舍弗勒轴承失效分析
常见轴承失效分析

对常见轴承失效分析的探讨摘要:轴承是社会生产最为关键的的零部件之一,同时也是最为损伤的零部件之一,所以,对于轴承的失效分析尤为重要,本文结合作者的工作经验主要阐述了轴承的失效分析,仅供参考。
关键词:轴承;失效分析一、轴承在生产中概述轴承是广泛应用于机械设备的零部件,是配套的精密零件,同时也是最易损坏的元件之一。
按轴承工作的摩擦性质来分,可分为滑动摩擦轴承(简称滑动轴承)和滚动摩擦轴承(简称滚动轴承)。
其中滚动轴承最常见,它一般由内、外两个套圈、一组滚动体和一个保持架组成。
本文结合工程案例主要分析了轴承的失效形式以及其改进的原因。
二、轴承损伤和失效的形式轴承在工作中丧失其规定的功能,导致故障或不能正常工作的现象称为失效。
轴承的失效可分为正常失效和早期失效两种。
按其损伤机理大致可分为:接触疲劳失效、磨损失效、断裂失效、塑性变形失效、腐蚀失效和游隙变化失效等几种基本形式。
1.接触疲劳失效接触疲劳失效是滚动轴承最常见的失效形式,是轴承表面受到交变应力的作用而产生的失效。
滚动轴承在高接触应力作用下,通过多次的应力循环后,在套圈或滚动体工作表面的局部区域产生小片或小块金属剥落,形成麻点或凹坑,从而引起振动,噪声增大,温度升高,磨损加剧,最终导致轴承不能正常工作的现象称为接触疲劳失效。
根据材质、工作条件、润滑条件等因素,接触疲劳失效可分为点蚀与剥落。
点蚀是由于表面出现麻点而失效,通常有非进展性和进展性之分,前者通常不影响轴承的使用,但如果使用一段时间后,由于某种原因,使点蚀不断扩展,进而形成进展性点蚀,表面会出现大面积的微剥落,最后使轴承失效。
剥落是在次表面产生疲劳裂纹,然后扩展至表面,使金属成片状脱落,可分为浅层剥落和硬化层剥落。
2.磨损失效工作过程中,轴承零件之间相对滑动摩擦导致工作表面金属不断损失的现象叫磨损。
持续的磨损会使轴承零件尺寸和形状变化,配合游隙增大,工作表面形貌恶化而丧失旋转精度,由此引起工作温度升高、振动、噪声、摩擦力矩增大等,导致轴承不能正常工作的现象叫磨损失效。
INA轴承的精度检测及调整
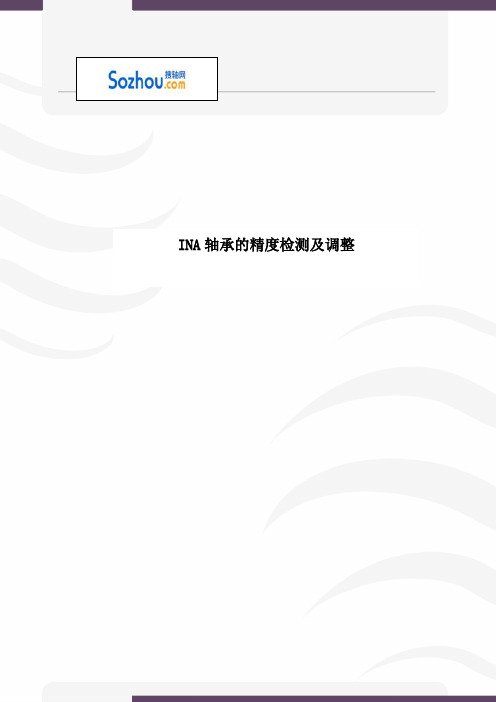
INA轴承的精度检测及调整INA品牌介绍INA轴承公司隶属于舍弗勒集团旗下的德国INA轴承公司,成立于1946年,总部位于德国的纽伦堡。
德国INA轴承公司自成立以来,一直致力于产品的创新,以满足客户之所需,并提供高质量的保证,使之成为全球滚动轴承首要供应商以及汽车制造商公认的合作伙伴。
X-life作为FAG和INA的优质产品对设计工程师提供了全新的设计机遇。
随着当前先进制造技术的应用,滚动体和滚道的整个接触表面变得更好,更加一致。
因此,在相同的载荷条件下,滚动体和与其配合的表面的应力,会有显著降低。
因此,在相同工作条件下,X-life 轴承工作寿命会更长。
另一方面,在相同额定寿命条件下,可以承受更高的载荷。
在这些优化的特征下,X-life轴承开启了新的应用前景,例如降低支承轴承的尺寸。
而且,更高的性价比最终增加了轴承支承整个的经济性。
应用领域德国INA轴承的产品涉及行业包括:农业机械行业、建筑行业、水力和风力工程行业、工程机械行业、机床及制造机械行业、材料处理及包装业、港口工程行业、电动工具行业、变速箱行业、半导体行业、泵与风机行业、工业机器人及自动化行业、橡胶、塑料及化工行业、纺织行业、拖拉机行业、木工机械行业等。
在这些行业中,德国INA轴承都得到了广泛的应用。
技术品质精湛的滚动轴承技术,工艺先进的生产工厂,优质超群的质量标准使INA轴承在全球享有盛名且经久不衰。
在千百万次实际应用中已经得到充分证明。
INA轴承产品是兼有成本和效益的可靠机械之件,INA轴承产品是兼有成本和效率的可靠机械之件,INA产品为旋转运动和直线运动乃至各种专用技术提供各种不同尺寸系列。
为各行各种专用技术提供各不同尺寸系列,为各行业的设计人员提供了难能可贵的技术支援。
润滑方法一般工作INA轴承采用稀油脂及油雾润滑方式,这些润滑方式具有各自的特点,但要满足现代化高速、高负荷的工作辊轴承的工作要求,则可认为较合适的是油汽润滑。
滚动轴承常见的失效形式和原因分析范文

滚动轴承常见的失效形式及原因分析+浪逐风尖2008-11-05 10:55滚动轴承在使用过程中,由于很多原因造成其性能指标达不到使用要求时就产生了失效或损坏.常见的失效形式有疲劳剥落、磨损、塑性变形、腐蚀、烧伤、电腐蚀、保持架损坏等。
一,疲劳剥落疲劳有许多类型,对于滚动轴承来说主要是指接触疲劳。
滚动轴承套圈各滚动体表面在接触应力的反复作用下,其滚动表面金属从金属基体呈点状或片状剥落下来的现象称为疲劳剥落。
