蜗杆传动机构的特点
蜗杆名词解释

蜗杆(Worm gear)是一种机械传动装置,由蜗轮和蜗杆组成。
蜗轮是一个带有螺旋齿的圆盘,而蜗杆是一个带有蜗旋的螺杆。
蜗轮的螺旋齿与蜗杆的蜗旋齿相互咬合,形成传动机构。
蜗杆传动具有一些特殊的特点和应用。
首先,蜗杆传动的传动比(即输入轴转动一周,输出轴转动的圈数)通常很高,可以达到很大的减速比。
这使得蜗杆传动在需要高减速比的应用中非常有用,如机床、输送带、提升装置等。
其次,蜗杆传动具有自锁性,即使在没有外部力的情况下,输出轴也不会主动转动回传动方向,这在某些需要防止倒转的场合非常重要。
蜗杆传动还有一些特殊的优点和限制。
例如,由于蜗杆的工作面积大,摩擦损失较大,传动效率通常较低。
此外,蜗杆传动在传动过程中也会产生较大的热量,需要考虑冷却和润滑等问题。
因此,在选择传动方式时,需要综合考虑传动比、自锁性、效率和冷却等因素。
总之,蜗杆是一种常见的机械传动装置,通过蜗轮和蜗杆的咬合来实现传递动力和减速的功能。
它在一些特殊的应用领域中具有重要的作用。
《机械设计》第12章 蜗杆传动
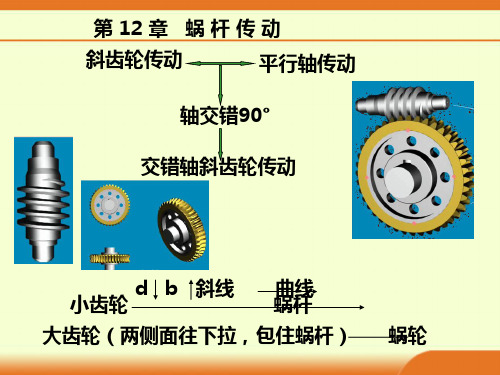
阿基米德蜗杆:αx=20°
标准值
法向直廓蜗杆、渐开线蜗杆:αn=20°
s
pz=zpx1 px1
2.蜗杆导程角γ和分度圆直径d1 螺纹
蜗杆
ψ πd1
tanψ =
s πd1
=
np πd1
∴ d1
=
Z1 tanγ
m
=
qm
γ πd1
tanγ
=
pZ πd1
=
πmZ πd1
1
=
mZ 1 d1
q
=
Z1 tanγ
具有良好的减摩性、耐磨性、跑合性和抗胶合能力
特点:软硬搭配
蜗杆硬:优质碳素钢、合金结构钢 经表面硬化及调制处理
蜗轮软:铸锡青铜、无锡青铜、灰铸铁
1、蜗杆材料
蜗杆一般采用碳素钢或合金钢制造。 对于高速重载的传动,蜗杆常用低碳合金钢, 如20Cr,20CrMnTi等,经渗碳淬火,表面硬度 HRC56~62,并应磨削。
MPa
= 12.86MPa < [σ F ]
齿根的弯曲疲劳强度校核合格。
(5)验算传动效率h
蜗杆分度圆速度为
v1
=
π d1n1
60×1000
=
3.14×112×1450 60×1000
m/
s
=
8.54m /
s
vs
= v1
cosλ
8.54
=
m / s = 8.59m / s
cos6.412°
查表4.9得
ρ v = 1°09′(1.15°)
h
(0.95
~
0.97)
tan tan( v)
H
480 d2
蜗杆传动机构的特点

蜗杆传动机构的特点
蜗杆传动机构是一种常用于减速装置的传动机构,具有如下特点:
1. 高传动比:蜗杆传动机构的传动比通常较大,可达到10:1
以上。
这使得它适用于需要较大减速比的场合,如工程机械、电动车辆等。
2. 大传动力:蜗杆传动机构的传动力矩较大,能够承受较大的负载。
这使得它适用于一些需要承受较大力矩的场合,如起重设备、石油机械等。
3. 反向离合功能:蜗杆传动机构具有一种特殊的反向离合功能,即只要蜗杆传动机构的输出端受到外力作用,传动机构就可以自动离合,避免了因外力反向作用引起的机械系统损坏。
4. 高传动效率:由于蜗杆传动机构的蜗杆与蜗轮摩擦面积大,因此其传动效率较高,一般可达到80%以上。
5. 安全可靠:蜗杆传动机构具有较好的自锁性能,即在没有外力作用时,输出轴不会自动运动。
这使得它在工作条件较为恶劣、要求安全可靠的场合得到广泛应用。
总之,蜗杆传动机构具有传动比大、传动力大、反向离合功能、传动效率高、安全可靠等特点,因此在各种机械传动装置中得到广泛应用。
蜗杆传动的基本参数

蜗杆传动的基本参数蜗杆传动是一种常见的传动机构,其主要由蜗轮与蜗杆组成。
蜗轮是一种齿轮,其齿形特殊,呈蜗旋线形状,而蜗杆是一种圆柱形的螺旋状轴。
