,如游戏、医学、教育等。
二、机床虚拟装配技术原理及方法1.建立机床虚拟模型:首先,通过三维建模软件(如AutoCAD、Solidworks等)绘制机床的各部件和装配关系,包括机架、滑块、导轨等。
然后,使用虚拟现实软件(如Unity、Unreal Engine等)将机床模型导入到虚拟环境中,完成机床虚拟模型的建立。
2.运动仿真与碰撞检测:利用虚拟现实软件中的物理引擎,对机床的运动进行仿真,包括滑块的上下运动、工件的旋转等。
通过设置适当的运动参数和物理特性,可以在虚拟环境中模拟出真实的机床运动。
同时,利用碰撞检测算法,检测机床部件之间的碰撞情况,以避免装配过程中的冲突和损坏。
3.用户交互与反馈:虚拟装配过程中,可以通过HTC头戴式显示器和手柄等设备,与模拟环境进行实时交互,例如通过手柄拾取和放置零件,调整机床的运动参数等。
同时,还可以通过视觉和听觉反馈,向用户提供装配过程的实时信息,以增强用户体验和操作准确性。
三、机床虚拟装配运动仿真的优势1.减少装配时间和成本:通过虚拟模拟和运动仿真,可以事先排除装配过程中的冲突和错误,提前解决问题,减少调试时间和成本。
- 1、下载文档前请自行甄别文档内容的完整性,平台不提供额外的编辑、内容补充、找答案等附加服务。
- 2、"仅部分预览"的文档,不可在线预览部分如存在完整性等问题,可反馈申请退款(可完整预览的文档不适用该条件!)。
- 3、如文档侵犯您的权益,请联系客服反馈,我们会尽快为您处理(人工客服工作时间:9:00-18:30)。
机床运动仿真
一、前言
计算机仿真技术就应用计算机对系统的数学模型求解,以研究实际系统运行的性能的技术,由于计算机仿真是应用计算机中的数学模型做实验,与用实物做实验比较,具有经济、安全、实验周期短等特点。
机床制造业是其它机械加工行业的基础行业,机床做为其它机械产品制造的基础、其作为"母机"作用的重要性是鲜而易见的。
在机床的设计制造过程中引进仿真技术可以大大缩短机床的研发周期、降低机床的研发成本、提高机床的可靠性。
本文通过对一简化机床从建立模型、装配、到机床运动仿真、分析的全过程,简述了仿真技术在机床行业机床设计过程中的应用。
二、机床建模、装配、仿真、分析
2.1机床设计目标确定:
假设该机床要实现螺纹加工的功能
2.2设计目标分析
机床要实现螺纹加工,就要求,机床的主运动部分和工件进给部分有一个确定的传动关系,
1(主轴)×U×T1 = S
U--从主轴到丝杠的总传动比;
T1--机床丝杠的导程(例如:CA6140型机床的T1=12mm);
S--被加工螺纹的导程;
1(主轴)--主轴转动一转。
由上式可知,改变U就能加工出不同的螺纹。
最终由以上公式把机床模型简化为:
齿轮组、蜗轮蜗杆传动组、齿轮齿条传动组;
其中数U由齿轮组实现;
参数T1由蜗轮蜗杆传动组、齿轮齿条传动组共同实现,也可由丝杠螺母组实现,本文采用前者。
软件选择:Pro/ENGINEER,Pro/Mechanism
Pro/ENGINEER作为一款集成了CAD/CAM/CAE/PDM的工程软件,其三维建模能力很强,而其中的Mechanism模块又具有运动/动力学仿真、动态、静态、力平衡等多种仿真、分析功能,并且Mechanism提供了各种机构配合方式,能够进
行连杆机构,凸轮机构、齿轮机构、齿轮系、螺旋机构、多种复合机构等进行仿真、分析。
2.3设计
2.3.1建模
用Pro/E中的"从方程"方法应用渐开线方程实现齿轮齿型轮廓的建模
正齿轮设计的渐开线方程为:
将其转化为Pro/E中的关系式为:
r=DB/2
theta=t×45
x=r*cos(theta)+sin(theta)*theta*pi/180
x=r*sin(theta)-cos(theta)*theta*pi/180
z=0
由以上公式在Pro/E中就可建立出一般正齿轮模型:
在建立了模型之后可以应用Pro/E中参数设计功能为齿轮各个尺寸参数建立"关系",样就可由一个齿轮实现相同类型、不同尺寸齿轮的建模了。
与之配合的正齿轮,只需修改一下"参数"中的数值就可完成建模。
蜗轮、蜗杆、齿条的建模方法和步骤与正齿轮建模基本相同,仅仅是蜗轮、蜗杆、齿条所用的齿廓方程与正齿轮不同而已。
蜗轮的齿廓方程为:
r=D5/2
theta=t*45
x=r*cos(theta)+sin(theta)*theta*pi/180
x=r*sin(theta)-cos(theta)*theta*pi/180
z=m*q/2
蜗杆的齿廓方程为:
1)螺线方程:
r=m*q/2
theta=t*tx*360
z=-t*la
2)渐开线方程:
r=D4/2
theta=t*60
x=r*cos(theta)+sin(theta)*theta*pi/180
x=r*sin(theta)-cos(theta)*theta*pi/180
z=0
齿条的剖面为一连续的梯形,建模较简单,无须方程。
就此实现了机床各个功能部件的建模。
2.3.2装配、仿真、分析
首先在Pro/E的装配模块中对机构进行组装然后转入Pro/Mechanism中进行仿真分析,由于机构比较复杂、可能出现的错误比较多,所以采用部分装配再仿真、分析,仿真、分析数据正确后再加入新部件,再分析、仿真的方法逐渐由部分到整体的实现机床模型的正确建立。
在Pro/Mechanism中可进行的分析测量的量有:位置、速度、加速度、连接反作用、净负荷、冲力。
在Pro/Mechanism中测量对模型各种运动参数进行测量,假如不符合要求,则重新建立模型,再次进行仿真、分析,直至模型达到设计要求为止。
由仿真、分析结果进行改进再仿真,直至达到设计要求,接着进行各部分功能细化,机床样机最终定型。
三、结论
本文借助Pro/E实现了对简化机床从建立模型、装配到仿真分析的全过程,最终实现了对机床样机的设计。
借助像Pro/E这样的三维CAD软件和仿真技术,大大缩短了新产品设计的周期;而且通过对数字化模型的分析可以提早发现产品的缺陷并加以修改,达到了优化设计的目的;直接在数字化模型上进行各种运动及材料特性的仿真分析而不用投入大量的力、财力进行产品试制,有效节约了生产成本。
应用仿真技术对机床行业,及各个机械行业都是大有裨益的。
发布时间:2006-11-27
∙相关主题关键字:
∙机床
∙仿真
∙theta
∙分析。