点蚀也是由于材料疲劳引起一种疲劳现象,但形状尺寸很小,点蚀扩展后将形成疲劳剥落。
疲劳剥落的形态特征一般具有一定的深度和面积,使滚动表面呈凹凸不平的鳞状,有尖锐的沟角.通常呈显疲劳扩展特征的海滩装纹路.产生部位主要出现在套圈和滚动体的滚动表面.轴承疲劳失效的机理很复杂,也出现了多种分析理论,如最大静态剪应力理论、最大动态剪应力理论、切向力理论、表面微小裂纹理论、油膜剥落理论、沟道表面弯曲理论、热应力理论等。
这些理论中没有一个理论能够全面解释疲劳的各种现象,只能对其中的部分现象作出解释。
目前对疲劳失效机理比较统一的观点有:1、次表面起源型次表面起源型认为轴承在滚动接触部位形成油膜的条件下运转时,滚动表面是以内部(次表面)为起源产生的疲劳剥落。
2、表面起源型表面起源型认为轴承在滚动接触部位未形成油膜或在边界润滑状态下运转时,滚动表面是以表面为起源产生的疲劳剥落。
3、工程模型工程模型认为在一般工作条件下,轴承的疲劳是次表面起源型和表面起源型共同作用的结果。
疲劳产生的原因错综复杂,影响因素也很多,有与轴承制造有关的因素,如产品设计、材料选用、制造工艺和制造质量等;也有与轴承使用有关的因素,如轴承选型、安装、配合、润滑、密封、维护等。
具体因素如下:A、制造因素1、产品结构设计的影响产品的结构设计是根据使用性能目标值来确定的,这些目标值如载荷容量、寿命、精度、可靠性、振动、磨损、摩擦力矩等。
在设计时,由于各种原因,会造成产品设计与使用的不适用或脱节,甚至偏离了目标值,这种情况很容易造成产品的早期失效。
浅谈轴承失效原因分析

轴承失效原因分析滚动轴承在使用过程中,由于很多原因造成其性能指标达不到使用要求时就产生了失效或损坏.常见的失效形式有疲劳剥落、磨损、塑性变形、腐蚀、烧伤、电腐蚀、保持架损坏等。
一,疲劳剥落疲劳有许多类型,对于滚动轴承来说主要是指接触疲劳。
滚动轴承套圈各滚动体表面在接触应力的反复作用下,其滚动表面金属从金属基体呈点状或片状剥落下来的现象称为疲劳剥落。
点蚀也是由于材料疲劳引起一种疲劳现象,但形状尺寸很小,点蚀扩展后将形成疲劳剥落。
疲劳剥落的形态特征一般具有一定的深度和面积,使滚动表面呈凹凸不平的鳞状,有尖锐的沟角.通常呈显疲劳扩展特征的海滩装纹路.产生部位主要出现在套圈和滚动体的滚动表面.轴承疲劳失效的机理很复杂,也出现了多种分析理论,如最大静态剪应力理论、最大动态剪应力理论、切向力理论、表面微小裂纹理论、油膜剥落理论、沟道表面弯曲理论、热应力理论等。
这些理论中没有一个理论能够全面解释疲劳的各种现象,只能对其中的部分现象作出解释。
目前对疲劳失效机理比较统一的观点有:1、次表面起源型次表面起源型认为轴承在滚动接触部位形成油膜的条件下运转时,滚动表面是以内部(次表面)为起源产生的疲劳剥落。
2、表面起源型表面起源型认为轴承在滚动接触部位未形成油膜或在边界润滑状态下运转时,滚动表面是以表面为起源产生的疲劳剥落。
3、工程模型工程模型认为在一般工作条件下,轴承的疲劳是次表面起源型和表面起源型共同作用的结果。
疲劳产生的原因错综复杂,影响因素也很多,有与轴承制造有关的因素,如产品设计、材料选用、制造工艺和制造质量等;也有与轴承使用有关的因素,如轴承选型、安装、配合、润滑、密封、维护等。
具体因素如下:A、制造因素1、产品结构设计的影响产品的结构设计是根据使用性能目标值来确定的,这些目标值如载荷容量、寿命、精度、可靠性、振动、磨损、摩擦力矩等。
在设计时,由于各种原因,会造成产品设计与使用的不适用或脱节,甚至偏离了目标值,这种情况很容易造成产品的早期失效。
轴承的失效分析

原因:・电流通过后产生的火花
对策业时安装有效的接地
故障形态示例12
原来如此!
现象:卡具材料硬度低,因外力及磨损等造成破损的现象。
原因:・瞬时负载过大、振动、冲击 对策:・调整负载条件及运行条件 ・润滑不良 ・调整润滑方法及润滑剂 ・急剧的旋转变动(急加速、急减速、 急停) 返回
故障形态示例6
原来如此!
现象:裂纹是微细裂痕、龟裂、割裂等损伤的总称。 缺口是指内圈、外圈及滚动部分局部缺失的状态。
原因 ・过载及冲击 ・过盈量过大 ・鳞片及烧熔现象加剧 ・安装时的打击及操作不 良
对策 ・调整、改进负载条件 ・调整过盈量 ・改进操作
原来如此!
故障形态示例7
现象:微振磨损是轴承受到振动时发生的一种磨损现象,其特征是形成色如铁锈 的摩擦锈斑。轨道面发生的微振磨损属于转动体间距磨损,看上去类似 布氏硬度压痕,因此也称为虚假表面变形(疑似压痕)。
原因 ・过盈量不足 ・轴承停止时的振动、摇摆、 输送中的振动
对策 ・加大过盈量 ・改进轴、轴衬的固定方法 ・采用粘稠度高的润滑脂
故障形态示例8
原来如此!