蜗杆传动具有结构紧凑、承载能力大、传动比大、传动效率高等优势,在各种机械设备和工业领域中广泛应用。
蜗杆的蜗杆头径是指蜗杆轴上蜗杆的直径大小。
蜗杆头径会影响蜗杆传动的承载能力,一般来说,蜗杆头径越大,蜗杆传动的承载能力越大。
蜗杆步距是指蜗轮一次旋转所推动蜗杆前进的距离。
蜗杆步距决定了蜗杆传动的细分能力,即蜗轮每转一周,蜗杆前进一个步距,从而确定了蜗杆传动的传动比。
蜗杆长度是指蜗轮的宽度。
蜗杆长度会影响蜗杆传动的工作平稳性和传递扭矩的能力。
蜗杆的模数是指蜗轮齿廓和蜗杆螺旋线的截面形状的尺寸之比,是一个重要的参数。
模数的选择需要综合考虑蜗杆传动的应力和变形。
压力角是指蜗杆螺旋线与轴向的夹角,是蜗杆传动的设计中重要的参数之一、压力角的大小会影响蜗杆传动的接触性能和传动效率。
旋向是指蜗杆螺旋线的旋转方向,一般分为左旋和右旋两种。
蜗轮的模数是指蜗轮齿廓和蜗杆螺旋线的截面形状的尺寸之比。
蜗轮的模数需要与蜗杆的模数匹配,以确保传动的精度和工作平稳性。
压力角是指蜗轮齿廓与垂直于传动方向的线之间的夹角。
压力角的选择需要综合考虑蜗轮的齿强度和接触性能。
齿数是指蜗轮上齿的数量,影响蜗杆传动的传动比。
齿宽是指蜗轮齿廓沿蜗轮轴向的宽度。
齿宽需要满足传动扭矩和载荷要求。
螺旋角是指蜗轮上蜗杆螺旋线的扭曲角度。
螺旋角的选择需要考虑蜗杆传动的传动比和传动效率。
蜗轮蜗杆传动详解
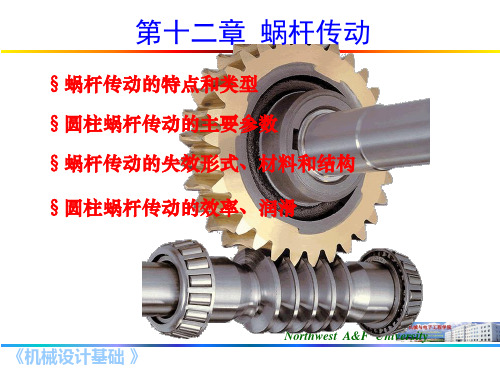
§蜗杆传动的特点和类型 §圆柱蜗杆传动的主要参数 §蜗杆传动的失效形式、材料和结构 §圆柱蜗杆传动的效率、润滑
《机械设计基础 》
Northwest A&F University
第一节 蜗杆传动的特点和类型
蜗杆传动是由蜗杆和蜗轮组成的,用于传,蜗轮是从动件。
第三节蜗杆传动的失效形式、材料和结构
二、蜗杆和蜗轮的结构
由于蜗杆的直径不大,所以常和轴做成一个整体(蜗杆 轴),当蜗杆的直径较大时,可以将轴与蜗杆分开制作。
无退刀槽,加工螺旋部分时只能用铣制的办法。
有退刀槽,螺旋部分可用车制,也可用铣制加工,但该结构
的刚度 较前一种差。
Northwest A&F University
蜗杆导程角
蜗轮螺旋角 径向间隙 标准中心距
第十二章 蜗杆传动
符号
d ha
hf da
df
c
a
计算公式
蜗杆
蜗轮
d1 mq
d2 mz
ha m h f 1.2m
d a1 (q 2)m da2 (Z2 2)m
d f 1 (q 2.4)m arctg Z1
q
d f 2 (Z 2 2.4)m
第十二章 蜗杆传动
第六节圆柱蜗杆传动的效率、润滑和热平衡计算
二、蜗杆传动的润滑
➢ 目的:减摩、散热。 ➢ 润滑油的粘度和给油方法可参照表11-5选取。 ➢ 一般根据相对滑动速度选择润滑油的粘度和给油方法。
蜗杆下置时,浸油深度应为蜗杆的一个齿高; 给油方法: 油池润滑: 蜗杆上置时,浸油深度约为蜗轮外径的 1/6~1/3。
圆弧圆柱蜗杆传动
环面蜗杆传动 蜗杆的外形是圆弧回转面,同时啮合的齿数多,传动平稳; 齿面利于润滑油膜形成,传动效率较高;
涡轮涡杆传动的特点

涡轮涡杆传动的特点
1.高效率:涡轮涡轮传动相对于齿轮传动和链传动等机械传动,具有更高的传动效率,可以达到90%以上。
2.高速比:涡轮涡轮传动在小尺寸中输出高扭矩,大速比。
可大幅度减少设备的体积和重量,满足高效率、小型化和轻量化的发展趋势。
3.高精度:涡轮涡轮传动具有高精度的传动特点,可实现精度高达0.1微米,适用于对精度要求较高的设备。
4.可靠性高:涡轮涡轮传动中没有摩擦部件,传动过程中没有磨损,故可靠性高,无需常规维护。
5.可逆性:涡轮涡轮传动不受传动方向的限制,可以灵活转向,实现正反转。
