高精度弯曲件工艺方案及改进措施探讨
弯曲件常见质量问题改善对策
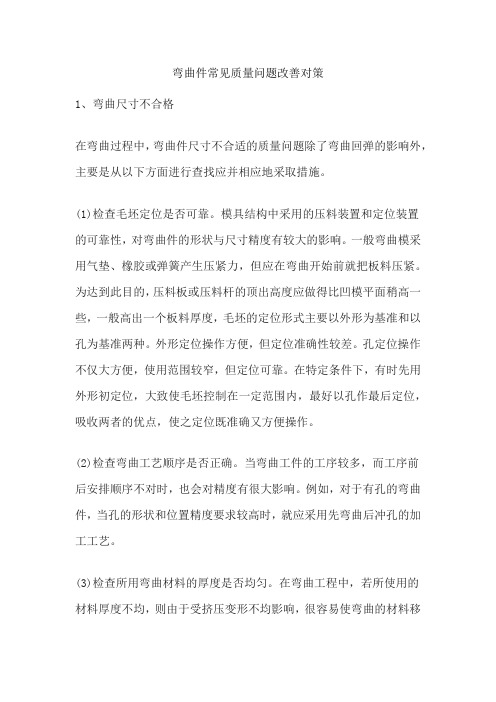
弯曲件常见质量问题改善对策1、弯曲尺寸不合格在弯曲过程中,弯曲件尺寸不合适的质量问题除了弯曲回弹的影响外,主要是从以下方面进行查找应并相应地采取措施。
(1)检查毛坯定位是否可靠。
模具结构中采用的压料装置和定位装置的可靠性,对弯曲件的形状与尺寸精度有较大的影响。
一般弯曲模采用气垫、橡胶或弹簧产生压紧力,但应在弯曲开始前就把板料压紧。
为达到此目的,压料板或压料杆的顶出高度应做得比凹模平面稍高一些,一般高出一个板料厚度,毛坯的定位形式主要以外形为基准和以孔为基准两种。
外形定位操作方便,但定位准确性较差。
孔定位操作不仅大方便,使用范围较窄,但定位可靠。
在特定条件下,有时先用外形初定位,大致使毛坯控制在一定范围内,最好以孔作最后定位,吸收两者的优点,使之定位既准确又方便操作。
(2)检查弯曲工艺顺序是否正确。
当弯曲工件的工序较多,而工序前后安排顺序不对时,也会对精度有很大影响。
例如,对于有孔的弯曲件,当孔的形状和位置精度要求较高时,就应采用先弯曲后冲孔的加工工艺。
(3)检查所用弯曲材料的厚度是否均匀。
在弯曲工程中,若所使用的材料厚度不均,则由于受挤压变形不均影响,很容易使弯曲的材料移动,产生弯曲件的高度尺寸不定。
解决措施是:将凹模修整成可换式镶块结构,通过调整弯曲模间隙的办法来解决;或更换材料,采用料厚均匀稳定的板料。
(4)检查模具两端的弯曲凹模圆角是否均匀一致。
弯曲模在长期使用过程中,常会使凹模圆角半径发生变化,且左右凹模圆角半径不对称一致,从而在弯曲过程中使弯曲件发生移动造成弯曲尺寸发生变化。
解决措施是:修磨凹模圆角半径合格,且使其左右堆成、大小一致。
(5)检查压力机的吨位、气垫压力是否合乎要求。
压力机的吨位及气垫压力会直接影响到弯曲件的尺寸精度,一般应选用吨位大些且精度较高的压力机,通常取加工力是压力机吨位70%-80%比较合适。
(6)检查并重新校核弯曲展开料是否正确。
弯曲件展开料是否正确直接影响到弯曲件尺寸是否合格。
高精度弯曲件工艺方案及改进措施探讨

高精度弯曲件工艺方案及改进措施探讨随着现代加工技术的不断发展,许多零件加工工艺得到了大幅度的优化,其中高精度弯曲件的加工技术得到了广泛的应用。
高精度弯曲件是一种精度要求非常高的零件,其加工质量直接决定了其在使用过程中的性能和寿命。
因此,研究高精度弯曲件的加工工艺方案及改进措施对于提高产品质量和供应能力具有重要意义。
高精度弯曲件的加工工艺方案通常包括以下几个方面:1.材料选择材料的选择是决定加工工艺方案的重要因素之一。
在选择材料时要考虑到零件的使用环境和使用要求,以及材料的成本、加工性能和机械性能等因素。
通常情况下,高强度、高韧性和耐腐蚀性能好的材料是首选。
2.模具设计模具的设计是决定加工工艺方案的另一个重要因素。
在设计模具时要根据零件的几何形状和尺寸、材料性能等因素确定模具的结构类型、尺寸和加工精度。
通常情况下,采用高精度数控刀具进行切削是一种较为常见的加工方式。
3.加工过程控制加工过程控制是确保零件加工精度的关键措施。
在加工过程中,需要掌握适当的加工参数,以确保整个加工过程的稳定性和一致性。
此外,还需要采用适当的加工润滑剂和冷却液,以确保加工质量和延长模具的使用寿命。
4.质量检测及控制质量检测及控制是确保零件加工质量的关键环节。
在加工完成后,需要通过各种检测手段对零件的尺寸精度、表面质量、硬度等进行检测。
如果发现零件存在质量问题,需要及时调整加工工艺参数或改进模具设计。
此外,还需要建立合理的质量控制体系,以确保零件加工质量的稳定性和一致性。
二、改进措施为进一步提升高精度弯曲件的加工质量和供应能力,需要采取一系列改进措施。
具体措施如下:1. 引进先进加工设备和技术引进先进加工设备和技术是提高高精度弯曲件加工能力的重要措施。
目前,一些国际知名的设备和技术已得到广泛应用,如高精度数控加工中心、激光切割机和全自动弯曲机等。
