弹簧感应热处理概要
弹簧热处理工艺流程
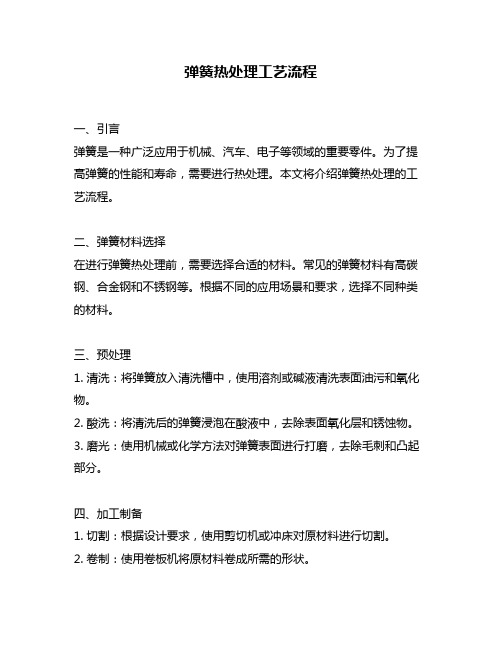
弹簧热处理工艺流程一、引言弹簧是一种广泛应用于机械、汽车、电子等领域的重要零件。
为了提高弹簧的性能和寿命,需要进行热处理。
本文将介绍弹簧热处理的工艺流程。
二、弹簧材料选择在进行弹簧热处理前,需要选择合适的材料。
常见的弹簧材料有高碳钢、合金钢和不锈钢等。
根据不同的应用场景和要求,选择不同种类的材料。
三、预处理1. 清洗:将弹簧放入清洗槽中,使用溶剂或碱液清洗表面油污和氧化物。
2. 酸洗:将清洗后的弹簧浸泡在酸液中,去除表面氧化层和锈蚀物。
3. 磨光:使用机械或化学方法对弹簧表面进行打磨,去除毛刺和凸起部分。
四、加工制备1. 切割:根据设计要求,使用剪切机或冲床对原材料进行切割。
2. 卷制:使用卷板机将原材料卷成所需的形状。
3. 预成形:将卷好的原材料放入预成形机中,进行初步成型。
4. 终成形:将预成形后的弹簧放入终成形机中,进行最终成型。
五、热处理1. 固溶处理:将弹簧放入固溶炉中,加热至固溶温度。
保持一定时间后,快速冷却至室温。
此过程可以消除材料内部的应力和组织不均匀性。
2. 淬火处理:将固溶后的弹簧放入淬火槽中,快速冷却至室温。
此过程可以提高弹簧的硬度和韧性。
3. 回火处理:将淬火后的弹簧放入回火炉中,加热至回火温度。
保持一定时间后,快速冷却至室温。
此过程可以改善弹簧的韧性和塑性。
六、表面处理1. 酸洗:将经过热处理的弹簧浸泡在酸液中,去除表面氧化层和锈蚀物。
2. 磨光:使用机械或化学方法对弹簧表面进行打磨,去除毛刺和凸起部分。
3. 镀层:根据需要,可以对弹簧表面进行镀铬、镀锌等处理,提高其耐腐蚀性。
七、质量检验1. 外观检查:对弹簧的外观进行检查,包括尺寸、形状、表面质量等。
2. 力学性能测试:对弹簧的硬度、韧性等力学性能进行测试。
3. 化学成分分析:对弹簧材料的化学成分进行分析。
八、包装运输将经过质量检验的弹簧进行包装,标注相关信息,并进行运输。
九、总结弹簧热处理是提高弹簧性能和寿命的重要工艺。
弹簧的热处理

, 沉淀硬化的不锈钢钢丝 , 钢
带和铜镍合金材料以冷成形工艺制作的弹簧 ,成形后需进行时效硬化处理 .
第三种 ,凡是用热成型和以退火材料冷卷的弹簧,均需进行淬火回火处理。
弹簧的淬火和回火
1 弹簧的淬火 淬火就是把钢加热到临界温度A C3 或 AC1 以上保温一定时间,使其奥氏体化,再以大于临界了冷却速度急剧了冷却,从而获
性 , 并采用高温快速加热的方法 , 对中小弹簧 , 可用脱氧良好的盐浴炉进行淬火加热 .
弹簧淬火宜在油中冷却 , 以避免变形和开裂 . 用尺寸较大的碳钢材料制造的弹簧 , 当
要求不高时 , 可用水冷 . 为了减小变形量 , 除了采用正确的加热和冷却方法外
, 有时还采用专用淬火夹具进行
成形淬火 , 例如板簧在弯板机上淬火 , 中 , 小型螺旋弹簧装在心轴上或专用夹具上进行加
50CrVA
820± 10
820± 10
870± 10 870± 10 850± 10
320--340 270
320--340 290 260 300
15--20 15
15--20 30 60 30
46--48 52--54 46--48
52 55--57
52
表 5--8 螺旋压缩弹簧轴心线对两端面的垂直度允许偏差
得马氏体组织的热处理方法。
对于一般热卷螺旋的弹簧,热弯板簧以及热冲压的蝶形弹簧,最好是在热成之后, 利用其余热立即淬火。这样可以省去一次加热,减少弹簧的氧化脱碳程度,既经济又改
善了弹簧的表面质量。例如 60Si2MnA 钢板弹簧目前采用的热处理工艺是在 900— 925℃
弯片之后,在 850— 880℃入油淬火。若受条件限制,也可在成形之后重新加热淬火。
弹簧的热处理
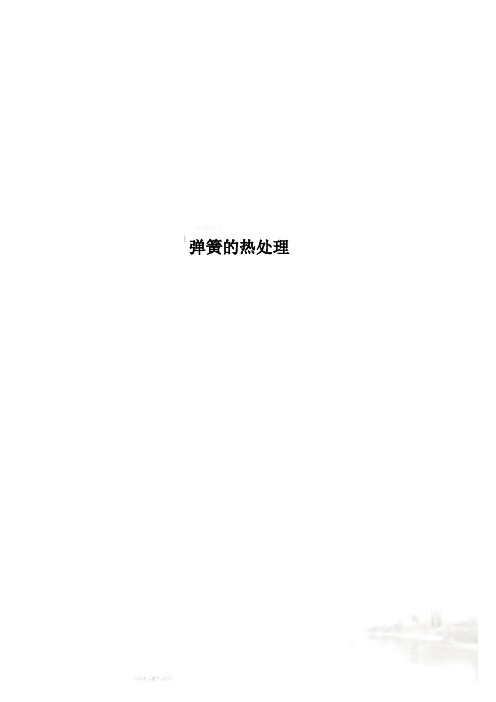
弹簧的热处理弹簧的热处理弹簧钢的特点—弹簧主要在动载荷下工作,即在冲击、振动的条件下,或在交变应力作用下工作,利用弹性变形来吸收冲击能量,起缓冲作用。
由于弹簧经常承受振动和长期在享变应力作用下工作,主要是疲劳破坏,故弹簧钢必须具有高的弹性极限和高疲劳极限。
此外,还应有足够的韧性和塑性,以防止在冲击力作用下突然脆断。
在工艺性论方面,弹簧钢应具有较好的淬透性和低的过热、脱碳敏感性。
降低弹簧表面粗糙度能提高疲劳寿命。
为了获得所需的性能,弹簧钢必须具有较高的含碳量。
碳素弹簧钢的含碳量在0.6-0.9%之间,由于碳素弹簧钢的淬透性差,故只用于制造截面尺寸不超过10-15mm的弹簧。
对于截面尺寸较大的弹簧,必须采用合金弹簧钢。
合金弹簧钢碳含量在0.45-0.75%之间,加入的合金元素有Mn ,Si ,W ,V ,Mo等。
它们的主要作用是提高淬透性和回火稳定性,强化铁素体和细化晶粒,有效地改善弹簧钢的力学性能,其中Cr ,W ,Mo还能提高钢的高温强度。
在热状态下成型的弹簧(直径或厚度一般在10mm以上)在冷状态下成型的弹簧(直径或厚度一般在10mm以下)热成型弹簧的热处理工艺--用这种方法成型弹簧多数是将热成型和热处理结合在一起进行的,而螺旋弹簧则大多数是在热成型后再进行热处理。
这种弹簧钢的热处理方式是淬火+中温回火,热处理后组织为回火托氏体。
这种组织的弹性极限和屈服极限高,并有一定的韧性。
冷成型弹簧的热处理工艺--对于用冷轧钢板、钢带或冷拉钢丝制成的弹簧,由于冷塑性变形使材料强化,己达到弹簧所要求的性能。
故弹簧成型后只需在250C左右范围内,保温30min 左右的去应力处理,以消除冷成型弹簧的门应力,并使弹簧定型即可。
耐热弹簧钢的热处理--内燃机的气阀弹簧是在较高温度下工作,有的还存在腐蚀性气氛,因此必须选用特殊的弹簧钢和合适的热处理规范。