6.噪声小:由于涡轮涡轮传动没有摩擦轮齿等机械接触,传动过程中噪声较小。
7.结构简单:涡轮涡轮传动不需要复杂的变速机构,结构简单,易于制造和安装。
6-9 蜗杆传动
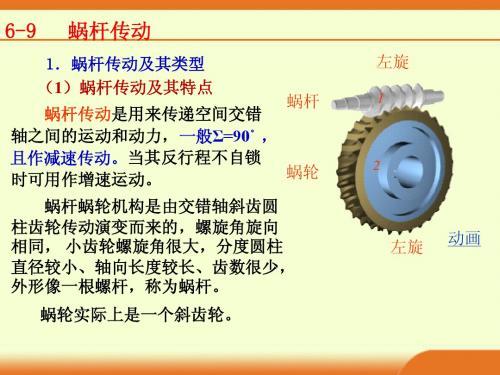
蜗杆
1
2
左旋
动画
蜗杆传动的特点和用途 1)传动比大,结构紧凑。 i=10—40,最大可达80。 若只传递运动,传动比可达1000。 2)传动平稳、振动、冲击噪声小。 3) 可制成具有自锁性的蜗杆。 4) 效率较低。η =0.7—0.8。 5) 轮齿间的相对滑动速度大,传动效 率低,需用减摩耐摩的材料制造蜗轮, 成本高。
整体式蜗轮
齿圈式蜗轮
镶铸式蜗轮
螺栓联接式蜗轮
观看涡轮照片
五 蜗杆传动的效率
1 蜗杆传动效率
h h1 h 2 h 3
h1─计及啮合摩擦损耗的效率; h2─计及轴承摩擦损耗的效率; h3─计及溅油损耗的效率; h1是对总效率影响最大的因素,可由下式确定: tan 式中: -蜗杆的导程角; h1 tan( v ) -当量摩擦角。
平面定轴轮系从动轮的转向,也可以采用画箭头的方法确定。 箭头方向表示齿轮(或构件)最前点的线速度方向。
3)空间定轴轮系传动速比的计算
传动速比的大小仍采用 推广式计算,确定从动轮的 转向,只能采用画箭头的方 法。圆锥齿轮传动,表示齿 轮副转向的箭头同时指向或 同时背离相互啮合处。 蜗杆传动,从动蜗轮转向 判定方法用蜗杆“左、右手 法则” 。
角标a和b分别表示输入和输出 轮系的速比计算,包括计算其速比的大小和确定输出轴 的转动方向两个内容。 最简单的定轴轮系是由一对齿轮所组成的。其传动速比为 i=n1/n2 = ±z2/ z1
一对齿轮的传动比大小为其齿数的反比。若考虑转向关 系,外啮合时,两轮转向相反,传动比取“-”号;内啮合时, 两轮转向相同,传动比取“+”号。
方向判断如图所示
例:如图所示的轮系,已知 z1=24, z2=46, z2’=23, z3=48, z4=35, z4’=
蜗杆传动的特点及应用
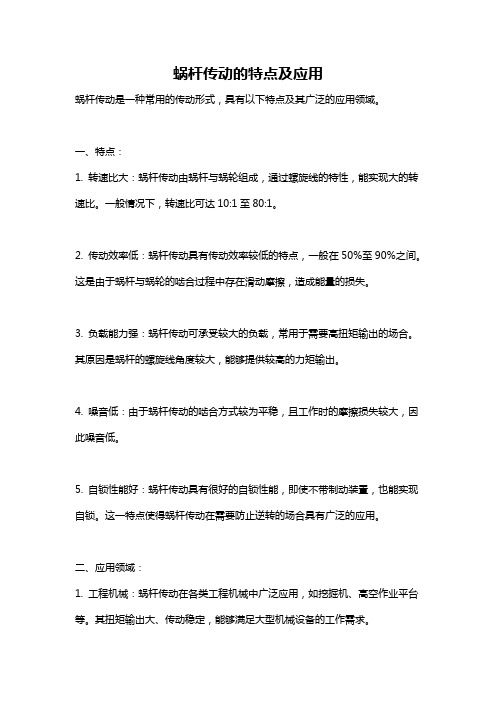
蜗杆传动的特点及应用蜗杆传动是一种常用的传动形式,具有以下特点及其广泛的应用领域。
一、特点:1. 转速比大:蜗杆传动由蜗杆与蜗轮组成,通过螺旋线的特性,能实现大的转速比。
一般情况下,转速比可达10:1至80:1。
2. 传动效率低:蜗杆传动具有传动效率较低的特点,一般在50%至90%之间。
这是由于蜗杆与蜗轮的啮合过程中存在滑动摩擦,造成能量的损失。
3. 负载能力强:蜗杆传动可承受较大的负载,常用于需要高扭矩输出的场合。
其原因是蜗杆的螺旋线角度较大,能够提供较高的力矩输出。
4. 噪音低:由于蜗杆传动的啮合方式较为平稳,且工作时的摩擦损失较大,因此噪音低。
5. 自锁性能好:蜗杆传动具有很好的自锁性能,即使不带制动装置,也能实现自锁。
这一特点使得蜗杆传动在需要防止逆转的场合具有广泛的应用。
二、应用领域:1. 工程机械:蜗杆传动在各类工程机械中广泛应用,如挖掘机、高空作业平台等。
其扭矩输出大、传动稳定,能够满足大型机械设备的工作需求。
2. 汽车制造:蜗杆传动在汽车制造中的应用主要体现在汽车座椅的调节、车窗升降等方面。
由于蜗杆传动自锁性能好,可以确保座椅和车窗在固定位置稳定。
3. 纺织设备:蜗杆传动在纺织设备中具有重要的应用,如纺纱机、织布机等。
其优点在于传动稳定、传动比例大,能够满足纺织设备对转速和力矩的要求。
4. 食品加工:蜗杆传动在食品加工设备中的应用主要体现在混合搅拌设备、切割设备等。
由于蜗杆传动的传动效率低、噪音低的特点,能够提供更好的操作环境。
5. 机械加工:蜗杆传动在机械加工中的应用主要体现在钻床、铣床等设备上。
由于蜗杆传动能够提供较高的力矩输出,适用于加工过程中需要大力矩的场合。