2. 采用高强度材料采用高强度、高韧性的材料是提高高精度弯曲件质量的关键措施。
该类材料具有优异的机械性能和抗弯曲性能,能够保证零件在使用过程中的安全性和可靠性。
高精度弯曲件工艺方案及改进措施探讨
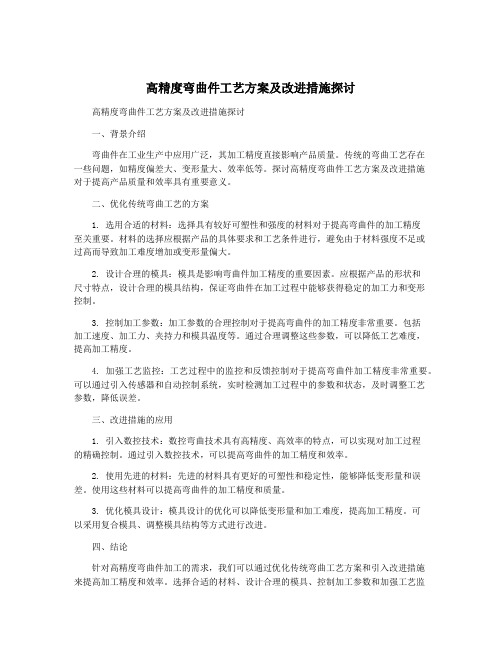
高精度弯曲件工艺方案及改进措施探讨高精度弯曲件工艺方案及改进措施探讨一、背景介绍弯曲件在工业生产中应用广泛,其加工精度直接影响产品质量。
传统的弯曲工艺存在一些问题,如精度偏差大、变形量大、效率低等。
探讨高精度弯曲件工艺方案及改进措施对于提高产品质量和效率具有重要意义。
二、优化传统弯曲工艺的方案1. 选用合适的材料:选择具有较好可塑性和强度的材料对于提高弯曲件的加工精度至关重要。
材料的选择应根据产品的具体要求和工艺条件进行,避免由于材料强度不足或过高而导致加工难度增加或变形量偏大。
2. 设计合理的模具:模具是影响弯曲件加工精度的重要因素。
应根据产品的形状和尺寸特点,设计合理的模具结构,保证弯曲件在加工过程中能够获得稳定的加工力和变形控制。
3. 控制加工参数:加工参数的合理控制对于提高弯曲件的加工精度非常重要。
包括加工速度、加工力、夹持力和模具温度等。
通过合理调整这些参数,可以降低工艺难度,提高加工精度。
4. 加强工艺监控:工艺过程中的监控和反馈控制对于提高弯曲件加工精度非常重要。
可以通过引入传感器和自动控制系统,实时检测加工过程中的参数和状态,及时调整工艺参数,降低误差。
三、改进措施的应用1. 引入数控技术:数控弯曲技术具有高精度、高效率的特点,可以实现对加工过程的精确控制。
通过引入数控技术,可以提高弯曲件的加工精度和效率。
2. 使用先进的材料:先进的材料具有更好的可塑性和稳定性,能够降低变形量和误差。
使用这些材料可以提高弯曲件的加工精度和质量。
3. 优化模具设计:模具设计的优化可以降低变形量和加工难度,提高加工精度。
可以采用复合模具、调整模具结构等方式进行改进。
四、结论针对高精度弯曲件加工的需求,我们可以通过优化传统弯曲工艺方案和引入改进措施来提高加工精度和效率。
选择合适的材料、设计合理的模具、控制加工参数和加强工艺监控是提高加工精度的关键。
引入数控技术、使用先进的材料、优化模具设计和引入人工智能技术等也是提高加工精度的重要手段。
高精度弯曲件工艺方案及改进措施探讨

高精度弯曲件工艺方案及改进措施探讨一、前言高精度的弯曲件是机械加工中常见的一种工艺,它在航空航天、汽车制造等领域都有着广泛的应用。
由于受到材料性能、设备精度、工艺流程等多方面因素的影响,高精度弯曲件的加工难度很高。
本文将从高精度弯曲件的工艺方案和改进措施两个方面展开讨论,以探讨如何提高高精度弯曲件的加工精度和效率。
二、高精度弯曲件的工艺方案1.材料选择高精度弯曲件的材料通常是金属材料,如不锈钢、铝合金等。
在选择材料时,需要考虑材料的变形性、硬度、导热性等因素。
一般来说,选择硬度适中、变形性好的材料可以提高弯曲件的加工精度。
2.工艺路线设计工艺路线的设计是高精度弯曲件加工的关键环节。
在设计工艺路线时,需要考虑到材料的特性、加工的难度、设备的精度等因素。
合理的工艺路线可以有效地减少加工难度,提高加工效率,同时保证产品的质量。
3.设备选择在高精度弯曲件加工中,设备的选择直接影响着加工的精度和效率。
一般来说,对于高精度的弯曲件加工,需要选择精度高、稳定性好的设备。
比如数控弯曲机、数控激光切割机等,这些设备能够提供更精确的加工,保证产品的精度要求。
4.工艺参数控制在实际的加工过程中,工艺参数的控制是非常重要的。
比如弯曲件的弯曲角度、弯曲速度、刀具切削深度等参数都需要精确控制,以保证产品的精度要求。
三、高精度弯曲件的改进措施1.提高设备精度设备的精度直接决定了产品的加工精度。
一方面可以通过更新设备,提高设备的加工精度。
另一方面可以通过对设备进行定期维护和保养,保证设备的稳定性和精度。
2.优化工艺路线通过优化工艺路线,可以降低产品的加工难度,提高加工效率,同时确保产品的质量。
