SEM铸造缺陷分析
铸造缺陷质量分析报告

铸造缺陷质量分析报告标题:铸造缺陷质量分析报告摘要:本次报告对一批铸造件的缺陷进行了详细分析,并提供了解决方案,以提高铸件的质量和可靠性。
通过对缺陷的分类、原因分析和改进措施的制定,本报告的目标是降低缺陷率、提高产品质量,并为企业的生产过程提供指导。
一、引言铸造工艺是一种常见且重要的金属加工方式,但由于多种因素的影响,铸造件常常出现各种缺陷。
本报告对以下几种常见铸造缺陷进行了分析:气孔、砂眼、夹渣和缩孔。
二、缺陷分类和特征1. 气孔:气孔是铸造件内部的圆形或椭圆形气体空洞,在表面上通常呈孔状。
这种缺陷的特征是大小不一、分布不均匀,并且可能与材料中的气体分离有关。
2. 砂眼:砂眼是在铸造件表面形成的小凹陷或孔穴,并且通常有砂粒残留。
这种缺陷的主要原因是在型腔填充过程中砂芯未能完全固化或砂芯破裂。
3. 夹渣:夹渣是铸造件内部存在金属残留或其他非金属杂质的缺陷。
它通常表现为呈条状、点状或块状分布的较暗色物质。
4. 缩孔:缩孔是在铸造件中形成的不完全填充的孔洞,通常位于较厚的截面部分。
这种缺陷的主要原因是在凝固过程中金属收缩引起的。
三、缺陷原因分析1. 气孔:气孔的形成主要与以下因素有关:金属液中溶解的气体、型腔设计不合理、浇注过程中液态金属的气体浸润和释放等。
解决方案包括采取适当的除气处理、改进型腔设计、控制浇注工艺等。
2. 砂眼:砂眼通常与砂芯制备和浇注过程中的温度、浇注速度等相关。
解决方案包括优化砂芯制备工艺、调整浇注参数以及改善浇注系统设计等。
3. 夹渣:夹渣的原因主要与金属液的净化和过滤不足、浇注过程中金属液与非金属杂质的接触等有关。
解决方案包括加强净化处理、使用过滤器、改进浇注工艺等。
4. 缩孔:缩孔的形成与金属凝固收缩不平衡、铸造温度过低、浇注过程中金属液的顺流速度等相关。
解决方案包括优化浇注工艺、控制冷却速度等。
四、改进措施根据对缺陷原因的分析,提出了以下改进措施:1. 加强除气处理:通过采用真空或压力浇注等技术,有效去除金属液中的气体;2. 优化砂芯工艺:提高砂芯的强度和温度稳定性,避免砂芯破裂;3. 加强金属液净化:采用有效的净化剂和过滤器,去除金属液中的杂质;4. 调整浇注参数:合理控制浇注温度和速度,确保金属液充满型腔;5. 优化冷却过程:控制冷却速度,减少金属凝固收缩引起的缺陷。
铸件缺陷分析PPT课件

铸件在凝固末期或刚凝固 后不久产生的裂纹。
03
铸件缺陷形成原因及机理分析
原材料因素
原材料质量
使用不合格或质量差的原材料, 如废钢、生铁等,其中含有的杂 质元素和气体可能导致铸件缺陷 。
原材料配比
原材料配比不合理,如碳、硅等 元素含量过高或过低,会影响铸 件的凝固过程和机械性能。
熔炼工艺因素
熔炼温度
介绍了常用的铸件缺陷检测与评估方法,如目视检查、无损检测、 金相分析等,以及各种方法的优缺点和适用范围。
缺陷预防与控制措施
重点讲解了铸件缺陷的预防和控制措施,包括优化铸造工艺、提高原 材料质量、加强过程监控等方面。
学员心得体会分享
知识收获
学员们表示通过本次课程,对铸件缺陷的类型、成因、检 测与评估方法有了更深入的了解,对铸件质量控制的重要 性有了更深刻的认识。
其他可能影响因素
生产环境
生产环境中的温度、湿度和清洁度等因素对铸件质量也有一 定影响。例如,湿度过高可能导致型砂粘结力下降,温度过 高则可能导致铁液冷却速度过快。
操作技能
操作工人的技能水平和经验对铸件质量也有重要影响。例如 ,合箱时定位不准确、浇注时铁液温度控制不当等都可能导 致铸件缺陷。
04
铸件缺陷预防措施与改进方法
控制熔炼温度
根据原材料成分和熔炼设备特点, 合理设置熔炼温度,避免过高或 过低的熔炼温度对铸件质量产生 不良影响。
调整化学成分
通过添加合金元素和调整废钢、生 铁等原材料的配比,控制铁水的化 学成分,提高铸件的力学性能和耐 蚀性。
减少熔炼杂质
采取过滤、除渣等措施,减少熔炼 过程中产生的氧化物、硫化物等杂 质,提高铁水的纯净度。
夹渣和夹杂物
01属夹杂物,夹杂 物则是金属或非金属杂质。
铸造工艺流程中的铸件缺陷分析与改进策略

铸造工艺流程中的铸件缺陷分析与改进策略铸造工艺是一种重要的金属加工方法,用于制造各种形状的金属件。
然而,在铸造过程中,铸件缺陷是一个常见的问题,它会影响到铸件的质量和性能。
因此,对于铸造工艺流程中的铸件缺陷进行深入分析,并提出改进策略,对于提高铸件质量和工艺效率具有重要意义。
一、铸件缺陷的分类与原因分析在铸造工艺中,铸件缺陷可以分为表面缺陷和内部缺陷两类。
常见的表面缺陷包括气孔、砂眼、砂洞等;内部缺陷主要有夹杂物、孔洞、收缩系数不均匀等。
1.1 气孔气孔是铸造工艺中最常见的表面缺陷之一。
其形成的原因通常有两个方面,一是液态金属中溶解气体含量过高,二是在金属凝固过程中,气体生成而未能有效排除。
造成气孔的常见因素包括砂芯质量不佳、浇注温度过高、浇注速度过快等。
1.2 砂眼和砂洞砂眼是指铸件表面局部凹陷的缺陷,而砂洞是指铸件内部或边缘凹陷的缺陷。
主要原因包括模具缺陷、浇注系统设计不合理、浇注金属温度过低等。
1.3 夹杂物夹杂物是指铸件中存在的杂质,如炉渣、油污等。
其主要原因包括铁水净化不彻底、砂芯质量不佳等。
1.4 孔洞孔洞是指铸件内部存在的封闭空腔。
常见的孔洞形式包括气孔和收缩孔。
造成孔洞的原因主要有铁水中含气量高、铸型泥浆含水量高等。
1.5 收缩系数不均匀收缩系数不均匀是指铸件不同部位的收缩量不一致。
这可能会引起铸件的内部应力集中,从而导致开裂和变形。
收缩系数不均匀的原因包括铸造合金的特性、浇注温度的控制等。
