湿式磨机出力影响因素
影响砂磨机工作效率和质量的因素
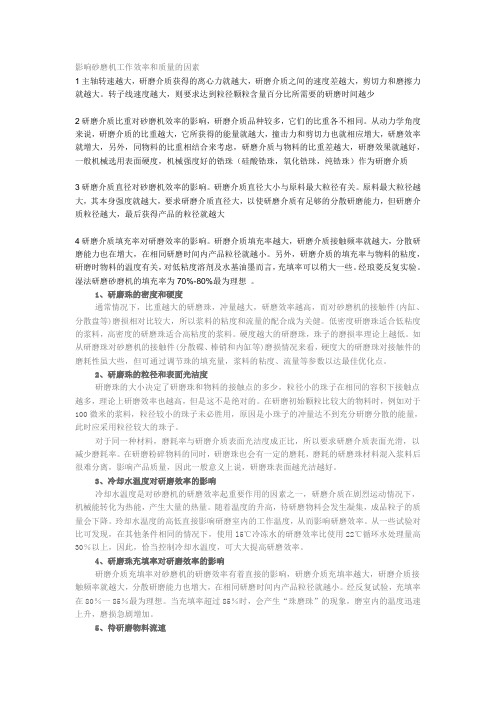
影响砂磨机工作效率和质量的因素1主轴转速越大,研磨介质获得的离心力就越大,研磨介质之间的速度差越大,剪切力和磨擦力就越大。
转子线速度越大,则要求达到粒径颗粒含量百分比所需要的研磨时间越少2研磨介质比重对砂磨机效率的影响,研磨介质品种较多,它们的比重各不相同。
从动力学角度来说,研磨介质的比重越大,它所获得的能量就越大,撞击力和剪切力也就相应增大,研磨效率就增大,另外,同物料的比重相结合来考虑,研磨介质与物料的比重差越大,研磨效果就越好,一般机械选用表面硬度,机械强度好的锆珠(硅酸锆珠,氧化锆珠,纯锆珠)作为研磨介质3研磨介质直径对砂磨机效率的影响。
研磨介质直径大小与原料最大粒径有关。
原料最大粒径越大,其本身强度就越大,要求研磨介质直径大,以使研磨介质有足够的分散研磨能力,但研磨介质粒径越大,最后获得产品的粒径就越大4研磨介质填充率对研磨效率的影响。
研磨介质填充率越大,研磨介质接触频率就越大,分散研磨能力也在增大,在相同研磨时间内产品粒径就越小。
另外,研磨介质的填充率与物料的粘度,研磨时物料的温度有关,对低粘度溶剂及水基油墨而言,充填率可以稍大一些。
经琅菱反复实验。
湿法研磨砂磨机的填充率为70%-80%最为理想。
1、研磨珠的密度和硬度通常情况下,比重越大的研磨珠,冲量越大,研磨效率越高,而对砂磨机的接触件(内缸、分散盘等)磨损相对比较大,所以浆料的粘度和流量的配合成为关健。
低密度研磨珠适合低粘度的浆料,高密度的研磨珠适合高粘度的浆料。
硬度越大的研磨珠,珠子的磨损率理论上越低。
如从研磨珠对砂磨机的接触件(分散碟、棒销和内缸等)磨损情况来看,硬度大的研磨珠对接触件的磨耗性虽大些,但可通过调节珠的填充量,浆料的粘度、流量等参数以达最佳优化点。
2、研磨珠的粒径和表面光洁度研磨珠的大小决定了研磨珠和物料的接触点的多少,粒径小的珠子在相同的容积下接触点越多,理论上研磨效率也越高,但是这不是绝对的。
在研磨初始颗粒比较大的物料时,例如对于100微米的浆料,粒径较小的珠子未必胜用,原因是小珠子的冲量达不到充分研磨分散的能量,此时应采用粒径较大的珠子。
影响磨机产质量的原因与对策(包含风扫磨)
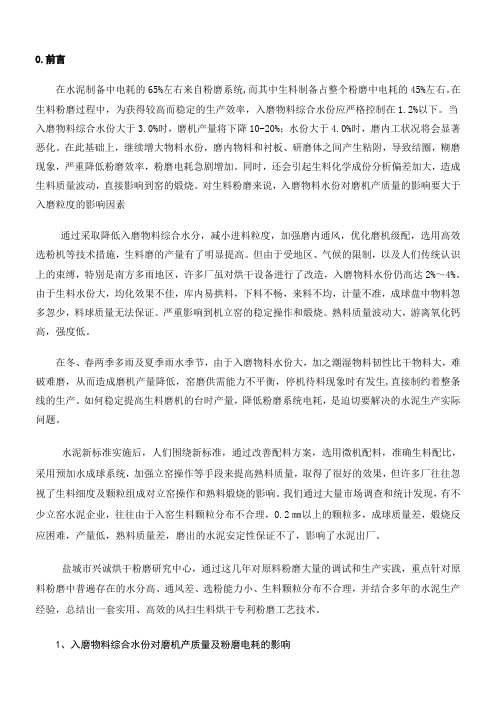
0.前言在水泥制备中电耗的65%左右来自粉磨系统,而其中生料制备占整个粉磨中电耗的45%左右。
在生料粉磨过程中,为获得较高而稳定的生产效率,入磨物料综合水份应严格控制在1.2%以下。
当入磨物料综合水份大于3.0%时,磨机产量将下降10-20%;水份大于4.0%时,磨内工状况将会显著恶化。
在此基础上,继续增大物料水份,磨内物料和衬板、研磨体之间产生粘附,导致结圈,糊磨现象,严重降低粉磨效率,粉磨电耗急剧增加。
同时,还会引起生料化学成份分析偏差加大,造成生料质量波动,直接影响到窑的煅烧。
对生料粉磨来说,入磨物料水份对磨机产质量的影响要大于入磨粒度的影响因素通过采取降低入磨物料综合水分,减小进料粒度,加强磨内通风,优化磨机级配,选用高效选粉机等技术措施,生料磨的产量有了明显提高。
但由于受地区、气候的限制,以及人们传统认识上的束缚,特别是南方多雨地区,许多厂虽对烘干设备进行了改造,入磨物料水份仍高达2%~4%。
由于生料水份大,均化效果不佳,库内易拱料,下料不畅,来料不均,计量不准,成球盘中物料忽多忽少,料球质量无法保证。
严重影响到机立窑的稳定操作和煅烧。
熟料质量波动大,游离氧化钙高,强度低。
在冬、春两季多雨及夏季雨水季节,由于入磨物料水份大,加之潮湿物料韧性比干物料大,难破难磨,从而造成磨机产量降低,窑磨供需能力不平衡,停机待料现象时有发生,直接制约着整条线的生产。
如何稳定提高生料磨机的台时产量,降低粉磨系统电耗,是迫切要解决的水泥生产实际问题。
水泥新标准实施后,人们围绕新标准,通过改善配料方案,选用微机配料,准确生料配比,采用预加水成球系统,加强立窑操作等手段来提高熟料质量,取得了很好的效果,但许多厂往往忽视了生料细度及颗粒组成对立窑操作和熟料煅烧的影响。
我们通过大量市场调查和统计发现,有不少立窑水泥企业,往往由于入窑生料颗粒分布不合理,0.2㎜以上的颗粒多,成球质量差,煅烧反应困难,产量低,熟料质量差,磨出的水泥安定性保证不了,影响了水泥出厂。
磨机产量低的原因
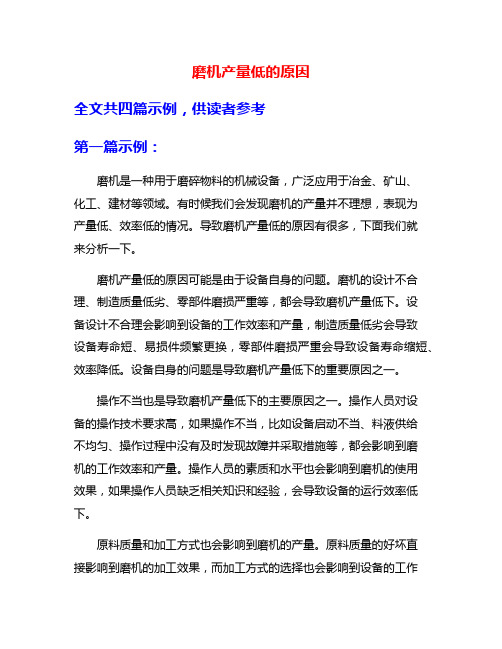
磨机产量低的原因全文共四篇示例,供读者参考第一篇示例:磨机是一种用于磨碎物料的机械设备,广泛应用于冶金、矿山、化工、建材等领域。
有时候我们会发现磨机的产量并不理想,表现为产量低、效率低的情况。
导致磨机产量低的原因有很多,下面我们就来分析一下。
磨机产量低的原因可能是由于设备自身的问题。
磨机的设计不合理、制造质量低劣、零部件磨损严重等,都会导致磨机产量低下。
设备设计不合理会影响到设备的工作效率和产量,制造质量低劣会导致设备寿命短、易损件频繁更换,零部件磨损严重会导致设备寿命缩短、效率降低。
设备自身的问题是导致磨机产量低下的重要原因之一。
操作不当也是导致磨机产量低下的主要原因之一。
操作人员对设备的操作技术要求高,如果操作不当,比如设备启动不当、料液供给不均匀、操作过程中没有及时发现故障并采取措施等,都会影响到磨机的工作效率和产量。
操作人员的素质和水平也会影响到磨机的使用效果,如果操作人员缺乏相关知识和经验,会导致设备的运行效率低下。
原料质量和加工方式也会影响到磨机的产量。
原料质量的好坏直接影响到磨机的加工效果,而加工方式的选择也会影响到设备的工作效率和产量。
如果原料质量较差,会导致设备难以达到预期的产量;如果选择了不合适的加工方式,设备的工作效率和产量也会受到影响。