弹簧淬火时常见的缺陷及防止措施(1)脱碳(降低使用寿命)--1、采用盐浴炉或拄制气氛加热炉加热。
拉簧热处理标准
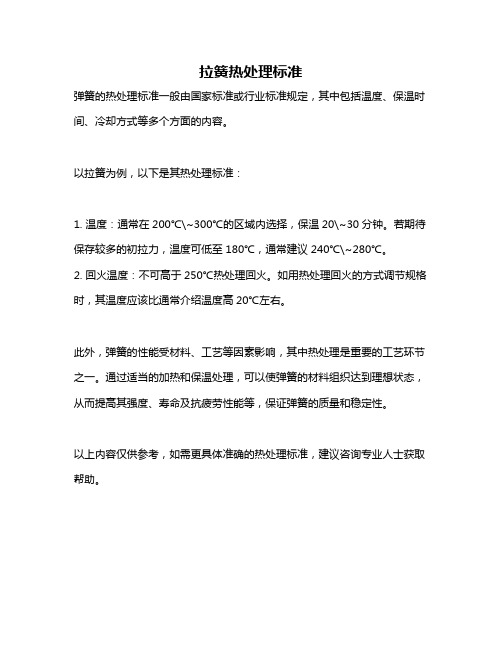
拉簧热处理标准
弹簧的热处理标准一般由国家标准或行业标准规定,其中包括温度、保温时间、冷却方式等多个方面的内容。
以拉簧为例,以下是其热处理标准:
1. 温度:通常在200℃\~300℃的区域内选择,保温20\~30分钟。
若期待保存较多的初拉力,温度可低至180℃,通常建议240℃\~280℃。
2. 回火温度:不可高于250℃热处理回火。
如用热处理回火的方式调节规格时,其温度应该比通常介绍温度高20℃左右。
此外,弹簧的性能受材料、工艺等因素影响,其中热处理是重要的工艺环节之一。
通过适当的加热和保温处理,可以使弹簧的材料组织达到理想状态,从而提高其强度、寿命及抗疲劳性能等,保证弹簧的质量和稳定性。
以上内容仅供参考,如需更具体准确的热处理标准,建议咨询专业人士获取帮助。
弹簧热处理操作规程
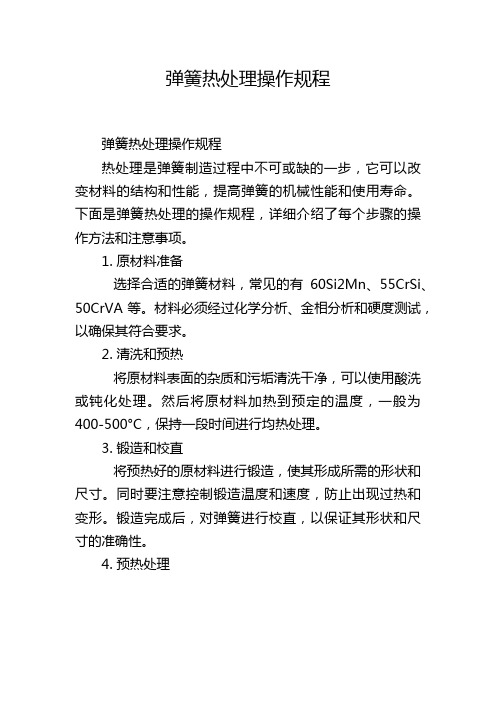
弹簧热处理操作规程弹簧热处理操作规程热处理是弹簧制造过程中不可或缺的一步,它可以改变材料的结构和性能,提高弹簧的机械性能和使用寿命。
下面是弹簧热处理的操作规程,详细介绍了每个步骤的操作方法和注意事项。
1. 原材料准备选择合适的弹簧材料,常见的有60Si2Mn、55CrSi、50CrVA等。
材料必须经过化学分析、金相分析和硬度测试,以确保其符合要求。
2. 清洗和预热将原材料表面的杂质和污垢清洗干净,可以使用酸洗或钝化处理。
然后将原材料加热到预定的温度,一般为400-500°C,保持一段时间进行均热处理。
3. 锻造和校直将预热好的原材料进行锻造,使其形成所需的形状和尺寸。
同时要注意控制锻造温度和速度,防止出现过热和变形。
锻造完成后,对弹簧进行校直,以保证其形状和尺寸的准确性。
4. 预热处理将锻造好的弹簧进行再次预热,一般温度范围为650-750°C,时间根据材料的厚度和大小而定。
预热过程可以改善弹簧的韧性和可加工性。
5. 淬火淬火是弹簧热处理中最重要的一步,它能使弹簧的组织变硬和强化。
淬火温度和速度的选择十分关键,一般情况下,淬火温度为780-820°C,淬火介质可以是水、油或盐溶液。
在淬火过程中,要控制淬火时间和冷却速度,以避免产生过硬或裂纹等缺陷。
6. 回火淬火后的弹簧较为脆硬,需要进行回火处理来消除内部应力和提高韧性。
回火温度一般选在250-400°C之间,时间根据需要来确定。
回火过程中要注意控制温度和时间,以防止过深回火或回火不足。
7. 表面处理弹簧热处理后,可能会在表面产生一些氧化物和脆性。
为了提高弹簧的耐腐蚀性和外观质量,可进行表面处理,如喷油、喷漆或镀锌等。
8. 检验完成热处理后,需要对弹簧进行检验。
常见的检验项目包括尺寸、力学性能、硬度等。
根据弹簧的用途和要求,可以选择适当的检验方法和仪器来进行检验。
9. 包装和存放检验合格的弹簧要进行包装,以防止损坏和污染。
304弹簧的热处理

304弹簧的热处理(原创实用版)目录一、304 弹簧的热处理概述二、304 弹簧的热处理过程三、304 弹簧热处理的影响因素四、304 弹簧热处理的注意事项五、304 弹簧热处理的应用领域正文一、304 弹簧的热处理概述304 弹簧是一种广泛应用于各种工程机械、仪器仪表和汽车等行业的弹性零件。
它的弹性和强度等性能受到热处理的影响,因此,对 304 弹簧进行合理的热处理至关重要。
二、304 弹簧的热处理过程304 弹簧的热处理过程主要包括以下几个步骤:1.预热:将弹簧放入炉中,加热至预定温度,以达到去除内应力和均匀加热的目的。
2.淬火:将预热的弹簧放入淬火介质(如水或油)中,快速冷却,以提高弹簧的硬度和强度。
3.回火:将淬火后的弹簧重新放入炉中,加热至一定温度,保温一段时间,然后自然冷却,以降低弹簧的硬度,提高弹性和韧性。
4.调质:对回火后的弹簧进行进一步的热处理,以调整其硬度和弹性。
三、304 弹簧热处理的影响因素1.温度:热处理的温度对弹簧的性能有着重要影响。
温度过高或过低都会导致弹簧的性能不佳。
2.冷却速度:淬火时的冷却速度直接影响弹簧的硬度和强度。
冷却速度过快,弹簧的韧性会降低;冷却速度过慢,弹簧的硬度和强度会不足。
3.回火温度:回火温度对弹簧的弹性和韧性有很大影响。
回火温度过高,弹簧的硬度和强度会降低;回火温度过低,弹簧的韧性会不足。
四、304 弹簧热处理的注意事项1.在热处理过程中,应严格控制温度、冷却速度等参数,以保证弹簧的性能。
2.热处理过程中,应确保弹簧表面清洁,避免氧化和污染。
3.弹簧在热处理过程中,应避免变形和损伤。
304弹簧的热处理
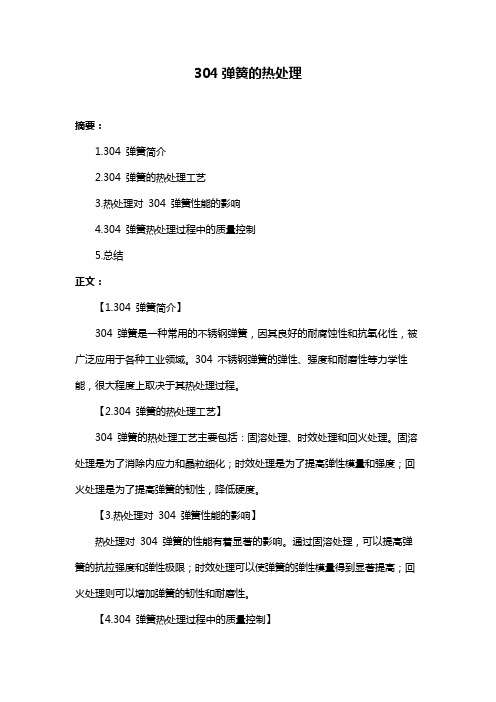
304弹簧的热处理
摘要:
1.304 弹簧简介
2.304 弹簧的热处理工艺
3.热处理对304 弹簧性能的影响
4.304 弹簧热处理过程中的质量控制
5.总结
正文:
【1.304 弹簧简介】
304 弹簧是一种常用的不锈钢弹簧,因其良好的耐腐蚀性和抗氧化性,被广泛应用于各种工业领域。
304 不锈钢弹簧的弹性、强度和耐磨性等力学性能,很大程度上取决于其热处理过程。
【2.304 弹簧的热处理工艺】
304 弹簧的热处理工艺主要包括:固溶处理、时效处理和回火处理。
固溶处理是为了消除内应力和晶粒细化;时效处理是为了提高弹性模量和强度;回火处理是为了提高弹簧的韧性,降低硬度。
【3.热处理对304 弹簧性能的影响】
热处理对304 弹簧的性能有着显著的影响。
通过固溶处理,可以提高弹簧的抗拉强度和弹性极限;时效处理可以使弹簧的弹性模量得到显著提高;回火处理则可以增加弹簧的韧性和耐磨性。