二、改进策略为了减少铸件缺陷,提高铸件质量和工艺效率,以下是一些改进策略的具体措施:2.1 优化模具设计模具设计是影响铸件质量的关键因素之一。
通过优化模具结构、提高模具材料质量和表面光洁度,可以减少砂眼、砂洞等表面缺陷的产生。
2.2 控制浇注温度和速度浇注温度和速度对铸件质量有着直接的影响。
合理控制浇注温度和速度,可以降低气孔和夹杂物等缺陷的产生。
2.3 改进铸型材料和工艺选择合适的铸型材料,对铸件质量和工艺效率的提高至关重要。
铸造缺陷鉴别
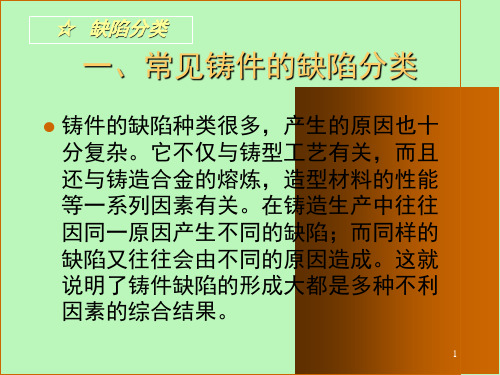
二、孔洞类铸造缺陷的鉴别
①、缩孔常见部位示意 图
17
二、孔洞类铸造缺陷的鉴别
②、缩松:铸件断面上 出现的分散而细小的 缩孔。有时借放大镜 才能发现。缩松部位 在水压试验时会渗漏 疏松:形状和缩松 相似,但孔洞更细小, 组织粗大,石墨粗大 等缺陷也可能导致铸 件组织疏松。
18
二、孔洞类铸造缺陷的鉴别
网状或脉状分布的毛 刺称脉纹。
24
三、多肉类缺陷的鉴别
2、抬 箱(抬 型): 铸件在 分型面 部位高 度和宽 度增大
25
三、多肉类缺陷的鉴别
3、涨砂: 铸件内、 外表面局 部胀大, 形成不规 则的瘤状 金属凸起 物。
26
三、多肉类缺陷的鉴别
4、冲砂: 铸件表面 上有粗糙 不规则的 金属瘤状 物,常位 于浇口附 近。在铸 件其它部 位则往往 出现砂眼。
36
六、残缺类缺陷
浇不到: 由于金 属液未 完全充 满型腔 而产生 的铸件 缺肉。
37
六、残缺类缺陷
2、缺 损:在 铸件清 理或搬 运时, 损坏了 铸件的 完整性。
38
七、尺寸、形状和重量差错类缺陷
1、变型: 由于收 缩应力 或型壁 变形、 开裂引 起的铸 件外形 和尺寸 与图纸 不符。
12
二、孔洞类铸造缺陷的鉴别
③、反应气孔:液态金 属的某些成分之间或 液态金属与铸型在界 面上发生化学反应产 生的气孔。 气孔位于铸件表皮 下,有的呈分散的针 状,有的隐藏在铸件 上部并伴有夹渣。
13
铸件气孔实例(1)
14
铸件气孔实例(2)
15
二、孔洞类铸造缺陷的鉴别
2、缩孔:形状为不规 则的封闭或敞露的孔 洞,孔壁粗糙并带有 枝状晶,且晶粒粗大。 常出现在铸件最后凝 固的部位(热节处)
铸造铸件缺陷质量评估

铸造铸件缺陷质量评估一、引言铸造是制造业中最为常见的加工方式之一,铸造铸件广泛应用于航空、汽车、造船等工业领域。
尽管铸造技术已经得到了长足的发展,但铸造铸件在生产过程中仍然很难避免缺陷的出现,如气孔、夹杂、缺口、裂纹等,这些缺陷会降低铸件的质量,甚至会对铸件的使用性能造成影响。
因此,对铸造铸件缺陷的质量评估显得十分重要。
二、铸造铸件缺陷的分类及产生原因(一)铸造铸件缺陷的分类铸造铸件的缺陷种类繁多,如气孔、夹杂、缩孔、缺口、裂纹等。
其中,气孔是最为常见的缺陷之一,主要是由于液态金属中难以排除的空气造成的。
夹杂是由于冷却速度不够快或金属液和包覆剂接触不良造成的,缩孔是由于铸件内部液态金属冷却后收缩过程中未能填满的空气所致,缺口和裂纹是由于铸件的凝固过程中金属液流动受阻或温度梯度过大引起的。
(二)产生缺陷的原因铸造铸件缺陷产生的原因主要包括金属液凝固过程中的气孔、夹杂、缩孔等缺陷,砂型质量问题,浇注温度问题,浇注系统、冷却系统的设计不合理,制造工艺参数不恰当等问题。
三、缺陷评估方法(一)人工评估法人工评估法是最为直观的评估方法之一,通过视觉检查或使用放大镜对铸件表面或切割面的缺陷进行评估。
这种方法操作简单,成本低廉,但是准确性较低,特别是对微小缺陷难以发现。
(二)X射线检测法X射线检测是一种非破坏性检测方法,可以检测出铸件内部的缺陷。
X射线检测的优点在于准确性高、速度快、应用范围广,可以检测出各种类型的铸件缺陷。
但是,这种检测方法的成本较高,同时需要特殊设备和专业技术人员进行操作。
(三)超声波检测法超声波检测也是一种非破坏性检测方法,主要用于检测铸件的表面和内部缺陷。
这种检测方法的优点在于操作简便,成本较低,但是对于微小缺陷的检测准确性差一些。
(四)磁粉检测法磁粉检测是一种破坏性检测方法,主要用于检测铸件的表面缺陷,例如裂纹、缺口等。
这种方法的成本较低,检测效果比较准确,但是它会对铸件造成永久性的伤害。
铸造工艺缺陷及解决措施
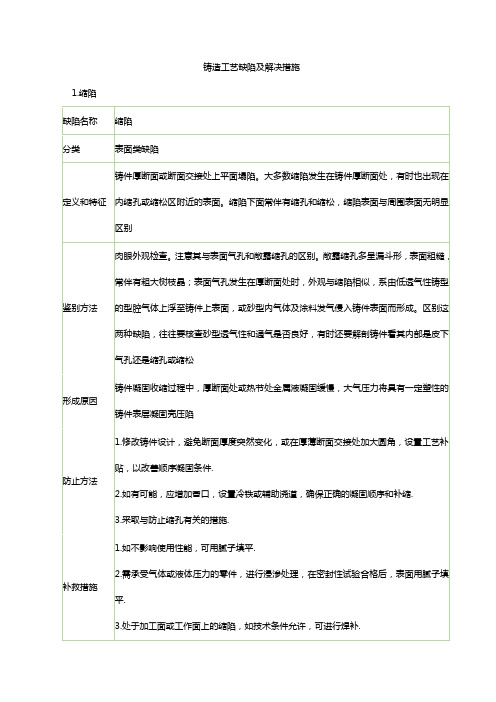
1.使用耐火度高的细粒原砂.
2.采用再生砂时,去除过细的砂粒、死烧粘土、灰分、金属氧化物、废金属、铁包砂及其他有害杂质,提高再生砂质量。定期补充适量新砂.
3.水是强烈氧化剂,应严格控制湿型砂水分,加入适量煤粉、沥青、碳氢化合物等含碳材料,在砂型中形成还原性气氛。但高压造型时应减少含碳材料加入量,以减少发气量.
防止方法
浇注前浇包中应备有足以充满铸型的金属液;浇注速度适当,浇注操作遵守工艺规程.
补救措施
概率因子
0.7
缺陷名称
未浇满
分类
残缺类缺陷
定义和特征
鉴别方法
形成原因
上箱过矮,金属的静压力小,易发生未浇满.
防止方法
保证有足够的液态金属压头充满型腔.
补救措施
浇注前浇包中应备有足以充满铸型的金属液;浇注速度适当,浇注操作遵守工艺规程
保证压铁的重量,箱夹的强度,数量足够,并选择合适的位置.
补救措施
概率因子
0.5
缺陷名称
跑火
分类
残缺类缺陷
定义和特征
鉴别方法
形成原因
金属液充型剧烈,易使型芯破裂造成跑火缺陷
防止方法
控制浇温,充型要平稳.
补救措施
概率因子
0.3
4.脉纹
缺陷名称
脉纹
分类
多肉类缺陷
定义和特征
鉴别方法
形成原因
硅砂在573℃发生相变膨胀,浇注时铸型表面易产生裂纹.