现象:锈蚀是金属表面在化学作用下生成的氧化物、氢氧化物皮膜。 腐蚀是与酸及碱液之间产生的化学作用而造成的侵蚀、氧化、 溶解现象。
原因 ・水、腐蚀性物质的浸入 ・空气中的水分结露 ・包装、保管状态不良、直接与手接触
故障形态示例10
原来如此!
现象:蠕变即内圈或外圈沿圆周方向发生移动的现象,是一种 发生在镜面、磨砂面并时而伴随粘咬的有害滑动现象。
原因:・过盈量不足 ・套筒紧固不足
对策:・加大内圈与轴或外圈与轴衬的过盈量 ・调整套筒紧固转矩 ・提高轴、轴衬的加工精度 ・提高轴衬刚性
轴承失效分析

TWB
ISO9002
野蛮安装,使两个挡边被打破, 滚子有伤痕。
安 装 不当
TWB
ISO9002
敲击使内圈端面破裂。同时使外圈滚道和滚子受损
安 装 不当
TWB
ISO9002
轴承内外圈断裂 由于安装时,轴上夹杂有灰尘或毛刺会使内圈壁面应力增大,当轴承受到很大的冲击交变载荷时,局部过载现象出现而断裂 。 轴承座内表面有部分凸面,当轴承受到很大的突发冲击载荷时,凸面处受力,使外圈断裂。
ISO9002
演示疲劳剥落的原理
A.从周期性滚子挤压滚道的形式
B. 原始夹杂物碎片
C. 碎片延升到表面
D. 碎片扩散
E. 波浪般的痕迹
F. 逐步蔓延
G. 典型的放射蔓延
疲劳剥落
TWB
ISO9002
疲劳剥落是轴承正常失效的形式。本图所示是典型失效的内圈,粗糙的表面与润滑失效有明显的差别。另外,可见受力情况也很好,两条滚道上的剥落区一样长。
TWB
二、失效分析的意义 失效分析可以找出机械故障部位、失效原因和机理,从而提供产品改进方向和防止问题发生的意见,它为设计者、生产者、使用者找出故障原因和预防措施。是提高产品质量的重要手段,是一门跨学科的综合性技术。失效分析结果需反馈到设计和生产中去,这样是为了保证产品可靠性和提高产品质量的一种重要手段。
常见轴承失效案例分析

润滑不良可能是由于润滑油选用不当、润滑油量不足、润滑油污染或润滑系统故障等原因造成的。当轴承缺乏良好的润滑时,金属与金属之间的直接接触会增加,导致摩擦和磨损迅速增加,进而引起轴承过热、运转困难或噪声等问题。
润滑不良导致的轴承失效
水分和杂质的侵入
水分和杂质侵入轴承会导致轴承生锈、运转不灵活和噪声等问题,严重影响轴承的使用寿命。
详细描述Βιβλιοθήκη 轴承材料的疲劳失效VS
磨损失效是指轴承在运转过程中,由于摩擦磨损导致材料逐渐损失的现象。
详细描述
磨损失效通常是由于润滑不良、异物进入、材料硬度过大或表面粗糙度不均匀等原因引起的。随着材料损失的增加,轴承的精度和性能会逐渐降低,最终可能导致轴承失效。为了减少磨损失效,需要定期维护和更换润滑油,保持轴承周围环境的清洁度,并选择合适的材料和表面处理技术。
总结词
轴承材料的磨损失效
总结词
腐蚀失效是指轴承材料受到化学腐蚀或电化学腐蚀而导致的性能下降或损坏的现象。
详细描述
腐蚀失效通常是由于轴承周围环境中的腐蚀性介质、潮湿空气、盐雾或酸碱溶液等引起的。腐蚀会导致轴承材料表面出现坑蚀、斑点或裂纹,严重时甚至可使轴承完全失效。为了防止腐蚀失效,需要选择耐腐蚀的材料和表面处理技术,同时保持轴承周围环境的干燥和清洁度,定期进行防锈处理和维护。
轴承结构的热设计不当
详细描述
总结词
总结词
轴承结构的刚度不足会影响其稳定性和使用寿命。
详细描述
轴承结构的刚度不足会导致轴承在运转过程中发生变形,影响其旋转精度和稳定性,从而降低其使用寿命。同时,刚度不足还可能导致轴承内部间隙增大,增加摩擦和磨损。
轴承结构的刚度不足
04
轴承使用环境失效案例
汽车轮毂轴承疲劳失效分析及预防研究

汽车轮毂轴承疲劳失效分析及预防研究中文摘要汽车轮毂轴承疲劳失效分析及预防研究中文摘要汽车轮毂轴承是汽车底盘及传动机构中非常重要的零部件之一,作用主要是承受汽车的重量及为轮毂的传动提供精确的向导。
轮毂轴承既承受径向载荷又承受轴向载荷,当汽车在斜面上转弯时还受到轴向力产生的弯矩作用,是一个非常重要的安全件,同时也是易损坏的零部件。
轴承的失效模式按照ISO 15243:2004(E)中的定义主要有疲劳、磨损、腐蚀、电腐蚀、塑性变形和破裂。
在正常使用条件下,轴承主要的失效模式是疲劳。
随着国内汽车产量不断攀升,2009年已经突破1000万台,轮毂轴承的产能也急剧增长,随之而来的汽车使用与保养尤其是属于安全件的轮毂轴承的使用及保养注意事项也需要有专门的人员参与研究。
通过对国外第一和第二代轮毂轴承(FAG)失效模式的统计和分析发现,在保修期内,最常见的失效模式是疲劳损伤,包括局部浅层疲劳和表层疲劳两种失效形式,具体表现为内外圈滚道和滚动体表面有疲劳裂纹或材质剥落。
结合轮毂轴承工作特点及对失效轴承的组织、硬度、材料和润滑状况分析,提出造成轴承疲劳失效的原因大多与轴承设计、轴承体材质、工艺关系甚小,而润滑不良致使润滑油膜形成不理想或游隙过大致使接触面滑动时,除在接触表面存在赫兹应力,还会在接触表面下方产生交变剪切应力,这种剪切应力会导致表面的材质疲劳而产生疲劳裂纹,然后扩展到表面形成材质剥落。
本文通过对汽车轮毂轴承零组件设计及润滑系统的客观分析以及对轮毂轴承疲劳失效成因的详细阐述,目的希望汽车使用者能更好的去预防疲劳失效,避免造成更多的,不必要的损失。