【4.304 弹簧热处理过程中的质量控制】
在304 弹簧的热处理过程中,需要严格控制温度、保温时间和冷却速度等工艺参数,以保证弹簧的性能和质量。
同时,还需要对热处理后的弹簧进行检测,如硬度检测、金相检测等,确保弹簧的质量符合要求。
【5.总结】
304 弹簧的热处理工艺对其性能起着至关重要的作用。
通过合理的热处理工艺,可以使304 弹簧具有良好的弹性、强度和耐磨性,满足各种工业领域的应用需求。
弹簧的热处理工艺
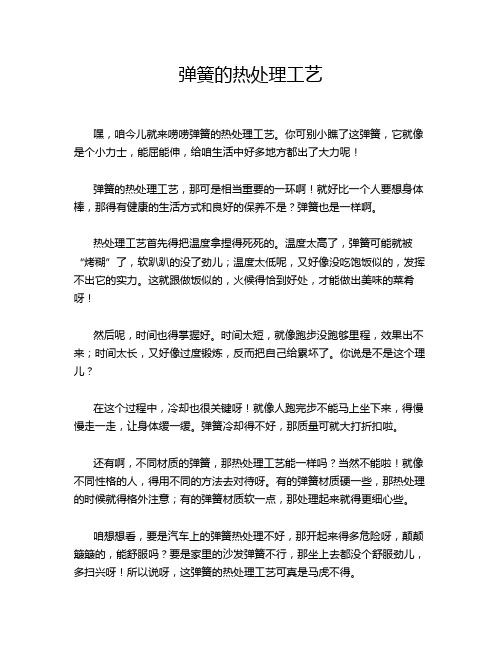
弹簧的热处理工艺嘿,咱今儿就来唠唠弹簧的热处理工艺。
你可别小瞧了这弹簧,它就像是个小力士,能屈能伸,给咱生活中好多地方都出了大力呢!弹簧的热处理工艺,那可是相当重要的一环啊!就好比一个人要想身体棒,那得有健康的生活方式和良好的保养不是?弹簧也是一样啊。
热处理工艺首先得把温度拿捏得死死的。
温度太高了,弹簧可能就被“烤糊”了,软趴趴的没了劲儿;温度太低呢,又好像没吃饱饭似的,发挥不出它的实力。
这就跟做饭似的,火候得恰到好处,才能做出美味的菜肴呀!然后呢,时间也得掌握好。
时间太短,就像跑步没跑够里程,效果出不来;时间太长,又好像过度锻炼,反而把自己给累坏了。
你说是不是这个理儿?在这个过程中,冷却也很关键呀!就像人跑完步不能马上坐下来,得慢慢走一走,让身体缓一缓。
弹簧冷却得不好,那质量可就大打折扣啦。
还有啊,不同材质的弹簧,那热处理工艺能一样吗?当然不能啦!就像不同性格的人,得用不同的方法去对待呀。
有的弹簧材质硬一些,那热处理的时候就得格外注意;有的弹簧材质软一点,那处理起来就得更细心些。
咱想想看,要是汽车上的弹簧热处理不好,那开起来得多危险呀,颠颠簸簸的,能舒服吗?要是家里的沙发弹簧不行,那坐上去都没个舒服劲儿,多扫兴呀!所以说呀,这弹簧的热处理工艺可真是马虎不得。
这就好比盖房子,根基没打好,房子能牢固吗?弹簧的热处理工艺就是它的根基呀,只有根基稳了,弹簧才能发挥出它该有的作用。
咱再打个比方,弹簧就像是个小战士,热处理工艺就是给它打造盔甲、磨砺武器,让它能在战场上冲锋陷阵呀!要是盔甲不结实,武器不锋利,那还怎么打仗呢?总之呢,弹簧的热处理工艺绝对不是小事一桩,那是关乎弹簧质量、关乎我们使用体验的大事呀!咱可得重视起来,让这些小弹簧们都能以最好的状态为我们服务呀!你说是不是这个道理呢?。
弹簧热处理

弹簧热处理(使用条件和要求)一、工作条件以及材料与热处理要求1.条件:形状简单,断面较小,受力不大的弹簧要求:65#钢785-815油淬,300°回火硬度HB512400℃回火硬度HB430500℃回火硬度HB36975#钢780-800油或水淬,400-420℃回火,HRC42-482.条件:中等负荷的大型弹簧要求:60Si2MnA 65Mn 870℃油淬,460℃回火,HRC40-45(农机座位弹簧65Mn 淬火回火HB280-370)3.条件:重负荷、高弹簧、高疲劳极限的大型弹簧和螺旋弹簧要求:50CrV A 60SiMnA 860油淬,475回火,HRC40-454.条件:在多次交变负荷ia工作的直径8-10mm的卷簧要求:50CrMnA 840-870油淬,450-480回火,HB387-4185.条件:机车、车辆、煤水车或板弹簧要求:55SiMn、60Si2Mn HRC39-45(HB363-432)解放牌汽车板簧55Si2Mn HB363-4416.条件:车辆及缓冲器螺旋弹簧、汽车张紧弹簧要求:55Si2Mn、60Si2Mn,60 Si2CrV A 淬火回火HRC40-477.条件:柴油泵柱塞弹簧、喷油嘴弹簧、农用柴油机气阀弹簧及中型、重型汽车的气门弹簧和板弹簧要求:50CrV A 淬火,回火HRC40-478.条件:在高温蒸汽下工作的卷簧和扁簧,自来水管道弹簧和耐海水浸蚀的弹簧,直径10-25要求:3Cr13 HRC39-46 4Cr13 HRC48-49 HRC47-49 HRC37-40 HRC31-35 HRC33-479.条件:在酸碱介质下工作的弹簧要求:2CrNi9 1100-1150水淬绕卷后消除应力,400℃回火60min,HB160-200 10.条件:弹簧挡圈,δ4 φ85要求:60Si2Mn 400预热,860油淬,430回火空冷HRC40-45二、备注1.弹簧热处理一般要求淬透,晶粒细,残余奥氏体少,脱碳层深度每边应符合:<φ6mm的钢丝或钢板,应<1.5%直径或厚度;>φ6mm的钢丝钢板,应<1.0%直径或厚度2.大型弹簧在热状态加工成型随即淬火-回火,中型弹簧在冷态加工成型(原材料要求球化组织或大部分球化),再淬火-回火,小型弹簧用冷轧钢带、冷拉钢丝等冷态加工成型后,低温回火3.处理后可进行喷丸处理40-50N/m2的压缩空气或离心机70m/s的线速度,将φ0.3-0.5mm(对于小零件、气门弹簧、齿轮等)、φ0.6-0.8mm(对板簧、曲轴、半轴等)铸铁丸或淬硬钢丸喷射到弹簧表面。
弹簧的热处理
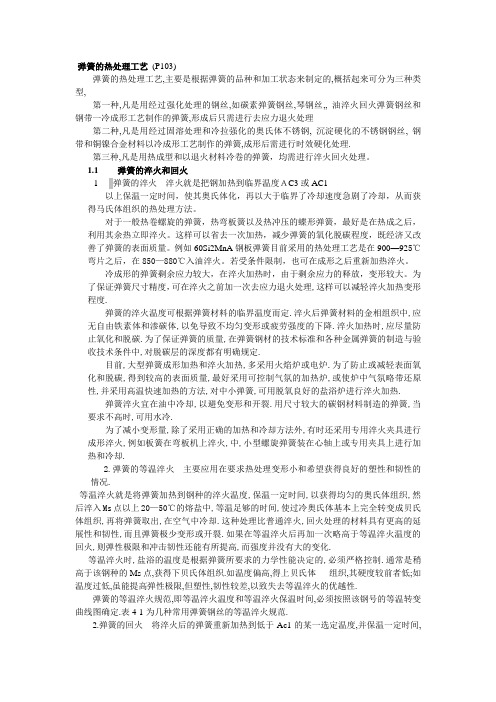
弹簧的热处理工艺(P103)弹簧的热处理工艺,主要是根据弹簧的品种和加工状态来制定的,概括起来可分为三种类型,第一种,凡是用经过强化处理的钢丝,如碳素弹簧钢丝,琴钢丝,, 油淬火回火弹簧钢丝和钢带一冷成形工艺制作的弹簧,形成后只需进行去应力退火处理第二种,凡是用经过固溶处理和冷拉强化的奥氏体不锈钢, 沉淀硬化的不锈钢钢丝, 钢带和铜镍合金材料以冷成形工艺制作的弹簧,成形后需进行时效硬化处理.第三种,凡是用热成型和以退火材料冷卷的弹簧,均需进行淬火回火处理。
1.1弹簧的淬火和回火1弹簧的淬火淬火就是把钢加热到临界温度AC3或AC1以上保温一定时间,使其奥氏体化,再以大于临界了冷却速度急剧了冷却,从而获得马氏体组织的热处理方法。