比如可以通过减少工序、改变工序顺序等方式来优化工艺路线。
3.加强员工培训员工是生产过程中重要的一环,他们的技术水平和操作技能直接影响着产品的质量。
可以通过加强员工培训,提高员工的技术水平和操作技能,以提高产品的加工精度。
4.引进先进的加工技术随着科学技术的不断进步,新的加工技术不断涌现。
高楼主材弯曲检查的质量问题与质量改进措施

高楼主材弯曲检查的质量问题与质量改进措施近年来,随着城市建设的快速发展,高楼主材弯曲检查已成为确保建筑质量和安全的重要环节。
然而,我们也不可忽视高楼主材弯曲检查中存在的一些质量问题。
本文将探讨这些问题,并提出相应的质量改进措施。
一、质量问题分析1. 不合格产品使用:在高楼主材弯曲检查中,出现不合格产品使用的情况,这对整个建筑的质量和安全都带来了极大的风险。
例如,使用质量低劣的钢材或混凝土,容易导致建筑结构的失稳和工程事故的发生。
2. 弯曲检查不到位:有时,施工单位在高楼主材弯曲检查过程中并未严格按照规范进行操作,导致对主材的弯曲程度和弯曲位置的检查不到位。
这种情况下,即便有弯曲,也可能会被忽略或误判,增加了质量隐患。
3. 检测设备不精准:另一个质量问题是检测设备不精准。
使用不准确的仪器和设备进行弯曲检查,会导致检测结果的不准确性,进而影响质量评估和监控。
这也会给高楼建筑的结构安全带来潜在威胁。
二、质量改进措施针对上述质量问题,为提高高楼主材弯曲检查的质量,我们应采取以下改进措施:1. 选择优质产品:在材料采购过程中,要确保选择符合质量标准的建筑主材。
与供应商建立稳定合作关系,加强供应链管理,可有效降低不合格产品使用的风险,确保施工过程中使用优质材料。
2. 加强施工现场管理:施工单位应加强对高楼主材弯曲检查过程的管理。
建立检查标准和流程,并进行培训,确保质量检查的准确性和完整性。
同时,加强对检查记录的保存和管理,以备将来的追溯和验收。
3. 使用精准检测设备:引入精准的弯曲检测设备,例如激光测量仪器和高精度测量工具。
这些设备可以提供准确的弯曲度和弯曲位置信息,有效避免人为误判和检测偏差,提高质量评估的准确性和可靠性。
4. 强化质量控制体系:建立完善的质量控制体系,包括从原材料采购、施工管理到最终验收的全过程质量控制。
加大对施工单位的技术培训和管理监督,培养专业人员的责任心和专业水平,确保高楼主材弯曲检查能够达到质量标准。
高精度弯曲件工艺方案及改进措施探讨
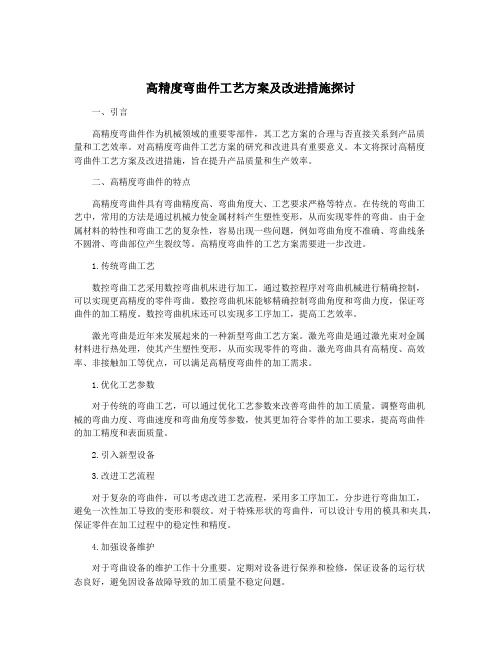
高精度弯曲件工艺方案及改进措施探讨一、引言高精度弯曲件作为机械领域的重要零部件,其工艺方案的合理与否直接关系到产品质量和工艺效率。
对高精度弯曲件工艺方案的研究和改进具有重要意义。
本文将探讨高精度弯曲件工艺方案及改进措施,旨在提升产品质量和生产效率。
二、高精度弯曲件的特点高精度弯曲件具有弯曲精度高、弯曲角度大、工艺要求严格等特点。
在传统的弯曲工艺中,常用的方法是通过机械力使金属材料产生塑性变形,从而实现零件的弯曲。
由于金属材料的特性和弯曲工艺的复杂性,容易出现一些问题,例如弯曲角度不准确、弯曲线条不圆滑、弯曲部位产生裂纹等。
高精度弯曲件的工艺方案需要进一步改进。
1.传统弯曲工艺数控弯曲工艺采用数控弯曲机床进行加工,通过数控程序对弯曲机械进行精确控制,可以实现更高精度的零件弯曲。
数控弯曲机床能够精确控制弯曲角度和弯曲力度,保证弯曲件的加工精度。
数控弯曲机床还可以实现多工序加工,提高工艺效率。
激光弯曲是近年来发展起来的一种新型弯曲工艺方案。
激光弯曲是通过激光束对金属材料进行热处理,使其产生塑性变形,从而实现零件的弯曲。
激光弯曲具有高精度、高效率、非接触加工等优点,可以满足高精度弯曲件的加工需求。
1.优化工艺参数对于传统的弯曲工艺,可以通过优化工艺参数来改善弯曲件的加工质量。
调整弯曲机械的弯曲力度、弯曲速度和弯曲角度等参数,使其更加符合零件的加工要求,提高弯曲件的加工精度和表面质量。