导致磨机产量低的原因有很多,除了设备自身的问题外,操作不当、原料质量和加工方式等方面也会影响到设备的工作效率和产量。
为了提高磨机的产量,我们需要全面分析问题、找到原因、采取措施,以期实现设备的高效运行和产量的提升。
【2000字】第二篇示例:磨机产量低的原因还可能与原料的品质有关。
原料的质量直接影响到磨机的加工效果,如果原料质量不好,或者含有杂质、硬块等,都会导致磨机的工作效率低下。
生产环节中要严格控制原料的质量,确保原料符合要求,避免影响磨机的正常工作。
磨机产量低的原因还可能与操作人员的技术水平有关。
磨机的操作需要一定的技术和经验,如果操作人员没有接受过专门的培训或者技术水平不高,就会导致设备的效率降低。
影响石灰石湿式球磨机出力的原因及处理方法
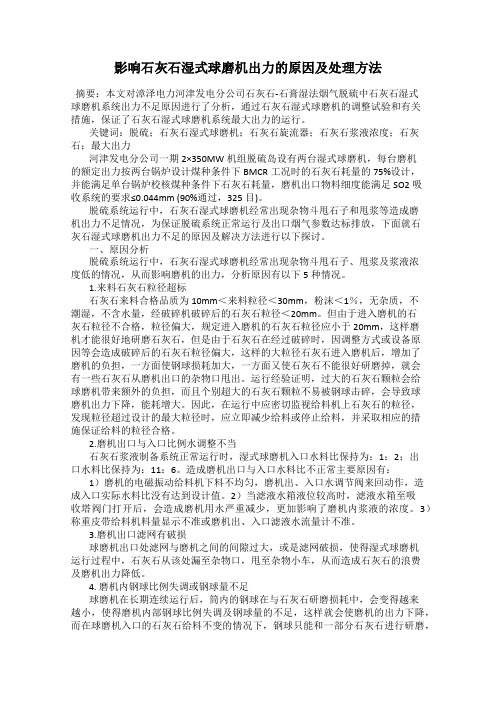
影响石灰石湿式球磨机出力的原因及处理方法摘要:本文对漳泽电力河津发电分公司石灰石-石膏湿法烟气脱硫中石灰石湿式球磨机系统出力不足原因进行了分析,通过石灰石湿式球磨机的调整试验和有关措施,保证了石灰石湿式球磨机系统最大出力的运行。
关键词:脱硫;石灰石湿式球磨机;石灰石旋流器;石灰石浆液浓度;石灰石;最大出力河津发电分公司一期2×350MW机组脱硫岛设有两台湿式球磨机,每台磨机的额定出力按两台锅炉设计煤种条件下BMCR工况时的石灰石耗量的75%设计,并能满足单台锅炉校核煤种条件下石灰石耗量,磨机出口物料细度能满足SO2吸收系统的要求≤0.044mm (90%通过,325目)。
脱硫系统运行中,石灰石湿式球磨机经常出现杂物斗甩石子和甩浆等造成磨机出力不足情况,为保证脱硫系统正常运行及出口烟气参数达标排放,下面就石灰石湿式球磨机出力不足的原因及解决方法进行以下探讨。
一、原因分析脱硫系统运行中,石灰石湿式球磨机经常出现杂物斗甩石子、甩浆及浆液浓度低的情况,从而影响磨机的出力,分析原因有以下5种情况。
1.来料石灰石粒径超标石灰石来料合格品质为10mm<来料粒径<30mm,粉沫<1%,无杂质,不潮湿,不含水量,经破碎机破碎后的石灰石粒径<20mm。
但由于进入磨机的石灰石粒径不合格,粒径偏大,规定进入磨机的石灰石粒径应小于20mm,这样磨机才能很好地研磨石灰石,但是由于石灰石在经过破碎时,因调整方式或设备原因等会造成破碎后的石灰石粒径偏大,这样的大粒径石灰石进入磨机后,增加了磨机的负担,一方面使钢球损耗加大,一方面又使石灰石不能很好研磨掉,就会有一些石灰石从磨机出口的杂物口甩出。
运行经验证明,过大的石灰石颗粒会给球磨机带来额外的负担,而且个别超大的石灰石颗粒不易被钢球击碎,会导致球磨机出力下降,能耗增大。
因此,在运行中应密切监视给料机上石灰石的粒径,发现粒径超过设计的最大粒径时,应立即减少给料或停止给料,并采取相应的措施保证给料的粒径合格。
4-4磨机生产率计算及影响因素

1.比生产率法 前苏联及我国曾有人建议采用七八个修正系数,但计算更繁琐,结果 也说不上更精确,没有得到广泛采用,这里仍介绍设计部门广泛采用 的计算方法。 按新生产-0.074mm级别计算,公式为: q=q0×K1×K2×K2×K3×K4 Q=qV=q0×K1×K2×K2×K3×K4×V 式中:q0——作为比较标准的磨机单位生产效率,t/(m3· h); q——要计算的磨机单位生产率,t/(m3· h); V——要计算的磨机有效容积,m3; Q——要计算磨机的生产率,t/h; K1——可磨性系数,一般由实验确定。 K2——磨机类型校正系数; D b 0.5 K ( ) K3——磨机直径校正系数,可由式 3
10 10 Wc Wi ( ) EF 1 EF 2 EF 7 EF 8 P80 F80
三、影响磨矿过程的因素
主要4大类影响因素 1.入磨矿石性质的影响 2.磨机结构及转速的影响 3.操作因素的影响 4.装补球方法的影响
1.入磨矿石性质的影响
1)矿石可磨性 (1)矿石越硬,可磨性越小,磨细能耗愈高,磨机处理能力愈小; (2)矿石愈细愈难磨,随磨矿比增大,可磨性系数减小; (3)可通过加热预处理、电热辐射、使用表面活性剂等方法,提高 矿石的可磨性。
N CG D
N 0.735CG D
经验指出,当装入的钢球是有效工作时,装球越多,生产率越高, 功率消耗越多。装球过多,由于转速的限制,靠近磨机中心的那部 分钢球只是蠕动,不能有效工作。
(2)装球率 一般为40-50%(球荷载面积与筒体截面积之比
装球率测量示意图
可用经验公式计算:
(50 - 127
D0 b0
计算得出,式中D和D0为要计算的和选做标准的磨机直径, b和b0为磨机衬板厚度,按次式计算结果见表4-7-3; K4——磨机给矿粒度和产品粒度系数, m K4 1 m2
磨机振动因素及相关防范措施
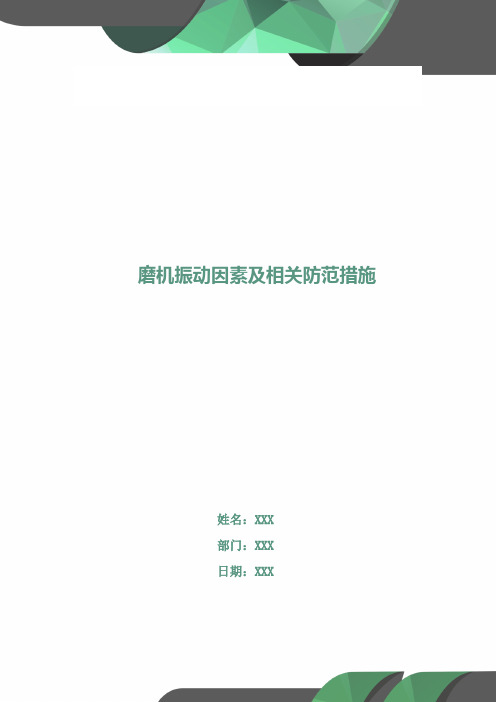
磨机振动因素及相关防范措施姓名:XXX部门:XXX日期:XXX磨机振动因素及相关防范措施一、料床的控制1、挡料环是维护磨机料床的关键部件,挡料环的高度直接决定了磨机的料层厚度,故挡料环是否完好或高度是否适中,将会影响磨机的料床状态。
一般在使用新辊皮和新磨盘衬板时挡料环的有效高度为120mm(MLS3424)、240mm(ATOx50)左右,在随着磨辊衬板和磨盘衬板磨损与日逐增时,挡料环的高度可以适当降低,从而以此来减小磨机运行的阻力,减小磨机振动。
2、立磨研磨机理主要是利用料床间物料与物料之间挤压研磨,操作中保证合理的料层,对于预防磨机的振动是非常必要的,磨内温度的控制的高低和磨机通风量的大小又决定了物料悬浮程度,故合理控制磨机出口温度和确保磨机通风顺畅也是保证料床波动的重要因素,一般在磨机正常运行情况下,磨盘料层控制在60~100mm厚度是最佳状态。
3、喂料的波动对于磨机的料床控制影响很大,波动的大小直接决定来料的均匀性,故在磨机正常运行状态下,加减产必须根据磨内差压和主机电流以及物料离析后粒度的波动的情况,加减产幅度不宜过大,正常情况下控制在5t/h以内。