概率因子
3.跑火
缺陷名称
跑火
分类
残缺类缺陷
定义和特征
鉴别方法
形成原因
砂箱的接合面未清理干净封箱不妥等因素使跑火缺陷容易发生
防止方法
常见铸造缺陷分析及质量检测方法概述论文

常见铸造缺陷分析及质量检测方法概述The analysis of frequent casting flaw and summary of detectmethod摘要:简要说明了铸造缺陷的种类及产生原因,重点阐述了缺陷质量控制及方法,并对实际生产中易出现的缺点作了说明,最后对无损检测技术作了补充说明。
Abstract: The types and causes of casting flaw are briefly introduced, focused on the method and control of casting flaw, and described the problems in production, finally, introduced some noninvasive testing technology.关键词:铸造缺陷质量检测无损检测Key words: casting flaws ;quality detecting;noninvasive testing technology1铸造缺陷的种类在铸造生产过程中,常见的缺陷有:气孔、粘砂、夹砂、砂眼、胀砂、冷隔、浇不足等,下面我们简要介绍一下各个类型的缺陷以及防治方法。
1.1气孔气体在金属液结壳之前未及时逸出,在铸件内生成的孔洞类缺陷。
气孔的内壁光滑,明亮或带有轻微的氧化色。
铸件中产生气孔后,将会减小其有效承载面积,且在气孔周围会引起应力集中而降低铸件的抗冲击性和抗疲劳性。
气孔还会降低铸件的致密性,致使某些要求承受水压试验的铸件报废。
另外,气孔对铸件的耐腐蚀性和耐热性也有不良的影响。
防止气孔的产生:降低金属液中的含气量,增大砂型的透气性,以及在型腔的最高处增设出气冒口等。
1.2粘砂铸件表面上粘附有一层难以清除的砂粒称为粘砂。
粘砂既影响铸件外观,又增加铸件清理和切削加工的工作量,甚至会影响机器的寿命。
防止粘砂:在型砂中加入煤粉,以及在铸型表面涂刷防粘砂涂料等。
铸造缺陷的特征、鉴别、成因及防治措施

铸造缺陷的特征、鉴别方法、成因及防治措施一、多肉类缺陷的防止措施总结1、飞翅缺陷的特征、鉴别方法、成因及防治措施(1)定义和特征产生在分型面、分芯面、芯头、活块及型与芯结合面等处,通常垂直于铸件表面的厚度不均匀的薄片状金属凸起物,又称为飞边或披缝。
(2)鉴别方法肉眼外观检查。
飞翅出现在型—型、型—芯、芯—芯结合面上,成连片状,系结合面间隙过大所致。
(3)形成原因①②③④⑤⑥⑦(4)防止方法①②③④⑤⑥⑦(5)补救措施2、毛刺缺陷的特征、鉴别方法、成因及防治措施(1)定义和特征(2)鉴别方法肉眼外观检查。
(3)形成原因①②③④⑤⑥⑦(4)防止方法①②③④⑤⑥⑦(5)补救措施3、冲砂缺陷的特征、鉴别方法、成因及防治措施(1)定义和特征(2)鉴别方法肉眼外观检查。
(3)形成原因①②③④⑤⑥⑦(4)防止方法①②③④⑤⑥⑦(5)补救措施4、胀砂缺陷的特征、鉴别方法、成因及防治措施(1)定义和特征(2)鉴别方法肉眼外观检查。
(3)形成原因①②③④⑤⑥⑦(4)防止方法①②③④⑤⑥⑦(5)补救措施5、抬型/抬箱缺陷的特征、鉴别方法、成因及防治措施(1)定义和特征(2)鉴别方法肉眼外观检查。
(3)形成原因(4)防止方法①②③④⑤(5)补救措施①②6、外渗物/外渗豆缺陷的特征、鉴别方法、成因及防治措施(1)定义和特征(2)鉴别方法肉眼外观检查。
(3)形成原因①②③(4)防止方法①②③④⑤⑥(5)补救措施7、掉砂缺陷的特征、鉴别方法、成因及防治措施(1)定义和特征(2)鉴别方法肉眼外观检查。
(3)形成原因①②③④⑤⑥⑦(4)防止方法①②③④⑤⑥⑦(5)补救措施二、孔洞类1、反应气孔缺陷的特征、鉴别方法、成因及防治措施(1)定义和特征(2)鉴别方法(3)形成原因①②③(4)防止方法①②③(5)补救措施2、卷入气孔缺陷的特征、鉴别方法、成因及防治措施(1)定义和特征(2)鉴别方法(3)形成原因①②③(4)防止方法①②③④(5)补救措施①②③3、侵入气孔缺陷的特征、鉴别方法、成因及防治措施(1)定义和特征(2)鉴别方法(3)形成原因①②③④(4)防止方法①②③④(5)补救措施①②③4、析出气孔缺陷的特征、鉴别方法、成因及防治措施(1)定义和特征(2)鉴别方法(3)形成原因①②③(4)防止方法(5)补救措施①②③5、疏松(显微缩松)缺陷的特征、鉴别方法、成因及防治措施(1)定义和特征(2)鉴别方法(3)形成原因①②③④⑤⑥⑦⑧⑨⑩(4)防止方法①②③④⑤⑥⑦⑧⑨⑩(5)补救措施①②③④6、缩孔缺陷的特征、鉴别方法、成因及防治措施(1)定义和特征(2)鉴别方法(3)形成原因①②③④⑤⑥⑦(4)防止方法①②③④⑤⑥⑦⑧(5)补救措施7、缩松缺陷的特征、鉴别方法、成因及防治措施(1)定义和特征(2)鉴别方法(3)形成原因①②③④⑤⑥⑦⑧⑨⑩(4)防止方法①②③④⑤⑥⑦⑧⑨⑩(5)补救措施①②③④三、裂纹、冷隔类1、白点(发裂)缺陷的特征、鉴别方法、成因及防治措施(1)定义和特征(2)鉴别方法(3)形成原因①②(4)防止方法①②③④(5)补救措施2、冷隔缺陷的特征、鉴别方法、成因及防治措施(1)定义和特征(2)鉴别方法肉眼外观检查。
铸造铸件常见缺陷分析报告

铸造铸件常见缺陷分析铸造工艺过程复杂,影响铸件质量的因素很多,常见的铸件缺陷名称、特征和产生的原因,见表。
文案大全文案大全文案大全文案大全铸件质量与气孔的关系1)合理选定铸造合金和铸件结构。
2)合理制定铸件技术要求(允许缺陷,具有规文案大全定)。