对于一般热卷螺旋的弹簧,热弯板簧以及热冲压的蝶形弹簧,最好是在热成之后,利用其余热立即淬火。
这样可以省去一次加热,减少弹簧的氧化脱碳程度,既经济又改善了弹簧的表面质量。
例如60Si2MnA钢板弹簧目前采用的热处理工艺是在900—925℃弯片之后,在850—880℃入油淬火。
若受条件限制,也可在成形之后重新加热淬火。
冷成形的弹簧剩余应力较大,在淬火加热时,由于剩余应力的释放,变形较大。
为了保证弹簧尺寸精度,可在淬火之前加一次去应力退火处理,这样可以减轻淬火加热变形程度.弹簧的淬火温度可根据弹簧材料的临界温度而定.淬火后弹簧材料的金相组织中,应无自由铁素体和渗碳体,以免导致不均匀变形或疲劳强度的下降.淬火加热时,应尽量防止氧化和脱碳.为了保证弹簧的质量,在弹簧钢材的技术标准和各种金属弹簧的制造与验收技术条件中,对脱碳层的深度都有明确规定.目前,大型弹簧成形加热和淬火加热,多采用火焰炉或电炉.为了防止或减轻表面氧化和脱碳,得到较高的表面质量,最好采用可控制气氛的加热炉,或使炉中气氛略带还原性,并采用高温快速加热的方法,对中小弹簧,可用脱氧良好的盐浴炉进行淬火加热.弹簧淬火宜在油中冷却,以避免变形和开裂.用尺寸较大的碳钢材料制造的弹簧,当要求不高时,可用水冷.为了减小变形量,除了采用正确的加热和冷却方法外,有时还采用专用淬火夹具进行成形淬火,例如板簧在弯板机上淬火,中,小型螺旋弹簧装在心轴上或专用夹具上进行加热和冷却.2.弹簧的等温淬火主要应用在要求热处理变形小和希望获得良好的塑性和韧性的情况.等温淬火就是将弹簧加热到钢种的淬火温度,保温一定时间,以获得均匀的奥氏体组织,然后淬入Ms点以上20—50℃的熔盐中,等温足够的时间,使过冷奥氏体基本上完全转变成贝氏体组织,再将弹簧取出,在空气中冷却.这种处理比普通淬火,回火处理的材料具有更高的延展性和韧性,而且弹簧极少变形或开裂.如果在等温淬火后再加一次略高于等温淬火温度的回火,则弹性极限和冲击韧性还能有所提高,而强度并没有大的变化.等温淬火时,盐浴的温度是根据弹簧所要求的力学性能决定的,必须严格控制.通常是稍高于该钢种的Ms点,获得下贝氏体组织.如温度偏高,得上贝氏体组织,其硬度较前者低;如温度过低,虽能提高弹性极限,但塑性,韧性较差,以致失去等温淬火的优越性.弹簧的等温淬火规范,即等温淬火温度和等温淬火保温时间,必须按照该钢号的等温转变曲线图确定.表4-1为几种常用弹簧钢丝的等温淬火规范.2.弹簧的回火将淬火后的弹簧重新加热到低于Ac1的某一选定温度,并保温一定时间,然后以适宜的冷却速度冷却的工艺方法,叫做回火.回火的目的是:获得所需要的力学性能,稳定弹簧的组织和尺寸以及消除内应力.表4-1 几种常用弹簧钢的等温淬火规范表1-8 美国弹簧标准名称和标准号(P20)。
弹簧材料的热处理技术
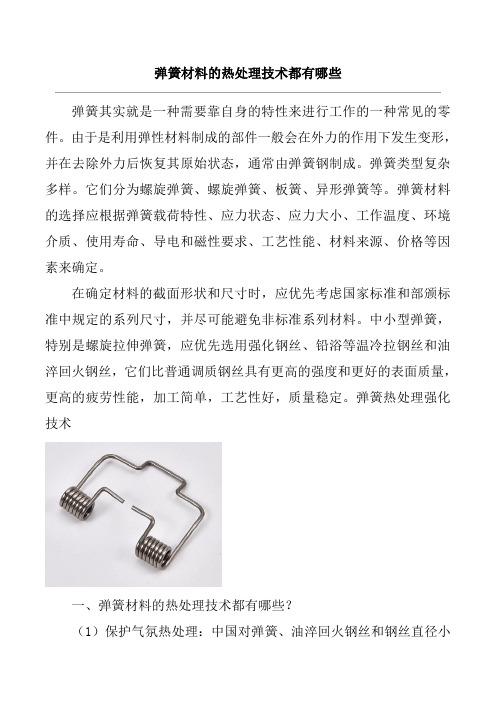
弹簧材料的热处理技术都有哪些弹簧其实就是一种需要靠自身的特性来进行工作的一种常见的零件。
由于是利用弹性材料制成的部件一般会在外力的作用下发生变形,并在去除外力后恢复其原始状态,通常由弹簧钢制成。
弹簧类型复杂多样。
它们分为螺旋弹簧、螺旋弹簧、板簧、异形弹簧等。
弹簧材料的选择应根据弹簧载荷特性、应力状态、应力大小、工作温度、环境介质、使用寿命、导电和磁性要求、工艺性能、材料来源、价格等因素来确定。
在确定材料的截面形状和尺寸时,应优先考虑国家标准和部颁标准中规定的系列尺寸,并尽可能避免非标准系列材料。
中小型弹簧,特别是螺旋拉伸弹簧,应优先选用强化钢丝、铅浴等温冷拉钢丝和油淬回火钢丝,它们比普通调质钢丝具有更高的强度和更好的表面质量,更高的疲劳性能,加工简单,工艺性好,质量稳定。
弹簧热处理强化技术一、弹簧材料的热处理技术都有哪些?(1)保护气氛热处理:中国对弹簧、油淬回火钢丝和钢丝直径小于15毫米的回火钢丝进行保护性大气热处理。
保护气氛热处理可以消除表面脱碳和氧化,提高材料的表面质量。
(2)感应加热或保护气氛感应加热热处理:这一过程通常在螺旋弹簧形成之前在金属丝上进行。
一些弹簧工厂将钢丝热处理与弹簧制造结合起来,以降低成本。
感应加热处理强化效果好,感应加热速度快,有利于细化晶粒,减少表面脱碳,能充分发挥和提高材料的强度和韧性。
(3)表面氮化热处理技术:近年来,高应力气门弹簧或其他高应力离合器弹簧也采用了表面氮化技术,以实现可靠的疲劳寿命。
更先进的技术是低温气体渗氮。
渗氮温度一般为(450 ~ 470)℃,气体渗氮时间为(5 ~ 20)小时。
弹簧喷丸强化工艺(4)组合喷丸技术:组合喷丸通常也称为多重喷丸工艺。
最经济的方法是使用二次喷丸。
这是通过用不同直径的射弹喷丸来实现的。
较大的颗粒首次用于获得残余压应力和表面光洁度。
(5)应力喷丸技术:应力喷丸也是一种相对经典的喷丸工艺,只是因为它难以应用于大规模生产,但近年来,由于应力喷丸设备的快速发展,它在大规模生产高应力汽车悬架弹簧方面取得了很大进展。
弹簧热处理工艺和过程
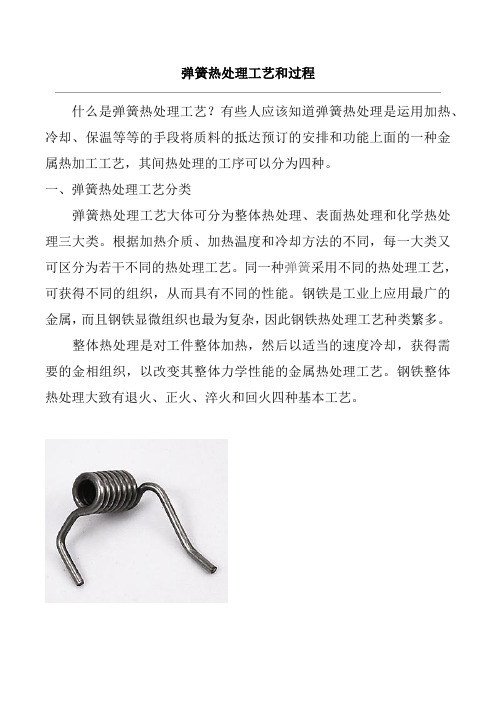
弹簧热处理工艺和过程什么是弹簧热处理工艺?有些人应该知道弹簧热处理是运用加热、冷却、保温等等的手段将质料的抵达预订的安排和功能上面的一种金属热加工工艺,其间热处理的工序可以分为四种。
一、弹簧热处理工艺分类弹簧热处理工艺大体可分为整体热处理、表面热处理和化学热处理三大类。
根据加热介质、加热温度和冷却方法的不同,每一大类又可区分为若干不同的热处理工艺。
同一种弹簧采用不同的热处理工艺,可获得不同的组织,从而具有不同的性能。
钢铁是工业上应用最广的金属,而且钢铁显微组织也最为复杂,因此钢铁热处理工艺种类繁多。
整体热处理是对工件整体加热,然后以适当的速度冷却,获得需要的金相组织,以改变其整体力学性能的金属热处理工艺。