6. 冶金设备:蜗杆传动在冶金设备中应用广泛,如轧机、钢丝拉拔机等。
冶金设备对传动精度和负载能力要求较高,蜗杆传动能够满足这些要求。
总结以上特点和应用领域,蜗杆传动作为一种传动方式,具有转速比大、负载能力强、噪音低等优点,广泛应用于工程机械、汽车制造、纺织设备、食品加工、机械加工和冶金设备等领域中。
简述蜗杆传动的特点

简述蜗杆传动的特点蜗杆传动是一种常见的传动装置,其特点主要体现在以下几个方面:1. 高传动比:蜗杆传动的传动比一般较高,通常在10:1到100:1之间。
蜗杆的螺旋形状决定了其传动效果,使得蜗杆传动可以实现大范围的传动比调节,满足不同设备的传动需求。
2. 紧凑结构:蜗杆传动具有紧凑的结构,占用空间小。
蜗杆传动通常由蜗杆和蜗轮组成,且垂直安装。
相比其他传动装置,如齿轮传动,蜗杆传动在垂直安装时可以更好地利用空间,节省设备的体积。
3. 平稳运行:蜗杆传动具有平稳的运行特点,传动过程中噪音较小,振动小。
由于蜗杆的螺旋形状,蜗杆传动可以实现多齿同时接触,使得传动过程中力的分布均匀,减小了噪音和振动的产生。
4. 自锁性:蜗杆传动具有良好的自锁性能,即在无外力作用下,传动装置可以保持静止状态。
这是由于蜗杆的斜面角度较大,使得蜗杆传动具有较高的摩擦角,可以防止装置在停止工作时的自发运动。
5. 传动效率较低:蜗杆传动的传动效率较低,通常在30%到90%之间。
这是由于蜗杆传动的蜗杆与蜗轮之间的摩擦和滑动。
在实际应用中,需要根据具体要求和条件选择合适的传动效率。
6. 承载能力强:蜗杆传动具有较强的承载能力,能够传递较大的转矩。
这是由于蜗杆传动的蜗杆和蜗轮的摩擦面积较大,且接触长度较长,能够承受较大的压力和载荷。
7. 长寿命:蜗杆传动具有较长的使用寿命,耐磨损、耐腐蚀。
传动过程中,蜗杆和蜗轮的接触面积大,摩擦面经过特殊处理,可以有效减少磨损和腐蚀,提高传动装置的寿命。
蜗杆传动的特点使得其在许多机械设备和工业领域得到广泛应用。
例如,蜗杆传动常用于起重机、输送机、搅拌机等设备中实现扭矩传递和传动比调节。
此外,在汽车和机床等领域,蜗杆传动也被用于变速器和传动装置中,实现不同速度和转矩的输出。
总的来说,蜗杆传动具有高传动比、紧凑结构、平稳运行、自锁性、传动效率较低、承载能力强、长寿命等特点。
这些特点使得蜗杆传动在各个领域得到广泛应用,满足不同设备的传动需求,为机械装置的运行提供了可靠的动力支持。
机械设计基础课件第六章蜗杆传动
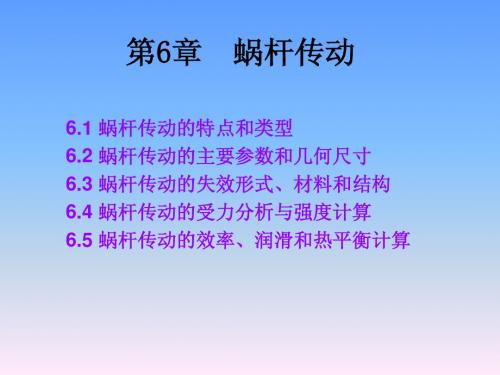
例如,齿形为A、齿形角α为20°、模数为10 mm、 分度圆直径为90 mm、头数为2的右旋圆柱蜗杆;齿数 为80的蜗轮以及由它们组成的圆柱蜗杆传动的标记如下。 蜗杆标记为:蜗杆
ZA10 90 R2
蜗轮标记为:蜗轮
ZA10 80
蜗杆传动标记为: ZA10 90 R 2 / 80
6.3
6.3.1
6.4.2
蜗杆传动的强度计算
蜗轮齿面接触疲劳强度计算与斜齿轮相似,由赫 兹公式可得,蜗杆传动接触强度校核公式
中间平面
2、传动比 i 、蜗杆头数Z1、蜗轮齿数Z2 传动比——从动轮齿数比主动轮齿数
n i 1
n2
Z 2
Z1
u
蜗杆头数Z1 一般Z1=1、2、4, 单头,i大,易自锁,效率低, 但精度好;多头杆,η↑,但加工困难,精度↓ 蜗轮齿数Z2 为避免根切, Z2 26 动力传动, Z2 80 具体应用传动比 i 、蜗杆头数Z1、蜗轮齿数Z2, 可以参考教材表6-1、6-2。
蜗杆传动的失效形式、材料和结构
蜗杆传动的滑动速度
在蜗杆传动中,蜗杆蜗轮的啮合齿面间 会产生很大的相对滑动速度 s 如图所示。
s
cos
1
sin
2
式中: 1 2 ——蜗杆和蜗轮 分度圆上的圆周速度.