另外还应杜绝断料现象的发生,从而避免因磨内短时间料层过薄,使磨机振动迅速上扬,轻则磨机跳停,重则损坏磨内各部件。
4、磨机喷水装置的失灵,特别是二期喷水装置一旦失灵,将会造成磨内料层波动大,磨机振动也会将随之上升。
故要确保二期磨内三只喷水管管道畅通完好,同时要求现场人员在每次停磨检查时要仔细对喷水系统进行检查和维护,确保喷水量均匀,同时操作员在操作中在调节第 2 页共 6 页喷水时幅度不宜过大,正常情况下每次按2m3/h调节,保证磨机出口温度稳定。
二、用风的控制1、尽量减少磨内用风的波动,合理调节系统各挡板。
特别是在开磨时调节旁路挡板时不能造成磨内用风的不够,进而引起磨机的振动,严禁旁路挡板开启开磨的非法操作。
2、尽量避免入磨风量变化过大的影响,一方面应减少窑系统的用风波动,例如增湿塔内垮料和DD炉内垮料,另一方面应杜绝磨内差压过高,磨内物料过多,料层过厚,物料循环负荷大,循环后的物料在磨内经集料锥返回磨盘,从而造成磨内用风突然短路,磨机入口正压,料层过厚,使磨机振动骤然上升,导致磨机跳停。
磨煤机出力不足的影响要素及应对措施
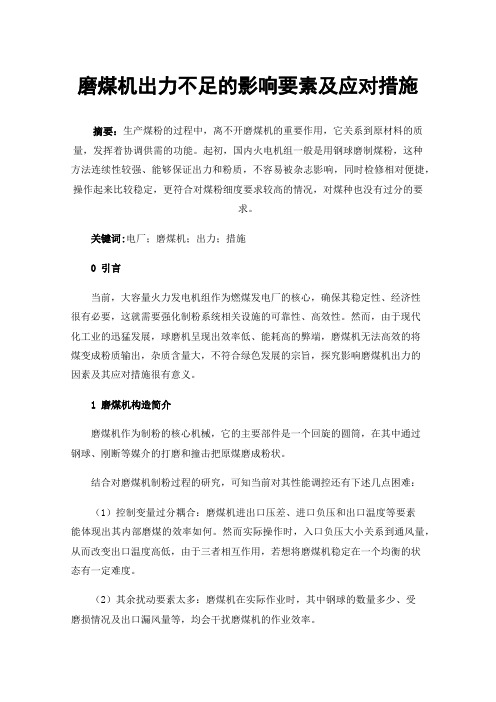
磨煤机出力不足的影响要素及应对措施摘要:生产煤粉的过程中,离不开磨煤机的重要作用,它关系到原材料的质量,发挥着协调供需的功能。
起初,国内火电机组一般是用钢球磨制煤粉,这种方法连续性较强、能够保证出力和粉质,不容易被杂志影响,同时检修相对便捷,操作起来比较稳定,更符合对煤粉细度要求较高的情况,对煤种也没有过分的要求。
关键词:电厂;磨煤机;出力;措施0引言当前,大容量火力发电机组作为燃煤发电厂的核心,确保其稳定性、经济性很有必要,这就需要强化制粉系统相关设施的可靠性、高效性。
然而,由于现代化工业的迅猛发展,球磨机呈现出效率低、能耗高的弊端,磨煤机无法高效的将煤变成粉质输出,杂质含量大,不符合绿色发展的宗旨,探究影响磨煤机出力的因素及其应对措施很有意义。
1磨煤机构造简介磨煤机作为制粉的核心机械,它的主要部件是一个回旋的圆筒,在其中通过钢球、刚断等媒介的打磨和撞击把原煤磨成粉状。
结合对磨煤机制粉过程的研究,可知当前对其性能调控还有下述几点困难:(1)控制变量过分耦合:磨煤机进出口压差、进口负压和出口温度等要素能体现出其内部磨煤的效率如何。
然而实际操作时,入口负压大小关系到通风量,从而改变出口温度高低,由于三者相互作用,若想将磨煤机稳定在一个均衡的状态有一定难度。
(2)其余扰动要素太多:磨煤机在实际作业时,其中钢球的数量多少、受磨损情况及出口漏风量等,均会干扰磨煤机的作业效率。
(3)差压波动信号:内部钢球磨损严重,存煤较多时,其通风性能变差,导致进出口压差强烈波动,但是钢球数量过多,存煤量一定时,系统反馈的差压波动信号较弱,这表明进出口压差变化存在一定的滞后性,会影响系统的内部调控。
2磨煤机出力不足原因一般来讲,可将磨煤机出力等同于制粉出力。
钢球磨煤机是借助其通风量大小来实现出力调控的,通常我们借助调节一次风机的出口风开度来改变锅炉内部负荷及出力。
然而这样可能会出现负荷太低、影响作业效率的情况。
通常情况下,我们将磨煤出力近似看作制粉出力。
试析脱硫湿磨机常见的问题分析及处理

试析脱硫湿磨机常见的问题分析及处理发布时间:2021-08-03T06:48:18.816Z 来源:《电力设备》2021年第5期作者:杜福明桑长勇李恒亮[导读] 修后设备各运行参数均达优良值,设备保持长周期正常平稳运行,取得了显著成效。
(华电潍坊发电有限公司山东潍坊 261000)摘要:湿式球磨机是石灰石脱硫进程中的重要生产设备。
湿式球磨机主要为石灰石和球磨机石灰石浆液供给脱硫吸附剂。
我国石灰石资源丰富,散布广泛,原料成本低。
并且,湿式球磨机在石灰石脱硫生产进程中具有工艺相对简单、设备投资低、能耗低、保护简单等特色。
基于此,现在我国石灰石脱硫大多采用湿式球磨机。
然而,石灰石湿法磨浆制备进程中仍存在一些问题有待处理,影响了石灰石生产的脱硫进程。
关键词:脱硫湿磨机;问题;处理办法1项目背景某电厂脱硫系统湿式球磨机由克莱德贝尔格曼供货,2018年4月发现其入口轴承跑内圈,塞尺测量轴承与轴装配位置间隙4~5 mm,因此需对其入口中空轴进行修复处理。
技术人员对比了国内几种大型轴颈修复工艺,通过分析比较并结合本项目的特点,发现因施工条件限制以及轴颈磨损过深,这几种修复工艺均不适用于本项目,所以决定针对本项目特点,依托自身检修力量开展技术攻关,探索出一种采用手工电弧焊修复的工艺对空心轴进行修复。
本项目实施后,修后设备各运行参数均达优良值,设备保持长周期正常平稳运行,取得了显著成效。
2湿式球磨机脱硫存在的问题及原因2.1脱硫湿式球磨机存在的问题现在,尽管湿法球磨脱硫工艺在脱硫工艺中得到了广泛应用,取得了良好的生产效益,但湿法球磨石灰石制浆工艺仍存在许多问题有待处理,其间最明显的问题是湿式球磨机脱硫工艺便是湿式球磨机脱硫工艺,最显著的三个问题是:(1)湿式球磨机电流骤变反常,即石灰石湿法制浆脱硫进程中,电机忽然呈现反常作业状况,直接影响湿式球磨机的正常运转;(2)湿式球磨机卸料槽溢流和卸料端排污口倾倒,即在湿式球磨机脱硫进程中,排污口随脱硫进程排出,湿磨机产值缺乏,能耗明显添加,合格浆量削减。
影响立磨产质量的因素

影响立磨产质量的因素1 引言我公司于2004年建成投产一条年产l00万吨水泥的生产线,使用德国莱歇公司LM56.2+2C/S辊式立磨分别粉磨矿渣和熟料,现就多年来使用经验,谈谈影响立磨产质量的因素,与大家共同探讨。
2 影响立磨产质量的因素(1)物料的影响喂料量的稳定是影响立磨正常运行的关键,特别是粉磨矿渣超细粉,喂料不均匀会导致料床产生磨振,温度也不好控制;风量及负压调节过于频繁也会影响到热风炉的控制,严重时可能导致热风炉结焦而停产;其次物料中含铁量的多少也会影响到立磨的产质量。