钢铁整体热处理大致有退火、正火、淬火和回火四种基本工艺。
二、弹簧热处理工艺过程弹簧热处理工艺一般包括加热、保温、冷却三个过程,有时只有加热和冷却两个过程。
这些过程互相衔接,不可间断。
弹簧加热是热处理的重要工序之一。
弹簧热处理的加热方法很多,最早是采用木炭和煤作为热源,近而应用液体和气体燃料。
电的应用使加热易于控制,且无环境污染。
利用这些热源可以直接加热,也可以通过熔融的盐或金属,以至浮动粒子进行间接加热。
弹簧加热时,工件暴露在空气中,常常发生氧化、脱碳(即钢铁零件表面碳含量降低),这对于热处理后零件的表面性能有很不利的影响。
因而金属通常应在可控气氛或保护气氛中、熔融盐中和真空中加热,也可用涂料或包装方法进行保护加热。
加热温度是热处理工艺的重要工艺参数之一,选择和控制加热温度,是保证热处理质量的主要问题。
加热温度随被处理的金属材料和热处理的目的不同而异,但一般都是加热到相变温度以上,以获得高温组织。
另外转变需要一定的时间,因此当金属工件表面达到要求的加热温度时,还须在此温度保持一定时间,使内外温度一致,使显微组织转变完全,这殌时间称为保温时间。
采用高能密度加热和表面热处理时,加热速度极快,一般就没有保温时间,而化学热处理的保温时间往往较长。
弹簧的热处理(一)

弹簧的热处理(一)来源:每天学点热处理弹簧及弹性元件,是量大面广的基础零件,可以说是无处不在。
在动力机械、电器、仪表、武器中作为控制性元件,也是非常关键的零件。
它的基本功能是利用材料的弹性和弹簧的结构特点,在产生及恢复变形时,可以把机械功或动能转换为形变能,或者把形变能转换为动能或机械功,以达到缓冲或减振、控制运动或复位、储能或测量等目的。
所以,在各类机械设备、仪器仪表、军工产品、电器、家具、家电甚至文具、玩具中都广泛使用弹簧。
影响弹簧质量和使用寿命的因素很多,如设计、选材、生产工艺及工况条件等等。
其中,材质和热处理对弹簧的各种性能及其使用寿命有重要的甚至是决定性的影响。
本文分四个主题,分别介绍各类机械设备中常用的弹簧材料和典型弹簧的热处理,对于特殊用途的弹性材料和元件的热处理只做扼要介绍。
一、弹簧的分类、服役条件、失效方式和性能要求1 弹簧分类弹簧种类很多,可按形状、承载特点、制造方法、材料成分和不同用途进行分类。
每一类中又分为若干小类和不同规格。
GB/T1805弹簧的标准中列出了22种,弹簧行业1990年提出的内部标准《弹簧种类》中,把弹簧分为15个小类。
弹簧行业多按形状分类,在机械制造业中多按用途分类或按上述两者综合命名。
如表1 。
▼表1 弹簧的分类典型螺旋弹簧及板簧如图1所示。
▲图1 典型螺旋弹簧及板簧2 弹簧的服役条件和失效形式2.1 弹簧的服役条件和应力状态弹簧的服役条件是指它的工作环境(温度和介质)及应力状态等因素。
工作温度可分为低温(室温以下)、室温、较高温(120℃~350℃)、高温(350℃以上)几个档次。
工作环境介质有空气、水蒸气、雨水、燃烧产物、以及酸、碱水溶液等。
普通机械弹簧一般是在室温或较高工作温度、大气条件下承受载荷。
也有用于耐蚀、承受高应力等各种特殊用途的弹簧。
工作持续时间也是一个值得考虑的重要因素。
▲气门弹簧是要求最严苛的弹簧之一弹簧的载荷特性由弹簧变形时的载荷(P或T)与变形(F或)之间的关系曲线表示。
弹簧热处理的工序及详细过程
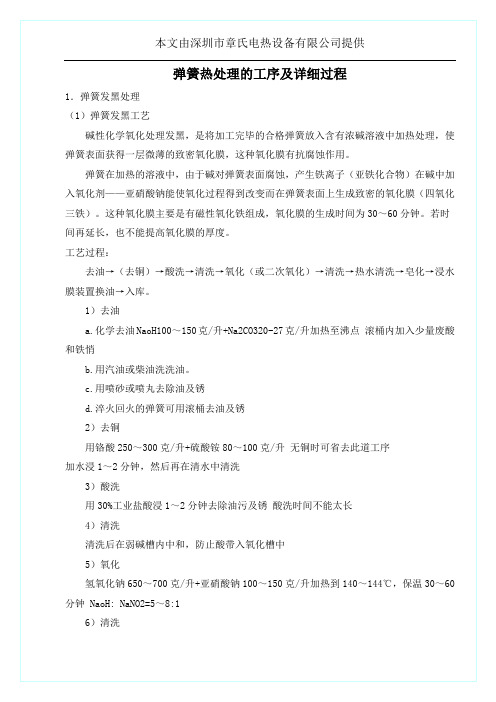
9)磷化槽添加磷酸锰铁盐与硝酸锌按1:2,钝化槽中的废重铬酸钾要集中统一处理,皂化槽中要经常补充皂片或三乙油酸皂。
10)若不要钝化时,可省去操作规程Ⅵ。
11)磷化前弹簧的喷沙、喷丸清理与磷化的间隔不得超过4小时,清理好后弹簧必须放入清洁的料框内。
(3)磷化质量检验方法
3)清洗
自来水冲洗去除酸性
4)磷化
磷酸锰铁盐30~35克/升,硝酸锌55~75克/升温度70~80℃保温10~15分钟,总酸度48~60游离酸2.5~6.7硫酸根≦0.5
5)清洗
自来水冲洗
6)钝化
重铬酸钾(K2Cr2O2)80~100克/升 90~100℃
7)清洗
自来水冲洗
8)清洗
热水90~100℃清洗1~2分钟
1)浸泡法
3%氯化钠NaCl,温度15~25℃,浸2小时无锈为合格。
2)点滴法之一
硫酸铜CuSO20.5N 40毫克氯化钠Nacl10% 20毫克,硫酸。0.1N0.8毫克。
点滴后不起黄时间越长质量越好,3分钟内不变色者为合格。
3)点滴法之二
硫酸铜CuSO4、SH20 66克/升,氯化钠NaCL32.5克/升,盐酸HCL 1:10 1.2克/升,点滴3分钟以上不发黄者为合格。
4)浸泡法
硫酸铜5%溶液,浸1分钟后工件表面不出现黄色为合格。
在检验工件磷化质量的同时,必须对磷化槽液进行定期化验总酸度、游离酸、酸根参数以确保日常的工件磷化质量。
3)按发黑工艺技术要求加入一定量亚硝酸钠(符合5~8:1);
4)用温度计测量发黑槽液湿度,确保槽液温度140~144℃,若温度过高要加水,并控制好加热电源;
5)发黑前,弹簧必须经充分的酸洗和清洗,拉力弹簧必须垂直装框,便于清洗;
弹簧和紧固件的热处理
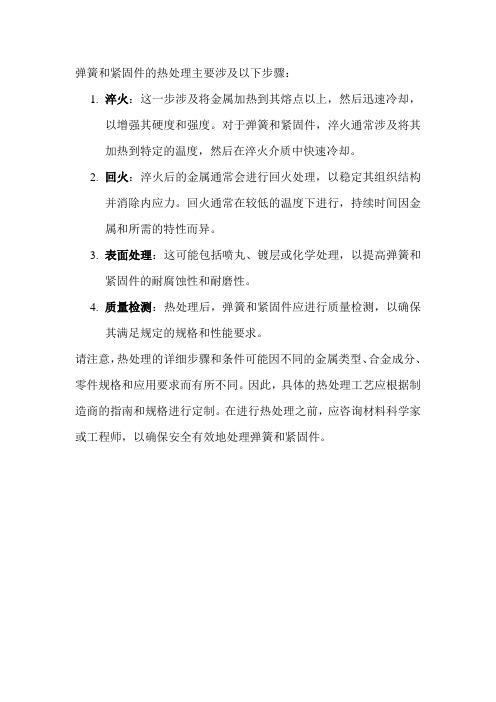
弹簧和紧固件的热处理主要涉及以下步骤:
1.淬火:这一步涉及将金属加热到其熔点以上,然后迅速冷却,
以增强其硬度和强度。
对于弹簧和紧固件,淬火通常涉及将其
加热到特定的温度,然后在淬火介质中快速冷却。
2.回火:淬火后的金属通常会进行回火处理,以稳定其组织结构
并消除内应力。
回火通常在较低的温度下进行,持续时间因金
属和所需的特性而异。
3.表面处理:这可能包括喷丸、镀层或化学处理,以提高弹簧和
紧固件的耐腐蚀性和耐磨性。