关键词:轮毂轴承;FAG;疲劳失效;滚道;滚动体;游隙;赫兹应力作者:陈雪峰指导教师:卫瑞元Abstract Failure Analysis & Prevention of Wheel bearing of Automobile due to FatigueFailure Analysis & Prevention of Wheel bearing ofAutomobile due to FatigueAbstractWheel bearing is one of the most important part in chassis and transmission of the Vehicle, which stands the weight and guides. On wheel bearing there are different force and torque, it’s a part related with safety.About deformation is described as ISO 15243:2004(E), there are fatigue failure, wear limit, corrosion wear, plastic deformation and broken, mostly is fatigue failure.With the development of the automotive industry, the demand of wheel wearing raises rapidly. So more and more people concern with the bearing.Analyzing the data of FAG, within the warranty there are deformations, partial shallow fatigue and surface, which can be found at wrinkle and material peeling from inner and outer trail and rolling surface. According to a series of FAG about metallographic structure, hardness and lubrication, This thesis concludes the result proposes that such failures are independent of material choice and manufacturing technology, the main cause are due insufficient lubrication and excessive clearance, besides Hertz force the varying stress are applied. This stress can cause surface material fatigue, as well as wrinkles and material peeling off.In this thesis, analyses the causes of the deformation, and suggests the user how to use the bearing efficient.Key words: Wheel bearing,FAG, fatigue failure, raceway, rolling elements, clearance, Hertz stressWritten by:Chen XuefengSupervised by:Wei RuiYuan苏州大学学位论文独创性声明及使用授权声明学位论文独创性声明本人郑重声明:所提交的学位论文是本人在导师的指导下,独立进行研究工作所取得的成果。
轴承失效原因及改善方法

轴承失效原因及改善方法随着当今以工业生产居多的日新月异社会市场经济的飞速发展,相关的工业也暴露出了一系列潜在的结构性问题,其中就包括了大量机械设备零部件使用不当造成资源浪费。
本文零部件中最具代表的轴承为例,分多方面详细了轴承各种失效的可能原因,并对不同的失效方法提出过热了不同针对性的明显改善方法,希望能对相关的工业技术操作人员带来的参考价值,进而能更好地使用轴承,降低社会资源的浪费,让机械设备上的每一个零部件都能够打造出出更大的价值。
<b>轴承是机械设备上的尤为最常用零件,是机械设备运转的核心保证,中会同样也是机械设备中曾极易失效的零部件之一。
在当今工厂的机械设备中,大型机械设备的零部件多采用滚动摩擦组件轴承,一方面由于其相对于滑动摩擦轴承较小极小的摩擦阻力,另一方面也是简易由于其结构的轻便性。
但是对于刮伤滚动轴承这种极易损坏的零部件而言,如果使用方法存在一定缺陷,就极容易造成轴承失效继而导致运转失灵。
失效的原因往往并不单一,而是由人工因素和自然因素多方面形成。
所以,相关技术工作人员应加强自身对于轴承结构的知晓,并熟练掌握安装和使用轴承的正确方法,进而了解垫圈轴承出现异常的多种可能性及其原因,并采取相对应的改善工具,才能延长轴承的使用年限,创造出更大的使用价值。