随着粉磨时间的增加,磨床内存积细铁颗粒就越多,不仅影响磨机的粉磨效率,增加辊套及磨盘的磨损,在同等条件下还会减小出磨成品的比表面积。
而物料中粗颗粒铁、大块铁较多或物料中有大块的输送胶带等杂物的话,还会造成叶轮喂料机的卡死导致停磨,即使入磨,也会增加立磨的振动,以致无法控制造成停机,严重影响磨机的正常运行。
因此要求入料稳定及多级除铁来稳定物料。
粉磨熟料时,由于熟料的物理性质不同,喂料量的均匀与否对立磨的运行不会有太大的影响,当然也不能相差太大(我公司立磨粉磨熟料运行时,喂料量同时在70~200t/h间变化时,短时间内也不会造成磨机的停磨),但会影响回料量的控制,太大时也会影响到出磨成品的比表面积。
熟料中细粉量的多少会影响到立磨的振动,如同时入磨的细粉太多(如清理收尘器的大量积灰等),入磨后控制不好会带来较大的振动,造成停机影响运行;而熟料中大颗粒物料(一般>60mm)太多,就会增加磨机回料,相应地会减少磨机产量。
(2)磨机操作压力的影响磨机操作压力的大小,会直接影响粉磨能力。
随着操作压力的增加,粉磨能力会不断增强,粉磨功耗也会随之增加,压力的大小和产质量之间应有适当的范围,在保证产质量的前提下,压力不应设得太大。
一般粉磨矿渣超细粉时压力设定较高,产量也高,而粉磨熟料时,熟料的易磨性相对较好,压力设定相对较小,太大不一定会带来产量的提高,还有可能增加回料量,增大磨机损耗,因此应根据磨况适时调节操作压力。
影响磨机产量的因素
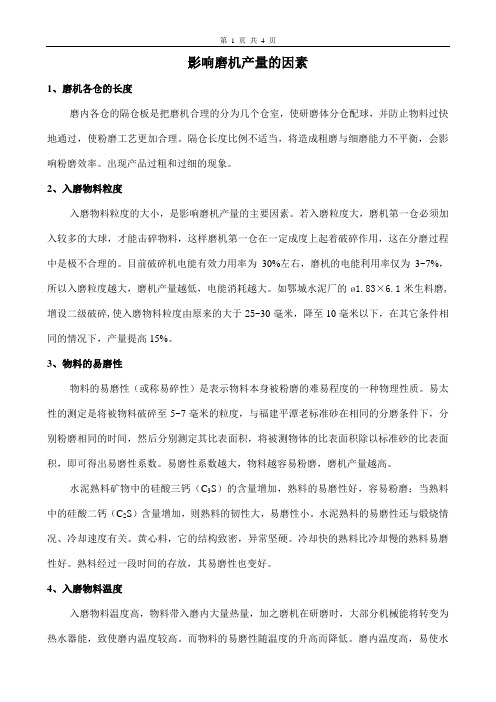
影响磨机产量的因素1、磨机各仓的长度磨内各仓的隔仓板是把磨机合理的分为几个仓室,使研磨体分仓配球,并防止物料过快地通过,使粉磨工艺更加合理。
隔仓长度比例不适当,将造成粗磨与细磨能力不平衡,会影响粉磨效率。
出现产品过粗和过细的现象。
2、入磨物料粒度入磨物料粒度的大小,是影响磨机产量的主要因素。
若入磨粒度大,磨机第一仓必须加入较多的大球,才能击碎物料,这样磨机第一仓在一定成度上起着破碎作用,这在分磨过程中是极不合理的。
目前破碎机电能有效力用率为30%左右,磨机的电能利用率仅为3~7%,所以入磨粒度越大,磨机产量越低,电能消耗越大。
如鄂城水泥厂的ø1.83×6.1米生料磨,增设二级破碎,使入磨物料粒度由原来的大于25~30毫米,降至10毫米以下,在其它条件相同的情况下,产量提高15%。
3、物料的易磨性物料的易磨性(或称易碎性)是表示物料本身被粉磨的难易程度的一种物理性质。
易太性的测定是将被物料破碎至5~7毫米的粒度,与福建平潭老标准砂在相同的分磨条件下,分别粉磨相同的时间,然后分别测定其比表面积,将被测物体的比表面积除以标准砂的比表面积,即可得出易磨性系数。
易磨性系数越大,物料越容易粉磨,磨机产量越高。
水泥熟料矿物中的硅酸三钙(C3S)的含量增加,熟料的易磨性好,容易粉磨;当熟料中的硅酸二钙(C2S)含量增加,则熟料的韧性大,易磨性小。
水泥熟料的易磨性还与煅烧情况、冷却速度有关。
黄心料,它的结构致密,异常坚硬。
冷却快的熟料比冷却慢的熟料易磨性好。
熟料经过一段时间的存放,其易磨性也变好。
4、入磨物料温度入磨物料温度高,物料带入磨内大量热量,加之磨机在研磨时,大部分机械能将转变为热水器能,致使磨内温度较高。
而物料的易磨性随温度的升高而降低。
磨内温度高,易使水泥因静电吸引而聚结,严重的会粘附研磨体和衬板,从而降低粉磨效率,明显地阻碍粉磨过程的顺利进行。
温度愈高,这种现象愈严重。
当温度超过100℃时,物料的小颗粒表面相互隔离的一层空气膜受到破坏,使粘附现象更为严重。
影响磨机产质量的磨内因素和磨机优质高产的技术途径
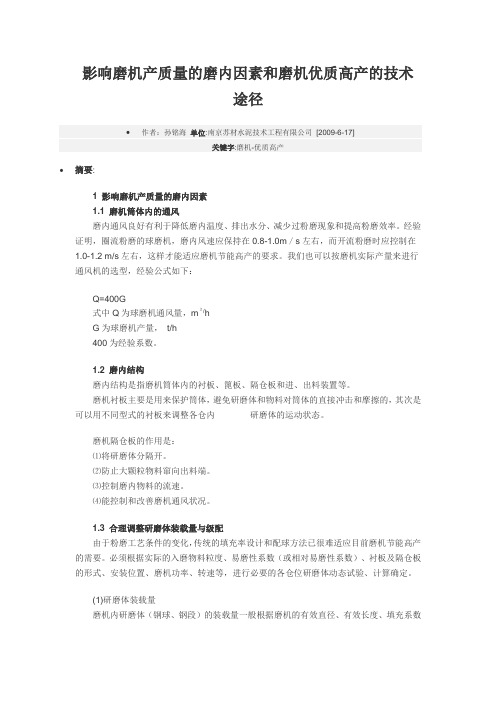
影响磨机产质量的磨内因素和磨机优质高产的技术途径∙作者:孙铭海单位:南京苏材水泥技术工程有限公司[2009-6-17]关键字:磨机-优质高产∙摘要:1 影响磨机产质量的磨内因素1.1 磨机筒体内的通风磨内通风良好有利于降低磨内温度、排出水分、减少过粉磨现象和提高粉磨效率。
经验证明,圈流粉磨的球磨机,磨内风速应保持在0.8-1.0m/s左右,而开流粉磨时应控制在1.0-1.2 m/s左右,这样才能适应磨机节能高产的要求。
我们也可以按磨机实际产量来进行通风机的选型,经验公式如下:Q=400G式中Q为球磨机通风量,m3/hG为球磨机产量,t/h400为经验系数。
1.2 磨内结构磨内结构是指磨机筒体内的衬板、篦板、隔仓板和进、出料装置等。
磨机衬板主要是用来保护筒体,避免研磨体和物料对筒体的直接冲击和摩擦的,其次是可以用不同型式的衬板来调整各仓内研磨体的运动状态。
磨机隔仓板的作用是:⑴将研磨体分隔开。
⑵防止大颗粒物料窜向出料端。
⑶控制磨内物料的流速。
⑷能控制和改善磨机通风状况。
1.3 合理调整研磨体装载量与级配由于粉磨工艺条件的变化,传统的填充率设计和配球方法已很难适应目前磨机节能高产的需要。
必须根据实际的入磨物料粒度、易磨性系数(或相对易磨性系数)、衬板及隔仓板的形式、安装位置、磨机功率、转速等,进行必要的各仓位研磨体动态试验、计算确定。
(1)研磨体装载量磨机内研磨体(钢球、钢段)的装载量一般根据磨机的有效直径、有效长度、填充系数和研磨体的比重等计算确定,较麻烦。
现特推荐一个由黄有丰教授提出并经生产实践检验可使用的筒易公式:研磨体装载量G=D2L t式中:D为磨机的有效直径m;L为磨机的有效长度m。
另还可根据研磨体装载量的吨数大致确定应配多大功率的电机。
即1吨研磨体量要求配备约10-12kW的电机功率。
研磨体的级配与入磨物料的粒度有着直接的关系,入磨物料的粒度一旦有变化,研磨体的级配则应作相应的调整。