4.质量检测:热处理后,弹簧和紧固件应进行质量检测,以确保
其满足规定的规格和性能要求。
请注意,热处理的详细步骤和条件可能因不同的金属类型、合金成分、零件规格和应用要求而有所不同。
因此,具体的热处理工艺应根据制造商的指南和规格进行定制。
在进行热处理之前,应咨询材料科学家或工程师,以确保安全有效地处理弹簧和紧固件。
弹簧钢热处理工艺
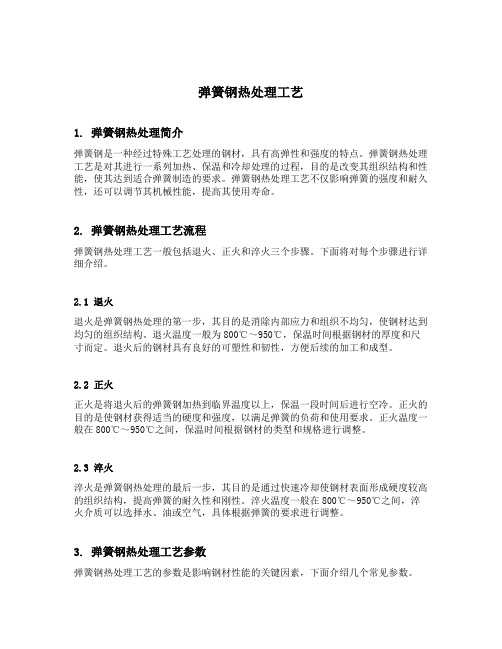
弹簧钢热处理工艺1. 弹簧钢热处理简介弹簧钢是一种经过特殊工艺处理的钢材,具有高弹性和强度的特点。
弹簧钢热处理工艺是对其进行一系列加热、保温和冷却处理的过程,目的是改变其组织结构和性能,使其达到适合弹簧制造的要求。
弹簧钢热处理工艺不仅影响弹簧的强度和耐久性,还可以调节其机械性能,提高其使用寿命。
2. 弹簧钢热处理工艺流程弹簧钢热处理工艺一般包括退火、正火和淬火三个步骤。
下面将对每个步骤进行详细介绍。
2.1 退火退火是弹簧钢热处理的第一步,其目的是消除内部应力和组织不均匀,使钢材达到均匀的组织结构。
退火温度一般为800℃~950℃,保温时间根据钢材的厚度和尺寸而定。
退火后的钢材具有良好的可塑性和韧性,方便后续的加工和成型。
2.2 正火正火是将退火后的弹簧钢加热到临界温度以上,保温一段时间后进行空冷。
正火的目的是使钢材获得适当的硬度和强度,以满足弹簧的负荷和使用要求。
正火温度一般在800℃~950℃之间,保温时间根据钢材的类型和规格进行调整。
2.3 淬火淬火是弹簧钢热处理的最后一步,其目的是通过快速冷却使钢材表面形成硬度较高的组织结构,提高弹簧的耐久性和刚性。
淬火温度一般在800℃~950℃之间,淬火介质可以选择水、油或空气,具体根据弹簧的要求进行调整。
3. 弹簧钢热处理工艺参数弹簧钢热处理工艺的参数是影响钢材性能的关键因素,下面介绍几个常见参数。
3.1 温度温度是弹簧钢热处理的主要参数之一,不同温度下钢材的组织结构和性能都会有所差异。
合理选择热处理温度可以使得钢材获得所需的硬度和强度,同时避免过热或过冷引起的不良效果。
3.2 保温时间保温时间是指钢材在一定温度下进行保温的时间,保温时间过短会导致组织不完全转变,保温时间过长则可能会影响生产效率。
保温时间的确定需要根据具体热处理工艺和钢材的特性进行调整。
3.3 冷却方式冷却方式是指钢材在热处理过程中的冷却方式,可以选择水淬、油淬或空冷等方式。
不同冷却方式会对钢材的组织结构和性能产生不同的影响,需要根据弹簧的要求进行选择。
304弹簧的热处理

304弹簧的热处理一、引言304弹簧作为一种常见的不锈钢弹簧,因其良好的耐腐蚀性能在各个领域得到广泛应用。
为了提高304弹簧的性能,热处理成为了必不可少的一环。
本文将详细介绍304弹簧的热处理过程,以及热处理对弹簧性能的影响。
二、304弹簧的热处理原理1.退火处理:退火处理是将304弹簧加热到一定的温度,然后缓慢冷却至室温。
退火处理可以消除内应力,提高弹簧的韧性,使其更容易塑性变形。
2.回火处理:回火处理是在退火处理后,将304弹簧重新加热到一定的温度,并保持一段时间,然后冷却至室温。
回火处理可以提高弹簧的强度,同时保持一定的韧性。
3.调质处理:调质处理是将304弹簧先进行淬火处理,使其具有高硬度和高强度,然后进行高温回火处理,以提高弹簧的韧性和耐磨性。
三、热处理工艺参数的选择1.温度:热处理温度的选择至关重要,不同的温度会导致不同的组织形态。
通常,退火处理的温度在800-900℃左右,回火处理的温度在500-600℃左右,调质处理的温度在400-500℃左右。
2.时间:热处理时间也会影响弹簧的性能。
时间过短,无法达到预期的处理效果;时间过长,可能导致弹簧变形或损坏。
通常,退火处理时间为1-2小时,回火处理时间为0.5-1小时,调质处理时间为1-2小时。
3.介质:热处理过程中,介质的选择也对弹簧的性能有一定影响。
常用的介质有空气、水、油等。
空气介质适用于退火和回火处理,水介质适用于快速冷却,油介质适用于缓慢冷却。
四、热处理对304弹簧性能的影响1.硬度:经过热处理后,304弹簧的硬度会有所提高,这有利于提高弹簧的耐磨性和抗疲劳性能。
2.强度:热处理可以提高304弹簧的强度,使其在承受较大载荷时不易断裂。
3.韧性:通过适当的热处理,304弹簧的韧性得到提高,使其在遇到冲击或弯曲时不易断裂。
五、热处理过程中的注意事项1.防止氧化和脱碳:在高温热处理过程中,应采取措施防止弹簧表面氧化和脱碳,以保证弹簧的表面质量。
镍钛弹簧热处理温度标准-概述说明以及解释

镍钛弹簧热处理温度标准-概述说明以及解释1.引言1.1 概述镍钛弹簧是一种具有形状记忆功能的金属弹簧,其广泛应用于多个领域,如航空航天、汽车工业和医疗器械等。
镍钛弹簧的热处理过程对其性能和稳定性起着至关重要的作用。
热处理可以通过调控材料的晶格结构和相变行为来提高弹簧的弹性模量、疲劳寿命和可靠性。
然而,镍钛弹簧热处理温度的选择对其性能至关重要。
过高或过低的热处理温度都可能导致弹簧性能的下降或不稳定。
因此,为了确保镍钛弹簧的质量和性能,制定一套科学、合理且可靠的热处理温度标准尤为重要。
本文将详细探讨镍钛弹簧热处理的基本原理、影响因素以及制定热处理温度标准的方法和重要性。
根据相关文献和实际应用经验进行梳理和总结,旨在为镍钛弹簧的热处理工艺提供科学的指导,并为相关领域的从业人员提供参考。
此外,本文还将介绍镍钛弹簧热处理温度标准在实际应用中的具体情况,以及对未来的展望。
1.2文章结构文章结构的目的是为了给读者提供一个清晰的框架,帮助他们更好地理解和阅读文章。
在本文中,我们将按照以下结构展开讨论镍钛弹簧热处理温度标准的相关话题。
第一部分是引言,主要包括三个方面内容。
首先是本部分的概述,简要介绍了文章要讨论的主题——镍钛弹簧热处理温度标准。