轴承故障原因类别工业中所采用的轴承,无论是滑动轴承还是滚动轴承,均都会有一定正常的使用年限。
超过这个使用单位成本以后,轴承才会因重复使用过度而正常满足要求报废,这个使用年资我们称之为轴承故障中正常的“疲劳寿命”。
然而从实际情况看来,可以达到正常达致使用年限的轴承并不多见,大部分的轴承都“英年早逝”,由于使用不当或多种自然意外受到损伤,从而导致轴承归零,继而导致机械设备出现故障。
这种并未达到使用年限就发生故障导致失效的情况,由于与其疲劳寿命的定义相反,工业技术操作人员多视作将其称为轴承故障。
引起轴承故障的原因是多种多样的,从表格中不难看出,轴承的失效原因中,不充分的润滑和轴承未能与机器接触良好是关键。
轴承失效分析

滚动轴承的失效原因 只有大约0.35 %的滚动轴承没有达到预期的寿命。
3.2 配合面状况
配合面的状况可以反映轴承套圈在轴和轴承座里的支撑情况,我们由此可以得出很多推断。套 圈相对配合面的转动会引起异音。它们也能导致微动腐蚀和磨损,从而进一步使润滑剂受到腐蚀 性和研磨性微粒的污染。另外随着套圈的支撑情况进一步恶化,微动腐蚀会使拆卸变得困难。 3.2.1 微动腐蚀 现象: 配合面上有黑褐色的拖痕,偶尔在靠近轴承或在润滑剂里也能发现棕色磨损物质。配合面发 生磨损(内孔,外圈外表面),对旋转件(通常是轴)来说有可能疲劳断裂,对静止件(通常是 轴承座)可能会破坏轴承的功能,见图4。 从这些微动腐蚀情况,通常可以推断出承载区的位臵 和尺寸及套圈的蠕动情况,见图5。
图一
图二
图三
1.2.2 局部损坏
轴承的局部损坏比如由滚动体引起的凹痕、静态腐蚀或断裂,都能够通过振动测量 及时发现这些问题。通过路径、速度和加速度传感器记录循环运动下的凹坑引起的 振动波。根据运转状况和期望的可信度,这些信号可以不同的方式做进一步处理。 最常见的是: – 测量有效值 – 测量振动值 – 通过包络检波进行信号分析 经验表明后者的可靠性和适用性更强。用一种特殊的信号处理方式,甚至可以找到 损坏的轴承部件。 (如下例所示) 在0到200 Hz间的包络信号频谱,下面: 完好的轴承;上面:损坏的轴承 nIR 内圈转速[min–1] 、fIR 内圈信号频率(循环频率) [Hz]
3、对拆下的轴承评估运转特性和 损坏情况
轴承失效不仅能揭示单个滚动轴承的失效,而且也能表明轴承布臵是否合理。 问题轴承拆卸的越早,轴承失效原因就能被发现的越早。保证轴承配臵平稳运行 的先决条件是:运行、环境条件和配臵中的所有部件(轴承,配合件,润滑剂, 密封)正确的配臵。轴承失效原因并不总单独存在于轴承本身。由于轴承材料和 生产失误造成的轴承失效非常少。
RCFA-教材轴承失效分析

轴承失效分析概述轴承在正常的安装和润滑维护情况下,一直可以使用到轴承的工作表面因疲劳而引起材料剥落为止,即可以使用到轴承的计算寿命的终止有时还可以超过计算寿命的数倍。
而在实际的使用中,滚动轴承常常因过早的损坏而报废,轴承的过早损坏可以来自轴承的制造缺陷和轴承材料的不良,但更多的则来自轴承的使用不当、维护和润滑不良等。
要正确地找出轴承损坏的原因是很困难的,一个轻微损坏的轴承可以从轴承的使用情况,特别是轴承工作表面的磨损状况、磨损的轨迹等来分析其损坏的原因。
而一个损坏严重的轴承或是因轴承的突发事故完全损坏的轴承,往往是最终的破坏现象掩盖了初始的残骸,由于这些现象常常是人们容易混淆了轴承损坏的最主要原因,因此只能从轴承的工作条件载荷、转速、润滑、支撑的整体结构如轴承的配置、配合及损坏形式用推理分析的方法,及借助其它的科学分析手段来判断。
在轴承的实际使用中一般情况下没有必要去追究轴承的损坏原因,而应立足于轴承故障的早期诊断。
防止因轴承损坏和事故而引起的停机、停产和损坏设备的更大损失。
对于重要部位,则应认真地研究和分析轴承损坏的原因,并采取相应的有效措施。
轴承失效分析是一项很细致的技术工作,其主要包括:一、背景调查:1.轴承的运行工作状态参数,如载荷、转速及原始轴承的有关数据的分析和计算。
2.轴承安装部位的形位公差的测量,轴承和轴颈、轴壳配合情况的分析,轴承座的安装配合和使用情况的调查,轴承的安装和拆卸的方法是否正确。
3.轴承损坏前的异常现象,如振动、噪声、温升,电机的电流变化以及外部负荷的变化。
等等。
二、现场情况:1.现象及现场保护,先要保护已损坏的轴承部位的现场,在拆卸轴承前应先记下有关的情况,特别要记下轴承外(内)圈相对轴承座负载方向的位置。
对已损坏的轴承零件要尽量收集完整。
2.现场检查轴承的润滑情况,并取样分析。
特别要注意混入油脂中的颗粒状物体要作进一步的分析。
3.检查轴承的密封是否失效,检查是否有异物、水(汽)从密封处进入轴承。
轴承失效分析
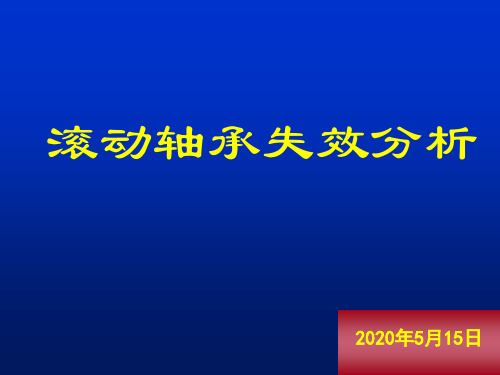
剥落 失效形式:滚动面材料剥离,呈明显的凹凸形状。 原因分析: 轴承在工作中承受的负荷超过极限负荷。 轴承安装不到位或安装倾斜,使轴承非正常运转。 轴或轴承座精度达不到要求,造成与轴承接触不 良(接触面小、过盈量超差、形位公差超差)。 游隙过小,滚动体运转卡阻。 异物进入轴承,轴承在运转时受阻。 轴承受到过大的轴向力,使轴承非正常运转 (球轴承的滚动体不在沟底,球面滚轴承一列滚 动体受力)。 异常高温造成轴承硬度下降。