(2)磨机填充率(系数)装入磨内研磨体之容积占磨机有效容积的百分比称为磨机的填充系数,又称填充率。
影响砂磨机工作效率和质量的因素
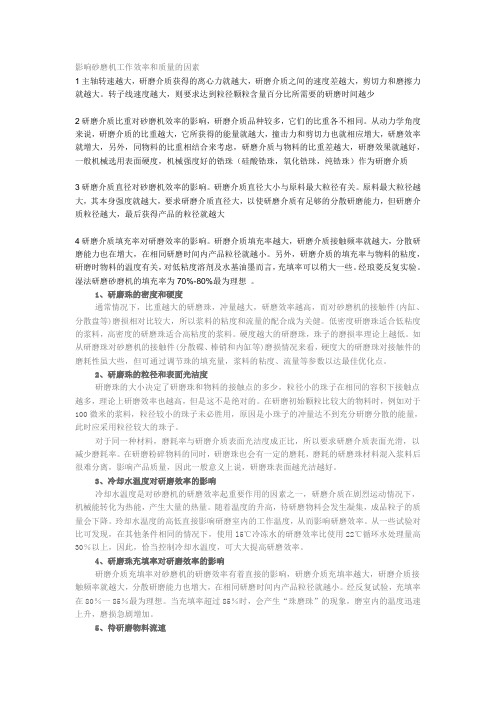
影响砂磨机工作效率和质量的因素1主轴转速越大,研磨介质获得的离心力就越大,研磨介质之间的速度差越大,剪切力和磨擦力就越大。
转子线速度越大,则要求达到粒径颗粒含量百分比所需要的研磨时间越少2研磨介质比重对砂磨机效率的影响,研磨介质品种较多,它们的比重各不相同。
从动力学角度来说,研磨介质的比重越大,它所获得的能量就越大,撞击力和剪切力也就相应增大,研磨效率就增大,另外,同物料的比重相结合来考虑,研磨介质与物料的比重差越大,研磨效果就越好,一般机械选用表面硬度,机械强度好的锆珠(硅酸锆珠,氧化锆珠,纯锆珠)作为研磨介质3研磨介质直径对砂磨机效率的影响。
研磨介质直径大小与原料最大粒径有关。
原料最大粒径越大,其本身强度就越大,要求研磨介质直径大,以使研磨介质有足够的分散研磨能力,但研磨介质粒径越大,最后获得产品的粒径就越大4研磨介质填充率对研磨效率的影响。
研磨介质填充率越大,研磨介质接触频率就越大,分散研磨能力也在增大,在相同研磨时间内产品粒径就越小。
另外,研磨介质的填充率与物料的粘度,研磨时物料的温度有关,对低粘度溶剂及水基油墨而言,充填率可以稍大一些。
经琅菱反复实验。
湿法研磨砂磨机的填充率为70%-80%最为理想。
1、研磨珠的密度和硬度通常情况下,比重越大的研磨珠,冲量越大,研磨效率越高,而对砂磨机的接触件(内缸、分散盘等)磨损相对比较大,所以浆料的粘度和流量的配合成为关健。
低密度研磨珠适合低粘度的浆料,高密度的研磨珠适合高粘度的浆料。
硬度越大的研磨珠,珠子的磨损率理论上越低。
如从研磨珠对砂磨机的接触件(分散碟、棒销和内缸等)磨损情况来看,硬度大的研磨珠对接触件的磨耗性虽大些,但可通过调节珠的填充量,浆料的粘度、流量等参数以达最佳优化点。
2、研磨珠的粒径和表面光洁度研磨珠的大小决定了研磨珠和物料的接触点的多少,粒径小的珠子在相同的容积下接触点越多,理论上研磨效率也越高,但是这不是绝对的。
在研磨初始颗粒比较大的物料时,例如对于100微米的浆料,粒径较小的珠子未必胜用,原因是小珠子的冲量达不到充分研磨分散的能量,此时应采用粒径较大的珠子。
湿式球磨机运行中常见问题分析

关键词 : 脱硫 湿式球 磨机 ; 工作原理 ; 结构特点 ; 常见 问题
中图分类号 : T M6 2 1 . 3 文献标识码 : A
湿 式球磨 机是石 灰石一 石膏 湿法脱硫 系统 中的制浆 设备 , 某 发电公司一期采用上海赛姆提 克机 械有限公 司生产 的湿式球 磨 机 2台 ,二期采用上海克莱德 贝尔格曼机械有 限公 司生产 的 湿式球磨机 2台 , 所 以球磨机的系统 配置都相 同。每 台磨机 的额
LI Bi n, LI Zhe n
ABS TRACT:T h e u s e o f a n t i — - mi s o p e r a t i o n l o c k i n g d e v i c e i s a n e f f e c t i v e t e c h n i c a l me a s u r e f o r p r e v e n t i n g t h e e l e c t r i c mi s o p e r a t i o n o f wo r k e r s i n s w i t c h i n g o p e r a t i o n . B a s e d o n e x p o u n d i n g t h e c o mp o n e n t s o f a n t i - mi s o p e r a t i o n l o c k i n g d e v i c e ,
2 . 1 球磨机 出力不够且容易甩出石子 某发 电公 司球磨机 出 口甩石 子主要体现在二期湿式球磨 机 上, 设计出力为 1 1 . 5 t / l 1 , 但实际运行时磨机给料量 只能达 到 7
~
的7 5 %设计并 能满足单 台锅炉校 核煤种条件 下石灰石 耗量 , 根
FGDM2965湿磨机故障的原因分析及处理对策
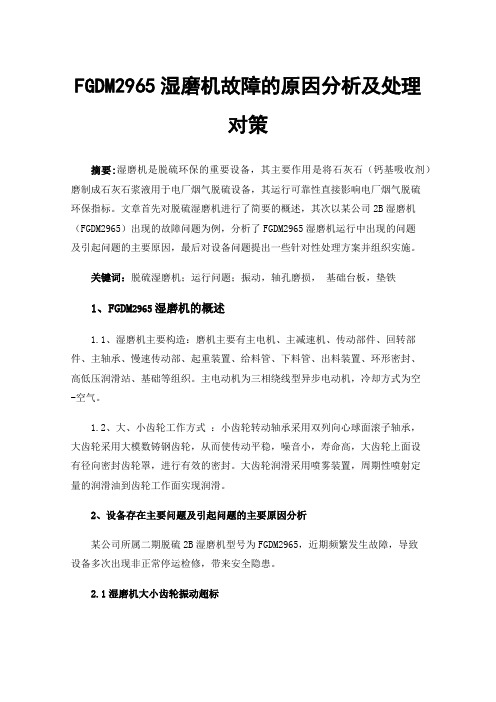
FGDM2965湿磨机故障的原因分析及处理对策摘要:湿磨机是脱硫环保的重要设备,其主要作用是将石灰石(钙基吸收剂)磨制成石灰石浆液用于电厂烟气脱硫设备,其运行可靠性直接影响电厂烟气脱硫环保指标。
文章首先对脱硫湿磨机进行了简要的概述,其次以某公司2B湿磨机(FGDM2965)出现的故障问题为例,分析了FGDM2965湿磨机运行中出现的问题及引起问题的主要原因,最后对设备问题提出一些针对性处理方案并组织实施。
关键词:脱硫湿磨机;运行问题;振动,轴孔磨损,基础台板,垫铁1、FGDM2965湿磨机的概述1.1、湿磨机主要构造:磨机主要有主电机、主减速机、传动部件、回转部件、主轴承、慢速传动部、起重装置、给料管、下料管、出料装置、环形密封、高低压润滑站、基础等组织。
主电动机为三相绕线型异步电动机,冷却方式为空-空气。
1.2、大、小齿轮工作方式:小齿轮转动轴承采用双列向心球面滚子轴承,大齿轮采用大模数铸钢齿轮,从而使传动平稳,噪音小,寿命高,大齿轮上面设有径向密封齿轮罩,进行有效的密封。
大齿轮润滑采用喷雾装置,周期性喷射定量的润滑油到齿轮工作面实现润滑。
2、设备存在主要问题及引起问题的主要原因分析某公司所属二期脱硫2B湿磨机型号为FGDM2965,近期频繁发生故障,导致设备多次出现非正常停运检修,带来安全隐患。
2.1湿磨机大小齿轮振动超标2.1.1查阅设备日常状态检测记录,发现湿磨机频繁出现水平向振动超标问题,现场检查,发现以小齿轮检测水平向、垂直向振动呈现跳跃式振幅波动,怀疑小齿轮主轴线基础台板下部空间存在虚空问题。