然后是文章结构,说明了整篇文章将按照什么样的顺序展开论述。
最后是目的,明确了撰写这篇文章的目标和意义。
第二部分是正文,是本文的核心内容。
首先介绍了镍钛弹簧热处理的基本原理,解释了为什么需要对镍钛弹簧进行热处理,以及热处理的作用和原理。
接着探讨了影响镍钛弹簧热处理的因素,包括材料的成分和性能、加热和冷却条件等。
最后,重点讨论了制定镍钛弹簧热处理温度标准的方法和依据,包括实验分析和经验总结等方面。
第三部分是结论。
首先,强调了制定镍钛弹簧热处理温度标准的重要性,指出合理的温度标准可以保证弹簧的性能和稳定性。
接着讨论了温度标准的实际应用,说明了标准在工程实践中的价值和意义。
最后进行总结与展望,回顾了本文的主要观点和结论,并展望了未来在镍钛弹簧热处理温度标准研究方面可能的发展方向。
弹簧热处理工艺流程与类型
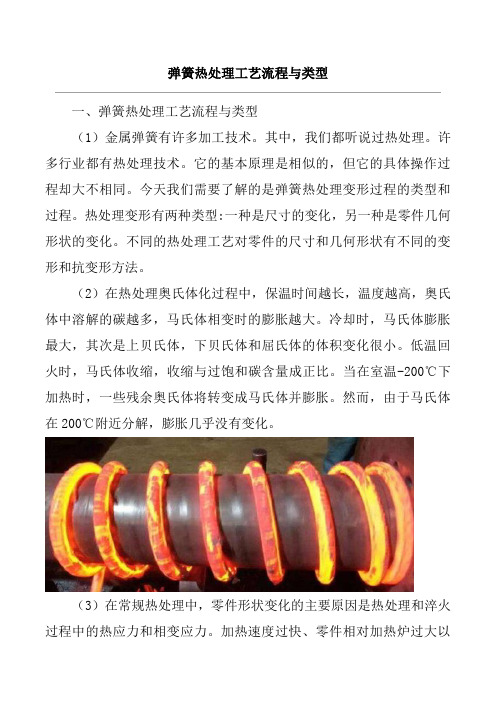
弹簧热处理工艺流程与类型一、弹簧热处理工艺流程与类型(1)金属弹簧有许多加工技术。
其中,我们都听说过热处理。
许多行业都有热处理技术。
它的基本原理是相似的,但它的具体操作过程却大不相同。
今天我们需要了解的是弹簧热处理变形过程的类型和过程。
热处理变形有两种类型:一种是尺寸的变化,另一种是零件几何形状的变化。
不同的热处理工艺对零件的尺寸和几何形状有不同的变形和抗变形方法。
(2)在热处理奥氏体化过程中,保温时间越长,温度越高,奥氏体中溶解的碳越多,马氏体相变时的膨胀越大。
冷却时,马氏体膨胀最大,其次是上贝氏体,下贝氏体和屈氏体的体积变化很小。
低温回火时,马氏体收缩,收缩与过饱和碳含量成正比。
当在室温-200℃下加热时,一些残余奥氏体将转变成马氏体并膨胀。
然而,由于马氏体在200℃附近分解,膨胀几乎没有变化。
(3)在常规热处理中,零件形状变化的主要原因是热处理和淬火过程中的热应力和相变应力。
加热速度过快、零件相对加热炉过大以及零件温度不同都会导致热变形。
在保温过程中,加工残余应力会被释放并变形,零件自重也会引起变形。
在冷却过程中,由于零件不同部分的冷却速度不同,会形成热应力使零件变形。
即使冷却速度相同,冷却在表面上总是快,在心脏上总是慢。
因此,第一相变表面使非相变芯塑性变形。
如果材料中存在合金成分的偏析或表面脱碳,相变应力将更加不均匀,更容易导致零件变形。
此外,如果零件厚度不均匀,冷却速度也会不同。
(4)在锻件热处理过程中,减少变形的零件应尽可能垂直放置,垂直放置在炉底,由两点水平支撑,支点位置在总长度的三分之一至四分之一之间,水平放置在耐热钢工装上。
(5)在零件的冷却过程中,淬火介质的类型、冷却性能和淬火能力都与变形有关。
冷却性能的变化可以通过改变粘度、温度、液体表面压力、添加剂、搅拌等来调节。
淬火油的粘度越高,温度越高,椭圆变形越小。
静止时,变形很小。
弹簧感应热处理概要

放线机构采用立式放线加气动翻转10~45。角放线, 2只放线机分时交替工作,保证连续放线不停车。矫直 机 由压送机构(配4 kW减速机l台),前牵引机(配7.5 kW 减速机1台,压送轮直径就20衄4对,液压压紧装 置), 矫直机构(配有水平矫直7辊,垂直矫直7辊, 1.1 kw 减速机2台,自动压紧)3部分组成。其中压送 及牵引通 过变频器进行控制,牵引机配11 kw减速机, 压送轮采用 液压压紧装置。带随动的液压剪切机(配 30 kw电机油泵), 保证剪切力及剪切速度,并能手动 /自动剪切及分料。淬火 冷却为带喷头油箱,外型尺 寸为3.5m×0.5 m×1.3 m。回火 冷却为带喷头水 箱,外型尺寸为2.5 m×0.5 m×1.3 m。收 线采用 卧式结构,收线机线盘直径2.8 m,配5.5 kw电 机, 2只收线机分时交替工作,能实现不问断连续收线, 单盘收线重量可达2.5 t。清洗机选用行星3轮清洗机 构, 配o.75 kw电机。涂油机采用浸油,刮油形式, 保证油 层均匀度。
要求: 3Cr13 HRC39-46 4Cr13 HRC48-50 HRC48-49 HRC47-49 HRC37-40 HRC31-35 HRC33-47 9.条件: 在酸碱介质下工作的弹簧 要求: 2Cr18Ni9 1100-1150℃水淬,绕卷后消除应力,400℃回
火60min,HB160-200 10.条件: 弹性挡圈δ4,Φ85 要求: 60Si2 400℃预热,860℃油淬,430℃回火空冷,HRC40-
7
电源的控制系统由整流触发、调节控制、逆变控 制及保护等组成。整流触发采用数字电路提供整 流桥晶闸管的6路触发脉冲。调节控制完成电源的 调功、限流、限压、电流负反馈,并设有过电流、 过电压、低水压、缺相、过温等保护。逆变控制 采用定时锁相功能及为scR、IGBT模块提供可靠的 触发驱动脉冲,保证设备具有极强的抗干扰能力 及稳定性。电源采用电压,电流双闭环控制,具 有恒电压运行功能。电源具有内控、外控功能, 内控时手动启停及调功,外控时可由PLC进行操作。
- 1、下载文档前请自行甄别文档内容的完整性,平台不提供额外的编辑、内容补充、找答案等附加服务。
- 2、"仅部分预览"的文档,不可在线预览部分如存在完整性等问题,可反馈申请退款(可完整预览的文档不适用该条件!)。
- 3、如文档侵犯您的权益,请联系客服反馈,我们会尽快为您处理(人工客服工作时间:9:00-18:30)。
电源的控制系统由整流触发、调节控制、逆变控 制及保护等组成。整流触发采用数字电路提供整 流桥晶闸管的6路触发脉冲。调节控制完成电源的 调功、限流、限压、电流负反馈,并设有过电流、 过电压、低水压、缺相、过温等保护。逆变控制 采用定时锁相功能及为scR、IGBT模块提供可靠的 触发驱动脉冲,保证设备具有极强的抗干扰能力 及稳定性。电源采用电压,电流双闭环控制,具 有恒电压运行功能。电源具有内控、外控功能, 内控时手动启停及调功,外控时可由PLC进行操作。