内圈沿轴向产生裂纹。如果裂口呈弧形,表明裂纹形成 于轴承运转中(持续的运转可能导致块状断裂)。如果裂 口边缘非常锋利,表明裂纹产生于装配过程中。
原因分析:
轴承有滑动,固定的内圈与轴有相对转动,润滑不足, 配合过紧,,轴圆度超差,回转部件表面有擦伤等。
预防措施:
改善润滑,如:加入添加剂,增加润滑油量,减少油中 杂质或水分的含量等。选择合适的配合公差。
裂纹 失效形式:轴承零件出现裂纹,甚至断裂、掉块。 原因分析: 轴承在工作中承受的负荷超过极限负荷。 安装轴承时敲击力过大。 轴的尺寸过大,与轴承内径过盈量超差。 轴的精度未达到要求,尺寸超差与轴承内径的过 盈过大造成。 材质不合格,存在缺陷裂纹。 轴承在热处理时出现淬火裂纹。 加工轴承零件时增大磨削量而产生磨削烧伤。
点蚀 失效形式:产生于滚动接触面上,呈黑色针孔状 凹坑,有一定深度,个别存在或密集分布。 原因分析:润滑不良时,在滚动接触应力的循环 作用下,金属亚表层夹杂物或碳化物形成应力集 中,进而产生微观裂纹,并逐渐发展成凹坑状的 微小剥离。或者润滑剂含杂质,或者密封不良。 磨耗 失效形式:产生于滚动接触面上或引导面上,呈 磨合状的浅沟槽,表面光亮。随滚动接触表面磨 耗的发展,轴承游隙增大。 原因分析:细微颗粒物进入轴承或润滑不良,在 滑动摩擦的作用下,零件接触处金属表面材料被 磨掉。
从失效案例分析轴承的早期失效

从失效案例分析轴承的早期失效随着社会的不断发展,工业上的机械化也在不断的进步。
特别是近几十年,科学技术的蓬勃发展,更带动了工业上的迅速发展。
在现代化的机电行业中,轴承这个基础工件的应用最为广泛。
不管是最普通的机械设备,还是高端的机电领域,轴承都是不可或缺的基础工件。
所以,在机械化建设的现代,能够确保轴承的正常工作是非常重要的,一定要保证轴承的设计能跟上机械化事业的进程。
标签:轴承失效;失效原因;案例分析随着社会经济的不断发展,工业领域也取得了飞跃式的进步。
在现代化的机械行业中,轴承的应用最广泛,从最普通的设备到高端的机电领域,都离不开轴承的支持,所以轴承能在各种不同的环境中保证正常的工作是相关的技术人员热切关注的问题之一。
为了跟上时代的进步,工业领域也在不断的发展、进步,轴承的应用技术也取得了相应的发展。
目前,国内的机械化生产中引进一些新型的轴承设计,推动了机械工程的发展,但同时,这些新型的轴承依然存在一些问题,比如轴承的早期失效。
1 轴承早期失效的主要原因及其形式1.1 轴承与其他工件之间的接触疲劳会造成轴承的早期失效。
轴承的这种接触疲劳主要发生在轴承的表面。
接触疲劳经常伴随着裂纹的產生,这种早期失效通常先从表面的最大切应力的地方开始,然后向其他部位扩展,造成整个表面的脱落,加速了轴承的早期失效。
1.2 各个工件之间的摩擦力会造成轴承的早期失效。
机械的运作会导致工件之间的磨损逐渐加剧,逐个损坏轴承的零件,最终会导致轴承失去尺寸上的精度,工件之间的磨损也会影响到工件形状的变化,失去工作中的精确度,影响工作的效果。
这种因为磨损造成轴承的早期失效是最普遍的失效方式之一,从形式上来看,这种方式主要分为磨粒磨损造成的失效和粘着磨损引起的轴承早期失效。
1.3 由于工件本身的缺陷以及载重过大造成轴承的断裂而引起的轴承早期失效。
如果机器出现突发状况或者安装、使用不当等等都会造成工件的缺陷断裂,所以在以后的工作、设计中,一定要注意加强轴承的质量控制。
解析轴承的潜在失效模式分析
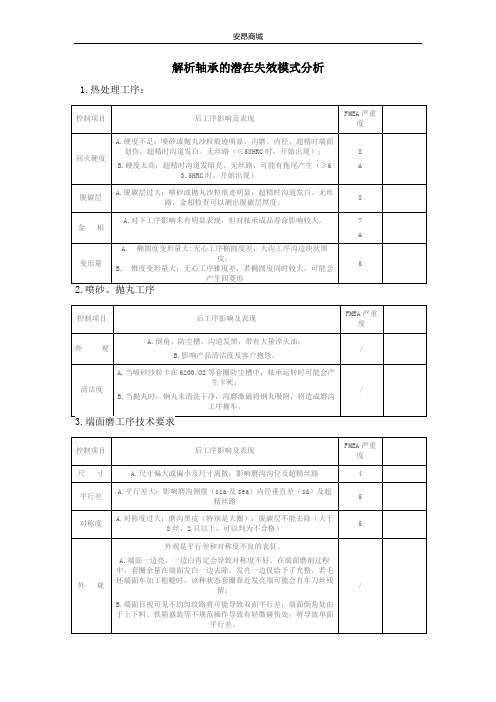
回火硬度
8 A
脱碳层
8 7 A
金
相
A. 变形量 B.
椭圆度变形量大:无心工序椭圆度差,大沟工序沟边块状黑 皮; 锥度变形量大:无心工序锥度差,若椭圆度同时较大,可能会 产生四菱形
5
2.喷砂、抛丸工序
控制项目 后工序影响及表现 A.倒角、防尘槽、沟道发黑,带有大量淬火油; B.影响产品清洁度及客户抱怨。 A.当喷砂沙粒卡在 6200/02 等套圈防尘槽中,轴承运转时可能会产 生卡死; B.当抛丸时,钢丸未清洗干净,沟磨激磁将钢丸吸附,将造成磨沟 工序撞车。 FMEA 严重 度 /
外
观
清洁度
/
3.端面磨工序技术要求
控制项目 尺 寸 后工序影响及表现 A.尺寸偏大或偏小及尺寸离散:影响磨沟沟位及超精丝路 A.平行差大:影响磨沟侧摆(sia 及 sea)内径垂直差(sd)及超 精丝路 A.对称度过大:磨沟黑皮(特别是大圈),脱碳层不能去除(大于 8 丝,2 只以上,可以判为不合格) 外观是平行差和对称度不良的表征。 A.端面一边亮,一边白肯定会导致对称度不好。在端面磨削过程 中,套圈余量在端面发白一边去除,发亮一边仅给予了光整。若毛 坯端面车加工粗糙时,该种状态套圈靠近发亮端可能会有车刀丝残 留; B.端面目视可见不均匀纹路将可能导致双面平行差,端面倒角处由 于上下料、铁箱盛装等不规范操作导致有轻微碰伤处,将导致单面 平行差。 FMEA 严重 度 4 5
曲
率
4Байду номын сангаас
安昂商城