2.引入新型设备3.改进工艺流程对于复杂的弯曲件,可以考虑改进工艺流程,采用多工序加工,分步进行弯曲加工,避免一次性加工导致的变形和裂纹。
对于特殊形状的弯曲件,可以设计专用的模具和夹具,保证零件在加工过程中的稳定性和精度。
4.加强设备维护对于弯曲设备的维护工作十分重要。
定期对设备进行保养和检修,保证设备的运行状态良好,避免因设备故障导致的加工质量不稳定问题。
五、结论在高精度弯曲件的加工中,工艺方案的选择和改进对产品质量和工艺效率具有重要影响。
管材高精度弯曲成形模具设计与工艺研究
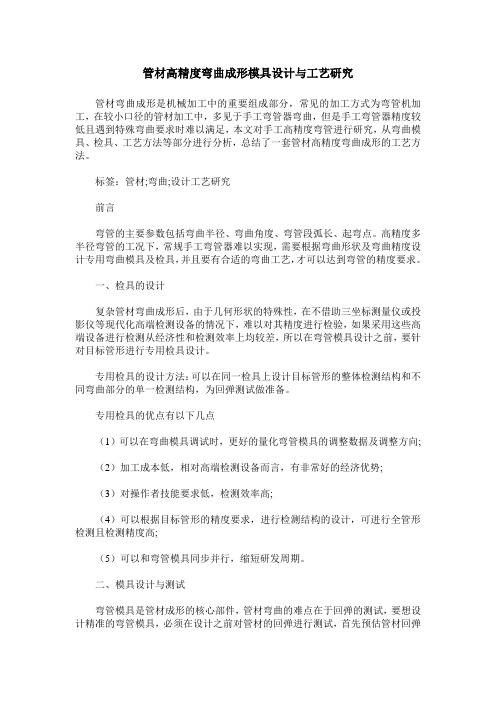
管材高精度弯曲成形模具设计与工艺研究管材弯曲成形是机械加工中的重要组成部分,常见的加工方式为弯管机加工,在较小口径的管材加工中,多见于手工弯管器弯曲,但是手工弯管器精度较低且遇到特殊弯曲要求时难以满足,本文对手工高精度弯管进行研究,从弯曲模具、检具、工艺方法等部分进行分析,总结了一套管材高精度弯曲成形的工艺方法。
标签:管材;弯曲;设计工艺研究前言弯管的主要参数包括弯曲半径、弯曲角度、弯管段弧长、起弯点。
高精度多半径弯管的工况下,常规手工弯管器难以实现,需要根据弯曲形状及弯曲精度设计专用弯曲模具及检具,并且要有合适的弯曲工艺,才可以达到弯管的精度要求。
一、检具的设计复杂管材弯曲成形后,由于几何形状的特殊性,在不借助三坐标测量仪或投影仪等现代化高端检测设备的情况下,难以对其精度进行检验,如果采用这些高端设备进行检测从经济性和检测效率上均较差,所以在弯管模具设计之前,要针对目标管形进行专用检具设计。
专用检具的设计方法:可以在同一检具上设计目标管形的整体检测结构和不同弯曲部分的单一检测结构,为回弹测试做准备。
专用检具的优点有以下几点(1)可以在弯曲模具调试时,更好的量化弯管模具的调整数据及调整方向;(2)加工成本低,相对高端检测设备而言,有非常好的经济优势;(3)对操作者技能要求低,检测效率高;(4)可以根据目标管形的精度要求,进行检测结构的设计,可进行全管形检测且检测精度高;(5)可以和弯管模具同步并行,缩短研发周期。
二、模具设计与测试弯管模具是管材成形的核心部件,管材弯曲的难点在于回弹的测试,要想设计精准的弯管模具,必须在设计之前对管材的回弹进行测试,首先预估管材回弹系数进行测试模具的设计,例如取目标管形弯曲半径的0.9倍进行模具设计,测试用的简易弯管模具主要由弯曲模(定轮)、一个绕其旋转的动轮、一个固定两轮的固定杆组成,在测试过程中,要以匀速进行弯曲。
在回弹量测试过程中,常见的错误为,直接观察弯管弧度部分是否与检具吻合,其实这是在测试弧长,影响弧长的前提因素有弯曲角度和弯曲半径,所以应该按照角度、半径、弧长的顺序进行测试。
精密加工改善方案
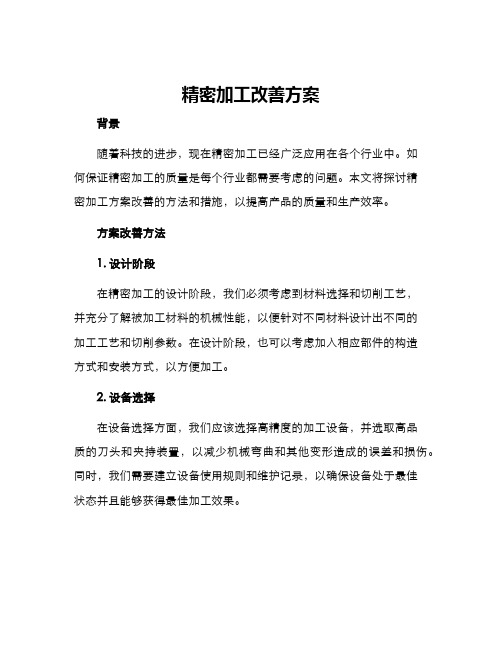
精密加工改善方案背景随着科技的进步,现在精密加工已经广泛应用在各个行业中。
如何保证精密加工的质量是每个行业都需要考虑的问题。
本文将探讨精密加工方案改善的方法和措施,以提高产品的质量和生产效率。
方案改善方法1. 设计阶段在精密加工的设计阶段,我们必须考虑到材料选择和切削工艺,并充分了解被加工材料的机械性能,以便针对不同材料设计出不同的加工工艺和切削参数。
在设计阶段,也可以考虑加入相应部件的构造方式和安装方式,以方便加工。
2. 设备选择在设备选择方面,我们应该选择高精度的加工设备,并选取高品质的刀头和夹持装置,以减少机械弯曲和其他变形造成的误差和损伤。
同时,我们需要建立设备使用规则和维护记录,以确保设备处于最佳状态并且能够获得最佳加工效果。
3. 控制加工参数在加工过程中,需要根据不同的加工要求调整刀头、加工速度和进给速度等关键参数,以取得最佳的加工效果。
此外,还需考虑整个加工过程的温度、压力等因素对加工过程的影响,并及时向操作人员传达着相应要求和控制措施。
4. 质量检测在加工完成后,必须对产品进行质量检测,并建立相应的质量记录。
质量检测的目的是检测加工的各项指标是否符合要求,还可以发现加工过程中的隐患,及时解决并防止下一次再次出现。