6.3.2
蜗杆传动的失效形式和设计Байду номын сангаас则
和齿轮传动一样,蜗杆传动的失效形式主要 有:胶合、磨损、疲劳点蚀和轮齿折断等。由于 蜗杆传动啮合面间的相对滑动速度较大,效率低, 发热量大,在润滑和散热不良时,胶合和磨损为 主要失效形式。 蜗杆传动的设计准则为:闭式蜗杆传动按蜗 轮轮齿的齿面接触疲劳强度进行设计计算,按齿 根弯曲疲劳强度校核,并进行热平衡验算;开式 蜗杆传动,按保证齿根弯曲疲劳强度进行设计。
蜗杆传动的特点
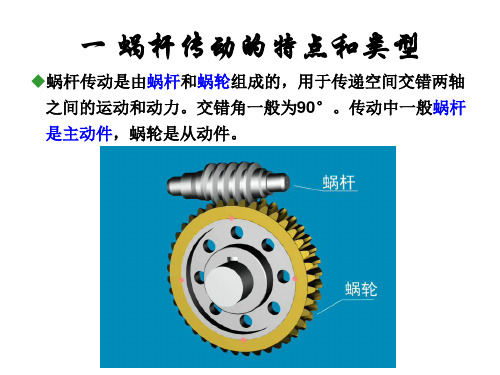
值选取。
z2= i z1 。 如 z2太小,将使传动平稳性变差。如 z2太大,蜗轮 直径将增大,使蜗杆支承间距加大,降低蜗杆的弯曲刚度。
一般取 z2=32~80
中间平面:通过蜗杆轴线并与蜗轮轴线垂直的平面。
是蜗杆的轴面
是蜗轮的端面
蜗杆、蜗轮的参数和尺寸大多在中间平面(主平面)内确定。
由于蜗轮是用与蜗杆形状相仿的滚刀,按范成原理切制轮齿, 所以ZA蜗杆传动中间平面内蜗轮与蜗杆的啮合就相当于渐 开线齿轮与齿条的啮合。
L p
主 平 面
B
在主平面内,蜗轮蜗杆的传动相当于齿轮齿条的啮合传动。
渐开线
基圆
渐开线蜗杆(ZI)
加工:刀刃与蜗杆的基圆柱相切 特点:端面---渐开线
后两种蜗杆的加工,刀具安装较困难,生产率低,故常用阿 基米德蜗杆。
二、圆柱蜗杆传动的主要参数:
1. 模数m和压力角α
中间平面:通过蜗杆轴线并与蜗轮轴线垂直的平面。
主平面
β1 γ=
一 蜗杆传动的特点和类型
蜗杆传动是由蜗杆和蜗轮组成的,用于传递空间交错两轴
之间的运动和动力。交错角一般为90°。传动中一般蜗杆
是主动件,蜗轮是从动件。
蜗杆传动的特点:
1.传动比大,一般 i =28~80; 2.重合度大,传动平稳,噪声低; 3.结构紧凑,可实现反行程自锁; 4. 蜗杆传动的主要缺点齿面的相对滑动速度大,效率低,
圆柱蜗杆传动
环面蜗杆传动
蜗杆的外形是圆弧回转面,同时啮合的齿数多,传动平稳;
蜗轮蜗杆传动设计

723
二、蜗轮蜗杆传动设计
—设计实例
1、蜗轮轮齿齿面接触强度计算 (1)选材料:确定许用接触压力[σH] 蜗杆用45钢,表面淬火45-50HRC; 蜗轮用ZCuSn10P1(10-1锡青铜)砂型铸造。由表查得 [σH]=200。 (2)选用蜗杆头数z1,确定蜗轮齿数z2 传动比i=n1/n2=960/70=13.71 因为传动比不大,为了提高传动效率,可选z1=2 则z2=i·z1=13.71×2=27.42,取z2=27。
mm
式中:Zρ为蜗杆传动的接触线长度和曲率半径对接触强度的影响系数 。
K为载荷系数。 其它的符号含义与齿轮传动部分相同。
713
三、蜗轮蜗杆传动设计
—普通蜗杆传动的承载能力计算
许用接触应力[σH],根据蜗轮材料的不同,可在下两表中选取。 1、蜗轮材料为灰铸铁及铸铝铁青铜时,其许用应力直接在下表选取 :
考虑啮合摩擦损耗是蜗杆的传动效率:
77
三、蜗轮蜗杆传动设计
—普通蜗杆传动的参数与尺寸
导程角γ增大时,传动效率将提高,导程角γ 与蜗杆 头数z1之间有如下关系:
显然,当蜗杆头数z1增多时,导程角γ增大,从而使传动效率提高。 但头数增多给制造带来困难,且效率提高不显著,故通常蜗杆头数取为1 、2、4、6 。
由于上述特点,蜗杆传动主要用于运动传递,而在动力传输中的应用 受到限制。
73
三、蜗轮蜗杆传动设计
—蜗杆传动类型
普通圆柱蜗杆传动
阿基米德蜗杆、渐开线蜗杆 法向直廓蜗杆、锥面包络圆柱蜗杆