现场振动检测情况单位:(μm)名称水平垂直轴向规定值结论推力端103-10939-5171100水平向超标承力端123-14646-6297120水平向超标2.1.2在转动机械中,要求基础台板每个地脚螺栓两侧安装一组垫铁,基础台板垫铁应间隔300mm安装一组,在磨机大小齿轮主轴线两侧应安装支撑垫铁,垫铁应电焊固定,基础二次灌浆[1]饱满,凝固时间不小于48小时。
橡胶衬板结构尺寸对湿式球磨机出力影响浅析

橡胶衬板结构尺寸对湿式球磨机出力影响浅析作者:杨杰来源:《中国科技博览》2014年第01期摘要胜利发电厂脱硫系统的两台FGDM3264型湿式球磨机进行橡胶衬板更换后出力发生了变化,对此现象进行了细致地对比分析,找出了衬板结构尺寸与磨机出力变化的关键所在,提出了行之有效的优化措施,达到了良好的效果。
关键词脱落系统橡胶衬板出力钢球中图分类号:TQ33前言湿式球磨机是火力发电厂脱硫系统的重要系统之一,其运行出力的状况,直接影响到电厂机组的环保经济运行。
胜利石油管理局胜利发电厂脱硫系统使用两台FGDM3264型湿式球磨机进行石灰石浆液的制备,2010年3月间更换了A磨机的橡胶衬板,换后磨机出力发生了0.8~1.4T/H的变化,对此进行了深入分析研究。
发现出力变化原因根衬板结构尺寸有关,因此,为保证磨机在最佳工况下运行,提高磨机出力、降低钢耗和电耗,我们提出了优化措施,并在B磨上实施,取得了良好效果,为为此类问题的解决提供了有效的解决方法。
1 本厂现状分析我厂石灰石碾磨系统为再循环式的湿式制浆系统,选用溢流式球磨机,能连续和非连续运行。
由称重给料机将石灰石(粒径≤20mm)从石灰石贮仓内送到湿式球磨机内磨制成浆液,石灰石浆液用泵输送到水力旋流器经分离后,大尺寸物料再循环,溢流物料存贮于石灰石浆液箱中,然后经石灰石浆液泵送至吸收塔。
在设计的工作容量范围内,能长期安全稳定运行并达到规定的细度要求。
设备年运行小时数为7500小时。
本厂脱硫系统设计采用FGDM3264型湿式球磨机。
2 更换橡胶衬板前后出力变化。
公用区浆液箱密度1203.9,一般在1200左右;水料比1:2.6,一般在1:2;旋流器出口直径40;磨头注水10m3/H,磨尾注水32m3/H。
更换橡胶衬板前平均出力为22 t/H,A磨更换橡胶衬板后平均出力16.1 t/H;B磨更换橡胶衬板后平均出力17.2t/H,运行200小时后两台磨机出力约为17.5 t/H,400小时后两台磨机出力约为18.75t/H,其中B磨出力一直略大于A磨出力。
脱硫湿磨机出力不足的原因分析及处理

脱硫湿磨机出力不足的原因分析及处理发布时间:2022-10-19T07:08:50.545Z 来源:《科技新时代》2022年第9期作者:冯新停[导读] 脱硫湿磨机是脱硫系统主要设备,主要作用是把石灰石颗粒磨制成合格的石灰石浆液,供脱硫系统使用冯新停大唐洛阳热电有限责任公司河南洛阳 471003摘要:脱硫湿磨机是脱硫系统主要设备,主要作用是把石灰石颗粒磨制成合格的石灰石浆液,供脱硫系统使用。
湿磨机稳定运行是脱硫系统稳定运行重要一环。
实际运行中,经常会出现湿磨机出力下降,达不到额定出力情况,原因很多,这篇文章主要从设备方面分析存在问题和解决途径。
关键词:湿磨机额定出力石灰石旋流器磨头水量旋流器喷嘴引言某公司脱硫系统于2006年投运,系统采用石灰石—石膏湿法烟气脱硫工艺技术。
脱硫制浆系统的工艺流程为:称重皮带给料机输送来的石灰石颗粒,汇同由滤液水泵输送来的滤液水及二级旋流器的底流浓浆一起进入球磨机筒体,被球磨机内的钢球撞击、挤压和碾磨成浆液,经旋流器进行水力旋流粗细分离,浆液中的大颗粒被分离到旋流器的底部形成底流浓浆,从湿磨机入口回到球磨机被再次碾磨,而浆液中的小颗粒则从顶部溢出,进入石灰石浆液箱备用。
我公司湿磨机采用的是沈阳重型机械有限责任公司MQS-T2875湿式球磨机,额定出力为15t/h。
(磨机制浆系统图)主要设备规范:湿式球磨机型号:MQS-T2875额定出力:15t/h给料粒度<20mm生产商:沈阳重型机械有限责任公司湿磨机浆液循环泵型号LCF100/320流量:108 m3/h扬程:35mH2O生产商:襄樊五二五泵业有限公司石灰石浆液旋流器型号:D4-16Φ165的旋流子4个(3用1备)输送量:60t/h。
生产商:MULTOTEC滤液水泵型号LCF65/310流量:60 m3/h扬程:15mH2O生产商:襄樊五二五泵业有限公司湿磨机循环浆液箱容积:8 M3一、存在问题脱硫1、2号湿磨机额定出力运行时,排渣口频繁出石子,最多时每小时达到100-300公斤。
脱硫湿法球磨机堵磨原因分析及处理

脱硫湿法球磨机堵磨原因分析及处理(总4页)--本页仅作为文档封面,使用时请直接删除即可----内页可以根据需求调整合适字体及大小--脱硫湿法球磨机堵磨原因分析及处理0、引言湿式球磨机是石灰石-石膏湿法脱硫系统中重要设备,其作用是磨制石灰石浆液,提供脱硫吸收剂。
国内石灰石分布广、储量大、价格便宜,加之湿磨系统较干磨系统设备投资费用低、系统简单、能耗低、运行费用低,因此,湿磨系统在火电厂脱硫中作为首选的石灰石浆液制备系统,应用非常广泛。
但随着运行时间的变长,湿磨制备石灰石浆液这种方式也暴露出不少问题,如磨制的石灰石浆液品质不合格,湿式球磨机出力不足,甚至发生湿式球磨机堵磨事件,影响了脱硫运行。
1、设备概况国电泰洲电厂2*1000MW机组脱硫采用石灰-石膏湿法脱硫工艺,一炉一塔,设计燃煤硫分为%,设计脱硫效率不小于%,1、2号脱硫装置分别2007年12月和2008年3月与主机组同步投运。
脱硫系统最初设计安装2套湿式球磨机系统完成了倍扩容改造,改造中又增加了1套湿式球磨机系统,单套湿磨系统工艺流程见图1。