5. 培训人员最后,我们需要对操作人员进行培训,提高人员的技能和责任感。
针对加工和检测的各项规定进行全面培训,并定期进行加工技能检测和质量意识培训,以确保操作人员的操作规范和质量意识。
结论对于精密加工来说,保证加工质量和效率是我们绕不开的问题。
通过对以上五个方面的改善方法,我们可以更好地掌握生产过程中的各项关键技术,并不断提高精密加工的质量和效率,从而取得更佳的生产效益,为企业发展做出贡献。
高精度弯曲件工艺方案及改进措施探讨

高精度弯曲件工艺方案及改进措施探讨高精度弯曲件的工艺方案对于整个生产制造过程至关重要,因为只有实施了合理的工艺方案,才可以保证产品的质量和性能。
本文将探讨高精度弯曲件的工艺方案及改进措施,以便为相关企业的生产提供参考。
一、工艺方案的选择1.弯曲机的选择高精度弯曲件加工的第一步是选择合适的弯曲机。
一般情况下,为了保证工件的加工精度和适应不同的弯曲曲率,选择具有多轴控制和多功能特点的数控弯曲机。
2.模具的选择模具的选择直接影响到高精度弯曲件的弯曲精度和质量,因此需要根据产品的加工要求进行相应的模具选择。
对于要求较高的产品,可以选用数控模具,通过自动调整来实现更加精细化的加工。
3.选择合适的工艺参数在进行高精度弯曲件的加工过程中,工艺参数的设置也是非常重要的一环。
需要根据工件材料、厚度、宽度、长度、弯曲曲率等因素来进行合理的参数设置。
当然,针对不同的工件,参数的设置也是有差异的。
二、改进措施的实施1.加强质量控制在高精度弯曲件的生产过程中,要加强对工件质量的控制,采用精密的检验工具,如三坐标测量仪、镜子等,来检验加工件的精度和质量。
对于出现问题的工件,需要及时进行处理或者放弃加工,以保证整个生产过程的质量。
2.加强员工培训为了确保高精度弯曲件的加工质量和生产效率,需要对生产人员进行专业的技能培训。
培训内容可以包括弯曲机的操作、模具的更换和维护、工艺参数的设置及检验方法等。
通过培训提升员工的专业知识水平和技能,使其在工作中熟练掌握相关技术,提高工作效率。
3.优化工艺流程通过研究和改进传统的工艺流程,可以有效提高高精度弯曲件的加工质量和效率。
例如,对于多品种、小批量的加工,可以采用自动化控制系统和智能化柔性生产系统,提高加工效率和质量稳定性。
4.选择高性能材料选择高性能材料是保证高精度弯曲件质量的关键措施之一。
选择具有高强度、高韧性、抗氧化性能和优异的紫外线稳定性的材料,可以有效提高产品的耐用性和稳定性。
高精度弯曲件工艺方案及改进措施探讨
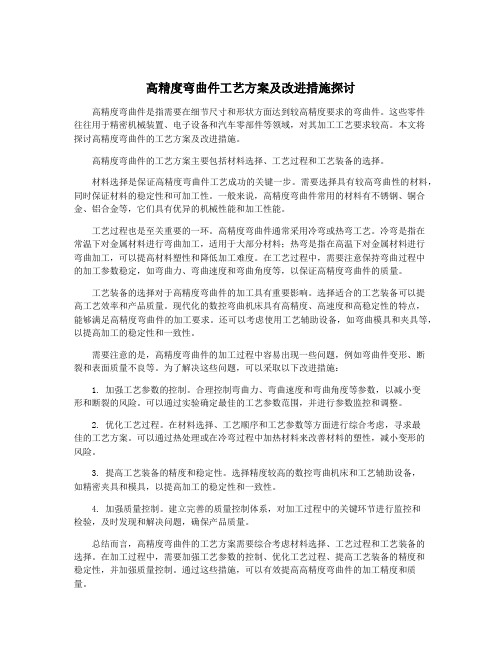
高精度弯曲件工艺方案及改进措施探讨高精度弯曲件是指需要在细节尺寸和形状方面达到较高精度要求的弯曲件。
这些零件往往用于精密机械装置、电子设备和汽车零部件等领域,对其加工工艺要求较高。
本文将探讨高精度弯曲件的工艺方案及改进措施。
高精度弯曲件的工艺方案主要包括材料选择、工艺过程和工艺装备的选择。
材料选择是保证高精度弯曲件工艺成功的关键一步。
需要选择具有较高弯曲性的材料,同时保证材料的稳定性和可加工性。
一般来说,高精度弯曲件常用的材料有不锈钢、铜合金、铝合金等,它们具有优异的机械性能和加工性能。
工艺过程也是至关重要的一环。
高精度弯曲件通常采用冷弯或热弯工艺。
冷弯是指在常温下对金属材料进行弯曲加工,适用于大部分材料;热弯是指在高温下对金属材料进行弯曲加工,可以提高材料塑性和降低加工难度。
在工艺过程中,需要注意保持弯曲过程中的加工参数稳定,如弯曲力、弯曲速度和弯曲角度等,以保证高精度弯曲件的质量。
工艺装备的选择对于高精度弯曲件的加工具有重要影响。
选择适合的工艺装备可以提高工艺效率和产品质量。
现代化的数控弯曲机床具有高精度、高速度和高稳定性的特点,能够满足高精度弯曲件的加工要求。
还可以考虑使用工艺辅助设备,如弯曲模具和夹具等,以提高加工的稳定性和一致性。
需要注意的是,高精度弯曲件的加工过程中容易出现一些问题,例如弯曲件变形、断裂和表面质量不良等。