um,最深可达 8um。 B.粗糙度过粗:超精时可能不能修复,留有白点; C.粗糙度过于光洁:超精深度超不下去。 残 磁 A.会造成超精工序撞车;带有残磁的套圈会吸引大量铁削,降低产 品清洁度;成品带有残磁,会使启动力矩增大。 波纹度又称振纹,其为系统刚性不足(机床床身刚性不足、电主轴 跳动大、砂轮切削能力弱、砂轮磨损不圆、砂轮裂纹、冷却液润滑 效果差等),自激振动与共振产生。在我公司,最常见为:砂轮在 磨削过程中,由于渗硫不均等原因,各个结合强度不一样,引起磨 粒脱落的快慢速度亦不一样,砂轮结合强度大的部分,磨粒不易脱 落,产生局部钝化。砂轮本身自然形成波纹状态,在磨削过程中引 起振动,产生振纹。 A.影响超精质量(振纹套圈若经超精后未修复,将残留有规律块状 砂轮花),振纹一般肉眼灯光下可见,同时刮色时可以看到段状刮 色浓、淡。在圆度仪上,滤波可见。 烧 伤 A.烧伤一般肉眼很难发现,必须用酸洗法检验。 由于刮色油物料与正常物料混料,或者刮色油物料未清洗干净,这 将导致超精后残留刮色油,如若半成品、成品清洗不净,将直接影 响轴承清洁度。 A.外圆划伤:外圆划伤,只要存在,不论能否在细磨修复,它都已 经在沟磨工序造成了沟磨圆度的较大或奇形怪状; 外 观 B.端面划伤:端面划伤可能由于端面工序粗糙度较大或者磁力较大 及靠山未修磨好等原因造成,流入下工序,可能会引起客户的抱 怨。 / 6 /
- 1、下载文档前请自行甄别文档内容的完整性,平台不提供额外的编辑、内容补充、找答案等附加服务。
- 2、"仅部分预览"的文档,不可在线预览部分如存在完整性等问题,可反馈申请退款(可完整预览的文档不适用该条件!)。
- 3、如文档侵犯您的权益,请联系客服反馈,我们会尽快为您处理(人工客服工作时间:9:00-18:30)。
剥落 Spalling
循环疲劳 Cyclic fatigue
内部杂质引起的剥落
Inclusion-origin spall
内部杂质引起的剥落
Inclusion-origin spall 盾形或细砾状痕迹Chevron or beach marks
表面损伤引起的剥落
Point surface-origin spall 典型的轴向扩展
带有隐患的运行轨迹
轴承座偏心(偏斜) 轴承座偏心(偏斜)
轴偏心(偏斜) 轴偏心(偏斜)
存在圆度偏差的轴承座
过度配合——预负荷
过度配合——预负荷 预负荷 过度配合
偏心径向负荷
不平衡负荷
滚动接触面- 滚动接触面-偏离运行轨道
偏斜 Misalignment
轴承座孔 HOUSING BORE 中心线
温度色变
» » » » »
150° -- 177° C 177° -- 205° C 205° -- 260° C + 260° C + 540° C
– 一般轴承可在温度达120° C 的条件下使用 – 过高的温度可导致硬度下降 – 大约降低2-4点洛氏硬度可减少寿命 50%
受热造成的裂痕
– 过度滑动和/或不 足的润滑 – 高磨擦热量 – 裂痕出现在滑动 方向的正确角度 上
疲劳损坏- 疲劳损坏-外部颗粒引起疲劳裂痕
检测到的初期阶段失效
经过1000小时运转后的失效
经过1200小时运转后的失效
在出现蚀损斑后如未及时发现,它会沿循环方向呈V型扩展, 在出现蚀损斑后如未及时发现,它会沿循环方向呈V型扩展,越来 沿循环方向呈 越大, 越大,导致轴承失效
疲劳损坏- 疲劳损坏-外来颗粒污染
疲劳损坏
对中不良引起疲劳裂痕
轴承运转轨迹偏移 滚道边缘受载区产生疲劳 磨损 补救措施: 补救措施: 调整轴承的安装位置,避 调整轴承的安装位置, 免静态过载和冲击载荷。 免静态过载和冲击载荷。
对磨磨损
(研磨磨损) 研磨磨损)
滚子与轨道的擦伤(粘性磨损) 滚子与轨道的擦伤(粘性磨损)
振动引起的磨损
原因: 原因 转速太快 保持架选型错误 补救措施: 补救措施 选择适合的保持架
保持架损坏
由于振动应力导致保持架铆接处断裂
球面滚子轴承保持架出现断裂现象
由于采用了不当的加热设备进行加热,导 致塑料保持架出现烧融现象
过载
– 静态或冲击负荷 – 塑性变形 – 滚动元件间隔出现凹陷现象 – 操作造成的损坏
失效原因: 轴承轴向过载,超过了最 大允许的赫兹应力
注意: 过载会导致轴承强烈破碎
滚动接触面-压痕 滚动接触面 压痕
圆柱滚子轴承受 高温导致压痕
原因分析: — 轴承的工作游隙太小(尤其对于高速旋转的轴承) — 润滑不当(润滑剂太多,搅油导致发热) — 由于外部过热,导致径向产生预紧力 — 由于保持架断裂,滚子的滚动受阻
过载导致保持架塑性变形
安装中出现的损坏(敲击过载) 安装中出现的损坏(敲击过载)
颗粒造成的凹痕
– 局部过载 – 颗粒的过度滚动 = 凹痕 – 由低碳钢/硬化钢/硬质矿物颗粒造成
操作造成的损坏
– 局部过载 – 由坚硬/锋利的物 体造成的刻痕
安装使用不当造成的失效
操作造成的损害
八、电蚀磨损
– 高电流 = 放电现 象 – 即时的本地加热 可导致熔化和/或 焊接现象的产生 – 放电痕达到100 µm
Typical, axial propagation
疲劳损坏
滚道表面出现与滚子节距相同的擦伤痕迹, 滚道表面出现与滚子节距相同的擦伤痕迹,滚子或滚 道变粗糟,表面材料的卷起。在对中不良的情况下, 道变粗糟,表面材料的卷起。在对中不良的情况下, 异物粘附在滚子上导致冷擦伤。 异物粘附在滚子上导致冷擦伤。