3)模型质量检验(模型合格—铸件合格)4)铸件质量检验(宏观,仪器)5 铸件热处理: 消除应力,降低硬度,提高切削性,保证机械性能,退火,正火等。
1 破坏金属连续性2 较少承载有效面积文案大全3 气孔附近易引起应力集中,机械性能4 弥散孔,气密性侵入气孔,砂型材料表面聚集的气体侵入金属液体中而形成气体来源,造型材料中水分,粘结剂,各种附加物等.气孔的特征: 多位于表面附近,尺寸较大,呈椭圆形或梨形孔的内表面被氧化。
气孔形成过程:文案大全浇注---水汽(一部分由分型面,通气孔排出,另一部分在表面聚集呈高压中心点)—气压升高,溶入金属---一部分从金属液中逸出—浇口,其余在铸件内部,形成气孔。
预防气孔的发生: 降低型砂(型芯砂)的发起量,增加铸型排气能力。
文案大全析出气孔: 溶于金属液中的气体在冷凝过程中,因气体溶解度下降而析出,使铸件形成气孔,原因: 金属熔化和浇注中与气体接触(H2 O2 NO CO等) 特征: 分布广,气孔尺寸甚小,影响气密性。
反应气孔: 金属液与铸型材料,型芯撑,冷铁或溶渣之间,因化学反应生成的气体而形成的气孔。
如: 冷铁有锈Fe3O4 + C –Fe + 文案大全CO 冷铁附近生成气孔防止: 冷铁型芯撑表面不得有锈蚀,油污,要干燥。
文案大全文案大全常见铸件缺陷及其预防措施文案大全文案大全文案大全文案大全文案大全文案大全。
铸造缺陷及其对策

某铸件在浇注过程中,由于模具表面存在油污和杂质,导 致金属液中混入杂质,最终在铸件表面形成明显的夹渣。
解决方案
保持模具表面干净整洁,避免油污和杂质混入金属液;采 用过滤网或过滤器等措施,去除金属液中的杂质。
裂纹案例
裂纹
在铸造过程中,由于铸件结构不合理、模具温度不均匀或金属液冷 却过快等原因,导致铸件中产生裂纹。
夹渣
总结词
夹渣是由于铸造过程中熔渣混入金属液中,在铸件凝固时未能及时浮出而形成的 夹杂物。
详细描述
夹渣通常表现为不规则的块状或颗粒状,大小不一,对铸件的机械性能和使用寿 命有一定影响。夹渣的形成与金属液的净化程度、浇注系统和模具的设计等因素 有关。
裂纹
总结词
裂纹是铸造过程中由于金属液的冷却收缩而产生的缝隙,通 常表现为细长的线性缺陷。
加强生产过程监控
对生产过程进行实时监控,及时发现并处理异常 情况。
3
提高员工技能水平
加强员工技能培训,提高员工操作技能和安全意 识。
引入先进技术与管理方法
引进现代化铸造设备
采用自动化、智能化的铸造设备,提高生产效 率和产品质量。
推行精益生产管理
引入精益生产管理理念和方法,优化生产流程, 降低生产成本。
建立完善的质量管理体系
建立完善的质量管理体系,确保产品质量符合标准要求。
05
铸造缺陷的修复与处理
焊接修复
总结词
焊接修复是一种常见的铸造缺陷修复方法,适用于修复裂纹、断裂等缺陷。
详细描述
焊接修复通过将焊料熔化填充铸造缺陷,冷却后形成坚固的连接,实现对铸造缺陷的修复。焊接修复 具有操作简便、快速、成本低等优点,但需注意焊接过程中可能产生的热影响区和焊接应力,可能导 致新的缺陷或变形。
铸造缺陷分析及工艺优化措施
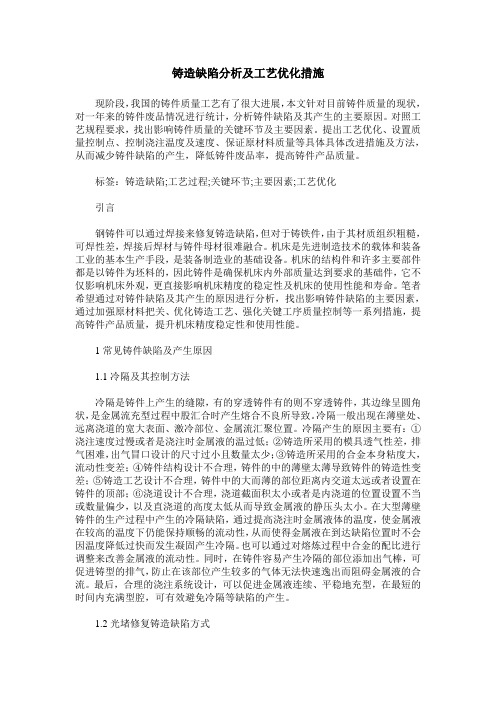
铸造缺陷分析及工艺优化措施现阶段,我国的铸件质量工艺有了很大进展,本文针对目前铸件质量的现状,对一年来的铸件废品情况进行统计,分析铸件缺陷及其产生的主要原因。
对照工艺规程要求,找出影响铸件质量的关键环节及主要因素。
提出工艺优化、设置质量控制点、控制浇注温度及速度、保证原材料质量等具体具体改进措施及方法,从而减少铸件缺陷的产生,降低铸件废品率,提高铸件产品质量。
标签:铸造缺陷;工艺过程;关键环节;主要因素;工艺优化引言钢铸件可以通过焊接来修复铸造缺陷,但对于铸铁件,由于其材质组织粗糙,可焊性差,焊接后焊材与铸件母材很难融合。
机床是先进制造技术的载体和装备工业的基本生产手段,是装备制造业的基础设备。
机床的结构件和许多主要部件都是以铸件为坯料的,因此铸件是确保机床内外部质量达到要求的基础件,它不仅影响机床外观,更直接影响机床精度的稳定性及机床的使用性能和寿命。
笔者希望通过对铸件缺陷及其产生的原因进行分析,找出影响铸件缺陷的主要因素,通过加强原材料把关、优化铸造工艺、强化关键工序质量控制等一系列措施,提高铸件产品质量,提升机床精度稳定性和使用性能。
1常见铸件缺陷及产生原因1.1冷隔及其控制方法冷隔是铸件上产生的缝隙,有的穿透铸件有的则不穿透铸件,其边缘呈圆角状,是金属流充型过程中股汇合时产生熔合不良所导致。
冷隔一般出现在薄壁处、远离浇道的宽大表面、激冷部位、金属流汇聚位置。
冷隔产生的原因主要有:①浇注速度过慢或者是浇注时金属液的温过低;②铸造所采用的模具透气性差,排气困难,出气冒口设计的尺寸过小且数量太少;③铸造所采用的合金本身粘度大,流动性变差;④铸件结构设计不合理,铸件的中的薄壁太薄导致铸件的铸造性变差;⑤铸造工艺设计不合理,铸件中的大而薄的部位距离内交道太远或者设置在铸件的顶部;⑥浇道设计不合理,浇道截面积太小或者是内浇道的位置设置不当或数量偏少,以及直浇道的高度太低从而导致金属液的静压头太小。
在大型薄壁铸件的生产过程中产生的冷隔缺陷,通过提高浇注时金属液体的温度,使金属液在较高的温度下仍能保持顺畅的流动性,从而使得金属液在到达缺陷位置时不会因温度降低过快而发生凝固产生冷隔。
铸造常见的缺陷与产生原因

铸造常见的缺陷与产生原因铸造是一种常用的金属加工方法,其用途广泛,但在生产过程中常常会产生一些缺陷,如气孔、夹渣、缩孔等。
这些缺陷不仅会影响铸件的外观质量,还可能降低其力学性能和使用寿命。
下面我将从不同的缺陷类型和产生原因两个方面详细介绍。
一、缺陷类型1. 气孔:气体在铸造过程中产生,并被封入铸件内部,形成孔隙。
气孔的尺寸和分布形态不同,可能是小孔、球形孔、管状孔等。