为了解决这些问题,可以采取以下改进措施:1. 加强工艺参数的控制。
合理控制弯曲力、弯曲速度和弯曲角度等参数,以减小变形和断裂的风险。
可以通过实验确定最佳的工艺参数范围,并进行参数监控和调整。
2. 优化工艺过程。
在材料选择、工艺顺序和工艺参数等方面进行综合考虑,寻求最佳的工艺方案。
可以通过热处理或在冷弯过程中加热材料来改善材料的塑性,减小变形的风险。
3. 提高工艺装备的精度和稳定性。
选择精度较高的数控弯曲机床和工艺辅助设备,如精密夹具和模具,以提高加工的稳定性和一致性。
第七节提高弯曲件质量的工艺措施

第七节提高弯曲件质量的工艺措施弯曲件的常见缺陷及解决办法在实际生产中,弯曲件容易出现的质量问题很多,如回弹、弯裂、偏斜、扭曲以及尺寸超差等。
影响弯曲件成形质量的因素也很多,在制定弯曲工艺以及弯曲模具设计时应该综合考虑。
1. 回弹(1) 采用刚性好的工件结构设计如图3—23 所示零件在弯曲区压制加强肋,不仅可以提高工件的刚度,也有利于抑制弯曲回弹。
(2) 从模具设计上考虑减少弹复在凸模上做出等于回弹角的斜度进行补偿,使制件回弹后恰好等于所要求的角度(图3—24)此外采用可调式弯曲模具结构(图3 —27),利用聚胺酯橡胶的软凹模代替金属的刚性凹模进行弯曲(图3—28)都可减小回弹f 2)fb)图3-25 弯曲件角部强压以减小回图3-26圆弧底弯曲凸模■图3— 27 可调式弯曲模具结构图3 — 28 聚胺酯橡胶软凹模弯曲模(3)采用拉弯工艺 采用拉弯工艺能使毛坯从内表面到外表面都处于拉应力的作用下,卸料时它们弹性变形的方向一致,因此可大大减少工件的回弹。
拉弯适用于长度和弯曲半径都很大的弯曲件。
⑷采用其他工艺方面的措施1) 在允许的情况之下,采用加热弯曲;2) 对U 形弯曲件,可采用较小的间隙甚至负间隙弯曲;3)坯料厚度不得超差,否则弯曲回弹量很难控制,尺寸精度很难保证2.弯裂弯曲过程中外层材料受拉,当相对弯曲半径小于最小相对弯曲半径咕阮t值时,外层材料会开裂(图3 —29)。
弯裂除了与材料本身塑性好坏有关之外,还与弯曲毛坯两侧边缘的加工状态、弯曲线与轧制方向的角度关系等因素有关。
弯裂的解决办法有:图3 —29 弯裂(1)材料方面1)选用塑性好的材料,采用退火或正火状态的软材料可较大幅度提高板料的弯曲加工极限值;2)板料表面不得有划伤、裂纹,侧边(剪切面) 不得有大的毛刺、裂口和冷作硬化等缺陷;3)弯曲制坯前,注意识别板料或卷料的轧制方向。
(2) 弯曲工艺方面剪切产生的毛刺在弯曲时会引起应力集中而使工件开裂,故应把有毛刺的一边放在弯曲内侧(图3—13 毛刺在外侧因此开裂)。
提高弯曲件折弯精度的工艺措施探析

() 1克服由于材料不均匀而导致折弯时出现的精度误差 。
为了能够减小 由于材料不均匀而导致的折 弯精度误差 ,在选
材的时候就应该尽量选择那些质地均匀的板材 。这可 以通过 对材料 采购环节来予 以控制 ,例如选择一个可靠 的材料供应 商进行 长期供应 , 保证材料的供应质量 的稳定性 , 便于选择一 个稳定 的工艺参数进行加工 。
tr ftepae b n ig p r fe le ic so e dn c u ay i n y e , e po esc nrlme s rs ueo h lt e dn at o uN d pee fb n ig ac rc sa a zd t rc s o t au e. s l h o
弯曲作为分析的对 象 , 探讨 了弯 曲件折弯精度 的控制工艺措
施。
1 间隙折弯法精度控制策略分析
11 间隙折弯工艺分析 .
的计算精度产生直接影响 。在计算 的过程 中一般采用折弯系 数 的方法予 以获得 。 该折弯系数属于经验数据 , 根据零件的具 体形状 、 尺寸以及板材材料的不同而有 所差别 , 但是在实际的 计算 时一般都采用 同一个值。 同时 , 时的加工误差也会引 下料 起展开料 的尺寸精度 , 会产生一个和理论值不 同的实 际值 , 使 得尺寸精度受到影响 。
13 提 高间隙折弯法折弯精度的工艺措施 .