弹簧感应热处理
目 录
Contents
第一章:请第在一此章处:输入您的标 弹簧感应热题处理简介
第二章:请第在二此章处:输入您的标 弹簧感应热题处理技术
第三章:请第在三此章处:输入您的标 弹簧感应热题处理案例
2
弹簧感应热处理简述
Click here to add your title
3
弹簧是机械行业和日常生活中最常用的零件。弹簧 在弹性 范围内使用,卸载后应回复到原来位置,塑性变 形越小越 好,因此钢丝应具有高的弹性极限、屈服强度 和抗拉强度。 屈强比越高,弹性极限就越接近抗拉强度, 因而越能提高 强度利用率,制成的弹簧弹力越强。弹簧 钢丝按生产工艺 可分为冷拉弹簧钢丝和油回火弹簧钢丝 两种,以晶闸管中 频感应加热和IGBT超音频感应加热电 源为核心,采用淬火 回火温度闭环,钢丝的张力闭环方 式,通过PLc集中控制, 完成系统的工艺控制,从而达 到系统的高效率、产品的高 质量、性能的高一致性。我 们新近开发投产了速率为30~ 45 m/min的油回火弹簧 钢丝生产线。
10
系统的主要特点 1)性能高且稳定 (1)采用交流变频调速传动系统,完全满足调节要 求,成
本低,结构简单,运行可靠,易于维护。 (2)采用双IGBT超音频感应加热电源,用30 kHz 在居里点
附近进行提温,并达到工艺淬火温度,提高系 统的可靠性 和稳定性。 (3)所有感应加热系统和传动系统均由PLc控制, 感应加热 系统采用输出电压闭环控制,传动系统实行速 度闭环控制, 确保机械部分的传动速度和感应加热部分 的输出功率保持 恒定。 (4)采用工艺参数分类存储技术,确保每种规格产 品在同 种工艺条件下生产。 (5)采用温度补偿技术,消除气温波动对产品质量 的影响。
4
弹簧钢丝的生产过程是将钢丝冷拉到所需尺寸后,通过 加热到淬火温度,获得奥氏体组织,然后淬火为马氏体, 再回火获得屈氏体组织。油回火钢丝具有极好的弹性和 非常高的力学性能,并且其疲劳强度及较高工作温度下 的抗应力、松驰性能也要比冷拉钢丝好得多。在重要用 途弹簧钢丝领域⋯,合金钢介入油回火生产也占有很大比 例,弹簧制造厂可以直接用油回火钢丝制造弹簧省去淬 火一回火工序,有较高的经济效益和社会效益。本生产 线系统由控制部分、机械传动部分和感应加热部分组成。 加热生产线工作原理流程示意图见图l。
放线机构采用立式放线加气动翻转10~45。角放线, 2只放线机分时交替工作,保证连续放线不停车。矫直 机 由压送机构(配4 kW减速机l台),前牵引机(配7.5 kW 减速机1台,压送轮直径就20衄4对,液压压紧装 置), 矫直机构(配有水平矫直7辊,垂直矫直7辊, 1.1 kw 减速机2台,自动压紧)3部分组成。其中压送 及牵引通 过变频器进行控制,牵引机配11 kw减速机, 压送轮采用 液压压紧装置。带随动的液压剪切机(配 30 kw电机油泵), 保证剪切力及剪切速度,并能手动 /自动剪切及分料。淬火 冷却为带喷头油箱,外型尺 寸为3.5m×0.5 m×1.3 m。回火 冷却为带喷头水 箱,外型尺寸为2.5 m×0.5 m×1.3 m。收 线采用 卧式结构,收线机线盘直径2.8 m,配5.5 kw电 机, 2只收线机分时交替工作,能实现不问断连续收线, 单盘收线重量可达2.5 t。清洗机选用行星3轮清洗机 构, 配o.75 kw电机。涂油机采用浸油,刮油形式, 保证油 层均匀度。
6
1.1加热电源
本生产线采用了晶闸管(SCR)中频电源和固态模 。 块 化(IGBT)超音频感应加热电源的组合来实现效率的 最 大化。对于感应加热电源乜】,由于圆棒料加热电源 所 需频率与棒料直径、电阻率及导磁率有关,同样直 径 的棒料,在居里点(疋=723。℃)前后导磁率将发生 剧 变,因此在居里点前与居里点后,加热电源要采用 不同 的频率。此生产线共有4台加热电源组成,淬火 加热采 用KGPS一250 kw/4~6 kHz晶闸管中频电源 (居里点前 升温)和IPS一160kW/30kHz IGBT超音频电 源(居里点 后升温),回火加热采用KGPS一100 kW/ 4~6 kHz两台 晶闸管中频感应加热电源。电源主回路 结构为晶闸管三相工频六脉全控整流,节能高效平波 电抗器,scR或IGBT并联逆变,将三相工频转化成单相 中频、超音频输出。
5
全自动弹簧感应热处理设备,整套设备由:中频 电源、电容柜、感应器、全自动送料架、卸料架 和控制柜组成。中频电源采用分体式结构设计, 电源柜为GGD标准柜。电容柜和感应器结构设计紧 凑,提高了加热效率。合理控制感应器与淬火圈 距离,缩短了红热棒料暴露在空气中的时间,减 少了棒料的氧化皮,降低了能耗。根据用户设定 的工艺参数,自动控制传动机构的速度。感应器 中没有工件时,自动控制系统自动降低中频电源 的输出功率;工件进入感应器,自动控制系统自 动提升中频电源的输出功率。
8
1.2控制部分和机械传动部分 整条生产线采用连线方式工作,由PLC中央控制台进行
集中统一协调控制。由于弹簧钢丝生产线为连续不问 断运行,故电机与电源的自动控制显得尤为重要,并 且将直接影响到产品的质量。电机传动部分采用ABB变 频调速电源来控制传送线的运行速度。利用集控台, 通过PLC及人机界面等控制系统,使生产线启动时,能 自动完成传动机构及各电源的启动,并自动实现速度 与功率上升的合理匹配,自动调节加热电源的功率。 温度闭环调节可保证淬火、回火的温度稳定,确保生 产线按最佳工艺参数运行,保证产品质量不受人工及 环境因素的影响。同时系统具有20套工艺参数的设定、 存储、调节,修改、统计等功能。人机界面中文图形 文本(触摸屏)可设定及实时显示电源功率、频率,钢 丝速度、长度、直径、质量及有关信息。