压痕和冲击
压痕 Brinnelling
假性压痕: 假性压痕:磨损 False brinnell:fretting
保持架损坏
现象:保持架边缘出现磨损 现象
原因: 原因 润滑剂中含有硬质颗粒 贫油或润滑剂选择错误 补救措施: 补救措施 确保装配环境清洁 过滤润滑剂 确保足够润滑
七、保持架损坏
现象: 现象:保持架外径面被轴承外圈擦伤
三、滚子与挡边接触面
正常运转情况下圆锥滚 子轴承的挡边运转痕迹
由于外界颗粒的侵入导 致挡边产生划痕
圆锥滚子轴承端面的划痕
滚子与挡边接触面
当滚子的端面与挡边接触时, 当滚子的端面与挡边接触时,在挡边或滚子 的端面上产生的咬粘现象
主要原因: 重载和/或高速下润滑不充分
滚子端面(与挡边) 滚子端面(与挡边)粘性磨损
滚子与挡边接触面
原因 球面滚子轴承上过大的轴向力 高温(热膨胀引起预载) 预防措施 恰当调整轴承安装位置 改善润滑 (提高润滑剂粘度, EP添加剂, 润滑剂量)
四、疲劳损坏
经典疲劳引起裂痕
症状: 轴承材料出现麻点或脱落,我们通常叫蚀损斑。 原因: 润滑不良(贫油),或受污物的作用而产生的。
由于滚珠的几何变形和弹性变形。在剧烈变化的荷载下润滑油膜破裂, 造成金属与金属的摩擦(球与滚道),引起接触表面由于粘连作用而发 生破裂,也就是蚀损斑。
轴承失效分析
一、配合面
圆柱滚子轴承内孔与轴产生磨损腐蚀
轴承内孔与轴慢慢 滑动造成抓痕
在外圈的固定的承 重点出现摩擦腐蚀
蠕动腐蚀
配合不当
现象 配合面上带有黑褐色斑点以及残留物 安装面磨损 运转噪声可能加剧 旋转部件可能发生断裂 原因 配合过松, 配合过松,导致配合件间产生微观相 对运动 轴或轴承座孔的形状偏差过大 预防、 预防、措施 选用合理的配合公差 提高轴或轴座的圆度和粗糙度 安装时在与轴承配合的部分涂敷合适 的润滑剂
二、滚动接触面出现的失效现象
从不同的运转轨迹可以 看出不同的载荷方式, 看出不同的载荷方式,是 点载荷还是圆周载荷
常规径向负荷区域
常规径向负荷区域
360°
150°
旋转内圈负荷
常规径向负荷区域
150°
360°
组合(径向和轴向) 组合(径向和轴向)负荷
轴向(推力) 轴向(推力)负荷
滚动接触面- 滚动接触面-偏离运行轨道
安装
S
U
E
E
NC
ES
INF L
污染
S
E
E
NC
ES
INF L
INF L
BE
A
R
G IN
PERFORM AN C
MANCE OR
轴承性能
F ER P
IN F
LUEN CES
IN
ES
INFL UENC
INFL UENC
ES
维护
S
E
E
NC
ES
INF L
S
E
NC
ES
INF L
UE
UE
NC
NC
INF L
U
CE AN M
疲劳剥落现象
边部偏载
润滑不当引起的表面初始疲劳
润滑不当造成磨损的过程
外部颗粒引起疲劳损坏 异物会造成研磨损伤、擦伤、槽痕、 异物会造成研磨损伤、擦伤、槽痕、圆周线痕或 碎屑污染等影响
补救措施: 补救措施: 1.彻底清理轴承及其配合件, 1.彻底清理轴承及其配合件,可能的话可进行涂 彻底清理轴承及其配合件 层处理结构, 改善密封结构 4.操作前冲洗油路, 4.操作前冲洗油路,过滤润滑油 操作前冲洗油路
电压过高引起的腐蚀现象
电蚀磨损——电压过高
电流通过引起的失效
过电流损坏
深沟球轴承在连续过电流的情况下造成外圈连续沟槽的条纹。
过电流损坏
连续过电流产生的连续条纹
电流腐蚀
过电流损坏
过电流主要是静电、接线错误、接地不 当、绝缘不够而造成轴承严重损伤,主 要表现为局部熔化造成凹坑或连续凹槽 导致噪音和振动。
判断分析步骤: 判断分析步骤:
分析轴承所在位置能承受径向还是轴向的力 判断轴承的运转轨迹 检查滚动体(如外圈直径和端面) 检查滚动体(如外圈直径和端面) 判断挡边与滚子或保持架的接触 判断保持架 判断轴承所在位置和接触面
失效原因查找
收集运行数据、监控数据 采集润滑剂样本 检查轴承环境 评估安装条件下的轴承状态 标记安装位置 卸下、标记并包装轴承和零件 检查轴承座
轴中心线
SHAFT
偏斜 Misalignment
小端面载荷集中Stress on small end
偏斜 Misalignment
不匀称磨损Uneven wear
滚动接触面-磨损痕迹 滚动接触面 磨损痕迹
深沟球轴承内径的运转轨迹倾斜 偏移) (偏移) 圆锥滚子轴承滚动接触面疲劳磨损
原因
轴承安装不当 贫油或润滑剂中有水分污 染 现象 低承载区滚道暗灰 高承载区压力抛光
Raceway滚道
Roller滚子
划 痕
润滑不当引起的擦伤 特征: 特征: — 滚子或滚道沿轴向出现磨痕 原因: 原因: — 没有形成承载油膜 — 润滑剂污染 补救措施: 补救措施: — 采用高粘度且含有EP添加剂的润滑 采用高粘度且含有EP添加剂的润滑 EP 剂 — 缩短润滑剂的更换周期 — 对润滑剂进行过滤 — 改善密封
BEAR I
NG
UE
UE
NC
NC
E
ARING PE RO BE
R
IN F
LUEN CES
IN
F
F
E LU
E LU
S NC E
INF L
U
S NC E
润滑
U
E
INF L
软质颗粒引起的凹痕较浅并有 较平的边缘突起