气孔的产生主要与以下几个因素有关:(1) 铝液中的气体:铝液中含有的氧和氢会在高温下产生氧化反应和水解反应,释放出氧气和氢气。
(2) 表面液相:铝液在铸模表面形成的氧化膜或润滑剂残留等可能导致铝液表面的液相存在,进一步促使气体产生。
(3) 细小颗粒:铝液中存在的颗粒会成为气体生成的核心,进而形成气孔。
2. 夹渣:铝液在充填过程中携带入模型腔内的杂质、氧化物或熔渣等,最终导致铸件内部出现夹杂物。
夹渣的产生原因主要有:(1) 原材料中的杂质:铝合金原材料中可能含有一些杂质,如氧化物、砂粒等。
(2) 熔化过程中的氧化:铝液在高温条件下容易与空气发生氧化反应,形成氧化物。
(3) 流动过程中的杂质:铝液在流动过程中可能带动模具内部的砂粒、润滑剂残留等。
3. 缩孔:铸件内部或者表面出现的凹陷或裂纹。
缩孔的产生原因主要有:(1) 升温不均:铝液升温不均会导致热胀冷缩不一致,从而在铸件内部产生收缩应力,进一步造成缩孔。
(2) 施加过大应力:当铸件过早地受到了外界应力(例如从模型中取出时),铸件内部的温度还没有完全降低,容易产生缩孔。
(3) 金属液体凝固时的收缩:铝合金在凝固过程中会出现一定的收缩,如果凝固过程中支撑不稳定,就会导致缩孔产生。
二、缺陷产生的原因1. 原材料:如果原材料中含有过多的杂质或者粒度过大、成分不均匀等情况,会直接导致铝液在充填模具的过程中产生缺陷。
2. 熔化处理:熔炼过程中的温度不稳定、炉温控制不当,以及熔化时间过长等问题都会导致铝液中含气量增加,从而产生气孔等缺陷。
铸造铸件常见缺陷分析
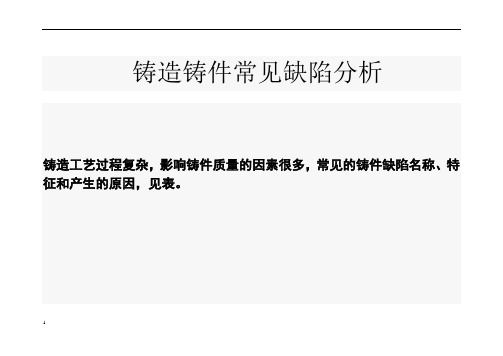
铸造铸件常见缺陷分析铸造工艺过程复杂,影响铸件质量的因素很多,常见的铸件缺陷名称、特征和产生的原因,见表。
常见铸件缺陷及产生原因缺陷名称特征产生的主要原因气孔在铸件内部或表面有大小不等的光滑孔洞①炉料不干或含氧化物、杂质多;②浇注工具或炉前添加剂未烘干;③型砂含水过多或起模和修型时刷水过多;④型芯烘干不充分或型芯通气孔被堵塞;⑤春砂过紧,型砂透气性差;⑥浇注温度过低或浇注速度太快等缩孔与缩松缩孔多分布在铸件厚断面处,形状不规则,孔内粗糙①铸件结构设计不合理,如壁厚相差过大,厚壁处未放冒口或冷铁;②浇注系统和冒口的位置不对;③浇注温度太高;④合金化学成分不合格,收缩率过大,冒口太小或太少砂眼在铸件内部或表面有型砂充塞的孔眼①型砂强度太低或砂型和型芯的紧实度不够,故型砂被金属液冲入型腔;②合箱时砂型局部损坏;③浇注系统不合理,内浇口方向不对,金属液冲坏了砂型;④合箱时型腔或浇口内散砂未清理干净粘砂铸件表面粗糙,粘有一层砂粒①原砂耐火度低或颗粒度太大;②型砂含泥量过高,耐火度下降;③浇注温度太高;④湿型铸造时型砂中煤粉含量太少;⑤干型铸造时铸型未刷涂斜或涂料太薄夹砂铸件表面产生的金属片状突起物,在金属片状突起物与铸件之间夹有①型砂热湿拉强度低,型腔表面受热烘烤而膨胀开裂;②砂型局部紧实度过高,水分过多,水分烘干后型腔表面开裂;③浇注位置选择不当,型腔表面长时间受高温铁水烘烤而膨胀开裂;④浇注温度过高,浇注速度太慢一层型砂错型铸件沿分型面有相对位置错移①模样的上半模和下半模未对准;②合箱时,上下砂箱错位;③上下砂箱未夹紧或上箱未加足够压铁,浇注时产生错箱冷隔铸件上有未完全融合的缝隙或洼坑,其交接处是圆滑的①浇注温度太低,合金流动性差;②浇注速度太慢或浇注中有断流;③浇注系统位置开设不当或内浇道横截面积太小;④铸件壁太薄;⑤直浇道(含浇口杯)高度不够;⑥浇注时金属量不够,型腔未充满浇不足铸件未被浇满裂纹铸件开裂,开裂处金属表面①铸件结构设计不合理,壁厚相差太大,冷却不均匀;②砂型和型芯的退让性差,或春砂过紧;③落有氧化膜砂过早;④浇口位置不当,致使铸件各部分收缩不均匀铸件质量与气孔的关系1)合理选定铸造合金和铸件结构。
铸造缺陷及其解决方法
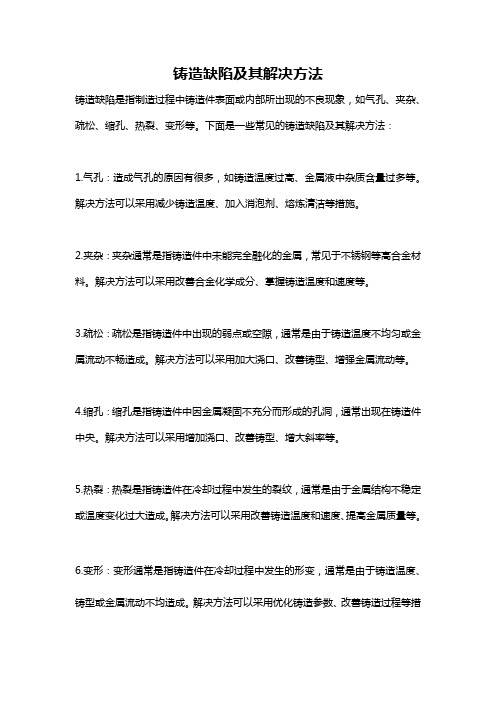
铸造缺陷及其解决方法
铸造缺陷是指制造过程中铸造件表面或内部所出现的不良现象,如气孔、夹杂、疏松、缩孔、热裂、变形等。
下面是一些常见的铸造缺陷及其解决方法:
1.气孔:造成气孔的原因有很多,如铸造温度过高、金属液中杂质含量过多等。
解决方法可以采用减少铸造温度、加入消泡剂、熔炼清洁等措施。
2.夹杂:夹杂通常是指铸造件中未能完全融化的金属,常见于不锈钢等高合金材料。
解决方法可以采用改善合金化学成分、掌握铸造温度和速度等。
3.疏松:疏松是指铸造件中出现的弱点或空隙,通常是由于铸造温度不均匀或金属流动不畅造成。
解决方法可以采用加大浇口、改善铸型、增强金属流动等。
4.缩孔:缩孔是指铸造件中因金属凝固不充分而形成的孔洞,通常出现在铸造件中央。
解决方法可以采用增加浇口、改善铸型、增大斜率等。
5.热裂:热裂是指铸造件在冷却过程中发生的裂纹,通常是由于金属结构不稳定或温度变化过大造成。
解决方法可以采用改善铸造温度和速度、提高金属质量等。
6.变形:变形通常是指铸造件在冷却过程中发生的形变,通常是由于铸造温度、铸型或金属流动不均造成。
解决方法可以采用优化铸造参数、改善铸造过程等措
施。
铸件缺陷的分析方法

铸件缺陷的分析方法在铸造生产中,要定期进行铸件缺陷分析,按照PDCA(Plan计划、Do执行、Check检查、Action总结处理)循环开展QC(Quality 质量、Control管理)小组活动,常用的铸件缺陷分析手法有直方图法、排列图法、因果图法、散布图法、控制图法、分层法、调查表法等。
1、直方图法直方图法是对定量数据分布情况的一种图形表示,如图1所示。
图1.直方图的基本形式(1)直方图的作用①了解整批或某一时间段内各种铸件缺陷的分布状况,从而确定主要铸件缺陷类型或主要铸件质量问题。