其齿面一般是在车床上用直线刀刃的车刀切制而成,车刀安装
圆柱蜗杆传动 位置不同,加工出的蜗杆齿面的齿廓形状不同。
圆弧圆柱蜗杆传动
724
机械设计06章(蜗杆传动)
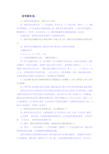
思考题答案:6-1 蜗杆传动有何特点,适用于什么场合?答:蜗杆传动的特点有:(1)结构紧凑、传动比大;(2)传动平稳、噪声小;(3)当蜗杆的导程角γ1小于轮齿间的当量摩擦角ϕv时,蜗杆传动具有自锁性;(4)相对滑动速度大,摩擦损耗大,易发热,传动效率低;(5)蜗轮用耐磨材料青铜制造制造,成本高。
适用的场合:蜗杆机构用来实现两个交错轴间的传动。
6-2 蜗杆传动的模数和压力角是在哪个平面上定义的?蜗杆传动正确啮合的条件是什么?答:蜗杆传动的模数和压力角是在中间平面内定义的即为标准值。
正确啮合条件:m a1=m t2=m,αa1=αt2=200,γ=β6-3 如何选择蜗杆的头数z1、蜗轮的齿数z2?答:较少的蜗杆头数(如:单头蜗杆)可以实现较大的传动比,但传动效率较低;蜗杆头数越多,传动效率越高,但蜗杆头数过多时不易加工。
通常蜗杆头数取为1、2、4、6。
(蜗杆头数与传动效率关系) 。
蜗轮齿数主要取决于传动比,即z2= i z1。
z2不宜太小(如z2>28),否则将使传动平稳性变差。
z2也不宜太大,否则在模数一定时,蜗轮直径将增大,从而使相啮合的蜗杆支承间距加大,降低蜗杆的弯曲刚度。
6-4设计蜗杆传动时如何确定蜗杆的分度圆直径d1和模数m,为什么要规定m和d1的对应标准值?答:中间平面:通过蜗杆轴线并垂直于蜗轮轴线的平面为中间平面(蜗杆轴面,蜗轮端面) 蜗杆传动的设计计算都是以中间平面内的参数和几何关系为标准,在中间平面上,蜗轮与蜗杆的啮合相当于渐开线齿轮与齿条的啮合。
GB10088-88已将d1标准化为一系列数值,蜗轮是由与蜗杆相似的滚刀展成切制而来的,蜗杆中圆直径d1不仅与m有关,还随Z1/tan γ的数值变化。
所以即使m相同,也会有很多不同直径的蜗杆,也就要求具备很多刀具,为减少刀具的型号,将蜗杆d1标准化。
6-5 蜗杆传动的失效形式是有哪几种、设计准则是什么?答:蜗杆传动的失效形式(主要是蜗轮失效)闭式传动:胶合点蚀;开式传动:磨损。
蜗轮蜗杆传动

目,国家标准对每一标准模数规定了一定数目的标准蜗杆分度圆直径d1(参见 表12-1)。 直径d1与模数m的比值称为蜗杆的直径系数q。即:
1. 模数m和压力角α 中间平面:通过蜗杆轴线并与蜗轮轴线垂直的平面。
主平面
β1 γ=β
第十二章 蜗杆传动
第二节圆柱蜗杆传动的主要参数和几何尺寸
中间平面:通过蜗杆轴线并与蜗轮轴线垂直的平面。 是蜗杆的轴面 是蜗轮的端面
v 蜗杆、蜗轮的参数和尺寸大多在中间平面(主平面)内确定。
v 由于蜗轮是用与蜗杆形状相仿的滚刀,按范成原理切制轮齿
由于蜗杆齿是连续的螺旋,其材料的强度又很高,因而失效总是出 现在蜗轮上,所以蜗杆传动只需对蜗轮轮齿进行强度计算。
第十二章 蜗杆传动
第五节圆柱蜗杆传动的强度计算
1. 蜗轮齿面接触疲劳强度计算
目的:防止“点蚀”和“胶合”失效。 强度条件:σH≤[σH] 以蜗杆蜗轮节点为计算点,计算齿面接触应力 σH 。 校核公式:
轴),当蜗杆的直径较大时,可以将轴与蜗杆分开制作。
无退刀槽,加工螺旋部分时只能用铣制的办法。
有退刀槽,螺旋部分可用车制,也可用铣制加工,但该结构 的刚度 较前一种差。
第十二章 蜗杆传动
第三节蜗杆传动的失效形式、材料和结构