间隙折弯加工过程 中 , 主要是利用上、 下模之间的间隙来 进行加工 的。 弯曲加工过程 中, 下模之间并不会 接触 , 在 上、 因 此应该尽量的避免定位与加工在行程 的底部 。 同时 , 合理 的调 整上模进入下模 的开 口深度来获得所需要 的弯 曲角度 。 以 , 所 利用这种过量折弯方法能够在模 具上 获得 多种开 口角度大于 下模实 际开 口角度 的角度 。 1 间隙折弯法 中影响折弯精度的相关因素 . 2 () 1 机床的挠 曲变形影响 。 由于加工过程中存在负载不均 匀 的问题 ,长时 间的加工之后容易导致机床 出现挠 曲变形 的 问题 。例如 , 折弯机 的工作长度 为 30 rm时 , 若 20 a 而两个左右
弯曲件常见质量问题改善对策

9
弯曲后两边对向的两孔轴心错移
材料回弹改变弯曲角度使中心线错移
①.增加校正工序
②.改进弯曲模结构减小材料回弹
10
弯曲线与两孔中心联机不平行
弯曲高度小于最小弯曲极限高度时弯曲部位出现外胀现象
①.增加折弯件高度尺寸
②.改进折弯件工艺方法
11
带切口的制件向下挠曲
切口使两直边向左右张开,制件底部出现挠度
①.改进制件结构
②.切口处增加工艺留量,使切口连接起来,弯曲后再将工艺留量切去
12
弯曲后宽度方向变形,被弯曲部位在宽度方向出现弓形挠度
由于制件宽度方向的拉深和收缩量不一致产生扭转和挠度
①.增加弯曲压力
②.增加校正工序
③.保证材料纹向与弯曲方向有一定角度
②.调整顶料装置,增加顶料力
③.增加顶料装置或校正
④.加整形工序
6
制件端面鼓起或不平
弯曲时材料外表面在圆周方向受拉产生收缩变形,内表面在圆周方向受压产生伸长变形,因而沿弯曲方向出现挠曲端面产生鼓起现象
①.制件在冲压最后阶段凸凹模应有足够压力
②.做出与制件外圆角相应的凹模圆角半径
③.增加工序完善
7
弯曲引起孔变形
④高度尺寸太小
①.设计压线或预折弯工艺
②.增加压料力
③.凸凹模间隙均匀、圆角抛光
④高度尺寸不能小于最小极限尺寸
2
弯曲角有裂缝
①.弯曲内半径太小
②.材料纹向与弯曲线平行
③.毛坯的毛刺一面向外
④.金属可塑性差
①.加大凸模弯曲半径
②.改变落料排样
③.毛刺改在制件内圆角
④.退火或采用软性材料
3
高精度弯曲件工艺方案及改进措施探讨

高精度弯曲件工艺方案及改进措施探讨摘要本文通过对某高精度弯曲件的结构和尺寸精度的分析,找到了影响零件尺寸精度不稳定和零件合格率低的主要因素,对原工艺方案进行了合理的调整,并设计了相应的二类工装,从而提高了零件的合格率,保证了零件的尺寸精度和位置精度。
关键词高精度弯曲件;尺寸精度;零件结构;厚度偏差1 零件结构及尺寸精度分析某高精度弯曲件,材料为1Cr18Ni9Ti,料厚为t=1.2mm。
零件中心螺纹孔M11*0.5-6H 其底孔为φ10.5深5.2min,对C基准的同轴度为φ0.05;中凸圆柱外圆尺寸为φ12.6,根部圆角为R0.5,对C基准的同轴度为φ0.1;外圆φ50.1±0.04高5.2,根部內圆角为R0.5,对底面(H面)的垂直度要求为0.05,底面(H面)有平面度要求为0.1;底部其余部位分布有若干孔及两对需切舌弯曲的竖直侧面,其中一对之间的距离为19.5±0.1,对B基准的对称度为0.1,弯曲内圆角半径为R0.5;另一对之间的距离为5.1±0.05,对底面(H面)的垂直度为0.05,弯曲内圆角半径为R0.5。
从零件各部位的尺寸和位置精度来看,0.05和0.1的精度要求对机加零件而言并不算高,但对于冲压成形的零件(不含冲裁零件)而言则超出了其精密级别的要求。
据相关资料显示,影响冲压成形零件精度的因素很多,比如材料的机械性能,材料的厚度,模具结构和精度,模具的安装和调整情况,以及冲压成形零件本身的形状尺寸等,对于精度要求较高的冲压成形件则必须严格控制材料的厚度公差。
现有资料可查到的与材料厚度偏差有关的零件尺寸公差最高只能达到IT13~IT14,而该高精度弯曲件上精度高的尺寸及位置精度几乎都与材料厚度偏差有关,且设计要求的尺寸精度都在IT11~IT12之间[1]。
2 工艺方法的分析探讨及解决措施通过对该弯曲件的结构和尺寸精度的分析,我们对该弯曲件有了初步的认识,下面就各个难点逐一进行工艺分析。
提高弯曲件精度的工艺措施

弯曲角的变化量为:
K 1 1 '
0 0'
一.回弹量的计算
图中给出了弯曲加载和卸载的过程。加
载过程沿折线OAB,总应变值
be
t
2
卸载过程沿线段BC,其弹性应变值和残
余塑性应变值分别为
弹性应变值
ε sp
Mt 2 EI
和残余塑性应变值re
因为有 εsp εbe εre
2
t
'
得
1 1M K
改写为:01 源自1 '即有
M EI 0
△α的大小:
M EI
0
K 1 1 M ' EI
应变中性层曲率的变化量
M—卸载弯矩,其值等于加载时的弯矩;
E— 弹性模量; I— 弯曲毛坯截面惯性矩, I 1 bt3
12
ρε —卸载前应变中性层曲率半径 α0 —弯曲角
△K与△α之间的关系为
K0
ρε —卸载前应变中性层曲率半径 α0 —弯曲角
二.影响弯曲回弹量的因素
(1)材料力学性能:材料的屈服强度σs越大(成
正比),弹性模量E越小(成反比) ,则回弹 量越大。当材料性能不稳定时,回弹量也不稳
(2定)相。对弯曲半径r/t: 当EMIr/t0较小时,外表面
上切向变形的总应变值较大,因而回弹量小。
解决方法:
采用带侧板的弯曲模; 设计翘曲量。
弯曲回弹