①及时掌握各工序能力及工序能力保证铸件质量的程度,并通过工序能力估算工序的铸件不合格率。
(2)直方图(又称频数分布图)的作图方法与步骤①收集数据(不少于100个,一般取100个为宜)。
①找出数据中的最大值与最小值,计算极差R。
①确定组数k与组距h(组数k值应根据样本数量决定,组数太少反映不出真实情况,组数太多又会减弱分布规律)。
①确定各组的上组界和下组界(分组的组界值要比抽取的数据多一位小数以使数据不会落在组界位置。
因此,先取测定单位的1/2,然后用最小值减去测定单位的1/2作为第1组的下界值,再加上组距,作为第1组的上界值,以此加到最大一组的上界值)。
⑤确定组的中心点[中心点=(上组界+下组界)/2],整理数据表中数据,制作频率表⑥绘制直方图(在方格纸上,以分组的组界值为横坐标,各组的频数为纵坐标,用直线连成直方块,即可得到直方图)。
2、排列图法排列图法是将一定期间所汇集的缺陷数、不良数等数据依项目、原因加以分类,并按其影响程度的大小加以排列的图形,如图2所示。
图2.排列图(铸件不合格品)(1)排列图的作用①分析铸件缺陷的主要类型。
①分析产生铸件缺陷的主要工序的原因。
①分析产生铸件缺陷的关键工序。
①分析铸件缺陷类型的主次地位等。
(2)排列图(又称柏拉图)的作图方法与步骤①收集一定期间的数据。
①将收集的数据进行整理。
射线检测中铸件常见缺陷特征辨析
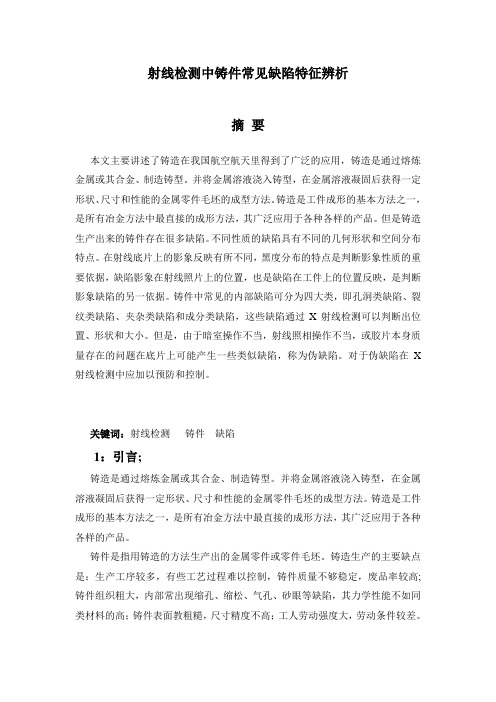
射线检测中铸件常见缺陷特征辨析摘要本文主要讲述了铸造在我国航空航天里得到了广泛的应用,铸造是通过熔炼金属或其合金、制造铸型。
并将金属溶液浇入铸型,在金属溶液凝固后获得一定形状、尺寸和性能的金属零件毛坯的成型方法。
铸造是工件成形的基本方法之一,是所有冶金方法中最直接的成形方法,其广泛应用于各种各样的产品。
但是铸造生产出来的铸件存在很多缺陷。
不同性质的缺陷具有不同的几何形状和空间分布特点。
在射线底片上的影象反映有所不同,黑度分布的特点是判断影象性质的重要依据,缺陷影象在射线照片上的位置,也是缺陷在工件上的位置反映,是判断影象缺陷的另一依据。
铸件中常见的内部缺陷可分为四大类,即孔洞类缺陷、裂纹类缺陷、夹杂类缺陷和成分类缺陷,这些缺陷通过X射线检测可以判断出位置、形状和大小。
但是,由于暗室操作不当,射线照相操作不当,或胶片本身质量存在的问题在底片上可能产生一些类似缺陷,称为伪缺陷。
对于伪缺陷在X 射线检测中应加以预防和控制。
关键词:射线检测铸件缺陷1:引言;铸造是通过熔炼金属或其合金、制造铸型。
并将金属溶液浇入铸型,在金属溶液凝固后获得一定形状、尺寸和性能的金属零件毛坯的成型方法。
铸造是工件成形的基本方法之一,是所有冶金方法中最直接的成形方法,其广泛应用于各种各样的产品。
铸件是指用铸造的方法生产出的金属零件或零件毛坯。
铸造生产的主要缺点是:生产工序较多,有些工艺过程难以控制,铸件质量不够稳定,废品率较高;铸件组织粗大,内部常出现缩孔、缩松、气孔、砂眼等缺陷,其力学性能不如同类材料的高;铸件表面教粗糙,尺寸精度不高;工人劳动强度大,劳动条件较差。
目前,我厂铸造生产出的工件大多数都是铸件,但是其存在很多的缺陷,因此我们常采用x射线检测,其特点:第一,对工件无特殊要求,检验结果显示直观;第二,检验技术和检验工作质量可以自我检测。
2:缺陷识别概述正确地识别射线照片上的影象,判断影象所代表的缺陷性质的基础是:(1)具有一定的材料和工艺方面的知识,掌握缺陷的可能形成和发生规律。
铸造缺陷分析
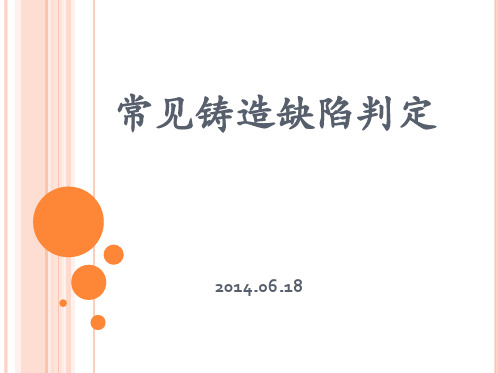
力学性能检测、金相检测、化学成分检测
拉伸试验机 光谱检验仪
冲击试验机 化学分析
此些
检测
方法
和前
面的
硬度
金相显微镜
检测 一起
可统
称为
力学性能:抗拉强度、 材料
屈服强度、延伸率、
检测
冲击功
金相组织:石墨形态、
石墨大小、球化级别、
基体组织
化学成分:C、SI、
MN、P、S、MG
超声波、磁粉、着色、X射线检测
大 类
序 号
缺陷名称
特征
31
硬度不符
硬度测试值不在规格之内或落差较大不符 合要求者
32 力学性能不符 性能
力学性能不符合相关标准或客户要求
成分 33 化学成分不符 金相
化学成分不符合相关标准或客户要求
组织 不合
34
金相组织不符
金相组织不符合相关标准或客户要求
格
铸件在凝固时出现化学成份不一至现象,
35
B. 裹携气孔(或卷入气孔); C. 析出气孔; D. 内生式反应气孔;
E. 外生式反应气孔
皮下 气孔
缩孔(1)
客户的投诉
热节缩孔
典型的缩孔特征
铸件表面缩凹, 可认为缩孔的
一种
缩孔(2)
冒口颈缩孔
内浇口缩孔
分类(4)
大 类
序 号
缺陷名称
特征
孔8 洞 类9 缺 陷 10
缩松 渣孔 砂孔
在铸件内部存在的微小不连贯的缩孔,聚 集在一处或多处,晶粒粗大,各晶粒间存在
常见铸造缺陷判定
2014.06.18
概念
1、铸造缺陷是铸造生产过程中,由于种种原因, 在铸件表面和内部产生的各种缺陷的总称;
铸件缺陷分析与失效分析
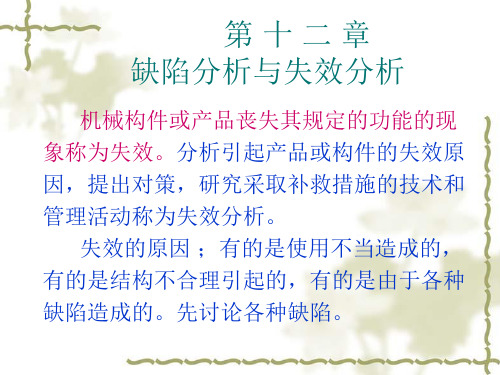
铸造缺陷
⒉内部气泡 特征:位于铸件内部的气泡.内壁光滑呈圆 形或椭圆形,宏观横断面低倍组织可观察到内 壁发亮的气泡. ㈡ 气泡的形成机理 ⒈析出气泡:钢液内气体随着温度降低溶解 度而析出,来不及逸出. ⒉侵入气泡:模壁泥芯壁的水分有机物挥发 分解碳酸盐分解的气体,来不及逸出.
铸造缺陷
⒊反应气泡:液态金属中的金属氧化物和液 态金属中的其它元素反应,液态金属与型腔壁 芯壁中的物质反应产生的气体.来不及逸出. ⒋卷入气泡:浇铸过程中,由于先注入的金 属液体表面已凝固,浇铸时带入的气体来不及 逸出.