为了减摩的需要,蜗轮通常要用青铜制作。为了节省铜材,当蜗轮直径较大时 ,采用组合式蜗轮结构,齿圈用青铜,轮芯用铸铁或碳素钢。常用蜗轮的结构 形式如下:
=2/10=0.2
γ =11.3099°(11°18‘36“)
(3) 传动中心距 a =0.5(q + z2 )
涡轮涡杆传动的特点

涡轮涡杆传动的特点涡轮涡杆传动,简称涡轮传动,是一种将高速旋转的涡轮机转速降低,输出扭矩的传动方式。
它具有以下特点:1.高效性:涡轮传动的转动部件全部为旋转部件,没有磨损、摩擦和损耗,因此具有高效性和长寿命。
2.高转矩:涡轮传动的转速可以很高,但输出扭矩也可以很大,适用于需要大扭矩的场合。
3.可靠性:涡轮传动的结构简单,没有传统传动中的齿轮、链条等易损部件,因此具有较高的可靠性和稳定性。
4.适应性强:涡轮传动可以适应不同的转速和扭矩需求,具有较高的灵活性。
5.噪音小:由于涡轮传动的转动部件全部为旋转部件,没有间隙和冲击,因此噪音较小。
6.重量轻:涡轮传动的结构简单,没有传统传动中的齿轮、链条等重量较大的部件,因此重量较轻。
在航空、航天、汽车、轮船、发电等领域中,涡轮涡杆传动已广泛应用。
例如,飞机的涡轮发动机、汽车的涡轮增压器、轮船的涡轮机和发电厂的涡轮发电机等。
涡轮传动的中心扩展下,我们可以探讨涡轮传动在未来的应用和发展趋势。
随着科技的不断进步,涡轮传动将不断发展壮大。
未来涡轮传动将更加智能化、数字化和网络化,具有更高的自适应性和可靠性。
同时,涡轮传动将更加轻量化、紧凑化和高效化,以适应未来节能减排的需求。
另外,涡轮传动将更加多样化和个性化,以满足不同行业和领域的需求。
例如,在航空领域,涡轮发动机将更加高效、可靠和安全,以适应未来航空业的快速发展。
在轮船领域,涡轮机将更加节能、环保和智能化,以适应未来航运业的需求。
在汽车领域,涡轮增压器将更加轻量化、高效化和数字化,以适应未来汽车的发展趋势。
涡轮涡杆传动具有高效、高转矩、可靠、适应性强、噪音小和重量轻等特点。
在未来,涡轮传动将更加智能化、数字化、网络化、轻量化、紧凑化、高效化、多样化和个性化,以适应不同领域和行业的需求。
机械设计基础 第12章 蜗杆传动
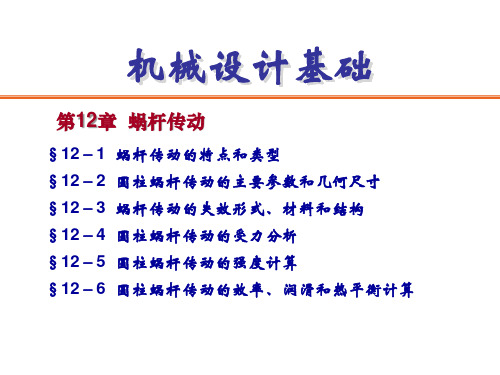
d1 mq
pz z1 px
tan pz z1 px z1m z1 d1 d1 d1 q
蜗杆导程 蜗杆轴向齿距
蜗杆导程角
d1越小(或q越小), 越大,传动效率越高,但蜗杆的刚度
和强度越低。 通常,转速高的蜗杆可取较小的d1值,蜗轮齿 数z2较大时可取较大的d1值。
当导程角 小于当量摩擦角时,蜗轮为主动时则发生自锁。
蜗杆材料:20Cr渗碳淬火;40Cr、35CrMo淬火;45调质
蜗轮材料:ZCuSn10P1 ZCuAl10Fe3
vs 25 m/s 耐磨性好、抗胶合
vs 6 m/s 价格便宜
HT200
vs 2 m/s 经济、低速
二、 蜗杆和蜗轮的结构 蜗杆结构:通常与轴为一体,蜗杆轴
蜗轮结构:整体式(铸铁蜗轮或尺寸很小的青铜蜗轮) 组合式(有色金属齿圈+钢或铸铁轮芯)
二、 蜗杆传动的类型 因蜗轮是用形状与蜗杆相同的滚刀加工而成,故蜗杆传动 的类型是按蜗杆的不同进行分类。
按蜗杆形状分:圆柱蜗杆和环面蜗杆。
圆柱蜗杆用直线刀刃的车刀车削成形,根据刀具安装位置 的不同,可加工出阿基米德蜗杆和渐开线蜗杆等。
圆柱蜗杆传动
环面蜗杆传动