3台湿式球磨机出力均为h,电机功率800kw,电机额定电流,简体直径3000mm,简体有效长度7000mm,简体工作转速min,进料石灰石颗粒直径小于13mm,与之配套石灰石旋流站入口压力控制值为109kPa。
2007年底投运至今,整体运行较稳定,但也存在不少问题,2012年6月发生一起湿式球磨机堵磨事件。
2、事件经过2012年6月21日17:48启动3号湿式球磨机系统制浆,启动后球磨机运行电流为,到6月22日02:45,3号湿式球磨机运行电流小幅下降到,从6月22日02:45到03:20,电流较快的从下降至,3号湿磨再循环箱补水明显增大15t/h左右,且液位波动大、难控制。
在以上时间段内,3号湿式球磨机石灰石给料量稳定控制在18-21t/h之间。
在3号球磨机运行电流下降较快的时间段及停运后,对系统进行了检查。
- 1、下载文档前请自行甄别文档内容的完整性,平台不提供额外的编辑、内容补充、找答案等附加服务。
- 2、"仅部分预览"的文档,不可在线预览部分如存在完整性等问题,可反馈申请退款(可完整预览的文档不适用该条件!)。
- 3、如文档侵犯您的权益,请联系客服反馈,我们会尽快为您处理(人工客服工作时间:9:00-18:30)。
湿式球磨机应在最佳出力(通常是设计出力)下运行,不应轻易改变出力。
出力太小,不仅使磨制单位重量石灰石的功耗增加,而且还会使产品浆液的浓度降低,达不到设计要求,或者使一、二级再循环箱液位难以保持;出力太大,会导致球磨机过负荷,造成球磨机电流增大,碾磨功效降低,一级再循环箱液位很快上涨且难于调节,石灰石浆液变稠,极易发生泵和管路的堵塞,循环倍率增加,材料磨损加剧,严重时会堵塞球磨机或将钢球带出,危及设备安全。
II应保证进入球磨机的石灰石粒径在设计的最大粒径以下。
运行经验证明,过大的石灰石颗粒会给球磨机带来额外的负担,而且个别超大的石灰石颗粒不易被钢球击碎,会导致球磨机出力下降,功耗增大。
因此,在运行中应密切监视给料机上石灰石的粒径,发现粒径超过设计的最大粒径时,应立即减少给料或停止给料,并采取相应的措施保证给料的粒径合格。
III球磨机应定期补加钢球,以保持球磨机的最佳钢球装载量。
钢球太少,会影响球磨机的出力;钢球太多,钢球不能被筒体有效提起,也会影响球磨机的出力,增加电耗。
经过一段时间运行后,应对全部钢球进行挑选,换入新球,以保证球磨机的功效。
IV运行中应定期对再循环泵、管道和再循环箱进行冲洗,旋流器也应定期切换、冲洗,以防止堵塞,影响正常运行和产品质量。
V改变二级旋流器底流喷嘴口径,可调节旋流器底流与溢流浆液量的比例,从而影响浓度、流经球磨机的水量、系统循环倍率等因素,除非系统发生重大改变,其喷嘴尺寸不应轻易调整。
VI运行中要密切关注石灰石成分的分析报告,Fe203、SiO2:等矿物质含量变大会增加钢球的磨损量。
当石灰石的品质发生重大变化时,应对系统重新调整,并通过试验的方法得到球磨机的最佳钢球装载量和最大出力。
WFGD湿式球磨机运行特性湿式球磨机的结构和工作原理与普通球磨机相同,但因其携带介质是水,故系统组成和运行有2个明显特点:(1)由再循环箱、再循环泵和旋流器构成两级分离系统,以调整产品浆液中固体颗粒的细度和浓度;(2)系统所有的箱罐、泵、管道、搅拌器均使用内衬像胶或防腐材料保护,管件连接处采用机械加密封材料密封。
I 旋流器旋流器是石灰石颗粒分离的关键设备,其结构同一般的离心式旋风器相同。
石灰石浆液由切向进入简体旋转,在离心力的作用下,大粒径的颗粒被甩向筒壁落下并由底流带出旋流器,小粒径的颗粒由中心管向上由溢流带出。
旋流器下部的底流喷嘴可拆换,通过使用不同口径的喷嘴,可以调整底流与溢流的比例。
旋流器对入口浆液中固体物的分离效率取决于旋流器的结构(筒径、入口尺寸、中心管直径及插入深度等)和运行工况(入口浆液速度、入口固体颗粒度等)。
在入口固体颗粒度一定的条件下,提高入口浆液速度即可提高旋流器的分离效率,从而在溢流中得到较细的固体颗粒。
II 系统循环倍率.循环倍率K是指旋流器入口固体质量与溢流中固体质量之比。
若不考虑再循环箱的液位,整个系统的循环倍率K应为两级旋流器循环倍率的乘积。
K值越大,说明系统中回到球磨机重新碾磨的固体越多.系统功耗越大,越不经济。
而且,设备材料磨损越快,使设备寿命缩短。
所以应在保证系统出力和产品细度的前提下,尽量减小系统的循环倍率。
在旋流器的结构和入口速度固定不变的情况下,球磨机出口固体粒径对K值有着决定性的影响。
粒径大时,经两级旋流器底流回到球磨机的固体颗粒增多,导致系统循环倍率增加,而球磨机出口固体粒径又决定于球磨机的破碎、碾磨能力和流经球磨机简体的水量。
字串1III 流经球磨机筒体的水量流经球磨机筒体的水量是运行中的一个重要参数,其大小反映了对球磨机内固体颗粒的携带能力。
水量大,水流速度高,被携带出球磨机的固体颗粒就多、粗,从而导致系统循环倍率增加;水量小,水流速度低,被携带出球磨机的固体颗粒就少、细,这样有些合格的颗粒仍会留在筒体内,被无益地磨成更细的颗粒,致使球磨机出力降低,单位电耗增加。
所以,流经球磨机简体的水量应与球磨机出力相对应,要控制在一个合适的范围内。
流经球磨机筒体的水由携带水和一、二级旋流器的底流共同组成,一、二级旋流器的底流在运行中一般不变,因此调节携带水量即可调节流经球磨机筒体的水量。
运行中携带水量与球磨机出力成一定比例,改变此比例应当慎重。
IV 细度调整保证球磨机出力稳定和相应的球磨机筒体水流量是保证球磨机出口石灰石颗粒度稳定的关键,通常可用下面2种方法调整石灰石的细度。
A 改变再循环泵的转速重庆发电厂石灰石浆液制备系统中,一、二级再循环箱均配有2台转速略有差别的再循环泵,通过使用不同转速的再循环泵(尤其是二级再循环泵)可改变旋流器的入口速度,从而对最终产品的细度进行微调。
B 改变二级旋流器小旋流筒的投用个数增加二级旋流器小旋流筒的投用个数,每个小旋流筒的入口速度降低,会导致溢流中颗粒变粗;反之,减少二级旋流器小旋流筒的投用个数,每个小旋流筒的入口速度提高,又会导致溢流中颗粒变细。