铸造缺陷
有液态金属的补充,在完全凝固后产生许多 细小的孔洞形成疏松。又分一般疏松,中心 疏松。在铸件和铸锭中所出现的组织不致密 现象称为疏松。
铸造缺陷
一般疏松3级, 中心疏松3级,
铸造缺陷
三.缩孔 由于最后凝固部位得不到液态金属的补充 而形成的空洞.缩孔的特征是宏观酸蚀试样的 中心区域呈不规则的折皱裂纹或孔洞,经常伴 随严重疏松夹渣和成分偏析. 四.夹杂 分非金属夹杂和异金属夹杂 ㈠非金属夹杂物 ⒈夹渣:形状不规则的非金属夹杂物,通常
㈠弹性变形失效: 弹性变形过量造成弹性 丧失。 ㈡塑性变形失效: 塑性变形过量造成变形 量超过一定极限,形状或尺寸变化造成失效不 能使用。
㈢蠕变变形失效: 零件长时期在一定温度 和压力作用下工作,即使小于屈服点也会缓 慢地产生塑性变形,这种现象称为蠕变。当 蠕变变形量超过规定数值后就会发生失效, 甚至产生蠕变断裂。 ㈣高温松弛失效: 零件在高温下失去弹性 功能,产生塑性变形而失效。
热处理缺陷
过程中的缺陷(过热、折叠等)都可以成为 淬火裂纹的诱发源。 ⒊形状结构对淬火裂纹的影响 形状结构设计不合理 截面尺寸不均匀 带有应力集中部位 ⒋原始组织对淬火裂纹的影响 均匀的球化P淬火后转变成M其比容变化 较小,故得到的M内应力较小不易开裂
铸造气孔电镜扫描分析
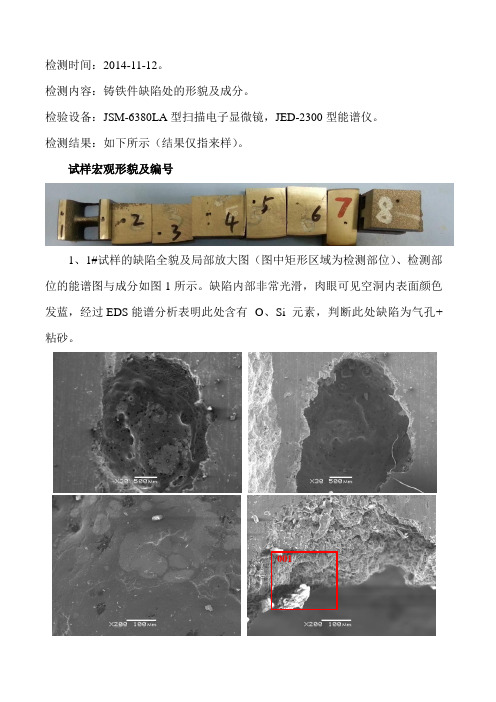
检测时间:2014-11-12。
检测内容:铸铁件缺陷处的形貌及成分。
检验设备:JSM-6380LA型扫描电子显微镜,JED-2300型能谱仪。
检测结果:如下所示(结果仅指来样)。
试样宏观形貌及编号1、1#试样的缺陷全貌及局部放大图(图中矩形区域为检测部位)、检测部位的能谱图与成分如图1所示。
缺陷内部非常光滑,肉眼可见空洞内表面颜色发蓝,经过EDS能谱分析表明此处含有O、Si元素,判断此处缺陷为气孔+粘砂。
001图1 1#试样缺陷全貌、局部放大图及001区能谱图与成分 2、2#试样的表层缺陷全貌及局部放大图如图2所示。
缺陷内部较光滑,未见到明显大块非导电物质,如夹砂、粘砂、夹杂物及夹渣。
缺陷内部002区成分见图2所示,经过EDS 能谱分析表明此处主要含有Fe 、Si 元素。
综合判断:2#试样的缺陷类型属于皮下皮孔。
元素Wt% C 6.23 O 1.20 Mg 2.86 Al 2.15 Si 9.47 Ti 2.19 Mn 4.15 Fe 余量O 47.99 Al 2.13 Si 37.46 K 0.15 Fe 余量002元素Wt%Na 1.09Si 3.79Mn 1.46Fe 余量图2 2#试样表层缺陷全貌、局部放大图及002区能谱图与成分3、3#试样的表层缺陷全貌及局部放大图如图3所示。
缺陷呈规则圆孔状,内部较光滑,未见到明显大块非导电物质,如夹砂、粘砂、夹杂物及夹渣。
缺陷内部003区经过EDS能谱分析表明此处主要含有Fe、Si元素。
综合判断:3#试样的缺陷类型属于皮下皮孔。
003元素Wt%Si 6.04Fe 余量图3 3#试样内部缺陷全貌、局部放大图及003区能谱图与成分4、4#试样的表层缺陷全貌及局部放大图如图4所示。
缺陷内部较光滑,未见到明显大块非导电物质,如夹砂、粘砂、夹杂物及夹渣等。
孔壁内部004区经过EDS能谱分析表明此处主要含有Fe、Si元素。
综合判断:4#试样的缺陷类型属于皮下皮孔。
- 1、下载文档前请自行甄别文档内容的完整性,平台不提供额外的编辑、内容补充、找答案等附加服务。
- 2、"仅部分预览"的文档,不可在线预览部分如存在完整性等问题,可反馈申请退款(可完整预览的文档不适用该条件!)。
- 3、如文档侵犯您的权益,请联系客服反馈,我们会尽快为您处理(人工客服工作时间:9:00-18:30)。
Volume expansion
由于入水口的铁 水乱流产生的气 泡,由于共晶凝 固時铁水体积膨 胀,气泡変形
大气孔缺陷-4 由于Mg气体引起气孔的分析例
Mg(铁水) ↓ Mg(气体)
大气孔缺陷-5 由于乙炔气体引起气孔的分析例
MgC2+H2O → C2H2
Graphite
分析气泡内部气 体,检测出乙炔 气体
粘砂缺陷分析例-4(化学性的)
Fe-Mn-Si-O 的分布呈重叠 状,石英砂表 面有低融点物 質生成。
4.5 包砂缺陷
由于鋳型出现裂纹、共晶凝固 時铁水的体积膨胀、呈飞边状 铁水钻进鋳型。 鋳型的原因 ①膨胀量大 ②高温強度低 ③充填性高 ④造型時裂了 ⑤由于鋳型的热量产生的保温 效果
共晶凝固時铁水 体积増加
针孔-7 熔渣生成型:接種剤熔渣的分析例
Inoculant Ba.Ca
检测出接種剤成 分(Ba,Ca)。 熔渣化
针孔缺陷-8 熔渣生成型:球化剤熔渣分析例
检测出球化剤 成分(Mg,Ba, Ca)。
Spheroidizer Mg,Ba.Ca
熔渣化
针孔缺陷-9 熔渣生成型:硫化锰熔渣的分析例
Manganese sulfide slag
(B-1) Solidification film oxidation type (B-2) Residual liquid oxidation and condensation type
氧化反应型针孔缺陷
针孔缺陷机理-3 (主要是亜共晶鋳鉄) 氧化反应型的针孔缺陷
溶解型针孔缺陷
针孔缺陷的机理-4(主要是亜共晶鋳鉄) 熔渣生成型的针孔缺陷
夹杂物缺陷分析例-6(球化剤)
检测出球 化剤成分
夹杂物缺陷分析例-7(陶瓷滤渣片)
Al成分多 破面多孔 耐火度高
夹杂物缺陷分析例-8(铁豆)
Cold shot
由于 铁豆 表面氧化, 熔渣在周囲 生成。
Slag
4.4 粘砂缺陷
A)物理的粘砂的要因 铁水静圧 铁水動圧 共晶凝固時铁水体積膨胀 鋳型間隙 鋳型背圧 汽态浸透 等 B)化学性粘砂的要因 铁水和鋳型浸湿 低融点物質的生成(铁橄榄石等) C)物理・化学性的粘砂要因 中間・複合型
冷龟裂和热 龟裂的对比
Dendrite
裂纹缺陷-2 由于异常元素的偏析造成裂纹
由于Cr,Cu, Al等的偏析 导致裂纹缺 陷
裂纹缺陷-3 由于阻碍球化导致出现裂纹(线状)
Flake graphite
由于阻 碍球化 导致裂 纹发生
Spheroidal graphite
4.7縮孔缺陷
夹杂物缺陷的分析例子-1(型砂)
Green sand Clay or slag
聚集起来的型砂。 在石英砂表面检测 出粘土矿物。 渣化后发生气体。
夹杂物缺陷的分析例子-2(芯砂)
Core sand
一般的来说由于芯 砂没粘有耐火度低 的粘土矿物质,所以 不聚集。 平滑的石英砂表面。
夹杂物缺陷分析例-3(夹砂和气体)