卸载后弯曲角形状和尺寸发生变化的现象,称 为弯曲回弹(简称回弹)。
弯曲回弹及其影响因素:
回弹后弯曲半径和弯曲角都发生了改变,由卸
载前应变中性层曲率半径ρε和弯曲角α0变为回 弹后的应变中性层曲率半径ρε´和弯曲角α0´。
第二讲弯曲工艺设计和提高精度的工艺措施

第三章 弯曲工艺与模具设计
2.最小弯曲半径rmin的数值参见表3.5 3.提高弯曲极限变形程度的方法 (1)经冷变形硬化的材料,可热处理后再弯曲。 (2)清除冲裁毛刺,或将有毛刺的一面处于弯曲受压的内缘。 (3)对于低塑性的材料或厚料,可采用加热弯曲。 (4)采取两次弯曲的工艺方法,中间加一次退火。 (5)对较厚材料的弯曲,如结构允许,可采取开槽后弯曲。
第三章 弯曲工艺与模具
纤 维 方 向 对 r的 /t min 影 响
第三章 弯曲工艺与模具设计
开 槽 后 进 行 弯 曲
第三章 弯曲工艺与模具设计
第五节 提高弯曲件精度的工艺措施
常见质量问题:拉裂、截面畸变、翘曲和弯曲回弹。 拉裂、截面畸变、
一、拉裂
第三章 弯曲工艺与模具设计
4.部分边缘弯曲 在局部弯曲某一段边缘时,为避免弯曲根部撕裂,应减小不 弯曲部分的长度B,使其退出弯曲线之外,即b≥r(如上页图a), 或在弯曲部分与不弯曲部分之间切槽,或在弯曲前预冲卸荷孔。
第三章 弯曲工艺与模具设计
5.弯曲件孔边距离 当t<2mm时, l ≥ t 当t≥2mm时, l ≥ 2t
第三章 弯曲工艺与模具设计
2.改变应力状态 (1)采用校正弯曲代替自由弯曲。 凸模角部做成局部突起,内层金属受挤压产生拉应力。 (2)纵向加压法。 凸模上的突肩使内外层金属切向均受压应力 (3)拉弯工艺。 用于大曲率半径成形,使内外层均受拉应力。
第三章 弯曲工艺与模具设计
3.利用回弹规律 (1)对于较硬材料,可根据回弹值对模具工作部分的形状和尺 寸进行修正。 (2)对于软材料,其回弹角小于5°时,可在模具上作出补偿
第三章 弯曲工艺与模具设计
5.工件的形状 一般而言,弯曲件越复杂,一次弯曲成形角的数量越多, 回弹量就越小。 (三)回弹值的确定 方法: 先根据经验数值和简单的计算来初步确定模具工作 部分尺寸,然后在试模时进行修正。
减小弯曲变形的措施小组讨论

减小弯曲变形的措施小组讨论
(1)提高接触刚度。
最常用的方法是改善机床部件主要零件接触面的配合质量。
例如,对机床导轨及装配基面进行刮研;提高顶尖锥体同主轴和尾座套筒锥孔的接触质量,多次修研加工精密零件用的中心孔等。
通过刮研可改善配合表面的粗糙度和形状精度,使实际接触面积增加,从而有效提高接触刚度。
提高接触刚度的另一措施是在接触面间预加载荷,这样可消除配合面间的间隙,增加接触面积,减少受力后的变形量,如在一些轴承的调整中就采用此项措施。
(2)提高工件、部件刚度。
对刚度较低的叉架类、细长轴等工件,其主要措施是减小支承间的长度,例如设置辅助支承、安装跟刀架或中心架。
加工中还常采用一些辅助装置提高机床部件刚度,如卧式铣床悬梁上的支架、卧式镗床后立柱上的支架就是用来提高刀具的安装刚度的。
(3)采用合理的装夹方法。
在夹具设计或工件装夹时都必须尽量减少工件的夹紧变形和弯曲力矩,如加工薄壁套筒内孔时用开口过渡环装夹,设计夹具时让工件上的加工部位悬伸尽量短等。
- 1、下载文档前请自行甄别文档内容的完整性,平台不提供额外的编辑、内容补充、找答案等附加服务。
- 2、"仅部分预览"的文档,不可在线预览部分如存在完整性等问题,可反馈申请退款(可完整预览的文档不适用该条件!)。
- 3、如文档侵犯您的权益,请联系客服反馈,我们会尽快为您处理(人工客服工作时间:9:00-18:30)。
高精度弯曲件工艺方案及改进措施探讨
高精度弯曲件是一种重要的工程零部件,其设计和加工必须满足高精度要求。
本文将探讨高精度弯曲件的工艺方案和改进措施。
1.设计方案
设计高精度弯曲件时应考虑以下几点:
(1)弯曲半径:应根据材料类型和尺寸大小来确定弯曲半径,弯曲半径越小,弯曲难度越大,应适度考虑折弯方式。
(2)弯曲角度:应在材料可承受范围内,根据应用需要确定弯曲角度。
(3)加工精度:考虑到加工中可能存在的误差,应将所需加工精度略高于设计精度。
2.工艺流程
(1)材料准备:应根据设计要求选择合适的材料,进行切割、磨光等预处理。
(2)制备弯曲模具:根据设计要求,制作合适的弯曲模具,可采用铸造、加工、压制等方式。
(3)弯曲加工:将材料放入弯曲模具中,通过压力和热力的作用,使材料弯曲成设计所需的形状。
(4)后处理:对弯曲件进行抛光、打磨、清洗等后处理,以确保其质量。
3.加工注意事项
(1)材料选择:应选择合适的材料,具有良好的韧性和可塑性,易于加工。
(2)弯曲速度:应掌握适宜的弯曲速度,过快或过慢都不利于加工,易造成材料破裂或变形。
(3)模具设计:设计合适的弯曲模具可以确保高精度的弯曲形状和尺寸。
1. 加工设备的改进
采用数控弯管机、喷砂机等高科技加工设备,提高加工精度和效率。
2. 不断提高员工技能水平
员工的技能水平决定着加工质量,加强技能培训和学习交流,提高员工的技术素质。
3. 强化质量管理
制定严格的质量标准和管理规范,强化检验和测试环节,及时发现和解决问题,以提高产品质量。
4. 优选供应商
建立长期稳定的供应商合作关系,优选优质、稳定的原材料供应商,以确保材料质量和供应能力。
总之,高精度弯曲件的生产需要从设计、材料选择、加工工艺和质量管理等多个方面进行综合考虑和优化改进,以确保产品质量、提高生产效率和市场竞争力。