实践证明,增加或减少一个小旋流筒,能使细度发生明显的变化。
字串4V 浓度调整调节水的流量即可调节整个系统石灰石和水的比例,达到调整系统出口浆液浓度的目的。
VI 电耗和钢球磨损量与普通的干式球磨机相比,湿式球磨机没有占总电耗较大比例的通风电耗,取而代之的是很小的水和石灰石浆液的输送电耗,因此总的电耗不大。
在额定出力下重庆发电厂湿式球磨机系统的电耗约为22(kW·h)/t。
钢球磨损量的大小与被磨物料的成分有关。
石灰石的主要成分是CaCO3和MgCO3,主要杂质有SiO2、A1203,、Fe203等,都是硬度较大的矿物质,因此湿式球磨机的钢球磨损量较大。
本篇文章来源于中国脱硫脱硝资讯网原文链接:/html/jishuwenzhang/2006/0725/774.html水泥厂的生产工艺主要是两磨一烧,粉磨的产量占全厂产量2/3,若磨机产量不高则影响窑磨平衡,影响全厂的生产;生料磨的质量主要是要求成份,配热(立窑需要配热,而旋窑的煤粉是由喷煤嘴喷入窑内)和细度合适均匀稳定,尤其是成份和配热的合适,均匀、稳定更为重要,它不仅影响着热工制度的稳定,还直接影响着水泥熟料的质量和热耗,而水泥磨的质量主要是细度,水泥细度的表示和例定方法最好用颗粒级配,但目前颗粒级配尚未普遍应用,有条件的还应尽可能用颗粒级配法,比表面积的测定方法应用的较多,还应进一步的普及,用其代替筛余法(因筛余法不能准确的表示水泥的细度),水泥磨的细度直接影响水泥的强度和凝结时间,因此直接影响水泥的性能和质量,影响销售和水泥厂的经济效益;生料和水泥磨的电力消耗约占水泥厂电力消耗的2/3左右,占水泥成本的1/3左右,因此要大幅度降低电耗,降低成本,提高经济效益,必须大幅度提高磨机产量,磨机产量大幅度提高后,单位产量电力消耗就会降低,从而使水泥厂电力消耗大幅度降低,经济效益明显提高,同时还减少了社会上电力紧张的压力。
一、影响磨机产质量的主要因素1.入磨物料粒度、水份、温度和易磨性:2.磨机结构:直径,长度,进、出料装置,隔仓板和衬板形式,磨机转速等;3.研磨体的级配和装载量;4.磨机通风;5.磨机操作;6.粉磨流程,及选粉机性能、有关参数等。
影响磨机产、质量诸多因素中,影响最大的是入磨物料的粒度、水分;其次是磨机的通风;而研磨体的级配和装载量及磨机操作,这两条不需要资金投入,只要提高认识水平和加强科学管理。
现着重影响大的因素作简要分析。
(一)入磨物料粒度、水分1.入磨物料粒度:全国磨机台时产量最高的是广东省,而广东省内产量最高是塔牌集团,φ2.2×6.5m生料和水泥磨,其产量分别≥44(t/h)、≥28(t/h)比一般水泥厂磨机量高出近一倍,塔牌集团磨机产量如此高的原因除了其管理科学外,主要是入磨物料粒度小,入磨物料粒度<1mm占98%,最大粒度<3mm。
2.入磨物料水分一般入磨物料水分应控制在1%左右,若水分大细粉易糊在研磨体,衬板和隔仓板的篦孔上,使粉磨效率降低,磨机产量降低,当水分达到5%左右时,磨机基本上不能进行工作,目前多数规模小些的企业基本上都没有烘干机,尤其是雨水多的地方或霉雨季节对磨机产量影响很大,严重时生料磨产量供不上窑用,使全厂产量都影响,影响市场和企业经济效益。
(二)入磨物料温度和易磨性研磨体在冲击过程中易产生静电,使微细颗粒荷电,易粘附在研磨体和衬板表面,产生缓冲作用,从而降低研磨效率,温度越高此现象越严重,此外温度高易使石膏脱水、水泥快凝,温度过高还使衬板变形、螺栓断裂……等设备事故。
因此入磨物料温度一般应<60℃。
物料易磨性与物料结构有关,如石灰石中粗晶的方解石晶体直径>1000(μm)易磨性最差,而粉晶(晶体直径10~100μm)和泥晶<10(μm)易磨性好。
熟料的易磨性与矿物组成有关,C3A和C3S易磨性较好,C2S和C4AF易磨性差,急冷熟料易磨性好,死烧大块易磨性差;矿渣中水淬好的易磨性好。
为使熟料入磨温度<60℃,熟料出窑后,必需要急冷,同时需要存放一段时间,严禁出窑即入磨。
(三)磨机通风:若磨机通风好,有利於将温度、水分及时排出,有利於微粉及时排出减少缓冲作用,提高粉磨效率,否则相反。
(四)研磨体级配和研磨体的装载量:研磨体的级配和研磨体的装载量合适与否,不紧影响磨机产量,还影响产品细度。
二、大幅度提高磨机产、质量,大幅度降低电耗主要方向和措施(一)首先应降低入磨物料粒度,入磨物料粒度最好使<1(mm)的>98%,最大粒度<3(mm)。
粒度大小对产量的影响,国外资料上介绍产量系数K0其计算公式如下:此公式适合我国情况,且生料和水泥磨均可用。
例1 某厂入磨物料细碎前平均粒度d0为25(mm),细碎后入磨物料平均粒度为5(mm),求细碎后磨机台时产量提高多少?例2 将例1将平均粒度为5(mm)的物料进一步细碎后平均粒度为2(mm),求磨机产量又提高多少?将物料的细碎任务全移至磨外进行,磨机内主要起研磨作用,这样不仅可大幅度提高产量,还可大幅度提高比表面积提高粉磨质量,若是水泥磨则明显提高水泥强度,由于产量的大幅度提高,使单位产量的电力消耗大幅度降低,这是最节能最科学的办法,因为细碎机的有效功一般为30%左右,而磨机的有效功仅3%左右。
要降低入磨物料粒度,要考虑如何选择好的细碎机,细碎机的选择首先要考虑其工作原理与结构是否合理;出细碎机粒度要尽可能小而且要均匀;材质好、设备事故少、使用寿命长,价格合理,售后服务好……等。
像郑州鼎盛工程技术公司生产的组合式细碎机,将粗、中、细碎的作用组合在一台破碎机内,能将入口粒度为50~60cm的粗块料,经过此机的粗、中、细碎后,出口粒度<1mm占55%左右,1~3mm占30%左右,3~5mm约占15%左右;出口加转筛后除<1mm占55%外,其余全部<3mm,而且材质好,尤其是易损的锤头也是组合式的,将最好的耐磨材料用在锤头敲击物料的部位。