•
针孔缺陷的机理-1 (主要是亜共晶鋳鉄) 物理型针孔缺陷
30 Pure Iron Eutectic Cast Iron
H2 Solubility,ppm
20
物理型针孔缺陷
10
γ
δ
0 1100 1200 1300 1400 Temp. ℃ 1500 1600
Liquid
针孔缺陷机理-2 (主要是亜共晶鋳鉄) 氧化反应型的针孔缺陷
针孔缺陷-3 氧化反应型:残液氧化濃縮型的分析例子
Dendrite
特征是在内部被检 测出O。 通过树枝状晶体结 晶后的残液的FeO,检 测出O。 检测出气体气泡核( MnS)和使表面張力下 降的Al,Ti。
针孔缺陷-4 溶解型:H2O分析例
Graphite
在浇包干燥不 十分時会発生。 气体气泡的核( MnS) 检测出微量的O
(D-2) (D-3) (D-4)
接種剤・球化剤系列熔渣 硫化物系熔渣 夹砂系列及夹杂异物系列熔渣
针孔缺陷分類的要点
• • • • • • • 缺陷形状(树枝状晶体形態):由于液相或固态液态共存区域,导致气泡的形状不 一样,所以可以推测出气泡发生的时间。 缺陷发生位置:根据和浇注的位置、方案的位置、凝固覆膜上、凝固覆膜正下方、 凝固関係、砂芯面附近等缺陷生成可了解到宏观信息。 石墨膜:由于主要在气泡里结晶的是石墨、根据石墨的有無或石墨的量,可以推 断出气泡的气体和气泡生成時间。在石墨膜上有成为气泡核的物質存在。石墨膜 也有剥落的。 核:根据形成气泡核的物質、硫化锰、微細熔渣、氧化物等,并依据其种类和量可 以推测出核的生成原因。 微量元素的检测:Al(与水蒸気的脱氧反应)、Ti(表面張力低下)、Zn(气化)、Cu(晶粒 边界偏析元素)、其他。 氧化:根据EDS分析中的氧气检测,判断金属氧化物的存在、缺陷是否是氧化反应 型。試料生锈时不能判定。另外,如果熔渣多的话,在熔渣中就含有氧气。 提高电流:在SEM分析中,非导電性物質2次電子的反射是无规则的,没有图像, 变成白色光泽状態的画像信息。因此,提高电流时,图像信息时,可以判断缺陷内 有非导電性物質。是作为缺陷内的非导電性物質的话熔渣、石英砂等非金属夹杂 物。 非金属夹杂物(熔渣):通过成分分析,了解到其发生的原因。作为例子,熔渣中如 果K多的话,石英砂熔渣化。Ca多的话,就是浇包熔渣和接種剤系列,根据Mn量, 来判断锰硅酸盐熔渣的生成度等。再有,多数是石英砂、滤渣片、涂料等造成的。
Dendrite
针孔缺陷-5 熔解型:N2分析例
Graphite Dendrite
冷芯盒做的砂芯 面上龟裂状的小气 孔(多数) O未检测出 气体气泡的核(MnS )
MnS
针孔缺陷-6 熔渣生成型:锰硅酸盐熔渣分析例
Manganese silicate slag
从锰硅酸盐系列熔 渣发生气体。 氧化Slag + C → CO,CO2(g)
熔渣生成型的针孔缺陷
针孔缺陷-1 物理型分析例子
Graphite
Nucleus
是液相发生的 ,由于表面張力 的原因変成球状 。气泡生成后,石 墨结晶。气泡核 存在在石墨膜上 。
针孔缺陷-2 氧化反应型:凝固膜氧化型的分析例子
缺陷内部与 非缺陷部的黒皮 部位比較,O多。 氧化物生成的自 由能量低的元素 偏析。
壳模砂芯的气体
有条纹状的锰硅 酸盐熔渣
Manganese silicate slag
大气孔缺陷-2 由于碱性酚醛树脂砂芯引起的气孔分析例
Dendrite
碱性酚醛树脂砂 芯气体 通过减低树脂量 来解決 变更成低树脂高 强度的石英砂
Catch of inclusion
大气孔缺陷-3 由于空气巻入引起的气孔分析例
硫化锰的熔渣 化
4.2 大气孔缺陷
卷入鋳型的气体 砂芯,砂型,塗型,铸型表面稳定剤,粘接剤 等
空气卷入
从浮渣、熔渣里发生的 气体 小气孔缺陷的成長
乱流,入水口,冷隔,铁豆
球化剤,接種剤,锰硅酸盐系列熔渣,夹砂等
物理型,氧化反应型,熔解型,熔渣生成型等
大气孔的缺陷-1 由于壳模砂芯气体引起的气孔分析例
粘砂缺陷的判定概念
物理性的粘砂缺陷
中間性的 粘砂缺陷
化学性的粘砂缺陷
粘砂缺陷分析例-1(物理性的)
石英砂是非熔 融石英砂与金 属的表面不重 叠
粘砂缺陷分析例-2(中間)
在石英硅砂表 面生成低融点 物質。 石英砂一部分 熔融。
粘砂缺陷分析例-3(中間)
粘砂部和铸件 部的界面看到 有熔融石英砂。
外面張力缺陷 包砂缺陷-1 粘砂缺陷
包砂缺陷-2(低融点物質)
Veining
低融点 物質生 成、从这 里发生 包砂
Low melting material
4.6 裂纹缺陷
热龟裂 ①在固相线附近的凝固収縮 ②由于硫黄的渗硫造成脆化 冷龟裂 ①打痕和冲击 ②由于拆箱早造成収縮
裂纹缺陷-1 热龟裂和冷龟裂
分析顺序 ①确认缺陷的全部。 ②确定缺陷内部分析的 部位。注意不要使检测 器出现阴影。 ③分析。 ④拍摄分析部位的SEM 图像 ⑤分析其他的分析部分 。 ⑥拍摄整体图像
⑤分析-2
由于試料的观察方向的不同,形状有时也会不一样。 最初先观察試料的整体,再依次扩大。
4.1针孔缺陷
根据表面分析将针孔缺陷分類
4.3 夹杂物缺陷
①夹砂 ②夹砂和夹渣 ③夹渣 ④夹杂其他异物 接種剤,铁豆,除渣剂,滤渣片,涂料等
发生夹杂物(夹砂缺陷)的机理
由于型砂・熔渣铁水造成的変化
Silica sand
Manganese silicate slag
夹杂物 (异物夹杂)
在鋳型型腔内,放置 浇包熔渣、除渣剂、 接種剤2種,人为地 制造夹杂异物的缺 陷。
①分析試料采集-1
在夹砂集中的部位和渣化处。 分析的地方,由于缺陷内部不一样,所以列举了N数。
①分析試料采集-2
試料1:左 没有石墨 膜、右 有 試料2:没有石墨膜 試料3:有石墨膜
分析的部位,有时缺陷内部 不一样。→列举N数。
刀片的成分
③試料清洗
試料2:将試料切断 時的脏东西(刀片) 通过清洗去掉 試料1:清洗时去掉 試料上的锈、毛刺。 用镊子等去掉毛刺
2.SEM・EDSの概説 3.SEM・EDSの試料制作 4.鋳造缺陷解析・・・・以气孔缺陷为例,如若有時間 的话,就其他缺陷作一说明
2.SEM・EDSの概要(SEM)
2.SEM・EDSの概要(EDS)
3. SEM・EDS的試料制作
① 采用的分析試料・・・要有代表性的、最少3处以 上。不能有锈、不能有涂料等的附着物。 ② 試料切断・・・不能损伤試料,要易于分析。特性X 線要可以检测出来。 ③ 試料的清洗・・・去掉切断時的脏东西。清洗后要 十分干燥。可以抽真空。 ④ 試料真空镀敷(离子涂覆)・・・真空镀敷时根据需 要进行。 ⑤ 分析・・・先用低倍率看整体,之后,再提高倍率。