阿基米德蜗杆:刀具两刃与蜗杆轴线共面;轴面内相当于 直线齿条,端面齿形为阿基米德螺线。 渐开线蜗杆:用两把车刀,其刀刃顶面切于蜗杆基圆柱; 端面齿廓为渐开线,在切于蜗杆基圆柱的剖面内,齿廓的 一侧为直线,轴面内为凸廓曲线。 蜗杆有左、右旋之分,常用的是右旋蜗杆。
蜗轮径向力
各力方向的确定: 类似于斜齿轮
【例】图示蜗杆传动,蜗杆1主动,转向如图。试指出蜗轮2、 3轮齿旋向及转向,并画出蜗杆1上啮合处的作用力三个分力 方向。
2
电梯蜗轮蜗杆传动的特点

电梯蜗轮蜗杆传动的特点
电梯蜗轮蜗杆传动是一种常见的传动方式,其特点主要包括以下几个方面:
1. 转速比大:电梯蜗轮蜗杆传动的转速比通常很大,可以达到20:1或更高。
这使得电梯能够通过较小的电机驱动,实现较大的升降高度。
2. 力矩传递平稳:蜗轮蜗杆传动的结构使得力矩传递非常平稳,较少出现冲击和振动,从而可以保证电梯的平稳运行。
3. 效率低:蜗轮蜗杆传动的效率通常较低,只有50%左右,这意味着电梯需要更大的电力输入才能实现同样的升降效果。
4. 维护成本高:由于蜗轮蜗杆传动的结构较为复杂,维护成本也比较高,需要定期进行润滑和检查,以保证传动的正常运转。
5. 可靠性较高:蜗轮蜗杆传动是一种结构简单、可靠性较高的传动方式,能够适应各种恶劣环境和工作条件,因此广泛应用于电梯等升降设备中。
- 1 -。
- 1、下载文档前请自行甄别文档内容的完整性,平台不提供额外的编辑、内容补充、找答案等附加服务。
- 2、"仅部分预览"的文档,不可在线预览部分如存在完整性等问题,可反馈申请退款(可完整预览的文档不适用该条件!)。
- 3、如文档侵犯您的权益,请联系客服反馈,我们会尽快为您处理(人工客服工作时间:9:00-18:30)。
蜗杆传动机构的特点
蜗杆传动机构是一种常见的传动装置,具有以下几个特点。
1. 转速比大:蜗杆传动机构的转速比通常较大,可以达到几十甚至几百倍。
这是由于蜗杆的螺旋形状决定的,使得蜗杆在传动过程中可以实现大范围的速度降低。
2. 传动效率低:蜗杆传动机构的传动效率较低,一般在30%~80%之间。
这是由于蜗杆与蜗轮之间的摩擦和滑动造成的,导致能量损失较大。
因此,在选择传动装置时,需要根据实际应用需求综合考虑。
3. 传动平稳:蜗杆传动机构的传动平稳性较好。
由于蜗杆与蜗轮之间的啮合面积大,传动过程中摩擦力较大,因此具有较好的抗冲击和减振性能。
这使得蜗杆传动机构在一些对传动平稳性要求较高的场合得到广泛应用。
4. 结构紧凑:蜗杆传动机构通常具有结构紧凑的特点。
蜗杆与蜗轮之间的啮合角度较小,使得整个传动装置的体积相对较小,可以在有限的空间内实现较大的速度降低。
因此,蜗杆传动机构在机械设计中常被用于空间有限的场合。
5. 可靠性高:蜗杆传动机构的可靠性较高。
蜗杆与蜗轮的啮合面积大,摩擦力大,使得传动装置的承载能力较强,能够承受较大的负
载。
同时,蜗杆传动机构的结构简单,零部件较少,减少了故障的可能性,提高了传动装置的可靠性。
6. 自锁性能好:蜗杆传动机构具有较好的自锁性能。
蜗杆与蜗轮的摩擦力使得蜗杆传动机构具有一定的防逆转能力,即使在停机或负载变化时,也能保持传动装置的稳定性,避免了意外事故的发生。
7. 加工精度要求高:蜗杆传动机构的加工精度要求较高。
蜗杆和蜗轮的啮合面积大,工作时摩擦力较大,因此需要保证蜗杆和蜗轮的啮合面具有较高的配合精度,避免因加工精度不足而导致的传动效率下降、噪声增加等问题。
蜗杆传动机构具有转速比大、传动效率低、传动平稳、结构紧凑、可靠性高、自锁性能好以及加工精度要求高等特点。
这些特点使得蜗杆传动机构在一些特定的工程领域,如工程机械、船舶、起重设备等方面得到了广泛应用。